- 1Innovation Centre for Nanomaterials in Energy and Environment (ICNEE), School of Chemical and Environmental Engineering, Wuhan Polytechnic University, Wuhan, Hubei, China
- 2Wuhan Coobase Facilities Company Limited, Wuhan, Hubei, China
A honeycomb rotary wheel fabricated from sheet adsorbent of silica gel is a competitive drying facility for air dehumidification in modern drying and air conditioning industries due to its large contacting area (3,000 m2/m3) and the rapid diffusion of the adsorbate compared to silica gel pellets. The delicate preparation procedure of hygroscopic silica gel is paramount for improved adsorption capacity by optimizing the surface area, pore size, and pore volume of silica gel. In this article, silica gel adsorbent in a honeycomb rotary wheel was fabricated by neutralizing the impregnated water glass solution with a modulus of 3.3 on the glass fiber sheet of the honeycomb matrix using CO2 at different pressure at room temperature instead of corrosive acids. The as-obtained silica gel absorbent was characterized by XRD, scanning electron microscopy (SEM), specific surface area and pore size analysis, and dynamic vapor/gas sorption analysis. The results showed that the as-obtained silica gel adsorbent is uniform in size and tunable in terms of specific surface area, pore size, pore volume, and adsorption capacity by CO2 pressure. The typical silica gel fabricated by CO2 of 0.25 MPa with a specific surface area of 764.86 m2/g, an average micropore size with a diameter of 2.94 nm, and a pore volume of 0.45 ml/g delivers a saturated adsorption capacity of as high as 287.24 mg/g at RH 50%, which is the best in adsorption performance compared to the previously reported results. This provides a new strategy for environment-friendly manufacturing of silica gel adsorbent in honeycomb rotary wheels for air dehumidification.
Introduction
Air humidity has always been drawing a worldwide concern both in our daily life and in various conventional (food, cosmetics, papermaking, pharmaceuticals, etc.) and emerging industries (microelectronics, lithium-related batteries, etc.) due to its role with respect to air quality and its requirement for the manufacture, preservation, transportation, and further processing of products (Aristov et al., 2002; Wu et al., 2018). Thus, air dehumidification technology has been attracting extensive interest academically and industrially. The traditional direct dehumidification technologies mainly consist of condensing dehumidification, heating dehumidification, membrane dehumidification, and liquid desiccant dehumidification, in which the relevant environmental issues owing to the utilization of a non-environment-friendly refrigerant, the energy-intensive requirement, high-cost membrane fabrication, etc. impede their further development, especially in today’s ever-increasing climate deterioration (Cha et al., 2007; Hwang et al., 2007; Bhagat et al., 2008; Iswar et al., 2017). In recent years, an adsorptive dehumidification technology by solid regenerable desiccant to selectively remove and separate the moisture from moist air under ambient conditions shows great promise for future air dehumidification (Kabeel, 2007; Bareschino et al., 2015).
Thus far, four types of solid desiccant dehumidifiers as adsorptive dehumidification technology have been proposed, namely, solid packed beds, rotating horizontal beds, multiple vertical beds, and honeycomb rotary wheels, among which only the honeycomb rotary wheels integrate the dehumidifier and desorption processes into one, demonstrating the lower pressure drop and large surface area for heat and mass transfer with respect to the desirable characteristics, such as high space efficiency, continuous adsorption–desorption cycles, high dehumidification, and utilization of low-grade heat sources, such as solar energy and waste heat, for adsorbent regeneration (Chung et al., 2001; Bhagat et al., 2008; Hindersmann, 2019). As a state-of-the-art solid desiccant dehumidification technology, the honeycomb rotary wheel consists of numerous parallel airflow passageway constructed typically with alternating sinusoidal corrugated fibrous substrate sheets and flat fibrous substrate sheets on whose surface a solid desiccant material is impregnated. As such, the widely dispersed desiccants work based on the famous Kelvin formula which shows the vapor pressure difference between the air and the desiccant to attract the moisture from the air until its vapor pressure is in equilibrium with the air. (Kodama et al., 1993; Jia et al., 2006).
