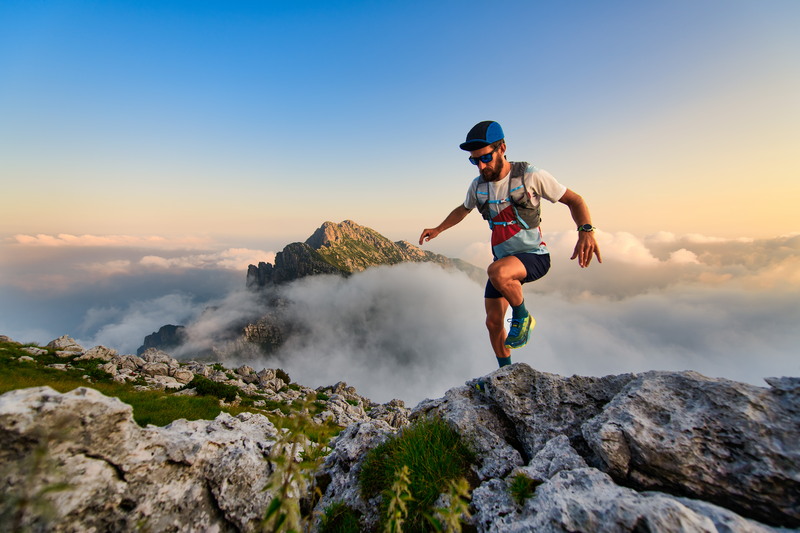
95% of researchers rate our articles as excellent or good
Learn more about the work of our research integrity team to safeguard the quality of each article we publish.
Find out more
ORIGINAL RESEARCH article
Front. Chem. Eng. , 13 December 2021
Sec. Catalytic Engineering
Volume 3 - 2021 | https://doi.org/10.3389/fceng.2021.789416
This article is part of the Research Topic Hierarchical and Multifunctional Materials in Chemical Engineering: Synthesis Strategies and Processing Challenges View all 7 articles
Sol-gel-based silica monoliths with hierarchical mesopores/macropores are promising catalyst support and flow reactors. Here, we report the successful preparation of cylindrically shaped Pt-loaded silica monoliths (length: 2 cm, diameter: 0.5 cm) with a variable mean macropore width of 1, 6, 10, or 27 μm at a fixed mean mesopore width of 17 nm. The Pt-loaded monolithic catalysts were housed in a robust cladding made of borosilicate glass for use as a flow reactor. The monolithic reactors exhibit a permeability as high as 2 μm2 with a pressure drop below 9 bars over a flow rate range of 2–20 cm3 min−1 (solvent: water). The aqueous-phase hydrogenation of p-nitrophenol to p-aminophenol with NaBH4 as a reducing agent was used as a test reaction to study the influence of mass transfer on catalytic activity in continuous flow. No influence of flow rate on conversion at a fixed contact time of 2.6 s was observed for monolithic catalysts with mean macropore widths of 1, 10, or 27 µm. As opposed to earlier studies conducted at much lower flow velocities, this strongly indicates the absence of external mass-transfer limitations or stagnant layer formation in the macropores of the monolithic catalysts.
Flow chemistry represents an enabling technology for various chemical transformations that are difficult or impossible to conduct in batch (Baumann et al., 2020) due to multiple advantages, such as realization of high surface-to-volume ratio, efficient mixing, improved heat and mass transfer, and increased selectivity and safety (Plutschack et al., 2017; Akwi and Watts, 2018). One of the widely studied tubular flow reactors is packed bed reactors (PBRs) as they are easy to design and to operate (Perry and Green, 2008). However, PBRs often suffer from problems such as inhomogeneous particle size distribution, high pressure drop, catalyst attrition, maldistribution of fluid, hot spot generation, and creation of stagnant fluid zones (Juan A. Conesa, 2019) (Levenspiel, 1999). In a PBR, the particle size can be reduced to decrease mass-transfer limitations and to increase the available surface area; however, in doing so, the overall bed porosity is reduced, resulting in lower permeability and elevated pressure drop. The problem persists even in the case of a PBR consisting of porous particles (Daneyko et al., 2011). Hence, it is difficult to tune the space available for convective mass transfer, the surface area, and the diffusion lengths simultaneously in a packed bed.
Hierarchical mesoporous/macroporous silica monoliths (HSMs) synthesized via the sol-gel technique (Lu et al., 2020) possess conducive textural properties such as high porosity and large surface-to-volume ratio for use as catalyst support in flow reactors (Enke et al., 2016; Mrowiec-Białoń et al., 2018). The sol-gel synthesis of HSMs applied to date is derived from the root method, i.e., the so-called Nakanishi procedure, that was originally developed for the preparation of monolithic silica materials for column chromatography applications (Nakanishi and Soga, 1991). The method consists of the sol-gel transition and polymer-assisted phase separation (hydrogel and solvent phases) that results in a fixation of the microporous/macroporous structure by polycondensation of silica oligomers. During alkaline treatment, micropores disappear and mesopores are formed by Ostwald ripening, resulting in a mesoporous/macroporous HSM (Nakanishi et al., 2007). The precise control over the hierarchical arrangement of mesopore and macropore domains in HSM is determined by the conditions of the synthesis procedure. The HSM consists of a porous silica skeleton containing nanoscale intraskeleton mesopores and microscale interskeleton macropore space. The large macropores allow fast advection-dominated mass transfer, while the small mesopores contribute a large surface area for catalyst loading and activity. Macropores provide the deterministic length scale for the bulk fluid flow analogous to the void spaces in a packed bed, while the skeleton thickness defines the diffusion length the same way as the one provided by the particle diameter (Leinweber et al., 2002; Vervoort et al., 2003; Saito et al., 2006; Fletcher et al., 2011; Stoeckel et al., 2015).
A practical advantage of HSMs is that we present a seamless monolith with the physical dimensions of the container within which the gel was dried. In this way, a desired reactor geometry can be realized for flow catalysis by merely hosting the HSM inside a viable cladding material. Owing to the extensively studied surface chemistry and versatility in synthesis steps, HSM supports can be functionalized via in situ as well as post-synthesis treatment with a variety of moieties and applied in numerous catalytic applications. Recent studies show successful implementation of silica monolithic catalysts as flow reactors in various chemical and biochemical transformations (El Kadib et al., 2009; Sachse et al., 2010; Linares et al., 2012; Sachse et al., 2012; Sachse et al., 2013; Szymańska et al., 2013; Hakat et al., 2016; Ciemięga et al., 2017; Haas et al., 2017; Liguori et al., 2017; Pélisson et al., 2017; Mrowiec-Białoń et al., 2018; Russell et al., 2020; Yamada et al., 2020; Ahmad et al., 2021; Turke et al., 2021).
