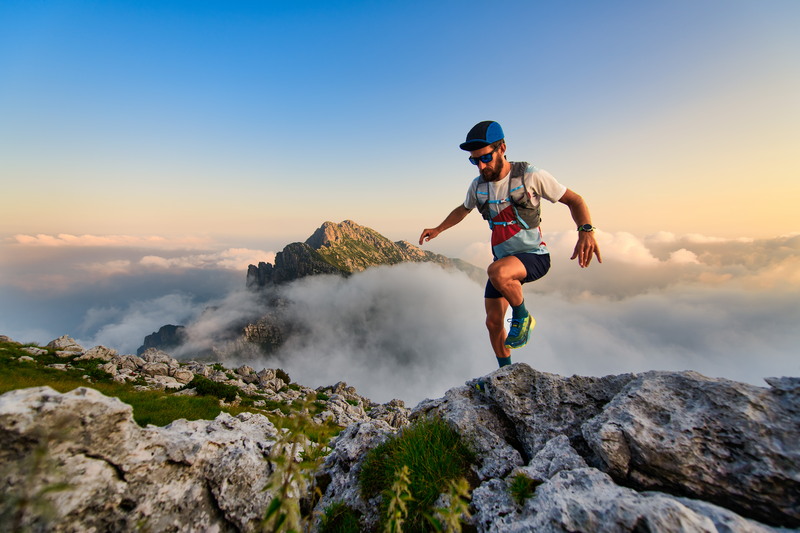
95% of researchers rate our articles as excellent or good
Learn more about the work of our research integrity team to safeguard the quality of each article we publish.
Find out more
MINI REVIEW article
Front. Chem. , 16 October 2020
Sec. Green and Sustainable Chemistry
Volume 8 - 2020 | https://doi.org/10.3389/fchem.2020.571504
This article is part of the Research Topic Perspectives on Carbon Dioxide Capture and Conversion View all 8 articles
The iron and steel industry is an energy-intensive sector, and large amounts of waste/ by-products are generated during the steelmaking process, such as CO2, metallurgical slag, and wastewater. Enhancing the development and deployment of treating waste from the steelmaking process will be environment friendly and resource-saving. Capturing CO2 by steel slag (SS) via mineralization is regarded to be an excellent choice due to the high basicity of the slag. In this paper, recent research on the steel slag-based carbon capture and storage (SS-CCS) by mineralization was summarized. Three routes of SS-CCS are compared including, direct gas-solid carbonation, direct aqueous carbonation, and indirect carbonation, respectively. Furthermore, the challenges and prospects for further development of the SS-CCS were discussed.
As climate change progresses, the increasing frequency of natural disasters is causing more people to pay attention (Cai et al., 2017; Han et al., 2017; Zou et al., 2017; Shan et al., 2018; Yi et al., 2019). It is reasonable to believe that the contribution of CO2 emissions to climate change is 76% (Intergovernmental panel on climate change, 2014). The BP Statistical Review of World Energy published data of CO2 discharge from global energy consumption in 2018. Results indicated that the carbon emission of the world reached 33.89 Gt CO2, the fastest growth since 2010 of a total of 2.0% (British Petroleum, 2019). There is no doubt that industries and society have a duty-bound responsibility to reduce CO2 emissions as the current pace of progress is inconsistent with Paris's climate goals.
Anthropogenic CO2 emissions result primarily from the burning of carbon-based fossil fuels, and China, the United States, and India together account for more than two-thirds of global energy growth (British Petroleum, 2019; Cui et al., 2019). A large amount of fossil fuels are consumed which emit large volumes of CO2 from iron and steelmaking processes. The contribution of CO2 emissions from iron and steelmaking processes to global CO2 emissions is about 6–7% (Doucet, 2010). Furthermore, besides the CO2 emissions, a substantial amount of metallurgical slag is generated during iron and steelmaking processes. Steelmaking slag (SS) is mainly used in road construction and cement industries in many countries due to its similar composition to Portland cement (Gedam et al., 2012; Saly et al., 2018). However, some SSs can release large amounts of toxic metals (e.g., Cr) affecting their utilization (Huiting and Forssberg, 2003). Moreover, undesired alterations of minerals in SS could cause volume instability as a result of swelling and cracking phenomena, such as the hydration of alkaline earth metal oxides (CaO and MgO), and the transformation from α-C2S to γ-C2S (Shi, 2004; Wang et al., 2010; Yildirim and Prezzi, 2011). Researchers proposed that unstable CaO, MgO, and silicates can be used to capture and bind CO2 by mineral carbonation to reduce carbon emissions and create a (thermodynamically) more stable material (Huijgen and Comans, 2006; Wang et al., 2019).
SS can be classified into many types according to the steps of the smelting process, including electric arc furnace slag (EAFS), basic oxygen furnace slag (BOFS), ladle furnace slag (LFS), argon oxygen decarburization slag (AODS), and continuous casting slag (CCS). The methods of steel slag-based carbon capture and storage (SS–CCS) may be divided into a direct carbonation route and an indirect carbonation route (Ibrahim et al., 2019).