The performance of the solid desiccant honeycomb rotary wheel depends, to a large extent, upon the characteristics of the desiccant materials such as high dehumidification capacity, fast kinetics, high stability, and the ability to regenerate at a low temperature. Silica gel is the most popular solid desiccant usually used in the honeycomb rotary wheel due to its low cost, high porosity, and excellent stability although it has a limited dehumidification capacity of 20%–30% of its initial weight and higher regeneration temperature of 60–100°C (Kuma and Hirose, 1996; La et al., 2010; Lee and Lee, 2012; Li et al., 2016). As we know, desiccant dehumidifies in that desiccants have open empty spaces between the molecules called capillaries. As such, the hygroscopic performance of the silica gel is determined by its intrinsic physical/chemical properties and the surface porous (capillary) structure including surface area, pore volume, average pore size, and pore size distribution, which are affected by the preparation procedures/variables of silica gel (Kodama et al., 1993; Neti and Wolfe, 2000; Liu, 2003; Manjunatha et al., 2013).
The general manufacturing variables of silica gel are quite complex including the type of starting materials, catalyst, solvent, reaction temperature, gelation schemes, drying temperature, etc. Many research works have investigated in detail the effects of the preparation procedure on the surface characteristics of silica gel. Especially for the silica gel used in the honeycomb rotary wheel with glass fibers as substrate, water glass is generally employed to act as the type of starting material due to its availability, low cost, and environment friendliness (Sarawade et al., 2010; O’Connor et al., 2016; Prasad et al., 2019). The different preparation procedures of silica gel by neutralization using different acids such as HCl, H3PO4, H2SO4, HNO3, and HCOOH were investigated to obtain the different surface characteristics of silica gel and thus the different dehumidification properties, which are also adopted to manufacture industrially silica gel desiccant in the honeycomb rotary wheel (Zhang et al., 2003; White et al., 2011; Wu et al., 2018; Yang et al., 2020). However, the usages of strong acids are unfavorable to operation and the environment due to their corrosion or volatility (Wang et al., 2013; Wei et al., 2013; Su et al., 2021). Herein, to our knowledge, it is the first time in this work to report that CO2 as nontoxic greenhouse gas was employed to neutralize the starting material water glass to prepare silica gel desiccant in the honeycomb rotary wheel and the preparation variables including CO2 pressure and the reaction time were optimized, the resulting silica gel desiccant in the honeycomb rotary wheel exhibits excellent surface characteristics and thus good dehumidification characteristics.
Experimental
Preparation of honeycomb silica gel
The flat glass fiber paper (Ahlstrom-Munksjo glassfibre Oy, Kotka, Finland) was cut to be 10 × 10 cm square and was rolled down to be corrugated glass fiber paper with colloidal silica (10 wt%, Chemical Engineering Sci.and Tech. Ltd. Company, Henan, China). Then, the flat and the prepared corrugated glass fiber paper were stacked alternately with a thickness of 10 cm to form a honeycomb monolith. The as-obtained honeycomb monolith was impregnated with water glass (ca. 3.3 modulus, 40 wt%, Haobo Chemical Engineering Ltd. Company, Shandong, China) for 2 hours and taken out to dry incompletely. The water glass-impregnated honeycomb monolith was placed in a high-pressure reactor and subjected to CO2 at different pressure for 3–5 h. After the reaction was complete, the honeycomb monolith was washed to remove the carbonate until the solution is close to being neutral followed by the aging in the deionized water for 2 h at 40°C. Finally, the honeycomb monolith with silica gel was completed by drying and calcination.
