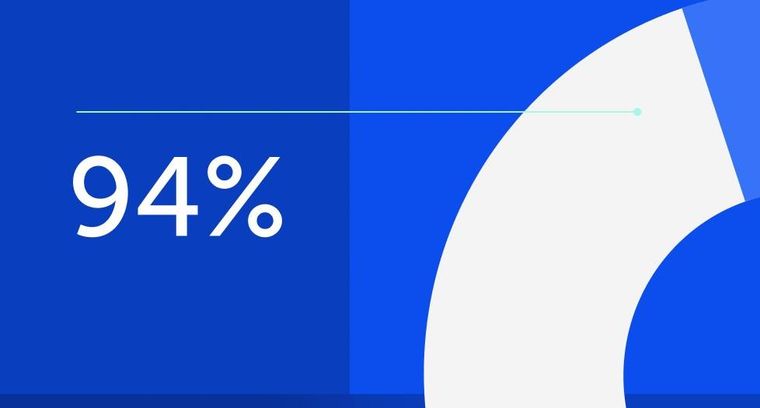
94% of researchers rate our articles as excellent or good
Learn more about the work of our research integrity team to safeguard the quality of each article we publish.
Find out more
ORIGINAL RESEARCH article
Front. Chem. Eng., 20 November 2020
Sec. Separation Processes
Volume 2 - 2020 | https://doi.org/10.3389/fceng.2020.596555
This article is part of the Research TopicFrom CO2 emissions to Fuels and Chemicals: Current Development, Challenges and Perspectives View all 6 articles
The capture of CO2 from the atmosphere via Direct Air Capture using solid supported-amine sorbents is an important option to reduce the atmospheric concentration of CO2. It addresses CO2 emissions from dispersed sources and delivers a location independent, sustainable carbon source. This study evaluates the possibility for a continuous adsorption process for direct air capture in a radial flow contactor, using both batch and continuous mode of operation. Gas and solid flow were varied to determine hydrodynamic feasible operating conditions. The operation modes are compared by their capture efficiencies in the optimal adsorption time range of 0.5
Direct air capture (DAC) is the extraction of CO2 directly from the atmosphere. It is considered a core element in reducing global CO2 emissions (Lackner et al., 2012). Capturing CO2 from air has the ability to: 1) mitigate CO2 emissions from dispersed sources, which contribute for approximately 45% of the total CO2 emissions in the US (USEPA, 2018), 2) deliver, anywhere, a renewable carbon source for carbon-neutral processes and 3) enable other carbon-negative products/technologies.
Even though we consider the CO2 concentration in air to be (too) high, it is very low regarding separation purposes. Therefore, a highly selective separation process is required. Adsorption is among the most promising technologies to capture CO2 from air (Goeppert et al., 2012; Brilman and Veneman, 2013; Lu et al., 2013; Sanz-Pérez et al., 2016; Yang et al., 2019; Stampi-Bombelli et al., 2020). Research on the development of adsorption materials is widely available in literature (Choi et al., 2009; D'Alessandro et al., 2010; Shekhah et al., 2014; Kumar et al., 2015; Sanz-Pérez et al., 2016; Gelles et al., 2020; Singh et al., 2020). Selective adsorption of CO2 onto the sorbent is usually based on a chemical reaction of CO2 with functional groups on the sorbents internal surface. Amines in particular are suitable for CO2 capture, as is evident from the benchmark CO2 absorption process using an aqueous ethanolamine solution (Topham et al., 2014). Caplow (1968), and later Danckwerts (1979), proposed a two-step reaction mechanism for reaction of amines with CO2 via the formation of a zwitterion (Caplow, 1968; Danckwerts, 1979). The zwitterion is then deprotonated by a base. On the other hand, Crooks and Donnellan (1989) proposed a termolecular mechanism where the reaction occurs in a single step. CO2 reacts simultaneously with the amine and with a base. They claim the termolecular mechanism is more likely than the zwitterion mechanism. Experimental results from Mukherjee et al. (2018) support this statement for the reaction of CO2 with benzylamine in an aqueous environment.
The sorbent used in this study has a polystyrene backbone with above mentioned benzylamine as functional group attached. The sorbent is able to capture CO2 at both dry and humid conditions. At humid conditions, depending on humidity, the CO2 capacity is up to 50% higher, suggesting that both carbamate formation and bicarbonate formation play a role.
A complete adsorption process cycle consists of two steps. The first step is the adsorption of CO2 onto the surface of the sorbent. This is preferred at ambient conditions, since large volumes are processed (at least 1,400 m3 for 1 kg of CO2) and a pre-treatment would be energy intensive. The second step is the regeneration of the sorbent. In this latter phase, the product gas is collected and lean sorbent is obtained for reuse in the adsorption step. The reaction of CO2 with the amine can be reversed by a temperature and/or pressure swing (Bos et al., 2018; Elfving et al., 2021). In this research, we focus on the adsorption step of a sorbent-based DAC process.
