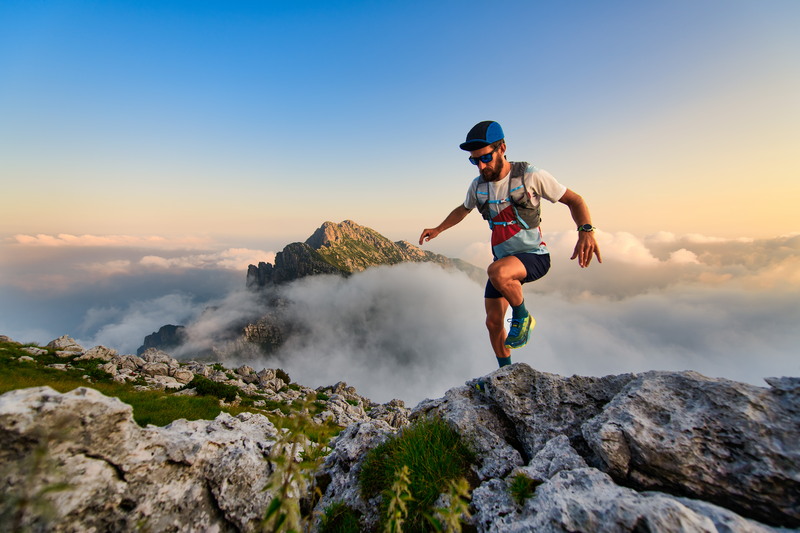
95% of researchers rate our articles as excellent or good
Learn more about the work of our research integrity team to safeguard the quality of each article we publish.
Find out more
ORIGINAL RESEARCH article
Front. Chem. , 14 February 2022
Sec. Inorganic Chemistry
Volume 9 - 2021 | https://doi.org/10.3389/fchem.2021.833024
This article is part of the Research Topic Inorganic Materials for Energy and Environmental Catalysis View all 18 articles
Preparation of the Magnéli Ti4O7 reactive electrochemical membrane (REM) with high purity is of great significance for its application in electrochemical advanced oxidation processes (EAOPs) for wastewater treatment. In this study, the Ti4O7 REM with high purity was synthesized by mechanical pressing of TiO2 powders followed by thermal reduction to Ti4O7 using the Ti powder as the reducing reagent, where the TiO2 monolith and Ti powder were separated from each other with the distance of about 5 cm in the vacuum furnace. When the temperature was elevated to 1333 K, the Magnéli phase Ti4O7 REM with the Ti4O7 content of 98.5% was obtained after thermal reduction for 4 h. Noticeably, the surface and interior of the obtained REM bulk sample has a homogeneous Ti4O7 content. Doping carbon black (0wt%-15wt%) could increase the porosity of the Ti4O7 REM (38–59%). Accordingly, the internal resistance of the electrode and electrolyte and the charge-transfer impedance increased slightly with the increasing carbon black content. The optimum electroactive surface area (1.1 m2) was obtained at a carbon black content of 5wt%, which increased by 1.3-fold in comparison with that without carbon black. The as-prepared Ti4O7 REMs show high oxygen evolution potential, approximately 2.7 V/SHE, indicating their appreciable electrocatalytic activity toward the production of •OH.
Ceramic porous sub-stoichiometric Ti oxides (TinO2n-1, 4≤n ≤ 10), known as Magnéli phases, were first synthesized and characterized in the 1950s (Zhou et al., 2018). Among these oxides, Ti4O7 exhibits excellent performance owing to its unique structure, e.g., excellent corrosion resistance and outstanding electrical conductivity with a value of 1000 S cm−1, which is higher than the 727 S cm−1 of graphitized carbon (Walsh and Wills, 2010). In light of this, the Ti4O7 material has been widely used as a cathodic protection during the electrodeposition process, in batteries as either an electrode material or an additive to the active materials (Zhang et al., 2017). In addition, due to its stability under anodic polarization and high oxygen evolution overpotential, Ti4O7 has been recently utilized as the inert anode material for weekly sorbed •OH production in the field of electrochemical wastewater treatment, which shows comparable electrocatalytic activity to the boron-doped diamond (BDD) anode for pollutant degradation (Bejan et al., 2009).
