- 1School of Chemistry and Chemical Engineering, University of Surrey, Guildford, United Kingdom
- 2UK Atomic Energy Authority, Culham Science Centre, Abingdon, United Kingdom
- 3Department of Chemical Engineering, University College London, London, United Kingdom
In this paper, the transesterification reaction of waste cooking oil (WCO) with methanol using KOH as catalyst to produce biodiesel was performed in a micro-reactor (1 mm ID) using a cross-flow inlet configuration. The effects of different variables such as, methanol-to-oil molar ratio, temperature, catalyst concentration, and residence time on biodiesel yield, as well as the associated flow patterns during the transesterification reaction were investigated and the relationship between flow characteristics and mass transfer performance of the system was examined. The work reveals important aspects and the links between the hydrodynamic behaviour and the mass transfer performance of the intensified reactors. It was found that high yield (>90%) of biodiesel can be achieved in one-stage reaction using cross-flow micro-reactors for a wide range of conditions, i.e., methanol-to-oil molar ratio: 8–14, catalyst concentration: 1.4%–1.8% w/w, temperature: 55°C–60°C, and residence times: 55–75 s.
1 Introduction
In recent years, the development of alternative and environmentally friendly fuels has received increased attention as a result of the limited fossil fuel resources and the need to reduce greenhouse gas emissions (Agency, 2018). The global energy mix, however, is still dominated by fossil fuels, where oil, coal, and natural gas account for around 84% of the global energy and 75% of the global greenhouse gas emissions (Ritchie et al., 2020). Biofuels, that are produced from bio-based materials, are an eco-friendly, renewable energy source, and while other renewable alternatives are still under development, they present one of the best candidates to replace fossil fuels. Despite their uptake, there are still challenges associated with production costs, availability, and ethical considerations as biofuel crops compete for arable land with food crops. From the different biofuel products, biodiesel has emerged as one of the most promising options to meet our energy challenges, especially in the transportation sectors (Knothe et al., 2015; Hajjari et al., 2017). The majority of the current commercial biodiesel production is carried out via a transesterification reaction between the triglycerides in the biomass and an alcohol in the presence of an acid or base catalyst (Noureddini and Zhu, 1997; Kumar and Sharma, 2016; Pontes et al., 2016). Production of biodiesel is a multi-parametric process, and several variables are involved. In addition, the simultaneous presence of different phenomena, such as mixing, heat and mass transfer, phase equilibrium changes, and main and side reactions, makes the production of biodiesel complex, which has to be precisely controlled (Qiu et al., 2010).
In the last decade, intensified approaches have been suggested as promising alternatives to batch processing (Kant Bhatia et al., 2021; Bashir et al., 2022). Small channel flow reactors in particular have high heat and mass transfer rates, because of the high surface area/volume ratios and the thin films that form which reduce the diffusion distances (Banerjee et al., 2019). As a result, residence times can be decreased and side reactions can be avoided, thus increasing the biodiesel yield (Tsaoulidis and Angeli, 2015; Tsaoulidis and Angeli, 2016). Furthermore, it has been shown that the liquid phases can be promptly separated at the end of the small channels by exploiting their different wettabilities with the channel walls or membranes (Tsaoulidis et al., 2013). Most of the works on biodiesel production in small channels are summarized in six recent reviews (Franjo et al., 2018; Madhawan et al., 2018; Tiwari et al., 2018; Banerjee et al., 2019; Natarajan et al., 2019; Thangarasu et al., 2022), and focus mainly on either first (edible oil-crops) or second (non-edible crops) generation feedstocks as shown in Table 1.
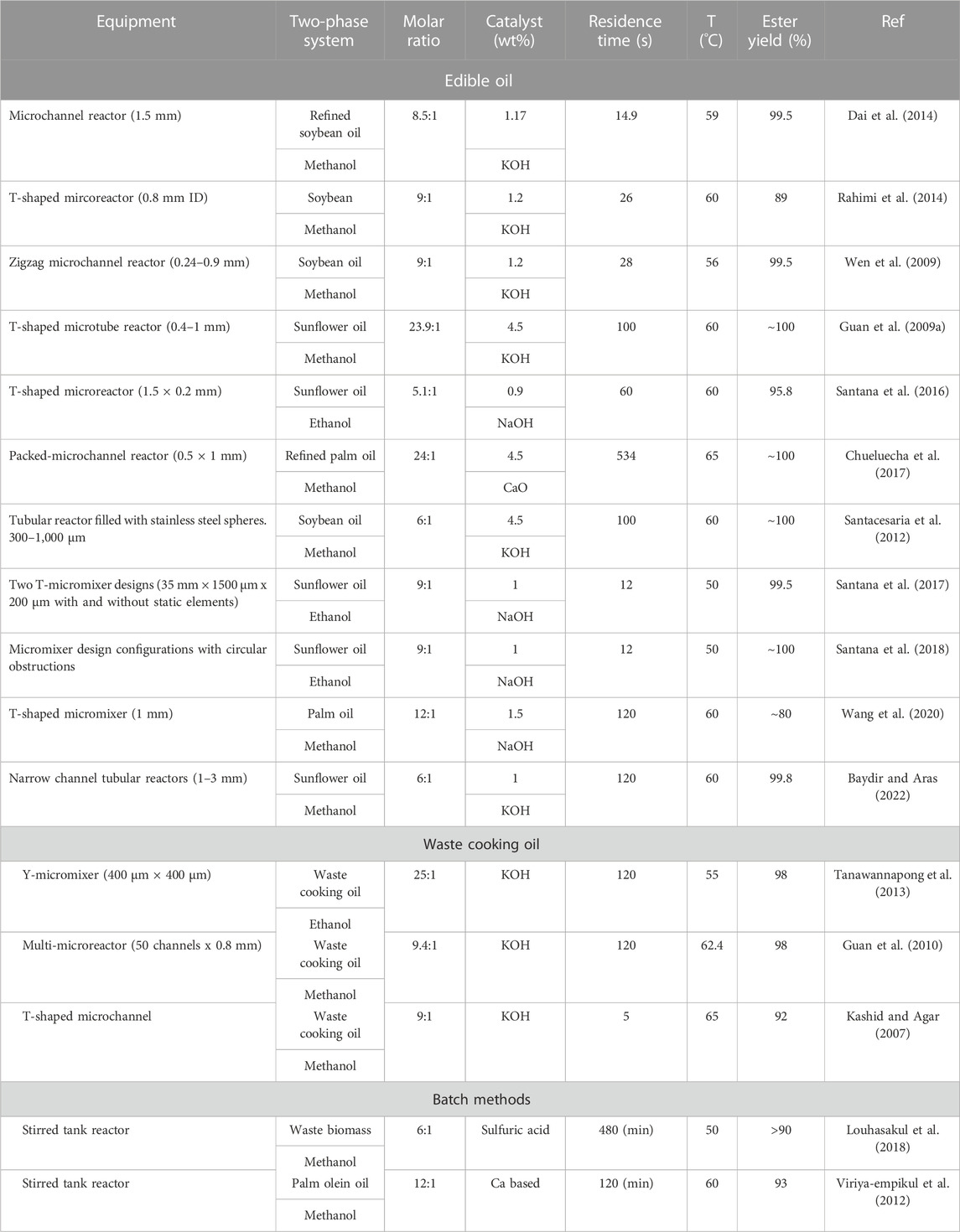
TABLE 1. Continuous biodiesel production from vegetable and waste cooking oil using micro-reactors and conventional reactors.
