- 1Institute of Multiphase Flows, Hamburg University of Technology, Hamburg, Germany
- 2Late Stage USP Development, Bioprocess Development Biologicals, Boehringer Ingelheim Pharma GmbH & Co., KG, Biberach, Germany
- 3Development Operations Biologicals, HP BioP L&I, Boehringer Ingelheim Pharma GmbH & Co., KG, Biberach, Germany
Aerated stirred tank reactors are widely used in bio-process engineering and pharmaceutical industries. To supply the organisms with oxygen and control the pH value, oxygen is transferred from air bubbles into the liquid phase, and, at the same time, carbon dioxide is stripped from the liquid phase with the same gas bubbles. The volumetric mass transfer coefficients for oxygen and carbon dioxide are, therefore, of crucial importance for the design and scale-up of aerated stirred tank reactors. In this experimental work, the volumetric mass transfer coefficients for oxygen and carbon dioxide are investigated simultaneously to study their mutual influence. The mass transfer performance for oxygen and carbon dioxide is conducted in stirred tank reactors on the 3 L laboratory scale, 30 L pilot scale, and 15,000 L production scale. First, the influence of dissolved carbon dioxide on the oxygen mass transfer performance is investigated in a 30 L pilot scale stirred tank reactor. The results show that the volumetric mass transfer coefficient of oxygen is not affected by the concentration of dissolved carbon dioxide, but the total mass flux of oxygen decreases with increasing carbon dioxide concentration due to the decreasing partial pressure difference. With rising gassing rate and volumetric power input, both mass transfer coefficients for oxygen and carbon dioxide show the same increasing trend. Although this trend can also be observed when scaling down to the 3 L laboratory scale reactor, a significantly different effect must be considered for the scale-up to the 15,000 L industrial scale reactor. The limited absorption capacity for carbon dioxide of the gas bubbles during the long residence time in the industrial scale reactor is noticeable here, which is why the specific interfacial area is of negligible importance. This effect is used to develop a method for independent control of oxygen and carbon dioxide mass transfer performance on an industrial scale and to increase the mass transfer performance for carbon dioxide by up to 25%.
1 Introduction
In bio-process engineering and pharmaceutical industries, the production of biologicals in high-density mammalian cell cultures is of great relevance (Matsunaga et al., 2009a). The cultivation of those cells is performed under aerobic conditions in aerated bioreactors. In order to sustain cellular metabolism and growth, an ideal supply of nutrients and dissolved oxygen must be ensured (Garcia-Ochoa and Gomez, 2009). Considering that most cells are able to retain nutrients, but only a small amount of dissolved oxygen is available at ambient pressure, oxygen is generally the limiting component (Eibl et al., 2009). Therefore, air or even pure oxygen is continuously supplied during the process to be transferred from the gaseous phase into the liquid phase. Simultaneously, carbon dioxide produced by cellular metabolism must be removed from the system by transfer from the liquid phase into the gaseous phase. If carbon dioxide stripping is insufficient, carbon dioxide accumulates in the culture medium. This can shift the pH value, which inhibits cell growth and productivity (Hu, 2018; Baehr, 2016; Matsunaga et al., 2009b; Sieblist et al., 2011b). In addition to the bio-processes, the carbon dioxide mass transfer is a crucial parameter in improving different techniques for carbon capture (Liu et al., 2018; Hu et al., 2020; Yu et al., 2024a; b).
Bubble columns or aerated stirred tank reactors are used to ensure a high mass transfer performance during biological processes (Matsunaga et al., 2009a). Aerated stirred tank reactors (STRs) provide high flexibility regarding their range of applications in combination with utilizing multiple different impeller types that create controlled and reproducible flow conditions. In addition, good mixing of two-phase flows with short mixing times and an efficient power input can be achieved (Fitschen et al., 2019). A crucial parameter for the design, characterization, and scale-up of stirred tank reactors, as well as for describing the mass transfer performance, is the volumetric mass transfer coefficient
For high- or even ultra-high seeding density cell culture processes, the scale-up of seed trains begins in laboratory scale STRs, proceeds to the pilot scale, and culminates on the industrial scale with thousands of liters (Catapano et al., 2009; Stepper et al., 2020). However, with an increased volume, the surface-to-volume ratio is decreased, and the carbon dioxide stripping through the liquid surface and the headspace of the reactor is reduced (Matsunaga et al., 2009b; Sieblist et al., 2011a).
