- 1Sustainable Technologies for Industrial Processes, Energy Transition, TNO, Petten, Netherlands
- 2Sustainable Process & Energy Systems, Energy Transition, TNO, Delft, Netherlands
Dimethyl ether (DME) is an important platform chemical and fuel that can be synthesized from CO2 and H2 directly. In particular, sorption-enhanced DME synthesis (SEDMES) is a novel process that uses the in situ removal of H2O with an adsorbent to ensure high conversion efficiency in a single unit operation. The in situ removal of steam has been shown to enhance catalyst lifetime and boost process efficiency. In addition, the hydrogen may be supplied through water electrolysis using renewable energy, making it a promising example of the (indirect) power-to-X technology. Recently, major advances have been made in SEDMES, both experimentally and in terms of modeling and cycle design. The current work presents a techno-economic evaluation of SEDMES using H2 produced by a PEM electrolyzer. A conceptual process design has been made for the conversion of CO2 and green H2 to DME, including the purification section to meet ISO fuel standards. By means of a previously developed dynamic cycle model for the SEDMES reactors, a DME yield per pass of 72.4 % and a carbon selectivity of 84.7% were achieved for the studied process design after optimization of the recycle streams. The production costs for DME by the power-to-X technology SEDMES process at 23 kt/year scale are determined at ∼€1.3 per kg. These costs are higher than the current market price but lower than the cost of conventional DME synthesis from CO2. Factors with the highest impact on the business cases are the electricity and CO2 cost price as well as the CAPEX of the electrolyzer, which is considered an important component for technology development. Furthermore, as the H2 cost constitutes the largest part of the DME production cost, SEDMES is demonstrated to be a powerful technology for efficient conversion of green H2 into DME.
Introduction
In the energy transition, industry plays an essential role. Industry accounted for 37% (156 EJ) of the total global energy use in 2017, of which around 70% originates from fossil fuels (IEA, 2019). These are used as a fuel and feedstock, leading to concomitant emissions of carbon dioxide. Conversely, according to the United Nations’ 2030 Agenda for Sustainable Development (UNFPA, 2020), industry needs to become sustainable, with increased resource-use efficiency and greater adoption of clean and environmentally sound technologies and industrial processes. Indeed, with increasing shares of renewables in electricity generation portfolios, the electrification of industrial processes contributes to the uptake of renewable energy in industry (IEA, 2019). In addition, through the development and implementation of circular practices including the chemical recycling of carbon dioxide, industry will become an essential element of the carbon-neutral economy (Centi and Perathoner, 2009; Olah et al., 2009; Ordomsky et al., 2017; SPIRE, 2020). The conversion of carbon dioxide into fuels and feedstock using electricity can thus contribute to a sustainable society (Artz et al., 2018; Detz et al., 2018; Kätelhön et al., 2019).
The conversion of carbon dioxide with electricity can be accomplished through the so-called power-to-X (PtX) technologies (Rego de Vasconcelos and Lavoie, 2019; Sánchez et al., 2019). Such PtX technologies comprise the direct electrochemical conversion of carbon dioxide to chemicals, as well as indirect conversion of carbon dioxide via thermochemical conversion routes, using hydrogen produced by electrolysis. Both approaches are currently under development in a multinational consortium in the European Interreg project Electrons to High-Value Chemical Products (E2C, 2020). As shown in Figure 1, the current work focuses on the indirect conversion of carbon dioxide with hydrogen to dimethyl ether (DME), a promising fuel and platform chemical (Semelsberger et al., 2006; Olah et al., 2009; Matzen and Demirel, 2016; Bongartz et al., 2018).
Although several routes exist and are currently in operation for the industrial synthesis of DME (Müller and Hübsch, 2000; Azizi et al., 2014), separation-enhanced synthesis routes have shown to offer major advantages in the conversion of carbon dioxide to chemicals (van Kampen et al., 2019). In fact, sorption-enhanced DME synthesis (SEDMES) has proven to yield a very high single-pass carbon selectivity to DME (Iliuta et al., 2011; van Kampen et al., 2020a; van Kampen et al., 2020b; van Kampen et al., 2020c). In this novel technology, steam is adsorbed in situ to overcome the thermodynamic limits of the reactions involved, resulting in the high single-pass DME yield. Previous research has focused on process development, including reactor engineering (Guffanti et al., 2020) and catalytic aspects (Boon et al., 2019; Liuzzi et al., 2020). A techno-economic assessment (TEA) of the SEDMES technology has not yet been published, although the production of DME from CO2 and water using renewable energy has been studied in terms of economics (Martín, 2016) and life cycle analysis (LCA) (Matzen and Demirel, 2016).
The Interreg E2C project has the objective to combine hydrogen from electrolysis with an advanced SEDMES technology leading to a versatile and powerful route from carbon dioxide to high-value chemical products. This includes the construction of a containerized and highly flexible pilot demonstrator, and the development of the business case.
This article presents the techno-economic assessment of DME synthesis from carbon dioxide using the SEDMES technology in the two sea areas, meaning the coastal regions along the Southern North Sea and the Channel area in England, France, the Netherlands, and Belgium. First, a flow sheet is developed for the process to produce DME starting from electricity and carbon dioxide, including downstream processing (DSP) (Figure 2). Specific attention will be paid to the SEDMES unit, presenting the first full design for the conversion of carbon dioxide and hydrogen to DME. Finally, the TEA is presented, with the goal to assess the cost of producing DME via the PtX SEDMES process and to identify the most important cost drivers and corresponding R&D priorities. Sensitivity analyses on these factors are discussed. While a comparative assessment to conventional DME synthesis is outside the scope of the current work, the economic potential of sorption-enhanced synthesis will be highlighted by comparison to DME synthesis from electricity and carbon dioxide via the conventional reactor technology.
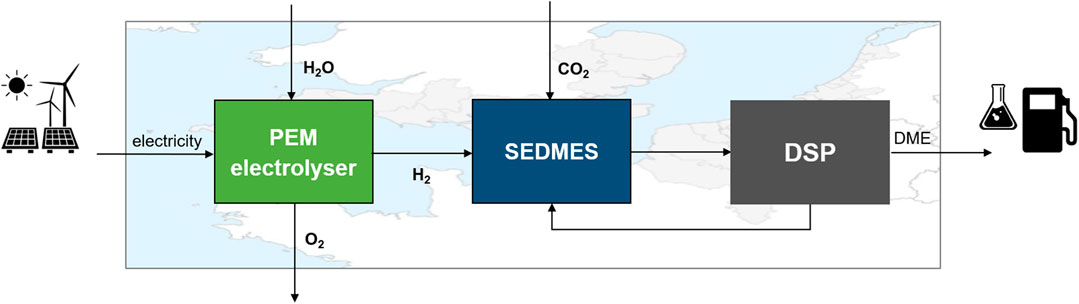
FIGURE 2. Overview of the envisioned PtX process to convert CO2 to dimethyl ether and scope of the techno-economic assessment.