However, to make use of the full potential of HSMs as flow reactors, several challenges still have to be overcome. The role of macropore width in relation to diffusion limitations therein and its effect on the catalytic activity have not been studied systematically. This is because the independent tuning of mesopore and macropore widths during the sol-gel synthesis while maintaining the specific surface area, pore volume, and/or porosity is challenging. The knowledge and general understanding on the macropore width needed to overcome the external, i.e., diffusion limitations within macropores, or stagnant layer formation therein, however, are crucial to enable the key advantage of improved mass transfer in HSMs (as compared to PBRs). Furthermore, it is difficult to wrap a reliably tight cladding around the monolith without compromising its mechanical integrity and restricting fluid bypass. Although the monoliths are hailed as promising reactors in flow applications, most of the studies were reported at low flow rates (1–2 cm3 min−1) and large contact times with very few exceptions (Szymańska et al., 2013). This seriously undermines the advantages of low pressure drop and focuses on mass-transfer investigation in flow conditions not relevant for practical applications. Another reason for this is the absence of a suitable (i.e., intrinsically fast) test reaction to observe the effect of advection-dominated mass transfer in macropores in relation to the catalytic activity at high fluid flow rates (>5 cm3 min−1).
This study is aimed to investigate the influence of macropore width on the catalytic activity of Pt-containing HSMs with reference to mass-transfer limitations in a catalytic aqueous-phase conversion in continuous flow. To address these issues, we used a modified synthesis approach to prepare HSMs with a variation of mean macropore width (wmacro) but a fixed mean mesopore width (wmeso). The other textural properties of the monoliths such as porosity and specific surface area were also fixed in a narrow range. The average skeleton thickness also varied in conjunction to the average macropore width. Borosilicate glass was used as a simple yet versatile cladding material for the synthesized HSM as opposed to largely used materials such as PEEK, heat-shrinkable PTFE, and epoxy resin. To observe the mechanical stability of the cladded monoliths and their hydrodynamic behavior in flow, permeability tests were performed. Various pressure drop–flow rate curves were generated for monoliths of varying wmacro to calculate permeabilities as a measure of flow characteristics related to the available macropore space. The dimensionless Reynolds number was calculated to envisage the transport phenomena due to bulk fluid transport in macropores. To investigate the role of monolith textural properties on catalytic activity with respect to mass-transfer limitations, the hydrogenation of p-nitrophenol (PNP) to p-aminophenol (PAP) using sodium borohydride (NaBH4) as reducing agent was employed as test reaction (Aditya et al., 2015). Previously, the PNP hydrogenation was successfully used to investigate mass-transfer limitations for Pt- and Pd-loaded catalysts in batch setup (Goepel et al., 2014; Al-Naji et al., 2015). The application of PNP hydrogenation was also investigated in flow microreactors at low flow rates; however, the reaction parameters were challenging to control such as self-hydrolysis of NaBH4 and the associated bubbling due to hydrogen release that reduced the available catalyst surface (Liu et al., 2017). During catalytic application of Pt-loaded monolithic flow reactors, the role of the variation of wmacro was investigated in possible mass-transfer limitations with reference to catalytic activity. Furthermore, the effect of the variation of reactants’ volumetric flow rate on catalytic conversion was examined for probability of stagnant layer formation at the fluid–skeleton interface influencing the mass transfer.
Sodium borohydride (NaBH4) (≥96%), tetraethyl orthosilicate (Si(OC2H5)4) (≥99%), and urea (CH4N2O) (≥99.5%) were purchased from Merck (Darmstadt, Germany). Polyethylene oxide (PEO, –CH2CH2O–)n (98%, M.W. 100,000 or 100 kDa) and p-nitrophenol (C6H5NO3) (99%) were purchased from Alfa Aesar (Haverhill, MA), and tetraammineplatinum(II) chloride hydrate (Pt (NH3)4Cl2·H2O) (98%) and Pluronic® F-127 were purchased from Sigma-Aldrich (Merck, Darmstadt, Germany). Ammonia (NH3) (25%) and sulfuric acid (H2SO4) (95%) were purchased from VWR International GmbH (Darmstadt, Germany). The deionized water used for solution preparations and aqueous-phase reactions was prepared using PURELAB Flex dispenser by Elga-Veolia (ELGA LabWater, Celle, Germany), with conductivities <0.055 µS. All the chemicals were used as purchased without further purification.
The HSMs with mesoporous/macroporous structure were synthesized using an already-established sol-gel procedure using PEO as a structure directing agent and urea as pore controlling agent. Urea proved to be a very suitable pore controlling agent, especially with respect to the mean mesopore width due to homogeneous pore widening during hydrothermal treatment (Kohns et al., 2018). However, to independently alter mean macropore width and to keep the mean mesopore width constant, the present synthesis procedure was modified via tuning of the gelation temperature (Meinusch et al., 2017).