Efficient gas-solid contacting is an important aspect of the DAC process, especially for the adsorption phase. Contactors for DAC include monolith (Kulkarni and Sholl, 2012), fluidized bed (Zhang et al., 2014) and fixed bed (Wurzbacher et al., 2012; Bajamundi et al., 2019; Yu and Brilman, 2020), of which the latter one is the most common. During adsorption, the sorbent material remains fixed in the reactor during the process. In the systems of Bajamundi et al. (2019) and Wurzbacher et al. (2012), sorbent regeneration occurs in the same reactor where the operating conditions are changed. As alternative, the sorbent itself can be transported between separate adsorption and desorption units, as utilized in the study of Yu and Brilman (2020). This limits the energy penalty for temperature swing regeneration as only the sorbent material needs to be heated, instead of the whole contactor.
Yu and Brilman (2020) designed a direct air capture system using a radial flow contactor with the option of sorbent circulation. Adsorption was performed in batches, where the complete sorbent batch was transported to the regeneration section at once. Freshly regenerated sorbent was then loaded to the radial flow contactor. This system also allows for full continuous operation as a cross-flow moving bed. In that study, a single run demonstrated the technical feasibility, but also a significant reduction in capture efficiency. In this work, we revisit this option to investigate opportunities for performance improvement.
Moving bed contactors are well suitable for processes with a rapid, but reversible decay in activity of the solid material. In chemical reaction technology, this situation is encountered when dealing with rapid catalyst deactivation (Ginestra and Jackson, 1985; Pilcher and Bridgwater, 1990; Shirzad et al., 2019). In adsorption technology, like here for DAC, a similar rapid decrease in activity occurs due to saturation of the sorbent. Moving bed contactors are already considered for post-combustion CO2 capture (Kim et al., 2013; Grande et al., 2017; Mondino et al., 2019). However, these employ a counter-current moving bed, whereas this study concerns a cross-flow moving bed. In a cross-flow moving bed contactor, the gas flow is perpendicular to the solid flow, which results in a drag force that acts upon the particles. Under certain process conditions this leads to undesired hydrodynamic phenomena known as “pinning” and “cavity” (Ginestra and Jackson, 1985; Doyle et al., 1986; Pilcher and Bridgwater, 1990; Long et al., 2015; Wang et al., 2020). The drag force exerted by the cross flow gas stream on the particles results in a friction force of the solids on the downstream (with respect to the gas flow) porous wall. At a sufficiently high gas velocity, this (partially or completely) prevents the solids from moving downwards. This phenomenon is known as “pinning”. A “cavity” may form between the upstream porous wall and the solids, thus reducing the effective bed length. As a result local gas bypassing will occur, which lowers the efficiency of the process.
Research into the hydrodynamics of a moving bed contactor started in the 1980s where Ginestra and Jackson (1985) analyzed the mechanism of “pinning” and “cavity” of a rectangular cross flow moving bed. Doyle et al. (1986) extended this analysis to a radial flow moving bed, since this configuration is more common for industrial applications. Pilcher and Bridgwater (1990) further investigated the mechanism of “pinning” by varying particle size and bed thickness and observed four distinct modes of pinning. In addition, they mention several other parameters that can influence the flow pattern of the solids such as solid distribution at the inlet and packing structure near the porous walls. Long et al. (2015) proposes a trapezoidal cross-flow moving bed, which significantly increases the critical gas velocity for “pinning” compared to a rectangular configuration. Another optimization is proposed by Wang et al. (2020), in which gas-solid baffles are placed in the middle of the bed that reduces pinning and cavity. However, the effect of the before mentioned phenomena on the actual performance and potential of the moving bed system is not discussed. In this study, we assess the possibility of performing direct air capture in a radial flow moving bed contactor. This is done by comparing the capture efficiency of this continuous system with that of the corresponding batch wise operated system. Therefore, we do not investigate whether phenomena like “pinning” and “cavity” occur. Instead, we investigate the magnitude of their influence within the desired operating range of direct air capture on the capture performance.
The sorbent material used in this study is Lewatit® VP OC 1065 (Lanxess). This is a polymeric, amine-functionalized sorbent with polystyrene-divinylbenzene copolymer as support and primary benzyl amines as functional groups. Using energy-dispersive X-ray spectroscopy, Alesi et al. (Alesi and Kitchin, 2012) determined the concentration of these functional groups at 7.5 mol/kg. Other physical properties of the sorbent can be found in Table 1. The sorbent was prepared in a two-step process, which is only required upon first use of the sorbent. In the first step, excess water is removed, since the sorbent originally, as purchased, contains up to 50 wt% water. For this, the sorbent is placed in an oven (80°C) under nitrogen flow for at least 16 h. Approximately 98% of the adsorbed water is removed. In the second step, a small amount of graphite (∼0.3 wt%) is mixed with the sorbent to reduces the static effects during sorbent handling.
The stability of the sorbent is validated to make sure that the quality of the sorbent does not decrease over time. A sample is taken at several time intervals during the experiments and the capacity is determined by thermogravimetric analysis. The CO2 capacity of the sorbent is measured at 1.76 ± 0.04 mol/kg at 40°C and 15% CO2 in N2. The performance of the sorbent did not decrease over time (Figure 1).