Methodology
Process Description
The studied process of DME production from captured CO2 and H2 formed in the electrolyzer powered by renewable energy is depicted schematically in Figure 2. The process consists of three main parts: i) a proton exchange membrane (PEM) water electrolyzer, ii) the SEDMES unit, and iii) distillation train for DME purification. A wind farm in the two sea areas would be a suitable energy source for the PEM, but this is out of the scope of this assessment. The flow sheet was designed using Aspen Plus software version 10 (Figure 3) (Aspen Plus). The Peng–Robinson equation of state was selected as a property method and validated using data on experimental results from the integrated NIST library (Jonasson et al., 1995). For this techno-economical evaluation, the electrolyzer was considered as a “black box” without studies of its process parameters.
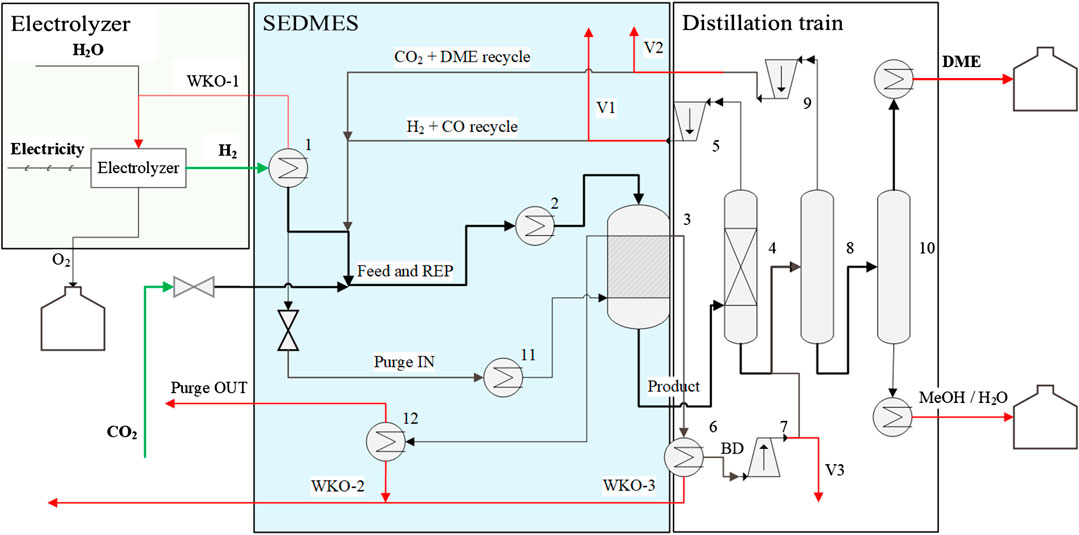
FIGURE 3. Flow sheet of the power-to-X technology sorption-enhanced dimethyl ether synthesis process, including the following main equipment: 1: heat exchanger for H2 dehumidification (cooling); 2: heat exchanger for the feed to reach operating temperature; 3: sorption-enhanced dimethyl ether synthesis columns; 4: flash drum to remove noncondensables; 5: blower for recycling of noncondensables; 6: heat exchanger to dehumidify blowdown stream; 7: compressor for blowdown; 8: distillation column for CO2 separation (DSP-1); 9: compressor for recycling of CO2; 10: distillation column for DME/MeOH + H2O separation (DSP-2); 11: heat exchanger for purge dehumidification (cooling); 12: heat exchanger for purge stream (heating).
Electrolyzer
The electrolyzer supplied with electricity from renewable sources splits water into hydrogen and oxygen streams. While hydrogen is used as a feedstock for further DME production, oxygen acts as a side product, which can be sold after purification. For the hydrogen production from electricity, a PEM electrolyzer is selected. PEM electrolysis is an upcoming technology that is currently entering the market with systems at limited scales (Hydrogenics, 2020; Hydron, 2020; ITM, 2020; Nel Hydrogen, 2020). Due to their advantages in terms of high-pressure operation, high efficiencies and hydrogen purity, it is expected that PEM will become the preferred choice over the currently industrially used alkaline electrolyzers, provided that the costs will be reduced (Shiva Kumar and Himabindu, 2019). The electricity input for the PEM electrolyzer is set to 40 MW because it is minimal commercially available size would allow for plant-scale operation.
Saturated hydrogen comes out of the electrolyzer at 80°C and 30 bara containing 1.5 wt% of water. It is therefore cooled to 28.2°C in order to reduce the water level to nearly 0 wt%. In the calculation, it was assumed that cooling water is available at temperature of 18.2°C, with a temperature difference in the gas/liquid heat exchanger of 10°C (Anantharaman et al., 2018). Operating pressure of the SEDMES unit is selected to be determined by the electrolyzer so that H2 would not need to be additionally pressurized, which contributes to the savings on a compressor installation and operation.
Sorption-Enhanced Dimethyl Ether Synthesis Unit
The feedstock for the DME production is captured CO2 supplied from a pipeline with a pipeline pressure of 80 bara. After CO2 is expanded to 30 bara, it is mixed with H2 in stoichiometric ratio and preheated to the SEDMES operating pressure which is selected to be 250°C. The feed thereafter goes through the SEDMES reactor section (three-column cycle design), which is described in the next subchapter, to be converted into DME. The SEDMES product is cooled and sent to a distillation train to achieve ISO standard purity of DME product. The purge stream is dried and reused in a recycle purge loop, and no gas losses were considered.
Distillation Train
The goal of the SEDMES separation train is to obtain DME with the desired specifications, denoted in Table 1. First, the SEDMES product is cooled and sent to a flash drum to separate the noncondensables such as unconverted H2 and the CO by-product. Depending on the temperature in the separator, some fractions of CO2 and DME are removed as gas fractions. Therefore, sensitivity studies on the optimal temperature in the flash column were performed. The column is operated at the pressure of the SEDMES product stream, which is considered to be 29 bara. Therefore, a compact compressor is needed to recycle the noncondensables back to the SEDMES reactor. Second, a first distillation column (DSP-1) is used for the separation of CO2 and DME, which is expected to be the most energy-intensive process due to similar characteristics of the compounds. Removed CO2 with some fraction of DME is compressed and recycled back to the SEDMES reactor to eliminate losses of the feed or the product. Finally, DME is separated from methanol and water fraction in the second distillation column (DSP-2) until the desired purity is achieved, cooled down, and stored in a tank ready for transportation.
