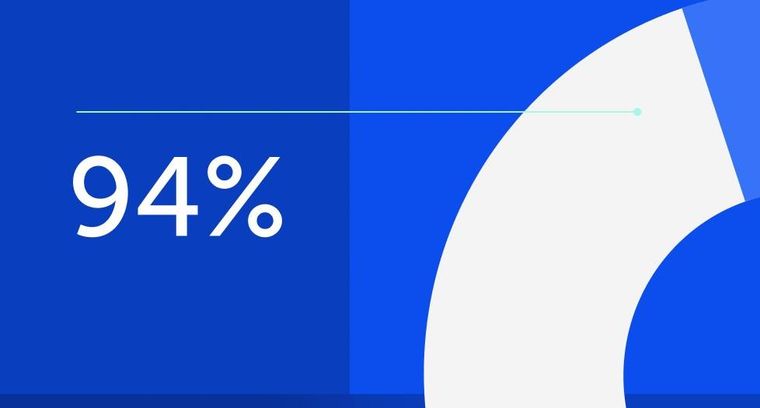
94% of researchers rate our articles as excellent or good
Learn more about the work of our research integrity team to safeguard the quality of each article we publish.
Find out more
REVIEW article
Front. Chem. Eng., 30 November 2022
Sec. Sustainable Process Engineering
Volume 4 - 2022 | https://doi.org/10.3389/fceng.2022.1008680
This article is part of the Research TopicSeparations for Energy and Environmental ApplicationsView all 5 articles
Under the Paris Agreement, established by the United Nations Framework Convention on Climate Change, many countries have agreed to transition their energy sources and technologies to reduce greenhouse gas emissions to levels concordant with the 1.5°C warming goal. Lithium (Li) is critical to this transition due to its use in nuclear fusion as well as in rechargeable lithium-ion batteries used for energy storage for electric vehicles and renewable energy harvesting systems. As a result, the global demand for Li is expected to reach 5.11 Mt by 2050. At this consumption rate, the Li reserves on land are expected to be depleted by 2080. In addition to spodumene and lepidolite ores, Li is present in seawater, and salt-lake brines as dissolved Li+ ions. Li recovery from aqueous solutions such as these are a potential solution to limited terrestrial reserves. The present work reviews the advantages and challenges of a variety of technologies for Li recovery from aqueous solutions, including precipitants, solvent extractants, Li-ion sieves, Li-ion-imprinted membranes, battery-based electrochemical systems, and electro-membrane-based electrochemical systems. The techno-economic feasibility and key performance parameters of each technology, such as the Li+ capacity, selectivity, separation efficiency, recovery, regeneration, cyclical stability, thermal stability, environmental durability, product quality, extraction time, and energy consumption are highlighted when available. Excluding precipitation and solvent extraction, these technologies demonstrate a high potential for sustainable Li+ extraction from low Li+ concentration aqueous solutions or seawater. However, further research and development will be required to scale these technologies from benchtop experiments to industrial applications. The development of optimized materials and synthesis methods that improve the Li+ selectivity, separation efficiency, chemical stability, lifetime, and Li+ recovery should be prioritized. Additionally, techno-economic and life cycle analyses are needed for a more critical evaluation of these extraction technologies for large-scale Li production. Such assessments will further elucidate the climate impact, energy demand, capital costs, operational costs, productivity, potential return on investment, and other key feasibility factors. It is anticipated that this review will provide a solid foundation for future research commercialization efforts to sustainably meet the growing demand for Li as the world transitions to clean energy.
Lithium (Li) is a fundamental metal for manufacturing batteries, ceramics, glass, lubricants, and flux powders, and air treatment processes (Zhang et al., 2019)). Figure 1 shows the predominant market end uses of Li in 2021. Before the 1970s, Li was a considerably obscure mineral commodity. However, it has experienced exponential growth in production in recent years. The annual Li mine production by country in 1970, 2000, and 2021 are provided for comparison in Figure 2. Yearly global Li production has expanded from an estimated 3,700 metric tons (MT) in 1970 to over 100,000 MT in 2021, a record high (USGS, 2017; U.S Geological Survey, 2022). This growth can be attributed to Li’s crucial role in the global energy transition. The most prevalent application for Li is in rechargeable lithium-ion batteries for renewable energy storage and electric vehicles. In addition to existing use in Li-ion batteries, Li might also experience growing demand from the hydrogen fuel sector, given that it can be converted to tritium, a potential fuel source for next-generation fuel reactors.
FIGURE 1. Pie chart showing market end uses of lithium as a percentage of global consumption in 2021 (U.S Geological Survey, 2022).
FIGURE 2. A bar chart showing the annual lithium production by country in 1970, 2000, and 2021. Note that the countries labeled with “NP” reported no data that year. Additionally, the United States withheld (W) its production data in 2021 (U.S Geological Survey, 2022; Mohr et al., 2012).
In 2021, international annual electric vehicle sales more than doubled to 6.6 million cars, or 9% of the international car market. This increase in sales is almost triple the global market share in 2019 (IEA, 2022). Summarily, electric vehicles were responsible for the total net growth of global car sales in 2021 (IEA, 2022). Of the 6.6 million cars, 4.7 million (71%) were Battery Electric Vehicles (BEVs), and 1.9 million (29%) were Plug-in Hybrid Electric Vehicles (PHEVs) (Irle, 2022). The typical lithium-ion battery capacities for BEVs and PHEVs are estimated to be 25 and 9 kWh, respectively (Vikström et al., 2013). Furthermore, it is estimated that 160 g of Li can supply one kWh of battery capacity (Kushnir and Sandén, 2012). Therefore, the estimated Li requirement for a BEV and PHEV is four and 1.4 kilograms, respectively. Applying these estimations, the 4.7 million BEVs and 1.9 million PHEVs required roughly 18,800 and 2,700 MT of Li, respectively. This combined mass equates to almost 22% of global Li production in 2021. Accordingly, the global consumption of Li in 2021 was estimated to be 93,000 MT, a 22% increase from 70,000 MT in 2020 (U.S Geological Survey, 2022). By 2030, the global Li demand is expected to exceed 2 Mt, with batteries accounting for 95% of this demand (Azevedo et al., 2018; U.S Geological Survey, 2022). In response, many countries are now prioritizing the development of technologies for low-cost Li extraction to combat impending supply shortages and price hikes. Technologies that enable extraction from low Li+ concentrated aqueous solutions are the leading edge of these development efforts.
Traditionally, Li has been mined from the Li-bearing minerals lepidolite, petalite, and spodumene contained in pegmatite formations. Lepidolite (K(Li, Al)3(Al, Si, Rb)4O10(F, OH)2), contains 3.58% Li content. It is no longer a major mining ore due to its high fluorine content. Petalite (LiAlSi4O10), contains 2.09% Li content. Its high iron content and low thermal expansion rate make it ideal for glass and ceramics, but it is also used for EV and battery storage applications. Of the three minerals, spodumene (LiAl(SiO3)2), has the highest Li content at 3.73% (Vikström et al., 2013). Its treatment chain can be completed in roughly 5 days and is consistently productive (Grosjean et al., 2012). The traditional sulfuric acid method for extracting Li from spodumene ores has a percent yield between 85% and 90% and a percent recovery of 60%–70% (Ellestad and Leute, 1950; Grosjean et al., 2012; Dessemond et al., 2019). However, the pegmatite formations spodumene is contained in are challenging to mine given their hardness and occurrence in difficult-to-reach belt deposits (Grosjean et al., 2012; Kesler et al., 2012). Additionally, the treatment process requires high-energy-demanding furnaces, pit-digging machines, and rock-crushing machines. Ultimately, these machines, the dust produced from excavation, and the concentrated chemicals used for processing cause environmental damage and pose health and safety risks (Aral and Vecchio-Sadus, 2008; Grosjean et al., 2012). These drawbacks to Li recovery from terrestrial mining and the rapid depletion of Li ores have led to the innovative practice of recovering Li from salt lake brines, or Direct Lithium Extraction (DLE). As of 2021, the worldwide Li reserves from ores and brines total an estimated 22 Mt. Salt lake brines account for almost 80% of this total (Zhang et al., 2019). It is important to note that the geographical distribution of these reserves is very uneven (see Figure 3) (U.S Geological Survey, 2022). More than half of the world’s Li reserves are found in the “ABC Triangle,” a phrase coined for the South American countries of Argentina, Bolivia, and Chile (Grosjean et al., 2012). The remaining resources are concentrated in Australia (25%) and China (7%) (U.S Geological Survey, 2022).
FIGURE 3. Pie chart showing lithium reserves by country as a percentage of the total world-wide reserves in 2021 (U.S Geological Survey, 2022).
New development in DLE technologies has garnered renewed interest in seawater extraction. Although the Li+ concentration is low at 0.1–0.2 ppm, seawater contains nearly 230 Gt of Li+, making it a potentially inexhaustible extraction source (Yang et al., 2018). Additionally, seawater’s abundance eliminates many of the geopolitical concerns surrounding land-based reserves because, essentially, any country with access to the ocean has the opportunity to strengthen its Li supply chain with seawater extraction (Månberger and Johansson, 2019; Kalantzakos, 2020). While the Li+ content in salt lake brines and seawater is vast, and extraction from these resources has the potential to be more sustainable than terrestrial mining, many technological challenges must be mitigated before these resources can be considered comprehensive solutions for the impending Li shortage (Graham et al., 2021; Kelly et al., 2021; Chordia et al., 2022). The main challenges facing DLE to date are the extraction technology’s Li+ selectivity, separation efficiency, recovery, and lifetime.
This paper reviews technology used for Li+ extraction from salt lake brine and seawater, or low Li+ concentration aqueous solutions. First, brine and seawater are classified according to their content. Subsequently, key advantages and challenges of the precipitation, solvent extraction, ion sieve adsorption, ion-imprinted membrane (IIM) extraction, and electrochemical extraction technologies are detailed. The Li+ adsorption capacity, selectivity, separation efficiency, recovery, regeneration, cyclical stability, thermal stability, environmental durability, product quality, extraction time, optimal pH value, and specific energy consumption are also highlighted when provided. The adsorption capacity is the maximum amount of Li+ that can be absorbed by the technology. Selectivity is the technology’s ability to exclusively select Li+ or other desired ions over competing ions present in the solution. The separation efficiency is a measure of the quality of Li+ separation from the solution achieved by the technology. It is measured by the ratio of the Li+ concentrate removed from the solution feed stream to the initial Li+ concentration in the solution. Furthermore, the recovery is the amount or percentage of pure Li product obtained after extraction and additional treatment processes, if any. Regeneration refers to the number of times the technology can be regenerated using a treatment process without significant losses in recovery. The cyclical stability indicates the number of times a technology can be reused before there are major losses in recovery. Thermal stability indicates the operating temperature(s) at which the technology achieves optimal performance. Environmental durability refers to the number of times the technology can be reused with minimal physical degradation. The product quality is the percent purity of the Li product recovered. The extraction time is the duration required to remove Li+ and recover the Li product. The pH value is the recommended solution pH for optimal Li+ extraction and recovery. Finally, the specific energy consumption is the total energy used to produce a unit weight of Li product. The review concludes with recommendations for enhancements and future research pathways of technologies for DLE from low Li+ concentration aqueous solutions.
Brines are excessively saline solutions found in continental, geothermal, and oil field deposits. The worldwide distribution of these brine types spans continental basins (58%), geothermal brines (3%), and oil field brines (3%) (USGS, 2017). Geothermal brines are byproducts of geothermal energy production activities. These heated saline deposits can be pumped to the surface for Li+ extraction, but their complex chemistry, high salinity, and high temperature (
Both salt lakes and seawater possess complex concentrations of chlorine (Cl−), sodium (Na+), potassium (K+), magnesium (Mg2+), calcium (Ca2+), copper (Cu2+), nitrate
Salt lake brines can generally be classified into four main types based on their composition: carbonate
The evaporation, purification, and reactive crystallization, or precipitation, Li+ extraction method is credited as the first technology investigated and applied in industrial applications. The Li+ concentration of naturally occurring salt lake brines is too low for cost-effective extraction without a pre-enrichment process (Vikström et al., 2013; Flexer et al., 2018). Consequently, solar energy is used to evaporate, and therefore, concentrate the Li+ in the brine after it is pumped from the salt lake into large evaporation ponds. The optimal conditions for this process are an arid climate, consistent, unidirectional winds, low salt water permeability, and low rainfall. This evaporitic enrichment process takes several months as the brine is cycled continuously through a series of ponds that increase in salt saturation. When lithium chloride (LiCl) concentration in the evaporation pond reaches approximately 6,000 ppm, the brine is pumped to a recovery pond. The ion salts that do not spontaneously precipitate, such as boron, calcium, magnesium, and sulfate, must be removed with chemical treatments. Lime (Ca(OH)2) is added to the brine to remove the Mg2+ as magnesium hydroxide (Mg(OH)2) and remove sulfate as calcium sulfate (CaSO4) via single-replacement and acid-base neutralization reactions, respectively. The remaining brine is treated with sodium carbonate (Na2CO3) to remove residual Ca2+ as CaCO3 through a single-replacement reaction. Additionally, the brine reaches critical supersaturation after Na2CO3 is introduced, and Li2CO3 crystallization begins. The crystal nuclei begin to form and grow as crystal ions spread and deposit on the Li2CO3 nuclei surfaces. The Li2CO3 nuclei grow into precipitated particles that aggregate into larger particles (Zhao et al., 2019). The final product is a chemically stable, odorless, white powder. Typically, the initial Li2CO3 product is dissolved and re-precipitated until battery-grade purity (99.5 wt%) is reached (Flexer et al., 2018). The final product is then used as a precursor for the Li compounds utilized for the cathodes and electrodes of Li-ion batteries. However, Li2CO3 can also be converted into other industrial salts or treated to yield pure Li metal.
This Li+ extraction method is the most conventional and economical method to date, primarily due to its use of solar energy for the Li+ enrichment process. Additionally, the chemicals added for each ion salt precipitation step and the production infrastructure afford low initial investment and operation costs. However, there are significant drawbacks associated with this extraction method. While Li2CO3 extraction from brine has lower life-cycle greenhouse gas (GHG) emissions than ore mining, the initial product quality is much lower (Kelly et al., 2021). Li2CO3 produced from terrestrial extraction achieves an initial purity close to 99% wt. Conversely, additional processing is required to achieve comparable purity with conventional brine extraction, where initial product purity ranges from 50 to 80% wt (Zhang et al., 2019). Furthermore, the chemicals used for precipitation and the waste produced by this process have raised many socio-environmental concerns (Anlauf, 2016; Liu et al., 2019; Dorn et al., 2020). There is a threat of Li2CO3 and sodium carbonate leaching into the environment and contaminating the soil, air, and freshwater supply of surrounding communities (Agusdinata et al., 2018). Similarly, large amounts of waste are produced during precipitation and generally left to accumulate on the margins of the ponds. A salt lake with an annual production rate of 18,000 MT will produce approximately 2 × 107 tons of waste, which translates to a land area of 10 km2 (Flexer et al., 2018). Therefore, practical resource, waste, and land-use management strategies are of utmost priority and should be developed in tandem with Li production expansion efforts. Further investigation into the potential impacts on human health and native biodiversity is also a critical component of expansion efforts.
The economy of traditional Li extraction from low Li+ concentration aqueous solutions is highly dependent on four key factors: 1) land and climate suitability; 2) production life cycle time; 3) the brine’s natural Li+ concentration; and 4) the mass ratio of competing ions to Li+ (i.e., Mg2+/Li+ mass ratio). Producing Li from brine is an intricate process because productivity is driven by environmental factors that are impossible to control and increasingly more difficult to predict due to the disruptive influence of climate change on historical weather patterns. Consequently, a single extraction facility can experience variations in production speed and efficiency throughout the year (Perez de Solay, 2017). This production instability is especially concerning, given that 12–24 months are required to enrich the brine for Li recovery alone. Consequently, traditional Li+ extraction is uneconomical for solutions with concentrations less than 30 ppm. For reference, Salar de Atacama has one of the world’s highest Li+ concentrations (2,100 ppm) and evaporation rates (3,200 mm/year), and the Li+ enrichment process ranges from 12 to 18 months. Finally, the Mg2+/Li+ mass ratio is perhaps the most critical consideration for determining application feasibility. High amounts of Mg2+ slow the evaporation process and prevent LiCl formation, the first step to Li2CO3 production. Additionally, excessive Mg2+ causes precipitant overconsumption, further contributing to precipitation efficiency challenges and increasing operational costs. Therefore, the traditional Li+ extraction method is economically infeasible for aqueous solutions with high Mg2+/Li+ mass ratios (
High Mg2+/Li+ precipitants continue to leverage traditional precipitation extraction’s most advantageous aspects: a solar-powered Li+ enrichment process (optional), low-cost chemical agents, and easy industrialization. Their extraction mechanism is identical: the precipitants are added to the aqueous extraction solution to generate supersaturation via chemical reactions. Once the extraction solution reaches critical supersaturation, the metal ions present (Li+, Na+, K+, Ca2+, Mg2+) can be crystallized in sequence so that the competing metal complexes are removed and a high purity Li complex is the final product. However, unlike traditional precipitants, they have effectively extracted Li+ from high Mg2+/Li+ and low Li+ concentration solutions. Additionally, their selectivity rates are comparable to or higher than the average selectivity rates achieved by traditional precipitants. The main challenges facing high Mg2+/Li+ precipitants are their sensitivity to precipitant dosage (precipitant to target ion molar ratio), pH, temperature, and very high competing ion concentrations. These factors directly impact the technology extraction efficiency, the recovery and quality of the Li products, and potential co-products. Similarly to traditional precipitants, high operational costs stemming from precipitant overconsumption, and pollution from process waste are potential challenges. Therefore, extensive experimentation is required to establish productive to optimal ranges for each precipitant performance factor and substantiate their techno-economic feasibility. Ultimately, their technological advantages combined with the opportunity to co-precipitate additional products for commercial resale indicate that high Mg2+/Li+ precipitants are promising for Li+ extraction from high Mg2+/Li+ mass ratio brines. However, further experimentation is needed to determine the feasibility of solely using these precipitants for Li extraction from seawater. To date, high Mg2+/Li+ precipitants have been paired with ion exchange technologies for seawater extraction (Um and Hirato, 2014). Table 3 provides the aqueous solution, Mg2+/Li+ mass ratio, recovery, thermal stability, products, product quality, extraction time, and optimal pH for various high Mg2+/Li+ precipitants.