Characterization of honeycomb silica gel
The powder X-ray diffraction (XRD) patterns were collected on a Japan Shimadzu DX-7000 advanced X-ray diffractometer using the Cu Kα radiation with λ = 0.15418 nm over 2θ degree from 10° to 70° at a scan rate of 4° min−1. Scanning electron microscopy (SEM) images were performed on a JEOL JSM-6700M scanning electron microscopy. Nitrogen physisorption was carried out at −196
Adsorption/desorption kinetics and isotherms of water vapor
The adsorption/desorption kinetics and isotherms of the water vapor on the silica gel were measured on a gravity dynamic vapor system (BSD-VVS, BeiShiDe Instrument). Before the measurement of vapor adsorption, the samples were dried at 200
Results and discussion
Silica gel as a solid desiccant in a honeycomb rotary wheel is thought to be environmentally friendly and its desiccant capacity is dependent on its surface structure including specific surface area, pore volume, pore size, etc. As such, it is vital to choose a suitable and clean fabrication procedure to tune the surface structure of the silica gel solid desiccant in a honeycomb rotary wheel. Indeed, the surface structure of silica gel is affected by many preparation variables consisting of starting materials, catalyst, reaction temperature and time, aging temperature and time, etc. So, it is difficult to control elaborately the preparation procedure to obtain the desirable silica gel with excellent desiccant capacity (Zhang et al., 2006; Zheng et al., 2014). In this work, water glass was used as a green and low-cost raw material for the preparation of silica gel desiccant in a honeycomb rotary by the neutralization of acids. Although it is more difficult to result in the good surface structure of silica gel than organic silicon as a starting material because inorganic salt yielded during the neutralization in the solution impacts greatly the gelatinization of the silica sol, water glass could be used as an adhesive agent for the formation of honeycomb monolith without any other organic adhesive introduction. More importantly, CO2 gas as the neutralized acid should be able to relieve the salt effect in the solution due to the usage of liquid acid on the gelation of silica sol. As demonstrated in Figure 1 for the monolith and the XRD pattern of the as-obtained honeycomb silica gel by the reaction of water glass and CO2, it can be seen that there is a weak broadening band at about 23o without any diffraction peaks of impurity, revealing the typical amorphous nature of SiO2 and thus a feasible preparation approach.
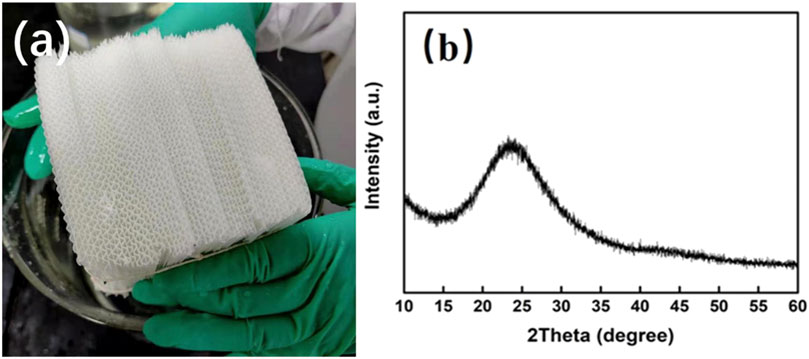
FIGURE 1. (A) Typical photograph of the as-obtained honeycomb silica gel with CO2 as the neutralized agent; (B) typical XRD pattern of silica gel powder detached from the honeycomb monolith.
Figure 2 shows the SEM images of the obtained honeycomb silica gel at a different state. From Figures 2A–C, it can be seen that the prepared silica gel is gelatinized well with a smooth and uniform surface, which could be further verified by the SEM images of the cross section of honeycomb silica gel monolith in Figures 2D–F, illustrating the complete reaction of water glass with CO2 to implement the polymerization between SiO2 molecules during gelatinization. From Figures 2G–I, it is indicated that the prepared silica gel is dispersed evenly between the networks of glass fiber paper, allowing the available maximal exposed surface, which is favorable to promote the adsorption capacity. Although it is not observed obviously the surface microstructure of the prepared silica gel by glass fiber paper as a substrate, the texture of the monolith is indicated to disperse widely the silica gel on fiber gel paper so that the pretty large contact area of the silica gel with vapor for desiccant is obtained, which shall be verified further by the following characterized surface structure including specific surface area, pore volume, pore diameters.
