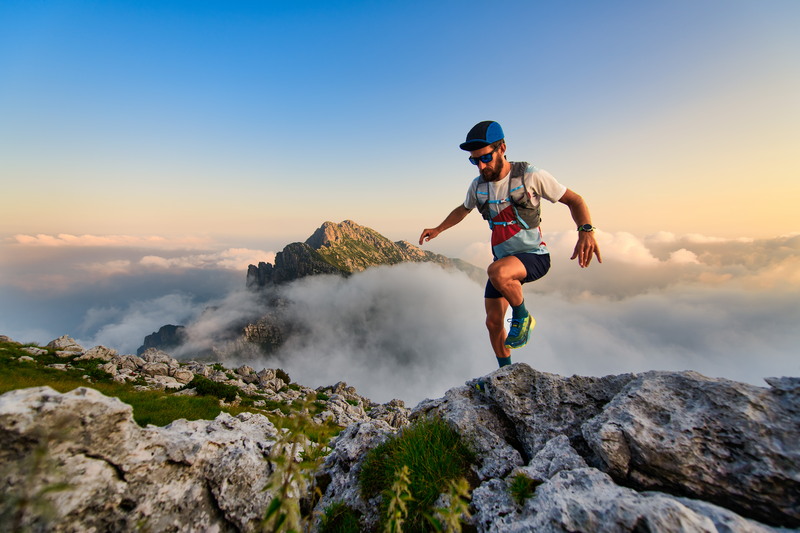
95% of researchers rate our articles as excellent or good
Learn more about the work of our research integrity team to safeguard the quality of each article we publish.
Find out more
ORIGINAL RESEARCH article
Front. Clim. , 13 October 2021
Sec. Carbon Dioxide Removal
Volume 3 - 2021 | https://doi.org/10.3389/fclim.2021.705032
This article is part of the Research Topic Pathways Towards Negative Emissions in Industry View all 6 articles
The pulp and paper industry has a high potential to contribute to negative emissions through carbon capture and storage (CCS) applied to existing processes. However, there is a need to investigate how CCS solutions also can be combined with implementation of other emerging technologies in pulp and paper mills. This paper investigates the integration of a novel calcination process in two kraft mills and evaluates its potential combination with capture and storage of CO2 from the calcination plant. The alternative calcination process uses electric gas-plasma technology combined with steam slaking and allows replacing the conventional fuel-driven lime kilns with a process driven by electricity. The novel calcination process generates a pure, biogenic, CO2 stream, which provides an opportunity to achieve negative emissions at relatively lower costs. The potential reduction of greenhouse gas emissions when replacing the lime kiln with the plasma calcination concept depends strongly on the emissions intensity of grid electricity, and on whether fossil fuel or biomass was used as a fuel in the lime kiln. If fossil fuel is replaced and electricity is associated with very low emissions, avoided CO2 emissions reach ~50 kt/a for the smaller mill investigated in the paper (ca 400 kt pulp per year) and almost 100 kt/a for the larger mill (ca 700 kt pulp per year). Further emission reductions could then be achieved through CCS from the electrified calcination process, with capture potentials for the two mills of 95 and 164 kt/a, respectively, and capture and storage costs estimated to 36–60 EUR/tCO2.
The pulp and paper industry undoubtedly has an important role to play in the industrial transition toward net zero emissions. With its renewable feedstock base and energy supply relying mainly on biomass, it is not considered as a hard-to-abate industrial sector. However, it is likely to be challenged in the future by increasing competition for these renewable, fossil-free resources (Material Economics., 2020). On the other hand, resource efficiency improvements and integration of new technologies and biomass conversion processes in pulp and paper mills present promising opportunities to extend their product portfolio to provide more biobased materials to other sectors where they can replace fossil alternatives. Furthermore, the pulp and paper industry, with its existing significant sources of biogenic CO2, has a high potential to contribute to negative emissions through carbon capture and storage (CCS). The potential for bio-energy carbon capture and storage (BECCS) in the pulp and paper industry has been estimated to 60 MtCO2 per year in Europe (Jönsson and Berntsson, 2012) and 20 MtCO2 per year in Sweden (Hansson et al., 2017; Rootzén et al., 2018). Kuparinen et al. (2019) estimate the global technical potential to capture CO2 from sulfate pulp mills to be 135 MtCO2/a.
For the pulp and paper industry to respond to the challenges and opportunities of expected and potential changes in resource and energy markets, it is crucial to explore all options available, including valorization of various biomass side streams, electrification of core process units, as well as different carbon capture utilization and storage (CCUS) solutions. Consequently, it is also important to consider the interplay between different technology pathways, e.g., how electrification of certain process units may affect the opportunities for carbon capture from the whole plant site.
Examples of new pathways for the pulp and paper industry that have received interest in recent literature include different options for valorizing black liquor (Akbari et al., 2018), including a dedicated development toward biofuel production (Jafri et al., 2020), as well as a move toward biorefining in general (de Blasio, 2019).
With regards to CCS, there are several studies which have investigated its potential in the pulp and paper industry. Hektor and Berntsson (2007) showed that thermal process integration with the pulping process and utility system could significantly reduce external fuel supply and thereby the cost for amine-based post-combustion capture from a recovery boiler. In a follow-up study (Hektor and Berntsson, 2009), the same authors then compared different heat supply options and compared the avoidance cost for post-combustion between a market pulp mill and an integrated pulp and paper mill. McGrail et al. (2012) instead considered carbon capture for a new biomass power island, which was designed for sufficient capacity to cover the mill's steam demand and run the capture process, but also with the flexibility to suspend the capture during unfavorable market conditions and then use excess heat for increased power generation. While it is clear that mills with a steam surplus available to drive the capture process have an advantage in terms of capture costs, such a steam surplus has many alternative uses, which compete with carbon capture. Jönsson et al. (2013) compared CCS to other options for utilizing a steam surplus in a pulp mill, and showed that generally, the best economic performance is achieved for different biomass export and valorization options, while CCS results in the higher CO2 emissions reduction. More recent studies of carbon capture in pulp and paper mills include the work of Onarheim et al. (2017a,b), who presented a comprehensive assessment of different configurations for amine-based post combustion capture of CO2 from the flue gases of the recovery boiler, the power boiler and the lime kiln in both a market pulp mill and an integrated pulp and board mill. The technical potential for negative emissions, and the effects on steam, fuel and electricity balances were evaluated (Onarheim et al., 2017b) as well as the techno-economic performance (Onarheim et al., 2017a). They showed that in order to reach the same pulp production cost as for a mill without CO2 capture, a negative CO2 emission credit of 60–80 €/t CO2 will be required. Further advancements of the process configuration for post-combustion capture from mill flue gases were investigated by Nwaoha and Tontiwachwuthikul (2019). All of the studies assumed capture plants to be retrofitted to current processes of pulp and paper mills, considering post-combustion capture from flue gases of conventional technology (recovery boiler, power boiler and lime kiln), and not considering the potential development of technology driven by biorefining and electrification strategies.
Only a few studies have investigated the potential of carbon capture from or in combination with emerging processes in the pulp and paper industry. These include the study by Möllersten et al. (2003)—one of the earliest studies on CCS in the pulp and paper industry—in which the potential for CO2 reduction in Swedish pulp and paper industry was investigated. Among various technology options considered, one alternative was the black liquor gasification (as a potential alternative to the still completely dominating recovery boiler technology) with pre-combustion CO2 capture and storage. In another paper, CCS was investigated in combination with biomass-based heat and power production technologies that could replace the conventional power boiler systems. It was found that the higher CO2 avoidance is achieved when capture is integrated with a biomass gasifier and water gas shift reaction. Preliminary cost assessments were also reported (Möllersten et al., 2006). A very recent example combining CCS with novel technology is the study by Santos et al. (2021), in which a completely new process concept based on calcium looping was proposed and evaluated. None of the aforementioned studies focus on the combination of electrification and carbon capture.
