- LRGP-CNRS Université de Lorraine, Nancy, France
Membrane processes are today one of the key technologies for industrial separations and are expected to play an important role in future sustainable production systems. The combination of materials science and process engineering has historically always been an essential condition to the development of new applications for membranes. The recent development of high performance nanostructured materials, together with new production technologies (such as 3D printing) and high performance computing possibilities is expected to open new horizons to membrane processes. The different challenges and prospects to be addressed to achieve this purpose are discussed, with an emphasis on the future of process industries in terms of feedstocks, energy sources, and environmental impact.
1 Introduction: Membrane Separations Today
Membranes are usually considered as the third wave of separation processes, thermal separations (e.g., distillation, evaporation) and auxiliary phase processes (e.g. absorption, liquid extraction, adsorption) being the first and second respectively (King, 1980; Koros, 2001). The industrial development of membrane indeed demanded advanced thin layer materials to be produced at a large scale; early attempts of microporous membranes preparation (with pore sizes below µm range) can be dated back 1920, while thin film dense membranes could not be obtained before 1960 (Hwang and Kammermeyer, 1975).
The key production challenges of membranes, which are still valid today, have been soon identified: first, a highly permeable material simultaneously showing a high enough selectivity is logically absolutely necessary. The antagonism between these two performances generates a so called trade-off curve, an empirical limit based on experimental data, that is obtained for the separation of gas and liquid mixtures (Robeson, 2008). The possibility to overpass the corresponding upper bond between permeance and selectivity is one of the key challenges of membrane science (Park et al., 2017).
In a second step, large scale production processes of membrane and module have to be developed with zero default standards.
Finally, the membrane process has to be implemented at the best place in the industrial process, with efficient pretreatment operations, in order to ensure the longest membrane material lifetime.
The development of membrane processes thus requires a combination of 1) high performance materials (chemistry being the key discipline), 2) robust and liable module production technologies and 3) process engineering and design tools (Prasad et al., 1994; Baker, 2004; Favre et al., 2017).
These three key steps (material, module, system) are sketched in Figure 1 as a science push contribution, while the application framework and constraints correspond to an industry pull action. Taking into account the tremendous developments recently achieved in the different directions shown on Figure 1, it can be expected that the place and role of membrane processes in a large range of industrial applications will significantly expand in the near future. This prospective statement, together with the associated challenges, is detailed hereafter.
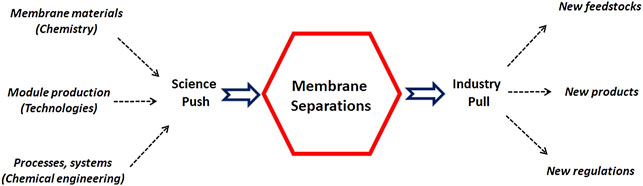
FIGURE 1. Synopsis of the industrial development framework of membrane processes: scientific advances (innovative materials, new production technologies, and process engineering methodologies) can synergistically contribute to current and future industrial needs.
2 The Future of Membrane Processes: Challenges and Prospects
2.1 Membrane Materials
To a large extent, polymers represent today the dominant material family of membrane separation processes (Baker and Low, 2014). This statement applies for porous (microfiltration, ultrafiltration, dialysis) or dense (reverse osmosis, gas separation, and pervaporation) industrial membranes. Polymers effectively offer unique possibilities in terms of thin separation layer production, through cheap, scalable, liable processing technologies (phase inversion, extrusion, hollow fiber spinning, and coating) (Nunes et al., 2020). Globally speaking, the permeability/selectivity trade-off is achieved based on statistical porous structures: pore size distribution in the nm to µm range for porous membranes, statistical free volume distribution in the subnanometer range for dense polymeric membranes (Figure 2). The same statement holds for inorganic membranes (i.e. alumina, carbon, metal oxides, silica…), which are produced by sintering/extrusion and are mostly used for microfiltration and ultrafiltration operations.
