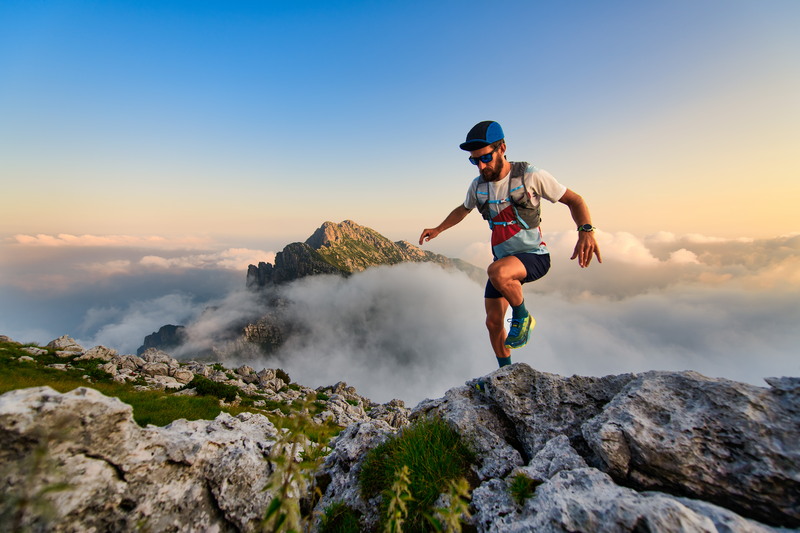
95% of researchers rate our articles as excellent or good
Learn more about the work of our research integrity team to safeguard the quality of each article we publish.
Find out more
ORIGINAL RESEARCH article
Front. Chem. Eng. , 05 January 2023
Sec. Computational Methods in Chemical Engineering
Volume 4 - 2022 | https://doi.org/10.3389/fceng.2022.978842
This article is part of the Research Topic Editors’ Showcase: Computational Methods in Chemical Engineering View all 8 articles
Nickel (Ni) in batteries (e.g., nickel-metal hydride battery (NiMH), lithium nickel cobalt aluminum oxide (NCA) and lithium nickel manganese cobalt oxide (NMC)) aim to ensure higher energy density and greater storage capacity. Two typical layered nickel-rich ternary cathode materials, NCA and NMC, are commercialized as advanced lithium-ion batteries (LiBs) for electric vehicles (EVs). The technology of those batteries has been improving by steadily increasing the nickel content in each cathode generation. In this study, we consider two types of batteries having a composite cathode made of Li [Ni0.80Co0.1Al0.1]O2, and Li [Ni0.33Mn0.33Co0.33]O2, which are the most common cathode materials for LiBs in EVs since 2010 and their functional recycling is performed. The increasing use of nickel in battery technologies has resulted in the continuous growth of demand for nickel over recent years. Nickel was added to the list of critical materials by the United States Geological Survey (USGS) already in 2021. Unfortunately now, the sustainable supply of nickel is even at higher risk due to the sanctions-related disruption of supplies from Russia. Therefore, enhancing the circularity of nickel starts to be vital for many economies. Demand for recycled nickel is growing, however, a systematic analysis of the sustainability of its recycling is still missing. Therefore, we provide a comprehensive assessment of the sustainability of the global primary and secondary production of nickel. Using system dynamics modelling integrated with geometallurgy principles and by analyzing the processing routes (pyrometallurgical and hydrometallurgical processes), we quantify the key environmental concerns across the life cycle of primary and secondary nickel required for sustainable mobility transition. Energy consumption, water use, and related emissions are assessed for all stages of the nickel supply chain, from mining to recycling. Our analysis shows the possibility of reducing the emissions by around 4.7 mt for GHG, 6.9 kt for PM2.5, 34.3 t for BC, 2.8 kt for CH4, 7.5 kt for CO, 3.3 mt for CO2, 169.9 t for N2O, 3.8 kt for NOx, 11.8 kt for PM10, 104.8 t for POC, 1.6 mt for SOx, and 232.5 t for VOC by engaging in the secondary production of nickel through the recycling of batteries. However, identical growth rate of energy consumption and water use compared to nickel mass flows means no technical progress has been achieved in different stages of the nickel supply chain towards sustainability over the period 2010–2030. Therefore, an improvement in technology is needed to save energy and water in nickel production processes. The results and findings of this study contribute to a better understanding of the necessity for improving closed-loop supply chain policies for nickel.
Nickel (Ni) is one of the key materials used in advanced infrastructure and technology solutions. It is also the fifth most abundant element on Earth (Makarova et al., 2018; Cruz et al., 2019). However, nickel is changing its usage profile and is now used as a chemical component in electric vehicle (EV) batteries. This is one of the main driving factors that the U.S. Geological Survey (USGS) (Nassar and Fortier, 2021) considered as reasons behind the expected growth in demand for nickel that makes a “compelling case for the inclusion of nickel in the critical mineral list”. Global primary nickel consumption in 2019 by industry showed that the stainless steel industry accounted for around 71% (∼1775 kt) followed by batteries [around 7% (∼175 kt)], casting and alloy steels [around 6% (∼150 kt)], electroplating [around 6% (∼150 kt)], and other applications [around 10% (∼250 kt)] (Gullen and Plungis, 2021). In global nickel consumption by sector manufacturing comes first with the share of 35% followed by metal products (19%), transport (16%), building and construction (15%), electric and electronics (11%), and others (4%).
