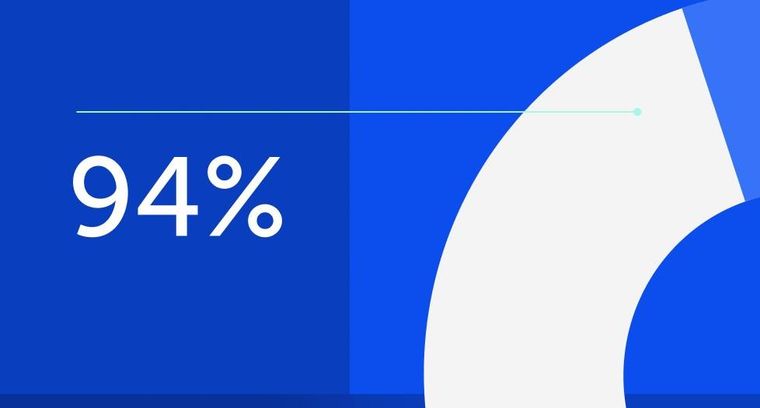
94% of researchers rate our articles as excellent or good
Learn more about the work of our research integrity team to safeguard the quality of each article we publish.
Find out more
REVIEW article
Front. Chem. Eng., 07 September 2022
Sec. Microfluidic Engineering and Process Intensification
Volume 4 - 2022 | https://doi.org/10.3389/fceng.2022.966451
Industrial organic synthesis is time and energy consuming, and generates substantial waste. Traditional conductive heating and mixing in batch reactors is no longer competitive with continuous-flow synthetic methods and enabling technologies that can strongly promote reaction kinetics. These advances lead to faster and simplified downstream processes with easier workup, purification and process scale-up. In the current Industry 4.0 revolution, new advances that are based on cyber-physical systems and artificial intelligence will be able to optimize and invigorate synthetic processes by connecting cascade reactors with continuous in-line monitoring and even predict solutions in case of unforeseen events. Alternative energy sources, such as dielectric and ohmic heating, ultrasound, hydrodynamic cavitation, reactive extruders and plasma have revolutionized standard procedures. So-called hybrid or hyphenated techniques, where the combination of two different energy sources often generates synergistic effects, are also worthy of mention. Herein, we report our consolidated experience of all of these alternative techniques.
Chemical processes can be found at the onset of all societal progress, and only the greener design of industrial production will facilitate the future of humankind. Green chemistry, and its complete merger with industry 4.0 strategies and the circular economy, will have an indisputable role in shaping the next generation of the chemical industry. This latest industrial and technological revolution, in part conceptualized and popularized at World Economic Forum meetings, focuses on innovation dominated by digitalization and robotization, along with more sustainable production models of food, clean water and energy. Over the last 2 decades, chemistry and chemical engineering, as both basic and applied disciplines, have progressively paid more attention to greener and sustainable approaches. It should be unnecessary to underline the key concepts of green chemistry in academia and research, but these are mainly aimed at reducing waste, maximizing efficiency and preventing serious threats to human health and the environment. The conditions for sustainable innovation not only include a series of conceptual protocols, such as atom economy, the reduction of derivatization steps and the use of eco-friendly solvents, among others, but also enabling technologies that help chemical industries with process intensification (Etzkorn, 2020). Ideally, they maximize heat and mass transfer, leading to significant acceleration and enchantments in yield/conversion, thus contributing to energy savings and lower production costs. The other pillar of chemical transformations and processing obviously lies in the catalytic methods, which are indispensable tools in modern organic/inorganic syntheses and material design. While catalysts have often been considered as tools to be tested empirically, only research groups with expertise in material characterization and structure/activity correlation have contributed to developing and characterizing new catalysts, with the ultimate goals of achieving better efficiency and selectivity. Such studies showcase the structural factors and working parameters required for optimal performance.
Chemical manufacturing in organic synthesis still relies on traditional batch reactors and procedures. Continuous flow systems have several advantages over batch processes, namely improved heat and mass transfer, which positively affect conversion, safety and reproducibility. The transition from batch-to continuous-flow synthetic processes is one of the more relevant advances in fine chemicals and pharmaceutical industries. The high level of molecular complexity and multiple functionality of active pharmaceutical ingredients (APIs) generally entail many synthetic steps, with work-up and purification affecting overall yield (Baumann and Baxendale, 2015), and everything being facilitated by continuous flow (Ferlin et al., 2020). Additional advantages are related to the small inventory and almost complete absence of reactor headspace, thus avoiding the risks associated with handling volatile solvents and toxic reagents (Gutmann et al., 2015; Movsisyan et al., 2016). In fact, it is fair to mention that the industrial exploitation of flow chemistry began almost one century ago when the Italian company Dipharma moved production of nitroglycerin to flow-mode, resulting in a much more efficient and safer process (Tagliapietra et al., 2019). Bearing in mind that safety constitutes a major concern in industrial entrepreneurship, the synthesis of potentially hazardous, if not explosive, reagents or reaction mixtures, can safely be carried out in continuously operated flow reactors (Seemann et al., 2021). A comparative analysis of the pros and cons in the synthesis of privileged heterocyclic scaffolds, present in most drugs, has highlighted the benefits of flow reactors (Alfano et al., 2021). Furthermore, although the setup of continuous-flow synthetic procedures of complex chemical architectures is not a trivial task, an economic analysis of continuous-flow protocols in comparison to equivalent batch-mode processes has highlighted that large savings can be achieved (Tagliapietra et al., 2020).
This account highlights the implementation of enabling technologies, which have become widespread in chemical synthesis and processing, as part of continuous operations. Although this analysis cannot be comprehensive and readers are referred to specific literature, the exploration of some non-conventional methods in continuous systems illustrate further improvements. Likewise, two or even more technologies can be sequentially hyphenated, and run at different scales, from milligram to multigram, thereby increasing applicability. Flow reactors can now be fabricated in multiple designs and shapes (i.e. micro and meso channels), and tailored for particular applications, including clinical and diagnostic use. Both tubing diameter and pump rates, among others, influence the flow regimes and impose other limitations. Clogging and precipitation, especially in heterogeneous transformations, are a serious drawback that results from channel miniaturization. The issue can be overcome by merging flow systems with thermal or mechanical activation. The vigorous agitation provided by ultrasonic waves is a valuable tool in microfluidics (Rivas et al., 2012; Noël et al., 2011). We show where it is likely to improve results and how the machine-assisted approach usually adheres to green chemistry principles. We also outline challenges and prospects for such fields. Highly automated industrial flow reactors have broadened applicability across fine chemicals and the pharmaceutical industry (Ferlin et al., 2021).
Table 1 summarizes the main technologies and energy sources used to promote chemical reactions, by improving mixing, dissolution and heating, and simplifying work-up and downstream processes, such as crystallization. Except ball milling, which is typically performed in batch mode (semi-continuous examples are also known), all of the following thermal and non-thermal techniques can be used in continuous-flow processes, with excellent heat and mass transfer capabilities, and provide easier scale-up.
Sonochemical reactions are carried out under ultrasound (US) in a frequency range between 20 and 100 kHz, which is extended to 300–500 kHz when radical pathways are expected (Bucciol and Cravotto, 2022). US generates cavitation in the liquid medium, a phenomenon that generates high-energy microenvironments (hot spots) and turbulence. Within this context, US-induced chemistry can be appropriately defined as cavitational chemistry (Martínez et al., 2021), and it has been widely applied both in research labs and in industrial production (Cravotto and Cintas, 2006). Cavitation refers to the generation of voids or micro cavities when a liquid suffers a sufficient pressure drop that disrupts its cohesive forces. The subsequent and violent collapse that occurs to restore the intermolecular interactions releases huge amounts of energy, which causes the aforementioned effects.
US can certainly be applied to almost all reaction types, including heterogeneously and homogeneously catalyzed reactions, ion exchange resin and enzyme catalyzed reactions, and phase transfer catalyzed reactions, as well as biphasic reactions. However, it is important to note that, while the use of US has been established as highly effective in laboratory scale operations, its successful transformation into commercial scale processing for organic synthesis applications in flow mode is still lacking due to number of engineering issues (Sancheti and Gogate, 2017). The combination of sonication and micro flow reactors may represent a new, emerging area in the context of organic flow processes, as previously foreseen by Rivas et al. (Rivas et al., 2012). This combination is technically feasible and could also lead to synergistic results in terms of higher product selectivity and lower waste generation, while sonication can also prevent pipes clogging. Although sonication has been generally utilized to generate liquid flow and avoid the deposition of solids, it can do much more. Current research aims to explore sonochemical processes themselves with microfluidics in order to create so called “micro-sono-reactors”. Under such conditions, cavitation collapse and associated phenomena, such as radical production and sonoluminescence among others, can be enhanced and fine-tuned. It should be mentioned that several US-assisted reactions lack reproducibility, mostly because cavitational energies are related to external parameters (frequency, power, reactor deign etc.) and solvent properties. Microfluidic devices can be adapted for the accurate control of temperature, mixing and frequency and pressure amplitudes while providing short residence times. Moreover, microfluidic systems entail reduced operation risks (explosive or run-away reactions, etc.) when performing reactions under extreme conditions. In addition, large-volume applications only require numbering up, which involves the parallel design of multiple reactors. US can, even more easily, be applied in flow chemistry by dipping the loops and tubing reactors into an ultrasonic bath. In this case numbering up and sizing up move in parallel considering the penetration depth of ultrasonic waves in the reaction medium, in general around 10–30 mm. Examples reported over the last decade include the oxidation of alcohols and aldehydes to carboxylic acids, as well as the Nef oxidation of nitroalkenes to carbonyls and acids, which can be performed in a flow reactor combined with a US bath using KMnO4 (Sedelmeier et al., 2010). Buchwald et al., have adopted the same strategy to perform some Pd-catalyzed amination reactions using a microreactor made of polytetrafluoroethylene (PTFE), which was placed in an ultrasonic bath (Noël et al., 2011). Likewise, other US assisted synthetic transformations have been reported (Hartman, 2012). Particularly worthy of note are US-promoted copper-catalyzed Huisgen 1,3-dipolar cycloadditions performed in a meso-flow reactor customized with a piezoelectric transducer (Tu et al., 2012) (Figure 1) to enhance reaction rate and efficiency. 1,4-Disubstituted triazoles were synthetized in 15–55% yields at 50–150°C, depending on the starting substrates, in only 5–10 min. Moreover, the results presented above demonstrate an enhanced version of click chemistry under meso-flow conditions utilizing US to generate triazoles under low temperature conditions.
The application of US to chemical process intensification is also illustrated by the large-scale multiple transducer sonochemical reactors (operating in continuous mode) that have been developed for biodiesel production from soybean oil via transesterification (Bucciol et al., 2020). Apart from the cost of the oil, the main parameters that influence the attractiveness of this process are energy consumption and the amounts of methanol and catalyst used. With extremely low ratios of methanol and catalyst, moderate energy consumption and a short reaction time, the US-assisted flow transesterification proposed by this team represents an example of synthetic process intensification by means of US, and provides future opportunities for US to be applied in continuous flow reactors both at academia and industrial level (Cintas et al., 2010).
HC typically occurs as the result of an increase in the kinetic energy through an area constriction, or the high-speed rotation of a rotor through a fluid (Wu et al., 2019). Ways to achieve this include throttling valves, orifice plates, venturi, cavitation jet mixers, two-stage orifice valves, high-pressure liquid whistles, high-pressure jet fluidisers and high-speed rotor–stator homogenisers, among others. The earliest use of HC technology in chemical processes is the intensification of oils hydrolysis (Pandit and Joshi, 1993). The use of a rotor-stator HC unit enabled the oxidative polymerization and emulsification of oils and the process industrialization with remarkable energy saving (Rinaldi et al., 2017). The production of fatliquors from waste frying oils may ensure a full embedding of the circular economy’s recycling concepts.
Mechanochemical energy has been successfully applied in synthetic chemistry using efficient ball mills, usually in solvent-free conditions. The possibility to perform reactions without a solvent or with very small amounts, such a glidant, is of paramount environmental and economic importance from an industrial point of view. Recent advances in ball mill set-ups with multi-sample jars allow parallel synthesis for a preliminary screening of substrates, catalysts and conditions to be completed at the milligram scale (Martina et al., 2018), before then moving up to kilo scales for semi-industrial production (Barge et al., 2020).
