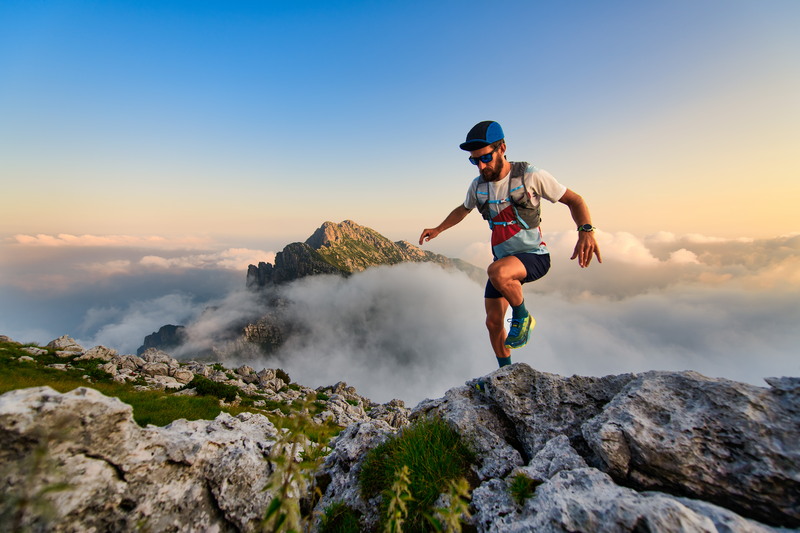
95% of researchers rate our articles as excellent or good
Learn more about the work of our research integrity team to safeguard the quality of each article we publish.
Find out more
ORIGINAL RESEARCH article
Front. Chem. , 29 September 2022
Sec. Catalytic Reactions and Chemistry
Volume 10 - 2022 | https://doi.org/10.3389/fchem.2022.1006981
This article is part of the Research Topic Celebrating 20 Years of CICECO – Aveiro Institute of Materials - Current and future perspectives in the use of Material Sciences, Chemistry, and Photonics for a more sustainable future View all 20 articles
The biomass-derived platform chemicals furfural and 5-(hydroxymethyl)furfural (HMF) may be converted to α-angelica lactone (AnL) and levulinic acid (LA). Presently, LA (synthesized from carbohydrates) has several multinational market players. Attractive biobased oxygenated fuel additives, solvents, etc., may be produced from AnL and LA via acid and reduction chemistry, namely alkyl levulinates and γ-valerolactone (GVL). In this work, hierarchical hafnium-containing multifunctional Linde type L (LTL) related zeotypes were prepared via top-down strategies, for the chemical valorization of LA, AnL and HMF via integrated catalytic transfer hydrogenation (CTH) and acid reactions in alcohol medium. This is the first report of CTH applications (in general) of LTL related materials. The influence of the post-synthesis treatments/conditions (desilication, dealumination, solid-state impregnation of Hf or Zr) on the material properties and catalytic performances was studied. AnL and LA were converted to 2-butyl levulinate (2BL) and GVL in high total yields of up to ca. 100%, at 200°C, and GVL/2BL molar ratios up to 10. HMF conversion gave mainly the furanic ethers 5-(sec-butoxymethyl)furfural and 2,5-bis(sec-butoxymethyl)furan (up to 63% total yield, in 2-butanol at 200°C/24 h). Mechanistic, reaction kinetics and material characterization studies indicated that the catalytic results depend on a complex interplay of different factors (material properties, type of substrate). The recovered-reused solids performed steadily.
Global warming and energy security issues related to the intense use of fossil fuels may be alleviated by the alternative use of widespread renewable sources and waste/surpluses to produce bioenergy and bioproducts, thereby avoiding greenhouse gas emissions, environmental pollution, and waste management issues (Roy et al., 2021; Koul et al., 2022). Vegetable biomass existing in terrestrial and aquatic areas constitutes an abundant source of carbohydrates that are partly disposed of as agricultural surpluses/residues, municipal solid waste, industrial (e.g., biorefineries) waste, sewage sludge, etc. (Cheng and Brewer, 2021; Koul et al., 2022; Narisetty et al., 2022). Carbohydrates may be chemically valorized into useful bioproducts for several industrial sectors. The most important selective catalytic routes of carbohydrates to bioproducts include the acid-catalyzed hydrolysis and dehydration reactions under relatively mild conditions, which lead to the bio-based furanic aldehyde platform chemicals 5-(hydroxymethyl)furfural (HMF) and furfural (FUR) (Liguori et al., 2015; Dutta, 2021; Fact, 2022).
HMF may be selectively converted to oxygenated fuel additives in alcohol media, namely 5-(alkoxymethyl)furfural (AMF) and 2,5-bis(alkoxymethyl)furan (BAMF) via etherification or reduction/etherification, respectively (Scheme 1) (Poullikkas, 2017; Kong et al., 2020; Hou et al., 2021). AMFs possess relatively high energy density, low toxicity and high stability (Li et al., 2016b; Kong et al., 2018; Hou et al., 2021; Liu et al., 2022). On the other hand, BAMFs may possess higher energy density, cetane number, miscibility and stability than AMFs, making them even more attractive fuel additives (Hu et al., 2018, 2020); e.g., BAMFs synthesized using n-butanol (which may be renewable and synthesized via fermentation of hexoses (Cho et al., 2014)) or secondary and tertiary alcohols (Gruter, 2009).
SCHEME 1. Hierarchical multifunctional LTL related materials prepared via top-down strategies for integrated catalytic transfer hydrogenation (CTH) and acid reactions of levulinic acid (LA), α-angelica lactone (AnL) and 5-(hydroxymethyl)furfural (HMF) to useful bioproducts such as alkyl levulinates (LE) and γ-valerolactone (GVL), or (from HMF) 5-(alkoxymethyl)furfural (AMF) and 2,5-bis(alkoxymethyl)furan (BAMF).
On the other hand, HMF and FUR may be converted to α-angelica lactone (AnL) and levulinic acid (LA), and AnL may be an intermediate to LA (Al-Shaal et al., 2015; Antonetti et al., 2016; Lima et al., 2018; Dutta and Bhat, 2021). LA was identified as one of the most valuable bioproducts derived from carbohydrates (Werpy and Petersen, 2004), and its market players include Biofine and DuPont (Fitzpatrick, 1995; Grand View Research, 2021). The growing LA market covers several sectors, from pharmaceuticals, agrochemicals, polymers, plasticizers, fuel and fuel additives to flavours, fragrances, cosmetics, and food additives (Morone et al., 2015; Dutta and Bhat, 2021; Di Bucchianico et al., 2022; Mordor Intelligence, 2022).
Both AnL and LA may be converted to alkyl levulinates (LE) and γ-valerolactone (GVL) (Manzer, 2005; Liguori et al., 2015; Zhang, 2016; Lima et al., 2018; Yu et al., 2019; Dutta and Bhat, 2021; Antunes et al., 2022a). LE and GVL are attractive oxygenated fuel additives (Morone et al., 2015); e.g., butyl levulinate blends can improve fuel properties such as conductivity, combustion emission, freezing point (Di Bucchianico et al., 2022). Furthermore, GVL has a growing market as a food flavouring agent and solvent, foreseen up to 2028 (Data Intelo, 2022), and is an interesting intermediate to diverse chemicals and fuels (Yu et al., 2019; Dutta and Bhat, 2021; Sajid et al., 2021).
The conversion of AnL and LA to GVL involves acid and reduction chemistry (Scheme 1). Hence, reducing agents are required, which may be H2 (for hydrogenation) or organic H-donors such as secondary alcohols or acids (for catalytic transfer hydrogenation (CTH)) (Dutta et al., 2019; Yu et al., 2019; Yu et al., 2020b, 2020a; Weng et al., 2020; Maumela et al., 2021). High GVL yields were reported for the reaction of LA with H2 (mainly produced from fossil fuels) using (expensive) noble metal catalysts (Huang et al., 2020; Bassi et al., 2021; Lu et al., 2022; Vu et al., 2022). However, the process economics and safety may be favoured by using (cheaper) non-noble metal catalysts (Xue et al., 2018; Dutta et al., 2019; Wang et al., 2020) and, on the other hand, organic H-donors instead of operating under high pressure H2 conditions, which requires robust, expensive infrastructures (Gilkey and Xu, 2016; Dutta et al., 2019; Nie et al., 2021).
A literature survey indicated that hafnium-containing catalysts may be effective for LA conversion to GVL via CTH chemistry, i.e., not requiring external H2 supply and noble metals, specifically: hafnium supported on organic supports such as sulfonated sugar cane bagasse (Huang et al., 2021), carbonized/sulfonated glucose (Jori and Jadhav, 2020), or graphite oxide (Li et al., 2020); hafnium-containing organic-inorganic coordination hybrids (including MOFs) (Xie et al., 2016; Rojas-Buzo et al., 2018; Antunes et al., 2022b); and zeolites (BEA (Antunes et al., 2022a), FAU (Tang et al., 2019)). According to the literature, Hf-containing catalysts (zeolites, hybrids) may perform superiorly to the Zr-analogues in the conversion of LA and LE to GVL (Luo et al., 2014; Tang et al., 2019; Li et al., 2020; Antunes et al., 2022a; 2022b). Of these, the non-carbon-based catalysts may possess longer lifetimes and better resistance against regeneration treatments such as calcination of coke/humins, enhancing productivity. In this sense, zeolites may be promising.
Zeolites are (fully inorganic) crystalline microporous aluminosilicates used in the industry, and are particularly attractive for catalytic and adsorption processes (Čejka et al., 2020). They possess considerable specific surface area, tuneable acidity and selectivity properties (Li et al., 2016b; Mon and Leyva-Pérez, 2021). Different zeolite topologies are commercially available (Kuznetsova et al., 2018), which may be modified via top-down or bottom-up strategies, broadening and/or improving their catalytic applications. For example, hierarchical (micro/mesoporous) zeotype catalysts may be effective for multiple reactions (Serrano et al., 2018). The few literature studies on the conversion of LA to GVL over micro/mesoporous zeotypes led to 22–99% GVL yield (Antunes et al., 2022a): Sn-containing Beta (Antunes et al., 2015; Winoto et al., 2016); Zr-containing Beta (Antunes et al., 2016a, 2016b; Morales et al., 2019; López-Aguado et al., 2020); Hf-USY (Tang et al., 2019) and Hf-AlBeta (Antunes et al., 2022a) which surpassed the performances of Sn- and Zr-counterparts. These promising results motivated us to explore different commercially available zeolite topologies and post-synthesis treatments for GVL production.
Linde type L zeolites consist of a microporous aluminosilicate framework (K6Na3(H2O)21[Al9Si27O72] for Si/Al = 3, but higher ratios are possible) with LTL topology, which allows diffusion along 1D 12-membered ring (MR) channels that have ca. 0.71 nm × 0.71 nm apertures and cages with ca. 1.2 nm diameter (Broach, 2010). The 1D 12 MR channel system is connected by a 3D 8 MR channel system (0.34 nm × 0.56 nm). LTL zeolites possess easily exchangeable cations located inside the 12 MR channels near the 8 MR windows. Although a literature survey indicates that LTL zeolitic catalysts are effective for hydrogenation reactions using externally supplied H2 (details discussed in the Supplementary Material), to the best of our knowledge, LTL catalysts were never reported in the literature for CTH reactions, in general.
Few hierarchical LTL type materials were prepared via different top-down strategies (e.g., with or without surfactants) and conditions (leading to enhanced mesopore volume (Vmeso)), partly depending on the catalytic applications: alkane aromatization (Vmeso increased from 0.079 to 0.44 cm3 g−1) (Lee and Choi, 2016); Knoevenagel condensation (Vmeso increased from 0.01 to 0.29 cm3 g−1) (Nilesh et al., 2016); dealkylation of aromatics (Vmeso increased from 0.08 to 0.28 cm3 g−1) (Al-Ani et al., 2019); and hydrogenation of d-xylose to xylitol (Vmeso increased from 0.010 to 0.14 cm3 g−1) (Tangale et al., 2019). Al-Ani et al. (Al-Ani et al., 2019) proposed that the formation of mesopores in LTL via mixed alkaline plus surfactant treatment was gradual in relation to that for more open pore structures such as the FAU and BEA topologies, allowing some control over the features of the LTL pore system.
