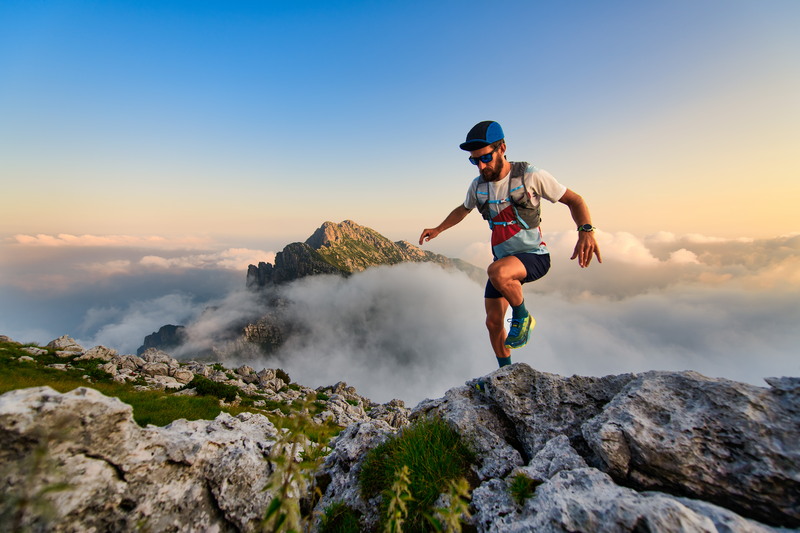
95% of researchers rate our articles as excellent or good
Learn more about the work of our research integrity team to safeguard the quality of each article we publish.
Find out more
REVIEW article
Front. Chem. Eng. , 02 December 2021
Sec. Chemical Reaction Engineering
Volume 3 - 2021 | https://doi.org/10.3389/fceng.2021.789102
This article is part of the Research Topic Hierarchical and Multifunctional Materials in Chemical Engineering: Synthesis Strategies and Processing Challenges View all 7 articles
In this review article, we first discussed the development of silica monoliths with hierarchical macro-/mesopore structure and their potential figures of merit as continuous-flow micro-/mesoreactors of up to 30 ml working volume. Making use of the flow hindrance of different pore structures seen from the Darcy law perspective, we discriminated four structures of the monoliths (M1–M4). We then summarized the most important results, mainly from our studies of continuous-flow structured monolithic reactors and rotating bed reactors (RBRs) filled with structured pellets, activated with various catalytic entities and enzymes. The results show that an increase in the flow rate and thus velocity in reactors activated with more conventional catalytic sites has no or a minor positive effect on the apparent reaction rate. On the contrary, in those with the most open structure (M1) and functionalized with enzymes, it could increase by more than two orders of magnitude even at low overpressures. The production systems worked stably for at least 200 h. To conclude, the synthetic system made of the hierarchically structured monoliths, or RBRs filled with structured catalytic pellets, lay the foundation for a new platform for the high-yield production of a wide variety of specialty chemicals, even on a multikilogram scale, in a safe and sustained manner.
For decades, the synthesis of fine chemicals and active pharmaceutical ingredients (APIs) was carried out in batch operations until in the early nineties that was about to start to change, sparked by the observation that chemical reactions are better controlled and run much faster in a continuous flow, especially in channels with submillimeter diameters (Ehrfeld et al., 2000; Stankiewicz, 2001). In such microreactors, catalysts are either coated onto the walls or embedded in porous beads packed into the channels. The increase in the surface-to-volume ratio to over 104 m2/m3, featured by microchannel reactors, additionally increases the space-time yield. On the one hand, it improves productivity and selectivity, and on the other hand, it improves economy and process safety. However, the throughputs in the µL/min range make microchannel reactors suitable for microsynthesis, rather than fine chemical synthesis on a multi-g/h scale. To overcome this limitation, polymeric, hybrid macrocellular (HIPE), or inorganic (silica) monolithic microchannel reactors (MMRs) and their carbon replicas were proposed (Xie et al., 1999; Kawakami et al., 2005; Roucher et al., 2019; Brun et al., 2011; van den Biggelaar et al., 2019; Baccour et al., 2020). They featured scores of very narrow flow-through pores and greatly expanded the surface area. However, most polymeric materials tend to swell in organic solvents and thus clog the flow-through channels, whereas the pore structure of the applied silica xerogels is prevailed by small mesopores which generate a very large but hardly accessible surface area and the need for an exceedingly large overpressure.
A breakthrough came with the development and application of silica monoliths that featured a very open multimodal macro-/mesopore structure, developed by Nakanishi et al. in the early nineties for chromatographic applications (Nakanishi et al., 2000), and first adapted to microreactor technology by the Montpellier group (El Kadib et al., 2009; Sachse et al., 2011a; Sachse et al., 2011b). Owing to an open porosity of about 85–88%, that is, much higher than that in packed beds of porous beads, and also much wider flow-through channels (ca. 5 µm dia. vs. 1–2 µm in monolithic chromatographic columns), larger flow rates could be applied at reduced overpressure. Moreover, an ample presence of mesopores in the silica skeleton (3–10 nm dia., mesopore volume ca. 1 cm3/g) resulted in an easily modifiable surface area of about 600 m2/g and hence afforded the in-flow reaction system with more than 106 m2/m3 of the surface-to-volume ratio. This multimodal pore structure enabled larger throughputs and catalyst loads and also much better control of the reaction and in effect, much higher productivities. In the transesterification and the Knoevenagel reactions, the productivities achieved were more than ten times higher than those of featured batch slurry reactors with crushed monoliths used as particulate catalysts, and also higher than those of packed-bed reactors filled with the same particles (El Kadib et al., 2009). Subsequently, the same team also devised an elegant method of direct transformation of amorphous macroporous silica monoliths into macroporous monoliths with a zeolite skeleton, leaving the macropore network intact (pseudomorphic transformation) (Sachse et al., 2011a; Sachse et al., 2011b). Somewhat earlier, but not less importantly, Smått et al. developed a double-templating variant of the original method and clearly demonstrated that the macro- and mesoporosity of the silica monoliths can be fine-tuned, independent of each other, over several length scales, by a modification of the composition of the reaction mixture (Smatt et al., 2003). That report paved the way for adapting the monolith’s pore structure to specific needs and overcoming existing methodological constraints.
After a slight modification of the original procedure of Smått et al. in the Gliwice group, we obtained silica monoliths which exhibited more open and isotropic structures than those reported before; it featured ultra-large macropores that were 30–50 µm and mesopores ca. 20 and 3–4 nm in size, with a total pore volume, Vt of 4 cm3/g (Pudło et al., 2006). In preliminary studies of their potentials, the monoliths, after being crushed to grains, were applied as supports for ionic liquids and enzymes (lipase) to afford highly active catalysts for the Baeyer–Villiger oxidation (BVO) reaction in the chemo and chemo-enzymatic modes and also for aerobic oxidation of primary alcohols in the batch (slurry) reactor (Chrobok et al., 2009, 2010; Drożdż et al., 2013). When the enzyme (lipase) was attached to crushed monolith grains, the particulate catalysts obtained appeared to be three times more active than when they were attached to mesoporous silica (MPS) from the SBA-15 family, and also much more active than the commercial catalyst of the same lipase (Novozym 435) (Drożdż et al., 2013). These studies, carried out over a decade ago, clearly demonstrated the scale of the benefits that can be expected from the use of silica materials with a multimodal pore structure.
While scores of articles highlight the advantages of using the MMR in various situations, they mainly present results obtained from studies of one (micro)reactor with a specific multimodal pore structure in one reaction. Not much attention has been paid to the intrinsic activity of the applied catalytic entities, the effect of the selected and other structural options on the accessibility and the catalyst load, and combined impact on overall performance. Such an approach does not allow for more conclusive observations on the effect of the specific selected pore structures on the productivity and performance of monolithic reactors with other pore structures (but of the same topology) that can also be drawn. In this short overview, mainly of our studies and written from a chemical engineering perspective, we summarize and evaluate the results obtained during over a 10-year study of various catalytically functionalized MMRs with different pore structures in different reactions but prepared and investigated using the same methodology. In addition to most typical monolithic reactors designed for continuous-flow synthesis, we also report on the performance of rotating bed reactors (RBRs, also nicknamed SpinChem), with baskets filled with monolithic beads, exhibiting the same pore structure as MMRs. It is noteworthy that such an RBR can be considered a monolithic reactor with internal recycle. Thus, combining all advantages of MMRs and RBRs also allows the residence time to be easily extended to achieve target conversion.