In this paper, we investigate the combination of electrification and CCS in the calcination process of pulp and paper mills. The calcination process is a core step in the recovery of cooking chemicals in the pulp mill. And even if the recovery boiler is the major emitter of carbon dioxide in a chemical pulp mill, the conventional calcination process (the lime kiln) is also one of the main emission sources in the mill, typically responsible for around 10% of total mill emissions, see e.g., Onarheim et al. (2017b) and Kuparinen et al. (2019). Furthermore, emissions from the calcination process include CO2 generated both from the chemical reaction (i.e., process related emissions, where the carbon originates from the biogenic wood raw material) and from the combustion of fuels in the lime kiln, which leads to higher concentrations (around 20%) compared to normal flue gases such as those from the recovery and power boilers at the mill (Onarheim et al., 2017b). The higher concentration creates opportunities for more cost-efficient capture.
The fuels used in lime kilns are still mainly fossil fuels such as fuel oil and natural gas, which makes the lime kiln one of the last remaining sources of fossil emissions from many mills. However, renewable fuels, mainly originating from side streams of the forestry and pulping industry are receiving increasing attention, and a wide range of different biomass fuels are being used in mills today (Kuparinen and Vakkilainen, 2017).
An alternative calcination process using electric gas-plasma technology and steam slaking has been proposed, and a feasibility study has been reported with a proposal for testing the technology in pilot scale (Lundqvist, 2017). The new technology could provide several benefits compared to the conventional calcination process, including reduced emissions, faster reaction times, and smaller equipment size. The electrification of the process is also expected to be more economically viable as the cost for low-carbon electricity is projected to fall (IEA NEA., 2020) while costs associated with fossil fuels and competition for renewable fuels are expected to rise. The replacement of fuel usage in a lime kiln, with electricity in a new plasma driven process either leads to a direct reduction of fossil fuel use and associated emissions at the mill, or to avoided use of biomass that instead can be used to replace fossil fuel or feedstock in other industries or sectors. While the formation of process-related biogenic CO2 cannot be avoided, the novel calcination process generates a pure CO2 stream, which consequently provides an opportunity to achieve negative emissions at relatively lower costs. However, no previous study has investigated how the integration of this electric calcination concept in a pulp or paper mill affects the overall energy balances and emissions of such plants.
This paper aims to investigate the impact of integrating electric plasma calcination with steam slaking into existing pulp and paper mills. Using a case study-based approach, the effects on heat integration potentials, on-site electricity generation and on- and off-site CO2 emissions were investigated along with an economic assessment comparing the conventional calcination concept with the new calcination technology. Furthermore, the potential for achieving negative emissions by capturing the CO2 from the calcination process was estimated. This CCS option was also evaluated in terms of indicative costs.
The dominating chemical pulping process is the kraft process. In this process, a water-based solution with sodium hydroxide and sodium sulfide (called white liquor) is used to dissolve and remove the lignin from the cellulose fibers in the wood. After the cooking process, the cellulose fibers are removed from the lignin-containing solution (called black liquor) for further refining through bleaching and drying, while the cooking chemicals in the black liquor are to be recovered in the recovery boiler and the causticizing plant. In the causticizing plant, calcium oxide (CaO) is needed which in turn is recovered in the calcination process. Figure 1 shows how these processes are connected.
The black liquor mainly consists of water, various organic compounds from the wood, and inorganic compounds originating from the cooking chemicals. After the cooking plant, the black liquor is concentrated in a multi-stage evaporator plant before being sent to the recovery boiler, where the organic components are combusted to produce high pressure steam, while the inorganic components end up as a smelt. This smelt from the bottom of the recovery boiler is dissolved in weak white liquor to form so called green liquor. The green liquor is then transported to the causticizing plant. The high-pressure steam from the recovery boiler is used in a combined heat and power generation system to cover the heat demands of the various processes in the mill. However, the steam production in the recovery boiler is determined by the chemical recovery load, and it is not available to manage the steam balances of the mill. Consequently, an additional power boiler (bark boiler) is used for extra steam production when needed.
The causticization plant is used to recovery cooking chemicals, or more specifically, sodium hydroxide (NaOH) from the green liquor. In this process, lime is used. Burnt lime, calcium oxide (CaO), is mixed with water to form slaked lime, calcium hydroxide (Ca(OH)2):
In the causticization process, the slaked lime then reacts with carbonate ions from the green liquor forming calcium carbonate and sodium hydroxide:
The calcium carbonate precipitates, while the remaining solution is the white liquor, which contains the regenerated cooking chemicals. After washing, the precipitated calcium carbonate (lime mud) needs to be regenerated to calcium oxide in a calcination step:
The carbon dioxide formed in the reaction is of biogenic origin, since the carbon in the carbonate ions originates from organic content in the black liquor, and thereby from the wood raw material.
The conventional technology used for the calcination process in pulp and paper mills is the rotary lime kiln. The lime kiln is heated up to 1,200°C by combustion of fossil fuels or biomass, thus adding combustion emissions to the unavoidable process-related emissions.
Electric plasma calcination has been proposed as an alternative technology for reburning of lime in the pulp and paper industry that could replace the conventional lime kiln (LimeArc Process AB., 2021). Plasma arc furnaces open for new possibilities to electrify high-temperature and high-volume processes that are otherwise difficult to electrify (Beyond Zero Emissions, 2018). Electric plasma technology is used in the metallurgical industry for melting, remelting and refining of metals and alloys. Plasma technology has also been investigated for calcination of limestone in the cement industry as a measure for emissions reduction (Wilhelmsson et al., 2018). However, so far, little attention has been given to electric plasma calcination of lime as a potential technology for the pulp and paper industry. Although a novel technology, it has been tested in different scales since 2004 (Lundqvist, 2008).
The following description of the technology is based on reports from various research and pre-study projects, primarily (Bjotveit et al., 2003; Lundqvist, 2008). The electric plasma technology uses an electric arc furnace with a plasma generator and a calcination reactor where the reburning of lime takes place. The electric arc furnace has an electric current that flows between two electrodes, forming an electric arc. The carbon dioxide is heated to around 4,000°C when it gets in contact with the electric current, is partly ionized, and leaves the furnace as a gas-plasma mixture. When leaving the arc, the ionized atoms start to deionized and return to normal gas phase. The reforming of carbon dioxide releases large quantities of energy which is used to drive the calcium carbonate reaction in the calcination reactor. The process occurs at 950°C, and the calcination reaction time is expected to be significantly reduced compared to the conventional calcination process.
It is advantageous to combine electric plasma calcination with steam slaking of the lime, which is an exothermic reaction. In the conventional process, the burnt lime is mixed directly with the water-containing green liquor at temperatures low enough to prevent boiling in the causticizing vessel. Thus, the heat of the exothermic hydration (slaking) reaction is recovered at low temperatures and cannot be used further on site. With steam slaking, steam or wet air is used in the lime slaking process together with the hot lime from the calcination generator. This means that the reaction heat can be recovered at higher temperatures, which enables production of high-quality steam for further use within the process. For example, the recovered heat can be used to dry the lime mud before it is fed to the electric plasma calcination reactor, thereby lowering the energy use of the reactor.
A detailed process schematic of the electric plasma calcination with steam slaking has been suggested by Bjotveit et al. (2003). This process configuration is illustrated in Figure 2. According to this process concept, the water vapor from the lime mud drier is proposed to be used as slaking medium in a steam slaker, while the reaction heat from the steam slaker is used to drive the lime mud drier. Additional excess heat is suggested to be used for production of process steam at around 4 bar.
