- 1College of Chemistry and Chemical Engineering, Xinyang Normal University, Xinyang, China
- 2Xinyang Key Laboratory of Low-Carbon Energy Materials, Xinyang Normal University, Xinyang, China
A suitable electrolyte is crucial to enhancing the electrochemical performance of magnesium (Mg) batteries. Here, the influence of Na2SiO3 on the electrochemical behavior of AZ31B Mg alloy in the Na2SO4-NaNO3 composite electrolyte was investigated. The results revealed that the activation potential of the AZ31B Mg alloy first represented a negative shift and then a positive shift with the increase in Na2SiO3. The most negative activation potential (−1.51 V) and the lowest polarization (−3.20 V) were found when 6 mM of Na2SiO3 was added; no discharge hysteresis was observed, and the polarization resistance value (R1) was 3,806 Ω. After 24 h immersion in the composite electrolyte with Na2SiO3, more and wider cracks appeared on the alloy surface, where a thick, dense film was formed, showing excellent discharge performance and corrosion resistance.
Introduction
In view of the limited nature and high price of lithium resources, the research on electrochemical energy storage devices, such as non-lithium batteries (Zhang J. L. et al., 2021; Liu et al., 2021; Wan et al., 2022) and supercapacitors (Zhang Y. et al., 2021; Wei et al., 2021) is increasing. Magnesium (Mg) holds a promising application in anode materials for the first-generation Mg battery owing to its abundance, small density (1.74 g cm−3), low cost, and excellent electrical conductivity (Bertasi et al., 2016; Yang et al., 2022). In addition, located on the diagonal of the periodic table, Mg and Li share many similar chemical properties. The standard electrode potential of metallic Mg is −2.36 V (vs. SHE), allowing the formation of large open-circuit voltage and working voltage (Deng et al., 2019; Maddegalla et al., 2021). Mg has an electrochemical equivalent of 0.454 g Ah−1 and a theoretical specific capacity up to 2,202 mAh g−1, enabling it to be applied to long-time discharge (Kékedy-Nagy et al., 2021). However, shortcomings also remain unresolved, such as the lessened battery storage capacity after discharge, voltage hysteresis, severe inferior corrosion resistance of the electrode, and poor current efficiency, forming the main obstructors of the commercial availability of Mg battery (Shao et al., 2015; Horia et al., 2022; Zhang et al., 2022). In the Mg battery, “voltage lag” is the essence of the passivation of the Mg electrode in the electrolyte. Passivation film hinders the reaction during battery discharge, and its breakdown promotes a smooth reaction. Therefore, a Mg battery is required for the normal voltage output over a period of time. The “hysteresis” in the Mg battery is mainly relevant to the coverage degree of surface passivation film and the rate and relaxation time of film breakdown (Gong et al., 2022; Wei et al., 2022).
Recently, employing a suitable additive into electrolytes has been proved to be simple and effective in changing the surface membrane structure of the Mg electrode, thus reducing voltage lag (Li et al., 2021). The presence of both 0.005 M EDTA-ZnNa2 and 0.01 M C6H11NaO7 has been demonstrated to remarkably inhibit corrosion and improve the performance of Mg battery for pure Mg in 3.5 wt% NaCl electrolyte (Qu et al., 2022). Zhao et al. (2016) investigated the discharge performance of an oxyanion corrosion inhibitor (Li2CrO4) as an electrolyte additive in 3.5 wt% NaCl electrolyte for Mg-air battery, verifying enormously reduced corrosion current density of AZ31B Mg alloys in the presence of 0.1 wt% Li2CrO4, which is beneficial to the intermittent discharge performance of the Mg-air battery.
Sodium metasilicate (Na2SiO3) is relatively cheap, environment-friendly, and non-toxic, often used as an anionic corrosion inhibitor (Kong et al., 2022). This thesis mainly explored the electrochemical performance and corrosion behavior of AZ31B Mg alloy in Na2SO4-NaNO3 and Na2SiO3 composite electrolyte to pick out the matching electrolyte, thus ensuring the activation of the electrode and inhibiting the hydrogen evolution-induced self-corrosion.