Two issues are crucial in MMR engineering: monolith preparation and its housing/cladding to obtain a ready-for-run reactor. Modification of a monolith to impart catalytic properties is typically divided into two parts: preliminary modification of the surface, followed by attachment and activation of catalytic entities, which are very often carried out in continuous flow, after its encasing. The preparation of silica monoliths with different pore structures, as well as with mixed oxides (silica–alumina and silica–titania) was described in much detail before (Smatt et al., 2003; Galarneau et al., 2016b; Szymańska et al., 2016b; Ciemięga et al., 2020), and for this reason, it is not discussed here. While the selected protocol is critical to determining the size of macropores, it has less impact on mesopores, which in silica monoliths are typically 6–9 nm in diameter and provide a specific surface area (BET) of about 300–700 m2/g and 1.0–1.2 cm3/g mesopore volume, that is, similar to most MPS. This similarity justifies the use of MPS of SBA or MCF family in comparative studies with batch (slurry) reactor performance. On the whole, these texture properties are very attractive. However, experiments with the liquid phase reactions in MMRs, which we performed, show that more immediate accessibility of catalytic sites, enabled by the large mesopores, is often much more important than the very large specific surface area that offers very high catalyst loading. For that reason, pristine silica monoliths were subjected to post-gelation alkaline treatment at elevated temperature, prior to drying, which stimulated the Ostwald ripening process and hence restructuring of silica in the mesopore size range. It ended up in the formation of larger mesopores (about 20 nm or even slightly more) and decrease in the surface area to 300–450 m2/g; we found the latter was still large enough to ensure a high catalyst loading. However, more recent studies show that this process can also affect the size and structure of the flow-through channel network (macropores) determined by the structure of the silica skeleton (Zhokh et al., 2020). In general, the alkaline modification of the mesopore structure has a very positive effect on the accessibility of the catalysts for reactants and hence also on the performance of the MMRs.
For practical reasons, most of the investigated MMRs used cylindrical rods of 4–6 mm in diameter and up to 100 mm length (Sachse et al., 2011a; Sachse et al., 2011b; Szymańska et al., 2013; Galarneau et al., 2016b; Szymańska et al., 2016b; Haas et al., 2017; Alotaibi et al., 2018; Ciemięga et al., 2020). However, by the meticulous control of the preparation procedure, we obtained monoliths even with a diameter of 18–20 mm, of approximately 3 cm2 of the effective cross-sectional area and hence more than 20 ml of the volume (Figure 1). Furthermore, bearing in mind the pressure drop–flow rate relationship (vide infra), the latter monoliths enabled throughputs in the range of 1,000–1,500 ml/min, with a pressure drop of ca. 300–400 kPa in a 10-cm long reactor (Szymańska et al., 2016b). Clearly, such monolithic mesoreactors enable multi-g/h production systems, even in a single-pass flow, and pave the way for the design of efficient low-pressure multireactor systems, making use of a modular micro-/mesoreactor platform.
FIGURE 1. Silica monoliths with the hierarchical pore structure applied as a core of the microreactor for continuous-flow processes.
The silica monoliths are encased in PTFE, LDPE, or borosilicate NMR tubes equipped with connectors or coated with polymeric resins: epoxy, PEEK (El Kadib et al., 2009; Sachse et al., 2011a; Szymańska et al., 2013; Hou et al., 2019; Ciemięga et al., 2020). The latter method is somewhat tricky as penetration of the resins into the porous monolith has to be avoided. In these cases, the properties of the polymeric casing define the upper operating temperature limit for the microreactor. An alternative solution, which overcomes the temperature limitation, is the synthesis of structured silica monoliths in the channels of the most typical cordierite honeycomb monolith, to obtain the reactor of the monoliths-in-monolith (MiM)–type structure (Berdys et al., 2015). Regardless of the selected protocol of the silica monolith synthesis, a perfect contact between two materials is crucial for the engineering of the MiM reactor. This was achieved by reacting silanols (terminal OH− groups) of internal silica monoliths with strong silanols, generated on the surface of the cordierite monolith by alkaline treatment, prior to the introduction of the silica sol. Both structure and flow characteristics of the embedded silica have been proven to be quite similar to those obtained for pure silica rods. The developed procedure, described in detail in Berdys et al. (2015), paves the way for MMRs with a robust structure adapted to operate at elevated temperatures.
The experiments showed (Koreniuk et al., 2015b; Galarneau et al., 2016a; Szymańska et al., 2016b) that irrespective of the size of macro- and mesopores, the pressure drop (∆P) vs. flow rate (
where L is the length of the monolith, η is the viscosity of the liquid, A is the cross-sectional area of the monolith, and K is the Darcy coefficient, the value of which is determined experimentally; it is proportional to ε·d2/τ, where d is the mean flow-through pore diameter, ε is open porosity, and τ is the tortuosity of the channels.
Figure 2 presents the results of measurements of ΔP/L vs.
FIGURE 2. SEM images of silica monoliths with different pore structures; cumulative pore volume distributions obtained from Hg-porosimetry (A); effect of back-pressure on the flow rate for M1–M4 monoliths (B).
The superior performance of MMRs in the continuous-flow reaction was first reported by the Montpellier group in the transesterification of triacetin with methanol (El Kadib et al., 2009). The silica monoliths (6 mm diameter., macropores ∼5 µm diameter., mesopores 13 nm, Vt ∼1.95 cm3/g, and SBET ∼650 m2/g) were grafted with arenesulfonic acid groups (0.95 mmol/g of silica) to generate strong Brönsted acid sites (BAS). The productivity afforded by the MMR was ca. 30 times higher than that of the batch reactor with crushed monoliths and about three times more than that of the packed-bed reactor, for the same conversions of about 84%.
Esterification of acetic acid with butanol was applied as a test reaction for an MiM-type reactor (Berdys et al., 2015), the surface of which was functionalized with the same catalytic sites as shown in El Kadib et al. (2009). Its performance was compared to that of a typical MMR (4 × 40 mm) prepared using the same monolith synthesis and modification procedures. Comparative studies of the MiM structure and the reference silica monoliths (MMR) revealed that the macropores in the MiM reactor were slightly smaller (10–40 µm) than those in the MMR counterpart (20–50 µm), as was the total pore volume Vt, but the specific surface area (SBET) was around 20% larger, due to the larger volume in the mesopore size range. Overall, the catalytic performance of the MiM reactor (acidic groups 0.6 mmol/gR) was similar to that of the MMR counterpart, but for the same flow rate, the conversion achieved in the MiM reactor was 6% lower than that in the MMR due to shorter mean residence time caused by lower pore volume.
The MMRs modified with the same (-SO3H) groups (0.65 mmol/gR) were studied in more detail in the synthesis of n-butyl acetate and n-butyl lactate (Koreniuk et al., 2015b; Ciemięga et al., 2017a). The experiments performed using monoliths of 4.5 × 10–40 mm (M1 structure) and the same residence time (155 s, i.e., fluid velocity over 5 mm/min) revealed no increase in conversion after a twofold increase in the reactant’s velocity and only a very slight increase after a fourfold increase (Koreniuk et al., 2015b). This indicated that in the applied range of velocities, the kinetics of the esterification reaction was fully controlled by the intrinsic reaction kinetics, and the external mass transport was negligible. The linear dependence of the catalytic activity on the concentration of acidic groups in the range of 0.15–0.65 mmol/g corroborated this observation. Finally, the stability of the MMR has been demonstrated during the 3-day esterification of lactic acid with n-butanol carried out at 140°C to boost the reaction kinetics (Koreniuk et al., 2015b). The monolith structure appeared to be well-preserved at both the micrometric and nanometric scales, and no change in the acidic group content was detected by FT-IR and thermogravimetric analysis after that period.
Next, in a rare study of the effect of pore structure, three MMRs (4.5 × 40 mm rods), labeled M1–M3, activated with sulfonic groups and possessing the same bimodal pore architecture, yet macro- and mesopores of different sizes, were compared in a continuous-flow synthesis of n-butyl actetate, with a packed-bed reactor filled with Amberlyst 15 used as the benchmark (Ciemięga et al., 2017b). While the pore structure of M1 was similar to that in Koreniuk et al. (2015b), other monoliths possessed much smaller flow-through (macro)pores: 4–6 (M2) and 1.3 µm in size (M3) (cf. Figure 2) and Vt decreasing from 4.0 to 3.0 cm3/g, for M1 and M3, respectively. The values of the permeability coefficient determined experimentally decreased very rapidly with the decrease in the size of the macropores, from 11.3 to 0.27 and to 0.025 µm2, for M1, M2, and M3, respectively, which implies a very rapid increase in pressure drop (backpressure) with increasing velocity of fluids. The specific surface area (SBET) of pristine silica monoliths increased from 328 to 413 to 575 m2/g for M1, M2, and M3, respectively, while the size of mesopores gradually decreased from 20 nm (M1) to 9 nm (M3). Thus, the accessibility of BASs decreased in the order M1>M2>M3. These trends continued after surface modification. Due to the increase in the surface area, the number of catalytic centers increased in the order M1<M2<M3. However, the order of their accessibility was reversed (Ciemięga et al., 2017a). Clearly, the observed complexity of relationships between structure, catalytic properties, and MMR performance leaves ample room for optimization to take full advantage of the catalysts and microreactor potentials, on the one hand, and the constraints imposed by the process, on the other hand.
