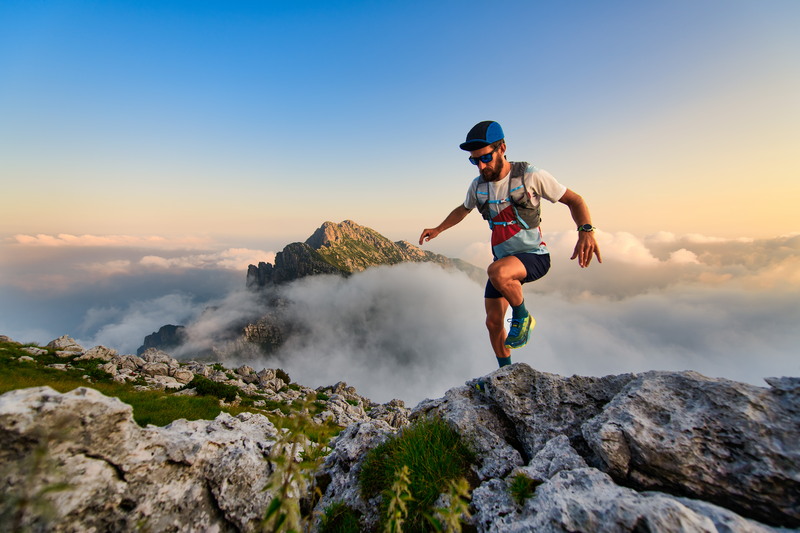
95% of researchers rate our articles as excellent or good
Learn more about the work of our research integrity team to safeguard the quality of each article we publish.
Find out more
ORIGINAL RESEARCH article
Front. Chem. Eng. , 13 September 2024
Sec. Sustainable Process Engineering
Volume 6 - 2024 | https://doi.org/10.3389/fceng.2024.1463638
This article is part of the Research Topic Catalytic Conversion of Waste Plastics into Valuable Products View all articles
In order to deal with legacy additives in plastic waste streams, multiple extraction processes are being developed. For sustainability and economic reasons, these processes call for the parallel implementation of revalorisation routes for the extracted toxic compounds, especially when dealing with large volumes as in the case of phthalate plasticizers. On account of its intrinsic value, the recovery of the aromatic fragment from such end-of-life phthalate ester mixtures was prioritized in this work. To that end, a hydrolysis-decarboxylation process was designed using hydrophobic zeolites and heterogeneous Pt-catalysts, in water as a safe and environmentally benign solvent. By carefully tuning the reaction parameters, the selective formation of phthalic acid, benzoic acid or benzene can be achieved in near-quantitative yields, next to the recovery of alkene and alcohol side chain fragments (yields up to 99%).
Phthalate plasticizers traditionally used in the plastic industry have recently been regulated by the European Chemicals Agency (ECHA) and by the United States Consumer Product Safety Commission (CPSC), due to serious concerns regarding their potential for endocrine disruption and reproductive toxicity (European Chemicals Agency, 2021; United States Consumer Product Safety Commission, 2019; Lorz et al., 2007; Groh et al., 2019). Nevertheless, these low molecular weight (LMW) phthalates are still extensively produced in emerging markets, such as Asia and Latin America (European Plasticisers, 2021). High molecular weight phthalates remain globally accepted and widely utilized, despite their obvious similarity to the aforementioned restricted plasticizers (European Plasticisers, 2021; Bocqué et al., 2016; Cadogan and Howick, 2000). The ongoing dominance of phthalate esters in the plasticizer market continues to challenge waste facilities in managing large streams of plastic waste containing these legacy additives (Pivnenko et al., 2016; Wagner and Schlummer, 2020). As a consequence, innovative recycling techniques aim to effectively extract the plasticizers from the plastic stream, ensuring that the recycled material complies with the European and American plastic legislation (LMW phthalate content may not exceed 0.1 wt%). These strategies in turn create the demand for revalorisation routes to treat the vast amounts of extracted phthalates, considering that they account for up to 40 wt% of flexible plastic products (Wagner and Schlummer, 2020; Fraunhofer IVV, 2023; Ügdüler et al., 2020; Arena and Ardolino, 2022).
Given that the diisononyl 1,2-cyclohexanedicarboxylate (DINCH) plasticizer is industrially produced via the ring hydrogenation of the corresponding virgin phthalate (i.e., diisononyl phthalate; DINP) (European Plasticisers, 2021; BASF, 2008; Brunner et al., 2001; De Munck et al., 2018; Grass et al., 2006; David et al., 2015; European Chemicals Agency, 2020; Crespo et al., 2007; Howick, 2021), the recent development of a revalorisation process capable of transforming phthalates extracted from real post-consumer plastic waste into safe DINCH-like plasticizers holds great promise (Windels et al., 2022). Nevertheless, the study also illustrates that obtaining one single, high-quality chemical from a wide battery of extracted phthalate esters is a major challenge, even with the proposed tandem transesterification-hydrogenation approach (Figure 1, top), which complicates commercialization of the obtained plasticizer mixture. Moreover, in light of the intrinsic value of aromatics, the loss of this functionality can be judged as undesirable (Bocqué et al., 2016). Taking these reflections into consideration, the main objective of this work is the catalytic conversion of end-of-life phthalate plasticizers into single, high quality aromatic products, such as phthalic acid (PA), benzoic acid (BA) or benzene (B) through a well-designed hydrolysis-decarboxylation process in water (Figure 1, bottom). First, the hydrolysis of dialkyl phthalate esters (DP) into monoalkyl phthalate (MP) and phthalic acid and primary alcohol fragments will be investigated using Brønsted-acid catalysts. Next, the decarboxylation of the generated phthalic acid will be explored using supported noble metal catalysts to selectively produce either benzoic acid or benzene. Subsequent efforts will be focused on efficient integration of both stages. Finally, the developed hydrolysis-decarboxylation strategy will be tested on legacy plasticizers extracted from plastic waste.