TABLE 3. High Mg2+/Li+ precipitant extraction from salt lake brines, simulated brines, and seawater.
The aluminate precipitation method has demonstrated excellent performance in Li+ recovery from high Mg2+/Li+ aqueous solutions in experiments dating back to 1960 (Goodenough, 1960; Goodenough and Stenger, 1961; Kaplan, 1963; Pelly, 1978; Epstein et al., 1981; Isupov et al., 1999; Hamzaoui et al., 2007; Hamzaoui et al., 2008; Yang et al., 2013; Li et al., 2015; Heidari and Momeni, 2017; Liu et al., 2018). Epstein et al. (1981) precipitated Li+ from the dead sea as lithium aluminate (LiAlO2), used a liquid-liquid extraction technique to separate the Li+ from the Al3+. Similarly, Kaplan (1963) recovered Li+ through LiAlO2 precipitation from dead sea brine. Typically, an aluminum salt (AlCl3 ⋅ H2O) and sodium hydroxide (NaOH) are added to the salt lake brines instead of lime and sodium carbonate. The amorphous aluminum hydroxide (Al(OH)3) created by this mixture selectively precipitates Li+. Lithium aluminate precipitate (LiCl.2Al(OH)3H2O) is produced, and the Li+ in the precipitate is expulsed by manipulating the solution pH: the Li+ is released from the precipitate in acidic and alkaline conditions Zhang et al. (2019). Experimental studies with synthetic brine report that the optimal values for Al/Li, mixing time, pH, and temperature are 4.7, 3 h, 7.2, and 25°C, respectively (Hamzaoui et al., 2007; Hamzaoui et al., 2008). The highest Li percent recovery achieved with these parameters is 73%. However, the actual recovery in natural brine systems decreased to 60%. This reduction in Li recovery is attributed to brine impurities, such as boron, and variable environmental conditions (Pauwels et al., 1995). The challenges associated with this particular precipitation method are the sensitivities to Al3+/Li+ ratio, mixing time, and the solution pH at ambient temperatures.
Furthermore, Heidari and Momeni (2017) conducted experimental studies on Li recovery from Urmia lake using lithium aluminate. An aluminum salt, aluminum chloride (AlCl3⋅6H2O), and NaOH were used to co-precipitate Li+ from two Urmia Lake water samples. The first sample had a Li+ concentration of 0.038 ppm and an approximated Mg2+/Li+ mass ratio of 326. The second sample had a Li+ concentration of 0.055 ppm and an approximated Mg2+/Li+ mass ratio of 207. Therefore, both samples are high Mg2+/Li+ and low Li+ concentration aqueous solutions. The first step in the extraction process involved adding and dissolving AlCl3⋅6H2O into the water samples. Next the alkaline reagent, NaOH, was added to increase the pH and form the precipitant, Al(OH)3. The Li+ ions present in the solution were then absorbed into the Al(OH)3. Finally, the Li+ was desorbed from the solid phase using sulfuric acid (H2SO4). The maximum Li recovery from both samples occurred at a pH of 7.5. The sample with the highest Li+ concentration, 0.055 ppm, had a percent recovery of 76.4%, whereas the sample with 0.038 ppm Li+ concentration had a percent recovery of 71%. These Li percentages of recovery are comparable to those achieved by traditional precipitants from salt lakes with Li+ concentrations three to four orders of magnitude higher than the two samples tested. Also, the high Mg2+/Li+ mass ratios did not impact either sample’s Li+ adsorption or desorption process. Therefore, this technology is promising for Li+ extraction from seawater, and other brines with Li+ concentrations less than 30 ppm. The main challenges for Li+ extraction via this precipitant are the sensitivities to ambient temperature, pH, and initial Li+ concentration. Heidari and Momeni (2017) indicate Li+ adsorption is reduced when temperatures exceed 30 °C. Furthermore, the amphoteric properties of the Al(OH)3 surface groups only enhance the Li+ adsorption capacity when the pH is in the 7 to 8 range (Zymon and Kurbiel, 1986). Finally, the efficiency of the Li+ adsorption process improves with increasing Li+ concentration, as seen in the percent recovery of the two samples. This finding suggests that an Li+ pre-concentration step will be required to improve the feasibility of this precipitant for large-scale Li production from aqueous solutions with very high Mg2+/Li+ mass ratios and seawater.
Isupov et al. (1999) used a sorbent synthesized from aluminum hydroxide and the chloride of the double hydroxide of lithium and aluminum (LADH-Cl) to precipitate and extract Li+ from natural brine. The reusable sorbent demonstrated Li percent recovery ranging from 93% to 96% and an LiCl product quality of 5–7 g/l. Paranthaman et al. (2017) developed a similar lithium aluminum layered double hydroxide chloride (Al-LDH) sorbent for Li+ extraction using a three-stage, bench-scale column extraction process. The aluminum Al-LDH (Li:Al ratio 1:3) sorbent selectively precipitated LiCl from geothermal brine with an initial Li+ concentration of 360 ppm. The Mg2+/Li+ ratio of the brine is unreported. In the column extraction process three solutions, the initial brine, intermediate wash (NaCl + LiCl), and final strip solution (purely LiCl), are fed into the column extractor. From there, two computer-operated pinch valves are used to cycle the column extractor through three steps: 1) loading the lithium sorbent with the LiCl present in the brine; 2) washing the sorbent to remove any unwanted ions that are trapped; 3) a final washing of the sorbent to desorb the LiCl ions.
The Al-LDH extraction technology demonstrated an approximated percent recovery of 91% and a high selectivity of Li+ compared to competing ions Na+ and K+ at 47.87 and 212 selectivity, respectively. The only chemical agents required for this process are NaCl and LiCl, and their low cost contributes to the economy of this technology. Additionally, the load-wash-elution cycle does not produce secondary waste, an important consideration for environmental contamination and land use. Although the sorbent composition and column extraction technique could be further optimized to improve selectivity, capacity, and competing ion removal, this novel sorbent technology is a promising solution for Li extraction from aqueous solutions with high competing ion to Li+ ratios.
The high concentrations of Mg2+ present in salt lake brines and seawater have motivated investigations into the potential economic benefits of Mg and Li co-precipitation extraction from aqueous solutions. Mg and its compounds are essential to the global agricultural, insulation, automotive, food, pharmaceutical, chemical industries. The International Magnesium Association estimates global Mg production exceeds 429,000 MT annually, with steady increases attributed to the demand for Mg2+ alloys in the automobile industry (Tran et al., 2013). On average, seawater contains about 1,300 ppm of Mg2+, and the estimated global resource of Mg bearing brines and bitterns is in the billions of tonnes. Therefore, a co-extraction technology that efficiently harvests Li and Mg from these abundant aqueous resources is of high economic value.
Quintero et al. (2020) explored the use of oxalic acid (C2H2O4) for Mg2+ and Ca2+ precipitation before Li+ precipitation. The recovery of these competing divalent ions before Li+ improves the efficiency of Li+ selectivity and produces high-quality calcium oxalate (CaC2O4) and magnesium oxalate (MgC2O4). They achieved a 90% Ca2+ removal rate and a maximum yield of 88% for the solid Li+ and Mg2+ products, lithium carbonate (Li2CO3) and magnesium hydroxide (Mg(OH)2), respectively. The Ca2+ extraction yield was obtained by adding oxalic acid and sodium hydroxide (NaOH) (5 M) to the Li-enriched refined brine and then allowing a 2 h lapse at room temperature. The Oxalic Acid/Ca was added until a molar ratio of 6:1 was achieved. A NaOH/Oxalate molar ratio of 3:3:1 was used to lower the extraction solution pH into a 0–1 range. The Li2CO3/Mg(OH)2 was then co-precipitated by adding 5M NaOH and sodium carbonate (Na2CO3). The Mg2+was precipitated with NaOH, then Na2CO3 was used to precipitate the Li2CO3.
Technologies that remove and co-precipitate competing ions (Mg2+ and Ca2+) from high Mg2+/Li+ and low Li+ concentration aqueous solutions demonstrate high Li+ yield and extraction efficiency rates. Additionally, their co-production of saleable products, such as magnesium hydroxide, present a lucrative opportunity to sustainably supply the industrial demand for these co-products and Li. Overall, they present a more efficient and sustainable crystallization process than what is used in traditional precipitation extraction. The main drawback of this technology is the sensitivity to pH and the concentration of competing ions during the co-precipitation processes. If the concentration of these ions is not controlled, they become impurities that decrease the co-precipitation efficiency and quality of the co-products. More authors have explored the use of oxalic acid to remove or co-precipitate competing ions in high Mg2+/Li+ and low Li+ concentration aqueous solutions. An et al. (2012) used calcium hydroxide and sodium oxalate in a two-step precipitation process to recover
Solvent extraction, also called liquid-liquid extraction (LLE), is a method used to separate compounds according to their relative solubilities into two immiscible liquid phases, an organic phase, and an aqueous phase. An organic phase containing the solvent is added to the aqueous Li solution to form organic Li+ complexes and equilibrate coexisting metals (Na+, Mg2+, Ca2+). The Li+ complexes and some residual impurity metals are transferred to the organic phase. However, most impurity metals remain in the Li+ depleted aqueous solution, or raffinate. The organic phase containing the extracted Li+ complexes is scrubbed to remove the remaining impurities. The scrubbed organic phase is stripped, typically with an acid, to remove the Li+ in a highly concentrated strip liquor. Finally, the Li+ stripped organic phase is regenerated and recycled to the extraction stage (Bang Mo, 1984; Butt et al., 2022). Cation exchange is the driving mechanism for the extraction, scrubbing, and stripping stages, and acid-base neutralization is the driving mechanism for the organic phase regeneration stage (Shi et al., 2018). This extraction process is typically stand-alone and does not require the pre-concentration of Li+ in the aqueous solution. Additionally, solvent extraction can achieve any concentration factor up to the saturation limit compared to other DLE technologies. However, like precipitation, solvent extraction generates high volumes of harmful waste during the scrubbing and stripping stages. Additionally, the corrosive nature of the solvents and process solutions point to equipment and environmental damages under continuous operating conditions. Finally, the most significant barrier to the techno-economic feasibility of solvents for low Li+ concentration solutions is their high cost compared to present-day industrial Li+ precipitants and solvents, which are ineffective for low Li+ concentration solutions. Table 4 provides the aqueous solution, Mg2+/Li+ mass ratio, selectivity, extraction efficiency, recovery, thermal stability, regeneration, Li product, extraction time, and optimal pH value for several solvents. Note that the extraction efficiency is the percentage of the Li+ solute that moves from the brine to the extraction solution.
Several studies have investigated chelating extractants, such as crown ether (CE) and its ether derivative for Li+ extraction. Their polydentate structure encourages Li+ selectivity. Extraction using these ethers follows Pearson’s hard-soft-acid-base (HSAB) principle. The principle asserts that soft acids prefer to bond with soft bases, and hard acids prefer to bond with hard bases. The hard acids possess tiny, highly charged, non-polarizable acceptor atoms. Conversely, softer acids have larger atoms with a lower charge. Also, the bond between the hard acids and bases is dominated by electrostatic interactions, and the bonds between soft acids and bases are covalent. Applying these principles to Li+ extraction, CEs that use ether oxygens, a hard base species, as donor atoms easily bond with hard acid, alkali metal cations such as Li+ (Lowry and Richardson, 1987; Pearson, 1990). Li+ separation efficiency depends on the cavity size of the CE or the CE derivative, especially when competitive ions such as Na+ and Mg2+ are present in the extraction solution. The most Li+ selective CEs are listed in Table 5 (Bartsch et al., 1985).
While the selectivity of CEs is competitive, even for high Mg2+/Li+ ratio solutions, the commercial use of Li+ extraction using CEs has been limited due to the high costs of the ethers and ether derivatives (Hamilton, 1984; Swain, 2016). Additionally, the influence of their underlying extraction mechanisms on the base metal extraction process is not well understood (Swain, 2016). A final consideration is the severely polluting and corrosive nature of the chemical agents used in solvent extraction that ultimately reduce the lifetime of the process equipment. These factors have contributed to the delay in commercializing this solvent extraction technology. However, the development of more economical CEs could bridge this gap. Future developmental efforts should focus on the three critical factors for CE Li extractability: 1) the structure and size of the CE ring; 2) the basicity of the pendent phenolic group (PPG); 3) the geometry between the CE center and the PPG (Katayama et al., 1985).
There are two classes of acidic extractants for liquid-liquid metal extraction: organophosphorus acids and carboxylic acids. Both acids extract Li+ from aqueous solutions by cation exchange (Peppard et al., 1958). This extraction process is facilitated by increasing the aqueous solution pH. Conversely, the Li+ stripping or elution process is triggered by increasing the acidity of the aqueous stripping solution (Xie et al., 2014). To date, acidic solvents have typically been used to extract rare earth and heavy rare earth metals from aqueous solutions, with organophosphorus acids being the more conventional and efficient acid class for extraction (Safarbali et al., 2016). Their characteristically high target ion selectivity and separation efficiency have prompted investigations into their use for aqueous Li+ extraction. However, the best separation and extraction performance has been achieved by a mixture of acidic and solvating extractants (Chen and Wu, 2000). The oxygen atoms in solvating extractants enable the aqueous solution molecules to be incorporated into the Li+ coordination sphere to form an extractable solvated complex (Fuks and Majdan, 2000; Roundhill, 2001). Hano et al. (1992) demonstrated this synergy in a foundational experiment investigating Li recovery from geothermal brine using organophosphorus acid and solvating extractants. Di-2-ethylhexyl-phosphoric acid (D2EHPA) and 2-ethylhexyl-phosphoric acid 2-ethylhexyl ester (MEHPA) were the extractant agents, and tri-n-butylphosphate (TBP) or tri-n-octylphosphine-oxide (TOPO) were the solvating extractants. The geothermal brine samples used in the experiments were hot spring water collected from Yamaga and Hazama, Japan.
The Yamaga water Na+/Li+ and Mg2+/Li+ ratios are ∼301 and ∼4. The Hazama water Na+/Li+ and Mg2+/Li+ ratios are ∼184 and ∼11, respectively. The Hazama water samples are high Mg2+/Li+ and low Li+ concentration aqueous solutions. The percent of Li+ extracted from the Yamaga water samples for D2EHPA and MEHPA were 42.5% and 42.2%, respectively. The percent Li+ extraction from the Hazama water samples for D2EHPa and MEHPA were 52% and 5.2%, respectively. The TOPO additive did not affect extraction behavior. However, the TBP additive increased Li+ extraction in all cases. Li+ extraction percentages for the Yamaga water samples with additive, or D2EHPA + TBP and MEHPA + TBP, were 52.6% and 47.6%, respectively. Similarly, the extraction percentages for the D2EHPA + TBP and MEHPA + TBP Hazama water samples were 88.3% and 11.7%, respectively. D2EHPA and MEHPA demonstrated high selectivity of Li+ ions over Na+ and K+. However, Ca2+ and Mg2+ had a greater affinity for the acidic extractants and demonstrated extraction percentages greater than 91% (excluding Ca2+) from the MEHPA and MEHPA + TBP Hazama water samples. D2EHPA + TBP demonstrated the highest extraction performance overall. In a similar study, (Jang et al., 2017), used D2EHPA and TBP to recover Li+ from oilfield brine in two phases. In the first phase, 94.4% of Ca2+ and Mg2+ ions were removed by D2EHPA. In the second phase, D2EHPA and TBP recovered Li at a 41.2% extraction rate. The total amount of Li recovered was 30.8%.
The results from these experiments indicate that combining acidic extractants D2EHPA and MEHPA and neutral extractants (TBP) is ideal for Li+ extraction from aqueous solutions with minimal divalent ion (Mg2+ and Ca2+) concentrations such as the Salar de Atacama and Lake Zabuye brines. The use of these solvents for Li extraction from high Mg2+/Li+ and Na+/Li+ seawater is infeasible because Li+ is too dilute. However, these extractants could be leveraged as pre-separation agents that remove the competing divalent ions (Mg2+ and Ca2+) before an additional selectivity process is used to extract the remaining Li+ ions from solutions with exorbitant competing ion to Li+ mass ratios. Many other authors have investigated other organophosphoric extractants and TBP for aqueous Li+ extraction in recent years (Torrejos et al., 2015; Nguyen and Lee, 2018; Su et al., 2022).
Ionic Liquids (ILs) are organic compounds comprised of ions with melting points at or below room temperature (25°C). They have many advantageous solvent properties, including high thermal stability, selectivity, and separation efficiency, but marginal volatility (Mori et al., 2015; Patil et al., 2015; Rama et al., 2015). These properties have garnered the interest of researchers working to develop augmented solvents for metal ion extraction. Traditionally, conventional molecular extractants have been combined with ILs that contain fluorinated anions because their immiscible properties facilitate the formation of hydrophobic complexes with the metal ions for extraction. However, extraction with fluorinated ILs leads to hydrofluoric acid contamination, limiting the reuse of ILs for continuous extraction.
