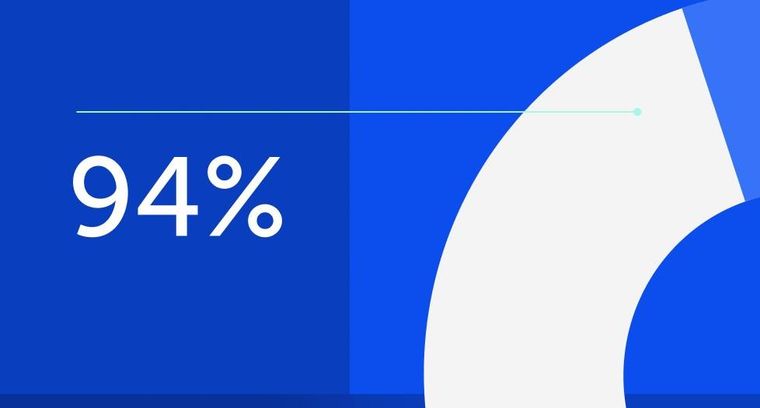
94% of researchers rate our articles as excellent or good
Learn more about the work of our research integrity team to safeguard the quality of each article we publish.
Find out more
ORIGINAL RESEARCH article
Front. Chem. Eng., 23 January 2024
Sec. Materials Process Engineering
Volume 5 - 2023 | https://doi.org/10.3389/fceng.2023.1307309
This article is part of the Research TopicDry Powder Coating in Manufacturing ProcessesView all 6 articles
The aim of this work was to demonstrate the potential of the concept of clean-label-capable flow additives. These are spray-dried food ingredients whose particle size is small enough (<10 µm) to take over the function of classic flow additives such as highly dispersed silicas. Their acceptance by customers and consumers has been declining for years, as they are primarily mineral excipients that are becoming increasingly unpopular in foods. This poses major problems for the food industry, as many food powders have poor flow properties and handling problems. The idea of clean-label flow additives is to create an alternative to meet consumer demands and industry requirements. Using four different cohesive food powders as examples, the authors demonstrate the effectiveness of this concept. For this purpose, flow additives were prepared from low-concentration solutions in a laboratory spray dryer. Dry particle coating was carried out in a tumbling mixer for 30 min, after which the flow properties of the coated powders were determined using a Schulze Ring shear tester. The results show that a significant improvement in the flowability of cohesive food powders is possible by using these spray-dried flow additives. In addition, an anti-caking effect could be observed. There is still a need for optimization in the production of such flow additives in order to increase their economy and effectiveness. Overall, the concept of clean-label flow additives shows great potential.
Powders play an important role in the food industry. On the one hand, the low water content prevents microbial spoilage and, on the other hand, reduces transport costs due to the lower mass. For this reason, many intermediate and consumer products in the food industry are now produced as powders. It is not uncommon, however, for food powders to exhibit poor flowability and/or a strong tendency for caking. These include massive problems during storage in silos, reduced dosing capability, disruptions in product conveying or even product loss. The resulting economic losses are difficult to estimate because such problems are handled in-house. However, according to estimates by Griffith (1991), losses due to caking are at least 0.5% of the total value of powders produced, which is a significant value considering the enormous quantities of powder produced and reduces the already low profit margins in the food industry.
The targeted agglomeration of the powder particles represents a possible measure for solving the problem (Hazlett et al., 2021), but in various cases it is not economical or simply not possible. The use of flow additives is another opportunity that has been known and used for decades to improve the handling properties of critical powders. Conventional flow additives are mostly inorganic, mineral and usually declarable compounds. Examples are silicas, carbonates, phosphates or stearates (Tomas and Kleinschmidt, 2009). Synthetic silicas in particular are considered the standard in the field of flow additives. Due to significantly decreasing customer acceptance, bans in some areas and critical studies, e.g., (Winkler et al., 2017; Yoo et al., 2022; Zickgraf et al., 2023), their use in the food industry is a sensitive topic. The development of clean-label-capable flow additives from foodstuffs is a forward-looking idea to meet technical requirements and customer demands. To do this, one must first understand the mode of action of such excipients.
