- 1School of Mechanical and Electrical Engineering, Quzhou College of Technology, Quzhou, China
- 2School of Materials Science and Engineering, Zhejiang University, Hangzhou, China
Hydrogen is a potential green alternative to conventional energy carriers such as oil and coal. Compared with the storage of hydrogen in gaseous or liquid phases, the chemical storage of hydrogen in solid complex hydrides is safer and more effective. In this study, the complex hydride composite 2LiBH4–Li3AlH6 with different amounts of TiF3 was prepared by simple ball-milling and its hydrogen storage properties were investigated. Temperature programmed desorption and differential scanning calorimetry were used to characterize the de/rehydrogenation performance, and X-ray diffraction and scanning electron microscopy (SEM) were used to explore the phase structure and surface topography of the materials. The dehydrogenation temperature decreased by 48°C in 2LiBH4–Li3AlH6 with 15 wt% TiF3 composites compared to the composite without additives while the reaction kinetics was accelerated by 20%. In addition, the influence of hydrogen back pressure on the 2LiBH4–Li3AlH6 with 5 wt% TiF3 composite was also investigated. The results show that hydrogen back pressure between 2.5 and 3.5 bar can improve the reversible performance of the composite to some extent. With a back pressure of 3.5 bar, the second dehydrogenation capacity increased to 4.6 wt% from the 3.3 wt% in the 2LiBH4–Li3AlH6 composite without hydrogen back pressure. However, the dehydrogenation kinetics was hindered. About 150 h, which is 100 times the time required without back pressure, was needed to release 8.7 wt% of hydrogen at 3.5 bar hydrogen back pressure. The SEM results show that aluminum was aggregated after the second cycle of dehydrogenation at the hydrogen back pressure of 3 bar, resulting in the partial reversibility of the 5 wt% TiF3-added 2LiBH4–Li3AlH6 composite.
Introduction
As a new energy source, hydrogen has great potential to solve the serious energy depletion and atmospheric pollution caused by excessive utilization of conventional energy sources. Hydrogen is the most abundant element in the Universe. The calorific value of 1 kg of hydrogen is 140 megajoules of energy, which is three times of that of the amount of energy released by the same weight of oil. Moreover, water vapor is the only combustion product of hydrogen, making it a pollution-free energy source. However, the limitations of hydrogen storage technology have hindered its practical application.
As a promising candidate for solid-state hydrogen storage, LiBH4 has a high theoretical gravimetric hydrogen density of 18.5 wt%, which is the highest among all the solid hydride materials. (Züttel et al., 2003) first studied the desorption properties of LiBH4. The material released 0.3 wt% hydrogen at 200°C and 1 wt% hydrogen at 320°C. After heating to 500°C, rapid hydrogen desorption was observed, and 9 wt% of hydrogen was released. This capacity meets the requirements of the US Department of Energy (DOE) (Jain et al., 2010), but the desorption temperature is too high for practical applications, and the dehydrogenation kinetics also need to be improved.
Many researchers have focused on the modification of LiBH4 using various methods, such as composite modification (Xia et al., 2011; Langmi et al., 2012; Bilen et al., 2015; Liu et al., 2015; Sofianos et al., 2017), catalyst modification (Puszkiel et al., 2014; Ma et al., 2016; Zhang et al., 2018), and nanoengineering (Zhao et al., 2014; Surrey et al., 2016; Sofianos et al., 2018). Compositing LiBH4 with other active hydrides is an effective way to enhance its hydrogen storage performance. For example, Liu et al., 2016 milled LiBH4 with AlH3 to form a 2LiBH4 + AlH3 composite. The dehydrogenation temperature of the 2LiBH4 + AlH3 composite was reduced by 30°C compared with pure LiBH4, and 11.2 wt% hydrogen was obtained. (Ding et al. 2019) found that in a nano-sized composite of LiBH4 and MgH2 prepared by ball-milling with aerosol spraying (BMAS), the LiBH4 released hydrogen at 265°C, and approximately 5.0 wt% H2 was reversible in the first five dehydrogenation and rehydrogenation cycles. Using the shrinking-core model, it was found that a larger interfacial area between LiBH4 and MgH2 improves the dynamics of the nano 2LiBH4 + MgH2 mixture (Ding et al., 2019).
Other researchers have prepared binary (Mao et al., 2009b; Yu et al., 2010; Hansen et al., 2013; Li et al., 2013; Mustafa et al., 2018; Yahya et al., 2019) or ternary (Yang et al., 2012; Liu et al., 2021) composite systems of LiBH4 and other complex hydrides (Halim Yap et al., 2018; Halim Yap and Ismail, 2018), such as LiBH4–LiAlH4 (Thaweelap and Utke, 2016; Meethom et al., 2020), LiBH4–Li3AlH6 (Choi et al., 2011b), LiBH4–NaBH4 (Dematteis et al., 2016), LiBH4–NaAlH4, LiBH4–Mg(BH4)2 (Zheng et al., 2020), LiBH4–Ca(BH4)2 (Ampoumogli et al., 2015), LiBH4–Mg2NiH4 (Bergemann et al., 2019), LiBH4–NaBH4–MgH2 (Xiang et al., 2018), and LiBH4–Li3AlH6–MgH2 (Lin et al., 2020). Bargeman et al. (Bergemann, et al. 2019) investigated the reaction mechanism of a LiBH4–Mg2NiH4 composite. They found that the dehydrogenation path was significantly influenced by the back pressure and temperature. When the back pressure was increased to 50 bar, Mg2NiH4 reacted with solid LiBH4 below 270°C, and the reaction enthalpy was reduced by 13 kJ/mol H2. In Thaweelap’s work (Thaweelap and Utke, 2016), LiBH4 and LiAlH4 were synthesized together with Ti-based catalysts or carbon nanotubes to achieve a synergistic effect between the catalysts and composites. Both the kinetics and thermodynamics of the samples were improved. In addition, the reversibility of the LiBH4–LiAlH4–MWCNT composite was increased to 3.7 wt% in the second cycle compared to 2.8 wt% in the LiBH4–LiAlH4 composite. Wu (Wu et al. 2012) revealed the reaction mechanism of a LiBH4–Li3AlH6 composite, which received 8.5 wt% hydrogen in the dehydrogenation process. Zhou (Zhou et al. 2017) prepared a 2LiBH4–LiAlH4 composite nanoconfined in an RFC aerogel, and found that both the thermodynamic and kinetic properties were enhanced.
