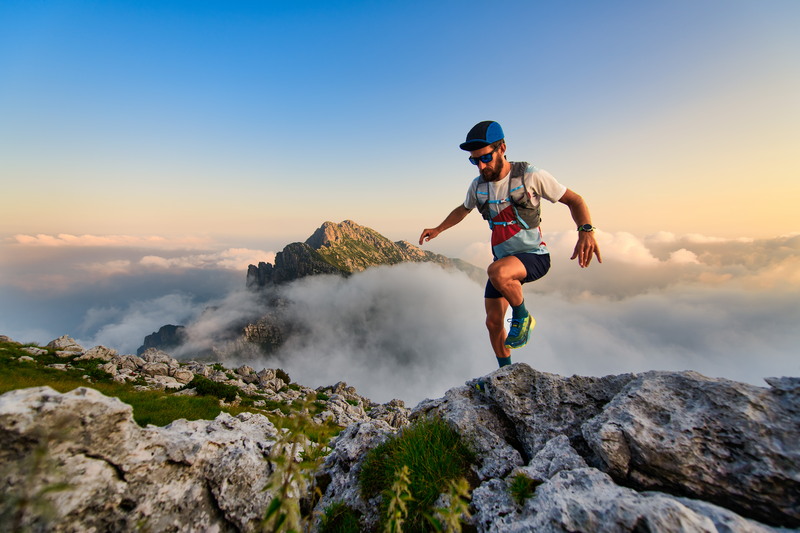
95% of researchers rate our articles as excellent or good
Learn more about the work of our research integrity team to safeguard the quality of each article we publish.
Find out more
ORIGINAL RESEARCH article
Front. Built Environ. , 27 May 2024
Sec. Construction Materials
Volume 10 - 2024 | https://doi.org/10.3389/fbuil.2024.1381169
This article is part of the Research Topic Sustainable Building Materials from Recycled Cement/Concrete and Recycled Industrial Wastes View all 5 articles
Introduction: Improper disposal of mollusk shells has led to environmental issues worldwide. Given their primary composition of calcium carbonate, these shells have been studied for their potential use as aggregate in cement composites, offering an environmentally appropriate destination for the waste and reducing virgin raw material use. However, there is a lack of research on the application of Sururu (Mytella falcata) shells, a species of mollusk commonly fished in countries such as Brazil. This study investigated the effects of Sururu shells waste from a Brazilian region on the mechanical and physical properties of mortar when partially replacing natural fine aggregate.
Methods: Three mortar mixtures were produced, replacing 10, 20, and 40% of natural sand with Sururu shell aggregate (SSA) by mass. The specimens underwent consistency and density tests in their fresh state, and compressive strength, dynamic modulus of elasticity, and capillary absorption tests in their hardened state.
Results: The results showed that workability decreased with the increase in SSA replacement, resulting in a reduction of 31.5% in consistency at 40% SSA replacement level. Compressive strength also decreased with SSA incorporation, but all samples continued to gain strength after 28 days, with 10% SSA samples showing only a 2.7% reduction compared to the control specimens. The dynamic modulus of elasticity was minimally impacted at 10% SSA, but significantly reduced at higher levels. Notably, SSA reduced capillary absorption in samples after 24, 48, and 72 h, indicating potential benefits in moisture management.
Discussion: It was concluded that replacing 10% of natural sand with SSA was the most suitable option, considering the investigated mechanical properties of the mortar produced with SSA. However, further research is recommended to examine the durability and environmental impact of this solution.
Every year, the global mariculture industry, which farms various mollusks like mussels, oysters, scallops, and crepidula, produces massive quantities of shell waste, with approximately 80% of harvested products ending up as discarded shells (Jović et al., 2019). These shells are frequently left haphazardly near farming areas, leading to severe environmental issues such as soil pollution, the destruction of mangrove forests, and disruptions to aquatic ecosystems caused by sediment buildup (Petrielli, 2008; Ruslan et al., 2022). Additionally, the unregulated dumping of these shells poses public health risks due to unsanitary conditions, with the waste often found in public spaces such as streets, empty plots, and coastal zones (Peceño et al., 2021; Soltanzadeh et al., 2021). The decomposition of organic remnants within these shells can also release unpleasant smells from gases like hydrogen sulfide, ammonia, and various amines, further exacerbating the problem (Tayeh et al., 2019; Hart, 2020; Tayeh et al., 2020; Hasnaoui et al., 2021; Kim et al., 2022).