FIGURE 1. CO2 capacity of the sorbent as function of operation time. The capacity is determined by thermogravimetric analysis at 40°C and 15% CO2 in N2. The average CO2 capacity is 1.76 mol/kg with a standard deviation of 0.04 mol/kg.
In all adsorption experiments, air is sucked in directly from the laboratory. The air composition (CO2 concentration and humidity) is affected by weather conditions, lab use and air ventilation. In all desorption experiments, high purity N2 is used.
Batch (or fixed bed) experiments are used as reference point for the continuous experiments. The experimental set-up is shown in Figure 2. The gas-solid contactor is a π-type radial flow contactor with inwards flow. The sorbent is contained between two porous faces with a mesh size of 400 µm. Yu and Brilman (2017) designed this contactor specifically for direct air capture. In this respect, a bed length of 40 cm and bed thickness of only 1.5 cm is selected, which enables operation at a low pressure drop. This results in an effective sorbent mass of 1.72 kg. Also, some sorbent is present in the volume between the radial flow part of the reactor and the rotary valve, which results in a total sorbent mass of approximately 2 kg. During adsorption, the air flow is controlled by a centrifugal fan (ER 120, Itho Daalderop). The CO2 concentration, temperature and pressure drop are measured. Two CO2 analyzers (LI-COR LI840A) determine the CO2 concentration in the inlet and outlet of the contactor, the temperature is monitored at three location in the sorbent bed (4, 19, and 36 cm from sorbent inlet) and in the ingoing air and, finally, the pressure drop between the inner and outer channel is measured with a differential pressure transmitter (DMD 341 from DB SENSORS).
FIGURE 2. Schematic of the experimental set-up. Blue arrows illustrate gas flow direction and red arrows illustrate solid flow direction (in case of a continuous process).
Adsorption and sorbent regeneration is performed in the radial flow contactor, so the same sorbent batch is used for all batch experiments. The sorbent is regenerated before all adsorption experiments. For this, a temperature of 100°C and a nitrogen flow of 70 NL/min (0.55 cm/s) is used. Regeneration is continued until the CO2 concentration in the outlet is below 10 ppm. This corresponds to an equilibrium capacity of approximately 2 mmol/kg. Batch adsorption experiments are performed for a superficial gas velocity of 0.10–0.40 m/s, corresponding to a Reynolds number of 4.2–17.8. Adsorption is continued until equilibrium is reached.
Continuous (or moving bed) experiments are carried out in the same set-up as batch experiments (Figure 2). The experiments are very similar to ones in the batch mode of operation, except that the solid particles are continuously added to and withdrawn from the contactor. The solid flux is driven by gravity and controlled with a rotary valve by adjusting the motor voltage. Steady-state operation is expected to begin after all sorbent in the contactor is replaced once with freshly added (regenerated) sorbent and this steady-state was maintained for another sorbent residence time. This procedure thus requires an available amount of sorbent of at least three times the sorbent hold-up of the contactor (hence, around 6 kg). The experiments are continued until all sorbent passed the contactor through the rotary valve. The performance of the moving bed configuration is evaluated between
The basis of this study is to compare the performance of the continuous operation with batch operation. Therefore, a methodology is required to fairly compare these results. As performance indicators, the gas- and solid efficiencies are used. The gas efficiency is defined as the fraction of CO2 that is captured from the air that is supplied (Eq. 1) and the solid efficiency is defined as the saturation level of the sorbent (Eq. 2). In both Eqs 1 and 2, we neglect the effect of the reduced CO2 concentration on the total gas flow rate. For batch operation, these are a function of time, since the sorbents get saturated as the adsorption progresses. Therefore, the solid efficiency increases with time. This results in a lower driving force for adsorption and, hence, a lower adsorption rate and decreasing gas efficiency over time. During continuous operation, on the other hand, a steady state situation is reached. Therefore, the continuous operated system results in a single gas and solid efficiency (Eqs 3 and 4, again, neglecting the effect of reduced CO2 concentration on the total gas flow rate).
A comprehensible method is required to compare both operation modes. The approach selected here is to process the same amount of sorbent for a given amount of time. In batch operation always the same amount of sorbent is used, whereas for the continuous operation this depends on the solid flux. To compare both process operating modes, the same gas-sorbent contact time is applied, which is calculated with Eq. 5. Note that this is not necessarily the real average residence time of the solid sorbent in the contactor since the value of
The adsorption time is normalized by the stoichiometric time. This is the point when the amount of CO2 fed is equal to the maximum amount of CO2 that can be adsorbed. The stoichiometric time concept was shown to be very useful for the optimization of a direct air capture process (Yu and Brilman, 2017).
For a batch process the stoichiometric time is calculated by Eq. 6. For a continuous process it is not possible to define a stoichiometric time, but is merely operating at a certain normalized adsorption time. This is found by combining Eqs. 5 and 6 to obtain Eq. 7. This is the ratio of the CO2 supply rate and the maximum CO2 removal rate.