The objective of this article is to compare the mass transfer performance of oxygen and carbon dioxide in laboratory- and industrial scale aerated stirred tank reactors. Moreover, a method for improving carbon dioxide stripping in a stirred tank reactor on an industrial scale is presented (Schulz and Wucherpfennig, 2021). For the investigations, an acrylic glass stirred tank reactor on an industrial scale with a total volume of
2 Materials and methods
The experimental results presented in this paper are obtained in a 3 L, 30 L, or 15,000 L STR.
2.1 Theory
For stirred tank reactors, the specific power input (Equation 1) by the stirrers is defined as
which includes the power number
In a single-phase and fully baffled system, the turbulent flow regime is reached in the case at a stirrer Reynolds number of
In the case of an ideal gas and liquid phase, the concentration of dissolved gases can be determined with Henry’s law (Lohrengel, 2017; Baehr, 2016), and gas–liquid mass transfer can be described by the two-film theory (Whitman, 1923). Without the presence of mammalian cells, the mass transfer for dissolved oxygen from the gaseous into the liquid phase (Equation 2) can be calculated as
with the concentration of dissolved oxygen
with
The volumetric mass transfer coefficient
with the superficial gas velocity
2.2 Experimental setup and measurement procedure
The performed experiments can be divided into three parts. The first part, conducted in the 30 L STR (see Figure 1), is the determination of the influence of dissolved carbon dioxide on the oxygen mass transfer coefficient. Based on these results, the measuring method for the second part is defined. The second part of this work was performed in the laboratory and industrial-scale STR. During this work, the mass transfer coefficients of carbon dioxide and oxygen are determined in both systems for different power inputs and superficial gas velocities. The third part of the experiments was conducted in the industrial-size STR as an alternative sparging strategy to test the independent control of the oxygen and carbon dioxide concentration.
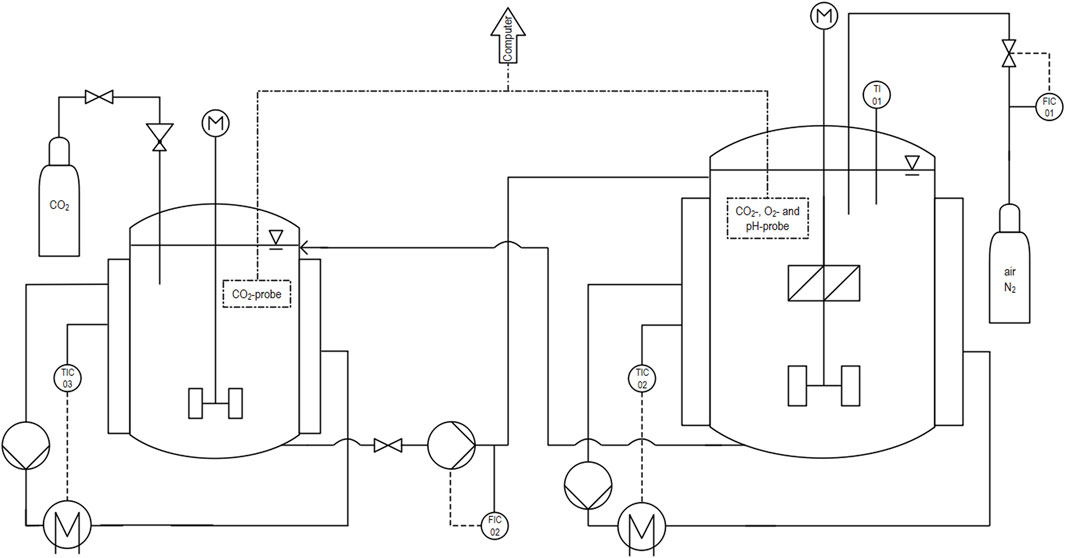
Figure 1. Process flow diagram of the experimental pilot scale setup with the connection of the 1.8-L (left) and the 30-L (right) stirred tank reactor.