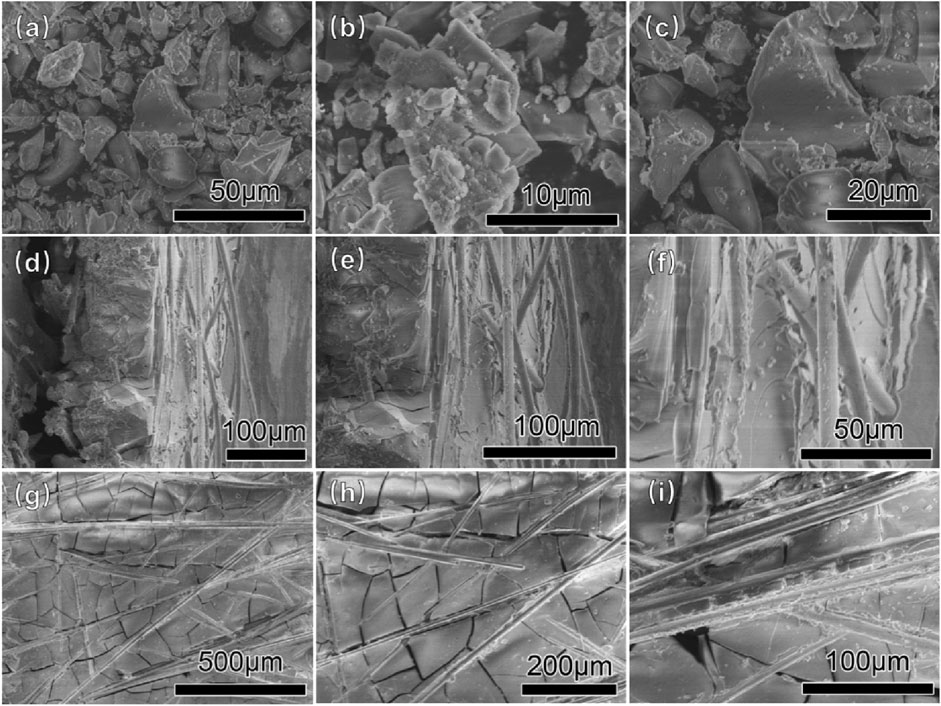
FIGURE 2. Typical SEM images of the as-obtained honeycomb silica gel with CO2 as the neutralized agent. (A–C) Silica gel powder detached from the honeycomb matrix; (D–F) cross section of honeycomb matrix; and (G–I) surface of the honeycomb matrix.
To optimize the effect of CO2 pressure on the surface structure, the preparation of the honeycomb silica gel using water glass as starting material was investigated at different CO2 pressure at ambient temperature. The nitrogen adsorption and desorption isotherms of the as-obtained honeycomb silica gel are shown in Figure 3. As indicated in Figure 3, all isotherms are identified as the typical Type IV, which are the characteristic isotherms of mesoporous materials at any pressure of CO2, preferably used as a desiccant as well. Nonetheless, the different isotherms at different pressure of CO2 demonstrate the different surface structures of the prepared honeycomb silica gel, displaying the regularity of CO2 on the surface structure of silica gel with the exception of the acid effect for the neutralization of water glass. As shown in Figure 4 for the changed surface structure with CO2 pressure including the pore size distribution, pore size, and pore volume, it could be seen that the most probable pore size between 2 and 10 nm is further evidence of the above typical Type IV BET isotherms of mesoporous materials although the pore size difference with CO2 pressure is markable, which should be embodied from the accumulative pore volume change with CO2 pressure. As known generally, the reaction of CO2 with water glass should be the neutralization of water glass by carbonic acid generated by CO2 and H2O, thus, CO2 pressure affects the reaction rate due to CO2 pressure dependence of CO2 concentration so that the surface structure of the generated silica gel is varied. All the detailed surface structure data of the prepared honeycomb silica gel at different CO2 were compiled in Table 1. From Table 1, it is clear that the surface structure of the prepared honeycomb silica gel is varied greatly with CO2 pressure, which could be explained by the famous Kelvin formula, as shown in the following equation:
where R is the gas constant, T is the thermodynamic temperature of the system, P2 and P1 are the saturated vapor pressure at different curved diameters R2 and R1, respectively, M is the molar mass of water, ρ is the density of water.
