- School of Environmental Science and Engineering, Jiangsu Key Laboratory of Atmospheric Environment Monitoring and Pollution Control, Jiangsu Collaborative Innovation Center of Atmospheric Environment, Nanjing University of Information Science and Technology, Nanjing, Jiangsu, China
Rational reusing the waste materials in spent batteries play a key role in the sustainable development for the future lithium-ion batteries. In this work, we propose an effective and facile solid-state-calcination strategy for the recycling and regeneration of the cathode materials in spent LiNi0.5Co0.2Mn0.3O2 (NCM523) ternary lithium-ion batteries. By systemic physicochemical characterizations, the stoichiometry, phase purity and elemental composition of the regenerated material were deeply investigated. The electrochemical tests confirm that the material characteristics and performances got recovered after the regeneration process. The optimal material was proved to exhibit the excellent capacity with a discharge capacity of 147.9 mAh g−1 at 1 C and an outstanding capacity retention of 86% after 500 cycles at 1 C, which were comparable to those of commercial NCM materials.
1 Introduction
Since the commercialization in 1990s, lithium-ion batteries (LIB) are popular in the fields of consumer electronics, energy storage systems and electric vehicles (EVs), due to the high energy density, long cycle life and flexible dimensions. Driven by the fast development of EVs in this decade, the LIB market demand has been rapidly expanding, and is expected to drastically rise to 87.5 billion dollars in 2027 (Li et al., 2021). In the LIBs market, the most widely used cathode materials are LiFePO4 (LFP) and ternary material LiNixCoyMnzO2, (NCM). With the rapid popularization of EVs in the global world, large numbers of LIBs have come into service. However, the power LIBs have only a limited service life of 8–10 years for the EVs (Dinger et al., 2010). It is worth mentioning that the NCM batteries dominate the powder battery market of EVs before 2021. Therefore, in the next 10 years, large amounts of NCM-type LIBs will get retired from the EVs. On the one hand, the abandonment of these LIBs will seriously pollute the ecological environment. Especially, the cathode materials in NCM batteries contain lots of metals such as Ni, Co, Mn, which are harmful to water, atmosphere and soil. On the other hand, the LIB industry is facing a crisis of resource shortage, because the overuse of the valuable Li, Ni Co, and Mn in the past decade, which are needed to be recycled (Roy et al., 2022). Therefore, clean and efficient recovery technologies are needed for sustainable development of LIBs.
Lots of efforts have been devoted to recycling the spent NCM LIBs. The hydrometallurgical process is currently the most general strategy, including a pre-treatment process, leaching process and the recovery process of the constituent metals (Kim et al., 2021). The pre-treatment process mainly aims at detaching the active materials from the collector, usually including discharging, dismantling, separating, etc. Yao et al. (2018). After the pre-treatment process, a leaching approach was carried out to transform the constituent elements into the metallic ions. The last step is getting the relevant metallic compounds from the leaching solutions, usually through the ways of evaporation, designed precipitation reactions, electrodeposition, new-type chemical reaction, etc. Gao et al. (2018), Gupta et al. (2022), Grima-Carmena et al. (2023), Gu et al. (2023), Ilyas et al. (2023), Qu et al. (2024).
The above recovery method is actually to enrich and separate the metal elements from the leaching solution through precipitation or extraction, and then to recycle them in the form of metal compounds (Jin et al., 2022). However, due to the similar chemical properties of Ni, Co, Mn ions, it is difficult to separate them, which need more procedures to get the pure products. Afterwards, the resultant metallic compounds are further used as the precursors for the synthesis of new ternary lithium materials. Obviously, these traditional ways are time-consuming and energy-intensive.
Therefore, directly regenerating valuable metals from the leaching solution into ternary lithium cathode materials is more attractive, which is thought to be an economic and efficient recycling method, maximizing the recovery value. In these years, some new strategies have been proposed by the scientists to simplify the recycling process of spent LIBs and to improve the economic benefit. Bai et, al. reported a novel leaching and precipitating system in waste NCM materials of LIBs, efficiently obtaining the Ni, Co, Mn and Li intermediates, which can be used to regenerate the NCM cathode material (Bai et al., 2023). He et al made use of the deep eutectic solvents (DESs) to leach the metal components from spent NCM LIBs. The resultant leaching solution was subjected to a co-precipitation reaction and high-temperature calcination, getting the regenerated LiNi0.5Co0.2Mn0.3O2 material (He et al., 2023). These reported works inspired us to directly regenerate the NCM material from the spent LIBs. However, there are several problems needed to be solved, such as high lost, complicated steps and deficient purity (Xiao et al., 2019; Zhou et al., 2024). Extracting the Ni, Co, Mn and Li from the spent NCM materials and efficiently transforming them into regenerated NCM materials by the designed stoichiometric ratio is not easy to realize. Another problem is the insufficient performance of the generated NCM materials compared with that of commercial new counterpart (He et al., 2023), thus hindering the wide applications.