Some catalysts such as CaH2 (Jiang et al., 2012), NbF5 (Mao et al., 2013), TiF3 (Mao et al., 2010) and NbCl5 (Tu et al., 2015) destabilize LiBH4 to decompose H2 under moderate conditions. Ming mixed LiBH4 with several additives using the ball-milling method (Au and Jurgensen, 2006). The modified mixtures desorbed hydrogen at a lower temperature and higher rate. Among the various additives, Ti-based catalysts had an obvious effect. Choi (Choi et al. 2011a) demonstrated that TiCl3 could promote desorption in a Li3AlH6/2LiBH4 composite at a lower temperature. Because of the catalyst effect of TiCl3, Li3AlH6 started to release hydrogen at 81°C, and LiBH4 released hydrogen at 226°C, which are 130 and 200°C lower than the temperatures at which hydrogen was released by pure Li3AlH6 and LiBH4, respectively. A novel two-dimensional (2D) layered Ti3C2 material was added to the LiBH4–THF solution to synthesize a series of LiBH4–χTi3C2 composites with different mass ratios. The LiBH4–2Ti3C2 composite released hydrogen at 172.6°C, and its activation energy was reduced by 50% compared to that of pure LiBH4 (Zang et al., 2018). TiF3 is a well known catalyst for solid-state hydrogen storage materials. It effectively improved the hydrogen storage performance of LiAlH4–MgH2 (Mao et al., 2011), MgH2–NaAlH4 (Ismail et al., 2012) and 2NaAlH4+Ca(BH4)2 (Mustafa and ismail, 2019) binary composite.
In this study, a ternary composite of 2LiBH4–Li3AlH6 with different amounts of TiF3 (the mass percent of TiF3 were 5, 10, and, 15%) was prepared by a high-energy ball milling method. The synergistic effects between the composite and the catalyst were investigated together with the influence of the hydrogen back pressure on the reversibility.
Materials and Methods
LiBH4 powder (95% purity) and TiF3 powder (99% purity) were purchased from Acros Organics and Sigma Aldrich, respectively. Li3AlH6 powder was obtained by mixing LiAlH4 (95% purity, Sigma Aldrich) and LiH (98% purity, Alfa Aesar) using a high-energy ball-milling method at a ball-to-powder ratio of 40:1 (Li et al., 2020). All the materials used in this work were stored in a glove box purchased from Mikrouna. The glove box was filled with high-purity argon to purge the atmosphere, and the water vapor content was less than 1 ppm. The 2LiBH4–Li3AlH6 series with and without TiF3 composites was weighed and mixed in this glove box, and then loaded in a sealed stainless ball-milling tank. Planetary ball-milling equipment (QM-3SP4) was used to grind the materials at 300 revolutions per minute for 1 h.
A Sievert-type instrument which recorded the pressure change of the hydrogen released during the heating process was used to evaluate the dehydrogenation/rehydrogenation performance of the materials. Approximately 200 mg of each sample was charged into a thin stainless-steel tube reactor. The reactor was then heated from ambient temperature to the set temperature at a constant heating rate. The time, temperature, and pressure data were recorded every ten seconds. The amount of hydrogen released or absorbed during the heating process was calculated using the ideal gas state equation. Differential scanning calorimetry (DSC, Netzsch STA 449F3/Netzsch Q403C) was used to evaluate the thermal effects of the materials. In the glove box, about 1–1.5 mg of samples were loaded each time and sealed in an aluminum crucible. Both the sample crucible and the reference crucible were placed in the reaction chamber of the DSC equipment, which was filled with flowing high purity argon at a flow rate of 50 ml/min.
X-ray diffraction (XRD, X'Pert-PRO) and scanning electron microscopy (SEM, FEI FSEM SIRION-100) were used to analyze the phase structure and observe the surface topography of the material. The XRD K-Alpha1 and K-Alpha2 wavelengths were 1.540598 Å and 1.544426 Å, respectively. The samples were sealed in a transparent macromolecular container to prevent oxidation. Fourier transform infrared spectroscopy (FT–IR, Bruker, Tensor 27) at the scan rate of 30 cm−1/min and resolution of 0.5 cm−1 was used for chemical bond analysis. The crucibles used in the experiments were aluminum crucibles.
Results and Discussion
DSC Traces of LiBH4, Li3AlH6, and LiBH4–Li3AlH6 Samples
The DSC traces of the Li3AlH6, LiBH4, and 2LiBH4–Li3AlH6 samples at the heating rate of 5°C/min from ambient temperature to 500°C are shown in Figure 1. In the Li3AlH6 sample (Figure 1A), there is an endothermic peak at 214°C due to the decomposition process of Li3AlH6. The last peak in the DSC trace of Li3AlH6 was the decomposition of LiH (Aresfernandez, 2007).The decomposition reaction of Li3AlH6 and the resulting products are described by Eq. 1 (Zang, et al., 2018):
There are three endothermic peaks in the DSC trace of LiBH4 shown in Figure 1B. The first peak at 111°C is the lattice transition peak of LiBH4, and the second peak at 287°C corresponds to the melting of LiBH4 (Züttel, et al., 2003). The third peak is wider than the first two and indicates the decomposition of LiBH4 (Li et al., 2017). The decomposition process is shown in Eq. 2 (Mao et al., 2009a):
Four endothermal peaks corresponding to the characteristic peaks of the components were observed for the 2LiBH4–Li3AlH6 composite. The LiBH4 in the 2LiBH4–Li3AlH6 composite melted at 274°C, which is 13°C lower than the melting point of pure LiBH4. The second and the forth endothermal peaks mean a rapid dehydrogenation temperature of Li3AlH6 and LiBH4, were 199 and 417°C (see Figure 1C), which were lower than pure Li3AlH6 and LiBH4, indicating that the dehydrogenation performance of the 2LiBH4–Li3AlH6 composite obtained a better thermal performance.
Influence of TiF3 on Hydrogen Desorption Performance of 2LiBH4–Li3AlH6 Composite
The hydrogen storage properties of the 2LiBH4–Li3AlH6 composite both in its original state and in the presence of TiF3 were investigated in this study. The samples were weighed and loaded in a glove box filled with pure argon. The mass percentages of TiF3 in the four samples were 0, 5, 10, and 15 wt%. All the samples were prepared by ball-milling for 1 h, and XRD was used to determine the composition of the samples. LiBH4 and Li3AlH6 peaks were observed in the 2LiBH4–Li3AlH6 sample without the TiF3 additive (Figure 2A). The main diffraction peaks of the three 2LiBH4–Li3AlH6 composites with different amount of TiF3 (Figures 2B–D) correspond to those of the 2LiBH4–Li3AlH6 sample without additive. The weak diffraction peaks at 23° or 70° in Figure 2C and Figure 2D could be attributed to TiF3. The absence of a TiF3 peak in Figure 2B may possibly be due to the small amount of highly dispersed TiF3. As the TiF3 content increased, the diffraction peak of Al in the 2LiBH4–Li3AlH6 with TiF3 composites gradually became obvious, and weak LiH peaks appeared at 38° and 44°. These results indicate that TiF3 destabilized Li3AlH6 by promoting its decomposition into LiH and Al during the ball-milling process (Ares, 2008).Approximately 1 mg of the prepared samples was loaded into an aluminum oxide crucible for the DSC test each time. The results are shown in Figure 3. Comparing the 2LiBH4–Li3AlH6 samples with TiF3 (Figures 3B–D) or without TiF3 (Figure 3A), the lattice transition peaks of LiBH4, which were between 112 and 115°C, were almost unchanged. The melting peak of LiBH4 decreased from 274 to 257°C as the amount of TiF3 increased. In addition, compared with the 2LiBH4–Li3AlH6 sample, the Li3AlH6 decomposition peak shifted obviously to lower temperatures and became wider in the 2LiBH4–Li3AlH6 with 5 wt% TiF3. In the samples with 10 and 15 wt% TiF3, the typical endothermic peak of Li3AlH6 was almost undetectable. A possible reason for this is the partial decomposition of Li3AlH6 during the ball-milling process (Liu, 2010). This result is consistent with the XRD patterns (Figure 2), in which LiH and Al were detected in the TiF3-added ball-milling samples, and indicates that TiF3 is an effective catalyst that can destabilize Li3AlH6 at a lower temperature. LiBH4 decomposed at 399, 382, and 369°C in the 2LiBH4–Li3AlH6 composite with 5, 10, and 15 wt% TiF3 additives, respectively. Faster dehydrogenation kinetics were also obtained as the dehydrogenation peak of LiBH4 became broader with the increase in the amount of TiF3 (Zang, et al., 2018). The introduction of the TiF3 catalyst promoted both the thermal decomposition and the kinetic properties of LiBH4 and Li3AlH6.