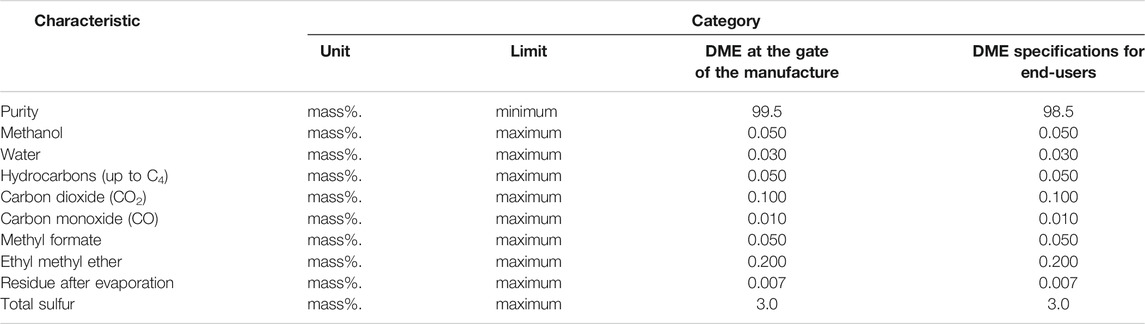
TABLE 1. ISO 16861:2015 standard for DME as a fuel (ISO, 2020).
Sorption-Enhanced Dimethyl Ether Synthesis Modeling
SEDMES is a reactive adsorption process in which steam is removed in situ by a sorbent. As a typical pressure swing adsorption (PSA) system, it is operated cyclic between reactive adsorption and sorbent regeneration. The studied case consists of four consecutive steps presented in Figure 4: adsorption (ADS): the feed is converted into DME on the catalyst, while steam is removed by a zeolite adsorbent; blowdown (BD): countercurrent depressurization of the system in order to desorb water; purge (PURGE): countercurrent flow of dry hydrogen to remove water from the column; repressurization (REP): cocurrent pressurization of the column with the feed stream. In order to maintain a continuous process, one column needs to be in adsorption mode, while another one undergoes regeneration. Therefore, a minimum of two columns is required for an efficient process. However, the duration of the regeneration has a critical effect on the process performance since a longer PURGE step provides drier conditions. In order to design the PURGE step to be longer than ADS, a minimum of three columns are required. Therefore, for the first TEA, a three-column cycle design is considered (Figure 4).

FIGURE 4. Three-column cycle design for the four-step SEDMES process with (ADS) adsorption step, (BD) blowdown step, (PURGE) purge step, (REP) repressurization step.
In order to design a cycle, the boundary conditions have to be set. Since adsorption and repressurization are performed with the same feed, it is important from a technical point of view to maintain a continuous feed flow. Additionally, it is beneficial to keep the REP step as short as possible to maintain production close to continuous. Such important parameters as cycle time and gas hourly space velocities (GHSV) of the feed and purge streams were tuned to achieve high DME yield at high production rate. A previously developed, verified and validated (van Kampen et al., 2020a; van Kampen et al., 2020c) one-dimensional dynamic reactor model (MATLAB) (van Kampen et al., 2020b) is used to study the SEDMES cycle. Several resulting output flows are subsequently studied in the overall process with downstream processing and recycle loops using Aspen Plus software.
The process performance was evaluated using carbon selectivity toward DME, carbon selectivity toward CO2, and the productivity as key parameters. The carbon selectivities were calculated as molar concentration–based selectivity for each of the carbon containing species, y(x):
Productivity P presented in Figure 5 (kg/hr) is defined as the mass of DME m collected during the adsorption step over the duration of this step τ per 1 reactor tube:
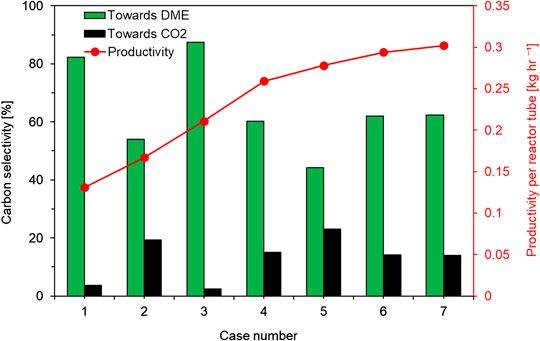
FIGURE 5. Results of the dynamic cycle modeling showing the trade-off between carbon selectivity and productivity for the chosen three columns SEDMES cycle design.
Downstream Processing Modeling
The first step of the DSP is a flash drum, which was optimized with respect to the fraction of CO2 slip to the liquid product (<6%mol.) in order to reduce the condenser duty from the next purification step. The pressure was maintained the same as the outlet stream of the reactor to reduce the electrical duty required for recompression of the recycle stream.
The liquid product of the flash drum is sent to the first distillation column. In this column, the separation of DME and CO2 takes place which is recognized as the most energy-intensive process in the DSP block. The resulting bottom product (DME) contains a level of methanol exceeding the limit of the ISO standard, and therefore, a second distillation column is required to separate the small fraction of methanol. For optimization of the distillation columns, the shortcut method (DSTWU) was used by which, a specified reflux ratio and the minimal number of stages were calculated. These results were then used as the input for simulation of RadFrac columns. The distillate/feed (D/F) ratio was varied in order to meet the following product specifications: 1stcolumn: CO2 < 0.1% wt; 2ndcolumn: methanol <0.05% wt.
The cold gas efficiency is a measure of the feedstock conversion into a product, accounting for the energy preserved in the gas phase. Here, the low heating value (LHV) of the components was used for the calculations. Since the LHV of CO2 is zero, CGE reflects the H2 conversion into DME product:
Economic Evaluation
Economic evaluation of the DME production cost was performed using relevant starting points listed in Table 3: Summary of the assumed key economic parameter indicators and assumptions for the PtX SEDMES process base case. For the CAPEX evaluation of the flash and distillation columns as well as tubular reactors of the SEDMES unit, Aspen APEA vr 10 software was used. The reactor was considered as a shell-and-tube heat exchanger, in order to enable heat management (Guffanti, 2020). Heuristics for design of the flash and distillation columns were used (ISO, 2020). The equipment costs were determined by the column diameters which are calculated for the given liquid (flash) and vapor (distillation column) flows. The height of the distillation columns was determined by the amount of stages and a typical height equivalent to a theoretical plate (HETP) for the packed bed columns. For the flash columns, a liquid residence time of 5 min was assumed. The costs for compressors were evaluated using data on electrical duty based on Aspen Plus simulations and Matche website (Matche, 2020). Installation factors for the compressors were taken from the literature (Humphreys & English, 1993). Finally, a sensitivity study on the prices of the main cost contributors on the DME production was performed. However, after the first cost estimated, the utilities and CAPEX contribution of the downstream processing to the total PtX SEDMES process were found to have a low impact on the DME production cost. Therefore, further optimizations of the DSP unit were left out of the scope of this study.