In this work, a facile synthesis approach was developed to regenerate the ternary LiNi0.5Co0.2Mn0.3O2 (NCM523) material from the leaching solution of spent cathode materials. By treating the waste NCM523 powders with organic acid, we obtain the leaching solution of metal ions. The solid precursor was obtained by subjecting the leaching solution to a precipitation process. The precipitates were directly used as the precursors of synthesizing the regenerated NCM523 material with a solid-state calcination method. The regenerated products were proved to possess the same constitutes, properties and nice electrochemical performances compared to the commercial NCM materials.
2 Experiment
2.1 Pretreatment
The waste NCM battery were put into a saturated salt solution to get completely discharged and then manually disassembled in an argon-filled glove box. The NCM powders could be peeled from the cathode plate by ultrasonic treatment in water. The powders were further calcined in the muffle furnace at 650°C to remove the PVDF and conductive carbon. Afterwards, the NCM powders were leached with a mixture of formic acid (2 vol%) and citric acid (0.5 mol/L). After filtration, the leaching solution was obtained.
2.2 Regeneration
In order to get the metallic precursor, 0.55 mol/L oxalic acid solution was used as the precipitant adding into the leaching solution, which was further aged at 50°C. The precipitates were possessed after a filtration process and then dried at 80°C overnight to obtain the ternary metal oxalate compounds. The as-prepared metal oxalate compounds were mixed with a certain proportion of lithium carbonate by ball milling and were used as the precursor of the regenerated NCM materials. At last, the mixture was calcined in the furnace, with the first heating temperature of 500°C for 5 h, and the second heating temperature for 12 h at a ramping rate of 5°C min-1. After natural cooling, we can get the regenerated NCM523 cathode material, noted as R-NCM-X, where X represents the heating temperature. If not noted, R-NCM refers to R-NCM-850.
2.3 Battery assembly and electrochemical measurements
The cathode electrodes were made up of active material powder, PVDF and conductive carbon (Ketjen Black), coated on aluminum foil with the mass ratio of 8:1:1. The electrochemical performances were tested in the CR2032 coin-type half cells using the Li disc as the anode, 1 M LiPF6 in EC/DEC (1:1 vol%) as the electrolyte and a Celegard 2400 membrane as the separator. Cyclic voltammetry (CV) and electrochemical impedance spectra (EIS) were conducted on the electrochemical workstation (CHI 760E). The EIS spectra were recorded with an amplitude of 5 mV in the frequency range from 0.01 Hz to 100000 Hz.
3 Results and discussions
The recycling process for spent NCM ternary batteries is schematically demonstrated in Scheme 1. A lifecycle of the NCM battery starts from a newly produced battery, which come into retirement after long-time charge and discharge cycles. The spent battery was subjected to the pretreatment to get the spent NCM cathode powders. After the acid leaching, the metallic solution containing Li, Ni, Co, Mn ions were possessed.
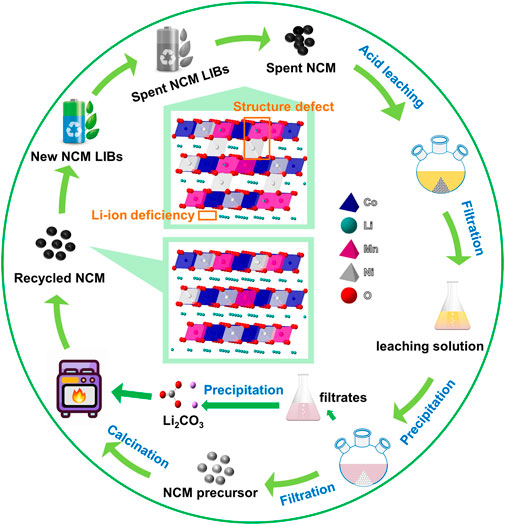
Scheme 1. The schematic illustration of the regeneration process for spent NCM ternary cathode materials.