By combining Eqs 1–7, the following relation is found:
Batchwise adsorption experiments were performed in the radial flow contactor for a superficial velocity of 0.10–0.40 m/s. Figure 3 shows the CO2 loading of the sorbent over time. Faster adsorption is observed at increasing flowrate due to the higher average bulk concentration over the radial length of the adsorption bed. External mass transfer and feed rate limitations are negligible above 0.20 m/s, hence internal mass transfer resistance and reaction rate limitations control the sorbent saturation rate. A flowrate above 0.20 m/s is therefore not preferred and the experiments at 0.10 and 0.20 m/s are used as basis for comparison between batch and continuous operation.
FIGURE 3. Breakthrough curves of the batch experiments for various superficial gas velocities. The equilibrium capacity at direct air capture conditions under the prevailing lab conditions is indicated as well.
The contact time of the gas phase with the sorbent is very short (0.04–0.15 s), therefore immediate breakthrough is observed. This is visible in the gas efficiency, which immediately drops considerably at the start of the adsorption, especially for the higher gas velocity (Figure 4). The capture efficiency decreases strongly with the gas velocity when going from 0.2 to 0.4 m/s, but the productivity increases to a much lesser extent (Figure 3). This effectively means that more compression power is spend for a faster adsorption of CO2. On the other hand, for the envisioned thermal swing adsorption process, this will save energy during desorption as more CO2 is produced with the same energy penalty. The time of adsorption is therefore a trade-off between compression duty and thermal energy duty. For this specific adsorption process using a radial flow contactor, circulating sorbent batches and the considered gas velocity range, the optimal adsorption time was found between 0.5
FIGURE 4. Gas and solid efficiencies as function of stoichiometric time corresponding to the measured breakthrough curves from Figure 3.
The operation window of a radial flow moving bed contactor in terms of gas velocity and solid flux is specific to each design. Phenomena as pinning and cavity limit the possible operating range of such a contactor (Ginestra and Jackson, 1985; Doyle et al., 1986; Chen et al., 2007). General parameters such as particle size, bed thickness and Reynolds number affect this operation range. However, other aspects are very specific such as the location of gas inlet, the distribution of solid particles and mesh size of the porous faces. To determine whether it is possible to operate this contactor at the desired process conditions, its hydrodynamic operation window with respect to gas and solids flow is determined. The solid flux is measured for gas velocities ranging from 0–0.5 m/s. For this, the solids are collected after the reactor and solid flux is determined by measuring the mass of the sorbent collected in a certain amount of time.
It was found that only the gas velocity affects the hydrodynamic operation range. No limitations are observed in terms of solid flux, at least up to 400 g/m2/s (Figure 5). This is in line with the investigation of Chen et al. (2007) for a comparable operation window in terms of gas velocity and solid flux. Above approximately 0.3 m/s the solid flux stops completely due to the effects of cavity formation and pinning. Irregularities in solid flux are sometimes observed below this threshold gas velocity down to approximately 0.25 m/s. In this range, the total solid flux is as expected. However, by visual observation it was found that the solid flow is either not continuous over time or not evenly distributed across the radial cross section. At gas velocities up to 0.2 m/s, this radial flow moving bed contactor can be operated without any notable disturbances in solid flow. These critical values for the gas velocity are much lower than reported by Chen et al. (2007), 0.3 m/s and 0.84 m/s respectively. This is caused by the smaller particle size (0.67 mm vs. 1.96 mm) and smaller bed thickness (15 mm vs. 105 mm).
FIGURE 5. Operation window for moving bed operation in the radial flow contactor. The solid flow is either good (green,
The optimal adsorption time, or solid residence time, for a DAC process (
Continuous adsorption experiments reach a steady state situation. Since adsorption is started with lean sorbent, this is observed after the bed is fully refreshed (Figure 6). The experiment runs until no more sorbent is available, hence the outlet CO2 concentration equals the inlet. After one sorbent refreshment, the CO2 concentration remains stable, however some fluctuations are present in all experiments. This indicates that some disturbances in either solid flux of gas distribution are always present.
FIGURE 6. Typical CO2 concentration profiles for a continuous adsorption experiment. A steady-state is observed after the sorbent is refreshed once. The experiment ends when all sorbent left the reactor.
The experimental conditions and results for the continuous adsorption experiments are given in Table 2. Air is extracted from the laboratory, hence some variation in the experimental (inlet-) conditions is unavoidable. The differences in temperature and CO2 concentration result in an equilibrium loading between 0.82 and 0.87 mol/kg. With this, the standard deviation in reaction rate remains within 4%. Relative humidity is another (weather) condition that is known to influence the equilibrium loading. The spread in the humidity (40–60% RH) is larger than the variation in the temperature and CO2 concentration in the current set of (indoor) experiments. However, we do not see a clear effect of this variation in relative humidity in the results. Overall, we conclude that within this dataset the fluctuations in experimental conditions do not influence the results significantly.
It is expected that the sorbent loading increases with sorbent residence time and gas velocity, similar to the batch process. This is indeed also observed for the continuous process. However, the influence of gas velocity seems less pronounced. Especially for a solid flux of 60 g/m2/s there is barely any increase in sorbent loading when the gas velocity increases from 0.10 to 0.22 m/s. For the gas efficiency there is a significant difference in efficiency noticeable. This indicates that also at 0.22 m/s some influence of cavity formation or pinning is present that is more prominent at a lower solid flux.
