- 1Department of Chemical and Environmental Engineering, University of Cincinnati (UC), Cincinnati, OH, United States
- 2Ultrasound and Optical Imaging Laboratory, Department of Bioengineering, The University of Texas at Arlington, Arlington, TX, United States
Coffee is the world’s second largest beverage only next to water. After coffee consumption, spent coffee grounds (SCGs) are usually thrown away and eventually end up in landfills. In recent years, technologies and policies are actively under development to change this century old practice, and develop SCGs into value added energy and materials. In this paper, technologies and practices are classified into two categories, those reuses SCGs entirely, and those breakdown SCGs and reuse by components. This article provided a brief review of various ways to reuse SCGs published after 2017, and provided more information on SCG quantity, SCG biochar development for pollutant removal and using SCG upcycle cases for education. SCG upcycle efforts align the best with the UN Sustainable Development Goals (SDG) #12 “ensure sustainable consumption and production patterns,” the resultant fuel products contribute to SDG #7 “affordable and clean energy,” and the resultant biochar products contribute to SDG #6, “clean water and sanitation.”
Introduction
Coffee is the world’s second most traded goods only next to oil, and it is the world’s second largest beverage only next to water. The world’s coffee consumption in 2020/2021 is nearly 10 million tonnes, with annual increase of about 1% since 2017 (ICO, 2021).
Only about 30% coffee bean’s mass can be extracted into the coffee we drink, thus a larger fraction ends up as spent coffee grounds, which has been mainly disposed of as waste. SCG reuse has received much more attention, especially in the recent decade. A byproduct from food and beverage applications, the quality of SCGs is higher and more consistent than other wastes, with the possibility to recycle single stream. These desirable aspects together with the diverse chemical compositions of SCGs, offer a desirable case for product upcycle. Indeed, public interests in SCG upcycle are increasing, together with supportive polices to drive technology development. This has been reflected in the number of publications as shown in Figure 1, which is also consistent with other similar reports. An increase in the number of publications on SCG reuse from 2011 to 2017 was reported by (Kourmentza et al., 2018), and another more significant increase afterwards (Bottani et al., 2019; Battista et al., 2021). As an example, a total of 189 publications on SCG reuse were found from Scopus database up to 2019 (Battista et al., 2021). This number aligns with that found in the Web of Science database with publications versus year by search term presented in Figure 1 with some specific search additions (pellet, biodiesel, biorefinery) to show different trends in research.
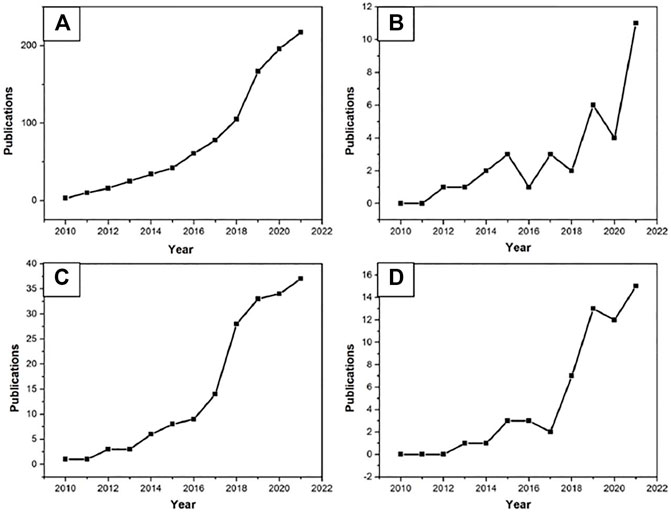
FIGURE 1. Number of publications from the Web of Science database from 2010 to 2021 based on the topic search category. (A) ‘spent coffee ground*’, (B) ‘spent coffee ground*’ and ‘pellet’, (C) ‘spent coffee ground*’ and ‘biodiesel’, (D) ‘spent coffee ground*’ and ‘biorefinery.’
The significant increase since 2018 may be due to the promotion of sustainable policy and practices, such as EU Directive 2018/851 amending Directive 2008/98/EC on waste, the initiatives in the US on landfill diversion, food waste reuse, and various similar initiatives elsewhere.
It is suggested that EU Directive 2018/851 boosted technology development of value-added compounds from SCGs, such as antioxidants and polyphenols, and as fillers on polymers, sustainable dyes, etc., have also been investigated, while SCG reuse as biodiesel and biomass fuel remain “trendy” (Battista et al., 2021). A 2019 review (McNutt and He, 2019) summarized different SCG reuse technologies in three categories, energy, food and health, and materials. Some technologies reused SCGs as a whole, such as compost, digestion, animal feed, material fillers, and solid fuels, etc. Other reuse technologies separate SCGs into different fractions and upcycle each fraction separately based on the concept of a biorefinery.
In recent years, there have been publicaitons on the biorefinery approach to reuse all the components of SCGs. Biorefining, as described by IEA, “is the sustainable processing of biomass into a spectrum of products and energy” (Van Ree et al., 2019). It refers to a series of sequential reuse processes to recover different components of SCGs in a zero-waste approach. As an example, SCG can be first extracted for water soluble polyphenols, caffeine, and antioxidants, etc. which have pharmaceutical and cosmetic applications and are deemed high value extracts. Next is hydrolysis to extract cellulose and hemicellulose as a substrate for fermentation as bioethanol or other biotechnology applications. Then it comes lipid extraction which can be used for biodiesel. Glycerin, the byproduct, can also be used as fuel or chemicals. The solids left can be developed into biochar, bio-oil, or fuel pellets (Mata et al., 2018).
Therefore, the goal of this review are three folds. First is to summarize recent SCG upcycle technologies since 2017, so as to identify current research interests. SCG reuse technologies and practices are classified into two categories, direct reuse and compositional reuse. Direct reuse refers to technology/practices using SCGs as a whole without much processing (except simple washing and dying), while compositional reuse refers to those separating SCGs into various components.
A second goal is to fill some gaps from previous reviews in SCG quantities and SCG redevelopment as biochar for pollutant removal. A third goal is to explore a simplified version of biorefinery to upcycle different components of SCGs at the community scale. A summary of the SCG inventory and compositional analysis of SCG will be first presented which provides a practical and theoretical basis of various reuse pathways.
SCG’s Quantities Generated From Different Sources
SCGs are generated by individuals, coffee shops, food services, and coffee producers. The exact determination of SCG inventory and compositional variation is limited from all of these generators largely due to its waste nature. SCG inventory information from coffee consumers also tends to be limited and sporadic.
An urban university (50,000 students) in a mid-sized US city can generate about 11 metric tonnes of SCGs annually from its campuses and vicinity. About 20 tonnes of SCGs can be collected from individual coffee shops in a town of about 45,000 people in the Eastern US (Carney, 2018). An inventory study in Sydney, Australia estimated that 3,000 metric tonnes of SCGs could be available for upcycle, and people accept a slight increase in cost for SCGs collection (PlanetArk, 2016). A detailed inventory in Italy by region indicated that more than 38,525 tonnes of SCGs can be produced in 2019 (Bottani et al., 2019).
Estimating SCG quantity from a community usually needs a detailed inventory of each commercial generator, while SCG generated by coffee producers tend to be inaccessible to the public. One of Nestle’s Spain facilities generated 45,000 metric tonnes of coffee grounds per year (Nestle, 2020). Another Nestle facility in Northeastern US produces about 40,000 tonnes of wet SCG annually. Starbucks has been estimated to generate approximately 90,000 tonnes of SCG per year in the United States alone (Misra et al., 2008).
A few internet sources indicated that Tim Horton sells two billion cups of coffee per year (Cuthbertson, 2018; CISION, 2020). Assuming 7–11 g of coffee produces a cup of coffee (Bottani et al., 2019; Bio-Bean 2021), it is estimated that Tim Horton has 180,000 tonnes of SCG per year, which is about 300,000 tonnes of wet SCGs per year (assuming 60% moisture).
Up to 50% of the SCGs are produced in small scales by coffee shops, restaurants, cafeterias or individuals, while large scale SCG producers are mostly from soluble coffee production (Taifouris et al., 2021). Since coffee shops must pay for SCGs disposal, many are willing to give them away at low or no cost. Inventory estimate from end users is a complex process and SCG collection is very costly.
Different SCG generation rates have been used by different types of SCG generators. As an example, coffee vendors report their coffee sales by cups. A widely cited estimation is that 0.65 g of SCG can be generated per Gram of green coffee beans (Murthy and Naidu, 2012). This is consistent with other studies, that coffee beans can lose 11–20% of weight due to roasting, and 20–32% of bean grinds/powders can be dissolved in water to become one cup of coffee (Go et al., 2016; Kamil et al., 2020). Another parameter for SCG estimation is that up to 0.91 g of SCGs can be generated per Gram of coffee (Dugmore, 2014).
SCG Compositions
SCGs usually come as wet with moisture contents varying from 42 wt% (Colantoni et al., 2021) to 65 wt% (Abomohra et al., 2021). The elemental compositions of SCGs are shown in Table 1, which highly dependent on the bean source and processing. The C/N ratio is a vital indicator for composting, ranged from 18:1 to 48:1. The low sulfur content (mostly <0.4%) suggested low sulfur dioxide formation expected when using SCGs as fuels. In addition, the ash content of SCGs is relatively low compared to other types of biomass fuels, such as wood (Todaro et al., 2015), bamboo, rice straw (Liu et al., 2013), palm kernel shell (Onochie et al., 2017), and oat hull (Abedi and Dalai, 2017). The low ash content makes SCGs desirable as a solid fuel, activated carbon or biochar. The average value of carbon element in SCG is from 46.23–68.52%, which is similar to data collected by two other research groups (Mata et al., 2018; Battista et al., 2021).
Although the heating value (HHV) of SCGs is lower than fossil fuels, it is higher than most other biomass, such as energy crops and wood chips, etc. while the nitrogen and sulfur content can be an air pollution issue when used as fuels.
The lignocellulosic contents of SCGs (Sluiter et al., 2008) results are shown in Table 2. The high cellulose and hemicellulose contents suggested SCG’s potential use as fermentation substrates (Zheng et al., 2009). The defatted (lipid removed by solvent extraction) SCG is also suitable for fermentation (Liu et al., 2017). Hemicellulose has a low decomposition temperature of about 220°C (Yang et al., 2007; Liu et al., 2015), which can decompose to form acetic acid at 400°C (Sermyagina et al., 2021), and tar during thermal recovery. These results are consistent with the literature (Ballesteros et al., 2014; Limousy et al., 2015; Mata et al., 2018).