Direct SS carbonation, that is, the reaction of SS and CO2 accomplished in a single reaction step, includes two-phase (direct gas-solid carbonation) and three-phases (direct aqueous carbonation) routes (Huijgen and Comans, 2005; Librandi et al., 2019). Since the year 2000, researchers have completely a number of studies on the possibility and potential of SS's carbonation for the storage of CO2. Table 1 lists the reported carbonation efficiency for EAFS, BOFS, and LFS with different operating parameters. It can be seen in Table 1 that the optimum conditions obtained in various studies are highly dependent on the physical and chemical properties of SS (e.g., particle size, chemical composition, and mineralogy) (Polettini et al., 2016a). Gas-solid carbonation of SS suffers from rather long reaction rates as a result of the formation of a carbonate layer and calcium-depleted silicate zones, which hinder the diffusion of gas into the particle center (Butt et al., 1996). Pretreatments of SS, like grinding (CO2 uptake rate of SS is more than 80% wt. when the particle size is <0.08 mm) and thermal activation (830–850°C at 1 atm CO2 of BOFS) can improve the reaction rate and carbon capture rate, but are energy-intensive (Ron and Jens, 2002; Santos et al., 2012).
Flue gases typically carry a lot of heat, and therefore direct gas-solid carbonation of SS for in situ CO2 sequestration is a promising process that recovers heat and increases the carbonation reaction rate. Tian et al. (2013) investigated the carbonation of SS with flue gas under various operational conditions. Temperature, CO2 concentration, and the presence of SO2 affect the carbon capture rate of the gas-solid carbonation of SS. The presence of SO2 has a positive effect on the SS mineralized CO2, especially during the diffusion-controlled stage, the reason probably being that SO2 increases the surface activation energy of SS, making CO2 easier to absorb. Though the maximum CO2 sequestration obtained at 151 ppm of SO2 was 88.5kg CO2 (76.1 kg CO2 without SO2 presence) which was, therefore, affected by the gas diffusion limitation.
Compared to the direct gas-solid carbonation of SS, a direct aqueous carbonation reaction has a higher chemical conversion rate. The three steps that occur in the reaction of SS with CO2 in aqueous solutions involve CO2 dissolution in water, Ca/Mg release from SS, and Ca or Mg carbonate precipitation. From the reaction mechanism of SS and CO2 in aqueous solution, it was found that the conversion rate of SS is related to the pressure of CO2, water amount, the amount of alkaline earth metal eluted from the SS, and the concentration of the lixiviant used. Pan et al. (2012) described the effect of CO2 pressure on the carbonation process, showing that an elevated pressure of 6 bar favors the dissolution of CO2 into the slurry (L/S, i.e., liquid to solid ratio, = 10 mL·g−1) at room temperature (Rushendra et al., 2016). However, there is an optimal CO2 pressure (CO2 pressure of 3 bar and L/S to 0.4 mL·g−1 at room temperature) on maximum CO2 uptake (13% wt.), beyond which the dissolution of SS becomes the limiting step of the carbonation process (Baciocchi et al., 2009). Beyond the optimal value, the carbonation efficiency (actual sequestration/theoretical sequestration capacity) of SS (27%) will not notably increase with the pressure but requires more heat and power (Rushendra et al., 2016). It was reported that a porous layer is formed during the Ca/Mg extraction from SS, which can obstruct further dissolution (Safari et al., 2009; Said et al., 2015). Furthermore, the reacted SS is covered by CaCO3 products, hindering gas diffusion and as a result also the carbonation reaction (Walton et al., 1997). It was observed that the thickness of the carbonated shell of the BOFS is about 200 μm, obtained at 200°C, 40% CO2 content, and 60% relative humidity (RH) (Ko et al., 2015). It is generally accepted that removing the “barrier layer” during the reaction is crucial to increase the dissolution rate of Ca/Mg from SS and to obtain high levels of conversion.
Researchers investigated the effects of operating conditions, such as temperature (25–100°C), particle size (<2 mm), and L/S (5–20 mL·g−1) on the kinetics of reactions (c.f., Table 1). It is necessary to closely control the temperature and water amount during the process of SS direct aqueous carbonation since increased temperatures can increase the carbonation reaction rate but reduce the solubility of CO2 in water (Bauer et al., 2011; Ukwattage et al., 2015). An appropriate water amount (L/S to 0.4 mL·g−1) can promote metal cations leaching from the SS (Baciocchi et al., 2010), while the presence of excessive water would block the diffusion of CO2 in the slurry (Fernández Bertos et al., 2004; Ko et al., 2015). Therefore, there has been an extensive research effort addressing the optimization of the liquid to solid ratio in the process, as low L/S ratios could reduce energy input requirements (differences in slag composition leads to different optimal L/S) (Sanna et al., 2014). Moreover, besides optimizing process parameters, changing the design of the reactor may promote carbonation progress. Compared to autoclave and slurry reactors, a rotating packed bed and rotary kiln is better dynamically, which can improve the contact probability between the gas and solid phases (Pan et al., 2014).
The carbonation process typically changes the original mineral composition of SS for several elements besides Ca and Mg. Mn silicate and oxide phases take part in the reaction and form new carbonates, causing a high dissolution degree of the original slag (Chang et al., 2018). There is a potential environmental risk that heavy metals and toxic elements, such as Cr, V, Ni, Pb, and Mo, elute during the carbonation process (Owais et al., 2019). Hence, Cr-bearing stainless steel slag (SSS) is rarely employed in the process of SS-CCS if the Cr exists in unstable phases. The authors of this paper studied the effects of chemical composition and cooling conditions on the crystallization behavior of stainless steel slag (Cao et al., 2018; Zhao et al., 2018a,b). It was proposed that a stabilization control of Cr during co-extraction of the Ca/Mg of SSS could be achieved by a modification treatment (Zhao et al., 2019a,b).