Catalytic tests were performed at the same flow rate selected to achieve a conversion less than 50% to discriminate the efficacy of different structures. Productivity expressed in mol of product formed per mass of the activated reactor (bulk catalyst) per reaction time proved to be fairly similar for the MMRs applied and about 67–68.5 mol/kgRh, and was 10% higher than in the packed-bed reactors of Amberlyst 15 beads (Ciemięga et al., 2017b). However, if the formed product was related to the amount of attached catalytic sites (mol H+), its value significantly differed and decreased in the order M1> M2>M3>> Amberlyst 15. Moreover, with the productivity afforded by the M1 reactor being more than twice as high as in other previously proposed catalytic and reactor systems, and also a very good stability of the sulfonic catalytic centers even at 300°C, the M1-SO3H type of the MMR emerges as a preferred system for the continuous-flow esterification reactions, suitable for operation even at an elevated temperature (Ciemięga et al., 2017a).
Since the discovery of the unique catalytic properties of titanium silicalite (TS-1) in the oxidation of organic compounds in the early 1980s (Taramasso et al., 1984), hundreds of studies have demonstrated the remarkable properties of various titania–silica mixed oxides as oxidation catalysts, using molecular oxygen or an aqueous solution of hydrogen peroxide. Catalytic properties were initially ascribed to the presence of isolated, tetrahedrally coordinated Ti(IV) sites. Then, highly dispersed dimeric forms of Ti were also found to provide good catalytic properties (Kholdeeva et al., 2002; Mrowiec-Białoń et al., 2004). Thus, an excellent dispersion of titanium in the silica skeleton is indispensable for the good catalytic properties of titania–silica mixed oxides, irrespective of their pore structure.
The MMRs with titania–silica monolithic cores (3.5 × 40 mm) were prepared by two methods: 1. direct synthesis of titania–silica monoliths with a nominal titanium content of 1, 2, and 5 wt% (D1, D2, and D5 samples) and 2. post-synthesis incorporation of titanium into silica monoliths using the grafting method (I1, I2, and I5 samples) (Mrowiec-Białoń et al., 2004). The preparation method appeared to be critical for macro- and mesopore structures of the monoliths, as well as for the dispersion of Ti species in the silica matrix. Those prepared by post-synthesis grafting had a pore structure fairly similar to that of the parent silica monolith (M1 type) in both the macropore and the mesopore size range. In stark contrast, the monoliths prepared by a direct method featured both macropore and mesopore structures much reduced in both pore size ranges. The macropore sizes ca. 8–10 µm and 2–4 μm and micropore size ca. 1.5 nm, as well as an overall porosity of 76 and 71%, for D1 and D2, respectively, strongly contrasted with 90% porosity, ca. 30 µm macropores and 20 nm mesopores present in all monoliths of the I-series. Moreover, these monoliths were not subjected to post-gelation alkaline treatment, which would hydrolyze the Si–O–Ti bonds. This drastic difference in the macropore structure and therefore flow-through potentials, illustrated in SEM images (compare Figure 2 and Figure 3) (Koreniuk et al., 2016), clearly evidences the profound influence of the titanium precursor on the formation of monoliths, but remarkably, the topology of the silica skeletons was still the same.
FIGURE 3. Relative dispersion vs. Ti content and SEM image of the macroporous structure of I2 and D2 monoliths.
A detailed instrumental analysis of all samples showed that titanium is much better dispersed in those samples provided by direct synthesis (D) than those by post-synthesis grafting (I), and that titanium dispersion in the silica matrix decreases with titanium content (Figure 3) (Koreniuk et al., 2016). Thus, the superior accessibility of the catalytic sites favors the use of post-synthesis grafting, whereas the much better titanium dispersion in D samples suggests the direct synthesis of mixed oxide monoliths.
Examination of the catalytic properties of MMRs obtained in the oxidation of 2,3,6-trimethylphenol (TMP) to 2,3,5-trimethylbenzoquinone (TMBQ) using an aqueous solution of H2O2 showed that the conversion of TMP is strongly dependent on both the pore structure and titanium content. For the decrease in the same flow rate, despite the reaction (residence) from 14.4 to 12,8 and 11.4 min, in reactors I1, I2, and I5, respectively, and even more in D samples, the conversion rapidly decreased in reverse order I5>I2>>I1>D2>>D1. This trend also remained valid for the TMBQ productivity related to the mass of the applied MMR. However, when the productivity was related to titanium content, the opposite trend was observed: I1>I2>>I5∼D1>D2, but still, the I-series proved to be better. Thus, the immediate availability of catalytic sites to the substrates, enabled by a very open structure, turned out to be much more important than the better intrinsic catalytic properties of titanium sites. Moreover, in a direct comparison of D2- and I2-MMR, carried out for a residence time of 4.5 min, flow rates differed by factor ca. 2.5 (larger for I2), and the reactor D2 provided much larger (50%) substrate conversion than I2 (35%). However, the nearly fivefold difference in productivity: 0.32 vs. 1.56 mmol/gRh, for D2 and I2, respectively, again strongly highlighted the advantages of MMRs obtained using post-synthesis modification.
In a comparative study of continuous-flow MMRs with batch (slurry) reactors with powdered monoliths and carried out under the same conditions and catalyst loading, batch reactors needed an hour to reach the same conversion as MMRs obtained in 10 minutes. As observed previously, the increase in titanium loading from 1 wt% to 2 wt% had a strong positive effect on the reaction rate, regardless of monolith synthesis, but a further increase to 5 wt% (possible only in I5) had a much smaller effect. This trend is perfectly portrayed by the TOF numbers related to the surface concentration of titanium, decreasing from 43 to 28 mol/molTisurfh for I1 and I5, respectively. Thus, the catalytic activity of Ti-MMRs fabricated using the direct deposition method is well-correlated with the surface titanium dispersion.
The performance of MMRs doped with various Lewis acid centers has been extensively studied in the chemoselective Meerwein–Ponndorf–Verley (MPV) reduction of carbonyl compounds—a widespread route for the synthesis of unsaturated secondary alcohols, and the results have been presented in a series of articles (Koreniuk et al., 2015a; Ciemięga et al., 2017b; Ciemięga et al., 2018; Maresz et al., 2018; Ciemięga et al., 2020). Preliminary studies showed that modification of silica monoliths (M1 structure) with zirconium (IV) propoxide (Zr-Pr-MMR) resulted in the formation of zirconium complexes with mixed propoxy/hydroxyl ligands bound to the silica surface, which were much more catalytically active than silica-supported zirconia (Zr-MMR) (Koreniuk et al., 2015a). Moreover, the complexes appeared to be protected against hydrolysis during this modification as well as during the reactor operation. The conversion of cyclohexanone in Zr-Pr-MMRs reached 90%, and excellent selectivity (ca. 100%) and stability of the 80-mm long reactor (4.5-mm dia.) were observed during eight reaction cycles (6 h/day). Further studies revealed that an excessive Zr content did not improve catalytic activity, and the nominal Zr/Si mass ratio of 0.14 was close to the optimal value (Ciemięga et al., 2017a). The productivity of cyclohexanol, of about 2.2 mmol/gRh at 88% substrate conversion, obtained in a continuous-flow 0.14Zr-Pr-MMR apparatus is more than two times as high as previously reported for Zr-MCM-41 in a batch (slurry) reactor and more than six times higher than when using powdered zirconia, that is, the catalysts recommended previously for this reaction. The modification of silica monoliths with various Lewis acid centers derived from different metal precursors, that is, metal alkoxides, chelated metal alkoxides, and salts showed that the microreactors doped with metal centers terminated with propoxy ligands were significantly (ca. 30%) more active than those exhibited by MMRs modified with oxides (Ciemięga et al., 2018). Much higher activity of Zr-Pr-MMR was also observed in the reduction of cyclohexanone and benzaldehyde with 2-butanol, than those modified with aluminum and titanium species, despite twice the concentration and strength of acid sites in aluminum-modified MMRs. Thus, the 0.14Zr-Pr-MMR–type microreactor appears to be the system of choice for in-flow synthesis of alcohols using the MPV reaction.