In this work, hierarchical multifunctional LTL zeotypes were prepared for integrated CTH and acid reactions of LA, AnL and HMF to useful bioproducts (Scheme 1). The catalysts were prepared from commercial KL zeolite via top-down strategies involving desilication, dealumination and solid-state impregnation (SSI) of hafnium (and zirconium for comparison). This is the first CTH application reported for the LTL family of zeolites. The influence of the post-synthesis treatments (e.g., with or without desilication) and conditions (e.g., acid concentration, hafnium loading) on the material properties and catalytic performances was studied. Mechanistic, reaction kinetics and material characterization studies indicated that the catalytic results depend on a complex interplay of different factors, and the relationships of material properties-catalytic performance may be different for different substrates.
All reagents and solvents were obtained from commercial sources and used as received (purities and suppliers are indicated in Supplementary Material). The materials were characterized (details given in the Supplementary Material) by powder X-ray diffraction (PXRD; crystalline structure, relative crystallinity (RC)), scanning electron microscopy (SEM; morphology), elemental mappings (distributions of Hf, Zr, Si, Al) and energy dispersive X-ray spectroscopy (EDS; Si/Al, Si/Hf ratios), nitrogen sorption isotherms (textural properties and pore size distributions), 27Al MAS NMR spectroscopy (types of Al sites), attenuated total reflectance Fourier Transform Infrared (ATR FT-IR) spectroscopy (surface chemistry), elemental analysis for carbon (adsorbed carbonaceous matter on the used catalysts), and FTIR of adsorbed pyridine (base probe) at 150 and 350°C (acid properties).
Hafnium-containing hierarchical LTL zeotypes and a Zr-counterpart were prepared via post-synthesis partial dealumination using oxalic acid (oxac), desilication (D) using KOH treatments, followed by dealumination using H2SO4, solid-state impregnation (SSI) of hafnium acetylacetonate used as Hf precursor and finally calcination.
Commercial KL zeolite was mildly dealuminated using 0.08 M aq. oxalic acid (30 ml solution per gram of zeolite) at 80°C for 3 h, with stirring. The solid was separated by filtration, thoroughly washed with hot Milli-Q water until neutral pH, dried overnight at 100°C, and finally calcined at 550°C (1°C min−1) in static air for 5 h, giving KL(oxac). Literature studies reported alkaline treatments of LTL type materials, using NaOH or KOH in the concentrations range 0.04–2.8 M (Lee and Choi, 2016; Nilesh et al., 2016; Al-Ani et al., 2019; Tangale et al., 2019). KL(oxac) was subsequently desilicated (D) using 0.2 M aq. KOH (30 ml per gram of zeolite) at 65°C for 30 min, with stirring. The mixture was cooled in an ice bath during 10 min and the solid was separated by filtration, thoroughly washed with hot Milli-Q water until neutral pH, and dried overnight at 100°C, giving D-KL.
D-KL was simultaneously ion-exchanged and dealuminated using H2SO4. According to the literature, KL may tolerate 0.4 M H2SO4 treatment for 1 h (Al-Ani et al., 2019); these conditions were applied to D-KL, but led to complete amorphization (Supplementary Material for details, Supplementary Figure S1). Hence, the concentration and time of the H2SO4 treatment were reduced. Specifically, D-KL was treated with 0.10, 0.15, 0.20 or 0.28 M aq. H2SO4 (30 ml per gram of zeolite) for 30 min at room temperature, with stirring. The solid was separated by filtration, thoroughly washed with hot Milli-Q water until neutral pH, and dried overnight at 100°C, giving D-HL(x), where x stands for the concentration of H2SO4 (0.10 ≤ x < 0.28 M).
For comparison, a material denoted HL was prepared by subjecting commercial KL to dealumination with 0.15 M aq. H2SO4 and then SSI of 0.28 mmolHf g−1 (the two treatments were carried out in a comparable fashion to that described above for the D-HL(x) materials). In a separate experiment, commercial KL was subjected to ion-exchange using 0.15 M aq. NH4NO3; the resultant material exhibited additional PXRD peaks, suggesting the presence of crystalline contaminations (which was reproducible; please see the Supplementary Material for details, Supplementary Figure S2), and, thus, this material was discarded.
The D-HL(x) precursors were subjected to SSI with Hf(acac)4 and subsequent calcination, giving yHf-D-HL(x) where y is the hafnium concentration (in the range 0.28–1.68 mmolHf g−1). The SSI process involved gentle grinding of 1 g of the aluminosilicate support with the desired amount of Hf(acac)4 precursor for 30 min, using an agate pestle and mortar. The resultant material was calcined at 550°C (1°C min−1) under air flow (20 ml min−1) for 6 h. Zeolite 0.28Hf-HL was prepared in a similar fashion, albeit using the support HL and y = 0.28 mmolHf g−1. The Zr-counterpart, namely 0.28Zr-D-HL(0.15), was prepared by the same protocol, albeit using Zr(acac)4 as precursor (0.158 g Zr(acac)4 per g of D-HL(0.15)).
The catalytic reactions were carried out using homemade tubular glass batch reactors (ca. 8 cm length, ca. 11 mm internal diameter) with a conic-shaped bottom, equipped with a PTFE-coated magnetic stirring bar (Supelco) and a PTFE valve (Normax) for purging. Each reactor was loaded with LA (in a concentration ranging from 0.14 to 0.45 M), catalyst (25.5 gcat L−1) and 2BuOH. The reactions of AnL and HMF were carried out using an initial substrate concentration of 0.45 M in 2BuOH. Bulk HfO2 was used in an equivalent molar amount of hafnium to that added together with the catalysts 1.40Hf-D-HL(x) to the reactor. Prior to control tests using D-HL(x), these materials were calcined under similar conditions to those described above for the Hf-containing zeotypes.
The loaded reactors were immersed in a thermostatically controlled oil bath heated at 200°C and stirred to 850 rpm to favour uniform temperature distribution and avoid external diffusional limitations. Reaction time was counted from the instant that the reactors were immersed in the oil bath. After a given reaction time, the reactors were cooled to room temperature prior to sampling. Freshly prepared samples were analyzed by HPLC for quantification of HMF or by gas chromatography (GC) for quantification of the reaction products and remaining substrates.
The HPLC analyses were carried out using a Knauer Smartline HPLC Pump 100 and a Shodex SH1011H + 300 mm × 8 mm (i.d.) ion exchange column (Showa Denko America, Inc. New York), coupled to a Knauer Smartline 2520 UV detector (254 nm). The column temperature was set at 50°C, and the mobile phase was 0.005 M aq. H2SO4 at a flow rate of 0.8 ml min−1. The GC analyses were carried out using an Agilent 7820A GC equipped with a capillary column (HP-5, 30 m × 0.320 mm × 0.25 mm; 35–300°C), spit injector (240°C) and a flame ionization detector (320°C), using H2 as carrier gas. The quantification of the substrates and reaction products was based on calibration curves using internal standards. Individual experiments were performed for a given reaction time, and the presented results are the mean values of at least two replicates with an error <6%.
The reaction products were identified using a Shimadzu QP2010 ultra-GC-MS (Izasa Scientific, Lisbon, Portugal) equipped with a split injector (240°C), ion source (200°C), interface (300°C), a Zebron ZB-5ms capillary GC column (ZB-5, 30 m × 0.25 μm × 0.25 mm; 35–300°C) and He as carrier gas (supporting databases: Wiley229 and NIST14). The identified products were 2-butyl levulinate (2BL) and GVL from LA; LA, 2BL and GVL from AnL; 5-methylfurfural (5MF), 5-(sec-butoxymethyl)furfural (BMF) and 2,5-bis(sec-butoxymethyl)furan (BBMF) from HMF.
The conversion (%) of the substrate (Sub) at a reaction time t was calculated using the formula, 100 × [(initial molar concentration of Sub)—(molar concentration of Sub at reaction time t)/(initial molar concentration of Sub)], and product (Prod) yield was calculated using formula 100 × [(molar concentration of Prod at time t)/(initial molar concentration of Sub)]. Catalytic activities (mmol gcat h−1) were calculated based on the substrate conversion at 5 h reaction.
The used catalysts were separated by centrifugation (10,000 rpm for ca. 5 min), thoroughly washed with the reaction solvent (2BuOH) and dried at 85°C overnight. The used catalysts were thermally regenerated at 550°C (heating rate of 1°C min−1) for 5 h, under an air flow (20 ml min−1). Selected catalysts (1.40Hf-D-HL(0.15), 1.12Hf-D-HL(0.28)) were used for five consecutive 5 h-batch runs (0.45 M LA, 2BuOH, 25.5 gcat L−1, 200°C).
Contact tests (CT) consisted of contacting the fresh catalysts 1.40Hf-D-HL(0.15) and 1.12Hf-D-HL(0.28) with 2BuOH at 200°C for 5 h, under the same conditions as those used for a normal catalytic test, but without substrate; then, the solid was separated by centrifugation (10,000 rpm) and the supernatant liquid phase was passed through a 220 μm pore size PTFE membrane; the substrate (LA) was added to this solution (to give an initial concentration of 0.45 M) and left to react for 5 h at 200°C (giving LP-CT); finally, the homogeneous mixture was analyzed by GC and the results were compared to those without catalyst.
Multifunctional LTL related materials (yHf-D-HL(x)) were prepared from commercial KL (Si/Al = 3) via top-down strategies for the target reactions of LA, AnL and HMF. The strategies consisted of mild dealumination (giving KL(oxac), Si/Al = 5); desilication (D) to introduce mesoporosity (giving D-KL, Si/Al = 3); dealumination using H2SO4 (giving D-HL(x), Si/Al in the range 5–41); solid-state impregnation (SSI) of hafnium and calcination. The influence of the acid concentration (x in the range 0.10–0.28 M H2SO4) and Hf loading (y in the range 0.28–1.68 mmolHf g−1) on the material properties was studied. The characterization studies of the zirconium counterpart 0.28Zr-D-HL(0.15) are discussed in the Supplementary Material (Supplementary Figure S3, Supplementary Table S1); the results were comparable to those for 0.28Hf-D-HL(0.15).
For the materials D-HL(x), increasing x led to increasing Si/Al ratio in the range 5-41, suggesting that partial removal of aluminum occurred (likely forming vacant sites) (Figure 1A, Supplementary Table S1). Although the materials HL (Si/Al = 6) and D-HL(0.15) (Si/Al = 9) were subjected to the same acid treatment using 0.15 M H2SO4, the latter possessed a higher Si/Al ratio, suggesting that the pretreatments facilitated dealumination. The SSI process did not significantly affect the Si/Al ratio, i.e., each pair of materials D-HL(x) and yHf-D-HL(x) with the same x possessed similar Si/Al ratio. Since no wash/extraction/filtration operations were performed after SSI, the amount of hafnium introduced in the SSI step remained in the solids, giving yHf-D-HL(x) with y in the range 0.28–1.68 mmolHf g−1 (Supplementary Table S1).
FIGURE 1. Si/Al ratio of the prepared materials (A) and relative crystallinity (RC) as a function of Si/Al (B). The RC values are given in Table S1.
The PXRD patterns of the materials KL, KL(oxac), HL, D-KL, D-HL(x) and yHf-D-HL(x) with x ≤ 0.15 indicated that the LTL topology was preserved (Lee and Choi, 2016; Nilesh et al., 2016; Al-Ani et al., 2019; Tangale et al., 2019), whereas the materials with x = 0.20 and 0.28 were mostly amorphous (Figure 2, Supplementary Table S1). The PXRD patterns of yHf-D-HL(0.15) with y < 1.68 mmolHf g−1 and of yHf-D-HL(0.28) with y < 1.40 mmolHf g−1 did not evidence the presence of other crystalline phases; peaks characteristic of hafnia monoclinic phase include ca. 28.6°, 31.8° and 34.7° (ICDD PDF-4+ 2020 reference code no. 04-005–4477) (Figure 2B). These results suggest that these materials possessed somewhat uniform metal/metalloid (Si, Al, Hf) distributions. The remaining materials with higher y exhibited weak reflections at ca. 28° and 32° assignable to polymeric hafnium oxide species. For the highest Hf loading of 1.68 mmolHf g−1 (for which formation of hafnium oxide particles may be more critical), the average crystallite size of the supported hafnium oxide particles (considering a spherical geometry) was very small, ca. 8–9 nm.