As of 2020, mollusk production worldwide was roughly estimated at 17.7 million tons, with Brazil being a significant contributor within South America (Marques et al., 2020; FAO, 2022). Within Brazil, the state of Santa Catarina alone contributes to 90% of the country’s mollusk yield (Marques et al., 2020). In specific communities, inadequate waste management has led to considerable environmental degradation. In Pernambuco, a state in the northeastern part of Brazil, there are numerous communities that depend on fishing for bivalve mollusks. However, these communities often lack the infrastructure required for the proper disposal of shells in an environmentally friendly manner, leading to soil pollution and damage to local mangroves. A notable example of this situation can be observed in Ilha de Deus (Figure 1), a small fishing community in Recife, the state capital. Home to around 2,000 residents, this community produces an estimated 408 tons of shell waste annually (Cardoso et al., 2023). One of the most commonly harvested mollusk species in this area is the Sururu (Mytella falcata), which typically measures about 50 mm long and 22 mm wide. The shells exhibit a distinctive color pattern, with a yellowish-brown hue on the anteroventral side and a greenish tint on the dorsal side.
Figure 1. Aerial view of Ilha de Deus community in eastern Brazil, depicting the uncontrolled accumulation of Sururu shell waste causing environmental concerns.
Mollusk shells typically contain at least one organic layer and two calcareous (calcium-rich) layers. The outermost layer is rich in proteins bound to chitin. It may include up to four crystalline layers of calcium carbonate, which can be purely aragonite or a mix of aragonite and calcite (Rimar, 2013). Table 1 presents the chemical composition and the loss on ignition (LOI) for shells from various mollusks, as observed in different studies. The quantity of calcium oxide present in mollusk shells indicates a similar chemical composition compared to natural aggregates, such as limestone. There is a significant variation in the reported CaO content across different studies, ranging from 48.0% to 95.82%. This difference is related to the origin and species of the mollusk (Hamada et al., 2023). The LOI, which ranges from 23.2% to 51.0%, is attributed to the presence of calcite, which decomposes into calcium oxide and carbon dioxide at high temperatures (Mo et al., 2018).
Recent research has increasingly focused on the potential of using recycled mollusk shells in concrete mixtures, either as a substitute for aggregates or as an additive to Portland cement (Oyejobi et al., 2019; Rodríguez-Galán et al., 2019; Edalat-Behbahani et al., 2021; El Biriane and Barbachi, 2021; Her et al., 2021; Leone et al., 2023). This recycling approach offers two significant advantages (Hamada et al., 2023): firstly, it mitigates environmental pollution by reducing the volume of waste that accumulates in open spaces and landfills. Secondly, its use as a replacement for aggregates and/or cement mitigates the environmental impact of cement production, characterized by substantial CO₂ emissions. Additionally, it reduces the procurement of natural concrete materials, thereby conserving global resources.
The use of recycled shells as aggregate and supplementary cementitious materials can lead to different effects on the mechanical properties of the cementitious composites produced. Table 2 summarizes the results from studies on the use of different recycled mollusk shells in concrete and mortar production, focusing on their effects on workability and compressive strength. This table highlights a diverse range of outcomes, emphasizing the inherent complexity and variability in this research field. Kuo et al. (2013) demonstrated the potential for improving mechanical properties of concrete by incorporating oyster shells. A significant enhancement in both compressive and tensile strength was observed when up to 50% of sand was replaced with mussel shells, with a significant increase of 24.12% in compressive strength at a 40% substitution rate (Boudjellal et al., 2020). Similarly, Ez-Zaki et al. (2016) identified an optimal replacement level of 40% of fine aggregate with mussel shell powder, which only slightly reduced compressive strength.