The regeneration process starts from a precipitation reaction as shown in Eq. (1), with the oxalic acid solution as the precipitant to acquire the ternary metallic precursor:
After acid leaching, the resultant immersion solution was subjected to a co-precipitation reaction for 18 h by adding 0.55 mol/L oxalic acid solution. The ternary metal ions were transformed from the immersion solution into metal−oxalate salts (MC2O4∙2H2O, M = Ni, Co and Mn) (Refly et al., 2020). After filtration, we can obtain the precipitated product PNCM-18h, which was further used as the precursor of the calcination process. In addition, the filtrate can be used to get lithium carbonate (Li2CO3) by adding the Na2CO3 solution as the precipitant. The SEM images of PNCM-18 h in Supplementary Figure S1A and Supplementary Figure S1B reproduce the typical morphology of α-oxalate crystal, which was also reported in the related works (Cho et al., 2006; Park et al., 2010; Zhang et al., 2018). Supplementary Figure S1C displays the digital photo of the precipitate with a color of light green, due to the relatively high content of Ni in the NCM523 material. XRD was conducted on the precipitated product PNCM-18h, as shown in Supplementary Figure S2, in which the characteristic diffraction peaks can be indexed to the standard PDF card of oxalate dihydrate (PDF#25-0582). The inset of Supplementary Figure S2 provides the elemental analysis through the selected-area EDS scanning, equipped with the SEM. It indicates that Ni, Co and Mn elements co-exists in the precipitated oxalate with the atomic ratio of 9.28%, 3.48% and 6.04%, close to the original ratio of 5:2:3 in NCM523 material. This result proves that the oxalic acid solution can be used as the precipitant of Ni, Co and Mn.
For the regeneration of NCM, lithium carbonate (Li2CO3) was added into the mixture of metal−oxalate salts, followed with a solid-sate high-temperature calcination process. Before the calcination process, the element contents of Ni, Co, Mn, Li were measured by ICP, in order to make sure the dosage of the necessary element additive, thus restoring the elementary composition of the spent NCM to the pristine NCM. During the calcination process, the ternary precursor PNCM-18 h reacts with Li2CO3 to form LiMO2, the calcination process of which is as shown in Eq. (2).
In order to analyze the crystalline structure, XRD was performed for commercial ternary new material N-NCM, regenerated ternary material R-NCM, and the pretreated waste ternary material S-NCM, with their patterns in Figure 1. The characteristic diffraction peaks of R-NCM and N-NCM in Figure 1A are consistent with the standard PDF card (PDF#70-4314), indicating a typical hexagonal
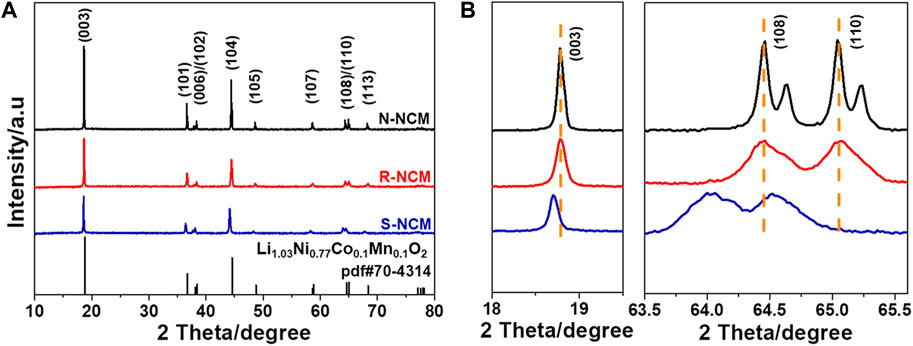
Figure 1. (A) XRD patterns of N-NCM, R-NCM and S-NCM; (B) magnified patterns in the ranges of 18.0°–19.5° and 64.0°–65.7°.
In order to visualize the morphology and elemental distribution before and after regeneration, scanning electron microscopy (SEM) and EDS spectroscopy (EDS) tests were carried out on N-NCM, R-NCM and S-NCM, as shown in Figure 2. Figures 2A,B show the SEM images of N-NCM with smooth surface. The SEM images of S-NCM were shown in Figures 2C,D showing that the particle shape in the S-NCM becomes irregular and there are obvious cracks on the surface of the particles. This kind of surface structure change is probably ascribed to reiterative intercalation and de-intercalation of Li ions during the long-term discharge and charge process. However, in the R-NCM (Figures 2E,F), the surface becomes smooth and basically free of cracks. Therefore, the structure and the surface morphology of R-NCM was reconstructed through the regeneration process.