Although “rudimentary” forms of mechanical activation, such as grinding and rubbing, have proven to be extremely useful in preparative chemistry, such procedures can also be inefficient due to limited contact and poor homogenization. Professional reactors, in the form of planetary ball mills and acoustic mixers, among others, allow for a more accurate control of operational parameters.
Reactive extrusion is a powerful technique for activating chemical reactions with mechanical forces in continuous flow. This feature allows the intrinsic batch nature of ball milling, which hinders industrial scale-up, to be overcome (Calcio Gaudino et al., 2022). Extrusion is commonly applied in the polymer, materials and food industries while organic synthesis has only recently been investigated (Bolt et al., 2022), by means of new versatile single and twin screw micro-extruders.
Despite the effectiveness of continuous extrusion technology in other fields, it was, remarkably, only in 2017 that the first documented studies were reported in the field of organic synthesis. In this context, Crawford, James and co-workers were the first to report the Knoevenagel reaction between vanillin and barbituric acid, performed under continuous twin screw extrusion (TSE) (Crawford et al., 2017a).
Following this successful translation from “batch-mode” ball-milling to the “flow-mode” extrusion of Knoevenagel reaction, the same authors explored the further reaction of vanillin and malononitrile with the introduction of Na2CO3 (10 mol%) as the catalyst. Kaupp and co-workers have previously shown the potentiality of the aldol reaction of ninhydrin and dimedone to provide a quantitative product without the need for purification steps (Kaupp et al., 2002; Kaupp et al., 2003). This reaction was exploited by Crawford and co-workers under continuous TSE. It was found, once again, that Na2CO3 (10 mol%) was crucial to affording the quantitative conversion of the desired condensation product, highlighting, once more, how TSE could provide an excellent alternative for continuous organic synthesis. Isoni et al., have developed a “greener” alternative for 4-chlorobenzaldehyde reduction in the presence of NaBH4 (Isoni et al., 2017) that is capable of multi-kilogram continuous scale operation under tween screw extrusion. Moreover, the versatility of continuous extrusion in carrying out multi-step reactions was later proved by Crawford, James and co-workers (Crawford et al., 2017b), who showed how multiple sequential reactions could be telescoped via the successive addition of reagents along the extrusion barrel. They exploited the Knoevenagel condensation of vanillin and malononitrile, followed by subsequent Michael addition, upon the feeding of dimedone (Figure 2).
FIGURE 2. Telescoped cascade processes through reactive tween extrusion. Reproduced from (Bolt et al., 2022) with permission from the Royal Society of Chemistry.
In 2018, Browne and co-workers translated a range of highly selective protocols for the synthesis of fluorinated building blocks, including heterocycles and 1,3-dicarbonyls, from batch milling conditions to continuous reactive extrusion protocols (Cao et al., 2018).
When a screw configuration, made up of kneading, conveying and reverse sections, was adopted, continuous extrusion was confirmed to produce a 70% yield of difluorinated products at a flow rate of 3.94 kg h−1, while only 0.14 kg h−1 could be reached under the optimized ball-milling process. Likewise, the mono-fluorinated diketone was produced in an excellent yield (up to 90%), with a throughput rate of 5.14 kg h−1. This work demonstrates the potentiality of extruder technology when applied as an intensification tool to build up previously established ball milling procedures.
In 2018, Métro and co-workers documented a crucial step towards the continuous solvent-free synthesis of di- and tri-peptides (such as Boc-Asp(OBzl)-Phe-OMe/Boc-Trp-Gly-OMe and Boc-Asp(OBzl)-Trp-Gly-OMe/Boc-Asp(OBzl)-Trp-Phe-OMe) when they adopted co-rotating recirculating screw extrusion (RSE) (Yeboue et al., 2018). In particular, they documented remarkable 20–200 fold increases in STY values for the RSE-assisted peptide coupling, compared to the “batch-mode” planetary ball mill and solution-phase counterparts (Figure 3).
FIGURE 3. Bulk solvent and CRM-free peptide coupling enabled by recirculating screw extrusion; (A) experimental set-up, (B) chemical synthesis. Reproduced from (Bolt et al., 2022) with permission from the Royal Society of Chemistry.
Still in 2020, a rapid solvent-free procedure, using a co-rotating tween screw extruder, to perform a multi-component Ugi reaction was reported by El-Remaily et al. (El-Remaily et al., 2020), and, at the same time in the field of sustainable active pharmaceuticals synthesis, Crawford, Colacino and co-workers reported the development of an extrusion methodology for the synthesis of hydantoin-based API’s (Crawford et al., 2020). In particular, Nitrofurantoin and Dantrolene were afforded with 100% and 84% conversions, respectively, in a more sustainable way by means of a reverse twin screw configuration (Galant et al., 2022). (Figure 4).
FIGURE 4. Process mass intensity (PMI), quantity of wastewater and cost for the gate-to-gate production of 1 kg of nitrofurantoin by TSE (left, yellow) and conventional solvent-batch (right, green) synthesis routes (Authors’ graphic inspired by Galant et al., 2022).
Finally, in 2021, Andersen et al., reported the first extrusion example of a nucleophilic aromatic substitution (SNAr) between benzylamine and 3-bromo-4-fluoro-nitrobenzene via TSE (Andersen et al., 2021) (Figure 5). The authors by investigating this model reaction, with an accurate temperature monitoring in small-scale ball mill, could predict the most suitable conditions for the scale-up in twin-screw extruder and the required residence time.
MW are basically RF waves, however there is difference between RF and MW as far as operating range and applications are concerned. MW range starts from 300 MHz to 300 GHz, with common ovens working at 2.45 GHz and industrial reactor at 915 MHz. MW are currently used in every facet of chemistry, providing efficient volumetric heating and much shorter reaction times, among a host of other benefits, making the technology a valid ally to green organic synthesis. Since the publication of “Microwaving myths”, in which several experts described the current status, and potential pitfalls, of synthetic application, new technological advances have been made that have broadened use and scientific interest (Van Noorden, 2008). In fine chemicals and drug discovery, almost all new compounds now have their first synthesis carried out under MW (Martina et al., 2021).
MW and flow technologies are a fine fit for each other when scale-up purposes are envisaged in organic synthetic fields. The main advantage of flow reactions is the high versatility and the best guaranteed safety for operators, especially when working with micro- and meso-reactors. Moreover, the small diameter of the flow reactors is perfect for the application of MW irradiation as it solves the problem encountered in scaling MW-assisted reactions; MW irradiation has a limited penetration depth that is defined by the material’s dielectric properties.
Faster heating rates, small reactor volumes and rapid changes in reaction temperature in real time are some of the salient features of continuous-flow MW-assisted organic synthetic (CF-MAOS) systems that aim to be a unique laboratory tool for the safe and fast optimization of reaction conditions and scale-up synthesis. Strauss (Strauss, 1999) pioneered this theory and described the first mono-mode MW reactor coupled to a flow system, the CMR (Continuous MW Reactor) MW reactor developed at CSIRO. As an example of the application of this equipment, he reported the degradative hydrolysis of ethyl 2-indolecarboxylic ester, for which it was possible to control the hydrolysis and the subsequent decarboxylation by fine tuning the process temperature. Several CF-MAOS examples have recently been reviewed and compared to batch processes (Horikoshi and Serpone, 2019). For instance, excellent conversions have been observed in a variety of cross coupling reactions and ring closing metathesis (RCM) reactions (using metal catalysts), as well as in nucleophilic aromatic substitutions NArS and Wittig reactions (that do not use metals) by adopting a custom-built micro-capillary MW reactor (Comer and Organ, 2005) (Figure 6). This paves the way for the use of microwave-assisted, flow capillary synthesis as a powerful and efficient means to replace one-at-a-time MW synthesis and provide libraries of compounds on a scale suitable for biological screening purposes with dramatic reaction rate enhancements.
FIGURE 6. Continuous flow MW microreactor. Reprinted with permission from (Comer and Organ, 2005). Copyright (2005) American Chemical Society.
Another interesting example of CF-MAOS has been reported by Nishioka et al., who, in 2013, developed a single-mode MW reactor to perform continuous-flow reactions at elevated pressures (Nishioka et al., 2013). The authors tested the reactor in the oxidative decomposition of ethylene over a palladium-dispersed tubular reactor and concluded that the selective heating of the catalyst was observed. This methodology can not only be applied to liquid flow reactions, but also to solid-state and gas-flow reactions. The system (Figure 7) is capable of operating at high temperature and pressure (310°C/60 bar) in an extremely energy efficient manner (MW power 0.six to six kW), thus providing a system to improve productivity through the rapid elevation of temperature and pressure.
FIGURE 7. Experimental setup of the MW-assisted flow reactor system and image of the MW cavity. The quartz reactor tube relates to the PEEK sheath, which is designed to resist up to 10 MPa. Reprinted with permission from (Nishioka et al., 2013). Copyright (2013) American Chemical Society.
A similar setup was designed by Akai and associates (Yokozawa et al., 2015). The system incorporated a solid-state MW generator (200W, 2.4–2.5 GHz) to perform fine adjustments to the irradiation frequency according to changes in electric permittivity. The resonance cavity was occupied by a helical tubular borosilicate glass reactor with an internal volume of 5.5–6.0 ml. This MW flow setup was tested with several solvents and known reactions such as the Fisher indole synthesis and Diels–Alder reactions. Immediately afterwards, a continuous flow MW-assisted palladium (II)-catalysed desulfitative synthesis of aryl ketones, starting from sodium aryl sulfinates and nitriles, was reported by Skillinghaug et al. (Skillinghaug et al., 2016). The desired aryl ketones were recorded in fair-to-good yields when a MW transparent aluminium oxide reactor (as a safe and thermostable alternative to borosilicate glass reactors) was used, among the others (Figure 8). Different behaviour for Silicon carbide (SiC) a typical MW absorbing material due to the excellent dielectric properties and thermal stability at high temperature.
FIGURE 8. MW-assisted continuous flow Palladium (II)-catalyzed desulfitative synthesis of aryl ketones. Reprinted with permission from (Skillinghaug et al., 2016). Copyright (2016) American Chemical Society.
Once again, in 2018, the versatility of MW technology was confirmed by other researchers (Egami et al., 2018) who applied MW for the rapid and continuous Johnson−Claisen rearrangement of allyl alcohol and triethyl orthoacetate by means of flow apparatus. The reactions could be performed without solvent and only a catalytic amount of acetic acid. When scaling up the MAOS to the industrial level, Benaskar and co-workers examined cost benefits (Benaskar et al., 2011). The authors assessed that, when MW were employed, a realistic cost-competitive process could be achieved using single-mode MW heating combined with a fixed-bed catalyst. Nevertheless, a comparison of the CAPEX impacts from the different heating techniques shows that the multi-mode MW cavity for flow systems is more expensive than all other heating techniques (Figure 9).
FIGURE 9. MAOS cost benefits outlook for Multi-Mode MM-MW and Single-Mode SM-MW (Authors’ graphic inspired by Benaskar et al., 2011).
Nowadays, the most commercially available MW-assisted flow reactors are designed by CEM, Sairem, Biotage, Syrris-wavecraft and Milestone. Of these, the FlowSynth system developed by Milestone is the only multimode instrument designed for flow chemistry. The reaction chamber is mounted vertically in the cavity and the mixture is pumped from the base to the top. The system can operate at temperatures of up to 230°C, pressures up to 30bar and flow rates in the range 10–200 ml min−1. One of the first examples of the use of FlowSynth was described by Shieh and associates, who reported the methylation of phenols using DBU as the catalyst (Shieh et al., 2001). The use of MW irradiation and flow conditions produced a dramatic rate enhancement in comparison to conventional heating, with a 1,900-fold increase for the congested phenol to give trimethoxybenzene. Cravotto and co-workers have documented the effectiveness of FlowSynth and have described MW-assisted γ-valerolactone production through levulinic acid hydrogenation in continuous flow mode over heterogeneous palladium (Tabasso et al., 2016), and, more recently, ruthenium catalyst (Ru/AC Ru/TiO2) (Grillo et al., 2021). A novel protocol for continuous MW-assisted alkyne semi-hydrogenation under heterogeneous catalysis was reported in 2018 (Calcio Gaudino et al., 2018). This challenging task has been accomplished using a multifaceted strategy which entails the US-assisted preparation of Pd nanoparticles (average Ø 3.0 ± 0.5 nm) that were produced on the μ-metric pores of sintered alumina spheres (Ø 0.8 mm) and a continuous flow reaction under H2 (flow rate 7.5 ml min−1) in a FlowSynth MW reactor (counter-pressure 4.5 bar). With such features, innovation in MW science (MW chemistry) is sure to progress and advance the CF-MAOS field. Currently the market offer several excellent continuous-flow MW reactors: C-Wave PRD (by C-Tech innovation, United Kingdom) capable of operating up to 250°C and 30 bar pressure; SAIDA’s flow-MW technology up to 230°C and 25 bar pressure (by SAIDA FDS Inc., Japan), µWaveFlow 20 (2.45 GHz) and µWaveFlow 40 (915 MHz) (by Püschner Microwave Power Systems, Germany), and other producers such as Sairem (France) and Microwave Chemical Co. Ltd (Japan).