The applied measuring methods are identical for all systems. To measure the concentration of dissolved oxygen
An open tube sparger (submersed sparger) is used in each system for aeration. The sparger is mounted below the stirrer, as can be seen in Figure 2, which shows an example of the laboratory setup. Mass flow controllers (Bronkhorst EL-Flow) are used to control the gas flow rates. The stirrer geometry is given in Table 1. The different stirrer spacing for the elephant ears (EE) and the combination of Rushton turbine (RT) and pitched blade (PB) is shown in Figures 2, 3. The lowest stirrer has the distance
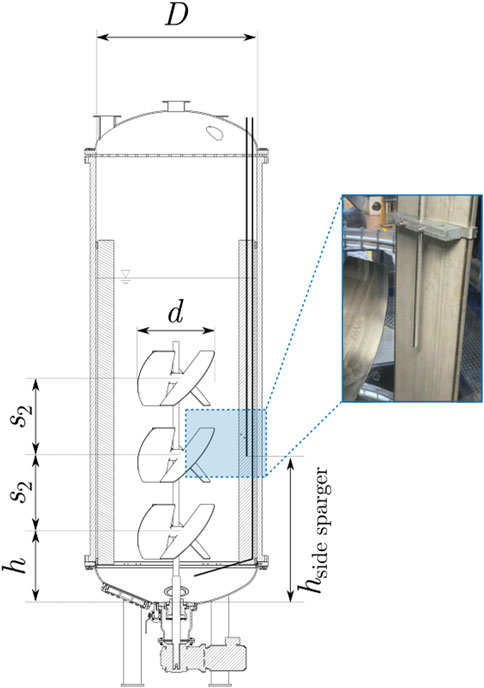
Figure 3. Schematic illustration of the stirred tank reactor on an industrial scale (15 kL STR) with the side sparger.
2.2.1 Pilot scale setup
The pilot scale reactor with a volume of 30 L is used to investigate the influence of a constant carbon dioxide concentration on the oxygen mass transfer performance. To ensure a constant carbon dioxide concentration inside of the pilot scale reactor, a 1.8 L stirred tank reactor is used to enrich the deionized water with carbon dioxide. The enriched water is subsequently pumped into the 30 L reactor by using a peristaltic pump (Ismatec ISM 405 A). A flow meter is used to control and adjust the pumping. The backflow from the 30 L reactor to the 1.8 L reactor is realized by a buoyancy-driven, siphon-like construction. The various dissolved carbon dioxide profiles between 5% and 15% of saturation concentration are simulated in the 30 L reactor by adjusting the volume flow of saturated carbon dioxide deionized water. The experiments are performed at a temperature of 20°C, which is controlled through an external heating and cooling circulator (IKA HRC 2). For the 30 L reactor, a stirrer setup consisting of an RT and a down-pumping PB is used. The 1.8 L reactor instead is only equipped with an RT as the only purpose is to enrich the deionized water with carbon dioxide. The stirrer frequency is controlled by a torque measurement instrument (HiTec Zang ViscoPakt-X7). The piping and instrumentation diagram (P&ID) of the setup is presented in Figure 1.
2.2.2 Laboratory scale setup
A glass STR with a volume of 3 L is used for the laboratory scale experiments. The geometry parameters and the stirrer combinations are displayed in Table 1. Further specifications of the stirrers and previously measured power numbers
2.2.3 Industrial scale setup
The industrial scale reactor uses an operating volume of 12.5 kL. The geometric specifications, the stirrer combinations, and further specifications, such as the previously measured power numbers
3 Experimental results
The following subsections provide the experimental results for the oxygen and carbon dioxide mass transfer performance in the stirred tank reactors on the laboratory (3 L STR), pilot (30 L STR), and industrial scales (15,000 L STR).
3.1 Influence of dissolved carbon dioxide concentration on oxygen mass transfer performance in a 30L stirred tank reactor
In Figure 4 the saturation concentration of dissolved oxygen
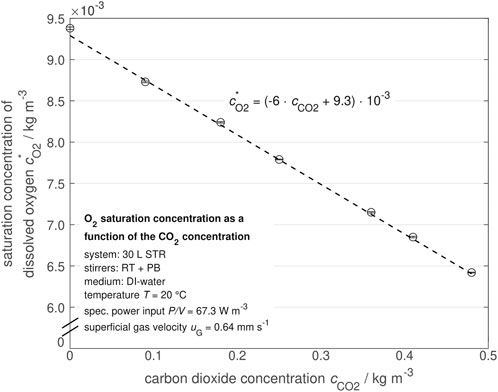
Figure 4. Saturation concentration of dissolved oxygen in dependency of the carbon dioxide concentration.
