- 1State Key Laboratory of the Gas Disaster Detecting Preventing and Emergency Controlling, China Coal Technology and Engineering Group Chongqing Research Institute, Chongqing, China
- 2Gas Research Branch, China Coal Technology and Engineering Group Chongqing Research Institute, Chongqing, China
- 3State Key Laboratory of Mining Response and Disaster Prevention and Control in Deep Coal Mines, Anhui University of Science and Technology, Huainan, China
- 4School of Safety Science and Engineering, Anhui University of Science and Technology, Huainan, China
Coal and gas outburst is an extremely complex dynamic phenomenon of mine gas, which is mainly manifested in a very short time. A large amount of coal and rock are thrown out from the coal body to the mining space and accompanied by a large volume of high-pressure gas. In the process of coal and gas outburst, the internal energy consumption of gas is composed of two parts: one is used to throw out broken coal and rock mass, and the other is used to pulverize broken coal. In this article, from the perspective of energy dissipation, the experiment of broken coal ejection with different coal particle sizes, different adsorption gas, and pressure is studied. The characteristics of coal ejection are studied and analyzed, and the proportion of adsorbed gas participating in the outburst work is quantitatively analyzed. The results show that after outburst excitation, residual gas will continue to desorb and work on outburst until the power is insufficient to throw coal body; compared with air, CO2 gas has a stronger ability to work on the outburst, and the outburst coal is thrown far away, and the pulverization effect is stronger. Through the energy analysis in the process of outburst, the results show that when the particle size of the coal sample is consistent, the greater the outburst pressure is, the larger the desorption amount of the adsorbed gas is, and the larger the volume involved in the outburst work is. When the test gas is consistent with the outburst pressure, the gas desorption amount of the small-size coal sample is more, the desorption gas has a stronger ability to work on the outburst, and the proportion of participating in outburst work is higher. The crushing degree of coal plays an important role in the expansion and release of gas internal energy.
1 Introduction
Coal and gas outburst is an extremely complex dynamic phenomenon in the process of underground mining in coal mines. It is mainly manifested in a short period of time. A large amount of coal and rock are thrown out to the mining space, and a large volume of high-pressure gas is sprayed out. The formation of coal and rock-gas flow with high-speed movement can directly strike and bury the workers, casualties, or equipment, and facilities near the underground, which poses a great threat to the safe production of coal mines. Frequent coal and gas outburst accidents have caused a large number of casualties.
Domestic and foreign scholars define the causes, conditions, and the whole process of coal and gas outburst as the coal and gas outburst mechanism (Dong, 2015). It has been reported that some experts have made abundant research results in highlighting the mechanisms. Beamish et al. (Basil and Beamish, 1998; Jin et al., 2018) believed that gas played an important role in the occurrence of coal and gas outbursts. Paterson (1986) analyzed the gas flow and stress distribution of two-dimensional coal seam, and considered that coal and gas outburst was structural instability under high gas pressure gradient; Noack and Li et al. (Klaus, 1998; Li et al., 2018) considered that ground stress played a leading role in the occurrence of outburst. Sato and Fujii (1989) studied the location of coal and gas outbursts in detail, and considered that the geological structure had obvious influence on the outburst. Cao et al. (2001) studied the influence of reverse faults in geological structures on the outburst. The results show that the coal seam in the lower wall of the reverse fault experienced more tectonic deformation than that in the upper wall. The area with high gas content almost always appears in the lower wall, and outburst is more likely to occur in these areas. Dmytro Rudakov (Dmytro and Valeriy, 2019) believed that the release of large amounts of gas in coal seam was caused by the decomposition of coal organic matter with unstable thermodynamics, and based on this, a one-dimensional mathematical model of gas flow in the outburst excitation stage was established. With the continuous improvement and enrichment of the outburst mechanism, people have gradually formed a unified understanding that coal and gas outburst is caused by the combined effect of ground stress, coal seam gas pressure, and coal’s physical and mechanical properties (Norbert, 1997; Alexeev et al., 2004; Jacek, 2014; Du et al., 2020a; Yin et al., 2020). At the same time, the gas internal energy has gradually become a hot topic for many scholars. Wang et al. (2017a) carried out outburst simulation experiments with different strength briquettes and created the gas containing conditions of “the same free gas content and different adsorbed gas content” by using different adsorption characteristics of gas. The influence of adsorbed gas content on outbursts was discussed. Valliappan S (Valliappan and Wohua, 1999) believed that the gas energy released from the gas desorbed from the coal matrix to the pores was the main reason for the outburst energy; Baohai Y (Yu et al., 2015) studied the gas expansion energy in the outburst process, and the results show that the gas expansion energy is the key source of outburst energy; Peng S J et al. (Peng et al., 2012; Zhi-qiang et al., 2012; Du et al., 2020b; Wu et al., 2021a) also verified the above point of view through many experiments and proved that gas expansion energy is the main energy of throwing and crushing coal; with the continuous research and breakthrough of scholars, gas expansion energy has also begun to be used to evaluate the risk of outburst. Yang D (Yang et al., 2018) and Xu L (Xu and Jiang, 2017) studied the initial desorption characteristics of gas through experiments, indicating that the initial expansion energy of released gas can reflect the risk of outbursts. At the same time, Zhao et al. (Wang et al., 2012; Yin et al., 2014; Zhou and Wang, 2016; Zhao et al., 2017; Du et al., 2020c; Wu et al., 2021b) research results show that gas expansion can also be used to evaluate the damage of coal and rock mass during the development of coal and gas outburst.