Recently, depositing Ti4O7 films at the Ti surface has been manufactured successfully by the plasma coating approach, which is a widely spread technology for many types of applications (corrosion protection, abrasion resistance, thermal barriers, etc.) (Ganiyu et al., 2016; Oturan et al., 2017). This preparation process is mainly proceeded by two steps: 1) reduction of TiO2 with coke to produce TixO2x-1 powder and 2) plasma elaboration of TixO2x-1 on the Ti-alloy substrate at 10,000–15,000°C accompanied by conversion of all sub-oxides of Ti to Ti4O7 [46]. However, the application of this Ti4O7 electrode is greatly limited by mass diffusion since there is a thick stagnant boundary layer (∼100 μm) at the plate electrode surface (Liu and Vecitis, 2012; Zaky and Chaplin, 2013). The flow-through mode, which is defined as operating with convective flow perpendicular to the porous electrode surface, allowed for enhanced mass transport rates relative to the traditional parallel flow mode by restricting the diffusional distance of reactants to a length-scale on the order of the pore radius of the electrode (Vecitis et al., 2011; Zaky and Chaplin, 2013; Guo et al., 2016a; Guo et al., 2016b). Thus, significant attention has been recently paid to the integration of membrane filtration and electrochemical process, known as the Ti4O7 reactive electrochemical membrane (REM), for aqueous contaminant degradation because this operation mode promotes the reaction between the contaminant and •OH produced at the anode surface. As a result, REMs based on electrochemical advanced oxidation processes (EAOPs) are a cutting edge class of electrodes that hold great promise in revolutionizing water/wastewater treatment (Zaky and Chaplin, 2013).
As for the preparation of the Ti4O7 REM, TiO2 is typically used as the main feedstock due to its abundance and relatively low cost. The mechanical pressing of Ti4O7 powders, followed by thermal sintering, has been widely used to fabricate the Ti4O7 REMs. There are many conventional approaches available to synthesize the Ti4O7 materials under controlled reducing conditions at relatively high temperature using different reducers such as metals (Kitada et al., 2012), carbon (Ganiyu et al., 2016), carbonaceous organic materials (Guo et al., 2019), and reducing atmosphere (H2 and NH3) (Li et al., 2010; Zhang et al., 2013; Lin et al., 2018). However, most of the production methods are energy and time-consuming. For example, the Ti4O7 REM was synthesized by reduction of commercial TiO2 ultrafiltration membranes at 1333 K for 50 h in the H2 atmosphere (Guo et al., 2016b). As another example, an ultrafiltration membrane layer composed of Ti4O7 and Ti6O11 was obtained by dip-coating of a TiO2 layer on the inner surface of a tubular Al2O3 membrane, followed by a reduction step under 30% H2 in the Ar atmosphere at 1308K for 7 h (Geng and Chen, 2016). High processing temperatures over 1000°C and such long time not only inevitably leads to morphology deformation but also results in particle aggregation and dense low surface area materials, which limit its practical applications as electrode materials, where high surface area, a large number of active sites, and a porous structure are all important for the performance (Lin et al., 2018). In addition to the cases under the reducing atmosphere (H2 and NH3), the as-prepared Ti4O7 REMs did not have high purity since the residual reducing reagents and their derivatives eventually reduce the purity of the obtained Magnéli Ti4O7 REM. However, the gaseous reduction process usually brings about high costs and potential danger. The high preparation costs and rigorously controlled fabrication conditions (H2 atmosphere) might limit their commercial development to some extent. Overall, the control of the stoichiometry of Magnéli phases according to the choice of precursors and thermal treatment is an interesting challenge for material science.
In the present study, thermal reduction of TiO2 by metal Ti under the vacuum condition was developed to prepare the Ti4O7 REM with high purity. The influences of the preparation temperature and thermal sintering time were optimized for Ti4O7 REM preparation. The Ti4O7 REM was characterized using X-ray diffraction (XRD), scanning electron microscopy (SEM), and mercury intrusion porosimetry. The water filtration performance of these REMs was evaluated based on the pressure-normalized permeate flux. In addition, the electrochemical properties of the REMs were studied by sweep voltammetry (CV) and electrochemical impedance spectroscopy (EIS).
TiO2 (99.99%, 25 nm particles) and Ti (99.9%, 10 nm particles) powder were purchased from Beijing Xingyuan Technology Co., Ltd. Carbon black (XC-72R) was bought from Cabot Corporation. Ethanol (EtOH) (99.99%, anhydrous), sodium sulfate (99.9%), potassium ferrocyanide (99.5%), and potassium ferricyanide (99.5%) were obtained from Sigma-Aldrich. All solutions were prepared using deionized water (18.2 MΩ cm−1 at 25°C).