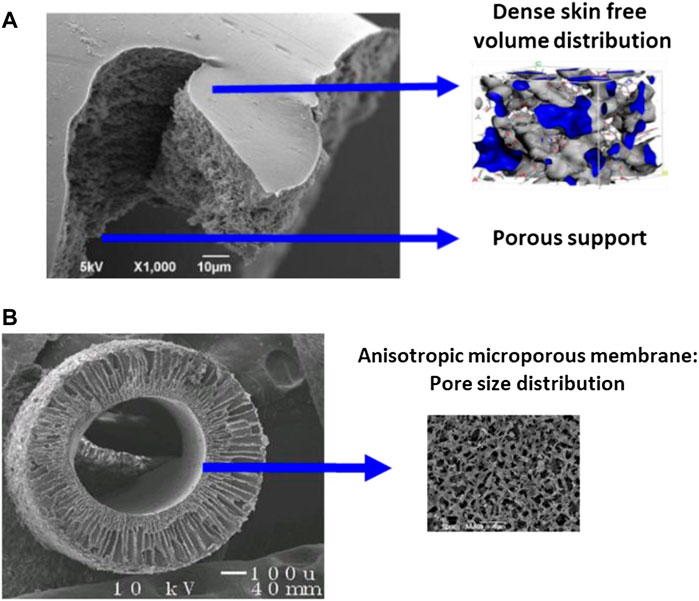
FIGURE 2. Examples of current industrial membrane materials. (A) Dense skin asymmetric polymeric membrane (reverse osmosis, gas separations). Productivity constraints require a very thin dense layer supported on a porous structure. The separation performances result from species solubility and diffusion into a subnanometer free volume distribution matrix. (B) Porous membrane (ultrafiltration, microfiltration, dialysis, membrane contactors, and transmembrane distillation). The porous separating layer, shows a pore size distribution in the nanometer to micrometer range, depending on the liquid mixture to be treated and species to be treated be separated. This type of structure can be based on polymeric or inorganic materials.
With the advent of the nanostructured materials revolution, breakthrough performances are achievable today, mostly at lab scale for membrane materials (Koros and Zhang, 2017). For instance, the classical permeability/selectivity trade-off limit of polymers for gas and, more recently, liquid separations, can be completely overpassed with materials showing a quasi-perfect monodisperse pore size such as zeolites (Young et al., 2017), carbon nanotubes (Skoulidas et al., 2002), Carbon Molecular Sieves (CMS) (Koh et al., 2016), graphenes (Geim, 2009), Metal Oxide Frameworks (MOF) (Gascon and Kapteijn, 2010), among others.
The combination of ultrathin structure (down to the atom level for graphene films), together with perfect lattice structure opens the way to very high separation performances. Moreover, most of the inorganic nanostructured materials mentioned above show high temperature resistance and compatibility with a very broad range of chemicals. The limitations of polymers, with upper operating temperature usually around 100 C and sensitivity to chemicals (e.g., chlorine for ultrafiltration and reverse osmosis in biotechnology and water treatment, heavy hydrocarbons for gas separations, solvents for organic solvent nanofiltration) effectively limit today the selection of membrane processes for industrial use. More specifically, the possibility to operate membrane modules under high temperature conditions could unlock novel hybrid processes such as membrane reactors. The association of catalysis and separation function in a single unit is indeed known to often offer improved performances (Agrawal, 2001; Van Kampen et al., 2021). Numerous studies have addressed this type of process for decades, for instance for hydrogen production with high temperature separation membranes based on palladium or inorganic membranes. The success of membrane bioreactors (Shannon et al., 2008), which has been achievable with polymeric materials given the low temperature operation level (ca 30 C), could then possibly apply to a new set of chemical reactors.
2.2 Production Technologies
Besides new material developments, major changes are also expected to occur for membrane module production. The development of a new tailor made module for a new membrane material is known to be tedious, long and costly. Moreover, module/membrane industrial production most often makes use of organic solvents (i.e., for polymer dissolution) that can lead to environmental concerns. Green solvents (water, supercritical CO2 .) have been proposed in order to limit these problems, but their use is far to be applicable to any type of polymer. Nevertheless, the large efforts and significant progress recently achieved in producing more sustainable membranes, employing green solvents and bio-based materials through the replacement of traditional toxic and harmful compounds should be stressed (Nunes et al., 2020). Simultaneously, solvent resistant membranes, such as fluorinated polymers and thin film polymers showing impressive mechanical resistance have been recently developed, opening new perspectives for polymeric membranes (Karan et al., 2015). Besides solvent use, potting and casing materials can also be an issue, with difficulties in terms of materials compatibility and defect free adhesion operation of resin potting for instance. Module production often relies on secret know-how. The challenges of module production also explain why the number of membrane equipment suppliers remains limited.
With the advent of 3D printing techniques, it might be that a completely new field of development emerges. The direct production of a membrane module through 3D printing in place of classical production techniques (e.g., hollow fiber spinning + resin potting) is not achievable yet, but it could become a reality in a near future. For instance, the production of ultrathin composite membrane samples, with dense skin layers down to 20 nm, has been recently reported, offering tremendous perspectives for development (Chowdhury et al., 2018). Several studies recently reported 3D possibilities for different types of membrane materials and processes (Bara et al., 2013; Bram et al., 2015; Nguyen et al., 2019). It has to be stressed that major limitations for large scale modules remain. Nevertheless, the direct 3D printing production of a membrane module based on either polymeric or inorganic materials could be a complete game changer. A rapid efficient module production could be achieved, with completely new possibilities offered in terms of structure.