The effect of alcohol-to-oil molar ratio was found to be one of the most important parameters for the conversion to biodiesel, irrespective of the microchannel type and configuration (Guan et al., 2009a; Wen et al., 2009; Dai et al., 2014; Rahimi et al., 2014). For a reversible reaction, and unless the products are removed from the process in situ, an excess of alcohol (methanol or ethanol) is required. In most of the studies, the increase of the biodiesel yield was linear when the methanol-to-oil molar ratio increased from 3:1 to 9:1, while it decreased at higher moral ratios. The decrease is attributed to different reasons, such as, methanol acting as an emulsifier that could cause a part of glycerol to remain in the biodiesel phase (Leung and Guo, 2006) or changes in the flow patterns. However, depending on the type and concentration of catalyst, different molar ratios have been reported to result in maximum yield (Table 1). The effect of temperature (Sun et al., 2008) has also been widely investigated. Most of the investigations were focused on temperatures below the normal boiling point of alcohol (methanol in most of the cases). The temperature also affects the viscosity of the oil and the interfacial tension between the oil and the methanol. In small channels, flow patterns are highly dependent on the physical properties of the two fluids, and temperature changes will result in changes in the flow patterns (Tsaoulidis et al., 2013). Moreover, at elevated temperatures the rate of saponification could also be accelerated, which will hinder the formation of biodiesel. Different mixing configurations have been investigated, including the common Y- and T-junctions to more complex ones such as omega, tesla, and zig-zag inlets (Martinez Arias et al., 2012). Geometric modifications in the channels affect the direction of flow, create disturbances and form vortices which increase the mass transfer and the rate of biodiesel synthesis (Santana et al., 2017). From the different patterns that form during two-phase flow in small channels, plug/segmented flow has two orders of magnitude higher interfacial area to volume ratio than parallel flow, enables the easy separation of the products at the end of the channel, offers high radial and reduced axial mixing, resulting in uniform residence times, and can easily be modelled (Jensen, 2017).
Although intensified reactors for biofuel production from crops showed higher yields in shorter residence times compared to conventional ones, the ethical considerations still remain. Waste cooking oil (WCO) is a very promising alternative that does not affect the food chain directly. It has been estimated that around 29 million tons of waste cooking oil are generated per year (Supple et al., 2002; Patil et al., 2012). Most recently, Paiz et al. (2022) (Paiz et al., 2022) performed an experimental parametric study on biodiesel synthesis from WCO using ethanol and KOH in a microreactor (Y-mixer, 400 μm × 400 μm) that was integrated with a heat exchanger. They reported a biodiesel conversion of 98% in 2 min, at experimental conditions of 55°C, 25:1 ethanol-to-oil molar ration, and 1.9 wt% KOH. Mohadesi et al. (2019) (Mohadesi et al., 2019) investigated the production of biodiesel from waste cooking oil in a design consisting of 50 microreactors of 0.8 mm ID each. According to their findings, the system operated at optimum conditions of 9.4:1 methanol-to-oil molar ratio, 1.16 wt% KOH, 120 s residence time, and 62.4°C temperature to produce biodiesel of ∼98% methyl ester. Aghel et al. (2017) (Aghel et al., 2018) reported the effects of different co-solvents (n-hexane and tetrahydrofuran) on the transesterification of waste cooking oil in a 0.8 mm microtube using a T-shaped inlet. They used kettle limescale as a heterogeneous catalyst, and achieved ∼97% biodiesel purity (Faty acid methyl ester, FAME%) in 10 min. Elkady et al. (2015) (Elkady et al., 2015) produced biodiesel from waste vegetable oil using a “KM-micromixer” of 0.2 mm ID with 1 wt% NaOH as catalyst and investigated the effect of different parameters in the presence of a co-solvent (tetrahydrofuran). Mazubert et al. (2014) (Mazubert et al., 2014) investigated the waste cooking oil transformation in a microstructured “flow reactor”™ provided by Corning and obtained 96% ester yield in 1.4 min at 97°C. Tanawannapong et al. (2013) (Tanawannapong et al., 2013) studied the effects of different parameters on the reduction of the acid value of WCO by esterification reaction (acid-catalysed) in a T-shaped microtube reactor, followed by a second transesterification reaction for constant conditions of KOH concentration 1 wt%, reaction temperature of 65°C and reaction time of 5 s, and obtained biodiesel with ∼92% methyl ester content. Guan et al. (2009) (Guan et al., 2010) used a simulant waste cooking oil by mixing sunflower oil with water or oleic acid, and investigated the conversion to biodiesel, production of soap due to the presence of water, and changes in flow patterns. Biodiesel yield reached 89% at 252 s in different microchannels ranging from 0.46 to 0.96 mm internal diameter.