The macroscopic behavior of powders and thus their handling properties are determined by the chemical composition of the material, their supramolecular state (amorphous, crystalline), dispersed state (particle size, shape, surface morphology, etc.), and the resulting interparticle interactions (Molerus, 1978; Tomas, 2004; Schulze, 2007). These include intangible field forces, especially van der Waals forces and electrostatic forces, interactions due to water adsorption layers, and also material bridging bonds due to liquids or solids (Palzer, 2007; Zafar et al., 2017). Some of these interactions exhibit a pronounced distance dependence and are only relevant over short distances. Figure 1A) shows this dependence of various interparticle interactions on the contact distance. Surface roughnesses increase the distance between the particles or prevent them from approaching each other more closely than up to their size. As a result, they act as spacers and thus significantly reduce the effective forces in some cases (Krupp, 1967). The effect of flow additives is described as analogous to a rough particle surface. Here, the smaller flow additive particles adhere to the surfaces of the larger carrier particles and act quasi as artificial roughness (guest particles, see Figure 2). While electrostatic forces require triboelectric charging, as can occur in pneumatic conveying systems, for example, and liquid bridges can only form on the particle surfaces with correspondingly large amounts of liquid, van der Waals interactions are always present. They are considered to be the main cause of poor flowability of finely dispersed powders and are preferred for explaining size effects (Lin et al., 2004; Hazlett et al., 2021). Mathematical formulations for calculating the effect of flow additives on the interparticle adhesive forces are also based on the consideration of van der Waals adhesive forces (Mei et al., 1997; Xie, 1997; Zimmermann et al., 2004). For three such models, the dependence on the size of the flow additive particles is shown in Figure 1B) (for detailed information, see, e.g., (Tomas and Kleinschmidt, 2009)).
FIGURE 1. Theoretical adhesion forces (A) between two spherical particles in dependence of the contact distance and (B) for different models in dependence of the flow additive size.
The attractive forces initially decrease as the size of the flow additives increases, since the distance between the carrier particles increases. However, as the flow additives particle size increases, their interactions with the contact partner also increase and the total attractive force starts to increase again. Therefore, the size of the flow additives is crucial for its effect. In addition, two areas are drawn in the figure. Highly dispersed silicas consist of chain-like aggregates of primary particles smaller than 10 nm. On the surface of carrier particles, they form spherical agglomerates of approximately 150–250 nm in diameter (Kleinschmidt, 2015). Producing particles this fine is extremely difficult.
The second area comprises particle sizes between 1 μm and 10 µm. The theoretical adhesion forces here are significantly larger compared to the highly dispersed silica, but still lower by at least a factor of 10 than those between two smooth carrier particles. It is easier to produce particles of this size, e.g., by spray drying. At the same time, one avoids the critically considered issue of nanoparticles in food.
The basic idea of clean-label flow additives is that particles can be prepared from any solid or dryable food product with a size well below 10 µm and these can take over the function of flow additive in cohesive food powders. The aim of this work was to demonstrate the potential behind this concept.
Four different materials were used as carrier powders. Maltodextrin DE6 was used as a fat-free material with a high glass transition temperature. Glucose syrup DE33 served as a likewise fat-free material, but with a much lower glass transition. The skim milk powder used had similarly low glass transition temperatures, but also a low fat content. Whole milk powder was used as the test material with a significantly higher fat content.
To ensure comparability, the materials were spray-dried under comparable process conditions (Anhydro MicraSpray 400, single-stage drying, inlet temperature 160°C, outlet temperature 80°C, pressure nozzle). The particle size distributions obtained can be found in Figure 3D). The distributions vary in width but are all monomodal, indicating little or no agglomeration. The particle sizes (d10 - d90) range from 20 μm to 220 µm. All four powders also exhibited cohesive flow behavior (see Figure 9).
FIGURE 3. Particle size distributions of carrier systems and flow additives (A) different dry matters, (B) different types of atomization, (C) different materials, carrier particles (D).
The same materials were used as for the carrier systems. Only the glucose syrup was exchanged for lactose. Both have about the same glass transition temperature, but lactose was of particular interest for use in milk-based powders.
