- 1School of Chemical Engineering, Shenyang University of Chemical Technology, Shenyang, Liaoning, China
- 2Nanjing IPE Institute of Green Manufacturing Industry, Nanjing, Jiangsu, China
- 3State Key Laboratory of Multiphase Complex Systems, Institute of Process Engineering, Chinese Academy of Sciences, Beijing, China
Modifying biodegradable poly (butylene adipate-co-terephthalate) (PBAT) plastic with inorganic fillers is critical for improving its overall performance, lowering the costs, and expanding its application scope. The chemical modification method for the inorganic filler determines the application performance of PBAT composites. In this work, gas—solid fluidization method was developed as a simple, efficient, and scalable strategy for chemically modifying CaCO3 filler. The modified CaCO3 filler was mixed with PBAT and melt extruded to prepare biodegradable PBAT/CaCO3 composites. The characterization results show that gas—solid fluidization method combines the traditional wet modification method’s excellent modification effect with the scalability of the traditional dry modification method. The effects of modification methods and amount of CaCO3 filling on the crystallinity, mechanical, and rheological properties of PBAT/CaCO3 composites were compared. The results demonstrated that PBAT/CaCO3 composites containing 30% gas—solid fluidization modified CaCO3 could still maintain excellent overall performance. As a result, this work provides a simple, efficient, and scalable method for chemically modifying inorganic fillers and preparing biodegradable composites.
1 Introduction
The widespread application of traditional petroleum-based plastics has resulted in serious environmental pollution issues. As a result, countries worldwide have enacted laws and regulations to encourage the use of biodegradable materials (Madhavan Nampoothiri et al., 2010; Kasirajan and Ngouajio, 2012); however, the cost of most biodegradable plastics is 2–4 times higher than that of traditional non-biodegradable materials, thereby making market adoption difficult. Therefore, developing low-cost, high-performance biodegradable materials is a tried-and-true method for reducing the environmental problems caused by waste plastics. Poly (butylene adipate-co-terephthalate) (PBAT) is one of the most promising environment-friendly materials to replace conventional plastics because it combines the ductility of aliphatic polyesters with the mechanical strength of aromatic polyesters (Biundo et al., 2016; Camani et al., 2021; Zhang et al., 2021); however, its low modulus, as well as poor gas barrier properties, low crystallinity, and high cost, have hampered its further development and application (Cavalcanti et al., 2007; Zhai et al., 2020; Wei et al., 2021). Therefore, modifying PBAT with functional materials is critical for improving its overall performance and lowering application costs.
Inorganic fillers with abundant sources and low prices are frequently used for the co-blending modification of PBAT (Mondal et al., 2014; Mukhopadhyay et al., 2015; Li et al., 2018; Xing et al., 2019), with CaCO3 being one of the most commonly used fillers in the polymer industry (Kemal et al., 2013; Mantia et al., 2013; Tang et al., 2014; Zapata et al., 2018); however, CaCO3 is a hydrophilic inorganic filler with poor interfacial bonding ability with the hydrophobic PBAT matrix, necessitating chemical functionalization treatment to modify its surface properties (Chen et al., 2004). Fatty acid salt modification (Wang et al., 2007; Jeong et al., 2009; Tran et al., 2010), phosphate ester modification (Sheng et al., 2004), coupling agent modification (Doufnoune et al., 2003; Li et al., 2019), surface polymer grafting modification (Han and Kim, 2012), and in situ polymerization (Li et al., 2021) are the most common chemical modification methods for inorganic fillers. Among these, coupling agent modification has the advantages of simplicity and low cost.
Titanate is a common coupling agent that, when surface functionalized, can significantly improve CaCO3 hydrophobicity (Wang et al., 2010). When compared with silane coupling agents, titanate coupling agent modified CaCO3 has better interfacial interactions with the polymer matrix, resulting in a more significant improvement in composite performance (Upadhyaya et al., 2012). Depending on the treatment method, surface functionalization methods for inorganic fillers are classified as dry or wet (Shi et al., 2006). Tran et al. (2010), for example, synthesized stearic acid-modified CaCO3 in Ca(OH)2 solution in situ and discovered that the corresponding water contact angle could reach 127.5°. In contrast, the water contact angle for dry-method-modified CaCO3 was only 110.3° (Jeong et al., 2009). As a result, wet modification method with a homogeneous treatment has a better functionalization effect than dry modification; however, it consumes a large amount of solvent and produces a significant amount of liquid waste, making it unsuitable for industrial-scale production. Therefore, it is highly desirable to develop a new chemical modification method that combines the benefits of dry and wet modification methods.
The gas—solid fluidization method was developed as a simple, efficient, and scalable strategy for chemically modifying CaCO3 filler. Additionally, the physicochemical properties of CaCO3 modified by gas—solid fluidization were compared with those of dry- and wet-modified products; the results confirmed this method’s excellent modification effect. The effects of surface modification methods and CaCO3 content on the crystalline properties, mechanical strength, and rheological performance of PBAT/CaCO3 composites were also investigated. The modification to gas—solid fluidization could significantly improve the interfacial compatibility between inorganic filler and polymer matrix, thereby laying the groundwork for large-scale preparation and application of high-performance biodegradable composites.