Current research mainly focuses on the development of heterogeneous catalysts to develop environmentally friendly biodiesel production processes, whilst in terms of intensification most of the work is focused on the use of vegetable oils. The potential of process intensification in microchannels in conjunction with the utilization of WCO needs further studies, to identify the effect of flow transitions on the reaction kinetics and on biodiesel yield (Maddikeri et al., 2012). The development of a continuous sustainable process that will reduce production costs, increase product uniformity for large-scale production, and utilise waste biomass is yet anticipated. Based on the research performed so far, it becomes apparent that biodiesel production in small channels is largely affected by the flow patterns before and during the formation of the new products, which are difficult but crucial to control. In this work, the effects of different parameters on the flow pattern formation and subsequently on the biodiesel yield of a viscous waste cooking oil are investigated, using KOH as a catalyst. A cross-flow mixer is used to obtain regular plug flow patterns with high interfacial area to volume ratio that will enhance interfacial mass transfer. The cross-flow mixer is also compared against a commonly used T-junction inlet. Biodiesel yield is investigated for a wide range of parameters, including temperature, methanol-to-oil molar ratio, residence time, catalyst concentration and mixing intensity.
2 Materials, experimental setup, and procedure
2.1 Materials
Processed waste cooking oil (WCO) was obtained from Greenergy. The acid value was 0.02 mg KOH/g, the saponification value was 194 mg KOH/g and the density was 912 kg/m3. Methanol (purity >99.5%), potassium hydroxide, heptane, and internal standard methyl heptadecanoate (purity >99.5%) were purchased from Sigma-Aldrich.
2.2 Experimental set up and methodology
A schematic of the test rig is shown in Figure 1. The polar solution was first prepared by dissolving a specified amount of the catalyst (KOH) into methanol, whilst prior to each experiment the methanol/KOH solution was degassed. Degassing was performed to avoid the formation of bubbles at high temperatures, which would disturb the flow pattern and affect mass transfer. The amount of catalyst used was calculated based on the waste cooking oil feed rate. Two high-precision pumps (Harvard PHD Ultra) were used to feed separately the methanol/KOH and the waste cooking oil into the small channel reactor. The two phases were introduced in the reactor through a cross-shaped mixer with all branches having the same internal diameter of 1 mm, which was also equal to the diameter of the main test section. The mixer and the test section were made of FEP. The mixer and the test section, which was coiled (Figure 1), were immersed in a temperature controlled (within ±0.1°C) water bath. The viscosity of the waste cooking oil was affected by changes of the temperature and the results are shown in Figure 2. The viscosity was measured using a rheometer (Anton Paar, MCR 302). The residence time was controlled by changing the length of the reaction channel, rather than adjusting the flow rates of the two phases, to ensure that mixing intensity and flow patterns remained the same at different residence times. The end of the reactor was placed in an ice bath to cease the reaction and the products were collected in a phial and the phases (crude biodiesel phase and glycerol) were separated by gravity (Figure 1). The biodiesel samples were washed with warm water to remove any residuals, and then dried, before they were analysed. For the visualization experiments the flow patterns were obtained at different points along the microreactor coil using a CMOS high-speed camera (Phantom V1212) with maximum resolution of 1,280 × 800 at 12,600 fps, equipped with a magnification lens (×12, LEICA Monozoom 7 optical system). High-speed images were used to estimate surface area to volume ratio during plug flow from the geometric characteristics of the plugs and slugs formed (Di Miceli Raimondi et al., 2008).
2.3 Analytical methods
The fatty acid methyl ester (FAME) content in the biodiesel samples at the end of the reactor was analysed by gas chromatography (Agilent 6,890 Series GC), using a fused silica capillary column (Stabilwax, 30 m × 0.25 mm × 0.25 μm) and a flame ionization detector (FID). Methyl heptadecanoate was used as the internal standard for the GC. The percentage of methyl ester content (FAME) in the samples was expressed following standard procedure (EN 14103) (T.C.C.T. 307, 2011).
where ∑A is the total peak area, AI is the peak area of the internal standard (methyl heptadecanoate), CI is the fixed concentration of the internal standard solution (mg/mL), VI is the volume of the internal standard solution used (mL), and m is the mass of sample (mg). For each set of conditions, the FAME content was measured a number of times to ensure that the standard deviation of 4 consecutive measurements was below 3%.
The biodiesel recovery was defined as the ratio of the mass of washed and dried biodiesel phase (after the separation from glycerol) to the initial mass of WCO used.
The biodiesel yield was then defined as follows:
2.4 Experimental design
The production of biodiesel from waste cooking oil depends on various parameters and their interactions. The effects of the main operational variables, such methanol-to-oil molar ratio, reaction temperature, residence time, catalyst concentration, and mixing intensity were investigated. The lower and upper limits of the experimental parameters are summarized in Table 2. The experiments were conducted 3 times for each set of conditions and an average value was used.
3 Results and discussion
One of the most significant variables affecting the transesterification reaction is the methanol-to-oil molar ratio. Since transesterification of waste cooking oil is essentially reversible in nature, the removal of products after formation can help reduce the amount of excess alcohol required for the reaction equilibrium to remain shifted towards the product formation (Pontes et al., 2016). In small channels, changes of the molar ratio can also affect the flow pattern. When two immiscible liquids, such as methanol and waste cooking oil, flow in a microchannel, the flow patterns formed can vary from separated to dispersed. Segmented (plug) flow in particular, enhances mass transfer, has large specific interfacial areas and can occur for a wide range of flowrates. This pattern is therefore ideal for the first step of the transesterification reaction between methanol and waste cooking oil, which is the mass transfer limited step (Kashid et al., 2005; Kashid and Agar, 2007; van Steijn et al., 2007; Tsaoulidis and Angeli, 2016). In the current system, methanol is the dispersed phase and moves as droplets with size larger than the diameter of the channel, separated by the WCO continuous phase.
In Figure 3 the transition is shown from the WCO and methanol phases to the biodiesel and glycerol ones along the microreactor coil. Changes on the flow pattern during the course of the reaction are expected since the initial reactants will eventually convert to products of different properties (viscosity and interfacial tension). However, it is very important to obtain initial regular plug flow patterns with high interfacial area to volume ratio especially in the beginning of the channel, where the mass transfer limited reaction of initial WCO and methanol (indicated with the red line in Figure 3A) takes place. The FAME that is produced in the first reaction step is soluble in both reactants and acts as a co-solvent, which enhances miscibility. The glycerol that forms later is almost insoluble to FAME and to WCO, but soluble to methanol. As the plugs progress, small ones coalesce (Figure 3B). In addition, the compositions of the phases change, and this seems to affect the plug shape and size. The plugs can coalesce (Figures 3B–D) and later can break again, giving smaller plugs and daughter droplets (Figure 3E). The diglycerides and monoglycerides that are produced during the reaction serve as emulsifiers to stabilize the surface of these glycerol/methanol plugs (Boocock et al., 1998; Darnoko and Cheryan, 2000). Similar flow behaviour was observed also in systems where sunflower oil was used; in those systems a homogeneous mixture was transformed to a dispersed flow of fine droplets which gradually aggregated to form larger ones (Guan et al., 2009b).