In order to further investigate the crystal structure of the regenerated material, high-resolution transmission electron microscopy (HRTEM) was carried out on the sample R-NCM, and the results are shown in Supplementary Figure S3. From Supplementary Figure S3A, the particle size of the regenerated material is around 0.5–1 μm. In Supplementary Figure S3B, it can be seen that the particles of the regenerated material displayed orderly lattice stripes, which indicates that the regenerated sample has a high degree of crystallinity, which is in line with the results of the XRD. In addition, the interplanar crystal spacing of R-NCM is calculated to be 0.48 nm, which is corresponded to the strongest diffraction peak of (003) crystal plane in the relative ternary NCM material (Zhang et al., 2019). EDS surface scanning was used to analyze the energy spectrum and elemental content of N-NCM, R-NCM and S-NCM, with the results shown in Supplementary Figure S4. The EDS analysis results show that all of three samples contain the major elements of O, Ni, Co, Mn and other elements such as C, F and Cu. According to the atomic percentages in the inset tables, the Ni: Co: Mn ratios of the materials are calculated as 0.46: 0.21: 0.32 for N-NCM, 0.46: 0.21: 0.33 for R-NCM and 0.44: 0.22: 0.34 for S-NCM, indicating that the elemental ratio of R-NCM is close to that of N-NCM. As can be seen from the EDS mapping scan in Supplementary Figure S5, the Ni, Co and Mn elements in R-NCM are uniformly distributed. In addition, there are no obvious changes in the elemental distribution of N-NCM, R-NCM and S-NCM. These results indicate that the contents of Ni, Co, Mn are steady but we need to care more about the content of Li. In order to measure the elemental contents of the three materials more accurately, the Li, Ni, Co and Mn contents in the materials were measured using an ICP-OES instrument, and the elemental molar ratios were further obtained. The results are shown in Table 2, which can be utilized as the basis of element complement. From Table 2, we can find that the contents of Ni, Co and Mn are stable, with no need of complement. However, S-NCM lost about 22% of Li, which may be caused by the irreversible reaction during long-term charging and discharging (Fan et al., 2020). Obviously, the regenerated sample R-NCM has regained the missing lithium, whose lithium content is higher than that in N-NCM. In addition, the content of Ni, Co, Mn in R-NCM can be accurately measured to be 0.497: 0.205: 0.298, which is very close to the ratio of 5: 2: 3.
X-ray photoelectron spectroscopy (XPS) was used to study the chemical valence states of C, O, Ni, Co and Mn on the surfaces of N-NCM, R-NCM and S-NCM, with the results shown in Figure 3. The survey spectrum of in Figure 3A shows that the three samples consist of Ni, Co Mn, C, and O. The C 1s spectrum of Figure 3B can be divided into three corresponding peaks CO32- (288.8 eV), C=O (286.5 eV) and C-C (284.8 eV) (Huang et al., 2019). The peak areas of the three peaks for CO32- (288.8 eV) are calculated to be 11.6%, 10.9% and 13.3%, respectively. The O 1s spectrum of Figure 3C can be fitted into two peaks, including impurity oxygen (531.9 eV, 533.3 eV) and lattice oxygen (529.5 eV), respectively (Liu et al., 2007; Chen et al., 2015), where the impurity oxygen is mainly ascribed to the impurity layer, from the adsorbed hydroxyl and carbonate species. The lattice oxygen is the O2- in M-O (288.8 eV) (M = Ni, Co, Mn) bonds of NCM material (Liu et al., 2013). It is clear that the percentage of impurity oxygen in R-NCM is lower than that of the S-NCM, but still higher than of that of N-NCM, indicating the existing difference between R-NCM and N-NC. The XPS spectra of Ni 2p are shown in Figure 3D. The binding energy peaks of Ni 2p3/2 and 2p1/2 are around 854.2 and 873.3 eV, respectively, and the satellite peaks are located at 861 eV and 879.1 eV, respectively (Li et al., 2014). The Ni 2p3/2 peaks can be split into two fitted peaks, i.e., Ni2+ (854.6 eV) and Ni3+ (855.7 eV). We can find by peak area calculation that the Ni2+/Ni3+ value of R-NCM is lower than that of S-NCM, but similar to that of N-NCM, indicating the lower content of Ni3+ in S-NCM. It is known that the Ni3+ is favorable to reduce the cation mixing and improve the electrochemical performance (Zhang et al., 2018). The XPS spectra of Co 2p are shown in Figure 3E, in which the binding energy peaks at around 780.0 eV and 795.1 eV are corresponded to Co 2p3/2 and 2p1/2 species for Co3+ (Hao et al., 2019). It is found that the Co 2p XPS spectra of the three samples were basically not different. Figure 3F shows the XPS spectra of Mn 2p. The fitted peaks at 642.3 eV and 654.2 eV correspond to Mn4+, and the fitted peaks at 640.9 eV and 652.8 eV correspond to Mn3+ (Deng et al., 2020). The presence of Mn3+ in S-NCM is due to the transition from a layered structure to a spinel structure, probably to compensate the change of charge. In addition, the signal of Mn3+ decrease in R-NCM, which is similar structure to N-NCM.