This technology is typically used in the food industry to rapidly increase temperature by exploiting the Joule effect that is generated by an electric current moving through a solution or a suspension with proper electric conductance. This highly energy efficient means of heating chemical reactions is the most recent improvement in organic synthesis (Silva et al., 2017). In general, organic reactions are fast, the yields and selectivities are high and the products are easily isolated and purified. There are numerous documented organic reactions carried out under ohmic heating (Soengas et al., 2016). Recently, Silva et al. (Silva et al., 2020) have reported a Suzuki–Miyaura reaction protocol that is based on the combined use of ohmic heating (ΩH) and supported ionic liquid phase catalysts. This methodology was applied to obtain different flavonoid derivatives in aqueous media in a sustainable and efficient way. Several static and flow ohmic heaters (only) have been developed for food applications with different electrode arrangements (Kaur and Singh, 2016). Static ohmic heaters can have a number of electrodes inserted within a container and are most commonly employed in small-scale applications, such as in water heaters and laboratory-scale chemical reactors, while flow ohmic heaters are the most common type employed in industrial applications, due to the inherent advantages of flow processes (Alkanan et al., 2021). However, suitable commercial static or flow ohmic heaters for chemical synthesis are not available (to our knowledge). With respect to ohmic heating reactors, there are several opportunities for the design of new ohmic devices, including:
ii) the miniaturization of the existing reactor prototype;
ii) the development of suitable reaction vessels (mainly closed vessels) to perform reactions beyond atmospheric pressure;
iv) the engineering and development of suitable ohmic heating reactors for flow organic synthetic applications;
iii) the coupling of an ohmic reactor with other enabling technologies (such as US) to improve organic synthesis sustainability.
However, the future exploitation of ohmic heating at an industrial scale will depend on economic studies to assess the overall costs and feasibility of its application, on the development of reliable predictive models of the ohmic heating pattern and on the improvement of safety and quality-assurance protocols.
Electromagnetic induction, conversely, can be carried out by applying a medium-frequency field (15–25 kHz) to magnetic nanoparticles, giving selective and almost instantaneous heating by exploiting the so-called Néel relaxation process and Eddy currents. The first generates heat as a consequence of magnetic hysteresis loss, whilst the second happens when very strong rapidly alternating magnetic field are exerted on conductive materials (Ceylan et al., 2011). Currently, superparamagnetic particles are used as an initial source of heating as they can be superheated (up to 500°C). In general, magnetic nanoparticles can change their heating profiles in relation to the percentage of output power, material nature and even shape and size of the particles. Furthermore, the adopted material can be chemically inert, used only to heat up the reaction system, or can have a catalytic role (i.e., functionalized MagSilica). Usually glass and PEEK (Polyetheretherketone) are the main materials applied to produce induction reactors, due to their transparency to inductive fields (Kirschning et al., 2006; Kirschning et al., 2012). Kirschning and co-workers were the first to exploit the flow application of inductive heating with magnetic nanoparticles, and they investigated a number of organic reactions, such as oxidations, Buchwald–Hartwig amination, Wittig reactions, palladium-catalyzed couplings, metathesis, Claisen rearrangements and Click cycloadditions (Kirschning et al., 2012). Furthermore, the same group developed a synthesis for the neuroleptic olanzapine in a three-step protocol by exploiting inductive heating (Hartwig et al., 2013, vide infra, Sect. 3.1).
IR is still in its infancy but provides efficient heat transfer with a deeper wave penetration than photochemistry at higher frequencies. IR heating can be conducted with inexpensive lamps, often a W filament sealed in a quartz capsule containing a halogen gas. The technique provides both homogeneous and short heating times with low energy consumption. Solvent-free protocols can be performed as well (Escobedo et al., 2016). Applications in food processing and organic synthesis, the latter providing some improvements over MW or mechanical activation, have been reported (Aboud et al., 2019; Zappimbulso et al., 2021).
Electrochemistry is, along with photochemistry (UV/Vis mode in particular), an old technology that is currently enjoying a renaissance, as using the “electron” as a chemical reagent is doubtlessly a green strategy. Selective functional group manipulations are among the most important applications in synthetic chemistry (Schotten et al., 2020). APIs can likewise be obtained through electrochemical methods in quicker and more sustainable processes than via other activation methods (Cantillo, 2022). Recent innovations include the use of rapid alternating current, rather than direct current as is usual in electrochemistry (Kawamata et al., 2021), and it is hoped that alternating polarity should find new vistas in synthesis and catalysis. Electrosynthesis can be carried out via a variety of procedures and technical variations, and portable electrochemical reactors are currently available at a moderate cost. Importantly, electrochemical flow reactors can easily be implemented and/or combined with other techniques, such as US or photochemistry (Folgueiras-Amador et al., 2017; Shida et al., 2021).
The electron transfer processes that occurs on the surface of an electrode represents the driving force for electrochemical reactions, thus reagents and electron mediators need to be in contact with electrode surfaces. For this reason, the design of appropriate systems depends on mass transport phenomena and the enhancement of electron transfer kinetics. These aspects are of even greater importance in the development of flow systems (Noël et al., 2019). The exploitation of microreactors (Figure 10) can meet the above-mentioned requirements, solving several issues and technological barriers that are usually encountered in conventional macro batch electrochemical synthesis.
The reduced distance between the electrodes, for example, cuts the electrode surface-to-reactor volume ratio and simultaneously avoids a high ohmic drop, resulting in a substantial increase in the mass transfer on the surface of the electrodes (Yoshida et al., 2008). These features are also of great importance for scale-up purposes, minimizing electrolytes and providing opportunities for high automatization. Over the last decade, great efforts have been made by flow chemists and electrochemists to develop electrochemical continuous flow systems suitable for organic synthesis applications (Atobe et al., 2018; Pletcher et al., 2018; Elsherbini et al., 2019; Elsherbini and Wirth, 2019).
Several examples of electrochemical flow approaches are available in literature, such as the electrooxidation of sulfides and sulfoxides without electrolytes, as supported by an automated two-step procedure (Amri and Wirth, 2021), and the electrochemical azolation of arenes via N−H/C−H cross coupling (Buglioni et al., 2021). By exploiting continuous-flow technology, numerous synthetic and purification steps can be merged into a single, streamlined flow configuration (Britton et al., 2017; Britton and Raston, 2017; Pieber et al., 2017). This approach is crucial for the synthesis of unstable intermediates and reactives, short-lived compounds and even in the conversion of hazardous and toxic species (Gutmann et al., 2015; Gutmann and Kappe, 2017; Kockmann et al., 2017; Elsherbini and Wirth, 2019). This application of flow electrochemical synthesis makes it possible to perform amino acid synthesis via the sequential condensation of aldehydes and amines, to form sensitive aldimines, which then undergo electroreductive carboxylation with CO2 (Naito et al., 2021).
Suga et al., have integrated the continuous production of unstable cyanohydrin, via reduction with LiAlH4, to synthesize vicinal amino alcohols (Sato et al., 2021). With a different approach, ortho-quinones can be generated, via anodic oxidation, and then quickly exploited in a Diels−Alder batch reaction (Tanaka et al., 2019). In this way, the typical poly-/isomerization and decomposition of the substrate can be avoided. Another interesting example, from Wirth et al., is the development of a flow method to prepare bench-unstable hypervalent iodine reagents, which are then coupled with a variety of synthetic pathways, including heterocycle synthesis, tosyloxylation and oxidations, all performed under flow conditions (Elsherbini et al., 2019).
In terms of transposition from lab scale to pilot and production scales, classical scaling up, by means of a geometrical enlarging strategy, cannot be considered, as electrochemical reactions are surface reactions: cell voltage and energy costs would raise proportionally to the interelectrode gap. For this reason, the main electrochemical flow scale-ups are provided by flow cells, which consist of modular units that can be stacked in parallel (numbering-up approach) (Zhang et al., 2017). A narrow interelectrode gap is the key to providing low cell voltage with a high specific area. This approach has been exploited by Peter et al., in the development of a safe alternative for the classical Birch reduction; a scalable electroreduction of arenes by stacking several electrodes in parallel (Peters et al., 2019). It worth noticing that, of all the electrochemical processes reported, roughly 7% have been commercialized and 15% piloted (Sequeira and Santos, 2009) (Figure 11).
FIGURE 11. Electrochemical organic processes: commercial/pilot overview (Authors’ graphic inspired by Sequeira and Santos, 2009).
There are several pitfalls that may actually limit piloting and commercial applications, such as mixing and mass transfer issues, poor process flexibility and even heat runaway. These issues can be efficiently solved or mitigated by transposition to continuous flow processes, which will enable industry to implement large scale electrosynthesis. The fact that almost all commercial electrochemical processes use flow cells is an important factor to emphasize in this conclusion (Goodridge and Scott, 1995; Sequeira and Santos, 2009; Atobe et al., 2018; Tanbouza et al., 2020).
Cross-disciplinary innovation is currently facilitating the development of new systems and their commercialization (Kirkaldy et al., 2018; Murray et al., 2019; Folgueiras-Amador et al., 2020). An example of this can be found in Ammonite electrolysis cells, which are developed by Green and associates in collaboration with Cambridge Reactor Design Ltd., who have elucidated reactor performance by means of model synthesis, namely the deprotection of PMB (para-methoxybenzyl) ethers and the methoxylation of N-formylpyrrolidine (Green et al., 2016; Green et al., 2017). Nevertheless, the most powerful example of organic electrochemistry is the synthesis of adiponitrile from acrylonitrile, generating up to 0.35 million tons/yr of adiponitrile, with a current efficiency close to 95% (Monsanto adiponitrile process) (Botte, 2014).
The application of photochemistry has experienced growing interest over the last decade, both in terms of academia and industrial realities. Commercial flow reactors are therefore becoming more readily available, in a move from home-built systems (Donnelly and Baumann, 2021).
The very first parameter to consider in photochemistry is light penetration. Thus, reactor dimensions are strictly related by the Lambert-Beer law and reaction media absorption. Flow processes overcome this issue by means of miniaturization, shortening the radiation path length. It is worth noticing that miniaturization technologies represent the real milestone in flow photochemistry, as they allow for unprecedented process intensification (Mizuno et al., 2016). In detail, a plethora of new photoreactors for continuous synthesis have been designed and produced: the Uniqsis PhotoSyn (Lima et al., 2018; Chen et al., 2019); the Firefly system from Cambridge Reactor Design (Elliott et al., 2016); the Vapourtec UV-150 reactor (Di Filippo and Baumann, 2020); and the Corning photoreactor system (Bianchi et al., 2020), which is a modified flow system for heterogeneous reactions, such as vortex (Britton et al., 2017), rotary (Clark et al., 2018), and oscillatory flow reactors (Rosso et al., 2020). All of this potentiality has led to a real rise in industrial R&D applications. Several reviews and books have been published on this topic, with attention being focused on applications of photochemistry in flow reactors (Gilmore and Seeberger, 2014; Oelgemöller et al., 2014; Pinho et al., 2015; Vaccaro, 2017). For this reason, only a few examples will be presented herein, with the sole aim of depicting the vast array of possibilities in the applicability of continuous-flow photochemical approaches in organic chemistry. Firstly, photomicroreactors have been widely exploited for cycloadditions, such as for diastereoselective photocycloadditions (Nijland and Harutyunyan, 2013; Brimioulle et al., 2015) that are enhanced by carbon dioxide (scCO2) as a solvent (Nishiyama et al., 2014), and, in general, for multiphase reaction systems (Mallia and Baxendale, 2016). Other examples involve photoisomerizations (Szymański et al., 2013; Baumann and Baxendale, 2015; Broichhagen et al., 2015), singlet oxygen mediated oxidations (Ogilby, 2010; Loponov et al., 2014), photocleavage/deprotection (Calin et al., 2013; Yueh et al., 2015), and photochemical decarboxylation (Dawes et al., 2015).