The Ti4O7 ceramic microfiltration membrane was prepared by the following route: TiO2 powder and carbon black were first mixed together and then put into a ZrO2 ball-milling bowl (500 ml in volume, Fritsch, Germany), where the load of carbon black was set to 7.5% of the mass of the TiO2 powder. A planetary ball-mill (Fritsch, Pulverisette 6, Germany) was utilized to mix the membrane contents, in which the grinding balls were a mixture of Nikkato ZrO2 balls in the diameters of 1, 2, 5, 10, and 20 mm. The volume of the balls and the material account for 1/3 of the volume of the ball mill tank, respectively. Anhydrous ethanol is used as a ball milling agent. After allowing it to dry at 60°C overnight, 10 g powders were mixed with 2–3wt% of ethanol and transferred to a disc mould and pressed under the pressure of 30 MPa by a hydraulic press (Specac, UK) to form the precursor of the REM. The membrane was first sintered in air for 4 h at 973 K for the removal of carbon black then was reduced in the presence of the Ti powder (about 4 g) in a vacuum (<8 × 10–3 MPa) tube furnace for the preparation of the Ti4O7 REM. The precursor of the Ti4O7 monolith and Ti powder were separated from each other, and the distance is about 5 cm. The heating/cooling rates were both 4 K min−1.
XRD analysis was performed to obtain the phase information of the Ti4O7 REM. The Scherrer equation was used to calculate the crystallite size. The Ti4O7 REM surface morphology was characterized by SEM. Mercury intrusion porosimetry was used to investigate the porous structures of the electrodes. The EIS and CV analyses were conducted with an electrochemical workstation (PGSTAT302N, Metrohm) and used a three-electrode setup with the Ti4O7 electrode as the working electrode, a platinum plate electrode (3 cm × 3 cm) as the counter electrode, and a saturated calomel electrode (SCE) as the reference electrode. EIS analysis was performed at the open circuit potential (OCP, 190 mV/SCE) over a frequency range of 10−2–104 Hz in 100 mM Na2SO4 supporting electrolyte solution with the presence of 5 mM K4Fe(CN)6 and 5 mM K3Fe(CN)6 redox couple. CV measurements were recorded at a voltage step of 0.05 V in 100 mM NaClO4 electrolyte. The electrochemically active surface area was calculated based on CV analysis at a scan rate from 5 to 30 mV s−1 in a potential range of −0.2–0.5 V.
The effect of thermal reduction temperature on the purity of the Ti4O7 REM was conducted in the range of 1133–1433 K. Figure 1 shows the XRD patterns of the REM samples prepared at various temperatures. It was observed that the color of the REM sample turned from white to light blue after thermal reduction at the reduction temperature of 1133 K. But the obtained REM sample was mainly rutile. This indicates that this reaction temperature was sufficient for the reduction of Ti4+ in anatase-TiO2 to Ti3+, while it was not high enough to transform anatase-TiO2 to the Magnéli phase. The phase transformation was observed at a sintering temperature of 1233 K, where the predominant phase was Ti6O11 and Ti5O9 was the marginal phase. When the temperature was elevated to 1333 K, the XRD patterns show the characteristic peaks for Ti4O7, and almost no peaks for other Magnéli phases suggests that a high purity Magnéli phase Ti4O7 REM was successfully fabricated. At this temperature, the Ti4O7 content of the samples was 98.5%, while the Ti3O5 content was only 1.5%. In contrast, when the reduction temperature was further increased to 1433 K, a single phase of Ti3O5 is formed, indicating that this reaction temperature was too high to synthesize pure Ti4O7.
To further find the optimal conditions for the synthesis of Ti4O7, the influence of thermal reduction time on the purity of the Ti4O7 REM was also studied. The XRD patterns of the as-prepared REM samples prepared at 1333K for 2, 4, and 6 h are shown in Figure 2. It is found that the Magnéli phase Ti4O7 was the major component at the thermal reduction time of 2–6 h. For 2 h, the as-prepared REM sample contains 24% Ti5O9, 10% Ti6O11, and 66% Ti4O7. When the thermal reduction time reached 4 h, XRD patterns show that Ti5O9 and Ti6O11 phases disappeared and Ti4O7 to be the main crystalline phase in the material with only <3% Ti3O5 left. Extending the reaction time to 6 h, the percentage of Ti3O5 phases increased slightly to 6%, and the percentage of Ti4O7 exhibited an insignificant change. These results mean that the thermal reduction time of 2 h is insufficient for the complete transformation of TiO2 to Ti4O7. However, as for 6 h, the increase of the miscellaneous peak, especially Ti3O5, indicates that the sample proceeded overreduction due to the longer thermal reduction time. These results illustrate the optimum reduction time for preparing the pure Ti4O7 REM was 4 h.
FIGURE 2. (A) XRD patterns of the as-prepared samples obtained at 1333 K for 2, 4, and 6 h; (B) Phase composition percentage.