The preparation of HSMs is adapted from Kohns et al. (2018). First, 1.8–2.2 g of PEO (M.W. 100 kDa), 2.2 g of urea, and 18 g of deionized water were added under vigorous stirring (in case of Mono-27, 0.5 g Pluronic® F-127 was added too). To this solution, 0.7–1.4 cm3 of sulfuric acid and 15.5 cm3 of tetraethyl orthosilicate were added under continuous stirring for 30 min. The reaction mixture turned into a viscous gel, which was poured into polytetrafluoroethylene (PTFE) tubes (7 mm inner diameter and 10 cm length) embedded in a PTFE block. The PTFE block was placed in a steel autoclave (300 cm3) for gelation at the temperature range of 313–328 K for 24 h. The autoclave was placed in an oven for aging and hydrothermal treatment at 393 K for 20 h. After cooling to room temperature, the wet gels were transferred to a flat trough (volume = 2,000 cm3) for five to six cycles of washing with distilled water until a neutral pH was obtained (taking approximately 6 h). The gels were dried at 393 K for 24 h by placing them horizontally in plastic vessels covered with water provided with a small leak in their lids resulting in crack-free HSMs (Kohns et al., 2021). The calcination was performed for 8 h with the temperature ramp of 3 K min−1 from room temperature to 873 K in a muffle furnace in air atmosphere. This way, four monoliths with constant mean mesopore width (16–19 nm) and mean macropore widths of 1 µm (2.2 g of PEO, 2.2 g of urea, and 1.4 cm³ of H2SO4, Tgelation = 323 K, sample code: Mono-1), 6 µm (2.0 g of PEO, 2.2 g of urea, and 1.4 cm³ of H2SO4, Tgelation = 323 K, Mono-6), 10 µm (1.8 g of PEO, 2.2 g of urea, and 1.4 cm³ of H2SO4, Tgelation = 323 K, Mono-10), and 27 µm (2.0 g of PEO, 0.5 g of F-127, 2.2 g of urea, and 0.7 cm³ of H2SO4, Tgelation = 313 K, Mono-27) were synthesized. The obtained monolithic rods each had the dimensions of 0.5 cm diameter (D) and 9 cm length (L). A paper cutter was used to cut a monolith into the desired length. This allowed for the subsequent use of monoliths in permeability analysis, catalyst loading, and material characterization without losing the shape.
The permeability test experiments were performed with the HSM samples containing mean macropore width, wmacro = 1, 6, 10, and 27 μm, to depict the influence of the varying wmacro on the fluid dynamics when pressure-induced flow was applied across the monolith. The monoliths were cut into 2 cm long pieces (diameter = 0.5 cm) using a paper cutter. Each piece was inserted into a borosilicate glass tube with 0.5 cm inner diameter and 0.5 mm wall thickness. The glass was heated with a flame to 1,773 K for ∼20 s and then pressed around the monolith. The glass was then allowed to cool at room temperature for ∼2–3 min until it took a seamless shape around the monolith external lateral surface. This ensured a tight contact of glass around the monolith without bypass. The glass-cladded monoliths were connected to a FLUSYS™ HPLC pump via Swagelok® Ultra-Torr fitting, and deionized water was used as the transporting fluid. The volumetric flow rate of water was varied over the range 2–20 cm3 min−1 at an increment rate of 2 cm3 min−1. All experiments were conducted at 398 K. The fluid was kept flowing at a specific flow rate until a steady state (i.e., a constant pressure drop) was achieved, and the corresponding pressure drop was measured using an electronic pressure transducer located upstream of the reactor. In case of pressure-driven flow through a porous material such as silica monoliths, the value of permeability (K) was calculated by Darcy’s law (Eq. 1) (Bear and Corapcioglu, 1972), where pressure drop (ΔP) across the porous material is a direct function of the fluid volumetric flow rate (q), the fluid viscosity (ƞ), and the length (L) of material in the direction of flow, while it is an indirect function of the cross-sectional area (A) perpendicular to the direction to flow.
The relationship is essentially a straight line between the flow rate and pressure drop if the flow is laminar. In that case, the slope provides information about the permeability of the material.
Before loading, the catalysts (Mono-1, Mono-10, and Mono-27) were pretreated in a vacuum oven at 343 K and 10 kPa for 24 h. The monoliths (0.5 cm diameter and 8 cm length) were then submerged into 20 cm3 of deionized water in an Erlenmeyer flask. The pH of the deionized water was adjusted to 10 by dropwise addition of 1 M ammonia solution, and the monoliths were kept in this solution for 1 h while stirring at 100 min−1. A 0.1 m aqueous solution of tetraammineplatinum(II) chloride hydrate was added dropwise with an aimed mass fraction of 1.5 wt.-% Pt relative to the mass of the monolith. The solution containing the monolith was stirred for 24 h (100 min−1) with pH readjusted to 10 every 3 h. The Pt-loaded monoliths were taken out, washed with 30 cm3 of deionized water until the pH was neutral, and dried for 48 h at 338 K in air atmosphere. The monoliths were calcined at 423 K for 16 h with flowing air at the flow rate of 70 cm3 min−1. Finally, reduction was performed at 623 K for 4 h at a temperature ramp of 5 K min−1 in 10 vol.-% H2 in N2 atmosphere.
The nitrogen physisorption experiments were performed on BELSORP®-miniX (Microtrac Retsch GmbH, Haan, Germany). The samples were pretreated for 24 h at 393 K under vacuum before measurement. The Brunauer–Emmett–Teller (BET) equation was used to calculate the specific surface area (p/p0 = 0.05–0.35). The mercury intrusion porosimetry (MIP) was conducted on a PoreMaster® (Quantachrome Instruments, Boynton Beach, FL) from 0.02 to 400 MPa. The mercury contact angle was set at 141°, and a surface tension of 0.48 N m−1 was used for the determination of pore widths, porosity, and specific pore volume. Pore width distribution in MIP was determined using the Washburn equation, assuming cylindrical pores in the software package [SOLID-SOLver of Intrusion Data (Version 1.6.6)]. The standard deviation for the determination of macropore width (wmacro) and mesopore width (wmeso) is ±10% and ±5%, respectively. Scanning electron microscopy (SEM) was performed using a Leo 1530 device (Zeiss, Oberkochen, Germany). The samples were placed on carbon tabs and glued with silver paste. For conductivity, the samples were sputtered with gold and investigated with a high tension of 5 kV. The monolith sample images were investigated at equal magnification for overall distribution of macropores. The skeleton thickness (ws) was calculated by taking the average of 100 measurements from the SEM images for each sample.
The Pt content of all catalysts was determined by optical emission spectroscopy with inductively coupled plasma (ICP-OES) using a Perkin Elmer Optima 8000 instrument (Waltham, USA). The wavelength chosen was 265.954 nm. Quantification was based on external calibrations. Prior to analysis, the solid samples were dissolved in concentrated acids (HCl, HNO3, and HF), applying microwave digestion. For the determination of Pt content in the core and periphery of the monolith, the outside of the monolith was cut off using a paper cutter up to a reduced diameter of 2.5 mm and then subsequently crushed and analyzed via ICP-OES after digestion. The remaining core was then also crushed and analyzed via ICP-OES after digestion. Scanning transmission electron microscopy (STEM) and transmission electron microscopy (TEM) were performed on JEM-2100 Plus (JEOL, Tokyo, Japan) operated at a 200 kV acceleration voltage. An Octane-T-Optima-30 (AMETEK, Berwyn, United States) detector was used for chemical analysis. The samples were mortared in ethanol, and a droplet was transferred to a TEM grid. For TEM tomography, a dual-axis tomography holder model 2040 (Fischione, PA, United States) was used where high tilt angles of ±70° could be achieved. Data reconstruction was performed by IMOD package version 4.11 and segmentation by a thresholding technique. The energy-dispersive X-ray (EDX) analysis was performed via a Bruker XFlash 6130 detector at high tension (20 kV), and hydrogen chemisorption was performed on an Autosorb-iQ® (Quantachrome Instruments, Boynton Beach, FL, United States).