This linear dependency is determined empirically but can be explained physically. As the experiments are performed in an open system, the total pressure
For a defined saturation concentration of dissolved oxygen, the volumetric oxygen mass transfer coefficient
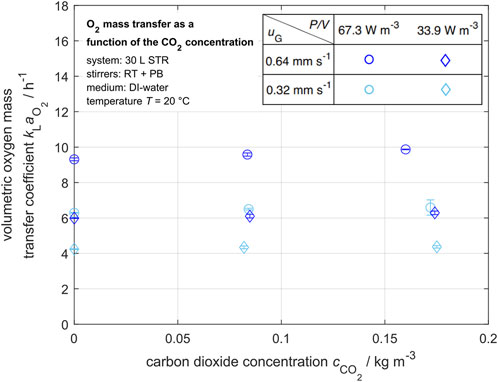
Figure 5. Volumetric oxygen mass transfer coefficient in dependency of the carbon dioxide concentration for various specific power inputs
In contrast, the volumetric oxygen mass transfer coefficient
3.2 Comparison of mass transfer performance on laboratory and industrial scales
For the stirred tank reactor on the laboratory scale (3 L STR), the determined volumetric oxygen mass transfer coefficient
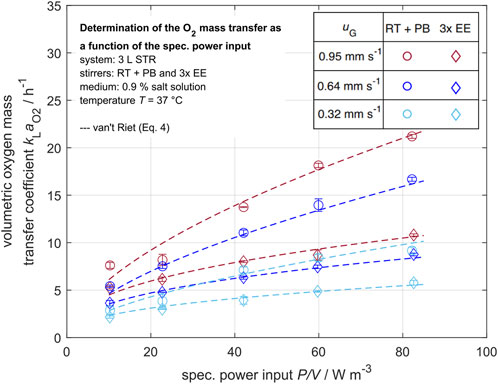
Figure 6. Volumetric oxygen mass transfer coefficient in dependency of the specific power input for various superficial gas velocities
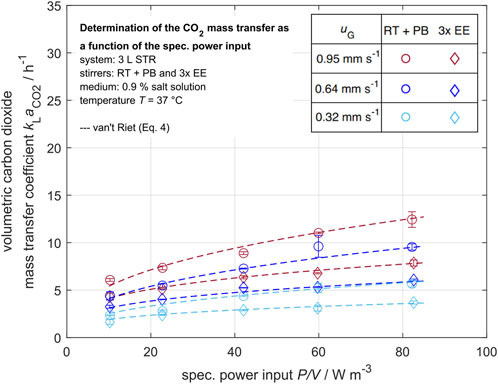
Figure 7. Volumetric carbon dioxide mass transfer coefficient in dependency of the specific power input for various superficial gas velocities
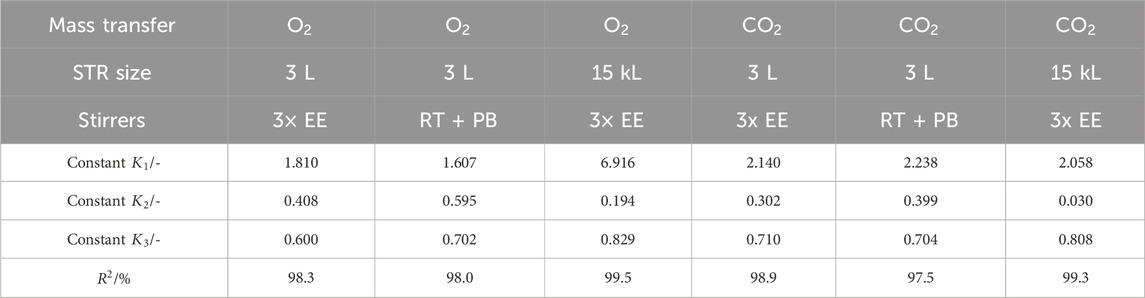
Table 2. Determined constants
As first shown in Figure 5, the volumetric mass transfer coefficients increase with rising specific power input and superficial gas velocity. This trend is observed to be stronger for oxygen than for carbon dioxide. For the superficial gas velocity of
For the stirred tank reactor on the industrial scale (15 kL STR) with three EE stirrers, the determined volumetric mass transfer coefficient of oxygen
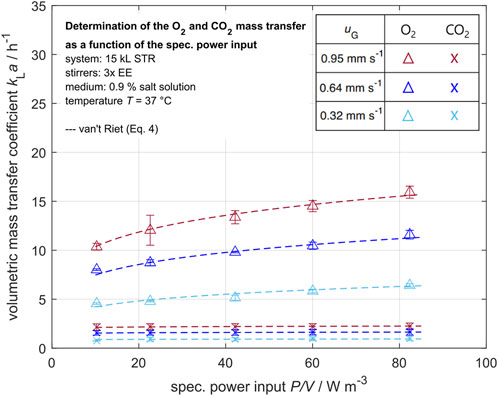
Figure 8. Volumetric mass transfer coefficients of oxygen and carbon dioxide in dependency of the specific power input for various superficial gas velocities
The determined volumetric oxygen mass transfer coefficients
The oxygen mass transfer coefficient outliers that can be seen in the data may be caused by changing ambient pressure, as the solubility of oxygen in water is highly pressure dependent. As the probes measure only locally, a certain error due to nonstationary effects is possible. Overall, the results are in good accordance with the van’t Riet correlation (van’t Riet, 1979).