Table 2. Summary of previous studies investigating the application of mollusk shells in concrete and mortar.
On the contrary, different outcomes have been observed in other studies when using seashells as a construction material. Olivia et al. (2015) and Sangeetha et al. (2022) observed that the partial substitution of cement with seashells in concrete production led to a decrease in compressive strength. However, in both studies, the samples incorporating shells exhibited acceptable strengths, exceeding 25 MPa after 28 days of curing. A recent literature review by Hamada et al. (2023) highlighted a discrepancy in mechanical strengths across studies utilizing seashells as filler material. Nonetheless, high levels of cement replacement with seashells reduce the concrete’s compressive, tensile, and flexural strengths. This reduction in strength has been attributed to the weak bond at the interface between the recycled shells and the cement paste, characterized by visible cracking and increased porosity. Moreover, research by Yoon et al. (2003) and Eo and Yi (2015) highlighted that the fineness of the recycled shell particles plays a critical role in the mechanical properties of concrete, with coarser shell aggregates resulting in less impact on the compressive strength compared to finer particles.
Incorporating recycled mollusk shells into concrete not only influences the mechanical properties but also affects other crucial aspects like workability and the modulus of elasticity of concrete. There is a consensus among most studies that replacing fine aggregates with recycled seashells tends to reduce the workability of concrete (Mo et al., 2018; Bamigboye et al., 2021). This reduction is often attributed to the irregular shapes of seashell particles, which can increase the interparticle friction among seashell aggregates and their higher specific surface area compared to traditional aggregates, leading to elevated water demand and absorption. Studies have also reported a decrease in the Modulus of Elasticity (MoE) in concrete mixtures incorporating seashells. Olivia et al. (2015) and Tayeh et al. (2019) found that the MoE of concrete with seashells is lower than that of cement concrete without seashells. However, they noted that the rate of increase in the MoE of seashell concrete over curing time surpasses that of cement concrete. Similarly, Yang et al. (2010) reported a 10% reduction in the modulus of elasticity in concrete samples where 20% of the aggregate was replaced with oyster shell, while Martínez-García et al. (2017) identified a 25% decrease when 25% of the aggregate was substituted with mussel shell waste.
It is noteworthy that none of the mentioned studies or literature reviews on the subject (Eziefula et al., 2018; Mo et al., 2018; Tayeh et al., 2019; Bamigboye et al., 2021; Hamada et al., 2023) have investigated the use of sururu shells, a mollusk commonly fished in some Latin American and Asian countries. Furthermore, it is evident that different types of seashells can produce different mechanical properties in cementitious systems. This study aimed to evaluate the impact of sururu shell aggregate (SSA) on the mechanical properties of mortar produced by partially substituting natural sand, both in its fresh and hardened states. Using sururu shell waste as an aggregate in construction not only provides a solution to its environmentally unsuitable disposal but also helps to address disposal issues in fishing communities worldwide, such as the Ilha de Deus community. Additionally, it helps to reduce the extraction of natural materials for construction purposes. The research findings contribute to the existing literature, furthering the advancement of research in this field.
Sururu shell waste was collected from the Ilha de Deus community in eastern Brazil, as shown in Figure 1. First, a manual sorting process was carried out to eliminate solid waste, followed by washing with running water to drain impurities like sand and small insects in the SSA. The washed shells were then dried in an oven at 100°C ± 5°C for 24 h. After drying, it was discovered that the ligament responsible for joining the shells had become detached. It was suspected that the decomposition of these ligaments over time could create voids in the cementitious composites, affecting their durability and longevity. To avoid this, the shells were sieved again to remove any excess of this material. Next, the shells were pulverized, using a 900 W power Britannia blender, until they reached the same fineness as fine aggregate and had a texture akin to sand grains. Each batch of SSA was pulverized for about 15 s. The pulverized shells were then sifted through a #200 sieve to eliminate any excess powdery material and fines, making them suitable for fine aggregate use. Figure 2 compares the SSA before and after the processing.
