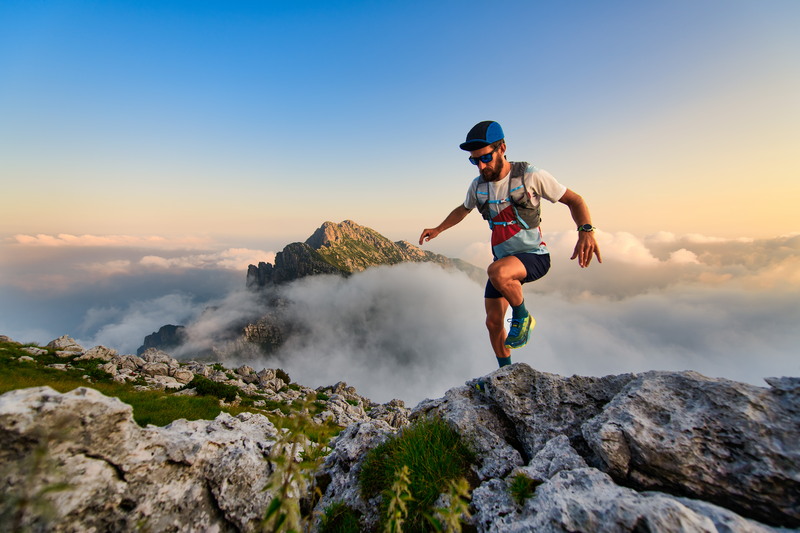
95% of researchers rate our articles as excellent or good
Learn more about the work of our research integrity team to safeguard the quality of each article we publish.
Find out more
ORIGINAL RESEARCH article
Front. Chem. , 07 April 2020
Sec. Green and Sustainable Chemistry
Volume 8 - 2020 | https://doi.org/10.3389/fchem.2020.00202
This article is part of the Research Topic Advanced Membrane Science and Technology for Sustainable Environmental Applications View all 6 articles
High stability Pd/ceramic/Ti-Al alloy composite membranes were prepared by electroless plating. Ceramic membranes fabricated by an in situ oxidation method were used as an inter-diffusion barrier between the Pd layer and the Ti-Al alloy support of the membranes to prevent intermetallic diffusion. The stabilities of the ceramic membranes at high temperatures in an H2 atmosphere were investigated. The permeation performances and stabilities of the Pd/ceramic/Ti-Al alloy composite membranes were also studied. The results showed that the thickness, pore size, and microstructure of the ceramic membranes did not change significantly after the treatment in an H2 atmosphere at high temperatures, indicating that the ceramic membranes prepared by the in situ oxidation method were stable in an H2 atmosphere at high temperatures. The thickness of the Pd layer was ~13 μm. The hydrogen permeability and H2/N2 selectivity of the Pd composite membranes at 773 K were 2.13 × 10−3 mol m−2 s−1 Pa−0.5 and 600, respectively. In addition, the H2 flux, N2 flux, and H2/N2 selectivity of the composite membranes remained nearly constant over three heat cycles (under the same conditions), indicating that the structures of the Pd/ceramic/Ti-Al alloy composite membranes were stable.
Recently, hydrogen has gained immense attention as a clean energy carrier for various industrial applications, especially for the development of fuel cells (Lemus and Duart, 2010; Vesborg et al., 2015; Sengodan et al., 2018). Pd membranes are widely used for hydrogen production and separation because of their high permeance and excellent selectivity for hydrogen (Keuler et al., 2002). The thickness of the Pd membrane is inversely proportional to the permeability. Hence, Pd-based membranes are usually prepared in the composite form, consisting of a thin, dense Pd top layer on a porous support (Zhang et al., 2006). Ti-Al alloys are considered promising porous supports for Pd membranes because of their higher specific strength, lower density, good oxidation resistance at higher temperatures, and similar thermal expansion co-efficient to that of Pd (Ma et al., 2007). However, although Ti-Al alloy averts the diffusion at temperatures lower than 873 K, the metal element diffusion phenomena occur between Pd and Ti-Al alloys after heat treatment at 973 K for 40 h in the presence of pure hydrogen (Zhang et al., 2011).