The XRD peaks for the reduced phases are relatively sharp (fwhm = 0.117° for 2 h, 0.084° for 4 h and 0.092° for 6 h) for the peaks at 26.4°, respectively. After accounting for instrumental broadening, the estimated crystallite sizes are 67 nm for 2 h, 90 nm for 4 h, and 119 nm for 6 h according to the Sherrer’s equation, while the crystallite size of the original TiO2 is 25 nm, indicating the crystallite growth. For further investigation of the phase composition of the productions, the XRD spectrums of the REM those were not grounded into powder are showed in Figure 3. In addition, the XRD peaks of the REM were perfectly coincident with those grounded into powder, meaning that the component of the REM bulk was homogeneous. It is noteworthy that as for the common carbothermal reduction approach with mixing carbon powder and TiO2, the surface and interior of the obtained bulk sample show different compositions (Tsumura et al., 2004; Toyoda et al., 2009).
The morphology and pore structure of the REM were characterized by SEM Hg porsimetry, respectively. The SEM images in Figures 4A–D show the samples prepared at 1333 K with different carbon black contents of 0wt%, 1.5wt%, 5wt%, and 10wt%. The pore size of four samples was almost similar due to the fact that the grain-growth behavior mainly depends on the sintering time and temperature (Guan et al., 2016). The SEM images of the REM exhibit a three-dimensionally assembled structure with macro porosity, and the crystallites were indeed intimately fused or even consolidated to form large single-crystal particles on the micrometer scale. During the high-temperature reduction process, the agglomerates of solid particles and particle bonding resulted in the formation of the porous structure inside the cavity in the presence of the porosity-producing agent. Figure 4 shows that the pore size increased with the increasing carbon black content. The size of pores in Figure 4D seems to be larger than that in Figure 4A, which may be explained by the different carbon contents of these two samples. The detailed pore structure of these membranes was characterized by Hg porosimetry, and the results are presented in the Figure 5. It is demonstrated that the REM sample possessed uniform macropores of 0.4–0.5 μm (Figure 6). The almost same macropore diameter and volume indicate that the well-defined macroporous structure of the monolith was retained. These results are consistent with the results of SEM images. Moreover, the REM exhibits a pore size distribution with ∼99% of the measured surface area associated with pores <0.5 μm, and essentially, the entire pore volume attributed to pores with 0.2–0.5 μm diameters. As shown in Figure 5, based on the porosimetry results, the porous surface area for the membrane without carbon black was estimated as 1.477 m2 g−1 with the porosity(θ) and median pore diameter of 0.382 and 0.380 μm, respectively. As the content of carbon black was elevated to 1.5wt%, the porous surface area was enhanced to 1.797 m2 g−1 with the increase in the porosity by 4.7%, while no difference was observed in the pore size as compared with that without the addition of carbon black. The membrane with 5wt% carbon black has a porous surface area of 2.011 m2 g−1, median pore diameter of 0.481 μm, and its porosity is 0.427 which is the same with the former. The porosity for the REM with 15wt% carbon black was determined as 0.594, specific surface area of 2.477 m2 g−1, and median pore diameter of 0.575 μm. As the volume of carbon black increased, the change of pore size is slight, and the porosity has a gap of 21% between the samples without carbon black and with 15% carbon black. Micron-sized pores dominated the REM pore volume, which facilitates water transport through the REM at low applied pressures and is expected beneficial for facilitating interfacial mass transfer during the electrochemical reaction. Porosimetry analysis results show that the average pore diameter was closed to the median pore diameter (based on pore volume data) showing symmetrically distribution pore size. The addition of high carbon black content was not recommended since it would cause the crack of the REM monolith during the flow-through operation mode.
FIGURE 4. SEM image of the samples obtained at 1333 K with different carbon black contents of 0wt% (A) 1.5wt%, (B) 5wt%, and (C) 10wt% (D).
FIGURE 5. Cumulative pore area and log differential intrusion pore volume of Hg intrusion porosimetry analysis for (A,E) 0wt%, (B,F) 1.5wt%, (C,G) 5wt%, and (D,H) 15wt%.
