- 1School of Chemical Engineering, College of Engineering, Universiti Teknologi MARA, Shah Alam Selangor, Malaysia
- 2Faculty of Applied Sciences, Universiti Teknologi MARA, Kampus Perlis, Arau, Malaysia
- 3Sime Darby Plantation Research Sdn Bhd, Carey Island, Pulau Carey, Malaysia
Recovery of oil palm resources is essential towards conserving environment. This study investigated the behaviour of oil palm kernel shells (PKS), palm mesocarp fibre (PMF) and empty fruit bunch (EFB) through microwave assisted pyrolysis. Power level (300–1,000 W), exposure time (10–30 min) and mass loading (20–50 g) were varied to determine its influence on char yield and calorific value at one-factor-at-a-time (OFAT) analysis. Model equations obtained from Box-Behnken design was used for Response Surface Methodology (RSM) in determining the optimum operating condition. It was found that the power level has least important influence on the solid char yield of EFB and PMF. No significant impact on the solid char yield of PMF beyond 10 min of exposure. Maximum mass inside the pyrolyser for EFB, PMF, and PKS are 40, 50, and 25 g, respectively. Calorific values of solid char produced were comparable to a low rank coal (>22 MJ/kg). From the RSM analysis, the optimum conditions for obtaining high char yield and calorific values have been determined with power level of 300 W, exposure time in the range of 16.7–32 min, and biomass mass in the range of 20–40.4 g. The outcome from this analysis is vital as it provides an alternative solution to utilise oil palm industrial wastes to be converted to solid fuel as source of renewable fuel and reduce its pollution to the environment.
1 Introduction
Current energy crisis and increase demand on energy utilisation due to industrialisation have called for seeking alternatives to fossil fuel. In Malaysia, oil palm as major agricultural industry has contributed significantly to the Malaysia economics and also its environment. Palm oil industry is the biggest contribution to biomass residues which can be used as renewable sources in this country (Norhidayu et al., 2017). To date, there are more than 450 palm oil mills operated in Malaysia, resulted in abundance of biomass wastes such as empty fruit bunches (EFB), palm mesocarp fibre (PMF), palm kernel shell (PKS) (Hirschmann, 2020). The biomass wastes have caused problems especially in the waste management and environmental impact where sustainability is the focus in an overall operation of the industry. Thus, many research works emerged in order to ensure the wastes are managed sustainably. One of the alternative solutions is by converting the biomass wastes from the oil palm mill to fuels and speciality chemicals via pyrolysis. The biomass wastes can be converted to solid fuel such as charcoal but the only problem in the production of charcoal is its slow process which takes hours or even days (Demirbaş, 2001; Panwar et al., 2012).
Manipulating heating source such as microwave energy is one of the alternatives of producing charcoal at a fast rate. Currently, microwave assisted pyrolysis technique has gained attention due to its advantage of volumetric heating. This unique phenomenon allows no direct contact between heating source and the biomass waste hence it will improve heating efficiency as compared to a conventional heating technique. Moreover, high heating rates may be achieved with microwave due to rapid interaction between electromagnetic wave and the waste. Consequently, utilization of microwave as heating source will reduce processing cost, produce better product quality, reduce hazards to humans and environment; and hence enhance quality of life (Jones et al., 2002; Appleton et al., 2005).
Several research had emerged on pyrolysis of biomass using microwave radiation such as pyrolysis of wood blocks (Miura et al., 2004), oil shale (El Harfi et al., 2000), plastic wastes (Ludlow-Palafox and Chase, 2001), pine saw dust (Chen et al., 2008), coffee hulls (Domínguez et al., 2007), palm trunk (Amouzgar et al., 2010), EFB (Mohd, 2017), palm fibre (Salema and Ani, 2012a), and PKS (Jamaluddin et al., 2013; Tripathi et al., 2020). Domínguez et al. (2007) had compared the pyrolysis of coffee hulls using microwave as energy source in comparison to conventional heating pyrolysis. It appeared that time taken to pyrolyse the materials is less than that in conventional pyrolysis. They found that the gas fraction produced from this process is increased accompanied by a decreased in solid fraction. Nonetheless, heating value of the solid fraction is similar to that of lignite. Salema and Ani (2012a) investigated on the microwave assisted pyrolysis of palm fibre and PKS using fluidised bed reactor. Their work particularly focused on upgrading liquid fuel. Solid char analysis was limited to an investigation of its surface image. Huang et al. (2008) had analysed total recovery of resources and energy from rice straw using this technique. The pyrolysis reaction was successfully carried out in an absence of absorber. Investigation focused on understanding the effect of microwave power (50–500 W) and particle size (20/40–<40 mesh) of feedstock on product yield. They found that particle size and microwave power level were the key parameters that affect performance of the microwave system.
Almost all microwave-assisted pyrolysis investigations were carried out by investigating the parameters based on one-factor-at-a-time (OFAT) method, where one parameter was varied while other parameters were fixed. Interactions between one parameter to another cannot be identified using OFAT technique, thus a statistical approach using response surface methodology (RSM) is a suitable technique in optimising a response (i.e., output variable) which is influenced by several factors (independent variables or input variables). The technique can be achieved by a careful design of experiments (DoE). The advantage of RSM is it requires less tests/runs and less time consuming by full-factorial design experiment. Moreover, this method allows the optimisation process by considering the variation of all the factors. The optimal design conditions can be done by using central composite design (CCD), Box Behnken design, D-optimal design and few other techniques. Application of RSM in search for optimum operating conditions have been explored by few researchers in this area. Jamaluddin et al. (2013) had carried out optimisation on microwave pyrolysis of PKS investigating the influence of nitrogen flowrate, exposure time and mass of samples on the elemental analysis and char yield. In their work, the power level was set constant at 300 W. They found out that the nitrogen flowrate has no influence on the respective response. Abas et al. (2018) had performed optimisation using RSM based on central composite design (CCD) on microwave pyrolysis of PMF; focusing on optimising the process conditions namely, temperature, activated carbon loading, and holding time towards liquid yield and total phenolic content (TPC). It was reported that the liquid oil yield increases with temperature from 350°C to 500°C, while further increase to 650°C reduces the yield. The combine effect of the temperature, time, and activated carbon (AC) loading for maximum yield and TPC content was operated at temperature of 536°C, 23.88 min, and 82.1 g of AC loading. Both Tripathi et al. (2020), Arafat Hossain et al. (2017) had employed CCD for optimisation of PMF and PKS, respectively; to identify the optimum conditions of radiation time, power and nitrogen flowrate towards optimum hydrogen and biochar yield; and biochar yield and Brunauer-Emmett-Teller (BET) surface area, respectively. Tripathi et al. (2020) highlighted that nitrogen flow has no effect on the yield and BET surface area.
Thus far, previous researchers have investigated on optimisation of microwave pyrolysis using RSM, however most of them are using the CCD technique. On top of that, the work has focused on different combination of process conditions that affect the response such as biochar yield, BET response, hydrogen yield, etc. Nevertheless, limited study has included the combined effect of sample mass loading during the microwave pyrolysis process of oil palm wastes. According to Antunes et al. (2018), sample mass loading affects the absorption of microwave energy which influence electromagnetic field intensity.
Hence, the aim of this work is to investigate thermochemical conversion using microwave pyrolysis technique of oil palm wastes such as EFB, PMF, and PKS into solid char. DoE has been used to identify the model equation statistically. RSM using Box-Behnken design method adds to the existing knowledge and aid to search for optimum operating conditions namely microwave power, radiation time and sample mass loading for microwave-assisted pyrolysis process. The influence of these factors on biochar yield and its calorific value were investigated based on OFAT and RSM analyses. The outcomes from this research indeed will contribute to the development of alternative technique in biomass processing and dependency on fossil fuel for energy source will be reduced. Pollution contributed by palm oil waste will also be reduced.