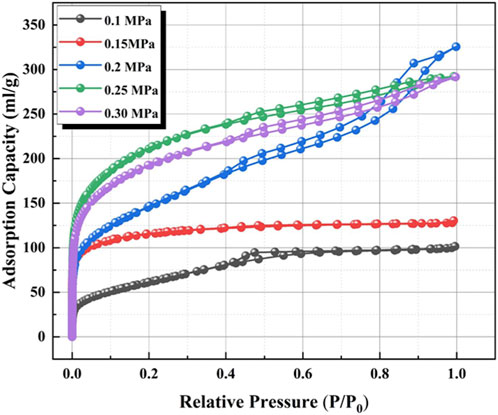
FIGURE 3. Nitrogen adsorption and desorption isotherms of the as-obtained honeycomb silica gel using water glass as the starting material at different CO2 pressures.
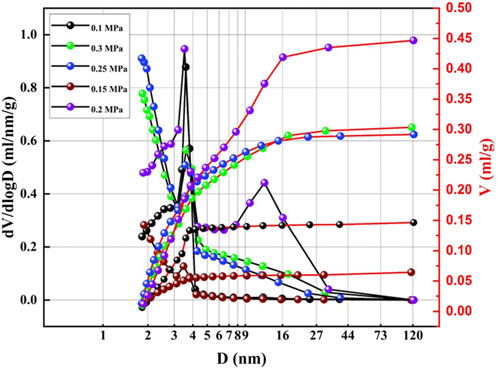
FIGURE 4. BJH (desorption) pore volume and pore size logarithm curves of the as-obtained honeycomb silica gel using water glass as the starting material at different CO2 pressures.
From Eq. 1, it is clear that the saturated vapor pressure at constant temperature is dependent on the pore diameter, and the larger the pore diameter, the larger the saturated vapor pressure. Thus, the adsorption capacity of desiccant is directly related to the pore volume and the specific surface area of desiccant with the average pore diameter of the mesopore (2–50 nm). Thus, the optimized CO2 pressure for the preparation of the honeycomb silica gel is about 0.25 MPa, which might be contributed to the unique gas acid effect with rapid diffusion.
To investigate the adsorptive characteristic of the prepared honeycomb silica gel, the adsorption/desorption kinetics was carried out at different humidity, as shown in Figure 5 for the typical adsorption/desorption kinetics at different humidity for the as-obtained honeycomb silica gel at CO2 pressure of 0.25 MPa. From Figure 5, it can be seen that the prepared silica gel at CO2 pressure of 0.25 MPa exhibits adsorptive ability at different relative humidity, which is indispensable for desiccant dehumidification used in industry due to the hash requirement of products to air humidity. Moreover, it could be further desorpted after saturated adsorption, exhibiting the cycling adsorption/desorption characteristics. The comparative adsorption capacity and time for saturated adsorption of different silica gels prepared at different CO2 pressure at a relative humidity of 50% were compiled in Table 2. In comparison, the silica gel prepared at CO2 pressure of 0.25 MPa shows the best high adsorption capacity and the suitable time for saturated adsorption at the relative humidity of 50%, which is attributed to the optimized surface structure, as shown above.
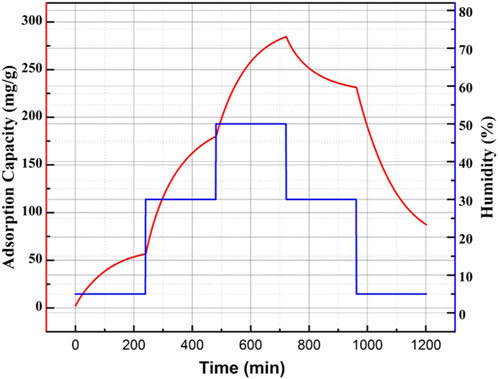
FIGURE 5. Typical adsorption/desorption kinetic curve at different humidities for the as-obtained honeycomb silica gel at a CO2 pressure of 0.25 MPa using water glass as the starting material.