In summary, the rich research results of many scholars in the field effectively promote the development of coal and gas outburst mechanisms, and provide theoretical guidance for the application of engineering research. However, there are few studies on the role of adsorbed gas in the process of outburst, especially the quantitative analysis of adsorbed gas work in the process of outburst. In this article, based on the existing results, combined with the mechanical impact crushing test of broken coal and the sudden unloading throw test of broken coal containing gas, the above problems are analyzed and studied. The purpose is to provide the basis for quantitative analysis of the energy of adsorbed gas participating in outbursts and lay the foundation for an in-depth understanding of the energy dissipation law of outbursts.
2 Energy Conversion in Coal and Gas Outburst
Coal and gas outburst is a process of energy accumulation and release. Mining disturbance breaks the original stress balance state and makes the load on the coal body in the mining area begin to transfer to the adjacent coal body. The adjacent coal body is subjected to strength failure, strain softening, and flow deformation due to the increase of pressure. In this process, a large amount of deformation energy is gathered, and a stress concentration area is formed. At the same time, due to the stress concentration, the compression of coal pore cracks is caused so that the gas pressure in the coal seam is also increased, and the potential of gas expansion work is also increased. Finally, a limit stress balance and high gas gradient area are formed in the coal wall in front of the work. The mechanical failure conditions are created for prominent subsequent excitation. The deformation and failure of the coal body developed to a critical condition, or under the action of external disturbance load, the coal body was destroyed and unstable. The stored elastic energy in the coal and rock mass quickly released and acted on the coal and rock mass so that the original fracture of the unloading coal body expanded and produced new fractures. At the same time, with the penetration of the fractures, the coal body gradually destroyed, and finally formed broken coal or pulverized coal. The expansion of primary fractures, the generation of new fractures, and the fragmentation of coal have created favorable conditions for the release of gas, which promotes rapid desorption of adsorbed gas to free gas and participates in the outburst and the formation of coal–gas–solid two-phase flow with broken coal. After the outburst excitation, the broken coal will be thrown out by the rapid expansion of gas, and the broken coal will be further pulverized in the process of throwing until gas expansion cannot be enough to throw the broken coal and terminate the outburst.
In the process of outburst energy release and dissipation, the proportion of friction heat, sound, vibration, and other energy consumed by outburst coal impacting roadway walls, support, and other obstacles is small. For the convenience of research, it can be ignored (Wen, 2003; Wang et al., 2015), and the energy dissipation in the process of outburst can be expressed as (Hu and Wen, 2013)
where W1 is the elastic potential energy of coal and rock mass in the outburst range; W2 is the gas internal energy of coal and rock mass in the outburst range; A1is the fracture energy of coal and rock mass; and A2 is the throwing power of coal and rock mass.
Combined with the dynamic phenomenon of coal and gas outburst and the above analysis, the energy in the process of the outburst comes from the release of elastic energy of coal body and internal energy of the gas, mainly acting on the crushing and throwing of coal body, and part of the energy is dissipated in the friction heat, sound, and vibration caused by the outburst coal body impacting the roadway wall, support, and other obstacles. Previous research results show that the elastic energy caused by ground stress in the process of outburst is first consumed, and after the ground stress destroys the coal body, the elastic energy of the coal body has been consumed (Jiang and Yu, 1996). The physical simulation experiment carried out in the laboratory also found that after the outburst excitation, the coal body in the outburst area was quickly released and destroyed, and the stress of the coal body near the outburst area decreased rapidly, almost simultaneously to zero (Jin, 2017). Therefore, it can be considered that after outburst excitation, the development of outburst is a process in which high-pressure gas flow quickly throws out a broken coal body. The energy of the thrown out broken coal body and pulverized broken coal body comes from gas expansion energy, and the gas expansion energy comes from the rapid analysis of free gas and adsorbed gas. At this stage, Eq 1 can be rewritten as
where Wf is the energy of free gas expansion participating in the work, J; Wα is the adsorption gas expansion involved in work energy, J; A1 is the energy consumed by gas-pulverized coal crushing, J; A2 is the gas that throws out the energy consumed by broken coal, J.
In the process of the outburst, the throwing power of gas to the coal sample is the kinetic energy when the coal sample is sprayed out of the hole, but the speed of throwing coal is different for different outbursts and different times of the same outburst. It is difficult to monitor in the field and test. Therefore, according to the equivalent distance and potential energy of the coal sample, the equivalent distance can be expressed as
where Sp is the equivalent distance, m; B is the outburst strength, kg; and dM is the mass of the thrown coal sample within the range x to dx of the outburst exit, kg; the coal and gas outburst is regarded as near-horizontal ejection (Hu and Wen, 2013), and the relationship between the equivalent distance Sp and the ejection velocity of the coal sample can be obtained by using the flat ejection formula:
where h is the coal seam thickness, m, and g is the acceleration of gravity, m/s2.