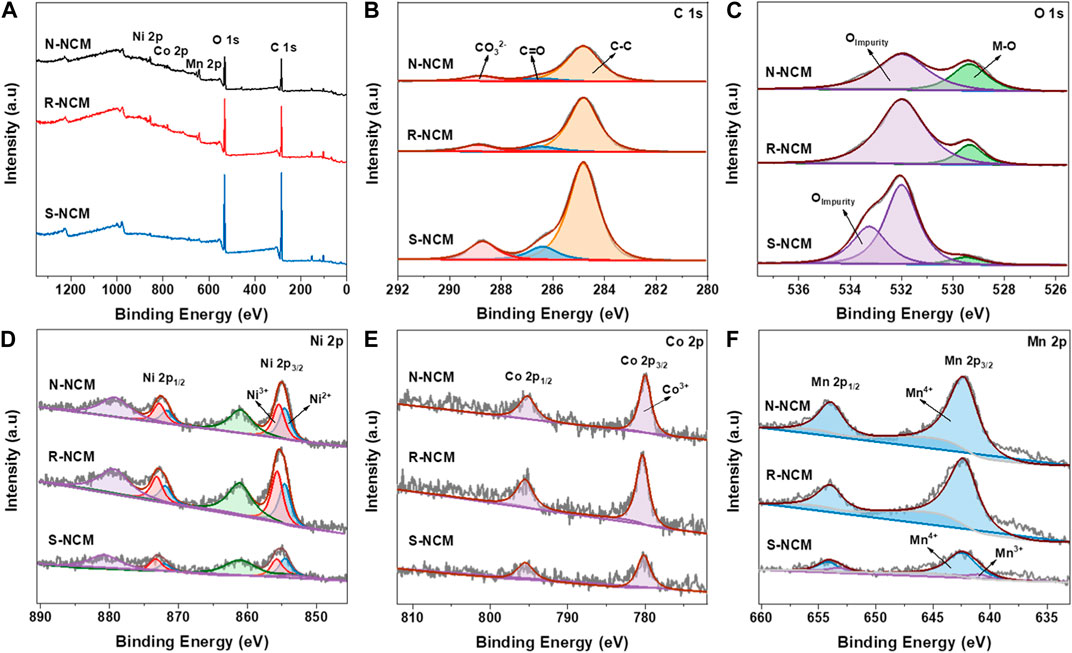
Figure 3. XPS spectra of N-NCM, R-NCM and S-NCM. (A) Survey scan; (B) C 1s spectra; (C) O 1s spectra; (D) Ni 2p spectra; (E) Co 2p spectra; (F) Mn 2p spectra.
In order to testify the effectivity of the regeneration process for the spent NCM materials, N-NCM, R-NCM and S-NCM were used as the cathode materials to assemble the 2032-type coin cells for the electrochemical performance evaluation. As shown in Figure 4, the batteries based on the three materials were charged and discharged at the voltage range of 2.5–4.3 V. Figure 4A shows the first-round charge/discharge curve of the battery at the rate of 0.1 C. The discharge curve of S-NCM is obviously steeper and the voltage plateau is relatively low. In addition, the charge/discharge specific capacity is lower, which is partly due to the loss of lithium, the change of crystalline structure and the surface transition during the long-term cycling process. The charge/discharge curves of R-NCM are longer and smoother than those of S-NCM, but very close to those of N-NCM. The discharge specific capacity of the R-NCM is 168.6 mAh
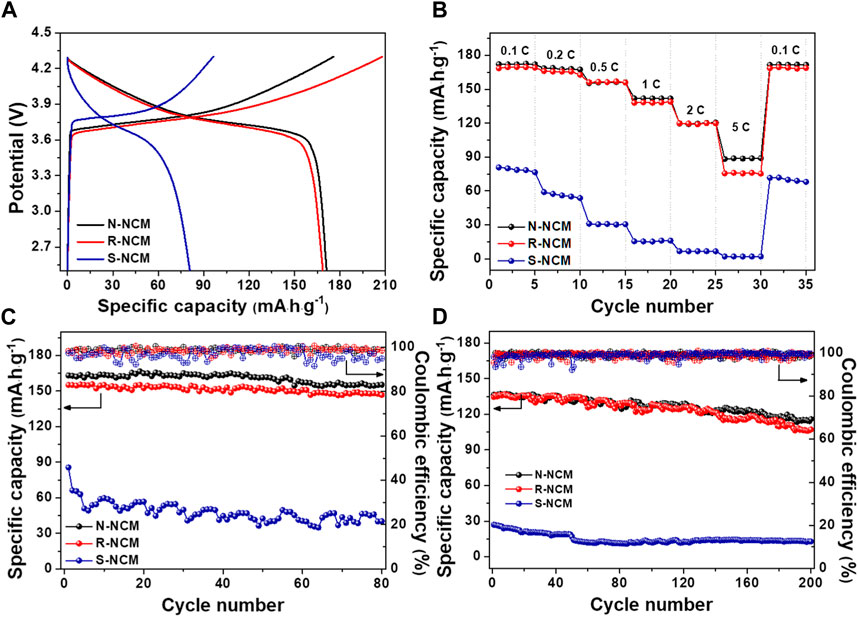
Figure 4. The battery performances for N-NCM, R-NCM and S-NCM. (A) First charge/discharge curves at 0.1 C; (B) discharge performance at different rates; (C) cycle performance and Coulombic efficiency at 0.2 C for 80 cycles; (D) cycle performance and Coulombic efficiency at 1 C for 200 cycles.
