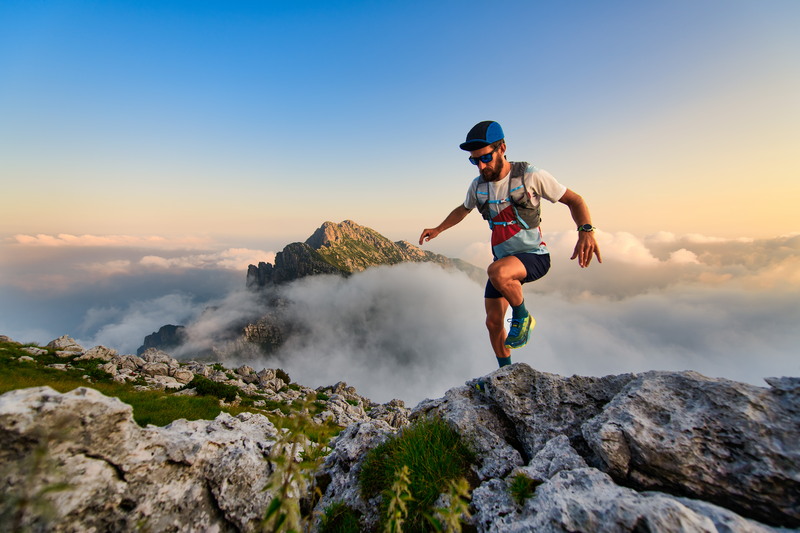
95% of researchers rate our articles as excellent or good
Learn more about the work of our research integrity team to safeguard the quality of each article we publish.
Find out more
ORIGINAL RESEARCH article
Front. Earth Sci. , 17 January 2023
Sec. Economic Geology
Volume 10 - 2022 | https://doi.org/10.3389/feart.2022.1071250
This article is part of the Research Topic Gas-Water-Rock Interaction and Multi Physical Field Coupling Mechanism View all 16 articles
Possible issues during mining of the upper coal seam in old goaf of nearby coal seams, including step subsidence, gas overflow in goaf, and roadway around rock fragmentation. Using the Hanjiawa Coal Mine’s upper coal seam mining, which takes place 28 m above the working face of the lower coal seam, as the research’s focal point. The paper focuses on the self-stability of the coal pillar in the old goaf, the failure form of the upper coal seam mining floor, the roof caving rule of the old goaf in the lower coal seam mining of the upper coal seam, and the bearing capacity of the interlayer rock strata using the pillar goaf stability evaluation system, field geological borehole electrical logging and borehole peeping, finite element difference numerical calculation, and other methods. The conclusion that the old goaf’s coal pillar can be completely stable and that the interlayer rock strata can bear the stress of upper coal seam mining is reached. The results show that the failure depth of the coal pillar in the lower coal seam old goaf is 1–3 m, the maximum failure depth accounting for 15% of the width of the coal pillar, and the failure depth of the roof in the old goaf is 0–3 m; After the mining of the upper coal seam, the floor above the coal pillar of the lower coal seam is plastic failure, and the failure depth is 1–10 m, and the failure depth of the roof of the old goaf of the lower coal seam is 3–15 m, which is 4 times greater than that before the mining. The maximum failure depth of the interlayer rock strata is 22 m, accounting for 78.6% of the rock strata spacing. The interlayer rock strata can bear the mining disturbance of the upper coal seam. The plastic zone of the floor of the upper coal seam is not connected with the plastic zone of the roof of the lower coal seam.
Since the 1990s, coal enterprises have actively or passively selected to mine the lower coal seam first due to the limitations of coal economic form, the pursuit of reasonable economic benefits, the insufficient accuracy of geological exploration in the mining area, poor production technical conditions and other reasons. With the continuous progress of mining technology and the improvement of economic situation, upward mining measures can be taken to recover the remaining coal seams, so as to improve the recovery rate of coal resources and increase production and efficiency for coal enterprises (Wang and Li, 1994; Singh et al., 2002; Du and Meng, 2009; Han et al., 2013).
Many scholars have done a lot of research on the problem of coal mining in the upper part of goaf. Sun et al. (2021) put forward the concepts of “partially balanced structure horizon” and “balanced structure horizon,” and established a method for judging the feasibility of upward mining under the condition of large mining height fully mechanized goaf. By means of theoretical analysis and similar simulation test, Feng (2009), Feng et al. (2009), Feng et al. (2010), Feng et al. (2011a), Feng et al. (2011b), Feng et al. (2019), and Bai et al. (2018) analyzed the evolution law of abutment pressure of upward mining in caving goaf and knife pillar goaf, established the stress-strain model, and put forward the theory and method for judging the feasibility in the technical conditions of upward fully mechanized mining in caving goaf and knife pillar goaf.