Figure 1. Revalorization strategies for legacy phthalate plasticizers extracted from end-of-life PVC waste: (top) Previously reported (trans)esterification-hydrogenation process yielding a mixture of DINCH-like plasticizers (Windels et al., 2022); (bottom) Current study involving the consecutive hydrolysis-decarboxylation of dialkyl phthalate esters (DP) into simple arenes, such as phthalic acid (PA), benzoic acid (BA) or benzene (B).
If successful, the proposed phthalate revalorization process could significantly reduce the amount of legacy plasticizers sent to incineration. Additionally, it has the potential to economically and sustainably support the recycling techniques that separate the plastic resin from these legacy plasticizers by producing various valuable compounds: the obtained diacid can be employed for the production of polyester resins, pigments and REACH-approved plasticizers, while benzoic acid is used in the industrial production of phenol, alkyd resins, food additives and benzoate plasticizers, amongst others (Lorz et al., 2007; European Plasticisers, 2021; Bocqué et al., 2016; Cadogan and Howick, 2000; Hillshafer et al., 2000; Zhu et al., 2002; Maki and Takeda, 2000; Opgrande et al., 2003). Besides, benzene acts as the starting material for many chemicals and plastics, which keeps the demand for the compound consequently high (Folkins, 2000). The primary alcohols obtained from the ester hydrolysis can equally usefully be exploited in the chemical industry, for example, in the production of REACH-approved plasticizers, detergents and fuels (European Plasticisers, 2021; Bocqué et al., 2016; Falbe et al., 2000). The prospect of (re-)generating REACH-approved plasticizers through additional esterification steps seems particularly intriguing as it closes the material loop.
In the first segment of this research, the double hydrolysis of dialkyl phthalate esters (DP) into phthalic acid (PA) was investigated (Table 1). Under the studied conditions (3 mmol bis(2-ethylhexyl) phthalate, DEHP; 25 mL H2O at 200 °C for 6 h), the diester exhibited a remarkable stability (<5% conversion), even when substantial amounts of homogeneous acid or base were added to the reaction mixture (Table 1, Entries 1–3) (Riemenschneider and Bolt, 2005). It is hypothesized that this arises from the very limited solubility of the organic plasticizer in the aqueous phase (Supplementary Table S2). Given the evident role of water in this reaction and the desire to avoid organic solvents, alternative heterogeneous catalysts were explored instead.
An evaluation of various Brønsted-acid zeolites was conducted (Table 1, Entries 4–13), leading to varying outcomes. For instance, aluminosilicates with too small pore sizes and/or a low Si/Al ratio (which suggests that their surface is rather hydrophilic) appear incapable of promoting the hydrolysis of the bulky and relatively apolar dioctyl phthalate ester (Table 1, Entries 4–8). In contrast, hydrophobic H-Y and H-Beta zeolites with high Si/Al ratios demonstrate enhanced hydrolysis rates, with PA yields up to 31% after 6 h (Table 1, Entries 9–13). Through the extension of the reaction time and/or an increase of the catalyst loading, complete phthalate conversion and quantitative yields of PA could be realized with both H-Y 40 and H-Beta 75 (Table 1, Entries 14–16). Remarkably, the intermediate monoalkyl phthalate (MP) was hardly detected during these experiments, implying a swift conversion of the second ester functionality once the bulky plasticizer molecule has made contact with the zeolite surface. In addition to promoting the hydrolysis of the phthalate ester bonds, these Brønsted-acid zeolites also catalyze the dehydration of the alcohols formed under current reaction conditions. (Liu et al., 2017; Chen et al., 2021). This conversion occurs rather fast once the alcohol (e.g., 2-ethyl-1-hexanol; 2-EH) is formed on the zeolite surface, resulting in a constant and remarkably high selectivity for octenes of ±90% during the hydrolysis of DEHP (Supplementary Figure S17). In other words, complete dioctyl phthalate conversion not only yields >99% PA, but also 10% 2-ethyl-1-hexanol and 90% isomeric octenes.