The production constraints of a membrane, be it flat or a hollow fiber, necessarily translates into 1D type module structures. With 3D printing, complex geometries (such as fractal or constructal), possibly including in situ turbulence promoters (in place of spacers), anisotropic membrane or module structures could be possible. It is important to stress that living systems make use of membranes for numerous applications (e.g., lung, kidney…) based on complex structures, far away from the constant cross Section 1D fluid flow. This is certainly not fortuitous, but it may reflect improved performances (energy efficiency, intensification) that are largely unexplored today in membrane science with synthetic polymers.
2.3 Process Design Methods
The synergy between materials and process studies has always been a key requirement of membrane applications. Similarly to any chemical engineering target, Process Systems Engineering (PSE) tools are very efficient for membrane process design purposes today, with different software environments (Biegler et al., 1997). The selection of the most efficient membrane material, together with the best place, best design and optimal operating conditions has been achieved for a great number of industrial applications (Bozorg et al., 2019). Nevertheless, complex processes such as multistage or hybrid systems still address some important and partly unsolved optimization issues. Significant progress has been recently achieved in this direction, but an important paradigm shift is currently under progress.
2.4 Membrane Processes in a New Industrial Environment
With the forecasted decrease of fossil fuel use, a completely new industrial landscape is on the way to become reality in a near future. In terms of feedstocks, renewables are expected to replace fossil hydrocarbons (Agrawal and Mallapragada, 2010; Favre, 2020). This will strongly impact the type of separation processes which are classically used in petrorefineries, with the predominant role of distillation. High performance membrane materials can drastically improve the energy efficiency of separation processes (Sholl and Lively, 2016; Castel and Favre, 2018).
Biorefineries will require efficient separation processes, adequate to achieve operation on aqueous, diluted mixtures containing heat sensitive biomolecules. Membrane processes which offer the possibility to separate complex mixtures without heat supply and require electricity in place of thermal driving force are considered as a key technology for biorefineries.
Moreover, the use of alternative driving forces could be of interest, besides the classical pressure, power based solution. Temperature difference (such as in transmembrane distillation or thermopervaporation), sweep operation (which can replace vacuum pumping is some cases) or more exotic driving forces such as light (Gérardin et al., 2021) or electrical fields (Wilcox, 2020) have been mostly discarded up to now. It might be that these novel approaches are in some cases reconsidered in a sustainable industrial framework, especially in an integrated, energy efficient network.
3 Discussion
The joined rapid evolution of advanced nanostructured materials, module production technologies and process engineering tools discussed in the previous sections is expected to generate significant changes in the production, place and role of membrane processes in industry.
- The new generation of membrane materials, to a large extent based on inorganic monodisperse structures, is likely to push membrane applications, through improved separation performances, and/or new applications under high temperature or aggressive environments. A sound collaboration between materials scientists and process engineers is however absolutely necessary in order to rigorously evaluate these new perspectives.
- The possibilities offered by new materials production technologies, especially 3D printing, is likely to generate a breakthrough in membrane module production. This field of research is very large and numerous development stoppers have to be solved, but the production tool is there, with spectacular developments in material science, and technological devices.
- Besides the traditional separation function, operated by membranes for decades, new possibilities are expected to emerge, where membranes fulfill at the same time multiple tasks (filtration, catalysis, support, and heat exchange.) (Liu et al., 2016). The development of biomimetic and stimuli responsive membrane materials (such as self repairing structures for instance) is also expected to lead to new applications (di Vincenzo et al., 2021).
- The development of modern, artificial intelligence type tools (neural networks, surrogate models, superstructure approaches, and genetic algorithms…) in Process Systems Engineering enables today the very fast identification of the optimal membrane, process design and operating conditions (Castel et al., 2020). The joined improvements of optimization algorithms and computing capacity opens the way for innovative processes, where the design of mutlimembrane, multistaged processes can be rigorously achieved.
Additionally, the shift of numerous industrial sectors from fossil to renewables feedstocks and energy offers promising perspectives for membrane applications. The rational design of downstream processes for biorefineries, which are expected to gradually replace fossil fuel based refineries, will require a smart combination of technological bricks, where membranes will for sure play a key role (Huang et al., 2008; Favre and Brunetti, 2022).
The different aspects listed throughout this prospective analysis are tentatively summarized in a general table (Supplementary Material).