Ma (2021) studied the creep failure law of coal pillars in room pillar goaf under overburden load, determined the critical instability state in the dynamic instability process of coal pillars, and established the stability evaluation system of pillar goaf with multiple indexes based on fuzzy comprehensive evaluation method. Leilei et al. (2021a) and Leilei et al. (2021b) studied the influence of water content on coal strength from the perspective of long-time water intrusion into coal, which is conducive to the study of long-term stability of coal pillars in the old goaf of the lower coal seam. Li et al. (2019) analyzed the feasibility of upward mining of coal seam under multi-layer goaf, put forward comprehensive discriminant indexes for upward mining, and established quantitative discriminant and evaluation system for “feasibility” of upward coordinated mining. Pan et al. (2022) and Yao et al. (2022) conducted compression tests on rocks with cracks of different angles around the hole by means of numerical simulation and laboratory tests, revealed the failure mode of defective rocks, studied the crack propagation and stress evolution mode of defective rocks, which can reflect the morphological evolution and stress evolution rules of the lower coal seam goaf.
Han et al. (2011) studied the case of upward mining in Kailuan mining area, divided the damage degree of the upper coal seam after the mining of the lower coal seam into five grades, and established the feasibility criterion of upward mining of the close coal seam group based on multiple regression analysis. Zhang et al. (2013) studied the continuity and integrity of the upper coal seam in the upward mining of the close coal seam group in Qinghemen Mine, Fuxin Mining Area, and determined the structural change characteristics of the upper coal seam after the mining of the lower coal seam. Han et al. (1998), Ma et al. (2007), and Ma et al. (2008) studied Pingsi Coal Mine and Suanlagou Coal Mine by using the traditional discrimination method for upward mining of coal seams. Based on the limitations of the traditional discrimination method, they revealed the upward mining mechanism of close coal seams, expounded the relationship between the overlying rock status of upper seams and upward mining, and analyzed the influence of overlying rock lithology and structure of upper seams on upward mining. Qu et al. (2008) analyzed and studied the feasibility of upward mining of coal seam affected by multiple uneven mining in the lower part, and drilled holes to explore the development height of fracture zone after mining of lower coal seams, so as to provide basis for upward mining. Cheng (2004) observed and summarized the upward mining of the middle group coal in Haizi Coal Mine, and pointed out that the upward mining of the coal mine has increased the mine output and removed the gas hazard of the middle group coal mining, which has significant technical and economic benefits.
Okere et al. (2020), He et al. (2021), Zhang et al. (2021), and Tao et al. (2022) improves the accuracy of stress estimation and clarifies the impact of different test methods on the evaluation of working fluid damage. A mathematical model that can quantitatively analyze the interbed interference of coalbed methane mining is established by the author. This mathematical model also establishes a foundation for understanding the interbed interference of close coal seams and the evaluation of mine in situ stress test.
Few studies have been done on the cross-goaf mining of the upper coal seam in the old goaf under the low mechanization room pillar mining conditions in the early mine. Earlier studies were mostly focused on the upward mining of the goaf in the fully mechanized face. The upper coal seam mining in the room pillar old goaf is not suited for the conventional upward mining discrimination method. In this paper, the stability discrimination method of the pillar goaf is used to determine the goaf left over by the mine, and the mining impact of the upper coal seam is simulated, providing a solid foundation for the mining of the upper coal seam under comparable circumstances.
No. 22 coal seam was mined before 2009, the room and pillar mining method was adopted, with single mining means and low mechanization degree of mining work. And the coal produced by roadway mining was used instead of working face mining. The mining layout is shown in Figure 1.
Three roadways are excavated at one side of the return air roadway. The roadway width is 3 m, with an interval of 50 m. The roadway in the middle is the haulage drift, and the roadways on both sides are the return air drift. The crossheading is dug out every 60 m during the roadway excavation process, and the working face is dug out between the two crossheadings from the haulage drift to the return air drift. The side of the working face is then expanded using a rake mining machine, and the top and bottom coal are recovered using blasting to create a mine-out area. The size of the mine-out area is 20 m × 8 m.
A single mining unit shall reserve 20 m coal pillar from the crossheading on both sides, and 5 m coal pillar from the haulage drift and the return air drift. Three drifts are excavated in a single mining area, and 20 m coal pillars are reserved in two adjacent mining areas.