2 Materials and Methods
2.1 Raw Materials and Characterisations
Oil palm biomass namely EFB, PMF, and PKS were collected from an oil palm mill located in Nilai, Negeri Sembilan, Malaysia. These biomass materials were by-products from various processes in the mills during production of crude palm oil. Low rank coal, i.e., Mukah Balingian coal used in this study was originated from Mukah, Sarawak, Malaysia. It was used for comparison purpose during combustion analysis using thermogravimetric analyser (TGA). For characterisation of biomass and coal samples, they were air dried for 2–3 days for removal of surface moisture. The samples were pulverised to <212 μm and subjected to chemical analyses as accordance to ASTM Standard Method and Testing. Proximate analysis (ASTM D 5142–02a) was performed using a thermo balance (TGA/SDRA51e) manufactured by Mettler Toledo. As for ultimate analysis, it was performed in accordance with ASTM D 5373–02 using Thermo Finnigan Flashed 1,112 analyser in order to identify elements present in the samples. Calorific values (HHV) of the samples were determined by using ASTM D 2015–96, using Ika-works C5000 calorimeter. Table 1 shows the characterisation of the samples used in this experiment.
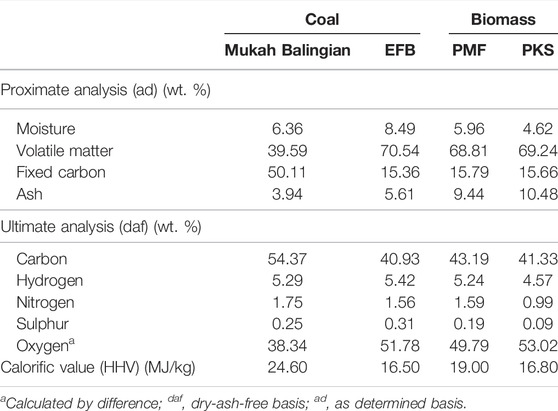
TABLE 1. Characterisation of Coal Mukah Balingian, empty fruit bunch (EFB), palm mesocarp fibre (PMF), and palm kernel shell (PKS).
2.2 Experimental Set-Up and Procedures
2.2.1 Microwave-Assisted Pyrolysis
Experimental set-up for microwave assisted pyrolysis of oil palm biomass is as shown in Figure 1. It consists of a microwave cavity, a reactor, and a condensing system. The system was set-up using a domestic microwave oven model Panasonic of 1 kW, 2.45 GHz, to which it is modified to place the quartz reactor. The reactor consists of 1 L quartz vessel having an ID 13 cm and height of 15 cm, and a lid to which three openings were made to allow the inlet-outlet flow of nitrogen gas and insertion of thermocouple. Two thermocouples of type K were place in the quartz reactor and microwave cavity to measure the bulk sample and the cavity temperatures, respectively. The thermocouples were insulated in a Teflon sheath and grounded, with its rounded edge (tip) having 3 mm diameter to prevent electric arching during course of the pyrolysis in microwave. Both thermocouples were connected via a data acquisition system known as LabView®. Calibration of the thermocouples has been carried out by calibrating it to a known temperature of materials. Outlet gas connection from the reactor was directed to the condensing system comprising of a liquid trap and a series of condenser. The gas outlet is bubble through a beaker of water before release to atmosphere. A measured biomass sample was placed in the quartz reactor along with approximately 5 g of charcoal (char obtained from tube furnace pyrolysis of PKS at 800°C and heating rate of 10°C/min), which has approximately <200 μm particle size, was placed in a crucible of ID of 2.7 and 4 cm height. The crucible was placed in the centre of the biomass sample. The reactor was purged using nitrogen gas, flowing at a rate of 5 L/min for 30 min, to ensure all oxygen was expelled from the system. Prior to starting the experiment, the nitrogen gas was fixed to 1 L/min, then exposure time and power level were set at a desired level. Pump was switched on to allow cold water to flow in the waterside of a Liebig condenser for condensing the volatile produced from the process. Upon completion, the reactor was set to cool down to room temperature.
The pump for the condensing system was switched off after the vapour is invisible. The collected solid and liquid products were then weighted and kept in a screw tight bottle. Respective yield for solid char (CYMW), liquid (LYMW), and gas (GYMW) for microwave irradiation pyrolysis experiment was calculated based on Eqs 1–3:
where wf is weight of solid char, wl, is weight of liquid product, and wi is weight of biomass feedstock. As for gas product, its yield was obtained by difference. Experiment was carried out at power level of 300, 600, and 1,000 W and at various exposure times of 10, 20, and 30 min. Each experimental run was repeated three times and average values were reported.
2.2.2 Design of Experiment
The optimum operating conditions for microwave irradiation pyrolysis of palm biomass materials was identified from optimisation technique using RSM. Model equation for the optimisation analysis were obtained from a series of experiment performed based on Box-Behnken design with each numerical factor was varied over three levels that is; +1, −1, and 0. In this study, a total of 17 experiments with five centre points have been carried out, and experimental run was randomised to minimise effects of uncontrolled factors. Operating parameters including power level, exposure time, and mass of samples that affect selected responses namely solid char yield and calorific value was investigated. Factors’ level and response for the microwave irradiation pyrolysis experiment used are as shown in Table 2.
Table 3 shows experimental runs designed for microwave irradiation pyrolysis experiment. Quadratic equation model for predicting the optimal point is expressed by Eq. 4.
where Y is response (dependent variable),
Design Expert ver.6.1.0 was used to design the experiment (DoE), which was used to develop the model equation and performing statistical evaluation from the designed data. Variability in independent variables was explained by multiple coefficients of determination, R2, while the model equation was used to predict optimum values (Montgomery, 2001).
3 Result and Discussion
3.1 Behavior of Microwave-Assisted Pyrolysis of Empty Fruit Bunch, Palm Mesocarp Fibre, and Palm Kernel Shells
Figures 2A–C shows temperature profile of EFB, PMF, and PKS during microwave irradiation pyrolysis process. The process was performed for a duration of 30 min and at power level of 300, 600, and 1,000 W, in a presence of microwave absorber. For a comparison purpose, a similar process without an addition of absorber at maximum power (1,000 W) was also obtained. In the absence of absorber, the temperature of the samples reached up to 80 to 111 ± 20°C even though it was operated at the highest power level. With the presence of the absorber, operating at the lowest power level, has induced pyrolysis reaction having temperature profile as shown in Figure 2. At a power level of 1,000 W, it took less than 2 min to raise the temperature up to 900°C for EFB, after which the temperature was slowly decreased to approximately 700°C and was maintained at this temperature until the end of the pyrolysis process. These temperature variations were observed at about 10 min of operation. After this duration, not much heating activity was observed and at the same time no vapour evolution was visible. Constant temperature recorded could be due to the system has attained equilibrium. Similar behaviour was observed for PMF and PKS. These observations were also reported by other researcher on similar work by Domínguez et al. (2006) on microwave pyrolysis of sewage sludge, Qing et al. (2010) on pyrolysis of oil shale, Huang et al. (2010)on rice husk and Salema and Ani (2011). Changes in power level resulted in unique temperature profiles for all the materials during microwave pyrolysis in the presence of absorber. Considering at 1,000 W, PMF reached its highest temperature almost instantly, while it took about 2 min for EFB heating to reach its highest temperature. On the other hand, PKS require long time to reach its highest temperature. Among the three-oil palm waste, PMF had reached the highest temperature during the pyrolysis process in comparison to EFB and PKS. It was observed that, when the temperature started to stabilise, the samples in the reactor showed a sign of incandescent (exhibit bright red colour) and remained incandescent throughout the processes. It is believed that during this period, charring of the solid samples took place. Menéndez et al. (1999) had reported similar observation during pyrolysis of active carbons derived from steam activation of bituminous coal during microwave treatment. The difference in the temperature profile and time may be due to the characteristics of the sample.