2 Experimental
2.1 Materials
PBAT (TH801T) pellets were provided by Xinjiang Lanshan Tunhe Polyester Co. (China). The PBAT samples had a melt flow index of 3.0–5.0 g/10 min (2.16 kg at 190°C), density of 1.20–1.28 g/cm3, and melting point of 110–120°C. The commercial CaCO3 powder was purchased from Lingshou Zhanteng Mineral Products Processing Plant (Hebei, China). Titanate was supplied by Shanghai Macklin Biochemical Technology Co. (China). And liquid paraffin was provided by Sinopharm Chemical Reagent Co. (Shanghai, China).
2.2 Surface modification of CaCO3
The pristine CaCO3 powder was dried at 80°C for 12 h before surface modification treatment to remove surface moisture. CaCO3 was gas—solid fluidized and modified by adding it into a glass fluidization reactor; 2.5% titanate coupling agent was added in the atomizing cup and mixed with liquid paraffin in a 1:1 mass ratio. The fluidization reactor was then placed in a vertical tube furnace. Next, the titanate coupling agent and liquid paraffin were atomized by an air compressor and reacted with CaCO3 at 60°C for 30 min (Figure 1); for the dry modification of CaCO3, they were then added to CaCO3 powder and reacted in a high-speed stirrer at 60°C for 30 min. Whereas, for the wet modification method, CaCO3 was dispersed into anhydrous ethanol (mass ratio 1:5), and then 2.5 wt.% titanate coupling agent and liquid paraffin were added into it and stirred at 60°C for 30 min. This sample was then filtered and dried at 80°C for 12 h.
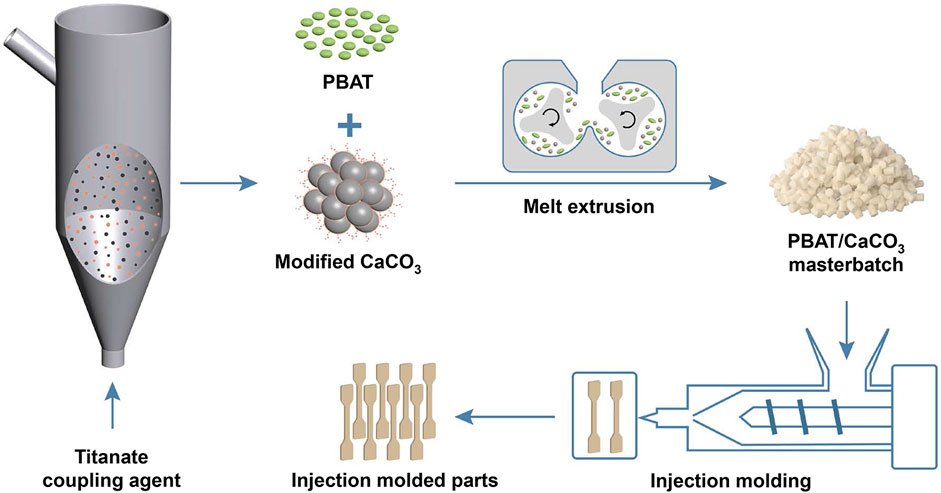
FIGURE 1. Schematic diagram for the preparation of gas—solid fluidization modified CaCO3 and the corresponding PBAT/CaCO3 composite.
2.3 Preparation of PBAT/CaCO3 composites
PBAT and CaCO3 in various mass ratios (Table 1) were mixed in a high-speed mixer before being added into a twin-screw extruder for blending and melt-extrusion, air-cooling, and pelletizing (Figure 1); the melting temperature was 160°C, and the extrusion rate was 90 rpm. The obtained pellet samples were dried at 80°C for 12 h to produce PBAT/CaCO3 composites. In addition, sample strips were created by extruding homogeneous pelletized blends through an injection molding machine in accordance with national standards (GB/T22554-2006) for tensile performance tests.
3 Results and discussion
3.1 Characterization of surface-modified CaCO3
3.1.1 Infrared spectral analysis
The surface chemical composition of the modified CaCO3 particles was studied using Fourier transform infrared (FT-IR) spectroscopy (Wang et al., 2010; Tang et al., 2014; Li et al., 2019); the results are shown in Figure 2A. The characteristic signals of unmodified CaCO3 particles are O–C–O in-plane bending vibration (728 cm−1), O–C–O out-of-plane bending vibration (882 cm−1), C–O asymmetric stretching vibration (1,019 cm−1), and C–O symmetric stretching vibration (1,448 cm−1). As compared to unmodified CaCO3, modified CaCO3 (CaCO3-d, CaCO3-w, and CaCO3-f) has characteristic absorption peaks of–CH3 (2,958 cm−1) and–CH2– (2,860 cm−1) stretching vibration. Meanwhile, compared with dry- and wet-modified CaCO3, the gas-solid fluidization modified product has stronger absorption peaks for–CH3 and–CH2– stretching vibration, verifying its excellent functionalization effect. These findings indicate that the long-chain alkyl groups of the titanate coupling agent have been encapsulated on the surface of CaCO3 particles. In addition, the modified CaCO3 particles exhibit a distinct absorption peak for C–Ti–O–CaCO3 at 1,024 cm−1, indicating that the surface groups of CaCO3 is converted from–OH to C–Ti–O–CaCO3 and the coupling agent is tightly adsorbed on the CaCO3 particle surface.