For the above-mentioned zeolite structures, stability issues have previously been reported when used in hot liquid water (Stuyck et al., 2020; Heard et al., 2020; Ravenelle et al., 2010; Ennaert et al., 2016). Therefore, recycling experiments were conducted with the most promising H-Y and H-Beta zeolites (Figure 2). Whereas H-Y 40 experienced a substantial loss in its hydrolysis activity per cycle (±30%), the reuse of the slightly less active H-Beta 75 resulted in stable outputs across four runs. In fact, H-Beta 75 outperformed the former H-Y 40 catalyst from the first recycle run onwards, proving more suitable for application. In line with these recycling results, powder X-ray diffraction (PXRD) demonstrated the loss of crystallinity of H-Y 40, while the characterization method confirmed the structural stability of H-Beta (Supplementary Figures S15, S16). The simultaneous loss of activity and crystallinity of the spent H-Y zeolite has been linked with the hydrolysis of framework bonds, producing an amorphous structure characterized by a highly reduced pore volume and a substantial decline in number of Brønsted acid sites (Stuyck et al., 2020; Heard et al., 2020). Based on the long-term stability of H-Beta 75, this commercial zeolite was selected for the remaining hydrolysis experiments.
Figure 2. Recycling experiments of the zeolites in the hydrolysis of DEHP. Reaction conditions: DEHP (3 mmol), H2O (Vtot = 25 mL), defined zeolite (391 mg), 8 bar N2, 200°C for 6 h. Between runs, the spent zeolite was washed with tetrahydrofuran and then dried at 60°C for 16 h.
In a subsequent set of experiments, several historically relevant phthalate plasticizers (diisobutyl phthalate, DIBP; dibutyl phthalate, DBP; benzylbutyl phthalate, BeBP; DEHP and DINP) were subjected to the revalorisation process (Figure 3). The double hydrolysis of LMW phthalates other than DEHP (i.e., DBP, DIBP and BeBP) proceeded smoothly, resulting in complete conversions within only 3 h of reaction time. On the other hand, the hydrolysis of DINP required prolonged reaction times (up to 28 h) in order to achieve complete plasticizer conversion and high PA yields. It appears that the hydrolysis of the phthalate plasticizers becomes progressively more challenging as the length of the hydrocarbon side chains increases. These observations can be related to the solubility of the various phthalate plasticizers: as the alkyl chain length of the esters increases, their water solubility decreases (Supplementary Table S2), and this also affects their ease of adsorption on the zeolite surface.
Figure 3. Hydrolysis of historically relevant phthalate plasticizers. Reaction conditions: Defined phthalate (3 mmol), H2O (Vtot = 25 mL), H-Beta 75 (391 mg), 8 bar N2, 200 °C for the specified time.
Next, the influence of the formed products on the hydrolysis rate was studied by adding half equivalents of an aromatic carboxylic acid (i.e., benzoic acid, BA) and of a long-chain primary alcohol (i.e., 2-ethylhexanol, 2-EH) to the phthalate mixture (Figure 4; Entries REF, BA and 2-EH). The increased average PA yield when BA was present at the beginning of the reaction may suggest a modest accelerating effect of carboxylic acids on the hydrolysis rate; however, the uncertainty in the data suggests that this influence may not be statistically significant. In any case, if the effect does occur, it would be helpful when dealing with plasticizer mixtures extracted from real plastic waste, which contain both low and high molecular weight phthalates (see below). On the other hand, the cleaved alcohol fragments are quickly converted into alkenes but seem to have little to no effect on the hydrolysis rate.
Figure 4. Progressing from the hydrolysis of virgin phthalate esters to real plastic waste-extracted plasticizers. Reaction conditions: DEHP (3 mmol), H2O (Vtot = 25 mL), H-Beta 75 (391 mg), 8 bar N2, 200°C for 6 h. Experiments were repeated five times to determine the indicated standard deviations. †Half an equivalent of the defined additive (1.5 mmol) was added to the reaction mixture. ‡The plasticizer fraction includes 2.25 mmol DEHP and 0.75 mmol DEHA. ¥The plasticizer fraction contains 95 wt% DEHP and 5 wt% PVC.
Phthalate extracts obtained from waste plastics can contain impurities; therefore the effect and fate of the detected extract contaminants on the hydrolysis reaction was investigated. As described elsewhere, the end-of-life plasticizers are extracted from post-consumer vinyl flooring, via a dissolution-precipitation approach whereafter the used solvents are removed from the supernatant by evaporation. The crude extract consists of ±75 weight % of the previously discussed phthalate plasticizers (DBP, DIBP, BeBP, DEHP and DINP), ±20% aliphatic plasticizers and ±5% residual PVC. Additionally, unspecified sulfur-components were detected in low amounts on solids that had been in contact with the plasticizer extract (Windels et al., 2022; Wagner and Schlummer, 2020).
Bis(2-ethylhexyl) adipate (DEHA) was selected as representative for the aliphatic plasticizers, given its substantial share in the extract, also reflecting its historical use. Hence, a blend comprising 75 mol% DEHP and 25 mol% DEHA was formulated at room temperature and subsequently employed as the plasticizer fraction (Figure 4, Entry DEHA). While the conversion rate of the phthalate ester is minimally affected, the adipate ester is likewise transformed into adipic acid under the tested conditions.
