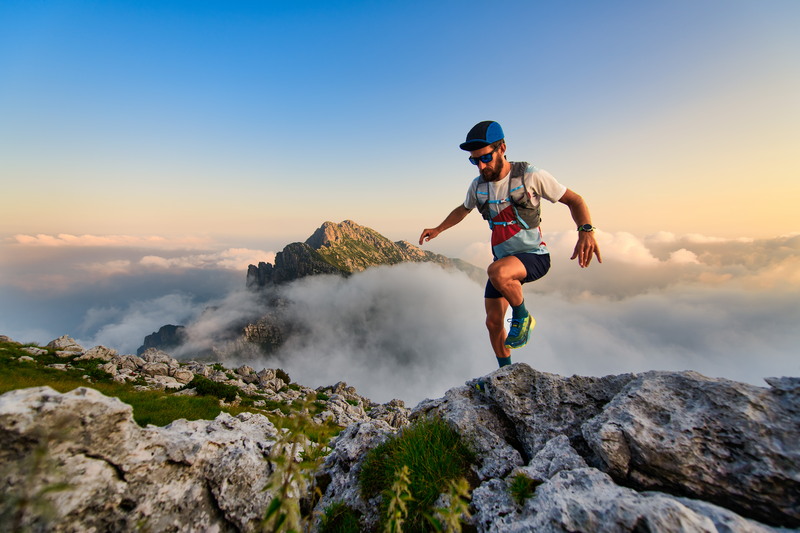
95% of researchers rate our articles as excellent or good
Learn more about the work of our research integrity team to safeguard the quality of each article we publish.
Find out more
METHODS article
Front. Earth Sci. , 25 April 2022
Sec. Geohazards and Georisks
Volume 10 - 2022 | https://doi.org/10.3389/feart.2022.894118
This article is part of the Research Topic Advances in Modeling, Assessment, and Prevention of Geotechnical and Geological Disasters View all 44 articles
The stability of section coal pillars is one of the most important factors affecting the stability of coal rock systems in the stope and roadway. This study aimed to develop an artificial intelligence methodology to predict and evaluate coal pillar stability. Data from 125 published coal pillar historical cases were collected to build a sample dataset. Meanwhile, a mean impact value-genetic algorithm-back propagation neural network (MIV-GA-BP) fusion model was established to predict the stability of section coal pillars. MIV tests indicated that the main factors influencing coal pillar stability are (in order of decreasing importance): the coal seam buried depth > coal seam thickness > working face length > coal elastic modulus > cohesion > tensile strength > internal friction angle > Poisson’s ratio > volume weight > coal seam dip angle. The relative weights of mine design parameters are generally greater than those of the physical and mechanical parameters of coal and rock mass. After the BP model was optimized by GA, the relative error, R value, and mean squared error were 5%, 0.95, and 0.13, respectively. These results confirm that the machine learning model has significant potential for improving coal pillar stability evaluations. The developed prediction model was applied to two field cases to verify its effectiveness, and the results indicated that the innovative method can be extended for use in similar geological conditions or other mining and geaological engineering fields.
In the context of long-term and large-scale underground mining in Chinese coal mines, the goaf represents one of the critical factors influencing the safety of mine production. Coal pillars are the main structural units contributing to the stability of a goaf, and therefore, it is crucial to evaluate the stability of coal pillars to enable efficient and safe mining in underground mines.
In recent decades, scholars have adopted various methods to understand and predict the stability of coal mine pillars. Empirical methods are usually based on an empirical formula that is used to estimate the strength of each coal pillar (Hustrulid, 1976; Jawed et al., 2013; Lai et al., 2020). Because it is difficult to determine the actual stress on an underground mine, the safety factor (FS) of the coal pillar (i.e., the ratio of its average strength to average stress) is computed to evaluate its stability (Deng et al., 2003). In general, FS > 1.0 is stable, whereas FS < 1.0 is unstable (Zhou et al., 2011; Wattimena, 2014; Zhou et al., 2022).
Numerical simulation technology has gradually been applied for coal pillar stability analysis. Deng et al. combined Monte Carlo and FLAC (Fast Lagrangian Analysis of Continua) methods to analyze the stability of coal pillars. Mortazavi et al. (2009) used UDEC (Universal Distinct Element Code) software to evaluate the influence of a pillar’s geometry and mechanical parameters on its deformation and failure. These studies have significantly improved our understanding regarding the stability of coal pillars; however, because of the numerous influencing factors, these two methods have difficulty considering the impact of uncertainty, and the limit of the safety factor is not clear.