The Pt-loaded HSM catalysts with mean wmacro, 1 and 27 μm, and diameter (D = 0.5 cm) were cut into four different lengths (L = 0.25, 0.5.1.0, and 2.0 cm) and cladded in borosilicate glass (see Permeability Test Experiments). The contact time of the reactants in the flow reactor was used as a fixed parameter to investigate the effect of mass-transfer limitations due to the variation of wmacro at different volumetric flow rates. A specific flow was maintained for the reactor of a particular length so that the contact time remains the same. For a cylindrical monolithic reactor, the contact time (tc) was calculated using the following equation:
where r is the monolith radius, L is the monolith length, q is the volumetric flow rate, and εT is the total porosity. The εT was calculated from Eq. 3 using the total pore volume (VTp) determined from MIP (Eq. 4) for the density (ρSilica = 2.2 g cm−3) of the silica monolith.
The flow rates were varied from q = 1 to 8 cm3 min−1 corresponding to the lengths of reactors from L = 0.25 to 2.0 cm, respectively. In this way, it was possible to observe conversion at steady state for each reactor at a fixed contact time and varying flow rates.
For each reaction run, the freshly prepared aqueous reactant mixture (0.4 mm PNP and 1.6 mm NaBH4) was pumped through the monolithic reactor. The reaction is reported as pseudo-first order with respect to PNP with an excess reducing agent (Gu et al., 2015). An Avantes (Apeldoorn, the Netherlands) AvaSpec-3648 high-resolution fiber-optic UV-Vis spectrometer with a reflectance-type dip probe was used to monitor the reactant concentration downstream of the reactor (Supplementary Figure S1). The PNP solution is light yellow in color and provides an absorbance peak at a wavelength of 313 nm. However, when aqueous solution of NaBH4 is added, the PNP anion is formed along with in situ generation of hydrogen. The hydrogenation of PNP to PAP initiates as soon as the reaction mixture comes into contact with a suitable active catalyst such as Pt. The absorbance peak at 400 nm was used for quantification of conversion as given in Goepel et al. (2014). No Pt leaching was observed via elemental analysis of the reactor effluent by ICP-OES.
The silica monoliths prepared by the sol-gel procedure possess a seamless, cylindrical morphology without cracks or bends along any physical dimension. Each monolith measures 0.5 cm in diameter and ∼9 cm in length. The characterization using MIP shows that each monolithic sample exhibits a bimodal mesoporous/macroporous pore width distribution. A variation of mean macropore width (wmacro) in the sequence of 1, 6, 10, and 27 µm is obtained while the mean mesopore width (wmeso) remains in a narrow range of 16–19 nm (Figure 1). The total porosity (εT) is comparable for all samples in the range of 87%–90%. Also, the specific volumes of the macropore (Vmacro) and the mesopore (Vmeso) systems are maintained in the range of 2.05–3.42 cm3 g−1 and 0.83–0.91 cm3 g−1, respectively. As expected, the increase in PEO as pore generator systematically decreases the mean macropore width (Kohns et al., 2018). The nitrogen physisorption isotherms (Figure 2) depict Type IV(a) isotherms with hysteresis that are typical of mesoporous material. In each sample, the hysteresis shape is defined by the empirical classification of the H1 type (Schlumberger and Thommes, 2021), suggesting that the monoliths consist of independent cylindrical pores without pore blockage with a three-dimensionally arranged ordered network in the overall sample. The BET surface area for all the monolith samples calculated from the nitrogen physisorption data is in a narrow range of 195–202 m2 g−1. Since there is no visible plateau in the physisorption isotherms for all these samples, the mean mesopore width identified by MIP is considered reliable. Nonetheless, there appears to be a convergence at the highest achievable pressure, depicting possibly unique and close values of mean mesopore widths.
FIGURE 1. Pore width distributions and contribution of the hierarchical arrangement of macropores and mesopores for HSM samples Mono-1 to Mono-27 analyzed via MIP.
The SEM images (Figure 3) show homogeneously distributed macropores throughout the samples separated by the silica skeleton thickness unique to each sample. The skeleton thickness (ws) increases consistently from 2 to 15 µm with increasing average macropore widths (from 1 to 27 µm). The detailed textural properties of the HSM samples are presented in Table 1.
FIGURE 3. SEM images of HSM samples (Mono-1 through Mono-27) exhibiting the homogeneous arrangement and size of macropores and the growth and thickness of the silica skeleton inside the overall structure.
TABLE 1. Textural properties [macropore width (wmacro), macropore volume (Vmacro), monolith skeleton thickness (ws), mesopore width (wmeso), mesopore volume (Vmeso), total porosity (εT), and BET surface area (SBET)] of the synthesized HSMs.
With water (ƞ = 0.89 cP at 298 K) as transporting fluid, all the silica monolith samples (Mono-1 to Mono-27) with dimensions L = 2 cm, D = 0.5 cm, and A = 0.196 cm2, exhibited a linear relationship, thus obeying Darcy’s law (Figure 4A). This linearity provided a value of permeability for each of the monoliths having a particular mean macropore width considered over the flow rate range 2–20 cm3 min−1 (Figure 4B). The permeabilities were 0.32, 0.46, 0.89, and 2.07 µm2 for samples Mono-1, Mono-6, Mono-10, and Mono-27, respectively. The values of permeability are ideal in terms of application of these monoliths in flow catalysis (Galarneau et al., 2016a). The maximum pressure recorded was only 900 kPa or 9 bar for Mono-1 at 20 cm3 min−1. The observed permeabilities suggest mechanically stable and homogeneously distributed macropores (Kohns et al., 2018). When hierarchical monoliths are applied as flow systems, the convective transport in macropores works in conjunction with the diffusive mass transfer in mesopores. Seeking analogy with a packed bed, the dimensionless Reynolds number (Re) is given by the relationship (Leinweber and Tallarek, 2003) (Eq. 5):
where
FIGURE 4. (A) Pressure drop relative to the applied volumetric flow rate of water across the glass-cladded HSM samples (Mono-1 to Mono-27) of L = 2 cm, D = 0.5 cm, and A = 0.196 cm2 at T = 298 K. (B) The calculated permeabilities as a function of the mean macropore width of the HSM.