Considering the excellent compatibility of phthalate esters with PVC (Bocqué et al., 2016; Howick, 2021), the deep removal of the polymer from such a plasticizer extract is known to be challenging. To evaluate the effect of residual polymer, some virgin PVC was dissolved in DEHP (5 wt% polymer, 3 h at 100°C) and after cooling back to room temperature used in the hydrolysis reaction (Figure 4, Entry PVC). Water is known to be an excellent anti-solvent for PVC (Grause et al., 2017; O’Rourke et al., 2023) and could cause the polymer to precipitate not only on the reactor walls, but also on the heterogeneous catalyst. However, the hydrolysis rate appears to be only slightly affected by this phenomenon, which suggests that the majority of the active sites of the heterogeneous catalyst remain available, indicative for only minimal fouling.
Thus, the dialkyl phthalate hydrolysis seems to be relatively insensitive to detected extract impurities. Therefore a crude plasticizer mixture, extracted from real PVC waste, was used in the following experiments (Figure 4, Entry Waste DP). With an equivalent yield of PA after 6 h (66% PA) compared to the reference DEHP hydrolysis (67% PA), it indeed appears that no waste extract impurity exerts a significant poisoning effect on the zeolite. As a consequence, quantitative yields of PA (>99%) could be obtained from real waste-extracted phthalate plasticizers by extending the reaction time to 22 h. The hydrolysis of legacy phthalate esters using a hydrophobic H-Beta zeolite in water emerges as an exceptionally robust detoxification method for these legacy plasticizers. Furthermore, the obtained aromatic product can be further revalorized into other drop-in chemicals such as benzoic acid and benzene (see below).
Next, we focus on the decarboxylation of PA to selectively obtain either benzoic acid (BA) or benzene (B). Although this specific catalytic reaction has not yet been documented, heterogeneous noble metals have repeatedly been reported for the decarboxylation of other organic acids (De Schouwer et al., 2017; Dawes et al., 2015; Verduyckt et al., 2016; De Schouwer et al., 2015) and were therefore evaluated for this reaction (Figure 5; Supplementary Figure S19). While the control experiment resulted in a minimal conversion of PA (<5% after 22 h; Supplementary Figure S18), all tested noble metal catalysts demonstrated varying degrees of activity for the decarboxylation under the employed reaction conditions (3 mmol PA, 2.5 mol% noble metal, 25 mL H2O at 225°C for 22 h). More specifically, Pd displayed the lowest activity among the tested metals, showing only 9% conversion after the first hour, while Ru- and Rh-catalysts exhibited an intermediate and remarkably similar decarboxylation rate (45% conversion after 1 h). Pt demonstrated an even higher decarboxylation activity, achieving complete PA conversion within the first hour of reaction. Moreover, each catalyst proved effective for the successive decarboxylation of BA to B under the same reaction conditions. As a result, all time profiles follow the typical course of consecutive reactions (Supplementary Figure S19), wherein the yield of the intermediate product (BA) reaches a maximum before progressing to complete transformation into the final product (B). Consequently, extended reaction times lead to near-quantitative yields of B while the selectivity towards BA requires additional optimization. At 225°C, there appears to be no significant selectivity difference between the noble metals (Figure 5; right), leading to a catalyst choice - being Pt/C - primarily determined by the decarboxylation activity. This choice is further supported by the steady output (PA conversion and BA selectivity) observed over four consecutive decarboxylation experiments, indicative of a stable catalyst (Supplementary Figure S20).
Figure 5. BA yield vs. time (left) and selectivity profiles (yield vs. conversion; right) of the noble metal screening in the decarboxylation of PA to BA and B. Reaction conditions: PA (3 mmol), H2O (Vtot = 25 mL), defined noble metal catalyst (2.5 mol% metal, 5 wt% metal on carbon), 8 bar N2, 225°C for 22 h.
Considering that the maximum concentration of the intermediate in consecutive reactions depends on the ratio of the reaction rate constants (Espenson, 1981), and may thus be influenced by the activation energies, the temperature dependency of both decarboxylation steps was examined. To that end, the initial conversion rates of PA and of BA were determined in separate reactions over a temperature range between 180 °C and 250°C, after which the obtained data were displayed in an Arrhenius plot (Figure 6). From this graph, it can be deduced that the decarboxylation rate of BA is more affected by the reaction temperature than that of PA, showing apparent activation energies of 63 and 32 kJ mol-1, respectively. Indeed, the time profiles obtained in this temperature range show a steady increase in the maximum BA yield with decreasing temperature, a trend further highlighted in the corresponding selectivity profiles (Supplementary Figure S20). Based on these insights, tuning the reaction parameters (time and temperature) allows a straightforward optimization of the product selectivity. A maximum yield of 86% BA was achieved with 2.5 mol% Pt at 180 °C after 5 h, while the B yield exceed 99% under more rigorous conditions (2.5 mol% Pt at 250°C for 22 h).
Figure 6. Arrhenius plot of the decarboxylation of PA (blue) and BA (green). Reaction conditions: PA or BA (3 mmol), H2O (Vtot = 25 mL), Pt/C (2.5 mol% metal, 5 wt% metal on carbon), 8 bar N2.