Figure 2. Detailed process schematic of electric plasma calcination with steam slaking. Solid lines represent mass flows and dashed lines represents heat flows.
After drying to essentially 0 % moisture content, sieving to remove inert solids, and deaeration, the lime mud is further preheated with hot carbon dioxide from the calcination reactor. The carbon dioxide is separated from the lime mud in a cyclone and the lime mud enters the calcination reactor where the reburning of lime occurs. The burned lime enters another cyclone where the hot carbon dioxide is separated and sent to the preheating unit.
Some of the carbon dioxide is compressed in two steps with inter-cooling for reuse in the plasma generator or as transport medium for the calcium carbonate entering the calcination reactor. The remaining carbon dioxide is removed from the system as a pure (biogenic) carbon dioxide stream which could be emitted, captured for storage, or further utilized.
The total power consumption of the electric plasma concept consists of the electric power demand of the plasma generator plus the power demand of the two compressors used to compress the carbon dioxide.
Two kraft mills located in Sweden were used to evaluate the proposed concept – one market pulp mill, and one integrated pulp and paper mill. The core pulping processes of an integrated pulp and paper mill and a market pulp mill are essentially the same (see section The Kraft Pulping Process), with the main difference that an integrated mill adds paper machines at the end of the pulp refining line. Because of this, an integrated mill has a significantly higher specific steam demand (per adt of pulp) than a market pulp mill, while the specific steam production in the recovery boiler is very similar. Typically, this means that market pulp mill can easily have a surplus of heat from the recovery boiler, while an integrated mill has a heat deficit, all due to the additional energy consumption of the paper production.
This is true also for the investigated case study mills. In the integrated pulp and paper mill, the energy from the recovery boiler alone is not enough to cover the hot utility demand of the process. Therefore, a bark boiler produces the additional energy required. This mill has a back-pressure turbine for own generation of electricity, but also purchases additional electricity from the grid. For the market pulp mill, the recovery boiler could provide enough heat to cover the hot utility demand of the process. The surplus steam, plus energy from the bark from an adjacent sawmill, is used for electricity production. This mill is equipped with both a back-pressure and a condensing turbine that generate enough electricity to be able to sell excess electricity to the grid.
The two case study mills investigated here also differ in terms of production capacity. The key characteristics of the mills are presented in Table 1 together with key assumptions relevant for the mill calcination processes.
To investigate how the novel calcination concept could be heat integrated with the rest of the mill processes, and how this would affect the power generation in the mills' steam turbine systems, a heat integration study was performed using a methodology based on Pinch Analysis, see e.g., (Klemeš, 2013).
Detailed operating data for process heat sources and heat sinks in the pulp mills were available from previous studies (Swing Gustafsson, 2013; Pedersén and Larsson, 2017) and was used as input to the Pinch Analysis. Minor adaptations were made to the stream data for the market pulp mill to remove streams related to the integrated condensing steam turbine cycle, since the sizing of this system was investigated separately in this work. The stream data, which is reported in the Supplementary Material, was used to construct the Grand Composite Curves (GCCs) for the mills. The resulting GCCs are presented in Figure 3 (with ΔTmin values chosen according to the original studies). These show the net heating and cooling demands for the processes assuming all opportunities for internal process heat recovery are exploited.
Figure 3. Grand composite curves for the investigated mills. (Left) Integrated pulp and paper mill. Based on data from Swing Gustafsson (2013). (Right) Market pulp mill. Based on data from Pedersén and Larsson (2017).
The potential for heat integration of the new electric plasma technology was then studied using key elements of an assessment methodology that was recently suggested for bottom-up assessment of process electrification options (Wiertzema et al., 2020). This methodology applies a foreground/background analysis with split GCCs to target the optimal integration of two processes, see e.g., Chapter 6 of the User Guide for Pinch Analysis by Kemp (2006) for a description of the principles of such an approach.
For the split GCC analysis, the electric plasma calcination was used as foreground. The remaining pulp/pulp and paper process represented in the background GCC was constructed by identifying and removing all process streams from the original pulp mill GCC that were connected to the conventional calcination process. The split GCC analysis provides a first overview of the potential for heat recovery.
The construction of the GCC of the electric plasma calcination with steam slaking was based on the process schematic presented in Figure 2, with assumptions according to Table 1, and assuming a ΔTmin of 10 K for heat exchanging (in line with the ΔTmin assumption for the integrated mill). The specific heat capacity for each component was estimated for the mean temperature of each stream. Reactor and slaker efficiencies were assumed to be 95%. The reaction for slaking of lime is an equilibrium reaction with an equilibrium temperature of 530 °C at 1 bar. The reaction needs to be performed well below the equilibrium temperature to achieve an acceptable reaction rate and good conversion of calcium hydroxide. However, it is desirable to have the reaction take place at as high temperature as possible, so that valuable steam can be produced from the reaction heat. There is thus a trade-off between high reaction rates and opportunities for high temperature heat recovery. In this work, it was assumed that the reaction temperature in the slaker is 200°C, in order to enable heat recovery at temperatures high enough for steam generation, while the reaction rate is still reasonable. The reaction heat for lime slaking at this temperature was estimated from the standard heat of reaction and heat capacity-temperature functions for the components. More details about these estimations as well as other assumptions underlying the modeling are available in Andersson and Skogström (2020).
In the next step, it was assumed that the new process is heat integrated with the existing mill processes via the utility steam system, i.e., without direct heat exchange between streams in the new calcination process and the existing mill. More specifically, steam is generated by heat exchange with hot carbon dioxide and heat from the steam slaking process. The amount of steam that can be generated was estimated from the GCC of the electric plasma calcination and steam slaking process.
Next, it was estimated how the addition of the new steam source from the calcination and steam slaking process (together with the removal of process streams connected to the lime kiln) would affect the potential integration of steam turbine cycles in the mill. This provided an estimation of the amount of electricity that can be generated in the mill, and how this potential is changed by integration of the new technology. This analysis was also performed using an energy targeting approach based on split GCCs. The stream data for the pulping process, including the steam generated from the plasma calcination and steam slaking plant, as well as the heat of combustion of the recovery boiler and bark boilers, was used to construct the GCC for the background process. The steam turbine cycle was represented as the foreground GCC. The approach is similar to that described in Svensson et al. (2019).
The main assumptions and simplifications for this analysis were:
• High temperature heat from combustion of black liquor in the recovery boiler is considered to be unavoidable excess heat available for steam generation, since the processing of black liquor in the recovery boiler is a necessary step in the recovery of chemicals.
• Since bark is available as a by-product at the mill sites, and there are constraints limiting the amount of bark that can be exported at a competitive price, it is assumed that the mills will primarily continue to use the amount of bark that they currently use – as long as they also can utilize the steam produced. Any potential reduction in process heat demand is used primarily to increase the steam flow through the mill's turbines, thereby increasing on-site generation of electricity. Bark boiler load is reduced only if the steam turbines are unable to accommodate increased throughput, in which case excess bark is sold.
• The steam cycle was modeled in a simplified way, limiting the turbine inlet steam pressure to a single level, and allowing a maximum of three steam levels for turbine extractions. These three steam headers were chosen to represent, as far as possible, the steam levels of the actual mills. The isentropic efficiencies of the steam turbines were estimated based on steam mass flows and pressure drops.
The procedure outlined above is suitable for energy targeting, i.e., estimating the potentials for minimum requirements for process heating and cooling, and how these requirements are affected when the conventional calcination process is replaced by the electricity-driven plasma process.