The size distribution of SCGs varies depending on the sources, and most are within 1 mm. Figure 2 shows the size distribution of SCGs obtained from a US coffee chain store and after processing (Srivastava, 2020). The majority (42 wt%) of raw SCGs are between 600 and 875 µm in size. After coffee oil removal via Soxhlet extraction, the size distribution shifted to smaller sizes with a majority (34 wt%) of SCGs having a size between 125 and 425 µm. The size distribution also shifted after direct transesterification.
Direct SCG Reuse
Refuse Derived Fuel
As an agro-industrial residual, SCG is also a renewable biomass. Their high caloric value, low ash, and low metal contents are desirable properties as a biomass fuel to replace fossil fuels in boilers or fireplaces. Research studies on SCG reuse as pellets or logs are also increasing over the years as SCG is considered as a renewable biomass fuel (Bottani et al., 2019).
SCG fuel pellets need to meet various standards of the counties/regions, such as the NF ago-pellet standard of France (Nosek et al., 2020), and the ENplus, a voluntary standard for biomass fuels in the EU mainly for ash and metals (Colantoni et al., 2021).
SCG pellets and logs are sold in Europe and the US (Bio-Bean, 2021). The reuse pathway of SCGs in boilers has undergone extensive development; in fact, it has been commercialized already due to the lower processing cost. SCGs are burnt for heat at several Nestlé facilities (Nescafe, 2020; Nestle, 2020). SCGs was used to fuel the roasting process in coffee roasting companies (Mayson and Williams, 2021; Allesina, et al., 2017) to reduce waste generation and save fuel cost.
As with other SCG recovery technologies, the SCG drying process is crucial in its applications as fuels. SCGs usually contains up to 60% moisture. A moisture content of less than 10% is desirable for transportation and to reduce microbial growth during storage (Tun et al., 2020). Tun et al., 2020 compared open-air sun drying, solar drying, and oven drying before concluding that solar drying was the most advantageous in terms of energy use and adequate SCG quality.
Studies indicated that burning SCG alone can result in incomplete combustion, lower boiler efficiency, and incompliance with regulations, such as the STN EN 303-5 2012 for maximum CO (Nosek et al., 2020). Another consideration is pellet durability, a property that is regulated due to concerns about transportation and slag formation in combustion systems; pellets produced with high SCG content can also result in poor mechanical pellet properties (Whittaker and Shield, 2017; Woo et al., 2021).
As a result of the above-mentioned reasons, SCGs tend to be mixed with other biomass residuals, such as wood/sawdust, tea leaves, coffee silver skin, etc. and processed into pellets or logs (Bottani et al., 2019; Kristanto and Wijaya, 2018; Lisowski et al., 2019; Park et al., 2020).
Anaerobic Digestion to Biogas
SCG digestion to produce biomethane is mainly through co-digestion with other organic wastes, such as food waste or manure, etc. and quantity control is essential to maintain good methane yield. A study using only SCGs for anaerobic digestion pretreated the SCGs with NaOH to break down lignin. The highest weight loading of NaOH (8%) was found to be the most effective with the yield of methane reaching 394 ml/g volatile solid (Girotto et al., 2018).
A study on SCG co-digestion with pig manure reported over an order of magnitude improvement in methane production from 0.12 to 1.4 Lmethane/Lreactor/day (Orfanoudaki et al., 2020). Other researchers have taken advantage of cow manure for co-digestion (Luz et al., 2017) by mixing SCGs and cow manure at 1:1 ratio, and reported approximately 10% higher biomethane yield compared to only cow manure. Akyol (2020) investigated a similar cow manure-SCG system to determine the ideal inoculum to substrate ratio (I:S). The methane yield increased with I:S from 0.5:1 up to 3:1, further increases in inoculum reduced methane output.
Co-digested raw and defatted SCGs with macroalgae, glycerin, and spent tea The SCG detaffing process increased specific methane yield by approximately 10% (Atelge et al., 2021). Kim et al., 2017 used food waste (FW co-digested food waste (containing SCGs), Ulva biomass, waste activated sludge, and whey. Teixeira et al., 2021 studied digestion of two different SCGs, with the industrial SCGs from a soluble coffee company and post-consumer SCGs from a university restaurant. For low SCG content (25 wt%), no significant difference was seen between the sources. However, at high SCG loading (75 wt%), the industrial SCG had an inhibitory effect that reduced methane yield.
As part of food waste from households and restaurants, SCGs will continue to be used in anerobic digestion. Since the free fatty acids and antioxidants can have inhibitory effects to biogas production, SCGs are better used as a co-substrate with proper quantity control.
SCG Direct Soil Application
SCG has been used by many individuals in their gardens much earlier than various laboratory-developed technologies, from the anecdotal notion of “SCG is good for acid-loving plants” to a plethora of information on the internet as well as laboratory studies. SCG can function as mulch, compost, fertilizer, or even pest repellant in gardens (Chalker-Scott, 2009). An urban university in Midwest US collected compost SCGs, together with yard waste. SCG is less than 30% and coffee filters remained in the pile as a carbon source. The compost pile is mechanically turned regularly and matures (color changing from light to dark) within 6 months to a year and is used for university landscapes and teaching gardens. SCG can be mixed with other components to be used as fertilizer and was found to enhance grapevine production (Ronga et al., 2020). SCG is also co-composted with manure or sludges and used for soil amendment (Emmanuel et al., 2017) SCG is rich in nitrogen and other organic materials and can be a potential medium to increase soil organic matter. However, the smaller particle size can be an issue for blocking water and air circulation when used as mulch. Multiple reports indicated that only a fraction of SCGs should be used as compost and its impact is plant-dependent.
Studies indicated that polyphenols, caffeine, and tannins in SCGs are possible causes of plant growth inhibition (Hardgrove and Livesley, 2016). SCG application (1% wt) can improve soil enzymatic activity but can also cause oxidative stress to earth worms at a higher (5%) percentage (Sanchez-Hernandez et al., 2019). The phytotoxicity can be reduced by composting, vermicomposting, or thermal treatment, etc. to reduce these compounds (Cervera-Mata et al., 2020), and the reduction of polyphenol resulted in more biomass accumulation.
SCG direct application for landscapes will still be practiced and is likely to increase due to its low cost. As an example, in the US, if the state law allows SCG to be composted together with other yard residuals, SCG compost will be more practiced by larger entities.
The impacts of various SCG derived soil amendments, especially SCG compost and SCG biochar, have been mixed so far. Further studies, such as the volume of application, the soil type, and the plant type, etc. on plant growth are warranted to better reuse SCG derived products for soil amendment.
Raw SCGs as Absorbents
Raw SCGs have been used for absorption of different pollutants. Yen et al., 2022 studied polystyrene particles adsorption and obtained a maximum efficiency of 74%. SCGs have also seen use for removing cadmium (Azouaou et al., 2010; Palma et al., 2017; Kim and Kim, 2020) and other heavy metals (Hao et al., 2017). SCG can absorb ozone but was less effective than activated carbon (Hsieh and Wen, 2020). Loffredo et al., 2020 compared SCGs adsorption performance with other biomass and other adsorbents (wood biochar, and hydrochar) on the adsorption effectiveness of ochratoxin A. SCG performed worse than wood biochar, hydrochar, humic acid, clementine peel and coconut fiber, but was than ground almond shells, hazelnuts, walnuts, and chestnuts. SCGs have also been used for dye adsorption (Safarik et al., 2012), and the effectiveness was highly dependent on dye type. Direct SCG and SCG biochar use for remediating heavy metal contaminated soil and water were compared by Kim et al., 2014. While both reduced the heavy metal bioavailability; the direct SCG use actually increased phytotoxicity, unlike the biochar. SCGs in these studies are usually washed and dried, but the performance was not as good as biochar or activated carbon.
Technologies for SCG Component Recovery
SCG Lipid Recovery
Lipids in SCG generally range from 8 to 20% and can be developed into different products. This is consistent with the lipid content of virgin coffee beans, ranging from 8 to 18% (Massaya et al., 2019).
Conversion of SCGs lipids to biodiesel (methyl/ethyl esters) continues to be one of the “trendy” research topics, while other uses, such as renewable diesel or bioplastics, are also emerging. This section summarized recent research in SCG oil extraction, SCG biodiesel production and technology innovations.
Table 3 summarized practices to extract SCG lipids after drying. Lipid extraction can be conducted with or without a Soxhlet. The high SCG oil yield of 30.4 wt% (Efthymiopoulos et al., 2019) might be related to the source of SCG and the long extraction time. Ultrasound was used to pretreat the SCGs, with higher lipid yield and lower acid value compared to those without. Having been successfully applied in caffeine extraction, supercritical CO2 extraction is also increasingly applied to SCG lipid extraction. The conditions reported in Table 4 are within the range of previous studies (Couto et al., 2009; Ribeiro et al., 2013; Akgün et al., 2014; Barbosa et al., 2014).
The supercritical CO2 extraction method has been studied as green and environmental-friendly technology to eliminate organic solvent used during the coffee oil extraction process. The optimal process variables were studied by Muangrat’s group. Moreover, the application of supercritical CO2 extraction method with co-solvents such as isopropanol, ethanol, and ethyl lactate was conducted and the result showed that the extraction time could be shortened by half compared to the Soxhlet extraction process to reach the same coffee oil yield. In addition, compared to the pure supercritical CO2 extraction method, supercritical CO2 extraction with co-solvents can get a higher antioxidant capacity (Coelho et al., 2020). The extraction of coffee oil with the assistance of microwave has also been studied recently and the extraction time has been shortened significantly, which is beneficial to reduce energy consumption (Yordanov et al., 2016; Hibbert et al., 2019). Non-thermal plasma pre-treatment prior to lipid extraction is reported to have increased yield when compared to Soxhlet alone and increased unsaturated fractions of the lipids (Cubas et al., 2020).
Depending on the FFA content, SCG lipid may need to go through esterification and then transesterification to become biodiesel. This conventional practice is still used, while direct-transesterification (in situ), which produces biodiesel from SCGs in one step without oil extraction has been implemented much more recently due to its simplicity.