To further investigate the kinetic properties and redox processes of the samples before and after regeneration, cyclic voltammetry (CV) tests were performed on N-NCM, R-NCM and S-NCM. Supplementary Figures S7A–C show the CV curves for the three materials in the voltage range of 2.5–4.3 V at a sweep rate of 0.1 mV
4 Conclusion
In a summary, an effective and facile solid-state-calcination strategy was developed to regenerate the waste NCM cathode materials in spent LIBs. The regenerated material was characterized by physicochemical characterizations, confirming that the hexagonal α-NaFeO2-type layered structure was recovered and the elementary constitute resorted to the pristine state. Due to recovery in material properties, the regenerated material can possess excellent electrochemical performance, very close to that of commercial NCM. This kind of method is easy to enlarge production for the industrial recycling of spent NCM LIBs.
Data availability statement
The raw data supporting the conclusions of this article will be made available by the authors, without undue reservation.
Author contributions
CY: Data curation, Investigation, Writing–original draft. YH: Formal Analysis, Writing–review and editing. JW: Data curation, Writing–review and editing. MZ: Data curation, Methodology, Writing–review and editing. JQ: Project administration, Writing–review and editing. LS: Funding acquisition, Methodology, Supervision, Writing–review and editing.
Funding
The author(s) declare that financial support was received for the research, authorship, and/or publication of this article. This work was supported by the fund of Natural Science Foundation of Jiangsu Province (BK20210651). Meanwhile, this work was also supported by Jiangsu Joint Laboratory of Atmospheric Pollution Control, and Jiangsu Engineering Technology Research Center of Environmental Cleaning Materials. CY is funded by the NUIST Students’ Platform for Innovation and Entrepreneurship Training Program (202310300027Z).
Conflict of interest
The authors declare that the research was conducted in the absence of any commercial or financial relationships that could be construed as a potential conflict of interest.
Publisher’s note
All claims expressed in this article are solely those of the authors and do not necessarily represent those of their affiliated organizations, or those of the publisher, the editors and the reviewers. Any product that may be evaluated in this article, or claim that may be made by its manufacturer, is not guaranteed or endorsed by the publisher.
Supplementary material
The Supplementary Material for this article can be found online at: https://www.frontiersin.org/articles/10.3389/fchem.2024.1400758/full#supplementary-material
References
Bai, X., Jiang, Z., Sun, Y., Liu, X., Jin, X., He, R., et al. (2023). Clean universal solid-state recovery method of waste lithium-ion battery ternary positive materials and their electrochemical properties. ACS Sustain. Chem. Eng. 11, 3673–3686. doi:10.1021/acssuschemeng.2c06630
Chen, Q., Du, C., Qu, D., Zhang, X., and Tang, Z. (2015). Synthesis and characterization of Zr-doped LiNi0.4Co0.2Mn0.4O2 cathode materials for lithium ion batteries. RSC Adv. 5, 75248–75253. doi:10.1039/c5ra14376d
Chen, Z., Liu, Y., Lu, Z., Hu, R., Cui, J., Xu, H., et al. (2019). Plasma-assisted coating of nanosized SnO2 on LiNi0.5Co0.2Mn0.3O2 cathodes for enhanced cyclic stability of lithium-ion batteries. J. Alloys Compd. 803, 71–79. doi:10.1016/j.jallcom.2019.06.281
Cho, T.-H., Shiosaki, Y., and Noguchi, H. (2006). Preparation and characterization of layered LiMn1/3Ni1/3Co1/3O2 as a cathode material by an oxalate co-precipitation method. J. Power Sources 159, 1322–1327. doi:10.1016/j.jpowsour.2005.11.080
Deng, B., Zhou, Z., Wang, W., and Wang, D. (2020). Direct recovery and efficient reutilization of degraded ternary cathode materials from spent lithium-ion batteries via a homogeneous thermochemical process. ACS Sustain. Chem. Eng. 8, 14022–14029. doi:10.1021/acssuschemeng.0c03989
Dinger, A., Martin, R., Mosquet, X., Rabl, M., Rizoulis, D., Russo, M., et al. (2010). Batteries for electric cars – challenges, opportunities, and the outlook to 2020, 1–18.