The product layer produced during the direct SS mineralization of CO2 hinders the leaching of Ca/Mg from the SS and the diffusion of gas to the surface of unreacted phases. The route of indirect SS carbonation is divided into two steps: Ca/Mg is extracted from the SS before the carbonation process, with the two steps possibly occurring under different process conditions and concentrations (Sanna et al., 2015). The first step is the recovery of Ca/Mg from the SS by leaching, and the second step is the dissolution of CO2 in the leachate followed by carbonate precipitation. It performs best when the extraction and carbonation process are optimized separately. The operating parameters such as the particle size (<250 μm), chemical composition of SS (Mainly CaO and MgO content), type and concentration of additives (lixiviants) (acid, CH3COOH, H2SO4, HNO3, HCl and HCOOH, ammonium salt, NH4Cl, NH4NO3, and CH3COONH4), residence time (1–700 h), and solution temperature (25–100°C) were studied to improve the extraction yield of Ca/Mg (Mattila and Zevenhoven, 2014; Bilen et al., 2016; Wang et al., 2018). The carbonate precipitation rate mainly depends on the CO2 flow speed (0.5–2 L/min), size of gas bubbles (~1.2–10 mm), and the concentration of hydrogen ion in the solution, i.e., pH (Mattila et al., 2012; Xu et al., 2014).
Both weak and strong acids (H2SO4, HCl, HNO3, HCOOH, and CH3COOH) can selectively leach Ca/Mg from natural rock (i.e., serpentinite, magnesite, wollastonite) and alkaline solid waste from industrial activities (i.e., steel slag), to obtain a Ca/Mg salt solution (Teir et al., 2007, 2009). Selectively extracting Ca/Mg from SS is challenging to implement, some Fe, Si, or other elements may be eluted during the leaching process. Alkaline substances may be required to add to the leachate to recover Fe and promote the carbonation. It has been calculated that capturing and storing one ton of CO2 may require several tons of make-up chemicals (1842 kg CO2/t NaOH), which is costly and gives a high energy penalty (per ton of NaOH must consume 2,230 kWh of electricity and 0.44 tons of steam) (Wang et al., 2018). Also, often the reactor needs to be made of corrosion-resistant materials.
Earlier work by Kodama et al. (2008); Teir (2008), and Eloneva et al. (2010a,b), Said et al. (2013) proposed that the aqueous solution of ammonium salt (NH4Cl, NH4NO3, and CH3COONH4) could be used to extract calcium from SS, and precipitated calcium carbonate (PCC) was prepared as a product. This route was named slag2PCC (c.f., Figure 1) by the team. The selective leaching of Ca from SS (c.f., Equation 1) and the formation of PCC (c.f., Equation 3) occur in the two separate extraction and carbonation reactors, respectively, while at the same time, residue slag and PCC products are removed via the circulation of the ammonium salt solvent solution between the extraction and carbonation reactors (Mattila and Zevenhoven, 2014; Said et al., 2016; Teir et al., 2016). Both the extraction and carbonation steps operate at ambient temperatures and pressures. The low temperature can suppress the ammonia slip and gives a lower energy penalty for solvent regeneration (Darde et al., 2009).
Figure 1. The slag2PCC route for PCC manufacturing from steelmaking slags: gas streams are in yellow arrows, aqueous streams are in blue arrows, and solid streams are in black arrows. Output items that are beneficial to the environment and resources are green, and items that have potential effects on the environment and resources are yellow.
The dissolution of CO2 in the aqueous ammonium salt solution is the speed-control part of the Slag2PCC process (c.f., Equation 2). Results reported that 4–5 mm CO2 bubbles dissolved when they rose ~1.6–1.9 m in an unmixed water column (Legendre and Zevenhoven, 2016, 2017). Recently, Zevenhoven et al. (2019) proposed that properly positioned mixing impellers can optimize the dissolution of CO2 bubbles at minimal mixing energy input. Incomplete CO2 dissolution is not only a flaw for the CCS but also a risk for an ammonia slip from the aqueous solution due to the dissolved ammonia possibly diffusing to and into CO2 bubbles (Zevenhoven et al., 2019). The second drawback is the ammonia evaporating from the solution and leaving with exit gas, which reduces the recycling of the ammonium salt solvent. Higher temperatures and lower solvent concentration can increase NH3 release (Said et al., 2016). Moreover, ammonium salt types also affect NH3 release (Eloneva et al., 2011). Furthermore, not all Ca be extracted from the slag, with about 70%-80% of Ca in converter slag (74–125 μm) dissolving in the ammonium nitrate solution (0.5–2 mol·L−1) (Mattila and Zevenhoven, 2014). Also a considerable amount of water may be needed to wash the PCC product and residue slag, which creates a significant environmental footprint (Hudd, 2014).
Although a large number of studies have focused on the reaction of CO2 with SS on a laboratory scale, it is still far from achieving the industrial level of several tons·h−1 processed. This is partly because of many challenges in terms of the differences in original mineralogy of SS, limitations of reaction kinetics, increase in energy and economic costs while optimizing process parameters, and minimizing environmental impacts.