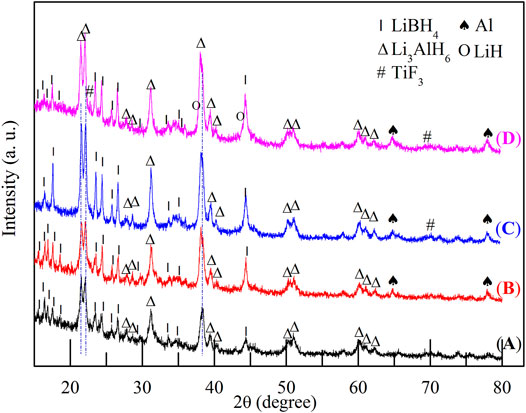
FIGURE 2. XRD patterns of 2LiBH4–Li3AlH6 samples with different amounts of TiF3 after ball-milling: (A) 0 wt%, (B) 5 wt%, (C) 10 wt%, and (D) 15 wt%.
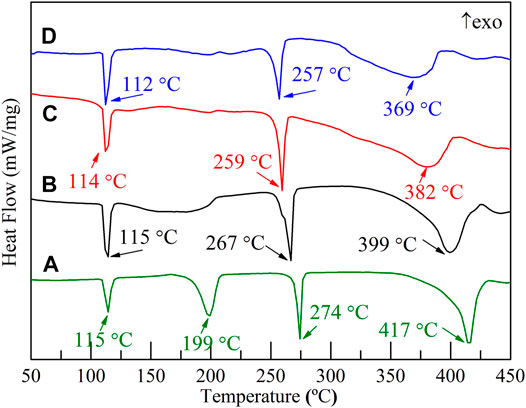
FIGURE 3. DSC traces of 2LiBH4–Li3AlH6 samples with different amounts of added TiF3: (A) 0 wt%, (B) 5 wt%, (C) 10 wt%, and (D) 15 wt%.
A temperature-programmed desorption (TPD) test was performed to study the dehydrogenation properties with and without TiF3 in the 2LiBH4–Li3AlH6 samples. Table 1 shows the theoretical hydrogen storage capacities of the 2LiBH4–Li3AlH6 samples with different amounts of TiF3. As the amount of TiF3 increased, the weight percentage of H in 1 g of ball-milled sample decreased from 9.24 wt% to 7.85 wt%, as shown in Table 1. Approximately 200 mg of each sample was loaded into a stainless-steel reactor. The reactor was heated from room temperature to 440°C at a heating rate of 5°C/min and maintained at 440°C for half an hour. The hydrogen desorption curves of the four samples are shown in Figure 4. The 2LiBH4–Li3AlH6 sample underwent a two-step dehydrogenation process in which the release of hydrogen began at 190°C and approximately 3 wt% of hydrogen was released in the first step. The second step began at approximately 330 C and the remaining 6.15 wt% of hydrogen was released. The total dehydrogenation capacity of 9.15 wt% is consistent with the theoretical hydrogen storage capacity. In the 2LiBH4–Li3AlH6 with 5 wt% TiF3 composite, the initial dehydrogenation temperatures of the two-step process decreased to 110 and 270°C. As the amount of TiF3 increased, the decomposition temperatures of Li3AlH6 and LiBH4 tended to decrease. The Li3AlH6 decomposed at 88°C in the 10 wt% TiF3-added 2LiBH4–Li3AlH6 composite, compared to 85°C in the 15 wt% TiF3-added sample. LiBH4 started to release hydrogen at 238°C in the 10 wt %-TiF3 added sample and at 225°C in the 15 wt% TiF3 added sample. These results indicate that the addition of TiF3 improved the thermodynamic properties of the 2LiBH4–Li3AlH6 composites. In contrast to the 2LiBH4–Li3AlH6 composite, the absence of a “platform area” between the first and second steps of the composites with TiF3 indicated that LiBH4 tended to decomposition at a lower temperature and the rate of hydrogen desorption were accelerated by the catalytic effect of TiF3. The time required for total decomposition decreased to 82 min when the TiF3 amount was 15 wt% compared to the 95 min required for the 2LiBH4–Li3AlH6 composite without TiF3. Clearly, the addition of TiF3 enhanced both the thermodynamic and kinetic properties of the 2LiBH4–Li3AlH6 composite system. However, the theoretical hydrogen storage capacity and the actual hydrogen desorption capacity of the composites with TiF3 decreased as the amount of TiF3 increased (shown in Table 1).

TABLE 1. Theoretical hydrogen storage capacity and actual hydrogen desorption capacity of 2LiBH4–Li3AlH6 samples with different amounts of TiF3.
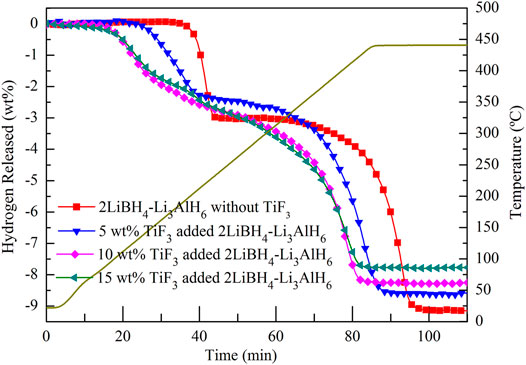
FIGURE 4. Hydrogen desorption curves of 2LiBH4–Li3AlH6 samples with different amounts of added TiF3.
To reveal the dehydrogenation pathway and catalytic effect of TiF3, the XRD patterns of the dehydrogenation products of the four samples are displayed in Figure 5. In the 2LiBH4–Li3AlH6 composite (Figure 5A), the presence of LiH, Al, and AlB2 phases indicates that LiBH4 reacted with Al generated from Li3AlH6 (Li et al., 2020) in situ to form AlB2, as shown in Eq. 3 (Choi et al., 2011b; Soru, 2014; Meethom, et al. 2020):
The unknown peak near 49° was also observed in previous studies (Mao et al., 2009a; Li, 2012). This peak was probably due to an intermediate dehydrogenation product of LiBH4 and Li3AlH6. In the samples with 10 wt% TiF3 (Figure 5C) and the 15 wt% TiF3 (Figure 5D), some Ti-based or F-based phases could be detected in addition to the peaks corresponding to LiH, Al, and AlB2. The LiF characteristic peaks near 38° and 79° correspond to the reaction products between LiBH4 and TiF3, as shown in Eq. 4 (Mao et al., 2009b; Guo, 2010).