Shi et al. (2017) investigated the use of two non-fluorinated ionic liquids (ILs), tetrabutylammonium bis(2-ethylhexyl)-phosphate ([N4444][DEHP]) and tetraoctylammonium bis(2-ethlyhexyl)-phosphate ([N8888]) for aqueous Li+ extraction. These novel ILs, or functionalized ionic liquids (FILs), were prepared via ion exchange and neutralizing reactions. The Li+ extraction performance of the DEHP-type FILs was tested using a multi-metal-ion solution that contained Li+, Na+, K+, Rb+, and Cs+. Both FILs preferred the alkali metal with the smallest ionic radius and the highest surface charge density. Therefore, Li+ had the leading electrostatic interactions and formed the most stable species with the FILs’ [DEHP]− anions. Additionally, the initial Li+ stripping percentage of 90% increased with the number of stripping stages, and complete Li+ stripping occurred after four stages with minimal reduction in the FILs’ extraction efficiency. Overall, the [N4444][DEHP] FILs demonstrated higher extraction efficiencies than [N8888][DEHP] at 92% and 83%, respectively, due to the increased steric hindrance associated with longer alkyl chains. Bai et al. (2022) investigated the synergy of a phosphate-based ionic liquid ([N1888][P507]) and a neutral extractant + acidic ion compound system (TBP + FeCl3) for Li+ extraction from high Mg2+/Li+ brine. At optimal extraction parameters, 97% of the Li+ solute could be stripped from the solvent. Additionally, an initial extraction efficiency of 61% was achieved after the first extraction-stripping-extraction cycle and rose above 70% for the five remaining cycles.
[N4444][DEHP] and [N8888][DEHP] FILs show promising continuous Li extraction efficiency from aqueous solutions containing competing monovalent ions (Na+ and K+). Both FILs outperformed DEHPA, a popular acidic extractant (Shi et al., 2017). However, further investigation into the performance of these FILs in the presence of competing divalent ions such as Mg2+ is needed to determine the feasibility of extraction from brines, seawater, and any other high Mg2+/Li+, low Li+ concentration solutions. Conversely, the novel (([N1888][P507]) + TBP + FeCl3) extractant system demonstrated promising Li+ separation and extraction from high Mg2+/Li+ salt lake brine. Unfortunately, there is a potential trade-off between separation and extraction efficiency: increasing the concentration of ([N1888][P507]) increases Li+ separation efficiency but causes slight reductions in the extraction efficiency. Further experimentation with extraction solutions similar to those of salt lake brines or seawater would provide more insight into the feasibility of ILs for these applications. In recent years, more authors have studied the performance of other FILs in either salt lake brines or high Mg2+/Li+ aqueous solutions (Gao et al., 2016; Wang et al., 2018; Zante et al., 2019; Bai et al., 2020; Bai et al., 2021; Olea et al., 2022).
Ion sieve adsorbents are inorganic materials containing template ions that are introduced into an inorganic compound by redox or an ion exchange reaction. A heating process is then used to obtain the compound oxide. After the compound oxide is formed, an eluent is used to remove the target ions from their crystal positions while retaining the vacancy sites on the crystal. The resulting sieve extracts Li+ via two adsorption mechanisms: physisorption driven by electrostatic interaction and chemical adsorption via ion exchange (Xu et al., 2019). Hence, the target ions can only be obtained in these crystal sites if the ionic radii are similar to the ionic radii of the template ion. Additionally, the material tends to have a higher selectivity for ions that form the best crystal configuration. As a result, the template ions create a reliable selection effect, allowing for the adsorption of target ions even if multiple ions are present in the solution. This process is known as the “ion-sieve effect” (Weng et al., 2020).
One critical techno-economic challenge facing ion sieves is their tendency to disintegrate during adsorption/desorption cycling. This loss is caused by biofouling and the hydrochloric acid treatments used for the Li+ desorption process. Both sources of loss reduce the adsorption capacity, selectivity, and separation efficiency of the ion sieve during cycling. Consequently, operational costs are driven up because more sieve is needed to compensate for these losses, and Li-ion sieve synthesis is expensive (Hu et al., 2022). Additionally, hydrochloric acid is generally the recovery solution used for sieves and its caustic nature raises concerns for environmental pollution. A final drawback is the extraction lead time. Typically, extraction using ion sieves takes days to complete. (Chung et al., 2008; Chitrakar et al., 2014).
Despite the drawbacks, ion sieves demonstrate high Li+ adsorption, selectivity, and cycle stability. Also, the sieves can be regenerated and reused, albeit with some loss after each cycle. More importantly, the adsorption capacity is not impacted by the presence of competing ions, such as Na+, K+, Na2+, and Mg2+. The passive nature of the extraction process is conducive to low initial investment and operation costs. Lastly, in addition to superior selectivity and separation efficiency, Li-ion sieves demonstrate higher theoretical uptake capacity. This feature is particularly desirable for Li+ extraction from high Mg2+/Li+ solutions with Li+ concentrations below 30 ppm.
Manganese dioxide exists in many different crystalline structures: α-MnO2, β-MnO2, γ-MnO2, and λ-MnO2. While each structure demonstrates a strong affinity for Li+, the spinel-type hydrous manganese oxides, λ-MnO2, are the top performers (Voinov, 1982; Chitrakar et al., 2000a; Chitrakar et al., 2000b; Liu et al., 2019). This top performance is attributed to the spinel structure of the λ-MnO2 ion sieve precursor, Li+ manganese oxide (LiMn2O4). The template spinel formula is (AB2O4), where the divalent cations, A, occupy eight tetrahedral voids, the trivalent ions, B, occupy 16 octahedral voids, and the oxygen anions, O, occupy the 32 face-centered cube lattice points (Hill et al., 1979). Therefore, the ratio of A: B: O is 8: 16: 32, which can be reduced to 1: 2: 4, or the conventional spinel formula.
As it relates to spinel LiMn2O4, the Li+ cations occupy the eight tetrahedral voids, manganese (III) and manganese (IV) occupy the 16 octahedral voids, and the oxygen anions occupy the 32 face-centered cube lattice points. The manganese ions have octahedral coordination with the oxygen anions, and the MnO6 octahedra share edges that create a three-dimensional host for the Li+ guest cations. Furthermore, the Li+ tetrahedral voids are located the furthest away from the manganese octahedral voids of the interstitial tetrahedra and octahedra. Consequently, each Li+ tetrahedron face is matched with an octahedral void (Xu et al., 2016). This combination of structural features inhibits easy Li-ion exchange without changing crystalline structure during reversible Li+ intercalation. Additionally, the Mn-O framework remains stable after desorption/regeneration with an acidic treatment (Wang et al., 2008; Wang et al., 2014).
The LiMn2O4 precursor has low Li+ adsorption capacity and stability. The maximum adsorption capacities achieved from seawater and salt lake brine are 1.1 and 30.9 mg/g, respectively (Chitrakar et al., 2000b; Wang et al., 2014). However, the stoichiometric proportion between Li: Mn can be altered to increase the theoretical Li+ capacity of LMO-type LISs (Xu et al., 2016). Chitrakar et al. (2000b) used a hydrothermal method to synthesize Li1.33Mn1.67O4 and cubic Li1.67Mn1.67O4, which achieved Li+ adsorption capacities of 25 and 37 mg/g from seawater and salt lake brine, respectively. The highest recorded Li+ adsorption capacities for Li1.33Mn1.67O4 from seawater and salt lake brine are 54.7 and 63 mg/g, respectively (Zandevakili et al., 2014; Ryu et al., 2016). Additionally, the highest recorded Li+ adsorption capacities for Li1.67Mn1.67O4, from seawater and salt lake brine are 40 and 28 mg/g, respectively (Chitrakar et al., 2001; Xiao et al., 2013). Currently, Li1.67Mn1.67O4 has the highest theoretical adsorption capacity at 72.8 mg/g. However, Li1.67Mn1.67O4 requires a two-step preparation process compared to the one-step required for the other precursors. Consequently, LiMn2O4 and Li1.33Mn1.67O4 are more economical for industrial Li+ extraction applications at this time. Table 6 provides the adsorption capacity, cyclical stability, thermal stability, environmental durability, extraction time, and optimal pH of various LMO-type LISs used for Li+ extraction from salt lake brines, simulated brines, and seawater.
The main challenges facing LMO-type LISs for large-scale, industrial Li+ extraction applications are the residual impacts of the precursor acid treatments. These acid treatments reduce the LMO-type adsorbent stability, adsorption capacity, and durability and cause environmental pollution. While the acid effectively removes most of the Li+ without disrupting the precursor crystalline structure, it simultaneously causes manganese to dissolve with each successive treatment (Shen and Clearfield, 1986; Wang et al., 2009; Xiao J. L. et al., 2015; Gao et al., 2018; Weng et al., 2020). The dissolution of the Mn is attributed to the Jahn Teller effect induced by trivalent manganese (Mn3+). The octahedral MnO6 structure becomes increasingly distorted, reducing the stability, adsorbent capacity, and durability, and causing considerable water pollution (Jin et al., 2018; Weng et al., 2020). To combat this dissolution phenomenon, many authors have experimented with replacing the Mn3+ with: divalent cobalt (Co2+), nickel (Ni2+), and magnesium (Mg2+); trivalent chromium (Cr3+), aluminum (Al3+, and iron (Fe3+); and, other rare-earth ions (Malyovanyi et al., 2003; Ein-Eli et al., 2005; Eftekhari et al., 2006; Wu et al., 2007; Iqbal and Ahmad, 2008; Amaral et al., 2010; Sakunthala et al., 2010; Wu et al., 2010; Helan et al., 2011; Xu et al., 2011; Xu et al., 2016). LMO-type precursors doped with Fe3+, antimony Sb(v), and Al3+ demonstrated the highest Li+ extraction capacity with minimal Mn dissolution. However, ascertaining the optimal molar ratio between the doping ions and Mn is critical for achieving a high Li+ adsorption capacity. Further investigation is needed into improving the cyclical stability and practical ion exchange capacity of Li-Mn-O precursors for large-scale Li production.
At present, there are two classifications for LTO-type LISs: layered H2TiO3 and spinel H4Ti5O12. The structure of H2TiO3 is attributed to the layered structure of the Li2TiO3 precursor that is synthesized to create the LIS. Similarly, the spinel structure of H4Ti5O12 is derived from the spinel structure of its precursor, Li4Ti5O12. Compared to LMO-type LISs, LTO-type LISs demonstrate high adsorption capacities, with marginal Ti loss. The main advantage of these LISs is that they are more ecologically friendly because titanium ions are environmentally benign and easy to remove from liquids (Xu et al., 2016; Gopinath et al., 2020). Unlike Mn, the Ti valence ions remain stable during permeation and adsorption. Consequently, LTO-type LISs demonstrate higher theoretical adsorption capacity and better recyclability for continuous extraction (Marthi et al., 2021). Additionally, the Ti-O bonds present in Li4Ti5O12 provide anti-acidic properties: an especially compelling feature for extraction from seawater and salt lake brines. The main drawback of LTO-type LISs is that they demonstrate slower Li+ adsorption rates than LMO-type LISs (Chitrakar et al., 2014). Table 7 provides the adsorption capacity, cyclical stability, thermal stability, environmental durability, extraction time, and optimal pH of various LTO-type LISs used for Li+ extraction from salt lake brines, simulated brines, and seawater.
The crystal structure of Li2TiO3 can be represented as a cubic close packing of oxygen atoms with metal atoms placed in the octahedral voids. Li+ and Ti4+ form two layers. The first layer is solely composed of Li atoms, and the second is composed of 2/3 Ti atoms and 1/3 Li atoms. The crystal structure is formed by successive stacks of oxygen, lithium, and titanium/lithium layers (e.g., O/Li-Ti/O/Li/O) that conform to the C2/c space group symmetry (Watanabe et al., 2020). This crystal formation of Li2TiO3, also known as monoclinic β-phase Li2TiO3, achieves nearly complete Li extraction (100%) to form monoclinic H2TiO3 when treated with acid at comparatively low temperatures (700°C). Two other phases of Li2TiO3 exist, α-phase and γ-phase, but the β-phase is the most promising for aqueous Li extraction. The α-phase has lower thermal stability and will transform into β-phase when exposed to temperatures above 300°C. Alternatively, γ-phase only achieves 50% Li+ extraction (Chitrakar et al., 2014).
Chitrakar et al. (2014) investigated the Li+ ion exchange reaction of H2TiO3 in brine collected from Salar de Uyuni, Bolivia. H2TiO3 demonstrated initial adsorption of 26 mg/g within 1 h and reached equilibrium after 24 h. A Li+ adsorptive capacity of 32 mg/g was achieved, reaching equilibrium after 8 h. The high concentrations of competing monovalent (Na+ and K+) and divalent (Mg2+ and Ca2+) ions present in the brine did not impact the Li+ selectivity. Finally, after elution with an HCl solution, H2TiO3 demonstrated a Li+ adsorptive capacity of 31.4 mg/g, 98% of the initial capacity reported. Zhang et al. (2016) prepared H2TiO3 using a sol-gel process and tested its Li+ adsorption performance from LiOH and LiCl + NaOH solutions. The maximum Li+ adsorption capacities from the LiOH and LiCl + NaOH solutions were 27.4 and 24.1 mg/g, respectively. They found that alkaline pH values and higher initial Li+ concentrations yield higher adsorption capacities.
While the theoretical adsorption capacity of H2TiO3 LISs is higher than most LMO-type LISs, the practical adsorption capacity demonstrated after recovery from brine or seawater is often lower (Dai et al., 2021). Authors have explored the use of doping to potentially increase the adsorption capacity of LISs (Chitrakar et al., 2014; Wang et al., 2019; Qian et al., 2021a; Qian et al., 2021b). Dai et al. (2021) tested the adsorption performance of Al-doped H2TiO3 using a LiCl solution. A maximum adsorption capacity of 32.1 mg/g was achieved, with the adsorption capacity remaining at 29.3 mg/g after five HCl elution cycles. The undoped H2TiO3 achieved a maximum of 29.73 mg/g. Although there was no major improvement in adsorption capacity, the Al-doped H2TiO3 demonstrated favorable adsorption selectivity and solubility resistance. Additionally, the dissolution of Ti after multiple regenerations was marginal (2.53%). Further investigation into doping materials and other capacity-increasing processes is recommended to improve the feasibility of H2TiO3 LISs for Li+ extraction from high Mg2+/Li+ and low Li+ concentration aqueous solutions. The chemical stability, cyclical stability, and eco-friendliness of H2TiO3 LISs signal their potential to surpass LMO-type LISs if their adsorption capacity is significantly improved.
In the Li4Ti5O12 spinel structure, Ti atoms occupy 5/6 of the 16 days octahedral voids, Li atoms occupy the remaining 16 days octahedral voids, and oxygen atoms occupy the 32e voids (Ohzuku et al., 1995). The resulting [Li1/3Ti5/3]16dO4 framework features face shared tetrahedral and octahedral interstitial Li-ion positions in the lattice that create three-dimensional connections for Li-ion migration. In addition to creating stronger Ti-O bonds, this spinel structure enables easy migration of Li+ ions for recovery and elution with minimal Ti dissolution (Ouyang et al., 2007). Consequently, H4Ti5O12 LISs have higher Li+ capacity and greater cyclical stability than LMO-type LISs (Xu et al., 2016). Furthermore, a preliminary study of Li4Ti5O12 for Li+ recovery from Salar de Atacama brine and seawater revealed that Li4Ti5O12 has high Li+ selectivity for aqueous solutions with high concentrations of H and Na+. Consequently, Li4Ti5O12 is predicted to be one of the most promising LIS precursors for large-scale Li+ extraction from brine and seawater (Snydacker et al., 2018).
Gu et al. (2016) studied the ion exchange properties and selectivity of Li4Ti5O12 for Li recovery from a LiOH solution. Li4Ti5O12 was prepared by a solid-state reaction of Li2CO3 and TiO2 then treated with nitric acid to form the H4Ti5O12 LIS. The LISs demonstrated excellent Li+ selectivity of 145.7 ml/g, with only a moderate reduction of 5.5% after three recovery/elution cycles. Wei et al. (2020) synthesized H4Ti5O12 nanofibers (P-HTO-NF) for Li recovery from simulated brine water (Li+ 40 mg/L, Na+ 241 mg/L, K+ 443 mg/L, Mg2+ 501 mg/L, Ca2+ 535 mg/L). The P-HTO-NF demonstrated an adsorption capacity of 59.1 mg/g, which is 93% of the theoretical capacity. Adsorption equilibrium occurred within 30 min. Also, the equilibrium distribution coefficient for Li+ was two orders of magnitude higher than the coefficients of the competing ions, indicating an extraordinary Li+ selectivity. Finally, the LIS demonstrated excellent cyclical stability, with capacity remaining at 86.5% after six cycles. Similarly, Zhao B. et al. (2020) explored using H4Ti5O12 sheets in place of the traditional powder adsorbent to recover Li from Lagoco Salt Lake samples and simulated brine. While the adsorption capacity was not as competitive at 21.57 mg/g, 96.84% of the initial adsorption capacity was retained after four cycles.
H4Ti5O12 LISs have demonstrated superior Li+ selectivity, adsorption capacity, chemical stability, and cyclical stability after multiple adsorption/elution cycles from high Mg2+/Li+ and low Li+ concentration aqueous solutions. The main challenge facing the commercialization of H4Ti5O12 LISs is their novelty. Few experiments have explored the performance of this sieve in traditional powder form, and the limited studies of alternative morphologies have remained at the bench scale. Further performance testing of H4Ti5O12 LISs for recovery from high Mg2+/Li+ and low Li+ concentration aqueous solutions is needed.