For a particulate bed of typical interparticle porosity (εp) of 0.36 (Tallarek et al., 2002), a particle size of 20 µm is equivalent to a mean macropore width of 1 µm in the monolith, while a particle size of 65 µm is equivalent to a 27 µm mean macropore width in a monolith corresponding to the same permeability values. A high permeability maintaining a low pressure drop is technically desirable since it allows the monoliths to operate in a high-flow-rate regime without high cost and mechanical stress that would be caused by high backpressure. The residence time distribution was also investigated for one of the HSM samples (Mono-6) to complement the observed flow behavior. Pulse inputs were given with a 0.5 mm aqueous solution of p-nitrophenol as a tracer (Supplementary Figure S2). The residence time distribution for an empty borosilicate glass was compared with one having the monolith inserted in it for volumetric flow rates of 2 and 4 cm3 min−1. The distributions completely overlapped each other, exhibiting no indication of maldistribution of the solute due to the presence of the monolith structure. Also, the tailing was observed to be reduced when the flow rate was shifted from a lower to a higher value of flow rate, which indicates a shift towards the ideal plug flow characteristics (Levenspiel, 1999).
The Pt-loaded HSMs with mean wmacro, 1, 10, and 27 μm, were chosen to study the role of the macropore width variation from the smallest to largest values in our samples on the catalytic activity in relation to mass-transfer limitations. The monolithic catalysts and subsequently the reactors hosting these catalysts were interchangeably called MonoCat-1, MonoCat-10, and MonoCat-27 for ease of discussion. The elemental analysis via ICP-OES indicated 1.22, 1.18, and 1.57 wt.-% of Pt in MonoCat-1, MonoCat-10, and MonoCat-27, respectively. The elemental analysis performed at two different sections of the monolith, i.e., the peripheral and the core regions, shows comparable metal loading (periphery: 1.18 wt.-%, core: 0.98 wt.-%) in depth along the monolith diameter for MonoCat-10 (Figure 5A). The SEM-EDX elemental line scan analyzed along the monolith diameter from the periphery towards the center of the monolith also exhibited a homogeneous distribution of Pt along the radial distance for MonoCat-1 (Figure 5B). The platinum nanoparticles (NPs) exhibit a distribution with an arithmetic mean of 3.1 nm as measured from STEM images for MonoCat-1 (Figure 6A). To ensure comparability of the monoliths concerning the Pt NP size, MonoCat-27 was also investigated concerning Pt NP size distribution (Supplementary Figure S3), and a very similar arithmetic mean of 2.6 nm was found. The three-dimensional reconstruction of TEM tomography data indicated a homogeneous distribution of the Pt NPs throughout the image domain (Figure 6B). The average size of the catalytic phase was an order of 8 times below the mean mesopore width of the monolithic catalyst, indicating that the catalyst was distributed evenly with a narrow size distribution and residing within the monolith skeleton.
FIGURE 5. (A) The distribution of Pt measured via elemental analysis determined at the peripheral and core regions of the monolith cross section (sample: MonoCat-10). (B) SEM-EDX line scan depicting a homogeneous radial distribution from the periphery to the center of the monolith cross section (sample: MonoCat-1).
FIGURE 6. (A) Size distribution histogram of the Pt NPs determined via STEM images (measurement of the diameter of 200 Pt particles) in MonoCat-1. (B) TEM tomography visualizing the reconstructed 3D model of Pt NPs embedded in the support material.
The hydrogenation of p-nitrophenol (PNP) to p-aminophenol (PAP) using sodium borohydride as a reducing agent offers several advantages as a test reaction for catalytic performance of Pt-loaded monolithic catalyst systems: (1) the reaction does not take place in the absence of a catalyst, (2) the reaction occurs in an aqueous phase that is easily accessible in the laboratory and requires no special handling except fresh solution preparation, (3) the reaction occurs at room temperature and ambient pressure, (4) steady state can usually be achieved in <3 min (Supplementary Figure S4), (5) the reaction is intrinsically fast (>70% PNP conversion can be achieved with a contact time <3 s), (6) the color change from the reactant PNP (dark yellow, in the presence of NaBH4) to the product PAP (colorless) can be easily tracked by simple (online) UV–vis spectroscopy.
Figure 7 illustrates the reactor cladding and the progress of the hydrogenation reaction as well as the UV–vis measurement principle. As a side note, it can be mentioned that glass cladding enables monitoring of the qualitative reaction progress with the naked eye and enables the use of other in situ characterization techniques at or in the direct vicinity of the monolithic reactor. Another significant advantage of PNP hydrogenation as a test reaction is the speed at which the steady state could be achieved. It takes only 16 s to attain ∼70% conversion at steady state for a reactor of 1 cm length when the volumetric flow rate of the reactant solution is shifted from 0 to 8 cm3 min−1 (Supplementary Figure S4). Similarly, a new steady state can be achieved in <1 min as soon as the flow rate is adjusted to a new value. This allows for very fast screening of reaction conditions. Since the glass-cladded reactors can be easily and quickly connected to the tubing of the setup via the Swagelok® Ultra-Torr fitting, fast screening of cladded monolithic reactors is also possible. Hence, the hydrogenation of PNP proved to be an inexpensive, fast, and facile test reaction to study the catalyst performance in flow configuration.
FIGURE 7. Photographic image of the glass-cladded monolithic reactor and the color change before and after the monolithic reactor illustrating the conversion of PNP (yellow colored) to PAP (colorless). For further details on the PNP hydrogenation, see Goepel et al. (2014).