An effective approach to prevent intermetallic diffusion is to develop an inter-diffusion barrier layer between the Pd membrane and the metal support. However, the inter-diffusion barrier layer must be stable under high-temperature oxidation and reduction atmospheres. Huang and Dittmeyer (2006) used TiO2, YSZ, and ZrO2 as a diffusion barrier between the Pd layer and the sintered-metal support of composite membranes. They indicated that YSZ was the most promising inter-diffusion barrier and showed better intermetallic diffusion prevention than ZrO2 and TiO2. Zhang et al. (2009) used two different methods (in situ oxidized metal and sol-gel-derived YSZ) to prepare intermetallic diffusion barriers between Pd layer and PSS support of Pd composite membranes. They found that both the inter-diffusion barrier layers showed effective intermetallic diffusion prevention and the membranes were stable at temperatures in the range of 773–873 K. However, only the YSZ inter-diffusion barrier layer could prevent diffusion at temperatures higher than 873 K. Mardilovich et al. (1998) carried out an in situ oxidation reaction prior to plating Pd/PSS membranes to form an oxide membrane layer on porous stainless steel to act as a diffusion barrier between Pd and PSS. They found that the membranes were stable to heat treatment at 623–723 K for 6,000 h. Shu et al. (1993) employed sputtering to prepare an ultrathin intermediate layer of titanium nitride between a Pd/Ag alloy membrane and a PSS substrate. The results showed that the membranes were stable at temperatures higher than 973 K. Zhang et al. (2012) fabricated TiO2 membranes as a diffusion barrier on a Ti-Al alloy support to avoid intermetallic diffusion and to smooth the Ti-Al alloy support. The electron probe microanalysis (EPMA) and energy-dispersive X-ray spectroscopy (EDX) cross-sectional line scans showed that the TiO2 layer was an effective inter-diffusion barrier and was stable after 40 h of heat treatment at 973 K in the presence of pure H2. However, the adhesion between the TiO2 layer and Ti-Al alloy supports at high temperatures should be improved.
In this study, the high-temperature stability of the ceramic/Ti-Al alloy support was investigated by the gravimetric method, gas flux measurements, EDX, X-ray diffraction, and scanning electron microscopy (SEM) in a hydrogen atmosphere. Then, Pd membranes were prepared on the surface of the ceramic/Ti-Al alloy support, and their morphologies, permeabilities, selectivities, and stabilities were investigated in detail.
Ti-Al alloy discs with a diameter of 34 mm, a thickness of 2.5 mm, and an average pore size of 6 μm were used as the support for preparing the thin Pd composite membranes. The porous Ti-Al alloy discs were prepared using the method reported by He et al. (2007).
Prior to preparing the membranes, the supports were cleaned with acetone in an ultrasonic bath for 2 h to remove surface dirt and grease and were then dried overnight at 423 K. The ceramic membranes were prepared on Ti-Al alloy discs by sintering the Ti-Al alloy discs under a static air atmosphere at 1,023 K for 2 h in an electric furnace at the heating and cooling rate of 2 K/min. The procedure for the preparation of ceramic membranes has been described in detail in Zhang et al. (2015).
Electroless plating was used to deposit the Pd membranes on porous ceramic/Ti-Al alloy supports (Alique et al., 2016). Prior to the preparation of the palladium membranes, the surface of the Ti-Al alloy supports was activated and sensitized to seed Pd nuclei (Keuler et al., 2002). The deposition of Pd membranes was carried out at 313 K, and the plating bath was changed after every 60 min until dense Pd membranes with an ideal thickness were obtained. Deionized water was applied to clean the surface of the palladium membranes immediately after electroless plating to remove the impurities adsorbed on the surface and pores of the Pd layer. The composite membranes were then dried overnight at 423 K for 12 h (Zhang et al., 2012).
An electronic balance (Sartorius BS2202S, Germany) was used to monitor the weight of the ceramic membranes. XRD (Bruker D8 Advance diffractometer, with Cu- radiation) was used to examine the phase composition of the ceramic/Ti-Al alloy composite membranes. EDX (JSM, 5600, LV, Japan) was used to analyze the composition of the ceramic membrane surface. The surface and cross-section of the palladium and ceramic membranes were investigated by SEM (Quanta 200, Philip, USA). The gas permeation of the composite membranes at high temperatures was measured using a permeability apparatus. The ceramic/Ti-Al alloy composite membranes were placed in a stainless steel permeator. The permeate side was maintained at atmospheric pressure, while the retentate side was fed with H2 or N2. A back-pressure regulator was used to control the upstream pressure. A mass flow controller (Models D08-4D/ZM, Beijing Sevenstar Electronics Co., Ltd., Beijing, China) was used to measure the single gas flux once the temperature and pressure became constant.