The TiH2 peaks at 36° and Al3Ti peaks at 31° and 44° may possibly be due to reaction products between Li3AlH6 and TiF3, the reaction mechanisms of which were explored in Liu’s work (Liu et al., 2010). The diffraction peak of AlB2 appeared at 57° in the 10 and 15 wt% TiF3-added samples, indicating that the amount of AlB2 was increased.
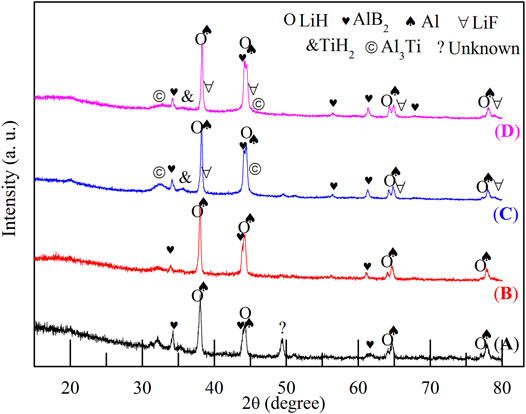
FIGURE 5. XRD patterns of dehydrogenated 2LiBH4–Li3AlH6 samples with different amounts of added TiF3: (A) 0 wt%, (B) 5 wt%, (C) 10 wt%, and (D) 15 wt%.
Reversible Performance of TiF3 Added 2LiBH4–Li3AlH6 Composite with Different Back Pressures
The reversible performance of the 2LiBH4–Li3AlH6 composite was investigated in this study. Approximately 200 mg samples of 2LiBH4–Li3AlH6 composite were loaded in a tubular reactor and heated to 450°C at a heating rate of 5°C/min. The dehydrogenated samples were maintained at 450°C for 250 min and then cooled down to ambient temperature naturally. The hydrogen adsorption process was performed at the hydrogen pressure of 100 bar at 450°C for 10 h. The dehydrogenation curves of the 2LiBH4–Li3AlH6 composite are shown in Figure 6. The hydrogen release capacity of the 2LiBH4–Li3AlH6 composite was 9.2 wt% in the first cycle, and 3.3 wt% and 2.4 wt% in the second and third cycles, respectively. Unlike the two-step desorption reactions of the first cycle, only one-step reactions occurred in the second and third cycles, and the initial dehydrogenation temperature reached as high as 400°C.
The observation of the B–H bond of LiBH4 at 2,200–2,400 cm−1 in the FT–IR curves of the ball-milled sample and the resorption sample (Figure 7) indicates that the 2LiBH4–Li3AlH6 composite was partially reversible, and that the reversible component was LiBH4. The formation process of LiBH4 is given by Eq. 5 (Li et al., 2012):
In the second and third dehydrogenation cycles, the hydrogen releasing capacities were lower than 3.5 wt%, which is significantly lower than the first one. Therefore, further research is required to improve the reversible performance. In a previous work, Mao (Mao et al., 2013) reported that hydrogen back pressure could improve the cyclic performance of LiBH4-based composites. As mentioned earlier, TiF3 is a superior catalyst for improving the hydrogen storage performance of the 2LiBH4–Li3AlH6 composite. Therefore, the studies that follow focus on the influence of hydrogen back pressure on the dehydrogenation and cyclic performance of TiF3-added 2LiBH4–Li3AlH6 composites. The 2LiBH4–Li3AlH6 with 5 wt% TiF3 composite was dehydrogenated at 425°C with initial hydrogen back pressures of 2.5, 3.0, and, 3.5 bar. The dehydrogenated samples then began to absorb hydrogen at 100 bar hydrogen pressure for 10 h. The dehydrogenation curves at different hydrogen back pressures in the first and second cycles are shown in Figure 8. The dehydrogenation capacity in the first cycle at the different hydrogen back pressures was about 8.2 wt% to 9.0 wt% in the 2LiBH4–Li3AlH6 with 5 wt% TiF3 composite, which is lower than its theoretical capacity. In the second dehydrogenation cycle, the amount of hydrogen released was 4.0 wt% or 4.6 wt%, which are higher than that of 2LiBH4–Li3AlH6 composite (3.3 wt%). From these results, it could be concluded that a hydrogen back pressure of between 2.5 and 3.5 bar and the addition of TiF3 could improve the reversible performance of the 2LiBH4–Li3AlH6 composite to some extent. However, the dehydrogenation kinetics of the 2LiBH4–Li3AlH6 with TiF3 composite was hindered by the hydrogen back pressure. It took more than 150 h to release 8.7 wt% hydrogen with 3.5 bar hydrogen back pressure in the TiF3-added 2LiBH4–Li3AlH6 composite, compared to 1.5 h in the composite without back pressure.
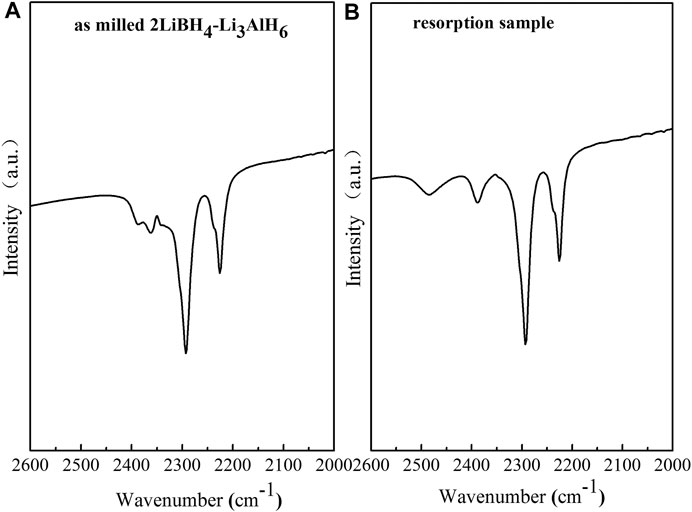
FIGURE 7. FT–IR curves of the 2LiBH4–Li3AlH6 samples: (A) after ball-milling and (B) rehydrogenation.