FIGURE 2. (A) PXRD patterns of (a) D-HL(x) with x = 0.28 (b), 0.20 (d), 0.15 (f), 0.10 (h); 0.28Hf-D-HL(x) with x = 0.28 (a), 0.20 (c), 0.15 (e), 0.10 (g); D-KL (i); KL (oxac) (j); 0.28Hf-HL (k); HL (l); KL (m). (B) PXRD patterns of yHf-D-HL(0.28) with y = 1.68 (a), 1.40 (b), 1.12 (c), 0.84 (d), 0.56 (e), 0.28 (f); D-HL(0.28) (g); yHf-D-HL(0.15) with y = 1.68 (h), 1.40 (i), 1.12 (j), 0.84 (k), 0.56 (l), 0.28 (m); D-HL(0.15) (n); bulk HfO2.
The oxalic acid and desilication treatments of KL did not significantly affect the relative crystallinity (RC ≥ 96%) (Figure 1B, Supplementary Table S1). Increasing x led to decreasing RC of the D-HL(x) materials. Hence, the increasing Si/Al ratio was accompanied by decreasing RC. The D-HL(x) and 0.28Hf-D-HL(x) materials with the same x, possessed similar RC; e.g., 73 and 71% RC for D-HL(0.15) and 0.28Hf-D-HL(0.15), respectively; 22 and 20% RC for D-HL(0.28) and 0.28Hf-D-HL (0.28), respectively. For the yHf-D-HL(0.15) materials, increasing y led to decreasing RC (Supplementary Table S1), which may be partly due to the presence of Hf species inside the pores, causing decreased scattering contrast and reduced intensities of the PXRD peaks. The range of RC of the yHf-D-HL(x) materials with x ≤ 0.15 and y ≤ 0.84 was comparable to that reported by Al-Ani et al. (Al-Ani et al., 2019) for hierarchical LTL materials prepared via a surfactant templated approach, at 80–100°C (59–74% RC). The materials yHf-D-HL(0.28) possessed low RC (less than 24%) (Supplementary Table S1).
The SEM images showed that, in general, the materials consisted of aggregates of small pseudo-spherical particles with sizes of up to ca. 30 nm (exemplified for some materials in Figure 3, Supplementary Figure S4, S5). The respective elemental mappings suggested somewhat uniform metal distributions (Figure 3, Supplementary Figure S4, S5) (noteworthy, it was not possible to discriminate HfOx nanocrystallites by SEM).
FIGURE 3. SEM images (left) and element mappings (Si–red, Al–green, Hf–purple) of KL (a), 5Hf-HL (b), D-KL (c), D-HL(x) (x = 0.15 (d), 0.20 (f), 0.28 (h)) and 0.28Hf-D-HL(x) (x = 0.15 (e), 0.20 (g), 0.28 (i)).
Commercial KL, HL, and KL(oxac) exhibited type I nitrogen sorption isotherms (Supplementary Figure S6A), characteristic of microporous materials (Gregg and Sing, 1982). The increasing N2 uptake as the relative pressure (p/p0) approached unity may be attributed to N2 sorption on the external surface of the relatively small crystallites. The desilicated materials D-KL and D-HL(x) exhibited type IV isotherms with an inflection point at p/p0 > 0.9 (inset of Supplementary Figure S6B), which is characteristic of mesoporous materials (Gregg and Sing, 1982). Whereas commercial KL possessed SEM = 32 m2 g−1 and Vmicro = 0.12 cm3 g−1, the desilicated D-KL material possessed SEM = 134 m2 g−1 and Vmicro = 0.15 cm3 g−1, i.e., the alkaline treatment introduced mesoporosity without affecting significantly Vmicro (Figure 4A, Supplementary Table S2). Consistently, D-HL(x) exhibited bimodal pore size distributions, in which the mesopore sizes were in the range 2.3–6 nm (Supplementary Figure S6C).
FIGURE 4. Textural properties of (A) KL, KL(oxal), D-KL and D-HL(x), and of (B) D-HL(x) and yHf-D-HL(x) materials prepared: micropore specific surface area (Smicro (black bars)), external/mesopore specific surface area (SEM (grey bars)) and micropore volume (Vmicro (*)). The values are given in Table S2.
For D-HL(x), increasing x up to 0.20 essentially led to decreasing Smicro and Vmicro without affecting considerably SEM (130–148 m2 g−1) (Figure 4A, Supplementary Table S2). Materials D-HL(x) with x ≤ 0.15 possessed comparable Vmicro to literature data for surfactant-templated LTL type materials (Al-Ani et al., 2019). For x = 0.28, Vmicro and Smicro decreased drastically to 0.01 cm3 g−1 and 11 m2 g−1, respectively, and the material was essentially mesoporous (SEM = 117 m2 g−1). Based on these results and PXRD, harsh dealumination seems to cause partial destruction and/or blockage of the micropores (e.g., possibly by inorganic debris formed during post-synthesis treatments).
The introduction of Hf in D-HL(x) with x ≤ 0.20, led to a decrease in Smicro and Vmicro, suggesting that Hf sites are at least partly located on the internal micropore surface (Figure 4B, Supplementary Table S2). For x = 0.28, the introduction of Hf led to a decrease in SEM (117 and 74 m2 g−1 for D-HL(0.28) and 1.12Hf-D-HL(0.28), respectively), suggesting that Hf sites may be located on the mesopore surface.
Furthermore, the micropore size distribution curves of KL showed medians at ca. 0.55 and at 0.75 nm, assignable to the 8-MR (3D) and 12-MR (1D) channels. Especially the peak at ca. 0.55 nm was significantly attenuated for D-HL(x) with x ≤ 0.20 and negligible for D-HL(0.28) (Supplementary Figure S7A). This was more pronounced after introducing Hf, suggesting that a fraction of Hf species may be located inside micropores and/or at micropore mouths of yHf-D-HL(x) with x ≤ 0.20 (exemplified for 0.28Hf-D-HL(x) in Supplementary Figure S7B).
The 27Al MAS NMR spectra of KL, HL, Hf-HL, KL(oxac), D-KL, D-HL(x) and yHf-D-HL(x) with x ≤ 0.15 showed a prominent peak centered at ca. 63 ppm, assigned to Al sites in tetrahedral coordination (Altetra) (Supplementary Figure S8). Increasing x above 0.15 led to the broadening of the Altetra peak and the appearance of a shoulder at ca. 53 ppm; the relative intensity of the latter peak increased with increasing x. These results suggest that the decreased crystallinity was accompanied by the formation of broader distributions of Altetra species (e.g., possessing different bond angles/lengths, coordination spheres). The materials D-HL(x) exhibited a weak resonance at ca. 0 ppm due to hexacoordinated (octahedral) Al species (Alocta), which was not verified for D-KL, suggesting that Alocta was formed during the acid treatment. A comparison of the materials before and after the introduction of hafnium indicated no significant differences in the Altetra spectral region, but the Alocta peak disappeared. Hence, it seems that Alocta species were partially linked to the framework of D-HL(x) and converted to Altetra during SSI/calcination. According to the literature for zeolites, Alocta and Altetra sites may interconvert (Mafra et al., 2012; Ravi et al., 2021); e.g., hydroxylated-hydrated Alocta sites and hydroxylated Altetra sites may interconvert (Yakimov et al., 2022). Possibly the two resonances at ca. 63 and 53 ppm may include four coordinated hydroxylated (Al(OSi)4-x(OH)x) and non-hydroxylated (Al(OSi)4) aluminum sites.
The FT-IR spectrum of adsorbed pyridine for zeolite HL showed the typical bands associated with Al sites possessing Lewis (L) acidity (metal-pyridine complexes, which may possess extra framework metal sites) and Brønsted (B) acidity (pyridinium ions): ca. 1,620 cm−1 and 1,454 cm−1 (L); ca. 1,635 cm−1 and 1,540 cm−1 (B); and 1,490 cm−1 (L + B) (Figure 5) (Zhu et al., 2016; Tang et al., 2019; Ravi et al., 2021). A band at 1,439 cm−1 may be due to pyridine molecules interacting with weak acid sites. The relative intensities of the bands at 1,454 cm−1 (L), 1,540 cm−1 (B) and 1,635 cm−1 (B) decreased after acid treatment and were hardly distinguishable in the spectra of the materials with x = 0.28. The introduction of hafnium led to the appearance of new bands at ca. 1,608 and 1,448 cm−1 which became stronger with increasing y up to ca. 0.84 mmolHf g−1 (above this value the spectral differences in relative intensities were not so evident). Hence, these two new bands may be attributed to Hf-containing acid sites. The appearance of these new bands after introducing Hf is in agreement with that reported by Tang et al. for Hf-USY (Tang et al., 2019). For the yHf-D-HL(0.28) materials, the 1,608 and 1,448 cm−1 bands predominated, suggesting that the acidity of these materials was essentially associated with Hf sites.
FIGURE 5. FT-IR spectra of adsorbed pyridine, at 150°C, for yHf-D-HL(0.28) with y = 1.40 (a), 1.12 (b), 0.84 (c), 0.56 (d), 0.28 (e); 0.28Hf-D-HL(0.20) (f); yHf-D-HL(0.15) with y = 1.40 (g), 1.12 (h), 0.84 (i), 0.56 (j), 0.28 (k); 0.28Hf-D-HL(0.10) (l); 0.28Hf-HL (m); HL (n). Hf signalizes the new bands which appeared after Hf introduction; Bz and Lz signalize typical bands associated with Brønsted and Lewis acid sites of a zeolitic type aluminosilicate framework.
Increasing x of the materials 0.28Hf-D-HL(x) led to decreasing amount of L and B acid sites (Figure 6, Supplementary Table S3). On the other hand, the introduction of Hf in HL gave 0.28Hf-HL possessing higher amounts of B and L acid sites (L increased from 82 to 128 μmol g−1, and B increased from 45 to 71 μmol g−1, respectively (Supplementary Table S3)). These results parallel those reported in the literature for Beta zeolites with and without hafnium (Antunes et al., 2022a).
FIGURE 6. Acid properties of the materials prepared from commercial KL via post-synthesis modifications: L = Lewis acid sites (top green bar), B = Brønsted acid sites (bottom blue bar) and L/B ratio (×). The values are given in Table S3.
For each set of materials yHf-D-HL(0.15) and yHf-D-HL(0.28), a maximum amount of L acid sites was reached as a function of y; specifically, at y = 0.56 and 0.84 for materials with x = 0.15 and 0.28, respectively (Figure 6, Supplementary Table S3). For the lower range of Hf loading (y), the increasing L acidity with increasing y suggests that uniformly distributed Hf-sites were introduced. On the other hand, for the higher range of Hf loadings, L may decrease due to 1) formation of dimeric/oligomeric Hf species which may possess reduced acidity and/or hinder the access of pyridine molecules to some acid sites of the aluminosilicate support, and 2) hafnium oxide nanoparticles formed at higher y may possess inaccessible Hf sites. For yHf-D-HL(0.15), the L/B ratios (1.7–2.5) did not vary considerably with y, whereas for yHf-D-HL(0.28) the L/B ratio (2.4–9.0) increased considerably with increasing y in the range 0.28–1.68 mmolHf g−1 (Figure 6).
In general, the yHf-D-HL(x) materials possessed moderate to strong L acid sites (L350/L150 up to ca. 0.33) and did not possess strong B acid sites (B350/B150 ≅ 0), Supplementary Table S3. For the 0.28Hf-D-HL(x) materials (i.e., Si/Al varied and Hf load was similar), the L acid strength increased with increasing x above 0.15 M H2SO4 (L350/L150 was similar for x = 0.10 and 0.15). On the other hand, the influence of y on the L acid strength was not straightforward: for yHf-D-HL(0.15), the L acid strength decreased with increasing y, whereas for yHf-D-HL(0.28) no straightforward relationship could be established. The acid properties may depend on several factors. The PXRD data indicated that condensed hafnium oxide species may be formed at higher y, which may impact on the amount and strength of accessible acid sites. The materials yHf-D-HL(x) may possess different metal (Al, Hf) acid sites, chemical structures and coordination spheres, bond angles/lengths and binding energies (e.g., distorted geometries), etc. For example, according to the literature, framework Lewis acid Hf sites may be hydrolyzed or non-hydrolyzed species, and the former may be stronger than the latter (Tang et al., 2019).