Ion-imprinted membranes (IIMs) are the combined product of membrane separation and ion-imprinting techniques. Membrane separation is a highly efficient technique that utilizes pores to filter and selective permeability to separate substances in aqueous solutions (Malliga et al., 2020). These aqueous solutions are driven through the membrane by a concentration, pressure, or potential gradient. Furthermore, ion-imprinting is a bio-inspired technique that mimics the “lock and key” interaction between natural receptors and ligands (Lu et al., 2019). During the ion imprinting process, polymeric matrices are loaded with artificial ionic recognition sites complementary to the template ion’s size and shape (Ertürk and Mattiasson, 2017). Protonation is then used to remove the template ions, leaving the recognition sites open for target ion adsorption. In summary, IIMs leverage the functionality provided by both technologies and can selectively separate and detect target ions via ion-selective recognition (Lu et al., 2019). Additionally, these membranes can be modified with interlayers or imprinted with nanomaterials that prevent membrane fouling, a major challenge for all membrane extraction technologies (He et al., 2022; Sun et al., 2022). Similarly, the antifouling properties suggest that the standard feed solution pretreatment required for most membrane technologies may not be required for IIMs. Li-IIMs’ high separation efficiency, selectivity, low energy consumption, easy operation, and unique antifouling properties have prompted recent investigations into its feasibility for Li+ extraction from low Li+ aqueous solutions. Table 8 provides the selectivity, rebinding capacity, thermal stability, regeneration, cyclical stability, specific energy consumption, extraction time, and optimal pH of various IIMs used for Li+ extraction from simulated brines. Note that the rebinding capacity is the degree to which the Li-ions in the aqueous solution can bind, detach, and rebind to the IIMs Li+ recognition sites.
The most significant challenges facing the commercialization of IIMs for industrial scale, aqueous Li+ extraction are pH sensitivity, temperature dependence, extraction time, and the ratio of template ions, ligands, and functional monomers (Lu et al., 2019). The pH value is generally the determining factor for IIM ion selectivity. When the pH value is too low, protons compete with target ions for binding sites, decreasing the membrane’s adsorption capacity. Increasing the pH value can reduce this competition. Ultimately, the pH value can be adjusted to trigger Li+ adsorption/desorption and, therefore, potential membrane regeneration for continuous extraction. However, extensive experimentation is required to identify the pH values that optimize Li+ adsorption/desorption rates without destroying the IIMs ion recognition sites. The optimal pH value varies across IIM technologies. Furthermore, IIMs demonstrate enhanced adsorption capacities at higher temperatures. Consequently, passive Li+ extraction from seawater and salt brines with cooler temperatures or extraction during winter months may be economically infeasible. Similar to the pH value, additional experimentation is required to identify an extraction time that maximizes recovery without damaging the IIMs. Extended elution periods do not guarantee higher percent recovery. Finally, the ratio of templates to ligands to functional monomers dictates the number of effective binding sites on the membrane. Therefore, research that identifies the optimal ratio of templates to ligands to functional monomers, which varies according to the materials used to prepare the IIMs, is critical to adsorption capacity and overall performance. Addressing these performance challenges will significantly improve the techno-economic feasibility of Li-IIMs, especially compared to other membrane extraction technologies that are subject to fouling and require pretreated extraction solutions.
Lu et al. (2018) developed and tested High-selective Li-Ion-Imprinted Membranes (Li-IIMs) with enhanced hydrophilicity and stability for aqueous Li+ extraction. Polyether sulfone membranes (PMs) were selected for their high porosity, high-pressure resistance, and high stability. PMs have also demonstrated satisfactory performance in other ion separation experiments (Maheswari et al., 2012; Mortaheb et al., 2014). Synthetic polydopamine (PDA) layers were synthesized on the surface of the PMs to enhance interfacial adhesion for the attachment of the ion-imprinted polymers. Additionally, silicon dioxide nanoparticles (SiO2) were added to the PMs surface to enhance their hydrophilicity and stability. Finally, 12-crown-4 ether and Li+ ions were imprinted on the PMs’ surfaces to create the adsorption cavities and ion recognition sites, respectively. The Li-IIMs demonstrated high relative selectivity with coefficients of 1.85 and 2.07 for Li+/Na+ and Li+/K+, respectively. The permselectivity (separation efficiency) factors were also high, with coefficients of 7.39 and 9.86 for Na+/Li+ and K+/Li+, respectively. The rebinding (adsorption) capacity reached a maximum of 90.3% of initial binding after five cycles of adsorption/desorption with a slight decline to 88.1% after ten cycles.
While the Li-IIMs demonstrated excellent performance, experiments with aqueous solutions that more closely resemble the ionic concentration of salt lake brine and seawater should be investigated. Even salt lakes with higher Li+ concentrations, like Salar de Atacama (2,100 ppm), have Na+/Li+ and K+/Li+ ratios greater than 10:1, as compared to the 1:1 concentration used in the Lu et al. (2018) experiments. In 2021, Ding et al. (2022) developed and tested a novel high-selective ion imprinted polymer (sans membrane) for Li+ extraction lake Zabuye brine samples. The technology achieved a maximum adsorption capacity of 1.1 mg/g. While this is promising for green Li+ extraction from carbonate type, low Mg2+/Li+ brines, experiments that investigate the performance of these ion-imprinted technologies in high Mg2+/Li+ aqueous solutions are needed.
Yu et al. (2020) investigated the use of polydimethylsiloxane-polydopamine (PDMS-PDA) Li-IIMs for rapid, high-efficiency recovery of Li from seawater. A powerfully adhesive PDA layer with numerous functional groups was synthesized on the PDMS membrane surface via the self-polymerization of dopamine to improve hydrophilicity. Carboxyl groups were then grafted onto the PDA functionalized substrate per the hydrolysis of succinic anhydride. The carboxyl-modified PDMS membranes were further modified to construct ester-modified membranes. The calix [4] arene ligand and Li-ions were used to create the absorption cavities and ion recognition sites, respectively. Finally, EDTA removed the template Li-ions from the prepared Li-IIMs.
The PDMS-PDA Li-IIMs demonstrated high thermal stability, with their rebinding capacity decreasing marginally with increasing temperatures. Similarly, the modified membranes were stable in acidic and alkaline conditions. However, the pH significantly impacted rebinding capacity; a pH of 3.0 was identified as the optimal value. Furthermore, a Li+ rebinding capacity of 51 mg/g was achieved. The PDMS-PDA Li-IIMS demonstrated high relative selectivity with coefficients of 1.71, 4.56, and 3.80 for Na+/Li+, K+/Li+, and Rb+/Li+, respectively. The permselectivity factors for Na+, K+, and Rb+ were approximately 2.52, 2.8, and 3.03, respectively. Finally, the PDMS-PDA Li-IIMS showed high adsorption/desorption cycle durability. Four successive regeneration cycles were completed over 10 days, and the rebinding capacities remained almost unchanged.
PDMS-PDA Li-IIMs demonstrated excellent performance overall and appear to be a viable technology for Li+ extraction from seawater. However, similar to the High-selective Li-IIMs developed by (Lu et al., 2018), investigations with aqueous solutions that simulate the ionic concentrations in seawater are recommended. Also, the cost and specific energy consumption implications for the stirring required to elute Li+ on an industrial scale should be further explored to determine the techno-economic feasibility of this technology.
Electrochemical Li capturing systems (ELiCSs) use electricity to drive ion-separation processes for Li+ extraction. There is a proportional relationship between the total charge storage of the systems electrode and the amount of Li+ extracted from an aqueous feed solution. The basic configuration of an ELiCS consists of an external power supply, electrodes, and an aqueous electrolyte, in this case, brine or seawater (Soffer and Folman, 1972; Kim et al., 2018; Yoon et al., 2019). Electrochemical technologies are particularly interesting for extraction from high Mg2+/Li+ and low Li+ concentrations solutions because they are environmentally sustainable and have demonstrated excellent recovery capacities, scalability, cycling efficiency, reversibility, and selectivity (Hoshino, 2013a; Lee et al., 2013; Kim et al., 2015; Yoon et al., 2019; Zhang et al., 2019; Zhao et al., 2020b; Srimuk et al., 2020). Additionally, electrochemical technologies can easily integrate energy recovery techniques that utilize the salinity gradient of the aqueous feed solutions to generate energy Zhang X. et al. (2021). Their characteristic high extraction efficiency and low environmental impact suggest that ELiCSs are more techno-economically feasible for Li+ extraction from low Li+ concentration solution than precipitants or solvents. However, the main disadvantages that must be addressed are their potentially high energy consumption due to process inefficiencies and high material costs Zhang Y. et al. (2021).
ELiCSs generally belong to one of three categories: battery-based (BB), membrane enhanced battery-based (MEBB), or electro-membrane-based (EMB) (Zavahir et al., 2021). BB ELiCSs use at least one faradic electrode to capture Li+ from aqueous solutions. The faradic electrode(s) capture Li-ions via conversion reaction or intercalation over the bulk of the electrode’s materials. They have greater storage capacity, Li+ selectivity, and capacitance but slower removal rates than non-faradic (capacitive) electrodes (Patrice et al., 2014; Yoon et al., 2019). The MEBB ELiCSs augment the battery-based configuration with an anion exchange membrane (AEM) for Li recovery. In the rocking chair configuration, the AEM splits the electrochemical cell into a cathode and an anode chamber that contain one Li+ intercalating electrode each. In the redox configuration, there is one intercalating electrode and one redox couple electrode. Continuous Li recovery is achieved by swapping the positions of the Li+ “capture” and “release” electrodes. Finally, the EMB, or electrodialysis configurations, have a series of AEM and cation exchange membranes (CEM) sandwiched between two faradic electrodes. Electric potential drives the Li+ through the CEMs towards concentrating compartments (Zavahir et al., 2021). Further information about the performance, advantages, and challenges of prominent ELICSs is provided in subsequent sections.
The electrochemically switched ion exchange system (ESIX), first proposed by the Pacific Northwest National Laboratory, is a battery-based ELiCS (when employed for Li capture). In the ESIX process, an electroactive ion exchange film is deposited onto a high surface area electrode. The redox reactions that drive ion uptake and elution are directly controlled by adjusting the electric potential of the film. A cathodic potential can be applied to intercalate Li+ into the film for Li recovery from an aqueous solution. This intercalation is driven by the film’s need to maintain charge neutrality. Conversely, when an anodic potential is applied, the film is oxidized, and Li is released from the film (Sukamto et al., 1998). Essentially, the ESIX combines electrochemistry and ion exchange to provide a Li recovery process with high selectivity and reversibility. Also, the ESIX utilizes a faradic and a capacitive electrode, the combined benefits of which bridge the performance gaps in conventional battery and capacitor-based recovery systems.
Adjustments to the conventional ESIX electrode configuration must be made to circumvent the mass transport challenges associated with Li recovery from high Mg2+/Li+ and low Li+ concentration aqueous solutions. An array of smaller electrodes with higher surface areas arranged into working and counter electrode pairs can be employed for recovery instead of a large, singular electrode (Joo et al., 2020; Zavahir et al., 2021). Additionally, keeping the volume of the recovered solution low is mandatory for obtaining a high Li-concentrated final product (Joo et al., 2020; Zavahir et al., 2021). The Li+ selectivity of the ESIX depends on the selectivity of the electrode materials. Several working and counter electrode materials have been tested to identify the best candidates for Li recovery from low concentration solutions: λ-MnO2/Pt (Kanoh et al., 1991; Kanoh et al., 1993; Kim et al., 2019; Liu et al., 2019); λ-MnO2/Ag (Lee et al., 2013; Xu et al., 2018; Kim et al., 2019; Joo et al., 2020)); λ-MnO2-activated carbon (AC) (Kim et al., 2015); λ-MnO2/NiHCF (Trócoli et al., 2017); λ-MnO2/LiMn2O4 (Liu et al., 2019); LMO/Boron Doped Diamond (BDD) (Kim et al., 2018); LMO/Polypyrrole (Ppy) (Marchini et al., 2016; Missoni et al., 2016); LMO/Ppy/Al2O3 (Zhao et al., 2020c); LiFePO4/Ag (Trócoli et al., 2014); and, FePO4/NiHCF (Trócoli et al., 2015). When applied for Li recovery from simulated brine, natural brines, and multi-ion solutions, the specific energy consumption for these electrode variations ranged from 1.4 kWh/kmol to 18.5 kWh/kmol. The AC counter electrode demonstrated a high Li recovery of 14.4 mg/g for a 25 min cycle, so it is recommended for all ESIX systems (Zhao et al., 2020d; Zavahir et al., 2021). Furthermore, the λ-MnO2 and LMO working electrodes demonstrate the highest adsorption capacities at 10 mg/g and 30 mg/g, respectively. Table 9 provides the selectivity, current efficiency, regeneration, adsorption capacity, recovery, specific energy consumption, product quality and extraction time of various ESIX working/counter electrode materials used for Li+ extraction from salt lake brines, simulated brines, and wastewater. Note that the current efficiency is a measure of how efficiently the electrodes transfer the charges driving the electrochemical extraction of Li+.
A major challenge facing ESIX for industrial operation is the flushing process needed to exchange the source solution for the recovery solution. Pure water, a precious resource, is required for flushing to prevent cross-contamination of the two solutions. Consequently, this process poses a considerable threat to process efficiency and sustainability. Furthermore, this batch operation is less efficient than other continuous mode technologies, such as electrodialysis (Zavahir et al., 2021). Additionally, the reported energy consumption for ESIX can be misleading because it is typically calculated using metrics from the first cycle only, which results in underestimated projections for total energy consumption over many cycles. Finally, as mentioned previously, maintaining a low recovery solution is critical to the quality of the Li recovered. At the bench level, recovery solutions at the μ scale require around five enrichment cycles. Therefore, the solution enrichment process at the commercial level can be expected to exceed 1,000 cycles (Zavahir et al., 2021). Further investigation into the practical energy consumption and sustainability of ESIX for Li recovery from brine and seawater is needed. A special focus on the solution flushing process and finding an alternative for pure water is recommended. In this vein, Trócoli et al. (2017) have developed a promising ion-pumping process that employs a λ-MnO2/NiHCF working/counter electrodes for Li+ recovery. No chemical reactants are required, the electrodes are recyclable, and most importantly, only a small volume of water is required.
Electrodialysis (ED) is an electrochemical membrane separation process that utilizes an ion-selective membrane and an electric potential gradient for ion separation from aqueous solutions(Gurreri et al., 2020). A typical electrodialysis cell comprises an alternating series of AEMs and CEMs between a cathode and an anode (Gmar and Chagnes, 2019). In the electrodialysis process for Li+ extraction, electric force drives Li+ ions in the feed solution from the positive side of the cell (cathode) to the negative side (anode) through an ion Li+ selective membrane. As a result, Li+ is concentrated on one side of the cell. Additional treatments are required to obtain the metallic or solid Li compounds dissolved in the Li+ enriched water. Similarly to other membrane technologies, ED systems require the feed solution to be pretreated so that Ca2+, Mg2+, and other metals that cause membrane fouling can be removed prior to Li+ extraction (Wang et al., 2022). However, compared to other membrane technologies such as nanofiltration, ED systems have higher recovery rates, lower energy consumption, and higher Li+/Mg2+ separation factors (Gmar and Chagnes, 2019).
ED systems are classified according to the attributes of their ion exchange membranes (IEMs): selective electrodialysis (SED) utilizes IEMS that have high selectivity for monovalent ions; bipolar membrane electrodialysis (BMED) utilizes bipolar IEMS; and finally, ion liquid membrane electrodialysis (ILMED) which employs liquid ion membranes (Zavahir et al., 2021). While ED technologies are already used for industrial hydrometallurgical processes to recover Li from industrial brines, ore concentrates, and spent LIBs, their use for recovery from high Mg2+/Li+ and low Li+ concentration solutions has been limited (Campione et al., 2018; Gmar and Chagnes, 2019). Table 10 provides the applied voltage, selectivity, current efficiency, separation efficiency, recovery, and specific energy consumption of various ED membranes for Li+ extraction from salt lake brines, simulated brines, and seawater.
SED employs monovalent anion exchange membranes (MAEMs) and monovalent cation exchange membranes (MCEMs) to transport the monovalent anions (Cl−) and cations (Li+, Na+, and K+) through the MAEMs and MCEMS and to the anode and cathode, respectively. The divalent anions
BMED employs a bipolar membrane (BM) comprising a cation-exchange layer, an anion-exchange layer, and a hydrophilic interface layer (Huang and Xu, 2006; Li et al., 2016; Gmar and Chagnes, 2019). When an electric field is applied to the BM, the water molecules in the hydrophilic layer separate into hydrogen (H+) and hydroxide (OH−) ions. Simultaneously, anions passing through the AEM are combined with H+, and cations passing through the CEM are combined with OH−. The resulting acidic and basic solutions are enriched in corresponding recovery compartments (Mani, 1991). The acidic and basic recovery compartment streams can be treated with precipitants to produce LiOH and other valuable co-products (Bazinet et al., 1998; Jiang et al., 2014; Xue et al., 2015; Gmar and Chagnes, 2019).
Similar to SED, BMED demonstrates higher Li recovery at higher voltages. However, the ion leakage induced by higher voltages reduces Li recovery, so finding an optimum applied voltage is critical. Furthermore, BMED is very promising for Li recovery from high Mg2+/Li+ and low Li+ concentration solutions (Bunani et al., 2017b; Gmar and Chagnes, 2019). Compared to the other ED processes, it has the highest average Li+ recovery range (60%–98%), lowest average extraction time (20–120 min), and the lowest SEC range (3–19 kWh/kmol) (Bunani et al., 2017a; Bunani et al., 2017b; İpekçi et al., 2018; İpekçi et al., 2020). Also, BMED is ecologically friendly, requiring no chemical reagents for recovery (e.g., lime or sodium carbonate). The production of a basic and acidic recovery stream provides an economic opportunity to co-recover other industrial minerals, such as boron (Jiang et al., 2014; Yang et al., 2014; Hwang et al., 2016; Bunani et al., 2017a; Bunani et al., 2017b; Chen et al., 2022).
The main drawback of BMED is the sensitivity to high ion concentrations. The BM permselectivity is significantly reduced due to the Donnan exclusion phenomena wherein salt leaks through the membrane into the Li product (Tanaka, 2015; Venugopal and Dharmalingam, 2016; Pärnamäe et al., 2021). The BM’s high cost and thermal instability have also contributed to the limited use of BMED for aqueous mineral recovery. A pretreatment to reduce initial concentration is required for optimal performance. Despite its disadvantageous aspects, BMED has demonstrated higher chemical stability, mechanical stability, current efficiency, permselectivity, durability, and lower electrical resistance and voltage drop than the conventional ED processes for Li recovery. Many authors are already exploring ways to improve BMED performance, such as decreasing the AEM thickness, combining BMs with MAEMS and MCEMs, and appending catalysts layers to the BMs (Wilhelm et al., 2001; Manohar et al., 2017; Wang et al., 2017; Chen et al., 2021).