A flow-through reactor was used to assess the permeation ability of REMs with ultra-pure water experiments which were carried out with the Ti4O7 REM. A digital gear pump was prepared to control the permeate flux and a pressure gage was used to record the hydraulic pressure. The evolution of the permeate flux with the carbon black content is plotted in Figure 7. It is found that the porosity and pore size both exerted the influence on the permeate flux. The REM without carbon black and with 1.5%wt carbon black have the same pore size of 380 nm but different porosity, e.g., 38 and 42%, respectively. The permeate flux of the latter increased 28% than the former. REMs with 1.5wt% and 5wt% carbon black have the same porosity of 0.42 and different pore size. With the bigger pore size and porosity, the increased extent of the permeate flux was much more evident. The permeate flux for the sample with the pore size of 480 nm increased by 57% than the sample with 380 nm pore size. The results of the REM membrane with 60% porosity and 580 nm pore size showed that the method improved the flux obviously with a 452% increase in the flux from 250 to 1379 L m−2 h−1 bar−1 than the original REM membrane. This indicates that a high content of carbon black was a crucial factor for the permeation ability of the REM membrane.
The resistance-in-series model was applied to evaluate the characteristics of the membrane flux; according to the Darcy law, the permeation flux (J) takes the following form:
where J is the permeation flux (L/m2 h),
The measurements of the electrochemically active surface area of each electrode were conducted within the potential region between hydrogen and oxygen evolution reaction, i.e., −0.2–0.5 V/SCE, at the sweep rates of 5–30 mV/s. As shown in Figure 8, the capacitive current decreases linearly with lowering sweep rates so that the apparent capacitance can be calculated from the slope of the charging current vs sweep rate. The double layer capacitances
where
FIGURE 8. Determination of double-layer capacitance at different scan rates (5–30 mV s−1) for REMs using CV in the 100 mM Na2SO4 electrolyte solution. CV scans: (A) 0wt%, (B) 1.5wt%, (C) 5wt%, and (D) 15wt%. Corresponding plots of charging currents versus scan rates: (E) 0wt%, (F) 1.5wt%, (G) 5wt%, and (H) 15wt%.
Comparative cyclic voltammograms of the four REM membranes with a nominal geometric surface area of 3.38 cm2 in the potential range of −0.2–0.5 V/SCE are shown in Figure 8. It was calculated that the REM samples without doping carbon black and with 1.5% carbon black have the almost same average roughness (2557–2563). As for 5wt% carbon black, the calculated surface roughness was 3250 and the total electroactive surface area was 1.1 m2, which accounted for approximately 54.6% of the porous surface area measured by Hg porosimetry and increased by 1.3-fold in comparison with that without carbon black. However, the REM membrane obtained with doping 15wt% carbon black has the lowest surface roughness at 1953. In summary, the electrochemically active area (i.e., the roughness factor) of the porous Ti4O7 electrode is 3 orders of magnitude higher than the apparent surface area of the REM membrane, which was favorable for the electrochemical reaction.
A stepwise increase in potential was implemented by recording the current response to obtain the water oxidation potential in the Na2SO4 electrolyte (Figure 9). For Ti4O7, there was a negligible response of the current when the potential was below 2.7 V/SHE. Further increasing potential resulted in an apparent enhancement of the current, indicating the potential for water oxidation was within the range of 2.5–2.7 V/SHE. This result was higher than that of the oxygen evolution potential of 2.5 V/SHE reported by Smith et al. and reached the highest reported value of 2.7 V/SHE (Miller-Folk et al., 1989; Graves et al., 1991; Kolbrecka and Przyluski, 1994; Grimm et al., 1998). Thus, we can infer that the as-prepared Ti4O7 REM exhibits an appreciable electrocatalytic activity toward the production of •OH.
Figure 9B shows the EIS curves of REMs at room temperature. Each of the curves consists of a straight line (at low frequency) and a depressed semicircle (at high frequency), which are related to the ion diffusion in the bulk of the electrode and the charge transfer process at the electrolyte–electrode interface, respectively. The Rs displays the internal resistance of the electrode and electrolyte, and the charge-transfer impedance (Rct) is expressed vividly by the depressed semicircle in the intermediate frequency region. As shown in Figure 9B and Table 1, Rs values of Ti4O7 were estimated to be 17.1 ± 0.17, 17.53 ± 0.18, 18.8 ± 0.19, and 19.6 ± 0.20 Ω, respectively, indicating a minimal difference between the conductivity of these REMs. But it can be seen that as the content of carbon black increased, the value of Rs increased, which may be associated with the porosity of the REM membrane samples. The existence of a large number of voids reduced the effective cross-section of current conduction and therefore decreased the conductivity. Notably, the charge transfer resistances (Rct) of these REMs were 3.57 ± 0.36, 3.68 ± 0.37, 4.14 ± 0.41, and 5.19 ± 0.52 Ω, respectively, which were three orders of magnitude smaller than that for the graphite plate electrode (You et al., 2016; Xie et al., 2020), suggesting a much higher charge transfer capacity of Ti4O7.