The process-related emissions from the calcination reaction are independent of the reburning method. In the electric plasma calcination process, only a very small fraction of the CO2 is required to operate the deaeration tank, which means that essentially all the CO2 formed in the reaction is emitted as a pure stream. The amount of CO2 formed in the reaction (CO2,calc.reaction) was estimated based on the chemical reaction and molecular weights of CaO and CO2, according to the following:
With the assumption of the same lime-to-pulp ratio for both mills (0.3 ton CaO/ton pulp, see Table 1), this was estimated to 95 ktCO2/a for the integrated mill and 164 ktCO2/a for the market pulp mill. These values correspond to the CO2 available for capture and storage (i.e., for negative emissions).
The total electric power demand for the plasma calcination plant (Pcalc.plant) was calculated according to the following:
Here, the only factor differing between the mills is the annual pulp production, which is provided in Table 1. As described above, the specific lime demand and annual operating time was assumed to be the same for both mills (0.3 ton CaO/ton pulp and 8,000 h/a, respectively, also reported in Table 1). The specific power consumption for the electric plasma concept was interpolated from values reported in Bjotveit et al. (2003) and thereby estimated at 5,300 kJ/kg CaO for the electric plasma generator and 190 kJ/kg CaO for the two compressors. For achieving negative emissions, the pure CO2 stream was assumed to be compressed to 110 bar for delivery to a CO2 interim storage hub, prior to transportation to the final storage site. Based on the annual flow of CO2 (calculated as described in section Estimating the Potential for Negative Emissions Through CCS), the electric power demand for this compression (PCO2comp) was calculated according to the following:
Here, the value for the specific electricity demand was derived from models used by Garðarsdóttir et al. (2018), from which it was estimated to be 89 kWh/tCO2. This value is in line with values reported in literature, see for example (Jackson and Brodal, 2019).
In addition to direct electric power demands of the plasma calcination process and CO2 compression, the increase in required grid electricity generation (Pgrid) is also affected by changes in on-site electricity generation in the steam turbines of the mill (Pturb) as resulting from the integration of excess heat from the new process in the mill's steam system. The net increase in grid electricity production is thus given by:
Replacing the lime kiln with the electric plasma calcination process and applying CCS to the emissions from the calcination reaction affect CO2 emissions in three ways, by:
• AvoidedCO2: (Fossil) combustion emissions are avoided by replacing fuel firing in the lime kiln with electricity.
• IndirectCO2: Indirect emissions associated with grid electricity generation increase when more electricity is used.
• NegativeCO2: Captured and stored biogenic CO2 from the calcination reaction leads to negative emissions (see section Estimating the Potential for Negative Emissions Through CCS).
The total emissions reduction (ReductionCO2) is thus determined by the following:
The mills investigated in this study have lime kilns that are fired with biomass. The integrated pulp and paper mill uses tall oil pitch, and the market pulp mill uses wood powder from sawdust. However, in many mills it is still common to fire the lime kiln with fossil fuel oil, thus the case in which a fossil fuel fired lime kill is replaced with electric plasma calcination case was also investigated. The energy use for a conventional lime kiln fired with fossil fuel oil was estimated at 6.0 MJ/kg CaO, based on data presented in Kuparinen et al. (2019). However, biomass fuels generally require higher firing rates to maintain the kiln production capacity. In line with previous studies (Kuparinen and Vakkilainen, 2017), the fuel demand for biomass fueled lime kilns was assumed to be 3% higher (i.e., 6.2 MJ/kg CaO).
The emission factor used for fuel oil as a lime kiln fuel was 275 gCO2eq/kWh. No fossil CO2 emissions were considered for the biomass fuels investigated. Sawdust and tall oil pitch are by-products from the forest industry, and therefore emissions for production or distribution of these fuels were assumed to be allocated to the main forest industry products. However, some processing (drying, grinding, and pulverization) is needed to prepare the sawdust for use in the lime kiln, which requires heat and electricity (98 kWel/MWfuel) according to Kuparinen and Vakkilainen (2017). In the investigated mill, the sawdust dryer is heat integrated with the rest of the mill. Heat for drying is provided by excess (biobased) heat from the process (this heat demand is represented as a cold stream in the stream data). The dryer is assumed to be kept in operation even if the lime kiln is replaced, since dried sawdust is also used for pellets production. However, the electricity used for wood powder production contributes with indirect emissions associated with grid electricity use with similar assumptions as described below for the electricity demand of the plasma calcination process. The indirect emissions related to sawdust preparation are, however, included in the term AvoidedCO2, and only when sawdust is used as a lime kiln fuel.
Electricity is used both for the plasma calcination process, and for compression of CO2 that will be sent to storage (see section Electricity Demand for the New Process Concept). The increase in electricity consumption may either increase the need for the mill to purchase electricity from the grid or reduce its export of renewable electricity. In either case, the net effect is that grid electricity production needs to increase. For the indirect emissions associated with this grid electricity production, a sensitivity analysis was performed in which the carbon intensity of grid electricity was varied between 0 and 900 gCO2/kWh. This range spans the entire range from net-zero build margin technologies in future electricity markets (e.g., wind and solar), to carbon-intensive power plants still in operation in current markets (e.g., coal-fired power plants).
Two different economic assessments were made. Firstly, costs of the novel calcination concept were compared to the costs of a conventional lime kiln in order to evaluate its potential economic competitiveness. Secondly, the capture, transport and storage cost for CCS was estimated, provided that that the electric plasma calcination was implemented. In the analysis, all possible care has been used to utilize relevant up-to-date prices and costs. However, as prices for energy as well as costs for equipment may vary substantially over time and between different regions, the main assumptions must always be updated when considering a specific, actual investment case.
For the cost comparison between the two calcination technologies, the total annual costs for the new technology were compared to the total annual costs for re-investing in the conventional technology at the end of the lifetime of the existing reburning unit. The investment costs assumed for the electric plasma calcination equipment and for a lime kiln were based on values reported by Bjotveit et al. (2003). The values were converted for currency and updated to 2019 cost levels using the Chemical Engineering Plant Cost Index (CEPCI). For the plasma generators, the cost in Bjotveit et al. (2003) were provided for three generator modules with a capacity of 5 MW each. It was assumed that such modules are implemented in parallel, and the costs were thus scaled linearly based on the number of modules required to meet the demand for the investigated mills. For all other equipment, investment costs were scaled using a cost-size exponent of 0.6.
The operating costs include operation and maintenance (O&M) corresponding to 4% of annualized investments, fuel or electricity costs and a yearly cost for changing of electrodes in the plasma generators, which was also taken from Bjotveit et al. (2003). Price assumptions for energy carriers, which represent current market conditions, are presented in Table 2. Prices for fuel oil and tall oil pitch were taken from previous studies connected to the actual mill (Olsson, 2020). The price of wood powder (pulverized sawdust) was calculated based on the market price of wood by-products for industrial customers, the cost of electricity required for pulverization, and annualized capital costs for the fuel preparation steps. Capital costs and electricity demand were estimated based on numbers reported by Kuparinen and Vakkilainen (2017). The price of bark was assumed to be about 20% lower than the market price of wood by-products in Sweden (16 €/MWh) (Swedish Energy Agency, 2019).
Since the electric plasma calcination process results in a pure stream of carbon dioxide, there is no need for further concentration of the CO2 and the total cost for CCS is limited to costs for compressing the CO2 and costs for transport and final storage.
For annualization of investment costs, a discount rate of 6 % was assumed. The economic lifetime of equipment was assumed to be 25 years, except for the lime kiln, which was assumed to have a lifetime of 40 years.
The capital cost for compression of CO2 was estimated using a cost function that was derived from process models of capture plants in previous work by Garðarsdóttir et al. (2018):
This function assumes a 4-stage compression with intercoolers for reaching 110 bar. As described in section Electricity Demand for the New Process Concept, this is the assumed pressure for delivery to a CO2 hub.