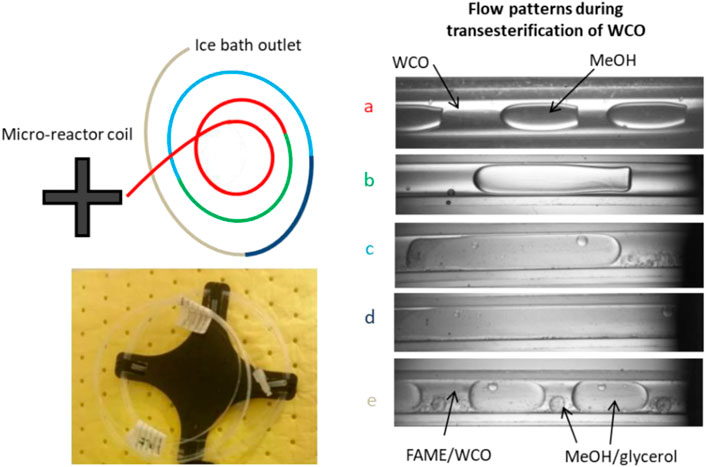
FIGURE 3. Flow pattern transition in a micro-reactor coil during transesterification of WCO to biodiesel. (Methanol-to-oil molar ratio, 12; Temperature, 60°C; catalyst concentration, 1.4 %w/w, residence time, 1 min; Qtot=60 cm3/h). (A–E) correspond to the flow pattern observed to each specific section of the reactor indicated by colour.
In Figure 4, the different flow configurations of WCO and methanol as a function of total flow rate, Qtot (sum of QWCO and QMeOH), and methanol-to-oil molar ratio at a constant temperature of 60°C, are shown. These flow patterns correspond to the initial part of the micro-reactor coil. At low total flowrates, plug flow forms for the whole range of methanol-to-oil molar ratios. By increasing the total flow rate, a jet forms at the mixing zone which then develops to separated flow further downstream. In the separated flow pattern, the mixing intensity within each phase as well as the interfacial area decreased, thus decreasing the overall mass transfer. An intermittent pattern was also observed where the flow consisted of short and elongated plugs (irregular flow). In Figure 5, the surface area to volume ratio as a function of the molar ratio and two representative cases at high and low methanol-to-oil molar ratio during plug flow are shown. At high molar ratio the number of dispersed segments was increased, which resulted in increased interfacial area available for mass transfer. For example, by increasing the methanol-to-oil molar ratio from 6 to 12 the interfacial area to volume ratio increased from 1,300 m2/m3 to 2,400 m2/m3.
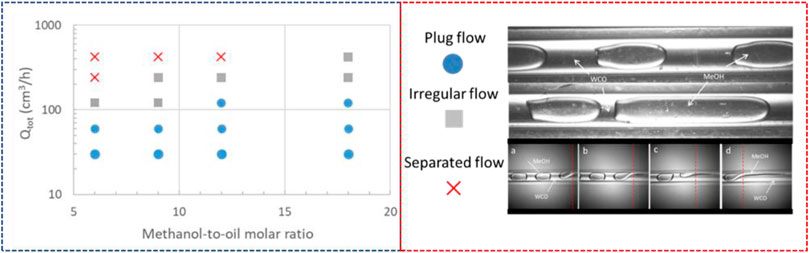
FIGURE 4. Flow pattern map of WCO-methanol two-phase flow at the initial part of the channel using a cross-flow mixer at 60°C (Catalyst concentration at 1.4% w/w). In “separated flow” image, (A–D) subscripts show the evolution from plug to separated flow.
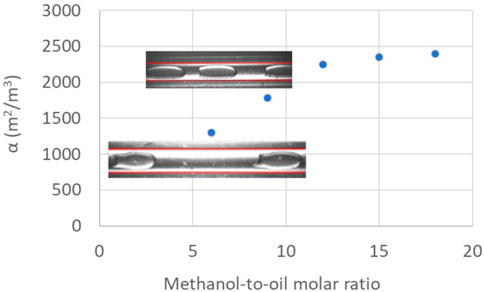
FIGURE 5. Interfacial area-to-volume ratio as a function of methanol-to-oil flow rate ratio during plug flow (Qtot=60 cm3/h).
In Figure 6, the biodiesel yield is plotted as a function of methanol-to-oil molar ratio and catalyst concentration at constant temperature (60°C) and residence time (70 s). As the molar ratio increases to intermediate values, biodiesel yield increases and then decreases again for higher molar ratios. The effect of catalyst concnetration, however, has a more complex effect; at low molar ratio, biodiesel yield increases by increasing catalyst concentration, but as the molar ratio increases, biodiesel yield increases and then decreases with catalyst concentration. It can be seen that at the lower limit of both parameters, i.e., methanol-to-oil molar ratio (6) or catalyst concentration (0.6% w/w), there is a positive effect on biodiesel yield when keeping one parameter constast and increasing the other. At low methanol-to-oil molar ratios, biodiesel yield did not exceed 80% regardless of catalyst concentration. At the highest methanol-to-oil molar ratio used, the catalyst concentration did not improve the biodiesel yield significantly. At the lowest catalyst concentration of 0.6% w/w, the biodiesel yield for the different molar ratios varied between 50% and 60%, indicating that the effect of the molar ratio is weak. The increase in biodiesel yield is more pronounced by increasing the catalyst concentration from 0.6% to 1.4% w/w, whilst further increase to 2.4% w/w showed only a slight improvement on biodiesel yield. As shown in Figure 4, at high molar ratios, more methanol segments are formed initially, which means that the interfacial area available for mass transfer is increased; this seems to improve the biodiesel yield. However, it was also observed that along the channel length, two or more consecutive plugs coalesce and form bigger plugs (Figure 3B), and as a result, the mass transfer efficiency decreases. In addition, the increased amount of methanol combined with the increased amount of catalyst acting as emulsifier, which promoted the mixing of the products i.e., glycerol and biodiesel (Boocock et al., 1998). This hinders the separation of the two phases and increases the amount of free glycerol in biodiesel above the acceptable levels (0.02% w/w).