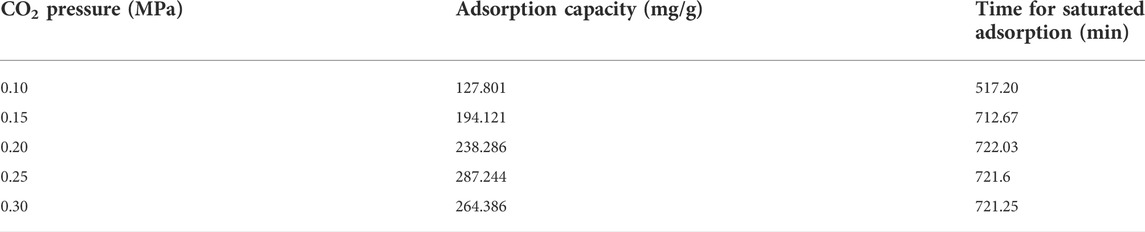
TABLE 2. Adsorption capacity and time for saturated adsorption of silica gel prepared at different CO2 pressures at a relative humidity of 50%
Conclusion
The honeycomb silica gel in a solid desiccant rotary wheel is fabricated environmentally friendly using water glass as starting material and CO2 as neutralized acid. Water glass is used as an adhesive agent as well allowing the formation of the honeycomb monolith without any additional organic adhesive agent and guarantees a clean manufacturing procedure. CO2 could tune the surface structure of silica gel including the specific surface area, pore volume, and pore size due to its rapid diffusion and pressure. The results indicate that the prepared honeycomb silica gel has a large specific surface area of as much as 760 m2/g, a large pore volume of 0.45 ml/g, and suitable mesoporous size of 2.94 nm at a CO2 pressure of 0.25 MPa, which allows the excellent performance of the prepared honeycomb silica gel as a solid desiccant with an adsorption capacity of 287.24 mg/g at a relative humidity of 50%. Therefore, the proposed green preparation procedure of the honeycomb silica gel as a solid desiccant is feasible and promising in the manufacturing of honeycomb rotary wheels for dehumidification.
Data availability statement
The original contributions presented in the study are included in the article/supplementary material; further inquiries can be directed to the corresponding author.
Author contributions
JY: writing and experiment design. JQ: experiment. JF: experiment design. CD: experiment. SC: writing and experiment.
Acknowledgments
The authors are pleased to acknowledge the funding support by the Wuhan Science and Technology Plan Project (No. 2020020602012123).
Conflict of interest
JY, JF, and SC were employed by Wuhan Coobase Facilities Company Limited.
The remaining authors declare that the research was conducted in the absence of any commercial or financial relationships that could be construed as a potential conflict of interest.
Publisher’s note
All claims expressed in this article are solely those of the authors and do not necessarily represent those of their affiliated organizations, or those of the publisher, the editors, and the reviewers. Any product that may be evaluated in this article, or claim that may be made by its manufacturer, is not guaranteed or endorsed by the publisher.