Several studies demonstrated how PEF are a versatile technology exploitable in different industrial areas in particular food processing. Among all the applications we can find solid/liquid extraction, pasteurization, drying and freezing, but also pesticides and contaminants remediation. In general, PEF consists in a treatment led by short electrical pulses (from μsec to msec) with field strength from 100 to 300 V/cm to 20–80 kV/cm (Koubaa et al., 2015). Inactivation of enzymes or pathogens is feasible by setting field strength to high values, without affecting general nutritional values (Sánchez-Vega et al., 2014). Working with low electric fields, on the other hand, it is possible to obtain a peculiar poration of biological membranes, exploitable for metabolites extraction or physical transformation (i.e. freezing and drying) (Barba et al., 2014; Deng et al., 2014). In general, the electroporation effect does not require high power consumption, and it increases the industrial attractiveness of PEF treatment. PEF attracted over the last years great interest for industrial by-product and agricultural residues valorisation (Rosello-Soto et al., 2015). Literature covered this topic with huge number of studies, evaluating different matrices according to their residual bioactive contents (i.e. catechins, phenolic acids, anthocyanins, vitamins, fatty acids) (Barba et al., 2015). It worth to mention that stability of these compounds have been extensively evaluated, in particular vitamins, polyphenols, amino acids, fatty acids. Different screenings have been made both on water-soluble vitamins (i.e. biotin, ascorbic acid, thiamine, folic acid, pantothenic acid and riboflavin) (Guderjan et al., 2007; Rivas et al., 2007) and fat-soluble vitamins (cholecalciferol, tocopherol, retinol), generally unaltered by pulsed fields (Bendicho et al., 2002; Cortés et al., 2006). PEF have been adopted also to reduce foods contaminants, such as Maillard-induced derivatives (i.e. acrylamide). The effects of electric fields on these compounds have been previously reviewed by Jaeger, et al. (2010), whilst other studies focused attention on pesticides, a crucial point for food processing as well. Degradation of diazinon, dimethoate, methamidophos, chlorpyrifos, pyrimethanil, vinclozolin, cyprodinil and procymidone were evaluated, in juices and wines (Chen et al., 2009; Zhang et al., 2012).
In plasma-based chemistry, gas discharge plasmas, generated from different power sources, provide a high-energy state that initiates ionization or electron impact-induced chemical reactions. The main applications in sustainable chemistry involve, for instance, the treatment and modification of biomass, and the destruction of waste and pollutants (Bruggeman et al., 2016; Dimitrakellis et al., 2022). To extend the discussion of cold plasma, this type of technique can rely on a few methods to generate RT plasma; low pressure glow discharge, dielectric barrier discharge (DBD), corona and plasma jets (Hippler et al., 2001). DBD plasma has been applied in flow mode for the degradation of several pollutants and even conversion, over air media. Piferi et al., have developed a plasma-assisted strategy for the abatement of Organic Volatile Compounds (VOCs), using propane, pentane and acetone as the model compounds (Piferi and Riccardi, 2022). The fast residence times of contaminated air flow were studied (approx. 20 min max.), revealing propane to be the most prone to degradation, with depletion efficiencies ranging between 2 and 7.5 g/kWh. Cold plasma was recently applied to convert CO2 to CO and O2, responding to the problem of carbon dioxide fixation/exploitation (Ding et al., 2022). Ding and co-workers proposed a flow protocol were ZrO2-coated frosted DBD plasma was exploited giving an overall conversion of 21.7%, under a flow rate of 10 ml/min, by exerting 14.5 W of discharge power and a max. Discharge voltage of 11.0 kV (2% of energy efficiency). A novel type of plasma system has made use of a tangled wire DBD reactor for the production of ammonia from N2 and H2 (Ma et al., 2021). Briefly, Ma et al., achieved the lowest energy cost (59.0 MJ/mol) for NH3 synthesis over a Cu electrode with a discharge power of 20 W, working at a flow rate of 250 ml/min. A DBD reactor has been exploited by Purwanto et al., to enhance the transesterification reaction for biodiesel production, achieving a 77.2% yield. The system applied a 5 wt% K2O/CaO–ZnO catalyst at 65°C with a weight hourly space velocity of 1.186 gfeed min−1 gcat−1 (Purwanto et al., 2020). Similar results (80.78% oleic acid conversion) have been achieved at RT with a flow rate of approx. 160 ml/min by Wu et al., in an homogeneous system (H2SO4 as a catalyst) (Wu et al., 2020). A plasma jet flow reactor has been studied for the continuous degradation of amoxicillin in waste water, with the effects of different types of gases being screened (N2, Air, Ar, O2) and degradation pathways being proposed via the determination of intermediates (Li et al., 2022). Acayanka et al., have also tested a recirculating system for amoxicillin degradation. They made use of gliding arc plasma and achieved an overall abatement of 98% (Acayanka et al., 2019). Regarding the degradation of pharmaceutically active compounds, the literature also reports the use of pulsed corona plasma technology for the continuous flow treatment of diclofenac and verapamil hydrochloride, which achieved an overall removal of 99% after fast treatment (max. 12 min) (Nippatlapalli et al., 2022). The cold-plasma technology is suitable for integration with other enabling technologies under flow conditions. For example, a recirculating hybrid reactor that combines US and pulsed discharge plasma has been developed for pollutant degradation, and Rhodamine B was adopted as the model compound. Complete degradation was achieved after 23.5 s working in acidic conditions with 32 kV of plasma discharge, 280 W of US power and with a 8 L/min flow rate (Komarov et al., 2020).
As mentioned in the introductory framework of this perspective, the implementation of continuous flow processing as a fundamental enabling technology has revolutionized the way chemistry is currently performed, from micro-to large-scale-based reactors. As outlined through this section on hybrid technologies, continuous flow methods can easily be combined to other sustainable technologies such as microwaves, ultrasound, photochemistry, electrochemistry, and inductive heating, among others, together with supported reagents/catalysts and a variety of solvent systems. Indisputably, the key application of such flow methods involves the synthesis of active pharmaceutical ingredients (APIs), some being essential WHO medicines. Thus, blockbuster drugs like celecoxib, efavirenz, fluconazole, imatinib, ribociclib, ibuprofen, hydroxychloroquine, valtarsan, tamoxifen, artemisinin, olanzapine, or atorvastatin, to name a few inhibitors, are manufactured under flow. This subsection cannot describe this issue in detail, although some considerations in the context of green chemistry are briefly discussed, with a few illustrations on API synthesis. Some recent overviews providing a general and well-balanced state-of-the-art status are recommended (Baumann and Baxendale, 2015; Porta et al., 2016; De Souza et al., 2018; Burange et al., 2022).
The implication of continuous processing is clearly compatible with the principles of green chemistry. In general, flow methods decrease the amount of raw materials and energy utilized in a given process, while maintaining real-time analysis, and augmented safety. Moreover, in-line reaction analysis enables facile automation, constant control of reaction parameters, and process reliability. Also, hybrid equipment facilitates process intensification leading to higher productivity and purity of reaction products (Burange et al., 2022; Kar et al., 2022). That said, a flow route is not necessarily superior to a conventional method, especially when all reaction metrics are critically examined. In fact, some pharmaceuticals benefit from hybrid batch-flow syntheses, while others are still produced by conventional approaches (Kar et al., 2022). The advantages of conducting synthesis in flow devices over batch protocols are mainly associated to faster completion under mild conditions and less unit operations, all figures resulting in a lower environmental impact and in a reduced footprint (Porta et al., 2016).
Figure 12 showcases the above-mentioned pluses, summarizing the flow synthesis of olanzapine, an antipsychotic drug used against schizophrenia and bipolar disorders. The multistep continuous synthesis took advantage of inductive heating (IH) as enabling technology to significantly accelerate reaction rates and to increase process efficiency (Hartwig et al., 2013). Here, an electromagnetic field at medium or high frequency is induced on magnetic nanoparticles to increase rapidly the temperature. The first step, a Buchwald-Hartwig coupling between an aryl iodide and an aminothiazole using Pd2 (dba)3 as catalyst and Xantphos as ligand took place in a reactor filled with steel beads and heated inductively at 50°C (15 kHz). After quenching with water and in-line extraction in a glass column, the mixture was passed through silica to remove the catalyst. Nitroaromatic compound 6 was reduced with Et3SiH and Pd/C at 40°C. The resulting aniline 7) could be obtained in quantitative yield. The reaction outcome was treated with HCl/MeOH and heated at 140°C (IH at 800 kHz). This acid-catalyzed reaction led to cyclic product 8 in 88% overall yield. The final step involving reaction of the latter with piperazine 9 was conducted on a reactor containing an inductive material (MagSilica) and silica-supported Ti(OiPr)4 and heated at 85°C (IH at 25 kHz), which led to olanzapine (10) in 83% yield.
FIGURE 12. Continuous flow synthesis of antipsychotic drug Olanzapine. Reprinted with permission from (Porta et al., 2016). Copyright (2016) American Chemical Society.
A six-step continuous flow synthesis of diclofenac (as sodium salt), a well-known non-stereoidal antiinflammatory drug (NSAID), has been recently developed starting from inexpensive aniline and chloroacetic acid (Wang et al., 2022). The entire process is displayed in Figure 13 and comprises a cascade etherification-Smiles rearrangement, in which the resulting 2-chloro-N-phenylacetamide and 2,6-dichlorophenol are converted into a hydroxyacetyl diphenylamine derivative that skips the formation of 2,6-dichloro-N-diphenylaniline. Further chlorination was followed by an intramolecular Friedel-Crafts-type cyclization and hydrolysis affording the wanted drug (in 63% isolated yield and a residence time of less than 3.5 h). The route is clearly advantageous over the batch protocol in terms of higher atom and step economies, within shorter reaction times, and allowing automatic operations.
FIGURE 13. Elaborated flow synthesis of sodium diclofenac involving sequential amination, chlorination, and hydrolysis protocols. Reprinted with permission from (Wang et al., 2022). Copyright (2022) Wiley-VCH GmbH.
The simple use of a single enabling technology is no longer satisfactory for the latest synthetic approaches, making the integration of two or more of these enabling techniques necessary (Kirschning et al., 2006). For this reason, the integration of flow approaches has increasingly acquired importance, allowing reaction intensification to be merged with high productivity rates. Almost all of the technologies listed in Table 2 have been successfully coupled with each other.
Continuous flow technology can also be synergistically combined with US. Jolhe et al., have studied the US-assisted preparation of performic acid (PFA) in a continuous flow micro-structured reactor (Jolhe et al., 2017). The optimum reaction conditions for PFA formation are a reactant flow rate of 50 ml/h, a molar ratio of formic acid to H2O2 of 1:1 and a temperature of 40°C. In addition, the authors have performed a comparative investigation of PFA synthesis both in batch and continuous flow systems. The first approach required 60 min for reaction completion, whilst, in flow mode, only 10 min were required and the maximum concentrations of PFA were obtained (3.55 mol/L). Several papers have reported the application of combined MW-US irradiation in different fields, including organic/inorganic synthesis, pollutant degradation, chemical digestion and even plant extraction (Cravotto and Cintas, 2007). The first application of this set-up resulted in biodiesel production. The synergy of MW and US leads to higher process efficiency; while MW dielectric heating can selectively act on a reaction mixture, US increases mass and heat transfer. There are two approaches to combining these technologies. The first involves the use of two different reactors, one for each technology. The second set-up involves simultaneous US and MW irradiation in the same hybrid reactor, usually with the use of a non-metallic horn (Pyrex, quartz, ceramic horns and specific polymers such as PEEK). Martina et al. (2016) another example of combined enabling technologies can be found in the large-scale ultrasonic atomization-type microwave nano-particle continuous-flow synthesis reactor created by the Kojundo Chemical Lab. Co. Ltd. It is a 3.5 m hybrid US-microwave reactor that has been used for the flow synthesis of ferrite on an industrial scale (Horikoshi and Serpone, 2013). Moreover, the versatility of US for flow chemistry purposes has been promptly illustrated by Horie and coworkers who devised a hybrid microreactor for the efficient photodimerization of maleic anhydride into cyclobutane tetracarboxylic dianhydride (Horie et al., 2010). The reaction solution was passed through a mm-sized fluorinated ethylene propylene (FEP) tube, which was simultaneously irradiated with a high-pressure Hg lamp (400 W) and an ultrasonic bath (100 W, 39 kHz) to prevent the deposition and adhesion of insoluble products (Figure 14). The hybrid flow microreactor could be operated continuously for more than 16 h without clogging and this method led to better product quality, improved conversion and reduced waste formation compared to a batch reactor.