There is a clear trade-off between solid efficiency (
The CO2 capacity of the sorbent (
FIGURE 7. Working capacity of the continuous process compared to the batch process at corresponding solid residence time.
Furthermore, we compare the batch and continuous processes by their gas and solid efficiencies. The adsorption time and solid residence time are normalized to their stoichiometric times and plotted in Figure 8A together with the dimensionless curves for the batch process. This allows for a fair comparison between gas velocities and reduces the influence of slightly different operation conditions as well. Batch operation is in all cases more efficient than a continuous process in terms of capture efficiency. A reduction of 15–25% is observed within the desired operation range of
FIGURE 8. Comparison of the continuous process with the batch process. Error margins represent the standard deviation by error propagation. (A) Gas and solid efficiency according to Eqs (1)–(4) and (B) the ratio of the efficiency between batch and continuous.
Although we operate in the “green” area of the operating window, we observe a decrease in performance of the continuous process compared to the batch process. We propose two effects that contribute to this. The first effect is the reduced solid hold-up in the radial flow contactor during continuous operation, which was briefly mentioned before. This reduces the residence time of the sorbent and lowers the adsorption rate. To give an idea, the solid hold-up for this sorbent at minimum fluidization is about 17% lower than for a fixed bed. In a cross-flow moving bed the reduction in solid hold-up is most likely not that large, but can still be significant. This may explain the decrease in capture efficiency for an increasing gas flow. However, this will not explain the decreased efficiency over time. The second effect that may play a role is the possible occurrence of non-homogeneous sorbent flow inside the contactor. Possible causes are the formation and collapse of cavities or deviation from plug flow behavior due to shear forces on the porous faces. This will contribute to a lower solid hold-up, as well as a wider residence time distribution of solid material.
Reduced gas-solid contacting is expected to give rise to a reduction in pressure drop. The pressure drop is measured between the inner channel and the outer channel. This is only measured at a single vertical position, but is confirmed to be constant along the axial length of the contactor. Along the azimuth angle we were not able to validate this, but it might vary due to the location of the gas inlet.
For a superficial gas velocity of 0.20 m/s, a small (some 10%) reduction in pressure drop is observed for the continuous operation in comparison to batch operation. This is in contrast with the results at a gas velocity of 0.10 m/s. The pressure drop is found to be independent of the solid flux (within the experimental range), and consequently the gas-solid contacting is also not likely to be affected by the solid flux. The difference in results between 0.10 and 0.20 m/s gas velocity in Figure 9, might indicate the formation of cavities in the radial bed and a (slightly) reduced sorbent hold-up.
During the adsorption process a temperature profile may develop. The reactive adsorption of CO2 on the surface of the sorbent is an exothermic process and the specific heat of the sorbent is low. However, the adsorbing particles are cooled by a large convective air flow. Since the saturation level of the sorbent negatively effects the reaction rate, a temperature profile as function of time or axial length of the contactor is expected for respectively the batch and continuous process. A possible gradient in temperature can affect the local reaction rate and hence capture efficiency. The temperature is measured at three locations in the bed (at a height of 4, 19 and 36 cm) and in the air inlet. For all experiments, the air inlet has a slightly different temperature due to temporal variations in the ambient temperature. For that reason, the temperature increase with respect to air inlet temperature is used for comparison and not the absolute temperature.
The temperature profiles in Figure 10A do not show large surprises. Convective cooling is very significant, as the temperature excursion is lower for 0.2 m/s while the average CO2 uptake rate is higher. One could argue that the higher temperature causes a higher reaction rate and that this is the difference observed in capture efficiency. However, the difference between continuous and batch processes, shown in Figure 8, is present for both gas velocities. In order to compare the temperature profiles to the batch process, the temperature should be described as a function of sorbent residence time. For example at 19 cm, the residence time of the sorbent is 27.2, 13.6 and 6.8 min for 0.5, 1 and 2 g/s (or 63, 125 and 250 g/m2/s) respectively. The temperature for the batch process is taken as the average temperature of the three locations.
FIGURE 10. Temperature increase during the steady-state phase of the radial flow moving bed experiments as function of: (A) axial location of the contactor (0 = top; 40 cm = bottom) and (B) solid residence time (batch process data is added for comparison). The error margins represent the standard deviation in the steady-state temperature.
With this transformation, the temperature profile is nearly identical for the batch and continuous process (Figure 10B). For the continuous process, the peak temperature seems slightly lower. This might be related to heat dispersion by the moving solids. Considering the reduced reaction rate during continuous operation, the temperature is actually expected to be lower than during batch operation. This is not the case, if any the temperature is higher for the continuous process. Therefore, convective cooling is less efficient in a continuous process, which indicates to a decrease in gas-solid contacting.