SS is a homogeneous solid waste and is composed of multiple mineral phases. Mineral phases such as bredigite (Ca7Mg(SiO4)4), srebrodolskite (Ca2Fe2O5), akermanite (Ca2MgSi2O7), β-and γ-polymorph (Ca2SiO4), merwinite (Ca3Mg(SiO4)2), and spinel (MgC2O4, mainly in stainless steel slag) exhibit varying degrees of carbonation kinetics during the process of mineralizing CO2. It has been reported that bredigite is the most reactive mineral, following by the polymorphs and wollastonite, while merwinite and diopside give the slowest carbonation conversions during a direct carbonation process (Bodor et al., 2013). The metallic oxide phases exhibited a relatively higher solubility than the silicate phases in aqueous solutions with various additives (Zhao et al., 2020). Therefore, non-sensitive Ca/Mg-bearing phases in SS reduce the CO2 capture rate and utilization rate of Ca and Mg resources. Furthermore, different types of SS, even the same kinds of SS from various steel mills, have different optimal process parameters for SS to capture CO2, because the main Ca/Mg-bearing phase of SS is different. Therefore, there are currently no systematic industrialization parameters suitable for the process of SS-CCS.
The formation of the product layer during the direct carbonation reaction is unavoidable and hinders the further chemical processing of metallurgical waste gas and SS. If physical or chemical methods can continuously remove the barrier layer during the reaction, the utilization rate of Ca/Mg resources in the SS can be significantly improved, and the emissions of unreacted CO2 gas can be reduced. Compared with the direct carbonation routes, the slag2PCC has a significantly higher chemical reaction rate, which can achieve selective leaching Ca and produce pure PCC. Not all CO2 gas molecules can be dissolved in this solution, and the dissolution of CO2 is the rate-controlling step of the slag2PCC process. NH3 loss from the solution lowers alkalinity and adds costs, which penalize the carbonation conversion and requires a subsequent gas treatment. Promoting the selective leaching rate of Ca in the steel slag and reaching higher efficiencies is necessary for the industrial-scale processing of the slag2PCC.
Both direct and indirect SS carbonation requires electricity for crushing, grinding, and sieving the slag aimed at increasing the reaction rate. It was found in an assessment that it takes 980–6,300 MJ t−1 CO2 and 246-427 kWh t−1 CO2 in the process of direct aqueous and indirect carbonation of SS, respectively, where the energy requirement is associated with heating, CO2 compression, and solid/liquid separation (Costa et al., 2016; Wang et al., 2018). Circulated pumping of the ammonium salt solution, gas compression input, solution agitation, and solids washing in the process of slag2PCC also requires power (Hudd, 2014). Besides the electricity, the washing of PCC products and recovery of solvent salts may require significant water as well, which increases the environmental burden. Therefore, it is necessary to systematically evaluate the relationship between energy input requirements and the benefit (and market value) of PCC products. Moreover, the treatment and application of carbonized slag and residual slag requires further study while the long-term leaching behavior of carbonated slag and residual slag and the potential environmental risks still need to be evaluated (Eloneva et al., 2010a; Zevenhoven et al., 2011).
The iron and steel industry is an energy-intensive sector, generating large amounts of waste during the steelmaking process, such as CO2, metallurgical slag, and wastewater. It is promising that it is possible to operate a CO2 capture process based on a reaction with SS on an industrial scale, since SSs are often cheap and readily available near large CO2 emitter sources. If physical or chemical methods can remove the barrier layer during the reaction, direct SS carbonation may be more natural to implement as a large-scale industrial application. This is not only due to the fact that the reaction is carried out in a single reactor, but also because the flue gas can provide all or part of the heat needed to improve the reaction's kinetics. In addition, modifying the mineral phase composition of the SS, which gives Ca/Mg in the sensitive phase of the carbonization reaction, has a positive effect on the application of SS–CCS.
Slag2PCC is a relatively complete process for co-processing steel slag and CO2 and is presently under investigation in pilot and laboratory scales (Said et al., 2013). In the future, it will be necessary to focus on avoiding NH3 losses from the solution and improving CO2 dissolution in the solutions for the slag2PCC process. Moreover, the energy input requirements of the slag2PCC process and the full economic and environmental benefits of the PCC still need to be systematically evaluated. The assessment results may differ for different countries and regions, which may be related to the scale of the steel mill and the distance between the steel mill and the application plant of PCC. Also, the treatment of solid residues generated by the SS-CCS process and environmental risk assessments need further study.
QZ carried out the concepts and design of the article. XC, QM, and JL provided literature research. XM carried out manuscript editing. CL, HS, and RZ performed manuscript review. All authors contributed to the article and approved the submitted version.
This work was supported by the National Natural Science Foundation of China (Nos. 51704068 and 52074078), the Liaoning Provincial Natural Science Foundation of China (No. 2019-MS-127), the National Training Program of Innovation and Entrepreneurship for Undergraduates (No. S202010145095), and the Fundamental Research Funds for the Central Universities (Nos. N182410001 and N2025035).
The authors declare that the research was conducted in the absence of any commercial or financial relationships that could be construed as a potential conflict of interest.