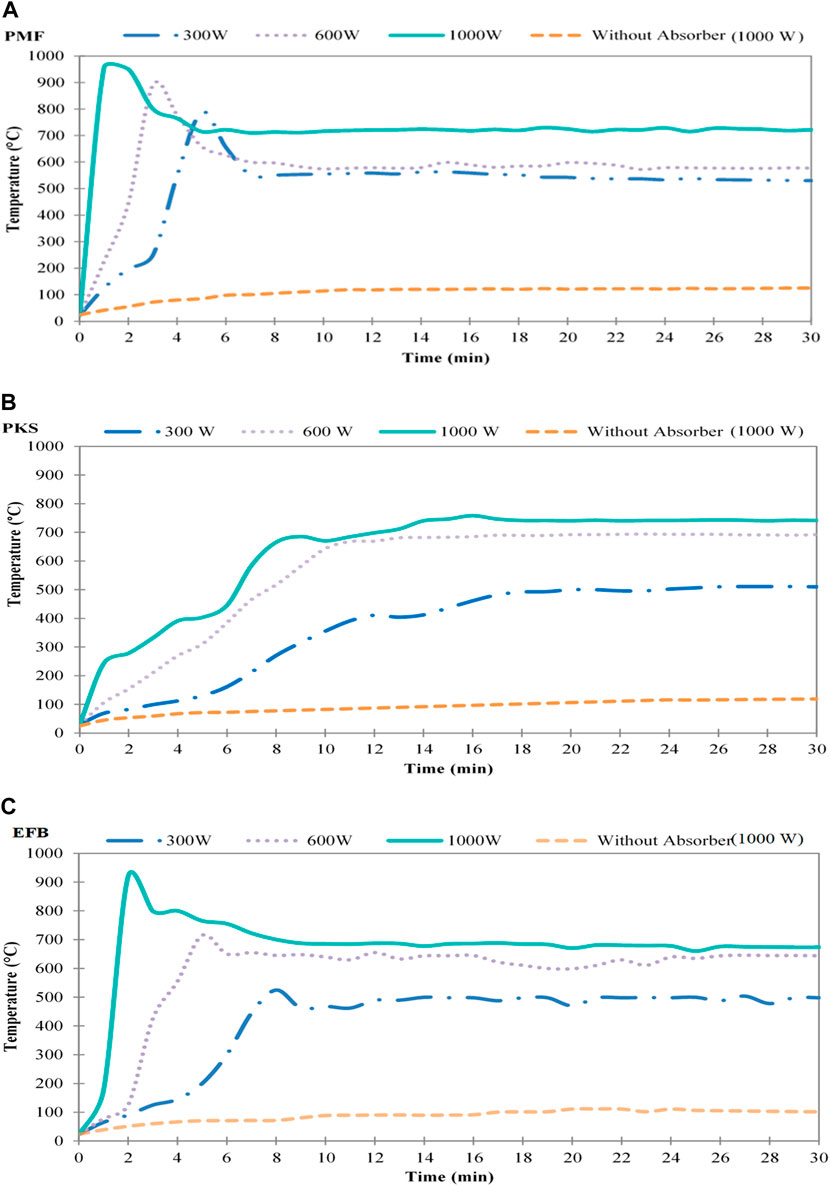
FIGURE 2. Temperature profile for microwave irradiation pyrolysis of (A) PMF, (B) PKS, and (C) EFB at different power level and at exposure time of 30 min.
The presence of absorber is essential as it absorbed the microwave energy. During pyrolysis, the absorber absorbed the energy radiated, which was converted into heat. The heat dissipated from the interaction between the absorber and the radiation energy, increased the biomass sample temperature, thus enable it to be pyrolysed hence forming solid char. This newly formed solid char will interact with the irradiated energy and converted it into heat and transfer the heat to the neighbouring biomass. In other word, the absorber act as a seeding to induce the heating so that the pyrolysis could take place. From the figures shown, constant temperature region indicates that complete pyrolysis process and the biomass has been converted to solid char. This was evident from the released of vapour at this period. Similar observation was reported by Salema and Ani (2012b), Zhao et al. (2012) where they carried out microwave pyrolysis of palm shell using an overhead stirrer and wheat straw, respectively.
3.2 Effect of Power Level on Fractional Yield
Figure 3 shows effect of power level on fractional yield during microwave irradiation pyrolysis of EFB, PMF, and PKS at exposure time of 30 min. It is important to note that, a complete decomposition of palm biomass materials was observed at the lowest power of 300 W, with operating temperature of 30 min. In general, solid fraction produced from this process decreases with power level. The highest solid yield was at low power level (300 W), with the highest value reported for PKS (∼ca. 34.75 wt. %), followed by PMF (∼ca. 32.25 wt. %) and EFB (∼ca. 25.8 wt. %). Low microwave power is translated into low temperature for pyrolysis reaction, hence, high production of solid (char). This is evident from temperature profile of the materials during microwave pyrolysis as depicted in Figure 2. According to Domínguez et al. (2006), increasing pyrolysis temperature, generally reduces solid yield and increases gas yield. Tripathi et al. (2020) reported that temperature increment leads to the start of secondary reactions and increases the interaction between the microwave radiation with water vapours released. The increased interaction leads to biomass dehydration and char formation. Hence further increase in temperature eventually reduced the char yield. Moreover, at high microwave power (>1,000 W), produced char were further decomposed into vapor. Thus, secondary pyrolysis reactions at high power level eventually reduced the char yield.
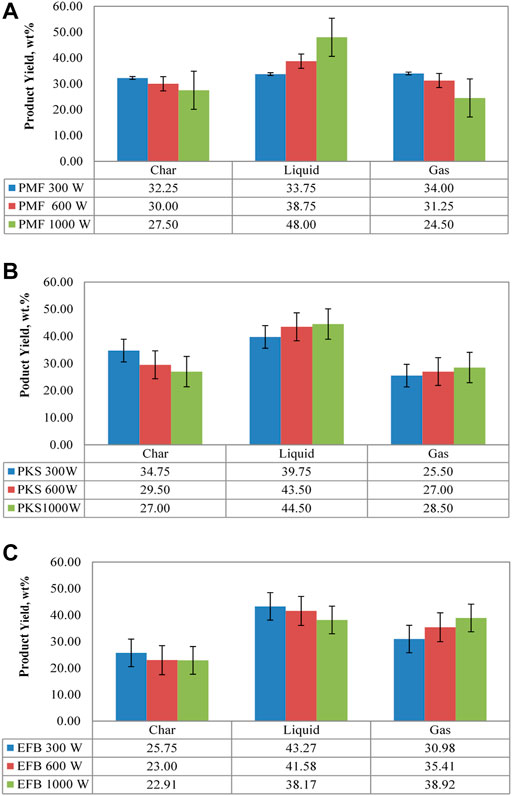
FIGURE 3. Product distribution of (A) PMF, (B) PKS, and (C) EFB during microwave assisted pyrolysis at power level of 300, 600, and 1000 W.
Comparatively, at any power level, the solid yield of PKS was the highest, followed by PMF and EFB. The high solid yield was attributed to high lignin (and carbon) content and also due to the large amount of inorganic materials which favour charring reactions (Di Blasi, 2009). This is consistent with the results obtained where PKS contained high lignin content (∼ca. 20–50.7 wt. %) as compared to EFB (∼14.5–30.5 wt. %) and PMF (∼16.1–27.7 wt. %) (Kim et al., 2013; Kong et al., 2014). The solid yields of EFB at 600 and 1,000 W are generally unchanged. Such a behaviour can be explained by variation in actual degradation temperature of the solid (in relation to the external heating temperature) becomes small, due to narrow range of temperatures characteristic of biomass pyrolysis and heat transfer resistance through the fixed bed (Di Blasi, 2009).
The solid yield from this research was consistent with that reported by Abdullah et al. (2010) on fast pyrolysis of EFB (ca. 23.9–27.6 wt. %), Mohd (2017) on microwave pyrolysis of EFB (ca. 22 wt. %); and Kim et al. (2010), Jamaluddin et al. (2013) on fast pyrolysis, and microwave pyrolysis of PKS (ca. 25–35 wt. %), respectively. However, the solid yield of PMF obtained from this analysis was lower than that reported by Salema and Ani (2011) (ca. 60 wt. %). They reported that the high solid yield reported in their work was due to incomplete pyrolysis reaction using microwave irradiation technique at power of 450 W and 25 min of exposure time.
Liquid yield for EFB pyrolysis recorded a decreasing trend with increasing power level in comparison to PMF and PKS, with the highest value achieved at 300 W. This is because of the higher moisture content of EFB in comparison to PMF and PKS. Fernandez et al. (2011) explained that microwave vaporise the inherent moisture of the materials prior to volatilising organic content releasing the moisture (in a form of steam) rapidly into the surrounding area, created preferential channels in the carbonaceous solid, which in turns favour the release of volatiles at low temperature (i.e., low power level).