With recent advances in data mining technology, intelligent evaluation models have been successfully applied in the field of mining engineering, which constitutes a key development direction for the future of coal mining. For example, Deng et al. (2002) used an improved finite element Monte Carlo method to analyze the reliability of point pillars in metal mines. Zhao et al. (2003) and Luo et al. (2007) evaluated the stability of coal pillars based on dynamic fuzzy reliability. Cauvin et al. (2009) combined the Monte Carlo and safety factor methods to analyze the stability of coal pillars Monjezi et al. (2011). used a neural network algorithm to predict coal pillar stress to guide coal pillar design strategies Idris et al. (2015). combined the Monte Carlo method, neural networks, and FLAC3D (Universal Distinct Element Code 3D) to analyze the stability of coal pillars during excavation. Wattimena et al. (2013) used multiple logistic regression model to predict the stability of 89 hard rock coal pillars. Zhou et al. (2015) compared the performance of six supervised learning algorithms [i.e., linear discriminant analysis (LDA), polynomial logic regression (MLR), random forest (RF), artificial neural network (ANN), support vector machine (SVM), and gradient hoist (GBM)] for coal pillar stability identification based on 251 examples of hard rock coal pillars; they determined that the SVM and RF algorithms showed superior performance. Ghasemi et al. (2010) used Monte Carlo simulations to study the influence of various parameters (e.g., uniaxial compressive strength of coal sample, width of coal pillar, height of coal pillar, width of entrance, and depth of covering) on the FS of coal pillars. Zhou et al. (2011) proposed two models for predicting the stability of coal pillars by employing support vector machine and Fisher discriminant analysis. However, the evaluation indicators of each of the described models are different, and anomaly detection is particularly important in high-dimensional data analysis. Thus, it is necessary to develop a reasonable and effective input parameter database and an intelligent model to evaluate the stability of coal pillars in Chinese mines.
Considering the limitations of the aforementioned models, the main contributions of the present study can be summarized as follows: 1) an energy conservation model of the longwall stope is introduced to identify the factors influencing coal pillar stability; 2) 125 historical cases of coal pillars in China are collected, and a large dataset comprising Chinese coal pillar information is compiled following anomaly detection and treatment; 3) the mean impact value (MIV) is used to evaluate the sensitivity of variables, and a genetic algorithm (GA) and back-propagation (BP) neural network fusion model is established to verify the prediction performance; 4) two field cases are discussed to evaluate the model’s prediction performance for coal pillar stability analysis.
Longwall mining induces the fracture of coal and rock mass. The phenomena of energy storage, energy consumption, and energy distribution co-exist during this process, which can be regarded as a gradual failure caused by energy transfer. As shown in Supplementary Figure S1, as the coal seam is mined out, the energy inside the system reaches an equilibrium state, resulting in the generation of an excavation disturbed zone (EDZ) (Lai et al., 2006), and the coal pillar is the main structural unit affecting the stability of the EDZ.
As shown in Supplementary Figure S2, the longwall stope and surrounding rock are regarded as a system wherein the balance between their energy components should be maintained. During the mining process of the working face, the back rock layer is allowed to collapse at a certain distance; the released energy increases the strain of the roof rock stratum, which causes the roof rock to fracture and cave, thus relieving the pressure and producing an area with a certain height above the stope, namely, the EDZ. The energy conservation model of the longwall stope was established by Rezaei et al. (2015). The total stress is determined according to the difference between the weight of overburden rock and the weight of the failure area. Then, the vertical component of the mining stress is determined by calculating the reciprocal angle of the strata collapse. Finally, the stress concentration coefficient of the coal pillar can be calculated according to the vertical component of the mining stress, which can guide the flow of the coal pillar stability analysis, as shown in Supplementary Figure S3.
The total strain energy consumption is stored in the mined coal body during roof rock fracture, caving, and pressure relief. Therefore, the strain energy in the mined coal body should be equal to that in the collapsed material in the failure area, as expressed in Eq. 1,
where Um is the strain energy in the EDZ, and Ud is the strain energy in the EDZ.
Rezaei et al. (2015) derived the formulas for calculating the stored strain energy in the coal seam, and the final equations for calculating the total energy storage of the coal seam are shown in Eqs 2, 3,
where v is the Poisson ratio of the rock mass; γ is the volume density of the overlying strata (N/m3); hs is the height of the coal seam; Lw is the height of the working face; Am is the cross-sectional area of the coal seam (such that Am = Lw × hs); σv is the vertical stress; H is the buried depth of the coal seam; and E is the elastic modulus of the coal seam. In general, in the failure zone (Ud), the storage strain energy of the material consists of elastic strain energy (UE) and viscoplastic strain energy (Uv). Here, Ad is the unit surface of the goaf (such that Ad = Lw × 1 m); σc is the uniaxial compressive strength of the goaf material; b is the expansion coefficient; σs is the stress threshold; B is the material constant related to viscosity and temperature; t is the pressure time of the goaf material; λ is the slope of the material hardening stage; and ω, a, and μ1 are material constants.
By substituting Eqs 2, 3 into Eq. 1, the EDZ height (Hd) under long-term conditions can be obtained using:
The vertical component of the mining stress (σa(v)) and the stress concentration coefficient (K) of the load transferred to the roadway and coal pillar can then be obtained, as shown in Eqs 5, 6, respectively:
These values enable the design of roadway supports and coal pillar stability analysis. The load of the overlying strata is transferred to the coal pillar through the suspended roof, which reveals different levels of integrity in different sections of the coal pillar (i.e., a crushing zone, a plastic zone, and an elastic zone).