Baciocchi, R., Costa, G., CO2 Di Gianfilippo, M., Polettini, A., Pomi, R., and Stramazzo, A. (2015). Thin-film versus slurry-phase carbonation of steel slag: uptake and effects on mineralogy. J. Hazard. Mater. 283, 302–313. doi: 10.1016/j.jhazmat.2014.09.016
Baciocchi, R., Costa, G., Di Bartolomeo, E., Polettini, A., and Pomi, R. (2010). Carbonation of stainless steel slag as a process for CO2 storage and slag valorization. Waste Biomass Valorization 1, 467–477. doi: 10.1007/s12649-010-9047-1
Baciocchi, R., Costa, G., Polettini, A., and Pomi, R. (2009). Influence of particle size on the carbonation of stainless steel slag for CO2 storage. Energy Procedia 1, 4859–4866. doi: 10.1016/j.egypro.2009.02.314
Bauer, M., Gassen, N., Stanjek, H., and Peiffer, S. (2011). Carbonation of lignite fly ash at ambient T and P in a semi-dry reaction system for CO2 sequestration. Appl. Geochem. 26, 1502–1512. doi: 10.1016/j.apgeochem.2011.05.024
Bilen, M., Altiner, M., and Yildirim, M. (2016). Evaluation of steelmaking slag for CO2 fixation by leaching-carbonation process. Part. Sci. Technol. 36, 368–377. doi: 10.1080/02726351.2016.1267285
Bodor, M., Santos, R. M., Kriskova, L., Elsen, J., Vlad, M., and van Gerven, T. (2013). Susceptibility of mineral phases of steel slags towards carbonation: mineralogical, morphological and chemical assessment. Eur. J. Mineral. 25, 533–549. doi: 10.1127/0935-1221/2013/0025-2300
British Petroleum (2019). BP Statistical Review of World Energy - June 2019. London, UK: Economic policy.
Butt, D. P., Lackner, K. S., Wendt, C. H., Conzone, S. D., Kung, H., Lu, Y. C., et al. (1996). Kinetics of thermal dehydroxylation and carbonation of magnesium hydroxide. J. Am.Ceramic Soc. 79, 1892–1898. doi: 10.1111/j.1151-2916.1996.tb08010.x
Cai, W. J., Li, K., Liao, H., Wang, H. J., and Wu, L. X. (2017). Weather conditions conducive to Beijing severe haze more frequent under climate change. Nat. Clim. Chang. 7, 257–262. doi: 10.1038/nclimate3249
Cao, L. H., Liu, C. J., Zhao, Q., and Jiang, M. F. (2018). Analysis on the stability of chromium in mineral phases in stainless steel slag. Metall. Res. Technol. 115:8. doi: 10.1051/metal/2017071
Chang, E. E., Pan, S. Y., Chen, Y. H., Tan, C. S., and Chiang, P. C. (2012). Accelerated carbonation of steelmaking slags in a high-gravity rotating packed bed. J. Hazard. Mater. 227-228, 97–106. doi: 10.1016/j.jhazmat.2012.05.021
Chang, J., Wang, D., and Fang, Y. (2018). Effects of mineralogical changes in BOFS during carbonation on pH and Ca and Si leaching. Constr. Build. Mater. 192, 584–592. doi: 10.1016/j.conbuildmat.2018.10.057
Costa, G., Polettini, A., Pomi, R., Stramazzo, A., and Zingaretti, D. (2016). Energetic assessment of CO2 sequestration through slurry carbonation of steel slag: a factorial study. Greenh. Gases Sci. Technol. 7, 530–541. doi: 10.1002/ghg.1659
Cui, D., Deng, Z., and Liu, Z. (2019). China's non-fossil fuel CO2 emissions from industrial processes. Appl. Energy 254, 1–9. doi: 10.1016/j.apenergy.2019.113537
Danielle, B., Lynda, K., Sébastien, S., Robert, H., Patrick, N., and Murielle, M. (2008). CO2 sequestration potential of steel slags at ambient pressure and temperature. Eng. Chem. Res. 47, 7610–7616. doi: 10.1021/ie701721j
Darde, V., Thomsen, K., van Well, W. J. M., and Stenby, E. H. (2009). Chilled ammonia process for CO2 capture. Energy Procedia 1, 1035–1042. doi: 10.1016/j.egypro.2009.01.137
Doucet, F. J. (2010). Effective CO2-specific sequestration capacity of steel slags and variability in their leaching behaviour in view of industrial mineral carbonation. Mineral. Eng. 23, 262–269. doi: 10.1016/j.mineng.2009.09.006
Eloneva, S., Mannisto, P., Said, A., Fogelholm, C. J., and Zevenhoven, R. (2011). Ammonium salt-based steelmaking slag carbonation: precipitation of CaCO3 and ammonia losses assessment. Greenh. Gases. 1, 305–311. doi: 10.1002/ghg.37
Eloneva, S., Puheloinen, E. M., Kanerva, J., Ekroos, A., Zevenhoven, R., and Fogelholm, C. J. (2010b). Co-utilisation of CO2 and steelmaking slags for production of pure CaCO3-legislative issues. J. Clean. Prod. 18, 1833–1839. doi: 10.1016/j.jclepro.2010.07.026
Eloneva, S., Said, A., Fogelholm, C. J., and Zevenhoven, R. (2010a). Feasibility study of a method utilizing carbon dioxide and steelmaking slags to produce precipitated calcium carbonate (PCC). Int. Con. Appl. Energy. 169–178.