3.3 Effect of Exposure Time on Fractional Yield
Figure 4 depicts the effect of exposure time on fractional yield at a power level of 300 W during microwave irradiation pyrolysis of oil palm biomass materials. Microwave irradiation pyrolysis of the oil palm biomass for 10 min resulted in highest solid yield of PKS followed by EFB and PMF. Through visual observation on the resulting solid fraction, PKS and EFB were not fully pyrolysed, where brownish sample instead of blackish char, formed at this condition. PKS and EFB were fully pyrolysed when the process was run for 15 min. Similar observation was reported by Domínguez et al. (2007), Huang et al. (2008), Salema and Ani (2011), Zhao et al. (2012), and Jamaluddin et al. (2013) on microwave irradiation of coffee hulls, rice straw, palm biomass (i.e., EFB and PMF), wheat straw, and PKS, respectively.
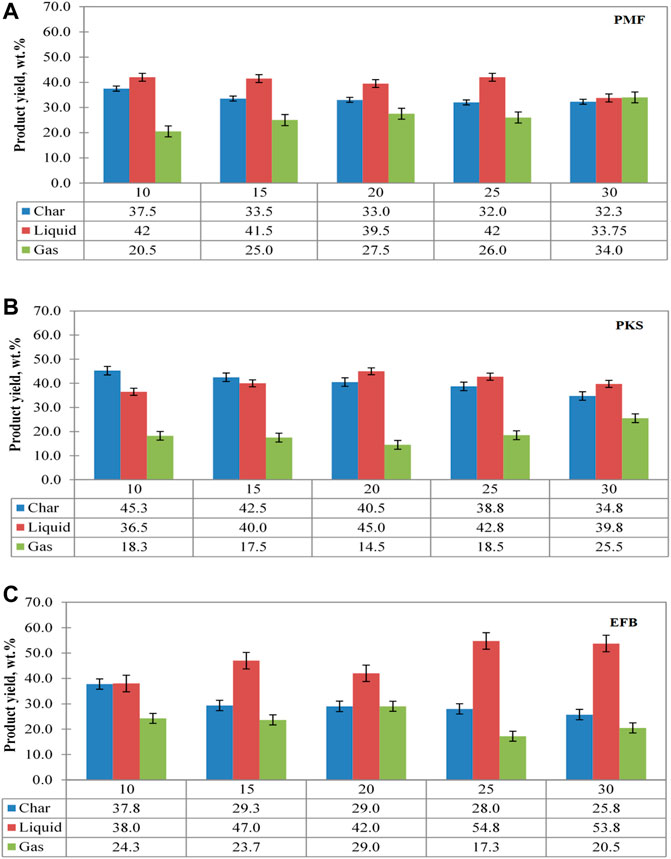
FIGURE 4. Effect of exposure time on product distribution for (A) PMF, (B) PKS, and (C) EFB at 300 W.
For pyrolysis of PMF, the char yield remains unchanged as the duration is increased, but the liquid yield showed a decreasing trend with an exception at 25 min exposure time. At low exposure time and power level, the volatile matter is difficult to escape from the main lignocellulosic skeleton. This is because at low heating rate, rate of dehydration to form stable anhydrocellulose is known to be limited and very slow. Thus, depolymerisation of the solid materials to primary volatiles was quite slow (Chen et al., 1997). Therefore, as time increases, there is adequate time for secondary decomposition of some heavy components into light gases (Chen et al., 2008). It appeared that the exposure time has less influence on the solid yield of PMF after 10 min of pyrolysis reaction. As the exposure time increased, further decomposition allows more volatile matter released. However, product yield for PMF seems well distributed as it is further exposed in microwave irradiation for 30 min.
As for EFB, solid and gas yield seemed to decrease with exposure time, but not as significant as an increased in liquid yield. Further reduction on solid yield was achieved after 25 min of microwave irradiation exposure, with the lowest yield of 25.8 wt. % achieved at 30 min of pyrolysis operation. As a result, volatile released in a form of liquid decreases hence increases the production of gas, though not so significant. With regards to PKS, the solid yield decreased significantly (18%) with exposure time as compared to that in PMF (13%) and EFB (11%). On a contrary, gas yield showed an increasing trend due to sufficient exposure time of microwave irradiation allows further cracking for production of liquid and gas (Di Blasi, 2009).
As the main focus of the present study concerns on the solid fraction of microwave irradiation pyrolysis of oil palm waste, thus, further evaluation on effect of exposure time on the produced solid char with respect to different power level. Figure 5 shows the effect of exposure time on the produced solid char at power level of 300, 600, and 1,000 W. It was observed that at any time, the lower the power level, the higher the solid char yield. Thus, in this regard, for higher yield of PMF char, the process has to be operated at low power level, i.e., 300 W. In a similar manner, EFB pyrolysis also yielded highest char when operating at this power level and exposure time. However, operating the pyrolysis at 10 min for low power level was unable to pyrolyse EFB fully. Taking this into account, EFB shall achieve highest char yield at low power level (i.e., 300 W) by operating for 15 min. When operating the process for 10 min using 600 and 1,000 W, the produced solid is in a fully pyrolysed form (char). This result suggests that the microwave assisted pyrolysis process of EFB would be operated at low power and at least at 15 min of exposure time. PKS char yield production with respect to exposure time was different than the other materials. Operating the pyrolysis process of PKS at 300 W for 10 min of exposure in the microwave energy, was unable to pyrolyse the PKS fully. Thus, for obtaining solid char of PKS at a low power level, the process requires longer exposure time for at least 15 min. The production of solid char from PKS has shown decreasing trend with respect to time. Operating the pyrolysis at 600 W or 1,000 W showed insignificant difference in the char yield when exposed to the microwave energy for about 20 min. Previously, Jamaluddin et al. (2013) had also performed similar work on PKS, however, in their work, the investigation was only carried out at 300 W. To date, limited literatures have reported on the effect of exposure time during microwave-irradiation pyrolysis process.
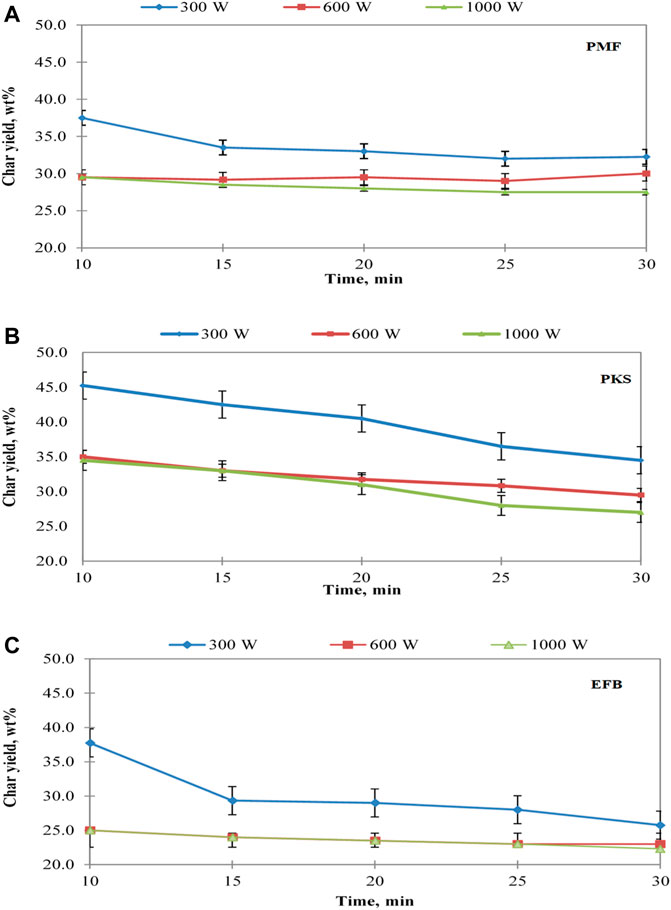
FIGURE 5. Effect of exposure time on char yield for (A) PMF (B) PKS, and (C) EFB at different power level.