The monolithic reactors MonoCat-1, MonoCat-10, and MonoCat-27 were applied in the continuous-flow aqueous-phase hydrogenation of PNP to PAP to investigate the influence of mean macropore width on mass-transfer limitations. Prior to these experiments, a linear increase of conversion was observed with an increase in contact time in the flow rate range of 1–8 cm3 min−1 (Supplementary Figure S5), again indicating a homogeneous distribution of reactants and plug flow characteristics in the reactor. To investigate the influence of mass-transfer limitations in macropores, the monolith length and flow rate were varied for the two reactors to keep the contact time constant. This allowed for an investigation into the influence of flow rate or average flow velocity on PNP conversion that was expected to influence the thickness of the stagnant layer formed at the interphase of the monolith skeleton and the bulk fluid. For MonoCat-1 to MonoCat-27, a constant conversion (∼75%) at a fixed contact time (2.6 s) was observed for flow rates between 1 and 8 cm3 min−1 (Figure 8). This is a strong indication for the absence of mass-transfer limitations or stagnant-layer formation in the macropores of the monolith. This observation differs from earlier studies (Galarneau et al., 2016b) but may be explained by the different flow rate regimes investigated. The absence of mass-transfer limitations in macropores observed in this work is likely attributed to the high flow rate that could be applied while still achieving measurable conversion due to an intrinsically fast catalytic conversion.
FIGURE 8. Conversion (XPNP) at constant contact time (tc ∼ 2.6 s) as a function of volumetric flow rate (q) with fixed diameter (D = 0.5 cm) and variable lengths (L = 0.25, 0.5, 1.0, and 2.0 cm); T = 298 K, cPNP = 0.40 mm, cNaBH4 = 1.60 mm.
Silica monoliths with a variation of macropore width of 1–27 µm and comparable textural properties such as mean mesopore width (17 nm), total porosity (90%), specific surface area (200 m2 g−1), and specific pore volume (3 cm3 g−1) were successfully synthesized. The monoliths (L = 2 cm and D = 0.5 cm) exhibit mechanical stability with consistently high permeability (up to 2 µm2) over the range of flow rates of 2–20 cm3 min−1 affiliated to the average macropore width at relatively low pressure drop (1 bar for 27 μm at 20 cm3 min−1). Pt was loaded as a catalytically active component with a particle size of 2–3 nm embedded homogeneously within the mesopores of the HSM. The aqueous-phase hydrogenation of PNP to PAP was for the first time shown as a facile and fast reaction to investigate the catalytic properties of monolithic catalysts as continuous-flow reactors. Thus, investigations of mass transfer at technically more relevant flow rates are possible due to a fast intrinsic conversion rate. No indication of mass-transfer limitations in macropores was observed for the applied conditions in contrast to earlier studies. This, again, highlights the potential of superior mass transfer in HSM reactors operated in continuous flow of liquid reaction mixtures.
The raw data supporting the conclusion of this article will be made available by the authors, without undue reservation.
HJ: Experiments (PNP hydrogenation, Pt addition, and flow experiments), manuscript writing. MG: Experiment planning, conception of study, manuscript writing and revision. DP: TEM experiments, manuscript revision. RK: monolith synthesis, monolith textural characterization experiments. DE: Experiment planning (monolith synthesis and characterization), manuscript revision. RG: Experiment planning, manuscript revision, conception of study.
This work was supported by the Higher Education Commission (HEC) of Pakistan under the programme Faculty Development for Ph.D. Candidates (Pakistan), 2018 (ID: 57435474) in collaboration with the German Academic Exchange Service (DAAD).
The authors declare that the research was conducted in the absence of any commercial or financial relationships that could be construed as a potential conflict of interest.
All claims expressed in this article are solely those of the authors and do not necessarily represent those of their affiliated organizations, or those of the publisher, the editors, and the reviewers. Any product that may be evaluated in this article, or claim that may be made by its manufacturer, is not guaranteed or endorsed by the publisher.
The author(s) acknowledge support from the German Research Foundation (DFG) and Universität Leipzig within the program of Open Access Publishing.
The Supplementary Material for this article can be found online at: https://www.frontiersin.org/articles/10.3389/fceng.2021.789416/full#supplementary-material
PBR, packed bed reactor; HSM, hierarchical silica monolith; PNP, p-nitrophenol; PAP, p-aminophenol; MIP, mercury intrusion porosimetry; NP, nanoparticle.
Aditya, T., Pal, A., and Pal, T. (2015). Nitroarene Reduction: A Trusted Model Reaction to Test Nanoparticle Catalysts. Chem. Commun. 51, 9410–9431. doi:10.1039/c5cc01131k
Ahmad, S., Sebai, W., Belleville, M.-P., Brun, N., Galarneau, A., and Sanchez-Marcano, J. (2021). Enzymatic Monolithic Reactors for Micropollutants Degradation. Catal. Today. 362, 62–71. doi:10.1016/j.cattod.2020.04.048
Akwi, F. M., and Watts, P. (2018). Continuous Flow Chemistry: Where Are We Now? Recent Applications, Challenges and Limitations. Chem. Commun. 54, 13894–13928. doi:10.1039/c8cc07427e
Al-Naji, M., Balu, A. M., Roibu, A., Goepel, M., Einicke, W.-D., Luque, R., et al. (2015). Mechanochemical Preparation of Advanced Catalytically Active Bifunctional Pd-Containing Nanomaterials for Aqueous Phase Hydrogenation. Catal. Sci. Technol. 5, 2085–2091. doi:10.1039/C4CY01174K
Baumann, M., Moody, T. S., Smyth, M., and Wharry, S. (2020). A Perspective on Continuous Flow Chemistry in the Pharmaceutical Industry. Org. Process. Res. Dev. 24, 1802–1813. doi:10.1021/acs.oprd.9b00524
Bear, J., and Corapcioglu, M. Y. (1972). Dynamics of Fluids in Porous Media. New York: Dover Publications Inc.