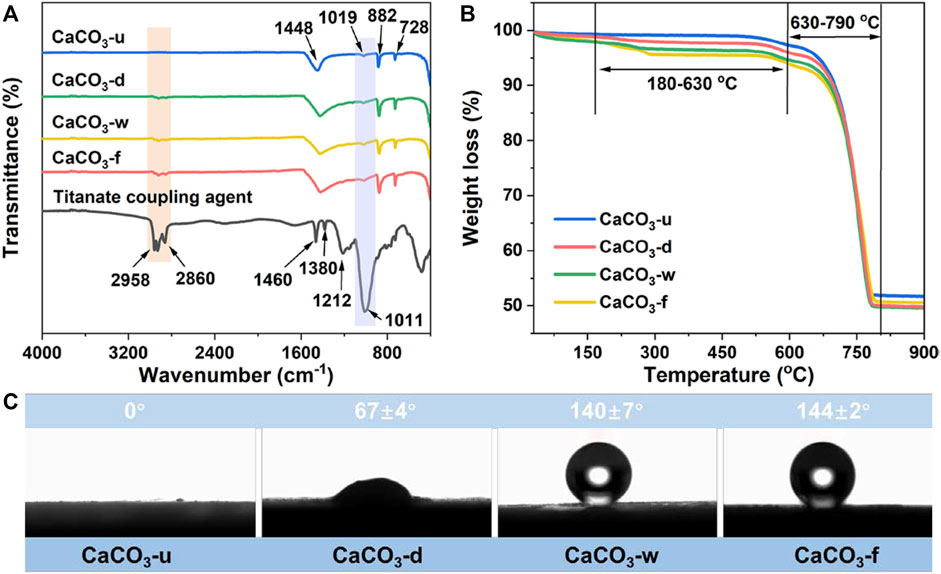
FIGURE 2. (A) FT-IR spectroscopy, (B) TGA, and (C) Water contact angle of CaCO3 samples prepared by different modification methods.
3.1.2 Thermogravimetric analysis
Thermal stability is an important parameter that could quantitatively reflect the amount of modification of coupling agent molecules (Tang et al., 2014); therefore, thermogravimetric analysis (TGA) was performed on CaCO3 particles before and after modification. The modified CaCO3 showed a progressive mass loss in the temperature range of 180°C–630°C due to the decomposition of titanate coupling and liquid paraffin attached to the CaCO3 particle surface (Figure 2B). Following that, a second mass loss occurs in the temperature range of 630°C–790°C due to the decomposition of CaCO3 into CaO and CO2. The mass loss of gas–solid fluidization modified CaCO3 is 5.27% in the temperature range of 180°C–630°C, which is higher than that of unmodified CaCO3 (.42%), dry-modified CaCO3 (2.85%), and wet-modified CaCO3 (4.83%). According to these findings, the gas–solid fluidization modification allows more titanate coupling agents to coat the surface of CaCO3.
3.1.3 Contact angle analysis
CaCO3 surface properties are crucial in determining its interfacial compatibility with polymer matrix (Jeong et al., 2009; Tran et al., 2010; Titone et al., 2020); therefore, the contact angles of unmodified and modified CaCO3 samples were tested to characterize hydrophobicity variation, and the results are shown in Figure 2C. Water droplets penetrate the powder sample so quickly that the observed contact angle is 0° because the unmodified CaCO3 is highly hydrophilic. The modification of titanate coupling agent treatment significantly increased the CaCO3 hydrophobicity, with corresponding contact angles increasing to 67°, 140°, and 144° for dry-, wet-, and gas–solid fluidization modified samples, respectively. CaCO3’s conversion from hydrophilic to lipophilic reduces its surface energy and improves the interfacial compatibility between the inorganic filler and polymer matrix. Notably, the hydrophobicity of CaCO3 modified by gas—solid fluidization is higher than that of dry and wet modification methods, indicating that the atomized coupling agent molecules could fully react with CaCO3 particles to form abundant chemical bonds.
3.2 Characterization of PBAT/CaCO3 composites
3.2.1 Crystallinity analysis
Because the crystallization and melting temperatures of the composite could directly reflect the interfacial compatibility between the inorganic filler and polymer matrix, differential scanning calorimetry analysis was performed to investigate the relevant parameters. The crystallization and melting temperatures of PBAT composites filled with different amounts of fluidization modified CaCO3 are shown in Figures 3A, B. The crystallization temperature of PBAT composites increases with the addition of CaCO3 (Figure 3A); this can be attributed to the formation of a coupling between CaCO3 and the PBAT matrix, which acts as a nucleus site for heterogeneous nucleation and causes PBAT molecules to crystallize further. For the complete melting of CaCO3-filled PBAT, higher enthalpy and temperature are required. As shown in Figure 3B, the melting temperature of PBAT composites increases and then decreases as the amount of added CaCO3 increases. When the CaCO3 content is 30 wt.%, the destructive effect on the composite material is very small, resulting in crystallization and a higher melting temperature; however, when the added content reaches 40 wt.%, the crystallinity rapidly decreases because the excessive content has a destructive effect on crystallization, resulting in a gradual decrease in the degree of crystallization of the composites. Furthermore, the higher the filler content is, the more obvious is the agglomeration phenomenon, which impedes molecular chain movement and makes the material less crystalline.