The capture efficiency of a continuous adsorption process in a radial flow moving bed contactor is significantly lower compared to the corresponding batch process. This efficiency decreases with 1) the increasing superficial gas velocity and 2) increasing adsorption time. The contacting of gas and solid becomes less effective for a moving bed. Temperature profiles support this statement, where a decline in convective cooling is observed. Also, the pressure drop is slightly lower, especially for 0.20 m/s. Since the pressure drop is only measured at a single location, local variations cannot be observed, but are most likely present. A reduced solid hold-up and irregularities in solid flow are identified as possible sources of the decrease in gas-solid contacting. The solid hold-up in the gas-solid contactor during a continuous process is estimated to be at most 17% lower than for a batch process. How the solids hold-up is affected by solid flux and gas velocity is not known and requires further study. Irregularities in solid flow give rise to a wider residence time distribution for the sorbent phase. A detailed and dedicated hydrodynamics study of this gas-solid contactor is therefore recommended and required to investigate the magnitude of these phenomena.
The reproducibility is validated for a batch operation experiment. Although weather conditions do not allow for an exact replication of the experiment, the deviation in loading after 4 h was only 2%. Continuous experiments are not reproduced due to the time consuming desorption procedure. However, for each and every experiment, the gas and solid flows are checked. Also, the performance of the sorbent itself is verified and found to be stable throughout the measurement campaign. Therefore, the results are considered reproducible and trends to be reliable.
All experiments started with nearly completely regenerated sorbents, since this ensures an equal starting point for all experiments. In an actual process with sorbent circulation, full regeneration is not likely because it takes too much time to reach such a high regeneration level. Since the required adsorption time is then also a bit shorter, the difference between continuous and batch may become smaller.
Two other factors diminish the difference between the performance of batchwise operation and continuous operation. These will be related to the process economics for both energy consumption as well as the effective use of invested capital on equipment. Firstly, in continuous operation, the availability of the gas-solid contactor is full time, whereas for batch wise operation the loading and unloading of the contactor must be accounted for. For the contactor in this study, the down time is about 4 min per cycle, but can vary widely for other configurations. The reduction in equipment availability can be as high as 30% (0.22 m/s and
This study compares the performance of a radial flow moving bed adsorption process with a batch process. The process is tailored for Direct Air Capture using a supported amine sorbent. In the desired operating regime for DAC, the capture efficiency of a continuous process is lowered by 15–25% compared to a batch process. This decrease in gas-solid contacting efficiency is higher with increasing superficial gas velocity, which indicates the occurrence of pinning and cavity even at these low Reynolds numbers. In addition, the continuous process performs increasingly worse as the adsorption progresses. Nonetheless, a continuous process can still become more profitable is case of a low gas velocity combined with a short adsorption phase, due to the time penalty for sorbent replacement during batch operation.
The raw data supporting the conclusions of this article will be made available by the authors, without undue reservation
MS and TJ designed this study and the methodology. TJ performed the experiments. MS, TJ, and WB were involved in the data analysis and data interpretation. MS wrote the manuscript under supervision of WB Methodology: MS and TJ, Data collection: TJ, Data analysis and interpretation: MS, TJ and WB, Writing: MS, Supervision: WB.
This research was funded by NORTH-WEST EUROPE INTERREG, grant number NWE 639 as part of the IDEA project (Implementation and development of economic viable algae-based value chains in North-West Europe).
The authors declare that the research was conducted in the absence of any commercial or financial relationships that could be construed as a potential conflict of interest.
Alesi, W. R., and Kitchin, J. R. (2012). Evaluation of a primary amine-functionalized ion-exchange resin for CO2 capture. Ind. Eng. Chem. Res. 51 (19), 6907–6915. doi:10.1021/ie300452c