The recent study of the MPV reduction of a number of aldehydes and ketones, with 2-butanol in 0.14Zr-Pr-MMRs with the M1 structure, showed that its kinetics can be quantified by the first-order kinetics equation (Ciemięga et al., 2018; Ciemięga et al., 2020). First, preliminary experiments performed using reactors 10–80 mm of length (4.5 mm dia., velocities varying from 2 to 16 mm/min) clearly proved the lack of external mass transport limitation of reaction kinetics (Maresz et al., 2018). The temperature dependence of the reaction rate allowed for the estimation of the activation energy for the reduction of hexanone as equal to 52 kJ/mol and the frequency factor k = 2.69 1/min. The reaction rate constants determining MPV reduction of different carbonyl aldehydes and ketones showed that aldehydes are more reactive and that steric hindrance is a prevalent factor that affects the reactivity of substrates. Interestingly enough, in the MPV reduction of citral, its trans product appeared to be the preferential form, and this could again be explained by the preferential reduction of the steric limitation for bonding between the Zr center and C=O.
The comparative study of continuous-flow 0.14Zr-Pr-MMRs of different pore structures (M1-, M2-, and M3-type) with 0.14Zr-Pr-SBA-15 and 0.14Zr-Pr-MCF mesoporous catalysts applied in a batch reactor showed that the choice of the reactor and pore structure of the catalyst greatly impacted the kinetics of the MPV reaction (Ciemięga et al., 2020). Regardless of the pore structure, the reaction kinetics could still be expressed by the first-order equation, but the reaction rate constants varied considerably. For the M3 type of the MMR structure, its value (0.200/min) was five times higher than for M1 (0.043/min), in stark contrast to the content of Lewis acid sites being only 2.2 times higher in M3-MMR than in the M1 counterpart, with values for M2 between. As expected, the content of the acid sites turned out to be directly related to the specific surface area, yet it was only twice as large in M3 as in M1. Thus, the additional positive effect of M3 on M1 and M2 could be explained by the much better accessibility of the catalytic sites present in M3 than in the other monoliths, hence making better use of their intrinsic catalytic potentials. This could be concluded from the results of meticulous pore structure characterization (Ciemięga et al., 2020). In more practical terms, for 20-min contact time, the substrate conversion in the M3-type reactor was complete, whereas it was about 90% in M2 and only ca. 60% in M1. But M3 generated huge flow resistance, which precluded higher flow rates, owing to the need for high backpressure, which was avoided. In the comparative study performed in the batch reactor using M1 particles and modified SBA-15 and MCF-based catalysts, the reaction rate constants were fairly similar, but an order of magnitude lower than in the continuous flow (MMRs, vide supra). This again highlights the clear advantage of continuous-flow synthesis and the use of monolithic reactors.
Already the very first report on the MMRs with immobilized enzymes revealed their stunning performance (Szymańska et al., 2013). The enzyme invertase, considered as a model biocatalyst, was attached covalently to the monoliths (4 × 20–50 mm) of M1 structure via amino groups with glutaraldehyde (GLA) activation. The MMR performance was tested in the continuous-flow hydrolysis of sucrose. The results were compared with those of the batch reactor filled with particulate catalysts of either MCF-bound invertase or invertase attached to crushed monoliths. It is noteworthy that the MCF-bound invertase was previously shown to be the most active, and the Michaelis–Menten formalism served as a platform for quantitative analysis among different MPS-based biocatalysts tested in this reaction. Thus, it set a very strict criterion for the effectiveness of MMRs.
The experiments showed that the hydrolysis of sucrose proceeds with a maximum reaction rate (Vmax = k2CE0) of more than 1,000 times higher in the monolithic bioreactor than in the slurry batch system with MCF-attached invertase, and 88% sucrose conversion after only 3.3 s of mean residence time clearly demonstrated huge practical potentials of the MMRs. The monolithic reactor operated smoothly up to an inlet sucrose concentration of about 500 mM, above which the increase in viscosity seriously hampered the flow of the solution through the reactor. Surprisingly enough, the value of KM (affinity constant in the Michaelis–Menten equation) of 34.9 mM was notably lower for the monolithic reactor than determined for the native enzyme (42.5 mM), clearly evidencing higher affinity to substrates of the enzymes embedded in the hierarchically structured MMR than the native, freely suspended ones. The latter value was much the same as the one determined for powdered catalysts made from crushed monoliths (43.7 mM), whereas for the KM MCF–bound invertase, the value of KM was even slightly higher (47.4 mM), indicating a slightly lower tendency to substrate-enzyme complex formation. Catalysts made of crushed monoliths turned out to be approximately 40% more active than those prepared with the use of MCFs, and the specific activity of MCF-supported invertase (1100 U/mg) was nearly three times lower than that of invertase attached to monolithic powders (2915 U/mg). Thus, the studies performed clearly demonstrated that a unique pore structure of M1 monoliths creates the most favorable conditions for expressing very high enzyme activity, especially in flow synthesis, and identified enzymatically modified MMRs as a new class of microbioreactors with unique capabilities.
The MMRs (6 × 40 mm) of the M1 structure with trypsin immobilized covalently, as previously reported (Szymańska et al., 2013), or by physical adsorption (M1 functionalized with cyano groups) were later tested in the proteolytic digestion of proteins, that is, the process important for the production of bioactive peptides and in the peptide mapping of proteins, critical for the whole proteomics (Szymańska et al., 2016b). The studies performed showed that only covalent bonding of the enzymes afforded MMRs with stable catalytic properties in the flow reaction, and the weak protein–support interactions, typical for physical adsorption, did not protect the enzyme against leaching caused by the shear forces of the flowing liquid. The proteolytic performance of the MMR was examined in the continuous flow digestion of myoglobin and cytochrome c. The proteolytic efficiency, determined by the amino acid sequence coverage and quantified by its value, consistently decreased with higher flow rates/shorter digestion time, indicating that the rate of digestion was controlled by the kinetics of proteolysis and not diffusion. After 2.4 min of treatment/residence time (flow rate 0.3 ml/min), sequence coverage values were about 40–50%, whereas for the 24-min process (0.03 ml/min), they were ca. 90 and 70%, for myoglobin and cytochrome c, respectively. The latter values are similar to those obtained after 12-h proteolysis using conventional procedures and also much better than those reported earlier for a monolithic reactor with the chromatographic column structure. And not less importantly, the MMRs prepared appeared to be ideally suited for coupling with the MALDI-TOF/TOF mass spectrometry apparatus, thus making a system for rapid digestion and peptide mapping.
Acyltransferase from Mycobacterium smegmatis (MsAcT) immobilized in the MMR (6 × 50 mm) of the M1 structure enabled quantitative, complete, and rapid transesterification of neopentylglycol (NPG) with ethyl acetate in a biphasic 50/50% system in less than 1 minute (Szymańska et al., 2016a). The enzyme was attached either covalently, the same as in Szymańska et al. (2013), or by specific His-tag–mediated adsorption on Ni or Co sites, introduced in the earlier pretreatment of the monolith. Surprisingly enough, the enzyme loadings obtained from different immobilization methods were fairly similar, around 3 mg/g, as was their catalytic performance. This was explained by a similar orientation of the enzyme attached by means of a different immobilization procedure. On the whole, NPG transesterification in the monolithic reactor qualitatively portrayed all the trends observed in the earlier batch reactor studies, but a huge quantitative discrepancy between the operating characteristics of the batch reactor and the continuous-flow monolithic reactor was observed. For very short residence times (flow rates >1.5 ml/min), the reaction of monoester formation was extremely fast, in stark contrast to the reaction of diester formation, the concentration of which grew very slowly with time. Already very shortly (30 s) after reaction start-up, substrate conversion exceeded 90%, and after another 15 s, the substrate was fully converted. Thus, a residence time of less than 1 minute was sufficient to achieve complete esterification of one alcohol group, which indicates great potential of the proposed system for the continuous synthesis of biodiesel. For longer reaction/residence times (flow rates <1 ml/min), the concentration of the diester at exit continued to grow at the expense of the monoester. This indicated that the rate of the MsAcT-catalyzed reaction was dramatically increased in the MMR compared to the batch reactor with the native enzyme, in which full conversion was not achieved even during 7 h, regardless of the enzyme loading. Finally, regardless of the mode of enzyme attachment, the monolithic reactor showed very stable performance during almost 50 h of continuous operation, and intermediate washing of the reactor and storage in a buffer did not change the initial activity (Szymańska et al., 2016a).