With the improvement of production technology, the requirements for mining the No. 19 coal seam overlying the goaf have been met. As shown in Figure 2, it can be obtained from the ZK-7 borehole column, the average interval between two coal seams is 25 m, the mining height of No. 22 coal seam is 8 m, the interval between coal seams is small and the mining height is large. According to the ratio discrimination method, “Three Zone” discrimination method and surrounding rock balance discrimination method and so on, it is difficult to mining the overlying coal seam. However, the traditional discrimination method is suitable for the determination of conventional wall mining conditions. Under the situation of room and pillar mining, the thick sandstone roof of NO. 22 coal seam will not fall after mining, and will play a role in the balanced rock stratum, so that No. 19 coal seam is above the balanced rock stratum.
In this study, the stability evaluation of pillar goaf, field geological borehole survey and finite element difference numerical simulation were used.
As a complex system, the stability of pillar mining goaf is affected by many factors. Ma (2021) developed a stability evaluation model for pillar goaf based on the findings of earlier studies, ranked the four primary influencing factors and their evaluation indices for pillar goaf stability according to weight scale, and concluded that the influence of geological factors, mining factors, strength factors, and environmental factors on the stability of the pillar goaf was gradually reduced.
The evaluation system of this evaluation model includes evaluation set U (Class I, Class II, Class III), factor set B (geological factors, mining factors, strength factors, environmental factors), and index set C (coal seam burial depth, dip angle, geological structure, etc.).
Class I stability of goaf is good: Goaf is stable and can resist certain external interference;
Class II stability of goaf is general: Goaf is stable, but it is easy to lose stability due to external interference
Class III stability of goaf is poor: Goaf cannot maintain its own stability.
Only when the stability of goaf is Class I or II, the overlying coal seam mining can be carried out. When the stability of goaf is Class III, it is difficult to carry out the overlying coal seam mining on the premise that the goaf detection and No. 19 coal seam detection are not done well.
The stability evaluation model of pillar goaf has established the classification standard and membership function calculation formula for 15 evaluation indexes. The classification standard of evaluation indexes is shown in Table 1.
TABLE 1. Classification standard of evaluation indexes Ma (2021).
For quantitative indexes of positive gain of numerical value, the membership function is calculated as follows (Ma, 2021):
For quantitative indexes of negative gain of numerical value, the membership function is calculated as follows (Ma, 2021):
Where, x is the specific value of quantitative indexes, and
For qualitative indexes, the expert scoring method is adopted to divide them into three categories: a, b and c, and the corresponding membership relationship is shown in Table 2.
TABLE 2. Membership relationship of qualitative indexes Ma (2021).
Firstly, the single-factor first-level fuzzy matrix
Establish the single-factor fuzzy comprehensive evaluation model:
Secondly, the four-factor second-level fuzzy comprehensive evaluation model is synthesized by weight vector X and matrix R:
Based on the goaf stability evaluation, ground borehole detection was done for goaf of the lower coal seam in order to confirm the accuracy of goaf stability evaluation, and the stability of the goaf roof was thoroughly assessed through borehole core breakage degree, borehole electrical measurement, and borehole peeping. In order to eliminate the impact of drilling technology on the core breakage degree, two sites above the goaf and adjacent solid coal were selected for detection.
FLAC3D is a finite element difference numerical simulation software, which is mostly used for geotechnical engineering simulation. Combined with the ZK-7 borehole column and rock mechanics parameters, the simulation calculation was carried out for the mining of No. 19 coal seam. The length × width × height of the model was 378 m × 338 m × 153 m, as shown in Figure 3, boundary constraints were imposed on the side and bottom of the model, and a vertical stress of 3 MPa was applied to the upper surface of the model. The Mohr Coulomb criterion was selected for the model, and the side pressure coefficient was taken as 1. See Table 3 for rock mechanical parameters.
The occurrence state diagram of No. 22 coal old goaf is shown in Figure 3. At present, the mining of No. 19 coal seam has not been carried out. The conventional wall mining method is used to carry out the simulation research on the mining of No. 19 coal seam. On the base of No. 22 coal seam mining, the mining of the overlying No. 19 coal seam is simulated. The working face length is 200 m, and the mining is pushed forward by 120 m. The mining is carried out 12 times by the way of gradual excavation, and the final mining position is located above the section-pillar center of the No. 22 coal seam.
According to the evaluation model, the stability of pillar goaf of No. 22 coal seam is evaluated as follows:
The geological structure of the room and pillar mining area is simple, there is no fault, and there is an aquifer in the overlying strata of the coal seam, which is the direct source of water filling for the goaf after mining. The parameters of various evaluation indexes can be obtained from the measured data and the existing geological data, as shown in Table 4.