3.4 Effect of Sample Mass on Solid Char Yield
Table 4 shows the trend of char yield at different initial mass for EFB, PMF, and PKS during pyrolysis at 300 W for 15 min of exposure time. It appears that, the initial mass of the biomass materials has an impact on the char yield. The char yield for PMF at initial mass of 60 g was the highest. Nevertheless, through physical observation, part of the sample (i.e., sample away from the absorber) was not fully pyrolysed (i.e., browning). At initial mass of 50 g, it was observed that the sample was fully pyrolysed with a char yield of 38.6 wt. %. As for EFB, the material could achieve fully pyrolysed condition up to 40 g as the initial mass. Unlike PKS, it only able to achieve fully pyrolysed condition up to 25 g. The reason for this behaviour could be mainly due to the nature of the materials. The PKS used for the current study was as received basis which is in the form of hard kernel shell whereas EFB and PMF are fibrous in nature. Nevertheless, PMF could be pyrolysed at much higher mass because it consists of short-lose-fibre as compared to EFB, which is long strain fibrous material. This analysis suggests on the importance of maximum limit of mass of samples to be used for microwave pyrolysis operation especially if the scale up of the operation is required. In this experiment, the amount of absorber used is maintained at 5 g.
3.5 Analysis of Produced Solid Char
Table 5 shows chemical analysis of raw oil palm biomass materials, and its produced char from microwave irradiation pyrolysis process at different power level for 30 min of exposure. It was observed that characteristics of the produced char were improved as compared to its parent material. Fixed carbon content of PKS char decreases with increasing power level. Similarly, calorific value of the char was also improved with respect to its raw counterpart indicating improvement of fuel heating value on pyrolysis. The calorific value (CV) of biomass char produced at 1,000 W is almost similar to the low rank coal (Mukah Balingian) (ca. 24 MJ/kg) (Qing et al., 2010). According to Biagini et al. (2002), in ensuring an auto combustion of a fuel for a particular combustion process, the calorific value should be at least a value of 20 MJ/kg. In this case it is proven that the solid product (i.e., biomass char) is a potential source as solid fuel in a combustion system as the calorific values are above 20 MJ/kg.
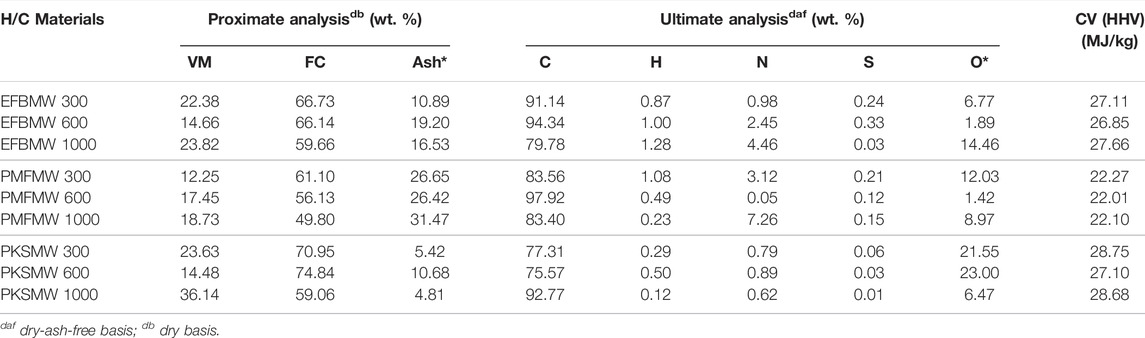
TABLE 5. Chemical properties of biomass and its produced chars at different power level operating at 30 min.
Values of H/C and O/C ratio for the biomass chars were found to be lower than Mukah Balingian (MB) coal and its raw form. It is clearly observed that lower proportion of oxygen and hydrogen, in comparison to carbon in the biomass char, has high energy value of fuel due to lower energy contained in carbon-oxygen and carbon-hydrogen bonds, than in carbon-carbon bonds (McKendry, 2002). This can be observed from Figure 6 where both the elemental loss was similar under both conditions. The plot also showed that the raw biomass transformed from aromatic nucleus with aliphatic side chain structure (H/C 0.0–0.15) to non-condensed aromatic structure (0.04–0.07) (Lanigan, 2010). Good raw biomass characteristic transformation was achieved using microwave assisted pyrolysis technique. The H/C and O/C of the produced char were lower than the parent raw materials and also Mukah Balingian coal (Idris et al., 2010). Energy content between a biomass and fossil fuels can also be compared by using H/C and O/C contents where low ratios of H/C and O/C accounts for high energy content of the materials. In a similar manner, it can be seen that the microwave irradiation pyrolysis technique could transform the materials into solid fuel that has good calorific value.
It has been demonstrated that, although materials (i.e., EFB, PMF, and PKS) derived from parent tree (oil palm tree), its behaviour during microwave irradiation pyrolysis is distinctive with respect to different operating parameters (i.e., power level, exposure time, and mass of sample), using one-factor-at-a-time analysis (OFAT). Hence, it is important to perform an optimisation with an objective of determining operating parameters that maximises char yield having high calorific value. Such optimisation cannot be achieved by OFAT analysis, hence require optimisation technique using RSM.
3.6 Statistical Analysis
Model equations were obtained from a set of experimental design as shown in Table 3. Relationship between factors [i.e., power level (P), exposure time (T), and mass (M)] and responses (char yield and calorific value) were investigated in this study. Experimental results were obtained from randomised experimental run as shown in Table 3.
Fitness of each model equation generated by the software, were tested statistically using analysis of variance (ANOVA) in order to evaluate significance of factors (i.e., power level, exposure time, and mass) that influence the response (i.e., char yield and calorific value) of the MW pyrolysis of EFB, PMF, and PKS. Results are summarised in Table 5. Amount of variation explained by the model after adjusting from numbers of parameter is measured by a term adjusted R2. High value of adjusted R2 indicates high fitness of the model. The model F-value for all biomass materials implies that the model is significant, and that the regression model provides a better fit to the data. p-value (prob > F value) less than 0.05 indicate model terms are significant, meaning that these are the factors that strongly influence the responses (i.e., char yield and calorific value). An insignificant lack-of-fit F-value is another predictor that verified fitness of data against the model.
From Table 6, it shows that power level is the significant model term for char yield production of the microwave irradiation pyrolysis of PMF, while power level and mass are significant for the calorific value response. Values of 1.62 and 2.84 for lack-of-fit of char yield (CY) and calorific value (CV), respectively, implies that lack-of-fit is not significant relative to pure error. The non-significant lack of fit is good as one requires the model to fit the data.