More recently, the same group demonstrated exceptional properties of two hydroxynitrile lyases (HNLs), covalently attached to the siliceous monolith (M1 structure, 6 × 40 mm), in the first-ever reported continuous-flow enantioselective synthesis of chiral cyanohydrins of major industrial importance. In just 3.2 min, process substrate conversion reached 97% and (ee) (97%) to give the space-time yield (STY) of (S)-mandelonitrile 71 g/Lh·mgenz (van der Helm et al., 2019). At first, two different HNLs were recombinantly expressed and purified, and enzyme parameters relevant for the immobilization were determined. Then, both enzymes were immobilized on the powdered siliceous MCF carriers functionalized with either amino or epoxy groups, and minimal enzyme loadings were determined. However, further stability tests revealed superior properties of the biocatalysts with the enzyme immobilized by amino groups and GLA, and hence, this method was further used in the engineering of MMRs. The experiments performed in the batch reactor with MCF-attached HNL (slurry) catalysts resulted in a final enantiomeric excess (ee) of 87% (S) at a 38% conversion of benzaldehyde after 3 h and 94% conversion after about 30 h, but with an (ee) of only 42% (S) (van der Helm et al., 2019). This poor performance of the batch system was explained by the competing racemic background reaction, prevailing in the later stages of the reaction, that is, similar to that observed before for other silica carriers. Fascinatingly, switching to a continuous-flow system, with the MMR functionalized in the same way as MCF-NHL powder catalysts, leads to a huge improvement of the catalytic performance. Full conversion and excellent (ee) [99% (S)] were achieved within few minutes, and continuous-flow MMR effectively suppressed the competing background reaction, especially at higher flow rates (van der Helm et al., 2019). Thus, the enzyme-catalyzed enantioselective reaction is significantly faster when boosted by operating at higher flow rates, due to greatly enhanced mixing of liquid reagents and boosted mass transport to the liquid–catalyst/enzyme interface. These outcomes are perfectly in line with the results reported earlier (vide supra) for acyltransferase from the MsAcT immobilized in the structured monolithic reactor (Szymańska et al., 2016a).
Two articles were reported on enzyme-modified MMRs (both M1 structures) in the kinetic resolution of racemic mixtures (Zielińska et al., 2017; Strub et al., 2019). The kinetic resolution of N-acylated phosphorus analogs of amino acids or their esters in the penicillin G acylase–modified MMR (6 × 40 mm) was shown to be a very convenient and effective method (ee ∼ 99%, E > 100) to resolve these compounds. Furthermore, and more importantly, from a fundamental study perspective, a meticulous examination of the reaction kinetics carried out in the MMR, for a broad range of flow rates, clearly demonstrated that at a very low velocity of liquids (flow rate 0.01 ml/min), the reaction rate was much the same as that for the native enzyme. However, the increase in the flow rate by a factor of 50 (0.5 ml/min) boosted the reaction rate by more than two orders of the magnitude (Zielińska et al., 2017). This sheds light on the mechanism behind huge intensification of the reaction rate, which we observed in the enzyme-modified MMRs at high or very high flow rates.
The monolithic reactor (M1 structure, 6 × 40 mm) functionalized with hexadecyl groups was applied in the continuous kinetic resolution of the non-equimolar diastereoisomeric mixture with S:R = 85:15 of secondary allylic alcohol using P. cepacia lipase (PCL), and the results obtained were compared with those from the batch reactor filled with MPS-attached PCL (Strub et al., 2019). The flow rates applied in the MMR varied from 0.5 to 36 ml/min, and hence, the mean residence/reaction times in a single-pass flow ranged from just a few seconds to slightly over 2 min. For a very short reaction time (ca. 2 s), the conversion to the corresponding ester was about 8–10%, but for 2.2 min, it was full, that is, 85% in this case. Moreover, as a minor isomer appeared to be a very poor substrate for the enzymatic system, the dr value appeared to be very high (dr > 200:1), and a smooth monotonic variation of substrate conversion with the change in the flow rate facilitated process control to obtain the targeted conversion simply by changing the flow rate (Strub et al., 2019). The operational stability of the system was checked in a 133-h continuous operation, after which the conversion was only slightly lower than that at the beginning, but no change in the flow rate/pressure drop relationship was observed during this experiment. The performance of the batch slurry system was poor; 1 ml of the catalyst was able to produce no more than ca. 0.3 mg of the product during 1 h, whereas 0.96 ml of the monolithic reactor afforded 17.8 mg of the product in the same period. In this respect, the MMR developed afforded a remarkable STY value of about 100 g/hl. To conclude, the performed studies show that the non-equimolar mixture of diastereoisomeric alcohol can be resolved very effectively and rapidly in a continuous-flow lipase-promoted transesterification carried out in the structured monolithic reactor.
An effective method of non-covalent attachment of the conjugates of dendronized polymer (denpol) and enzyme into the silica monolith of the M1 structure has been shown to provide highly active enzymes stably immobilized in the structured monolithic reactors (Hou et al., 2019). The monolithic bioreactors obtained showed constant activity when repeatedly used at room temperature, after storage at 4°C, and also during continuous operation for 700 min. Compared to the previously developed micropipette-based rapid quantitative determination of H2O2 in aqueous solution, the product formation in such a modified MMR was always equal to or higher than that in micropipettes, despite the substantially shorter reacting time of substrates within the monolith than that of the micropipette. This effect could be explained by the very high surface-to-volume ratio featured by the monolithic microreactor, and especially when compared to the micropipette-based reactor. Moreover, the outflow signal depended linearly on the H2O2 concentration in the range of 1–50 µM (Hou et al., 2019). However, more importantly, the developed method provides a unique opportunity to co-immobilize stably different enzymes in the nearest vicinity in small confinements and hence imitates their operation in most real situations. Thus, the study contributes to and expands the toolbox currently available for bioanalytical and biosynthetic continuous-flow applications.
While the previous studies made use of a single monolithic reactor, the continuous-flow synthesis of trehalose from basic sugars was carried out in a bi-enzymatic (UDP-glucose pyrophosphorylase—TaGalU and trehalose transferase—mCherry-TuTreT) cascade process, using two MMRs connected in series (Figure 4) (Kowalczykiewicz et al., 2022). First, the immobilizations of both enzymes on functionalized silica supports were studied, and then suitable conditions for operation were determined. A drastic difference in the operating temperature, specific activity, and stability of each enzyme precluded their co-immobilization in a single reactor and necessitated a cascade made of two units, operating at different temperatures, with enzyme loadings adjusted to compensate for the difference in their activity. Prolonged continuous-flow operation showed that the system is operationally stable and offers high production capacity, but due to neutral pH and the type of substrate (glucose), it appeared to be prone to microbiological infections (Kowalczykiewicz et al., 2022). To conclude, the cascade developed, owing to its modular structure, can be further expanded, ideally to the full synthesis of trehalose and its analogues from glucose. But its engineering, described in much detail in the study by Kowalczykiewicz et al., 2022 can also serve as a model for the development of continuous-flow synthesis of various APIs with only catalytic amounts of substrates.
Structured monolithic microreactors feature a huge surface-to-volume ratio, and they also enable very intensive external mass transfer, both of which boost their catalytic performance. However, the residence time in a single-pass through-flow is limited by the length of the monolith and the applied flow rate, and it bears on substrate conversion, and hence the process economy. An effective solution that does not adversely affect intensity is the use of rotating bed reactors (RBR), sometimes nicknamed “SpinChem” reactors. RBRs make use of the spinning annular basket and the reactor concept and combine the advantages of packed bed reactors (PBRs) and stirred tank reactors (STRs). The reactants inside the rotating annular basket filled with catalyst beads are pushed away by centrifugal forces, and their new portions are drawn into the cell from the top and bottom, thus enabling their recycling inside the vessel. In this way, the catalyst beads, while rotating in the reactor, remain densely packed inside a basket, like those in the PBR, and this precludes their collisions and disintegration observed during vigorous mixing in STRs. In addition to that, the intensive flow of liquid reactants through the packed bed at high rotation speed boosts the liquid–solid volumetric mass transfer much more than the values observed in the standard fixed-bed (micro)reactors and also batch slurry reactors (STRs). Furthermore, the micromixing time in RBRs can even be as short as 10–4 s, that is, two orders of magnitude less than those in typical STRs with fine particulate catalysts, and that is of great, if not critical importance for very rapid reactions (Yang et al., 2005). Finally, but not less importantly, the reaction time is not restricted in RBRs, and once the target conversion is achieved, the catalytic cell can be separated from the vessel, washed, or otherwise treated to prevent (bio)catalyst decay in repeated applications and reused (Mallin et al., 2013).
So far, the RBR baskets were mostly packed with common particulate (bio)catalysts, for example, Novozym 435 (Pithani et al., 2019), provided the size was larger than 0.4–0.5 mm. However, to make full use of RBR potentials to improve reaction kinetics, we proposed to load the basket with larger catalytic pellets/beads, a few millimeters in size, but with a hierarchical pore structure, as in the M-monoliths (vide supra) (Szymańska et al., 2017). Such studies were carried out more recently, and the structured catalytic pellets did indeed enhance the reaction kinetics up to an order of magnitude, compared to the RBR packed with the most conventional particulate catalysts (Odrozek et al., 2017; Szymańska et al., 2017; Kowalczykiewicz et al., 2021). These studies are summarized in the following.