References
Aristov, Y. I., Restuccia, G., Cacciola, G., and Parmon, V. N. (2002). A family of new working materials for solid sorption air conditioning systems. Appl. Therm. Eng. 22, 191–204. doi:10.1016/s1359-4311(01)00072-2
Bareschino, P., Diglio, G., Pepe, F., Angrisani, G., Roselli, C., and Sasso, M. (2015). Modelling of a rotary desiccant wheel: Numerical validation of a variable properties model. Appl. Therm. Eng. 78, 640–648. doi:10.1016/j.applthermaleng.2014.11.063
Bhagat, S. D., Park, K.-T., Kim, Y.-H., Kim, J.-S., and Han, J.-H. (2008). A continuous production process for silica aerogel powders based on sodium silicate by fluidized bed drying of wet-gel slurry. Solid State Sci. 10, 1113–1116. doi:10.1016/j.solidstatesciences.2007.11.016
Cha, Y. C., Kim, C. E., Lee, S. H., Hwang, H. J., Moon, J. W., Han, I. S., et al. (2007). Synthesis of silica aerogel thin film from waterglass. Solid State Phenom. 124-126, 671–674. doi:10.4028/www.scientific.net/ssp.124-126.671
Chung, T.-W., Yeh, T.-S., and Yang, T. C. K. (2001). Influence of manufacturing variables on surface properties and dynamic adsorption properties of silica gels. J. Non-Crystalline Solids 279, 145–153. doi:10.1016/s0022-3093(00)00411-7
Hindersmann, A. (2019). Experimental investigation of a method to avoid channel marks during vacuum infusion. J. Compos. Mater. 54, 2147–2158. doi:10.1177/0021998319889120
Hwang, H. J., Kim, C. E., and Cha, Y. C. (2007). Strengthening of water glass based aerogel by TEOS. Mater. Sci. Forum 544-545, 1053–1056. doi:10.4028/www.scientific.net/msf.544-545.1053
Iswar, S., Malfait, W. J., Balog, S., Winnefeld, F., Lattuada, M., and Koebel, M. M. (2017). Effect of aging on silica aerogel properties. Microporous Mesoporous Mater. 241, 293–302. doi:10.1016/j.micromeso.2016.11.037
Jia, C. X., Dai, Y. J., Wu, J. Y., and Wang, R. Z. (2006). Experimental comparison of two honeycombed desiccant wheels fabricated with silica gel and composite desiccant material. Energy Convers. Manag. 47, 2523–2534. doi:10.1016/j.enconman.2005.10.034
Kabeel, A. E. (2007). Solar powered air conditioning system using rotary honeycomb desiccant wheel. Renew. Energy 32, 1842–1857. doi:10.1016/j.renene.2006.08.009
Kodama, A., Goto, M., Hirose, T., and Kuma, T. (1993). Experimental study of optimal operation for a honeycomb adsorber operated with thermal swing. J. Chem. Eng. Jpn. 26, 530–535. doi:10.1252/jcej.26.530
Kuma, T., and Hirose, T. (1996). Performance of honeycomb rotor dehumidifiers in improved methods of adsorbent preparation. J. Chem. Eng. Jpn. 29, 376–378. doi:10.1252/jcej.29.376
La, D., Dai, Y. J., Li, Y., Wang, R. Z., and Ge, T. S. (2010). Technical development of rotary desiccant dehumidification and air conditioning: A review. Renew. Sustain. Energy Rev. 14, 130–147. doi:10.1016/j.rser.2009.07.016
Lee, J., and Lee, D.-Y. (2012). Sorption characteristics of a novel polymeric desiccant. Int. J. Refrig. 35, 1940–1949. doi:10.1016/j.ijrefrig.2012.07.009
Li, Y., Cheng, X., Cao, W., Gong, L., Zhang, R., and Zhang, H. (2016). Development of adiabatic foam using sodium silicate modified by boric acid. J. Alloys Compd. 666, 513–519. doi:10.1016/j.jallcom.2016.01.139
Liu, Y. (2003). Pore structure of new composite adsorbent SiO2·xH2O·yCaCl2 with high uptake of water from air. Sci. China Ser. E 46, 551–559. doi:10.1360/02ye0480
Manjunatha, C. M., Bojja, R., Jagannathan, N., Kinloch, A. J., and Taylor, A. C. (2013). Enhanced fatigue behavior of a glass fiber reinforced hybrid particles modified epoxy nanocomposite under WISPERX spectrum load sequence. Int. J. Fatigue 54, 25–31. doi:10.1016/j.ijfatigue.2013.04.008