One possibility for the production of clean-label-capable flow additives is spray drying. The aim here is to obtain the smallest possible particle size. In order to achieve this, two essential aspects have to be considered. Firstly, an attempt must be made to produce a small droplet size. The finer the droplets produced, the smaller the solid particles will be after drying. Since atomization is limited in terms of the droplet sizes that can be produced, it is also necessary to keep the dry substance of the feed as low as possible. During the first drying stage, the water contained is evaporated, causing the droplets to shrink until they finally form a particle. The less solid matter is contained in the droplet at the beginning of drying, the smaller the resulting particles become. Thus, in addition to the atomizer, the surface tension, viscosity and solids concentration of the feed solution also have a major influence on the droplet and particle sizes produced. Surface tension and viscosity are mainly dependent on the temperature and solids concentration of the feed. The surface tension of the feed solution was determined using a bubble pressure tensiometer (SITA science line t 100) in the range of 1–30 wt.-%. The viscosity of the feed solution was determined using a rheometer (Anton Paar MCR 302) with a cone-plate system. The shear rate varied between 1 and 100 1/s. The viscosities determined were relatively constant in this range and an average value was calculated. All tests were carried out in duplicate.
The flow additives were prepared in a laboratory spray dryer (GEA Niro Mobile Minor™) at 160°C air inlet temperature. The feed rate was adjusted, so that the air outlet temperature was 80°C (approx. 1.5–2.5 L/h). The atomizers used were a rotary or wheel atomizer (GEA Niro 010,084–0001), a two-fluid or pneumatic nozzle (Düsen-Schlick Model 970), and an ultrasonic nozzle (Hielscher Ultrasonics S26d18S). The parameters of each atomizer were varied to find the settings that produced the smallest particle sizes for given feed and drying conditions.
The application of flow additives is called dry particle coating and can in principle be realized by any solid mixing process. The small flow additive particles adhere to the surfaces of the larger carrier particles. The prerequisite for this is, as already mentioned, a size difference of about a factor of 10 or greater. According to Hersey (1975), such a process is called "ordered mixing". The distribution of the smaller gas particles on the surface of the larger carrier particles becomes more and more homogeneous in the course of the process. Typical mixing times to achieve maximum flowability are around 10–20 min (Kleinschmidt, 2015).
A tumbling mixer (Bioengineering Inversina 2L) was used for the experiments. The speed was 48 rpm. The carrier material was placed in the mixing vessel first and then the flow additive was added on top, so that both powders were separated from each other at the beginning. The filling level of the 1,000 mL mixing container was about 50%. Each of the powders were mixed for 30 min. The determination of the time is based on literature data and own empirical values. The amount of flow additives was variated between 1 and 10 wt.-%.
Particle size distributions were determined by laser diffraction (Malvern Mastersizer 3,000, wet dispersion). Isopropanol served as dispersing medium and the evaluation was performed using the Fraunhofer approximation.
Scanning electron micrographs (JEOL JSM IT-100) of the powders were also taken for qualitative evaluation of the results. For this purpose, the powder samples were vapor-deposited with a gold layer (sputtered) in advance.
The flow behavior of the powders was characterized by shear tests with a Schulze ring shear tester (RST-XS). The design of the system and the measuring procedure are described in detail in the literature (Schulze, 1994; Schulze, 1995; Schulze, 1996). In contrast to many other measuring systems, shear testers allow a quantitative statement to be made regarding the flowability, the time consolidation and the compression behavior. Furthermore, a valid standard exists for the ring shear tester used (ASTM, 2008). Comparable results are obtained to the translational shear cells according to Jenike, which have been established since the 1960s (Schulze, 1994; Schulze, Heinrici, and Zetzener, 2001). However, the reproducibility is considerably higher (Verlinden, 2000). A standard measuring cell with a filling volume of 30 mL was used. A total of 6 yield loci were measured (3 stress levels, double determination). From the data obtained, the consolidation stress σ1 and the unconfined yield strength σc can be determined. According to Jenike (1964), their ratio is called flowability and is used to characterize the flow behavior (see Table 1).
Caking was also measured using a ring shear tester. The samples were first preconditioned (7 days storage at 20°C and 40% relative humidity without load). They were then filled into the shear cells and pre sheared. They were then stored again in the climate chamber for the respective storage times (up to 72 h). During this time, the samples were loaded with weights on the shear lid (vertical stress corresponded to the consolidation stress σ1). After storage the sample were sheared to failure.
The flow additive particle size obtained during spray drying is strongly determined by the dry mass of the feed, since this influences on the one hand the viscosity and surface tension of the emulsion to be atomized, and on the other hand the ratio of droplet size after atomization and particle size after drying (Elversson and Millqvist-Fureby, 2005; Vicente et al., 2013). Figure 3A) shows this relationship for maltodextrin DE6 with dry masses of 1–30 wt.-%. The particle size distributions increase with growing dry mass. At 1 wt.-%, a distribution between 1 μm and 10 µm could be obtained. Even with 15 wt.-%, particles smaller than 10 µm could still be produced. The particle size distribution obtained from the emulsion with 30 wt.-% was already clearly outside the target range (see Figure 3A) and did not produce any measurable improvement in flowability (see Figure 6).