First, silica pellets of conical shape, 3 or 5 mm in size, and either M1 or M2 pore structures (Figure 5) (Szymańska et al., 2017), were prepared, and after covalent attachment of the enzyme invertase, their performance was examined in the reaction of sucrose hydrolysis using the RBR from SpinChem® (Szymańska et al., 2017). The experiments showed that for the same enzyme loading and rotation speed, the larger pellets of the M1 structure were 6–7 times more active than the corresponding pellets with the M2 structure. Moreover, they were even about ten times more active than the reference biocatalysts prepared using mesopore-predominated Kieselgel 60 as the enzyme support (applied as a reference). In effect, 96–99% substrate conversion was achieved in a reaction time of 75 min, while for the pellets with the M2 structure, it was ∼30%, and for the benchmark with the same enzyme content, the conversion was only ∼20%. And not less importantly, the larger catalytic pellets of the M1-type proved to be stable during at least 10 reaction runs. After regeneration, by calcination of deactivated catalysts and immobilization of fresh enzymes, the catalytic pellets could be reused at least 4–5 times without a notable decline in catalytic performance (Szymańska et al., 2017).
A more in-depth study of the reaction kinetics using M1- and M2-type structure pellets revealed that the reaction rate increased rapidly with an increase in the rotation speed (and hence fluid velocity) up to 500 rpm and then more slowly and tended to stabilize at about 750 rpm (centrifugal acceleration ∼11.5 g), a clear sign of a very strong positive effect of external mass transfer and micromixing on the apparent reaction rate. The reaction rates for the M1 pellets at the beginning of the reaction were 2.4 and 1.7 mM/minmgenz, and the higher value for the 5-mm pellets was due to the more intensive percolation of the reactants through the more open catalytic bed and its effect on the reaction kinetics (Szymańska et al., 2017). In this respect, what is a bit surprising is the large difference in activity between the pellets of the M1 and M2 structures, despite the same size and enzyme loading, and the apparently not very large difference in the pore structure in both macro- and mesopore size range.
The RBR with laccase covalently immobilized on the M1 pellets proved to be a very effective synthetic system also for the three-phase aerobic enzymatic oxidation of benzoic acid derivatives (Odrozek et al., 2017). The substrate conversion was strongly affected by the intensity of forced aeration and the speed of basket rotation, up to 500 rpm in particular. In a comparative study using a bubble column reactor with the same amount of immobilized catalysts and supplied air, the STY recorded for the RBR was a factor fourfold larger than that featured by the bubble column. It can be ascribed to the combined effect of both very intensive (mass) transfer of oxygen to a liquid phase at high (500 rpm) rotation speeds and its very rapid use in the enzyme-catalyzed reaction. In summary, by making use of a sustainable and environmentally benign catalyst and oxidant, the proposed system can be seen as a promising development for the intensive synthesis of various chemicals according to the principles of green chemical technology.
Most recently, the performance of the same synthetic system has been tested in hydrolysis and esterification reactions carried out in either the aqueous phase or organic solvents using CALB lipase (Kowalczykiewicz et al., 2021). The enzyme was attached to the pre-functionalized pellets in an open-lid conformation, either by covalent bonding or by adsorption forces. Compared to the same RBR but filled with commercial Novozym 435, the silica pellets grafted with both octyl and amino entities appeared the most effective in hydrolytic applications; they were both stable and highly active. For reactions in organic solvents, the silica pellets grafted with octyl groups appeared to be an optimal solution. Surprisingly enough, even most typical organic solvents appeared to exert a significant effect on the pore structure of Novozym 435 and hence its operational stability, which is often overlooked. To conclude, the synthetic system made of RBR filled with structured catalytic pellets lays the foundation for a new platform for the high-yield production of a wide variety of specialty chemicals on a multi-kilogram scale in a safe and sustained manner.
The reported studies clearly demonstrate that by boosting the kinetics of the reaction, and sometimes even a significant improvement of selectivity, structured monolithic reactors open new attractive prospects for the high-yield production of specialty chemicals in a continuous-flow system. The advantages of monolithic micro-/mesoreactors are considerable, sometimes very impressive and even astonishing, as observed in the enzymatic reactors, but they are well-documented and based on solid scientific foundations. In principle, they rely on greatly enhanced micromixing and external mass transfer to the skeleton surface (flow-through pore side), and an expanded external surface of the monoliths, readily accessible to reactants. Compared to most common mesoporous materials of spherical shape and size of ca. 50 µm, the surface area of crushed monoliths (dominated by cylindrical struts ca. 5–10 µm dia.) and also the flow-through surface area of the monoliths, may be roughly 3 to 6 times larger, which directly translates into enhanced reaction kinetics in both batch slurry systems, with the use of crushed monoliths and in monolithic reactors. This large external surface area of the silica skeleton also facilitates the access of substrates to the catalytic sites located deeper in its expanded (meso)pore structure and has a very positive effect on the efficiency of monolithic reactors. It should be noted that contrary to common belief, the intensity of mass transfer to fine porous catalytic particles or enzyme molecules flowing in the blobs of liquid reactants is low because the slip velocity between the solids and the liquids is extremely low, unlike in flows through the packed beds or structured monolithic reactors.
The experiments showed that for the more conventional catalytic sites, the increase of the reactant velocity in the monoliths had a moderate or no appreciable effect on the apparent reaction kinetics. In stark contrast, in the monoliths activated with most enzymes, the rise of velocity boosted the reaction kinetics even two orders of the magnitude, compared to batch reactors or free-flow experiments with native enzymes. The former can be ascribed to the slow intrinsic kinetics of many conventional catalysts, with the characteristic times of the intrinsic catalytic reaction similar to or longer than those of extremely intensive mass transport and lateral mixing in the monolithic reactors, especially at larger flow velocities. In contrast, the dramatic increase in reaction kinetics when enzymes are used can be explained by this intensive mass transfer and lateral mixing in tortuous channels of the structured monoliths, which relaxed the overwhelming diffusional limitation of the reaction rate featured by many enzymes in the batch reactors. Clearly, that very intensive mass transport is much easier and safer to implement by increasing the velocity in the monoliths generating low flow resistance (M1 and M2 structure), than in those which need a very large overpressure (M3 and M4 structure). The larger flow rates also boost overall productivity, and hence also process economy. Meanwhile, the enormous shearing stresses generated in monoliths with M3 and M4 structures can destabilize the enzyme or other susceptible catalysts. That is why the monoliths of the M1 structure proved so effective not only in the continuous flow application but also in the packing of the rotating bed reactors.
In the case of a very rapid reaction, the monoliths/pellets of the M1-type of the structure are the optimal solution in continuous-flow applications and RBRs, while in the case of slower intrinsic reaction kinetics, the M2 structure monoliths may also be a rational option worth considering. The observed complexity of the relationships between structure, catalytic properties, and MMR performance opens up a wide range of possibilities to modify and optimize the process of fabrication. First, it is worthwhile to develop a one-step method for silica monoliths modified with transition metals (Ti, Zr) with larger porosity both in the mesopore and macropore size range. The development of even larger structured monoliths/reactors and their application, making use of the numbering-up scale-up concepts, should significantly improve both the economy and safety of fine chemical production. Finally, the advancement of micro-/mesoreactors with multifunctional reactive cores, while challenging, opens a unique opportunity to generate a synergy of structural properties of materials and specific properties of the applied active sites. This should lead to a new class of high-performance reactors tailored to specific complex/sequential reactions. Although the monolithic reactors display some disadvantages, typical for all microreactors, that is, high manufacturing costs, clogging of flow channels with solid particles, and restriction to small-scale processes, on the whole, the structured monolithic reactors exhibit very promising and sometimes unique properties, which were demonstrated in this short review.
KS helped with the draft writing and drawing preparation. AC helped with the draft writing and drawing preparation. KM wrote the draft and drawing preparation. WP contributed to writing a draft. JM wrote the draft. JM-B wrote the draft. AJ wrote the draft and approved its final draft.
This research was partially funded by the National Science Centre of Poland, Grant number 2016/23/B/ST8/00627.
The authors declare that the research was conducted in the absence of any commercial or financial relationships that could be construed as a potential conflict of interest.
All claims expressed in this article are solely those of the authors and do not necessarily represent those of their affiliated organizations, or those of the publisher, the editors, and the reviewers. Any product that may be evaluated in this article, or claim that may be made by its manufacturer, is not guaranteed or endorsed by the publisher.