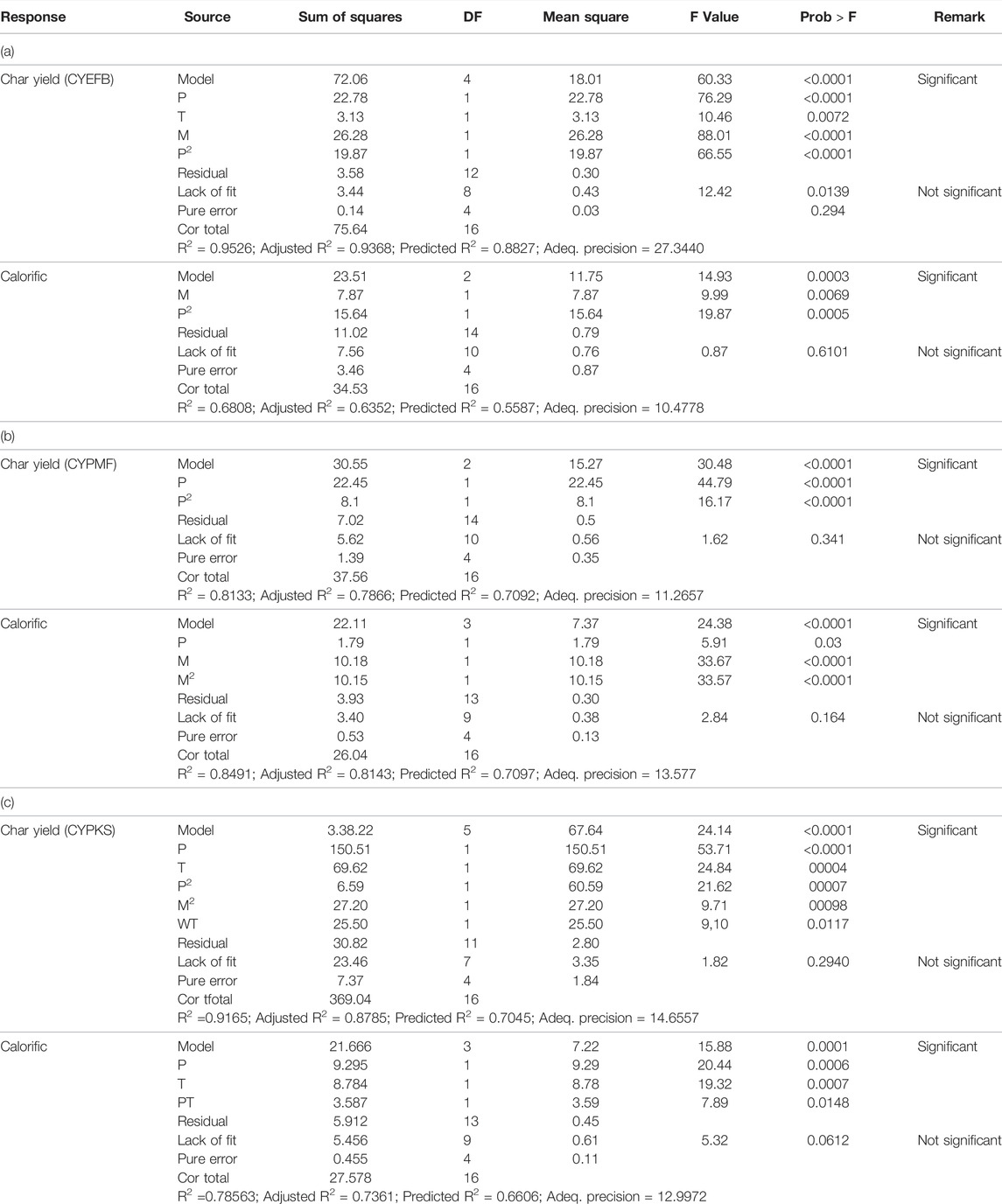
TABLE 6. ANOVA analysis for DOE of MW pyrolysis of (a) EFB, (b) PMF, and (c) PKS, for response of char yield and calorific value.
For PKS, all three factors (power level, time, and mass) are the significant terms in predicting the char yield (CY) from the quadratic model. While only power level and time are the significant terms for predicting the calorific value (CV). As for EFB, all the factors are significant terms for predicting char yield (CY), while only mass and power level are the significant terms for prediction of calorific value (CV).
Results showed that the experimental data are best fitted in a quadratic model with only power level and its interaction affects the char yield of MW pyrolysis of EFB, PMF, and PKS, respectively, as shown in Eqs 5–7. The model equation for calorific value (CV) is shown in Eqs 8–10 for PMF, PKS, and EFB, respectively. The results show that, the calorific value of char yield was only significantly affected by the mass of sample and the power level.
where CY is char yield (wt. %) and P is power level (W), and M is mass of samples (g). The determination of the coefficients involved in the model prediction, gained at 95% confidence interval was summarised in Table 6. As for EFB, adjusted R2 for Eqs 5, 8 are 93.7% and 63.5%, respectively. The response surface model of PMF as represented by Eqs 6, 9 fitted the data at adjusted R2 value of 78.7% and 81.4%, respectively. Adjusted R2 value of 87.8% and 73.6%, are reported for PKS as represented by the model equation of Eqs 7, 10. Predicted and actual value of CV and CY are as shown in Figure 7. From the analysis, the response surface models (Eqs 5–10) were used further for optimisation (maximisation).
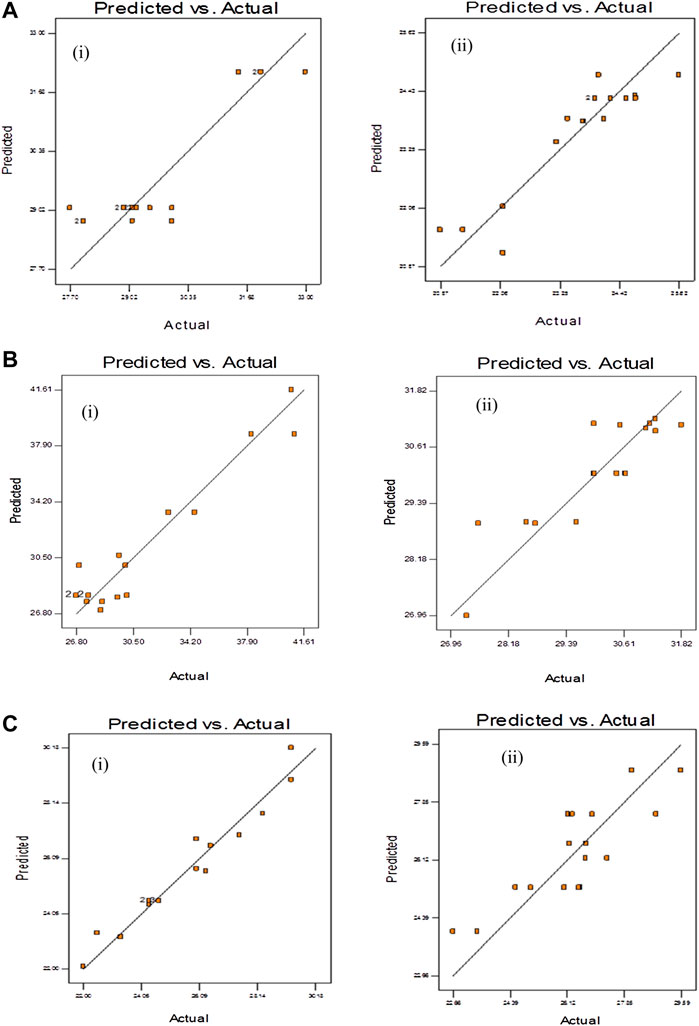
FIGURE 7. Predicted vs. actual value of (i) char yield and (ii) calorific value from the response surface model of microwave irradiation pyrolysis of (A) PMF, (B) PKS, and (C) EFB.
3.7 Optimisation Analysis
The search for optimum conditions that maximizes the char yield and calorific value during the microwave irradiation pyrolysis process was performed using Design Expert (6.0) for RSM. Figure 8 shows the response surface contour plot for the optimum responses (i.e., char yield and calorific value) obtained for EFB, PMF, and PKS. The optimum conditions for maximum char yield and calorific value were obtained when the microwave irradiation pyrolysis of PMF was carried out at power level of 300 W, 17 min of exposure time in the microwave and a mass of 40.4 g of PMF samples. For PKS, the optimum conditions were at 300 W, 32 min, and 20 g. As for EFB, the optimum conditions were 300 W, 31 min and 40 g. Table 7 summaries the conditions in actual and coded values.
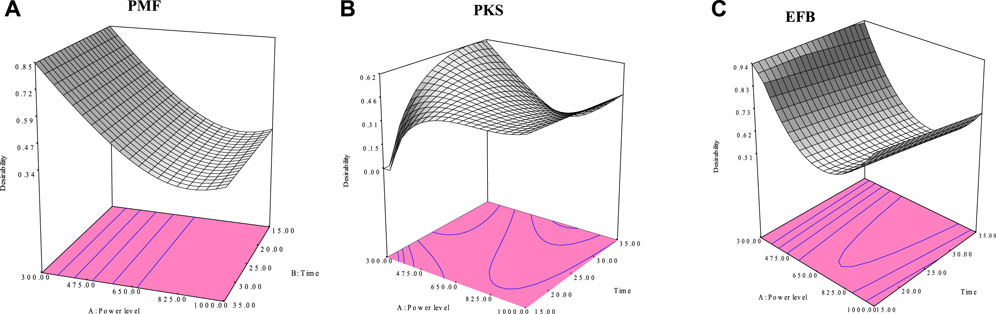
FIGURE 8. Response surface methodology for maximisation condition for optimum yield and CV of (A) PMF, (B) PKS, and (C) EFB microwave irradiation pyrolysis.