The atomizer used also has an influence on the droplet size produced and thus on the particle size after drying. A comparison between the systems used can be found in Figure 3B). Here, again using the example of maltodextrin DE6 (1 wt.-%), the best achievable (smallest) particle size distributions are shown. It can be regarded that the centrifugal atomizer (atomizer wheel) as well as the ultrasonic (US) nozzle produce a very similar particle size distribution. In the case of the ultrasonic atomizer, the flowrate is also very important. It can only be changed to a limited extent, which is why the influence on the outlet temperature was negligible. If it increases, larger droplets and particles are also produced, which leads to a bimodal distribution. The smallest particle size distribution was achieved at a flow rate of 15%. The largest particle size distribution was achieved at 60% flow rate. Both extremes are shown in Figure 3B). In both cases, however, the size distributions are significantly above the set limit of 10 µm. This drastically worsens the effectiveness of the produced flow additives. Only the externally mixing two-fluid or pneumatic nozzle used was able to produce such a fine droplet size distribution that particles of less than 10 µm were produced after drying. Therefore, all further investigations were carried out by atomizing the flow additives from a 1 wt.-% solution by means of a two-fluid nozzle and then drying.
Figure 3C) shows the particle size distributions obtained in this way for all four test materials used as flow additives. Furthermore, SEM images of the samples were made to get an impression of their morphology (see Figure 4). Overall, these correspond well with the results of the particle size analysis. For maltodextrin DE6 and skim milk powder a narrow particle size distribution between 1 μm and 10 µm was realized. The SEM images of maltodextrin show round, non-agglomerated particles with a size below 10 µm. The skim milk particles are about the same size on the SEM images, but appear to be partially agglomerated. Since the particle size analysis showed only minor differences, it can be assumed that the primary particles only loosely adhere together and are disintegrated during dispersion. In contrast, whole milk powder and lactose showed a much broader distribution. On the SEM images of both samples, compact agglomerates with a grape structure can be seen. Visually, the two samples are very similar. In the case of whole milk, the agglomerates can be attributed to the high fat content, which has a negative effect on atomization. The whole milk powder produced also had an excessively high free fat content, resulting in massive agglomeration and lump formation. Therefore, whole milk powder or similar fat-containing products were not used as flow additives. Although the dried lactose also tended to agglomerate and revealed a bimodal particle size distribution (see Figure 3C), good effectiveness as a flow additive was nevertheless demonstrated (see Figure 9). It is suspected that the primary particles produced are very small but they agglomerate during drying. These agglomerates are subsequently partially destroyed again during the dry particle coating process (see Figures 8C, D).
First of all, it was to be clarified how the quantitative influence of the particle size of the flow additives affects their flowability-improving effect. For this purpose, flow additives were prepared under different conditions in order to obtain different particle size distributions. The example of maltodextrin DE will be used to illustrate this. Specifically, maltodextrin DE6 served both as a carrier material and as a flow additive, so that this is a clean-label solution in the narrower sense. Therefore, the feed concentration was varied from 1 to 30 wt.-%. Figure 5 shows the measured viscosity and surface tension of these feed solutions as a function of dry mass and feed temperature. Two effects are very clear. On the one hand, viscosity and surface tension increase exponentially with the dry mass. On the other hand, they decrease with higher temperatures. However, the temperature increase in the considered range of 20°C–60°C can only partially compensate for the effects of the increase in dry matter. Viscosity and surface tension increase massively from about 15 wt.-%. This inevitably has an effect on the particle sizes produced, which also increase (see Figure 3A). From the point of view of producing the smallest possible particles, a low dry mass in the feed and a high feed temperature therefore make sense. The flow additives prepared were then added to the carrier material at 2.5 wt.-% in each case, and both powders were mixed for 30 min (tumbling mixer). In order to obtain a better comparison with the performance of conventional flow additives, another sample of the carrier system was coated with 1 wt.-% Aerosil® 200. For this ultrafine silica and carrier particles of this size range it is known, that approximately 1 wt.