Next, the integration of the decarboxylation reaction with the preceding hydrolysis of end-of-life phthalate plasticizers was attempted (Figure 7). In a first evaluation, 0.2 equivalents of 2-EH and 1.8 equivalents of 1-octene were added to the standard PA decarboxylation mixture in order to simulate the reaction blend obtained after the complete hydrolysis of DEHP (Figure 7, Entry Org. layer). Visual inspection of the liquid mixture at room temperature revealed the preferential localization of the Pt-catalyst in the organic top layer, both before and after the experiment (Supplementary Figure S23). Such behavior could explain the observed drastic decline of the decarboxylation rate when alcohol and alkene fragments are present in the liquid mixture. It may suggest strong competitive adsorption of the long-chain alcohol and alkene molecules on the carbon-supported noble metal catalyst, even if the liquid fractions were to become more miscible at elevated reaction temperatures. This catalyst inhibition phenomenon implies that a one-pot hydrolysis-decarboxylation process as such would be inefficient, demanding an intermediate purification step. Hence, from this point onwards the side-chain fragments (primary alcohols and alkenes) were removed from the hydrolysis mixture prior to the decarboxylation experiment. This separation was achieved by completely dissolving PA in the aqueous phase at room temperature through addition of NaOH (without base addition only ±30% PA dissolves), followed by separation of both immiscible liquids through decantation. Less than 5% of the PA was lost during this purification procedure. The following control experiment revealed that the added base has no significant negative impact on the decarboxylation reaction, rendering additional purification steps of the aqueous layer unnecessary (Figure 7, Entry NaOH).
Figure 7. Progressing from the decarboxylation of virgin PA to the coupled revalorisation process of real plastic waste-extracted plasticizers: Time profiles of the decarboxylation trials. Reference reaction conditions: PA (3 mmol), H2O (Vtot = 25 mL), Pt/C (2.5 mol% metal, 5 wt% metal on carbon), 8 bar N2, 200°C for 5 h. Entry Org. Layer: Addition of 2-EH (0.6 mmol) and 1-octene (5.4 mmol). Entry NaOH: Addition of 100 mg NaOH. Entries Adipic Acid, PVC and Waste PA: After the complete hydrolysis of the plasticizers (conditions as described in Figure 4 with an extended reaction time of 22 h), the carboxylic acids were separated from the organic layer by addition of NaOH and decantation. After these manipulations, the decarboxylation was executed as mentioned in the reference conditions above.
Next, the effect of waste extract impurities, such as aliphatic plasticizers and residual PVC, on the Pt-catalyzed decarboxylation of phthalic acid was investigated (Figure 7). To simulate the real situation as accurately as possible, the decarboxylation test was preceded by the complete hydrolysis of the DEHP/impurity mixture (conditions as stated in Figure 4 with an extended reaction time of 22 h) and the abovementioned PA purification procedure. In a first evaluation, the fate of co-extracted adipate plasticizers (such as DEHA) was studied. Adipic acid, obtained from the hydrolysis of DEHA, remained unseparated from PA during the purification procedure and was consequently subjected to Pt-decarboxylation. The aliphatic carboxylic acid exhibited low stability under the studied reaction conditions, resulting in the formation of pentanoic acid and butane through single and double decarboxylation. On the other hand, the conversion rate of PA (and BA) increased compared to the reference experiment, despite an unchanged carboxylic acid to Pt molar ratio (Figure 7, entries Reference and Adipic Acid). In other words, it appears that co-extracted aliphatic plasticizers have no adverse effect on the hydrolysis-decarboxylation procedure to revalorize phthalate plasticizers, but are themselves stepwise broken down into more simple compounds.
In a final experiment prior to the evaluation of the coupled revalorisation process on real plastic waste-derived substrates, the effect of residual PVC in the plasticizer stream on the Pt-catalyzed decarboxylation was examined. This involved again the complete hydrolysis of a DEHP/PVC mixture (conditions as specified in Figure 4 with an extended reaction time of 22 h) and the subsequent purification of the aqueous phase. Exploiting the excellent antisolvent characteristics of water for PVC (Grause et al., 2017), the polymer was effectively separated from the aromatic substrate (the polymer could not be detected anymore using 1H-NMR), and therefore not subjected to the decarboxylation experiment. However, the reduced decarboxylation rate observed in the obtained aqueous mixture implies that the Pt-catalyst is still hindered by (undetectable) traces of polymer chains that were transferred into the decarboxylation mixture Figure 7, Entry PVC).
Ultimately, waste plasticizers as such were subjected to the tandem hydrolysis-decarboxylation, as most of the co-extracted compounds demonstrated limited interference with the second step of the proposed revalorisation process. After the complete hydrolysis of the waste phthalate esters and the subsequent removal of the organic top layer, the carboxylic acids were decarboxylated almost as efficiently as when virgin PVC was added to the plasticizer mixture (Figure 7, Entry Waste PA and PVC). Thus, the retarding effects of residual chlorinated components on the PA conversion rate slightly outweigh the accelerating influences, such as the presence of adipic acid. Nevertheless, complete PA conversion is reached between 2.5 and 5 h of reaction time and a similar BA selectivity is obtained throughout the experiments under current conditions (Supplementary Figure S22). This observation underlines the inherent robustness of the proposed revalorisation process, although the lifespan of the zeolite and Pt-catalyst might be affected by the purity of the plasticizer stream.
