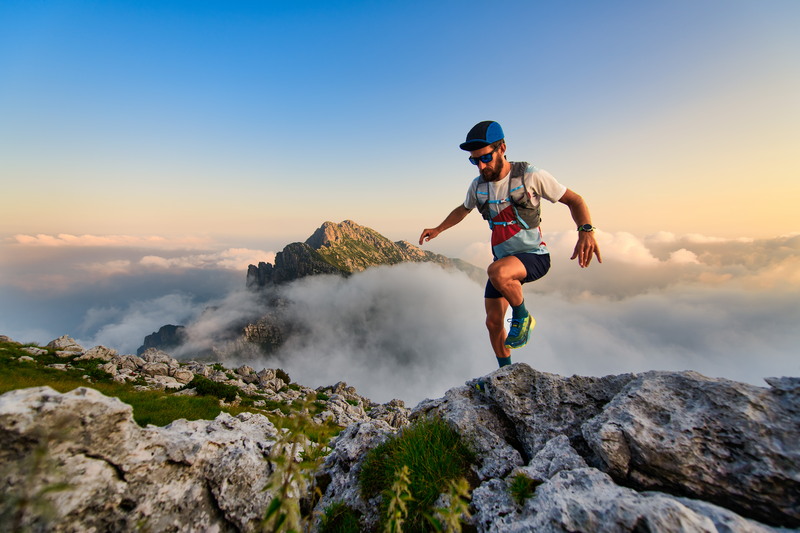
95% of researchers rate our articles as excellent or good
Learn more about the work of our research integrity team to safeguard the quality of each article we publish.
Find out more
ORIGINAL RESEARCH article
Front. Chem. , 27 April 2022
Sec. Chemical Physics and Physical Chemistry
Volume 10 - 2022 | https://doi.org/10.3389/fchem.2022.899287
This article is part of the Research Topic Micro/Nano Materials for Energy Storage and Conversion View all 14 articles
Iron-chromium redox flow batteries (ICRFBs) have the advantages of high safety, long cycle life, flexible design, and low maintenance costs. Polyacrylonitrile-based graphite felt composite material has good temperature resistance, corrosion resistance, large surface area and excellent electrical conductivity, and is often used as the electrode material of ICRFB, but its chemical activity is poor. In order to improve the activity of the graphite felt electrode, In3+ was used for modification in this paper, and the modified graphite felt was used as the electrode material for iron-chromium batteries. The structure and surface morphology of the modified graphite felt were analyzed by the specific surface area analyzer and scanning electron microscope; the electrochemical impedance spectroscopy and cyclic voltammetry experiments were carried out on the electrochemical workstation to study the electro catalytic activity of In3+ modified graphite felt and its performance in ICRFBS. The results show that the graphite felt electrode modified with a concentration of 0.2 M In3+ was activated at 400°C for 2 h, and its surface showed a lot of grooves, and the specific surface area reached 3.889 m2/g, while the specific surface area of the untreated graphite felt was only 0.995 m2/g significantly improved. Electrochemical tests show that the electrochemical properties of graphite felt electrodes are improved after In3+ modification. Therefore, the In3+ modified graphite felt electrode can improve the performance of ICRFB battery, and also make it possible to realize the engineering application of ICRFB battery.
In recent years, with the depletion of non-renewable resources such as coal, oil, and natural gas, renewable energy such as wind, hydro, and tidal energy has developed rapidly (Mankge et al., 2021; Hargreaves et al., 2020). Therefore, it is very important to develop large-scale and high-efficiency energy storage systems (Ani 2021; Züttel et al., 2022). As a large-scale power storage system, flow batteries have the characteristics of high capacity and wide application fields (environments), and will usher in a period of rapid development (Yang et al., 2021; Sankaralingam et al., 2021; Huang et al., 2021). In most flow batteries, iron-chromium flow batteries use low-cost Cr3+/Cr2+ pairs to reduce Cr2+ and Fe3+/Fe2+ pairs to oxidize Fe3+, respectively. Electrochemical redox reaction is carried out in Cr3+ electrolyte and acidic Fe2+ electrolyte (Zhang et al., 2020; Wu et al., 2021; Ahn et al., 2021). A typical iron-chromium flow battery system is shown in Figure 1, which consists of a point stack unit, an electrolyte, electrolyte storage and supply unit, and a management and control unit (Chen et al., 2020).