The ceramic membranes were prepared on Ti-Al alloy supports by an in situ oxidation method at 1,023 K for 2 h in an air atmosphere followed by their heat treatment in an H2 atmosphere for 20 h at 773, 873, and 973 K, respectively. The stability test results of the membranes are summarized in Table 1. From the table, it is clear that the weight of the ceramic/Ti-Al alloys did not change when the heat treatment was carried out at temperatures lower than 973 K. This indicates that the oxide layers were stable at temperatures lower than 973 K. As can be seen from Table 2, the change in the N2 flux of the ceramic/Ti-Al alloy composite membranes after the heat treatment was negligible. This indicates that the heat treatment did not destroy the pore structure of the ceramic membranes and that the ceramic layers were stable at high temperatures.
Table 1. Percent of weight gain of ceramic/Ti-Al alloy composite membrane after treatment in H2 atmosphere at different temperatures for 20 h.
Table 2. Percent of N2 flux change of ceramic/Ti-Al alloy composite membrane after treatment in H2 atmosphere at different temperatures for 20 h.
The surface SEM images of the ceramic/Ti-Al alloys are shown in Figure 1. The oxidation layer was evident, and no surface damages were observed even after the heat treatment at 973 K for 20 h in an H2 atmosphere. Hence, the ceramic layer prepared by in situ oxidation was stable in an H2 atmosphere. This is consistent with the weight and N2 flux measurement results.
Figure 1. (A) Oxidized at 750°/2 h X300. (B) 700°/H2/20 h X300. (C) Oxidized at 750°/2 h X1200. (D) 700°/H2/20 h X1200. Surface SEM micrographs of the ceramic/Ti-Al alloy composite membrane in H2 atmosphere at different temperature for 20 h.
In order to investigate the effect of heat treatment on the elemental composition of the surface of the Ti-Al alloy support, an EDX analysis of the membranes was carried out. As shown in Figure 2, oxygen was present on the support surface even after the heat treatment at 973 K in an H2 atmosphere for 20 h, indicating that the ceramic layer prepared by in situ oxidation was stable at higher temperatures in an H2 atmosphere.
Figure 2. (A) Ceramic/Ti-Al alloy composite membrane. (B) 700°/H2/20 h. EDX characterization of the ceramic/T i-Al alloy composite membrane after treatment in H2 atmosphere at different temperature for 20 h.
The XRD patterns of the ceramic/Ti-Al alloy membrane are shown in Figure 3. The characteristic peak keeps constant even after the heat treatment in an H2 atmosphere for 20 h at 773, 873, and 973 K, indicating that the ceramic/Ti-Al alloy composite membranes were highly stable to high temperatures in an H2 atmosphere. These results are consistent with the EDX results shown in Figure 2.
Figure 3. XRD patterns of the ceramic/Ti-Al alloy composite membrane in H2 atmosphere at different temperature for 20 h.
The results of gravimetric, gas flux, SEM, EDX, and XRD analyses show that the ceramic layer prepared by the in situ oxidation method is a promising inter-diffusion barrier for Pd/ceramic/Ti-Al alloy composite membranes.
The cross-sectional and surface SEM images of the Pd/ceramic/Ti-Al alloy composite membranes are shown in Figure 4. Figure 4A shows that the surface of the Pd membrane was not very smooth and homogeneous (mainly because of the high surface roughness of the ceramic/Ti-Al alloy support); however, no pinholes or cracks were observed. Although the images show smaller areas of the membranes, the gas leak test results further confirmed that the membranes had no defects at room temperature. Figure 4B shows that the thickness of the Pd membranes was uniform and was ~11–14 μm, which is consistent with the value determined by the gravimetric method (average thickness = ~ 13 μm).
Figure 4. (A) Surface. (B) Cross-section. SEM photographs of the Pd/ceramic/Ti-Al alloy composite membrane.