Economic Ni resources are found in either magmatic sulfide [(Ni,Fe)9S8] (2.3% Ni) or laterite [(Fe,Ni)O(OH)] (1% Ni) type deposits (Norgate et al., 2007). According to the US Geological Survey (USGS) (McRae, 2020), global nickel reserves were estimated to be around 89 million metric tons (mt) in 2019 with global nickel mine production of about 2.7 mt. Indonesia has got around 21 mt of nickel reserves followed by Australia (around 20 mt), Brazil (11 mt), Russia (6.9 mt), Cuba (5.5 mt), Philippines (4.8 mt), China (2.8 mt), Canada (2.6 mt), United States (0.11 mt), and other countries (in total 14 mt). The global primary nickel consumers in 2019 were China (55% of total nickel consumption) followed by other regions of Asia (24%), Europe and Africa (15%) and Americas (6%) (IEA, 2021). Global demand for nickel comes mainly from China [1,226 thousand tonnes (kt)], Europe (329 kt), Indonesia (191 kt), Japan (152 kt), United States (121 kt), Korea (68 kt), India (65 kt), Taiwan (56 kt), and other regions (in total accounting for 85 kt) (Campagnol et al., 2017; Gullen and Plungis, 2021).
Value-wise, the top ten global leading importers of nickel and products containing Ni in 2019 included China whose imports reached US $5.51 billion, United States of America (US$ 2.93 billion), Japan ($2.77 billion), Germany ($1.87 billion), Netherlands ($1.83 billion), United Kingdom ($1.52 billion), France ($1.38 billion), Korea ($1.1 billion), Finland ($0.95 billion), and Italy ($0.82 billion) (data taken from https://comtrade.un.org/). The list of world leading exporters of nickel and products containing Ni by country in 2019 included United States of America ($3.12 billion), Russia ($2.99 billion), Canada ($2.98 billion), Netherlands ($2.01 billion), Germany ($1.57 billion), United Kingdom ($1.40 billion), Norway ($1.26 billion), Indonesia ($1.26 billion), Australia ($1.18 billion), and Finland ($1.03 billion) (data from https://comtrade.un.org/). However, the disruption of nickel supply chain caused by Russia in the early 2022 hit this market rather badly. According to the World Bank, average price of nickel in the global market was US $13,914 per metric ton in 2020 and it was expected to reach US $15,530 in 2025 (World Bank Group, 2017). However, due to the disruption of the nickel supply chain by Russia, the price reached US $48,241 already in March 2022 (data taken from https://markets.businessinsider.com/commodities/nickel-price).
In addition, rising fossil fuel costs and environmental concerns relating to global climate change have placed greater emphasis on using green energy technologies (Golroudbary et al., 2022a). In line with the transition from fossil fuels to green energy sources, e-mobility is one of the major technologies to be used with a view of achieving a climate-neutral society. The number of EVs has been increasing in recent years. Battery is one of the key components of an EV and the essential components of a battery are two electrodes, an anode and a cathode. Nickel is the principal metal used for the production of lithium-ion batteries (LiBs) and two most commonly used systems s based on lithium nickel cobalt aluminum oxide (NCA) and lithium nickel manganese cobalt oxide (NMC). NCA and NMC are widely used, especially in e-mobility, due to their high energy density. The surge in demand for nickel exhibited by the battery industry due to increasing EVs sales adds on to the deficit of this material. Previous studies show that demand for nickel from EV batteries will grow at 32% compound annual growth rate (CAGR) in 2019–2030, driving up nickel consumption in rechargeable batteries to 24% annually to 1.27 m tonnes by 2030 (Mo and Jeon, 2018; Nkrumah et al., 2022).
The rapid growth of EVs and the criticality of nickel nurture the need for sustainable recycling of this material. Considering LiBs applications in EVs, the end of life of batteries is defined as the decrease of the dischargeable capacity of the battery by less than 30% of its initial value (Zülke et al., 2021). The lifetime of batteries will vary considerably depending on several factors e.g., quality of used chemical materials, operating temperature, exposure to certain voltages/currents, rest periods, and the presence of efficient battery (thermal) management systems (Birkl et al., 2017). Spent LiBs could be viewed as the secondary source of nickel. Previous studies suggest an estimated 1.6 mt of spent battery packs will be available in 2030 (Zhang et al., 2018; Su and Urban, 2021). Therefore, these batteries need to be recycled in a sustainable way. Following this line of reasoning, it is necessary to pay more attention to circularity of critical materials such as nickel. Special attention is paid to the efficiency of recycling of LiBs for hydro- or pyrometallurgical post-treatment processes. However, systematic assessment of the sustainability of recovering Ni from spent LiBs and its comparison with global primary production of this material are missing. Previously conducted studies highlighted methodological challenges, such as high uncertainty and lack of knowledge about the environmental impact of nickel production in several regional case studies covering Indonesia (Kurniawan et al., 2020, 2021) and Cuba (Pacheco et al., 1999). This major gap in literature distorts a holistic global view on Ni recycling, especially with respect to the environmental impact of its secondary production. Several studies on the environmental impact of nickel conducted using the life cycle assessment (LCA) are summarized in Table 1.