Table 4 summarized recent improvements on making biodiesel from SCGs. New catalysts have been reported for the in-situ (direct transesterification) process, such as waste eggshell and 1,8-diazabicyclo [5.4.0]undec-7-ene (DBU). For in-situ processes without catalysts, a co-solvent of ethanol and 1,2-dichloroethane (DCE) was used and ethyl esters were produced. A unique deacidification treatment prior to the in-situ reaction was conducted (Tuntiwiwattanapun et al., 2017), and the acid value was significantly reduced from 5.93 mg KOH/g oil to around 0.59 mg KOH/g oil. A low yield of 8.7 wt% might be caused by the low reaction temperature and inefficiency of waste eggshell. Palmitic acid methyl ester (C16:0) and linoleic acid methyl ester (C18:2) were two major fatty acid methyl esters (FAME) in SCG biodiesel, consistent with earlier studies.
Technology improvements on the SCG biodiesel process include the following, catalyst improvements such as immobilized sulfuric acid on silica gel (Karmee, 2017), ultrasound to improve oil extraction during direct transesterification (Kim Y. S. et al., 2020), production of ethyl esters using enzymes (Gonçalves et al., 2020), and supercritical fluids extraction (Son et al., 2018; Battista et al., 2021).
In addition, SCG biodiesel can be blended with alcohols to better improve cold flow or density to meet Euro-diesel requirements (Atabani and Al-Rubaye, 2020).
Phimsen et al. (2016) extracted coffee oil using solvent extraction and converted it to renewable diesel (hydrotreated diesel) which contains C15 and C17 hydrocarbons. Bio oil from hydrothermal liquefication is also studied due to its higher HHV than the methyl esters (Marx et al., 2020). but further reformulation is typically needed before use.
The SCG to biodiesel process has not been commercialized so far. SCG drying process (e.g., up to 60% moisture) is energy intensive and can make the biodiesel process economically uncompetitive (Taifouris et al., 2021) during production. Since caffeine in biodiesel can increase NOx emissions (Jenkins et al., 2014), water wash, or even better, a recovery process with water prior to lipid extraction, will be very beneficial to improve the purity lipid extraction.
SCG Solids as Biochar
Pyrogenic carbonaceous materials are produced by heating carbon-containing feedstocks under almost no oxygen, which can be developed into both biochar and activated carbon (AC). AC can be upgraded from biochar by undergoing an additional activation step (Rashidi and Yusup, 2020), and is mainly used for pollutant absorption. Studies on SCG conversion into AC were not reviewed here as there are not that many after the review of McNutt and He, 2019.
Biochars are typically much cheaper than AC since they are usually made with waste feedstocks, at lower temperatures, and do not undergo the “activation” step, lowering process costs. Biochars tend to have smaller surface areas, but more functional groups (Gale et al., 2021). In recent years, research interests have gradually shifted to converting SCGs into biochar instead of AC.
Compared with other ago-industrial biomass, SCGs have a competitive advantage as biochar; they can be obtained with relatively high purity and are already in uniform sizes. Therefore, they can be a promising feedstock for pyrolytic carbon products. Biochar can potentially be used in a wide variety of ways, with some well-known applications such as soil carbon sequestration, pollutant removal, and soil amendment (Schmidt and Wilson, 2014; Hagemann et al., 2018).
SCG Biochar are usually prepared under nitrogen or CO2. Using CO2 as carrier gas can accelerate the thermal cracking of organic compounds but increases CO formation, which reduces yield (Kim Y. et al., 2019). A study compared SCG biochars made with both nitrogen and carbon dioxide. There was no yield difference, while lower biochar pH can be observed at temperatures below 400°C with biochar made under CO2 as seen in Table 5 (Srivastava, 2020). The biochars were made with both as-received SCG and also the solids left from in situ transesterification (Doped SCG). The latter is acidic while the majority of biochars are alkaline. Acidic biochar can be desirable for select fruits and vegetables, such as berries.
SCG biochar use as a soil amendment continues to be practiced. For example, SCG biochar was produced by slow pyrolysis at 550°C and had an alkaline pH for liming use (Stylianou et al., 2020).
SCG Biochar for Pollutant Removal
Functionalization prior and during biochar production are much easier than after it is made. SCGs are uniform in sizes, easily accessible, and low cost, which are ideal for functionalization to increase selectivity of pollutant removal. In recent years, SCG biochar for pollutant removal has been pursued with increasing interest but with limited review summaries. Heavy metal adsorption by SCG biochar, a relatively “traditional” application, is summarized in Table 6. One improvement is doping to obtain magnetic biochar for easier separation, denoted as iron modified in Table 6. Cho et al. (2017) also explored the gas used for pyrolysis and determined that biochar made in nitrogen had higher As (V) absorption despite a smaller surface area than those made in carbon dioxide.
SCG biochar use for antibiotic adsorption and removal, such as tetracycline (TC) sulfadiazine (SDZ), sulfamethoxazole (SMX), and diclofenac (DCF) is a newer application and is shown in Table 7. Table 7 also shows the use of SCG biochar for dye adsorption of malachite green dye (MG-D) and methylene blue dye (MB-D). Mohamad et al. (2020) used an experimental matrix to determine optimized conditions of treatment based on classical experiments, the best predicted results are shown in Table 7. Lee et al. (2021) used iron impregnated SCG biochar to degrade methylene blue dye (MB-D) in conjunction with cold plasma. Lee et al., 2021 also determined the effect of the system on the total organic carbon (TOC) with MB-D showing maximum removal efficiency as high as 98.3%.
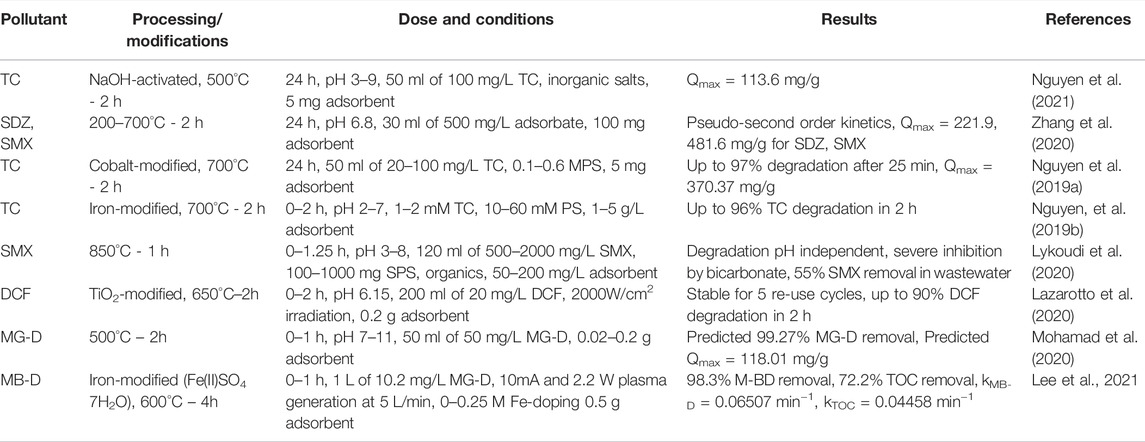
TABLE 7. Recent studies on SCG derived biochar adsorption of pharmaceuticals, antibiotics, and dyes.
Tala and Chantara (2019) used biochar from SCG (slow pyrolysis at 500°C) to remove 16-polycyclic aromatic hydrocarbons (PAH) from ambient air. The adsoption capacity of the produced biochar was comparable to a commercial sorbent, XAD-2. McNutt and He (2019) summarized recent studies on SCG derived activation carbon. A few more recent developments are included herein. SCG AC was used to remove bisphenol-A (Alves et al., 2019) and phenolic compounds (Rosson et al., 2020). Bisphenol-A (BPA) was removed from groundwater using activated carbon produced from SCGs with ZnCl2 as an activating agent. The activated carbon showed high efficiency for BPA adsorption of 98% (123.2 mg/g) which surpassed the commercial AC tested as control. Rosson et al. (2020) treated SCGs with KOH as the activating agent. The adsorption of organic compounds studied included methylene blue, erythrosine B, bromothymol blue, phenol, 3-chlorophenol, and BPA. The produced AC showed similar adsorption characteristics to the commercial AC.
SCG derived biochar has also been tested for non-adsorption or applications such as composite fillers (Arrigo et al., 2020), as a value-added ferrous material (Biswal et al., 2021), as molecular sieves through the modification of activated carbon (Kaya et al., 2020) with defatted SCGs, for supercapacitor application (Adan-Mas et al., 2021) and as catalytic support for iron nanoparticles (Acosta et al., 2020).
SCGs as New Materials
Many bioactive compounds remain in SCGs after coffee brewing, although the quality and quantity vary depending on how they are treated (Panusa et al., 2013; Vandeponseele et al., 2021). This has led to increased interests in recovering antioxidants for a wide variety of uses (Ballesteros et al., 2017; Hwang et al., 2019; Zengin et al., 2020). Ethanol appears to be the most common solvent for extracting antioxidants although alternative methods have been explored. Samsalee et al., 2021 explored ultrasonic assisted extraction to generate an antioxidant rich protein extract. SCGs have also been used as a source of fiber and antioxidants use in baked goods at 4% weight loading without impacting the food preparation process or food quality (Martinez-Saez et al., 2017). Recovery of antioxidants from SCGs has been researched substantially in recent years (Kourmentza et al., 2018; McNutt and He 2019) and therefore not much covered here.
Polymer or monomer production via SCGs has seen interest to replace traditional petroleum-based options. The production of monomers using an extracted oil from SCGs and the use of sulfuric acid pretreated SCG slurry were both explored using engineered bacteria (Bhatia et al., 2018; Kim J. W. et al., 2019). Alternatively, polyhydroxyalkanoate (PHA) was produced with coffee oil after removing microbial inhibitors (Kovalcik et al., 2018). Tukacs et al., 2017 used microwave heated SCGs mixed with 2 M sulfuric acid to generate levulinic acid with a yield of around 13%, which successfully reduced the reaction time from 8 h using a traditional heating method (oil bath) to 30 min.
SCGs have been explored as a sustainable dye for cotton and wool fabrics which showed improved colorfastness over other natural dyes, high UV blocking activity, and significant antioxidant activity (Koh and Hong, 2017). Mongkholrattanasit et al., 2021 used chitosan to introduce amino groups, citric acid to crosslink, and sodium hypophosphite as a catalyst to develop the dye for cotton. The color and wrinkle resistance of the fabric was seen to last 20 washes but the tensile strength was affected.