In this work, legacy phthalate plasticizers extracted from post-consumer PVC flooring waste have been catalytically revalorized into simple aromatics and alkenes, via a tunable hydrolysis-decarboxylation process. In preliminary hydrolysis experiments, conventional phthalate plasticizers exhibited a remarkable resistance against the breaking of their ester bonds. However, the commercially available zeolite H-Beta 75, characterized by its hydrophobic surface and relatively large pores, combined excellent hydrolysis activity with hot liquid water stability. This enabled the complete conversion of legacy phthalate plasticizers into phthalic acid and alkenes (obtained from the dehydration of the generated primary alcohol fragments).
Next, the decarboxylation of the formed phthalic acid was developed to selectively yield either benzoic acid or benzene. The tested noble metal on carbon catalysts exhibited varying decarboxylation activity (Pt > Ru ≈ Rh >> Pd) with a rather similar selectivity for benzoic acid. Interestingly, the intermediate benzoic acid could be more selectively obtained at lower temperatures and shorter reaction times, while benzene was obtained in quantitative yields at high temperatures and/or long reaction times. Due to the negative effect of the hydrolyzed (and dehydrated) side-chain fragments on the decarboxylation rate, an intermediate removal of the organic top layer was needed for the successful coupling of both reactions. To that end, the carboxylic acids were completely dissolved in the aqueous phase by addition of NaOH, followed by decantation to separate both immiscible liquids.
When performing this tandem process on real post-consumer plastic waste extracted phthalate plasticizers, the revalorisation method proved remarkably robust: the hydrolysis demonstrated a very limited interference from co-extracted impurities, while the decarboxylation was only slightly delayed by trace amounts of residual PVC.
In essence, the flexible hydrolysis-decarboxylation process allows for the selective transformation of real plastic waste-extracted phthalate plasticizers into either phthalic acid (>99% yield), benzoic acid (83% yield) or benzene (95% yield). Additionally, primary alcohols and alkenes are produced as valuable by-products during the zeolite-catalyzed hydrolysis of the phthalate esters.
The original contributions presented in the study are included in the article/Supplementary Material, further inquiries can be directed to the corresponding author.
SW: Investigation, conceptualization, Writing–original draft, Writing–review and editing. NS: Investigation, Writing–review and editing. WS: Writing–review and editing. DDV: Writing–review and editing, Supervision.
The author(s) declare that financial support was received for the research, authorship, and/or publication of this article. This project has received funding from the European Union’s Horizon 2020 research and innovation programme under grant agreement no. 821366 (programma acronym: Circular Flooring). WS is grateful to FWO for his PhD fellowship (1SC1519N) and DDV thanks FWO for project funding (SBO project S001819N Triple Cycle).
The authors are thankful to Fraunhofer IVV for the delivery of extracted plasticizers from post-consumer PVC flooring waste.
The authors declare that the research was conducted in the absence of any commercial or financial relationships that could be construed as a potential conflict of interest.
All claims expressed in this article are solely those of the authors and do not necessarily represent those of their affiliated organizations, or those of the publisher, the editors and the reviewers. Any product that may be evaluated in this article, or claim that may be made by its manufacturer, is not guaranteed or endorsed by the publisher.
The Supplementary Material for this article can be found online at: https://www.frontiersin.org/articles/10.3389/fceng.2024.1463638/full#supplementary-material
Arena, U., and Ardolino, F. (2022). Technical and environmental performances of alternative treatments for challenging plastics waste. Resour. Conserv. Recycl 183, 106379. doi:10.1016/j.resconrec.2022.106379
BASF (2008). BASF increases plasticizer production, reorganizes businesses. Addit. Polym. 2008, 6. doi:10.1016/S0306-3747(08)70030-7
Bocqué, M., Voirin, C., Lapinte, V., Caillol, S., and Robin, J.-J. (2016). Petro based and bio based plasticizers: chemical structures to plasticizing properties. J. Polym. Sci. Part A Polym. Chem. 54, 11–33. doi:10.1002/pola.27917
Brunner, M., Böttcher, A., Breitscheidel, B., Halbritter, K., Henkelmann, J., Thil, L., et al. (2001). Method for hydrogenating benzene polycarboxylic acids or derivatives thereof by using a catalyst containing macropores. U.S. Patent No 6,284,917 B1. Washington, DC: U.S. Patent and Trademark Office.
Cadogan, D. F., and Howick, C. J. (2000) Plasticizers in ullmann's encyclopedia of industrial Chemistry. Germany: Wiley-VCH Verlag GmbH and Co. KGaA, 600–618.