-% is enough to reach the maximum improvement of flowability (Kleinschmidt, 2015). Subsequently, the samples were taken and analyzed in the ring shear tester. The results are shown in Figure 6 as flow functions. The flow function of the untreated maltodextrin was in the measured range at ffc = 3 to 4 and can therefore be regarded as cohesive. First of all, it can be stated that three of the four flow additives caused an improvement of the flowability. As expected, the highly dispersed silica caused the most significant change. The flow function is in the range ffc > 10 and can be characterized as free flowing. Powders with such good flowability are generally completely unproblematic in handling. Exceptions are segregation effects, which can also occur with larger particle sizes. The spray-dried maltodextrin from the 1 wt.-% solution also showed a significant effect. Although the flowability could not be improved as much as with the silica (ffc > 10), the flow function is still in the range of easy flowing in the range of σ1 = 2,000 Pa to 8,000 Pa. Among the spray-dried flow aids, it showed the greatest improvement. Here, too, the handling should be improved in the long term. The flow additive spray-dried from a 15 wt.-% solution resulted in a significantly lower improvement. No improvement was observed for the flow additive spray-dried from a 30 percent solution. The larger flow additive particles cause a greater adhesive force and therefore poorer flowability. It must be taken into account that the same additive masses were compared here. With a smaller particle size, this means a larger number of particles and therefore a different degree of surface coverage of the carrier particles. Nevertheless, the particle sizes of the flow additives, distribution spreads and densities are very similar, so that they should only differ slightly in their number on the carrier surfaces.
FIGURE 5. Viscosity and surface tension of maltodextrin DE6 solutions as a function of dry matter for different temperatures.
FIGURE 6. Flow functions of Maltodextrin DE6 Powder as carrier system, uncoated and coated with several flow additives.
The reduction in unconfined yield strength and thus the increase in flowability was generally greater at higher stress levels. One possible explanation is that although there is deformation of the contact points (between the flow aids and carrier particles), the increase in the contact area and thus the increase in van der Waals adhesive forces is low (Tomas, 2004). Accordingly, if the load is sufficiently high, the flow aids would have to be sufficiently deformed or pressed into the carrier surface so that the carrier particles come into direct contact again and the adhesive forces increase significantly. However, no such effect was observed in the measured stress range of 2,000 to 8,000 Pa.
In general, however, it can be stated that a small particle size of the flow additives also brings a greater effect. A further reduction to about 1 μm–2 µm could again make a significant difference.
The next step was to clarify the quantitative relationship between the amount of flow additive used and its effect. This was again investigated using the example of maltodextrin DE6. The spray-dried maltodextrin from the 1 wt.-% served as the flow additive. The amount used was varied from 1% to 10% by weight.
Figure 7 shows the results of this test series. For better comparability, not the flow functions but the flowability ffc,5, i.e., the ffc value at σ1 = 5,000 Pa, are shown here. The ffc5 represents the stresses during storage in bags (Schulze, 2007), which is typical for foodstuffs. Although this is a simplification that does not show all the details of the flow function, trends can be shown well. The flowability increases already at 1 wt.-% flow additives into the range of “easy-flowing”. This trend continues almost linearly up to an amount of 3.5 wt.-%. A further addition to 5 wt.-% does not cause any further improvement of the flowability and the values do not rise again until 7.5 wt.-%. However, the increase is minimal and the entire range from 3.5 to 7.5 wt% can be considered a plateau. Further increasing the amount of flow additive to 10 wt% again worsens the flowability. From these data, it can be concluded that a maximum amount of flow additive of about 5 wt.-% is sufficient to achieve maximum results. However, the differences achieved between 2.5 and 5 wt.-% of flow additive addition are comparatively small. For this reason, an addition quantity of 2.5–3.5 wt.-% can be considered perfectly adequate from an economic point of view for the considered systems. Other particle sizes would result in different ratios of particles (number of flow additive particles per carrier particle), in different surface coverage levels and so in different flowabilities.
FIGURE 7. Flowability of Maltodextrin DE6 powder as carrier system as a function of the amount of flow additive.
In addition, SEM images of the samples were made. For the samples with 2.5 and 7.5 wt.-% flow additive, these can be found in Figure 8. The success of the coating is obvious. The flow additive particles adhere, on the surface of the carrier particles. They still seem to be uniformly distributed, indicating that the dry particle coating process has reached the final state (homogeneous distribution) and the mixing time was sufficient. The sample with 7.5 wt.-% flow additive also shows significantly more fine particles on the carrier surface, which are closer together. However, the carrier surface is not yet completely covered.