The cost for transport and storage of CO2 will depend on the development and scale-up of infrastructure for CCS. In Johnsson et al. (2020), the system cost for CO2 transport and storage was estimated to be 25–40 €/tCO2 for capture plants in Sweden, from which the CO2 is transported via transport hubs and ships to deep-sea storage well sites off the coast of Norway. The cost range depends on how many emission point sources and transport hubs are connected to such a CO2 collection and transport system. In this work, this whole range was considered to represent the uncertainties in transport and storage cost.
The GCC of the electric plasma calcination with steam slaking was constructed based on the process schematic presented in section Background About Kraft Pulping and Its Calcination Process, and is presented in Figure 4 (The stream data used to construct the GCC is available in the Supplementary Material).
The GCC shows that the process generates 1.7 MJ of high temperature excess heat per kg wet lime mud. This heat is available at temperatures well above the temperature of low-pressure steam in the mills (ca 145°C), and consequently available for process heat integration with the rest of the mill via the low-pressure steam header.
The GCC of the electric plasma calcination was then scaled to fit the lime production of each investigated mill (see Table 1), and the potential for recovering the excess heat from the calcination process to heat other streams in the pulp mill was estimated using split GCC analysis. The results are presented in Figure 5.
Figure 5. Split GCCs illustrating the potential heat integration of the electric plasma calcination process with the rest of the pulping processes. (Left) Integrated pulp and paper mill. (Right) Market pulp mill.
The results show that it is theoretically possible to integrate the electric plasma calcination with steam slaking with the existing mills to achieve a reduction of utility demand for the integrated processes. The total theoretical savings potential for the integrated mill is 19 MW and for the market pulp mill 26 MW (i.e., around 10% of the minimum hot utility demand for the mills with conventional processes, which were 211 and 231 MW, respectively).
The results above represent an estimation of the maximum heat recovery and utility savings that could be achieved by direct heat exchange between the new process and other parts of the mill. However, it was assumed that integration of the new process is most likely be achieved via the steam utility system of the mill, where it will affect the potential for power generation in the steam turbines. The electric plasma calcination and steam slaking process can therefore be represented in the process GCC by a hot stream representing the steam that can be generated by the electric plasma calcination concept.
Figure 6 shows how the integrated steam turbine cycles in mills are affected by the introduction of a new steam source from the plasma calcination and steam slaking plant and removal of streams related to the lime kiln process.
Figure 6. Integrated steam cycles (dashed lines) for the investigated mills with W denoting potential power generation. Mill processes (solid lines) includes heat from the recovery boiler and bark boiler. Gray lines: Original mill with lime kiln. Black lines: Mill with electric plasma calcination and steam slaking process. Note that the temperature axis has been cut off and high-temperature heat is available above 500°C to generate the indicated amount of steam.
The integrated pulp and paper mill relies on the bark boiler as a supplement to the recovery boiler to satisfy the process hot utility demand. No surplus of steam is generated, and the mill is not equipped with a condensing turbine. This means that the steam exiting the back-pressure steam turbine exactly covers the heat demand of the process. Consequently, if the steam production in the bark boiler is kept constant, while the steam demand is reduced thanks to the integration of excess heat from the novel steam slaking process, this would result in an excess of low-pressure steam from the mill of around 13 MW. This excess steam cannot be used for electricity production since there is no condensing turbine in the integrated mill and it is assumed that the steam excess is not sufficient to motivate investment in such a turbine. Instead, the integrated mill is assumed to reduce the load of the bark boiler to avoid producing unnecessary amounts of steam. The bark that is no longer used is sold to the market. However, the reduction in steam production has a negative effect on the cogeneration of electricity. The integration of the new electrified calcination concept with steam slaking thus results in a reduction of steam production in the bark boiler of about 17 MW, but also a reduction in electricity co-generation potential of 4.3 MW, for the integrated pulp and paper mill.
In the market pulp mill, heat generation from the boilers provides sufficient amounts of steam for electricity generation in the low-pressure condensing turbine. The integration of the new electrified calcination concept with steam slaking results in an increased power generation potential of 5.6 MW for the market pulp mill.
It was assumed that the mill replaces lime losses (2–5% of lime flow) by purchasing lime, and not by make-up limestone. In this case, the carbon dioxide released in the calcination reaction is entirely biogenic since the carbon originates from the wood raw material. These are emissions that can be easily captured from the electric plasma calcination process, for further transport to a permanent geological storage location, and thereby contribute to negative emissions. As described in section Estimating the Potential for Negative Emissions Through CCS (Equation 1), the potential was estimated to 95 ktCO2/a for the integrated mill and 164 ktCO2/a for the market pulp mill.
The electricity consumption estimated for an electric plasma calcination process integrated in each of the two case study mills (see Equation 2) is presented in Table 3. Table 3 also includes the estimated electricity demand for compression of captured CO2 (see Equation 3). In both mills, electricity consumption would increase by around 50%. However, the increased electricity demand affects the electricity balances differently for the two mills investigated. In the integrated pulp and paper mill electricity imports from the grid would increase. In the market pulp mill, which is a net exporter of electricity to the grid, electricity exports would be reduced. Table 3 also shows that in both mills, the integration of the new process leads to a net increase in demand for grid electricity production as calculated according to Equation (4).
Table 3. Resulting net increase in grid electricity production for the two investigated mills due to changes in electricity demands and on-site steam turbine power generation.
As described in section Integration via the Steam Utility System, the integration of the electric plasma calcination process leads to a reduction in back-pressure steam turbine power generation for the integrated pulp and paper mill. This reduction of own electricity generation must be compensated by further increasing the power purchase from the grid. Conversely, for the market pulp mill, the electricity production can increase as a result of integrating the electric plasma calcination process, since excess heat from the steam slaking process is used to generate steam for the condensing turbine. The increase in electricity production was used to cover part of the electric power demand for the electric plasma generator. This dampens the increase in demand for grid electricity and thereby also the emissions associated with electricity use slightly in the market pulp mill.
The replacement of the lime kiln has consequences for both on-site and off-site CO2 emissions. Combustion emissions from the lime kiln are avoided, while the grid electricity production is increased, leading to indirect emissions associated with grid electricity production. The emissions from combustion in the lime kiln can be of either fossil or biogenic origin. For the integrated pulp and paper mill, the integration of the new process also affects the combustion of bark in the power boiler, but these emissions are also of biogenic origin. Consequently, if the emissions from the conventional lime kiln are greater than the indirect emissions associated with electricity use for the electric plasma technology, there is a potential to reduce emissions by the change of technology. This emission reduction can be obtained even without accounting for the potential for capture and storage of biogenic CO2. Figure 7 shows a comparison of lime kiln emissions with indirect grid emissions, for different emission intensities for grid electricity, and for different lime kiln fuels. For the indirect emissions associated with grid electricity, it was assumed that the electric plasma calcination replaces the lime kiln and is integrated with the steam utility system of the mill.
Figure 7. CO2 emissions that differ between the calcination process concepts: Emissions from the lime kiln (if fired with fossil fuel oil or biobased fuel) and indirect emissions related to increased electricity demand for a mill switching to an electric plasma calcination concept.