To compare the carbon dioxide mass transfer performance of the laboratory and the industrial scale STR, the normalized volumetric carbon dioxide mass transfer coefficients
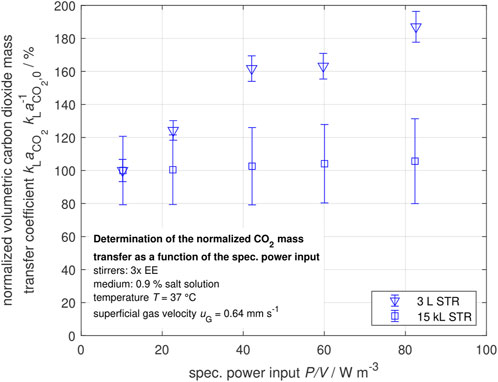
Figure 9. Normalized volumetric carbon dioxide mass transfer coefficient in dependency of the specific power input for a constant superficial gas velocity
Figure 9 indicates that the carbon dioxide mass transfer performance in the laboratory scale STR can be improved up to 80% in the investigated operation parameter range by increasing the specific power input
The carbon dioxide mass transfer performance seems to be independent of the power input. It can be seen that the gas bubbles are rapidly saturated by carbon dioxide. In this case, an increased specific surface area due to an increased power input would have no influence on the carbon dioxide stripping (Sieblist et al., 2011b; Xing et al., 2017; Xu et al., 2017). This highlights the difficulties in scaling up from the laboratory to the industrial scale while accounting for mass transfer due to the saturation of rising gas bubbles through carbon dioxide. This is in good accordance with the effects observed by Mostafa and Gu (2003) and Garnier et al. (1996) in industrial-size STRs, who found a strong impact of the aeration rate on the carbon dioxide mass transfer. Therefore, a different approach is needed to improve the carbon dioxide mass transfer performance. In the following section, the influence of higher superficial gas velocities, injected as side aeration, on the carbon dioxide mass transfer performance is discussed.
3.3 Independent control of mass transfer performance for oxygen and carbon dioxide by using side aeration on an industrial scale
Additional side aeration is used on an industrial scale to enhance the mass transfer performance of carbon dioxide with a reduced influence on the oxygen mass transfer performance (Schulz and Wucherpfennig, 2021). The sparger for the side aeration and its arrangement can be seen in Figure 3.
In Figure 10, the normalized volumetric mass transfer coefficients
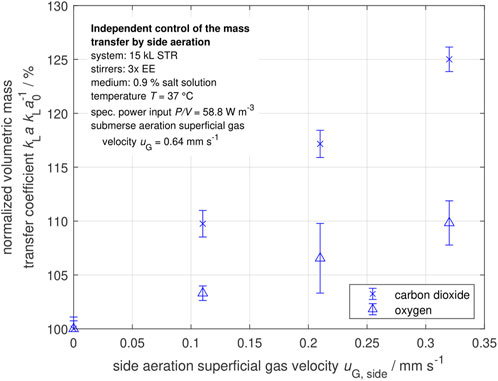
Figure 10. Normalized volumetric mass transfer coefficients of oxygen and carbon dioxide in dependency of the side aeration superficial gas velocity for a constant specific power input
With increased side aeration superficial gas velocity, the volumetric oxygen mass transfer coefficient has a slight increase of +9.8% in the investigated range. At the same time, the volumetric carbon dioxide mass transfer coefficient increases up to 25.0%. With the side aeration, large gas bubbles enter the system with a smaller specific surface area and a larger volume than the small gas bubbles from the submersed aeration. As carbon dioxide is well-soluble in water (molar Henry coefficient of
4 Conclusion
In this work, the mass transfer performance of oxygen and carbon dioxide are experimentally investigated in an aqueous salt solution by analyzing the volumetric mass transfer coefficients in STRs on various scales. For the simultaneous analysis, the volumetric oxygen mass transfer coefficient is investigated from the gaseous phase into the liquid phase, and the volumetric carbon dioxide mass transfer coefficient is investigated from the liquid phase into the gaseous phase for varying power inputs and superficial gas velocities. In the pilot-scale STR, the volumetric oxygen mass transfer coefficient remains constant and is not dependent on the dissolved carbon dioxide concentration for the investigated range.