Bajamundi, C. J. E., Koponen, J., Ruuskanen, V., Elfving, J., Kosonen, A., Kauppinen, J., et al. (2019). Capturing CO2 from air: technical performance and process control improvement. J. of CO2 Utilization. 30, 232–239. doi:10.1016/j.jcou.2019.02.002
Bos, M. J., Kersten, S. R. A., and Brilman, D. W. F. (2020). Wind power to methanol: renewable methanol production using electricity, electrolysis of water and CO2 air capture. Appl. Energy 264, 114672. doi:10.1016/j.apenergy.2020.114672
Bos, M. J., Kroeze, V., Sutanto, S., and Brilman, D. W. F. (2018). Evaluating regeneration options for bulk CO2 removal from biogas using solid amine sorbents. Ind. Eng. Chem. 57, 11141–11153. doi:10.1021/acs.iecr.8b00768
Brilman, D. W. F., and Veneman, R. (2013). Capturing atmospheric CO2 using supported amine sorbents. Energy Procedia. 37, 6070–6078. doi:10.1016/j.egypro.2013.06.536
Caplow, M. (1968). Kinetics of carbamate formation and breakdown. J. Am. Chem. Soc. 90 (24), 6795–6803. doi:10.1021/ja01026a041
Chen, Y., Zhu, X., Wu, Y., and Zhu, Z. (2007). The investigation of pressure drop in moving-beds. Front. Chem. Eng. China. 1 (2), 184–189. doi:10.1007/s11705-007-0034-4
Choi, S., Drese, J. H., and Jones, C. W. (2009). Adsorbent materials for carbon dioxide capture from large anthropogenic point sources. ChemSusChem. 2 (9), 796–854. doi:10.1002/cssc.200900036
Crooks, J. E., and Donnellan, J. P. (1989). Kinetics and mechanism of the reaction between carbon dioxide and amines in aqueous solution. J. Chem. Soc., Perkin Trans. 2 (4), 331–333. doi:10.1039/P29890000331
D’Alessandro, D. M., Smit, B., and Long, J. R. (2010). Carbon dioxide capture: prospects for new materials. Angew. Chem. Int. Ed. 49 (35), 6058–6082. doi:10.1002/anie.201000431
Danckwerts, P. V. (1979). The reaction of CO2 with ethanolamines. Chem. Eng. Sci. 34 (4), 443–446. doi:10.1016/0009-2509(79)85087-3
Doyle, F. J., Jackson, R., and Ginestra, J. C. (1986). The phenomenon of pinning in an annular moving bed reactor with crossflow of gas. Chem. Eng. Sci. 41 (6), 1485–1495. doi:10.1016/0009-2509(86)85233-2
Driessen, R. T., Knaken, B., Buzink, T., Jacobs, D. A. F., Hrstka, J., and Brilman, D. W. F. (2020a). Design and proof of concept of a continuous pressurized multi-stage fluidized bed setup for deep sour gas removal using adsorption. Powder Technol. 366, 859–872. doi:10.1016/j.powtec.2020.03.013
Driessen, R. T., van der Linden, J. J. Q., Kersten, S. R. A., Bos, M. J., and Brilman, D. W. F. (2020b). Characterization of mass transfer in a shallow fluidized bed for adsorption processes: modeling and supporting experiments. Chem. Eng. J. 388, 123931. doi:10.1016/j.cej.2019.123931
Elfving, J., Kauppinen, J., Jegoroff, M., Ruuskanen, V., Järvinen, L., and Sainio, T. (2021). Experimental comparison of regeneration methods for CO2 concentration from air using amine-based adsorbent. Chem. Eng. J. 404, 126337. doi:10.1016/j.cej.2020.126337
Gelles, T., Lawson, S., Rownaghi, A. A., and Rezaei, F. (2020). Recent advances in development of amine functionalized adsorbents for CO2 capture. Adsorption. 26 (1), 5–50. doi:10.1007/s10450-019-00151-0
Ginestra, J. C., and Jackson, R. (1985). Pinning of a bed of particles in a vertical channel by a cross flow of gas. Ind. Eng. Chem. Fund. 24 (2), 121–128. doi:10.1021/i100018a001
Goeppert, A., Czaun, M., Surya Prakash, G. K., and Olah, G. A. (2012). Air as the renewable carbon source of the future: an overview of CO2 capture from the atmosphere. Energy Environ. Sci. 5 (7), 7833–7853. doi:10.1039/C2EE21586A
Grande, C. A., Kvamsdal, H., Mondino, G., and Blom, R. (2017). Development of moving bed temperature swing adsorption (MBTSA) process for post-combustion CO2 capture: initial benchmarking in a NGCC context. Energy Procedia. 114, 2203–2210. doi:10.1016/j.egypro.2017.03.1357
Kim, K., Son, Y., Lee, W. B., and Lee, K. S. (2013). Moving bed adsorption process with internal heat integration for carbon dioxide capture. International Journal of Greenhouse Gas Control. 17, 13–24. doi:10.1016/j.ijggc.2013.04.005
Kulkarni, A. R., and Sholl, D. S. (2012). Analysis of equilibrium-based TSA processes for direct capture of CO2 from air. Ind. Eng. Chem. Res. 51 (25), 8631–8645. doi:10.1021/ie300691c
Kumar, A., Madden, D. G., Lusi, M., Chen, K.-J., Daniels, E. A., Curtin, T., et al. (2015). Direct air capture of CO2 by physisorbent materials. Angew. Chem. Int. Ed. 54 (48), 14372–14377. doi:10.1002/anie.201506952
Lackner, K. S., Brennan, S., Matter, J. M., Park, A. H. A., Wright, A., and van der Zwaan, B. (2012). The urgency of the development of CO2 capture from ambient air. Proc. Natl. Acad. Sci. Unit. States Am. 109 (33), 13156–13162. doi:10.1073/pnas.1108765109
Lanxess (2017). Product information Lewatit VP OC 1065. [Online]. Available at https://products.lanxess.com/ (Accessed September 20, 2020).