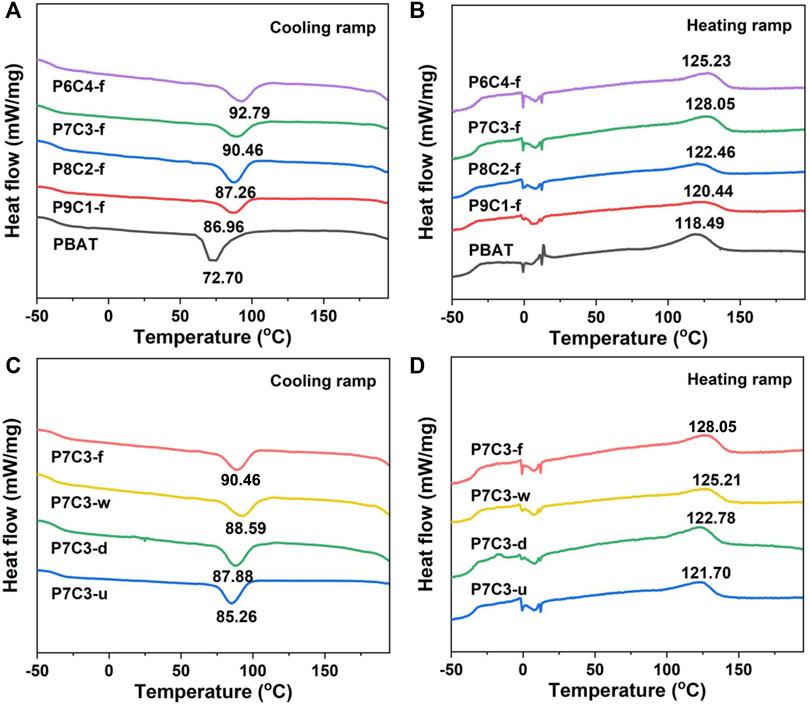
FIGURE 3. (A) Cooling and (B) heating ramps of PBAT composites filled with different amounts of gas–solid fluidization modified CaCO3. (C) Cooling and (D) heating ramps of PBAT composites filled with 30 wt.% CaCO3 modified by different methods.
Figures 3C, D show that the melting and crystallization temperatures of composites filled with 30 wt.% CaCO3 using various modified methods differ. The crystallinity of P7C3-u, P7C3-d, P7C3-w, and P7C3-f was calculated to be 26.98%, 28.22%, 33.01%, and 33.39%, respectively (Table 2). The crystallinity of P7C3-d is lower than that of P7C3-w and P7C3-f due to the poor nucleation ability of PBAT composites. It is demonstrated that as the crystallinity of the polymer matrix increases, the composites will have higher modulus, better thermal stability, and higher strength. As a result, the PBAT composites containing gas—solid fluidization modified CaCO3 have high crystallinity and effectively improve the interfacial compatibility between the filler and matrix molecules.
The degree of crystallinity (Χc) is estimated from ΔHm/ΔHm0 ωPBAT × 100%, where ΔHm is the fusion heat of the sample, ΔHm0 is the melting enthalpy that equal 114J/g for PBAT, and ωPBAT is the mass content of PBAT in the composite.
3.2.2 Rheological properties
The rheological properties of PBAT/CaCO3 composites were investigated to determine the dispersibility of inorganic filler in the polymer matrix and intermolecular interactions. Figures 4A–C depict the frequency dependence of PBAT composites filled with various amounts of gas—solid fluidized modified CaCO3. Figure 4A shows that the storage modulus (G′) of PBAT composites increases with increasing frequency, which can be attributed to the chain segment of PBAT macromolecules being unable to keep up with the shear rate and thus resisting the shear stress, resulting in a greater resistance with higher frequency. Furthermore, the G′ values increase as the CaCO3 content increases because the addition of CaCO3 improves the interaction of the blended system and requires more energy for deformation. Figure 4B depicts the variation of the loss modulus (G″) with the addition of gas–solid fluidization modified CaCO3. The G″ values, for both pure PBAT and PBAT/CaCO3 composites, increase as frequency increases. As frequency increases, so does intermolecular friction and loss capacity, resulting in a higher loss modulus. The interactions between PBAT macromolecular chains and CaCO3 particles play a decisive role in the intermolecular friction in PBAT composites filled with varying amounts of CaCO3. As a result, the increased CaCO3 causes higher energy loss due to friction. Figure 4C depicts the change in complex viscosity with the addition of gas—solid fluidization modified CaCO3. The PBAT/CaCO3 composite viscosity is higher in the low-frequency region than that in the high-frequency region, indicating shear thinning behavior. Meanwhile, the PBAT/CaCO3 composite viscosity increases with filler content, indicating that the chemical modification treatment significantly increases intermolecular fusion between PBAT and CaCO3, thereby impeding molecular chain movement.