As mentioned in the Introduction, HMF, AnL and LA may be formed in carbohydrate conversion processes, and converted to GVL under acid and reduction conditions, and thus it is interesting to study their reactivities, envisaging future integrated reaction systems over multifunctional catalysts. The acid sites of the aluminosilicate LTL framework may promote the acid reactions (e.g., esterification, etherification). On the other hand, desilication and partial dealumination of the framework may form vacant sites for introducing hafnium via SSI, furnishing the zeolite with CTH activity. In this fashion, multifunctional LTL type catalysts may be produced, capable of promoting several paths that lead to target bioproducts.
To study the influence of the post-synthesis conditions, the catalytic studies consisted of firstly studying the influence of the acid treatment (dealumination degree) of D-HL(x) (x = 0.10, 0.15, 0.20 or 0.28 M H2SO4) on the LA reaction, keeping constant the amount of impregnated hafnium (y = 0.28 mmolHf g−1). Subsequently, the influence of the Hf loading (y in the range 0.28–1.68 mmolHf g−1) was studied for two sets of materials, namely (crystalline micro/mesoporous) yHf-D-HL(0.15) and (mostly amorphous, mesoporous) yHf-D-HL(0.28). Kinetic, mechanistic, catalyst stability and finally substrate scope (AnL, HMF) were studied for selected catalysts.
The reaction of LA in the presence of the yHf-D-HL(x) materials gave GVL and 2BL in a high total yield (>90%) with molar ratios GVL/2BL in the range 0.2–3.5, at 200°C, 24 h. Without a catalyst, the reaction was much slower and GVL was not formed, under similar conditions (17% conversion, 9% 2BL yield) (Figure 7).
FIGURE 7. Catalytic performances of the prepared catalysts (A,B) for LA conversion (*) to GVL (black bars) and 2BL (white bars). Tests without catalyst or in the presence of HfO2 are included for comparison (A). Reaction conditions: 0.45 M LA in 2BuOH, 200°C, 24 h.
Literature studies suggest that the conversion of LA to GVL in alcohol medium may be favoured by L and B acidity (Li et al., 2017; Xu et al., 2017; Li et al., 2018; Tang et al., 2019; He et al., 2020; Li et al., 2021), such as Lewis acid Hf sites (Kumar et al., 2016; Tang et al., 2019). A comparative study for the aluminosilicates HL and D-HL(0.15) (both prepared via acid treatment using x = 0.15 M H2SO4), and the respective Hf-containing materials 0.28Hf-HL and 0.28Hf-D-HL(0.15), indicated that the aluminosilicates effectively converted LA to 2BL, but failed to give GVL (Figure 7A). The formation of GVL required the presence of Hf sites. Nevertheless, bulk HfO2 led to similar results to the blank test without catalyst (24% LA conversion, 8% 2BL yield, and GVL was not formed), suggesting that the type of Hf sites may be determinant for GVL formation.
The zirconium catalyst 0.28Zr-D-HL(0.15) was less effective than its counterpart 0.28Hf-D-HL(0.15); the former led to less than half the GVL yield reached in the presence of 0.28Hf-D-HL(0.15) (9 and 22% GVL yield, at 200°C/24 h) (Figure 7A). Hence, hafnium catalysts seem more promising for the target reaction, which parallels literature studies for Hf- versus Zr-Beta (Antunes et al., 2022a), and Hf- versus Zr- and Sn-USY (Tang et al., 2019).
A comparative study for (non-desilicated) 0.28Hf-HL and (desilicated) 0.28Hf-D-HL(0.15) (which possessed the same Hf loading (y = 0.28 mmolHf g−1) and were subjected to similar acid treatment using x = 0.15 M H2SO4) indicated that the desilicated catalyst 0.28Hf-D-HL(0.15) was more active than 0.28Hf-HL (100 74% and LA conversion, respectively), led to higher 2BL + GVL total yield (90 and 71%, respectively) and higher GVL/2BL molar ratio (0.33 and 0.13, respectively) (Figure 7A), suggesting a favourable effect of desilication on the catalytic performance for targeting GVL.
The influence of the acid treatment (dealumination degree) on the catalytic performance was studied keeping constant the Hf loading (y = 0.28 mmolHf g−1), i.e., comparing the 0.28Hf-D-HL(x) catalysts (Figure 8, Figure 9). Catalysts 0.28Hf-D-HL(x) led mainly to 2BL and GVL, which were formed in high total yield (96–99%, Figure 7), with GVL/2BL molar ratios in the range 0.2–1.4, at 24 h, 200°C. The activity (mmol gcat−1 h−1, based on conversion at 5 h) increased with decreasing x in the order 1.55 (x = 0.28) < 1.68 (x = 0.20) < 1.74 (x = 0.15) < 1.91 (x = 0.10), which correlated with the increasing amounts of B and L acid sites (Figure 8A) and increasing SBET and Smicro (Figure 8B); SEM was roughly constant, and no clear correlation could be established with the L/B ratio.
FIGURE 8. Influence of (A) the amount of acid sites (L (■), B (♦) and L + B (•)) and (B) textural properties (SBET (-), SEM (×), Smicro (*) on catalytic activity of 0.28Hf-D-HL(x) for LA conversion. Reaction conditions: 0.45 M LA in 2BuOH, 25.5 gcat L−1, 200°C, 5 h.
FIGURE 9. Influence of the amount of acid sites (L (■), B (♦) and L + B (•)) and Smicro/SEM ratio (▲), on GVL yield ((A), (C)) and GVL/2BL molar ratio ((B), (D)), at 5 h ((A), (B)) and 24 h ((C), (D)) for the reaction of LA in the presence of 0.28Hf-D-HL(x). Reaction conditions: 0.45 M LA in 2BuOH, 25.5 gcat L−1, 200°C.
Although the activity of 0.28Hf-D-HL(x) decreased with increasing x, GVL yield and GVL/2BL ratios at 5 and 24 h increased (Figure 9). This may be partly due to a levelling off effect of the lower amounts of total acid sites for higher x, by a lower ratio Smicro/SEM which may avoid steric hindrance effects, favouring GVL formation.
Further studies were carried out to check the influence of the Hf loading (y), specifically for the two sets of materials yHf-D-HL(x) with x = 0.15 and 0.28. yHf-D-HL(0.15) led mainly to 2BL (51–71% yield), and GVL was formed in 22–38% yield at 200°C/24 h (Figure 7B), whereas yHf-D-HL(0.28) led mainly to GVL (57–77% yield), and 2BL was formed in 22–45% yield at 200°C/24 h (Figure 7B).
According to the literature, stronger L acidity may enhance CTH activity (Li et al., 2017). However, taking into consideration all the Hf-containing materials prepared (yHf-D-HL(x), 0.28Hf-HL), GVL yield increased somewhat linearly with decreasing L acid strength (R2 = 0.9835) (Figure 10). These results may be due to an interplay of several factors. For example, for materials with y = 0.28 mmolHf g−1, the L acid strength increased with increasing Smicro/SEM (Supplementary Table S2, S3); specifically, L350/L150 was 0.39 (0.28Hf-HL) > 0.33 (0.28Hf-D-HL(0.10)) > 0.32 (0.28Hf-D-HL(0.15)) > 0.17 (0.28Hf-D-HL(0.20)) > 0.15 (0.28Hf-D-HL(0.28)), and Smicro/SEM followed a similar order, 2.21 (0.28Hf-HL) > 1.37 (0.28Hf-D-HL(0.10)) > 0.94 (0.28Hf-D-HL(0.15)) > 0.72 (0.28Hf-D-HL(0.20)) > 0.07 (0.28Hf-D-HL(0.28)). Hence, for these materials with y = 0.28 mmolHf g−1, lower Smicro/SEM may be a main factor in favour of GVL formation. For the remaining materials with y > 0.28 mmolHf g−1, the L acid strength dependency on y (and thus on GVL yields) was not straightforward; higher y may lead to relevant differences in surface chemistry, impacting on catalytic performances.
FIGURE 10. Influence of the L acid strength (based on the ratio L350/L150) on GVL yields for the Hf-containing catalysts. Reaction conditions: 0.45 M LA in 2BuOH, 25.5 gcat L−1, 200°C, 24 h.
In the conversion of LA to GVL, the secondary alcohol (2BuOH) plays multiple roles, i.e., as solvent and as reducing, etherification and esterification agent. The acid-catalyzed esterification of LA gives alkyl levulinates (LE), and the CTH of LA and LE may give 4-hydroxypentanoic acid (HPA) and alkyl 4-hydroxypentanoates (HPE), respectively, i.e., the carbonyl group in position C4 is reduced to an alcohol group. Literature studies reported that HPA/HPE may undergo etherification at the alcohol group in position C4, giving 4-alkoxypentanoic acid (APA) and alkyl 4-alkoxypentanoates (APE), respectively (Tang et al., 2015; Li et al., 2016a; Valekar et al., 2016; Wang et al., 2017). Although HPA/HPE/APA/APE were not identified for the yHf-H-DL(x) catalysts, one cannot exclude their possible formation and subsequent lactonization (and dealkoxylation in the case of HPE/APE) to give GVL (Li et al., 2016a; Wang et al., 2017). According to the literature, even the intrinsic acidity of LA may promote relatively fast lactonization of HPA (Xie et al., 2016; Winoto et al., 2019).
To gain mechanistic insights, the kinetic curves of the reaction of LA were measured for (crystalline, micro/mesoporous) 1.40Hf-D-HL(0.15) and (mostly amorphous, mesoporous) 1.12Hf-D-HL(0.28), at 200°C (Supplementary Figure S9). For the two catalysts, the LA conversion versus time profiles were roughly coincident, and it was verified an approximately linear dependency (R2 ≥ 0.995) of ln ([LA]0/[LA]) on reaction time (considering the integrated rate law: ln ([LA]0/[LA]) = k t, where k is the kinetic constant and t is reaction time) (Supplementary Figure S9A). These results suggest that the reaction rate was apparently first order in LA concentration. Luo et al. reported a first order dependency on substrate concentration, for the reaction of LE to GVL over Hf-zeolites in 2BuOH (Luo et al., 2014).
Despite the similar catalytic activities, the two materials exhibited different kinetic curves of GVL and 2BL formation (Figure 11). For 1.40Hf-D-HL(0.15), GVL and 2BL were formed in parallel until ca. 98% conversion (Figure 11A), suggesting that GVL may be formed from LA without the intermediate formation of 2BL. Somewhat parallel formation of GVL and 2BL was also verified for 1.12Hf-D-HL(0.28) in an initial stage, but as LA conversion increased from 80 to 100% (20% difference), the 2BL yield dropped from 37 to 22% (15% difference) and GVL yield increased considerably from 43 to 77% (34% difference) (Figure 11B). The increment in GVL yield (34%) was approximately equal to the total consumption of LA plus 2BL (35%) in the same time interval (8–24 h), suggesting that both LA and 2BL were converted to GVL.
FIGURE 11. Dependency of LA conversion (-), GVL yield (Δ) and 2BL yield (o) on reaction time for 1.40Hf-D-HL(0.15) (A) and 1.12Hf-D-HL(0.28) (B). Reaction conditions: 0.45 M LA in 2BuOH, 25.5 gcat L−1, 200°C.
One cannot rule out the hypothesis of other intermediates, besides 2BL, being involved in the formation of GVL. For example, the reaction of LA in the presence of 1.12Hf-D-HL(0.28) using lower [LA]0 of 0.11 M, was complete within 1 h and, yet GVL continued to be formed (64–91% GVL yield between 1 and 5 h), while 2BL concentration remained approximately constant (9–10% 2BL yield between 1 and 5 h) (Supplementary Figure S9B). Hence, it seems that the intermediates to GVL were not fully quantified. Possible explanations for this include: 1) some intermediates may be essentially adsorbed on the catalyst´s surface and thus not analyzed in the liquid bulk; 2) some intermediates may be unstable under the analytical conditions.