FIGURE 14. Flow cell for maleic anhydride dimerization under photochemical and ultrasonic irradiation (Authors’ graphic inspired by Horie et al., 2010).
Other examples of the combination of enabling technologies are available in literature. For example, the combination of a reactive extrusion process and US has been studied for the preparation of crosslinked polypropylene (Mingtao et al., 2017). Polypropylene is widely used in the thermoforming, blow molding and foaming processes. Therefore, the crosslinked structure in polypropylene is highly desired to fulfill the requirement of high melt strength. Thanks to its high productivity and low cost, the reactive extrusion process, in the presence of a low peroxide concentration, is preferred for crosslinked polypropylene preparation, but this process alone might also deteriorate the extent of branching and crosslinking due to fewer reactive points. Yang and coworkers have thus applied US to the outlet of the extruder, inducing partial radical recombination with the resulting formation of a new crosslinked system and higher molecular weight. The US-assisted extrusion process can be considered a robust method for controlling the crosslinked system and promoting melt strength.
In a recent work, a combination of non-conventional technologies has also been applied to water treatment via simultaneous irradiation with hydrodynamic cavitation and plasma discharge (Abramov et al., 2021). Treatment with the combination of cavitation and plasma produces shock-waves via the action of collapsing bubbles, ultraviolet radiation, hydroxyl radicals and ozone formation (Figure 15). All of these effects participated in producing a peculiar effect on the treated liquid, such as disinfection by cavitation, disinfection by radicals and ozone, disinfection by UV light, prolonged oxidation after treatment and homogenization. The authors analysed, in particular, the effects of this treatment on E. Coli concentration. With the hybrid set-up, more than 95% of microorganisms were suppressed, which contrasts with the 10% reduction provided by hydrodynamic cavitation alone. Additionally, a 7% methanol solution was used as a model organic pollutant to study the effectiveness of the combined system on pollutant decomposition in water. After treatment, the concentration of methanol was decreased 5-fold. Several publications have described the combination of MW technology and micro-channel reactors under flow mode conditions.
FIGURE 15. Hydrodynamic and plasma discharge: Laboratory set-up for useful for advanced oxidation process (AOP). Reprinted with permission from (Abramov et al., 2021). Copyright (2021) Elsevier.
He et al., have performed a Suzuki-Miyaura cross-coupling reaction using a heterogeneous Pd-supported catalyst (Pd/Al2O3) in a custom-built microreactor heated by means of MW irradiation (He et al., 2004). Two-reactor designs have been developed. In the first (Figure 16A), the top and bottom plates of the microreactor were both 3 mm thick. The catalyst channel was 1.5 mm wide, 80 µm deep and 15 mm long and connected to the inlet and outlet reservoirs by channels that were 130 µm wide and 50 µm deep. In the second (Figure 16B), the thickness of the top plate is 10 mm and the bottom plate is 3 mm, the catalyst channel which was 1.5 mm wide, 50 µm deep and 15 mm long. The dimensions of the catalyst channel were unaltered, and a thin gold film, with two different thicknesses (10 or 15 nm), was added to the outer surface (He et al., 2004).
FIGURE 16. Microreactor employed in Suzuki–Miyaura couplings (He et al., 2004). Reproduced with permission of Royal Society of Chemistry.).
Different heating methods for the microreactor design were tested: room temperature, oil bath, MW heating and MW combined with gold coating. In all cases, a flow rate of 5 μl min−1 was used and the best conversion (99%) was obtained at low MW power (55 W) with the gold coating to enhance heat transfer. Finally, the authors compared the two designs and observed that design A required longer residence times due to the lower flow rate, but required less catalyst and less MW energy, giving good product yields (between 72% and 90%, with reference to the starting compound).
General consensus indicates that chemistry should be re-designed to facilitate safe, secure and sustainable research. Such concerns appear to be critical in contemporary science. This is particularly true for people working in chemical companies and laboratories, where work and production may involve potential risks of exposure to hazardous materials, along with spills into the environment, thereby increasing damage still further. Together with green chemistry principles for the prevention and minimization of impacts, machined chemistry can help us to enhance efficiency while reducing waste and cost. This article provides a concise overview of all the main synthetic technologies used for process intensification, either alone or in combination, in accordance with the general trend to move from batch to continuous-flow production.
Literature search MC; Original Draft Preparation, GG, ECG and GC; Review and Editing, PC and GC.
This research was funded by the regional project “Green Pharma” (F.E.S.R. 2014/2020). Financial support from the Junta de Extremadura and European Regional Development Fund (GR21039) is warmly appreciated as well.
The authors declare that the research was conducted in the absence of any commercial or financial relationships that could be construed as a potential conflict of interest.
All claims expressed in this article are solely those of the authors and do not necessarily represent those of their affiliated organizations, or those of the publisher, the editors and the reviewers. Any product that may be evaluated in this article, or claim that may be made by its manufacturer, is not guaranteed or endorsed by the publisher.
Aboud, S. A., Altemimi, A. B., Al-HiIphy, A., Yi-Chen, L., and Cacciola, F. (2019). A comprehensive review on infrared heating applications in food processing. Molecules 24, 4125. doi:10.3390/molecules24224125
Abramov, V. O., Abramova, A. V., Cravotto, G., Nikonov, R. V., Fedulov, I. S., and Ivanov, V. K. (2021). Flow-mode water treatment under simultaneous hydrodynamic cavitation and plasma. Ultrason. Sonochem. 70, 105323. doi:10.1016/j.ultsonch.2020.105323
Acayanka, E., Tarkwa, J. B., and Laminsi, S. (2019). Evaluation of energy balance in a batch and circulating non-thermal plasma reactors during organic pollutant oxidation in aqueous solution. Plasma Chem. Plasma process. 39, 75–87. doi:10.1007/s11090-018-9946-7
Alfano, A., Brindisi, M., and Lange, H. (2021). Flow synthesis approaches to privileged scaffolds – recent routes reviewed for green and sustainable aspects. Green Chem. 23, 2233–2292. doi:10.1039/D0GC03883K
Alkanan, Z. T., Altemimi, A. B., Al-Hilphy, A. R. S., Watson, D. G., and Pratap-Singh, A. (2021). Ohmic heating in the food industry: Developments in concepts and applications during 2013–2020. Appl. Sci. (Basel). 11, 2507. doi:10.3390/app11062507
Amri, N., and Wirth, T. (2021). Flow electrosynthesis of sulfoxides, sulfones, and sulfoximines without supporting electrolytes. J. Org. Chem. 86 (22), 15961–15972. doi:10.1021/acs.joc.1c00860
Andersen, J., Starbuck, H., Tia, C., Martin, S., and Mack, J. (2021). Milligram-scale, temperature-controlled ball milling to provide an informed basis for scale-up to reactive extrusion. Green Chem. 23, 8501–8509. doi:10.1039/d1gc02174e
Atobe, M., Tateno, H., and Matsumura, Y. (2018). Applications of flow microreactors in electrosynthetic processes. Chem. Rev. 118, 4541–4572. doi:10.1021/acs.chemrev.7b00353
Barba, F. J., Brianceau, S., Turk, M., Boussetta, N., and Vorobiev, E. (2015). Effect of alternative physical treatments (ultrasounds, pulsed electric fields, and high-voltage electrical discharges) on selective recovery of bio-compounds from fermented grape pomace. Food bioproc. Tech. 8 (5), 1139–1148. doi:10.1007/s11947-015-1482-3
Barba, F. J., Grimi, N., and Vorobiev, E. (2014). New approaches for the use of nonconventional cell disruption technologies to extract potential food additives and nutraceuticals from microalgae. Food Eng. Rev. 7 (1), 45–62. doi:10.1007/s12393-014-9095-6
Barge, A., Baricco, F., Cravotto, G., Fretta, R., and Lattuada, L. (2020). Mechanochemistry applied to the synthesis of X-ray contrast agent. ACS Sustain. Chem. Eng. 8, 12825–12830. doi:10.1021/acssuschemeng.0c02928
Baumann, M., and Baxendale, I. R. (2015). The synthesis of active pharmaceutical ingredients (APIs) using continuous flow chemistry. Beilstein J. Org. Chem. 11, 1194–1219. doi:10.3762/bjoc.11.134
Benaskar, F., Ben-Abdelmoumen, A., Patil, N. G., Rebrov, E. V., Meuldijk, J., Hulshof, L. A., et al. (2011). Cost analysis for a continuously operated fine chemicals production plant at 10 kg/day using a combination of microprocessing and microwave heating. J. Flow. Chem. 2, 74–89. doi:10.1556/jfchem.2011.00015
Bendicho, S., Espachs, A., Arántegui, J., and Martín, O. (2002). Effect of high intensity pulsed electric fields and heat treatments on vitamins of milk. J. Dairy Res. 69 (1), 113–123. doi:10.1017/s0022029901005258
Bianchi, P., Petit, G., and Monbaliu, J-C. M. (2020). Scalable and robust photochemical flow process towards small spherical gold nanoparticles. React. Chem. Eng. 5, 1224–1236. doi:10.1039/D0RE00092B
Bolt, R. R. A., Leitch, J. A., Jones, A. C., Nicholson, W. L., and Browne, D. L. (2022). Continuous flow mechanochemistry: Reactive extrusion as an enabling technology in organic synthesis. Chem. Soc. Rev. 51, 4243–4260. doi:10.1039/D1CS00657F
Botte, G. G. (2014). Electrochemical manufacturing in the chemical industry. Interface Mag. 23, 49–55. doi:10.1149/2.F04143IF
Brimioulle, R., Lenhart, D., Maturi, M. M., and Bach, T. (2015). Enantioselective catalysis of photochemical reactions. Angew. Chem. Int. Ed. 54 (13), 3872–3890. doi:10.1002/anie.201411409
Britton, J., and Raston, C. L. (2017). Multi-step continuous-flow synthesis. Chem. Soc. Rev. 46, 1250–1271. doi:10.1039/C6CS00830E
Britton, J., Stubbs, K. A., Weiss, G. A., and Raston, C. L. (2017). Vortex fluidic chemical transformations. Chem. Eur. J. 23, 13270–13278. doi:10.1002/chem.201700888
Broichhagen, J., Frank, J. A., and Trauner, D. (2015). A roadmap to success in photopharmacology. Acc. Chem. Res. 48 (7), 1947–1960. doi:10.1021/acs.accounts.5b00129
Bruggeman, P. J., Kushner, M. J., Locke, B. R., Gardeniers, J. G. E., Graham, W. G., Graves, D. B., et al. (2016). Plasma-liquid interactions: A review and roadmap. Plasma Sources Sci. Technol. 25, 053002. doi:10.1088/0963-0252/25/5/053002
Bucciol, F., Colia, M., Calcio Gaudino, E., and Cravotto, G. (2020). Enabling technologies and sustainable catalysis in biodiesel preparation. Catalysts 10 (9), 988. doi:10.3390/catal10090988
Bucciol, F., and Cravotto, G. (2022). “The contribution of green chemistry to industrial organic chemistry,” in Sustainable organic synthesis: Tools and strategies. Editors S. Protti, and A. Palmieri (Cambridge: Royal Society), 549–574.