There are several works partly addressing the problem of environmental impact of nickel supply chain. As presented in Table 1, most studies have evaluated the environmental footprint of a specific stage of nickel production (mining and refining) or manufacturing of specific products (e.g. batteries production and its impact at the local scale). Unfortunately, they do not allow for a holistic analysis of environmental impacts of nickel recycling, e.g. energy and water consumption across all processes involving nickel. This study provides a comprehensive assessment of the sustainability of the global primary and secondary production of nickel. Using system dynamics modelling integrated with geometallurgy principles and analyzing processing routes (pyrometallurgical and hydrometallurgical processes), we quantify the key environmental concerns across the life cycle of primary and secondary nickel required for sustainable mobility transition. Energy consumption, water use, and related emissions such as greenhouse gas (GHG), carbon dioxide (CO2), methane (CH4), sulfur oxides (SOx), nitrogen oxides (NOx), carbon monoxide (CO), volatile organic compounds (VOC), particulate matter of a diameter smaller than 2.5 μm (PM2.5), nitrous oxide (N2O), particulate organic carbon (POC), black carbon (BC), and airborne particulate matter smaller than 10 μm (PM10) are assessed for all stages of the nickel supply chain, from mining to recycling.
Figure 1 shows the details of mass flows in the model of nickel supply chain. The proposed model consists of global nickel flows, the respective energy and water consumption and related emissions. The model is focusing on two types of batteries having a composite cathode made of Li [Ni0.80Co0.1Al0.1]O2, and Li [Ni0.33Mn0.33Co0.33]O2, which are the most common cathode materials for LiBs in EVs. Looking at the closed-loop supply chain of nickel, at the beginning of the system there is raw material - nickel - obtained from the mining stage. In the processing stage, a chemical transformation turns it into cathodic materials that are very relevant for battery manufacturing. Therefore, in the production stage, nickel ends up in the battery cell which is integrated in a battery. Finally, the battery is placed in EVs in the automotive industry. In order to ensure sustainable recycling and efficient circularity of nickel, spent batteries need to be collected and they have to be processed in a way that enables the recovery of valuable critical materials such as nickel (Quinteros-Condoretty et al., 2021). One of the key intermediate products in the recycling stage is the so called “black mass”, coming from mechanical processing of spent batteries. After spent batteries have been collected, they are disassembled, shredded, and sorted. In this process metals that are available in battery components such as copper and aluminum contacts or the casings made of steel can be removed directly and put into classical recycling cycles. Plastics can be removed in the same way and what is left is the black mass. The latter contains active materials of the battery including carbon or graphite from the anode and valuable materials (e.g., Ni, co, Mn, Li) from the cathode (Golroudbary et al., 2019). These materials are usually contaminated due to the fact that the sorting phase is not overly precise and clean. In this study we focus on nickel. There are two main chemical methods that deploy pyrometallurgical and hydrometallurgical processes to process black mass into recovered materials.
Pyrometallurgy means that the black mass or a battery module are put into a smelter which heats it up to about 1,500° in a highly intensive process that burns graphite. This provides part of the combustion energy but it also increases the carbon footprint. Nickel, with other materials such as cobalt and copper, is melted and they form an alloy which can then be separated and split into individual elements. Other metals and contaminations are separated as slag while additional substances are added in order to separate those slag materials. Slag will be usually used in the construction industry. Since there is no economically viable recycling technology, lithium is lost in slag.
Hydrometallurgy takes place at moderate temperatures in an aqueous sulfuric acid solution. The process can be used to recycle nickel and other materials such as cobalt, copper as well as lithium, manganese and graphite (Golroudbary et al., 2019). However, two main challenges of this method are: high investment required because of several steps involved in the process and high amounts of by-products or waste from it.
Systematic environmental analysis of sustainability of the global supply chain of nickel is still missing. Moreover, life cycle assessment of nickel is particularly sensitive to methodological differences, e.g., variations in allocation procedures can significantly change the environmental impact per kg of product. Therefore, our analysis of nickel production is based on LiBs case studies to bridge this gap.