ILMED comprises two ion exchange membranes separated by an ionic liquid membrane (ILM). As previously mentioned, Ionic liquids (ILs) are unique liquids that have garnered attention as negligible vapor pressure alternatives to traditional organic solvents. Perhaps the most attractive feature of ILs for ED Li recovery is that they can be customized with pre-selected characteristics such as high thermal stability, moisture stability, and ion selectivity, by careful selection of the cation and anion (Seddon et al., 2000; Seddon et al., 2002; Deetlefs et al., 2006; Zavahir et al., 2021). ILMs have successfully been used for critical and heavy metals from aqueous solutions (Chen and Chen, 2016; Makanyire et al., 2016; Zante et al., 2019; Imdad and Dohare, 2022). The high permselectivity, separation efficiency, and low energy consumption demonstrated in previous studies support the integration of ILMS into the ED process for Li recovery from high Mg2+/Li+ and low Li+ concentration solutions.
When employing ILMED for Li recovery, the ILM must be sealed with a coat for durability and efficient recovery. After sealing novel, ion liquid impregnated organic membranes (IL-I-OM) with Nafion N-324, Hoshino (2013b) found that the membrane’s durability increased, the concentration of Li+ in the cathode increased by 5.94%, and the recovery of Li from seawater increased up to 22.2%. In addition to fortifying the IL-I-OM, the Nafion N-324 coating sealed the inside the IL-I-OM, resulting in an increase in Li+ concentration at the minimum voltage (2 V) and Li recovery. Similarly, in Hoshino (2013a), two CEMs were used to seal the ends of the IL-I-OM. To test selectivity, the CEMs employed were only permeable to the competing cations present in the seawater (Na+, K+, Mg2+, and Ca2+). The divalent cations were successfully separated from the monovalent cations and enriched in the cathode compartment. The Li+ was retained in the anode compartment, and a maximum separation efficiency of 63% was achieved. Other experiments explored the impacts of high Mg2+/Li+ mass ratios and voltage on ILMED SEC and Li recovery (Zhao Z. et al., 2020; Liu et al., 2020). Liu et al. (2020) observed a 99.5% reduction in the brine Mg2+/Li+ mass ratio after 12 h at 20°C and 3 V. Also, a minimum SEC of 16 Wh/g Li+ was achieved, compared to the 40 Wh/g Li+ for typical ED processes.
Zante et al. (2019) found that for an IL-TBP ILMED adding equimolar sodium carbonate and sodium hydrogen carbonate to the feedstream could reduce the loss of IL and extend the lifetime of the ILM. IL-TBP ILMED achieved a maximum extraction efficiency of 80%, and high selectivity for Li+ over Mg2+ and Na+, even when the competing ions were present in high concentrations. Despite their limited application, ILMED demonstrates high Li+ selectivity and competing monovalent and divalent ion separation efficiency at low voltages. The main challenges facing the commercialization of ILMED for industrial-scale Li recovery from aqueous solutions are the flux drops in membrane stability and the dissolution of IL to the feedstream after short periods of (2 days) of continuous use (Ma et al., 2000; Zante et al., 2019). Further investigation into treatments or mechanisms that minimize the loss of IL is needed to improve the feasibility of ILMED for recovery from brines and seawater.
The exponential growth in demand for the world’s exhaustible Li supply signals an impending shortage unless we expand current extraction resources to include high Mg2+/Li+ mass ratio and low Li+ concentration aqueous solutions such as seawater and most brines. Several technologies, including high Mg2+/Li+ precipitants, novel solvent extractants, Li-ion sieves, Li-ion-imprinted membranes, and electrochemical Li capturing systems, have been identified for Li+ extraction from these resources. However, each technology has unique challenges that have limited their application beyond bench-scale experiments. High Mg2+/Li+ precipitants leverage low reagent costs and passive extraction, but an Li+ enrichment step is required for feasibility. The high cost and low manufacturability combined with the associated environmental concerns make most novel solvent extractants infeasible for seawater, or most salt-lake brines. In contrast, LMO-type and LTO-type ion sieves are very promising for Li+ extraction from high Mg2+/Li+ and low Li+ concentration solutions. However, the powder morphology of the adsorbents reduce their durability and efficiency for continuous extraction. Li-IIMs leverage a unique combination of membrane separation technology and target ion-imprinting that achieves high rebinding capacity, selectivity, and recovery, but low specific energy consumption. The main challenges facing their commercialization are their sensitivity to pH, temperature, extraction time, and ion-recognition sites. Finally, ELICSs demonstrate great potential for extracting Li+ from solutions with high competing ion to Li+ ratios with their characteristically high separation and extraction efficiency. Their main challenges are operating cost, high energy demand, and very high competing ion to Li+ mass ratios.
A techno-economic analysis and life cycle assessment for each of the extraction technologies reviewed is needed. Both of these activities will further elucidate the climate impact, energy demand, operational costs, capital costs, productivity, and potential ROI for large scale projects using these technologies. Additionally these benchmarks can be used to develop pathways that move these technologies from bench-scale experiments to continuous demonstrations, and eventual pilot-scale systems. A recommended pathway is further exploration of the synergies between these technologies. The literature suggests that a strategic combination of two or more of the technologies reviewed can mitigate their individual challenges.
OM and MH contributed to the conceptualization of the manuscript. OM conducted the literature review and prepared the manuscript. OM and MH contributed to reviewing and revising the manuscript; All authors have read and agreed to the published version of the manuscript.
This work is supported by the John Colman Family, The Alfred P. Sloan Foundation (Grant No: G-2019-11435), the National GEM Consortium, and in part by a New Frontier Grant from Cornell University’s College of Arts and Sciences.
The authors declare that the research was conducted in the absence of any commercial or financial relationships that could be construed as a potential conflict of interest.
All claims expressed in this article are solely those of the authors and do not necessarily represent those of their affiliated organizations, or those of the publisher, the editors and the reviewers. Any product that may be evaluated in this article, or claim that may be made by its manufacturer, is not guaranteed or endorsed by the publisher.
Agusdinata, D. B., Liu, W., Eakin, H., and Romero, H. (2018). Socio-environmental impacts of lithium mineral extraction: Towards a research agenda. Environ. Res. Lett. 13, 123001. doi:10.1088/1748-9326/aae9b1
Amaral, F. A., Bocchi, N., Brocenschi, R. F., Biaggio, S. R., and Rocha-Filho, R. C. (2010). Structural and electrochemical properties of the doped spinels Li1.05M0.02Mn1.98O3.98N0.02 (M=Ga3+, Al3+, or Co3+; N=S2 or F) for use as cathode material in lithium batteries. J. Power Sources 195, 3293–3299. doi:10.1016/j.jpowsour.2009.12.002
An, J. W., Kang, D. J., Tran, K. T., Kim, M. J., Lim, T., and Tran, T. (2012). Recovery of lithium from Uyuni salar brine. Hydrometallurgy 117-118, 64–70. doi:10.1016/j.hydromet.2012.02.008
Angino, E. E., and Billings, G. K. (1966). Lithium content of sea water by atomic absorption spectrometry. Geochimica Cosmochimica Acta 30, 153–158. doi:10.1016/0016-7037(66)90104-9
Anlauf, A. (2016). “Greening the imperial mode of living? Socio-ecological (in) justice, electromobility, and lithium mining in Argentina,” in Fairness and justice in natural resource politics (England, UK: Routledge), 176–192.
Aral, H., and Vecchio-Sadus, A. (2008). Toxicity of lithium to humans and the environment—A literature review. Ecotoxicol. Environ. Saf. 70, 349–356. doi:10.1016/J.ECOENV.2008.02.026
Azevedo, M., Campagnol, N., Hagenbruch, T., Hoffman, K., Lala, A., and Ramsbottom, O. (2018). Lithium and cobalt-a tale of two commodities. Brussels, Belgium: McKinsey and Company: Metals and Mining, 1–25.
Bai, R., Wang, J., Wang, D., Cui, J., and Zhang, Y. (2022). Recovery of lithium from high Mg/Li ratio salt-lake brines using ion-exchange with NaNTf2 and TBP. Hydrometallurgy 213, 105914. doi:10.1016/j.hydromet.2022.105914
Bai, R., Wang, J., Wang, D., Zhang, Y., and Cui, J. (2021). Selective separation of lithium from the high magnesium brine by the extraction system containing phosphate-based ionic liquids. Sep. Purif. Technol. 274, 119051. doi:10.1016/j.seppur.2021.119051
Bai, X., Dai, J., Ma, Y., Bian, W., and Pan, J. (2020). 2-(Allyloxy) methylol-12-crown-4 ether functionalized polymer brushes from porous PolyHIPE using UV-initiated surface polymerization for recognition and recovery of lithium. Chem. Eng. J. 380, 122386. doi:10.1016/j.cej.2019.122386
Bang Mo, K. (1984). Membrane-based solvent extraction for selective removal and recovery of metals. J. Membr. Sci. 21, 5–19. doi:10.1016/S0376-7388(00)83060-4
Bartsch, R. A., Czech, B. P., Kang, S. I., Stewart, L. E., Walkowiak, W., Charewicz, W. A., et al. (1985). High lithium selectivity in competitive alkali metal solvent extraction by lipophilic crown carboxylic acids. J. Am. Chem. Soc. 107, 4997–4998. doi:10.1021/ja00303a030
Bazinet, L., Lamarche, F., and Ippersiel, D. (1998). Bipolar-membrane electrodialysis: Applications of electrodialysis in the food industry. Trends Food Sci. Technol. 9, 107–113. doi:10.1016/S0924-2244(98)00026-0
Bradley, D., and McCauley, A. (2013). A preliminary deposit model for lithium-cesium-tantalum (LCT) pegmatites, 6. United States: USGS.
Brown, K. A., Williams, W. J., Carmack, E. C., Fiske, G., François, R., McLennan, D., et al. (2020). Geochemistry of small Canadian arctic rivers with diverse geological and hydrological settings. J. Geophys. Res. Biogeosci. 125, e2019JG005414. doi:10.1029/2019JG005414
Bunani, S., Arda, M., Kabay, N., Yoshizuka, K., and Nishihama, S. (2017a). Effect of process conditions on recovery of lithium and boron from water using bipolar membrane electrodialysis (BMED). Desalination 416, 10–15. doi:10.1016/j.desal.2017.04.017
Bunani, S., Yoshizuka, K., Nishihama, S., Arda, M., and Kabay, N. (2017b). Application of bipolar membrane electrodialysis (BMED) for simultaneous separation and recovery of boron and lithium from aqueous solutions. Desalination 424, 37–44. doi:10.1016/j.desal.2017.09.029
Butt, F. S., Lewis, A., Chen, T., Mazlan, N. A., Wei, X., Hayer, J., et al. (2022). Lithium harvesting from the most abundant primary and secondary sources: A comparative study on conventional and membrane technologies. Membranes 12, 373. doi:10.3390/membranes12040373
Campione, A., Gurreri, L., Ciofalo, M., Micale, G., Tamburini, A., and Cipollina, A. (2018). Electrodialysis for water desalination: A critical assessment of recent developments on process fundamentals, models and applications. Desalination 434, 121–160. doi:10.1016/j.desal.2017.12.044
Chen, J., and Wu, Z. (2000). Solvation extraction by amines and synergistic solvation extraction with neutral or acidic extractants. Mineral Process. Extr. Metallurgy Rev. 21, 49–87. doi:10.1080/08827500008914165
Chen, L., and Chen, J. (2016). Asymmetric membrane containing ionic liquid [A336] [P507] for the preconcentration and separation of heavy rare earth lutetium. ACS Sustain. Chem. Eng. 4, 2644–2650. doi:10.1021/acssuschemeng.6b00141
Chen, Q.-B., Ji, Z.-Y., Liu, J., Zhao, Y.-Y., Wang, S.-Z., and Yuan, J.-S. (2018). Development of recovering lithium from brines by selective-electrodialysis: Effect of coexisting cations on the migration of lithium. J. Membr. Sci. 548, 408–420. doi:10.1016/j.memsci.2017.11.040
Chen, Q.-B., Wang, J., Liu, Y., Zhao, J., Li, P.-F., and Xu, Y. (2021). Sustainable disposal of seawater brine by novel hybrid electrodialysis system: Fine utilization of mixed salts. Water Res. 201, 117335. doi:10.1016/j.watres.2021.117335
Chen, T., Bi, J., Zhao, Y., Du, Z., Guo, X., Yuan, J., et al. (2022). Carbon dioxide capture coupled with magnesium utilization from seawater by bipolar membrane electrodialysis. Sci. Total Environ. 820, 153272. doi:10.1016/j.scitotenv.2022.153272
Chitrakar, R., Kanoh, H., Makita, Y., Miyai, Y., and Ooi, K. (2000a). Synthesis of spinel-type lithium antimony manganese oxides and their Li+ extraction/ion insertion reactions. J. Mat. Chem. 10, 2325–2329. doi:10.1039/B002465L
Chitrakar, R., Kanoh, H., Miyai, Y., and Ooi, K. (2000b). A new type of manganese oxide (MnO2⋅0.5H2O) derived from Li1.6Mn1.6O4 and its lithium ion-sieve properties. Chem. Mat. 12, 3151–3157. doi:10.1021/cm0000191
Chitrakar, R., Kanoh, H., Miyai, Y., and Ooi, K. (2001). Recovery of lithium from seawater using manganese oxide adsorbent (H1.6Mn1.6O4) derived from Li1.6Mn1.6O4. Ind. Eng. Chem. Res. 40, 2054–2058. doi:10.1021/ie000911h
Chitrakar, R., Makita, Y., Ooi, K., and Sonoda, A. (2014). Lithium recovery from salt lake brine by H2TiO3. Dalton Trans. 43, 8933–8939. doi:10.1039/C4DT00467A
Chitrakar, R., Makita, Y., Ooi, K., and Sonoda, A. (2012). Selective uptake of lithium ion from brine by H1.33Mn1.67O4 and H1.6Mn1.6O4. Chem. Lett. 41, 1647–1649. doi:10.1246/cl.2012.1647
Chordia, M., Wickerts, S., Nordelöf, A., and Arvidsson, R. (2022). Life cycle environmental impacts of current and future battery-grade lithium supply from brine and spodumene. Resour. Conservation Recycl. 187, 106634. doi:10.1016/J.RESCONREC.2022.106634
Chung, K. S., Lee, J. C., Kim, W. K., Kim, S. B., and Cho, K. Y. (2008). Inorganic adsorbent containing polymeric membrane reservoir for the recovery of lithium from seawater. J. Membr. Sci. 325, 503–508. doi:10.1016/J.MEMSCI.2008.09.041
Craig, H. (1969). Geochemistry and origin of the red sea brines bt - hot brines and recent heavy metal deposits in the red sea: A geochemical and geophysical account. Berlin, Heidelberg: Springer Berlin Heidelberg, 208–242. doi:10.1007/978-3-662-28603-6_22
Dai, X., Zhan, H., Qian, Z., Li, J., Liu, Z., and Wu, Z. (2021). Al-doped H2TiO3 ion sieve with enhanced Li+ adsorption performance. RSC Adv. 11, 34988–34995. doi:10.1039/D1RA06535A
Deetlefs, M., Seddon, K. R., and Shara, M. (2006). Predicting physical properties of ionic liquids. Phys. Chem. Chem. Phys. 8, 642–649. doi:10.1039/B513453F
Dessemond, C., Lajoie-Leroux, F., Soucy, G., Laroche, N., and Magnan, J.-F. (2019). Spodumene: The lithium market, resources and processes. Minerals 9, 334. doi:10.3390/min9060334
Ding, T., Wu, Q., Nie, Z., Zheng, M., Wang, Y., and Yang, D. (2022). Selective recovery of lithium resources in salt lakes by polyacrylonitrile/ion-imprinted polymer: Synthesis, testing, and computation. Polym. Test. 113, 107647. doi:10.1016/j.polymertesting.2022.107647
Dorn, F. M., Ruiz Peyré, F., and Peyré, F. R. (2020). Lithium as a strategic resource: Geopolitics, industrialization, and mining in Argentina. J. Lat. Am. Geogr. 19, 68–90. doi:10.1353/lag.2020.0101
Draper, J. J., and Jensen, A. R. (1976). The geochemistry of Lake Frome, a playa lake in South Australia. BMR J. Aust. Geol. Geophys. 1, 83–104.
Eftekhari, A., Moghaddam, A. B., and Solati-Hashjin, M. (2006). Electrochemical properties of LiMn2O4 cathode material doped with an actinide. J. Alloys Compd. 424, 225–230. doi:10.1016/j.jallcom.2005.10.088
Ein-Eli, Y., Urian, R. C., Wen, W., and Mukerjee, S. (2005). Low temperature performance of copper/nickel modified LiMn2O4 spinels. Electrochimica Acta 50, 1931–1937. doi:10.1016/j.electacta.2004.09.002
Ellestad, R. B., and Leute, K.-M. (1950). Method of extracting lithium values from spodumene ores. US2516109A.