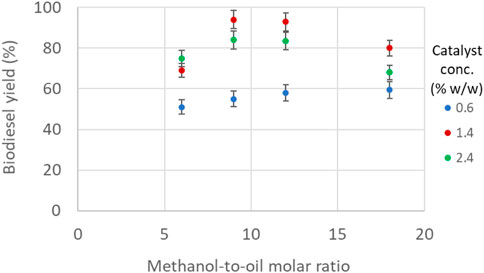
FIGURE 6. Biodiesel yield as a function of methanol-to-oil molar ratio and catalyst concentration (constant temperature 60°C, constant residence time 70 s).
To investigate the effect of methanol-to-oil molar ratio on biodiesel production at different residence times, reaction temperature and catalyst concentration were kept constant at 60°C and at 1.4% w/w, respectively, where the highest biodiesel yields were achieved for a wide range of methanol-to-oil molar ratios (Figure 6). As can be seen in Figure 7, by increasing the residence time the biodiesel yield increased for all methanol-to-oil molar ratios. However, at short residence times the biodiesel yield cannot reach values higher than 70%. Yields higher than 90% were achieved for intermediate values of molar ratios and residence times higher than 70 s.
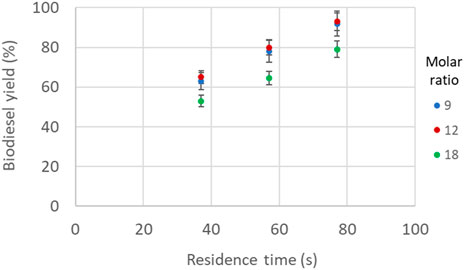
FIGURE 7. Biodiesel yield as a function of methanol-to-oil molar ratio and residence time (constant temperature 60°C, constant catalyst concentration 1.4% w/w).
The transesterification process is an endothermic reaction and will be affected by the temperature (Xiao et al., 2010). The flow pattern was also affected by the temperature. At low temperatures, the regular plug flow pattern shown in Figure 3A was established for a longer part of the reactor coil. This is attributed to the fact that the temperature affects the viscosity of the WCO (see Figure 2), and the flow configuration, whilst the lower temperature did not improve the reaction rate and thus the formation of the products. Thus, at low temperature the transition from two-phase to single phase and reverse (Figures 3C–E) was not observed. The effect of temperature was investigated in the range of 40°C–60°C and is shown in Figures 8A, B. In general, it can be seen that the biodiesel yield increases significantly by increasing the temperature from 40°C to 60°C. For a constant residence time, the highest biodiesel yield (>90%) was obtained for temperatures beyond 50°C, and for molar ratios ranging from 10 to 15. For a constant molar ratio, it can be seen in Figure 8B that the effect of residence time is less pronounced as the temperature increases. For temperatures higher than 50°C, biodiesel yield higher than 80% can be achieved for residence times longer than 40 s.
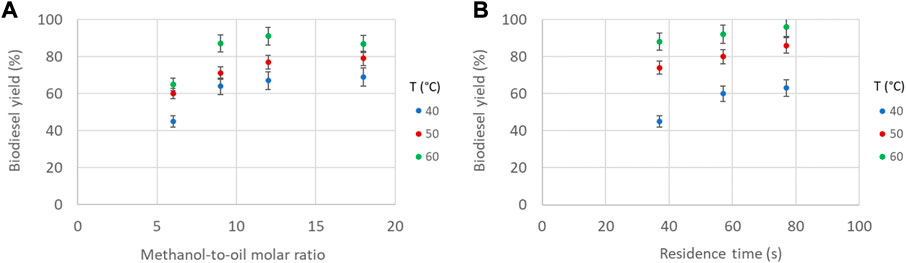
FIGURE 8. Biodiesel yield as a function of (A) methanol-to-oil molar ratio and temperature (constant residence time 70 s, constant catalyst concentration 1.4% w/w) and (B) residence time and temperature. (Constant molar ratio 10, constant catalyst concentration 1.8% w/w).
The effects of residence time and catalyst concentration on biodiesel yield at a constant temperature and molar ratio are shown in Figure 9. It can be seen that for the conditions shown the residence time does not have as significant impact as the catalyst concentration. At catalyst concentration 0.6% the residence time has almost no effect, while the biodiesel yield does not exceed 55%. By increasing the catalyst concentration, the effect of residence time becomes more apparent, where longer residence times result in higher biodiesel yield. For catalyst concentrations between 1.2% and 2% w/w, the biodiesel yield is in the range of 80%–90% for residence times up to 50 s, while at longer residence times, the biodiesel yield reached values higher than 90%.
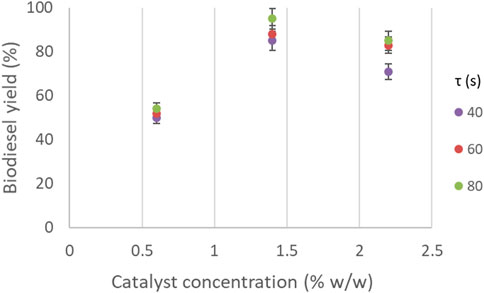
FIGURE 9. Biodiesel yield as a function of residence time and catalyst concentration. (Constant molar ratio 10, constant temperature 60°C).
The effect of the mixing zone configuration on the biodiesel yield was also investigated and shown in Figure 10 for different total flowrates. To investigate the effect of the mixing zone the cross-flow mixer was compared with the widely used T-junction at the same conditions. In both mixers the side branches had the same diameter (1 mm) as the main channel. For both configurations, the WCO was introduced from the branch that is on the same axis as the main channel (Figure 11). As can be observed from Figure 10, the biodiesel yield is higher when the cross-flow mixer is used for the whole range of total flowrates investigated. At low flow rates, up to 60 cm3/h, both mixing zones produced plug flow pattern that was stable along the tube. However, with the cross-flow mixer, smaller plugs were formed compared to the T-junction, which resulted in higher interfacial area-to-volume ratio and therefore higher overall mass transfer. By increasing the flow rate, for both mixers a decrease in the biodiesel yield was observed. This was attributed to the change of the flow pattern as indicated in Figure 4 from plug to separated flow. With the cross-flow mixer, plug flow formed at flow rates up to 120 cm3/h, whilst in the T-junction a stable plug flow was observed for flow rates only up to 70 cm3/h. Beyond those flowrates, a jet was formed, which initially resulted in plug flow but progressively the jet propagated along the channel resulting in a separated flow pattern (Figure 4C) where mass transfer rates are reduced. Similar observations were made by Borovinskaya et al. (2018), who investigated the patterns of ethanol - soybean oil two-phase flow using a T-junction.