Buglioni, L., Beslac, M., and Noël, T. (2021). Dehydrogenative azolation of arenes in a microflow electrochemical reactor. J. Org. Chem. 86 (22), 16195–16203. doi:10.1021/acs.joc.1c01409
Burange, A. S., Osman, S. M., and Luque, R. (2022). Understanding flow chemistry for the production of active pharmaceutical ingredients. iScience 25, 103892. doi:10.1016/j.isci.2022.103892
Calcio Gaudino, E., Grillo, G., Manzoli, M., Tabasso, S., Maccagnan, S., and Cravotto, G. (2022). Mechanochemical applications of reactive extrusion from organic synthesis to catalytic and active materials. Molecules 27, 449. doi:10.3390/molecules27020449
Calcio Gaudino, E., Manzoli, M., Carnaroglio, D., Wu, Z., Grillo, G., Rotolo, L., et al. (2018). Sonochemical preparation of alumina-spheres loaded with Pd nanoparticles for 2-butyne-1, 4-diol semi-hydrogenation in a continuous flow microwave reactor. RSC Adv. 8, 7029–7039. doi:10.1039/C8RA00331A
Calin, O., Eller, S., and Seeberger, P. H. (2013). Automated polysaccharide synthesis: Assembly of a 30mer mannoside. Angew. Chem. Int. Ed. 52 (22), 5862–5865. doi:10.1002/anie.201210176
Cantillo, D. (2022). Synthesis of active pharmaceutical ingredients using electrochemical methods: Keys to improve sustainability. Chem. Commun. 58, 619–628. doi:10.1039/D1CC06296D
Cao, Q., Howard, J. L., Crawford, D. E., James, S. L., and Browne, D. L. (2018). Translating solid state organic synthesis from a mixer mill to a continuous twin screw extruder. Green Chem. 20, 4443–4447. doi:10.1039/C8GC02036A
Ceylan, S., Coutable, L., Wegner, J., and Kirschning, A. (2011). Inductive heating with magnetic materials inside flow reactors. Chem. Eur. J. 17, 1884–1893. doi:10.1002/chem.201002291
Chen, F., Zeng, L., Zhang, Y., Liao, X., Ge, Y., Hu, X., et al. (2009). Degradation behaviour of methamidophos and chlorpyrifos in apple juice treated with pulsed electric fields. Food Chem. 112 (4), 956–961. doi:10.1016/j.foodchem.2008.07.016
Chen, Y., May, O., Blakemore, D. C., and Ley, S. V. (2019). A Photoredox coupling reaction of Benzylboronic esters and carbonyl compounds in batch and flow. Org. Lett. 21, 6140–6144. doi:10.1021/acs.orglett.9b02307
Cintas, P., Mantegna, S., Calcio Gaudino, E., and Cravotto, G. (2010). A new pilot flow reactor for high-intensity ultrasound irradiation. Application to the synthesis of biodiesel. Ultrason. Sonochem. 17 (6), 985–989. doi:10.1016/j.ultsonch.2009.12.003
Clark, C. A., Lee, D. S., Pickering, S. J., Poliakoff, M., and George, M. W. (2018). UV PhotoVap: Demonstrating how a simple and versatile reactor based on a conventional rotary evaporator can be used for UV photochemistry. Org. Process Res. Dev. 22, 595–599. doi:10.1021/acs.oprd.8b00037
Comer, E., and Organ, M. G. (2005). A microreactor for microwave-assisted capillary (continuous flow) organic synthesis. J. Am. Chem. Soc. 127, 8160–8167. doi:10.1021/ja0512069
Cortés, C., Torregrosa, F., Esteve, M. J., and Frígola, A. (2006). Carotenoid profile modification during refrigerated storage in untreated and pasteurized orange juice and orange juice treated with high-intensity pulsed electric fields. J. Agric. Food Chem. 54 (17), 6247–6254. doi:10.1021/jf060995q
Cravotto, G., and Cintas, P. (2007). The combined use of microwaves and ultrasound: Improved tools in process chemistry and organic synthesis. Chem. Eur. J. 13 (7), 1902–1909. doi:10.1002/chem.200601845
Cravotto, G., and Cintas, P. (2006). Power ultrasound in organic synthesis: Moving cavitational chemistry from academia to innovative and large-scale applications. Chem. Soc. Rev. 35, 180–196. doi:10.1039/B503848K
Crawford, D. E., Miskimmin, C. K., Cahir, J., and James, S. L. (2017b). Continuous multi-step synthesis by extrusion – telescoping solvent-free reactions for greater efficiency. Chem. Commun. 53, 13067–13070. doi:10.1039/C7CC06010F
Crawford, D. E., Miskimmin, C. K. G., Albadarin, A. B., Walker, G., and James, S. L. (2017a). Organic synthesis by twin screw extrusion (TSE): Continuous, scalable and solvent-free. Green Chem. 19, 1507–1518. doi:10.1039/C6GC03413F
Crawford, D. E., Porcheddu, A., McCalmont, A. S., Delogu, F., James, S. L., and Colacino, E. (2020). Solvent-free, continuous synthesis of hydrazone-based active pharmaceutical ingredients by twin-screw extrusion. ACS Sustain. Chem. Eng. 8, 12230–12238. doi:10.1021/acssuschemeng.0c03816
Dawes, G. J. S., Scott, E. L., Le Nôtre, J., Sanders, J. P. M., and Bitter, J. H. (2015). Deoxygenation of biobased molecules by decarboxylation and Decarbonylation−A review on the role of heterogeneous, homogeneous and bio-catalysis. Green Chem. 17 (6), 3231–3250. doi:10.1039/C5GC00023H
De Souza, J. M., Galaverna, R., De Souza, A. A. N., Brocksom, T. J., Pastre, J. C., De Souza, R. O. M. A., et al. (2018). Impact of continuous flow chemistry in the synthesis of natural products and active pharmaceutical ingredients. An. Acad. Bras. Cienc. 90, 1131–1174. doi:10.1590/0001-3765201820170778
Deng, Q., Zinoviadou, K. G., Galanakis, C. M., Orlien, V., Grimi, N., Vorobiev, E., et al. (2014). The effects of conventional and non-conventional processing on glucosinolates and its derived forms, isothiocyanates: Extraction, degradation, and applications. Food Eng. Rev. 7 (3), 357–381. doi:10.1007/s12393-014-9104-9
Di Filippo, M., and Baumann, M. (2020). Continuous flow synthesis of Quinolines via a scalable tandem Photoisomerization-cyclization process. Eur. J. Org. Chem. 2020, 6199–6211. doi:10.1002/ejoc.202000957
Dimitrakellis, P., Delikonstantis, E., Stefanidis, G. D., and Vlachos, D. G. (2022). Plasma technology for lignocellulosic biomass conversion toward an electrified biorefinery. Green Chem. 24, 2680–2721. doi:10.1039/D1GC03436G
Ding, W., Xia, M., Shen, C., Wang, Y., Zhang, Z., Tu, X., et al. (2022). Enhanced CO2 conversion by frosted dielectric surface with ZrO2 coating in a dielectric barrier discharge reactor. J. CO2 Util. 61, 102045. doi:10.1016/j.jcou.2022.102045
Donnelly, K., and Baumann, M. (2021). Scalability of photochemical reactions in continuous flow mode. J. Flow. Chem. 11, 223–241. doi:10.1007/s41981-021-00168-z
Egami, H., Tamaoki, S., Abe, M., Ohneda, N., Yoshimura, T., Okamoto, T., et al. (2018). Scalable microwave-assisted johnson–claisen rearrangement with a continuous flow microwave system. Org. Process Res. Dev. 22 (8), 1029–1033. doi:10.1021/acs.oprd.8b00185
El-Remaily, M. A. E. A. A. A., Soliman, A. M. M., and Elhady, O. M. (2020). Green method for the synthetic Ugi reaction by twin screw extrusion without a solvent and catalyst. ACS Omega 5, 6194–6198. doi:10.1021/acsomega.0c00369
Elliott, L. D., Berry, M., Harji, B., Klauber, D., Leonard, J., and Booker-Milburn, K. I. (2016). A small-footprint, high-capacity flow reactor for UV photochemical synthesis on the kilogram scale. Org. Process Res. Dev. 20, 1806–1811. doi:10.1021/acs.oprd.6b00277
Elsherbini, M., Winterson, B., Alharbi, H., Folgueiras-Amador, A. A., Génot, C., and Wirth, T. (2019). Continuous-flow electrochemical generator of hypervalent iodine reagents: Synthetic applications. Angew. Chem. Int. Ed. 58, 9811–9815. doi:10.1002/anie.201904379
Elsherbini, M., and Wirth, T. (2019). Electroorganic synthesis under flow conditions. Acc. Chem. Res. 52, 3287–3296. doi:10.1021/acs.accounts.9b00497
Escobedo, R., Miranda, R., and Martínez, J. (2016). Infrared irradiation: Toward green chemistry, a review. Int. J. Mol. Sci. 17, 453. doi:10.3390/ijms17040453
Ferlin, F., Lanari, D., and Vaccaro, L. (2020). Sustainable flow approaches to active pharmaceutical ingredients. Green Chem. 22, 5937–5955. doi:10.1039/D0GC02404J
Ferlin, F., Valentini, F., Sciosci, D., Menzio, J., Cravotto, G., Martina, K., et al. (2021). Si-Gly-CD-PdNPs as a hybrid heterogeneous catalyst for environmentally friendly continuous flow Sonogashira cross-coupling. Green Chem. 23, 7210–7218. doi:10.1039/D1GC02490F
Folgueiras-Amador, A. A., Qian, X., Xu, H., and Wirth, T. (2017). Catalyst- and supporting-electrolyte-free electrosynthesis of benzothiazoles and thiazolopyridines in continuous flow. Chem. Eur. J. 7, 487–491. doi:10.1002/chem.201705016
Folgueiras-Amador, A. A., Teuten, A. E., Pletcher, D., and Brown, R. C. D. (2020). A design of flow electrolysis cell for ‘Home’ fabrication. React. Chem. Eng. 5, 712–718. doi:10.1039/D0RE00019A
Galant, O., Cerfeda, G., McCalmont, A. S., James, S. L., Porcheddu, A., Delogu, F., et al. (2022). Mechanochemistry can reduce life cycle environmental impacts of manufacturing active pharmaceutical ingredients. ACS Sustain. Chem. Eng. 10 (4), 1430–1439. doi:10.1021/acssuschemeng.1c06434
Gilmore, K., and Seeberger, P. H. (2014). Continuous flow photochemistry. Chem. Rec. 14, 410–418. doi:10.1002/tcr.201402035
Goodridge, F., and Scott, K. (1995). “Electrolytic reactor design, selection, and scale-up,” in Electrochemical process engineering (Boston, MA: Springer), 177–244. doi:10.1007/978-1-4899-0224-5_5
Green, R. A., Brown, R. C. D., Pletcher, D., and Harji, B. (2016). An extended channel length microflow electrolysis cell for convenient laboratory synthesis. Electrochem. Commun. 73, 63–66. doi:10.1016/j.elecom.2016.11.004
Green, R. A., Jolley, K. E., Al-Hadedi, A. A. M., Pletcher, D., Harrowven, D. C., De Frutos, O., et al. (2017). Electrochemical deprotection of para-methoxybenzyl ethers in a flow electrolysis cell. Org. Lett. 19, 2050–2053. doi:10.1021/acs.orglett.7b00641
Grillo, G., Manzoli, M., Bucciol, F., Tabasso, S., Tabanelli, T., Cavani, F., et al. (2021). Hydrogenation of levulinic acid to γ-valerolactone via green microwave-assisted reactions either in continuous flow or solvent-free batch processes. Ind. Eng. Chem. Res. 60 (46), 16756–16768. doi:10.1021/acs.iecr.1c02960
Guderjan, M., Elez-Martinez, P., and Knorr, D. (2007). Application of pulsed electric fields at oil yield and content of functional food ingredients at the production of rapeseed oil. Innovative Food Sci. Emerg. Technol. 8 (1), 55–62. doi:10.1016/j.ifset.2006.07.001
Gutmann, B., Cantillo, D., and Kappe, C. O. (2015). Continuous flow technology-a tool for the safe manufacturing of active pharmaceutical ingredients. Angew. Chem. Int. Ed. 54, 6688–6728. doi:10.1002/anie.201409318
Gutmann, B., and Kappe, C. O. (2017). Forbidden chemistries - paths to a sustainable future engaging continuous processing. J. Flow. Chem. 7, 65–71. doi:10.1556/1846.2017.00009
Hartman, R. L. (2012). Managing solids in microreactors for the upstream continuous processing of fine chemicals. Org. Process Res. Dev. 16, 870–887. doi:10.1021/op200348t
Hartwig, J., Ceylan, S., Kupracz, L., Coutable, L., and Kirschning, A. (2013). Heating under high-frequency inductive conditions: Application to the continuous synthesis of the neurolepticum olanzapine (zyprexa). Angew. Chem. Int. Ed. 52, 9813–9817. doi:10.1002/anie.201302239
He, P., Haswell, S. J., and Fletcher, P. D. (2004). Microwave heating of heterogeneously catalysed Suzuki reactions in a micro reactor. Lab. Chip 4 (1), 38–41. doi:10.1039/b313057f
R. Hippler, S. Pfau, M. Schmidt, and K. H. Schoenbach (Editors) (2001). Low temperature plasma physics: Fundamental aspects and applications (Weinheim, Germany: Wiley-VCH Verlag GmbH & Co.).