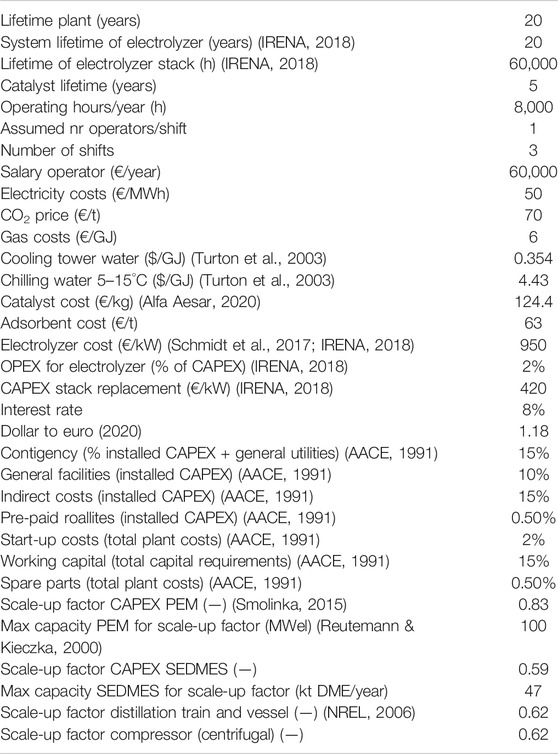
TABLE 3. Summary of the assumed key economic parameter indicators and assumptions for the power-to-X technology SEDMES process base case.
The installation cost for the PEM electrolyzer is assumed to be 950 €/kW (Table 3) (IRENA, 2018), which is on the low side of reported ranges in the literature (Schmidt et al., 2017). The electrolyzer is assumed to use 49 kWh per 1 kg of H2 (efficiency of 68% LHV) (Martín, 2016). The cost of CO2 varies significantly depending on the capture technology and source used (Armstrong et al., 2019; Della Vigna et al., 2019). We assumed a relatively optimistic CO2 price of 70 €/t CO2 based on the estimated average CO2 abatement costs of current technologies for the industry and power sector (Della Vigna et al., 2019), and study a range from 50 to 250 € per ton in our sensitivity analysis. Similarly, energy prices are dependent on many factors in the (future) energy market, and the impact on the PtX SEDMES process for a broad range of energy prices is studied. For the base case, we adopt a value of 50 €/MWh based on the Dutch Climate and Energy Outlook 2019 (Schoots & Hammingh, 2019).
DME production costs were calculated using following equation:
Annualized CAPEX is calculated using following equation, where n is the lifetime plant and i is the interest rate:
When performing the sensitivity analysis, one of the studied parameters is the total annual production of DME using the PtX SEDMES process. The annual capacity influences the annualized CAPEX per ton DME, coming from the economy of the scale effect: for higher throughput, the capital expenses become smaller per kilogram product.
The estimation of the CAPEX for the SEDMES unit, the PEM electrolyzer, and the distillation columns depending on the annual production is done as follows, where
It must be noted that when the new capacity
Results and Discussion
Sorption-Enhanced Dimethyl Ether Synthesis Modeling
For the first PtX SEDMES production cost estimate, a simple tuning of the SEDMES cycle design parameters was performed, varying the cycle times and flows (Table 4). The results in terms of productivity and carbon selectivity toward DME of this dynamic cycle modeling are given in Figure 5. As is typical for sorption-enhanced processes, there is a trade-off between carbon selectivity and productivity observed for the SEDMES process. The potential benefit of high carbon selectivity toward DME (C-DME) > 80% and low carbon selectivity toward CO2 (C-CO2) < 5% includes reduced duties for the distillation train, lower volume of recycles, and thus potentially higher resource efficiency. As case #3 exhibits the highest C-DME (84.7%) among the studied cases and a reasonably high productivity (higher than the case #1), this case was selected for further simulations and techno-economical evaluations, which are discussed below.
The conditions and compositions of the inlet and outlet streams for the selected case are listed in Table 5. The yield per pass for SEDMES under these conditions is 65%, which is 57% points more than the conversion without sorption enhancement (maximum 8% for conventional DME synthesis). The BD stream for this case is considerably large (10 vs 7.5 kg/m3reactor during adsorption mode) and contains valuable components (8.2 mol% DME product and 79.1 mol% unconverted feed). It is thus essential to further process and recycle the BD product. There are two options for this: 1) recycling the BD product directly to the feed stream or 2) sending the BD product to the distillation train. Since the BD stream is one-third of the feed (30 kg/m3reactor), consisting of 8.2 mol% of DME, it will keep on changing the feed composition due to accumulation of DME if option 1 is adopted. We anticipate that this will increase C-DME, while decreasing the conversion per pass. Sending the BD product to the distillation train allows collecting additional DME as a product and, therefore, removing undesired product recycling. Therefore, the BD stream will be sent to the DSP as well (option 2).
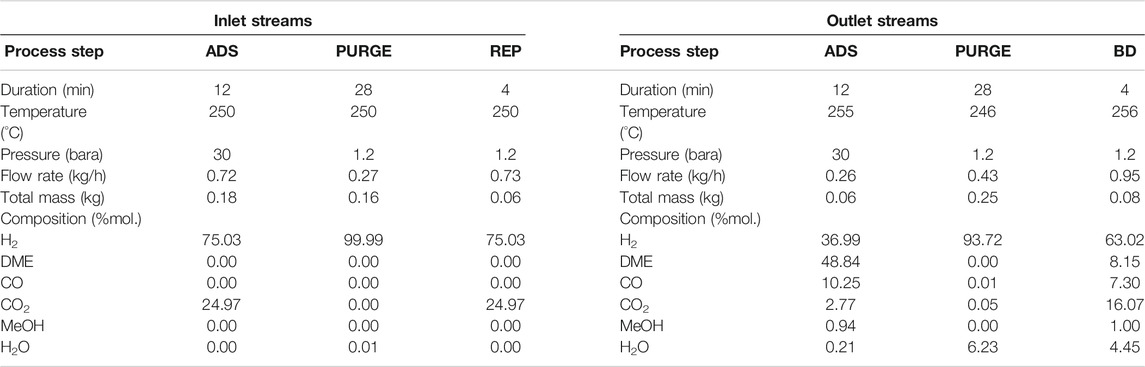
TABLE 5. Conditions and compositions of the inlet and outlet streams simulated using the dynamic cycle model for a single 0.008 m (Olah et al., 2009) reactor tube.