The key materials of flow batteries include electrodes, membranes, electrolytes, etc. Among them, graphite felt is the most commonly used electrode material in flow batteries (Zhang et al., 2017; Yue et al., 2010). At present, the activation methods of graphite felt are generally divided into two methods: adding oxygen-containing functional groups on the surface and introducing surface catalytic substances (Zhang et al., 2019). In terms of increasing the oxygen-containing functional groups on the surface, methods such as acidified K2Cr2O7 solution (Hassan et al., 2019), KMnO4 solution (Hassan et al., 2020), and laser coating modification (Daugherty et al., 2020) and aerogel modification (Jiang et al., 2019) are generally used. The introduction of oxygen-containing functional groups can not only increase the carbon and oxygen sites of the graphite felt modified electrode, increase the electrode activity, but also accelerate the charge transfer speed and improve the dynamic performance of the electrode (Na et al., 2018). The specific surface area of the felt (Jiang et al., 2019). In terms of introducing surface catalytic substances, electrostatic spraying graphene oxide coating (Anantha et al., 2021), rare earth composite oxide (Wang et al., 2020). and noble metal particles such as Pt and Ag are generally used as the main decoration (Xia et al., 2020; Lou et al., 2021), which can increase the current density and improve the current efficiency.
Indium and indium oxide are promising oxides (Xinyuan et al., 2021), and current research is mainly focused on the fact that indium and indium oxide can inhibit the hydrogen evolution reaction of the anode and improve the Coulombic efficiency of the battery. Leung et al. deposited zinc on a carbon composite electrode in a methane sulfonic acid medium and added 2 × 10−3 moldm−3 indium oxide as a hydrogen suppressor, and the energy efficiency was increased from 62 to 73% (Leung et al., 2011). Wang et al. used In3+ as an additive to improve the stability and performance of ICFBS, and their studies showed that In3+ can not only effectively inhibit the hydrogen evolution reaction, but also promote the reaction kinetics to a certain extent (Wang et al., 2021). The research on In3+ modified graphite felt electrodes has not been reported in detail. Therefore, it is of great significance to study the electro catalytic activity of In3+ modified graphite felt and its performance in ICRFBS.
Graphite felt (GF, 5 mm, Gansu Haoshi Carbon Fiber Co., Ltd.) was heat-treated at 400°C for 2 h as the base material. Take three appropriate amounts of In2O3 powder and add them to a beaker of 3 M dilute hydrochloric acid respectively to prepare a 0.1, 0.2, and 0.3 M InCl3 solution. The following chemical reactions mainly take place in this process:
Three groups of graphite felts of the same size were immersed in 0.1, 0.2, and 0.3 M InCl3 solutions for 8 h, respectively. Then it was dried in a drying oven at 80°C for 15 h. The dried graphite felt was thermally activated in a medium-temperature experimental furnace at 400°C for 2 h. That is, the active graphite felt electrode for iron-chromium flow battery whose surface is coated with InCl3 is prepared.
Scanning electron microscope (SEM) was used to observe the microscopic morphology of graphite felt, and X-ray energy dispersive spectroscopy (EDS) was used to determine the types and contents of elements on the surface of the samples. The N2 adsorption and desorption isotherms and the specific surface area (BET) and pore size distribution of each sample were measured by a specific surface area and pore size tester, and the pore size distribution was compared and analyzed by the BJH method (Chen et al., 2020).
Electrochemical performance was measured at room temperature using Wuhan Koster electrochemical workstation, and the flow battery electrolyte solution consisted of 1.0 M CrCl3 + 1.0 M FeCl2 + 3.0 M HCl solution. A three-electrode system was used for electrochemical measurement, 0.4 cm2 graphite felt was used as the working electrode, 1.0 cm2 platinum sheet was used as the counter electrode, and the reference electrode was a calomel electrode. Cyclic voltammetry tests were performed at a scan rate of 5 mV/s and a voltage range of −0.8–0.8 V. Electrochemical impedance measurements were performed in the frequency range from 0.01Hz to 100 kHz with an AC voltage amplitude of 5 mV and polarization potentials of 0.4V and −0.5 V, respectively.