Substituting the numerical values of each index into the calculation formula of membership function, the fuzzy relation matrix of each influencing factor can be obtained as follows:
Substituting the weight and membership degree of each index into Eq. 8, the single factor first-level fuzzy comprehensive evaluation vector is obtained as follows:
Based on the above calculation, the four-factor second-level fuzzy comprehensive evaluation matrix can be obtained. According to the weight vector of the four factors, the second-level fuzzy comprehensive evaluation vector can be calculated as:
According to the calculation results of second-level fuzzy comprehensive evaluation, the membership degree of the stability class of the goaf to the stability class of I, II, and III is 0.507, 0.387, and 0.106 respectively. Obviously, the membership degree of the stability class of Class I is the highest, so the stability evaluation of goaf is good, that is, the goaf can be stable by itself at present. And can resist certain external interference.
In order to clarify the stability of the roof in the goaf of No. 22 coal seam and the integrity of No. 19 coal seam, coring was started from 30 m above No. 19 coal seam. Among them, the core recovery rate of borehole above solid coal is 85.95%, and the core recovery rate of borehole above goaf is 84.73%. The electrical survey results of the borehole above the goaf show that there is still 1.3 m of top coal in the goaf roof that has not collapsed, indicating that the roof of goaf in No. 22 coal seam has good integrity. The overburden of the No. 22 coal seam has good integrity, and no visible fissures are created, according to the borehole peep. The column of two boreholes is shown in Figure 4.
FIGURE 4. Column of boreholes in goaf and solid coal. (A) Goaf borehole Column; (B) Solid coal borehole column.
According to the numerical calculation results, the main stress distribution cloud diagram of coal pillar of No. 22 coal seam is shown in Figure 5. It can be seen from Figure 5 that the principal stress of the crossheading-pillar is concentrated. Among them, the maximum principal stress P1 shows an obvious decreasing trend towards the center of the crossheading-pillar at the shoulder angle and bottom angle of the goaf, the minimum principal stress P3 has the maximum stress at the center of the crossheading-pillar, and the stress decreases towards goaf and roadway.
FIGURE 5. Distribution cloud diagram of principal stress in No. 22 coal pillar. (A) Maximum principal stress distribution cloud diagram; (B) Minimum principal stress distribution cloud diagram.
In order to clarify the influence of mining stress distribution on the plastic zone of coal pillar, a 60 m × 60 m × 1 m working face model and a 43 m × 43 m × 1 m roadway model are established respectively. The rock mechanics parameters are shown in Table 4. The stresses above the working face and roadway are extracted for numerical simulation calculation. The results are shown in Figure 6.
FIGURE 6. Plastic zone development pattern of single mining unit. (A) Plastic zone of goaf; (B) Plastic zone of roadway.
It can be seen from Figure 6 that the plastic failure depth of coal pillar at the side of goaf is 0.5–2.5 m, that of coal pillar at the side of roadway is 0.5 m, so the elastic zone in the middle of coal pillar is 17 m, and the plastic failure degree of a single coal pillar is 15%. Namely, the stripping degree of coal pillar is 15%, and it can remain stable.
It can be seen from Figure 7 that after the mining of No. 22 coal, the stress concentration occurred on both sides of the working face and on both sides of the roadway, with the maximum peak principal stress of 12.19 MPa and the stress concentration factor of 2.47. The stress of the overlying strata above the working face decreases, and the maximum and minimum principal stresses are distributed in an arch shape. The principal stress gradient of the thick fine-sandstone layer above the roof is large. Under its support, the overlying strata are less affected by goaf of the lower coal seam. The location of Coal Seam No. 19 is close to the original rock stress state. Except that there are some plastic zones in the top coal of No. 22 coal seam, there is no obvious plastic state in the overlying strata.
FIGURE 7. Principal stress distribution diagram of roof strata of No. 22 coal. (A) Maximum principal stress distribution diagram; (B) Minimum principal stress distribution diagram; In the figure, the lithology of each roof layer is shown in ZK-7 borehole column.
The size of the crossheading-pillar between the two mining units in the room pillar mining of No. 22 coal seam is large, but the size of the drift-pillar between the mining unit and the haulage drift and the return air drift is only 5 m, so the plastic failure is relatively serious in the direction of the No. 22 coal seam mining unit excavating. The distribution of the plastic zone of No. 19 coal seam mining step by step is shown in Figure 8.
FIGURE 8. Plastic failure law diagram of No. 19 coal mining. (A) Push forward 10 m; (B) Push forward 20 m; (C) Push forward 30 m; (D) Push forward 40 m; (E) Push forward 50 m; (F) Push forward 60 m; (G) Push forward 70 m; (H) Push forward 80 m; (I) Push forward 90 m; (J) Push forward 100 m; (K) Push forward 110 m; (L) Push forward 120 m.