Fernández Bertos, M., Li, X., Simons, S. J. R., Hills, C. D., and Carey, P. J. (2004). Investigation of accelerated carbonation for the stabilisation of MSW incinerator ashes and the sequestration of CO2. Green Chem. 6, 428–436. doi: 10.1039/B401872A
Gedam, V. V., Jha, R., Labhasetwar, P., and Engelsen, C. J. (2012). A comprehensive physico-chemical, mineralogical and morphological characterization of Indian mineral wastes. Environ. Monitor. Assess. 185, 6343–6352. doi: 10.1007/s10661-012-3029-7
Ghacham, A. B., Pasquier, L. C., Cecchi, E., Blais, J. F., and Mercier, G. (2016). CO2 sequestration by mineral carbonation of steel slags under ambient temperature: parameters influence, and optimization. Environ. Sci. Pollut. Res. 23, 17635–17646. doi: 10.1007/s11356-016-6926-4
Han, Z. Y., Zhou, B. T., Xu, Y., Wu, J., and Shi, Y. (2017). Projected changes in haze pollution potential in China: an ensemble of regional climate model simulations. Atmos. Chem. Phys. 17, 10109–10123. doi: 10.5194/acp-17-10109-2017
Hudd, H. (2014). Post-Treatment of Precipitated Calcium Carbonate (PCC) Produced From Steel Converter Slag. (Master's thesis). Turku: Åbo Akademi University
Huijgen, W. J. J., and Comans, R. N. J. (2005). Mineral CO2 sequestration by steel slag carbonation. Environ. Sci. Technol. 39, 9676–9682. doi: 10.1021/es050795f
Huijgen, W. J. J., and Comans, R. N. J. (2006). Carbonation of steel slag for CO2 sequestration: leaching of products and reaction mechanisms. Environ. Sci. Technol. 40, 2790–2796. doi: 10.1021/es052534b
Huiting, S., and Forssberg, E. (2003). An overview of recovery of metals from slags. Waste Manage. 23, 933–949. doi: 10.1016/S0956-053X(02)00164-2
Ibrahim, M., El-Naas, M., Benamor, A., Al-Sobhi, S., and Zhang, Z. (2019). Carbon mineralization by reaction with steel-making waste: a review. Processes 7:115. doi: 10.3390/pr7020115
Intergovernmental panel on climate change (2014). IPCC Fifth Assessment Report.2014: Intergovernmental Panel on Climate Change. Geneva: World Meteorological Organization.
Ko, M. S., Chen, Y. L., and Jiang, J. H. (2015). Accelerated carbonation of basic oxygen furnace slag and the effects on its mechanical properties. Constr. Build. Mater. 98, 286–293. doi: 10.1016/j.conbuildmat.2015.08.051
Kodama, S., Nishimoto, T., Yamamoto, N., Yogo, K., and Yamada, K. (2008). Development of a new pH-swing CO2 mineralization process with a recyclable reaction solution. Energy 33, 776–784. doi: 10.1016/j.energy.2008.01.005
Legendre, D., and Zevenhoven, R. (2016). A numerical Euler–Lagrange method for bubble tower CO2 dissolution modeling. Chem. Eng. Res. Des. 111, 49–62. doi: 10.1016/j.cherd.2016.04.010
Legendre, D., and Zevenhoven, R. (2017). Detailed experimental study on the dissolution of CO2 and air bubbles rising in water. Chem. Eng. Sci. 158, 552–560. doi: 10.1016/j.ces.2016.11.004
Librandi, P., Costa, G., Stendardo, S., and Rennto, B. (2019). Carbonation of BOF slag in a rotary kiln reactor in view of the scale-up of the wet route process. Environ. Prog. Sustain. Energy 38, 1–9. doi: 10.1002/ep.13140
Mattila, H. P., Grigaliunait, I., and Zevenhoven, R. (2012). Chemical kinetics modeling and process parameter sensitivity for precipitated calcium carbonate production from steelmaking slags. Chem. Eng. J. 192, 77–89. doi: 10.1016/j.cej.2012.03.068
Mattila, H. P., and Zevenhoven, R. (2014). Design a continuous process setup for precipitated calcium carbonate production from steel converter slag. ChemSusChem 7, 903–913. doi: 10.1002/cssc.201300516
Owais, M., Järvinen, M., Taskinen, P., and Said, A. (2019). Experimental study on the extraction of calcium, magnesium, vanadium and silicon from steelmaking slags for improved mineral carbonation of CO2. J. CO2 Util. 31, 1–7. doi: 10.1016/j.jcou.2019.02.014
Pan, S. Y., Chang, E. E., and Chiang, P. C. (2012). CO2 capture by accelerated carbonation of alkaline wastes: a review on its principles and applications. Aerosol. Air Qual. Res. 12, 770–791. doi: 10.4209/aaqr.2012.06.0149
Pan, S. Y., Chiang, P. C., Chen, Y. H., Tan, C. S., and Chang, E. E. (2014). Kinetics of carbonation reaction of basic oxygen furnace slags in a rotating packed bed using the surface coverage model: maximization of carbonation conversion. Appl. Energy 113, 267–276. doi: 10.1016/j.apenergy.2013.07.035
Polettini, A., Pomi, R., and Stramazzo, A. (2016a). Carbon sequestration through accelerated carbonation of BOF slag: influence of particle size characteristics. Chem. Eng. J. 298, 26–35. doi: 10.1016/j.cej.2016.04.015
Polettini, A., Pomi, R., and Stramazzo, A. (2016b). CO2 sequestration through aqueous accelerated carbonation of BOF slag: a factorial study of parameters effects. J. Environ. Manage. 167, 185–195. doi: 10.1016/j.jenvman.2015.11.042
Ron, Z., and Jens, K. (2002). “Direct dry Mineral carbonation for CO2 emissions reduction in finland,” in 27th International Technical Conference on Coal Utilization & Fuel Systems Clearwater (Clearwater, FL).