Chen, F., Shetty, M., Wang, M., Shi, H., Liu, Y., Camaioni, D. M., et al. (2021). Differences in mechanism and rate of zeolite-catalyzed cyclohexanol dehydration in apolar and aqueous phase. ACS Catal. 11, 2879–2888. doi:10.1021/acscatal.0c05674
Crespo, J. E., Balart, R., Sanchez, L., and López, J. (2007). Substitution of di(2 ethylhexyl) phthalate by di(isononyl) cyclohexane 1,2 dicarboxylate as a plasticizer for industrial vinyl plastisol formulations. J. Appl. Polym. Sci. 104, 1215–1220. doi:10.1002/app.25760
David, R. M., White, R. D., Larson, M. J., Herman, J. K., and Otter, R. (2015). Toxicity of Hexamoll® DINCH® following intravenous administration. Toxicol. Lett. 238, 100–109. doi:10.1016/j.toxlet.2015.07.013
Dawes, G. J. S., Scott, E. L., Le Nôtre, J., Sanders, J. P. M., and H Bitter, J. (2015). Green Chem. 17, 3232–3250. doi:10.1039/c5gc00023h
De Munck, N., Goris, H., and Van Driessche, E. (2018) Process for the hydrogenation of phthalate esters. Geneva, Switzerland: World Intellectual Property Organization.
De Schouwer, F., Adriaansen, S., Claes, L., and De Vos, D. E. (2017). Bio-based N-alkyl-2-pyrrolidones by Pd-catalyzed reductive N-alkylation and decarboxylation of glutamic acid. Green Chem. 19, 4919–4929. doi:10.1039/c7gc01829k
De Schouwer, F., Claes, L., Claes, N., Bals, S., Degrève, J., and De Vos, D. E. (2015). Pd-catalyzed decarboxylation of glutamic acid and pyroglutamic acid to bio-based 2-pyrrolidone. Green Chem. 17, 2263–2270. doi:10.1039/c4gc02194k
Ennaert, T., Van Aelst, J., Dijkmans, J., De Clercq, R., Schutyser, W., Dusselier, M., et al. (2016). Potential and challenges of zeolite chemistry in the catalytic conversion of biomass. Chem. Soc. Rev. 45, 584–611. doi:10.1039/c5cs00859j
Espenson, J. H. (1981). Chemical kinetics and reaction mechanisms. United States of America: McGraw-Hill Book Company.
European Plasticisers (2021). Plasticisers. Available at: https://www.plasticisers.org/plasticisers/ (Accessed July 1, 2023).
European Chemicals Agency (2020). Substance Infocard: 1,2-Cyclohexanedicarboxylic acid, 1,2-diisononyl ester. Available at: https://echa.europa.eu/nl/substance-information/-/substanceinfo/100.103.017 (Accessed July 1, 2023).
European Chemicals Agency (2021). Annex XVII to REACH – conditions of restriction: Entry 51. Available at: https://echa.europa.eu/substances-restricted-under-reach (Accessed July 1, 2023).
Falbe, J., Bahrmann, H., Lipps, W., and Mayer, D. (2000) Alcohols, aliphatic in ullmann’s encyclopedia of industrial Chemistry. Germany: Wiley-VCH Verlag GmbH and Co. KGaA, 235–261.
Folkins, H. O. (2000) Benzene in ullmann’s encyclopedia of industrial Chemistry. Germany: Wiley-VCH Verlag GmbH and Co. KGaA, 237–268.
Grass, M., Kaizik, A., Buschken, W., Tuchlenski, A., Maschmeyer, D., Gaudschun, K.-A., et al. (2006). Catalyst and method for hydrogenating aromatic compounds. U.S. Patent No 2006/0183936A1. Washington, DC: U.S. Patent and Trademark Office.
Grause, G., Hirahashi, S., Toyoda, H., Kameda, T., and Yoshioka, T. (2017). Solubility parameters for determining optimal solvents for separating PVC from PVC-coated PET fibers. J. Mater. Cycles Waste Manage. 19, 612–622. doi:10.1007/s10163-015-0457-9
Groh, K. J., Backhaus, T., Carney-Almroth, B., Geueke, B., Inostroza, P. A., Lennquist, A., et al. (2019). Overview of known plastic packaging-associated chemicals and their hazards. Sci. Total Environ. 651, 3253–3268. doi:10.1016/j.scitotenv.2018.10.015
Heard, C. J., Grajciar, L., Uhlík, F., Shamzhy, M., Opanasenko, M., Čejka, J., et al. (2020). Zeolite (In)Stability under aqueous or steaming conditions. Adv. Matter. 32, 2003264. doi:10.1002/adma.202003264
Hillshafer, D., and Magnus, G. (2000). Phthalic anhydride based polyester-ether polyols and urethane prepolymers produced therefrom. E.U. Patent No 1 237 975 B1. Munich, Germany: U.S. European Patent Office.
Howick, C. J. (2021). Plasticizers in kirk-othmer encyclopedia of chemical Technology. John Wiley and Sons.
Liu, Y., Vjunov, A., Shi, H., Eckstein, S., Camaioni, D. M., Mei, D., et al. (2017). Enhancing the catalytic activity of hydronium ions through constrained environments. Nat. Commun. 8, 14113. doi:10.1038/ncomms14113
Lorz, P. M., Towae, F. K., Enke, W., Jäckh, R., Bhargava, N., and Hillesheim, W. (2007) Phthalic acid and derivatives in ullmann's encyclopedia of industrial Chemistry. Germany: Wiley-VCH Verlag GmbH and Co. KGaA, 131–180.