The United States Geological Survey (USGS) (Ober, 2020), European Commission (Blengini et al., 2020), GREET-2020 software (Wang et al., 2020), Statista database (Gullen and Plungis, 2021), and other studies (Rahimpour Golroudbary et al., 2019, 2020; Golroudbary et al., 2022b) are used as the primary data sources. A novel dynamic model is developed based on the system dynamics (SD) methodology introduced by Forrester (1997) by integrating the life cycle assessment and geo-metallurgical approach. The significance of this combination lies in the ability to quantify mass flows and assess environmental consequences within a holistic system considering the dynamic behavior and interaction of multiple parameters of the global nickel supply chain over time. This type of dynamic modeling creates a bridge between mass flow analysis and environmental assessment as it allows researchers from both fields to tackle new research questions with unique comprehensiveness. The proposed model consists of global nickel flows, the respective energy and water consumption and related emissions. The model is composed of three main parts: i) extractive stage which includes mining of nickel and processing metal and its alloys ii) production stage which includes manufacturing of LiBs, and iii) recycling stage which includes secondary production of nickel.
The model consists of two types of equations (state and rate) for quantifying the stocks and flows in given systems.
Stocks (state equations) in the mass flows of the model can be used to environmentally analyze the performance of countries involved in mining and processing stages, as well as global nickel production in battery manufacturing over time. Flows (rate equations) correspond to the production of nickel, manufacturing of products, energy consumption, water use, and related emissions such as GHG, PM2.5, BC, CH4, CO, CO2, N2O, NOx, PM10, POC, SOx, and VOC. Table 2 provides more details on the input parameters of the proposed model as well as the classification of the type of variables and their description.
Eq. 1 corresponds to the global stock of nickel (
Eq. 3 describes the global stock of processed nickel (
Eq. 5 describes the global stock of LiBs product “l” (
In the recycling stage, Eq. (7) represents the cumulative amount of nickel available in the collected spent battery “l” (with
Eq. 9 represents the cumulative amount of recycled nickel from spent battery “l” (with
For all mass flows over time, the environmental assessment (energy, water and emissions) is given in an identical form in the model. Seven main stages are considered in the environmental assessment including nickel ore mining, nickel ore beneficiation and preparation, nickel concentrate by primary extraction, using nickel in production of NCA, using nickel in production of NMC, recycling NCA and recycling NMC. Total cumulative and annual amount of energy consumed in each stage are calculated using Eqs 11, 12.
In Eq. 11,
Identically, the total cumulative and annual amount of water consumed in stage “j” of nickel supply chain can be given by Eqs 13, 14 where, the cumulative amount of water directly linked to the stage “j” in the year “t” is shown by
The life-cycles of emission rates from energy sources are adapted from the GREET model (Wang et al., 2020). GHG intensities are calculated using IPCC AR5 100-year Global Warming Potential values (Stocker et al., 2013) of 1 (CO2), 36 (CH4), and 298 (N2O). We applied Eqs 15, 16 to estimate the total and annual emissions of each life cycle stage of nickel supply chain.
In Eq. 15,
Europe needs approximately 225 kt of nickel for cathodes to reach the goal of the European Battery Alliance—300 GWh+/year of battery production in Europe by 2025. Figure 2 presents the global nickel flows in different stages, mining including nickel ore mining, beneficiation and preparation (Figure 2A); production focused on using nickel in battery industries, including NCA and NMC (Figure 2B); and recycling stage including secondary production of nickel from spent NCA and NMC (Figure 2C). The results show that primary nickel production will reach approximately 4.3 million tonnes in 2030 while 13% of it will be used by battery industries. According to the analysis, the production of NMC and NCA accounts for 62% and 31% of nickel applied in battery industries, respectively. There is a dynamic trend for secondary nickel production, which is mainly affected by delay mechanisms in the system based on the lifetime of batteries and the efficiency of their collection. The detailed calculations show that 46% of nickel used in the battery industry can be available for secondary production. Given the existing technologies of battery recycling, 84% and 16% of recovered nickel would be available from globally spent NCA and NMC, respectively. Notably, the analysis shows 58% growth of the consumption of nickel in the battery industry between 2010 and 2030.
FIGURE 2. Global mass flows of nickel between 2010 and 2030. (A) Mining stage, (B) production stage, (C) Recycling stage.
The production of nickel requires energy and water. Accordingly, Figure 3 presents energy consumption and water use through three main stages of the nickel supply chain including mining, production and recycling between 2010 and 2030. It is necessary to note that the process of recycling depends on several factors, such as life span of batteries, collection rate, dismantling, mechanical pretreatment, policies in different countries relevant to batteries collecting, storage and secondary production processes. The energy consumption of recycling NCA and NMC are significantly increased from 2010 to 2015 due to the growing amount of collected spent batteries in this period. Growing amount of discharged batteries requires more and more energy for their recycling. The results show an identical growth rate of energy consumption and water use compared with the mass flow of nickel between 2010 and 2020 which corresponds, respectively, to 30%, 38%, 28%, 71% and 71% for mining, processing, use of nickel in the battery industry, recycling of NCA and NMC. It is estimated that the growth rates will reach 60%, 64%, 58%, 52% and 95% in 2030 for mining, processing, use of nickel in the battery industry, and recycling of NCA and NMC, respectively. The identical growth rate of energy and water consumption compared to nickel mass flows means no technical progress has been achieved in different stages of the nickel supply chain towards sustainability in the period 2010–2030. Therefore, improvement is still required in technology to save energy and water in nickel production processes.