Figure 7 shows that if the lime kiln is fired with fossil fuel oil, the replacement of the lime kiln with an electric plasma calcination process may lead to significant emission reductions if grid electricity has a low fossil carbon emission intensity. This is the case assuming average grid emission factors in low-carbon markets such as the Swedish or Nordic electricity system (20 and 125 gCO2/kWh, respectively), but also if a consequential approach is adopted and it is assumed that the new electricity demand is covered by build margin technologies required for decarbonization of the power sector in the future, such as wind and solar power (see e.g., Reichenberg et al., 2018). The break-even emission intensity, for which the emissions would be the same for the electric plasma calcination and the lime kiln is 253 gCO2/kWh for the integrated pulp and paper mill and 350 gCO2/kWh for the market pulp mill. These values can be compared to average European grid electricity in 2019 (275 gCO2/kWh) or the emission intensity for electricity from a new, conventional natural gas combined cycle plant (337 gCO2/kWh). For mill-specific calculations, Figure 7 can also be used by applying the average carbon emission intensity for the specific electricity purchased by the mill.
However, the investigated mills use biomass fuels in their lime kilns (tall oil pitch and sawdust). As described in section Assessment of Changes in CO2 Emissions, the use of these biomass fuels is assumed to be carbon neutral. Even if this is a simplified assumption, it was considered reasonable for this type of by-products for forest industry operations. With this assumption, the replacement of a biomass-fired lime kiln with an electrified process would result in increased greenhouse gas emissions for any grid emission intensity above zero. On the other hand, by replacing biomass driven calcination processes with electric plasma technology, significant amounts of biomass are released for use in other sectors which could lead to a net decrease of emissions if considering a wider system boundary (see Pettersson et al., 2020 for further information about how scarcity of biomass resources can be handled in carbon balances). The yearly use of biomass that would be avoided in the two investigated mills was estimated at 90 kt/a of sawdust for the market pulp mill and 20 kt/a of tall oil pitch for the integrated mill. Another advantage of using an electric plasma calcination process instead of biomass fuels in lime kilns could be a more stable and reliable operation, since biomass-based lime kiln operation is associated with concerns regarding unforeseen process interruptions and fire risk (Kuparinen and Vakkilainen, 2017).
If the CO2 emissions from the electric plasma calcination process are compressed and sent to long-term storage, these represent negative emissions (see section Potential for Carbon Capture). This also leads to a small increase in electricity demand for compression. The resulting total emissions reduction from the electric plasma calcination with CCS was determined according to Equation (5), and are shown in Figure 8.
Figure 8. Total reduction of CO2 emissions associated with replacing a lime kiln by an electric plasma technology equipped with CCS. The total reduction includes avoided emissions associated with fuel use in the lime kiln, negative emissions from captured and stored biogenic CO2 and adjustment for indirect emissions associated with increased electricity use.
As expected, the emission intensity of electricity has a strong influence on the results. In particular, the electricity used for the electric plasma calcination needs to be associated with low carbon emissions in order to reach large emissions reduction when replacing a lime kiln fired with biomass.
It was assumed that investment in the electric plasma technology would only be relevant as an alternative to investing in a new lime kiln, e.g., when the existing lime kiln needs to be scrapped at the end of its technical lifetime, or if increased calcination capacity is required as part of increasing the production capacity in the mill. Therefore, the cost comparison between the two technologies includes the annualized investment costs for both alternatives. Table 4 shows the total costs for the novel plasma calcination plant and steam slaker, and Table 5 shows the total costs for a conventional lime kiln.
Table 4. Total costs for investment and operation of the electric plasma calcination plant (without carbon capture).
The results indicate that the total annualized costs for the two technologies are comparable, for the assumed prices of fuels and electricity. In particular, introducing the electric plasma calcination seems promising for the integrated mill (independently of which fuel is used in the lime kiln), and for the market pulp mill if replacing a lime kiln fired by fossil fuel oil. However, the cost of electric plasma calcination is clearly sensitive to the price of electricity, which is illustrated in Figure 9.
Figure 9 shows the total annualized cost for the two process alternatives as a function of the electricity price assuming either a fossil or a biomass fuel in the lime kiln. The electric process is the cheapest option for electricity prices below 40 EUR/MWh in the (larger) market pulp mill, and below 50 EUR/MWh in the (smaller) integrated mill. However, these breakpoints would shift, for example, if the cost of emitting CO2 would increase (which would increase the cost of the lime kiln with fossil fuel oil), or if the demand for biomass fuels would increase and drive up the market prices for biobased fuels (which would increase the cost of the lime kiln with biobased fuels). It is also important to note that the risk and investment costs for the electric plasma calcination process are substantially higher than for a lime kiln, since this emerging technology is still at a low TRL level.
In mills where the existing lime kiln is a bottleneck for pulp production, it may also be interesting to invest in a smaller plasma calcination process as a capacity booster for lime production. However, this opportunity was not considered further here, since the smaller plant would imply a substantially smaller flow of pure CO2 for capture, and thereby lead to significantly poorer economy of scale for CCS applied to the novel process.
Due to the uncertainties related to capital costs as well as future prices of energy carriers, it was further assumed that the electric plasma calcination process would only be selected if it becomes economically competitive compared to conventional lime kiln technology, and in that case, no additional cost for the electric plasma calcination concept is allocated to the cost of achieving negative emissions.
Furthermore, since the electric plasma calcination process results in a pure stream of carbon dioxide, there is no need for further concentration of the CO2 and the total cost for CCS is limited to costs for compressing the CO2 and costs for transport and final storage. These costs, i.e., the additional costs for negative emissions, assuming the electric plasma calcination process is implemented in the mill, are shown in Table 6.
The results show that the costs for achieving negative emissions by capture and storage of CO2 from the electric plasma calcination plant are in the range of 36–60 EUR/tCO2, with lower costs for the larger (market pulp) mill thanks to economies of scale (694,000 adt/a compared to 405,000 adt/a).
These cost levels are clearly lower than other costs reported in literature for negative emissions from pulp and paper mills. For example, Onarheim et al. (2017a) reports costs of avoided emissions ranging from 52 to 66 EUR/tCO2 for a 800,000 adt/a market pulp mill and 71–89 EUR/tCO2 for a 740,000 adt/yr integrated mill (i.e., these mills are comparable in size to the market pulp mill in our study). When considering capture specifically from the lime kiln, they estimated avoidance costs in the order of 73–84 EUR/tCO2. Note, however, that our costs are per ton of CO2 captured and stored, not per ton avoided, since we did not include any emissions associated with the electricity used for compression.
An alternative to permanent storage of captured CO2 is to utilize the captured CO2 in other processes. Kuparinen et al. (2019) discuss several options for carbon capture and utilization (CCU) within the pulp and paper mills and map their potential. For example, they estimate the potential use for tall oil production to 4–6 kg CO2/adt, for production of precipitated calcium carbonate to 20 kg CO2/adt, and for lignin separation to 35 kg CO2/adt (assuming a lignin separation rate of 20%). They conclude that these utilization possibilities are currently small compared to the total capture potential from the mills (e.g., <3% of the capture potential from the recovery boiler). However, compared to the potential capture from the electric plasma calcination process (236 kg CO2/adt), the option of utilizing CO2 for production of precipitated calcium carbonate or for lignin extraction would constitute a more significant share.
High lignin extraction rates significantly reduce the steam production in the recovery boiler and thereby also the generation of electricity in the steam turbines of the mill. Depending on the steam balances of the mills, this loss in steam production might need to be compensated by increased load on the power boiler. However, for energy-efficient market pulp mills, it is likely that the steam production from the recovery boiler will be sufficient to cover the process steam demand also when lignin is extracted. In that case, the loss in electricity generation leads to increased demand for electricity purchased from the grid, in addition to the new demand for electricity to operate the plasma generators.
There could also be opportunities to utilize CO2 for production of electrofuels by combining CO2 with hydrogen from water electrolysis. Also for such opportunities, the potential is expected to be limited to a share of the captured CO2, with the main constraint assumed to be the capacity of the mill's connection to the electricity grid (Jannasch et al., 2019). The potential for reduced emissions through electrofuel production is highly dependent on the carbon intensity of the electricity used for electrolysis, and on what type of fuel is replaced by the electrofuel.