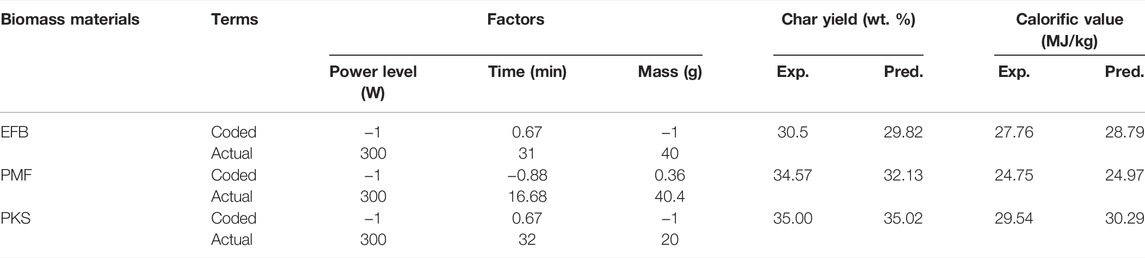
TABLE 7. Optimum conditions for maximum char yield and calorific value of microwave irradiation pyrolysis of EFB, PMF, and PKS.
Predicted values do not deviate much from the experimental data (±5%). It is evident that high quality of biomass char for three biomass materials in terms of energy content, and highest yield were obtained at power level of 300 W. Although the three biomass materials are derived from oil palm three, each of them, behaves differently during the microwave pyrolysis. It is proved that combination of the three parameters had resulted different quality of solid charcoal. Characteristic parameter interaction is shown on a contour plot in Figure 8. In a nutshell, RSM has been successfully used to determine the optimum conditions for producing high char yield and calorific value.
4 Conclusion
Investigation on oil palm biomass from a milling process had revealed different characteristics when exposed to microwave irradiation pyrolysis technique. Microwave pyrolysis is an alternative method of converting oil palm biomass and the process depend on power level, radiation time and mass loading. Fibrous materials such as palm mesocarp fibre can be pyrolyzed at 10 min, whereas both EFB and PKS require longer radiation time. Mass loading of the sample in the reactor play an important role in producing product as it relates to microwave penetration depth. It has been proven that one-factor-of-a-time analysis is not sufficient to identify the optimum operating parameter in converting the materials, hence it requires a statistical analysis technique such as RSM. The outcome from the analysis found that optimisation of microwave irradiation pyrolysis technique of oil palm biomass has provided different optimum operating condition for each palm biomass materials (i.e., EFB, PMF, and PKS). Optimum yield with the optimum calorific value for all the three materials can be done at low power (300 W), with different time and mass loading. Conversion technology by using microwave assisted pyrolysis able to improve the characteristic of oil palm biomass materials. Solid product from this system has potential to be used as solid fuel for combustion purpose. The outcome from this analysis is vital as it provides an alternative solution to utilise oil palm wastes to be converted to bio-coal as source of renewable fuel and to reduce pollution from oil palm industry.
Data Availability Statement
The original contributions presented in the study are included in the article/supplementary material, further inquiries can be directed to the corresponding author.
Author Contributions
SI: Conceptualisation, methodology, data curation, preparation of data and writing- original draft; NR: Conceptualisation, supervision, writing- review and editing; KI: Conceptualisation, supervision, grant acquisition, project administration, writing-review and editing; MM and NM: Grant Lead and member @ Industry, sample provision, writing- review and editing.
Funding
The project was funded by the Sime Darby Research Sdn. Bhd [100-RMI/Sime Darby 16/6/2 (23/2009)], Research Management Centre (RMC), Funding of the project already completed on 2015.
Conflict of Interest
The authors declare that the research was conducted in the absence of any commercial or financial relationships that could be construed as a potential conflict of interest.
Publisher’s Note
All claims expressed in this article are solely those of the authors and do not necessarily represent those of their affiliated organizations, or those of the publisher, the editors and the reviewers. Any product that may be evaluated in this article, or claim that may be made by its manufacturer, is not guaranteed or endorsed by the publisher.
Acknowledgments
The authors would like to thank the Sime Darby Research Sdn. Bhd. for funding the project [100-RMI/Sime Darby 16/6/2 (23/2009)], Research Management Centre (RMC), University Technology MARA and Faculty of Chemical Engineering for providing continuous support to undertake this project.
References
Abas, F. Z., Ani, F. N., and Zakaria, Z. A. (2018). Microwave-assisted Production of Optimized Pyrolysis Liquid Oil from Oil Palm Fiber. J. Clean. Prod. 182, 404–413. doi:10.1016/j.jclepro.2018.02.052
Abdullah, N., Gerhauser, H., and Sulaiman, F. (2010). Fast Pyrolysis of Empty Fruit Bunches. Fuel 89, 2166–2169.
Amouzgar, P., Abdul Khalil, H. P. S., Salamatinia, B., Zuhairi Abdullah, A., and Issam, A. M. (2010). Optimization of Bioresource Material from Oil Palm Trunk Core Drying Using Microwave Radiation; A Response Surface Methodology Application. Bioresour. Technol. 101, 8396–8401. doi:10.1016/j.biortech.2010.05.061
Antunes, E., Jacob, M. V., Brodie, G., and Schneider, P. A. (2018). Microwave Pyrolysis of Sewage Biosolids: Dielectric Properties, Microwave Susceptor Role and its Impact on Biochar Properties. J. Anal. Appl. Pyrolysis 129, 93–100. doi:10.1016/j.jaap.2017.11.023
Appleton, T. J., Colder, R. I., Kingman, S. W., Lowndes, I. S., and Read, A. G. (2005). Microwave Technology for Energy-Efficient Processing of Waste. Appl. Energy 81, 85–113. doi:10.1016/j.apenergy.2004.07.002
Arafat Hossain, M., Ganesan, P., Jewaratnam, J., and Chinna, K. (2017). Optimization of Process Parameters for Microwave Pyrolysis of Oil Palm Fiber (OPF) for Hydrogen and Biochar Production. Energy Convers. Manag. 133, 349–362. doi:10.1016/j.enconman.2016.10.046
Biagini, E., Lippi, F., Petarca, L., and Tognotti, L. (2002). Devolatilization Rate of Biomasses and Coal-Biomass Blends: An Experimental Investigation. Fuel 81, 1041–1050. doi:10.1016/S0016-2361(01)00204-6
Chen, G., Yu, Q., and Sjöström, K. (1997). Reactivity of Char from Pyrolysis of Birch Wood. J. Anal. Appl. Pyrolysis 40-41, 491–499. doi:10.1016/S0165-2370(97)00014-4
Chen, M.-q., Wang, J., Zhang, M.-x., Chen, M.-g., Zhu, X.-f., Min, F.-f., et al. (2008). Catalytic Effects of Eight Inorganic Additives on Pyrolysis of Pine Wood Sawdust by Microwave Heating. J. Anal. Appl. Pyrolysis 82, 145–150. doi:10.1016/j.jaap.2008.03.001
Demirbaş, A. (2001). Biomass Resource Facilities and Biomass Conversion Processing for Fuels and Chemicals. Energy Convers. Manag. 42, 1357–1378. doi:10.1016/S0196-8904(00)00137-0
Di Blasi, C. (2009). Combustion and Gasification Rates of Lignocellulosic Chars. Prog. Energy Combust. Sci. 35, 121–140. doi:10.1016/j.pecs.2008.08.001
Domínguez, A., Menéndez, J. A., Fernández, Y., Pis, J. J., Nabais, J. M. V., Carrott, P. J. M., et al. (2007). Conventional and Microwave Induced Pyrolysis of Coffee Hulls for the Production of A Hydrogen Rich Fuel Gas. J. Anal. Appl. Pyrolysis 79, 128–135. doi:10.1016/j.jaap.2006.08.003
Domínguez, A., Menéndez, J. A., Inguanzo, M., and Pís, J. J. (2006). Production of Bio-Fuels by High Temperature Pyrolysis of Sewage Sludge Using Conventional and Microwave Heating. Bioresour. Technol. 97, 1185–1193. doi:10.1016/j.biortech.2005.05.011
El Harfi, K., Mokhlisse, A., Chanâa, M. B., and Outzourhit, A. (2000). Pyrolysis of the Moroccan (Tarfaya) Oil Shales under Microwave Irradiation. Fuel 79, 733–742. doi:10.1016/S0016-2361(99)00209-4
Fernandez, Y., Arenillas, A., and Menendez, J. A. (2011). “Microwave Heating Applied to Pyrolysis,” in Advances in Induction and Microwave Heating of Mineral and Organic Materials (IntechOpen), 723–752. doi:10.5772/13548
Hirschmann, R. (2020). Palm Oil Industry in Malaysia: Statistics & Facts. Available at: https://www.statista.com/topics/5814/palm-oil-industry-in-malaysia/.