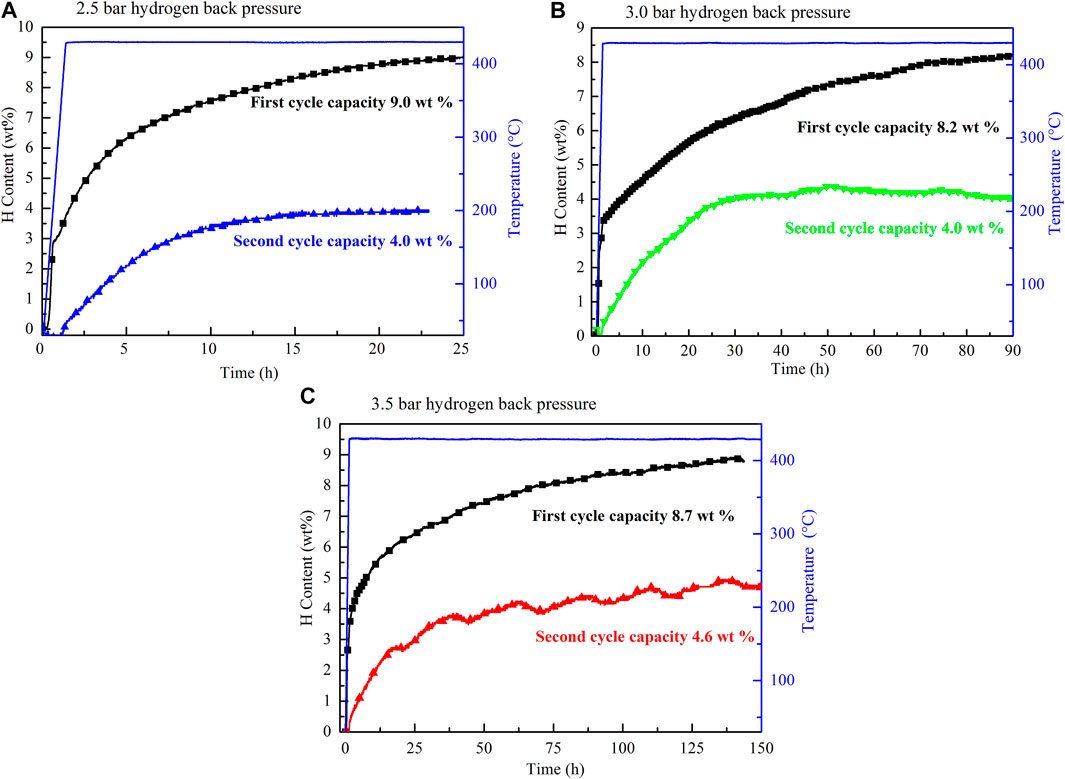
FIGURE 8. Cyclic dehydrogenation curves of the TiF3-added 2LiBH4–Li3AlH6 composites with (A) 2.5 bar, (B) 3.0 bar, and (C) 3.5 bar of hydrogen back pressure in the first and second dehydrogenation cycles.
The XRD patterns of the second-cycle dehydrogenation products are shown in Figure 9. Three phases, namely, AlB2, LiH, and Al, were detected in all the curves. Compared with Figure 5B, the diffraction intensity of AlB2 increased in Figures 9A–C, which resulted in the improved reversible performance.
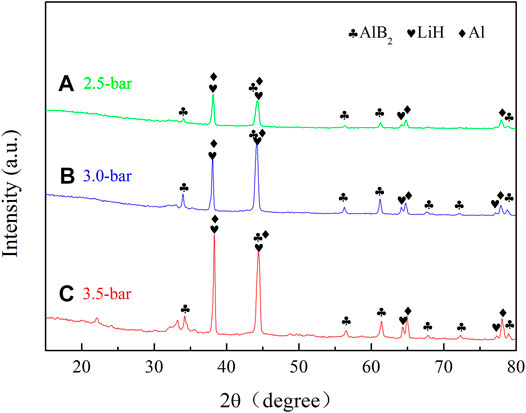
FIGURE 9. XRD patterns of the second cycle dehydrogenation products of TiF3-added 2LiBH4–Li3AlH6 composites with different back pressures: (A) 2.5 bar, (B) 3.0 bar, and (C) 3.5 bar.
The surface topography of the 2LiBH4–Li3AlH6 composites under different conditions was observed by SEM. The ball-milled sample (Figure 10A) displayed a coral-like structure. At 50,000 × magnification (inset of Figure 10A), the particles had a rod-shaped appearance with a length of approximately 3 μm and a width of 1 μm. After the first cycle of dehydrogenation, the particles agglomerated into aggregates (Figure 10B) instead of rod-shaped structures. After the second cycle of dehydrogenation at the back pressure of 3 bar, some spherical particles were formed, as shown in Figure 10C. Using the energy dispersive spectrometer, these particles were found to consist of metallic aluminum. The aggregation and growth of metallic aluminum led to a poor dispersion and reduced active surface area of the dehydrogenation products, which may explain the partial reversibility of the 2LiBH4–Li3AlH6 composites (Meethom et al., 2020).
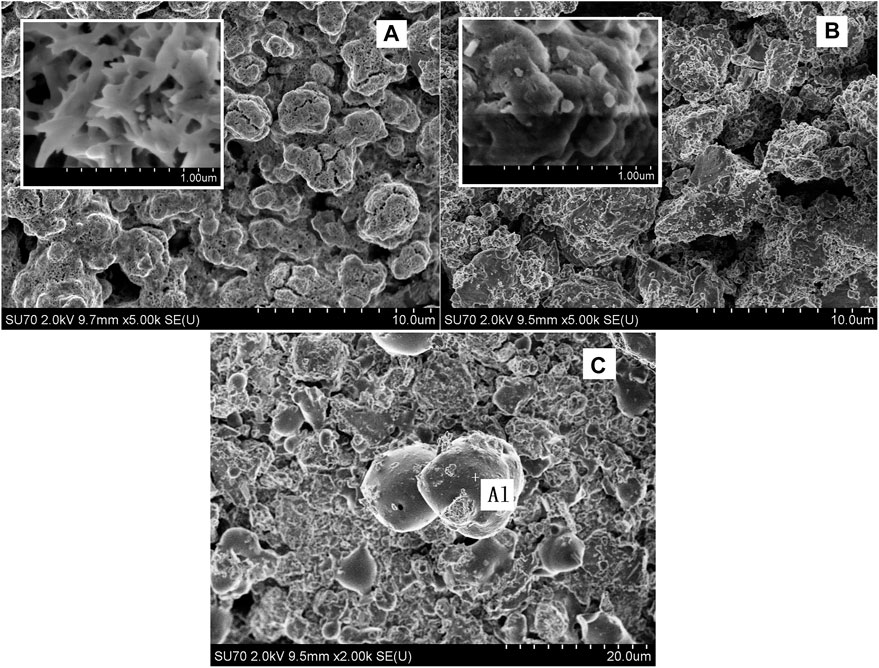
FIGURE 10. SEM images of the 2LiBH4–Li3AlH6 composites: (A) ball-milled sample, (B) sample after first dehydrogenation cycle, and (C) sample after second dehydrogenation cycle with 3 bar back pressure.