FIGURE 10. Effect of total flow rate on the biodiesel yield. (Molar ratio 10, temperature 60°C, residence time 1 min, catalyst concentration 1.6% w/w).
4 Conclusion
In this work biodiesel was produced by transesterification of waste cooking oil with methanol/KOH solutions using a micro-reactor. The effects of methanol-to-oil ratio, temperature, catalyst concentration, and residence time on biodiesel yield (conversion efficiency) were investigated. The explanations were further enhanced using hydrodynamic observations. In addition, the effect of mixing intensity was also investigated. It would be difficult to give a clear verdict on the best combination of the experimental variables to achieve the highest biodiesel yield, since the total flow that affects the flow rates should also be factored in the parametric studies. The highest biodiesel yield (96.4%) was obtained at 80 s, for methanol-to-oil molar ratio 10, and catalyst concentration 1.4% w/w. In general, the experimental data showed that the biodiesel yield could reach levels above 90% for, methanol-to-oil molar ratio: 8–14, catalyst concentration: 1.4%–1.8% w/w, temperature: 55°C–60°C, and residence times: 55–75 s. It was found that biodiesel yield increases and then decreases when the methanol-to-oil molar ratio and the catalyst concentration increase. The yield increases with the temperature and the residence time. Control of the flow pattern could increase biodiesel yield significantly, since it was observed that biodiesel yield was affected by the flow pattern. To achieve increased throughput that can meet industrial demands, scale out (or numbering up) should be combined with increased channel size (scale-up), as otherwise it would result to reactor designs that include a large number of very small channels and high pressure drops.
Data availability statement
The raw data supporting the conclusions of this article will be made available by the authors, without undue reservation.
Author contributions
Conceptualization, DT and PA; Methodology, DT; Experimental studies, DT and EG-O; Formal analysis, DT; Writing and editing, DT, EG-O, and PA. All authors have read and agreed to the published version of the manuscript.
Funding
The project was supported by Greenergy Ltd by supplying the waste cooking oil, contributing to the analysis of the samples, and providing technical feedback. The project was also supported by an EPSRC Impact Acceleration Account (EP/R511638/1), an EPSRC grant on Feasibility Studies in Energy (EP/P034101/1), and the EU Horizon 2020 Research and Innovation Programme IProPBio under the Marie Sklodowska-Curie grant agreement 778168.
Conflict of interest
The authors declare that the research was conducted in the absence of any commercial or financial relationships that could be construed as a potential conflict of interest.
Publisher’s note
All claims expressed in this article are solely those of the authors and do not necessarily represent those of their affiliated organizations, or those of the publisher, the editors and the reviewers. Any product that may be evaluated in this article, or claim that may be made by its manufacturer, is not guaranteed or endorsed by the publisher.
References
Aghel, B., Mohadesi, M., and Sahraei, S. (2018). Effect of different cosolvents on transesterification of waste cooking oil in a microreactor. Chem. Eng. Technol. 41 (3), 598–605. doi:10.1002/ceat.201700025
Banerjee, R., Kumar, S. P. J., Mehendale, N., Sevda, S., and Garlapati, V. K. (2019). Intervention of microfluidics in biofuel and bioenergy sectors: Technological considerations and future prospects. Renew. Sustain. Energy Rev. 101, 548–558. doi:10.1016/j.rser.2018.11.040
Bashir, M. A., Wu, S., Zhu, J., Krosuri, A., Khan, M. U., and Ndeddy Aka, R. J. (2022). Recent development of advanced processing technologies for biodiesel production: A critical review. Fuel Process. Technol. 227, 107120. doi:10.1016/j.fuproc.2021.107120
Baydir, E., and Aras, O. (2022). Increasing biodiesel production yield in narrow channel tubular reactors. Chem. Eng. Process. - Process Intensif. 170, 108719. doi:10.1016/j.cep.2021.108719
Boocock, D. G., Konar, S. K., Mao, V., Lee, C., and Buligan, S. (1998). Fast formation of high-purity methyl esters from vegetable oils. J. Am. Oil Chemists' Soc. 75 (12), 1167–1172. doi:10.1007/s11746-998-0307-1
Chueluecha, N., Kaewchada, A., and Jaree, A. (2017). Biodiesel synthesis using heterogeneous catalyst in a packed-microchannel. Energy Convers. Manag. 141, 145–154. doi:10.1016/j.enconman.2016.07.020
Dai, J.-Y., Li, D.-Y., Zhao, Y.-C., and Xiu, Z.-L. (2014). Statistical optimization for biodiesel production from soybean oil in a microchannel reactor. Industrial Eng. Chem. Res. 53 (22), 9325–9330. doi:10.1021/ie4037005
Darnoko, D., and Cheryan, M. (2000). Kinetics of palm oil transesterification in a batch reactor. J. Am. Oil Chemists' Soc. 77 (12), 1263–1267. doi:10.1007/s11746-000-0198-y
Di Miceli Raimondi, N., Prat, L., Gourdon, C., and Cognet, P. (2008). Direct numerical simulations of mass transfer in square microchannels for liquid–liquid slug flow. Chem. Eng. Sci. 63 (22), 5522–5530. doi:10.1016/j.ces.2008.07.025
Elkady, M., Zaatout, A., and Balbaa, O. (2015). Production of biodiesel from waste vegetable oil via KM micromixer. J. Chem. 2015, 1–9. doi:10.1155/2015/630168
Franjo, M., Šalić, A., and Zelić, B. (2018). Microstructured devices for biodiesel production by transesterification. Biomass Convers. Biorefinery 8 (4), 1005–1020. doi:10.1007/s13399-018-0341-7
Thangarasu, G. R. V., Vinayakaselvi M, A., and Ramanathan, A. (2022). A critical review of recent advancements in continuous flow reactors and prominent integrated microreactors for biodiesel production. Renew. Sustain. Energy Rev. 154, 111869. doi:10.1016/j.rser.2021.111869
Guan, G., Kusakabe, K., Moriyama, K., and Sakurai, N. (2009). Transesterification of sunflower oil with methanol in a microtube reactor. Industrial Eng. Chem. Res. 48 (3), 1357–1363. doi:10.1021/ie800852x
Guan, G., Sakurai, N., and Kusakabe, K. (2009). Synthesis of biodiesel from sunflower oil at room temperature in the presence of various cosolvents. Chem. Eng. J. 146 (2), 302–306. doi:10.1016/j.cej.2008.10.009
Guan, G., Teshima, M., Sato, C., Mo Son, S., Faisal Irfan, M., Kusakabe, K., et al. (2010). Two-phase flow behavior in microtube reactors during biodiesel production from waste cooking oil. AIChE J. 56 (5), 1383–1390.