FIGURE 3. Energy consumption and water use in global nickel production between 2010 and 2030. (A) Energy consumption, (B) Water use.
The results show that the highest energy and water consumption corresponds to the mining stage in the supply chain of nickel. Keeping this in mind, much more water will be needed in the next 30 years, especially 85% more in energy production (The World Bank, 2016); therefore, the water footprint of nickel production should be assessed carefully. In this study, two types of water use are considered: direct (water consumed on-site) and indirect (water consumed in the upstream supply chain). Several factors influence direct and indirect water use. For example, the grade of ore in the mining stage or the degree of water recycling that occurs in the concentrator and tailings storage facility affect direct water consumption in the production of nickel. Also, the processing routes influence water consumption in nickel production. Our analysis shows the same trend in direct and indirect water use for nickel production. Notably, the required indirect water consumption is higher than the direct one for nickel hydrometallurgical processes. However, pyrometallurgy process consumes more direct water than indirect one.
Figure 4 shows the amount of emissions generated by the nickel supply chain in 2030. Also, Table 3 represents the contribution of each stage of Ni supply chain in generating emissions between 2010 and 2030. The highest GHG emissions from the mining stage oscillated around 846.2 kt in 2010 and reached 1.2 mt in 2020. Estimates suggest that 2 mt of GHG emissions will be generated by the mining of nickel in 2030. The highest PM2.5 are reported for the primary extraction stage (2.9 kt in 2010 and 6.7 kt in 2030). The largest amount of BC is generated by the beneficiation and preparation stage (5.8 kt in 2010 most probably reaching 16.1 kt in 2030). Methane is one of the gases influencing the warming of the planet. Methane is emitted during the process of production and transportation. Methane’s lifetime in the atmosphere is much shorter than carbon dioxide (CO2), but CH4 is more efficient at trapping radiation than CO2 (Zahraee et al., 2020, 2022). In mining stage, CH4 is mainly generated through the process of using energy sources such as coal, natural gas and oil. Also, several studies have confirmed that the oxidation of electrolytes will produce flammable and toxic gas mixtures such as CO2 and CH4 (Sun et al., 2016; Yu et al., 2022). The mining stage produces the largest amount of CH4 of all stages (1.4 kt in 2010 and estimated 7.9 kt in 2030). The highest amount of CO emission among all stages is produced through the primary extraction stage which is around 1.5 kt in 2010 and will reach 12.8 kt in 2030. The mining stage is the biggest source of CO2 emissions from the nickel supply chain (around 800.2 kt in 2010 estimated to reach 4.6 mt in 2030). The biggest emissions of N2O are generated by the beneficiation and preparation stage; they will grow from 48.3 t in 2010 to 134.4 t in 2030. Also, this stage generates the largest amounts of NOx of all other stages (around 783.9 t in 2010 estimated to reach 5.2 kt in 2030). The largest amounts of PM10 are generated by the primary extraction stage (around 4.2 kt in 2010, estimated to reach 9.9 kt in 2030). Unfortunately, all three stages of mining, beneficiation and preparation, and primary extraction generate a very high amount of POC which was around 14.7 t, 13.6 t and 12.2 t in 2010 respectively and is estimated to reach 85.5 t, 90.1 t, and 110.2 t in 2030. The highest amounts of SOx come from the primary extraction stage (around 671.2 kt in 2010, estimated to reach 1.6 mt in 2030). Both mining and beneficiation and preparation stages generate the highest amounts of VOC emissions (around 55.6 t and 34.6 t in 2010 respectively, estimated to reach 140.7 t and 96.2 t in 2030). Detailed calculations show that the circularity of nickel and recycling processes can significantly contribute to the reduction of emissions. Our analysis offers the possibility of mitigate around 4.7 mt of GHG, 6.9 kt of PM2.5, 34.3 t of BC, 2.8 kt of CH4, 7.5 kt of CO, 3.3 mt of CO2, 169.9 t of N2O, 3.8 kt of NOx, 11.8 kt of PM10, 104.8 t of POC, 1.6 mt of SOx, and 232.5 t of VOC by pursuing secondary production of nickel through the recycling of batteries.
The development and use of lithium-ion batteries (LiBs) to support vehicle electrification has been rapidly growing. It is estimated LiBs technologies will dominate mobility applications globally by 2030. However, most of the LiBs producers, e.g., European countries are largely dependent on imported raw materials such as nickel for manufacturing of lithium nickel cobalt aluminum oxide (NCA) and lithium nickel manganese cobalt oxide (NMC). Therefore, sustainability of the supply chain of nickel is essential to mitigate the supply risk related to materials required for LiBs production. Also, to ensure sustainability of the entire value chain of LiBs we need a comprehensive description and analysis of the nickel supply chain in a long-term perspective that would take account of environmental policies striving to reduce energy and water consumption and decrease emissions.