Then the work of gas throwing out the outburst coal sample is
According to Wang et al. (Jin), the crushing work can be expressed as
where f is the consistent coefficient of coal; ρ is the density of coal, kg/m3; D is the average particle size of coal before crushing, m; and d is the average particle size of coal after crushing, m.
Coal has strong adsorption of gas, so there are a large amount of adsorbed gas in the coal seam. There is a significant difference between the process of gas expansion and the conventional gas expansion when coal and gas outburst occurs. At the same time, the adsorbed gas in the coal body will continue to desorb and participate in the outburst work. Therefore, the amount of gas in the outburst work is between the amount of free gas and the total amount of gas. In the process of outburst, on the one hand, the free gas expansion at the moment of pressure relief works on the outburst, and on the other hand, the adsorbed gas is desorbed continuously, and the power source is continuously supplemented and involved in the outburst work, which makes it difficult to accurately analyze the adsorbed gas internal energy in the process of outburst. Therefore, it is necessary to calculate the gas internal energy from another point of view. If the loss of other energy in the outburst process is ignored, the whole outburst process is regarded as an adiabatic process. Assuming that the gas expansion energy in the outburst process fully affects the ejection and crushing of the outburst coal body, the amount of adsorbed gas participating in the work can be expressed as follows:
Formula for calculating expansion energy of free gas:
where V1 is the free gas volume involved in the outburst work, m3/t; P1 is the gas pressure of working face after coal thrown out, MPa; P0 is the coal seam gas pressure before the outburst, MPa; and n is the process index; for isothermal process, n = 1, adiabatic process, n = 1.31, and for variable process, n = 1–1.31.
3 Test Scheme
The test equipment adopts the self-developed visual simulation experiment system of the dynamic effect of coal and gas outburst to carry out the simulation experiment of gas-containing coal ejection. The test system is mainly composed of a high-pressure sealing chamber, inflatable system, outburst control device, pipeline system, and data acquisition system. The length of the high-pressure sealing cavity is 30 cm, and the inner diameter is 10 cm. The gas-filled/vacuum-pumping dual-purpose interface is opened at its tail, and the three-way conical valve is used for sealing, so as to realize the conversion of the gas-filled and vacuum-pumping interface during the test. There are three uniformly distributed sensor interfaces at the top of the cavity, which can be used to monitor the temperature, pressure, and gas concentration in the cavity, as shown in Figure 1. During the test, the protruding cavity was connected with the protruding control device by flange and fixed on the ground through the support. The outburst control device is controlled by a pneumatic electromagnetic ball valve. The designed pressure strength is 1.5 MPa. During the test, the gas pressure in the valve reaches 0.6 MPa, and pressure is maintained. When the pressure relief is needed, the instantaneous exposure of the outburst port is realized through the power switch. The material of the pipeline system is the transparent acrylic pipe, the length of each pipe is 1 m, and the inner diameter is 10 cm. During the test, the flange connection is used between the pipes and the control device of the outburst port, and the bracket is fixed on the ground. There are four uniformly distributed sensor interfaces above the pipeline with corresponding plugs. The pneumatic system is mainly composed of high-pressure cylinders and vacuum pumps. After the completion of coal sample filling and sensor layout, the high-pressure sealing cavity is vacuumed and inflated. By filling gas into the high-pressure sealing tube step by step, the gas pressure in the high-pressure sealing cavity is monitored by means of a data acquisition system and pressure sensors on the high-pressure sealing cavity so that it can reach the adsorption equilibrium and meet the pressure requirements of the experimental design. The data acquisition system mainly includes a computer, a data acquisition card, supporting sensors, a high-speed camera, and a transmitter. During the test, the parameters such as gas pressure, gas concentration, and temperature in the simulated roadway and sealing chamber can be automatically monitored and collected by the system, the overall structure of the test system is shown in Figure 2.
The coal sample used in this experiment is the M8 coal seam in the Fengchun Coal Mine of Chongqing. The average thickness of the M8 coal seam is 1.61 m, the original gas content is 25.87 m3/t, and the measured maximum gas pressure is 3.8 MPa, which is the coal and gas outburst coal seam. In order to systematically study the working ability of adsorbed gas in the process of coal and gas outburst, two different gases and three different particle sizes of coal samples were designed in this experiment. The sudden unloading simulation test of broken coal containing gas under three different pressure (absolute pressure) conditions was carried out. The parameters of the test scheme are shown in Table 1.
4 Test Results and Analysis
4.1 Test Results
In order to fully reflect the results of simulation tests, the outburst strength, that is, the total mass of outburst coal, the mass distribution of outburst coal, and the average particle size of outburst coal, are counted. These three physical quantities are also important indexes for calculating the energy dissipation of outbursts. The quality of outburst coal powder was counted according to 1m, and the particle size was screened according to 3, 1, 0.5, 0.25, and 0.1 mm.