After the No. 22 coal is mined, the part of drift-pillar near the cut-hole is plastic failure, and the part of drift-pillar near the crossheading-pillar is still in the elastic state. The crossheading-pillar and the section-pillar are less affected by mining.
According to Figure 8, when the No. 19 coal seam starts mining, the surrounding rock stress is redistributed, which has a mining influence on the roof and floor and the No. 22 coal seam goaf. When the No. 19 coal seam faces push forward within 40 m, the plastic failure depth of the No. 22 coal seam roof is 3 m, and the total lateral failure range is 62 m. When the working face of the No. 19 coal seam is pushed forward 50 m, the No. 19 coal seam is located above the drift-pillar of No. 22 coal seam, and the No. 19 coal roof appears plastic failure with the failure depth of 1 m and the failure width of 22 m. The plastic failure depth of the No. 22 coal goaf roof in front of the working face remains unchanged, and the lateral failure range increases to 64 m.
When the No. 19 coal face continues to push forward, plastic failure occurs on the floor of No. 19 coal working face above the drift-pillar of No. 22 coal seam and gradually increases with the advance of the working face, with the maximum failure depth of 8 m; When the No. 19 coal face is pushed to the upper part of the next mining unit of the No. 22 coal seam, due to the influence of the overburden rotary stress, the roof of goaf is failure more deeply, with the maximum failure depth of 8 m, and there is a certain failure area in the interlayer strata. The failure area is located at the side of the roof of the second mining unit of the No. 22 coal seam close to the drift-pillar; When the No. 19 coal face is pushed to the top of the section-pillar in the No. 22 coal seam, the floor of the No. 19 coal face witch above the section-pillar has plastic failure, the maximum depth of plastic failure is 10 m, and the plastic failure of the roof of the goaf on the other side of the coal pillar in the No. 22 coal seam mining area has intensified, the maximum depth of failure is 8 m. There is no plastic failure in front of the No. 19 coal seam, and the plastic zone of the No. 19 coal seam is not connected with the plastic zone of the No. 22 coal seam.
The stress curve of coal pillar can well reflect the current stress state of coal pillar. The principal stress curve of coal pillar in the old goaf is shown in Figure 9.
It can be seen from Figure 9 that due to the roof subsidence of the goaf, the stress of the coal pillar is concentrated, and the principal stress of the coal pillar at 0–2 m on the side of the goaf increases sharply; At the position of 2–15 m, the principal stress of coal pillar decreases and tends to be stable; The principal stress of 15–20 m coal pillar increases again, which is caused by the stress concentration of roadway surrounding rock. The maximum principal stress P1 reaches the peak value in the range of 2–4 m due to the influence of the roof subsidence and rotation in the goaf, and reaches the peak value again in the range of 18–20 m due to the influence of the stress concentration in the surrounding rock of the roadway. The minimum principal stress P3 is small due to the goaf on both sides of the coal pillar. The abutment pressure of coal pillars in two adjacent crossheading are symmetrical to each other.
The principal stress curves of the roof strata on both sides of the crossheading-pillar of the No. 22 coal seam are shown in Figure 10. It can be seen from Figures (a) and (b) that after the mining of the No. 22 coal seam, the stress balance of the surrounding rock is destroyed. The top coal of the No. 22 coal seam is not mined as the direct roof, and its stress concentration is the largest. The top thick fine-sandstone layer is used as the control layer to isolate the impact of the old goaf on the overburden. The No. 19 coal seam has stress changes only at the corresponding position above the No. 22 coal seam old goaf, and the corresponding position above the coal pillar is close to the original rock stress state. The occurrence of the old goaf of No. 22 coal seam has little impact on No. 19 coal seam. This result is consistent with the result of the old goaf stability evaluation, that is, the goaf itself can remain stable.
FIGURE 10. Principal stress distribution diagram of roof strata of No. 22 coal. (A) Maximum principal stress distribution curve of roof strata of No. 22 coal; (B) Minimum principal stress distribution curve of roof strata of No. 22 coal.
Figure 11 shows the plastic failure pattern expansion diagram of the upper coal seam at different advancing positions.
FIGURE 11. Expansion diagram of plastic failure patterns at different advancing positions in upper coal seam.
It can be seen from Figure 8 that before No. 19 coal seam is mined, the failure depth of No. 22 coal seam old goaf is 0–3 m, that is, the top coal of No. 22 coal seam is partially collapsed, which is consistent with the results of drilling detection. The results of drilling detection in the goaf show that there is still 1.3 m of top coal on the roof of old goaf.