Hou and Ma (1989) proposed a method for calculating the width of the stress limit equilibrium zone, as expressed in Eq. 7,
where φ and c represent the internal friction angle and cohesion of the coal seam, respectively.
Therefore, the coal pillar stability analysis in longwall mining involves a multi-factor nonlinear coupling problem, and the following factors affecting the stability of the coal pillar must be considered as thoroughly as possible.
1) Static parameters (the static physical and mechanical parameters of the coal and rock mass): elastic modulus, Poisson’s ratio, internal friction angle, cohesion, bulk density, etc.
2) Engineering disturbance parameters (also known as engineering design parameters): coal seam thickness, working face length, coal seam burial depth, coal seam dip angle (θ), coal pillar width (M), etc.
3) Time-varying parameters (parameters of goaf materials that vary over time): temperature, pressure, etc.
In conclusion, the influencing factors of coal pillar stability were determined, thereby providing a theoretical basis for establishing a coal pillar database. Additionally, the analysis offers reasonable model input factors for predicting coal pillar multi-factor nonlinear coupling disasters under engineering disturbance. Moreover, coal pillar stability control measures can be designed based on stope stress transfer to reduce mining stress transfer (e.g., via roof cutting and pressure relief), strengthen the support strength (i.e., roadway support), and optimize the coal pillar size.
In mining and geotechnical engineering, it is difficult to determine reliable input parameters and find effective methods for accurately describing this nonlinear relationship, and as a result, it is often challenging to assess reliability. This report aims to establish a coal pillar database and develop reliable datasets through data mining technology to improve the calculation performance of the described prediction model. The coal pillar data transfer pathway is illustrated in Supplementary Figure S4.
Certain coal pillar parameters are needed to establish the prediction model. To avoid overtraining, three parameter selection principles are applied. First, the sensitive parameters reflecting the stability of the coal pillar should be used as the evaluation index. Second, these parameters should be physically independent from one another. Finally, the parameter data should be easy to obtain. Combined with the factors influencing coal pillar stability, the coal seam thickness, working face length, coal seam buried depth, coal seam dip angle, coal elastic modulus, Poisson’s ratio, internal friction angle, cohesion, and volume weight are selected as independent variables, and the coal pillar width is taken as the dependent variable.
Notably, coal pillar stability is also impacted by other parameters, such as the overburden breaking state, disturbance characteristics, temperature and pressure of goaf materials, and monitoring signals. However, these index data are difficult to obtain (Dai et al., 2020), and without these indicators, the coal pillar stability can still be predicted within the allowable range of engineering measurement error.
The data used in this study were collected using internet research search engines and academic databases, including China National Knowledge Infrastructure (CNKI) and Google Scholar. The compiled data comprises 125 published coal pillar design history cases, including journal articles (90%) published by colleges and universities between 2002 and 2019. The missing items have been added to the original collection from available sources in other bodies of literature. Some data is based on existing technical reports and engineering survey data from research and design institutes.
The statistical distribution of the geographical locations of the mines is presented in Supplementary Figure S5. The most-studied geographical regions are Shaanxi (32%) and Shanxi (56%). Coal mines with section coal pillar widths of 11–20 m accounted for the highest proportion (60%), and the utilization of pillars less than 10 m or more than 30 m wide corresponded to 4 and 2.4%, respectively. Supplementary Figure S6 shows the original coal pillar dataset.
Single-variable empirical formulas are often used in coal pillar design and stability evaluations; these variables include γ, H, L, or Hd, and μ (Salamon and Munro, 1967; Bieniawski, 1968; Wilson, 1972). Previous studies (Dai et al., 2020) initially showed that coal pillar size can be estimated with reasonable accuracy, and it is more effective to use multiple measurement parameters for such predictions than to use a single parameter. Therefore, the input variables of the prediction model are σ, c, E, φ, γ, μ, H, α, h, and L, while M is the single output variable in this study.
The main tasks of this stage include data cleaning, integration, transformation, and reduction. This process is illustrated in Supplementary Figure S7.
As shown in Supplementary Figure S7A, the coal pillar database cleaning stage deals with missing and abnormal values. The missing values are filled by interpolation. If there are excess abnormal values, the data can be deleted directly. When there are fewer, the data can be added from other sources, i.e., data for adjacent working faces in the same mine are collected, and the average value is calculated to correct the abnormal value. As shown in Supplementary Figure S7B, the feature attribute expressions from multiple data sources are not necessarily matching. The main purpose is to detect and handle conflicts involving different meanings with the same name, same meanings with different names, and different units. 1) Different meanings with the same name: attribute ID (coal pillar value) in data source A1 and attribute ID (coal pillar value) in data source A2, respectively, describe small coal pillars and wide coal pillars, i.e., they describe significantly distinct entities. In this study, coal pillar data sources citing widths of less than 9 m are excluded. 2) Same meaning with different names: attribute ID (modulus of elasticity, Poisson’s ratio, bulk density) in data source B1 and attribute ID (bulk modulus, shear modulus, density) in data source B2 are related to one another, and they can be transformed and unified using:
where E is the elastic modulus, v is Poisson’s ratio, K is the bulk modulus, G is the shear modulus, γ is the bulk density, ρ is the density, and g is the acceleration of gravity. 3) Units are not consistent: the same entity is described with different measurement units.