Epstein, J. A., Feist, E. M., Zmora, J., and Marcus, Y. (1981). Extraction of lithium from the dead sea. Hydrometallurgy 6, 269–275. doi:10.1016/0304-386X(81)90044-X
Ertürk, G., and Mattiasson, B. (2017). Molecular imprinting techniques used for the preparation of biosensors. Sensors 17, 288. doi:10.3390/s17020288
Flexer, V., Baspineiro, C. F., and Galli, C. I. (2018). Lithium recovery from brines: A vital raw material for green energies with a potential environmental impact in its mining and processing. Sci. Total Environ. 639, 1188–1204. doi:10.1016/J.SCITOTENV.2018.05.223
Fuks, L., and Majdan, M. (2000). Features of solvent extraction of lanthanides and actinides. Mineral Process. Extr. Metallurgy Rev. 21, 25–48. doi:10.1080/08827500008914164
Gao, A., Sun, Z., Li, S., Hou, X., Li, H., Wu, Q., et al. (2018). The mechanism of manganese dissolution on Li1.6Mn1.6O4 ion sieves with HCl. Dalton Trans. 47, 3864–3871. doi:10.1039/C8DT00033F
Gao, D., Guo, Y., Yu, X., Wang, S., and Deng, T. (2016). Extracting lithium from the high concentration ratio of magnesium and lithium brine using imidazolium-based ionic liquids with varying alkyl chain lengths. J. Chem. Eng. Jpn. /. JCEJ. 49, 104–110. doi:10.1252/jcej.15we046
Gmar, S., and Chagnes, A. (2019). Recent advances on electrodialysis for the recovery of lithium from primary and secondary resources. Hydrometallurgy 189, 105124. doi:10.1016/j.hydromet.2019.105124
Godfrey, L. V., Chan, L. H., Alonso, R. N., Lowenstein, T. K., McDonough, W. F., Houston, J., et al. (2013). The role of climate in the accumulation of lithium-rich brine in the Central Andes. Appl. Geochem. 38, 92–102. doi:10.1016/J.APGEOCHEM.2013.09.002
Goodenough, R. D. (1960). Recovery of lithium, United States. Available at: https://patents.google.com/patent/US2964381A.
Goodenough, R. D., and Stenger, V. A. (1961). Recovery of lithium from lithium aluminate complex. United States US2980497A , 2, 980, 497.
Gopinath, K. P., Madhav, N. V., Krishnan, A., Malolan, R., and Rangarajan, G. (2020). Present applications of titanium dioxide for the photocatalytic removal of pollutants from water: A review. J. Environ. Manag. 270, 110906. doi:10.1016/j.jenvman.2020.110906
Gouda, V. K., Banat, I. M., Riad, W. T., and Mansour, S. (1993). Microbiologically induced corrosion of UNS N04400 in seawater. Corrosion 49, 63–73. doi:10.5006/1.3316036
Graham, J. D., Rupp, J. A., and Brungard, E. (2021). Lithium in the green energy transition: The quest for both sustainability and security. Sustainability 13, 11274. doi:10.3390/su132011274
Grosjean, C., Herrera Miranda, P., Perrin, M., and Poggi, P. (2012). Assessment of world lithium resources and consequences of their geographic distribution on the expected development of the electric vehicle industry. Renew. Sustain. Energy Rev. 16, 1735–1744. doi:10.1016/J.RSER.2011.11.023
Gruber, P. W., Medina, P. A., Keoleian, G. A., Kesler, S. E., Everson, M. P., and Wallington, T. J. (2011). Global lithium availability. J. Ind. Ecol. 15, 760–775. doi:10.1111/j.1530-9290.2011.00359.x
Gu, L., Sun, X.-L., Zhou, W., Ren, D.-H., Qiu, D., Gu, Z.-G., et al. (2016). Ion exchange properties and lithium isotopes selectivity of H0.36La0.55TiO3, H4Ti5O12 and H2Ti3O7. J. Radioanal. Nucl. Chem. 307, 973–983. doi:10.1007/s10967-015-4239-6
Guo, Z.-Y., Ji, Z.-Y., Chen, Q.-B., Liu, J., Zhao, Y.-Y., Li, F., et al. (2018). Prefractionation of LiCl from concentrated seawater/salt lake brines by electrodialysis with monovalent selective ion exchange membranes. J. Clean. Prod. 193, 338–350. doi:10.1016/j.jclepro.2018.05.077
Gurreri, L., Tamburini, A., Cipollina, A., and Micale, G. (2020). Electrodialysis applications in wastewater treatment for environmental protection and resources recovery: A systematic review on progress and perspectives. Membranes 10, 146. doi:10.3390/membranes10070146
Hamilton, A. D. (1984). 5.21 - crown ethers and cryptands. Oxford: Pergamon, 731–761. doi:10.1016/B978-008096519-2.00127-2
Hamzaoui, A. H., Hammi, H., and M’nif, A. (2007). Operating conditions for lithium recovery from natural brines. Russ. J. Inorg. Chem. 52, 1859–1863. doi:10.1134/S0036023607120091
Hamzaoui, A. H., Jamoussi, B., and M’nif, A. (2008). Lithium recovery from highly concentrated solutions: Response surface methodology (RSM) process parameters optimization. Hydrometallurgy 90, 1–7. doi:10.1016/j.hydromet.2007.09.005
Hano, T., Matsumoto, M., Ohtake, T., Egashir, N., and Hori, F. (1992). Recovery of lithium from geothermal water by solvent extraction technique. Solvent Extr. Ion Exch. 10, 195–206. doi:10.1080/07366299208918100
Harvianto, G. R., Kim, S.-H., and Ju, C.-S. (2016). Solvent extraction and stripping of lithium ion from aqueous solution and its application to seawater. Rare Met. 35, 948–953. doi:10.1007/s12598-015-0453-1
He, G., Li, Z., Liu, Y., Liu, M., Zhu, C., Zhang, L., et al. (2022). A novel lithium ion-imprinted membrane with robust adsorption capacity and anti-fouling property based on the uniform multilayered interlayer. Desalination 539, 115973. doi:10.1016/j.desal.2022.115973
He, G., Zhang, L., Zhou, D., Zou, Y., and Wang, F. (2015). The optimal condition for H2TiO3–lithium adsorbent preparation and Li+ adsorption confirmed by an orthogonal test design. Ionics 21, 2219–2226. doi:10.1007/s11581-015-1393-3
Heidari, N., and Momeni, P. (2017). Selective adsorption of lithium ions from Urmia Lake onto aluminum hydroxide. Environ. Earth Sci. 76, 551. doi:10.1007/s12665-017-6885-1
Helan, M., Berchmans, L. J., Syamala Kumari, V. S., RaviSankar, R., and Shanmugam, V. M. (2011). Molten salt synthesis of LiGd0 01Mn1 99O4 using chloride–carbonate melt. Mater. Res. Innovations 15, 130–134. doi:10.1179/143307511X12998222918958
Hill, R. J., Craig, J. R., and Gibbs, G. V. (1979). Systematics of the spinel structure type. Phys. Chem. Min. 4, 317–339. doi:10.1007/BF00307535
Hoshino, T. (2013a). Development of technology for recovering lithium from seawater by electrodialysis using ionic liquid membrane. Fusion Eng. Des. 88, 2956–2959. doi:10.1016/j.fusengdes.2013.06.009
Hoshino, T. (2013b). Preliminary studies of lithium recovery technology from seawater by electrodialysis using ionic liquid membrane. Desalination 317, 11–16. doi:10.1016/j.desal.2013.02.014
Hu, H., Guo, J., Liu, M., Li, Y., Wu, B., Xiong, L., et al. (2022). Preparation and characterization of high-stability lithium ion-sieves with aluminosilicate framework. Hydrometallurgy 213, 105929. doi:10.1016/j.hydromet.2022.105929
Huang, C., and Xu, T. (2006). Electrodialysis with bipolar membranes for sustainable development. Environ. Sci. Technol. 40, 5233–5243. doi:10.1021/es060039p
Huang, W., Liu, S., Liu, J., Zhang, W., and Pan, J. (2018). 2-Methylol-12-crown-4 ether immobilized PolyHIPEs toward recovery of lithium(i). New J. Chem. 42, 16814–16822. doi:10.1039/C8NJ01961D
Hwang, C. W., Jeong, M. H., Kim, Y. J., Son, W. K., Kang, K. S., Lee, C. S., et al. (2016). Process design for lithium recovery using bipolar membrane electrodialysis system. Sep. Purif. Technol. 166, 34–40. doi:10.1016/j.seppur.2016.03.013
IEA (2022). Global EV Outlook 2022 Securing supplies for an electric future. Paris, France: OECD, 221.
Imdad, S., and Dohare, R. K. (2022). A critical review on heavy metals removal using ionic liquid membranes from the industrial wastewater. Chem. Eng. Process. - Process Intensif. 173, 108812. doi:10.1016/j.cep.2022.108812
İpekçi, D., Altıok, E., Bunani, S., Yoshizuka, K., Nishihama, S., Arda, M., et al. (2018). Effect of acid-base solutions used in acid-base compartments for simultaneous recovery of lithium and boron from aqueous solution using bipolar membrane electrodialysis (BMED). Desalination 448, 69–75. doi:10.1016/j.desal.2018.10.001
İpekçi, D., Kabay, N., Bunani, S., Altıok, E., Arda, M., Yoshizuka, K., et al. (2020). Application of heterogeneous ion exchange membranes for simultaneous separation and recovery of lithium and boron from aqueous solution with bipolar membrane electrodialysis (EDBM). Desalination 479, 114313. doi:10.1016/j.desal.2020.114313
Iqbal, M. J., and Ahmad, Z. (2008). Electrical and dielectric properties of lithium manganate nanomaterials doped with rare-Earth elements. J. Power Sources 179, 763–769. doi:10.1016/j.jpowsour.2007.12.115
Isupov, V. P., Kotsupalo, N. P., Nemudry, A. P., and Menzeres, L. T. (1999). “Aluminium hydroxide as selective sorbent of lithium salts from brines and technical solutions,” in Adsorption and its applications in industry and environmental protection. Editor A. Da̧browski (Amsterdam, Netherlands: Elsevier), 120, 621–652. doi:10.1016/S0167-2991(99)80567-9
Jamal, A., and Khzahee, M. (2019). The influence of the dead sea water decline on the concentration changes of lithium and strontium trace elements.
Jang, E., Jang, Y., and Chung, E. (2017). Lithium recovery from shale gas produced water using solvent extraction. Appl. Geochem. 78, 343–350. doi:10.1016/j.apgeochem.2017.01.016
Ji, P.-Y., Ji, Z.-Y., Chen, Q.-B., Liu, J., Zhao, Y.-Y., Wang, S.-Z., et al. (2018). Effect of coexisting ions on recovering lithium from high Mg2+/Li+ ratio brines by selective-electrodialysis. Sep. Purif. Technol. 207, 1–11. doi:10.1016/j.seppur.2018.06.012
Ji, Z.-y., Chen, Q.-b., Yuan, J.-s., Liu, J., Zhao, Y.-y., and Feng, W.-x. (2017). Preliminary study on recovering lithium from high Mg2+/Li+ ratio brines by electrodialysis. Sep. Purif. Technol. 172, 168–177. doi:10.1016/j.seppur.2016.08.006
Jiang, C., Wang, Y., Wang, Q., Feng, H., and Xu, T. (2014). Production of lithium hydroxide from Lake Brines through electro–electrodialysis with bipolar membranes (EEDBM). Ind. Eng. Chem. Res. 53, 6103–6112. doi:10.1021/ie404334s
Jin, Y., Jiang, Q., Zhao, Y., alAnthuvan Rajesh, J., and Min, B.-K. (2018). IOP conference series: Earth and environmental science LiMn 2 O 4 microspheres as high-performance cathode materials for Li-ion batteries you may also like controllable fabrication of CoMn 2 O 4 microflowers and microspheres as high-performance lithium ion battery anode material cubic spinel AB 2 O 4 type porous ZnCo 2 O 4 microspheres: Facile hydrothermal synthesis and their electrochemical performances in pseudocapacitor. IOP Conf. Ser. Earth Environ. Sci. 108, 22011. doi:10.1088/1755-1315/108/2/022011
Jones, B. F., Naftz, D. L., Spencer, R. J., and Oviatt, C. G. (2009). Geochemical evolution of great Salt Lake, Utah, USA. Aquat. Geochem. 15, 95–121. doi:10.1007/s10498-008-9047-y
Joo, H., Kim, S., Kim, S., Choi, M., Kim, S.-H., and Yoon, J. (2020). Pilot-scale demonstration of an electrochemical system for lithium recovery from the desalination concentrate. Environ. Sci. Water Res. Technol. 6, 290–295. doi:10.1039/C9EW00756C
Kalantzakos, S. (2020). The race for critical minerals in an era of geopolitical realignments. Int. Spectator 55, 1–16. doi:10.1080/03932729.2020.1786926
Kanoh, H., Ooi, K., Miyai, Y., and Katoh, S. (1993). Electrochemical recovery of lithium ions in the aqueous phase. Sep. Sci. Technol. 28, 643–651. doi:10.1080/01496399308019512
Kanoh, H., Ooi, K., Miyai, Y., and Katoh, S. (1991). Selective electroinsertion of lithium ions into a platinum/.lambda.-manganese dioxide electrode in the aqueous phase. Langmuir 7, 1841–1842. doi:10.1021/la00057a002
Kaplan, D. (1963). Process for the extraction of lithium from dead sea solutions. Isr. J. Chem. 1, 115–120. doi:10.1002/ijch.196300021
Katayama, Y., Nita, K., Ueda, M., Nakamura, H., Takagi, M., and Ueno, K. (1985). Synthesis of chromogenic crown ethers and liquid-liquid extraction of alkali metal ions. Anal. Chim. Acta 173, 193–209. doi:10.1016/S0003-2670(00)84957-0
Katz, A., Starinsky, A. A., Katz, A., and Starinsky, Á. A. (2009). Geochemical history of the dead sea. Aquat. Geochem. 15, 159–194. doi:10.1007/s10498-008-9045-0
Kelly, J. C., Wang, M., Dai, Q., and Winjobi, O. (2021). Energy, greenhouse gas, and water life cycle analysis of lithium carbonate and lithium hydroxide monohydrate from brine and ore resources and their use in lithium ion battery cathodes and lithium ion batteries. Resour. Conservation Recycl. 174, 105762. doi:10.1016/j.resconrec.2021.105762
Kesler, S. E., Gruber, P. W., Medina, P. A., Keoleian, G. A., Everson, M. P., and Wallington, T. J. (2012). Global lithium resources: Relative importance of pegmatite, brine and other deposits. Ore Geol. Rev. 48, 55–69. doi:10.1016/J.OREGEOREV.2012.05.006
Kim, S., Joo, H., Moon, T., Kim, S.-H., and Yoon, J. (2019). Rapid and selective lithium recovery from desalination brine using an electrochemical system. Environ. Sci. Process. Impacts 21, 667–676. doi:10.1039/C8EM00498F
Kim, S., Kim, J., Kim, S., Lee, J., and Yoon, J. (2018). Electrochemical lithium recovery and organic pollutant removal from industrial wastewater of a battery recycling plant. Environ. Sci. Water Res. Technol. 4, 175–182. doi:10.1039/C7EW00454K
Kim, S., Lee, J., Kang, J. S., Jo, K., Kim, S., Sung, Y.-E., et al. (2015). Lithium recovery from brine using a λ-MnO2/activated carbon hybrid supercapacitor system. Chemosphere 125, 50–56. doi:10.1016/j.chemosphere.2015.01.024
Kushnir, D., and Sandén, B. A. (2012). The time dimension and lithium resource constraints for electric vehicles. Resour. Policy 37, 93–103. doi:10.1016/j.resourpol.2011.11.003
Lambert, J., Avila-Rodriguez, M., Durand, G., and Rakib, M. (2006). Separation of sodium ions from trivalent chromium by electrodialysis using monovalent cation selective membranes. J. Membr. Sci. 280, 219–225. doi:10.1016/j.memsci.2006.01.021
Lawagon, C. P., Nisola, G. M., Mun, J., Tron, A., Torrejos, R. E. C., Seo, J. G., et al. (2016). Adsorptive Li+ mining from liquid resources by H2TiO3: Equilibrium, kinetics, thermodynamics, and mechanisms. J. Industrial Eng. Chem. 35, 347–356. doi:10.1016/j.jiec.2016.01.015
Lee, J., Yu, S.-H., Kim, C., Sung, Y.-E., and Yoon, J. (2013). Highly selective lithium recovery from brine using a λ-MnO2–Ag battery. Phys. Chem. Chem. Phys. 15, 7690–7695. doi:10.1039/C3CP50919B
Li, E., Kang, J., Ye, P., Zhang, W., Cheng, F., Yin, C., et al. (2019a). A prospective material for the highly selective extraction of lithium ions based on a photochromic crowned spirobenzopyran. J. Mater. Chem. 7 (6), 903–907. doi:10.1039/C8TB02906G
Li, Q., Fan, Q., Wang, J., Qin, Z., Zhang, X., Wei, H., et al. (2019b). Hydrochemistry, distribution and formation of lithium-rich brines in salt lakes on the Qinghai-Tibetan plateau. Miner. (Basel). 9, 528. doi:10.3390/min9090528
Li, T., Tan, H., and Fan, Q. (2006). Hydrochemical characteristics and origin analysis fo the undergrond brines in west quaidam basin. J. Salt Lake Res. 14, 26–32.
Li, Y.-h., Zhao, Z.-w., Liu, X.-h., Chen, X.-y., and Zhong, M.-l. (2015). Extraction of lithium from salt lake brine by aluminum-based alloys. Trans. Nonferrous Metals Soc. China 25, 3484–3489. doi:10.1016/S1003-6326(15)64032-8
Li, Y., Shi, S., Cao, H., Wu, X., Zhao, Z., and Wang, L. (2016). Bipolar membrane electrodialysis for generation of hydrochloric acid and ammonia from simulated ammonium chloride wastewater. Water Res. 89, 201–209. doi:10.1016/j.watres.2015.11.038
Limjuco, L. A., Nisola, G. M., Lawagon, C. P., Lee, S.-P., Seo, J. G., Kim, H., et al. (2016). H2TiO3 composite adsorbent foam for efficient and continuous recovery of Li+ from liquid resources. Colloids Surfaces A Physicochem. Eng. Aspects 504, 267–279. doi:10.1016/j.colsurfa.2016.05.072
Liu, G., Zhao, Z., and He, L. (2020). Highly selective lithium recovery from high Mg/Li ratio brines. Desalination 474, 114185. doi:10.1016/j.desal.2019.114185
Liu, W., Agusdinata, D. B., and Myint, S. W. (2019). Spatiotemporal patterns of lithium mining and environmental degradation in the Atacama Salt Flat, Chile. Int. J. Appl. Earth Observation Geoinformation 80, 145–156. doi:10.1016/j.jag.2019.04.016
Liu, X., Zhong, M., Chen, X., and Zhao, Z. (2018). Separating lithium and magnesium in brine by aluminum-based materials. Hydrometallurgy 176, 73–77. doi:10.1016/j.hydromet.2018.01.005
Lowry, T., and Richardson, K. (1987). Mechanism and theory in organic chemistry. New York, United States: Harper & Row.