Conclusion
In this study, the dehydrogenation performance and influence of back pressure on the 2LiBH4–Li3AlH6 with/without TiF3 composites were investigated. TiF3 enabled Li3AlH6 and LiBH4 to desorb hydrogen at lower temperatures. With an increase in the amount of TiF3, the dehydrogenation temperature decreased significantly. In the 15% TiF3-added composite, Li3AlH6 decomposed at 85°C and LiBH4 at 225°C, that is, at 105°C lower for each component compared with the undoped sample. However, when the TiF3 content was increased to 15 wt%, the hydrogen capacity of the composite was reduced to 7.85 wt%, which is 15% lower than that without the 2LiBH4–Li3AlH6 composite. In the reversibility evaluation, the hydrogen back pressures of 2.5 bar, 3.0 bar, and 3.5 bar hydrogen were adopted. The results indicate that the back pressure could enhance the reversible performance of 2LiBH4–Li3AlH6 composite to some extent. A reversible hydrogen capacity of 4.6 wt% was obtained with a back pressure of 3.5 bar in the TiF3-added 2LiBH4–Li3AlH6 composites. However, the kinetics of the TiF3-added 2LiBH4–Li3AlH6 composites were hindered. More than 150 h were required to complete the hydrogen release process at the hydrogen back pressure of 3.5 bar. The SEM results showed that metallic aluminum was aggregated, resulting in poor dispersion of the dehydrogenated phases and reduced active surface area. Further research is needed to improve the desorption and absorption performance of LiBH4.
Data Availability Statement
The original contributions presented in the study are included in the article/Supplementary Material, further inquiries can be directed to the corresponding author.
Author Contributions
YL and LC: conception and design of study. YL and YZ: acquisition of data. YL analysis and/or interpretation of data. YL: drafting the manuscript. YZ and LC revising the manuscript critically for important intellectual content. YL, YZ, and LC approval of the version of the manuscript to be published.
Funding
This work was supported by the National Natural Science Foundation of China (51671173), the Quzhou Science and Technology Guidance Project (2020012) and the Zhejiang Province Education Department Project (FG2020220). The authors would like to acknowledge these funds for their support.
Conflict of Interest
The authors declare that the research was conducted in the absence of any commercial or financial relationships that could be construed as a potential conflict of interest.
Acknowledgments
We would like to thank Editage (www.editage.com) for English language editing.
References
Ampoumogli, A., Charalambopoulou, G., Javadian, P., Richter, B., Jensen, T. R., and Steriotis, T. (2015). Hydrogen Desorption and Cycling Properties of Composites Based on Mesoporous Carbons and a LiBH4-Ca(BH4)2 Eutectic Mixture. J. Alloys Comp. 645, S480–S484. doi:10.1016/j.jallcom.2014.12.077
Ares, J. R., Aguey-Zinsou, K.-F., Porcu, M., Sykes, J. M., Dornheim, M., Klassen, T., et al. (2008). Thermal and Mechanically Activated Decomposition of LiAlH4. Mater. Res. Bull. 43 (5), 1263–1275. doi:10.1016/j.materresbull.2007.05.018
Aresfernandez, J., Agueyzinsou, F., Elsaesser, M., Ma, X., Dornheim, M., Klassen, T., et al. (2007). Mechanical and Thermal Decomposition of LiAlH4LiAlH4 with Metal Halides. Int. J. Hydrogen Energ. 32 (8), 1033–1040. doi:10.1016/j.ijhydene.2006.07.011
Au, M., and Jurgensen, A. (2006). Modified Lithium Borohydrides for Reversible Hydrogen Storage. J. Phys. Chem. B 110 (13), 7062–7067. doi:10.1021/jp056240o
Bergemann, N., Pistidda, C., Uptmoor, M., Milanese, C., Santoru, A., Emmler, T., et al. (2019). A New Mutually Destabilized Reactive Hydride System: LiBH4-Mg2NiH4. J. Energ. Chem. 34, 240–254. doi:10.1016/j.jechem.2019.03.011
Bilen, M., Yılmaz, O., and Gürü, M. (2015). Synthesis of LiBH4 from LiBO2 as Hydrogen Carrier and its Catalytic Dehydrogenation. Int. J. Hydrogen Energ. 40 (44), 15213–15217. doi:10.1016/j.ijhydene.2015.02.085
Choi, Y. J., Lu, J., Sohn, H. Y., Fang, Z. Z., Kim, C., Bowman, R. C., et al. (2011a). Reaction Mechanisms in the Li3AlH6/LiBH4 and Al/LiBH4 Systems for Reversible Hydrogen Storage. Part 2: Solid-State NMR Studies. J. Phys. Chem. C 115 (13), 6048–6056. doi:10.1021/jp109113f
Choi, Y. J., Lu, J., Sohn, H. Y., and Fang, Z. Z. (2011b). Reaction Mechanisms in the Li3AlH6/LiBH4 and Al/LiBH4 Systems for Reversible Hydrogen Storage. Part 1: H Capacity and Role of Al. J. Phys. Chem. C 115 (13), 6040–6047. doi:10.1021/jp109112t
Dematteis, E. M., Dematteis, E. R., Roedern, E., Pinatel, E. R., Corno, M., Jensen, T. R., et al. (2016). A Thermodynamic Investigation of the LiBH4-NaBH4 System. RSC Adv. 6, 60101–60108. doi:10.1039/c6ra09301a
Ding, Z., Lu, Y., Li, L., and Shaw, L. (2019). High Reversible Capacity Hydrogen Storage through Nano-LiBH4 + Nano-MgH2 System. Energ. Storage Mater. 20, 24–35. doi:10.1016/j.ensm.2019.04.025
Ding, Z., Wu, P., and Shaw, L. (2019). Solid-state Hydrogen Desorption of 2 MgH2 + LiBH4 Nano-Mixture: A Kinetics Mechanism Study. J. Alloys Comp. 806, 350–360. doi:10.1016/j.jallcom.2019.07.218
Guo, Y. H., Yu, X. B., Gao, L., Xia, G. L., Guo, Z. P., and Liu, H. K. (2010). Significantly Improved Dehydrogenation of LiBH4destabilized by TiF3. Energy Environ. Sci. 3 (4), 465–470. doi:10.1039/b915779d
Halim Yap, F. A., and Ismail, M. (2018). Functions of MgH2 in the Hydrogen Storage Properties of a Na3AlH6-LiBH4 Composite. J. Phys. Chem. C 122 (42), 23959–23967. doi:10.1021/acs.jpcc.8b07934