Fan, E., Yang, J., Huang, Y., Lin, J., Arshad, F., Wu, F., et al. (2020). Leaching mechanisms of recycling valuable metals from spent lithium-ion batteries by a malonic acid-based leaching system. ACS Appl. Energy Mater. 3, 8532–8542. doi:10.1021/acsaem.0c01166
Gao, W., Song, J., Cao, H., Lin, X., Zhang, X., Zheng, X., et al. (2018). Selective recovery of valuable metals from spent lithium-ion batteries–Process development and kinetics evaluation. J. Clean. Prod. 178, 833–845. doi:10.1016/j.jclepro.2018.01.040
Grima-Carmena, L., Oyonarte-Andrés, S., Giner-Sanz, J. J., García-Gabaldón, M., Bosch-Mossi, F., and Pérez-Herranz, V. (2023). Statistical analysis of the effect of the electrochemical treatment and the acid concentration on the leaching of NMC cathodes from spent Li-ion batteries. J. Environ. Chem. Eng. 11, 110423. doi:10.1016/j.jece.2023.110423
Gu, K., Gao, X., Chen, Y., Qin, W., and Han, J. (2023). Closed-loop recycling of spent lithium-ion batteries based on selective sulfidation: an unconventional approach. Waste Manag. 169, 32–42. doi:10.1016/j.wasman.2023.06.027
Gupta, S., Pant, K. K., and Corder, G. (2022). An environmentally benign closed-loop process for the selective recovery of valuable metals from industrial end-of-life lithium-ion batteries. Chem. Eng. J. 446, 137397. doi:10.1016/j.cej.2022.137397
Hao, J., Yu, Z., Liu, H., Song, W., Liu, J., Kong, L., et al. (2019). Enhancing electrochemical performances of LiNi0.5Co0.2Mn0.3O2 cathode materials derived from NiF2 artificial interface at elevated voltage. J. Alloys Compd. 806, 814–822. doi:10.1016/j.jallcom.2019.07.349
He, T., Dai, J., Dong, Y., Zhu, F., Wang, C., Zhen, A., et al. (2023). Green closed-loop regeneration of ternary cathode materials from spent lithium-ion batteries through deep eutectic solvent. Ionics 29, 1721–1729. doi:10.1007/s11581-023-04967-3
Huang, B., Liu, D., Qian, K., Zhang, L., Zhou, K., Liu, Y., et al. (2019). A simple method for the complete performance recovery of degraded Ni-rich LiNi0.70Co0.15Mn0.15O2 cathode via surface reconstruction. ACS Appl. Mater. Interfaces 11, 14076–14084. doi:10.1021/acsami.8b22529
Ilyas, S., Srivastava, R. R., and Kim, H. (2023). Cradle-to-cradle recycling of spent NMC batteries with emphasis on novel Co2+/Ni2+ separation from HCl leached solution and synthesis of new ternary precursor. Process Saf. Environ. Prot. 170, 584–595. doi:10.1016/j.psep.2022.12.045
Jin, Y., Zhang, T., and Zhang, M. (2022). Advances in intelligent regeneration of cathode materials for sustainable lithium-ion batteries. Adv. Energy Mater. 12, 2201526. doi:10.1002/aenm.202201526
Kim, K., Raymond, D., Candeago, R., and Su, X. (2021). Selective cobalt and nickel electrodeposition for lithium-ion battery recycling through integrated electrolyte and interface control. Nat. Commun. 12, 6554. doi:10.1038/s41467-021-26814-7
Li, J., Fleetwood, J., Hawley, W. B., and Kays, W. (2021). From materials to cell: state-of-the-art and prospective technologies for lithium-ion battery electrode processing. Chem. Rev. 122, 903–956. doi:10.1021/acs.chemrev.1c00565
Li, L., Zhang, X., Chen, R., Zhao, T., Lu, J., Wu, F., et al. (2014). Synthesis and electrochemical performance of cathode material Li1.2Co0.13Ni0.13Mn0.54O2 from spent lithium-ion batteries. J. Power Sources 249, 28–34. doi:10.1016/j.jpowsour.2013.10.092
Liu, H., Yang, Y., and Zhang, J. (2007). Reaction mechanism and kinetics of lithium ion battery cathode material LiNiO2 with CO2. J. Power Sources 173, 556–561. doi:10.1016/j.jpowsour.2007.04.083
Liu, W., Hu, G., Du, K., Peng, Z., and Cao, Y. (2013). Enhanced storage property of LiNi0.8Co0.15Al0.05O2 coated with LiCoO2. J. Power Sources 230, 201–206. doi:10.1016/j.jpowsour.2012.12.065