Horie, T., Sumino, M., Tanaka, T., Matsushita, Y., Ichimura, T., and Yoshida, J.-i. (2010). Photodimerization of maleic anhydride in a microreactor without clogging. Org. Process Res. Dev. 14, 405–410. doi:10.1021/op900306z
Horikoshi, S., and Serpone, N. (2019). Microwave flow chemistry as a methodology in organic syntheses, enzymatic reactions, and nanoparticle syntheses. Chem. Rec. 19, 118–139. doi:10.1002/tcr.201800062
S. Horikoshi, and N. Serpone (Editors) (2013). Microwaves in nanoparticle synthesis: Fundamentals and applications (Weinheim, Germany: Wiley-VCH VerlagGmbH&Co.).
Isoni, V., Mendoza, K., Lim, E., and Teoh, K. (2017). Screwing NaBH4 through a barrel without a bang: A kneaded alternative to fed-batch carbonyl reductions org. Org. Process Res. Dev. 21, 992–1002. doi:10.1021/acs.oprd.7b00107
Jaeger, H., Janositz, A., and Knorr, D. (2010). The Maillard reaction and its control during food processing. The potential of emerging technologies. Pathol. Biol. 58 (3), 207–213. doi:10.1016/j.patbio.2009.09.016
Jolhe, P. D., Bhanvase, B. A., Patil, V. S., Sonawane, S. H., and Potoroko, I. (2017). Ultrasound assisted synthesis of performic acid in a continuous flow microstructured reactor. Ultrason. Sonochem. 39, 153–159. doi:10.1016/j.ultsonch.2017.03.059
Kar, S., Sanderson, H., Roy, K., Benfenati, E., and Leszczynski, J. (2022). Green chemistry in the synthesis of pharmaceuticals. Chem. Rev. 122, 3637–3710. doi:10.1021/acs.chemrev.1c00631
Kaupp, G., Naimi-Jamal, M. R., and Schmeyers, J. (2002). Quantitative reaction cascades of ninhydrin in the solid state. Chem. Eur. J. 8, 594–600. doi:10.1002/1521-3765(20020201)8:3<594:aid-chem594>3.0.co;2-5
Kaupp, G., Naimi-Jamal, M. R., and Schmeyers, J. (2003). Solvent-free Knoevenagel condensations and Michael additions in the solid state and in the melt with quantitative yield. Tetrahedron 59, 3753–3760. doi:10.1016/s0040-4020(03)00554-4
Kaur, N., and Singh, A. K. (2016). Ohmic heating: Concept and applications-A review. Crit. Rev. Food Sci. Nutr. 56, 2338–2351. doi:10.1080/10408398.2013.835303
Kawamata, Y., Hayashi, K., Carlson, E., Shaji, S., Waldmann, D., Simmons, B. J., et al. (2021). Chemoselective electrosynthesis using rapid alternating polarity. J. Am. Chem. Soc. 143, 16580–16588. doi:10.1021/jacs.1c06572
Kirkaldy, N., Chisholm, G., Chen, J. J., and Cronin, L. (2018). A practical, organic-mediated, hybrid electrolyser that decouples hydrogen production at high current densities. Chem. Sci. 9, 1621–1626. doi:10.1039/c7sc05388f
Kirschning, A., Kupracz, L., and Hartwig, J. (2012). New synthetic opportunities in miniaturized flow reactors with inductive heating. Chem. Lett. 41, 562–570. doi:10.1246/cl.2012.562
Kirschning, A., Solodenko, W., and Mennecke, K. (2006). Combining enabling techniques in organic synthesis: Continuous flow processes with heterogenized catalysts. Chem. Eur. J. 12, 5972–5990. doi:10.1002/chem.200600236
Kockmann, N., Thenée, P., Fleischer-Trebes, C., Laudadio, G., and Noël, T. (2017). Safety assessment in development and operation of modular continuous-flow processes. React. Chem. Eng. 2, 258–280. doi:10.1039/C7RE00021A
Komarov, S., Yamamoto, T., Fang, Y., and Hariu, D. (2020). Combined effect of acoustic cavitation and pulsed discharge plasma on wastewater treatment efficiency in a circulating reactor: A case study of rhodamine B. Ultrason. Sonochemistry 68, 105236. doi:10.1016/j.ultsonch.2020.105236
Koubaa, M., Rosello-Soto, E., Sic-Zlabur, J., Rezek-Jambrak, A., Brncic, M., Grimi, N., et al. (2015). Current and new insights in the sustainable and green recovery of nutritionally valuable compounds from Stevia rebaudiana Bertoni. J. Agric. Food Chem. 63 (31), 6835–6846. doi:10.1021/acs.jafc.5b01994
Li, W., Zhou, R., Zhou, R., Weerasinghe, J., Zhang, T., Gissibl, A., et al. (2022). Insights into amoxicillin degradation in water by non-thermal plasmas. Chemosphere 291, 132757. doi:10.1016/j.chemosphere.2021.132757
Lima, F., Grunenberg, L., Rahman, H. B. A., Labes, R., Sedelmeier, J., and Ley, S. V. (2018). Organic photocatalysis for the radical couplings of boronic acid derivatives in batch and flow. Chem. Commun. 54, 5606–5609. doi:10.1039/C8CC02169D
Loponov, K. N., Lopes, J., Barlog, M., Astrova, E. V., Malkov, A. V., and Lapkin, A. A. (2014). Optimization of a scalable photochemical reactor for reactions with singlet oxygen. Org. Process Res. Dev. 18 (11), 1443–1454. doi:10.1021/op500181z
Ma, Y., Tian, Y., Zeng, Y., and Tu, X. (2021). Plasma synthesis of ammonia in a tangled wire dielectric barrier discharge reactor: Effect of electrode materials. J. Energy Inst. 99, 137–144. doi:10.1016/j.joei.2021.09.002
Mallia, C. J., and Baxendale, I. R. (2016). The use of gases in flow synthesis. Org. Process Res. Dev. 20, 327–360. doi:10.1021/acs.oprd.5b00222
Martina, K., Cravotto, G., and Varma, R. S. (2021). Impact of microwaves on organic synthesis and strategies toward flow processes and scaling up. J. Org. Chem. 86, 13857–13872. doi:10.1021/acs.joc.1c00865
Martina, K., Rotolo, L., Porcheddu, A., Delogu, F., Cravotto, G., Colacino, E., et al. (2018). High throughput mechanochemistry: Application to parallel synthesis of benzoxazines. Chem. Commun. 54, 551–554. doi:10.1039/C7CC07758K
Martina, K., Tagliapietra, S., Barge, A., and Cravotto, G. (2016). Combined microwaves/ultrasound, a hybrid technology. Top. Curr. Chem. (Cham). 374, 79. doi:10.1007/s41061-016-0082-7
Martínez, R. F., Cravotto, G., and Cintas, P. (2021). Organic sonochemistry: A chemist’s timely perspective on mechanisms and reactivity. J. Org. Chem. 86, 13833–13856. doi:10.1021/acs.joc.1c00805
Mingtao, Y., Jiang, L., and Shaoyun, G. (2017). A reactive extrusion process with the aid of ultrasound for preparing crosslinked polypropylen. Polym. Eng. Sci. 57, 821–829. doi:10.1002/pen.24457
Mizuno, K., Nishiyama, Y., Ogaki, T., Terao, K., Ikeda, H., and Kakiuchi, K. (2016). Utilization of microflow reactors to carry out synthetically useful organic photochemical reactions. J. Photochem. Photobiol. C Photochem. Rev. 29, 107–147. doi:10.1016/j.jphotochemrev.2016.10.002
Movsisyan, M., Delbeke, E. I. P., Berton, J. K. E. T., Battilocchio, C., Ley, S. V., and Stevens, C. V. (2016). Taming hazardous chemistry by continuous flow technology. Chem. Soc. Rev. 45, 4892–4928. doi:10.1039/C5CS00902B
Murray, A. T., Voskian, S., Schreier, M., Hatton, T. A., and Surendranath, Y. (2019). Electrosynthesis of hydrogen peroxide by phase-transfer catalysis. Joule 3, 2942–2954. doi:10.1016/j.joule.2019.09.019
Naito, Y., Nakamura, Y., Shida, N., Senboku, H., Tanaka, K., and Atobe, M. (2021). Integrated flow synthesis of α-amino acids by in situ generation of aldimines and subsequent electrochemical carboxylation. J. Org. Chem. 86 (22), 15953–15960. doi:10.1021/acs.joc.1c00821
Nijland, A., and Harutyunyan, S. R. (2013). Light on the horizon? Catalytic enantioselective photoreactions. Catal. Sci. Technol. 3 (5), 1180–1189. doi:10.1039/C3CY20858C
Nippatlapalli, N., Ramakrishnan, K., and Philip, L. (2022). Enhanced degradation of complex organic compounds in wastewater using different novel continuous flow non – thermal pulsed corona plasma discharge reactors. Environ. Res. 203, 111807. doi:10.1016/j.envres.2021.111807
Nishioka, M., Miyakawa, M., Daino, Y., Kataoka, H., Koda, H., Sato, K., et al. (2013). Single-mode microwave reactor used for continuous flow reactions under elevated pressure. Ind. Eng. Chem. Res. 52, 4683–4687. doi:10.1021/ie400199r
Nishiyama, Y., Mori, R., Nishida, K., Tanimoto, H., Morimoto, T., and Kakiuchi, K. (2014). Diastereodifferentiating [2 + 2] photocycloaddition of a chiral cyclohexenone with cyclopentene in supercritical carbon dioxide using a flow microreactor. J. Flow. Chem. 4 (4), 185–189. doi:10.1556/JFC-D-14-00012
Noël, T., Cao, Y., and Laudadio, G. (2019). The fundamentals behind the use of flow reactors in electrochemistry. Acc. Chem. Res. 52 (10), 2858–2869. doi:10.1021/acs.accounts.9b00412
Noël, T., Naber, J. R., Hartman, R. L., McMullen, J. P., Jensen, K. F., and Buchwald, S. L. (2011). Palladium-catalyzed amination reactions in flow: Overcoming the challenges of clogging via acoustic irradiation. Chem. Sci. 2, 287–290. doi:10.1039/C0SC00524J
Oelgemöller, M., Hoffmann, N., and Shvydkiv, O. (2014). From ‘lab & light on a chip’ to parallel microflow photochemistry. Aust. J. Chem. 67, 337–342. doi:10.1071/CH13591
Ogilby, P. R. (2010). Singlet oxygen: There is indeed something new under the sun. Chem. Soc. Rev. 39 (8), 3181–3209. doi:10.1039/B926014P
Pandit, A. B., and Joshi, J. B. (1993). Hydrolysis of fatty oils: Effect of cavitation. Chem. Eng. Sci. 48, 3440–3442. doi:10.1016/0009-2509(93)80164-L
Peters, B. K., Rodriguez, K. X., Reisberg, S. H., Beil, S. B., Hickey, D. P., Kawamata, Y., et al. (2019). Scalable and safe synthetic organic electroreduction inspired by Li-ion battery chemistry. Science 363, 838–845. doi:10.1126/science.aav5606
Pieber, B., Gilmore, K., and Seeberger, P. H. (2017). Integrated flow processing - challenges in continuous multistep synthesis. J. Flow. Chem. 7, 129–136. doi:10.1556/1846.2017.00016
Piferi, C., and Riccardi, C. (2022). A study on propane depletion by surface dielectric barrier discharges. Clean. Eng. Technol. 8, 100486. doi:10.1016/j.clet.2022.100486
Pinho, V. D., Miranda, L. S. M., and de Souza, R. O. M. A. (2015). Photochemistry under continuous flow conditions. Rev. Virtual Quim 7, 144–164. doi:10.5935/1984-6835.20150009
Pletcher, D., Green, R. A., and Brown, R. C. D. (2018). Flow electrolysis cells for the synthetic organic chemistry laboratory. Chem. Rev. 118, 4573–4591. doi:10.1021/acs.chemrev.7b00360
Porta, R., Benaglia, M., and Puglisi, A. (2016). Flow chemistry: Recent developments in the synthesis of pharmaceutical products. Org. Process Res. Dev. 20, 2–25. doi:10.1021/acs.oprd.5b00325
Purwanto, P., Buchori, L., and Istadi, I. (2020). Reaction rate law model and reaction mechanism covering effect of plasma role on the transesterification of triglyceride and methanol to biodiesel over a continuous flow hybrid catalytic-plasma reactor. Heliyon 6 (10), e05164. doi:10.1016/j.heliyon.2020.e05164