Experiment
Chemicals and materials
In this study, Na2SO4, NaNO3, and Na2SiO3 of analytical grade (≥99%) were utilized. The electrolyte was obtained by a mixture of 2 M Na2SO4 and 2 M NaNO3 (volume ratio = 1:9), and the Na2SiO3 concentration ranged from 0.2 to 1.0 mM.
According to our previous work (Xu et al., 2017), the AZ31B Mg alloy (3.0 wt% Al, 1.0 wt% Zn, 0.2 wt% Mn, and 96.8 wt% Mg) was purchased from Wuxi Xinbiao Metal Material Co. Ltd. in China. The Mg alloy was sheared into an appropriate size of 1 × 1 cm with a thickness of 0.6 cm, then embedded with electric conductive copper wire, and encapsulated with epoxy resin in quick succession. Subsequently, these prepared samples were used as the working electrode for the electrochemical analysis.
Electrochemical characterization
The electrochemical characterization was performed on an electrochemical measurement system (CHI660E, China) using a standard three-electrode system comprising the graphite rod as the counter electrode, the saturated calomel electrode as the reference electrode, and the AZ31B Mg alloy as the working electrode.
The influence of Na2SiO3 additive on the electrochemical behavior of AZ31B Mg alloy electrode in the Na2SO4-NaNO3 composite electrolyte was investigated by the linear sweep voltammetry (LSV) at a sweep rate of 1 mV s−1. The discharge curves were explored at a discharge current density of 3 mA cm−2. Moreover, the electrochemical impedance spectroscopy (EIS) was conducted at open circuit potentials in the range of 10–2∼105 Hz with an amplitude of 5 mV.
Surface morphology analysis
The effect of the Na2SiO3 additive on the morphology of the corrosive film layer on the Mg alloy electrode surface immersed into the Na2SO4-NaNO3 composite electrolyte with or without Na2SiO3 (0.6 mM) for 24 h was revealed by the scanning electron microscopy (SEM, HITACHI S 4800) at an operating voltage of 15 kV.
Results and discussion
The AZ31B Mg alloy electrodes were soaked in the Na2SO4-NaNO3 composite electrolytes of different Na2SiO3 concentrations (
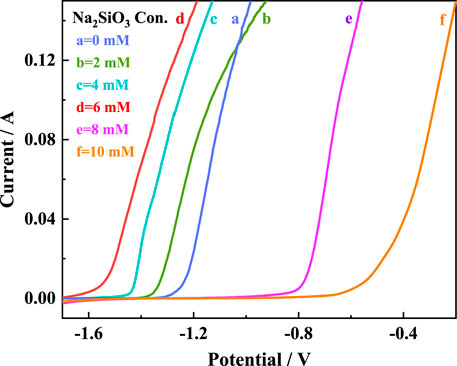
FIGURE 1. LSV curves of AZ31B Mg alloy electrodes in Na2SO4-NaNO3 composite electrolyte with different concentrations of Na2SiO3.
Figure 2 illustrates the discharge curves of AZ31B Mg alloy electrodes in the composite electrolytes with varying
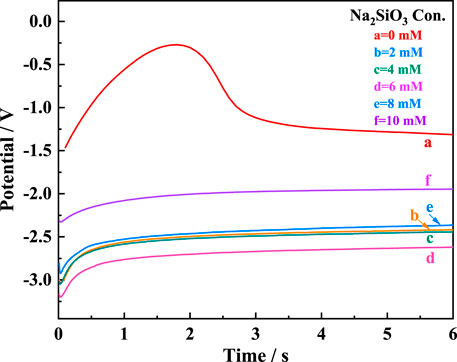
FIGURE 2. Discharge curves of AZ31B Mg alloy electrode in the Na2SO4-NaNO3 composite electrolyte with different
Notably, the Na2SiO3 addition reduced the discharge potential, which was −1.93 V in the composite electrolyte without Na2SiO3 at 3 mA cm−2. In particular, when
The EIS spectra of the AZ31B Mg alloy electrodes after 24 h immersion in the composite electrolytes of varying Na2SiO3 concentrations are shown in Figure 3. EIS was conducted at an open-circuit potential of 10–2∼105 Hz, with a sinusoidal disturbance amplitude of 5 mV. The insert illustrated the equivalent circuit of the EIS system. In the equivalent circuit diagram, Rs was induced by the solution resistance; 下标 corresponded to the high-frequency charge-transfer resistance arising from the alloy surface and corrosive film layer. CPE1 denoted the double-layer capacitance induced by irregular oxide film on the alloy surface.