Alotaibi, M., Manayil, J. C., Greenway, G. M., Haswell, S. J., Kelly, S. M., Lee, A. F., et al. (2018). Lipase Immobilised on Silica Monoliths as Continuous-Flow Microreactors for Triglyceride Transesterification. React. Chem. Eng. 3 (1), 68–74. doi:10.1039/c7re00162b
Baccour, M., Lamotte, A., Sakai, K., Dubreucq, E., Mehdi, A., Kano, K., et al. (2020). Production of Formate from CO2 Gas under Ambient Conditions: towards Flow-Through Enzyme Reactors. Green. Chem. 22, 3727–3733. doi:10.1039/d0gc00952k
Berdys, M., Koreniuk, A., Maresz, K., Pudło, W., Jarzębski, A. B., and Mrowiec-Białoń, J. (2015). Fabrication and Performance of Monolithic Continuous-Flow Silica Microreactors. Chem. Eng. J. 282, 137–141. doi:10.1016/j.cej.2015.01.132
Brun, N., Babeau-GarciaAchard, A. M. F., Achard, M.-F., Sanchez, C., Durand, F., Laurent, G., et al. (2011). Enzyme-based Biohybrid Foams Designed for Continuous Flow Heterogeneous Catalysis and Biodiesel Production. Energy Environ. Sci. 4, 2840–2844. doi:10.1039/C1EE01295A
Chrobok, A., Baj, S., Pudło, W., and Jarzębski, A. (2009). Supported Hydrogensulfate Ionic Liquid Catalysis in Baeyer-Villiger Reaction. Appl. Catal. A: Gen. 366 (1), 22–28. doi:10.1016/j.apcata.2009.06.040
Chrobok, A., Baj, S., Pudło, W., and Jarzębski, A. (2010). Supported Ionic Liquid Phase Catalysis for Aerobic Oxidation of Primary Alcohols. Appl. Catal. A: Gen. 389 (1-2), 179–185. doi:10.1016/j.apcata.2010.09.022
Ciemięga, A., Maresz, K., and Mrowiec-Białoń, J. (2018). Meervein-Ponndorf-Vereley Reduction of Carbonyl Compounds in Monolithic Siliceous Microreactors Doped with Lewis Acid Centres. Appl. Catal. A: Gen. 560, 111–118. doi:10.1016/j.apcata.2018.04.037
Maresz, K., Ciemięga, A., and Mrowiec-Białoń, J. (2020). Monolithic Microreactors of Different Structure as an Effective Tool for in Flow MPV Reaction. Chem. Eng. J. 379, 122281. doi:10.1016/j.cej.2019.122281
Ciemięga, A., Maresz, K., Malinowski, J., and Mrowiec-Białoń, J. (2017a). Continuous-Flow Monolithic Silica Microreactors with Arenesulphonic Acid Groups: Structure-Catalytic Activity Relationships. Catalysts 7 (9), 255. doi:10.3390/catal7090255
Ciemięga, A., Maresz, K., and Mrowiec-Białoń, J. (2017b). Continuous-flow Chemoselective Reduction of Cyclohexanone in a Monolithic Silica-Supported Zr(OPri)4 Multichannel Microreactor. Microporous Mesoporous Mater. 252, 140–145. doi:10.1016/j.micromeso.2017.06.023
Drożdż, A., Chrobok, A., Baj, S., Szymańska, K., Mrowiec-Białoń, J., and Jarzębski, A. B. (2013). The Chemo-Enzymatic Baeyer-Villiger Oxidation of Cyclic Ketones with an Efficient Silica-Supported Lipase as a Biocatalyst. Appl. Catal. A: Gen. 467, 163–170. doi:10.1016/j.apcata.2013.07.009
Ehrfeld, W., Hessel, V., and Lowe, H. (2000). Microeactors: New Technology for Modern Chemistry. Weinheim: Willey-VCH.
El Kadib, A., Chimenton, R., Sachse, A., Fajula, F., Galarneau, A., and Coq, B. (2009). Functionalized Inorganic Monolithic Microreactors for High Productivity in Fine Chemicals Catalytic Synthesis. Angew. Chem. Int. Ed. 48 (27), 4969–4972. doi:10.1002/anie.200805580
Galarneau, A., Abid, Z., Said, B., Didi, Y., Szymanska, K., Jarzębski, A., et al. (2016a). Synthesis and Textural Characterization of Mesoporous and Meso-/Macroporous Silica Monoliths Obtained by Spinodal Decomposition. Inorganics 4 (2), 9. doi:10.3390/inorganics4020009
Galarneau, A., Sachse, A., Said, B., Pelisson, C.-H., Boscaro, P., Brun, N., et al. (2016b). Hierarchical Porous Silica Monoliths: A Novel Class of Microreactors for Process Intensification in Catalysis and Adsorption. Comptes. Rendus. Chim. 19 (1-2), 231–247. doi:10.1016/j.crci.2015.05.017
Haas, C. P., Müllner, T., Kohns, R., Enke, D., and Tallarek, U. (2017). High-performance Monoliths in Heterogeneous Catalysis with Single-phase Liquid Flow. React. Chem. Eng. 2 (4), 498–511. doi:10.1039/c7re00042a
Hou, C., Ghéczy, N., Messmer, D., Szymańska, K., Adamcik, J., Mezzenga, R., et al. (2019). Stable Immobilization of Enzymes in a Macro- and Mesoporous Silica Monolith. Acs Omega 4 (4), 7795–7806. doi:10.1021/acsomega.9b00286
Kawakami, K., Sera, Y., Sakai, S., Ono, T., and Ijima, H. (2005). Development and Characterization of a Silica Monolith Immobilized Enzyme Micro-bioreactor. Ind. Eng. Chem. Res. 44 (1), 236–240. doi:10.1021/ie049354f
Kholdeeva, O. A., Trukhan, N. N., Vanina, M. P., Romannikov, V. N., Parmon, V. N., Mrowiec-Białoń, J., et al. (2002). A New Environmentally Friendly Method for the Production of 2,3,5-Trimethyl-P-Benzoquinone. Catal. Today 75 (1-4), 203–209. doi:10.1016/S0920-5861(02)00070-6
Koreniuk, A., Maresz, K., and Mrowiec-Białoń, J. (2015a). Supported Zirconium-Based Continuous-Flow Microreactor for Effective Meerwein-Ponndorf-Verley Reduction of Cyclohexanone. Catal. Commun. 64, 48–51. doi:10.1016/j.catcom.2015.01.021
Koreniuk, A., Maresz, K., Odrozek, K., Jarzębski, A. B., and Mrowiec-Białoń, J. (2015b). Highly Effective Continuous-Flow Monolithic Silica Microreactors for Acid Catalyzed Processes. Appl. Catal. A: Gen. 489, 203–208. doi:10.1016/j.apcata.2014.10.047
Koreniuk, A., Maresz, K., Odrozek, K., and Mrowiec-Białoń, J. (2016). Titania-Silica Monolithic Multichannel Microreactors. Proof of Concept and Fabrication/Structure/catalytic Properties in the Oxidation of 2,3,6-Trimethylphenol. Microporous Mesoporous Mater. 229, 98–105. doi:10.1016/j.micromeso.2016.04.020
Kowalczykiewicz, D., Szymańska, K., Gillner, D., and Jarzębski, A. B. (2021). Rotating Bed Reactor Packed with Heterofunctional Structured Silica-Supported Lipase. Developing an Effective System for the Organic Solvent and Aqueous Phase Reactions. Microporous Mesoporous Mater. 312, 110789. doi:10.1016/j.micromeso.2020.110789
Kowalczykiewicz, D., Przypis, M., Mestrom, L., Kumpf, A., Tischler, D., Hagedoorn, P.-L., et al. (2022). Engineering of Continuous Bienzymatic Cascade Process Using Monolithic Microreactors - in Flow Synthesis of Trehalose. Chem. Eng. J. 427, 131439. doi:10.1016/j.cej.2021.131439
Mallin, H., Muschiol, J., Byström, E., and Bornscheuer, U. T. (2013). Efficient Biocatalysis with Immobilized Enzymes or Encapsulated Whole Cell Microorganism by Using the SpinChem Reactor System. ChemCatChem 5 (12), 3529–3532. doi:10.1002/cctc.201300599
Maresz, K., Ciemięga, A., and Mrowiec-Białoń, J. (2018). Selective Reduction of Ketones and Aldehydes in Continuous-Flow Microreactor-Kinetic Studies. Catalysts 8 (5), 221. doi:10.3390/catal8050221
Mrowiec-Białoń, J., Jarzębski, A. B., Kholdeeva, O. A., Trukhan, N. N., Zaikovski, V. I., Kriventsov, V. V., et al. (2004). Properties of the Sol-Gel TiO2-SiO2 Oxidation Catalysts Prepared Using Ethyl Silicate 40 as a Silica Precursor. Appl. Catal. A: Gen. 273 (1-2), 47–53. doi:10.1016/j.apcata.2004.06.040
Nakanishi, K., Takahashi, R., Nagakane, T., Kitayama, K., Koheiya, N., Shikata, H., et al. (2000). Formation of Hierarchical Pore Structure in Silica Gel. J. Sol-Gel Sci. Technol. 17 (3), 191–210. doi:10.1023/A:1008707804908
Odrozek, K., Szymańska, K., Lewanczuk, M., Dzido, G., Pudło, W., Bryjak, J., et al. (2017). Aerobowe, Enzymatyczne Utlenianie Pochodnych Kwasu Benzoesowego W Reaktorze Z Wirującym Złożem O Hierarchicznej Strukturze Porów. Chem. Rev. 1 (12), 72–75. doi:10.15199/62.2017.12.7
Pithani, S., Karlsson, S., Emtenäs, H., and Öberg, C. T. (2019). Using Spinchem Rotating Bed Reactor Technology for Immobilized Enzymatic Reactions: A Case Study. Org. Process. Res. Dev. 23 (9), 1926–1931. doi:10.1021/acs.oprd.9b00240
Pudło, W., Gawlik, W., Mrowiec-Białoń, J., Buczek, T., Malinowski, J. J., and Jarzębski, A. B. (2006). Materials with Multimodal Hierarchical Porosity. Inżynieria Chem. i Procesowa 27 (1), 177–185.