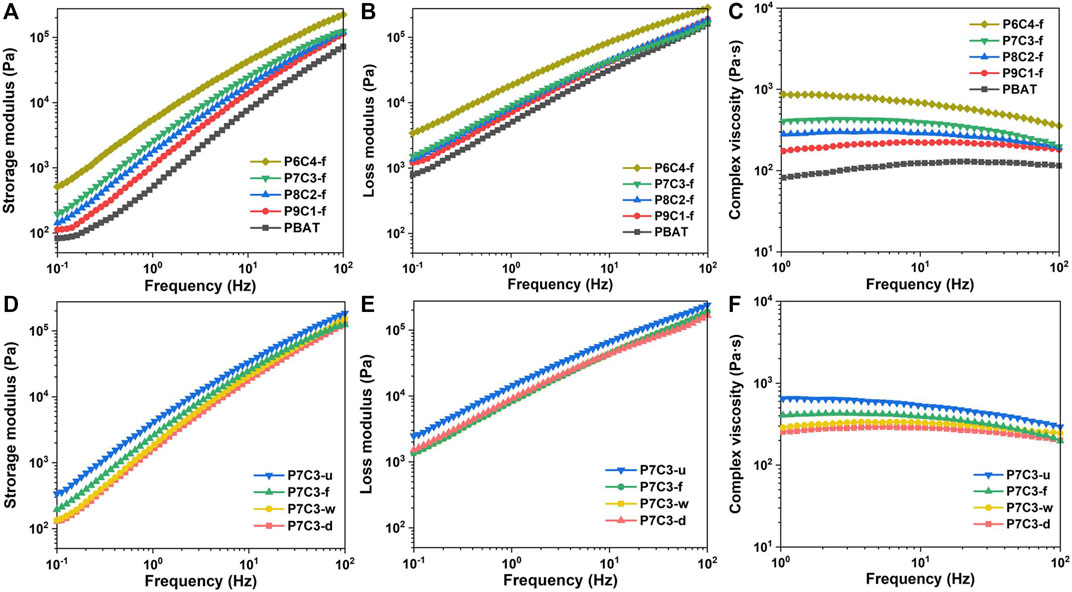
FIGURE 4. (A) Storage modulus, (B) loss modulus, and (C) complex viscosities of PBAT composites filled with different content of gas–solid fluidization modified CaCO3. (D) Storage modulus, (E) loss modulus, and (F) complex viscosities of PBAT composites filled with 30 wt.% CaCO3 obtained by different modification methods.
Figures 4D, E show the variation of storage and loss modulus with frequency for composites filled with 30 wt.% CaCO3 and modified in various ways. Chemical modification treatment reduces the mobility of molecule chains, resulting in a longer relaxation time and lower energy storage modulus when compared to an unmodified PBAT/CaCO3 composite. Figure 4F depicts the variation in viscosity with frequency for composites filled with various concentrations of modified CaCO3. The modified CaCO3-filled composites have a higher viscosity than the unmodified ones due to improved interfacial compatibility, which facilitates intermolecular movement and, thus, reduces viscosity. Furthermore, the PBAT composite filled with gas—solid fluidization modified CaCO3 has the lowest viscosity, indicating that the coupling agent and PBAT molecular chains are effectively cross-linked.
3.2.3 Mechanical strength
Tensile strength and elongation at break were used to evaluate the mechanical properties of the composites for determining the effect of filler modification methods and content on them. Figure 5 depicts the results. Overall, the order of tensile strength and elongation at break is PBAT > P9C1 > P8C2 > P7C3 > P6C4 because in the blended system, as the filler amount increases, the mechanical properties decrease due to the poor compatibility between CaCO3 and PBAT. Furthermore, the high CaCO3 content will result in non-uniform dispersion and obvious agglomeration, resulting in decreased mechanical properties. The overall experimental result for the chosen CaCO3 filling amount is 30 wt.%, which not only maintains the performance of the composite material but also reduces its cost.
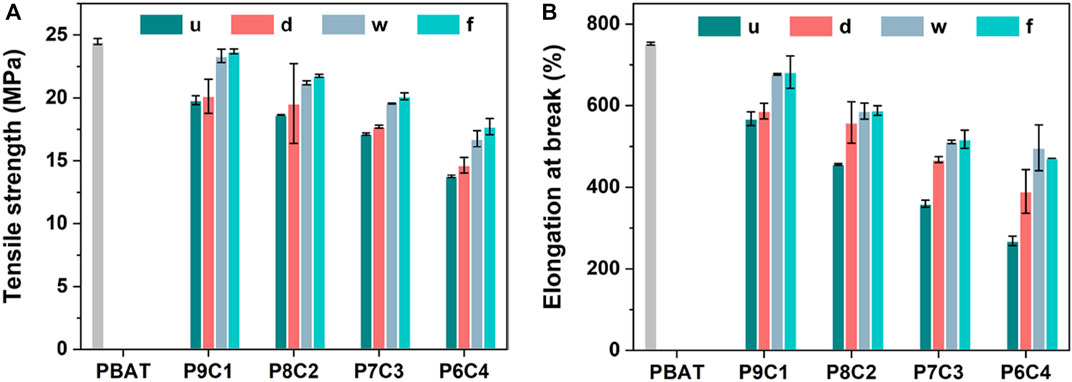
FIGURE 5. (A) Tensile strength and (B) elongation at break of PBAT composites filled with different content and modification method of CaCO3.
The tensile strength and elongation at break of PBAT composites filled with 30 wt.% modified CaCO3 were higher than those of unmodified CaCO3 due to the plasticizing effect of the coupling agent alkyl chains increasing the composite interfacial bonding energy; however, there is no interaction between the two phases of the matrix without the modifier, and it behaves as a brittle material. The results showed that adding the modifier significantly improved the mechanical properties of the composites. The tensile strengths of PBAT composites filled with modified CaCO3 (P7C3-d, P7C3-w, and P7C3-f) were increased by 3%, 14%, and 17%, respectively, compared with the unmodified CaCO3; and the corresponding elongation at break increased by 30%, 42%, and 44%, respectively. The relatively higher tensile strength and elongation at break of PBAT composites filled with gas–solid fluidization modified CaCO3 were attributed to the uniform distribution of the modifier molecules on the surface of CaCO3 during the gas—solid fluidized modification method, which resulted in better dispersion of the modified CaCO3 in the PBAT matrix and promoted the cross-linking of PBAT with the modified CaCO3, significantly improving the strength and toughness of the composite. As a result, the overall mechanical properties of the composites, such as strength and toughness, were significantly improved.