As shown in Supplementary Figure S7C, the data transformation stage standardizes the data to meet the requirements of mining tasks and algorithms. Different coal pillar attributes often have different dimensions and units. Therefore, data standardization processing is necessary to eliminate the influence of different dimensions and sizes between indicators. This study used minimum-maximum normalization to map the results between (0,1). The conversion function is expressed in Eq. 9, (Wang et al., 2013),
where Xmax and Xmin are the maximum and minimum values in the data series, respectively, and Xij is the actual observed value.
As shown in Supplementary Figure S7D, the data specification stage merges many data points into attributes, such as filtering input parameters, which have a greater impact on weight. This improves modeling accuracy and reduces data mining time.
Prior to modeling, statistical analysis of the coal pillar database is very important. The basic descriptive results are shown in Supplementary Table S1.
The abnormal values in the database negatively impact the algorithm’s ability to determine the exact relationship between input and output parameters, thereby reducing the reliability of the model. In addition, outliers must be identified because they may create random phenomena with different behaviors in a single dataset.
Supplementary Figure S8 shows the box diagram of coal pillar characteristics. The center line of most attributes is in the center of the corresponding box, which means that the input parameters have generally symmetrical distributions. Among the influencing factors, tensile strength, cohesion, bulk density, coal seam dip angle, and buried depth include some abnormal values, which need to be processed.
Correlation analysis of the parameters in the coal pillar database is a fundamental aspect of data mining. Supplementary Figure S9 shows a scatter plot matrix for the dataset, where the distribution of each attribute is shown in the diagonal of the graph. The vertical axis of the diagonal histogram represents the frequency, the lower triangle area represents the scatter distribution of the dataset, and the range of the upper triangle area (which indicates the standard correlation coefficient between each pair of attributes) is from –1 to 1. When this parameter is close to 1 or –1, there is a strong positive or strong negative correlation, respectively Koo and Li (2016). proposed that R values < 0.5, between 0.5 and 0.75, between 0.75 and 0.9, and >0.90 indicate poor, medium, good, and excellent correlations, respectively. Most parameters have relatively poor correlations with one another (i.e., R < 0.5), which suggests that each characteristic attribute is independent from the others. In addition, the independent datasets essentially follow normal distributions, with few outliers. This may indicate that, although the amount of available data is relatively small, it is true that the distribution is approximately random.
High-dimensional data are difficult to visualize, and therefore, it is necessary to compress the dataset. Currently, MIV is considered one of the best indicators for evaluating the correlations between variables in neural networks (Wang, 2013). Specifically, MIV is used to measure the weight matrix change for each variable in a neural network; this process can quantitatively describe the importance of an independent variable to the dependent variable. Back-propagation neural networks are widely used because of their simple defining principle and facile implementation. However, BP also has limitation, i.e., it is easy to shake, easy to fall into a local minimum, and sensitive to the initial value in the training process. After the fusion of the genetic algorithm and BP, the GA can control the convergence of the model and improve the optimization time performance of the algorithm (Goldberg, 1989). Supplementary Figure S10 shows the principle of a MIV-BP-GA model.
Before modeling, the entire dataset is divided into a training set and a test set, which are used for training the model and evaluating the generalization performance of training model, respectively. Optimization analysis is typically used to determine how to divide the data into a training set and a test (Qi et al., 2018a). In this study, the proportions corresponding to the training set and test set were determined by a trial-and-error method where the size of the training set was increased between 30 and 90%. This analysis revealed optimal training set and test set proportions of 80 and 20%, respectively. The test set should be mutually exclusive relative to the training set as much as possible. Moreover, the training and test sets should have similar statistical characteristics because they are randomly extracted from the same complete dataset.
To improve the evaluation performance of the prediction model, it is necessary to carefully select an appropriate verification method for parameter adjustment. K-fold cross-validation (CV) is the most popular strategy to overcome data scarcity (Braga-Neto et al., 2004). K-fold CV reduces variance by averaging the results of different K-folds of the training set. In this study, the K value was set to 10 based on a previous report (Rodriguez et al., 2010). The 10-fold CV process applied in this study is shown in Supplementary Figure S11. The performance evaluation indices, e.g., mean squared error (MSE) and R, of each calculation model can be calculated using Eqs 10, 11, respectively:
Ten characteristic attributes were used as input for 50 iterations of an MIV test (Koo and Li, 2016), and adjustment rates of 10, 20, and 30% were used to calculate the MIV of each attribute. Different input and output variables exhibit positive and negative correlations, which indicates that MIV can have positive and negative numbers. To compare the influential weights of different input parameters, all MIVs were taken as absolute values, and the weight changes were calculated under each |MIV| mediation rate. Owing to the similar influential weight trends under each regulation rate, a rate of 20% was used for analysis, as shown in Supplementary Figure S12.