Long, W., Xu, J., Fan, Y., and Lu, C. (2015). Pinning and cavity in two types of cross-flow moving beds. Powder Technol. 269, 66–74. doi:10.1016/j.powtec.2014.09.013
Lu, W., Sculley, J. P., Yuan, D., Krishna, R., and Zhou, H.-C. (2013). Carbon dioxide capture from air using amine-grafted porous polymer networks. J. Phys. Chem. C. 117 (8), 4057–4061. doi:10.1021/jp311512q
Mondino, G., Grande, C. A., Blom, R., and Nord, L. O. (2019). Moving bed temperature swing adsorption for CO2 capture from a natural gas combined cycle power plant. Int. J. Greenh. Gas Control. 85, 58–70. doi:10.1016/j.ijggc.2019.03.021
Mukherjee, S., Bandyopadhyay, S. S., and Samanta, A. N. (2018). Kinetic study of CO2 absorption in aqueous benzylamine solvent using a stirred cell reaction calorimeter. Energy Fuels. 32 (3), 3668–3680. doi:10.1021/acs.energyfuels.7b03743
Pilcher, K. A., and Bridgwater, J. (1990). Pinning in a rectangular moving bed reactor with gas cross-flow. Chem. Eng. Sci. 45 (8), 2535–2542. doi:10.1016/0009-2509(90)80139-6
Sanz-Pérez, E. S., Murdock, C. R., Didas, S. A., and Jones, C. W. (2016). Direct capture of CO2 from ambient air. Chem. Rev. 116 (19), 11840–11876. doi:10.1021/acs.chemrev.6b00173
Shekhah, O., Belmabkhout, Y., Chen, Z., Guillerm, V., Cairns, A., Adil, K., et al. (2014). Made-to-order metal-organic frameworks for trace carbon dioxide removal and air capture. Nat. Commun. 5, 4228. doi:10.1038/ncomms5228
Shirzad, M., Karimi, M., Silva, J. A. C., and Rodrigues, A. E. (2019). Moving bed reactors: challenges and progress of experimental and theoretical studies in a century of research. Ind. Eng. Chem. Res. 58 (22), 9179–9198. doi:10.1021/acs.iecr.9b01136
Singh, G., Lee, J., Karakoti, A., Bahadur, R., Yi, J., Zhao, D., et al. (2020). Emerging trends in porous materials for CO2 capture and conversion. Chem. Soc. Rev. 49 (13), 4360–4404. doi:10.1039/d0cs00075b
Stampi-Bombelli, V., van der Spek, M., and Mazzotti, M. (2020). Analysis of direct capture of CO2 from ambient air via steam-assisted temperature-vacuum swing adsorption. Adsorption., 26, 1183. doi:10.1007/s10450-020-00249-w
Topham, S., Bazzanella, A., Schiebahn, S., Luhr, S., Zhao, L., Otto, A., et al. (2014). “Carbon dioxide,” in Ullmann’s encyclopedia of industrial chemistry. (Weinheim, Germany: Wiley-VCH Verlag GmbH), 1–43.
USEPA (2018). Carbon dioxide emissions. [Online]. Available at https://www.epa.gov/ghgemissions/overview-greenhouse-gases#carbon-dioxide (Accessed August 18, 2020).
Wang, R., Wang, D., Fan, Y., Lu, C., Hu, B., and Zhang, S. (2020). Cavity, pinning and air lock in both rectangular and radial cross-flow moving beds with a gas-solid baffle. Powder Technol. 374, 449–461. doi:10.1016/j.powtec.2020.07.021
Wurzbacher, J. A., Gebald, C., Piatkowski, N., and Steinfeld, A. (2012). Concurrent separation of CO2 and H2O from air by a temperature-vacuum swing adsorption/desorption cycle. Environ. Sci. Technol. 46 (16), 9191–9198. doi:10.1021/es301953k
Yang, M., Ma, C., Xu, M.-m., Wang, S., and Xu, L. (2019). Recent advances in CO2 adsorption from air: a review. Curr. Pollut. Reports. 5, 272–293.
Yu, Q., and Brilman, D. W. F. (2017). Design strategy for CO2 adsorption from ambient air using a supported amine based sorbent in a fixed bed reactor. Energy Procedia. 114, 6102–6114. doi:10.1016/j.egypro.2017.03.1747
Yu, Q., and Brilman, W. (2020). A radial flow contactor for ambient air CO2 capture. Appl. Sci. 10 (3), 1080. doi:10.3390/app10031080
Keywords: direct air capture, radial flow adsorber, supported amine sorbents, adsorption, moving bed adsorber
Citation: Schellevis M, Jacobs T and Brilman W (2020) CO2 Capture From Air in a Radial Flow Contactor: Batch or Continuous Operation?. Front. Chem. Eng. 2:596555. doi: 10.3389/fceng.2020.596555
Received: 19 August 2020; Accepted: 14 October 2020;
Published: 20 November 2020.
Edited by:
Adele Brunetti, National Research Council (CNR), ItalyReviewed by:
Mohammad Younas, University of Engineering & Technology Peshawar, PakistanCopyright © 2020 Schellevis, Jacobs and Brilman. This is an open-access article distributed under the terms of the Creative Commons Attribution License (CC BY). The use, distribution or reproduction in other forums is permitted, provided the original author(s) and the copyright owner(s) are credited and that the original publication in this journal is cited, in accordance with accepted academic practice. No use, distribution or reproduction is permitted which does not comply with these terms.
*Correspondence: Michel Schellevis, aC5tLnNjaGVsbGV2aXNAdXR3ZW50ZS5ubA==
Disclaimer: All claims expressed in this article are solely those of the authors and do not necessarily represent those of their affiliated organizations, or those of the publisher, the editors and the reviewers. Any product that may be evaluated in this article or claim that may be made by its manufacturer is not guaranteed or endorsed by the publisher.
Research integrity at Frontiers
Learn more about the work of our research integrity team to safeguard the quality of each article we publish.