SCGs have also been exploited for their carbon content and porosity to generate energy storage materials such as a Li-S battery cathode (Kim B. et al., 2020). Yeşiltepe and Şeşen, 2020 pelletized SCG with mill scale, battery paste (separated from steel casing and washed to remove electrolyte), and bentonite (binder). The pellets were dried before reduction in argon purged furnace at 1,250–1,400°C. The pellets showed a 70% metallization rate of ferromanganese and a 91.18% pelletizing process efficiency.
A Simplified Zero-Waste Case
Since SCG upcycle at community levels are much smaller in scales, it is essential to pick and choose the compatible pathways. An example is shown in Figure 3 to separate SCGs into lignocellulosic, lipid and solid fractions. As received SCGs first undergo lignocellulose extraction (process A), with 4% dilute sulfuric acid and heat at 95°C for 120 min (Alvira et al., 2010). The products can be used for fermentation and made into bioethanol or biobutanol (Mussatto et al., 2012). Since this is also a wet process, there is no need to dry the collected SCGs. The wet SCG-solids (SCG1) will then be coated with 20% sulfuric acid, dried, and will go through a direct transesterification process B (Liu et al., 2017), where the liquids will be separated and purified into biodiesel. Lipid separation by solvent extraction is another defat alternative to make coffee oil from process B. A few studies indicated that acid hydrolysis followed by lipid extraction is feasible as nonpolar lipids remain largely unaffected since process A uses water as solvent (Go et al., 2016; Juarez et al., 2018; Passadis et al., 2020).
The remaining solids (SCG2) will be made into biochar through a thermal process C. Since hemicellulose can range from 32 to 42% (Massaya et al., 2019) and has a low temperature for thermal decomposition, it is reasonable to extract this fraction prior to solids recovery to reduce the formation of tar. This process takes advantage of the moisture of the as provided SCGs and also results in a functionalized acidic biochar.
By separating SCG into components, the amount of remaining waste is reduced and the opportunity to produce multiple value-added products can be achieved. However, the commercialization of this process has been limited so far likely due to high cost and feedstock quantity.
SCG Upcycle as a Case Study for Education and Outreach
SCG reuse technologies and practices also offer excellent educational opportunities to the general public, and can be tailored to engage a wide variety of audience. Educational products can range from colorful handouts, fact sheets to journal publications. The outreach venue can range from public events (e.g., the Earth Day) to formal classrooms (Lu et al., 2020). As an example, SCG reuse has been implemented into college lectures and experimental courses. It can be suitable as a case study for a class on sustainability or waste management. Process simulation of the scale up and technoeconomic analysis of various technology choices suit perfectly for a design class. SCG upcycle efforts align the best with the UN Sustainable Development Goals (SDG) #12 “ensure sustainable consumption and production patterns,” the resultant fuel products contribute to SDG #7 “affordable and clean energy,” and the resultant biochar products contribute to SDG #6, “clean water and sanitation.” Therefore, it can be integrated in-context of many education and outreach activities.
Conclusion
The SCG can be a very versatile feedstock based on its compositions. The range of applications for SCGs is incredibly broad with some focused on the entire use of SCGs, others based on specific compositions. Technologies/practices for direct SCG reuse tend to be low cost and will continue to be practiced. Their use may be limited due to the incompatibility of certain SCG components, e.g., biological inhibition in direct soil application and anaerobic digestion, and the nitrogen and sulfur contents resulting in air pollutant formation when used as fuel. In contrast, the biorefinery approach have the potential to reuse most fractions of SCGs and is close to the zero-waste goal. This approach can be limited by feedstock quantity and cost of technologies.
The valorization of SCGs will result in waste diversion and resource conservation. Currently, many of these valorization technologies are still in laboratory stage. In order to reduce SCGs as waste, proper choice of products/processes is essential. Meanwhile, innovative and low cost technologies are needed to more effectively extract targeted components from SCGs, and to lower the cost of product development. Supportive policies, investment, detailed economic analysis and customer discovery will be necessary. SCG valorization efforts also provide great opportunities to educate the public about sustainable practices.
Author Contributions
YL summarized SCGs compositions, reviewed and discussed SCG lipid recovery and SCG biodiesel. KJ reviewed and discussed refuse derived fuel, anaerobic digestion to biogas, raw SCGs as adsorbents, SCGs to biochar, SCG biochar for pollutant removal, and SCGs as new materials. ML drafted the abstract, introduction, conclusions, and other sections of this manuscript as well as the overall editing.
Funding
The financial support of NSF IIP 1838771 is gratefully acknowledged for supporting biochar production from raw and acid doped SCGs, with different carrier gases (nitrogen and carbon dioxide) under various temperatures. The financial support of NSF AY REU funds from 2012–2015 is gratefully acknowledged for supporting the development of direct transesterification of SCGs and compositional studies.
Conflict of Interest
The authors declare that the research was conducted in the absence of any commercial or financial relationships that could be construed as a potential conflict of interest.
Publisher’s Note
All claims expressed in this article are solely those of the authors and do not necessarily represent those of their affiliated organizations, or those of the publisher, the editors, and the reviewers. Any product that may be evaluated in this article, or claim that may be made by its manufacturer, is not guaranteed or endorsed by the publisher.
Acknowledgments
The authors greatly appreciate the contribution from Dr. Tan Xin for sugar content analysis, Dr. Yanmei Zhou, Elizabeth Williams, Garrett Schwein, Jinqi Liu and Suhas Srivastava for biochar production and metal absorption tests.
References
Abedi, A., and Dalai, A. K. (2017). Study on the Quality of Oat hull Fuel Pellets Using Bio-Additives. Biomass and Bioenergy 106, 166–175. doi:10.1016/J.BIOMBIOE.2017.08.024
Abomohra, A. E. F., Zheng, X., Wang, Q., Huang, J., and Ebaid, R. (2021). Enhancement of Biodiesel Yield and Characteristics through Iin-Ssitu Solvo-thermal Co-transesterification of Wet Microalgae with Spent Coffee Grounds. Bioresour. Techn. 323 (December 2020), 23–31. doi:10.1016/j.biortech.2020.124640
Acosta, L., Galeano-Caro, D., Medina, O. E., Cortés, F. B., and Franco, C. A. (2020). Nano-Intermediate of Magnetite Nanoparticles Supported on Activated Carbon from Spent Coffee Grounds for Treatment of Wastewater from Oil Industry and Energy Production. Process. 639 (1), 63. doi:10.3390/PR9010063
Adan-Mas, A., Alcaraz, L., Arévalo-Cid, P., López-Gómez, F. A., and Montemor, F. (2021). Coffee-derived Activated Carbon from Second Biowaste for Supercapacitor Applications. Waste Manag. 120, 280–289. doi:10.1016/J.WASMAN.2020.11.043
Akgün, N. A., Bulut, H., Kikic, I., and Solinas, D. (2014). Extraction Behavior of Lipids Obtained from Spent Coffee Grounds Using Supercritical Carbon Dioxide. Chem. Eng. Techn. 37 (11), 1975–1981. doi:10.1002/ceat.201400237
Akyol, Ç. (2020). In Search of the Optimal Inoculum to Substrate Ratio during Anaerobic Co-digestion of Spent Coffee Grounds and Cow Manure. Waste Manag. Res. 38 (11), 1278–1283. doi:10.1177/0734242X20914731
Allesina, G., Pedrazzi, S., Allegretti, F., and Tartarini, P. (2017). Spent Coffee Grounds as Heat Source for Coffee Roasting Plants: Experimental Validation and Case Study. Appl. Therm. Eng. 126, 730–736. doi:10.1016/J.APPLTHERMALENG.2017.07.202
Alves, A. C. F., Antero, R. V. P., Ojala, S. A., and Scalize, P. S. (2019). Activated Carbon Produced from Waste Coffee Grounds for an Effective Removal of Bisphenol-A in Aqueous Medium. Environ. Sci. Pollut. Res. Int. 26 (24), 24850–24862. doi:10.1007/S11356-019-05717-7
Alvira, P., Tomás-Pejó, E., Ballesteros, M., and Negro, M. J. (2010). Pretreatment Technologies for an Efficient Bioethanol Production Process Based on Enzymatic Hydrolysis: A Review. Bioresour. Techn. 101 (13), 4851–4861. doi:10.1016/J.BIORTECH.2009.11.093
Arrigo, R., Bartoli, M., and Malucelli, G. (2020). Poly(lactic Acid)-Biochar Biocomposites: Effect of Processing and Filler Content on Rheological, thermal, and Mechanical Properties. Polymers 12, 892. doi:10.3390/POLYM12040892
Atabani, A. E., and Al-Rubaye, O. K. (2020). Valorization of Spent Coffee Grounds for Biodiesel Production: Blending with Higher Alcohols, FT-IR, TGA, DSC, and NMR Characterizations. Biomass Convers. Biorefinery 12 (3), 577–596. doi:10.1007/S13399-020-00866-Z
Atabani, A. E., Mercimek, S. M., Arvindnarayan, S., Shobana, S., Kumar, G., Cadir, M., et al. (2018). Valorization of Spent Coffee Grounds Recycling as a Potential Alternative Fuel Resource in Turkey: An Experimental Study. J. Air Waste Manag. Assoc. 68 (3), 196–214. doi:10.1080/10962247.2017.1367738
Atelge, M. R., Atabani, A. E., Abut, S., Kaya, M., Eskicioglu, C., Semaan, G., et al. (2021). Anaerobic Co-digestion of Oil-Extracted Spent Coffee Grounds with Various Wastes: Experimental and Kinetic Modeling Studies. Bioresour. Techn. 322, 124470. doi:10.1016/J.BIORTECH.2020.124470
Azouaou, N., Sadaoui, Z., Djaafri, A., and Mokaddem, H. (2010). Adsorption of Cadmium from Aqueous Solution onto Untreated Coffee Grounds: Equilibrium, Kinetics and Thermodynamics. J. Hazard. Mater. 184 (1–3), 126–134. doi:10.1016/J.JHAZMAT.2010.08.014
Ballesteros, L. F., Ramirez, M. J., Orrego, C. E., Teixeira, J. A., and Mussatto, S. I. (2017). Optimization of Autohydrolysis Conditions to Extract Antioxidant Phenolic Compounds from Spent Coffee Grounds. J. Food Eng. 199, 1–8. doi:10.1016/J.JFOODENG.2016.11.014
Ballesteros, L. F., Teixeira, J. A., and Mussatto, S. I. (2014). Chemical, Functional, and Structural Properties of Spent Coffee Grounds and Coffee Silverskin. Food Bioproc. Eng., 3493–3503. doi:10.1007/s11947-014-1349-z
Barbosa, H. M. A., De Melo, M. M. R., Coimbra, M. A., Passos, C. P., and Silva, C. M. (2014). Optimization of the Supercritical Fluid Coextraction of Oil and Diterpenes from Spent Coffee Grounds Using Experimental Design and Response Surface Methodology. J. Supercrit. Fluids 85, 165–172. doi:10.1016/j.supflu.2013.11.011
Battista, F., Zuliani, L., Rizzioli, F., Fusco, S., and Bolzonella, D. (2021). Biodiesel, Biogas and Fermentable Sugars Production from Spent Coffee Grounds: A cascade Biorefinery Approach. Bioresour. Techn. 342, 125952. doi:10.1016/J.BIORTECH.2021.125952
Bhatia, S. K., Kim, J. H., Kim, M. S., Kim, J., Hong, J. W., Hong, Y. G., et al. (2018). Production of (3-Hydroxybutyrate-Co-3-Hydroxyhexanoate) Copolymer from Coffee Waste Oil Using Engineered Ralstonia Eutropha. Bioproc. Biosyst. Eng. 41 (2), 229–235. doi:10.1007/S00449-017-1861-4
Bio-Bean (2021). Coffee Pellets. Available at: https://www.bio-bean.com/elements/pellets/. (accessed Feb, , 2022).