Supplementary Figure S12 shows that the factors influencing the stability of coal pillar have the following relative importance: H > h > L > E > c > σ > φ > μ > γ > θ. The influence scores of engineering disturbance parameters (e.g., H, h, L) are generally greater than those related to the physical and mechanical parameters of rock mass (e.g., c, σ, φ, μ, γ), which indicates that analyzing the mining design and engineering disturbance factors is crucial for ensuring the stability of coal pillars. The Shaanxi and Shanxi areas of China have suitable coal seam geological conditions, and thus, the dip angle of coal seams can be ignored, although the buried depth, thickness of coal seams, and length of the working face should be taken into account. In terms of the physical and mechanical parameters of the rock mass, there is little difference among the parameters, although it is clear that the elastic modulus, cohesion, and tensile strength should be obtained accurately. Of course, the internal friction angle, Poisson’s ratio, and bulk density are also of analytical significance. To reduce the data dimension and enhance the prediction time and accuracy of the model, the coal seam dip angle is eliminated (with an elimination rate of 10%), and the other nine variables are included in the prediction model.
One of the most difficult tasks in modeling is determining the network training algorithm and network structure. The number of hidden layer nodes has a significant impact on the model’s prediction performance (Mohamad et al., 2016). The upper limit of hidden layer nodes is 2Ni+1, where Ni is the number of input parameters. Considering the prepared dataset (where Ni = 9). The optimal number of hidden layer nodes is 14, which indicates a three-layer topology structure. Parameter tuning is essential for successful modeling. In this study, a GA is used to optimize the network parameters. The model parameters are shown in Supplementary Table S2.
MSE and R served as evaluation indicators. Supplementary Figure S13A compares the predicted and experimental values; the relative error between the expected value and the value predicted by the network prediction model is less than 5%. The regression analysis is shown inSupplementary Figure S13B. Most points fall near the fitting line, the R value of the predicted and expected values is 0.83, and the MSE of the model is 0.15, indicating that the prediction effect of the MIV-BP-GA model is both reasonable and applicable.
The Yujing coal mine (YCM) and the Xiaobaodang coal mine (XCM) were used to validate the engineering applicability of the developed model for real mines. The location and development plan of these mines are presented in Supplementary Figure S14.
According to the background of the 90101 fully-mechanized top coal caving face in the YCM, the 90101 working face length is 151 m, the average buried depth is 180 m, the coal mining thickness of the working face is 5.6–9.5 m (average thickness = 8.1 m), and the inclination angle is 2. The MIV-GA-BP model was used to predict the coal pillar width of the typical working face in this section of the mine (Supplementary Table S3).
The coal pillar width predicted by the MIV-GA-BP model was 16.4742 m. When a 16-m-wide pillar used in the field design, the surrounding rock deformation of the roadway was small, and the control effect was good.
The coal seam dip angle of the 112202 working face in the XCM is 1–3, with an average coal thickness of 5.5 m and an average buried depth of 300 m. The coal pillar width of the typical working face in this section (112202) was predicted using the developed model (Supplementary Table S4).
The coal pillar of the 112202 working face is predicted to be 22.4652 m, whereas a 20-m-wide coal pillar was used in the field design. Extensive calculations indicate that the coal pillar on the XCM site has potential instability, thus highlighting the important guiding role of coal pillar stability evaluations before mining.
According to on-site investigations, the 112202 working face encounters hidden dangers, such as large deformation, a serious slope, and difficult coal pillar support in the empty section. Under conditions involving fast advancing speeds (15 m/d) and strong mining at the super-long working face (350 m), a large area of roadway roof has fallen in the leading face area (Supplementary Figure S15). This confirms that the coal pillar stability identification model applied herein exhibits certain accuracy.
Stability control technology for “roadway advanced reinforcement support” was formulated for the 112202 working face by combining the prediction results and mining process parameters. The reinforcement and support measures were designed for the advanced area (T1–T6 in Supplementary Figure S15) with potential safety hazards.
For the roadway roof (Supplementary Figure S16A): 1) the roof is paved with diamond-shaped metal mesh (mesh = 50 × 50 mm); 2) the roof anchor cable is a Φ21.6 × 8300 mm steel strand with four supports in each row (spacing between supports = 1500 mm, pre-tightening force = 200 kN, anchoring force ≥280 kN), and the double-layer W-shaped steel guard plate (4 × 280 × 5100 mm) is used as a connection; 3) the anchor bolt is supported with a W-shaped steel guard plate (4 × 280 × 4300 mm), and a left-hand screw thread steel bolt without longitudinal reinforcement and an arch prestressed tray (150 × 150 × 10 mm) are used for support.