The data on the inlet and outlet streams generated by means of the dynamic cycle model (MATLAB) were used as an input for the flow sheet simulations in the Aspen Plus environment to provide the new feed composition after purification and recycling. This new feed composition was used in the cycle model to simulate the process after the iteration, and new mass flows were generated that are listed in Table 6. It can be observed that the feed composition after the chosen recycling routes does not noticeably deviate from the original feed composition, and it introduces 1.43 mol% DME. Therefore, for the first DME production, cost evaluation for one iteration of recycling seems to be sufficient. The yield per pass with the recycle increased to 72.4%. After performing all the recycling processes, it was calculated that 5966 reactor tubes of 0.008 m3 per reactor column are required to process the fixed H2 feed.
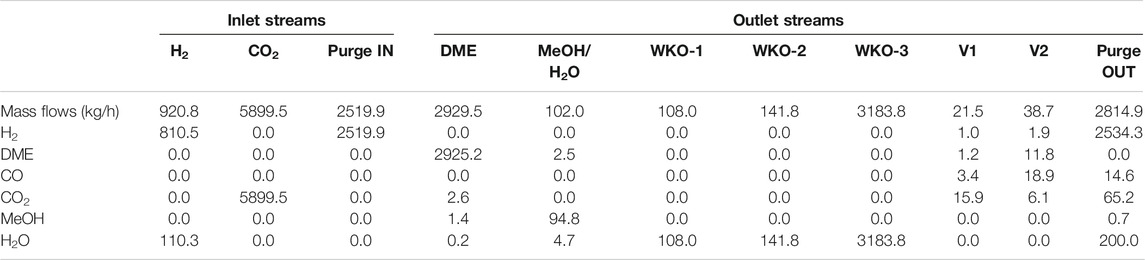
TABLE 6. Mass flows and composition of the input and output streams for the power-to-X technology SEDMES process simulated using ASPEN.
Economic Evaluation
The first techno-economical evaluation of PtX DME production from CO2 and green H2 by means of the SEDMES technology was performed, and the main cost contributors are listed in Table 7. The total investment cost for envisioned plant is 48 M€. The contribution of the operational costs (OPEX) exceeds the capital cost (CAPEX) contribution 2.75 times. The OPEX mainly comprises electricity (72%) and CO2 cost (14%). Since the electricity usage is mainly related to H2 production (99.2%) in the PEM electrolyzer, it is evident that the cost of H2 is the cost-driving factor for the DME production in the studied scenario with a hydrogen production cost of ∼€3.8 per kg of H2. Therefore, it is important to design a process with maximum H2 conversion into DME. This is also supported by the impact of electrolyzer cost on the total installation cost, where hydrogen production makes up 78% of the installation cost contribution.
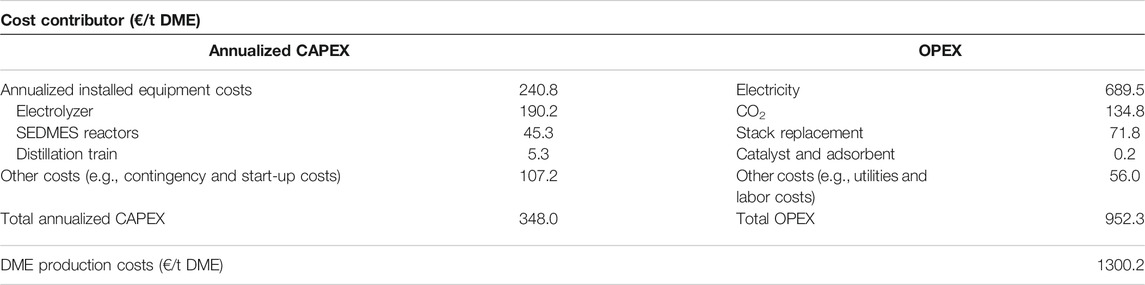
TABLE 7. Breakdown of the costs contributors of the power-to-X technology DME production using SEDMES in euro per ton of DME.
In order to reach this high H2 conversion, all hydrogen losses, mostly in the vent streams, should be minimized. This can be achieved by reducing the size of recycle streams which is strongly related to the DME yield per pass. As discussed earlier, the single-pass DME yield for the SEDMES process under these conditions is over 72%, while for the conventional indirect DME production process, the yield would only be 19% at more severe conditions (100 bara standard operation) (Martin Mendez, 2016). The high single-pass conversion and high selectivity to DME make SEDMES technology more efficient in converting the valuable H2 and reducing its loss, which is crucial due to the major impact of the hydrogen production on the total cost. Moreover, during the SEDMES process, high amounts of steam are produced, which can be purified and reused to produce H2 in the PEM electrolyzer.
The cold gas efficiency (CGE) reflects the conversion of H2 to DME based on their lower heating value (LHV). For the overall SEDMES process (after purification), the CGE is already 90%, while the theoretical maximum for the conversion of CO2 and H2 to DME is 92%. The losses consist of MeOH by-product formation (1.98%) and losses in recycle vents (up to 0.02%). Hence, the CGE could be optimized further by minimizing by-product formation and/or recycling. Noteworthy, the overall efficiency of 90% exceeds the theoretical maximum CGE of 88% for the conversion of CO2 and H2 to methanol, indicating that PtX SEDMES is inherently more efficient.
The results indicate that the installation cost for the SEDMES unit is 19% of the total installation cost (6.3% per reactor column); thus, further studies on the effect of the number of SEDMES reactor columns on the production cost would be of interest. More SEDMES reactor columns would allow different cycle designs, including pressure equalization, to improve the carbon selectivity toward DME, DME yield, and/or production rate, whereas two columns would potentially allow to reduce installation costs.
For the studied case, a DME production rate of 23 kt/year is achieved, which corresponds to a production cost of 1.30 €/kgDME (Figure 6). Currently, the DME market price is around €0.56 per kg of DME (Hepburn et al., 2019), and the production cost of PtX DME thus exceeds the market price of fossil-based DME. However, the costs lie well below those found as the average cost of producing DME from CO2 according to Hepburn et al. (2019) (2.74 $/kg). Furthermore, the reported production cost is in the same range as evaluated by Martin for conventional DME synthesis combined with water electrolysis (1.43 €/kg), although his assessment has the benefit of scale (197 versus 23 kt/year) and includes revenues of O2 sales (Martín, 2016). This similar cost could be expected, whereas it is shown that the hydrogen production is the major determining factor. However, besides the technical benefits of the SEDMES technology, the results for relatively small-scale DME production reported here also indicate that the SEDMES technology is not more expensive than the conventional technology and even has the potential of reducing the cost over the conventional route.