The surface morphology of graphite felt electrode observed by scanning electron microscope is shown in Figure 2. A small amount of impurities attached to the surface is the untreated graphite felt (Figure 2A), and a large number of deep “grooves” appeared along the fiber axis on the surface of the heat-treated graphite felt (Figure 2B). Figures 2C–E show the heat-treated graphite felt electrodes impregnated with InCl3 solutions of different concentrations, respectively. It can be seen that after immersion in the InCl3 solution, the depth of the “grooves” increases on the surface and is accompanied by the generation of irregular holes. When the concentration of InCl3 solution was 0.2 M (Figure 2D), the specific surface area of the graphite felt increased significantly to 3.889 m2/g, while the specific surface area of the untreated graphite felt was only 0.995 m2/g. In addition to the increase in the specific surface area of the graphite felt electrode, the EDS test results (Figure 3) showed that InCl3 was successfully coated on the fiber surface with uniform distribution, which may increase the activation point of the graphite felt electrode, which is beneficial to improve the performance of the electrode.
FIGURE 2. 5.00 KX Scanning Electron Micrograph (SEM) (A), untreated graphite felt (B), heat treated graphite felt (C), heat treated graphite felt impregnated with 0.1 M InCl3 solution (D), heat treated graphite felt impregnated with 0.2 M InCl3 solution (E), heat treated graphite felt impregnated with 0.3 M InCl3 solution.
Take five pieces of graphite felt of the same size and put it into the electrolyte at the same time, observe its falling speed and position in three time periods of instant, 10 and 30 min, and judge its wettability.
It can be seen from Figure 4 that when the graphite felt is impregnated with InCl3 solution, its lipophilicity is significantly improved, and it will quickly sink into the electrolyte at the moment of contact, and the sinking speed of graphite felt impregnated with 0.2 M InCl3 solution will be slightly faster than Graphite felt impregnated with other concentrations of InCl3 solution. This method can measure the hydrophilicity of graphite felt, but the error is large. It can also be proved that the hydrophilicity of graphite felt is enhanced after being impregnated with InCl3 solution.
FIGURE 4. Samples from left to right are untreated graphite felt, heat-treated graphite felt, heat-treated graphite felt after immersion in 0.1 M InCl3 solution, heat-treated graphite felt after immersion in 0.2 M InCl3 solution, and heat-treated graphite felt after immersion in 0.3 M InCl3 solution, (A), momentary Contact; (B), soak for 10 min; (C), soak for 30 min.
In order to better understand the properties of graphite felt after immersion in InCl3 solution, we measured the resistance of each sample. Figure 5 shows the change of the line resistance value of each sample.
FIGURE 5. respectively GF; TGF; 0.1 M InCl3 solution impregnated heat-treated graphite felt; 0.2 M InCl3 solution impregnated heat-treated graphite felt; 0.3 M InCl3 solution impregnated heat-treated graphite felt line resistance.
It can be seen from Figure 5 that the line resistance of GF is the largest, while the line resistance of TGF is slightly lower than that of GF, from 0.17 Ω/cm to 0.1 Ω/cm, and the reduction range is 41.17%. All have decreased, the decrease range is 17.64, 35.29, 17.65%, and it can be seen that the graphite felt impregnated with 0.2 M InCl3 solution has the lowest resistance.
As shown in Figure 6, the redox peak intensity of the cyclic voltammetry of the untreated graphite felt electrode is small, indicating that its electrochemical activity is low, and it is not suitable for direct use as an electrode material for iron-chromium batteries. The heat-treated graphite felt electrodes showed more obvious redox peaks after heat treatment and InCl3 solution immersion, indicating that the electrochemical performance of the heat-treated graphite felt electrodes was significantly improved compared with the untreated ones. Among them, the electrochemical performance of graphite felt electrode (d) after impregnation with InCl3 solution concentration of 0.2 M is the best, and the peak value of its wave peak is also stronger. It can be observed from Figure 6 that the peak current values of the positive electrode of the heat-treated graphite felt electrode and the graphite felt after being impregnated with InCl3 solution and then heat-treated are 587 mA, 642 mA, 692 mA, and 644 mA, all of which are greater than 524 mA. It can be proved that heat treatment after immersion in InCl3 solution can improve the electrochemical activity of the redox pair in Fe-Cr batteries.
FIGURE 6. how’s samples (a), GF; (b), TGF; (c), heat-treated graphite felt after immersion in 0.1 M InCl3 solution; (d), heat-treated graphite felt after immersion in 0.2 M InCl3 solution; (e), heat-treated graphite felt after immersion in 0.3 M InCl3 solution, cycle Voltammetry curve.