3.2.4 Morphological analysis
Morphological analysis of the blends is frequently used to help us understand their compatibility and dispersion. Figures 6A–P depict scanning electron microscope (SEM) morphological images of PBAT composites filled with various CaCO3 contents and modification methods. According to the cross-sectional comparison in Figure 6, when the filler content was increased from 10 to 30 wt.%, CaCO3 was uniformly dispersed on the cross-sectional surface of the blends, and the surface was relatively flat, but when the filler content was increased to 40 wt.%, the tendency to form agglomerates was more obvious, and the interfacial compatibility was poor, resulting in poor performance of the composite. As a result, the optimal amount of CaCO3 filler preferred to be added is 30 wt.%. According to the longitudinal comparison in Figure 6, the general improvement in the apparent morphology of PBAT composites filled with dry-modified CaCO3 is due to poor dispersion uniformity and poor titanate modification effect by dry modification, which further leads to poor particle–matrix interfacial compatibility. In contrast, PBAT composites filled with gas—solid fluidization modified CaCO3 resulted in improved CaCO3 particle agglomeration, with large crystal size and low degree of agglomeration. Furthermore, the CaCO3 filler was well embedded in the PBAT matrix, and the two were more tightly bonded, resulting in improved composite performance.
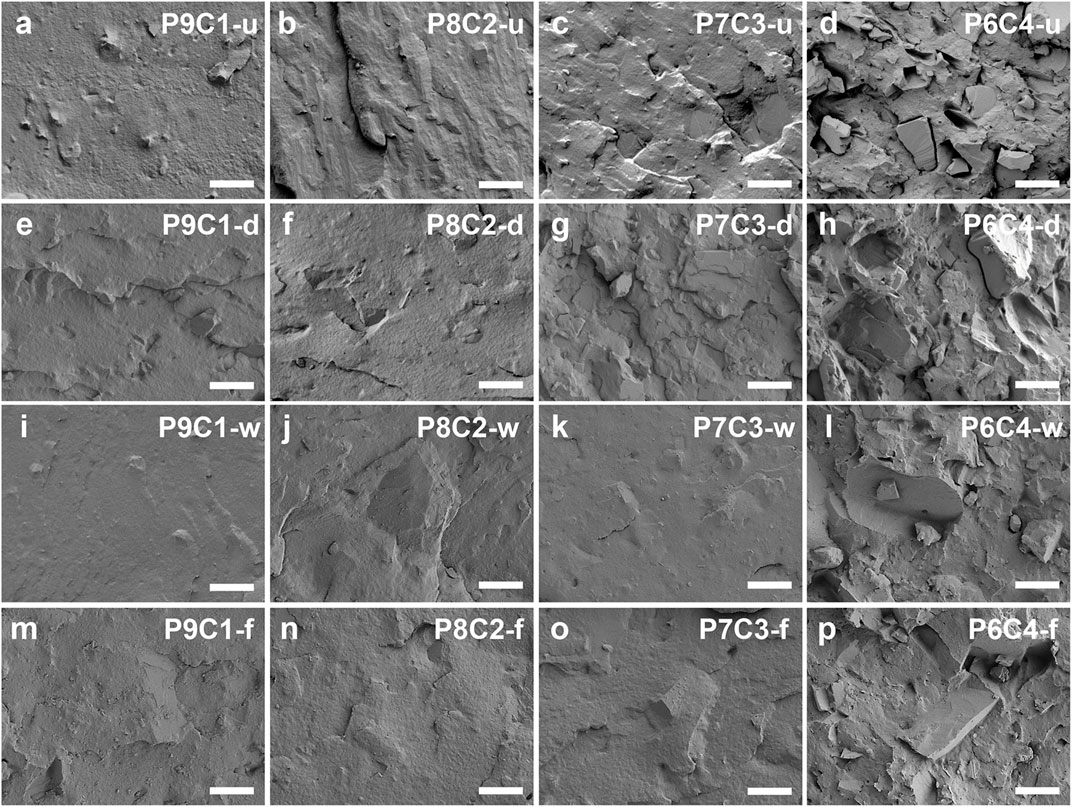
FIGURE 6. SEM images of PBAT composites filled with (A) 10, (B) 20, (C) 30, and (D) 40 wt.% of unmodified CaCO3; composites filled with (E) 10, (F) 20, (G) 30, and (H) 40 wt.% of dry-modified CaCO3; composites filled with (I) 10, (J) 20, (K) 30, and (L) 40 wt.% of wet-modified CaCO3; and composites filled with (M) 10, (N) 20, (O) 30, and (P) 40 wt.% of gas—solid fluidization modified CaCO3. The scale bar length is 20 µm.
4 Conclusion
A gas—solid fluidization method was proposed in this work to modify CaCO3. To generate biodegradable PBAT/CaCO3 composites, the modified CaCO3 filler was melt blended with PBAT and injection molded. The effects of various modification methods and filling amounts on the crystalline, mechanical, and rheological properties of PBAT/CaCO3 composites were investigated for comparison with dry and wet methods. The results showed that PBAT composites filled with gas—solid fluidization modified CaCO3 (at 30 wt.%) improved crystallinity (33.39%), and had excellent mechanical and rheological properties with uniform dispersion and interfacial compatibility. Therefore, the strategy proposed in this work provides an efficient modification method for preparing PBAT/CaCO3 composites that are low in cost and high in performance and can be applied more effectively in the field of ground film and other plastics.