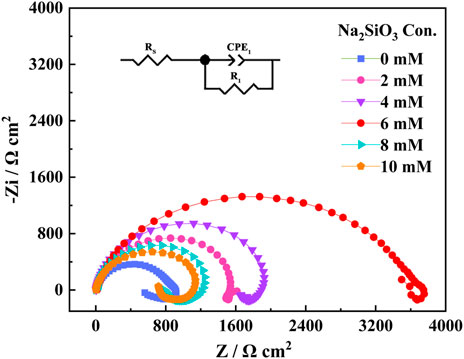
FIGURE 3. Nyquist curves of EIS for AZ31B Mg alloy electrodes in the Na2SO4-NaNO3 composite electrolyte with different concentrations of Na2SiO3.
As shown in Figure 3, the EIS plots exhibited capacitive loops of similar shapes at low and high frequencies, and only some changes took place in the radii of the capacitive loops, indicating that the corrosion mechanism of the AZ31B Mg alloy was free from the influence of the addition amount of Na2SiO3. At a Na2SiO3 concentration of 6 mM, the capacitive reactance diameter reached the maximum. According to the curves, R1 was 957 Ω in the absence of Na2SiO3. With the Na2SiO3 addition, the resistance value was enhanced significantly, indicating the prohibited corrosion of the AZ31B Mg alloy in the Na2SO4-NaNO3 composite electrolyte. When
The surface morphology images of AZ31B Mg alloy electrodes after 24 h immersion in the Na2SO4-NaNO3 composite electrolyte are shown in Figure 4. Figures 4A,B show the SEM images of electrodes soaked in the absence of Na2SiO3. After 24 h of soaking, a thick, dense, and smooth film was formed on the Mg alloy electrode. Despite their large number, the cracks appearing on the surface were very narrow (generally <3 μm in width). As a result of hydrogen evolution from the electrode during the early soaking stages, a few small holes and pits were formed on the film. After 24 h of soaking in the presence of 6 mM Na2SiO3 (Figures 4C,D), the alloy surface exhibited more and wider cracks (the widest cracks exceeded 10 μm in width). A thick and dense film was formed, effectively protecting the Mg alloy electrode and enhancing its corrosion resistance.
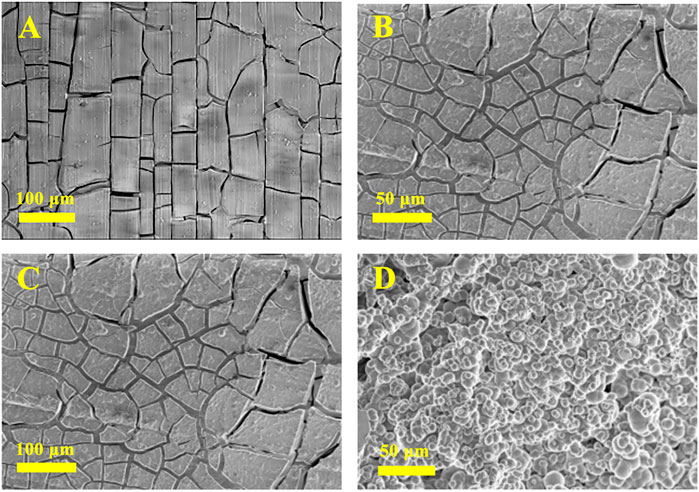
FIGURE 4. SEM of the AZ31B Mg alloy soaked in the Na2SO4-NaNO3 composite electrolyte in the absence (A,B) and presence (C,D) of Na2SiO3 for 24 h.
Conclusion
The influence of Na2SiO3 on the electrochemical and corrosion behavior of the AZ31B Mg alloy electrode in the Na2SO4-NaNO3 composite electrolyte (the volume ratio of 2 M Na2SO4 to 2 M NaNO3 was 1:9) was investigated in this work. When
Data availability statement
The raw data supporting the conclusions of this article will be made available by the authors without undue reservation.