Single gas permeation is an effective and simple method to measure the N2 and H2 permeation of palladium composite membranes. The pressure dependence of the hydrogen flux of the Pd composite membranes at various temperatures is shown in Figure 5. The H2 permeation flux increased with an increase in the pressure difference . The temperature also had an obvious effect on the H2 permeation flux. These phenomena can be caused by the solution-diffusion mechanism.
Figure 5. The dependence of hydrogen flux of Pd/ceramic/Ti-Al alloy composite membrane on - at various temperatures.
Figure 6 shows the H2/N2 selectivity of the Pd composite membranes at different pressure and temperature. The results show that the selectivity increased with an increase in the temperature from 673–773 K. The H2/ N2 selectivity was found to be within the range of 200–700 under the operating conditions. This can be attributed to the thin Pd layers and the high surface roughness of the support.
Table 3 shows a comparison of the membranes prepared in this study with those reported previously. The previously reported membranes had a thickness of ~20 μm and a hydrogen permeance coefficient of ~10−3-10−4 mol m−2 s−1 Pa−0.5. On the other hand, the hydrogen permeance coefficient of the membranes prepared in this study was of the order of 10−3 mol m−2 s−1 Pa−0.5. Hence, the selectivity of these membranes should be improved further.
Activation energy (E) is another critical parameter affecting the membrane permeability. The relationship between the hydrogen permeance of membranes and temperature can be shown by the Arrhenius equation as:
The Arrhenius relation between temperature and the hydrogen permeance is shown in Figure 7. The average activation energy for H2 permeation of the palladium composite membranes was calculated to be 13.86 kJ·mol−1 from 673–773 K, which is in agreement with the previously reported value. Table 4 lists the apparent activation energy of various membranes. These apparent activation energies were quite dispersed, due to various factors such as temperature, pressure, membrane structure, and other factors. Although the thicknesses of the Pd membranes were similar, different Pd membranes had different compositions, physical and chemical structures, and apparent activation energies.
The long-term stability of Pd composite membranes is crucial for practical applications. To investigate the effect of temperature variations on the H2 permeation of the composite membranes, temperature cycling was performed. Figures 8–10 show the hydrogen flux, nitrogen flux, and H2/N2 selectivity of the Pd/ceramic/Ti-Al composite membranes operating in three heat cycles of 673 K → 723 K → 773 K → 723 K → 673 K(at ΔP = 0.1 MPa). Under the same operating conditions, the H2 flux, the N2 flux, and H2/N2 selectivity of the Pd/ceramic/Ti-Al composite membranes showed no significant changes during the three heat cycles from 673–773 K, indicating that the Pd/ceramic/Ti-Al composite membranes possessed good thermal stability. This also shows that the ceramic layers were stable and could effectively avoid the inter-diffusion of metals.
Figure 8. Variation of the hydrogen flux of Pd composite membrane during thermal cycling (ΔP = 0.1 MPa).
Figure 9. Variation of the nitrogen flux of Pd composite membrane during thermal cycling (ΔP = 0.1 MPa).
Figure 10. Variation of the H2/N2 selectivity of Pd composite membrane during thermal cycling (ΔP = 0.1 MPa).
Ceramic membranes fabricated on porous Ti-Al alloy supports by an in situ oxidation method were used as the barrier layer between a palladium layer and a Ti-Al alloy disc to avoid intermetallic diffusion. The stabilities of the ceramic/Ti-Al alloy at high temperature were investigated in an H2 atmosphere, using gravimetric analysis, gas flux measurements, SEM, EDX, and XRD. The results showed that the thickness, pore size, and microscopy structure of the ceramic membrane were stable, even after heat treatment for 20 h at temperatures ranging from 773–973 K in an H2 atmosphere. This suggested that these ceramic layers are promising inter-diffusion barriers. Pd membranes were prepared on the ceramic/Ti-Al alloy substrates by using the electroless plating method. The average thickness and permeability of the membranes were ~13 μm and 2.13 × 10−3 mol m−2 s−1 Pa−0.5, respectively. The activation energy for H2 permeation was 13.86 kJ·mol−1 from 673–773 K. Heat cycling was performed to examine the stability of the composite membranes. The H2 flux, N2 flux, and H2/N2 selectivity of the membranes showed no observable changes after three heat cycles from 673–773 K, indicating that the Pd composite membranes had good thermal stability.