4.1.1 Outburst Strength and Distance
The ratio of outburst coal quality to total coal filling is defined as the outburst relative strength (Jin, 2017). It can be seen from Table 2 and Figure 3 that with the increase of outburst gas pressure, the relative strength of outburst also increases, almost linearly increasing, and the maximum throw distance also increases with the increase of pressure. When the air pressure and the initial particle size of the coal sample are the same, the ability of CO2 to work for outburst coal is stronger than that of air, and more pulverized coal is thrown out, and the throw distance is farther. From the above experimental results, we can know that the greater the outburst pressure, the more the energy released by gas expansion, the stronger the ability to work on coal, and the more the amount of coal thrown out; the larger the initial kinetic energy of the thrown coal is, the farther the distance of the thrown coal migration is. When the pressure is the same as the particle size of the coal sample, the ability of CO2 gas to work for outburst coal is better than that of air, indicating that the gas with strong adsorption has stronger ability to work. When an outburst occurs, the outburst strength is greater.
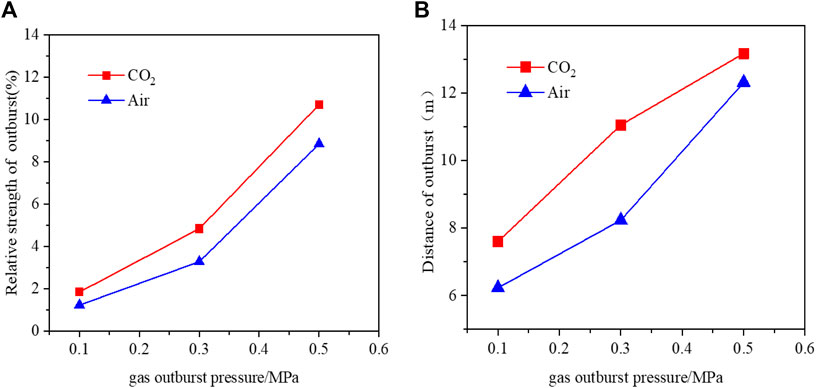
FIGURE 3. Relationship between outburst pressure and outburst relative strength, and outburst distance.
4.1.2 Quality Distribution Characteristics of Outburst Coal
It can be seen from Figure 4 that the gas type, outburst gas pressure, and coal sample particle size all affect the quality distribution of outburst coal. Although the quality distribution of outburst coal has a certain degree of fluctuation, the overall quality distribution law is basically consistent with the quality distribution law of typical coal and gas outburst. There are more outburst coal samples near the outburst mouth. With the increase in distance, the quality of outburst coal generally shows a decreasing trend. It can also be seen from Figures 4A and B that when the outburst pressure is large, the initial kinetic energy obtained by the outburst coal body is larger, and the thrown distance is farther. When the gas pressure is small, the outburst coal is mainly distributed near the outburst mouth due to the small initial kinetic energy.
It can be seen from Figure 4C that under the same pressure condition, the coal sample with a larger particle size was thrown farther, while the coal sample with a smaller particle size was thrown closer to the outburst port, but the quality of outburst coal was relatively large. The main reason for this phenomenon is that although the large-size coal sample obtains a large initial kinetic energy at the outburst moment, its adsorption is relatively weak, the gas adsorption is small, and the residual gas in the cavity after the outburst is relatively small, resulting in the fact that the residual gas is not enough to be thrown out of the coal body.
4.1.3 Particle Size Distribution Characteristics of Outburst Coal
From the statistical results of Table 3, we can know that there are coal samples with particle size less than the initial particle sizes in each group of experimental outburst coal. It shows that in the process of coal and gas outburst driven by gas, gas not only has a throwing effect on outburst coal but also has a certain powdering effect on outburst coal in the process of outburst. In the thrown coal, the diameter of pulverized coal after crushing is counted as the particle size below the initial particle size. The initial particle size of the data in Figure 5 is 3–10 mm, and the diameter of outstanding pulverized coal is counted as 1–3 mm and below. In addition, it can be seen from Figure 5 that with the decrease of gas pressure, the pulverization effect of gas on outburst coal decreases. Due to the strong adsorption of CO2, the amount of desorption expansion and work gas is larger than that of air when outbursts occurs. Therefore, when the pressure and initial particle size are the same, the pulverization effect of CO2 on outburst coal is stronger than that of air.
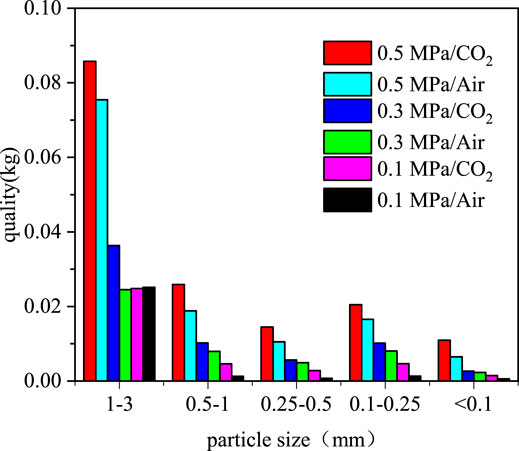
FIGURE 5. Particle size distribution of outburst coal with particle size less than 3 mm (initial particle sizes are 3–10 mm).