Electrochemical impedance spectroscopy further analyzed the effect of heat treatment after immersion in InCl3 solution on the electrochemical performance of iron-chromium batteries. Figure 7 shows the Nyquist plots of a-e graphite felt electrodes. It can be observed from the figure that in all Nyquist diagrams, the semicircular part exists in the high frequency region, and the linear part exists in the low frequency region, which can indicate the interaction between iron ions and chromium ions on the graphite felt electrode. Redox reactions are affected by both the rate of charge transfer and the rate of diffusion. In Figure 7, when the electron transfer step at the electrode/electrolyte interface is the control step, the electrode process is corresponding to the semicircle arc located in the high frequency region, and the difficulty of the electron transfer is determined by the semicircle arc. Reflected by the radius of the arc (Rct), the smaller the resistance, the less difficult the transfer of electrons will be, and the smaller the radius will be; the diffusion coefficient of the reaction particles in the solution is the control step. Corresponding to the slash (Rs). Observing Figure 7, it can be seen that heat treatment after immersion in InCl3 solution can significantly reduce the charge transfer resistance of the iron-chromium redox couple, and the high-frequency arc radius is significantly smaller than that before treatment, indicating that heat treatment after immersion in InCl3 solution can accelerate the redox couple of iron-chromium. Reaction and charge transfer rates. However, it is easier for electrons to transfer on the graphite felt after being immersed in InCl3 solution and then heat-treated, that is, and the charge transfer resistance of the graphite felt is greatly reduced at this time, which further indicates that the heat-treated graphite felt electrode after being immersed in InCl3 solution is in iron. The electrochemical performance of chromium flow batteries has been greatly improved.
FIGURE 7. Samples (a), GF; (b), TGF; (c), heat-treated graphite felt after immersion in 0.1 MM InCl3 solution; (d), heat-treated graphite felt after immersion in 0.2 MM InCl3 solution; (e), heat-treated graphite felt after immersion in 0.3 MM InCl3 solution, electrochemical impedance Diagram and Equivalent Circuit Diagram.
In this paper, the graphite felt was immersed in InCl3 solution and then heat treated, so that indium ions were successfully introduced into the surface of the graphite felt to prepare an active electrode. The comprehensive SEM, EDS, BET, resistance, lipophilicity, and electrochemical test results can get conclusion:
1) In3+ was successfully coated on the surface of the fiber, and the distribution was uniform, which increased the activation point of the graphite felt electrode, which was beneficial to improve the performance of the electrode. When the In3+ concentration was 0.2 M, the specific surface area of the graphite felt increased significantly to 3.889 m2/g, while the specific surface area of the untreated graphite felt is only 0.995 m2/g.
2) The hydrophilicity of graphite felt impregnated with InCl3 solution is obviously enhanced, and it can be seen that the graphite felt impregnated with 0.2 M InCl3 solution has the lowest resistance.
3) Heat treatment after immersion in InCl3 solution can accelerate the redox reaction and charge transfer rate of iron-chromium charge, and the charge transfer resistance of the graphite felt after immersion in InCl3 solution is greatly reduced, thereby further improving its electrochemical performance.
The original contributions presented in the study are included in the article/Supplementary Material, further inquiries can be directed to the corresponding author.
YS is the experimental designer and executor of this study, completing the data analysis and writing the first draft of the paper; NC, H-LR, L-LG, and ZL participated in the experimental design and analysis of the experimental results; X-MW is the designer and responsible for the project People, instructed experimental design, data analysis, thesis writing and revision. All authors read and agree to the final text.
This work is funding by the National Key Research and Development Program (2020YFC1909300), Regional joint fund project of Liaoning Provincial Department of science and technology (2020-YKLH-27), the Foundation of Liaoning Key Laboratory of Chemical Additive Synthesis and Separation (ZJNK 2001) and the Yingkou Institute of Technology Innovation Team Project (TD201901).
The authors declare that the research was conducted in the absence of any commercial or financial relationships that could be construed as a potential conflict of interest.
All claims expressed in this article are solely those of the authors and do not necessarily represent those of their affiliated organizations, or those of the publisher, the editors and the reviewers. Any product that may be evaluated in this article, or claim that may be made by its manufacturer, is not guaranteed or endorsed by the publisher.