Biswal, S., Pahlevani, F., and Sahajwalla, V. (2021). Synthesis of Value-Added Ferrous Material from Electric Arc Furnace (EAF) Slag and Spent Coffee Grounds. JOM 73 (6), 1878–1888. doi:10.1007/S11837-021-04678-Y
Bottani, E., Tebaldi, L., and Volpi, A. (2019). The Role of ICT in Supporting Spent Coffee Grounds Collection and Valorization: A Quantitative Assessment. Sustainability 657211 (23), 6572. doi:10.3390/SU11236572
Caetano, N. S., Caldeira, D., Martins, A. A., and Mata, T. M. (2017). Valorisation of Spent Coffee Grounds: Production of Biodiesel via Enzymatic Catalysis with Ethanol and a Co-solvent. Waste Biomass Valor. 8 (6), 1981–1994. doi:10.1007/S12649-016-9790-Z
Caetano, N. S., Silva, V. F. M., Melo, A. C., Martins, A. A., and Mata, T. M. (2014). Spent Coffee Grounds for Biodiesel Production and Other Applications.Clean Technologies and Environmental Policy. 16 (7), 1423–1430. doi:10.1007/S10098-014-0773-0
Carney, M. (2018). Taking Out the Trash. Penn State Altoona. Available at: https://altoona.psu.edu/feature/taking-out-trash. (accessed Feb, 2022).
Cervera-Mata, A., Navarro-Alarcón, M., Rufián-Henares, J., Montilla-Gómez, J., and Delgado, G. (2020). Phytotoxicity and Chelating Capacity of Spent Coffee Grounds: Two Contrasting Faces in its Use as Soil Organic Amendment. Sci. Total Environ. 717, 137247. doi:10.1016/J.SCITOTENV.2020.137247
Chalker-Scott, L. (2009). Coffee Grounds - Will They Perk up Plants. Master Gardener, 3–4. Available at: https://s3.wp.wsu.edu/uploads/sites/403/2015/03/coffee-grounds.pdf (Accessed March, 2022).
Chen, W. H., Du, J. T., Lee, K. T., Ong, H. C., Park, Y. K., and Huang, C. C. (2021). Pore Volume Upgrade of Biochar from Spent Coffee Grounds by Sodium Bicarbonate during Torrefaction. Chemosphere 275, 129999. doi:10.1016/j.chemosphere.2021.129999
Cho, D. W., Yoon, K., Kwon, E. E., Biswas, J. K., and Song, H. (2017). Fabrication of Magnetic Biochar as a Treatment Medium for As(V) via Pyrolysis of FeCl3-Pretreated Spent Coffee Ground. Environ. Pollut. 229, 942–949. doi:10.1016/J.ENVPOL.2017.07.079
Chwastowski, J., Bradło, D., and Żukowski, W. (2020). Adsorption of Cadmium, Manganese and Lead Ions from Aqueous Solutions Using Spent Coffee Grounds and Biochar Produced by its Pyrolysis in the Fluidized Bed Reactor. Mater. 278213 (12), 2782. doi:10.3390/MA13122782
CISION. (2020). Tim Hortons® to Eliminate Approximately 200 Million Cups a Year by Ending the Practice of “double-cupping.” (2020, October 21). Available at: https://www.newswire.ca/news-releases/tim-hortons-r-to-eliminate-approximately-200-million-cups-a-year-by-ending-the-practice-of-double-cupping–820475803.html. (accessed Feb, 2022).
Coelho, J. P., Filipe, R. M., Paula Robalo, M., Boyadzhieva, S., Cholakov, G. S., and Stateva, R. P. (2020). Supercritical CO2 Extraction of Spent Coffee Grounds. Influence of Co-solvents and Characterization of the Extracts. J. Supercrit. Fluids 161. doi:10.1016/j.supflu.2020.104825
Colantoni, A., Paris, E., Bianchini, L., Ferri, S., Marcantonio, V., Carnevale, M., et al. (2021). Spent Coffee Ground Characterization, Pelletization Test and Emissions Assessment in the Combustion Process. Scientific Rep. 11 (1), 1–14. doi:10.1038/s41598-021-84772-y
Couto, R. M., Fernandes, J., da Silva, M. D. R. G., and Simões, P. C. (2009). Supercritical Fluid Extraction of Lipids from Spent Coffee Grounds. J. Supercrit. Fluids 51 (2), 159–166. doi:10.1016/j.supflu.2009.09.009
Cubas, A. L. V., Medeiros Machado, M., Tayane Bianchet, R., Alexandra da Costa Hermann, K., Alexsander Bork, J., Angelo Debacher, N., et al. (2020). Oil Extraction from Spent Coffee Grounds Assisted by Non-thermal Plasma. Sep. Purif. Techn. 250, 117171. doi:10.1016/J.SEPPUR.2020.117171
Cuthbertson, R. (2018). In the Quest for Cleaner Fuels, a Scientist Turns to Tim Hortons Coffee Grounds. CBC News. Available at: https://www.cbc.ca/news/canada/nova-scotia/scientist-turns-to-tim-hortons-coffee-grounds-1.4889437. (accessed Feb, 2022).
Dugmore, T. (2014). The Business of Food Waste. Available at: https://www.slideshare.net/GreenEconomyCoalition/tom-dugmore-the-business-of-food-waste. (accessed Feb, 2022).
Efthymiopoulos, I., Hellier, P., Ladommatos, N., Kay, A., and Mills-Lamptey, B. (2019). Effect of Solvent Extraction Parameters on the Recovery of Oil from Spent Coffee Grounds for Biofuel Production. Waste Biomass Valor. 10 (2), 253–264. doi:10.1007/s12649-017-0061-4
Emmanuel, S. A., Yoo, J., Kim, E. J., Chang, J. S., Park, Y. I., and Koh, S. C. (2017). Development of Functional Composts Using Spent Coffee Grounds, Poultry Manure and Biochar through Microbial Bioaugmentation. J. Environ. Sci. Health 52 (11), 802–811. doi:10.1080/03601234.2017.1356165
Gale, M., Nguyen, T., Moreno, M., and Gilliard-Abdulaziz, K. L. (2021). Physiochemical Properties of Biochar and Activated Carbon from Biomass Residue: Influence of Process Conditions to Adsorbent Properties. ACS Omega 6 (15), 10224–10233. doi:10.1021/ACSOMEGA.1C00530/SUPPL
Girotto, F., Lavagnolo, M. C., and Pivato, A. (2018). Spent Coffee Grounds Alkaline Pre-treatment as Biorefinery Option to Enhance Their Anaerobic Digestion Yield. Waste Biomass Valor. 9 (12), 2565–2570. doi:10.1007/S12649-017-0033-8/FIGURES/3
Go, A. W., Conag, A. T., and Cuizon, D. E. S. (2016). Recovery of Sugars and Lipids from Spent Coffee Grounds: A New Approach. Waste Biomass Valor. 7 (5), 1047–1053. doi:10.1007/s12649-016-9527-z
Goh, B. H. H., Ong, H. C., Chong, C. T., Chen, W. H., Leong, K. Y., Tan, S. X., et al. (2020). Ultrasonic Assisted Oil Extraction and Biodiesel Synthesis of Spent Coffee Ground. Fuel 261 (October 2019), 116121. doi:10.1016/j.fuel.2019.116121
Gonçalves, E. C. S., Martínez Pérez, M., Vici, A. C., Salgado, S., de Souza Rocha, M., and Zaghetto de Almeida, P., (2020). Potential Biodiesel Production from Brazilian Plant Oils and Spent Coffee Grounds by Beauveria Bassiana Lipase 1 Expressed in Aspergillus nidulans A773 Using Different Agroindustry Inputs. J. Clean. Prod. 256, 120513. doi:10.1016/J.JCLEPRO.2020.120513
Hagemann, N., Spokas, K., Schmidt, H. P., Kägi, R., Böhler, M. A., and Bucheli, T. D. (2018). Activated Carbon, Biochar and Charcoal: Linkages and Synergies across Pyrogenic Carbon’s ABCs. Water 18210 (2), 182. doi:10.3390/W10020182
Hao, L., Wang, P., and Valiyaveettil, S. (2017). Successive Extraction of As(V), Cu(II) and P(V) Ions from Water Using Spent Coffee Powder as Renewable Bioadsorbents. Scientific Rep. 7 (1), 1–12. doi:10.1038/srep42881
Hardgrove, S. J., and Livesley, S. J. (2016). Applying Spent Coffee Grounds Directly to Urban Agriculture Soils Greatly Reduces Plant Growth. Urban For. Urban Green. 18, 1–8. doi:10.1016/J.UFUG.2016.02.015
Hibbert, S., Welham, K., and Zein, S. H. (2019). An Innovative Method of Extraction of Coffee Oil Using an Advanced Microwave System: in Comparison with Conventional Soxhlet Extraction Method. SN Appl. Sci. 1 (11), 1–9. doi:10.1007/s42452-019-1457-5
Hsieh, P. F., and Wen, T. Y. (2020). Evaluation of Ozone Removal by Spent Coffee Grounds. Scientific Rep. 2020 10:1 10 (1), 1–8. doi:10.1038/S41598-019-56668-5
Hussain, N., Chantrapromma, S., Suwunwong, T., and Phoungthong, K. (2020). Cadmium (II) Removal from Aqueous Solution Using Magnetic Spent Coffee Ground Biochar: Kinetics, Isotherm and Thermodynamic Adsorption. Nucl. Fusion 60. doi:10.1088/1741-4326/abab52
Hwang, H. S., Winkler-Moser, J. K., Kim, Y., and Liu, S. X. (2019). Antioxidant Activity of Spent Coffee Ground Extracts toward Soybean Oil and Fish Oil. Eur. J. Lipid Sci. Techn. 121 (4), 1800372. doi:10.1002/EJLT.201800372
ICO. (2021). Coffee Market Report. Available at: https://www.ico.org/(accessed Feb, 2022).