Data Availability Statement
The original contributions presented in the study are included in the article/Supplementary Material, further inquiries can be directed to the corresponding author.
Author Contributions
EF: Concept and writing.
Conflict of Interest
The author declares that the research was conducted in the absence of any commercial or financial relationships that could be construed as a potential conflict of interest.
Publisher’s Note
All claims expressed in this article are solely those of the authors and do not necessarily represent those of their affiliated organizations, or those of the publisher, the editors and the reviewers. Any product that may be evaluated in this article, or claim that may be made by its manufacturer, is not guaranteed or endorsed by the publisher.
Supplementary Material
The Supplementary Material for this article can be found online at: https://www.frontiersin.org/articles/10.3389/fceng.2022.916054/full#supplementary-material
References
Agrawal, R., and Mallapragada, D. (2010). Chemical Engineering in a Solar Energy-Driven Sustainable Future. AIChE J. 56 (11), 2762–2768. doi:10.1002/aic.12435
Agrawal, R. (2001). Separations: Perspective of a Process Developer/designer. AIChE J. 47 (5), 967–971. doi:10.1002/aic.690470503
Baker, R. W., and Low, B. T. (2014). Gas Separation Membrane Materials: A Perspective. Macromolecules 47, 6999–7013. doi:10.1021/ma501488s
Bara, J. E., Hawkins, C. I., Neuberger, D. T., and Poppell, S. W. (2013). 3D Printing for CO2 Capture and Chemical Engineering Design. Nanomater. Energy 2 (5), 235–243. doi:10.1680/nme/13.00021
Biegler, L., Grossmann, I., and Westerberg, A. (1997). Systematic Methods for Chemical Process Design. Englewood Cliffs, NJ: Prentice-Hall.
Bozorg, M., Addis, V., Piccialli, A., Ramírez-Santos, C., Castel, I., et al. (2019). Polymeric Membrane Materials for Nitrogen Production from Air: A Process Synthesis Study. Chem. Eng. Sci. 207, 1196–1213. doi:10.1016/j.ces.2019.07.029
Bram, M., Dornseiffer, J., Hoffmann, J., Gestel, T., Meulenberg, W. A., and Stöver, D. (2015). Inkjet Printing of Microporous Silica Gas Separation Membranes. J. Am. Ceram. Soc. 98 (8), 2388–2394. doi:10.1111/jace.13657
Castel, C., Bounaceur, R., and Favre, E. (2020). Engineering of Membrane Gas Separation Processes: State of the Art and Prospects. J. Membr. Sci. Res. 6 (3), 295–303.
Castel, C., and Favre, E. (2018). Membrane Separations and Energy Efficiency. J. Membr. Sci. 548, 345–357. doi:10.1016/j.memsci.2017.11.035
Chowdhury, M. R., Steffes, J., Huey, B. D., and McCutcheon, J. R. (2018). 3D Printed Polyamide Membranes for Desalination. Science 361, 682–686. doi:10.1126/science.aar2122
di Vincenzo, M., Tiraferri, A., Musteata, V.-E., Chisca, S., Sougrat, R., Huang, L.-B., et al. (2021). Biomimetic Artificial Water Channel Membranes for Enhanced Desalination. Nat. Nanotechnol. 16, 190. doi:10.1038/s41565-020-00796-x
Favre, E. (2017). Polymeric Membranes for Gas Separation. Comprehensive Membrane Science and Technology. Editors E. Drioli, and L. Giorno (New York: Elsevier), Vol. II, pp155–212.