Halim Yap, F. A., Mustafa, N. S., Yahya, M. S., Mohamad, A. A., and Ismail, M. (2018). A Study on the Hydrogen Storage Properties and Reaction Mechanism of Na3AlH6LiBH4 Composite System. Int. J. Hydrogen Energ. 43 (17), 8365–8374. doi:10.1016/j.ijhydene.2018.03.070
Hansen, B. R. S., Ravnsbæk, D. B., Reed, D., Book, D., Gundlach, C., Skibsted, J., et al. (2013). Hydrogen Storage Capacity Loss in a LiBH4-Al Composite. J. Phys. Chem. C 117 (15), 7423–7432. doi:10.1021/jp312480h
Ismail, M., Zhao, Y., Yu, X. B., and Dou, S. X. (2012). Improved Hydrogen Storage Performance of MgH2-NaAlH4 Composite by Addition of TiF3. Int. J. Hydrogen Energ. 37 (10), 8395–8401. doi:10.1016/j.ijhydene.2012.02.117
Jain, I. P., Jain, P., and Jain, A. (2010). Novel Hydrogen Storage Materials: A Review of Lightweight Complex Hydrides. J. Alloys Comp. 503 (2), 303–339. doi:10.1016/j.jallcom.2010.04.250
Jiang, K., Xiao, X., Chen, L., Han, L., Li, S., Ge, H., et al. (2012). A Comparative Study of the Hydrogen Storage Properties of LiBH4 Doping with CaHCl and CaH2. J. Alloys Comp. 539, 103–107. doi:10.1016/j.jallcom.2012.06.039
Langmi, H. W., McGrady, G. S., Newhouse, R., and Rönnebro, E. (2012). Mg2FeH6-LiBH4 and Mg2FeH6-LiNH2 Composite Materials for Hydrogen Storage. Int. J. Hydrogen Energ. 37 (8), 6694–6699. doi:10.1016/j.ijhydene.2012.01.020
Li, G., Matsuo, M., Deledda, S., Sato, R., Hauback, B. o. r. C., and Orimo, S.-i. (2013). Dehydriding Property of LiBH4 Combined with Mg2FeH6. Mater. Trans. 54 (8), 1532–1534. doi:10.2320/matertrans.M2013145
Li, Y., Li, P., and Qu, X. (2017). Investigation on LiBH4-CaH2 Composite and its Potential for Thermal Energy Storage. Sci. Rep. 7, 41754. doi:10.1038/srep41754
Li, Y., Wu, S., Zhu, D., He, J., Xiao, X., and Chen, L. (2020). Dehydrogenation Performances of Different Al Source Composite Systems of 2LiBH4 + M (M = Al, LiAlH4, Li3AlH6). Front. Chem. 8, 227. doi:10.3389/fchem.2020.00227
Li, Y., Xiao, X., Chen, L., Han, L., Shao, J., Fan, X., et al. (2012). Effects of Fluoride Additives on the Hydrogen Storage Performance of 2LiBH4-Li3AlH6 Destabilized System. J. Phys. Chem. C 116 (42), 22226–22230. doi:10.1021/jp307572x
Lin, W., Xiao, X., Wang, X., Wong, J.-W., Yao, Z., Chen, M., et al. (2020). Extreme High Reversible Capacity with over 8.0 Wt% and Excellent Hydrogen Storage Properties of MgH2 Combined with LiBH4 and Li3AlH6. J. Energ. Chem. 50, 296–306. doi:10.1016/j.jechem.2020.03.076
Liu, D. M., Tan, Q. J., Gao, C., Sun, T., and Li, Y. T. (2015). Reversible Hydrogen Storage Properties of LiBH4 Combined with Hydrogenated Mg11CeNi Alloy. Int. J. Hydrogen Energ. 40 (20), 6600–6605. doi:10.1016/j.ijhydene.2015.03.130
Liu, H., Wang, X., Zhou, H., Gao, S., Ge, H., Li, S., et al. 2016). Improved Hydrogen Desorption Properties of LiBH4 by AlH3 Addition. Int. J. Hydrogen Energ., 41(47), 22118–22127. doi:10.1016/j.ijhydene.2016.09.177
Liu, S.-S., Zhang, Y., Sun, L.-X., Zhang, J., Zhao, J.-N., Xu, F., et al. (2010). The Dehydrogenation Performance and Reaction Mechanisms of Li3AlH6 with TiF3 Additive. Int. J. Hydrogen Energ. 35 (10), 4554–4561. doi:10.1016/j.ijhydene.2009.12.108
Liu, X.-S., Liu, H.-Z., Qiu, N., Zhang, Y.-B., Zhao, G.-Y., Xu, L., et al. (2021). Cycling Hydrogen Desorption Properties and Microstructures of MgH2-AlH3-NbF5 Hydrogen Storage Materials. Rare Met. 40, 1003–1007. doi:10.1007/s12598-020-01425-1
Ma, Y., Li, Y., Liu, T., Zhao, X., Zhang, L., Han, S., et al. (2016). Enhanced Hydrogen Storage Properties of LiBH4 Generated Using a Porous Li3BO3 Catalyst. J. Alloys Comp. 689, 187–191. doi:10.1016/j.jallcom.2016.07.313
Mao, J. F., Guo, Z. P., Liu, H. K., and Yu, X. B. (2009a). Reversible Hydrogen Storage in Titanium-Catalyzed LiAlH4-LiBH4 System. J. Alloys Comp. 487 (1–2), 434–438. doi:10.1016/j.jallcom.2009.07.158
Mao, J. F., Yu, X. B., Guo, Z. P., Poh, C. K., Liu, H. K., Wu, Z., et al. (2009b). Improvement of the LiAlH4−NaBH4 System for Reversible Hydrogen Storage. J. Phys. Chem. C 113 (24), 10813–10818. doi:10.1021/jp808269v
Mao, J., Guo, Z., Leng, H., Wu, Z., Guo, Y., Yu, X., et al. (2010). Reversible Hydrogen Storage in Destabilized LiAlH4−MgH2−LiBH4 Ternary-Hydride System Doped with TiF3. J. Phys. Chem. C 114 (26), 11643–11649. doi:10.1021/jp1012208
Mao, J., Guo, Z., Yu, X., Ismail, M., and Liu, H. (2011). Enhanced Hydrogen Storage Performance of LiAlH4-MgH2-TiF3 Composite. Int. J. Hydrogen Energ. 36 (9), 5369–5374. doi:10.1016/j.ijhydene.2011.02.001
Mao, J., Guo, Z., Yu, X., and Liu, H. (2013). Combined Effects of Hydrogen Back-Pressure and NbF5 Addition on the Dehydrogenation and Rehydrogenation Kinetics of the LiBH4-MgH2 Composite System. Int. J. Hydrogen Energ. 38 (9), 3650–3660. doi:10.1016/j.ijhydene.2012.12.106
Meethom, S., Kaewsuwan, D., Chanlek, N., Utke, O., and Utke, R. (2020). Enhanced Hydrogen Sorption of LiBH4-LiAlH4 by Quenching Dehydrogenation, Ball Milling, and Doping with MWCNTs. J. Phys. Chem. Sol. 136, 109202. doi:10.1016/j.jpcs.2019.109202
Mustafa, N. S., Halim Yap, F. A., Yahya, M. S., and Ismail, M. (2018). The Hydrogen Storage Properties and Reaction Mechanism of the NaAlH4 + Ca(BH4)2 Composite System. Int. J. Hydrogen Energ. 43 (24), 11132–11140. doi:10.1016/j.ijhydene.2018.04.234
Mustafa, N. S., and Ismail, M. (2019). Significant Effect of TiF3 on the Performance of 2NaAlH4+Ca(BH4)2 Hydrogen Storage Properties. Int. J. Hydrogen Energ. 44 (39), 21979–21987. doi:10.1016/j.ijhydene.2019.06.080