Ciemięga, A., Maresz, K., Malinowski, J., and Mrowiec-Białoń, J. (2017). Continuous-Flow Monolithic Silica Microreactors with Arenesulphonic Acid Groups: Structure-Catalytic Activity Relationships. Catalysts 7, 255. doi:10.3390/catal7090255
Daneyko, A., Höltzel, A., Khirevich, S., and Tallarek, U. (2011). Influence of the Particle Size Distribution on Hydraulic Permeability and Eddy Dispersion in Bulk Packings. Anal. Chem. 83, 3903–3910. doi:10.1021/ac200424p
El Kadib, A., Chimenton, R., Sachse, A., Fajula, F., Galarneau, A., and Coq, B. (2009). Functionalized Inorganic Monolithic Microreactors for High Productivity in Fine Chemicals Catalytic Synthesis. Angew. Chem. Int. Ed. 48, 4969–4972. doi:10.1002/anie.200805580
Enke, D., Gläser, R., and Tallarek, U. (2016). Sol-gel and Porous Glass-Based Silica Monoliths With Hierarchical Pore Structure for Solid-Liquid Catalysis. Chem. Ingenieur Technik. 88, 1561–1585. doi:10.1002/cite.201600049
Fletcher, P. D. I., Haswell, S. J., He, P., Kelly, S. M., and Mansfield, A. (2011). Permeability of Silica Monoliths Containing Micro- and Nano-Pores. J. Porous Mater. 18, 501–508. doi:10.1007/s10934-010-9403-3
Galarneau, A., Abid, Z., Said, B., Didi, Y., Szymanska, K., Jarzębski, A., et al. (2016a). Synthesis and Textural Characterization of Mesoporous and Meso-/Macroporous Silica Monoliths Obtained by Spinodal Decomposition. Inorganics. 4, 9. doi:10.3390/inorganics4020009
Galarneau, A., Sachse, A., Said, B., Pelisson, C.-H., Boscaro, P., Brun, N., et al. (2016b). Hierarchical Porous Silica Monoliths: A Novel Class of Microreactors for Process Intensification in Catalysis and Adsorption. Comptes Rendus Chim. 19, 231–247. doi:10.1016/j.crci.2015.05.017
Goepel, M., Al-Naji, M., With, P., Wagner, G., Oeckler, O., Enke, D., et al. (2014). Hydrogenation Ofp-Nitrophenol Top-Aminophenol as a Test Reaction for the Catalytic Activity of Supported Pt Catalysts. Chem. Eng. Technol. 37, 551–554. doi:10.1002/ceat.201300731
Gu, S., Lu, Y., Kaiser, J., Albrecht, M., and Ballauff, M. (2015). Kinetic Analysis of the Reduction of 4-Nitrophenol Catalyzed by Au/Pd Nanoalloys Immobilized in Spherical Polyelectrolyte Brushes. Phys. Chem. Chem. Phys. 17, 28137–28143. doi:10.1039/c5cp00519a
Haas, C. P., Müllner, T., Kohns, R., Enke, D., and Tallarek, U. (2017). High-Performance Monoliths in Heterogeneous Catalysis With Single-phase Liquid Flow. React. Chem. Eng. 2, 498–511. doi:10.1039/C7RE00042A
Hakat, Y., Kotbagi, T. V., and Bakker, M. G. (2016). Silver Supported on Hierarchically Porous SiO2 and Co3O4 Monoliths: Efficient Heterogeneous Catalyst for Oxidation of Cyclohexene. J. Mol. Catal. A: Chem. 411, 61–71. doi:10.1016/j.molcata.2015.10.015
Hormann, K., and Tallarek, U. (2013). Analytical Silica Monoliths with Submicron Macropores: Current Limitations to a Direct Morphology-Column Efficiency Scaling. J. Chromatogr. A. 1312, 26–36. doi:10.1016/j.chroma.2013.08.087
Kohns, R., Anders, N., Enke, D., and Tallarek, U. (2021). Influence of Pore Space Hierarchy on the Efficiency of an Acetylcholinesterase‐Based Support for Biosensorics. Adv. Mater. Inter. 8, 2000163. doi:10.1002/admi.202000163
Kohns, R., Haas, C. P., Höltzel, A., Splith, C., Enke, D., and Tallarek, U. (2018). Hierarchical Silica Monoliths With Submicron Macropores as Continuous-Flow Microreactors for Reaction Kinetic and Mechanistic Studies in Heterogeneous Catalysis. React. Chem. Eng. 3, 353–364. doi:10.1039/C8RE00037A
Leinweber, F. C., Lubda, D., Cabrera, K., and Tallarek, U. (2002). Characterization of Silica-Based Monoliths With Bimodal Pore Size Distribution. Anal. Chem. 74, 2470–2477. doi:10.1021/ac011163o
Leinweber, F. C., and Tallarek, U. (2003). Chromatographic Performance of Monolithic and Particulate Stationary Phases. J. Chromatogr. A. 1006, 207–228. doi:10.1016/S0021-9673(03)00391-1
Liguori, F., Barbaro, P., Said, B., Galarneau, A., Santo, V. D., Passaglia, E., et al. (2017). Unconventional Pd@sulfonated Silica Monoliths Catalysts for Selective Partial Hydrogenation Reactions Under Continuous Flow. ChemCatChem. 9, 3245–3258. doi:10.1002/cctc.201700381
Linares, N., Hartmann, S., Galarneau, A., and Barbaro, P. (2012). Continuous Partial Hydrogenation Reactions by Pd@unconventional Bimodal Porous Titania Monolith Catalysts. ACS Catal. 2, 2194–2198. doi:10.1021/cs3005902
Liu, A., Yang, L., Traulsen, C. H.-H., and Cornelissen, J. J. L. M. (2017). Immobilization of Catalytic Virus-Like Particles in a Flow Reactor. Chem. Commun. 53, 7632–7634. doi:10.1039/c7cc03024j
Lu, X., Hasegawa, G., Kanamori, K., and Nakanishi, K. (2020). Hierarchically Porous Monoliths Prepared via Sol-Gel Process Accompanied by Spinodal Decomposition. J. Sol-gel Sci. Technol. 95, 530–550. doi:10.1007/s10971-020-05370-4
Meinusch, R., Ellinghaus, R., Hormann, K., Tallarek, U., and Smarsly, B. M. (2017). On the Underestimated Impact of the Gelation Temperature on Macro- and Mesoporosity in Monolithic Silica. Phys. Chem. Chem. Phys. 19, 14821–14834. doi:10.1039/c7cp01846k
Mrowiec-Białoń, J., Ciemięga, A., Maresz, K., Szymańska, K., Pudło, W., and Jarzębski, A. B. (2018). Review on Hierarchically Micrsostructured Monolithic Reactors for High Yield Continuous Production of fine Chemicals. Chem. Process. Eng. 39, 367–375. doi:10.24425/122957
Nakanishi, K., and Soga, N. (1991). Phase Separation in Gelling Silica-Organic Polymer Solution: Systems Containing Poly(sodium Styrenesulfonate). J. Am. Ceram. Soc. 74, 2518–2530. doi:10.1111/j.1151-2916.1991.tb06794.x