This paper seeks to provide a comprehensive assessment of the sustainability of the global supply chain of nickel by quantifying the key environmental concerns across its life cycle. The results show the possible availability of primary and secondary nickel required for sustainable mobility transition until 2030. The results suggest it is possible to reduce emissions such as GHG, PM2.5, BC, CH4, CO, CO2, N2O, NOx, PM10, POC, SOx, and VOC from the secondary production of nickel through the recycling of batteries and by improving its circularity. However, an identical growth rate of energy consumption and water use compared to nickel mass flows means no technical progress has been made in different stages of the nickel supply chain towards sustainability over the period 2010–2030. Therefore, an essential improvement in technology is still required to save energy and water through nickel production processes. Findings of this study highlight the necessity to improve the technological efficiency of recycling processes including the collection and recovery of nickel to ensure environmental sustainability.
We need to bear in mind that due to the ever-changing dynamics of material flows, further research will be needed in the near future to update the findings of this study and consider the technological progress made in every stage of the supply chain of nickel.
The original contributions presented in the study are included in the article/supplementary material, further inquiries can be directed to the corresponding authors.
SR: Conceptualization, Data curation, Methodology, Verification and validation, Formal analysis, Investigation, Visualization, Writing—original draft preparation, Writing—review and editing. AK: Conceptualization, Formal analysis, Writing—original draft preparation, Writing—review and editing, supervision. BP: Conceptualization, Formal analysis, Writing—review and editing, supervision. ML: Conceptualization, Formal analysis, Writing—review and editing, supervision.
The authors would like to acknowledge Viipuri Management Research Lab of LUT University for providing access to AnyLogic software (University 8.5.0). SRG would like to acknowledge the support of the LEAP-RE 2021 EU-AU project: REcycling of spent Li-ion batteries and end-life photovoltaic panels: From the development of metal recovery processes to the implementation of a START-up, RESTART jointly funded by the EU and the Academy of Finland (Decision No. 352365) at Aalto University.
The authors declare that the research was conducted in the absence of any commercial or financial relationships that could be construed as a potential conflict of interest.
All claims expressed in this article are solely those of the authors and do not necessarily represent those of their affiliated organizations, or those of the publisher, the editors and the reviewers. Any product that may be evaluated in this article, or claim that may be made by its manufacturer, is not guaranteed or endorsed by the publisher.
Bai, Y., Zhang, T., Zhai, Y., Jia, Y., Ren, K., and Hong, J. (2022). Strategies for improving the environmental performance of nickel production in China: Insight into a life cycle assessment. J. Environ. Manage. 312, 114949. doi:10.1016/j.jenvman.2022.114949
Bartzas, G., and Komnitsas, K. (2015). Life cycle assessment of ferronickel production in Greece. Resour. Conserv. Recycl. 105, 113–122. doi:10.1016/j.resconrec.2015.10.016
Birkl, C. R., Roberts, M. R., McTurk, E., Bruce, P. G., and Howey, D. A. (2017). Degradation diagnostics for lithium ion cells. J. Power Sources 341, 373–386. doi:10.1016/j.jpowsour.2016.12.011
Blengini, G. A., Latunussa, C. E. L., Eynard, U., Torres de Matos, C., Wittmer, D., Georgitzikis, K., et al. (2020). Study on the EU’s list of critical raw materials (2020) final report. Brussels, Belgium: EU publications. doi:10.2873/904613
Campagnol, N., Hoffman, K., Lala, A., and Ramsbottom, O. (2017). The future of nickel: A class act. Basic Mater, 1–16.
Cruz, M. J., Makarova, I. V., Kharitonov, D. S., Dobryden, I., Chernik, A. A., Grageda, M., et al. (2019). Corrosion properties of nickel coatings obtained from aqueous and nonaqueous electrolytes. Surf. Interface Anal. 51, 943–953. doi:10.1002/sia.6683
Eckelman, M. J. (2010). Facility-level energy and greenhouse gas life-cycle assessment of the global nickel industry. Resour. Conserv. Recycl. 54, 256–266. doi:10.1016/j.resconrec.2009.08.008
Forrester, J. W. (1997). Industrial dynamics. J. Oper. Res. Soc. 48, 1037–1041. doi:10.1038/sj.jors.2600946
Golroudbary, S. R., Calisaya-Azpilcueta, D., and Kraslawski, A. (2019). The life cycle of energy consumption and greenhouse gas emissions from critical minerals recycling: Case of lithium-ion batteries. Procedia CIRP 80, 316–321. doi:10.1016/j.procir.2019.01.003
Golroudbary, S. R., Makarava, I., Kraslawski, A., and Repo, E. (2022a). Global environmental cost of using rare Earth elements in green energy technologies. Sci. Total Environ. 832, 155022. doi:10.1016/j.scitotenv.2022.155022
Golroudbary, S. R., Makarava, I., Repo, E., Kraslawski, A., and Luukka, P. (2022b). Magnesium life cycle in automotive industry. Procedia CIRP 105, 589–594. doi:10.1016/j.procir.2022.02.098
Gullen, A., and Plungis, J. (2021). Nickel industry worldwide. New York: Statista. Available at: https://www.statista.com/study/15792/nickel-statista-dossier/.
