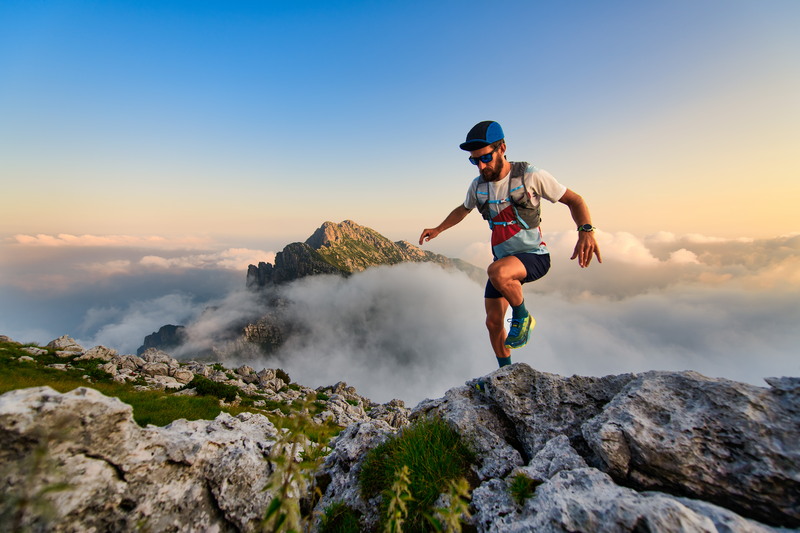
95% of researchers rate our articles as excellent or good
Learn more about the work of our research integrity team to safeguard the quality of each article we publish.
Find out more
EDITORIAL article
Front. Chem. Eng. , 04 May 2022
Sec. Chemical Reaction Engineering
Volume 4 - 2022 | https://doi.org/10.3389/fceng.2022.902127
This article is part of the Research Topic Hierarchical and Multifunctional Materials in Chemical Engineering: Synthesis Strategies and Processing Challenges View all 7 articles
Editorial on the Research Topic
Hierarchical and Multifunctional Materials in Chemical Engineering: Synthesis Strategies and Processing Challenges
The efficiency of catalysts, adsorbents, and molecular sieves are not only linked to the nature of the active phase but also to numerous features such as porosity (size, homogeneity, interconnectivity) and morphology (particles, extrudates, monoliths), which are strongly dependent on the synthesis strategies, the coating methods, and on the design of the envisaged reactors and technology. The creation of hierarchical porous materials allows the improvement of heat and mass transfer, as well as a better control of the contact time, an important parameter for increasing selectivity and limiting secondary reactions.
Hierarchical micro-/mesoporous materials based on MFI zeolite nanoslabs dipcoated on membranes or hexagonally shaped around micellar templates structured into spherical particles gave unique molecular separation behavior as for CO2 capture, oligopeptides separation, and high yield in isomerization reactions Sree et al. The micellar templating combining to Keggin (HPW) ions was successfully applied to synthesize a hierarchical reinforced metal organic framework (MOF) as Cu3(BTC)2 with 5 nm diameter mesopores. Another dual template approach allowed to synthesize nanotubes of LDH (Zn, Al, Eu).
Hierarchical meso-/macroporous monoliths were developed as a solution for in-flow applications avoiding fine particles to be handled or particles to be packed. In the early nineties, it was observed that chemical reactions are better controlled and run much faster in a continuous flow, especially in channels with submillimeter diameters. The improvement in the surface-to-volume ratio to over 100 m2/m3 in microchannel reactors increases the space-time yield Szymańska et al. It improves productivity, selectivity, economy, and process safety. A family of hierarchical silica monoliths, discovered by Nakanishi’s group in 1991 (Nakanishi and Soga, 1991), prepared by a combination of phase separation (spinodal decomposition) and sol-gel process, features a unique network of interconnected and uniform macropores adjustable in the range 1–50 μm. A monolith (cylinder: 10 cm length, 1.2 cm diameter) with macropores diameters (20–50 μm) shows a water permeability of 20 μm2 enables flow rates of 700 ml/min with low overpressure (600 kPa) Szymańska et al. The mesopores in the struts are adjustable (4–30 nm). These monoliths were first successfully used as chromatographic columns for high-speed analysis (Nakanishi, 1997) and commercialized by Merck in 2001 by developing PEEK cladding. Indeed, the insertion of the monoliths in housing/cladding to obtain a ready-for-run reactor is of prime importance. In 2009, the application of these monoliths (inserted in heat shrinkable Teflon gains) with unique transport properties was extended to catalytic applications by Galarneau’s group (El Kadib et al., 2009) revealing higher productivity (3–10 times) in comparison to packed-bed reactors for a large variety of fine chemicals and active pharmaceutical ingredients due to precise control of contact times (Galarneau et al., 2016). The group of Jatoi et al. showed the absence of external mass-transfer limitations or stagnant layer formation with these monoliths (inserted in borosilicate tubes) by running the catalytic test reaction of liquid-phase hydrogenation of p-nitrophenol. However, owing to the much larger linear velocity of monoliths featuring the largest macropores (20–50 μm), external mass transfer and lateral homogenization (micromixing) can greatly improve overall reaction kinetics in the case of catalysts as enzymes that feature characteristic turnover frequencies on the microsecond scale. In the latter case, the external mass transfer hinders and so determines the apparent kinetics of the reaction Szymańska et al. For instance, the grafting of enzymes (laccases) in the mesopores (20 nm diameter) of the monoliths (macropores of 20 μm diameter) allowed to efficiently treat wastewater containing various pharmaceutical molecule pollutants, but only in a recycling configuration; a single-pass flow was not enough efficient for this commercial enzyme Sebai et al. Monoliths functionalized with recombinantly expressed and purified hydroxynitrile lyases enabled the continuous-flow enantioselective [ee = 99% (S)] synthesis of industrially important chiral cyanohydrins of in a short space of time Szymańska et al. The reaction was faster when operating at higher flow rates, due to greatly enhanced mixing of liquid reagents and boosted mass transport to the liquid-catalysts/enzyme interface. Another strategy to use the monoliths with internal recycle is to develop rotating bed reactors (500 rpm, centrifugal acceleration 11.5 g) with baskets filled with monolithic beads Szymańska et al. Lu and Nakanishi has extended the synthesis of such monoliths to a great variety of oxides such as Ti, Al, Zr, Mg, Mn, Fe, Co, Ni, Cu, and Zn (and also binary system as Mn-Co, Mn-Zn) and to various metal compositions such as metal phosphates, organic-polymers/carbons, and MOF.