Mohanty, D., Kalnaus, S., Meisner, R. A., Rhodes, K. J., Li, J., Payzant, E. A., et al. (2013). Structural transformation of a lithium-rich Li1.2Co0.1Mn0.55Ni0.15O2 cathode during high voltage cycling resolved by in situ X-ray diffraction. J. Power Sources 229, 239–248. doi:10.1016/j.jpowsour.2012.11.144
Park, Y.-U., Kim, J., Gwon, H., Seo, D.-H., Kim, S.-W., and Kang, K. (2010). Synthesis of multicomponent olivine by a novel mixed transition metal oxalate coprecipitation method and electrochemical characterization. Chem. Mater. 22, 2573–2581. doi:10.1021/cm903616d
Qu, X., Zhou, F., Wang, D., Cai, Y., Zhao, J., Ma, J., et al. (2024). Pre-extraction of Li from spent lithium-ion batteries through an Ethanol-Water vapor thermal reduction approach. Chem. Eng. J. 482, 148608. doi:10.1016/j.cej.2024.148608
Refly, S., Floweri, O., Mayangsari, T. R., Sumboja, A., Santosa, S. P., Ogi, T., et al. (2020). Regeneration of LiNi1/3Co1/3Mn1/3O2 cathode active materials from end-of-life lithium-ion batteries through ascorbic acid leaching and oxalic acid coprecipitation processes. ACS Sustain. Chem. Eng. 8, 16104–16114. doi:10.1021/acssuschemeng.0c01006
Roy, J. J., Rarotra, S., Krikstolaityte, V., Zhuoran, K. W., Cindy, Y. D.-I., Tan, X. Y., et al. (2022). Green recycling methods to treat lithium-ion batteries E-waste: a circular approach to sustainability. Adv. Mater. 34, 2103346. doi:10.1002/adma.202103346
Wu, F., Tian, J., Su, Y., Wang, J., Zhang, C., Bao, L., et al. (2015). Effect of Ni2+ content on lithium/nickel disorder for Ni-rich cathode materials. ACS Appl. Mater. interfaces 7, 7702–7708. doi:10.1021/acsami.5b00645
Xiao, J., Li, J., and Xu, Z. (2019). Challenges to future development of spent lithium ion batteries recovery from environmental and technological perspectives. Environ. Sci. Technol. 54, 9–25. doi:10.1021/acs.est.9b03725
Yao, Y., Zhu, M., Zhao, Z., Tong, B., Fan, Y., and Hua, Z. (2018). Hydrometallurgical processes for recycling spent lithium-ion batteries: a critical review. ACS Sustain. Chem. Eng. 6, 13611–13627. doi:10.1021/acssuschemeng.8b03545
Zhang, X., Bian, Y., Xu, S., Fan, E., Xue, Q., Guan, Y., et al. (2018). Innovative application of acid leaching to regenerate Li(Ni1/3Co1/3Mn1/3)O2 cathodes from spent lithium-ion batteries. ACS Sustain. Chem. Eng. 6, 5959–5968. doi:10.1021/acssuschemeng.7b04373
Zhang, Y., Hao, T., Huang, X., Duan, J., Meng, Q., Wang, D., et al. (2019). Synthesis of high performance nano-over-lithiated oxide coated LiNi0.6Co0.2Mn0.2O2 from spent lithium ion batteries. Mater. Res. Express 6, 085521. doi:10.1088/2053-1591/ab209f
Keywords: spent lithium-ion batteries, cathode material, recycle, regeneration, electrochemical performance, ternary lithium-ion batteries
Citation: Yang C, Hao Y, Wang J, Zhang M, Song L and Qu J (2024) Research on the facile regeneration of degraded cathode materials from spent LiNi0.5Co0.2Mn0.3O2 lithium-ion batteries. Front. Chem. 12:1400758. doi: 10.3389/fchem.2024.1400758
Received: 14 March 2024; Accepted: 11 April 2024;
Published: 30 April 2024.
Edited by:
Xianguang Meng, North China University of Science and Technology, ChinaCopyright © 2024 Yang, Hao, Wang, Zhang, Song and Qu. This is an open-access article distributed under the terms of the Creative Commons Attribution License (CC BY). The use, distribution or reproduction in other forums is permitted, provided the original author(s) and the copyright owner(s) are credited and that the original publication in this journal is cited, in accordance with accepted academic practice. No use, distribution or reproduction is permitted which does not comply with these terms.
*Correspondence: Li Song, c29uZ2xpQG51aXN0LmVkdS5jbg==; Jiaan Qu, MDAwOTY4QG51aXN0LmVkdS5jbg==