All datasets generated for this study are included in the article/supplementary material.
DZ and YF: conceptualization. JZ: data curation. PY: investigation. YC and JZ: methodology. DZ: writing and editing. All authors have read and agreed to the published version of the manuscript.
This work was supported by the National Nature Science Foundation of China (No. 21206065; No. 21666018).
The authors declare that the research was conducted in the absence of any commercial or financial relationships that could be construed as a potential conflict of interest.
The reviewer YJ declared a shared affiliation, though no other collaboration, with one of the authors YF to the handling editor.
Alique, D., Imperatore, M., Sanz, R., Calles, J. A., and Baschetti, M. G. (2016). Hydrogen permeation in composite Pd-membranes prepared by conventional electroless plating and electroless pore-plating alternatives over ceramic and metallic supports. Int. J. Hydrog. Energy 41, 19430–19438. doi: 10.1016/j.ijhydene.2016.06.128
Bosko, M. L., Ojeda, F., Lombardo, E. A., and Cornaglia, L. M. (2009). NaA zeolite as an effective diffusion barrier in composite Pd/PSS membranes. J. Membr. Sci. 331, 57–65. doi: 10.1016/j.memsci.2009.01.005
Dittmeyer, R., Höllein, V., and Daub, K. (2001). Membrane reactors for hydrogenation and dehydrogenation processes based on supported palladium. J. Mol. Catal. A Chem. 173, 135–184. doi: 10.1016/S1381-1169(01)00149-2
He, Y. H., Jiang, Y., Xu, N. P., Zou, J., Huang, B. Y., Liu, C. T., et al. (2007). Fabrication of Ti-Al micro/nanometer-sized porous alloys through the kirkendall effect. Adv. Mater. 19, 2012–2016. doi: 10.1002/adma.200602398
Huang, Y., and Dittmeyer, R. (2006). Preparation and characterization of composite Pd membranes on sinter-metal support with ceramic barrier against intermetallic diffusion. J. Membr. Sci. 282, 296–310. doi: 10.1016/j.memsci.2006.05.032
Jung, S. H., Kusakabe, K., Morooka, S., and Sang-Done, K. (2000). Effects of co-existing hydrocarbons on hydrogen permeation through a palladium membrane. J. Membr. Sci. 170, 53–60. doi: 10.1016/S0376-7388(99)00357-9
Keuler, J., Lorenzen, L., and Miachon, S. (2002). Preparing and testing Pd films of thickness 1-2 micrometer with high selectivity and high hydrogen permeance. Sep. Purif. Technol. 37, 379–402. doi: 10.1081/SS-120000794
Lemus, R. G., and Duart, M. M. J. (2010). Updated hydrogen production costs and parities for conventional and renewable technologies. Int. J. Hydrog. Energy 35, 3929–3936. doi: 10.1016/j.ijhydene.2010.02.034
Li, A. W., Grace, J. R., and Lima, C. J. (2007). Preparation of thin Pd-based composite membrane on planar metallic substrate: part II. preparation of membranes by electroless plating and characterization. J. Membr. Sci. 306, 159–165. doi: 10.1016/j.memsci.2007.08.042
Ma, L., Hao, X. D., and Sun, Y. (2007). Preparation of Ti-Al alloy sheet by electron beam physical vapor deposition. Trans. Nonferrous Met. Soc. China 17, 477–481.