Im, G., and Yeom, S. H. (2020). Repeated Biodiesel Production from Waste Coffee Grounds via a One-step Direct Process with a Cartridge Containing Solid Catalysts Manufactured from Waste Eggshells. Biotechnol. Bioproc. Eng. 25 (4), 623–632. doi:10.1007/s12257-019-0369-y
Jenkins, R. W., Stageman, N. E., Fortune, C. M., and Chuck, C. J. (2014). Effect of the Type of Bean, Processing, and Geographical Location on the Biodiesel Produced from Waste Coffee Grounds. Energy Fuels 28 (2), 1166–1174. doi:10.1021/ef4022976
Juarez, G. F. Y., Pabiloña, K. B. C., Manlangit, K. B. L., and Go, A. W. (2018). Direct Dilute Acid Hydrolysis of Spent Coffee Grounds: A New Approach in Sugar and Lipid Recovery. Waste Biomass Valor. 9 (2), 235–246. doi:10.1007/S12649-016-9813-9/FIGURES/7
Kamil, M., Ramadan, K. M., Olabi, A. G., Al-Ali, E. I., Ma, X., and Awad, O. I. (2020). Economic, Technical, and Environmental Viability of Biodiesel Blends Derived from Coffee Waste. Renew. Energy 147, 1880–1894. doi:10.1016/J.RENENE.2019.09.147
Karmee, S. K. (2017). Technical Valorisation of Spent Coffee Grounds and Food Waste Using Sulphuric Acid Immobilised on Silica. 10.1080/17597269.2017.1378989 11 (2), 155–161. doi:10.1080/17597269.2017.1378989
Kaya, M., Atelge, M. R., Bekirogullari, M., Eskicioglu, C., Atabani, A. E., Kumar, G., et al. (2020). Carbon Molecular Sieve Production from Defatted Spent Coffee Ground Using ZnCl2 and Benzene for Gas Purification. Fuel 277, 118183. doi:10.1016/J.FUEL.2020.118183
Kaya, M. (2020). Production of Metal-free Catalyst from Defatted Spent Coffee Ground for Hydrogen Generation by Sodium Borohyride Methanolysis. Int. J. Hydrogen Energ. 45 (23), 12731–12742. doi:10.1016/j.ijhydene.2019.08.013
Kim, J. W., Jang, J. H., Yeo, H. J., Seol, J., Kim, S. R., and Jung, Y. H. (2019). Lactic Acid Production from a Whole Slurry of Acid-Pretreated Spent Coffee Grounds by Engineered Saccharomyces cerevisiae. Appl. Biochem. Biotechnol. 189 (1), 206–216. doi:10.1007/S12010-019-03000-6/FIGURES/4
Kim, Y., Lee, J., Yi, H., Fai Tsang, Y., and Kwon, E. E. (2019). Investigation into Role of CO 2 in Two-Stage Pyrolysis of Spent Coffee Grounds. Bioresour. Techn. 272, 48–53. doi:10.1016/J.BIORTECH.2018.10.009
Kim, B., Park, J., Baik, S., and Lee, J. W. (2020). Spent Coffee Derived Hierarchical Porous Carbon and its Application for Energy Storage. J. Porous Mater. 27 (2), 451–463. doi:10.1007/S10934-019-00826-7/FIGURES/7
Kim, J., Kim, H., Baek, G., and Lee, C. (2017). Anaerobic Co-digestion of Spent Coffee Grounds with Different Waste Feedstocks for Biogas Production. Waste Manag. 60, 322–328. doi:10.1016/J.WASMAN.2016.10.015
Kim, M. S., and Kim, J. G. (2020). Adsorption Characteristics of Spent Coffee Grounds as an Alternative Adsorbent for Cadmium in Solution. Environments - MDPI, 7(4). doi:10.3390/ENVIRONMENTS7040024
Kim, M. S., Min, H. G., Koo, N., Park, J., Lee, S. H., Bak, G. I., et al. (2014). The Effectiveness of Spent Coffee Grounds and its Biochar on the Amelioration of Heavy Metals-Contaminated Water and Soil Using Chemical and Biological Assessments. J. Environ. Manage. 146, 124–130. doi:10.1016/J.JENVMAN.2014.07.001
Kim, Y. S., Woo, D. G., and Kim, T. H. (2020). Characteristics of Direct Transesterification Using Ultrasound on Oil Extracted from Spent Coffee Grounds. Environ. Eng. Res. 25 (4), 470–478. doi:10.4491/EER.2019.076
Koh, E., and Hong, K. H. (2017). Preparation and Properties of Wool Fabrics Dyed with Spent Coffee Ground Extract. Textile Res. J. 89 (1), 13–19. doi:10.1177/0040517517736469
Kourmentza, C., Economou, C. N., Tsafrakidou, P., and Kornaros, M. (2018). Spent Coffee Grounds Make Much More Than Waste: Exploring Recent Advances and Future Exploitation Strategies for the Valorization of an Emerging Food Waste Stream. J. Clean. Prod. 172, 980–992. doi:10.1016/J.JCLEPRO.2017.10.088
Kovalcik, A., Kucera, D., Matouskova, P., Pernicova, I., Obruca, S., Kalina, M., et al. (2018). Influence of Removal of Microbial Inhibitors on PHA Production from Spent Coffee Grounds Employing Halomonas Halophila. J. Environ. Chem. Eng. 6 (2), 3495–3501. doi:10.1016/J.JECE.2018.05.028
Kristanto, G. A., and Wijaya, H. (2018). Assessment of Spent Coffee Ground (SCG) and Coffee Silverskin (CS) as Refuse Derived Fuel (RDF). IOP Conference Series. Earth and Environmental Science 195, 012056. doi:10.1088/1755-1315/195/1/012056
Lazarotto, J. S., de Lima Brombilla, V., Silvestri, S., and Foletto, E. L. (2020). Conversion of Spent Coffee Grounds to Biochar as Promising TiO2 Support for Effective Degradation of Diclofenac in Water. Appl. Organomet. Chem. 34 (12), 1–11. doi:10.1002/aoc.6001
Lee, J. C, J. C., Kim, H. J., Kim, H. W., and Lim, H. (2021). Iron-impregnated Spent Coffee Ground Biochar for Enhanced Degradation of Methylene Blue during Cold Plasma Application. J. Ind. Eng. Chem. 98, 383–388. doi:10.1016/j.jiec.2021.03.026
Lee, K. T, K.-T., Cheng, C.-L., Lee, D.-S., Chen, W.-H., Vo, D.-V. N., Ding, L., et al. (2021). Spent Coffee Grounds Biochar from Torrefaction as a Potential Adsorbent for Spilled Diesel Oil Recovery and as an Alternative Fuel. Energy, 239, 122467. doi:10.1016/j.energy.2021.122467
Limousy, L., Jeguirim, M., Labbe, S., Balay, F., and Fossard, E. (2015). Performance and Emissions Characteristics of Compressed Spent Coffee Ground/wood Chip Logs in a Residential Stove. Energ. Sust. Dev. 28, 52–59. doi:10.1016/J.ESD.2015.07.002
Lisowski, A., Olendzki, D., Świętochowski, A., Dąbrowska, M., Mieszkalski, L., Ostrowska-Ligęza, E., et al. (2019). Spent Coffee Grounds Compaction Process: Its Effects on the Strength Properties of Biofuel Pellets. Renew. Energ. 142 (C), 173–183. doi:10.1016/J.RENENE.2019.04.114
Liu, W. J., Jiang, H., and Yu, H. Q. (2015). Development of Biochar-Based Functional Materials: Toward a Sustainable Platform Carbon Material. Chem. Rev. 115 (22), 12251–12285. doi:10.1021/ACS.CHEMREV.5B00195
Liu, Y. (2015). Making Biodiesel from Spent Coffee Grounds through in Situ Transesterification. MS thesis. Cincinnati, OH: University of Cincinnati.
Liu, Y., Tu, Q., Knothe, G., and Lu, M. (2017). Direct Transesterification of Spent Coffee Grounds for Biodiesel Production. Fuel 199, 157–161. doi:10.1016/j.fuel.2017.02.094
Liu, Z., Liu, X., Fei, B., Jiang, Z., Cai, Z., and Yu, Y. (2013). The Properties of Pellets from Mixing Bamboo and rice Straw. Renew. Energ. 55, 1–5. doi:10.1016/J.RENENE.2012.12.014
Loffredo, E., Scarcia, Y., and Parlavecchia, M. (2020). Removal of Ochratoxin A from Liquid media Using Novel Low-Cost Biosorbents. Environ. Sci. Pollut. Res. 27 (27), 34484–34494. doi:10.1007/S11356-020-09544-Z/TABLES/3
Lu, M., Mata, A., and Liu, J. (2020). “Making Biodiesel from Waste, a Versatile Chemistry Module to Incorporate Sustainability Education,” in Chemistry Education for a Sustainable Society, Volume 2: Innovations in Undergraduate Curricula, ACS Symposium Series. Editors S. Obare, C. H. Middlecamp, and K. E. Peterman, 93–112.