Roucher, A., Roussarie, E., Gauvin, R. M., Rouhana, J., Gounel, S., Stines-Chaumeil, C., et al. (2019). Bilirubin Oxidase-Based Silica Macrocellular Robust Catalyst for on Line Dyes Degradation. Enzyme Microb. Technol. 120, 77–83. doi:10.1016/j.enzmictec.2018.10.004
Sachse, A., Galarneau, A., Coq, B., and Fajula, F. (2011a). Monolithic Flow Microreactors Improve fine Chemicals Synthesis. New J. Chem. 35 (2), 259–264. doi:10.1039/c0nj00965b
Sachse, A., Galarneau, A., Fajula, F., Di Renzo, F., Creux, P., and Coq, B. (2011b). Functional Silica Monoliths with Hierarchical Uniform Porosity as Continuous Flow Catalytic Reactors. Microporous Mesoporous Mater. 140 (1-3), 58–68. doi:10.1016/j.micromeso.2010.10.044
Smått, J.-H., Schunk, S., and Lindén, M. (2003). Versatile Double-Templating Synthesis Route to Silica Monoliths Exhibiting a Multimodal Hierarchical Porosity. Chem. Mater. 15 (12), 2354–2361. doi:10.1021/cm0213422
Stankiewicz, A. (2001). Process Intensification in In-Line Monolithic Reactor. Chem. Eng. Sci. 56 (2), 359–364. doi:10.1016/S0009-2509(00)00236-0
Strub, D. J., Szymańska, K., Hrydziuszko, Z., Bryjak, J., and Jarzębski, A. B. (2019). Continuous Flow Kinetic Resolution of a Non-equimolar Mixture of Diastereoisomeric Alcohol Using a Structured Monolithic Enzymatic Microreactor. React. Chem. Eng. 4 (3), 587–594. doi:10.1039/c8re00177d
Szymańska, K., Pudło, W., Mrowiec-Białoń, J., Czardybon, A., Kocurek, J., and Jarzębski, A. B. (2013). Immobilization of Invertase on Silica Monoliths with Hierarchical Pore Structure to Obtain Continuous Flow Enzymatic Microreactors of High Performance. Microporous Mesoporous Mater. 170, 75–82. doi:10.1016/j.micromeso.2012.11.037
Szymańska, K., Odrozek, K., Zniszczoł, A., Torrelo, G., Resch, V., Hanefeld, U., et al. (2016a). MsAcT in Siliceous Monolithic Microreactors Enables Quantitative Ester Synthesis in Water. Catal. Sci. Technol. 6 (13), 4882–4888. doi:10.1039/c5cy02067k
Szymańska, K., Pietrowska, M., Kocurek, J., Maresz, K., Koreniuk, A., Mrowiec-Białoń, J., et al. (2016b). Low Back-Pressure Hierarchically Structured Multichannel Microfluidic Bioreactors for Rapid Protein Digestion - Proof of Concept. Chem. Eng. J. 287, 148–154. doi:10.1016/j.cej.2015.10.120
Szymańska, K., Odrozek, K., Zniszczoł, A., Pudło, W., and Jarzębski, A. B. (2017). A Novel Hierarchically Structured Siliceous Packing to Boost the Performance of Rotating Bed Enzymatic Reactors. Chem. Eng. J. 315, 18–24. doi:10.1016/j.cej.2016.12.131
Taramasso, M., Perego, C., and Notari, B. (1984). Preparation of Porous Crystalline Synthetic Material Comprised of Silicon and Titanium Oxides. US Patent 4 410 501.
van den Biggelaar, L., Soumillion, P., and Debecker, D. P. (2019). Biocatalytic Transamination in a Monolithic Flow Reactor: Improving Enzyme Grafting for Enhanced Performance. RSC Adv. 9, 18538–18546. doi:10.1039/C9RA02433F
van der Helm, M. P., Bracco, P., Busch, H., Szymańska, K., Jarzębski, A. B., and Hanefeld, U. (2019). Hydroxynitrile Lyases Covalently Immobilized in Continuous Flow Microreactors. Catal. Sci. Technol. 9 (5), 1189–1200. doi:10.1039/c8cy02192a
Xie, S., Svec, F., and Fréchet, J. M. J. (1999). Design of Reactive Porous Polymer Supports for High Throughput Bioreactors: Poly(2-Vinyl-4,4-Dimethylazlactone-Co-Acrylamide-Co-Ethylene Dimethacrylate) Monoliths. Biotechnol. Bioeng. 62 (1), 30–35. doi:10.1002/(Sici)1097-0290(19990105)62:1<30::Aid-Bit4>3.0.Co;2-E
Yang, H.-J., Chu, G.-W., Zhang, J.-W., Shen, Z.-G., and Chen, J.-F. (2005). Micromixing Efficiency in a Rotating Packed Bed: Experiments and Simulation. Ind. Eng. Chem. Res. 44 (20), 7730–7737. doi:10.1021/ie0503646
Zhokh, A., Strizhak, P., Maresz, K., Ciemięga, A., and Mrowiec-Białoń, J. (2020). Diffusion in Hierarchical Silica Monoliths: Impact of Pore Size and Probe Molecule. Heat Mass. Transfer 56 (12), 3199–3207. doi:10.1007/s00231-020-02929-3
Zielińska, K., Szymańska, K., Mazurkiewicz, R., and Jarzębski, A. (2017). Batch and In-Flow Kinetic Resolution of Racemic 1-(N-Acylamino)alkylphosphonic and 1-(N-Acylamino)Alkylphosphinic Acids and Their Esters Using Immobilized Penicillin G Acylase. Tetrahedron: Asymmetry 28 (1), 146–152. doi:10.1016/j.tetasy.2016.11.007
Keywords: in-flow synthesis, structured monolithic reactors, micro-/mesoreactors, enzymatic microreactors, process intensification
Citation: Szymańska K, Ciemięga A, Maresz K, Pudło W, Malinowski J, Mrowiec-Białoń J and Jarzębski AB (2021) Catalytic Functionalized Structured Monolithic Micro-/Mesoreactors: Engineering, Properties, and Performance in Flow Synthesis: An Overview and Guidelines. Front. Chem. Eng. 3:789102. doi: 10.3389/fceng.2021.789102
Received: 04 October 2021; Accepted: 05 November 2021;
Published: 02 December 2021.
Edited by:
Anne Galarneau, UMR5253 Institut de chimie moléculaire et des matériaux Charles Gerhardt Montpellier (ICGM), FranceReviewed by:
Andrey N. Zagoruiko, Boreskov Institute of Catalysis (RAS), RussiaCopyright © 2021 Szymańska, Ciemięga, Maresz, Pudło, Malinowski, Mrowiec-Białoń and Jarzębski. This is an open-access article distributed under the terms of the Creative Commons Attribution License (CC BY). The use, distribution or reproduction in other forums is permitted, provided the original author(s) and the copyright owner(s) are credited and that the original publication in this journal is cited, in accordance with accepted academic practice. No use, distribution or reproduction is permitted which does not comply with these terms.
*Correspondence: Katarzyna Szymańska, a2F0YXJ6eW5hLnN6eW1hbnNrYUBwb2xzbC5wbA==; Julita Mrowiec-Białoń, SnVsaXRhLk1yb3dpZWMtQmlhbG9uQHBvbHNsLnBs; Andrzej B. Jarzębski, YW5kcnplai5qYXJ6ZWJza2lAcG9sc2wucGw=
Disclaimer: All claims expressed in this article are solely those of the authors and do not necessarily represent those of their affiliated organizations, or those of the publisher, the editors and the reviewers. Any product that may be evaluated in this article or claim that may be made by its manufacturer is not guaranteed or endorsed by the publisher.
Research integrity at Frontiers
Learn more about the work of our research integrity team to safeguard the quality of each article we publish.