Favre, E., and Brunetti, A. (2022). “The Impact of Membrane Engineering in the Circular Economy,” in Membrane Engineering in the Circular Economy : Renewable Sources Valorization in Energy and Downstream Processing in Agro-Food Industry. 1st edition (Elsevier), Vol. 1. chap 2. doi:10.1016/b978-0-323-85253-1.00013-7
Favre, E. (2020). Specialty Grand Challenges in Separation Processes. Front. Chem. Eng. 2, 1. doi:10.3389/fceng.2020.00001
Gascon, J., and Kapteijn, F. (2010). Metal-Organic Framework Membranes-High Potential, Bright Future? Angew. Chem. Int. Ed. 49, 1530–1532. doi:10.1002/anie.200906491
Geim, A. K. (2009). Graphene: Status and Prospects. Science 324, 1530–1534. doi:10.1126/science.1158877
Gérardin, F., Cloteaux, A., Simard, J., and Favre, É. (2021). A Photodriven Energy Efficient Membrane Process for Trace VOC Removal from Air: First Step to a Smart Approach. Chem. Eng. J. 419. doi:10.1016/j.cej.2021.129566
Huang, H. J., Ramaswamy, S., Tschirner, U. W., and Ramarao, B. V. (2008). A Review of Separation Technologies in Current and Future Biorefineries. Sep. Purif. Technol. 62, 1–21. doi:10.1016/j.seppur.2007.12.011
Karan, S., Jiang, Z., and Livingston, A. W. (2015). Sub–10 Nm Polyamide Nanofilms with Ultrafast Solvent Transport for Molecular Separation. Science 348, 6241–1347. doi:10.1126/science.aaa5058
Koh, D.-Y., McCool, B. A., Deckman, H. W., and Lively, R. P. (2016). Reverse Osmosis Molecular Differentiation of Organic Liquids Using Carbon Molecular Sieve Membranes. Science 353, 804–807. doi:10.1126/science.aaf1343
Koros, W. J. (2001). The 'Third Wave. J. Membr. Sci. 187 (1–2), 1. doi:10.1016/s0376-7388(01)00425-2
Koros, W. J., and Zhang, C. (2017). Materials for Next-Generation Molecularly Selective Synthetic Membranes. Nat. Mater 16, 289–297. doi:10.1038/nmat4805
Liu, Z., Wang, W., Xie, R., Ju, X. J., and Chu, L. Y. (2016). Stimuli-responsive Smart Gating Membranes. Chem. Soc. Rev. 45, 460. doi:10.1039/c5cs00692a
Nguyen, D. T., Hornbostel, K., Murialdo, M. R., Ye, C., Smith, W., Baker, S., et al. (2019). 3D Printed Polymer Composites for CO2 Capture. Industrial Eng. Chem. Res. 58 (48), 22015–22020. doi:10.1021/acs.iecr.9b04375
Nunes, S. P., Culfaz-Emecen, P. Z., Ramon, G. Z., Visser, T., Koops, G. H., Jin, W., et al. (2020). Thinking the Future of Membranes: Perspectives for Advanced and New Membrane Materials and Manufacturing Processes. J. Membr. Sci. 598, 117761. doi:10.1016/j.memsci.2019.117761
Park, H. B., Kamcev, J., Robeson, L. M., Elimelech, M., and Freeman, B. D. (2017). Maximizing the Right Stuff: The Trade-Off between Membrane Permeability and Selectivity. Science 356, 1137. doi:10.1126/science.aab0530
Prasad, R., Shaner, R. L., and Doshi, K. J. (1994). “Comparison of Membranes with Other Gas Separation Technologies,” in Polymeric Gas Separation Membranes. Editors D.R. Paul, and Y.P. Yampol׳skii (Boca Raton, FL: CRC Press), 531–614.
Shannon, M. A., Bohn, P. W., Elimelech, M., Georgiadis, J. G., Mariñas, B. J., and Mayes, A. M. (2008). Science and Technology for Water Purification in the Coming Decades. Nature 452, 301–310. doi:10.1038/nature06599
Sholl, D. S., and Lively, R. P. (2016). Seven Chemical Separations to Change the World. Nature 532, 435–437. doi:10.1038/532435a
Skoulidas, A. I., Ackerman, D. M., Johnson, J. K., and Sholl, D. S. (2002). Rapid Transport of Gases in Carbon Nanotubes. Phys. Rev. Lett. 89, 185901. doi:10.1103/physrevlett.89.185901
Van Kampen, J., Boon, J., and van Sint Annaland, M. (2021). Separation Enhanced Methanol and Dimethyl Ether Synthesis. J. Mater. Chem. A 9, 14627–14629. doi:10.1039/D1TA03405G
Keywords: membrane, separations, materials, engineering, sustainable, industry
Citation: Favre E (2022) The Future of Membrane Separation Processes: A Prospective Analysis. Front. Chem. Eng. 4:916054. doi: 10.3389/fceng.2022.916054
Received: 08 April 2022; Accepted: 28 April 2022;
Published: 17 May 2022.
Edited by:
Adele Brunetti, National Research Council (CNR), ItalyReviewed by:
Francesco Galiano, Italian National Research Council, ItalyCopyright © 2022 Favre. This is an open-access article distributed under the terms of the Creative Commons Attribution License (CC BY). The use, distribution or reproduction in other forums is permitted, provided the original author(s) and the copyright owner(s) are credited and that the original publication in this journal is cited, in accordance with accepted academic practice. No use, distribution or reproduction is permitted which does not comply with these terms.
*Correspondence: Eric Favre, RXJpYy5GYXZyZUB1bml2LWxvcnJhaW5lLmZy