In summary, 1.12Hf-D-HL(0.28) seems to effectively promote GVL formation via intermediate formation of 2BL. This catalyst possessed lower Smicro/SEM than 1.40Hf-D-HL(0.15) (ca. 0.3 and 0.6, respectively), which may facilitate reaction pathways involving bulkier intermediates and transition states, e.g., LE/HPE/APE are bulkier than LA/HPA/APA, respectively. Luo et al. reported for methyl levulinate conversion to GVL over Hf-Beta, in 2BuOH, a dual-binding mechanism where the alkyl levulinate and the alcohol H-donor interacted (involving a hydride shift) with a single metal site forming a voluminous six-membered transition state (Luo et al., 2014). Accordingly, steric hindrance may become important for catalysts possessing higher Smicro/SEM.
Based on the above results, it is interesting to compare the catalytic performances of yHf-D-HL(x) to hafnium silicates possessing high mesopore surface area, such as the mesoporous hafnium silicate Hf-TUD-1(50), previously described by our group (Antunes et al., 2021). Hf-TUD-1(50) possessed a similar Hf load of 0.31 mmolHf g−1 to 0.28Hf-D-HL(0.28), but higher L + B = 130 μmol g−1, L/B = 12 and mesopore specific surface area of ca. 660 m2 g−1 (Antunes et al., 2021); for 0.28Hf-D-HL(0.28), L + B = 47 μmol g−1, L/B = 2.4 and SBET = 119 m2 g−1. Hf-TUD-1(50) led to 29% GVL yield at 200°C/24 h (Supplementary Table S4, entry 6), which was approximately half of that for 0.28Hf-D-HL(0.28) (57% yield), under similar reaction conditions. Hence, the enhanced mesopore surface area of Hf-TUD-1(50) was not sufficient to warrant high GVL yield. Catalyst 0.28Hf-D-HL(0.28) possesses distinct surface chemistry partly because it has in its genesis an LTL type (starting) material.
To the best of our knowledge, this is the first study for LTL zeotype catalysts for LA conversion to GVL. Supplementary Table S4 further compares the catalytic performance of yHf-D-HL(x) to literature data for the reaction of LA to GVL, in the presence of micro/mesoporous zeotypes or mesoporous silicas/silicates, using an alcohol as reducing agent (Kuwahara et al., 2014; Antunes et al., 2015, 2016a, 2016b; Hengne et al., 2016; Winoto et al., 2016; Kuwahara et al., 2017; Xu et al., 2017; Zhou et al., 2018; Kumar and Srivastava, 2019; Morales et al., 2019; Tang et al., 2019; He et al., 2020; Kumaravel et al., 2020; López-Aguado et al., 2020; García et al., 2021; Ostovar et al., 2021; Antunes et al., 2022a). The different studies were carried out using different reaction conditions, making it difficult to establish clear comparisons. Without considering the differences in reaction conditions, and based solely on GVL yields, the best result for 0.28Hf-D-HL(0.28) (91% GVL yield, entry 5) was comparable to some of the best results indicated in Supplementary Table S4. GVL yields of at least 90% were reported for micro/mesoporous zeotypes such as Hf-WdeSAlBeta-m (entry 7) (Antunes et al., 2022a), Hf-USY (entry 17) (Tang et al., 2019) and Zr-AlBeta (entry 11) (López-Aguado et al., 2020) which led to 99% (180°C/24 h), 95% (150°C/10 h) and 92% GVL yield (170°C/6 h), respectively, and some Zr-containing mesoporous SBA-15 type catalysts (synthesized using the relatively expensive polymeric template Pluronic P123) which led to 90–95% GVL yield (entries 19, 20) (Kuwahara et al., 2014, 2017; Zhou et al., 2018). Catalyst 1.12Hf-D-HL(0.28) led to 64% GVL yield at 200°C/1 h (Figure 9B), which was higher than that reported for Ni-Sepiolite (<1% yield at 180°C/2 h, entry 25) (García et al., 2021). Moderate GVL yields were reported for a composite Zr-AlBeta/TUD-1 (31% at 150°C/72 h, entry 13) (Antunes et al., 2016b) and mesoporous Zr (7.6wt%)-SBA-15-SGD (33% at 160°C/6 h, entry 18) (Ostovar et al., 2021). GVL was not formed for Zr-TUD-1 and ZrAl-TUD-1 at 120°C/24 h (entries 14 and 15, respectively) (Antunes et al., 2016b; 2016a).
The fresh and used catalysts 0.28Hf-D-HL(x) (x = 0.10, 0.15, 0.20, 0.28) exhibited similar (white) colour, and the material balances closed in at least 91 mol%, considering GVL and 2BL as the useful bioproducts. ATR FT-IR spectroscopy indicated the presence of carbonaceous matter in the solids (exemplified for 0.28Hf-D-HL(0.15) in Supplementary Figure S10). The used catalyst exhibited new weak bands which were not verified for the fresh catalyst; ca. 1,460 cm−1 assignable to C-H vibrations of adsorbed organic matter (O´Dell et al., 2008), ca. 1,377 cm−1 assignable to metal-alkoxide type groups (Lynch et al., 1964), ca. 1,700 cm−1 which may be associated with the carbonyl moiety of carboxylic acid or ester functional groups (Nandiyanto et al., 2019), and ca. 1,400 cm−1 assignable to carboxylate groups (Nandiyanto et al., 2019). The thermal treatment of the catalyst at 550°C led to the disappearance of these new bands, and the spectrum was similar to that of the original catalyst. Hence, the surface chemistry was preserved during the catalytic and thermal regeneration processes. Furthermore, the PXRD patterns of the thermally regenerated solids were similar to those of the respective original catalysts (Supplementary Figure S11).
Elemental analysis of the washed-dried 0.28Hf-D-HL(x) catalysts (after a 5 h batch run) indicated that the carbon content (wt% C) increased with decreasing x, in the order 1.2 wt% (x = 0.28) < 1.7 wt% (x = 0.20) < 2.8 wt% (x = 0.15) < 3.7 w% (x = 0.10). While enhanced adsorption of carbonaceous matter did not seem to negatively affect LA conversion (54, 49, 47 and 44% conversion for x = 0.10, 0.15, 0.20 and 0.28, respectively), it led to decreasing GVL yields and GVL/2BL ratios.
The thermally regenerated solids 1.40Hf-D-HL(0.15) and 1.12Hf-D-HL(0.28) were reused and performed somewhat steadily for five consecutive 5 h-batch runs at 200 °C (Figure 12). For the two catalysts, the contact tests (details in the experimental section) indicated that LP-CT led to similar results to those without catalyst; 14–15% LA conversion, 13–15% 2BL yield, and GVL was not formed (Figure 12). These results suggest that no active species were leached from the catalysts. Consistently, EDS of the fresh and used catalysts indicated that Si/Al and Si/Hf remained similar: for fresh and used 1.40Hf-D-HL(0.15), Si/Al = 8 and Si/Hf = 8; for fresh and used 1.12Hf-D-HL(0.28), Si/Al = 40 and 44, respectively, and Si/Hf = 9 for the two solids. Not only the PXRD patterns (Supplementary Figure S11), but also the morphology and metal distributions (Supplementary Figure S12), textural and acid properties (Supplementary Table S5) of the fresh and used catalysts were roughly comparable, suggesting that the materials were relatively stable.
FIGURE 12. Conversion of LA (*) and yields of GVL (black bars) and 2BL (grey bars) in the presence of (A) 1.40Hf-D-HL(0.15) and (B) 1.12Hf-D-HL(0.28). The contact tests (LP-CT) for each catalyst as well as the blank test (without catalyst at 5 h) are included for comparison. Reaction conditions: 0.45 M LA in 2BuOH, 25.5 gcat L−1, 200°C, 5 h.
The reaction of AnL to GVL involves acid and reduction chemistry (e.g., hydration, CTH and lactonization) (Li et al., 2018; Antunes et al., 2022a, 2022b). According to the literature, the reversible reaction between AnL and LA may occur via hydration-dehydration (Dutta and Bhat, 2021; Liu et al., 2021; Yuan et al., 2021), but AnL was not detected in the experiments using LA as substrate, whereas LA was formed using AnL as substrate. This is in agreement with literature studies for Hf-containing catalysts in alcohol media (Al-Shaal et al., 2015; Li et al., 2018; Antunes et al., 2022b, 2022a).
The reaction of AnL in the presence of HL and D-HL(0.15) gave LA and 2BL in high total yields (88 and 97% yield, respectively, at ca. 100% conversion, 200 °C/24 h), but no GVL was formed (Table 1). Hence, the aluminosilicate supports were essentially effective for converting AnL to 2BL.
TABLE 1. Performance of the prepared catalysts in the reaction of α-angelica lactone.a
The introduction of hafnium was required to confer CTH activity for GVL formation (Table 1). A comparison of 0.28Hf-HL (non-desilicated) and 0.28Hf-D-HL(0.15) (desilicated), both subjected to the same acid treatment (x = 0.15 M H2SO4), indicates a favourable effect of desilication on GVL yield; 9 and 29% for the non-desilicated and the desilicated materials, respectively, at 91–93% AnL conversion, 200°C/24 h.
Increasing x from 0.10 to 0.28 led to 2BL plus GVL, which were formed in a total yield in the range 93–94% at 98–100% AnL conversion (Table 1). In parallel to that verified with LA as substrate, the GVL/2BL ratio (and GVL yields) increased with decreasing Smicro/SEM (increasing x) (Supplementary Figure S13A).
To check the influence of the Hf loading on the AnL reaction, comparative studies were carried out for yHf-D-HL(0.15) with y = 0.28 and 1.40, and, on the other hand, for yHf-D-HL(0.28) with y = 0.28 and 1.12 (Table 1). For each pair of materials with equal x, the GVL/2BL ratio and GVL yields were higher for the catalyst with higher y; the best results were obtained for 1.12Hf-D-HL(0.28), i.e., 54% GVL yield and GVL/2BL = 1.26, at 100% AnL conversion, 200 °C/24 h.
Catalysts yHf-D-HL(x) were further explored for the reaction of HMF (Table 2). The aluminosilicates HL and D-HL(0.15) led to somewhat comparable results; 5-methylfurfural (5MF), 2BL and 5-(sec-butoxymethyl)furfural (BMF) were formed in total yields of 91 and 85%, at 95 and 90% HMF conversion, respectively, 200°C/24 h. The main product was BMF (73–75% yield) which may be formed via etherification of HMF. HMF to BMF may be enhanced by B acid sites (Ly et al., 2017). BMF may undergo acid-catalyzed ring-opening to 2BL, although the latter was formed in only 4–6% yield. On the other hand, 5MF was formed in 8–10% yield. Ly et al. reported minor amounts of 5MF formed in the reaction of HMF in the presence of Al/SiO2 (aluminium supported on a commercial silica) in 2BuOH at 180°C/6 h (Ly et al., 2017). Elsayed et al. reported HMF to 5MF in 1-butanol, at 200°C, in the presence of Zr-Fe magnetic supported on activated carbon (Elsayed et al., 2021). Hence, 5MF may be a by-product in CTH/alcohol systems.
TABLE 2. Performance of the prepared catalysts in the reaction of 5-(hydroxymethyl)furfural (HMF).a
The introduction of hafnium in the materials led mainly to BMF (e.g., 35 and 54% yield for (non-desilicated) 0.28Hf-HL and (desilicated) 0.28Hf-D-HL(0.15), respectively). 2BL was formed in very low amounts, and thus the subsequent conversion of 2BL to GVL did not take place to a measurable extent (Table 2). The diether 2,5-bis(sec-butoxymethyl)furan (BBMF) was formed in up to 21% yield at 200°C/24 h, only in the presence of the Hf-containing catalysts. This path may involve integrated acid (etherification) and CTH (carbonyl group reduction) reactions.
Increasing x for the 0.28Hf-D-HL(x) materials led to decreasing HMF conversion and increasing BBMF yield (Table 2). Although the amounts of B and L acid sites decreased with increasing x, Smicro/SEM decreased, favouring BBMF formation (Supplementary Figure S13B). Steric effects may be important for materials with higher Smicro/SEM, negatively impacting on the formation of the relatively bulky diether BBMF.
The effect of the Hf loading was studied for yHf-D-HL(0.15) (y = 0.28, 1.40 mmolHf g−1) and yHf-D-HL(0.28) (y = 0.28, 1.12) (Table 2). A higher Hf loading did not enhance HMF conversion, total product yields or BBMF yields. No clear relationship could be established between the L acid strength of all the Hf-containing catalysts and BBMF yields. These results did not parallel those for the integrated acid-CTH reactions of LA. According to the literature, the optimal material properties (e.g., L acidity) of Hf-zeolites for CTH reaction systems may depend on the type of substrate (Luo et al., 2014). HMF is a relatively bulky molecule and somewhat less reactive than LA and AnL, which may pose different requirements on materials properties.