The determined mass transfer performance of oxygen and carbon dioxide on the laboratory scale STR shows that the volumetric mass transfer coefficient has a comparable trend within the operating parameters. This is not transferable to the industrial scale STR. In this case, the volumetric carbon dioxide mass transfer coefficient cannot be significantly improved by an increased power input because carbon dioxide accumulates within the gas bubbles. Therefore, an easy scale-up of the carbon dioxide mass transfer performance is an open challenge for future research. This effect is utilized to develop and test a method for the industrial scale stirred tank reactor to enhance the mass transfer performance of carbon dioxide independently from the oxygen mass transfer by using additional side aeration. Due to the side aeration, the volumetric oxygen mass transfer coefficient increases only slightly, while the volumetric carbon dioxide mass transfer coefficient shows a more significant increase with a maximum of +25.0%. This method enables more independent control of the oxygen and carbon dioxide concentrations in industrial scale STR and, thus, more reliable scaling and processes.
The insights gathered for aerated STRs can be transferred to other fields like the chemical industry or carbon capture technologies. To improve the knowledge of the carbon dioxide mass transfer in aerated STRs, further experiments, such as the measurement of concentration profiles within the gaseous phase over the reactor height, will be performed to enable more detailed modeling.
Data availability statement
The raw data supporting the conclusions of this article will be made available by the authors, without undue reservation.
Author contributions
NN: visualization, writing–original draft, writing–review and editing, formal analysis, and investigation. JF: conceptualization, methodology, writing–review and editing, formal analysis, and project administration. IH: conceptualization, data curation, formal analysis, investigation, methodology, visualization, and writing–original draft. MK: project administration and writing–review and editing. TS: conceptualization, methodology, and writing–review and editing. TW: conceptualization, funding acquisition, methodology, project administration, and writing–review and editing. MS: conceptualization, funding acquisition, project administration, supervision, and writing–review and editing.
Funding
The author(s) declare that financial support was received for the research, authorship, and/or publication of this article. The authors gratefully acknowledge the company Boehringer Ingelheim Pharma GmbH & Co. KG for its financial support in conducting the presented research work.
Acknowledgments
In particular, the authors would like to thank their students Helena Ostrinksy and Jakob Schulze. Publishing fees were supported by the Funding Programme Open Access Publishing of Hamburg University of Technology (TUHH).
Conflict of interest
Authors JF, MK, TS, and TW were employed by Boehringer Ingelheim Pharma GmbH & Co., KG.
The authors declare that this study received funding from Boehringer Ingelheim Pharma GmbH & Co. KG. The funder had the following involvement in the study: Dr. Jürgen Fitschen was a former PhD student at the TUHH and was involved in the planning and measuring phase of the study. Experiments were discussed upfront with the funder.
Publisher’s note
All claims expressed in this article are solely those of the authors and do not necessarily represent those of their affiliated organizations, or those of the publisher, the editors, and the reviewers. Any product that may be evaluated in this article, or claim that may be made by its manufacturer, is not guaranteed or endorsed by the publisher.
References
Baehr, H. D. (2016). Thermodynamik: Grundlagen und technische Anwendungen. Berlin Heidelberg: Springer Vieweg, 16. aktualiiserte auflage edn.
Benz, G. T. (2021). Agitator design for gas–liquid fermenters and bioreactors. first edn. Wiley. doi:10.1002/9781119650546
Bernemann, V., Fitschen, J., Leupold, M., Scheibenbogen, K.-H., Maly, M., Hoffmann, M., et al. (2024). Characterization data for the establishment of scale-up and process transfer strategies between stainless steel and single-use bioreactors. MDPI Fluids 9, 115. doi:10.3390/fluids9050115
Bouaifi, M., Hebrard, G., Bastoul, D., and Roustan, M. (2001). A comparative study of gas hold-up, bubble size, interfacial area and mass transfer coefficients in stirred gas-liquid reactors and bubble columns. Chem. Eng. Process. 40, 97–111. doi:10.1016/s0255-2701(00)00129-x
Boyd, C. E. (2020). “Water quality: an introduction,” in Springer eBooks earth and environmental science. 3rd ed. Cham: Springer.
Catapano, G., Czermak, P., Eibl, R., Eibl, D., and Pörtner, R. (2009). “Bioreactor design and scale-up,” in Cell and tissue reaction engineering (Springer), 173–259.
Eibl, R., Eibl, D., Pörtner, R., Catapano, G., and Czermak, P. (2009). “Cell and tissue reaction engineering: with a contribution by martin fussenegger and wilfried weber,” in Principles and practice. Springer. doi:10.1007/978-3-540-68182-3
Fitschen, J., Bernemann, V., Haase, I., and Hofmann, S. (2023). Gitlab Repository: determintation of volumetric mass transfer coefficient in STR.