Luz, F. C., Cordiner, S., Manni, A., Mulone, V., and Rocco, V. (2017). Anaerobic Digestion of Coffee Grounds Soluble Fraction at Laboratory Scale: Evaluation of the Biomethane Potential. Appl. Energy 207, 166–175. doi:10.1016/J.APENERGY.2017.06.042
Lykoudi, A., Frontistis, Z., Vakros, J., Manariotis, I. D., and Mantzavinos, D. (2020). Degradation of Sulfamethoxazole with Persulfate Using Spent Coffee Grounds Biochar as Activator. J. Environ. Manage. 271. doi:10.1016/J.JENVMAN.2020.111022
Martinez-Saez, N., García, A. T., Pérez, I. D., Rebollo-Hernanz, M., Mesías, M., Morales, F. J., et al. (2017). Use of Spent Coffee Grounds as Food Ingredient in Bakery Products. Food Chem. 216, 114–122. doi:10.1016/J.FOODCHEM.2016.07.173
Marx, S., Venter, R., Karmee, S. K., Louw, J., and Truter, C. (2020). Biofuels from Spent Coffee Grounds: Comparison of Processing Routes. Biofuels, July, 1–7. doi:10.1080/17597269.2020.1793538
Massaya, J., Prates Pereira, A., Mills-Lamptey, B., Benjamin, J., and Chuck, C. J. (2019). Conceptualization of a Spent Coffee Grounds Biorefinery: A Review of Existing Valorisation Approaches. Food Bioproducts Process. 118, 149–166. doi:10.1016/J.FBP.2019.08.010
Mata, T. M., Martins, A. A., and Caetano, N. S. (2018). Bio-refinery Approach for Spent Coffee Grounds Valorization. Bioresour. Techn. 247, 1077–1084. doi:10.1016/J.BIORTECH.2017.09.106
Mayson, S., and Williams, I. D. (2021). Applying a Circular Economy Approach to Valorize Spent Coffee Grounds. Resources. Conservation and Recycling 172, 105659. doi:10.1016/J.RESCONREC.2021.105659
McNutt, J., and He, Q. (2019). (SophiaSpent Coffee Grounds: A Review on Current Utilization. J. Ind. Eng. Chem. 71, 78–88. doi:10.1016/J.JIEC.2018.11.054
Misra, M., Kondamudi, N., and Strull, J. (2008). High Quality Biodiesel Production from Spent Coffee Grounds. AIChE Annu. Meet. Available at: https://aiche.confex.com/aiche/2008/techprogram/P139846.HTM. (accessed Feb, 2022).
Mohamad, M., Wannahari, R., Mohammad, R., Shoparwe, N. F., Nawi, A. S. M., Lun, K. W., et al. (2020). Adsorption of Malachite green Dye Using Spent Coffee Ground Biochar: Optimisation Using Response Surface Methodology. Jurnal Teknologi 83 (1), 27–36. doi:10.11113/jurnalteknologi.v83.14904
Mongkholrattanasit, R., Nakpathom, M., and Vuthiganond, N. (2021). Eco-dyeing with Biocolorant from Spent Coffee Ground on Low Molecular Weight Chitosan Crosslinked Cotton. Sust. Chem. Pharm. 20. doi:10.1016/J.SCP.2021.100389
Muangrat, R., and Pongsirikul, I. (2019). Recovery of Spent Coffee Grounds Oil Using Supercritical CO2: Extraction Optimization and Physicochemical Properties of Oil. CYTA - J. Food 17 (1), 334–346. doi:10.1080/19476337.2019.1580771
Mueanmas, C., Nikhom, R., Petchkaew, A., Iewkittayakorn, J., and Prasertsit, K. (2019). Extraction and Esterification of Waste Coffee Grounds Oil as Non-edible Feedstock for Biodiesel Production. Renew. Energ. 133, 1414–1425. doi:10.1016/j.renene.2018.08.102
Murthy, P. S., and Naidu, M. (2012). Sustainable Management of Coffee Industry By-Products and Value Addition—A Review. Resour. Conservation Recycling 66, 45–58. doi:10.1016/J.RESCONREC.2012.06.005
Mussatto, S. I., Machado, E. M. S., Carneiro, L. M., and Teixeira, J. A. (2012). Sugars Metabolism and Ethanol Production by Different Yeast Strains from Coffee Industry Wastes Hydrolysates. Appl. Energ. 92, 763–768. doi:10.1016/J.APENERGY.2011.08.020
Nescafe (2020). Nescafé Factory Now Running on Recycled Coffee. Available at: https://www.nestle.com.au/en/stories/recycled-coffee (accessed Feb, 2022).
Nestle (2020). Nestlé Will Reuse its Coffee Waste to Generate Biomass. Available at: https://expobiomasa.com/en/district-heating-district-heating/Nestle-will-reuse-its-coffee-waste-to-generate-biomass (accessed Feb, 2022).
Nguyen, H. C., Nguyen, M. L., Wang, F. M., Juan, H. Y., and Su, C. H. (2020). Biodiesel Production by Direct Transesterification of Wet Spent Coffee Grounds Using Switchable Solvent as a Catalyst and Solvent. Bioresour. Techn. 296 (October 2019), 122334. doi:10.1016/j.biortech.2019.122334
Nguyen, V. T., Hung, C. M., Nguyen, T. B., Chang, J. H., Wang, T. H., Wu, C. H., et al. (2019b). Efficient Heterogeneous Activation of Persulfate by Iron-Modified Biochar for Removal of Antibiotic from Aqueous Solution: A Case Study of Tetracycline Removal. Catalysts 9 (1), 1–14. doi:10.3390/catal9010049
Nguyen, V. T., Nguyen, T. B., Chen, C. W., Hung, C. M., Huang, C. P., and Dong, C. (2019a). Cobalt-impregnated Biochar (Co-SCG) for Heterogeneous Activation of Peroxymonosulfate for Removal of Tetracycline in Water. Biores. Technol. 292. doi:10.1016/J.BIORTECH.2019.121954
Nguyen, V. T., Nguyen, T. B., Huang, C. P., Chen, C. W., Bui, X. T., and DongDi, C. (2021). Alkaline Modified Biochar Derived from Spent Coffee Ground for Removal of Tetracycline from Aqueous Solutions. J. Water Process Eng. 40 (August 2020), 101908. doi:10.1016/j.jwpe.2020.101908
Nosek, R., Tun, M. M., and Juchelkova, D. (2020). Energy Utilization of Spent Coffee Grounds in the Form of Pellets. Energies 2020, Vol. 13, Page 123513 (5), 1235. doi:10.3390/EN13051235
Onochie, U. P., Obanor, A. I., Aliu, S. A., and Ighodaro, O. O. (2017). Proximate and Ultimate Analysis of Fuel Pellets from Oil Palm Residues. Niger. J. Techn. 36 (3), 987–990. doi:10.4314/njt.v36i3.44
Orfanoudaki, A., Makridakis, G., Maragkaki, A., Fountoulakis, M. S., Kallithrakas-Kontos, N. G., and Manios, T. (2020). Anaerobic Co-digestion of Pig Manure and Spent Coffee Grounds for Enhanced Biogas Production. Waste Biomass Valor. 11 (9), 4613–4620. doi:10.1007/S12649-019-00796-6/FIGURES/6
Palma, L., Stoller, M., Silvina Patterer, M., Bavasso, I., Sambeth, J. E., and Medici, F. (2017). Cadmium Removal from Acqueous Solution by Adsorption on Spent Coffee Grounds. Chem. Eng. Trans. 60, 2017. doi:10.3303/CET1760027
Panusa, A., Zuorro, A., Lavecchia, R., Marrosu, G., and Petrucci, R. (2013). Recovery of Natural Antioxidants from Spent Coffee Grounds. J. Agric. Food Chem. 61 (17), 4162–4168. doi:10.1021/JF4005719
Park, J., Kim, B., Son, J., and Lee, J. W. (2018). Solvo-thermal In Situ Transesterification of Wet Spent Coffee Grounds for the Production of Biodiesel. Bioresour. Techn. 249 (August 2017), 494–500. doi:10.1016/j.biortech.2017.10.048
Park, S., Kim, S. J., Oh, K. C., Cho, L., Kim, M. J., Jeong, I. S., et al. (2020). Investigation of Agro-Byproduct Pellet Properties and Improvement in Pellet Quality through Mixing. Energy 190. doi:10.1016/J.ENERGY.2019.11638
Passadis, K., Fragoulis, V., Stoumpou, V., Novakovic, J., Barampouti, E. M., Mai, S., et al. (2020). Study of Valorisation Routes of Spent Coffee Grounds. Waste Biomass Valor. 11 (10), 5295–5306. doi:10.1007/s12649-020-01096-0
Phimsen, S., Kiatkittipong, W., Yamada, H., Tagawa, T., Kiatkittipong, K., Laosiripojana, N., et al. (2016). Oil Extracted from Spent Coffee Grounds for Bio-Hydrotreated Diesel Production. Energ. Convers. Manag. 126, 1028–1036. doi:10.1016/J.ENCONMAN.2016.08.085
PlanetArk (2016). Coffee Go Ground. Planet Ark Environmental Foundation. Available at: https://planetark.org/newsroom/archive/1059 (Accessed Feb, 2022).