4.2 Energy Analysis During Outburst Occurrence
Combining Formulas (5) ∼ (6), the throwing power and crushing power of coal samples under different test conditions are calculated. The expansion energy of free gas and adsorbed gas are calculated from Formula (7) to (8). The calculation results are shown in Table 4.
It can be seen from Table 4 and Figure 6A that with the increase of outburst pressure, the crushing effect and ejection effect of test gas on outburst coal are enhanced, and the amount of adsorbed gas participating in work is also increasing. When the outburst pressure is small (0.1 MPa), the ejection effect and crushing effect of CO2 and air on coal are relatively small, and the sum of ejection work and crushing work is less than that of free gas internal energy, so it is considered that the adsorbed gas does not participate in outburst work under this condition. When the particle size is consistent with the outburst pressure, the crushing and ejection work of CO2 gas for outburst coal is greater than that of air, and the amount of adsorbed gas participating in the work is larger. In addition, compared with the experimental results under the condition of 0.3 MPa/CO2, it is found that the fragmentation degree of coal samples also affects the release of gas internal energy. When the fragmentation degree of coal samples is small, that is, the particle size is small, the gas expansion energy is larger, and the crushing work and ejection work of coal samples are also increased accordingly, as shown in Figure 6B. The reason for this phenomenon, on the one hand, is that because the coal sample with a smaller particle size has a larger specific surface area, stronger adsorption capacity for CO2 gas, and larger gas internal energy is stored in the coal body; on the other hand, when the pressure is suddenly unloaded, the smaller particle size coal samples with a more obvious crushing degree are conducive to the rapid desorption of adsorbed gas and participate in the prominent work. Therefore, the degree of coal fragmentation plays an important role in the release of gas internal energy in coal. The higher the degree of coal fragmentation is, the more conducive it is to the rapid release of gas internal energy and works on the outburst.
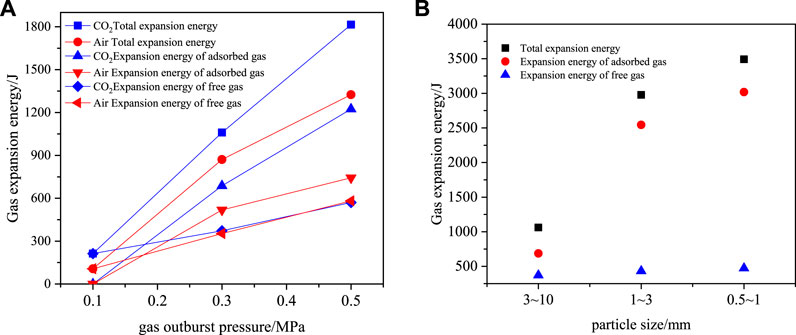
FIGURE 6. Effect of pressure and particle size on gas expansion energy. (A) Effect of outburst pressure on gas expansion energy. (B) Effect of particle size on gas expansion energy.
4.3 Work Proportion Analysis of Adsorption Gas
The gas in the coal seam mainly exists in the adsorbed state, and its content can generally reach 80–90%. At present, the research on the influence of adsorbed gas on outbursts is not deep enough. In the process of outbursts, on the one hand, the instantaneous expansion and release of free gas can work on outbursts. On the other hand, the process of rapid desorption of adsorbed gas to continuously supplement free gas and participate in the work of outburst is relatively complex, resulting in the current consensus on how much adsorbed gas is desorbed and how much is involved in the work of outburst (Wang et al., 2017b), and the existing research results believe that the slow escape of gas on the outburst work efficiency is low, or even not work, only when the coal is seriously damaged will quickly desorb participate in the outburst work (Wen, 2003). Therefore, the desorption of adsorbed gas in the process of coal and gas outburst will experience the whole process of rapid desorption, slow desorption, and stop desorption. Although some of the residual adsorbed gas is slowly desorbed into free gas, this part of adsorbed gas is not fully involved in work. It is necessary to know the adsorption capacity of coal samples with different particle sizes under different gas pressures and the volume of adsorbed gas participating in the work. The gas adsorption capacity per unit mass of coal can be expressed as
where Q is the coal of unit mass adsorbing gas volume, m3, at gas pressure p, m3; a is the maximum surface adsorption of coal per unit mass, m3/kg; b is the adsorption coefficient; A is the ash in coal, %; and M is the moisture in coal, %.
Using the formula of gas expansion energy (8), the volume of the adsorbed gas work is inversely solved, and the volume ratio of adsorbed gas participating in the outburst is calculated by combining Formula (9). The calculation results are shown in Table 5.