As shown in Figure 11, when the No. 19 coal face advances to the 60 m position, the failure depth of the No. 19 coal face roof is 4 m and the failure area is 85 m2. From the 70 m position, the plastic failure depth increases by 80%, 10%, 40%, 55%, 12%, 26%, and the plastic failure area increases by 70%, 60%, 50%, 55%, 34%, 39% compared with the previous position; When the No. 19 coal face advances to the 70 m position, the failure depth of the floor of the No. 19 coal face is 6 m, and the failure area is 66 m2. From the 80 m position, the plastic failure depth increases by 33%, 13%, 0%, 11%, 20%, and the plastic failure area increases by 71%, 25%, 11%, 21%, 103% compared with the previous position; Within 40 m of No. 19 coal working face advancing, the failure depth of No. 22 coal goaf roof is 3 m, the failure depth does not change, and the failure area increases by 11%. When No. 19 coal working face advancing to 50 m position, the failure depth of No. 22 coal goaf roof is 4 m, and the failure area is 167 m2. Compared with the previous position, the plastic failure depth increases by 33%, 25%, 180%, 7%, and the failure area of plastic zone increases by 9%, 14%, 36%, 22% in the 50–80 m position. In the 90–120 m position, the plastic failure depth of No. 22 coal roof does not increase, and the failure area increases by 24%.
In the process of upper coal seam mining, the interlayer strata are failure in different positions and degrees. The maximum failure depth of interlayer strata is 22 m, accounting for 78.6% of the total thickness of interlayer strata.
Based on the above research, it can be concluded that the old goaf itself can remain stable before the mining of the upper coal seam, the top coal above the old goaf has partially collapsed, and there is no collapse of the interlayer rock strata. When the upper coal seam starts to be mined, the old goaf of the lower coal seam can bear certain mining influence, and the interlayer rock stratum remains stable.
The key to the mining of the upper coal seam is the stability of the interlayer strata. When the interlayer strata are intact, the upper coal seam can be mined normally. When there are cracks in the interlayer strata, the upper coal seam will be affected by the overflow of gas and water in the lower goaf. When the coal pillar and wall of the current coal seam goaf are stripped and the roof falls, the thickness of the interlayer strata decreases and the bearing capacity weakens. There may be some problems such as broken surrounding rock and difficult support in the upper coal seam mining.
Based on the above research and mine geological data, the following control measures are taken for the hazards in the mining process of upper coal seam:
(1) When mining upper coal seam, reasonable length of working face should be selected, the size of working face should be appropriately reduced, and the support strength of roadway and working face should be increased to reduce the bearing pressure of interlayer strata and reduce the probability of the formation of through cracks.
(2) Due to the advance of the working face, the increase of the abutment pressure will lead to the surrounding rock breaking in the advance roadway. The “anchor mesh cable” combined support can be adopted, and materials such as lengthened anchor bolts and grouting anchor bolts can be selected. If more support is required, the surrounding rock can be strengthened by grouting or increasing the support density.
(1) The pillar goaf stability evaluation method is adopted to calculate the stability of the lower coal seam old goaf, and the membership degree of the goaf to Class I stability is 0.507. Therefore, the stability of the old goaf is evaluated as good, and the goaf can stabilize itself and resist certain external interference.
(2) The numerical analysis shows that the plastic failure depth of the crossheading-pillar in the room and pillar mining of the lower coal seam is 15%, and the overlying thick fine-sandstone is used as the control layer, which insulates the influence of the lower mining and stress redistribution, and makes the upper coal seam stable.
(3) The conventional wall mining method is used to simulate and analyze the mining of upper coal seam. It is concluded that with the advance of the mining, the failure depth of interlayer strata will gradually increase due to the influence of the overburden rotary stress and coal pillar stress concentration in the lower coal seam. The maximum failure depth accounted for 78.6% of the interlayer spacing. The interlayer rock strata can bear the mining disturbance of the upper coal seam.
(4) Based on the above research, targeted control measures are proposed for hazards in the upper coal seam mining process.
The original contributions presented in the study are included in the article/Supplementary Material, further inquiries can be directed to the corresponding author.
HL: Writing, methodology. CH: Data curation, writing—original draft. ZW: Investigation. CL: Numerical simulation. LG: Numerical simulation. JL: Data curation. HW: Methodology.
This work was partially supported by the National Natural Science Foundation of China (Grant No. 51574224), the National Natural Science Foundation of China (Grant No. 52004289) and the Fundamental Research Funds for the Central Universities (Grant No. 2022XJNY01).
The authors wish to sincerely thank various organizations for their financial support.