Data availability statement
The original contributions presented in the study are included in the article/supplementary material, further inquiries can be directed to the corresponding author.
Author contributions
CH conceived the idea. JS, CL, and CH designed the experiments and wrote the manuscript. JS performed the experiments. YS, MY, and LL discussed the results and commented on the manuscript.
Funding
This work is financially supported by the Key Research Program of Nanjing IPE Institute of Green Manufacturing Industry.
Conflict of interest
The authors declare that the research was conducted in the absence of any commercial or financial relationships that could be construed as a potential conflict of interest.
Publisher’s note
All claims expressed in this article are solely those of the authors and do not necessarily represent those of their affiliated organizations, or those of the publisher, the editors and the reviewers. Any product that may be evaluated in this article, or claim that may be made by its manufacturer, is not guaranteed or endorsed by the publisher.
References
Biundo, A., Hromic, A., Pavkov-Keller, T., Gruber, K., Quartinello, F., Haernvall, K., et al. (2016). Characterization of a poly(butylene adipate-co-terephthalate)- hydrolyzing lipase from Pelosinus fermentans. Appl. Microbiol. Biotechnol. 100, 1753–1764. doi:10.1007/s00253-015-7031-1
Camani, P. H., Souza, A. G., Barbosa, R. F. S., Zanini, N. C., Mulinari, D. R., and Rosa, D. S. (2021). Comprehensive insight into surfactant modified-PBAT physico-chemical and biodegradability properties. Chemosphere 269, 128708. doi:10.1016/j.chemosphere.2020.128708
Cavalcanti, F. N., TeóFILO, E. T., Rabello, M. S., and Silva, S. M. L. (2007). Chain extension and degradation during reactive processing of PET in the presence of triphenyl phosphite. Polym. Eng. Sci. 47, 2155–2163. doi:10.1002/pen.20912
Chen, J.-F., Wang, J.-X., Liu, R.-J., Shao, L., and Wen, L.-X. (2004). Synthesis of porous silica structures with hollow interiors by templating nanosized calcium carbonate. Inorg. Chem. Commun. 7, 447–449. doi:10.1016/j.inoche.2004.01.003
Doufnoune, R., Chebira, F., and Haddaoui, N. (2003). Effect of titanate coupling agent on the mechanical properties of calcium carbonate filled polypropylene. Int. J. Polym. Mater. 52, 967–984. doi:10.1080/714975875
Han, Y., and Kim, H. (2012). Surface modification of calcium carbonate with cationic polymer and their dispersibility. Mater. Trans. 53, 2195–2199. doi:10.2320/matertrans.m2012236
Jeong, S.-B., Yang, Y.-C., Chae, Y.-B., and Kim, B.-G. (2009). Characteristics of the treated ground calcium carbonate powder with stearic acid using the dry process coating system. Mater. Trans. 50, 409–414. doi:10.2320/matertrans.mrp2008351
Kasirajan, S., and Ngouajio, M. (2012). Polyethylene and biodegradable mulches for agricultural applications: A review. Agron. Sustain. Dev. 32, 501–529. doi:10.1007/s13593-011-0068-3
Kemal, I., Whittle, A., Burford, R., Vodenitcharova, T., and Hoffman, M. (2013). Toughening of unmodified polyvinylchloride through the addition of nanoparticulate calcium carbonate and titanate coupling agent. J. Appl. Polym. Sci. 127, 2339–2353. doi:10.1002/app.37774
Li, C.-Q., Liang, C., Chen, Z.-M., Di, Y.-H., Zheng, S.-L., Wei, S., et al. (2021). Surface modification of calcium carbonate: A review of theories, methods and applications. J. Central South Univ. 28, 2589–2611. doi:10.1007/s11771-021-4795-6
Li, J., Lai, L., Wu, L., Severtson, S. J., and Wang, W.-J. (2018). Enhancement of water vapor barrier properties of biodegradable poly(butylene adipate-co-terephthalate) films with highly oriented organomontmorillonite. ACS Sustain. Chem. Eng. 6, 6654–6662. doi:10.1021/acssuschemeng.8b00430
Li, J., Yang, S., Liu, Y., Muhammad, Y., Su, Z., and Yang, J. (2019). Studies on the properties of modified heavy calcium carbonate and SBS composite modified asphalt. Constr. Build. Mater. 218, 413–423. doi:10.1016/j.conbuildmat.2019.05.139
Madhavan Nampoothiri, K., Nair, N. R., and John, R. P. (2010). An overview of the recent developments in polylactide (PLA) research. Bioresour. Technol. 101, 8493–8501. doi:10.1016/j.biortech.2010.05.092
Mantia, F. P. L., Morreale, M., Scaffaro, R., and Tulone, S. (2013). Rheological and mechanical behavior of LDPE/calcium carbonate nanocomposites and microcomposites. J. Appl. Polym. Sci. 127, 2544–2552. doi:10.1002/app.37875