Rushendra, R. T. D., Palanivelu, K., and Ramachandran, A. (2016). Direct mineral carbonation of steelmaking slag for CO2 sequestration at room temperature. Environ. Sci. Pollut. Res. Int. 23, 7349–7359. doi: 10.1007/s11356-015-5893-5
Safari, V., Arzpeyma, G., Rashchi, F., and Mostoufi, N. (2009). A shrinking particle-shrinking core model for leaching of a zinc ore containing silica. Int. J. Miner. Process. 93, 79–83. doi: 10.1016/j.minpro.2009.06.003
Said, A., Laukkanen, T., and Jarvinen, M. (2016). Pilot-scale experimental work on carbon dioxide sequestration using steelmaking slag. Appl. Energy 177, 602–611. doi: 10.1016/j.apenergy.2016.05.136
Said, A., Mattila, H. P., Järvinen, M., and Zevenhoven, R. (2013). Production of precipitated calcium carbonate (PCC) from steelmaking slag for fixation of CO2. Appl. Energy 112, 765–771. doi: 10.1016/j.apenergy.2012.12.042
Said, A., Mattila, O., Eloneva, S., and Järvinen, M. (2015). Enhancement of calcium dissolution from steel slag by ultrasound. Chem. Eng. Process. 89, 1–8. doi: 10.1016/j.cep.2014.12.008
Saly, F., Guo, L., Ma, R., Gu, C., and Sun, W. (2018). Properties of steel slag and stainless steel slag as cement replacement materials: a comparative study. J. Wuhan Univ. Technol. Mater. Sci. Ed. 33, 1444–1451. doi: 10.1007/s11595-018-1989-3
Sanna, A., Uibu, M., Caramanna, G., Kuusik, R., and Maroto-Valer, M. M. (2014). A review of mineral carbonation technologies to sequester CO2. Chem. Soc. Rev. 43, 8049–8080. doi: 10.1039/C4CS00035H
Sanna, A., Uibu, M., Caramanna, G., Kuusik, R., and Maroto-Valer, M. M. (2015). ChemInform abstract: a review of mineral carbonation technologies to sequester CO2. ChemInform. 46, 8049–8080. doi: 10.1002/chin.201506312
Santos, R. M., Ling, D., Sarvaramini, A., Guo, M., Elsen, J., Larachi, F., and van Gerven, T. (2012). Stabilization of basic oxygen furnace slag by hot-stage carbonation treatment. Chem. Eng. J. 203, 239–250. doi: 10.1016/j.cej.2012.06.155
Shan, Y. L., Guan, D. B., Klaus, H., Zheng, B., Steven, J. D., Lichao, J., et al. (2018). City-level climate change mitigation in China. Sci. Adv. 4:eaaq0390. doi: 10.1126/sciadv.aaq0390
Shi, C. Y. (2004). Steel slag-its production, processing, characteristics, and cementitious properties. J. Mater. Civ. Eng. 16, 230–236. doi: 10.1061/(ASCE)0899-1561(2004)16:3(230)
Teir, S. (2008). Fixation of carbon dioxide by producing carbonations from minerals and steelmaking slags (Ph.D (Eng) thesis). Helsinki University of Technology Espoo Finland; Tekniikka & talous.
Teir, S., Eloneva, S., Fogelholm, C. J., and Zevenhoven, R. (2009). Fixation of carbon dioxide by producing hydromagnesite from serpentinite. Appl. Energy. 86, 214–218. doi: 10.1016/j.apenergy.2008.03.013
Teir, S., Kotiranta, T., Pakarinen, J., and Mattila, H. P. (2016). Case study for production of calcium carbonate from carbon dioxide in flue gases and steelmaking slag. J. CO2 Util. 14, 37–46. doi: 10.1016/j.jcou.2016.02.004
Teir, S., Revitzer, H., Eloneva, S., Fogelholm, C. J., and Zevenhoven, R. (2007). Dissolution of natural serpentinite in mineral and organic acids. Int. J. Miner. Process. 83, 36–46. doi: 10.1016/j.minpro.2007.04.001
Tian, S., Jiang, J., Chen, X., Yan, F., and Li, K. (2013). Direct gas-solid carbonation kinetics of steel slag and the contribution to in situ sequestration of flue gas CO2 in steel-making plants. ChemSusChem 6, 2348–2355. doi: 10.1002/cssc.201300436
Ukwattage, N. L., Ranjith, P. G., Yellishetty, M., Bui, H. H., and Xu, T. (2015). A laboratory-scale study of the aqueous mineral carbonation of coal fly ash for CO2 sequestration. J. Clean Prod. 103, 665–674. doi: 10.1016/j.jclepro.2014.03.005
Walton, J. C., Bin-Shafique, S., Smith, R. W., Gutierrez, N., and Tarquin, A. (1997). Role of carbonation in transient leaching of cementitious wasteforms. Environ. Sci. Technol. 31, 2345–2349. doi: 10.1021/es960964j
Wang, C. Y., Bao, W. J., Guo, Z. C., and Li, H. Q. (2018). Carbon dioxide sequestration via steelmaking slag carbonation in alkali solutions: experimental investigation and process evaluation. Acta Metall. Sin. 31, 771–784. doi: 10.1007/s40195-017-0694-0
Wang, D., Chang, J., and Ansari, W. S. (2019). The effects of carbonation and hydration on the mineralogy and microstructure of basic oxygen furnace slag products. J. CO2 Util. 34, 87–98. doi: 10.1016/j.jcou.2019.06.001