For all potential CCU opportunities, the potential emission reductions depend on what the products (e.g., the lignin, the electrofuel) are used for and what they replace. Since only a fraction of the captured CO2 can be utilized due to other capacity limitations for the aforementioned CCU concepts, the option of CCS to achieve negative emissions becomes highly interesting as the only option with the capacity to handle the entire CO2 flow.
Integration of an electric gas-plasma calcination process with steam slaking in a pulp mill to replace the conventional lime kiln technology would make it possible to eliminate firing fuel to provide the heat necessary for calcination. The results presented in this paper show that it could also reduce the primary steam demand for the rest of the pulp mill processes (by ~10%) by utilizing excess heat from the new process. For an energy-efficient market pulp mill, with the possibility to utilize excess steam in a condensing turbine stage, this translates into a possible increase of the on-site electricity production, thereby slightly dampening the increased demand for electricity for the plasma calcination process. For an integrated pulp and paper mill, the reduced steam demand could make it possible to reduce the steam production in the bark boiler. Whether this is an interesting option or not depends on the market for exporting bark from the mill, and if the corresponding loss in co-generation of electricity is acceptable.
The resulting reduction of greenhouse gas emissions when replacing the lime kiln with the plasma calcination concept depends on whether fossil fuel or biomass is used as a fuel in the existing lime kiln. If fossil fuel is used and electricity is associated with very low emissions, more than 50 kt/a of CO2 emissions can be avoided in the integrated pulp and paper mill investigated in the case study, and almost 100 kt/a in the case study market pulp mill. If biomass is replaced, the electrification will only lead to reduced emissions if the released biomass replaces fossil fuels somewhere else and the electricity used has a low carbon footprint. However, if that is the case, there is great potential to achieve significant emission reductions. The investment cost of the new calcination technology was found to be in the same order of magnitude as the investment cost of the conventional lime kiln, although the risks and uncertainties are significantly more pronounced.
However, the plasma calcination process with steam slaking also offers an opportunity to capture concentrated biogenic CO2 at low costs. In the two studied mills, the capture potentials were 95 and 164 kt/a for the integrated pulp and paper mill, and the market pulp mill, respectively. This way, the emission reduction potential of the electric plasma calcination concept is further improved by combining the electrification strategy with biogenic carbon capture and storage to achieve negative emissions.
The costs estimated for achieving negative emissions by capture and storage of biogenic CO2 from the electric plasma calcination plant range from 36 to 60 EUR/tCO2. These cost levels are clearly lower than other costs reported in literature for negative emissions from pulp and paper mills.
The original contributions presented in the study are included in the article/Supplementary Material, further inquiries can be directed to the corresponding author/s.
HW contributed with the main conceptual idea for the research study. HW and ES discussed and developed the methodology. All authors were involved in the supervision of a master's thesis that contributed with data collection and a first analysis of this data. ES reviewed and updated the data, further extended the analysis, and interpreted the results. SH and HW reviewed and provided critical feedback and helped shape the research, analysis and manuscript. All authors approved the final version of the manuscript.
This work was conducted partly within the project PROCEL Opportunities for decarbonisation of industrial processes through increased electrification which was financed by the Swedish Energy Agency (project number P42221). Additional funding was provided by the Energy Area of Advance at Chalmers University of Technology.
ES was employed at CIT Industriell Energi AB at the time of the study. CIT Industriell Energi AB is a consulting company specializing in knowledge transfer between academia, industry and government agencies, focusing primarily on efficient and sustainable industrial energy use. It is a wholly owned subsidiary to the foundation Chalmers Industriteknik.
The remaining authors declare that the research was conducted in the absence of any commercial or financial relationships that could be construed as a potential conflict of interest.
All claims expressed in this article are solely those of the authors and do not necessarily represent those of their affiliated organizations, or those of the publisher, the editors and the reviewers. Any product that may be evaluated in this article, or claim that may be made by its manufacturer, is not guaranteed or endorsed by the publisher.
Our sincere thanks go to the master's thesis students Elin Andersson and Arvid Skogström whose thesis project is the basis for this work.
The Supplementary Material for this article can be found online at: https://www.frontiersin.org/articles/10.3389/fclim.2021.705032/full#supplementary-material
Akbari, M., Oyedun, A. O., Jain, S., and Kumar, A. (2018). Options for the conversion of pulp and paper mill by-products in Western Canada. Sustain. Energy Technol. Assess. 26, 83–92. doi: 10.1016/j.seta.2017.10.003
Andersson, E., and Skogström, A. (2020). Process Integration of Electric Plasma Calcination in Pulp and Paper Plants Techno-Economic and Greenhouse Gas Emission Assessment Including CO2 Utilisation Options. [master's thesis]. Göteborg: Chalmers University of Technology.
Beyond Zero Emissions (2018). Electrifying Industry – Zero Carbon Industry Plan. Melbourne: Beyond Zero Emissions.
Bjotveit, S., Gordon, A., Ohlsson, K., Rutqvist, E., Williamsson, E., Westermark, M., et al. (2003). Förstudie: Eldriven kalcinering. Stockholm: Kungliga Tekniska Högskolan.
de Blasio, C. (2019). “Integrated biorefinery concepts,” in Fundamentals of Biofuels Engineering and Technology, ed C. de Blasio (Switzerland: Springer), 155–171.
Eurostat (2019). Electricity Prices for Non-household Consumers. Available online at: https://ec.europa.eu/eurostat/databrowser/view/NRG_PC_205__custom_726575/default/table?lang=en (accessed March 24, 2021).
Garðarsdóttir, S. Ó., Normann, F., Skagestad, R., and Johnsson, F. (2018). Investment costs and CO2 reduction potential of carbon capture from industrial plants – A Swedish case study. Int. J. Greenhouse Gas Control 76, 111–124. doi: 10.1016/j.ijggc.2018.06.022
Glader, K. (2011). Measures for increased energy efficiency at Iggesund mill: Pinch analysis of the pulp production lines at a paperboard mill. [master's thesis]. Göteborg: Chalmers University of Technology.
Hansson, J., Hackl, R., Taljegard, M., Brynolf, S., and Grahn, M. (2017). The potential for electrofuels production in sweden utilizing fossil and biogenic CO2 point sources. Front. Energy Res. 5:4. doi: 10.3389/fenrg.2017.00004
Hektor, E., and Berntsson, T. (2007). Future CO2 removal from pulp mills - Process integration consequences. Energy Conv. Manage. 48, 3025–3033. doi: 10.1016/j.enconman.2007.06.043
Hektor, E., and Berntsson, T. (2009). Reduction of greenhouse gases in integrated pulp and paper mills: possibilities for CO2 capture and storage. Clean Technol. Environ. Policy 11, 59–65. doi: 10.1007/s10098-008-0166-3
Jackson, S., and Brodal, E. (2019). Optimization of the energy consumption of a carbon capture and sequestration related carbon dioxide compression processes. Energies 12:1603. doi: 10.3390/en12091603
Jafri, Y., Wetterlund, E., Mesfun, S., Rådberg, H., Mossberg, J., Hulteberg, C., et al. (2020). Combining expansion in pulp capacity with production of sustainable biofuels – Techno-economic and greenhouse gas emissions assessment of drop-in fuels from black liquor part-streams. Appl. Energy 279:115879. doi: 10.1016/j.apenergy.2020.115879
Jannasch, A.-K., Pihl, H., Wolf, J., Lindström, R., Ahlroth, M., Schönström, J., et al. (2019). Integration of the Electro-Fuel Concept in Pulp and Paper Industry for a Future Electricity System in Balance and a Sustainable Energy System With Minimal Carbon Foot Print. Lund: RISE Research Institutes of Sweden.