In this study, the Ti4O7 REM fabrication process combined the following two steps: 1) the oxygen atoms in the TiO2 monolith reunited to oxygen and then effused into the vacuum environment at the higher reaction temperature and 2) the emanated oxygen is captured by the Ti powder. Thermodynamically, the reaction driving force enables titanium oxidation and TiO2 reduction. For step one, the general reaction can be given as
where Tin–1O2n–3 and TinO2n–1 are the closest compounds in the Ti–O binary phase diagram. In these reactions, only oxygen is the gas phase, and others are pure solid. Then, the Gibbs free energy could be written as
where
When
Based on the data of the Ti–O system, the diagram of this relationship is shown in Figure 10, called the Ti–O system phase stable diagram.
From Figure 10, Ti4O7 could be synthesized from TiO2 if the oxygen partial pressure and temperature were accurately controlled. If the system oxygen partial pressure is higher than the equilibrium value, the metal will be oxidized, and if it is lower than the equilibrium value, then the oxide will be reduced. The lower the temperature was, the wider the range of the oxygen partial pressure for Ti4O7 existed. When the temperature was adjacent to 1333 K and
Table 2 is the equilibrium oxygen partial pressure of reactions in the Ti-O system at the temperature of 1233, 1333, and 1433 K. As the temperature increases by every 100 K, the oxygen partial pressure can increase by several orders of magnitude. It means that raising the temperature could make the reaction occur more easily and more distinguished; thus, the possibility to fabricate a single-phase material is greatly raised. However, it should be noted that the treatment time must be reduced at a high thermal reduction temperature since it probably induced the overreduction of TiO2 to some TinO2n-1, such as Ti3O5 (Figure 2).
TABLE 2. Equilibrium oxygen partial pressure of reactions in the Ti–O system at a specified temperature.
Excess amount Ti was use to decrease the oxygen pressure and ensure more complete reduction of TiO2 during the process. It has been shown that the growth of titanium oxide mainly in the form of rutile at and above 10−7 MPa and at the temperature below 1573 K. However, at lower pressures and at higher temperatures and after oxygen saturation of the a-phase, all the oxides of titanium (e.g., Ti2O, TiO, Ti2O3, Ti3O5, and TiO2) are formed as reaction products depending on the oxygen pressure and elapsed time of reaction. As a matter of fact, the last oxidized product is not TiO2 but the mixture of various titanium oxide (Figure 11). As the temperature was 1273 K, the oxygen partial pressure
In this study, the high purity Ti4O7 REM was successfully synthesized by mechanical pressing of TiO2 powders followed by thermal reduction to Ti4O7 using the Ti powder as the reducing reagent. Carbon black was introduced to the monolithic TiO2 precursor to control the pore size and morphology of the Ti4O7 REM. The pore properties modification increased the electroactive surface area by approximately 1.3-fold, which increased the reactivity of the Ti4O7 REM toward outer sphere electron transfer reactions. The electrodes had high porosities (38–59%), which showed high permeate fluxes of up to 1379 ± 8 LMH bar−1. These results indicated that the Ti4O7 monolithic electrodes could find various electrochemical applications in water treatment and energy storage and conversion.
The original contributions presented in the study are included in the article/Supplementary Material; further inquiries can be directed to the corresponding authors.
GQ was responsible for conceptualization, investigation, formal analysis, and writing of the original draft. XW contributed to project administration, resources, validation, and reviewing and editing. JZ and CS carried out investigation and formal analysis. XX helped with software and methodology. YZ, FR, and NZ performed the formal analysis and investigation.
All authors were employed by the company Testing and Evaluation Research Co., Ltd. of Sinopec Shengli OilField.
All claims expressed in this article are solely those of the authors and do not necessarily represent those of their affiliated organizations, or those of the publisher, the editors, and the reviewers. Any product that may be evaluated in this article, or claim that may be made by its manufacturer, is not guaranteed or endorsed by the publisher.