Author contributions
YZ: Data curation, Investigation, Writing-original draft. QZ: Data curation, Investigarion. CS: Writing-review and editing. CL: Project administration, Linguistic modification.
Funding
This work was supported by Henan Province’s key research and development and promotion of the Science and Technology Project (no. 222102320336).
Conflict of interest
The authors declare that the research was conducted in the absence of any commercial or financial relationships that could be construed as a potential conflict of interest.
Publisher’s note
All claims expressed in this article are solely those of the authors and do not necessarily represent those of their affiliated organizations or those of the publisher, the editors, and the reviewers. Any product that may be evaluated in this article, or claim that may be made by its manufacturer, is not guaranteed or endorsed by the publisher.
References
Bertasi, F., Sepehr, F., Pagot, G., Paddison, S. J., and Di Noto, V. (2016). Magnesium batteries: Toward a magnesium-iodine battery (adv. Funct. Mater. 27/2016). Adv. Funct. Mat. 27, 4859. doi:10.1002/adfm.201670174
Deng, M., Wang, L., Höche, D., Lamaka, S. V., Snihirova, D., Vaghefinazari, B., et al. (2019). Clarifying the decisive factors for utilization efficiency of Mg anodes for primary aqueous batteries. J. Power Sources 441, 227201. doi:10.1016/j.jpowsour.2019.227201
Ge, Y. F., Jiang, B. L., and Shi, H. Y. (2013). Effect of Na2SiO3 concentration on energy consumption during arcing process of micro-arc oxidation on aluminum alloys. Chin. J. Nonferrous Mater. 23, 950–956. doi:10.19476/j.ysxb.1004.0609.2013.04.009
Gong, C., Yan, X., He, X., Su, Q., Liu, B., Chen, F., et al. (2022). Influence of homogenization treatment on corrosion behavior and discharge performance of the Mg-2Zn-1Ca anodes for primary Mg-air batteries. Mat. Chem. Phys. 280, 125802. doi:10.1016/j.matchemphys.2022.125802
Horia, R., Nguyen, D. T., Eng, A. Y. S., and Seh, Z. W. (2022). Comparative study of conventional electrolytes for rechargeable magnesium batteries. Batter. Supercaps 5, e202200011. doi:10.1002/batt.202200011
Kékedy-Nagy, L., Abolhassani, M., Greenlee, L. F., and Pollet, B. G. (2021). An electrochemical study of ammonium dihydrogen phosphate on Mg and Mg alloy electrodes. Electrocatalysis 12, 251–263. doi:10.1007/s12678-021-00646-x
Kong, D., Ren, W., Qi, L., Zhang, Y., and Chen, H. (2022). Enhanced bonding strength of AZ31B/carbon-fiber-reinforced plastic laminates by anodization treatment in a saturated Na2SiO3 solution. Mater. Sci. Eng. A 840, 142982. doi:10.1016/j.msea.2022.142982
Li, J., Wei, Z., and Gao, Z. (2021). Improving corrosion and discharge performance of magnesium alloy via sodium stannate additive. J. Xinyang Normal Univ. Nat. Sci. Ed. 1, 93–98. doi:10.3969/j.issn.1003-0972.2021.01.015
Liu, S., Li, X. Z., Huang, B., Yang, J. W., Chen, Q. Q., Li, Y. W., et al. (2021). Controllable construction of yolk-shell Sn-Co@void@C and its advantages in Na-ion storage. Rare Met. 40, 2392–2401. doi:10.1007/s12598-021-01729-w
Maddegalla, A., Mukherjee, A., Blázquez, J. A., Azaceta, E., Leonet, O., Mainar, A. R., et al. (2021). Cover feature: AZ31 magnesium alloy foils as thin anodes for rechargeable magnesium batteries (ChemSusChem 21/2021). ChemSusChem 14, 4611. doi:10.1002/cssc.202102057
Qu, J., Luo, H., Liu, Z., Wang, H., Chen, Y., and Yang, L. (2022). Effect of sodium-zinc EDTA and sodium gluconate as electrolyte additives on corrosion and discharge behavior of Mg as anode for air battery. Mat. Corros. 2022, 1–12. doi:10.1002/maco.202213322