Wang, G., Wang, Y., and Gao, Z. (2010). Use of steel slag as a granular material: volume expansion prediction and usability criteria. J. Hazard. Mater. 184, 555–560. doi: 10.1016/j.jhazmat.2010.08.071
Xu, A. J., Zhang, H. N., and Dong-feng, H. E. (2014). Carbonation behavior assessment of RH slag batch after aqueous extraction at environmental pressure. J. Iron Steel Res. Int. 21, 74–81. doi: 10.1016/S1006-706X(14)60125-4
Yi, K., Meng, J., Yang, H. Z., He, C. L., Henze, D. K., Liu, J. F., et al. (2019). The cascade of global trade to large climate forcing over the Tibetan Plateau glaciers. Nat. Commun. 10:3281. doi: 10.1038/s41467-019-10876-9
Yildirim, I. Z., and Prezzi, M. (2011). Chemical, mineralogical and morphological properties of steel slag. Adv. Civ. Eng. 13:463638. doi: 10.1155/2011/463638
Zevenhoven, R., Fagerlund, J., and Songok, J. K. (2011). CO2 mineral sequestration: developments toward large-scale application. Greenh. Gases 1, 48–57. doi: 10.1002/ghg3.7
Zevenhoven, R., Legendre, D., Said, A., and Järvinen, M. (2019). Carbon dioxide dissolution and ammonia losses in bubble columns for precipitated calcium carbonate (PCC) production. Energy 175, 1121–1129. doi: 10.1016/j.energy.2019.03.112
Zhao, Q., Jing, Y., Li Kai, W., and You Cheng, J. L. (2020). Recovery of calcium and magnesium bearing phases from iron-and steelmaking slag for CO2 sequestration. Process Saf. Environ. Protect. 135, 81–90. doi: 10.1016/j.psep.2019.12.012
Zhao, Q., Liu, C. J., Cao, L., Cao, L. H., Jiang, M. F., Li, B. K., et al. (2018a). Shear-force based stainless steel slag modification for chromium immobilization. ISIJ Int. 59, 583–589. doi: 10.2355/isijinternational.ISIJINT-2017-678
Zhao, Q., Liu, C. J., Gao, T. C., Cao, L. H., and Jiang, M. F. (2018b). Growth and aggregation control of spinel by shear-force-based melting modification of stainless steel slag. Int. J. Miner. Metall. Mater. 25, 1140–1147. doi: 10.1007/s12613-018-1665-9
Zhao, Q., Liu, C. J., Gao, T. C., Gao, L., Sacen, H., and Zevenhoven, R. (2019a). Remediation of stainless steel slag with MnO for CO2 mineralization. Process Saf. Environ. Protect. 127, 1–8. doi: 10.1016/j.psep.2019.04.025
Zhao, Q., Liu, K., Sun, L. F., Liu, C. J., Jiang, M. F., Sacen, H., and Zevenhoven, R. (2019b). Towards carbon sequestration using stainless steel slag via phase modification and Co-extraction of calcium and magnesium. Process Saf. Environ. Protect. 133, 73–81. doi: 10.1016/j.psep.2019.11.004
Keywords: carbon capture and storage, steel slag, carbon emission reduction, waste management, mineralization
Citation: Zhao Q, Chu X, Mei X, Meng Q, Li J, Liu C, Saxén H and Zevenhoven R (2020) Co-treatment of Waste From Steelmaking Processes: Steel Slag-Based Carbon Capture and Storage by Mineralization. Front. Chem. 8:571504. doi: 10.3389/fchem.2020.571504
Received: 11 June 2020; Accepted: 17 August 2020;
Published: 16 October 2020.
Edited by:
Sebastiao M. P. Lucena, Federal University of Ceara, BrazilReviewed by:
Miguel Angel Centeno, Instituto de Ciencia de Materiales de Sevilla (ICMS), SpainCopyright © 2020 Zhao, Chu, Mei, Meng, Li, Liu, Saxén and Zevenhoven. This is an open-access article distributed under the terms of the Creative Commons Attribution License (CC BY). The use, distribution or reproduction in other forums is permitted, provided the original author(s) and the copyright owner(s) are credited and that the original publication in this journal is cited, in accordance with accepted academic practice. No use, distribution or reproduction is permitted which does not comply with these terms.
*Correspondence: Xiaohui Mei, MTkxMDU0NEBzdHUubmV1LmVkdS5jbg==
Disclaimer: All claims expressed in this article are solely those of the authors and do not necessarily represent those of their affiliated organizations, or those of the publisher, the editors and the reviewers. Any product that may be evaluated in this article or claim that may be made by its manufacturer is not guaranteed or endorsed by the publisher.
Research integrity at Frontiers
Learn more about the work of our research integrity team to safeguard the quality of each article we publish.