Nakanishi, K., Tanaka, N., Nakanishi, K., and Tanaka, N. (2007). Sol-Gel With Phase Separation. Hierarchically Porous Materials Optimized for High-Performance Liquid Chromatography Separations. Acc. Chem. Res. 40, 863–873. doi:10.1021/ar600034p
Pélisson, C.-H., Nakanishi, T., Zhu, Y., Morisato, K., Kamei, T., Maeno, A., et al. (2017). Grafted Polymethylhydrosiloxane on Hierarchically Porous Silica Monoliths: A New Path to Monolith-Supported Palladium Nanoparticles for Continuous Flow Catalysis Applications. ACS Appl. Mater. Inter. 9, 406–412. doi:10.1021/acsami.6b12653
Plutschack, M. B., Pieber, B., Gilmore, K., and Seeberger, P. H. (2017). The Hitchhiker's Guide to Flow Chemistry. Chem. Rev. 117, 11796–11893. doi:10.1021/acs.chemrev.7b00183
Russell, M. G., Veryser, C., Hunter, J. F., Beingessner, R. L., and Jamison, T. F. (2020). Monolithic Silica Support for Immobilized Catalysis in Continuous Flow. Adv. Synth. Catal. 362, 314–319. doi:10.1002/adsc.201901185
Sachse, A., Galarneau, A., Di Renzo, F., Fajula, F., and Coq, B. (2010). Synthesis of Zeolite Monoliths for Flow Continuous Processes. The Case of Sodalite as a Basic Catalyst. Chem. Mater. 22, 4123–4125. doi:10.1021/cm1014064
Sachse, A., Hulea, V., Finiels, A., Coq, B., Fajula, F., and Galarneau, A. (2012). Alumina-Grafted Macro-/Mesoporous Silica Monoliths as Continuous Flow Microreactors for the Diels-Alder Reaction. J. Catal. 287, 62–67. doi:10.1016/j.jcat.2011.12.003
Sachse, A., Linares, N., Barbaro, P., Fajula, F., and Galarneau, A. (2013). Selective Hydrogenation over Pd Nanoparticles Supported on a Pore-Flow-Through Silica Monolith Microreactor With Hierarchical Porosity. Dalton Trans. 42, 1378–1384. doi:10.1039/c2dt31690k
Saito, H., Nakanishi, K., Hirao, K., and Jinnai, H. (2006). Mutual Consistency between Simulated and Measured Pressure Drops in Silica Monoliths Based on Geometrical Parameters Obtained by Three-Dimensional Laser Scanning Confocal Microscope Observations. J. Chromatogr. A. 1119, 95–104. doi:10.1016/j.chroma.2006.03.087
Schlumberger, C., and Thommes, M. (2021). Characterization of Hierarchically Ordered Porous Materials by Physisorption and Mercury Porosimetry-A Tutorial Review. Adv. Mater. Inter. 8, 2002181. doi:10.1002/admi.202002181
Stoeckel, D., Kübel, C., Loeh, M. O., Smarsly, B. M., and Tallarek, U. (2015). Morphological Analysis of Physically Reconstructed Silica Monoliths With Submicrometer Macropores: Effect of Decreasing Domain Size on Structural Homogeneity. Langmuir. 31, 7391–7400. doi:10.1021/la5046018
Szymańska, K., Pudło, W., Mrowiec-Białoń, J., Czardybon, A., Kocurek, J., and Jarzębski, A. B. (2013). Immobilization of Invertase on Silica Monoliths With Hierarchical Pore Structure to Obtain Continuous Flow Enzymatic Microreactors of High Performance. Microporous Mesoporous Mater. 170, 75–82. doi:10.1016/j.micromeso.2012.11.037
Tallarek, U., Leinweber, F. C., and Seidel-Morgenstern, A. (2002). Fluid Dynamics in Monolithic Adsorbents: Phenomenological Approach to Equivalent Particle Dimensions. Chem. Eng. Technol. 25, 1177–1181. doi:10.1002/1521-4125(20021210)25:12<1177:aid-ceat1177>3.0.co;2-v
Turke, K., Meinusch, R., Cop, P., Prates da Costa, E., Brand, R. D., Henss, A., et al. (2021). Amine-Functionalized Nanoporous Silica Monoliths for Heterogeneous Catalysis of the Knoevenagel Condensation in Flow. ACS Omega. 6, 425–437. doi:10.1021/acsomega.0c04857
Vervoort, N., Gzil, P., Baron, G. V., and Desmet, G. (2003). A Correlation for the Pressure Drop in Monolithic Silica Columns. Anal. Chem. 75, 843–850. doi:10.1021/ac0262199
Keywords: hierarchical pore system, silica monolith, flow reactor, mass transfer, platinum catalysis, PNP hydrogenation, test reaction, p-nitrophenol
Citation: Jatoi HUK, Goepel M, Poppitz D, Kohns R, Enke D, Hartmann M and Gläser R (2021) Mass Transfer in Hierarchical Silica Monoliths Loaded With Pt in the Continuous-Flow Liquid-Phase Hydrogenation of p-Nitrophenol. Front. Chem. Eng. 3:789416. doi: 10.3389/fceng.2021.789416
Received: 04 October 2021; Accepted: 17 November 2021;
Published: 13 December 2021.
Edited by:
Anne Galarneau, UMR5253 Institut de chimie moléculaire et des matériaux Charles Gerhardt Montpellier (ICGM), FranceReviewed by:
Pierluigi Barbaro, National Research Council (CNR), ItalyCopyright © 2021 Jatoi, Goepel, Poppitz, Kohns, Enke, Hartmann and Gläser. This is an open-access article distributed under the terms of the Creative Commons Attribution License (CC BY). The use, distribution or reproduction in other forums is permitted, provided the original author(s) and the copyright owner(s) are credited and that the original publication in this journal is cited, in accordance with accepted academic practice. No use, distribution or reproduction is permitted which does not comply with these terms.
*Correspondence: Roger Gläser, cm9nZXIuZ2xhZXNlckB1bmktbGVpcHppZy5kZQ==
Disclaimer: All claims expressed in this article are solely those of the authors and do not necessarily represent those of their affiliated organizations, or those of the publisher, the editors and the reviewers. Any product that may be evaluated in this article or claim that may be made by its manufacturer is not guaranteed or endorsed by the publisher.
Research integrity at Frontiers
Learn more about the work of our research integrity team to safeguard the quality of each article we publish.