Bejan, D., Malcolm, J. D., Morrison, L., and Bunce, N. J. (2009). Mechanistic Investigation of the Conductive Ceramic Ebonex as an Anode Material. Electrochimica Acta 54 (23), 5548–5556. doi:10.1016/j.electacta.2009.04.057
Ganiyu, S. O., Oturan, N., Raffy, S., Cretin, M., Esmilaire, R., van Hullebusch, E., et al. (2016). Sub-stoichiometric Titanium Oxide (Ti4O7) as a Suitable Ceramic Anode for Electrooxidation of Organic Pollutants: A Case Study of Kinetics, Mineralization and Toxicity Assessment of Amoxicillin. Water Res. 106, 171–182. doi:10.1016/j.watres.2016.09.056
Geng, P., and Chen, G. (2016). Magnéli Ti 4 O 7 Modified Ceramic Membrane for Electrically-Assisted Filtration with Antifouling Property. J. Membr. Sci. 498, 302–314. doi:10.1016/j.memsci.2015.07.055
Graves, J. E., Pletcher, D., Clarke, R. L., and Walsh, F. C. (1991). The Electrochemistry of Magnéli Phase Titanium Oxide Ceramic Electrodes Part I. The Deposition and Properties of Metal Coatings. J. Appl. Electrochem. 21 (10), 848–857. doi:10.1007/bf01042450
Grimm, J., Bessarabov, D., and Sanderson, R. (1998). Review of Electro-Assisted Methods for Water Purification. Desalination 115 (3), 285–294. doi:10.1016/s0011-9164(98)00047-2
Guan, K., Qin, W., Liu, Y., Yin, X., Peng, C., Lv, M., et al. (2016). Evolution of Porosity, Pore Size and Permeate Flux of Ceramic Membranes during Sintering Process. J. Membr. Sci. 520, 166–175. doi:10.1016/j.memsci.2016.07.023
Guo, D., Shibuya, R., Akiba, C., Saji, S., Kondo, T., and Nakamura, J. (2016). Active Sites of Nitrogen-Doped Carbon Materials for Oxygen Reduction Reaction Clarified Using Model Catalysts. Science 351 (6271), 361–365. doi:10.1126/science.aad0832
Guo, L., Jing, Y., and Chaplin, B. P. (2016). Development and Characterization of Ultrafiltration TiO2 Magnéli Phase Reactive Electrochemical Membranes. Environ. Sci. Technol. 50 (3), 1428–1436. doi:10.1021/acs.est.5b04366
Guo, Y., Li, J., Pitcheri, R., Zhu, J., Wen, P., and Qiu, Y. (2019). Electrospun Ti4O7/C Conductive Nanofibers as Interlayer for Lithium-Sulfur Batteries with Ultra Long Cycle Life and High-Rate Capability. Chem. Eng. J. 355, 390–398. doi:10.1016/j.cej.2018.08.143
Kitada, A., Hasegawa, G., Kobayashi, Y., Kanamori, K., Nakanishi, K., and Kageyama, H. (2012). Selective Preparation of Macroporous Monoliths of Conductive Titanium Oxides TinO2n-1 (N = 2, 3, 4, 6). J. Am. Chem. Soc. 134 (26), 10894–10898. doi:10.1021/ja302083n
Kolbrecka, K., and Przyluski, J. (1994). Sub-stoichiometric Titanium Oxides as Ceramic Electrodes for Oxygen Evolution—Structural Aspects of the Voltammetric Behaviour of TinO2n−1. Electrochim. Acta 39 (11), 1591–1595. doi:10.1016/0013-4686(94)85140-9
Li, X., Zhu, A. L., Qu, W., Wang, H., Hui, R., Zhang, L., et al. (2010). Magneli Phase Ti4O7 Electrode for Oxygen Reduction Reaction and its Implication for Zinc-Air Rechargeable Batteries. Electrochimica Acta 55 (20), 5891–5898. doi:10.1016/j.electacta.2010.05.041
Lin, H., Niu, J., Liang, S., Wang, C., Wang, Y., Jin, F., et al. (2018). Development of Macroporous Magnéli Phase Ti4O7 Ceramic Materials: As an Efficient Anode for Mineralization of Poly- and Perfluoroalkyl Substances. Chem. Eng. J. 354, 1058–1067. doi:10.1016/j.cej.2018.07.210
Liu, H., and Vecitis, C. D. (2012). Reactive Transport Mechanism for Organic Oxidation during Electrochemical Filtration: Mass-Transfer, Physical Adsorption, and Electron-Transfer. J. Phys. Chem. C 116 (1), 374–383. doi:10.1021/jp209390b
Miller-Folk, R. R., Noftle, R. E., and Pletcher, D. (1989). Electron Transfer Reactions at Ebonex Ceramic Electrodes. J. Electroanal. Chem. Interf. Electrochem. 274 (1), 257–261. doi:10.1016/0022-0728(89)87047-0
Oturan, N., Ganiyu, S. O., Raffy, S., and Oturan, M. A. (2017). Sub-stoichiometric Titanium Oxide as a New Anode Material for Electro-Fenton Process: Application to Electrocatalytic Destruction of Antibiotic Amoxicillin. Appl. Catal. B: Environ. 217, 214–223. doi:10.1016/j.apcatb.2017.05.062