Fitschen, J., Maly, M., Rosseburg, A., Wutz, J., Wucherpfennig, T., and Schlüter, M. (2019). Influence of spacing of multiple impellers on power input in an industrial-scale aerated stirred tank reactor. Chem. Ing. Tech. 91, 1794–1801. doi:10.1002/cite.201900121
Gabelle, J.-C., Augier, F., Carvalho, A., Rousset, R., and Morchain, J. (2011). Effect of tank size on kla and mixing time in aerated stirred reactors with non-Newtonian fluids. Can. J. Chem. Eng. 89, 1139–1153. doi:10.1002/cjce.20571
Garcia-Ochoa, F., and Gomez, E. (2009). Bioreactor scale-up and oxygen transfer rate in microbial processes: an overview. Biotechnol. Adv. 27, 153–176. Citation Status MEDLINE. doi:10.1016/j.biotechadv.2008.10.006
Garnier, A., Voyer, R., Tom, R., Perret, S., Jardin, B., and Kamen, A. (1996). Dissolved carbon dioxide accumulation in a large scale and high density production of TGF receptor with baculovirus infected Sf-9 cells 22. Cytotechnology 22, 53–63. doi:10.1007/BF00353924
Hu, W.-S. (2018). “Includes bibliographical references and index,” in Engineering principles in biotechnology. Hoboken, NJ, USA Chichester, West Sussex: Wiley.
Hu, X. E., Liu, L., Luo, X., Xiao, G., Shiko, E., Zhang, R., et al. (2020). A review of N-functionalized solid adsorbents for post-combustion CO2 capture. Appl. Energy 260, 114244. doi:10.1016/j.apenergy.2019.114244
Klamt, A. (1995). Conductor-like screening model for real solvents: a new approach to the quantitative calculation of solvation phenomena. J. Phys. Chem. 99, 2224–2235. doi:10.1021/j100007a062
Knoll, A., Maier, B., Tscherrig, H., and Büchs, J. (2005). The oxygen mass transfer, carbon dioxide inhibition, heat removal, and the energy and cost efficiencies of high pressure fermentation. Adv. Biochem. Engineering/Biotechnology 92, 77–99. doi:10.1007/b98918
Kraume, M. (2020). Transportvorgänge in der Verfahrenstechnik: Grundlagen und apparative Umsetzungen. auflage edn. Berlin Heidelberg: Springer Lehrbuch, 3.
Liu, L., Chen, H., Shiko, E., Fan, X., Zhou, Y., Zhang, G., et al. (2018). Low-cost DETA impregnation of acid-activated sepiolite for CO2 capture. Chem. Eng. J. 353, 940–948. doi:10.1016/j.cej.2018.07.086
Lohrengel, B. (2017). “Thermische Trennverfahren: Trennung von Gas-Dampf- und Flüssigkeitsgemischen,”, 3. Berlin Boston: De Gruyter Oldenbourg. , durchgesehene und bibliografisch ergänzte ausgabe edn. doi:10.1515/9783110473223
Matsunaga, N., Kano, K., Maki, Y., and Dobashi, T. (2009a). Estimation of dissolved carbon dioxide stripping in a large bioreactor using model medium. J. Biosci. Bioeng. 107, 419–424. doi:10.1016/j.jbiosc.2008.11.017
Matsunaga, N., Kano, K., Maki, Y., and Dobashi, T. (2009b). Culture scale-up studies as seen from the viewpoint of oxygen supply and dissolved carbon dioxide stripping. J. Biosci. Bioeng. 107, 412–418. doi:10.1016/j.jbiosc.2008.12.016
Montgomery, H. A. C., Thom, N. S., and Cockburn, A. (1964). Determination of dissolved oxygen by the winkler method and the solubility of oxygen in pure water and sea water. J. Appl. Chem. 14, 280–296. doi:10.1002/jctb.5010140704
Mostafa, S. S., and Gu, X. S. (2003). Strategies for improved dCO2 removal in large-scale fed-batch cultures. Biotechnol. Prog. 19, 45–51. doi:10.1021/bp0256263
Paul, E. L., Atiemo-Obeng, V. A., and Kresta, S. M. (2004). in Handbook of industrial mixing: science and practice (Hoboken, NJ, USA: Wiley-Interscience).
Royce, P. N. C., and Thornhill, N. F. (1991). Estimation of dissolved carbon dioxide concentrations in aerobic fermentations. AIChE J. 37, 1680–1686. doi:10.1002/aic.690371111
Schulz, T. W., and Wucherpfennig, T. (2021). Bioreactor or fermenter for the culturing of cells or microorganisms in suspension in industrial scale.