FIGURE 8. SEM pictures of maltodextrin DE6 with 2.5 and 7.5 wt.-% flow additives (A, B) and of whole milk powder with 2.5 wt.-% Lactose (C, D).
Figure 9 shows the results of all combinations of the carrier particles with the spray-dried flow additives (1 wt.-% in feed, pneumatic nozzle), each with 2.5 wt% addition. Through this comparison, the influence of the different raw materials on the effect as flow additive for different carrier systems shall be considered.
FIGURE 9. Flow functions of different food powders (carrier system), uncoated and coated with several flow additives.
It was found that all flow additives were able to improve the flowability of the carrier systems, but their effectiveness varied. Maltodextrin DE6 as a flow additive with its small particle size and narrow distribution range performed well in all cases and significantly reduced the unconfined yield strength at the same consolidation stress. The situation was similar with skim milk powder. Only the combination of skim milk powder as carrier and flow additive showed poor results. The effect of lactose was very different. While the flowability of the carrier systems maltodextrin DE6 and whole milk powder improved noticeably with lactose, the effect on skim milk powder and glucose syrup DE33 was less pronounced. Why the effect of all flow additives on glucose syrup DE33 was so low also remains obscure. The effect of the flow additives on whole milk powder, otherwise, was very high. This can be explained by the high content of surface free fat, which is partly responsible for the cohesive character of the powder. Due to the flow additive particles, which act as spacers between the carrier particles, no liquid bridges of free fat can form and the interparticle interactions are lower.
In general, it can be stated that the material composition of the flow additives seems not play a significant role in their effectiveness. Rather, it increases with decreasing average particle size and distribution width. This relationship is shown in Figure 10. There, the ffc,5 values are plotted as a function of the average particle size d50 for the example of maltodextrin DE 6 as a carrier system already discussed. Silica shows an extreme improvement in flowability. In addition to the significantly smaller particle size (approx. 150–250 nm agglomerates on the carrier surface) the amount used (1 wt.-%) represents the optimum (Kleinschmidt, 2015). As the aim was to use as few flow additives as possible, the results for the other (clean-label) systems will be discussed here for the addition of 2.5 wt.-%, although these are below the optimum quantity. Based on the particle size analysis, the d50 value for lactose is 43 µm. However, as already discussed, the primary particles found on the carrier particle surface are smaller. A clear trend can be seen for the other flow additives. As the particle size of the flow additive decreases, the flowability of the coated powders increases.
FIGURE 10. Flowability ffc,5 of maltodextrin DE6 coated with different flow additives as a function of flow additive particle size.
A power function can be well fitted as a trendline. Even if the changes in flowability are not too large, a clear trend can be recognized.
As a final aspect of the effectiveness of the flow additives, their influence on time consolidation (caking) was investigated (storage in a climate chamber at 40% r.H and 20°C). For the four carrier materials used, only for the whole milk powder a clear caking could be observed within a short storage time (≤72 h) and at temperatures below the glass transition. For this reason, the caking experiments were carried out using only whole milk powder as carrier system. Figure 11 shows the yield locus and time time yield loci of untreated and coated whole milk powder at a stress level of σ1 ≈ 4,000 Pa. Powdered food products are usually bagged and stored directly after production. With an average bulk density of circa 600–800 kg/m3, this 4,000 Pa roughly corresponds to the stress level that occurs during storage (see Schulze, 2007). The pure whole milk powder shows a significant increase in strength after only 1 day of storage. The flowability is reduced from 3.07 to 2.44. The behavior of the sample with 2.5 wt.-% flow additive is completely different. After 24 h, no changes could be measured here. Only after 2 days of storage was an increase in shear stress measurable. The corresponding time yield locus, however, is only slightly above the momentary yield locus, and the decrease in flowability from ffc = 3.86 to ffc = 3.20 is comparatively small.
The results are not sufficient to be able to assume with certainty that the flow additives have an anti-caking effect. However, it can be assumed that this is the case as long as the glass transition temperature is not exceeded.
The results show that it is possible to produce fine particles of less than 10 µm in size by spray drying soluble foods, which can then be used as flow additives. Their size is decisive for their effectiveness. In general, this increases with decreasing particle size. Compared with highly dispersed silica, the effect of the clean-label flow promoters is less pronounced, but significant improvements in flowability have nevertheless been measured.