Huang, Y. F., Kuan, W. H., Lo, S. L., and Lin, C. F. (2010). Hydrogen-rich Fuel Gas from Rice Straw via Microwave-Induced Pyrolysis. Bioresour. Technol. 101, 1968–1973. doi:10.1016/j.biortech.2009.09.073
Huang, Y. F., Kuan, W. H., Lo, S. L., and Lin, C. F. (2008). Total Recovery of Resources and Energy from Rice Straw Using Microwave-Induced Pyrolysis. Bioresour. Technol. 99, 8252–8258. doi:10.1016/j.biortech.2008.03.026
Idris, S. S., Rahman, N. A., Ismail, K., Alias, A. B., Rashid, Z. A., and Aris, M. J. (2010). Investigation on Thermochemical Behaviour of Low Rank Malaysian Coal, Oil Palm Biomass and Their Blends during Pyrolysis via Thermogravimetric Analysis (TGA). Bioresour. Technol. 101, 4584–4592. doi:10.1016/j.biortech.2010.01.059
Jamaluddin, M. A., Ismail, K., Mohd Ishak, M. A., Ab Ghani, Z., Abdullah, M. F., Safian, M. T.-U., et al. (2013). Microwave-assisted Pyrolysis of Palm Kernel Shell: Optimization Using Response Surface Methodology (RSM). Renew. Energy 55, 357–365. doi:10.1016/j.renene.2012.12.042
Jones, D. A., Lelyveld, T. P., Mavrofidis, S. D., Kingman, S. W., and Miles, N. J. (2002). Microwave Heating Applications in Environmental Engineering-A Review. Resour. Conservation Recycl. 34, 75–90. doi:10.1016/S0921-3449(01)00088-X
Kim, S.-J., Jung, S.-H., and Kim, J.-S. (2010). Fast Pyrolysis of Palm Kernel Shells: Influence of Operation Parameters on the Bio-Oil Yield and the Yield of Phenol and Phenolic Compounds. Bioresour. Technol. 101, 9294–9300. doi:10.1016/j.biortech.2010.06.110
Kim, S. W., Koo, B. S., Ryu, J. W., Lee, J. S., Kim, C. J., Lee, D. H., et al. (2013). Bio-oil from the Pyrolysis of Palm and Jatropha Wastes in a Fluidized Bed. Fuel Process. Technol. 108, 118–124. doi:10.1016/j.fuproc.2012.05.002
Kong, S.-H., Loh, S.-K., Bachmann, R. T., Rahim, S. A., and Salimon, J. (2014). Biochar from Oil Palm Biomass: A Review of its Potential and Challenges. Renew. Sustain. Energy Rev. 39, 729–739. doi:10.1016/j.rser.2014.07.107
Lanigan, B. (2010). Microwave Processing of Lignocellulosic Biomass for Production of Fuels. PhD Thesis. York: University of York.
Ludlow-Palafox, C., and Chase, H. A. (2001). Microwave-induced Pyrolysis of Plastic Wastes. Ind. Eng. Chem. Res. 40, 4749–4756. doi:10.1021/ie010202j
McKendry, P. (2002). Energy Production from Biomass (Part 1): Overview of Biomass. Bioresour. Technol. 83, 37–46. doi:10.1016/S0960-8524(01)00118-3
Menéndez, J. A., Menéndez, E. M., Iglesias, M. J., García, A., and Pis, J. J. (1999). Modification of the Surface Chemistry of Active Carbons by Means of Microwave-Induced Treatments. Carbon N. Y. 37, 1115–1121. doi:10.1016/S0008-6223(98)00302-9
Miura, M., Kaga, H., Sakurai, A., Kakuchi, T., and Takahashi, K. (2004). Rapid Pyrolysis of Wood Block by Microwave Heating. J. Anal. Appl. Pyrolysis 71, 187–199. doi:10.1016/S0165-2370(03)00087-1
Mohd, N. A. (2017). Conventional and Microwave Pyrolysis of Empty Fruit Bunch and Rice Husk Pellets. PhD Thesis. Sheffield: University of Sheffield, 1–163. doi:10.1016/j.jclepro.2010.07.007
Norhidayu, A., Nur-Syazwani, M., Radzil, R., Amin, I., and Balu, N. (2017). The Production of Crude Palm Oil in Malaysia. Int. J. Econ. Manag. 11, 591–606.
Panwar, N. L., Kothari, R., and Tyagi, V. V. (2012). Thermo Chemical Conversion of Biomass - Eco Friendly Energy Routes. Renew. Sustain. Energy Rev. 16, 1801–1816. doi:10.1016/j.rser.2012.01.024
Qing, W., Guojun, J., Hongpeng, L., Jingru, B., and Shaohua, L. (2010). Variation of the Pore Structure during Microwave Pyrolysis of Oil Shale. Oil Shale 27, 135–146. doi:10.3176/oil.2010.2.04
Salema, A. A., and Ani, F. N. (2011). Microwave Induced Pyrolysis of Oil Palm Biomass. Bioresour. Technol. 102, 3388–3395. doi:10.1016/j.biortech.2010.09.115
Salema, A. A., and Ani, F. N. (2012a). Microwave-assisted Pyrolysis of Oil Palm Shell Biomass Using an Overhead Stirrer. J. Anal. Appl. Pyrolysis 96, 162–172. doi:10.1016/j.jaap.2012.03.018
Salema, A. A., and Ani, F. N. (2012b). Pyrolysis of Oil Palm Empty Fruit Bunch Biomass Pellets Using Multimode Microwave Irradiation. Bioresour. Technol. 125, 102–107. doi:10.1016/j.biortech.2012.08.002
Tripathi, M., Bhatnagar, A., Mubarak, N. M., Sahu, J. N., and Ganesan, P. (2020). RSM Optimization of Microwave Pyrolysis Parameters to Produce OPS Char with High Yield and Large BET Surface Area. Fuel 277, 118184. doi:10.1016/j.fuel.2020.118184
Keywords: oil palm biomass, biomass char, Box-Behnken, response surface methodology, microwave-assisted pyrolysis
Citation: Idris SS, Rahman NA, Ismail K, Mohammed Yunus MF and Mohd Hakimi NIN (2022) Microwave-Assisted Pyrolysis of Oil Palm Biomass: Multi-Optimisation of Solid Char Yield and Its Calorific Value Using Response Surface Methodology. Front. Chem. Eng. 4:864589. doi: 10.3389/fceng.2022.864589
Received: 28 January 2022; Accepted: 20 June 2022;
Published: 09 August 2022.
Edited by:
Costas Tsouris, Oak Ridge National Laboratory (DOE), United StatesReviewed by:
Alya Rozhan, International Islamic University Malaysia, MalaysiaPooya Lahijani, Universiti Sains Malaysia (USM), Malaysia
Copyright © 2022 Idris, Rahman, Ismail, Mohammed Yunus and Mohd Hakimi. This is an open-access article distributed under the terms of the Creative Commons Attribution License (CC BY). The use, distribution or reproduction in other forums is permitted, provided the original author(s) and the copyright owner(s) are credited and that the original publication in this journal is cited, in accordance with accepted academic practice. No use, distribution or reproduction is permitted which does not comply with these terms.
*Correspondence: Siti Shawalliah Idris, c2hhd2FsMDc1QHVpdG0uZWR1Lm15