IEA (International Energy Agency) (2021). The role of critical minerals in clean energy transitions. Paris, France: IEA Publ., 283. Available at: https://www.iea.org/reports/the-role-of-critical-minerals-in-clean-energy-transitions.
Kallitsis, E., Korre, A., Kelsall, G., Kupfersberger, M., and Nie, Z. (2020). Environmental life cycle assessment of the production in China of lithium-ion batteries with nickel-cobalt-manganese cathodes utilising novel electrode chemistries. J. Clean. Prod. 254, 120067. doi:10.1016/j.jclepro.2020.120067
Khoo, J. Z., Haque, N., Woodbridge, G., McDonald, R., and Bhattacharya, S. (2017). A life cycle assessment of a new laterite processing technology. J. Clean. Prod. 142, 1765–1777. doi:10.1016/j.jclepro.2016.11.111
Kurniawan, A. R., Murayama, T., and Nishikizawa, S. (2020). A qualitative content analysis of environmental impact assessment in Indonesia: A case study of nickel smelter processing. Impact Assess. Proj. apprais. 38, 194–204. doi:10.1080/14615517.2019.1672452
Kurniawan, A. R., Murayama, T., and Nishikizawa, S. (2021). Appraising affected community perceptions of implementing programs listed in the environmental impact statement: A case study of nickel smelter in Indonesia. Extr. Ind. Soc. 8, 363–373. doi:10.1016/j.exis.2020.11.015
Makarova, I. V., Kharitonov, D. S., Dobryden, I. B., and Chernik, A. A. (2018). Corrosion behavior in acid and alkaline media of nickel coatings deposited at room temperature. Russ. J. Appl. Chem. 91, 1441–1450. doi:10.1134/s1070427218090069
McRae, M. E. (2020). Nickel statistics and information. U. S. Geol. Surv. Min. Commod. Summ. Available at: https://www.usgs.gov/centers/national-minerals-information-center/nickel-statistics-and-information.
Mistry, M., Gediga, J., and Boonzaier, S. (2016). Life cycle assessment of nickel products. Int. J. Life Cycle Assess. 21, 1559–1572. doi:10.1007/s11367-016-1085-x
Mo, J. Y., and Jeon, W. (2018). The impact of electric vehicle demand and battery recycling on price dynamics of lithium-ion battery cathode materials: A vector error correction model (vecm) analysis. Sustain 10, 2870. doi:10.3390/su10082870
Mudd, G. M. (2010). Global trends and environmental issues in nickel mining: Sulfides versus laterites. Ore Geol. Rev. 38, 9–26. doi:10.1016/j.oregeorev.2010.05.003
Nassar, N. T., and Fortier, S. M. (2021). Methodology and technical input for the 2021 review and revision of the US Critical Minerals List. Reston, VA: United States Geological Survey. Available at: https://pubs.er.usgs.gov/publication/ofr20211045
Nkrumah, P. N., Echevarria, G., Erskine, P. D., and van der Ent, A. (2022). Farming for battery metals. Sci. Total Environ. 827, 154092. doi:10.1016/j.scitotenv.2022.154092
Norgate, T. E., Jahanshahi, S., and Rankin, W. J. (2007). Assessing the environmental impact of metal production processes. J. Clean. Prod. 15, 838–848. doi:10.1016/j.jclepro.2006.06.018
Norgate, T., and Jahanshahi, S. (2011). Assessing the energy and greenhouse gas footprints of nickel laterite processing. Min. Eng. 24, 698–707. doi:10.1016/j.mineng.2010.10.002
Ober, J. A. (2020). Mineral commodity summaries 2020. Available at: https://pubs.usgs.gov/periodicals/mcs2020/mcs2020.pdf.
Pacheco, R. L. R., Candela, L., Fabregat, S., Cortes, A., and Queralt, I. (1999). “Environmental impact of nickel industries in Cuba. A case of study from Moa mining district,” in Proceedings of the International Mine Water Association Congress, Sevilla, Spain, 389–394.