Hajjari, M., Tabatabaei, M., Aghbashlo, M., and Ghanavati, H. (2017). A review on the prospects of sustainable biodiesel production: A global scenario with an emphasis on waste-oil biodiesel utilization. Renew. Sustain. Energy Rev. 72, 445–464. doi:10.1016/j.rser.2017.01.034
Jensen, K. F. (2017). Flow chemistry—microreaction technology comes of age. AIChE J. 63 (3), 858–869. doi:10.1002/aic.15642
Kant Bhatia, S., Kant Bhatia, R., Jeon, J.-M., Pugazhendhi, A., Kumar Awasthi, M., Kumar, D., et al. (2021). An overview on advancements in biobased transesterification methods for biodiesel production: Oil resources, extraction, biocatalysts, and process intensification technologies. Fuel 285, 119117. doi:10.1016/j.fuel.2020.119117
Kashid, M. N., and Agar, D. W. (2007). Hydrodynamics of liquid–liquid slug flow capillary microreactor: Flow regimes, slug size and pressure drop. Chem. Eng. J. 131 (1), 1–13. doi:10.1016/j.cej.2006.11.020
Kashid, M. N., Gerlach, I., Goetz, S., Franzke, J., Acker, J., Platte, F., et al. (2005). Internal circulation within the liquid slugs of a liquid-liquid slug-flow capillary microreactor. Industrial Eng. Chem. Res. 44 (14), 5003–5010. doi:10.1021/ie0490536
Knothe, G., Krahl, J., and Van Gerpen, J. The biodiesel handbook. Elsevier 2015. Amsterdam, Netherlands.
Kumar, M., and Sharma, M. P. (2016). Selection of potential oils for biodiesel production. Renew. Sustain. Energy Rev. 56, 1129–1138. doi:10.1016/j.rser.2015.12.032
Leung, D., and Guo, Y. (2006). Transesterification of neat and used frying oil: Optimization for biodiesel production. Fuel Process. Technol. 87 (10), 883–890. doi:10.1016/j.fuproc.2006.06.003
Louhasakul, Y., Cheirsilp, B., Maneerat, S., and Prasertsan, P. (2018). Direct transesterification of oleaginous yeast lipids into biodiesel: Development of vigorously stirred tank reactor and process optimization. Biochem. Eng. J. 137, 232–238. doi:10.1016/j.bej.2018.06.009
Maddikeri, G. L., Pandit, A. B., and Gogate, P. R. (2012). Intensification approaches for biodiesel synthesis from waste cooking oil: A review. Industrial Eng. Chem. Res. 51 (45), 14610–14628. doi:10.1021/ie301675j
Madhawan, A., Arora, A., Das, J., Kuila, A., and Sharma, V. (2018). Microreactor technology for biodiesel production: A review. Biomass Convers. Biorefinery 8 (2), 485–496. doi:10.1007/s13399-017-0296-0
Martinez Arias, E. L., Fazzio Martins, P., Jardini Munhoz, A. L., Gutierrez-Rivera, L., and Maciel Filho, R. (2012). Continuous synthesis and in situ monitoring of biodiesel production in different microfluidic devices. Industrial Eng. Chem. Res. 51 (33), 10755–10767. doi:10.1021/ie300486v
Mazubert, A., Aubin, J., Elgue, S., and Poux, M. (2014). Intensification of waste cooking oil transformation by transesterification and esterification reactions in oscillatory baffled and microstructured reactors for biodiesel production. Green Process. Synthesis 3 (6), 419–429. doi:10.1515/gps-2014-0057
Mohadesi, M., Aghel, B., Maleki, M., and Ansari, A. (2019). Production of biodiesel from waste cooking oil using a homogeneous catalyst: Study of semi-industrial pilot of microreactor. Renew. Energy 136, 677–682. doi:10.1016/j.renene.2019.01.039
Natarajan, Y., Nabera, A., Salike, S., Dhanalakshmi Tamilkkuricil, V., Pandian, S., Karuppan, M., et al. (2019). An overview on the process intensification of microchannel reactors for biodiesel production. Chem. Eng. Process. - Process Intensif. 136, 163–176. doi:10.1016/j.cep.2018.12.008
Noureddini, H., and Zhu, D. (1997). Kinetics of transesterification of soybean oil. J. Am. Oil Chemists' Soc. 74 (11), 1457–1463. doi:10.1007/s11746-997-0254-2
Paiz, S., Costa Junior, J. M., Pontes, P. C., dade Carvalho, J. D. C. G., de Moraes, D. B., de Souza, C. G., et al. (2022). Experimental parametric analysis of biodiesel synthesis in microreactors using waste cooking oil (WCO) in ethilic route. J. Braz. Soc. Mech. Sci. Eng. 44 (5), 179. doi:10.1007/s40430-022-03476-0
Patil, P. D., Gude, V. G., Reddy, H. K., Muppaneni, T., and Deng, S. (2012). Biodiesel production from waste cooking oil using sulfuric acid and microwave irradiation processes. J. Environ. Prot. 3 (1), 107–113. doi:10.4236/jep.2012.31013
Pontes, P. C., Chen, K., Naveira-Cotta, C. P., Costa Junior, J. M., Tostado, C. P., and Quaresma, J. N. N. (2016). Mass transfer simulation of biodiesel synthesis in microreactors. Comput. Chem. Eng. 93, 36–51. doi:10.1016/j.compchemeng.2016.05.010
Qiu, Z., Zhao, L., and Weatherley, L. (2010). Process intensification technologies in continuous biodiesel production. Chem. Eng. Process. Process Intensif. 49 (4), 323–330. doi:10.1016/j.cep.2010.03.005
Rahimi, M., Aghel, B., Alitabar, M., Sepahvand, A., and Ghasempour, H. R. (2014). Optimization of biodiesel production from soybean oil in a microreactor. Energy Convers. Manag. 79, 599–605. doi:10.1016/j.enconman.2013.12.065
Ritchie, H., Roser, M., and Rosado, P. (2020). Energy. Our World Data. https://ourworldindata.org/energy.