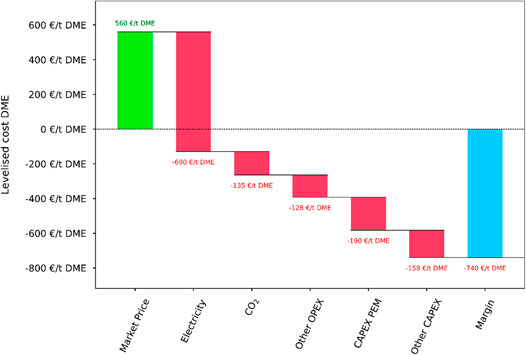
FIGURE 6. Waterfall chart showing the main cost contributions to the production cost for a ton of DME using the power-to-X technology SEDMES process.
The results of the sensitivity analysis on the cost contributors to PtX SEDMES process are depicted in Figure 7. The central value of around 1,300 €/tDME represents our base case. The DME production costs are notably dominated by the PEM electrolyzer at a given efficiency, and the electricity cost has the largest impact on the fuel production costs. Therefore, improving the electrolyzer efficiency is one possibility to achieve a lower DME production cost. By increasing the efficiency to 75% the cost drops to below 1,200 €/tDME. Another promising development to cut CAPEX costs of the electrolyzer is replacement of the PEM electrolyzer with its less expensive anion exchange membrane (AEM) alternative (Vincent and Bessarabov, 2018). However, this should not come with a high loss in efficiency. In the E2C project, AEM electrolyzers with non-noble metal catalysts are already being developed to reduce the electrolyzer costs (Loh et al., 2020; Ullah et al., 2020).
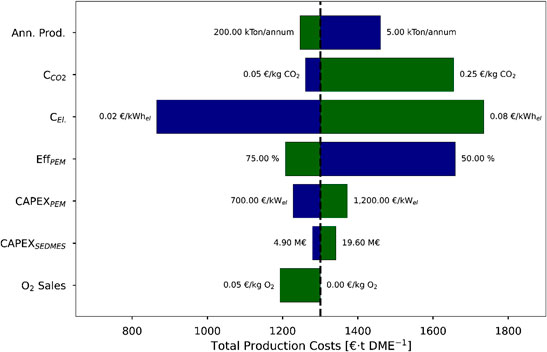
FIGURE 7. Sensitivity analysis on the main cost contributing factors to the power-to-X technology SEDMES process. H2 is produced by PEM electrolysis and reacts with captured CO2 to produce DME. Ann Prod, annual production scale; CCO2, carbon dioxide cost; CEl, electricity cost; EffPEM, efficiency of the PEM electrolyzer; CAPEXPEM, capital costs electrolyzer; CAPEXSEDMES, capital costs SEDMES unit. Blue and green bar indicate lower and higher values compared to the base case, respectively.
The sensitivity analysis indicates that the reduction in the electricity price has the highest potential to bring down the production cost. Regions with high wind and solar availability, such as coastal areas, will probably have high supplies of renewable electricity in the future, leading to significantly reduced price and, even to grid balancing problems. If the PtX SEDMES process is compatible with the intermittency of energy, this provides the process with the opportunity to use the power excess for the production of DME. Therefore, the compatibility of the PtX SEDMES process with intermittent electricity is an interesting research direction, which will be investigated in the E2C project.
Like other processes, the costs of PtX technologies are known to be reduced by economies of scale (Schmidt et al., 2017). Therefore, production scale of DME with the PtX SEDMES process was also investigated in the sensitivity analysis. As can be discerned from Figure 7, the increase from 23 to 200 kt DME/year (production scale from Martín (2016)) brings the DME cost below 1,300 €/t DME, outperforming the conventional DME synthesis route even further (Martín, 2016). Additionally, the SEDMES PtX technology allows DME production at very small scale envisioned for the decentralized PtX technology. An annual production of 5 kt/year only increases CAPEX by ca. 150 €/t DME. This is an additional advantage of a sorption-enhanced technology over the conventional DME production, which is unattractive for small-scale production (Detz et al., 2018).
The costs of the PtX SEDMES process are also sensitive to the cost of CO2. The CO2 price constitutes 14% of total OPEX and 10% of the total production cost. The break-even cost for CO2, which is required to make the process economically viable, is −0.31 €/kgCO2, meaning that incentives for CO2 utilization and/or costs for emission should amount to this value. Although it is foreseen that policy changes in CO2 emission will have a high impact on the price formation, 310 €/tCO2 is significantly more than any suggested carbon dioxide tax so far (Hepburn et al., 2019).
The impact of the CAPEX of the SEDMES unit was also investigated. As can be seen from Figure 7, reducing the capital costs of this installation has a limited effect on the DME production price. Another option to make the PtX SEDMES process more attractive is to sell the produced oxygen (credit 0.05 €/kg) from the PEM electrolyzer as a product. As can be seen from Figure 7, this would lower the DME production price with around 10 cents.
Conclusion
In this article, the techno-economic assessment of the PtX SEDMES process, producing fuel-grade DME from carbon dioxide and green H2, is presented. By means of a previously developed dynamic cycle model for the SEDMES reactors, a DME yield per pass of 72.4% and a carbon selectivity toward DME of 84.7% were achieved for the studied process design after optimization of the recycles streams. The production cost for DME was found to be ∼€1.3 per kg for a relatively small-scale production plant of 23 kt/year. Although the production cost is higher than the current market price for fossil-based DME, the results are more promising than other studies on DME production from CO2 by conventional DME synthesis processes. The environmental impact of the proposed PtX SEDMES process should be analyzed in the follow-up work.
The main cost contributing factors within the PtX process are related to the H2 production by the PEM electrolyzer. The energy costs have the largest impact on the production price followed by the CAPEX of the PEM electrolyzer. The sensitivity analysis indicates that also the CO2 price has an impact on the production cost. A break-even cost, which is required to make the process economically viable, for this feedstock is −310 €/tCO2. Since the main cost drivers of the PtX SEDMES process are related to the PEM electrolyzer, research directions should be geared toward reducing electrolyzer costs by enhancing efficiencies and the use of less expensive materials. Moreover, SEDMES is demonstrated to be a powerful technology for efficient conversion of green H2 into DME, which is an essential benefit due to the determining role of the hydrogen cost in the total production cost.
Data Availability Statement
The raw data supporting the conclusions of this article will be made available by the authors, without undue reservation.
Conflict of Interest
The authors declare that the research was conducted in the absence of any commercial or financial relationships that could be construed as a potential conflict of interest.