A direct influence of the material composition of the flow additives on their effectiveness could not be found. However, in the case of the fat-containing whole milk powder, it was not possible to produce sufficiently small particles under the given process conditions. The spray-dried lactose also tended to agglomerate during drying due to its low glass transition temperature, whereby these agglomerates were partially disintegrated again by the dry particle coating process and thus a sufficient effect could be achieved. Nevertheless, short-chain carbohydrates with low glass transition temperatures and fatty materials as flow aids should be avoided as far as possible in order to avoid the problem of agglomeration.
In addition to improving flowability, an anticaking effect was also observed.
Overall, the concept of clean-label flow additive has great potential. In order to transfer this into industrial practice, it will be crucial to optimize their production, since spray drying of a 1 wt.-% solution is not economical. This can be done by optimizing the atomization to produce finer droplets from higher concentrated solutions or by pulverizing powdered food.
The original contributions presented in the study are included in the article/Supplementary material, further inquiries can be directed to the corresponding author.
SK: Conceptualization, Data curation, Formal Analysis, Funding acquisition, Investigation, Methodology, Project administration, Resources, Software, Supervision, Validation, Visualization, Writing–original draft, Writing–review and editing. IH: Investigation, Methodology, Writing–review and editing. TK: Formal Analysis, Funding acquisition, Project administration, Writing–review and editing.
The author(s) declare financial support was received for the research, authorship, and/or publication of this article. This work was supported by the FEI/AiF within the program for promoting the Industrial Collective Research (IGF) of the Federal Ministry of Economic Affairs and Climate Action (BMWK), based on a resolution of the German Parliament.
The authors declare that the research was conducted in the absence of any commercial or financial relationships that could be construed as a potential conflict of interest.
All claims expressed in this article are solely those of the authors and do not necessarily represent those of their affiliated organizations, or those of the publisher, the editors and the reviewers. Any product that may be evaluated in this article, or claim that may be made by its manufacturer, is not guaranteed or endorsed by the publisher.
ASTM (2008). Standard shear test method for bulk solids using the Schulze ring shear tester. United States: ASTM International.
Elversson, J., and Millqvist-Fureby, A. (2005). Particle size and density in spray drying—effects of carbohydrate properties. J. Pharm. Sci. 94 (9), 2049–2060. doi:10.1002/jps.20418
Hazlett, R., Schmidmeier, C., and O’Mahony, J. A. (2021). Approaches for improving the flowability of high-protein dairy powders post spray drying – a review. Powder Technol. 388, 26–40. doi:10.1016/j.powtec.2021.03.021
Hersey, J. A. (1975). Ordered mixing: a new concept in powder mixing practice. Powder Technol. 11 (1), 41–44. doi:10.1016/0032-5910(75)80021-0
Jenike, A. W. (1964). Storage and flow of solids. Bulletin No. 116 of the Utah engineering experiment station. Salt Lake City - Utah: Utah Engineering Experiment Station.
Kleinschmidt, S. (2015). “Improvement of the flowability of fine cohesive powders by nano scaled flow additives,”. dissertation thesis (Magdeburg (Germany): Otto-von-Guericke-University).
Krupp, H. (1967). Particle adhesion theory and experiment. Adv. Colloid Interface Sci. 1 (2), 111–239. doi:10.1016/0001-8686(67)80004-6
Lin, Q., Rudolph, V., Weigl, B., and Earl, A. (2004). Interparticle van Der Waals force in powder flowability and compactibility. Int. J. Pharm. 280 (1–2), 77–93. doi:10.1016/j.ijpharm.2004.05.001
Mei, R., Shang, H., Klausner, J. F., and Kallman, E. (1997). A contact model for the effect of particle coating on improving the flowability of cohesive powders. KONA Powder Part. J. 15, 132–141. doi:10.14356/kona.1997017
Molerus, O. (1978). Effect of interparticle cohesive forces on the flow behaviour of powders. Powder Technol. 20 (2), 161–175. doi:10.1016/0032-5910(78)80045-X
Palzer, S. (2007). Chapter 13 Agglomeration of dehydrated consumer foods. Handb. Powder Technol. 11, 591–671. doi:10.1016/S0167-3785(07)80048-0
Schulze, D. (1994). Entwicklung und Anwendung eines neuartigen Ringschergerätes. Aufbereitungstechnik 35, 524–535.