ZW was employed by Zuoyun Hanjiawa Coal Industry Co., Ltd., Shanxi Coal Imp. & Exp. Group. CL was employed by China CAMC Engineering Co., Ltd.
The remaining authors declare that the research was conducted in the absence of any commercial or financial relationships that could be construed as a potential conflict of interest.
All claims expressed in this article are solely those of the authors and do not necessarily represent those of their affiliated organizations, or those of the publisher, the editors and the reviewers. Any product that may be evaluated in this article, or claim that may be made by its manufacturer, is not guaranteed or endorsed by the publisher.
Bai, J., Feng, G., Wang, S., Qi, T., Yang, J., Guo, J., et al. (2018). Vertical stress and stability of interburden over an abandoned pillar working before upward mining: A case study. R. Soc. open Sci. 5 (8), 180346. doi:10.1098/rsos.180346
Cheng, X. (2004). Research and practice on ascending mining under complicated geological conditions. Coal Sci. Technol. (1), 44–46. doi:10.13199/j.cst.2004.01.46.chengxm.013
Du, J. P., and Meng, X. R. (2009). Mining technology. Xuzhou, China: China University of Mining and Technology Press. (In Chinese).
Feng, G. (2009). Study on the theory and its application of upward mining of left-over coal. Taiyuan: Taiyuan University of Technology.
Feng, G., Yan, X., Wang, X., Kang, L., and Zhai, Y. (2009). Determination of key positions of strata controlling in rocks between coal seams for upward mining. Chin. J. Rock Mech. Eng. 28 (S2), 3721–3726. doi:10.3321/j.issn:1000-6915.2009.z2.061
Feng, G., Zheng, J., Ren, Y., Wang, X., Kang, L., and Liu, H. (2010). Decision theory and method on feasibility on the upward fully mechanized mining of the left-over coal above gob area mined with caving method. J. China Coal Soc. 35 (11), 1863–1867. doi:10.13225/j.cnki.jccs.2010.11.018
Feng, G., Ren, Y., Wang, X., Li, J., and Kang, L. (2011). Experimental study on the upward mining of the left-over coal above gob area mined with caving method in Baijiazhuang Coal Mine. J. China Coal Soc. 36 (4), 544–550. doi:10.13225/j.cnki.jccs.2011.04.015
Feng, G., Ren, Y., Wang, X., Li, J., Kang, L., et al. (2011). Experimental study on the movement and deformation of rock strata berween coal seams in the coal mining above gob area. J. Min. Saf. Eng. 28 (3), 430–435. doi:10.3969/j.issn.1673-3363.2011.03.018
Feng, G., Yang, C., Zhang, Y., Bai, J., Guo, J., Du, Y., et al. (2019). Temporal and spatial evolution law of abutment pressure during upward long-wall mining in the wedge residual pillar mining area. J. Min. Saf. Eng. 36 (5), 857–866. doi:10.13545/j.cnki.jmse.2019.05.001
Han, W., Wang, L., and Zhou, J. (1998). Observation and investigation of ascending mining of seams in pindingshan No. 4 mine. J. China Coal Soc. 3, 45–48.
Han, J., Zhang, H., Zhang, P., and Li, T. (2011). Feasibility study on upward mining in seam group with short distance to each other in kailuan mining area. Coal Sci. Technol. 39 (10), 14–17. doi:10.13199/j.cst.2011.10.19.hanj.011
Han, J., Song, W. H., and Zhu, Z. J. (2013). Upward mining technology of close coal seams. Beijing, China: China Coal Industry Publishing House. (In Chinese).
He, J., Okere, C. J., Su, G., Hu, P., Zhang, L., Xiong, W., et al. (2021). Formation damage mitigation mechanism for coalbed methane wells via refracturing with fuzzy-ball fluid as temporary blocking agents. J. Nat. Gas Sci. Eng. 90, 103956. doi:10.1016/j.jngse.2021.103956
Leilei, S., Zhang, H., Jianping, W., Li, B., and Han, H. (2021). Modeling and experiment for effective diffusion coefficient of gas in water-saturated coal. Fuel 284, 118887. doi:10.1016/j.fuel.2020.118887
Leilei, S., Jianping, W., Xi, Y., Wang, H., Wen, Z., Li, B., et al. (2021). The influence of long-time water intrusion on the mineral and pore structure of coal. Fuel 290, 119848. doi:10.1016/j.fuel.2020.119848
Li, Y., Lei, M., Zheng, Q., Liu, S., Lv, H., Liu, L., et al. (2019). Quantitative criterion on coordinated ascending mining in close multiple“ thin-medium-thick” coal seams. J. China Coal Soc. 44 (S2), 410–418. doi:10.13225/j.cnki.jccs.2019.0794
Ma, H. (2021). Coupling effect of coal pillar-roof and stability evaluation of pillar goaf. Xuzhou: China University of Mining and Technology.