Author Contributions
JK developed the computational (MATLAB) model and GS performed the modelling. GS and MS developed the flowsheet in Aspen and gathered the data with input from CM and SS. GS performed the calculations, while CM performed the sensitivity study. All authors provided critical feedback and helped shape the research and analysis. GS and SS wrote the manuscript in consultation with JK and JB. JB conceived the original idea for the study and supervised the project together with SS.
Funding
This project has received funding from the Interreg 2 Seas programme 2014–2020 co-funded by the European Regional Development Fund under subsidy contract no 2S03–019 E2C. Additional funding has been received by Smartport, Provincie Zuid-Holland, Provincie Noord-Holland, and the Dutch Ministry for Economic Affairs and Climate Policy.
Acknowledgments
We acknowledge Florian Estreguil from CPE Lyon and TNO, Katy Armstrong and Peter Sanderson from the university of Exeter and Jan Wilco Dijkstra and Yvonne van Delft from TNO, for fruitful discussions that helped improving the quality of this manuscript.
References
AACE (1991). Conducting technical and economic evaluations: as applied for the process and utility industries. Morgantown, WV: AACE International Recommended Practice
Alfa Aesar (2020). Available at: https://www.alfa.com/en/catalog/045776/
Anantharaman, R., Bolland, O., Booth, N., Van Dorst, E., Sanchez Fernandez, E., Franco, F., et al. (2018). D2.4.3. European best practice guidelines for assessment of CO2 capture technologies (Version 8/3/2011). Available at: https://doi.org/10.5281/zenodo.1312801
Armstrong, K., Sanderson, P., and Styring, P. (2019). “Promising CO2 point sources for utilisation,” in Carbon dioxide utilization fundamentals. M. N. Styring (Editor) (De Gruyter), 47–62. doi:10.1515/9783110563191-004
Artz, J., Müller, T. E., Thenert, K., Kleinekorte, J., Meys, R., Sternberg, A., et al. (2018). Sustainable conversion of carbon dioxide: an integrated review of catalysis and life cycle assessment. Chem. Rev. 118 (2), 434–504. doi:10.1021/acs.chemrev.7b00435.
Aspen Plus (2020). Available at: https://www.aspentech.com/en/products/engineering/aspen-plus
Azizi, Z., Rezaeimanesh, M., Tohidian, T., and Rahimpour, M. R. (2014). Dimethyl ether: a review of technologies and production challenges. Chem. Eng. Process: Process Intensification. 82, 150–172. doi:10.1016/j.cep.2014.06.007.
Bongartz, D., Doré, L., Eichler, K., Grube, T., Heuser, B., Hombach, L. E., et al. (2018). Comparison of light-duty transportation fuels produced from renewable hydrogen and green carbon dioxide. Appl. Energy. 231, 757–767. doi:10.1016/j.apenergy.2018.09.106
Boon, J., van Kampen, J., Hoogendoorn, R., Tanase, S., van Berkel, F. P. F., and van Sint Annaland, M. (2019). Reversible deactivation of γ-alumina by steam in the gas-phase dehydration of methanol to dimethyl ether. Catal. Commun. 119, 22–27. doi:10.1016/j.catcom.2018.10.008
Centi, G., and Perathoner, S. (2009). Opportunities and prospects in the chemical recycling of carbon dioxide to fuels. Catal. Today. 148 (3–4), 191–205. doi:10.1016/j.cattod.2009.07.075
Della Vigna, M., Stavrinou, Z., Bhandari, N., Mehta, N., and Singer, B. (2019). Carbonomics: the future of energy in the age of climate change.
Detz, R. J., Reek, J. N. H., and van der Zwaan, B. C. C. (2018). The future of solar fuels: when could they become competitive? Energy Environ. Sci. 11 (7), 1653–1669. doi:10.1039/c8ee00111a
E2C (2020). Electrons to high-value chemical products - E2C. Available at: https://www.voltachem.com/e2c
Guffanti, S., Giorgio Visconti, C., van Kampen, J., Boon, J., and Groppi, G. (2020). Reactor modelling and design for sorption enhanced dimethyl ether synthesis. Chem. Eng. J. 2020, 126573. doi:10.1016/j.cej.2020.126573
Hepburn, C., Adlen, E., Beddington, J., Carter, E. A., Fuss, S., Mac Dowell, N., et al. (2019). The technological and economic prospects for CO2 utilization and removal. Nature. 575 (7781), 87–97. doi:10.1038/s41586-019-1681-6
Humphreys, K., and English, L. M. (1993). Project and cost engineers’ handbook, 3rd Edition. New York: CRC Press
Hydrogenics (2020). Available at: http://www.hydrogenics.com/wp-content/uploads/Renewable-Hydrogen-Brochure.pdf
Hydron (2020). Available at: https://hydron-energy.com/products/
IEA (2019). Tracking Industry 2019. Available at: https://www.iea.org/reports/tracking-industry-2019.