For the mining side of roadway (Supplementary Figure S16B): 1) the mining side is reinforced with a Φ22 × 2600 mm high-strength glass fiber-reinforced plastic anchor rod and a pine pallet (400 × 200 × 50 mm) with circular glass fiber-reinforced plastic mesh; 2) there are four anchors in each row (spacing between rows = 850 × 900 mm, top anchor bolt = 300 mm away from the roof, elevation angle = 15°) with plastic steel mesh laid on the upper part (mesh size = 40 × 40 mm), 3) before the support, the W-shaped tray should be unloaded, and the failed bolt should be repaired.
For the coal pillar side of roadway (Supplementary Figure S16C): 1) diamond-shaped metal mesh (mesh = 50 × 50 mm) is laid on the side; 2) the anchor cable is a Φ21.6 × 4800 mm steel strand with three supports in each row (spacing between anchor cables = 1000 mm, row spacing = 900 mm), and each row of the anchor cable is connected through a W-shaped steel guard plate (4 × 280 × 2200 mm); 3) one anchor rod (Φ22 × 2600 mm left-handed screw thread steel bolt without longitudinal reinforcement) is constructed at the lower part of each row of anchor cables, 800 mm away from the lowest anchor cable, and equipped with an arch prestressed tray (150 × 150 × 10 mm).
The applicability of reinforcement support was evaluated by monitoring the roadway displacement and coal pillar crack evolution.
A surrounding rock displacement monitoring station was installed in the roadway reinforcement area to evaluate the stability of the surrounding rock and to provide a reference for the subsequent roadway support design or further optimization. The statistical results obtained from monitoring surrounding rock displacement at two representative stations are presented in Supplementary Figure S17.
As shown in Supplementary Figure S17A, the mining stress significantly affects the surrounding rock deformation of the roadway section when the working face advances by 50–60 m. In particular, the deformation of surrounding rock (∼230 mm) is greater than that of the roof (∼100 mm), and the deformation of the working face is slightly larger than that of the coal pillar. The deformation of the working face side in the two stations was 1.61 times and 1.75 times that of the coal pillar side owing to the difference in the support strength of the two sides. To facilitate mining, an FRP(Fiber Reinforced Polymer) bolt can be used to support the working face. Under the influence of mining stress, the ability of an FRP bolt to control surrounding rock deformation is much weaker than that of a high-strength screw steel bolt, and therefore, the deformation of working face side is greater than that of coal pillar side. In general, the surrounding rock of the roadway is deformed to a certain extent under the mining stress of the working face; however, the deformation is very small, and the stability of the surrounding rock is high. Supplementary Figure S18 shows a real photograph of the roadway. The reinforcement and support measures have achieved ideal support effects, which can promote safe mining at the 112202 working face.
As shown in Supplementary Figure S19, after implementing the reinforcement measures, the internal damage to the coal pillar is detected up to 180 m in front of the working face. Within 0–60 m in front of the working face, internal fractures have developed in the coal pillar but not penetrated, thus sufficiently meeting the requirements of safe mining. Between 60 and −180 m in front of the working face, the coal pillar is only affected by the disturbance of the adjacent goaf, which is relatively high inside the coal pillar on the side of the working face. This shows that the roadway reinforcement and support measures are effective.
The results presented herein lead to the following conclusions:
1) Coal pillar instability induced by mining stress transfer was analyzed, and the main influencing factors are static parameters (e.g., E, μ, φ, c, γ, σ) and engineering design parameters (L, h, H, θ, M).
2) The key parameters of 125 coal pillar design cases in China were collected and used to establish a coal pillar database by applying a data mining method. The weights of factors influencing coal pillar stability were determined based on MIV calculations to fall in the order: H > h > L > E > c > σ > φ > μ > γ > θ. Meanwhile, a GA-BP prediction model was formulated. The prediction results indicated that the relative error rate was controlled within 5%, the R of predicted versus expected values was 0.95, and the MSE was 0.13; thus, the developed method provides a new approach for intelligent coal pillar risk assessments.
3) The applicability of the model was evaluated based on two field cases. The relative error of the YCM coal pillar was 3%, and there was no major safety hazard in the field. However, the designed value in the XCM coal pillar was too small, and there were some disasters, such as roadway deformation and spalling in the field. After formulating an “advance area roadway reinforcement support” strategy, the roadway stability was improved significantly, thereby confirming the applicability of the developed prediction model.
4) The model described herein depends on the reliability of the collected training dataset, and it can be applied for cases with similar geological conditions (i.e., rock type, geological conditions, etc.). This method can also be used in other aspects of mining and geotechnical engineering.
The original contributions presented in the study are included in the article/supplementary material, further inquiries can be directed to the corresponding author.
All authors listed have made a substantial, direct, and intellectual contribution to the work and approved it for publication.
Supported by the National Natural Science Foundation of China (No. 51904227), the 973 Key National Basic Research Program of China (No. 2015CB251602),the Natural Science Foundation of Shaanxi Province (No. 2018JQ5194).
The authors declare that the research was conducted in the absence of any commercial or financial relationships that could be construed as a potential conflict of interest.