Hierarchical multifunctional LTL zeotypes were prepared for the chemical valorization of HMF, LA and AnL via integrated catalytic transfer hydrogenation (CTH) and acid reactions in 2-butanol (2BuOH) at 200°C. This is the first CTH application reported for LTL related materials.
The catalysts were prepared via top-down strategies involving desilication, dealumination (x = 0.10–0.28 M H2SO4) and solid-state impregnation (SSI) of different amounts of hafnium (y), giving yHf-D-HL(x). The influence of the Hf loading (y) was studied for two groups of materials yHf-D-HL(x) with x = 0.15 (crystalline micro/mesoporous) and x = 0.28 (mostly amorphous, mesoporous).
Molecular level spectroscopic studies indicated: broader distributions of Altetra sites with increasing x; SSI/calcination introduced Lewis acid Hf sites; and the Hf loading (y) may affect, to different extents, the textural properties, distributions and types (and strength) of acid sites, etc. Mechanistic and kinetic studies suggested that Al sites may promote esterification and etherification reactions (e.g., LA to 2BL), whereas Hf sites were required for CTH (e.g., GVL formation from LA and AnL).
For materials with y = 0.28 mmolHf g−1 (lower Hf loading), GVL yields increased with decreasing Lewis acid strength and Smicro/SEM ratio. The decreasing L acid strength may avoid strongly adsorbed carbonaceous matter on the catalysts, and, on the other hand, lower Smicro/SEM may avoid steric hindrance and facilitate cyclization of intermediates (especially of relatively bulky ones, e.g., esters versus corresponding carboxylic acids), enhancing GVL formation. For materials with y > 0.28 mmolHf g−1, GVL formation may depend on an interplay of several factors, e.g., L acid strength, distribution and type of acid sites.
Although 0.28Hf-D-HL(0.28) was mostly amorphous and mesoporous, it performed far superiorly to ordered mesoporous hafnium silicate Hf-TUD-1 possessing similar Hf loading. The top-down strategy and, on the other hand, having an LTL zeolite in its genesis, may result in unique surface properties of yHf-D-HL(0.28) type materials. The 1.12Hf-D-HL(0.28) catalyst led to 77% GVL yield at 200°C/24 h (using 0.45 M initial LA concentration), and 91% GVL yield at 200°C/5 h (0.11 M initial LA concentration).
HMF was a more demanding substrate than LA and AnL for the formation of GVL. The main product was BMF, and GVL was not formed in measurable amounts at 200°C/24 h. HMF conversion to BMF and 2BL did not require Hf sites (HL was effective), whereas the diether BBMF was solely formed in the presence of Hf-containing catalysts (21% yield for 0.28Hf-D-HL(0.28)).
Based on catalytic and characterization studies, the materials were relatively stable. The zirconium catalyst 0.28Zr-D-HL(0.15) possessed acid and CTH activity, but performed inferiorly to the analogue 0.28Hf-D-HL(0.15).
Overall, post-synthesis modifications of commercial LTL zeolites may broaden their catalytic application profiles. The top-down strategies and conditions may be optimized to tune material properties and meet superior catalytic performances. A challenge may be to further enhance mesoporosity without considerable reduction of crystallinity.
The original contributions presented in the study are included in the article/Supplementary Material, further inquiries can be directed to the corresponding authors.
MA: data curation, formal analysis, investigation, methodology, conceptualization, writing–original draft preparation, validation, visualization, writing–review and editing. AFS: data curation, formal analysis, investigation, methodology, writing–original draft preparation. AF: data curation, formal analysis, investigation, methodology. FR: formal analysis, funding acquisition. PN: data curation, formal analysis. MP: visualization, writing–review and editing. AAV: conceptualization, validation, visualization, project administration, writing–review and editing, and supervision.
This work was developed within the scope of the project CICECO-Aveiro Institute of Materials, UIDB/50011/2020, UIDP/50011/2020 & LA/P/0006/2020, financed by national funds through the FCT/MEC (PIDDAC). The positions held by MMA and AF were funded by national funds (OE), through FCT, IP, in the scope of the framework contract foreseen in the numbers 4, 5 and 6 of article 23 of the Decree-Law 57/2016 of 29 August, changed by Law 57/2017 of 19 July. The position held by AFS was funded by Project POCI-01-0145-FEDER-030075 (COMPETE 2020 Operational Thematic Program for Competitiveness and Internationalization) co-financed by national funds through the FCT/MCTES and the European Union through the European Regional Development Fund under the Portugal 2020 Partnership Agreement. The NMR spectrometer used is part of the National NMR Network (PTNMR) and is partially supported by Infrastructure Project No 022161 (co-financed by FEDER through COMPETE 2020, POCI and PORL and FCT through PIDDAC).
The authors are grateful to Dr. Rosário Soares from Chemistry Department, CICECO-Aveiro Institute of Materials (University of Aveiro) for the helpful measurements of RC (PXRD). The authors thank all funding institutions indicated in the previous section.
The authors declare that the research was conducted in the absence of any commercial or financial relationships that could be construed as a potential conflict of interest.
All claims expressed in this article are solely those of the authors and do not necessarily represent those of their affiliated organizations, or those of the publisher, the editors and the reviewers. Any product that may be evaluated in this article, or claim that may be made by its manufacturer, is not guaranteed or endorsed by the publisher.
The Supplementary Material for this article can be found online at: https://www.frontiersin.org/articles/10.3389/fchem.2022.1006981/full#supplementary-material
Al-Ani, A., Haslam, J. J. C., Mordvinova, N. E., Lebedev, O. I., Vicente, A., Fernandez, C., et al. (2019). Synthesis of nanostructured catalysts by surfactant-templating of large-pore zeolites. Nanoscale Adv. 1, 2029–2039. doi:10.1039/c9na00004f
Al-Shaal, M. G., Ciptonugroho, W., Holzhäuser, F. J., Mensah, J. B., Hausoul, P. J. C., and Palkovits, R. (2015). Catalytic upgrading of α-angelica lactone to levulinic acid esters under mild conditions over heterogeneous catalysts. Catal. Sci. Technol. 5, 5168–5173. doi:10.1039/c5cy00446b
Antonetti, C., Licursi, D., Fulignati, S., Valentini, G., and Galletti, A. M. R. (2016). New frontiers in the catalytic synthesis of levulinic acid: From sugars to raw and waste biomass as starting feedstock. Catalysts 6, 196. doi:10.3390/catal6120196
Antunes, M. M., Lima, S., Neves, P., Magalhães, A. L., Fazio, E., Fernandes, A., et al. (2015). One-pot conversion of furfural to useful bio-products in the presence of a Sn, Al-containing zeolite beta catalyst prepared via post-synthesis routes. J. Catal. 329, 522–537. doi:10.1016/j.jcat.2015.05.022
Antunes, M. M., Lima, S., Neves, P., Magalhães, A. L., Fazio, E., Neri, F., et al. (2016a). Integrated reduction and acid-catalysed conversion of furfural in alcohol medium using Zr, Al-containing ordered micro/mesoporous silicates. Appl. Catal. B Environ. 182, 485–503. doi:10.1016/j.apcatb.2015.09.053
Antunes, M. M., Neves, P., Fernandes, A., Lima, S., Silva, A. F., Ribeiro, M. F., et al. (2016b). Bulk and composite catalysts combining BEA topology and mesoporosity for the valorisation of furfural. Catal. Sci. Technol. 6, 7812–7829. doi:10.1039/c6cy00223d
Antunes, M. M., Silva, A. F., Bernardino, C. D., Fernandes, A., Ribeiro, F., and Valente, A. A. (2021). Catalytic transfer hydrogenation and acid reactions of furfural and 5-(hydroxymethyl)furfural over Hf-TUD-1 type catalysts. Molecules 26, 7203. doi:10.3390/molecules26237203
Antunes, M. M., Silva, A. F., Fernandes, A., Pillinger, M., Ribeiro, F., and Valente, A. A. (2022a). Renewable bio-based routes to γ-valerolactone in the presence of hafnium nanocrystalline or hierarchical microcrystalline zeotype catalysts. J. Catal. 406, 56–71. doi:10.1016/j.jcat.2021.12.022
Antunes, M. M., Silva, A. F., Fernandes, A., and Valente, A. A. (2022b). γ-Valerolactone synthesis from α-angelica lactone and levulinic acid over biobased multifunctional nanohybrid catalysts. Catal. Today 394–396, 268–281. doi:10.1016/j.cattod.2021.08.027
Bassi, R., Baeza, P., Sepulveda, C., Ghampson, I. T., Camu, E., Brückner, A., et al. (2021). Conversion of levulinic acid over rhenium oxide catalysts: Effect of metal content. Appl. Catal. A Gen. 625, 118328. doi:10.1016/j.apcata.2021.118328
Broach, R. W. (2010). “Zeolite types and structures,” in Zeolites in industrial separation and catalysis. Editor Dr. Santi Kulprathipanja (Glasgow: Wiley‐VCH Verlag GmbH & Co. KGaA), 27–59. doi:10.1002/9783527629565
Čejka, J., Millini, R., Opanasenko, M., Serrano, D. P., and Roth, W. J. (2020). Advances and challenges in zeolite synthesis and catalysis. Catal. Today 345, 2–13. doi:10.1016/j.cattod.2019.10.021
Cheng, F., and Brewer, C. E. (2021). Conversion of protein-rich lignocellulosic wastes to bio-energy: Review and recommendations for hydrolysis + fermentation and anaerobic digestion. Renew. Sustain. Energy Rev. 146, 111167. doi:10.1016/j.rser.2021.111167
Cho, J., Kim, S., Lee, D., Kim, B.-R., and Jung, J.-W. (2014). Method for producing biofuel using marrine algae-derived galactan. US Pat. U. S. 8, 795393.
Data Intelo (2022). Global gamma valerolactone (CAS 108-29-2) market by type (food grade, industrial grade), by application (food flavors, solvent, monomer intermediate, others) and by region (North America, Latin America, Europe, Asia Pacific, and Middle East and Africa). Ontario, United States. Available at: https://dataintelo.com/report/global-gamma-valerolactone-%28cas-108-29-2%29-market/ (Accessed July 24, 2022).)
Di Bucchianico, D. D. M., Wang, Y., Buvat, J. C., Pan, Y., Casson Moreno, V., and Leveneur, S. (2022). Production of levulinic acid and alkyl levulinates: A process insight. Green Chem. 24, 614–646. doi:10.1039/d1gc02457d
Dutta, S., and Bhat, N. S. (2021). Recent advances in the value addition of biomass-derived levulinic acid: A review focusing on its chemical reactivity patterns. ChemCatChem 13, 3202–3222. doi:10.1002/cctc.202100032
Dutta, S. (2021). Valorization of biomass-derived furfurals: Reactivity patterns, synthetic strategies, and applications. Biomass Convers. Biorefin. doi:10.1007/s13399-021-01924-w
Dutta, S., Yu, I. K. M., Tsang, D. C. W., Ng, Y. H., Ok, Y. S., Sherwood, J., et al. (2019). Green synthesis of gamma-valerolactone (GVL) through hydrogenation of biomass-derived levulinic acid using non-noble metal catalysts: A critical review. Chem. Eng. J. 372, 992–1006. doi:10.1016/j.cej.2019.04.199
Elsayed, I., Jackson, M. A., and Hassan, E. B. (2021). Catalytic hydrogenation and etherification of 5-Hydroxymethylfurfural into 2-(alkoxymethyl)-5-methylfuran and 2, 5-bis(alkoxymethyl)furan as potential biofuel additives. Fuel Process. Technol. 213, 106672. doi:10.1016/j.fuproc.2020.106672
Fact, M. R. (2022). 5-Hydroxymethylfurfural market. Available at: https://www.factmr.com/report/5-hydroxymethylfurfural-market (Accessed July 24, 2022).
Fitzpatrick, S. W. (1995). Production of levulinic acid from carbohydrate-containing materials. US 5608105A.