Santana, H. S., Tortola, D. S., Reis, É. M., Silva, J. L., and Taranto, O. P. (2016). Transesterification reaction of sunflower oil and ethanol for biodiesel synthesis in microchannel reactor: Experimental and simulation studies. Chem. Eng. J. 302, 752–762. doi:10.1016/j.cej.2016.05.122
Santacesaria, E., Di Serio, M., Tesser, R., Turco, R., Tortorelli, M., and Russo, V. (2012). Biodiesel process intensification in a very simple microchannel device. Chem. Eng. Process. Process Intensif. 52, 47–54. doi:10.1016/j.cep.2011.12.001
Santana, H. S., Silva, J. L., Tortola, D. S., and Taranto, O. P. (2018). Transesterification of sunflower oil in microchannels with circular obstructions. Chin. J. Chem. Eng. 26 (4), 852–863. doi:10.1016/j.cjche.2017.08.018
Santana, H. S., Tortola, D. S., Silva, J. L., and Taranto, O. P. (2017). Biodiesel synthesis in micromixer with static elements. Energy Convers. Manag. 141, 28–39. doi:10.1016/j.enconman.2016.03.089
Sun, J., Ju, J., Ji, L., Zhang, L., and Xu, N. (2008). Synthesis of biodiesel in capillary microreactors. Industrial Eng. Chem. Res. 47 (5), 1398–1403. doi:10.1021/ie070295q
Supple, B., Howard-Hildige, R., Gonzalez-Gomez, E., and Leahy, J. J. (2002). The effect of steam treating waste cooking oil on the yield of methyl ester. J. Am. Oil Chemists' Soc. 79 (2), 175–178. doi:10.1007/s11746-002-0454-1
Tanawannapong, Y., Kaewchada, A., and Jaree, A. (2013). Biodiesel production from waste cooking oil in a microtube reactor. J. Industrial Eng. Chem. 19 (1), 37–41. doi:10.1016/j.jiec.2012.07.007
T.C.C.T. 307, , BS EN 14103:2011 Fat and oil derivatives. Fatty acid methyl esters (FAME). Determination of ester and linolenic acid methyl ester contents, https://standards.iteh.ai/catalog/standards/cen/1b4bd61d-8511-411c-ab1d-5035954af6f4/en-14103-2011 (2011).
Tiwari, A., Rajesh, V., and Yadav, S. (2018). Biodiesel production in micro-reactors: A review. Energy Sustain. Dev. 43, 143–161. doi:10.1016/j.esd.2018.01.002
Tsaoulidis, D., and Angeli, P. (2016). Effect of channel size on liquid-liquid plug flow in small channels. AIChE J. 62 (1), 315–324. doi:10.1002/aic.15026
Tsaoulidis, D., and Angeli, P. (2015). Effect of channel size on mass transfer during liquid–liquid plug flow in small scale extractors. Chem. Eng. J. 262, 785–793. doi:10.1016/j.cej.2014.10.012
Tsaoulidis, D., Dore, V., Angeli, P., Plechkova, N. V., and Seddon, K. R. (2013). Dioxouranium(VI) extraction in microchannels using ionic liquids. Chem. Eng. J. 227, 151–157. doi:10.1016/j.cej.2012.08.064
van Steijn, V., Kreutzer, M. T., and Kleijn, C. R. (2007). μ-PIV study of the formation of segmented flow in microfluidic T-junctions. Chem. Eng. Sci. 62 (24), 7505–7514. doi:10.1016/j.ces.2007.08.068
Viriya-empikul, N., Krasae, P., Nualpaeng, W., Yoosuk, B., and Faungnawakij, K. (2012). Biodiesel production over Ca-based solid catalysts derived from industrial wastes. Fuel 92 (1), 239–244. doi:10.1016/j.fuel.2011.07.013
Wang, X., Xu, X., Wang, Q., Huang, Z., He, J., and Qiu, T. (2020). Fatty acid methyl ester synthesis through transesterification of palm oil with methanol in microchannels: Flow pattern and reaction kinetics. Energy and Fuels 34 (3), 3628–3639. doi:10.1021/acs.energyfuels.9b03365
Wen, Z., Yu, X., Tu, S.-T., Yan, J., and Dahlquist, E. (2009). Intensification of biodiesel synthesis using zigzag micro-channel reactors. Bioresour. Technol. 100 (12), 3054–3060. doi:10.1016/j.biortech.2009.01.022
Keywords: process intensifcation, biodiesel, microchannels, sustainability, clean energy, flow patterns
Citation: Tsaoulidis D, Garciadiego-Ortega E and Angeli P (2023) Intensified biodiesel production from waste cooking oil and flow pattern evolution in small-scale reactors. Front. Chem. Eng. 5:1144009. doi: 10.3389/fceng.2023.1144009
Received: 13 January 2023; Accepted: 31 March 2023;
Published: 21 April 2023.
Edited by:
Aaron Beeler, Boston University, United StatesReviewed by:
Steven Lim, Tunku Abdul Rahman University, MalaysiaBisheswar Karmakar, Vel Tech Rangarajan Dr.Sagunthala R&D Institute of Science and Technology, India
Copyright © 2023 Tsaoulidis, Garciadiego-Ortega and Angeli. This is an open-access article distributed under the terms of the Creative Commons Attribution License (CC BY). The use, distribution or reproduction in other forums is permitted, provided the original author(s) and the copyright owner(s) are credited and that the original publication in this journal is cited, in accordance with accepted academic practice. No use, distribution or reproduction is permitted which does not comply with these terms.
*Correspondence: Dimitrios Tsaoulidis, ZC50c2FvdWxpZGlzQHN1cnJleS5hYy51aw==