All claims expressed in this article are solely those of the authors and do not necessarily represent those of their affiliated organizations, or those of the publisher, the editors and the reviewers. Any product that may be evaluated in this article, or claim that may be made by its manufacturer, is not guaranteed or endorsed by the publisher.
The Supplementary Material for this article can be found online at: https://www.frontiersin.org/articles/10.3389/feart.2022.894118/full#supplementary-material
Bieniawski, Z. T. (1968). The Effect of Specimen Size on Compressive Strength of Coal. Int. J. Rock Mech. Mining Sci. Geomechanics Abstr. 5, 325–335. doi:10.1016/0148-9062(68)90004-1
Braga-Neto, U., Hashimoto, R., Dougherty, E. R., Nguyen, D. V., and Carroll, R. J. (2004). Is Cross-Validation Better Than Resubstitution for Ranking Genes? Bioinformatics 20 (2), 253–258. doi:10.1093/bioinformatics/btg399
Cauvin, M., Verdel, T., and Salmon, R. (2009). Modeling Uncertainties in Mining Pillar Stability Analysis. Risk Analysis Official Publication Society Risk Analysis 29 (10), 1371–1380. doi:10.1111/j.1539-6924.2009.01237.x
Dai, J., Shan, P., and Zhou, Q. (2020). Study on Intelligent Identification Method of Coal Pillar Stability in Fully Mechanized Caving Face of Thick Coal Seam. Energies 13 (2), 305–315. doi:10.3390/en13020305
Deng, J., Li, X. B., and Gu, D. S. (2002). Reliability Analysis on Pillar Structure Using a New Monte-Carlo Finite Element Method[J]. Chin. J. Rock Mech. Eng. 21 (4).
Deng, J., Yue, Z. Q., Tham, L. G., and Zhu, H. H. (2003). Pillar Design by Combining Finite Element Methods, Neural Networks and Reliability: A Case Study of the Feng Huangshan Copper Mine, China. Int. J. Rock Mech. Mining Sci. 40 (4), 585–599. doi:10.1016/S1365-1609(03)00042-X
Ghasemi, E., Shahriar, K., Sharifzadeh, M., and Hashemolhosseini, H. (2010). Quantifying the Uncertainty of Pillar Safety Factor by Monte Carlo Simulation—A Case Study. Arch. Min Sci. 55, 623–635.
Goldberg, D. E. (1989). Genetic Algorithms in Search, Optimization and Machine Learning. New York, USA: Addison-Wesley Longman Publishing. doi:10.1111/j.1365-2486.2009.02080.x
Hou, C. J., and Ma, N. J. (1989). Stress in In-Seam Roadway Sides and Limit Equilibrium Zone[J]. China Coal Soc. 4, 21–29.
Hustrulid, W. A. (1976). A Review of Coal Pillar Strength Formulas. Rock Mech. 8 (2), 115–145. doi:10.1007/BF01239762
Idris, M. A., Saiang, D., and Nordlund, E. (2015). Stochastic Assessment of Pillar Stability at Laisvall Mine Using Artificial Neural Network. Tunnelling Underground Space Techn. 49, 307–319. doi:10.1016/j.tust.2015.05.003
Jawed, M., Sinha, R. K., and Sengupta, S. (2013). Chronological Development in Coal Pillar Design for Bord and Pillar Workings: A Critical Appraisal. J. Geol. Min. Res. 5 (1), 1–11. doi:10.5897/JGMR12.010
Koo, T. K., and Li, M. Y. (2016). A Guideline of Selecting and Reporting Intraclass Correlation Coefficients for Reliability Research. J. Chiropractic Med. 15 (2), 155–163. doi:10.1016/j.jcm.2016.02.012
Lai, X., Cai, M., Ren, F., Xie, M., and Esaki, T. (2006). Assessment of Rock Mass Characteristics and the Excavation Disturbed Zone in the Lingxin Coal Mine beneath the Xitian River, China. Int. J. Rock Mech. Mining Sci. 43 (4), 572–581. doi:10.1016/j.ijrmms.2005.10.005
Lai, X., Xu, H., Fan, J., Wang, Z., Yan, Z., Shan, P., et al. (2020). Study on the Mechanism and Control of Rock Burst of Coal Pillar under Complex Conditions. Geofluids 2020, 1–19. doi:10.1155/2020/8847003
Luo, H., Yang, S. J., Tao, G. Q., and Zeng, C. (2007). Stability Analysis of Ore Pillar and Application Using Concept of Dynamic Fuzzy Reliability Based on Finite Element Method-Artificial Neural Network-Monte Carlo Simulation[J]. J. China coal Soc. (09), 902–906.