To produce large-scale monoliths and to operate processes at elevated temperatures, a new strategy appears as the monoliths-in monolith synthesis by synthesizing the monolith into the millimetric channels of a monolith, as a cordierite honeycomb monolith, after its activation by alkaline treatment to generate surface reacting OH groups and favoring the anchorage of the inner monolith Szymańska et al. This strategy is in line with the development of catalyst particles closely packed in monoliths, and most significantly in thermally conductive metallic cellular monoliths to combine high mass transfer with heat-transfer for limited exo- and endo-thermic reactions Balzarotti et al. Different monoliths have been proposed, including honeycomb, open-cell foams (as copper or aluminum foams), and new periodic open cellular structures with tune cell shape produced by additive manufacturing methods. Selective laser melting technique is demonstrated to be industrially ready for many materials such as aluminum and stainless steel. Foams exhibit effective thermal conductivities up to 10 and 20 W/m/K if aluminum and copper are employed, respectively. Struts with diameters ranging from 0.4 to 1 mm were effectively produced with porosity up to 93%. Copper monoliths with struts of 0.5 mm diameter were also obtained by replicas of polymeric monoliths obtained by stereolithography. The efficiency of such high mass and heat transfer reactors was demonstrated for the process intensification of Fischer-Tropsch synthesis and of methane steam reforming (strongly endothermic) to produce hydrogen Balzarotti et al. All of these monoliths could be used in series for cascade reactions.
AG, ST, CC, and SE were all guest associate editors of this editorial. AG drafted this editorial, which was further edited by ST, CC, and SE. All the authors agreed to publication.
The authors declare that the research was conducted in the absence of any commercial or financial relationships that could be construed as a potential conflict of interest.
All claims expressed in this article are solely those of the authors and do not necessarily represent those of their affiliated organizations, or those of the publisher, the editors and the reviewers. Any product that may be evaluated in this article, or claim that may be made by its manufacturer, is not guaranteed or endorsed by the publisher.
We thank all authors and all reviewers for their valuable contributions.
El Kadib, A., Chimenton, R., Sachse, A., Fajula, F., Galarneau, A., and Coq, B. (2009). Functionalized Inorganic Monolithic Microreactors for High Productivity in Fine Chemicals Catalytic Synthesis. Angew. Chem. Int. Ed. Engl. 48, 4969–4972. doi:10.1002/anie.200805580
Galarneau, A., Sachse, A., Said, B., Pelisson, C.-H., Boscaro, P., Brun, N., et al. (2016). Hierarchical Porous Silica Monoliths: a Novel Class of Microreactors for Process Intensification in Catalysis and Adsorption. Comptes Rendus Chim. 19, 231–247. doi:10.1016/j.crci.2015.05.017
Nakanishi, K. (1997). Pore Structure Control of Silica Gels Based on Phase Separation. J. Porous Mater. 4, 67–112. doi:10.1023/a:1009627216939
Keywords: monolith, hierarchical porosity, mass transfer, heat transfer, catalysis
Citation: Galarneau A, Thomas S, Cammarano C and Esposito S (2022) Editorial: Hierarchical and Multifunctional Materials in Chemical Engineering: Synthesis Strategies and Processing Challenges. Front. Chem. Eng. 4:902127. doi: 10.3389/fceng.2022.902127
Received: 22 March 2022; Accepted: 04 April 2022;
Published: 04 May 2022.
Edited and reviewed by:
Senentxu Lanceros-Mendez, Basque Center for Materials, SpainCopyright © 2022 Galarneau, Thomas, Cammarano and Esposito. This is an open-access article distributed under the terms of the Creative Commons Attribution License (CC BY). The use, distribution or reproduction in other forums is permitted, provided the original author(s) and the copyright owner(s) are credited and that the original publication in this journal is cited, in accordance with accepted academic practice. No use, distribution or reproduction is permitted which does not comply with these terms.
*Correspondence: Anne Galarneau, YW5uZS5nYWxhcm5lYXVAZW5zY20uZnI=; Sebastien Thomas, c2ViYXN0aWVuLnRob21hc0B1bmlzdHJhLmZy; Claudia Cammarano, Y2xhdWRpYS5jYW1tYXJhbm9AZW5zY20uZnI=; Serena Esposito, c2VyZW5hX2VzcG9zaXRvQHBvbGl0by5pdA==
Disclaimer: All claims expressed in this article are solely those of the authors and do not necessarily represent those of their affiliated organizations, or those of the publisher, the editors and the reviewers. Any product that may be evaluated in this article or claim that may be made by its manufacturer is not guaranteed or endorsed by the publisher.
Research integrity at Frontiers
Learn more about the work of our research integrity team to safeguard the quality of each article we publish.