García, A., Miguel, P. J., Pico, M. P., Álvarez-Serrano, I., López, M. L., García, T., et al. (2021). γ-valerolactone from levulinic acid and its esters: Substrate and reaction media determine the optimal catalyst. Appl. Catal. A Gen. 623, 118276. doi:10.1016/j.apcata.2021.118276
Gilkey, M. J., and Xu, B. (2016). Heterogeneous catalytic transfer hydrogenation as an effective pathway in biomass upgrading. ACS Catal. 6, 1420–1436. doi:10.1021/acscatal.5b02171
Grand View Research (2021). Levulinic acid market demand to reach 3,820 tons by 2020. Available at: https://www.grandviewresearch.com/press-release/global-levulinic-acid-market (Accessed July 24, 2022).
Gregg, S. J., and Sing, K. S. W. (1982). Adsorption surface area and porosity. 2nd ed. London, UK: Academic Press.
Gruter, G. J. M. (2009). Hydroxymethylfurfural ethers from sugars or HMF and branched alcohols. WO/2009/030506.
He, J., Li, H., Xu, Y., and Yang, S. (2020). Dual acidic mesoporous KIT silicates enable one-pot production of γ-valerolactone from biomass derivatives via cascade reactions. Renew. Energy 146, 359–370. doi:10.1016/j.renene.2019.06.105
Hengne, A. M., Kadu, B. S., Biradar, N. S., Chikate, R. C., and Rode, C. V. (2016). Transfer hydrogenation of biomass-derived levulinic acid to γ-valerolactone over supported Ni catalysts. RSC Adv. 6, 59753–59761. doi:10.1039/c6ra08637c
Hou, Q., Qi, X., Zhen, M., Qian, H., Nie, Y., Bai, C., et al. (2021). Biorefinery roadmap based on catalytic production and upgrading 5-hydroxymethylfurfural. Green Chem. 23, 119–231. doi:10.1039/d0gc02770g
Hu, L., Jiang, Y., Wang, X., He, A., Xu, J., and Wu, Z. (2020). Recent advances and mechanistic insights on the production of biomass-derived 2, 5-bis(alkoxymethyl)furans. Biomass Convers. Biorefin. doi:10.1007/s13399-020-01062-9
Hu, L., Xu, J., Zhou, S., He, A., Tang, X., Lin, L., et al. (2018). Catalytic advances in the production and application of biomass-derived 2, 5-dihydroxymethylfuran. ACS Catal. 8, 2959–2980. doi:10.1021/acscatal.7b03530
Huang, X., Liu, K., Vrijburg, W. L., Ouyang, X., Iulian Dugulan, A., Liu, Y., et al. (2020). Hydrogenation of levulinic acid to γ-valerolactone over Fe-Re/TiO2 catalysts. Appl. Catal. B Environ. 278, 119314. doi:10.1016/j.apcatb.2020.119314
Huang, R., Liu, Y., Zhang, J., Wei, J., Peng, L., and Tang, X. (2021). Catalytic transfer hydrogenation of levulinic acid to γ-valerolactone over an acids-base trifunctional Hf-bagasse coordination complex derived catalyst. Fuel 305, 121557. doi:10.1016/j.fuel.2021.121557
Jori, P. K., and Jadhav, V. H. (2020). Efficient synthesis of γ-valerolactone-A potential fuel from biomass derived levulinic acid using catalytic transfer hydrogenation over Hf@CCSO3H catalyst. Catal. Lett. 150, 2038–2044. doi:10.1007/s10562-020-03119-w
Kong, Q. S., Li, X. L., Xu, H. J., and Fu, Y. (2020). Conversion of 5-hydroxymethylfurfural to chemicals: A review of catalytic routes and product applications. Fuel Process. Technol. 209, 106528. doi:10.1016/j.fuproc.2020.106528
Kong, X., Zhu, Y., Fang, Z., Kozinski, J. A., Butler, I. S., Xu, L., et al. (2018). Catalytic conversion of 5-hydroxymethylfurfural to some value-added derivatives. Green Chem. 20, 3657–3682. doi:10.1039/c8gc00234g
Koul, B., Yakoob, M., and Shah, M. P. (2022). Agricultural waste management strategies for environmental sustainability. Environ. Res. 206, 112285. doi:10.1016/j.envres.2021.112285
Kumar, A., and Srivastava, R. (2019). CePO4, a multi-functional catalyst for carbohydrate biomass conversion: Production of 5-hydroxymethylfurfural, 2,5-diformylfuran, and γ-valerolactone. Sustain. Energy Fuels 3, 2475–2489. doi:10.1039/c9se00272c
Kumar, V. V., Naresh, G., Sudhakar, M., Anjaneyulu, C., Bhargava, S. K., Tardio, J., et al. (2016). An investigation on the influence of support type for Ni catalysed vapour phase hydrogenation of aqueous levulinic acid to γ-valerolactone. RSC Adv. 6, 9872–9879. doi:10.1039/c5ra24199e
Kumaravel, S., Thiripuranthagan, S., Durai, M., Erusappan, E., and Vembuli, T. (2020). Catalytic transfer hydrogenation of biomass-derived levulinic acid to γ-valerolactone over Sn/Al-SBA-15 catalysts. New J. Chem. 44, 8209–8222. doi:10.1039/d0nj01288b
Kuwahara, Y., Kaburagi, W., and Fujitani, T. (2014). Catalytic conversion of LevulinicAcid and its esters to γ-valerolactone over silica-supported zirconia catalysts. Bull. Chem. Soc. Jpn. 87, 1252–1254. doi:10.1246/bcsj.20140205
Kuwahara, Y., Kaburagi, W., Osada, Y., Fujitani, T., and Yamashita, H. (2017). Catalytic transfer hydrogenation of biomass-derived levulinic acid and its esters to γ-valerolactone over ZrO2 catalyst supported on SBA-15 silica. Catal. Today 281, 418–428. doi:10.1016/j.cattod.2016.05.016
Kuznetsova, E. D., Blatova, O. A., and Blatov, V. A. (2018). Predicting new zeolites: A combination of thermodynamic and kinetic factors. Chem. Mater. 30, 2829–2837. doi:10.1021/acs.chemmater.8b00905
Lee, K., and Choi, M. (2016). Hierarchically micro-/mesoporous Pt/KL for alkane aromatization : Synergistic combination of high catalytic activity and suppressed hydrogenolysis. J. Catal. 340, 66–75. doi:10.1016/j.jcat.2016.05.010
Li, F., France, L. J., Cai, Z., Li, Y., Liu, S., Lou, H., et al. (2017). Catalytic transfer hydrogenation of butyl levulinate to γ-valerolactone over zirconium phosphates with adjustable Lewis and Brønsted acid sites. Appl. Catal. B Environ. 214, 67–77. doi:10.1016/j.apcatb.2017.05.013
Li, H., Fang, Z., and Yang, S. (2016a). Direct catalytic transformation of biomass derivatives into biofuel component γ-valerolactone with magnetic nickel-zirconium nanoparticles. ChemPlusChem 81, 135–142. doi:10.1002/cplu.201500492
Li, H., Yang, S., Riisager, A., Pandey, A., Sangwan, R. S., Saravanamurugan, S., et al. (2016b). Zeolite and zeotype-catalysed transformations of biofuranic compounds. Green Chem. 18, 5701–5735. doi:10.1039/c6gc02415g
Li, H., Yang, T., and Fang, Z. (2018). Biomass-derived mesoporous Hf-containing hybrid for efficient Meerwein- Ponndorf-Verley reduction at low temperatures. Appl. Catal. B Environ. 227, 79–89. doi:10.1016/j.apcatb.2018.01.017
Li, J., Zhao, S., Li, Z., Liu, D., Chi, Y., and Hu, C. (2021). Efficient conversion of biomass-derived levulinic acid to γ-valerolactone over polyoxometalate@Zr-based Metal−Organic frameworks: The synergistic effect of Brønsted and Lewis acidic sites. Inorg. Chem. 60, 7785–7793. doi:10.1021/acs.inorgchem.1c00185
Li, X., Du, Z., Wu, Y., Zhen, Y., Shao, R., Li, B., et al. (2020). A novel hafnium-graphite oxide catalyst for the Meerwein-Ponndorf-Verley reaction and the activation effect of the solvent. RSC Adv. 10, 9985–9995. doi:10.1039/c9ra10795a
Liguori, F., Moreno-Marrodan, C., and Barbaro, P. (2015). Environmentally friendly synthesis of γ-valerolactone by direct catalytic conversion of renewable sources. ACS Catal. 5, 1882–1894. doi:10.1021/cs501922e
Lima, C. G. S., Monteiro, J. L., de Melo Lima, T., Weber Paixão, M., and Corrêa, A. G. (2018). Angelica lactones: From biomass-derived platform chemicals to value-added products. ChemSusChem 11, 25–47. doi:10.1002/cssc.201701469
Liu, X., Yu, D., Luo, H., and Li, C. (2022). Catalytic upgrading of lignocellulosic biomass sugars toward biofuel 5-ethoxymethylfurfural. Front. Chem. 9, 831102. doi:10.3389/fchem.2021.831102
Liu, Y., Liu, X., Li, M., Meng, Y., Li, J., Zhang, Z., et al. (2021). Recyclable Zr/Hf-containing acid-base bifunctional catalysts for hydrogen transfer upgrading of biofuranics: A review. Front. Chem. 9, 812331. doi:10.3389/fchem.2021.812331
López-Aguado, C., Paniagua, M., Melero, J. A., Iglesias, J., Juárez, P., Granados, M. L., et al. (2020). Stable continuous production of γ-valerolactone from biomass-derived levulinic acid over Zr-Al-Beta zeolite catalyst. Catalysts 10, 678. doi:10.3390/catal10060678
Lu, Y., Wang, Y., Tang, Q., Cao, Q., and Fang, W. (2022). Synergy in Sn-Mn oxide boosting the hydrogenation catalysis of supported Pt nanoparticles for selective conversion of levulinic acid. Appl. Catal. B Environ. 300, 120746. doi:10.1016/j.apcatb.2021.120746
Luo, H. Y., Consoli, D. F., Gunther, W. R., and Román-Leshkov, Y. (2014). Investigation of the reaction kinetics of isolated Lewis acid sites in Beta zeolites for the Meerwein-Ponndorf-Verley reduction of methyl levulinate to γ-valerolactone. J. Catal. 320, 198–207. doi:10.1016/j.jcat.2014.10.010
Ly, N., Al-Shamery, K., Chan-Thaw, C. E., Prati, L., Carniti, P., and Gervasini, A. (2017). Impact of support oxide acidity in Pt-catalyzed HMF hydrogenation in alcoholic medium. Catal. Lett. 147, 345–359. doi:10.1007/s10562-016-1945-9
Lynch, C. T., Mazdiyasni, K. S., Smith, J. S., and Crawford, W. J. (1964). Infrared spectra of transition metal alkoxides. Anal. Chem. 36, 2332–2337. doi:10.1021/ac60218a034
Mafra, L., Vidal-moya, J. A., and Blasco, T. (2012). “Structural characterization of zeolites by advanced solid state NMR spectroscopic methods,” in Annual reports on NMR spectroscopy (Elsevier B.V.), 259–351. doi:10.1016/B978-0-12-397020-6.00004-0
Manzer, L. (2005). Preparation of levulinic acid asters from α-angelic lactone and olefins; use of ester compositions as fuel additivies. WO 2005/075405.
Maumela, M., Marx, S., and Meijboom, R. (2021). Heterogeneous Ru catalysts as the emerging potential superior catalysts in the selective hydrogenation of bio-derived levulinic acid to γ-valerolactone: Effect of particle size, solvent, and support on activity, stability, and selectivity. Catalysts 11. doi:10.3390/catal11020292
Mon, M., and Leyva-Pérez, A. (2021). “Chapter Two - zeolites catalyze selective reactions of large organic molecules,” in Advances in catalysis. Editors O. Diéguez, Montserrat, and Pàmies (Elsevier B.V.), 59–102.
Morales, G., Melero, J. A., Iglesias, J., Paniagua, M., and López-Aguado, C. (2019). From levulinic acid biorefineries to γ-valerolactone (GVL) using a bi-functional Zr-Al-Beta catalyst. React. Chem. Eng. 4, 1834–1843. doi:10.1039/c9re00117d
Mordor Intelligence (2022). Levulinic acid market- growth, trends, covid-19 impact, and forecasts (2022–2027). Available at: https://www.mordorintelligence.com/industry-reports/levulinic-acid-market (Accessed July 24, 2022).