Sieblist, C., Hägeholz, O., Aehle, M., Jenzsch, M., Pohlscheidt, M., and Lübbert, A. (2011a). Insights into large-scale cell-culture reactors: II. Gas-phase mixing and CO2 stripping. Biotechnol. J. 6, 1547–1556. doi:10.1002/biot.201100153
Sieblist, C., Jenzsch, M., Pohlscheidt, M., and Lübbert, A. (2011b). Insights into large-scale cell-culture reactors: I. Liquid mixing and oxygen supply. Biotechnol. J. 6, 1532–1546. doi:10.1002/biot.201000408
Simmons, M., Zhu, H., Bujalski, W., Hewitt, C., and Nienow, A. (2007). Mixing in a model bioreactor using agitators with a high solidity ratio and deep blades. Chem. Eng. Res. Des. 85, 551–559. doi:10.1205/cherd06157
Stepper, L., Filser, F. A., Fischer, S., Schaub, J., Gorr, I., and Voges, R. (2020). Pre-stage perfusion and ultra-high seeding cell density in CHO fed-batch culture: a case study for process intensification guided by systems biotechnology. Bioprocess Biosyst. Eng. 43, 1431–1443. doi:10.1007/s00449-020-02337-1
Van’t Riet, K. (1979). Review of measuring methods and results in nonviscous gas-liquid mass transfer in stirred vessels. Industrial & Eng. Chem. Process Des. Dev. 18, 357–364. doi:10.1021/i260071a001
VDI (2013). Wärmeatlas: mit 320 Tabellen. VDI-Buch Berlin u.a., 11. Springer Vieweg.bearb. und erw. aufl. edn.
Whitman, W. G. (1923). The two-film theory of gas absorption. Chem. Metall. Eng. 29, 146–148. doi:10.1016/0017-9310(62)90032-7
Xing, Z., Lewis, A. M., Borys, M. C., and Li, Z. J. (2017). A carbon dioxide stripping model for mammalian cell culture in manufacturing scale bioreactors. Biotechnol. Bioeng. 114, 1184–1194. doi:10.1002/bit.26232
Xu, S., Hoshan, L., Jiang, R., Gupta, B., Brodean, E., O’Neill, K., et al. (2017). A practical approach in bioreactor scale-up and process transfer using a combination of constant P/V and vvm as the criterion. Biotechnol. Prog. 33, 1146–1159. doi:10.1002/btpr.2489
Yu, C., Ling, H., Cao, W., Deng, F., Zhao, Y., Cao, D., et al. (2024a). Revealing the potential of cyclic amine morpholine (MOR) for CO2 capture through a comprehensive evaluation framework and rapid screening experiments. Chem. Eng. J. 495, 153402. doi:10.1016/j.cej.2024.153402
Yu, C., Ling, H., Shen, Z., Yang, H., Cao, D., and Hu, X. (2024b). A general model for prediction of the 2 equilibrium solubility in aqueous tertiary amine systems. Syst. n/a 70, e18551. doi:10.1002/aic.18551
Keywords: mass transfer performance, volumetric mass transfer coefficient of oxygen and carbon dioxide, carbon dioxide stripping, stirred tank reactor, experimental results
Citation: Nickel N, Fitschen J, Haase I, Kuschel M, Schulz TW, Wucherpfennig T and Schlüter M (2024) Novel sparging strategies to enhance dissolved carbon dioxide stripping in industrial scale stirred tank reactors. Front. Chem. Eng. 6:1470991. doi: 10.3389/fceng.2024.1470991
Received: 26 July 2024; Accepted: 17 October 2024;
Published: 15 November 2024.
Edited by:
Ioannis Papantoniou, KU Leuven, BelgiumReviewed by:
Xiayi (Eric) Hu, Xiangtan University, ChinaFrancesco Bianco, University of Cassino, Italy
Copyright © 2024 Nickel, Fitschen, Haase, Kuschel, Schulz, Wucherpfennig and Schlüter. This is an open-access article distributed under the terms of the Creative Commons Attribution License (CC BY). The use, distribution or reproduction in other forums is permitted, provided the original author(s) and the copyright owner(s) are credited and that the original publication in this journal is cited, in accordance with accepted academic practice. No use, distribution or reproduction is permitted which does not comply with these terms.
*Correspondence: Nicolas Nickel, bmljb2xhcy5uaWNrZWxAdHVoaC5kZQ==