Iliuta, I., Iliuta, M. C., and Larachi, F. (2011). Sorption-enhanced dimethyl ether synthesis-multiscale reactor modeling. Chem. Eng. Sci. 66 (10), 2241–2251. doi:10.1016/j.ces.2011.02.047
ISO (2020). ISO standard. Available at: https://www.iso.org/standard/57835.html
ITM (2020). Available at: https://www.itm-power.com/products
Jonasson, A., Persson, O., and Fredenslund, A. (1995). High pressure solubility of carbon dioxide and carbon monoxide in dimethyl ether. J. Chem. Eng. Data. 40 (1), 296–300. doi:10.1021/je00017a066
Kätelhön, A., Meys, R., Deutz, S., Suh, S., and Bardow, A. (2019). Climate change mitigation potential of carbon capture and utilization in the chemical industry. Proc. Natl. Acad. Sci. U.S.A. 116 (23), 11187–11194. doi:10.1073/pnas.1821029116
Liuzzi, D., Peinado, C., Peña, M. A., van Kampen, J., Boon, J., and Rojas, S. (2020). Increasing dimethyl ether production from biomass-derived syngas via sorption enhanced dimethyl ether synthesis. Sustain. Energy Fuels. 4 (11), 5674–5681. doi:10.1039/d0se01172j
Loh, A., Li, X., Taiwo, O. O., Tariq, F., Brandon, N. P., Wang, P., et al. (2020). Development of Ni–Fe based ternary metal hydroxides as highly efficient oxygen evolution catalysts in AEM water electrolysis for hydrogen production. Int. J. Hydrogen Energy. 45(46), 24232–24247. doi:10.1016/j.ijhydene.2020.06.253
Martín, M. (2016). Optimal year-round production of DME from CO2 and water using renewable energy. J. CO2 Util. 13, 105–113. doi:10.1016/j.jcou.2016.01.003
Martin Mendez, L. (2016). Process design and control of dimethyl ether synthesis. Madrid: Polytechnic University of Madrid
Matche (2020). Available at: http://www.matche.com/equipcost/Default.html
Matzen, M., and Demirel, Y. (2016). Methanol and dimethyl ether from renewable hydrogen and carbon dioxide: alternative fuels production and life-cycle assessment. J. Clean. Prod. 139, 1068–1077. doi:10.1016/j.jclepro.2016.08.163
Müller, M., and Hübsch, U. (2000). “Dimethyl ether,” in Ullmann’s encyclopedia of industrial chemistry. Weinheim (Germany): Wiley-VCH Verlag GmbH & Co. KGaA. doi:10.1002/14356007.a08_541
Nel Hydrogen (2020). Available at: https://nelhydrogen.com/water-electrolysers-hydrogen-generators/
NREL (2006). Equipment design and cost estimation for small modular biomass systems, synthesis gas cleanup, and oxygen separation equipment; task 2: gas cleanup design and cost estimates—black liquor gasification. Golden, CO: National Renewable Energy Laboratory. doi:10.2172/882504
Olah, G. A., Goeppert, A., and Prakash, G. K. S. (2009). Chemical recycling of carbon dioxide to methanol and dimethyl ether: from greenhouse gas to renewable, environmentally carbon neutral fuels and synthetic hydrocarbons. J. Org. Chem. 74 (2), 487–498. doi:10.1021/jo801260f
Ordomsky, V. V., Dros, A.-B., Schwiedernoch, R., and Khodakov, A. Y. (2017). “Challenges and role of catalysis in CO2 conversion to chemicals and fuels,” in Nanotechnology in catalysis. Weinheim (Germany): Wiley-VCH Verlag GmbH & Co. KGaA. 803–850. doi:10.1002/9783527699827.ch30
Rego de Vasconcelos, B., and Lavoie, J.-M. (2019). Recent advances in power-to-X technology for the production of fuels and chemicals. Front. Chem. 7. doi:10.3389/fchem.2019.00392
Reutemann, W., and Kieczka, H. (2000). “Formic acid,” in Ullmann’s encyclopedia of industrial chemistry. Weinheim (Germany): Wiley-VCH Verlag GmbH & Co. KGaA. doi:10.1002/14356007.a12_013
Sánchez, O. G., Birdja, Y. Y., Bulut, M., Vaes, J., Breugelmans, T., and Pant, D. (2019). Recent advances in industrial CO2 electroreduction. Curr. Opin. Green Sustain. Chem. 16, 47–56. doi:10.1016/j.cogsc.2019.01.005
Schmidt, O., Gambhir, A., Staffell, I., Hawkes, A., Nelson, J., and Few, S. (2017). Future cost and performance of water electrolysis: an expert elicitation study. Int. J. Hydrogen Energy. 42 (52), 30470–30492. doi:10.1016/j.ijhydene.2017.10.045
Semelsberger, T. A., Borup, R. L., and Greene, H. L. (2006). Dimethyl ether (DME) as an alternative fuel. J. Power Sources. 156 (2), 497–511. doi:10.1016/j.jpowsour.2005.05.082
Shiva Kumar, S., and Himabindu, V. (2019). Hydrogen production by PEM water electrolysis - a review. Mater. Sci. Energy Technol. 2 (3), 442–454. doi:10.1016/j.mset.2019.03.002
Smolinka, T. (2015). Cost break down and analysis of PEM electrolysis systems for different industrial and power to gas applications.
SPIRE (2020). SPIRE 2050 vision towards the next generation of European process industries. Available at: https://www.spire2030.eu/sites/default/files/users/user85/Vision_Document_V5_Pages_Online_0.pdf
Turton, R., Bailie, R. C., Whiting, W. B., and Shaeiwitz, J. A. (2003). Analysis, synthesis, and design of chemical processes. 7th Edition. Upper Saddle River: Prentice Hall
Ullah, H., Loh, A., Trudgeon, D. P., and Li, X. (2020). Density functional theory study of NiFeCo trinary oxy-hydroxides for an efficient and stable oxygen evolution reaction catalyst. ACS Omega. 2020, 0c02679. doi:10.1021/acsomega.0c02679
UNFPA (2020). Transforming our world: the 2030 Agenda for sustainable development. Available at: https://sustainabledevelopment.un.org/post2015/transformingourworld
van Kampen, J., Boon, J., van Berkel, F., Vente, J., and van Sint Annaland, M. (2019). Steam separation enhanced reactions: review and outlook. Chem. Eng. J. 374, 1286–1303. doi:10.1016/j.cej.2019.06.031
van Kampen, J., Boon, J., Vente, J., and van Sint Annaland, M. (2020a). Sorption enhanced dimethyl ether synthesis for high efficiency carbon conversion: modelling and cycle design. J. CO2 Util. 37, 295–308. doi:10.1016/j.jcou.2019.12.021
van Kampen, J., Boon, J., Vente, J., and van Sint Annaland, M. (2020b). Sorption enhanced dimethyl ether synthesis under industrially relevant conditions: experimental validation of pressure swing regeneration. Energy Environ. Sci.
van Kampen, J., Booneveld, S., Boon, J., Vente, J., and van Sint Annaland, M. (2020c). Experimental validation of pressure swing regeneration for faster cycling in sorption enhanced dimethyl ether synthesis. Chem. Commun. doi:10.1039/d0cc06093c
Keywords: sorption-enhanced reaction, dimethyl ether, electrolysis, power-to-X, electrification, industry, techno-economic analysis
Citation: Skorikova G, Saric M, Sluijter SN, van Kampen J, Sánchez-Martínez C and Boon J (2020) The Techno-Economic Benefit of Sorption Enhancement: Evaluation of Sorption-Enhanced Dimethyl Ether Synthesis for CO2 Utilization. Front. Chem. Eng. 2:594884. doi: 10.3389/fceng.2020.594884
Received: 14 August 2020; Accepted: 20 October 2020;
Published: 22 December 2020.
Edited by:
Simon Roussanaly, SINTEF Energy Research, NorwayReviewed by:
Juan Gabriel Segovia Hernandez, University of Guanajuato, MexicoQingchun Yang, Hefei University of Technology, China
Copyright © 2020 Skorikova, Saric, Sluijter, van Kampen, Sánchez-Martínez and Boon. This is an open-access article distributed under the terms of the Creative Commons Attribution License (CC BY). The use, distribution or reproduction in other forums is permitted, provided the original author(s) and the copyright owner(s) are credited and that the original publication in this journal is cited, in accordance with accepted academic practice. No use, distribution or reproduction is permitted which does not comply with these terms.
*Correspondence: Jurriaan Boon, anVycmlhYW4uYm9vbkB0bm8ubmw=