It can be seen from Table 5 that the proportion of gases involved in the outburst work in the desorption amount of adsorbed gas is between 6.63 and 33.80%, and the volume of adsorbed gas involved in the outburst work accounts for 5.33–19.54% of the total adsorption amount.As Figure 7A shows, when the particle size of the test gas is consistent with the coal sample, the greater the outburst pressure, the desorption amount of the adsorbed gas is relatively large, and the volume of the work involved in the outburst is also larger. The proportion of the work volume to the total adsorption amount has a certain fluctuation. When the pressure is 0.1 MPa, there is no adsorbed gas to participate in the outburst work, and the proportion of 0.3 MPa is relatively higher than 0.5 MPa. It shows that when the gas pressure is low, due to the pressure drop in the cavity being too fast, the power of adsorption gas desorption is not enough to work on the outburst. When the outburst pressure is relatively large, the pressure in the outburst chamber drops instantly, but the speed of absorbing gas to supplement the power is relatively fast. Therefore, this part of the gas will participate in the outburst work. However, with the continuous decline of the pressure, the subsequent supplement power is no longer sufficient to work on the outburst, resulting in the loss of this part of the gas. When the pressure drop of 0.5 MPa is larger than that of 0.3 MPa, the desorption amount of gas is more, and the continuous desorption time is longer. When the pressure drops to a certain critical value from 0.1 to 0.3 MPa, the subsequent desorbed gas no longer participates in the outburst work, resulting in more adsorbed gas not participating in the outburst work, so the proportion of adsorbed gas participating in the outburst work is less than 0.3 MPa. When the test gas is consistent with the outburst pressure (Figure 7B), the adsorbed gas desorbed from the coal sample with a smaller particle size is larger than that of the coal sample with a larger particle size, and the adsorbed gas volume participating in the work is also higher, indicating that the smaller the particle size, the more conducive to the rapid desorption of adsorbed gas in coal and participating in the work of outburst.
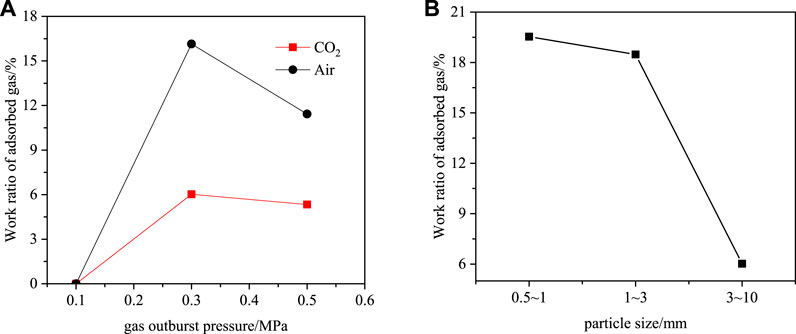
FIGURE 7. Relationship between work ratio of adsorbed gas and outburst pressure, and coal particle size.
When the particle size of the coal sample corresponds to the outburst pressure, although the work ability of air on outburst coal is less than that of carbon dioxide gas, and the adsorption and desorption amount is also less than that of carbon dioxide gas, the proportion of work involved in desorption volume is relatively high. Combined with the change of air pressure in the outburst chamber (Figure 8), this phenomenon can be explained under the experimental conditions as follows: when the outburst is excited, the free gas in the chamber is released instantly and works on the outburst, resulting in the decrease of air pressure in the outburst chamber, but the adsorbed gas will continue to be desorbed as a supplemental power source for the outburst until it is not enough to throw out the broken coal, so the gas pressure will not decrease linearly, and Figure 8 shows that the rate of pressure drop of carbon dioxide gas is significantly lower than that of air. Although the adsorption capacity of carbon dioxide gas is large, it will continue to desorb relatively more gas, but when the pressure drops to a certain extent, the power of residual gas is no longer enough to work on the outstanding gas, which leads to the subsequent slow desorption of the gas to do “no work.” Therefore, although the adsorption capacity, desorption capacity, and workability of carbon dioxide gas are greater than those of air, the proportion of gas volume participating in work is lower than that of air.
5 Conclusion
(1) The mass distribution characteristics and particle size distribution characteristics of pulverized coal after outburst show that the ability of CO2 gas for the outburst work is greater than that of air. When the test gas is CO2, the throw distance of outburst coal is farther, and the pulverized effect of outburst coal is stronger than that of air.
(2) The test results of coal samples with different particle sizes show that the degree of coal fragmentation affects the release of gas internal energy to a large extent. The higher the degree of coal fragmentation, the more conducive it is to the rapid release of gas internal energy and participation in the outburst work. The larger the pressure is, the larger the desorption amount of adsorbed gas is, and the larger the volume of work is.
(3) The larger the pressure of outburst gas is, the larger the desorption amount of adsorbed gas is, and the larger the volume of the outburst work is. The desorption amount of adsorbed gas in coal samples with small particle sizes is greater than that in coal samples with large particle sizes, and the ability to work in outburst coal is stronger. The volume proportion of adsorbed gas participating in work is also higher; that is, the degree of coal crushing plays an important role in the expansion and release of gas.
Data Availability Statement
The raw data supporting the conclusion of this article will be made available by the authors, without undue reservation.
Author Contributions
I would like to thank XN for his guidance and help in the process of experimentation and thesis writing.
Funding
This work was financially supported by the Technological Innovation and Entrepreneurship Fund Special Project of Tiandi Technology Co., Ltd. (2021-2-TD-ZD008) and the State Key Laboratory Open Fund Project (SKLMRDPC20KF01).
Conflict of Interest
The authors declare that the research was conducted in the absence of any commercial or financial relationships that could be construed as a potential conflict of interest.
Publisher’s Note
All claims expressed in this article are solely those of the authors and do not necessarily represent those of their affiliated organizations, or those of the publisher, the editors, and the reviewers. Any product that may be evaluated in this article, or claim that may be made by its manufacturer, is not guaranteed or endorsed by the publisher.