Neti, S., and Wolfe, E. I. (2000). Measurements of effectiveness in a silica gel rotary exchanger. Appl. Therm. Eng. 20, 309–322. doi:10.1016/s1359-4311(99)00031-9
O’Connor, D., Calautit, J. K., and Hughes, B. R. (2016). A novel design of a desiccant rotary wheel for passive ventilation applications. Appl. Energy 179, 99–109. doi:10.1016/j.apenergy.2016.06.029
Prasad, A. K., Yadav, L., and Yadav, A. (2019). Comparative analysis of different design of rotary dehumidifier. Heat. Trans. Asian. Res. 48, 2193–2215. doi:10.1002/htj.21480
Sarawade, P. B., Kim, J.-K., Hilonga, A., and Kim, H. T. (2010). Influence of aging conditions on textural properties of water-glass-based silica aerogels prepared at ambient pressure. Korean J. Chem. Eng. 27, 1301–1309. doi:10.1007/s11814-010-0173-z
Su, M., Han, X., Chong, D., Wang, J., Liu, J., and Yan, J. (2021). Experimental study on the performance of an improved dehumidification system integrated with precooling and recirculated regenerative rotary desiccant wheel. Appl. Therm. Eng. 199, 117608. doi:10.1016/j.applthermaleng.2021.117608
Wang, W., Wu, L., Li, Z., Fang, Y., Ding, J., and Xiao, J. (2013). An overview of adsorbents in the rotary desiccant dehumidifier for air dehumidification. Dry. Technol. 31, 1334–1345. doi:10.1080/07373937.2013.792094
Wei, X., Wang, W., Xiao, J., Zhang, L., Chen, H., and Ding, J. (2013). Hierarchically porous aluminosilicates as the water vapor adsorbents for dehumidification. Chem. Eng. J. 228, 1133–1139. doi:10.1016/j.cej.2013.05.062
White, S. D., Goldsworthy, M., Reece, R., Spillmann, T., Gorur, A., and Lee, D.-Y. (2011). Characterization of desiccant wheels with alternative materials at low regeneration temperatures. Int. J. Refrig. 34, 1786–1791. doi:10.1016/j.ijrefrig.2011.06.012
Wu, X. N., Ge, T. S., Dai, Y. J., and Wang, R. Z. (2018). Review on substrate of solid desiccant dehumidification system. Renew. Sustain. Energy Rev. 82, 3236–3249. doi:10.1016/j.rser.2017.10.021
Yang, F., Wu, X. N., Peng, J. J., Ge, T. S., Dai, Y. J., and Wang, R. Z. (2020). Investigation on humidification performance of silica gel rotary wheel system in winter. Build. Environ. 183, 107064. doi:10.1016/j.buildenv.2020.107064
Zhang, X. J., Dai, Y. J., and Wang, R. Z. (2003). A simulation study of heat and mass transfer in a honeycombed rotary desiccant dehumidifier. Appl. Therm. Eng. 23, 989–1003. doi:10.1016/s1359-4311(03)00047-4
Zhang, X. J., Sumathy, K., Dai, Y. J., and Wang, R. Z. (2006). Dynamic hygroscopic effect of the composite material used in desiccant rotary wheel. Sol. Energy 80, 1058–1061. doi:10.1016/j.solener.2005.07.008
Keywords: honeycomb rotary wheel, dehumidification, CO2, silica gel, absorbent
Citation: You J, Qin J, Du C, Fu J and Cheng S (2022) CO2-assisted fabrication of silica gel adsorbent in honeycomb rotary wheels for air dehumidification. Front. Chem. 10:1038095. doi: 10.3389/fchem.2022.1038095
Received: 06 September 2022; Accepted: 16 September 2022;
Published: 04 October 2022.
Edited by:
Zhenyu Sun, Beijing University of Chemical Technology, ChinaReviewed by:
Jiehua Liu, Hefei University of Technology, ChinaFeng Han, Shandong Agricultural University, China
Copyright © 2022 You, Qin, Du, Fu and Cheng. This is an open-access article distributed under the terms of the Creative Commons Attribution License (CC BY). The use, distribution or reproduction in other forums is permitted, provided the original author(s) and the copyright owner(s) are credited and that the original publication in this journal is cited, in accordance with accepted academic practice. No use, distribution or reproduction is permitted which does not comply with these terms.
*Correspondence: Siqing Cheng, aWNuZWVAd2hwdS5lZHUuY24=