Ahn, Y., Moon, J., Park, S. E., Shin, J., Wook Choi, J., and Kim, K. J. (2021). High-performance Bifunctional Electrocatalyst for Iron-Chromium Redox Flow Batteries. Chem. Eng. J. 421, 127855. doi:10.1016/j.cej.2020.127855
Anantha, M. S., Anarghya, D., Hu, C., Reddy, N., Venkatesh, K., and Muralidhara, H. B. (2021). Electrochemical Performance of Graphene Oxide Modified Graphite Felt as a Positive Electrode in All-Iron Redox Flow Batteries. J. Appl. Electrochem. 51 (2), 331–344. doi:10.1007/s10800-020-01490-5
Ani, V. A. (2021). Development of an Intelligent Power Management System for Solar PV-Wind-Battery-Fuel-Cell Integrated System. Front. Energ. Res. 9. doi:10.3389/fenrg.2021.613958
Chen, N., Zhang, H., Luo, X.-D., and Sun, C.-Y. (2020). SiO2-decorated Graphite Felt Electrode by Silicic Acid Etching for Iron-Chromium Redox Flow Battery. Electrochimica Acta 336, 135646. doi:10.1016/j.electacta.2020.135646
Daugherty, M. C., Hsieh, C.-T., Aaron, D. S., Ashraf Gandomi, Y., Li, J., Zheng, Y., et al. (2020). Enabling High Rate Capability, Low Internal Resistance, and Excellent Cyclability for Vanadium Redox Flow Batteries Utilizing Ultrafast Laser-Structured Graphite Felt. Electrochimica Acta 344, 136171. doi:10.1016/j.electacta.2020.136171
Hargreaves, J. J., and Jones, R. A. (2020). Long Term Energy Storage in Highly Renewable Systems. Front. Energ. Res. 8. doi:10.3389/fenrg.2020.00219
Hassan, A., and Tzedakis, T. (2019). Enhancement of the Electrochemical Activity of a Commercial Graphite Felt for Vanadium Redox Flow Battery (VRFB), by Chemical Treatment with Acidic Solution of K2Cr2O7. J. Energ. Storage 26, 100967. doi:10.1016/j.est.2019.100967
Hassan, A., and Tzedakis, T. (2020). Facile Chemical Activation of Graphite Felt by KMnO4 Acidic Solution for Vanadium Redox Flow Batteries. Appl. Surf. Sci. 528, 146808. doi:10.1016/j.apsusc.2020.146808
Huang, Z., Mu, A., Wu, L., Wang, H., and Zhang, Y. (2021). Electrolyte Flow Optimization and Performance Metrics Analysis of Vanadium Redox Flow Battery for Large-Scale Stationary Energy Storage. Int. J. Hydrogen Energ. 46 (63), 31952–31962. doi:10.1016/j.ijhydene.2021.06.220
Jiang, F., He, Z., Guo, D., and Zhou, X. (2019). Carbon Aerogel Modified Graphite Felt as Advanced Electrodes for Vanadium Redox Flow Batteries. J. Power Sourc. 440, 227114. doi:10.1016/j.jpowsour.2019.227114
Leung, P. K., Ponce-de-León, C., Low, C. T. J., and Walsh, F. C. (2011). Zinc Deposition and Dissolution in Methanesulfonic Acid onto a Carbon Composite Electrode as the Negative Electrode Reactions in a Hybrid Redox Flow Battery. Electrochimica Acta 56 (18), 6536–6546. doi:10.1016/j.electacta.2011.04.111
Lou, Y., Fu, D., Fabre, B., Fourcade, F., Amrane, A., Pasturel, M., et al. (2021). Bismuth Coated Graphite Felt Modified by Silver Particles for Selective Electroreduction of CO2 into Formate in a Flow Cell. Electrochimica Acta 371, 137821. doi:10.1016/j.electacta.2021.137821
Mankge, N. S., Madito, M. J., Hlongwa, N. W., and Kuvarega, A. T. (2022). Review of Electrochemical Production of Doped Graphene for Energy Storage Applications. J. Energ. Storage 46, 103527. doi:10.1016/j.est.2021.103527
Na, Z., Sun, X., and Wang, L. (2018). Surface-functionalized Graphite Felts: Enhanced Performance in Cerium-Based Redox Flow Batteries. Carbon 138 (18), 363–368. doi:10.1016/j.carbon.2018.07.052
Sankaralingam, R. K., Seshadri, S., Sunarso, J., Bhatt, A. I., and Kapoor, A. (2021). Overview of the Factors Affecting the Performance of Vanadium Redox Flow Batteries. J. Energ. Storage 41, 102857. doi:10.1016/j.est.2021.102857