References
Alexeev, A. D., Revva, V. N., Alyshev, N. A., and Zhitlyonok, D. M. (2004). True Triaxial Loading Apparatus and its Application to Coal Outburst Prediction. Int. J. Coal Geology. 58, 245–250. doi:10.1016/j.coal.2003.09.007
Basil, B., and Beamish, P. (1998). Instantaneous Outbursts in Underground Coal Mines: An Overview and Association with Coal Type. Int. J. coal Geology. 35 (1-4), 27
Cao, Y., He, D., and David, C. (2001). Coal and Gas Outbursts in Footwalls of Reverse Faults. Int. J. coal Geology. 48 (1-2), 47–63. doi:10.1016/s0166-5162(01)00037-4
Dmytro, R., and Valeriy, S. (2019). A Mathematical Model of Gas Flow during Coal Outburst Initiation. Int. J. Mining Sci. Technol. 29 (5), 791–796. doi:10.1016/j.ijmst.2019.02.002
Dong, K. (2015) Failure and Outburst Mechanism of Coal and Gas Microelement [ Dissertation ]. Xi'An, China: Xi'an University of Science and Technology.
Du, K., Li, X. F., Yang, C. Z., Zhou, J., Chen, S. J., and Manoj, K. (2020). Experimental Investigations on Mechanical Performance of Rocks under Fatigue Loads and Biaxial Confinements [J]. J. Cent. south Univ. (27), 2985–2998. doi:10.1007/s11771-020-4523-7
Du, K., Li, X., Tao, M., and Wang, S. (2020). Experimental Study on Acoustic Emission (AE) Characteristics and Crack Classification during Rock Fracture in Several Basic Lab Tests. Int. J. Rock Mech. Mining Sci. 133, 104411. doi:10.1016/j.ijrmms.2020.104411
Du, K., Yang, C., Su, R., Tao, M., and Wang, S. (2020). Failure Properties of Cubic Granite, marble, and sandstone Specimens under True Triaxial Stress. Int. J. Rock Mech. Mining Sci. 130, 104309. doi:10.1016/j.ijrmms.2020.104309
Hu, Q., and Wen, G. (2013). Mechanical Mechanism of Coal and Gas Outburst. Beijing, China: Beijing Science Press.
Jacek, S. (2014). A Comparison of the Influence of Adsorbed Gases on Gas Stresses Leading to Coal and Gas Outburst. Fuel 114 (1), 288
Jiang, C., and Yu, Q. (1996). Research on the Law of Energy Dissipation in the Process of Coal and Gas Outburst. Coal J. (02), 173
Jin, K. (2017 ). Research on the Formation Mechanism and Disaster-Causing Characteristics of High-Pressure Pulverized Coal-Gas Two-phase Flow in the Process of Coal and Gas Outburst [ Dissertation ]. Xuzhou, China: China University of Mining and Technology.
Jin, K., Cheng, Y., Ren, T., Zhao, W., Tu, Q., Dong, J., et al. (2018). Experimental Investigation on the Formation and Transport Mechanism of Outburst Coal-Gas Flow: Implications for the Role of Gas Desorption in the Development Stage of Outburst. Int. J. Coal Geology. 194, 45–58. doi:10.1016/j.coal.2018.05.012
Klaus, N. (1998). Control of Gas Emissions in Underground Coal Mines. Int. J. Coal Geology. 35 (1), 57–82.
Li, W., Campos-Vargas, C., Marzahn, P., and Sanchez-Azofeifa, A. (2018). On the Estimation of Tree Mortality and Liana Infestation Using a Deep Self-Encoding Network. Int. J. Appl. Earth Observation Geoinformation 73, 1–13. doi:10.1016/j.jag.2018.05.025
Norbert, S. (1997). “Laboratory Study of the Phenomenon of Methane and Coal Outburst,” in International Journal of Rock Mechanics and Mining Sciences (Oxford, England, 55.
Paterson, L. (1986). A Model for Outbursts in Coal. Int. J. Rock Mech. Mining Sci. Geomechanics Abstr. 23 (4), 327–332. doi:10.1016/0148-9062(86)90644-3
Peng, S. J., Xu, J., Yang, H. W., and Liu, D. (2012). Experimental Study on the Influence Mechanism of Gas Seepage on Coal and Gas Outburst Disaster. Saf. Sci. 50 (4), 816–821. doi:10.1016/j.ssci.2011.08.027
Sato, K., and Fujii, Y. (1989). Source Mechanism of a Large Scale Gas Outburst at Sunagawa Coal Mine in Japan. 129(3-4). 325–343. doi:10.1007/978-3-0348-9270-4_5
Valliappan, S., and Wohua, Z. (1999). Role of Gas Energy during Coal Outbursts. Int. J. Numer. Meth. Engng. 44 (7), 875–895. doi:10.1002/(sici)1097-0207(19990310)44:7<875::aid-nme527>3.0.co;2-g
Wang, G., Wu, M., Wang, H, Huang, Q., and Yang, Z. (2015). Sensitivity Analysis of Influencing Factors of Coal and Gas Outburst Based on Energy Balance Model. J. rock Mech. Eng. (02), 238–248.