Toyoda, M., Yano, T., Tryba, B., Mozia, S., Tsumura, T., and Inagaki, M. (2009). Preparation of Carbon-Coated Magneli Phases TinO2n−1 and Their Photocatalytic Activity under Visible Light. Appl. Catal. B: Environ. 88 (1-2), 160–164. doi:10.1016/j.apcatb.2008.09.009
Tsumura, T., Hattori, Y., Kaneko, K., Hirose, Y., Inagaki, M., and Toyoda, M. (2004). Formation of the Ti4O7 Phase through Interaction between Coated Carbon and TiO2. Desalination 169 (3), 269–275. doi:10.1016/s0011-9164(04)00533-8
Vecitis, C. D., Gao, G., and Liu, H. (2011). Electrochemical Carbon Nanotube Filter for Adsorption, Desorption, and Oxidation of Aqueous Dyes and Anions. J. Phys. Chem. C 115 (9), 3621–3629. doi:10.1021/jp111844j
Walsh, F. C., and Wills, R. G. A. (2010). The Continuing Development of Magnéli Phase Titanium Sub-oxides and Ebonex Electrodes. Electrochimica Acta 55 (22), 6342–6351. doi:10.1016/j.electacta.2010.05.011
Xie, J., Ma, J., Zhang, C., Kong, X., Wang, Z., and Waite, T. D. (2020). Effect of the Presence of Carbon in Ti4O7 Electrodes on Anodic Oxidation of Contaminants. Environ. Sci. Technol. 54 (8), 5227–5236. doi:10.1021/acs.est.9b07398
You, S., Liu, B., Gao, Y., Wang, Y., Tang, C. Y., Huang, Y., et al. (2016). Monolithic Porous Magnéli-phase Ti4O7 for Electro-Oxidation Treatment of Industrial Wastewater. Electrochimica Acta 214, 326–335. doi:10.1016/j.electacta.2016.08.037
Zaky, A. M., and Chaplin, B. P. (2013). Porous Substoichiometric TiO2 Anodes as Reactive Electrochemical Membranes for Water Treatment. Environ. Sci. Technol. 47 (12), 6554–6563. doi:10.1021/es401287e
Zhang, L., Kim, J., Zhang, J., Nan, F., Gauquelin, N., Botton, G. A., et al. (2013). Ti4O7 Supported Ru@Pt Core-Shell Catalyst for CO-tolerance in PEM Fuel Cell Hydrogen Oxidation Reaction. Appl. Energ. 103, 507–513. doi:10.1016/j.apenergy.2012.10.017
Zhang, Y., Yao, S., Zhuang, R., Luan, K., Qian, X., Xiang, J., et al. (2017). Shape-controlled Synthesis of Ti4O7 Nanostructures under Solvothermal-Assisted Heat Treatment and its Application in Lithium-Sulfur Batteries. J. Alloys Compd. 729, 1136–1144. doi:10.1016/j.jallcom.2017.09.252
Keywords: Ti4O7, reactive electrochemical membrane, Ti, TiO2, thermal reduction
Citation: Qi G, Wang X, Zhao J, Song C, Zhang Y, Ren F and Zhang N (2022) Fabrication and Characterization of the Porous Ti4O7 Reactive Electrochemical Membrane. Front. Chem. 9:833024. doi: 10.3389/fchem.2021.833024
Received: 10 December 2021; Accepted: 20 December 2021;
Published: 14 February 2022.
Edited by:
Suqing Wu, Wenzhou University, ChinaReviewed by:
Xing Xu, Shandong University, ChinaCopyright © 2022 Qi, Wang, Zhao, Song, Zhang, Ren and Zhang. This is an open-access article distributed under the terms of the Creative Commons Attribution License (CC BY). The use, distribution or reproduction in other forums is permitted, provided the original author(s) and the copyright owner(s) are credited and that the original publication in this journal is cited, in accordance with accepted academic practice. No use, distribution or reproduction is permitted which does not comply with these terms.
*Correspondence: Xiaohui Wang, d2FuZ3hpYW9odWkxNTMuc2x5dEBzaW5vcGVjLmNvbQ==
†These authors have contributed equally to this work
Disclaimer: All claims expressed in this article are solely those of the authors and do not necessarily represent those of their affiliated organizations, or those of the publisher, the editors and the reviewers. Any product that may be evaluated in this article or claim that may be made by its manufacturer is not guaranteed or endorsed by the publisher.
Research integrity at Frontiers
Learn more about the work of our research integrity team to safeguard the quality of each article we publish.