Johnsson, F., Normann, F., and Svensson, E. (2020). Marginal abatement cost curve of industrial CO2 capture and storage – A Swedish case study. Front. Energy Res. 8:175. doi: 10.3389/fenrg.2020.00175
Jönsson, J., and Berntsson, T. (2012). Analysing the potential for implementation of CCS within the European pulp and paper industry. Energy 44, 641–648. doi: 10.1016/j.energy.2012.05.028
Jönsson, J., Pettersson, K., Berntsson, T., and Harvey, S. (2013). Comparison of options for utilization of a potential steam surplus at kraft pulp mills-Economic performance and CO2 emissions. Int. J. Energy Res. 37, 1017–1035. doi: 10.1002/er.2905
Kemp, I. (2006). Pinch Analysis and Process Integration: A User Guide on Process Integration for the Efficient Use of Energy. 2nd ed. Oxford: Butterworth-Heinemann (Elsevier).
Klemeš, J. J. (2013). Handbook of Process Integration: Minimisation of Energy and Water Use, Waste and Emissions. Cambridge: Woodhead Publishing.
Kuparinen, K., and Vakkilainen, E. (2017). Green pulp mill: renewable alternatives to fossil fuels in lime kiln operations. BioResources 12, 4031–4048. doi: 10.15376/biores.12.2.4031-4048
Kuparinen, K., Vakkilainen, E., and Tynjäl,ä, T. (2019). Biomass-based carbon capture and utilization in kraft pulp mills. Mitigat. Adapt. Strateg. Glob. Change 24, 1213–1230. doi: 10.1007/s11027-018-9833-9
LimeArc Process AB. (2021). LimeArc. Available online at: https://limearcprocess.se/ (accessed March 17, 2021).
Lundqvist, R. (2008). Ångsläckning av kalk - kinetik och teknik. Stockholm: Värmeforsk - Skogsindustriella programmet.
Material Economics. (2020). A Net-Zero Transition for EU Industry: What Does It Mean for the Pulp & Paper Industry? Stockholm: Material Economics.
McGrail, B. P., Freeman, C. J., Brown, C. F., Sullivan, E. C., White, S. K., Reddy, S., et al. (2012). Overcoming business model uncertainty in a carbon dioxide capture and sequestration project: case study at the Boise White Paper Mill. Int. J. Greenhouse Gas Control 9, 91–102. doi: 10.1016/j.ijggc.2012.03.009
Möllersten, K., Gao, L., and Yan, J. (2006). CO2 capture in pulp and paper mills: CO2 balances and preliminary cost assessment. Mitigat. Adapt. Strateg. Global Change 11, 1129–1150. doi: 10.1007/s11027-006-9026-9
Möllersten, K., Yan, J., and Westermark, M. (2003). Potential and cost-effectiveness of CO2 reductions through energy measures in Swedish pulp and paper mills. Energy 28, 691–710. doi: 10.1016/S0360-5442(03)00002-1
Nwaoha, C., and Tontiwachwuthikul, P. (2019). Carbon dioxide capture from pulp mill using 2-amino-2-methyl-1-propanol and monoethanolamine blend: Techno-economic assessment of advanced process configuration. Appl. Energy 250, 1202–1216. doi: 10.1016/j.apenergy.2019.05.097
Olsson, D. (2020). Optimering av kalkcykeln på Iggesunds bruk med avseende på specifik energianvändning. [master's thesis]. Uppsala: SLU, Institutionen för energi och teknik.
Onarheim, K., Santos, S., Kangas, P., and Hankalin, V. (2017a). Performance and cost of CCS in the pulp and paper industry part 2: economic feasibility of amine-based post-combustion CO2 capture. Int. J. Greenhouse Gas Control 66, 60–75. doi: 10.1016/j.ijggc.2017.09.010
Onarheim, K., Santos, S., Kangas, P., and Hankalin, V. (2017b). Performance and costs of CCS in the pulp and paper industry part 1: performance of amine-based post-combustion CO2 capture. Int. J. Greenhouse Gas Control 59, 58–73. doi: 10.1016/j.ijggc.2017.02.008
Pedersén, A., and Larsson, A. (2017). Energy Efficiency Study at a Softwood Kraft Pulp Mill. [master's thesis]. Göteborg: Chalmers University of Technology.
Pettersson, K., Axelsson, E., Eriksson, L., Svensson, E., Berntsson, T., and Harvey, S. (2020). Holistic methodological framework for assessing the benefits of delivering industrial excess heat to a district heating network. Int. J. Energy Res. 44, 2634–2651. doi: 10.1002/er.5005
Reichenberg, L., Hedenus, F., Odenberger, M., and Johnsson, F. (2018). The marginal system LCOE of variable renewables – Evaluating high penetration levels of wind and solar in Europe. Energy 152, 914–924. doi: 10.1016/j.energy.2018.02.061
Rootzén, J., Kjärstad, J., Johnsson, F., and Karlsson, H. (2018). “Deployment of BECCS in basic industry - a Swedish case study,” in International Conference on Negative CO2 Emissions, May 22-24 2018, 1–13.
Santos, M. P. S., Manovic, V., and Hanak, D. P. (2021). Unlocking the potential of pulp and paper industry to achieve carbon-negative emissions via calcium looping retrofit. J. Clean. Prod. 280:124431. doi: 10.1016/j.jclepro.2020.124431
Svensson, E., Morandin, M., and Harvey, S. (2019). Characterization and visualization of industrial excess heat for different levels of on-site process heat recovery. Int. J. Energy Res. 43, 7988–8003. doi: 10.1002/er.4787
Swedish Energy Agency (2019). Wood Fuel and Peat Prices. Available online at: https://pxexternal.energimyndigheten.se/pxweb/en/Trädbränsle-ochtorvpriser/-/EN0307_2.px/table/tableViewLayout2/ (accessed January 10, 2020).
Swing Gustafsson, M. (2013). Industrial Excess Heat for District Heating Comparison of Potentials From Top-Down and Bottom-Up Studies for Energy-Intensive Process Industries. [master's thesis]. Göteborg: Chalmers University of Technology.
Keywords: industrial electrification, pulp and paper, negative emissions, calcination, CO2 capture and storage (CCS)
Citation: Svensson E, Wiertzema H and Harvey S (2021) Potential for Negative Emissions by Carbon Capture and Storage From a Novel Electric Plasma Calcination Process for Pulp and Paper Mills. Front. Clim. 3:705032. doi: 10.3389/fclim.2021.705032
Received: 04 May 2021; Accepted: 16 September 2021;
Published: 13 October 2021.
Edited by:
Anna Skorek-Osikowska, Silesian University of Technology, PolandReviewed by:
Stefano Stendardo, Energy and Sustainable Economic Development (ENEA), ItalyCopyright © 2021 Svensson, Wiertzema and Harvey. This is an open-access article distributed under the terms of the Creative Commons Attribution License (CC BY). The use, distribution or reproduction in other forums is permitted, provided the original author(s) and the copyright owner(s) are credited and that the original publication in this journal is cited, in accordance with accepted academic practice. No use, distribution or reproduction is permitted which does not comply with these terms.
*Correspondence: Simon Harvey, c2ltb24uaGFydmV5QGNoYWxtZXJzLnNl
Disclaimer: All claims expressed in this article are solely those of the authors and do not necessarily represent those of their affiliated organizations, or those of the publisher, the editors and the reviewers. Any product that may be evaluated in this article or claim that may be made by its manufacturer is not guaranteed or endorsed by the publisher.
Research integrity at Frontiers
Learn more about the work of our research integrity team to safeguard the quality of each article we publish.