Lu, J., Qin, Y., Wu, Y., Meng, M., Yan, Y., and Li, C. (2019). Recent advances in ion-imprinted membranes: Separation and detection via ion-selective recognition. Environ. Sci. Water Res. Technol. 5, 1626–1653. doi:10.1039/C9EW00465C
Lu, J., Qin, Y., Zhang, Q., Wu, Y., Cui, J., Li, C., et al. (2018). Multilayered ion-imprinted membranes with high selectivity towards Li+ based on the synergistic effect of 12-crown-4 and polyether sulfone. Appl. Surf. Sci. 427, 931–941. doi:10.1016/j.apsusc.2017.08.016
Ma, P., Chen, X. D., and Hossain, M. D. M. (2000). Lithium extraction from a multicomponent mixture using supported liquid membranes. Sep. Sci. Technol. 35, 2513–2533. doi:10.1081/SS-100102353
Maheswari, P., Prasannadevi, D., and Mohan, D. (2012). Preparation and performance of silver nanoparticle incorporated polyetherethersulfone nanofiltration membranes. High. Perform. Polym. 25, 174–187. doi:10.1177/0954008312459865
Makanyire, T., Sanchez-Segado, S., and Jha, A. (2016). Separation and recovery of critical metal ions using ionic liquids. Adv. Manuf. 4, 33–46. doi:10.1007/s40436-015-0132-3
Malliga, P., Bela, R. B., and Shanmugapriya, N. (2020). Chapter 5 - conversion of textile effluent wastewater into fertilizer using marine cyanobacteria along with different agricultural waste. Amsterdam, Netherlands: Elsevier, 87–111. doi:10.1016/B978-0-12-817951-2.00005-5–
Malyovanyi, S. M., Andriiko, A. A., and Monko, A. P. (2003). Synthesis and electrochemical behavior of Fe-doped overstoichiometric LiMn2O4-based spinels. J. Solid State Electrochem. 8, 7–10. doi:10.1007/s10008-003-0414-8
Månberger, A., and Johansson, B. (2019). The geopolitics of metals and metalloids used for the renewable energy transition. Energy Strategy Rev. 26, 100394. doi:10.1016/j.esr.2019.100394
Mani, K. N. (1991). Electrodialysis water splitting technology. J. Membr. Sci. 58, 117–138. doi:10.1016/S0376-7388(00)82450-3
Manohar, M., Shukla, G., Pandey, R. P., and Shahi, V. K. (2017). Efficient bipolar membrane with protein interfacial layer for optimal water splitting. J. Industrial Eng. Chem. 47, 141–149. doi:10.1016/j.jiec.2016.11.025
Marchini, F., Rubi, D., del Pozo, M., Williams, F. J., and Calvo, E. J. (2016). Surface chemistry and lithium-ion exchange in LiMn2O4 for the electrochemical selective extraction of LiCl from natural Salt Lake Brines. J. Phys. Chem. C 120, 15875–15883. doi:10.1021/acs.jpcc.5b11722
Marthi, R., Asgar, H., Gadikota, G., and Smith, Y. R. (2021). On the structure and lithium adsorption mechanism of layered H2TiO3. ACS Appl. Mat. Interfaces 13, 8361–8369. doi:10.1021/acsami.0c20691
Millero, F. J., and Chetirkin, P. V. (1980). The density of Caspian Sea waters. Deep Sea Res. Part A. Oceanogr. Res. Pap. 27, 265–271. doi:10.1016/0198-0149(80)90017-5
Missoni, L. L., Marchini, F., del Pozo, M., and Calvo, E. J. (2016). A LiMn2O4-polypyrrole system for the extraction of LiCl from natural brine. J. Electrochem. Soc. 163, A1898–A1902. doi:10.1149/2.0591609jes
Moazeni, M., Hajipour, H., Askari, M., and Nusheh, M. (2015). Hydrothermal synthesis and characterization of titanium dioxide nanotubes as novel lithium adsorbents. Mater. Res. Bull. 61, 70–75. doi:10.1016/j.materresbull.2014.09.069
Mohr, S. H., Mudd, G. M., and Giurco, D. (2012). Lithium resources and production: Critical assessment and global projections. Minerals 2 (1), 65–84. doi:10.3390/min2010065
Moran, S. (2018). Chapter 6 - clean water characterization and treatment objectives. Oxford, United Kingdom: Butterworth-Heinemann, 61–67. doi:10.1016/B978-0-12-811309-7.00006-0
Mori, T., Takao, K., Sasaki, K., Suzuki, T., Arai, T., and Ikeda, Y. (2015). Homogeneous liquid–liquid extraction of U(VI) from HNO3 aqueous solution to betainium bis(trifluoromethylsulfonyl)imide ionic liquid and recovery of extracted U(VI). Sep. Purif. Technol. 155, 133–138. doi:10.1016/j.seppur.2015.01.045
Mortaheb, H., Moghadasi, M., and Garmsiri, M. (2014). “Synthesis of porous polyether sulfone ion-exchange membrane, investigation on its properties and characterizations,” in The 8thInternational Chemical Engineering Congress & Exhibition, 2014-02-24 (Kish, Iran.
Nguyen, T., and Lee, M. (2018). A review on the separation of lithium ion from leach liquors of primary and secondary resources by solvent extraction with commercial extractants. Processes 6, 55. doi:10.3390/pr6050055
Nie, X.-Y., Sun, S.-Y., Song, X., and Yu, J.-G. (2017). Further investigation into lithium recovery from salt lake brines with different feed characteristics by electrodialysis. J. Membr. Sci. 530, 185–191. doi:10.1016/j.memsci.2017.02.020
Ohzuku, T., Ueda, A., and Yamamoto, N. (1995). Zero-strain insertion material of Li[Li1/3Ti5/3]O4 for rechargeable lithium cells. J. Electrochem. Soc. 142, 1431–1435. doi:10.1149/1.2048592
Olea, F., Durán, G., Díaz, G., Villarroel, E., Araya-López, C., Cabezas, R., et al. (2022). Ionic liquids for the selective solvent extraction of lithium from aqueous solutions: A theoretical selection using COSMO-RS. Minerals 12, 190. doi:10.3390/min12020190
Ouyang, C. Y., Zhong, Z. Y., and Lei, M. S. (2007). Ab initio studies of structural and electronic properties of Li4Ti5O12 spinel. Electrochem. Commun. 9, 1107–1112. doi:10.1016/j.elecom.2007.01.013
Paranthaman, M. P., Li, L., Luo, J., Hoke, T., Ucar, H., Moyer, B. A., et al. (2017). Recovery of lithium from geothermal brine with lithium–aluminum layered double hydroxide chloride sorbents. Environ. Sci. Technol. 51, 13481–13486. doi:10.1021/acs.est.7b03464
Pärnamäe, R., Mareev, S., Nikonenko, V., Melnikov, S., Sheldeshov, N., Zabolotskii, V., et al. (2021). Bipolar membranes: A review on principles, latest developments, and applications. J. Membr. Sci. 617, 118538. doi:10.1016/j.memsci.2020.118538
Patil, A. B., Pathak, P. N., Shinde, V. S., Alyapyshev, M. Y., Babain, V. A., and Mohapatra, P. K. (2015). A novel solvent system containing a dipicolinamide in room temperature ionic liquids for actinide ion extraction. J. Radioanal. Nucl. Chem. 305, 521–528. doi:10.1007/s10967-015-4028-2
Patrice, S., Yury, G., and Bruce, D. (2014). Where do batteries end and supercapacitors begin? Science 343, 1210–1211. doi:10.1126/science.1249625
Pauwels, H., Brach, M., and Fouillac, C. (1995). Study of Li+ adsorption onto polymeric aluminium (III) hydroxide for application in the treatment of geothermal waters. Colloids Surfaces A Physicochem. Eng. Aspects 100, 73–82. doi:10.1016/0927-7757(95)03185-G
Pearson, R. G. (1990). Hard and soft acids and bases—The evolution of a chemical concept. Coord. Chem. Rev. 100, 403–425. doi:10.1016/0010-8545(90)85016-L
Peppard, D. F., Mason, G. W., Driscoll, W. J., and Sironen, R. J. (1958). Acidic esters of orthophosphoric acid as selective extractants for metallic cations—Tracer studies. J. Inorg. Nucl. Chem. 7, 276–285. doi:10.1016/0022-1902(58)80078-0
Pouraghabarar, M., Taleshi, S., and Chaichi, M. J. (2021). Determination of lithium abundances in seawater in the southern coast of the caspian sea and river estuaries. J. Mar. Sci. Technol. 19, 66–72. doi:10.22113/jmst.2018.109755.2088
Qian, F., Guo, M., Qian, Z., Zhao, B., Li, J., Wu, Z., et al. (2021a). Enabling highly structure stability and adsorption performances of Li1.6Mn1.6O4 by Al-gradient surface doping. Sep. Purif. Technol. 264, 118433. doi:10.1016/j.seppur.2021.118433
Qian, F., Zhao, B., Guo, M., Wu, Z., Zhou, W., and Liu, Z. (2021b). Surface trace doping of Na enhancing structure stability and adsorption properties of Li1.6Mn1.6O4 for Li+ recovery. Sep. Purif. Technol. 256, 117583. doi:10.1016/j.seppur.2020.117583
Quintero, C., Dahlkamp, J. M., Fierro, F., Thennis, T., Zhang, Y., Videla, Á., et al. (2020). Development of a co-precipitation process for the preparation of magnesium hydroxide containing lithium carbonate from Li-enriched brines. Hydrometallurgy 198, 105515. doi:10.1016/j.hydromet.2020.105515
Rama, R., Rout, A., Venkatesan, K. A., Antony, M. P., and Vasudeva Rao, P. R. (2015). Extraction behavior of americium(III) in benzoylpyrazolone dissolved in pyrrolidinium based ionic liquid. Sep. Sci. Technol. 50, 150615133350006–150615133352169. doi:10.1080/01496395.2015.1050109
Reig, M., Vecino, X., Valderrama, C., Gibert, O., and Cortina, J. L. (2018). Application of selectrodialysis for the removal of as from metallurgical process waters: Recovery of Cu and Zn. Sep. Purif. Technol. 195, 404–412. doi:10.1016/j.seppur.2017.12.040
Roundhill, D. M. (2001). Extraction of metals from soils and waters. Berlin, Germany: Springer Science & Business Media.
Ryu, T., Haldorai, Y., Rengaraj, A., Shin, J., Hong, H.-J., Lee, G.-W., et al. (2016). Recovery of lithium ions from seawater using a continuous flow adsorption column packed with granulated chitosan–lithium manganese oxide. Ind. Eng. Chem. Res. 55, 7218–7225. doi:10.1021/acs.iecr.6b01632
Safarbali, R., Yaftian, M. R., and Zamani, A. (2016). Solvent extraction-separation of La(III), Eu(III) and Er(III) ions from aqueous chloride medium using carbamoyl-carboxylic acid extractants. J. Rare Earths 34, 91–98. doi:10.1016/S1002-0721(14)60583-4
Sakunthala, A., Reddy, M. V., Selvasekarapandian, S., Chowdari, B. V. R., and Selvin, P. C. (2010). Synthesis of compounds, Li(MMn11/6)O4 (M=Mn1/6, Co1/6, (Co1/12Cr1/12), (Co1/12Al1/12), (Cr1/12Al1/12)) by polymer precursor method and its electrochemical performance for lithium-ion batteries. Electrochimica Acta 55, 4441–4450. doi:10.1016/j.electacta.2010.02.080
Schmidt, A., Mestmäcker, F., Brückner, L., Elwert, T., and Strube, J. (2019). Liquid-liquid extraction and chromatography process routes for the purification of lithium. Mater. Sci. Forum 959, 79–99. doi:10.4028/www.scientific.net/MSF.959.79
Seddon, K. R., Stark, A., and Torres, M.-J. (2000). Influence of chloride, water, and organic solvents on the physical properties of ionic liquids. Pure Appl. Chem. 72, 2275–2287. doi:10.1351/pac200072122275
Seddon, K. R., Stark, A., and Torres, M.-J. (2002). “Viscosity and density of 1-Alkyl-3-methylimidazolium ionic liquids,” in Clean solvents (Washington, United States: American Chemical Society), 4–34. 819 of ACS Symposium Series. doi:10.1021/bk-2002-0819.ch004
Shen, X.-M., and Clearfield, A. (1986). Phase transitions and ion exchange behavior of electrolytically prepared manganese dioxide. J. Solid State Chem. 64, 270–282. doi:10.1016/0022-4596(86)90071-X
Shi, C., Jing, Y., Xiao, J., Wang, X., Yao, Y., and Jia, Y. (2017). Solvent extraction of lithium from aqueous solution using non-fluorinated functionalized ionic liquids as extraction agents. Sep. Purif. Technol. 172, 473–479. doi:10.1016/j.seppur.2016.08.034
Shi, D., Zhang, L., Peng, X., Li, L., Song, F., Nie, F., et al. (2018). Extraction of lithium from salt lake brine containing boron using multistage centrifuge extractors. Desalination 441, 44–51. doi:10.1016/j.desal.2018.04.029
Shi, X.-c., Zhang, Z.-b., Zhou, D.-f., Zhang, L.-f., Bai-zhen, C., and Yu, L.-l. (2013). Synthesis of Li+ adsorbent (H2TiO3) and its adsorption properties. Trans. Nonferrous Metals Soc. China 23, 253–259. doi:10.1016/S1003-6326(13)62453-X
Snydacker, D. H., Hegde, V. I., Aykol, M., and Wolverton, C. (2018). Computational discovery of Li–M–O ion exchange materials for lithium extraction from brines. Chem. Mat. 30, 6961–6968. doi:10.1021/acs.chemmater.7b03509
Soffer, A., and Folman, M. (1972). The electrical double layer of high surface porous carbon electrode. J. Electroanal. Chem. Interfacial Electrochem. 38, 25–43. doi:10.1016/S0022-0728(72)80087-1
Srimuk, P., Su, X., Yoon, J., Aurbach, D., and Presser, V. (2020). Charge-transfer materials for electrochemical water desalination, ion separation and the recovery of elements. Nat. Rev. Mat. 5, 517–538. doi:10.1038/s41578-020-0193-1
Steiner, Z., Landing, W. M., Bohlin, M. S., Greaves, M., Prakash, S., Vinayachandran, P. N., et al. (2022). Variability in the concentration of lithium in the indo-pacific ocean. Glob. Biogeochem. Cycles 36, 6–7. doi:10.1029/2021GB007184
Stringfellow, W. T., and Dobson, P. F. (2021). Technology for the recovery of lithium from geothermal brines. Energies 14, 6805. doi:10.3390/EN14206805
Su, H., Tan, B., Zhang, J., Liu, W., Wang, L., Wang, Y., et al. (2022). Modelling of lithium extraction with TBP/P507–FeCl3 system from salt-lake brine. Sep. Purif. Technol. 282, 120110. doi:10.1016/j.seppur.2021.120110
Sukamto, J. P. H., Lilga, M. L., and Orth, R. K. (1998). Electrically switched cesium ion exchange. Tech. rep., United States. doi:10.2172/1118
Summerhayes, C. P., and Thorpe, S. A. (1996). Oceanography: An illustrated guide. New York, United States: John Wiley, 165–181. Chapter 11.
Sun, D., Zhou, T., Lu, Y., Yan, Y., Liu, C., and Che, G. (2022). Ion-imprinted antifouling nanocomposite membrane for separation of lithium ion. Korean J. Chem. Eng. 39, 2482–2490. doi:10.1007/s11814-022-1176-2
Sun, Y., Wang, Q., Wang, Y., Yun, R., and Xiang, X. (2021). Recent advances in magnesium/lithium separation and lithium extraction technologies from salt lake brine. Sep. Purif. Technol. 256, 117807. doi:10.1016/j.seppur.2020.117807
Swain, B. (2016). Separation and purification of lithium by solvent extraction and supported liquid membrane, analysis of their mechanism: A review. J. Chem. Technol. Biotechnol. 91, 2549–2562. doi:10.1002/jctb.4976
Takeuchi, T. (1980). Extraction of lithium from sea water with metallic aluminum. J. Nucl. Sci. Technol. 17, 922–928. doi:10.1080/18811248.1980.9732675
Tanaka, Y. (2015). 17 - bipolar membrane electrodialysis. Amsterdam: Elsevier, 369–392. doi:10.1016/B978-0-444-63319-4.00017-1
Torrejos, R. E. C., Nisola, G. M., Park, M. J., Beltran, A. B., Seo, J. G., Lee, S.-P., et al. (2015). Liquid–liquid extraction of Li+ using mixed ion carrier system at room temperature ionic liquid. Desalination Water Treat. 53, 2774–2781. doi:10.1080/19443994.2014.931534
Torrejos, R. E. C., Nisola, G. M., Song, H. S., Han, J. W., Lawagon, C. P., Seo, J. G., et al. (2016). Liquid-liquid extraction of lithium using lipophilic dibenzo-14-crown-4 ether carboxylic acid in hydrophobic room temperature ionic liquid. Hydrometallurgy 164, 362–371. doi:10.1016/j.hydromet.2016.05.010
Tran, K. T., Han, K. S., Kim, S. J., Kim, M. J., and Tran, T. (2016). Recovery of magnesium from Uyuni salar brine as hydrated magnesium carbonate. Hydrometallurgy 160, 106–114. doi:10.1016/j.hydromet.2015.12.008
Tran, K. T., Van Luong, T., An, J.-W., Kang, D.-J., Kim, M.-J., and Tran, T. (2013). Recovery of magnesium from Uyuni salar brine as high purity magnesium oxalate. Hydrometallurgy 138, 93–99. doi:10.1016/j.hydromet.2013.05.013
Trócoli, R., Battistel, A., and LaMantia, F. (2015). Nickel hexacyanoferrate as suitable Alternative to Ag for electrochemical lithium recovery. ChemSusChem 8, 2514–2519. doi:10.1002/cssc.201500368
Trócoli, R., Battistel, A., and Mantia, F. L. (2014). Selectivity of a lithium-recovery process based on LiFePO4. Chem. Eur. J. 20, 9888–9891. doi:10.1002/chem.201403535
Trócoli, R., Erinmwingbovo, C., and LaMantia, F. (2017). Optimized lithium recovery from brines by using an electrochemical ion-pumping process based on λ-MnO2 and nickel hexacyanoferrate. ChemElectroChem 4, 143–149. doi:10.1002/celc.201600509
Um, N., and Hirato, T. (2014). Precipitation behavior of Ca(OH)2, Mg(OH)2, and Mn(OH)2 from CaCl2, MgCl2, and MnCl2 in NaOH-H2O solutions and study of lithium recovery from seawater via two-stage precipitation process. Hydrometallurgy 146, 142–148. doi:10.1016/j.hydromet.2014.04.006
U.S Geological Survey (2022). Mineral commodity summary - lithium carbonate. United States: U.S Geological Survey.