Rashidi, N. A., and Yusup, S. (2020). Biochar as Potential Precursors for Activated Carbon Production: Parametric Analysis and Multi-Response Optimization. Environ. Sci. Pollut. Res. 27 (22), 27480–27490. doi:10.1007/S11356-019-07448-1/FIGURES/3
Ribeiro, H., Marto, J., Raposo, S., Agapito, M., Isaac, V., Chiari, B. G., et al. (2013). From Coffee Industry Waste Materials to Skin-Friendly Products with Improved Skin Fat Levels. Eur. J. Lipid Sci. Techn. 115 (3), 330–336. doi:10.1002/ejlt.201200239
Ronga, D., Parisi, M., Barbieri, L., Lancellotti, I., Andreola, F., and Bignami, C. (2020). Valorization of Spent Coffee Grounds, Biochar and Other Residues to Produce Lightweight Clay Ceramic Aggregates Suitable for Nursery Grapevine Production. Horticulturae 586 (4), 58. doi:10.3390/HORTICULTURAE6040058
Rosson, E., Garbo, F., Marangoni, G., Bertani, R., Lavagnolo, M. C., Moretti, E., et al. (2020). Activated Carbon from Spent Coffee Grounds: A Good Competitor of Commercial Carbons for Water Decontamination. Appl. Sci. 559810 (16), 5598. doi:10.3390/APP10165598
Safarik, I., Horska, K., Svobodova, B., and Safarikova, M. (2012). Magnetically Modified Spent Coffee Grounds for Dyes Removal. Eur. Food Res. Techn. 234 (2), 345–350. doi:10.1007/S00217-011-1641-3
Samsalee, N., Sothornvit, R., Samsalee, N., and Sothornvit, R. (2021). Physicochemical, Functional Properties and Antioxidant Activity of Protein Extract from Spent Coffee Grounds Using Ultrasonic-Assisted Extraction. AIMS Agric. Food 6 (3), 864–878. doi:10.3934/AGRFOOD.2021052
Sanchez-Hernandez, J. C., Ríos, J. M., Attademo, A. M., Malcevschi, A., and Andrade Cares, X. (2019). Assessing Biochar Impact on Earthworms: Implications for Soil Quality Promotion. J. Hazard. Mater. 366, 582–591. doi:10.1016/J.JHAZMAT.2018.12.032
Schmidt, H. P., and Wilson, K. (2014). The 55 Uses of Biochar. Biochar J. Available at: www.biochar-journal.org/en/ct/2 (Accessed March, 2022).
Sermyagina, E., Mendoza, C., and Deviatkin, I. (2021). Effect of Hydrothermal Carbonization and Torrefaction on Spent Coffee Grounds. Agron. Res. 19 (Special Issue 1), 928–943. doi:10.15159/AR.21.023
Shin, J., Lee, S. H., Kim, S., Ochir, D., Park, Y., Kim, J., et al. (2021). Effects of Physicochemical Properties of Biochar Derived from Spent Coffee Grounds and Commercial Activated Carbon on Adsorption Behavior and Mechanisms of Strontium Ions (Sr 2+). Environ. Sci. Pollut. Res. Int. 28 (30), 40623–40632. doi:10.1007/S11356-020-10095-6
Sluiter, A., Hames, B., Ruiz, R., Scarlata, C., Sluiter, J., Templeton, D., et al. (2008). Determination of Structural Carbohydrates and Lignin in Biomass: Laboratory Analytical Procedure (LAP) (Revised July 2011). Available at: http://www.nrel.gov/biomass/analytical_procedures.html. (accessed Feb, 2022).
Son, J., Kim, B., Park, J., Yang, J., and Lee, J. W. (2018). Wet In Situ Transesterification of Spent Coffee Grounds with Supercritical Methanol for the Production of Biodiesel. Bioresour. Techn. 259 (February), 465–468. doi:10.1016/j.biortech.2018.03.067
Srivastava, S. (2020). Zero Waste Utilization of Spent Coffee Grounds (SCGs) and the Feasibility Study of Heavy Metal Removal from the Aqueous Phase with SCG Biochar. MS Thesis. Cincinnati, OH: University of Cincinnati.
Stylianou, M., Christou, A., Dalias, P., Polycarpou, P., Michael, C., Agapiou, A., et al. (2020). Physicochemical and Structural Characterization of Biochar Derived from the Pyrolysis of Biosolids, Cattle Manure and Spent Coffee Grounds. J. Energ. Inst. 93 (5), 2063–2073. doi:10.1016/J.JOEI.2020.05.002
Taifouris, M., Corazza, M. L., and Martín, M. (2021). Integrated Design of Biorefineries Based on Spent Coffee Grounds. Ind. Eng. Chem. Res. 60 (1), 494–506. doi:10.1021/ACS.IECR.0C05246/SUPP
Tala, W., and Chantara, S. (2019). Use of Spent Coffee Ground Biochar as Ambient PAHs Sorbent and Novel Extraction Method for GC-MS Analysis. Environ. Sci. Pollut. Res. Int. 26 (13), 13025–13040. doi:10.1007/S11356-019-04473-Y
Taleb, F., Ammar, M., and Mosbah, M. (2020). Chemical Modification of Lignin Derived from Spent Coffee Grounds for Methylene Blue Adsorption. Scientific Rep. 10 (1), 1–13. doi:10.1038/s41598-020-68047-6
Tarigan, J. B., Ginting, M., Mubarokah, S. N., Sebayang, F., Karo-Karo, J., Nguyen, T. T., et al. (2019). Direct Biodiesel Production from Wet Spent Coffee Grounds. RSC Adv. 9 (60), 35109–35116. doi:10.1039/c9ra08038d
Teixeira, R. A., Bueno, B. A., Borges, R. M., and Bringhenti, J. R. (2021). Biochemical Methane Potential of Spent Coffee Grounds via Co-digestion with Food Waste. Bioenergy Res. 1, 1–12. doi:10.1007/S12155-021-10351-8/TABLES/5
Todaro, L., Rita, A., Cetera, P., and D’Auria, M. (2015). Thermal Treatment Modifies the Calorific Value and Ash Content in Some wood Species. Fuel 140, 1–3. doi:10.1016/J.FUEL.2014.09.060
Tukacs, J. M., Holló, A. T., Rétfalvi, N., Cséfalvay, E., Dibó, G., Havasi, D., et al. (2017). Microwave-Assisted Valorization of Biowastes to Levulinic Acid. ChemistrySelect 2 (4), 1375–1380. doi:10.1002/SLCT.201700037
Tun, M. M., Raclavská, H., Juchelková, D., Růžičková, J., Šafář, M., Štrbová, K., et al. (2020). Spent Coffee Ground as Renewable Energy Source: Evaluation of the Drying Processes. J. Environ. Manage. 275, 111204. doi:10.1016/J.JENVMAN.2020.111204
Tuntiwiwattanapun, N., Monono, E., Wiesenborn, D., and Tongcumpou, C. (2017). In-situ Transesterification Process for Biodiesel Production Using Spent Coffee Grounds from the Instant Coffee Industry. Ind. Crops Prod. 102, 23–31. doi:10.1016/j.indcrop.2017.03.019
Van Ree, R., De Jong, E., and Kwant, K. (2019). Biorefining in a Future BioEconomy. Available at: https://www.ieabioenergy.com/wp-content/uploads/2019/11/IEA-Bioenergy_Task-42-Triennium-2016-2018-1.pdf.
Vandeponseele, A., Draye, M., Piot, C., and Chatel, G. (2021). Study of Influential Parameters of the Caffeine Extraction from Spent Coffee Grounds: From Brewing Coffee Method to the Waste Treatment Conditions. Clean. Tech. 3 (2), 335–350. doi:10.3390/CLEANTECHNOL3020019
Whittaker, C., and Shield, I. (2017). Factors Affecting wood, Energy Grass and Straw Pellet Durability – A Review. Renew. Sust. Energ. Rev. 71, 1–11. doi:10.1016/J.RSER.2016.12.119
Woo, D. G., Kim, S. H., and Kim, T. H. (2021). Solid Fuel Characteristics of Pellets Comprising Spent Coffee Grounds and Wood Powder. Energies 202114 (Vol. 14), 371. doi:10.3390/EN14020371
Yang, H., Yan, R., Chen, H., Lee, D. H., and Zheng, C. (2007). Characteristics of Hemicellulose, Cellulose and Lignin Pyrolysis. Fuel 86 (12–13), 1781–1788. doi:10.1016/J.FUEL.2006.12.013
Yen, P. L., Hsu, C. H., Huang, M. L., and Liao, V. H. C. (2022). Removal of Nano-Sized Polystyrene Plastic from Aqueous Solutions Using Untreated Coffee Grounds. Chemosphere 286, 131863. doi:10.1016/J.CHEMOSPHERE.2021.131863
Yeşiltepe, S., and Şeşen, M. K. (2020). Production of Composite Pellets from Waste Coffee Grounds, Mill Scale and Waste Primary Battery to Produce Ferromanganese; a Zero Waste Approach. Acta Metallurgica Slovaca 26 (2), 45–48. doi:10.36547/AMS.26.2.540
Yordanov, D., Mustafa, Z., Milina, R., and Tsonev, Z. (2016). Multi-criteria Optimisation Process of the Oil Extraction from Spent Coffee Ground by Various Solvents. Oxidation Commun. 39 (2), 1478–1487.
Zengin, G., Sinan, K. I., Mahomoodally, M. F., Angeloni, S., Mustafa, A. M., Vittori, S., et al. (2020). Chemical Composition, Antioxidant and Enzyme Inhibitory Properties of Different Extracts Obtained from Spent Coffee Ground and Coffee Silverskin. Foods 7139 (6), 713. doi:10.3390/FOODS9060713
Zhang, X., Zhang, Y., Ngo, H. H., Guo, W., Wen, H., Zhang, D., et al. (2020). Characterization and Sulfonamide Antibiotics Adsorption Capacity of Spent Coffee Grounds Based Biochar and Hydrochar. Sci. Total Environ. 716. doi:10.1016/j.scitotenv.2020.137015
Keywords: spent coffee grounds, upcycle, direct transesterification, biodiesel, biochar, direct SCG reuse, compositional SCG recovery, refuse derived fuel
Citation: Johnson K, Liu Y and Lu M (2022) A Review of Recent Advances in Spent Coffee Grounds Upcycle Technologies and Practices. Front. Chem. Eng. 4:838605. doi: 10.3389/fceng.2022.838605
Received: 18 December 2021; Accepted: 02 March 2022;
Published: 14 April 2022.
Edited by:
Fahmi Abu Al-Rub, Jordan University of Science and Technology, JordanReviewed by:
Ivy Ai Wei Tan, Universiti Malaysia Sarawak, MalaysiaAikaterini Ioannis Vavouraki, Technical University of Crete, Greece
Copyright © 2022 Johnson, Liu and Lu. This is an open-access article distributed under the terms of the Creative Commons Attribution License (CC BY). The use, distribution or reproduction in other forums is permitted, provided the original author(s) and the copyright owner(s) are credited and that the original publication in this journal is cited, in accordance with accepted academic practice. No use, distribution or reproduction is permitted which does not comply with these terms.
*Correspondence: Mingming Lu, bWluZ21pbmcubHVAdWMuZWR1