Mondal, D., Bhowmick, B., Mollick, M. M. R., Maity, D., Ranjan Saha, N., Rangarajan, V., et al. (2014). Antimicrobial activity and biodegradation behavior of poly(butylene adipate-co-terephthalate)/clay nanocomposites. J. Appl. Polym. Sci. 131. doi:10.1002/app.40079
Mukhopadhyay, N., Panwar, A. S., Kumar, G., Samajdar, I., and Bhattacharyya, A. R. (2015). Influence of non-covalent modification of multiwalled carbon nanotubes on the crystallization behaviour of binary blends of polypropylene and polyamide 6. Phys. Chem. Chem. Phys. 17, 4293–4310. doi:10.1039/c4cp05060f
Sheng, Y., Zhou, B., Zhao, J., Tao, N., Yu, K., Tian, Y., et al. (2004). Influence of octadecyl dihydrogen phosphate on the formation of active super-fine calcium carbonate. J. Colloid Interface Sci. 272, 326–329. doi:10.1016/j.jcis.2003.11.062
Shi, Q., Wang, L., Yu, H., Jiang, S., Zhao, Z., and Dong, X. (2006). A novel epoxy resin/CaCO3 nanocomposite and its mechanism of toughness improvement. Macromol. Mater. Eng. 291, 53–58. doi:10.1002/mame.200500223
Tang, Z., Cheng, G., Chen, Y., Yu, X., and Wang, H. (2014). Characteristics evaluation of calcium carbonate particles modified by surface functionalization. Adv. Powder Technol. 25, 1618–1623. doi:10.1016/j.apt.2014.05.017
Titone, V., La Mantia, F. P., and Mistretta, M. C. (2020). The effect of calcium carbonate on the photo-oxidative behavior of poly(butylene adipate-co-terephthalate). Macromol. Mater. Eng. 305, 2000358. doi:10.1002/mame.202000358
Tran, H. V., Tran, L. D., Vu, H. D., and Thai, H. (2010). Facile surface modification of nanoprecipitated calcium carbonate by adsorption of sodium stearate in aqueous solution. Colloids Surfaces A Physicochem. Eng. Aspects 366, 95–103. doi:10.1016/j.colsurfa.2010.05.029
Upadhyaya, P., Nema, A. K., Sharma, C., Kumar, V., Agrawal, D. D., and Kumar, M. (2012). Physicomechanical study of random polypropylene filled with treated and untreated nano-calcium carbonate. J. Thermoplast. Compos. Mater. 26, 988–1004. doi:10.1177/0892705711433349
Wang, C., Sheng, Y., Hari, B., Zhao, X., Zhao, J., Ma, X., et al. (2007). A novel aqueous-phase route to synthesize hydrophobic CaCO3 particles in situ. Mater. Sci. Eng. C 27, 42–45. doi:10.1016/j.msec.2006.01.003
Wang, Z. H., Chen, J. H., Yin, W. Z., and Han, Y. X. (2010). Study on the surface modification of nanometer calcium carbonate. Adv. Mater. Res. 92, 229–234. doi:10.4028/www.scientific.net/amr.92.229
Wei, X. Y., Ren, L., Sun, Y. N., Zhang, X. Y., Guan, X. F., Zhang, M. Y., et al. (2021). Sustainable composites from biodegradable poly(butylene succinate) modified with thermoplastic starch and poly(butylene adipate-co-terephthalate): Preparation and performance. New J. Chem. 45, 17384–17397. doi:10.1039/d1nj03208a
Xing, Q., Buono, P., Ruch, D., Dubois, P., Wu, L., and Wang, W.-J. (2019). Biodegradable UV-blocking films through core–shell lignin–melanin nanoparticles in poly(butylene adipate-co-terephthalate). ACS Sustain. Chem. Eng. 7, 4147–4157. doi:10.1021/acssuschemeng.8b05755
Zapata, P. A., Palza, H., Diaz, B., Armijo, A., Sepulveda, F., Ortiz, J. A., et al. (2018). Effect of CaCO(3) nanoparticles on the mechanical and photo-degradation properties of LDPE. Molecules 24, 126. doi:10.3390/molecules24010126
Zhai, X., Wang, W., Zhang, H., Dai, Y., Dong, H., and Hou, H. (2020). Effects of high starch content on the physicochemical properties of starch/PBAT nanocomposite films prepared by extrusion blowing. Carbohydr. Polym. 239, 116231. doi:10.1016/j.carbpol.2020.116231
Keywords: gas—solid fluidization, chemical modification, biodegradable composites, rheological properties, mechanical properties
Citation: Shang J, Li C, Song Y, Yan M, Li L and Hu C (2023) Gas-solid fluidization modification of calcium carbonate for high-performance poly (butylene adipate-co-terephthalate) (PBAT) composites. Front. Chem. 10:1119978. doi: 10.3389/fchem.2022.1119978
Received: 09 December 2022; Accepted: 28 December 2022;
Published: 12 January 2023.
Edited by:
Heng Zhang, Guizhou University, ChinaCopyright © 2023 Shang, Li, Song, Yan, Li and Hu. This is an open-access article distributed under the terms of the Creative Commons Attribution License (CC BY). The use, distribution or reproduction in other forums is permitted, provided the original author(s) and the copyright owner(s) are credited and that the original publication in this journal is cited, in accordance with accepted academic practice. No use, distribution or reproduction is permitted which does not comply with these terms.
*Correspondence: Chaoquan Hu, Y3FodUBpcGUuYWMuY24=