USGS (2017). “Lithium. U.S. Geological Survey professional paper 1802-K,” in Critical mineral resources of the United States—economic and environmental geology and prospects for future supply (United States: USGS), 1, 34.
Venugopal, K., and Dharmalingam, S. (2016). Composite ion exchange membrane based electrodialysis cell for desalination as well as acid and alkali productions 3.
Vikström, H., Davidsson, S., and Höök, M. (2013). Lithium availability and future production outlooks. Appl. Energy 110, 252–266. doi:10.1016/J.APENERGY.2013.04.005
Voinov, M. (1982). MnO2: Structure and activity. Electrochimica Acta 27, 833–835. doi:10.1016/0013-4686(82)80204-1
Voutchkov, N. (2010). Introduction to reverse osmosis desalination - a SunCam online continuing education course. doi:10.13140/RG.2.2.13908.60801
Wang, C., Zhai, Y., Wang, X., and Zeng, M. (2014). Preparation and characterization of lithium λ-MnO2 ion-sieves. Front. Chem. Sci. Eng. 8, 471–477. doi:10.1007/s11705-014-1449-3
Wang, H., Ding, F., Jin, G., Li, C., and Meng, H. (2017). Ultra-thin graphene oxide intermediate layer for bipolar membranes using atomizing spray assembly. Colloids Surfaces A Physicochem. Eng. Aspects 520, 114–120. doi:10.1016/j.colsurfa.2017.01.041
Wang, J., Yue, X., Wang, P., Yu, T., Du, X., Hao, X., et al. (2022). Electrochemical technologies for lithium recovery from liquid resources: A review. Renew. Sustain. Energy Rev. 154, 111813. doi:10.1016/j.rser.2021.111813
Wang, L., Meng, C. G., Han, M., and Ma, W. (2008). Lithium uptake in fixed-pH solution by ion sieves. J. colloid interface Sci. 325, 31–40. doi:10.1016/j.jcis.2008.05.005
Wang, L., Meng, C. G., and Ma, W. (2009). Study on Li+ uptake by lithium ion-sieve via the pH technique. Colloids Surfaces A Physicochem. Eng. Aspects 334, 34–39. doi:10.1016/j.colsurfa.2008.09.050
Wang, S., Li, P., Cui, W., Zhang, H., Wang, H., Zheng, S., et al. (2016). Hydrothermal synthesis of lithium-enriched β-Li2TiO3 with an ion-sieve application: Excellent lithium adsorption. RSC Adv. 6, 102608–102616. doi:10.1039/C6RA18018C
Wang, S., Zhang, M., Zhang, Y., Zhang, Y., Qiao, S., and Zheng, S. (2019). High adsorption performance of the Mo-doped titanium oxide sieve for lithium ions. Hydrometallurgy 187, 30–37. doi:10.1016/j.hydromet.2019.05.004
Wang, X., Jing, Y., Liu, H., Yao, Y., Shi, C., Xiao, J., et al. (2018). Extraction of lithium from salt lake brines by bis[(trifluoromethyl)sulfonyl]imide-based ionic liquids. Chem. Phys. Lett. 707, 8–12. doi:10.1016/j.cplett.2018.07.030
Watanabe, A., Matsunaga, T., Abulikemu, A., Shimoda, K., Yamamoto, K., Uchiyama, T., et al. (2020). Structural analysis of imperfect Li2TiO3 crystals. J. Alloys Compd. 819, 153037. doi:10.1016/j.jallcom.2019.153037
Wei, S., Wei, Y., Chen, T., Liu, C., and Tang, Y. (2020). Porous lithium ion sieves nanofibers: General synthesis strategy and highly selective recovery of lithium from brine water. Chem. Eng. J. 379, 122407. doi:10.1016/j.cej.2019.122407
Weng, D., Duan, H., Hou, Y., Huo, J., Chen, L., Zhang, F., et al. (2020). Introduction of manganese based lithium-ion Sieve-A review. Prog. Nat. Sci. Mater. Int. 30, 139–152. doi:10.1016/j.pnsc.2020.01.017
Wilhelm, F. G., Pünt, I., van der Vegt, N. F. A., Wessling, M., and Strathmann, H. (2001). Optimisation strategies for the preparation of bipolar membranes with reduced salt ion leakage in acid–base electrodialysis. J. Memb. Sci. 182, 13–28. doi:10.1016/S0376-7388(00)00519-6
Williams, A. E., and McKibben, M. A. (1989). A brine interface in the Salton Sea Geothermal System, California: Fluid geochemical and isotopic characteristics. Geochimica Cosmochimica Acta 53, 1905–1920. doi:10.1016/0016-7037(89)90312-8
Wu, H. M., Belharouak, I., Abouimrane, A., Sun, Y.-K., and Amine, K. (2010). Surface modification of LiNi0.5Mn1.5O4 by ZrP2O7 and ZrO2 for lithium-ion batteries. J. Power Sources 195, 2909–2913. doi:10.1016/j.jpowsour.2009.11.029
Wu, H. M., Tu, J. P., Chen, X. T., Li, Y., Zhao, X. B., and Cao, G. S. (2007). Effects of Ni-ion doping on electrochemical characteristics of spinel LiMn2O4 powders prepared by a spray-drying method. J. Solid State Electrochem. 11, 173–176. doi:10.1007/s10008-005-0082-y
Xiao, J.-L., Sun, S.-Y., Wang, J., Li, P., and Yu, J.-G. (2013). Synthesis and adsorption properties of Li1.6Mn1.6O4 spinel. Ind. Eng. Chem. Res. 52, 11967–11973. doi:10.1021/ie400691d
Xiao, J. L., Sun, S. Y., Song, X., Li, P., and Yu, J. G. (2015b). Lithium ion recovery from brine using granulated polyacrylamide-MnO2 ion-sieve. Chem. Eng. J. 279, 659–666. doi:10.1016/j.cej.2015.05.075
Xiao, J., Nie, X., Sun, S., Song, X., Li, P., and Yu, J. (2015a). Lithium ion adsorption–desorption properties on spinel Li4Mn5O12 and pH-dependent ion-exchange model. Adv. Powder Technol. 26, 589–594. doi:10.1016/j.apt.2015.01.008
Xie, F., Zhang, T. A., Dreisinger, D., and Doyle, F. (2014). A critical review on solvent extraction of rare earths from aqueous solutions. Miner. Eng. 56, 10–28. doi:10.1016/j.mineng.2013.10.021
Xiong, Y., Ge, T., Xu, L., Wang, L., He, J., Zhou, X., et al. (2022). A fundamental study on selective extraction of Li+ with dibenzo-14-crown-4 ether: Toward new technology development for lithium recovery from brines. J. Environ. Manag. 310, 114705. doi:10.1016/j.jenvman.2022.114705
Xu, H., Xu, L., Chen, B.-z., Shi, X.-c., and Yang, X. (2009). Separating technique for magnesium and lithium from high Mg/Li ratio salt lake brine. J. Central South Univ. Sci. Technol. 40, 36–40.
Xu, N., Li, S., Guo, M., Qian, Z., Li, W., and Liu, Z. (2019). Synthesis of H4Mn5O12 nanotubes lithium ion sieve and its adsorption properties for Li+ from aqueous solution. ChemistrySelect 4, 9562–9569. doi:10.1002/slct.201901764
Xu, W., Yuan, A., Tian, L., and Wang, Y. (2011). Improved high-rate cyclability of sol–gel derived Cr-doped spinel LiCryMn2 yO4 in an aqueous electrolyte. J. Appl. Electrochem. 41, 453–460. doi:10.1007/s10800-011-0255-6
Xu, X., Chen, Y., Wan, P., Gasem, K., Wang, K., He, T., et al. (2016). Extraction of lithium with functionalized lithium ion-sieves. Prog. Mater. Sci. 84, 276–313. doi:10.1016/j.pmatsci.2016.09.004
Xu, X., Zhou, Y., Feng, Z., Kahn, N. U., HaqKhan, Z. U., Tang, Y., et al. (2018). A self-supported λ-MnO2 film electrode used for electrochemical lithium recovery from brines. ChemPlusChem 83, 521–528. doi:10.1002/cplu.201800185
Xue, S., Wu, C., Wu, Y., Chen, J., and Li, Z. (2015). Bipolar membrane electrodialysis for treatment of sodium acetate waste residue. Sep. Purif. Technol. 154, 193–203. doi:10.1016/j.seppur.2015.09.040
Yaksic, A., and Tilton, J. E. (2009). Using the cumulative availability curve to assess the threat of mineral depletion: The case of lithium. Resour. Policy 34, 185–194. doi:10.1016/J.RESOURPOL.2009.05.002
Yang, H. J., Li, B., Chai, X. L., and Li, W. (2013). Studies on the interaction mechanism between lithium chloride and amorphous Al(OH)<sub>3</sub>. Adv. Mat. Res. 634-638, 126–129. doi:10.4028/www.scientific.net/AMR.634-638.126
Yang, S., Zhang, F., Ding, H., He, P., and Zhou, H. (2018). Lithium metal extraction from seawater. Joule 2, 1648–1651. doi:10.1016/j.joule.2018.07.006
Yang, Y., Gao, X., Fan, A., Fu, L., and Gao, C. (2014). An innovative beneficial reuse of seawater concentrate using bipolar membrane electrodialysis. J. Membr. Sci. 449, 119–126. doi:10.1016/j.memsci.2013.07.066
Yoon, H., Lee, J., Kim, S., and Yoon, J. (2019). Review of concepts and applications of electrochemical ion separation (EIONS) process. Sep. Purif. Technol. 215, 190–207. doi:10.1016/j.seppur.2018.12.071
Yu, C., Lu, J., Dai, J., Dong, Z., Lin, X., Xing, W., et al. (2020). Bio-inspired fabrication of Ester-functionalized imprinted composite membrane for rapid and high-efficient recovery of lithium ion from seawater. J. Colloid Interface Sci. 572, 340–353. doi:10.1016/J.JCIS.2020.03.091
Zandevakili, S., Ranjbar, M., and Ehteshamzadeh, M. (2014). Recovery of lithium from Urmia Lake by a nanostructure MnO 2 ion sieve. Hydrometallurgy 149, 148–152. doi:10.1016/j.hydromet.2014.08.004
Zante, G., Boltoeva, M., Masmoudi, A., Barillon, R., and Trébouet, D. (2019). Lithium extraction from complex aqueous solutions using supported ionic liquid membranes. J. Membr. Sci. 580, 62–76. doi:10.1016/j.memsci.2019.03.013
Zavahir, S., Elmakki, T., Gulied, M., Ahmad, Z., Al-Sulaiti, L., Shon, H. K., et al. (2021). A review on lithium recovery using electrochemical capturing systems. Desalination 500, 114883. doi:10.1016/j.desal.2020.114883
Zhang, L., Zhou, D., Yao, Q., and Zhou, J. (2016). Preparation of H2TiO3-lithium adsorbent by the sol–gel process and its adsorption performance. Appl. Surf. Sci. 368, 82–87. doi:10.1016/j.apsusc.2016.01.203
Zhang, Q. H., Li, S. P., Sun, S. Y., Yin, X. S., and Yu, J. G. (2009). Lithium selective adsorption on 1-D MnO2 nanostructure ion-sieve. Adv. Powder Technol. 20, 432–437. doi:10.1016/j.apt.2009.02.008
Zhang, X., Zhao, W., Zhang, Y., and Jegatheesan, V. (2021a). A review of resource recovery from seawater desalination brine. Rev. Environ. Sci. Biotechnol. 20, 333–361. doi:10.1007/s11157-021-09570-4
Zhang, Y., Hu, Y., Wang, L., and Sun, W. (2019). Systematic review of lithium extraction from salt-lake brines via precipitation approaches. Miner. Eng. 139, 105868. doi:10.1016/j.mineng.2019.105868
Zhang, Y., Paepen, S., Pinoy, L., Meesschaert, B., and Van der Bruggen, B. (2012). Selectrodialysis: Fractionation of divalent ions from monovalent ions in a novel electrodialysis stack. Sep. Purif. Technol. 88, 191–201. doi:10.1016/j.seppur.2011.12.017
Zhang, Y., Sun, W., Xu, R., Wang, L., and Tang, H. (2021b). Lithium extraction from water lithium resources through green electrochemical-battery approaches: A comprehensive review. J. Clean. Prod. 285, 124905. doi:10.1016/J.JCLEPRO.2020.124905
Zhao, B., Guo, M., Qian, Z., Li, J., Wu, Z., and Liu, Z. (2020a). The adsorption behavior of lithium on spinel titanium oxide nanosheets with exposed (114) high-index facets. Dalton Trans. 49, 14180–14190. doi:10.1039/D0DT02960B
Zhao, C., Zhang, Y., Cao, H., Zheng, X., Van Gerven, T., Hu, Y., et al. (2019). Lithium carbonate recovery from lithium-containing solution by ultrasound assisted precipitation. Ultrason. Sonochemistry 52, 484–492. doi:10.1016/j.ultsonch.2018.12.025
Zhao, X., Feng, M., Jiao, Y., Zhang, Y., Wang, Y., and Sha, Z. (2020b). Lithium extraction from brine in an ionic selective desalination battery. Desalination 481, 114360. doi:10.1016/j.desal.2020.114360
Zhao, X., Jiao, Y., Xue, P., Feng, M., Wang, Y., and Sha, Z. (2020c). Efficient lithium extraction from brine using a three-dimensional nanostructured hybrid inorganic-gel framework electrode. ACS Sustain. Chem. Eng. 8, 4827–4837. doi:10.1021/acssuschemeng.9b07644
Zhao, X., Li, G., Feng, M., and Wang, Y. (2020d). Semi-continuous electrochemical extraction of lithium from brine using CF-NMMO/AC asymmetric hybrid capacitors. Electrochimica Acta 331, 135285. doi:10.1016/j.electacta.2019.135285
Zhao, Z., Liu, G., Jia, H., and He, L. (2020e). Sandwiched liquid-membrane electrodialysis: Lithium selective recovery from salt lake brines with high Mg/Li ratio. J. Membr. Sci. 596, 117685. doi:10.1016/j.memsci.2019.117685
Zhou, Z., Qin, W., and Fei, W. (2011). Extraction equilibria of lithium with tributyl phosphate in three diluents. J. Chem. Eng. Data 56, 3518–3522. doi:10.1021/je200246x
Zymon, W., and Kurbiel, J. (1986). “Application of previously precipitated active aluminium hydroxide (AAH) for removal of refractory substances from wastewater,” in Chemistry for protection of the environment 1985. Editors L. Pawlowski, G. Alaerts, and W. Lacy (Amsterdam, Netherlands: Elsevier), 29, 345–353. doi:10.1016/S0166-1116(08)70951-8
Keywords: low Li concentration aqueous extraction, aqueous lithium extraction, direct lithium extraction, DLE technology review, sustainable lithium recovery, lithium resources, critical minerals, seawater extraction
Citation: Murphy O and Haji MN (2022) A review of technologies for direct lithium extraction from low Li+ concentration aqueous solutions. Front. Chem. Eng. 4:1008680. doi: 10.3389/fceng.2022.1008680
Received: 01 August 2022; Accepted: 10 November 2022;
Published: 30 November 2022.
Edited by:
Costas Tsouris, Oak Ridge National Laboratory (DOE), United StatesReviewed by:
Yang Zhang, Qingdao Institute of Bioenergy and Bioprocess Technology (CAS), ChinaCopyright © 2022 Murphy and Haji. This is an open-access article distributed under the terms of the Creative Commons Attribution License (CC BY). The use, distribution or reproduction in other forums is permitted, provided the original author(s) and the copyright owner(s) are credited and that the original publication in this journal is cited, in accordance with accepted academic practice. No use, distribution or reproduction is permitted which does not comply with these terms.
*Correspondence: Olivia Murphy, b202NkBjb3JuZWxsLmVkdQ==
Disclaimer: All claims expressed in this article are solely those of the authors and do not necessarily represent those of their affiliated organizations, or those of the publisher, the editors and the reviewers. Any product that may be evaluated in this article or claim that may be made by its manufacturer is not guaranteed or endorsed by the publisher.
Research integrity at Frontiers
Learn more about the work of our research integrity team to safeguard the quality of each article we publish.