Rinaldi, L., Wu, Z., Giovando, S., Bracco, M., Crudo, D., Bosco, V., et al. (2017). Oxidative polymerization of waste cooking oil with air under hydrodynamic cavitation. Green Process Synth. 6, 425–432. doi:10.1515/gps-2016-0142
Rivas, A., Rodrigo, D., Company, B., Sampedro, F., and Rodrigo, M. (2007). Effects of pulsed electric fields on water-soluble vitamins and ACE inhibitory peptides added to a mixed orange juice and milk beverage. Food Chem. 104 (4), 1550–1559. doi:10.1016/j.foodchem.2007.02.034
Rivas, D. F., Cintas, P., and Gardeniers, H. J. G. E. (2012). Merging microfluidics and sonochemistry: Towards greener and more efficient micro-sono-reactors. Chem. Commun. 48, 10935–10947. doi:10.1039/C2CC33920J
Rosello-Soto, E., Galanakis, C. M., Brncic, M., Orlien, V., Trujillo, F. J., Mawson, R., et al. (2015). Clean recovery of antioxidant compounds from plant foods, by-products and algae assisted by ultrasounds processing. Modeling approaches to optimize processing conditions. Trends Food Sci. Technol. 42 (2), 134–149. doi:10.1016/j.tifs.2015.01.002
Rosso, C., Gisbertz, S., Williams, J. D., Gemoets, H. P. L., Debrouwer, W., Pieber, B., et al. (2020). An oscillatory plug flow photoreactor facilitates semi-heterogeneous dual nickel/carbon nitride photocatalytic C–N couplings. React. Chem. Eng. 5, 597–604. doi:10.1039/D0RE00036A
Sancheti, S. V., and Gogate, P. R. (2017). A review of engineering aspects of intensification of chemical synthesis using ultrasound. Ultrason. Sonochem. 36, 527–543. doi:10.1016/j.ultsonch.2016.08.009
Sánchez-Vega, R., Elez-Martínez, P., and Martín-Belloso, O. (2014). Influence of high intensity pulsed electric field processing parameters on antioxidant compounds of broccoli juice. Innovative Food Sci. Emerg. Technol. 29, 70–77. doi:10.1016/j.ifset.2014.12.002
Sato, E., Fujii, M., Tanaka, H., Mitsudo, K., Kondo, M., Takizawa, S., et al. (2021). Application of an electrochemical microflow reactor for cyanosilylation: Machine learning-assisted exploration of suitable reaction conditions for semi-large-scale synthesis. J. Org. Chem. 86 (22), 16035–16044. doi:10.1021/acs.joc.1c01242
Schotten, C., Nicholls, T. P., Bourne, R. A., Kapur, N., Nguyen, B. N., and Willans, C. E. (2020). Making electrochemistry easily accessible to the synthetic chemist. Green Chem. 22, 3358–3375. doi:10.1039/D0GC01247E
Sedelmeier, J., Ley, S. V., Baxendale, I. R., and Baumann, M. (2010). KMnO4-mediated oxidation as a continuous flow process. Org. Lett. 12, 3618–3621. doi:10.1021/ol101345z
Seemann, A., Panten, J., and Kirschning, A. (2021). Flow chemistry under extreme conditions: Synthesis of macrocycles with musklike olfactoric properties. J. Org. Chem. 86, 13924–13933. doi:10.1021/acs.joc.1c00663
Sequeira, C. A. C., and Santos, D. M. F. (2009). Electrochemical routes for industrial synthesis. J. Braz. Chem. Soc. 20, 387–406. doi:10.1590/S0103-50532009000300002
Shida, N., Nakamura, Y., and Atobe, M. (2021). Electrosynthesis in laminar flow using a flow microreactor. Chem. Rec. 21 (9), 2164–2177. doi:10.1002/tcr.202100016
Shieh, W.-C., Dell, S., and Repiˇc, O. (2001). 1, 8-diazabicyclo[5.4.0]undec-7-ene (DBU) and microwave-accelerated green chemistry in methylation of phenols, indoles, and benzimidazoles with dimethyl carbonate. Org. Lett. 3, 4279–4281. doi:10.1021/ol016949n
Silva, V. L. M., Santos, L. M. N., and Silva, A. M. S. (2017). Ohmic heating: An emerging concept in organic synthesis. Chem. Eur. J. 23, 7853–7865. doi:10.1002/chem.201700307
Silva, V. L. M., Soengas, R. G., and Silva, A. M. S. (2020). Ionic liquids and ohmic heating in combination for Pd-catalyzed cross-coupling reactions: Sustainable synthesis of flavonoids. Molecules 25, 1564. doi:10.3390/molecules25071564
Skillinghaug, B., Rydfjord, J., Sävmarker, J., and Larhed, M. (2016). Microwave heated continuous flow palladium(II)-Catalyzed desulfitative synthesis of aryl ketones. Org. Process Res. Dev. 20 (11), 2005–2011. doi:10.1021/acs.oprd.6b00306
Soengas, R. G., Silva, V. L. M., Pinto, J., Rodríguez-Solla, H., and Silva, A. M. S. (2016). Ohmic heating and ionic liquids in combination for the indium-promoted synthesis of 1-halo alkenyl compounds: Applications to Pd-catalysed cross-coupling reactions. Eur. J. Org. Chem. 99-107, 99–107. doi:10.1002/ejoc.201501162
Strauss, C. R. (1999). Invited review. A combinatorial approach to the development of environmentally benign organic chemical preparations. Aust. J. Chem. 52, 83–96. doi:10.1071/c98156
Szymański, W., Beierle, J. M., Kistemaker, H. A. V., Velema, W. A., and Feringa, B. L. (2013). Reversible photocontrol of biological systems by the incorporation of molecular photoswitches. Chem. Rev. 113 (8), 6114–6178. doi:10.1021/cr300179f
Tabasso, S., Grillo, G., Carnaroglio, D., Calcio Gaudino, E., and Cravotto, G. (2016). Microwave-assisted γ-valerolactone production for biomass lignin extraction: A cascade protocol. Molecules 21 (4), 413. doi:10.3390/molecules21040413
Tagliapietra, S., Binello, A., Bucciol, F., Trukhan, V., Colia, M., and Cravotto, G. (2020). Green enabling technologies for competitive synthesis of pharmaceutical lead compounds. Curr. Pharm. Des. 26, 5700–5712. doi:10.2174/1381612826999201116163951
Tagliapietra, S., Calcio Gaudino, E., Martina, K., Barge, A., and Cravotto, G. (2019). Microwave irradiation in micro- meso-fluidic systems; hybrid technology has issued the challenge. Chem. Rec. 19, 98–117. doi:10.1002/tcr.201800057
Tanaka, K., Yoshizawa, H., and Atobe, M. (2019). A flow microreactor approach to a highly efficient Diels - alder reaction with an electrogenerated o-quinone. Synlett 30, 1194–1198. doi:10.1055/s-0037-1611725
Tanbouza, N., Ollevier, T., and Lam, K. (2020). Bridging lab and industry with flow electrochemistry. iScience 23, 101720. doi:10.1016/j.isci.2020.101720
Tu, N. P., Hochlowski, J. E., and Djuric, S. W. (2012). Ultrasound-assisted click chemistry in continuous flow. Mol. Divers. 16, 53–58. doi:10.1007/s11030-011-9331-4
L. transpose, (Editor) (2017). Sustainable flow chemistry: Methods and applications (Weinheim, Germany: Wiley-VCH Verlag GmbH & Co.).
Wang, L., Liu, M., Jiang, M., Wan, L., Li, W., Cheng, D., et al. (2022). Six-step continuous flow synthesis of diclofenac sodium via cascade etherification/smiles rearrangement strategy: Tackling the issues of batch processing. Chemistry 28, e202201420. in press. doi:10.1002/chem.202201420
Wu, S., Bashir, M. A., and Zhu, J. (2020). Optimization of a liquid-phase plasma discharge process for biodiesel synthesis from pure oleic acid. Fuel Process. Technol. 202, 106368. doi:10.1016/j.fuproc.2020.106368
Wu, Z., Ferreira, D. F., Crudo, D., Bosco, V., Stevanato, L., Costale, A., et al. (2019). Plant and biomass extraction and valorisation under hydrodynamic cavitation. Processes 7 (12), 965. doi:10.3390/pr7120965
Yeboue, Y., Gallard, B., Le Moigne, N., Jean, M., Lamaty, F., Martinez, J., et al. (2018). Peptide couplings by reactive extrusion: Solid-tolerant and free from carcinogenic, mutagenic and reprotoxic chemicals. ACS Sustain. Chem. Eng. 6, 16001–16004. doi:10.1021/acssuschemeng.8b04509
Yokozawa, S., Ohneda, N., Muramatsu, K., Okamoto, T., Odajima, H., Ikawa, T., et al. (2015). Development of a highly efficient single-mode microwave applicator with a resonant cavity and its application to continuous flow syntheses. RSC Adv. 5, 10204–10210. doi:10.1039/c4ra12428f
Yoshida, J., Kataoka, K., Horcajada, R., and Nagaki, A. (2008). Modern strategies in electroorganic synthesis. Chem. Rev. 108, 2265–2299. doi:10.1021/cr0680843
Yueh, H., Voevodin, A., and Beeler, A. B. (2015). Development of a photolabile amine protecting group suitable for multistep flow synthesis. J. Flow. Chem. 5 (3), 155–159. doi:10.1556/JFC-D-14-00016
Zappimbulso, N., Capozzi, M. A., Porcheddu, A., Farinola, G. M., and Punzi, A. (2021). Solvent-free reactions for the synthesis of indolenine-based squaraines and croconaines: Comparison of thermal heating, mechanochemical milling, and IR irradiation. ChemSusChem 14, 1363–1369. doi:10.1002/cssc.202002763
Zhang, J., Wang, K., Teixeira, A. R., Jensen, K. F., and Luo, G. (2017). Design and scaling up of microchemical systems: A review. Annu. Rev. Chem. Biomol. Eng. 8, 285–305. doi:10.1146/annurev-chembioeng-060816-101443
Keywords: continuous-flow reactors, hybrid techniques, ultrasound, microwaves, hydrodynamic cavitation, plasma, photochemistry, ohmic heating
Citation: Grillo G, Cintas P, Colia M, Calcio Gaudino E and Cravotto G (2022) Process intensification in continuous flow organic synthesis with enabling and hybrid technologies. Front. Chem. Eng. 4:966451. doi: 10.3389/fceng.2022.966451
Received: 10 June 2022; Accepted: 17 August 2022;
Published: 07 September 2022.
Edited by:
Tsutomu Ono, Okayama University, JapanReviewed by:
Asami Yoshii, Industry Technology Center of Wakayama Prefecture, JapanCopyright © 2022 Grillo, Cintas, Colia, Calcio Gaudino and Cravotto. This is an open-access article distributed under the terms of the Creative Commons Attribution License (CC BY). The use, distribution or reproduction in other forums is permitted, provided the original author(s) and the copyright owner(s) are credited and that the original publication in this journal is cited, in accordance with accepted academic practice. No use, distribution or reproduction is permitted which does not comply with these terms.
*Correspondence: Pedro Cintas, cGVjaW50YXNAdW5leC5lcw==; Giancarlo Cravotto, Z2lhbmNhcmxvLmNyYXZvdHRvQHVuaXRvLml0
Disclaimer: All claims expressed in this article are solely those of the authors and do not necessarily represent those of their affiliated organizations, or those of the publisher, the editors and the reviewers. Any product that may be evaluated in this article or claim that may be made by its manufacturer is not guaranteed or endorsed by the publisher.
Research integrity at Frontiers
Learn more about the work of our research integrity team to safeguard the quality of each article we publish.