Mohamad, E. T., Faradonbeh, R. S., Armaghani, D. J., Monjezi, M., and Majid, M. Z. A. (2016). An Optimized ANN Model Based on Genetic Algorithm for Predicting Ripping Production. Neural Comput. Applic 28, 393–406. doi:10.1007/s00521-016-2359-8
Monjezi, M., Hesami, S. M., and Khandelwal, M. (2011). Superiority of Neural Networks for Pillar Stress Prediction in Bord and Pillar Method. Arab J. Geosci. 4 (5-6), 845–853. doi:10.1007/s12517-009-0101-x
Mortazavi, A., Hassani, F. P., and Shabani, M. (2009). A Numerical Investigation of Rock Pillar Failure Mechanism in Underground Openings. Comput. Geotechnics 36 (5), 691–697. doi:10.1016/j.compgeo.2008.11.004
Qi, C., Fourie, A., Ma, G., Tang, X., and Du, X. (2018a). Comparative Study of Hybrid Artificial Intelligence Approaches for Predicting Hangingwall Stability. J. Comput. Civ. Eng. 32 (2), 04017086. doi:10.1061/(asce)cp.1943-5487.0000737
Rezaei, M., Hossaini, M. F., and Majdi, A. (2015). Development of a Time-dependent Energy Model to Calculate the Mining-Induced Stress over gates and Pillars. J. Rock Mech. Geotechnical Eng. 7 (3), 306–317. doi:10.1016/j.jrmge.2015.01.001
Rodriguez, J. D., Perez, A., and Lozano, J. A. (2010). Sensitivity Analysis of K-fold Cross Validation in Prediction Error Estimation. IEEE Trans. Pattern Anal. Mach. Intell. 32 (3), 569–575. doi:10.1109/TPAMI.2009.187
Salamon, M. D. G., and Munro, A. H. (1967). A Study of the Strength of Coal Pillars. J. S Afr. Inst. Min Metall. 68, 55–67.
Wang, X. C. (2013). MATLAB Neural Network 43 Case Analysis. Beijing, China: University of Aeronautics and Astronautics Press.
Wang, X., Shi, F., Yu, L., and Li, Y. (2013). MATLAB Neural Network 43 Case Analysis. Beijing, China: University 521 of Aeronautics and Astronautics Press.
Wattimena, R. K., Kramadibrata, S., Sidi, I. D., and Azizi, M. A. (2013). Developing Coal Pillar Stability Chart Using Logistic Regression. Int. J. Rock Mech. Mining Sci. 58, 55–60. doi:10.1016/j.ijrmms.2012.09.004
Wattimena, R. K. (2014). Predicting the Stability of Hard Rock Pillars Using Multinomial Logistic Regression. Int. J. Rock Mech. Mining Sci. 71, 33–40. doi:10.1016/j.ijrmms.2014.03.015
Zhao, K., Cai, M. F., Rao, Y. Z., Rao, J., and Zhu, J. X. (2003). Study on Fuzzy Random Reliability Analysis for Block Stability in Caved Area[J]. Rock Soil Mech. 24 (6), 987–990 doi:10.3969/j.issn.1000-7598.2003.06.025
Zhou, J., Li, X.-b., Shi, X.-z., Wei, W., and Wu, B.-b. (2011). Predicting Pillar Stability for Underground Mine Using Fisher Discriminant Analysis and SVM Methods. Trans. Nonferrous Met. Soc. China 21 (12), 2734–2743. doi:10.1016/s1003-6326(11)61117-5
Zhou, J., Li, X., and Mitri, H. S. (2015). Comparative Performance of Six Supervised Learning Methods for the Development of Models of Hard Rock Pillar Stability Prediction. Nat. Hazards 79 (1), 291–316. doi:10.1007/s11069-015-1842-3
Keywords: underground mining, coal pillar stability, data mining, artificial intelligence, pre-control technique
Citation: Shan P, Sun H, Lai X, Dai J, Gao J, Yang P, Li W, Li C and Yan C (2022) Numerical Method for Predicting and Evaluating the Stability of Section Coal Pillars in Underground Longwall Mining. Front. Earth Sci. 10:894118. doi: 10.3389/feart.2022.894118
Received: 11 March 2022; Accepted: 25 March 2022;
Published: 25 April 2022.
Edited by:
Xiaodong Fu, Institute of Rock and Soil Mechanics (CAS), ChinaReviewed by:
Xing Huang, Institute of Rock and Soil Mechanics (CAS), ChinaCopyright © 2022 Shan, Sun, Lai, Dai, Gao, Yang, Li, Li and Yan. This is an open-access article distributed under the terms of the Creative Commons Attribution License (CC BY). The use, distribution or reproduction in other forums is permitted, provided the original author(s) and the copyright owner(s) are credited and that the original publication in this journal is cited, in accordance with accepted academic practice. No use, distribution or reproduction is permitted which does not comply with these terms.
*Correspondence: Haoqiang Sun, MTg3MTA4MTM1MzhAcXEuY29t
Disclaimer: All claims expressed in this article are solely those of the authors and do not necessarily represent those of their affiliated organizations, or those of the publisher, the editors and the reviewers. Any product that may be evaluated in this article or claim that may be made by its manufacturer is not guaranteed or endorsed by the publisher.
Research integrity at Frontiers
Learn more about the work of our research integrity team to safeguard the quality of each article we publish.