Ma, L., Wang, L., Zhang, D., Liu, Y., Liu, J., Zhang, T., et al. (2007). Applicationg and study on feasibility of near distance coal seam group Ascending mining. J. Hunan Univ. Sci. Technol. Nat. Sci. Ed. (4), 1–5. doi:10.3969/j.issn.1672-9102.2007.04.001
Ma, L., Wang, L., Qiao, J., Wang, S., et al. (2008). Study of ascending mining of short-range-seams in pingdingshan no. 4 coal mine. J. Min. Saf. Eng. (3), 357–360. doi:10.3969/j.issn.1673-3363.2008.03.023
Okere, C. J., Su, G., Zheng, L., Cai, Y., Li, Z., and Liu, H. (2020). Experimental, algorithmic, and theoretical analyses for selecting an optimal laboratory method to evaluate working fluid damage in coal bed methane reservoirs. Fuel 282, 118513. doi:10.1016/j.fuel.2020.118513
Pan, H., Jiang, N., Gao, Z., Liang, X., and Yin, D. (2022). Simulation study on the mechanical properties and failure characteristics of rocks with double holes and fractures. Geomechanics Eng. 30 (1), 93–105. doi:10.12989/GAE.2022.30.1.093
Qu, G., Lin, D., and Wang, B. (2008). Technology on ascending mining affected by mining action of non-equipoise time after time. J. Min. Saf. Eng. (2), 217–221. doi:10.3969/j.issn.1673-3363.2008.02.020
Singh, A. K., Singh, R., Sarkar, M., Mandal, P. K., and Sharma, D. (2002). Inclined slicing of a thick coal seam in ascending order - a case study. Cim. Bull. 95 (1095), 124–128.
Sun, C., Yan, S., Xu, N., Liu, Y., et al. (2021). Key problems of upward mining under the condition of fully mechanized goaf with large mining height. J. Min. Saf. Eng. 38 (3), 449–457. doi:10.13545/j.cnki.jmse.2020.0086
Tao, X., Okere, C. J., Su, G., and Zheng, L. (2022). Experimental and theoretical evaluation of interlayer interference in multi-layer commingled gas production of tight gas reservoirs. J. Petroleum Sci. Eng. 208, 109731. doi:10.1016/j.petrol.2021.109731
Wang, L. Q., and Li, Z. H. (1994). Ascending mining technology of coal seams. Beijing, China: China Coal Industry Publishing House. (In Chinese).
Yao, D. H., Jiang, N., Wang, X., Jia, X., and Lv, K. (2022). Mechanical behaviour and failure characteristics of rocks with composite defects of different angle fissures around hole. Bull. Eng. Geol. Environ. 81 (7), 290. doi:10.1007/s10064-022-02783-z
Zhang, H., Han, J., Hai, L., Li, M., and Qiao, H. (2013). Study on closed multiple-seam in the ascending mining technology. J. Min. Saf. Eng. 30 (1), 63–67.
Keywords: close coal seams, upper coal seam mining, stability of old goaf, stress distribution, evolution of plastic zone
Citation: Liu H, Hao C, Wang Z, Li C, Guo L, Liang J and Wang H (2023) Study on stability of underlying room and pillar old goaf in close coal seam and mining of the upper coal seam. Front. Earth Sci. 10:1071250. doi: 10.3389/feart.2022.1071250
Received: 16 October 2022; Accepted: 22 November 2022;
Published: 17 January 2023.
Edited by:
Leilei Si, Henan Polytechnic University, ChinaReviewed by:
Chinedu J. Okere, Texas Tech University, United StatesCopyright © 2023 Liu, Hao, Wang, Li, Guo, Liang and Wang. This is an open-access article distributed under the terms of the Creative Commons Attribution License (CC BY). The use, distribution or reproduction in other forums is permitted, provided the original author(s) and the copyright owner(s) are credited and that the original publication in this journal is cited, in accordance with accepted academic practice. No use, distribution or reproduction is permitted which does not comply with these terms.
*Correspondence: Linfeng Guo, bGluZl9nQDE2My5jb20=
Disclaimer: All claims expressed in this article are solely those of the authors and do not necessarily represent those of their affiliated organizations, or those of the publisher, the editors and the reviewers. Any product that may be evaluated in this article or claim that may be made by its manufacturer is not guaranteed or endorsed by the publisher.
Research integrity at Frontiers
Learn more about the work of our research integrity team to safeguard the quality of each article we publish.