Morone, A., Apte, M., and Pandey, R. A. (2015). Levulinic acid production from renewable waste resources: Bottlenecks, potential remedies, advancements and applications. Renew. Sustain. Energy Rev. 51, 548–565. doi:10.1016/j.rser.2015.06.032
Nandiyanto, A. B. D., Oktiani, R., and Ragadhita, R. (2019). How to read and interpret FTIR spectroscope of organic material. Indones. J. Sci. Technol. 4, 97–118. doi:10.17509/ijost.v4i1.15806
Narisetty, V., Cox, R., Bommareddy, R., Agrawal, D., Ahmad, E., Pant, K. K., et al. (2022). Valorisation of xylose to renewable fuels and chemicals, an essential step in augmenting the commercial viability of lignocellulosic biorefineries. Sustain. Energy Fuels 6, 29–65. doi:10.1039/d1se00927c
Nie, R., Tao, Y., Nie, Y., Lu, T., Wang, J., Zhang, Y., et al. (2021). Recent advances in catalytic transfer hydrogenation with formic acid over heterogeneous transition metal catalysts. ACS Catal. 11, 1071–1095. doi:10.1021/acscatal.0c04939
Nilesh, Q., Tangale, P., Sonar, S. K., Niphadkar, P. S., and Joshi, P. N. (2016). Hierarchical K/LTL zeolites: Synthesis by alkali treatment, characterization and catalytic performance in Knoevenagel condensation reaction. J. Ind. Eng. Chem. 40, 128–136. doi:10.1016/j.jiec.2016.06.016
Ostovar, S., Saravani, H., and Rodríguez-Padrón, D. (2021). Versatile functionalized mesoporous Zr/SBA-15 for catalytic transfer hydrogenation and oxidation reactions. Renew. Energy 178, 1070–1083. doi:10.1016/j.renene.2021.06.095
O´Dell, L. A. G., Philips, N., Holland, M. A., Mountjoy, G., Pickup, D. M., Newport, R. J., et al. (2008). Characterisation of sol–gel prepared (HfO2)x(SiO2)1-x (x = 0.1, 0.2 and 0.4) by 1H, 13C, 17O and 29Si MAS NMR, FTIR and TGA. Solid State Nucl. Magn. Reson. 33, 16–24. doi:10.1016/j.ssnmr.2007.11.001
Poullikkas, A., Omidvarborna, H., and Kim, D. S. (2017). A review on synthesis of alkoxymethyl furfural, a biofuel candidate. Renew. Sustain. Energy Rev. 71, 908–926. doi:10.1016/j.rser.2016.12.118
Ravi, M., Sushkevich, V. L., and Bokhoven, J. A. V. (2021). On the location of Lewis acidic aluminum in zeolite mordenite and the role of framework-associated aluminum in mediating the switch between Brønsted and Lewis acidity. Chem. Sci. 12, 4094–4103. doi:10.1039/d0sc06130a
Rojas-Buzo, S., García-García, P., and Corma, A. (2018). Catalytic transfer hydrogenation of biomass-derived carbonyls over hafnium-based metal–organic frameworks. ChemSusChem 11, 432–438. doi:10.1002/cssc.201701708
Roy, S., Dikshit, P. K., Sherpa, K. C., Singh, A., Jacob, S., and Chandra Rajak, R. (2021). Recent nanobiotechnological advancements in lignocellulosic biomass valorization: A review. J. Environ. Manage. 297, 113422. doi:10.1016/j.jenvman.2021.113422
Sajid, M., Farooq, U., Bary, G., Azim, M. M., and Zhao, X. (2021). Sustainable production of levulinic acid and its derivatives for fuel additives and chemicals: Progress, challenges, and prospects. Green Chem. 23, 9198–9238. doi:10.1039/d1gc02919c
Serrano, D. P., Melero, J. A., Morales, G., Iglesias, J., and Pizarro, P. (2018). Progress in the design of zeolite catalysts for biomass conversion into biofuels and bio-based chemicals. Catal. Rev. 60, 1–70. doi:10.1080/01614940.2017.1389109
Tang, B., Li, S., Song, W. C., Yang, E. C., Zhao, X. J., Guan, N., et al. (2019). Hierarchical FAU-type hafnosilicate zeolite as a robust Lewis acid catalyst for catalytic transfer hydrogenation. ACS Sustain. Chem. Eng. 7, 16329–16343. doi:10.1021/acssuschemeng.9b03347
Tang, X., Zeng, X., Li, Z., Li, W., Jiang, Y., Hu, L., et al. (2015). In situ generated catalyst system to convert biomass-derived levulinic acid to γ-valerolactone. ChemCatChem 7, 1372–1379. doi:10.1002/cctc.201500115
Tangale, N. P., Niphadkar, P. S., Joshi, P. N., and Dhepe, P. L. (2019). Hierarchical K/LTL zeolite as solid base for aqueous phase hydrogenation of xylose to xylitol. Microporous Mesoporous Mater. 278, 70–80. doi:10.1016/j.micromeso.2018.11.017
Valekar, A. H., Cho, K. H., Chitale, S. K., Hong, D. Y., Cha, G. Y., Lee, U. H., et al. (2016). Catalytic transfer hydrogenation of ethyl levulinate to γ-valerolactone over zirconium-based metal-organic frameworks. Green Chem. 18, 4542–4552. doi:10.1039/c6gc00524a
Vu, H. T., Harth, F. M., Goepel, M., Linares, N., García–Martínez, J., and Gläser, R. (2022). Enhanced activity of a bifunctional Pt/zeolite Y catalyst with an intracrystalline hierarchical pore system in the aqueous-phase hydrogenation of levulinic acid. Chem. Eng. J. 430, 132763. doi:10.1016/j.cej.2021.132763
Wang, J., Liu, J., Yu, X., Zhang, W., Zhang, G., Liu, M., et al. (2020). Non-noble metal catalysts for transfer hydrogenation of levulinic acid: The role of surface morphology and acid-base pairs. Mat. Today Energy 18, 100501. doi:10.1016/j.mtener.2020.100501
Wang, R., Wang, J., Zi, H., Xia, Y., Wang, H., and Liu, X. (2017). Catalytic transfer hydrogenation of ethyl levulinate to γ-valerolactone over zirconium(IV) Schiff base complexes on mesoporous silica with isopropanol as hydrogen source. Mol. Catal. 441, 168–178. doi:10.1016/j.mcat.2017.07.026
Weng, R., Yu, Z., Xiong, J., and Lu, X. (2020). Effects of water in the heterogeneous catalytic valorization of levulinic acid into γ-valerolactone and its derivatives. Green Chem. 22, 3013–3027. doi:10.1039/d0gc01082k
Werpy, T., and Petersen, G. (2004). Top value added chemicals from biomass volume I. United States: National Renewable Energy Lab, 76. doi:10.2172/15008859
Winoto, H. P., Ahn, B. S., and Jae, J. (2016). Production of γ-valerolactone from furfural by a single-step process using Sn-Al-Beta zeolites: Optimizing the catalyst acid properties and process conditions. J. Ind. Eng. Chem. 40, 62–71. doi:10.1016/j.jiec.2016.06.007
Winoto, H. P., Fikri, Z. A., Ha, J. M., Park, Y. K., Lee, H., Suh, D. J., et al. (2019). Heteropolyacid supported on Zr-Beta zeolite as an active catalyst for one-pot transformation of furfural to γ-valerolactone. Appl. Catal. B Environ. 241, 588–597. doi:10.1016/j.apcatb.2018.09.031
Xie, C., Song, J., Zhou, B., Hu, J., Zhang, Z., Zhang, P., et al. (2016). Porous hafnium phosphonate: Novel heterogeneous catalyst for conversion of levulinic acid and esters into γ-valerolactone. ACS Sustain. Chem. Eng. 4, 6231–6236. doi:10.1021/acssuschemeng.6b02230
Xu, S., Yu, D., Ye, T., and Tian, P. (2017). Catalytic transfer hydrogenation of levulinic acid to γ-valerolactone over a bifunctional tin catalyst. RSC Adv. 7, 1026–1031. doi:10.1039/c6ra25594a
Xue, Z., Liu, Q., Wang, J., and Mu, T. (2018). Valorization of levulinic acid over non-noble metal catalysts: Challenges and opportunities. Green Chem. 20, 4391–4408. doi:10.1039/c8gc02001a
Yakimov, A. V., Ravi, M., Verel, R., Sushkevich, V. L., Bokhoven, J. A. V., and Cop, C.(2022). Structure and framework association of Lewis acid sites in MOR zeolite. J. Am. Chem. Soc. 144, 10377–10385. doi:10.1021/jacs.2c02212
Yu, Z., Lu, X., Bai, H., Xiong, J., Feng, W., and Ji, N. (2020a). Effects of solid acid supports on the bifunctional catalysis of levulinic acid to γ-valerolactone: Catalytic activity and stability. Chem. Asian J. 15, 1182–1201. doi:10.1002/asia.202000006
Yu, Z., Lu, X., Liu, C., Han, Y., and Ji, N. (2019). Synthesis of γ-valerolactone from different biomass-derived feedstocks: Recent advances on reaction mechanisms and catalytic systems. Renew. Sustain. Energy Rev. 112, 140–157. doi:10.1016/j.rser.2019.05.039
Yu, Z., Lu, X., Xiong, J., Li, X., Bai, H., and Ji, N. (2020b). Heterogeneous catalytic hydrogenation of levulinic acid to γ-valerolactone with formic acid as internal hydrogen source. ChemSusChem 13, 2916–2930. doi:10.1002/cssc.202000175
Yuan, Q., Van De Bovenkamp, H. H., Zhang, Z., Piskun, A. S., Sami, S., Havenith, R. W. A., et al. (2021). Mechanistic investigations into the catalytic levulinic acid hydrogenation, insight in H/D exchange pathways, and a synthetic route to d8-γ-valerolactone. ACS Catal. 11, 10467–10477. doi:10.1021/acscatal.1c02662
Zhang, Z. (2016). Synthesis of γ-valerolactone from carbohydrates and its applications. ChemSusChem 9, 156–171. doi:10.1002/cssc.201501089
Zhou, Y. H., Luo, Y. J., Lin, Y. T., and Huang, Y. B. (2018). Enhanced transfer hydrogenation activity of Zr-doped mesoporous silica through sol-gel method for the reduction of biomass-derived unsaturated carbon-oxygen bonds. ChemistrySelect 3, 11071–11080. doi:10.1002/slct.201802176
Keywords: heterogeneous catalysis, vegetable biomass, zeolite LTL, hafnium, levulinic acid, γ-valerolactone, furanics
Citation: Antunes MM, Silva AF, Fernandes A, Ribeiro F, Neves P, Pillinger M and Valente AA (2022) Micro/mesoporous LTL derived materials for catalytic transfer hydrogenation and acid reactions of bio-based levulinic acid and furanics. Front. Chem. 10:1006981. doi: 10.3389/fchem.2022.1006981
Received: 29 July 2022; Accepted: 06 September 2022;
Published: 29 September 2022.
Edited by:
Zhen Ma, Fudan University, ChinaReviewed by:
Sandip Kumar Singh, University of Kansas, United StatesCopyright © 2022 Antunes, Silva, Fernandes, Ribeiro, Neves, Pillinger and Valente. This is an open-access article distributed under the terms of the Creative Commons Attribution License (CC BY). The use, distribution or reproduction in other forums is permitted, provided the original author(s) and the copyright owner(s) are credited and that the original publication in this journal is cited, in accordance with accepted academic practice. No use, distribution or reproduction is permitted which does not comply with these terms.
*Correspondence: Margarida M. Antunes, bWFyZ2FyaWRhLmFudHVuZXNAdWEucHQ=; Anabela A. Valente, YXRhdkB1YS5wdA==
Disclaimer: All claims expressed in this article are solely those of the authors and do not necessarily represent those of their affiliated organizations, or those of the publisher, the editors and the reviewers. Any product that may be evaluated in this article or claim that may be made by its manufacturer is not guaranteed or endorsed by the publisher.
Research integrity at Frontiers
Learn more about the work of our research integrity team to safeguard the quality of each article we publish.