Maki, T., and Takeda, K. (2000) Benzoic acid and derivatives in ullmann's encyclopedia of industrial Chemistry. Germany: Wiley-VCH Verlag GmbH and Co. KGaA, 329–342.
Opgrande, J. L., Brown, E. E., Hesser, M., and Andrews, J. (2003) Benzoic acid in kirk-othmer encyclopedia of chemical Technology. United States: John Wiley and Sons, 625–637.
O’Rourke, G., Hennebel, T., Stalpaert, M., Skorynina, A., Bugaev, A., Janssens, K., et al. (2023). Catalytic tandem dehydrochlorination–hydrogenation of PVC towards valorisation of chlorinated plastic waste. Chem. Sci. 14, 4401–4412. doi:10.1039/d3sc00945a
Pivnenko, K., Eriksen, M. K., Martín-Fernández, J. A., Eriksson, E., and Astrup, T. F. (2016). Recycling of plastic waste: presence of phthalates in plastics from households and industry. Waste Manage. 54, 44–52. doi:10.1016/j.wasman.2016.05.014
Ravenelle, R. M., Schüssler, F., D’Amico, A., Danilina, N., van Bokhoven, J. A., Lercher, J. A., et al. (2010). J. Phys. Chem. C 114, 19582–19595. doi:10.1021/jp104639e
Fraunhofer IVV (2023) Recycling plastics – the CreaSolv® process. Available at: https://www.ivv.fraunhofer.de/en/recycling-environment/recycling-plastics-creasolv.html, (Accessed July 1, 2024).
Riemenschneider, W., and Bolt, H. M. (2005) Ester, organic in ullmann’s encyclopedia of industrial Chemistry. Germany: Wiley-VCH Verlag GmBH and Co. KGaA, 245–266.
Stuyck, W., Verduyckt, J., Kranjc, A., Mali, G., and De Vos, D. E. (2020). Green Chem. 22, 7812–7822. doi:10.1039/D0GC02298E
Ügdüler, S., Van Geem, K. M., Roosen, M., Delbeke, E. I. P., and De Meester, S. (2020). Challenges and opportunities of solvent-based additive extraction methods for plastic recycling. Waste Manage. 104, 148–182. doi:10.1016/j.wasman.2020.01.003
United States Consumer Product Safety Commission (2019). Phthalates business guidance and small entity compliance guide. Available at: https://www.cpsc.gov/Business--Manufacturing/Business-Education/Business-Guidance/Phthalates-Information (Accessed July 1, 2023).
Verduyckt, J., Van Hoof, M., De Schouwer, F., Wolberg, M., Kurttepeli, M., Eloy, P., et al. (2016). PdPb-catalyzed decarboxylation of proline to pyrrolidine: highly selective formation of a biobased amine in water. ACS Catal. 6, 7303–7310. doi:10.1021/acscatal.6b02561
Wagner, S., and Schlummer, M. (2020). Legacy additives in a circular economy of plastics: current dilemma, policy analysis, and emerging countermeasures. Resour. Conserv. Recycl 158, 104800. doi:10.1016/j.resconrec.2020.104800
Windels, S., Diefenhardt, T., Jain, N., Marquez, C., Bals, S., Schlummer, M., et al. (2022). Catalytic upcycling of PVC waste-derived phthalate esters into safe, hydrogenated plasticizers. Green Chem. 24, 754–766. doi:10.1039/d1gc03864h
Keywords: heterogeneous catalysis, green chemistry, plastic waste utilization, phthalate plasticizers, revalorization, legacy additives
Citation: Windels S, Seynaeve N, Stuyck W and De Vos DE (2024) Catalytic revalorization of plastic waste phthalate plasticizers into simple aromatics and alkenes. Front. Chem. Eng. 6:1463638. doi: 10.3389/fceng.2024.1463638
Received: 12 July 2024; Accepted: 26 August 2024;
Published: 13 September 2024.
Edited by:
Matthijs Ruitenbeek, Dow Benelux, NetherlandsReviewed by:
Yinglong Wang, Qingdao University of Science and Technology, ChinaCopyright © 2024 Windels, Seynaeve, Stuyck and De Vos. This is an open-access article distributed under the terms of the Creative Commons Attribution License (CC BY). The use, distribution or reproduction in other forums is permitted, provided the original author(s) and the copyright owner(s) are credited and that the original publication in this journal is cited, in accordance with accepted academic practice. No use, distribution or reproduction is permitted which does not comply with these terms.
*Correspondence: Dirk E. De Vos, ZGlyay5kZXZvc0BrdWxldXZlbi5iZQ==
†ORCID: Simon Windels, orcid.org/0000-0003-4539-8553; Wouter Stuyck, orcid.org/0000-0002-2887-0580; Dirk E. De Vos, orcid.org/0000-0003-0490-9652
Disclaimer: All claims expressed in this article are solely those of the authors and do not necessarily represent those of their affiliated organizations, or those of the publisher, the editors and the reviewers. Any product that may be evaluated in this article or claim that may be made by its manufacturer is not guaranteed or endorsed by the publisher.
Research integrity at Frontiers
Learn more about the work of our research integrity team to safeguard the quality of each article we publish.