Wang, H., Li, D., Chen, L., and Han, H. (2020). La and Sr Composite Oxides-Modified Graphite Felt for Aqueous Organic Redox Flow Batteries. Chem. Res. Chin. Univ. 36 (6), 1255–1260. doi:10.1007/s40242-020-0108-0
Wang, S., Xu, Z., Wu, X., Zhao, H., Zhao, J., Liu, J., et al. (2021). Excellent Stability and Electrochemical Performance of the Electrolyte with Indium Ion for Iron-Chromium Flow Battery. Electrochimica Acta 368, 137524. doi:10.1016/j.electacta.2020.137524
Wang, X., and Lu, B. (2021). Influences of Silica Additive on Sintering and Hall Effect of Novel Transparent In2O3 Semiconductive Ceramics. Scripta Materialia 193, 137–141. doi:10.1016/j.scriptamat.2020.10.053
Wu, S., Lv, X., Ge, Z., Wang, L., Dai, L., and He, Z. (2021). Thiourea-Grafted Graphite Felts as Positive Electrode for Vanadium Redox Flow Battery. Front. Chem. 8. doi:10.3389/fchem.2020.626490
Xia, L., Long, T., Li, W., Zhong, F., Ding, M., Long, Y., et al. (2020). Highly Stable Vanadium Redox‐Flow Battery Assisted by Redox‐Mediated Catalysis. Small 16 (38), 2003321. doi:10.1002/smll.202003321
Yang, Z., Wei, Y., Zeng, Y., and Yuan, Y. (2021). Effects of Iin-Ssitu Bismuth Catalyst Electrodeposition on Performance of Vanadium Redox Flow Batteries. J. Power Sourc. 506, 230238. doi:10.1016/j.jpowsour.2021.230238
Yue, L., Li, W., Sun, F., Zhao, L., and Xing, L. (2010). Highly Hydroxylated Carbon Fibres as Electrode Materials of All-Vanadium Redox Flow Battery. Carbon 48 (11), 3079–3090. doi:10.1016/j.carbon.2010.04.044
Zhang, H., Chen, N., Sun, C., and Luo, X. (2020). Investigations on Physicochemical Properties and Electrochemical Performance of Graphite Felt and Carbon Felt for Iron‐chromium Redox Flow Battery. Int. J. Energ. Res 44 (5), 3839–3853. doi:10.1002/er.5179
Zhang, H., Tan, Y., Li, J., and Xue, B. (2017). Studies on Properties of Rayon- and Polyacrylonitrile-Based Graphite Felt Electrodes Affecting Fe/Cr Redox Flow Battery Performance. Electrochimica Acta 248, 603–613. doi:10.1016/j.electacta.2017.08.016
Zhang, H., Tan, Y., Luo, X. D., Sun, C. Y., and Chen, N. (2019). Polarization Effects of a Rayon and Polyacrylonitrile Based Graphite Felt for Iron‐Chromium Redox Flow Batteries. Chem. Electro Chem. 6 (12), 3175–3188. doi:10.1002/celc.201900518
Keywords: iron-chromium flow battery, graphite felt, indium ion, specific surface area, electrochemical performance
Citation: Su Y, Chen N, Ren H-I, Guo L-I, Li Z and Wang X-m (2022) Preparation and Properties of Indium Ion Modified Graphite Felt Composite Electrode. Front. Chem. 10:899287. doi: 10.3389/fchem.2022.899287
Received: 18 March 2022; Accepted: 28 March 2022;
Published: 27 April 2022.
Edited by:
Hailong Wang, Ningxia University, ChinaCopyright © 2022 Su, Chen, Ren, Guo, Li and Wang. This is an open-access article distributed under the terms of the Creative Commons Attribution License (CC BY). The use, distribution or reproduction in other forums is permitted, provided the original author(s) and the copyright owner(s) are credited and that the original publication in this journal is cited, in accordance with accepted academic practice. No use, distribution or reproduction is permitted which does not comply with these terms.
*Correspondence: Xiao-min Wang, dHkuY29tLmNuQDEyNi5jb20=
Disclaimer: All claims expressed in this article are solely those of the authors and do not necessarily represent those of their affiliated organizations, or those of the publisher, the editors and the reviewers. Any product that may be evaluated in this article or claim that may be made by its manufacturer is not guaranteed or endorsed by the publisher.
Research integrity at Frontiers
Learn more about the work of our research integrity team to safeguard the quality of each article we publish.