Peters, J., Buchholz, D., Passerini, S., and Weil, M. (2016). Life cycle assessment of sodium-ion batteries. Energy Environ. Sci. 9, 1744–1751. doi:10.1039/c6ee00640j
Quinteros-Condoretty, A. R., Golroudbary, S. R., Albareda, L., Barbiellini, B., and Soyer, A. (2021). Impact of circular design of lithium-ion batteries on supply of lithium for electric cars towards a sustainable mobility and energy transition. Procedia CIRP 100, 73–78. doi:10.1016/j.procir.2021.05.012
Rahimpour Golroudbary, S., El Wali, M., and Kraslawski, A. (2020). Rationality of using phosphorus primary and secondary sources in circular economy: Game-theory-based analysis. Environ. Sci. Policy 106, 166–176. doi:10.1016/j.envsci.2020.02.004
Rahimpour Golroudbary, S., Krekhovetckii, N., El Wali, M., and Kraslawski, A. (2019). Environmental sustainability of niobium recycling: The case of the automotive industry. Recycling 4, 5. doi:10.3390/recycling4010005
Stocker, T. F., Qin, D., Plattner, G.-K., Tignor, M., Allen, S. K., Boschung, J., et al. (2013). Climate change 2013: The physical science basis. Contrib. Work. Gr. I fifth Assess. Rep. Intergov. panel Clim. Chang. 1535.
Su, C., and Urban, F. (2021). Circular economy for clean energy transitions: A new opportunity under the COVID-19 pandemic. Appl. Energy 289, 116666. doi:10.1016/j.apenergy.2021.116666
Sun, J., Li, J., Zhou, T., Yang, K., Wei, S., Tang, N., et al. (2016). Toxicity, a serious concern of thermal runaway from commercial Li-ion battery. Nano Energy 27, 313–319. doi:10.1016/j.nanoen.2016.06.031
The World Bank (2016). High and dry: Climate change, water, and the economy. NW Washington, DC: The World Bank. Available at: https://www.worldbank.org/en/topic/water/publication/high-and-dry-climate-change-water-and-the-economy.
Wang, M., Elgowainy, A., Lee, U., Bafana, A., Benavides, P. T., Burnham, A., et al. (2020). Summary of expansions and updates in GREET®2020. United States: OSTI. GOV.
Wei, W., Samuelsson, P. B., Tilliander, A., Gyllenram, R., and Jönsson, P. G. (2020). Energy consumption and greenhouse gas emissions of nickel products. Energies 13, 5664. doi:10.3390/en13215664
World Bank Group (2017). The growing role of minerals and metals for a low carbon future. NW Washington, DC: World Bank. Available at: http://documents.worldbank.org/curated/en/207371500386458722/The-Growing-Role-of-Minerals-and-Metals-for-a-LowCarbon-Future.
Yu, W., Guo, Y., Shang, Z., Zhang, Y., and Xu, S. (2022). A review on comprehensive recycling of spent power lithium-ion battery in China. eTransportation 11, 100155. doi:10.1016/j.etran.2022.100155
Zahraee, S. M., Golroudbary, S. R., Shiwakoti, N., Stasinopoulos, P., and Kraslawski, A. (2020). Transportation system analysis of empty fruit bunches biomass supply chain based on delivery cost and greenhouse gas emissions. Procedia Manuf. 51, 1717–1722. doi:10.1016/j.promfg.2020.10.239
Zahraee, S. M., Golroudbary, S. R., Shiwakoti, N., and Stasinopoulos, P. (2022). Palm oil biomass global supply chain: Environmental emissions vs. technology development of maritime transportation. Procedia CIRP 105, 817–822. doi:10.1016/j.procir.2022.02.135
Zhang, X., Li, L., Fan, E., Xue, Q., Bian, Y., Wu, F., et al. (2018). Toward sustainable and systematic recycling of spent rechargeable batteries. Chem. Soc. Rev. 47, 7239–7302. doi:10.1039/c8cs00297e
Keywords: critical materials, environmental sustainability, green energy, nickel, dynamics modelling, decarbonization measures, lithium-ion battery recycling
Citation: Golroudbary SR, Kraslawski A, Wilson BP and Lundström M (2023) Assessment of environmental sustainability of nickel required for mobility transition. Front. Chem. Eng. 4:978842. doi: 10.3389/fceng.2022.978842
Received: 26 June 2022; Accepted: 13 December 2022;
Published: 05 January 2023.
Edited by:
Fabricio Nápoles, Michoacana University of San Nicolás de Hidalgo, MexicoReviewed by:
Cornelius Satria Yudha, Sebelas Maret University, IndonesiaCopyright © 2023 Golroudbary, Kraslawski, Wilson and Lundström. This is an open-access article distributed under the terms of the Creative Commons Attribution License (CC BY). The use, distribution or reproduction in other forums is permitted, provided the original author(s) and the copyright owner(s) are credited and that the original publication in this journal is cited, in accordance with accepted academic practice. No use, distribution or reproduction is permitted which does not comply with these terms.
*Correspondence: Saeed Rahimpour Golroudbary, U2FlZWQuUmFoaW1wb3VyQGFhbHRvLmZp; Andrzej Kraslawski, QW5kcnplai5rcmFzbGF3c2tpQGx1dC5maQ==
Disclaimer: All claims expressed in this article are solely those of the authors and do not necessarily represent those of their affiliated organizations, or those of the publisher, the editors and the reviewers. Any product that may be evaluated in this article or claim that may be made by its manufacturer is not guaranteed or endorsed by the publisher.
Research integrity at Frontiers
Learn more about the work of our research integrity team to safeguard the quality of each article we publish.