Shao, Y., Rajput, N. N., Hu, J., Hu, M., Liu, T., Wei, Z., et al. (2015). Nanocomposite polymer electrolyte for rechargeable magnesium batteries. Nano Energy 12, 750–759. doi:10.1016/j.nanoen.2014.12.028
Wan, M., Zeng, R., Meng, J., Cheng, Z., Chen, W., Peng, J., et al. (2022). Post-synthetic and in situ vacancy repairing of iron hexacyanoferrate toward highly stable cathodes for sodium-ion batteries. Nano-Micro Lett. 14, 9. doi:10.1007/s40820-021-00742-z
Wang, N., Wang, R., Peng, C., Peng, B., Feng, Y., and Hu, C. (2014). Discharge and corrosion performance of AP65 magnesium alloy in simulated seawater: Effect of temperature. J. Mat. Eng. Perform. 23, 4374–4384. doi:10.1007/s11665-014-1222-2
Wei, Q., Li, Q., Jiang, Y., Zhao, Y., Tan, S., Dong, J., et al. (2021). High-energy and high-power pseudocapacitor-battery hybrid sodium-ion capacitor with Na+ intercalation pseudocapacitance anode. Nano-Micro Lett. 13, 55. doi:10.1007/s40820-020-00567-2
Wei, Z., Pan, Q., and Han, X. (2022). Effect of changes in geothermal water temperature on corrosion behavior of stainless steel pipes. J. Xinyang Normal Univ. Nat. Sci. Ed. 1, 113–117. doi:10.3969/j.issn.1003-0972.2022.01.019
Xu, J., Yang, Q., Huang, C., Javed, M. S., Aslam, M. K., and Chen, C. (2017). Influence of additives fluoride and phosphate on the electrochemical performance of Mg-MnO2 battery. J. Appl. Electrochem. 47, 767–775. doi:10.1007/s10800-017-1074-1
Yang, J., Miao, X., Zhang, C., Zheng, J., Sun, C., Zhang, Y., et al. (2022). In-situ lattice tunnel intercalation of vanadium pentoxide for improving long-term performance of rechargeable magnesium batteries. ChemNanoMat 8, e202200025. doi:10.1002/cnma.202200025
Zhang, C., Wang, A., Guo, L., Yi, J., and Luo, J. (2022). A moisture-assisted rechargeable Mg-CO2 battery. Angew. Chem. Int. Ed. Engl. 61, e202200181. doi:10.1002/anie.202200181
Zhang, J. L., Li, C. L., Wang, W. H., and Yu, D. Y. W. (2021). Facile synthesis of hollow Cu3P for sodium-ion batteries anode. Rare Met. 40, 3460–3465. doi:10.1007/s12598-021-01718-z
Zhang, Y., Zhao, T., and Li, S. (2021). Influence of different morphologies on the supercapacitive performance of NiCo2O4 particles. J. Xinyang Normal Univ. Nat. Sci. Ed. 01, 99–104.
Keywords: AZ31B Mg alloy, composite electrolyte, Na2SiO3, electrochemical performance, corrosion behavior
Citation: Zhang Y, Zhu Q, Su C and Li C (2022) Electrochemical behavior of Mg electrode in sodium salt electrolyte system. Front. Chem. 10:992400. doi: 10.3389/fchem.2022.992400
Received: 12 July 2022; Accepted: 16 August 2022;
Published: 09 September 2022.
Edited by:
Xiaohang Zheng, Harbin Institute of Technology, ChinaReviewed by:
Xiu-Cheng Zheng, Zhengzhou University, ChinaLing Jiang, Dalian Institute of Chemical Physics (CAS), China
Copyright © 2022 Zhang, Zhu, Su and Li. This is an open-access article distributed under the terms of the Creative Commons Attribution License (CC BY). The use, distribution or reproduction in other forums is permitted, provided the original author(s) and the copyright owner(s) are credited and that the original publication in this journal is cited, in accordance with accepted academic practice. No use, distribution or reproduction is permitted which does not comply with these terms.
*Correspondence: Yu Zhang, emhhbmd5dUB4eW51LmVkdS5jbg== Chao Li, bGljaGFvOTguMy42QDE2My5jb20=