Mardilovich, P. P., She, Y., Ma, Y. H., and Min-Hon, R. (1998). Defect-free palladium membranes on porous stainless steel support. AICHE J. 44, 310–322. doi: 10.1002/aic.690440209
Rothenbergera, K. S., Cuginia, A. V., Howarda, B. H., Killmeyer, R. P., Ciocco, B M. V, Morreale, D., et al. (2004). High pressure hydrogen permeance of porous stainless steel coated with a thin palladium film via electroless plating. J. Membr. Sci. 244, 55–68. doi: 10.1016/j.memsci.2004.06.036
Sengodan, S., Lan, R., Humphreys, J., Du, D., Xu, W., Wang, H., et al. (2018). Advances in reforming and partial oxidation of hydrocarbons for hydrogen production and fuel cell applications. Renew. Sust. Energy Rev. 82, 761–780. doi: 10.1016/j.rser.2017.09.071
Shu, J., Grandjean, B. P. A., Ghali, E., and Kaliaguine, S. (1993). Simultaneous deposition of Pd and Ag on porous stainless steel by electroless plating. J. Membr. Sci.77, 181–195. doi: 10.1016/0376-7388(93)85068-8
Tong, J. H., Matsumura, Y., and Suda, H. (2005). Thin and dense Pd/CeO2/MPSS composite membrane for hydrogen separation and steam reforming of methane. Sep. Purif. Technol. 46, 1–10. doi: 10.1016/j.seppur.2005.03.011
Vesborg, P. C., Seger, B., and Chorkendorff, I. (2015). Recent development in hydrogen evolution reaction catalysts and their practical implementation. J. Phys. Chem. 6, 951–957. doi: 10.1021/acs.jpclett.5b00306
Wu, L. Q., Xu, N. P., and Shi, J. (2000). Preparation of a palladium composite membrane by an improved electroless plating technique. Ind. Eng. Chem. Res. 39, 342–348. doi: 10.1021/ie9904697
Zahedia, M., Afraa, B., Dehghani-Mobarakea, M., and Bahmani, M. (2009). Preparation of a Pd membrane on a WO3 modified porous stainless steel for hydrogen separatio. J. Membr. Sci. 333, 45–49. doi: 10.1016/j.memsci.2009.01.053
Zhang, D. Q., Fan, Y. Q., Xu, N. P., and He, Y. H. (2011). Effect of intermetallic diffusion between Pd and Ti-Al alloy on the performance of Pd/Ti-Al alloy composite membranes. J. Membr. Sci. 377, 221–230. doi: 10.1016/j.memsci.2011.04.052
Zhang, D. Q., Wu, J. Y., Li, B., and Fan, Y. Q. (2015). Preparation of ceramic membranes on Ti-Al alloy supports by an in-situ oxidation method. J. Membr. Sci. 476, 554–560. doi: 10.1016/j.memsci.2014.10.053
Zhang, D. Q., Zhou, S. Y., Fan, Y. Q., Xu, N. P., and He, Y. H. (2012). Preparation of dense Pd composite membranes on porous Ti-Al alloy support by electroless plating. J. Membr. Sci. 387–388, 24–29. doi: 10.1016/j.memsci.2011.10.004
Zhang, J., Xu, H. Y., and Li, W. Z. (2006). High-purity COx-free H2 generation from NH3 via the ultra permeable and highly selectivity Pd membranes. J. Membr. Sci. 277, 85–93. doi: 10.1016/j.memsci.2005.10.014
Keywords: in situ oxidation, Ti-Al alloy, ceramic, Pd composite membrane, hydrogen separation
Citation: Zhang D, Zhao J, Yang P, Chen Y and Fan Y (2020) Preparation of High Stability Pd/Ceramic/Ti-Al Alloy Composite Membranes by Electroless Plating. Front. Chem. 8:202. doi: 10.3389/fchem.2020.00202
Received: 09 November 2019; Accepted: 04 March 2020;
Published: 07 April 2020.
Edited by:
Shuaifei Zhao, Deakin University, AustraliaReviewed by:
Gaofeng Zeng, Shanghai Advanced Research Institute (CAS), ChinaCopyright © 2020 Zhang, Zhao, Yang, Chen and Fan. This is an open-access article distributed under the terms of the Creative Commons Attribution License (CC BY). The use, distribution or reproduction in other forums is permitted, provided the original author(s) and the copyright owner(s) are credited and that the original publication in this journal is cited, in accordance with accepted academic practice. No use, distribution or reproduction is permitted which does not comply with these terms.
*Correspondence: Dongqiang Zhang, emhhbmdkcUBsdXQuY24=
Disclaimer: All claims expressed in this article are solely those of the authors and do not necessarily represent those of their affiliated organizations, or those of the publisher, the editors and the reviewers. Any product that may be evaluated in this article or claim that may be made by its manufacturer is not guaranteed or endorsed by the publisher.
Research integrity at Frontiers
Learn more about the work of our research integrity team to safeguard the quality of each article we publish.