Puszkiel, J., Gennari, F. C., Arneodo Larochette, P., Troiani, H. E., Karimi, F., Pistidda, C., et al. (2014). Hydrogen Storage in Mg-LiBH4 Composites Catalyzed by FeF3. J. Power Sourc. 267, 799–811. doi:10.1016/j.jpowsour.2014.05.130
Sofianos, M. V., Sheppard, D. A., Rowles, M. R., Humphries, T. D., Liu, S., and Buckley, C. E. (2017). Novel Synthesis of Porous Mg Scaffold as a Reactive Containment Vessel for LiBH4. RSC Adv. 7, 36340–36350. doi:10.1039/C7RA05275H
Sofianos, M. V., Sheppard, D. A., Silvester, D. S., Lee, J., Paskevicius, M., Humphries, T. D., et al. (2018). Electrochemical Synthesis of Highly Ordered Porous Al Scaffolds Melt-Infiltrated with LiBH4for Hydrogen Storage. J. Electrochem. Soc. 165 (2), D37–D42. doi:10.1149/2.0481802jes
Soru, S., Taras, A., Pistidda, C., Milanese, C., Bonatto Minella, C., Masolo, E., et al. (2014). Structural Evolution upon Decomposition of the LiAlH4+LiBH4 System. J. Alloys Comp. 615, S693–S697. doi:10.1016/j.jallcom.2013.12.027
Surrey, A., Bonatto Minella, C., Fechler, N., Antonietti, M., Grafe, H.-J., Schultz, L., et al. (2016). Improved Hydrogen Storage Properties of LiBH4 via Nanoconfinement in Micro- and Mesoporous Aerogel-like Carbon. Int. J. Hydrogen Energ. 41 (12), 5540–5548. doi:10.1016/j.ijhydene.2016.01.163
Thaweelap, N., and Utke, R. (2016). Dehydrogenation Kinetics and Reversibility of LiAlH4-LiBH4 Doped with Ti-Based Additives and MWCNT. J. Phys. Chem. Sol. 98, 149–155. doi:10.1016/j.jpcs.2016.07.005
Tu, G., Xiao, X., Jiang, Y., Qin, T., Li, S., Ge, H., et al. (2015). Composite Cooperative Enhancement on the Hydrogen Desorption Kinetics of LiBH 4 by Co-doping with NbCl 5 and Hexagonal BN. Int. J. Hydrogen Energ. 40 (33), 10527–10535. doi:10.1016/j.ijhydene.2015.06.168
Wu, X., Wang, X., Cao, G., Li, S., Ge, H., Chen, L., et al. (2012). Hydrogen Storage Properties of LiBH4-Li3AlH6 Composites. J. Alloys Comp. 517, 127–131. doi:10.1016/j.jallcom.2011.12.054
Xia, G.-l., Leng, H.-y., Xu, N.-x., Li, Z.-l., Wu, Z., Du, J.-l., et al. (2011). Enhanced Hydrogen Storage Properties of LiBH4-MgH2 Composite by the Catalytic Effect of MoCl3. Int. J. Hydrogen Energ. 36 (12), 7128–7135. doi:10.1016/j.ijhydene.2011.03.060
Xiang, M., Zhang, Y., Zhu, Y., Guo, X., Chen, J., and Li, L. (2018). Ternary LiBH4-NaBH4-MgH2 Composite as Fast Ionic Conductor. Solid State Ionics 324, 109–113. doi:10.1016/j.ssi.2018.06.015
Yahya, M. S., Ali, N. A., Sazelee, N. A., Mustafa, N. S., Halim Yap, F. A., and Ismail, M. (2019). Intensive Investigation on Hydrogen Storage Properties and Reaction Mechanism of the NaBH4-Li3AlH6 Destabilized System. Int. J. Hydrogen Energ. 44 (39), 21965–21978. doi:10.1016/j.ijhydene.2019.06.076
Yang, Y., Gao, M., Liu, Y., Wang, J., Gu, J., Pan, H., et al. (2012). Multi-hydride Systems with Enhanced Hydrogen Storage Properties Derived from Mg(BH4)2 and LiAlH4. Int. J. Hydrogen Energ. 37 (14), 10733–10742. doi:10.1016/j.ijhydene.2012.04.068
Yu, X. B., Guo, Y. H., Sun, D. L., Yang, Z. X., Ranjbar, A., Guo, Z. P., et al. (2010). A Combined Hydrogen Storage System of Mg(BH4)2−LiNH2with Favorable Dehydrogenation. J. Phys. Chem. C 114 (10), 4733–4737. doi:10.1021/jp910547s
Zang, L., Sun, W., Liu, S., Huang, Y., Yuan, H., Tao, Z., et al. (2018). Enhanced Hydrogen Storage Properties and Reversibility of LiBH4 Confined in Two-Dimensional Ti3C2. ACS Appl. Mater. Inter. 10 (23), 19598–19604. doi:10.1021/acsami.8b02327
Zhang, Y., Liu, Y., Yang, Y., Li, Y., Hu, J., Gao, M., et al. (2018). Superior Catalytic Activity of In Situ Reduced Metallic Co for Hydrogen Storage in a Co(OH) 2 -containing LiBH 4/2LiNH 2 Composite. Mater. Res. Bull. 97, 544–552. doi:10.1016/j.materresbull.2017.09.037
Zhao, Y., Jiao, L., Liu, Y., Guo, L., Li, L., Liu, H., et al. (2014). A Synergistic Effect between Nanoconfinement of Carbon Aerogels and Catalysis of CoNiB Nanoparticles on Dehydrogenation of LiBH4. Int. J. Hydrogen Energ. 39 (2), 917–926. doi:10.1016/j.ijhydene.2013.10.137
Zheng, J., Yao, Z., Xiao, X., Wang, X., He, J., Chen, M., et al. (2021). Enhanced Hydrogen Storage Properties of High-Loading Nanoconfined LiBH4-Mg(BH4)2 Composites with Porous Hollow Carbon Nanospheres. Int. J. Hydrogen Energ. 46, 852–864. doi:10.1016/j.ijhydene.2020.09.177
Zhou, H., Wang, X., Liu, H., and Yan, M. (2017). Enhanced Hydrogen Storage Properties of 2LiBH4-LiAlH4 Nanoconfined in Resorcinol Formaldehyde Carbon Aerogel. J. Alloys Comp. 726, 525–531. doi:10.1016/j.jallcom.2017.07.080
Keywords: 2LiBH4-Li3AlH6, hydrogen storage performance, catalytic modification, hydrogen back pressure, reversible performance
Citation: Li Y, Zhang Y and Chen L (2021) Effect of Different Amounts of TiF3 on the Reversible Hydrogen Storage Properties of 2LiBH4–Li3AlH6 Composite. Front. Chem. 9:693302. doi: 10.3389/fchem.2021.693302
Received: 10 April 2021; Accepted: 03 May 2021;
Published: 14 May 2021.
Edited by:
Feng Luo, East China University of Technology, ChinaReviewed by:
Haizhen Liu, Guangxi University, ChinaTomasz Czujko, Military University of Technology in Warsaw, Poland
Copyright © 2021 Li, Zhang and Chen. This is an open-access article distributed under the terms of the Creative Commons Attribution License (CC BY). The use, distribution or reproduction in other forums is permitted, provided the original author(s) and the copyright owner(s) are credited and that the original publication in this journal is cited, in accordance with accepted academic practice. No use, distribution or reproduction is permitted which does not comply with these terms.
*Correspondence: Yuxian Zhang, enl4QHF6Y3QubmV0