Wang, H., Zhang, B., Yuan, L., Li, Q., Li, S., Xue, J., et al. (2017). Influence of Adsorbed Gas Content on Coal and Gas Outburst and Energy Analysis. J. rock Mech. Eng. (10), 2449–2456.
Wang, H., Zhang, B., Yuan, L., Li, Qingchuan., Li, Shucai., Xue, Junhua., et al. (2017). Influence of Adsorbed Gas Content on Coal and Gas Outburst and Energy Analysis. J. rock Mech. Eng. (10), 2449–2456.
Wang, K., Zhou, A., Zhang, J., and Zhang, P. (2012). Real-time Numerical Simulations and Experimental Research for the Propagation Characteristics of Shock Waves and Gas Flow during Coal and Gas Outburst. Saf. Sci. 50 (4), 835–841. doi:10.1016/j.ssci.2011.08.024
Wen, G. (2003). Research on Coal and Gas Outburst Energy. Chongqing, China: Mining safety and environmental protection, 1–3.06
Wu, Hao., Ma, Dan., Spearing, A. J. S., and Zhao, Guoyan. (2021). Fracture Phenomena and Mechanisms of Brittle Rock with Different Numbers of Openings under Uniaxial Loading. Geomechanics Eng. 25 (6), 481–493. doi:10.12989/gae.2021.25.6.481
Wu, H., Dai, B., Cheng, L., Lu, R., Zhao, G., and Liang, W. (2021). Experimental Study of Dynamic Mechanical Response and Energy Dissipation of Rock Having a Circular Opening under Impact Loading. Mining, Metall. Exploration 38 (2), 1111–1124. doi:10.1007/s42461-021-00405-y
Xu, L., and Jiang, C. (2017). Initial Desorption Characterization of Methane and Carbon Dioxide in Coal and its Influence on Coal and Gas Outburst Risk. Fuel 203, 700–706. doi:10.1016/j.fuel.2017.05.001
Yang, D., Chen, Y., Tang, J., Li, X., Jiang, C., Wang, C., et al. (2018). Experimental Research into the Relationship between Initial Gas Release and Coal-Gas Outbursts. J. Nat. Gas Sci. Eng. 50, 157–165. doi:10.1016/j.jngse.2017.12.015
Yin, Z., Chen, W., Hao, H., Chang, J., Zhao, G., Chen, Z., et al. (2020). Dynamic Compressive Test of Gas-Containing Coal Using a Modified Split Hopkinson Pressure Bar System. Rock Mech. Rock Eng. 53 (2), 815–829. doi:10.1007/s00603-019-01955-w
Yin, Z. Q., Ma, H. F., Ma, H. F., Hu, Z. X., and Zou, Y. (2014). Effect of Static - Dynamic Coupling Loading on Fracture Toughness and Failure Characteristics in Marble. Jestr 7 (2), 169–174. doi:10.25103/jestr.072.25
Yu, B., Su, C., and Wang, D. (2015). Study of the Features of Outburst Caused by Rock Cross-Cut Coal Uncovering and the Law of Gas Dilatation Energy Release. Int. J. Mining Sci. Technol. 25 (3), 453–458. doi:10.1016/j.ijmst.2015.03.020
Zhao, W., Cheng, Y., Guo, P., Jin, K., Tu, Q., and Wang, H. (2017). An Analysis of the Gas-Solid Plug Flow Formation: New Insights into the Coal Failure Process during Coal and Gas Outbursts. Powder Technol. 305, 39–47. doi:10.1016/j.powtec.2016.09.047
Zhi-qiang, Y., Li, X., Jin, J., Xian-qun, H., and du, K. (2012). Failure Characteristics of High Stress Rock Induced by Impact Disturbance under Confining Pressure. unloadingTransactions Nonferrous Met. Soc. China 22 (1), 175–184. doi:10.1016/S1003-6326(11)61158-8
Keywords: coal and gas outburst, gas expansion energy, energy dissipation, expansion energy of adsorbed gas, crushing energy
Citation: Zhao Y and Niu X (2022) Experimental Study on Work of Adsorption Gas Expansion After Coal and Gas Outburst Excitation. Front. Earth Sci. 10:886309. doi: 10.3389/feart.2022.886309
Received: 28 February 2022; Accepted: 24 March 2022;
Published: 09 May 2022.
Edited by:
Kun Du, Central South University, ChinaReviewed by:
Hao Wu, China University of Mining and Technology, ChinaXiaobo Zhang, Nanchang University, China
Liang Cui, Lakehead University, Canada
Copyright © 2022 Zhao and Niu. This is an open-access article distributed under the terms of the Creative Commons Attribution License (CC BY). The use, distribution or reproduction in other forums is permitted, provided the original author(s) and the copyright owner(s) are credited and that the original publication in this journal is cited, in accordance with accepted academic practice. No use, distribution or reproduction is permitted which does not comply with these terms.
*Correspondence: Yi Zhao, Mzc0MjAyMzY3QHFxLmNvbQ==; XinGang Niu, eGluZ2FuZzIwMjAxMkAxNjMuY29t