Schulze, D. (1995). “Appropriate devices for the measurement of flow properties for silo design and quality control,” in Preprints PARTEC 95 (Nürnberg: IMVU), 45–56.
Schulze, D. (1996). Flowability and time consolidation measurements using a ring shear tester. Powder Handl. Process. 8 (3), 221–226.
Schulze, D. (2007). Powders and bulk solids. Berlin, Heidelberg: Springer. doi:10.1007/978-3-540-73768-1
Schulze, D., Heinrici, H., and Zetzener, H. (2001). The ring shear tester as a valuable tool for silo design and powder characterization. Powder Handl. Process. 13, 19–24.
Tomas, J. (2004). Fundamentals of cohesive powder consolidation and flow. Granul. Matter 6 (2–3), 75–86. doi:10.1007/s10035-004-0167-9
Tomas, J., and Kleinschmidt, S. (2009). Improvement of flowability of fine cohesive powders by flow additives. Chem. Eng. Technol. 32, 1470–1483. doi:10.1002/ceat.200900173
Verlinden, A. (2000). Experimental assessement of shear testers for measuring flow properties of bulk solids. dissertation thesis (Bradford: UK: University of Bradford).
Vicente, J., Pinto, J., Menezes, J., and Gaspar, F. (2013). Fundamental analysis of particle formation in spray drying. Powder Technol. 247, 1–7. doi:10.1016/j.powtec.2013.06.038
Winkler, H. C., Kornprobst, J., Wick, P., Von Moos, L. M., Trantakis, I., Schraner, E. M., et al. (2017). MyD88-dependent pro-interleukin-1β induction in dendritic cells exposed to food-grade synthetic amorphous silica. Part. Fibre Toxicol. 14, 21. doi:10.1186/s12989-017-0202-8
Xie, H.-Y. (1997). The role of interparticle forces in the fluidization of fine particles. Powder Technol. 94 (2), 99–108. doi:10.1016/S0032-5910(97)03270-1
Yoo, N.-K., Youn, S.-M., and Choi, S.-J. (2022). Oral toxicokinetics, tissue distribution, and 28-day oral toxicity of two differently manufactured food additive silicon dioxides. Int. J. Mol. Sci. 23, 4023. doi:10.3390/ijms23074023
Zafar, U., Vivacqua, V., Calvert, G., Ghadiri, M., and Cleaver, J. A. S. (2017). A review of bulk powder caking. Powder Technol. 313, 389–401. doi:10.1016/j.powtec.2017.02.024
Zickgraf, F. M., Murali, A., and Landsiedel, R. (2023). Engineered nanomaterials and the microbiome: implications for human health. Curr. Opin. Toxicol. 35, 100429. doi:10.1016/j.cotox.2023.100429
Keywords: flow additives, anti-caking, dry particle coating, flowability, cohesive powders, food powders
Citation: Kleinschmidt S, Heide I and Kleinschmidt T (2024) Ultrafine food powders as clean-label flow additives. Front. Chem. Eng. 5:1307309. doi: 10.3389/fceng.2023.1307309
Received: 04 October 2023; Accepted: 27 December 2023;
Published: 23 January 2024.
Edited by:
Kunn Hadinoto, Nanyang Technological University, SingaporeReviewed by:
Katherine Kho, Indonesia International Institute for Life-Sciences (i3L), IndonesiaCopyright © 2024 Kleinschmidt, Heide and Kleinschmidt. This is an open-access article distributed under the terms of the Creative Commons Attribution License (CC BY). The use, distribution or reproduction in other forums is permitted, provided the original author(s) and the copyright owner(s) are credited and that the original publication in this journal is cited, in accordance with accepted academic practice. No use, distribution or reproduction is permitted which does not comply with these terms.
*Correspondence: Sebastian Kleinschmidt, c2ViYXN0aWFuLmtsZWluc2NobWlkdEBocy1hbmhhbHQuZGU=
Disclaimer: All claims expressed in this article are solely those of the authors and do not necessarily represent those of their affiliated organizations, or those of the publisher, the editors and the reviewers. Any product that may be evaluated in this article or claim that may be made by its manufacturer is not guaranteed or endorsed by the publisher.
Research integrity at Frontiers
Learn more about the work of our research integrity team to safeguard the quality of each article we publish.