The loss on ignition (LOI) of SSA samples was measured using a muffle furnace. Initially, a 10 g sample of SSA powder passed through sieve #200 and dried at 110°C in an oven. Afterward, a portion of the dried sample was subjected to a muffle furnace and heated to 1,000°C for 2 h to measure the loss in mass. Thermogravimetric analysis (TGA) was performed on SSA using a Shimadzu DTG-60. The test was performed on a 35 mg sample, with a temperature range from 23°C to 900°C and a heating rate of 10°C/min.
To explore the impact of using SSA as a substitute for fine aggregate in cementitious composites, mortar samples were produced by blending CPII-Z-32 Portland cement and sand in a 1:3 ratio with a water-to-cement ratio of 0.55, following the guidelines laid out in NBR 7215 (Associacao Brasileira De Normas Tecnicas, 1997). Four different mixes were created, with the first serving as the control group containing no SSA. In the remaining three mixes, 10%, 20%, and 40% of the fine aggregate (by mass) were replaced with SSA, respectively. A total of 72 cylindrical specimens, measuring 50 mm in diameter and 100 mm in height, were cast with 18 specimens for each mix, as shown in Figure 3. Table 3 outlines additional information about the compositions of the mixes used in this study.
The consistency index test was conducted on mortar following the standard procedure of Brazilian NBR 7215 (Associacao Brasileira De Normas Tecnicas, 1997). The test entails dropping the mortar from a specified height onto a larger diameter table 30 times within 30 s and measuring the average of two base diameters of the resulting mass in millimeters.
NBR 7215 is quite similar to the methodology of ASTM C1437 (ASTM C1437-20, 2020). However, there are some differences between the two standards, particularly in measuring equipment. For example, the NBR 7215 standard requires a larger table diameter of 500 ± 10 mm compared to the ASTM C230 specifications of 255 ± 2.5 mm. Additionally, the conical mold used for the mortar specimen is slightly larger in the NBR 7215 standard, measuring 65 ± 0.5 mm in height, 80 ± 0.5 mm in the top opening, and 125 ± 0.5 mm in the base opening, while the ASTM standard specifies 50 ± 0.5 mm, 70 ± 0.5 mm, and 100 ± 0.5 mm, respectively. Furthermore, the NBR standard requires 30 drops in 30 s for the table, while the ASTM C1437 standard requires 25 drops in 15 s. In the NBR standard, the final result is determined by averaging the mortar mass between two base diameters expressed in millimeters. On the other hand, the ASTM C4137 procedure calculates the increasing percentage of the original base diameter by averaging four base diameters.
The density of the fresh mortar was evaluated according to the NBR 13278 standard (Associacao Brasileira De Normas Tecnicas, 2005) using a rigid cylindrical container made of non-absorbent material, which is calibrated before use. The calibration process involves measuring and recording the weight of the empty container, filling it with water, and measuring the volume and total weight to determine its volume. The mortar is then prepared and placed in the container, which is subsequently weighed. The density of the mortar is computed by dividing the difference between the weight of the container filled with the mortar and the empty container by the container’s volume.
The NBR 7215 (Associacao Brasileira De Normas Tecnicas, 1997) standard was used to test compressive strength mortar specimens. The ASTM C109 (ASTM C1437-20, 2020) method is the equivalent standard for determining the compressive strength of mortars. The procedures for mortar preparation, specimen curing, storage, and determining compressive strength are the same for both methods. The main difference is in the molding of the specimens. NBR 7215 uses cylindrical specimens with a diameter and height of 50 ± 0.2 mm and 100 ± 0.5 mm, respectively. In comparison, ASTM C109 uses cubic molds with a side length of 50 mm. Additionally, the number of specimens required for testing is also different.
A 58-E4800 Ultrasonic Pulse Velocity Tester, as shown in Figure 4, was utilized to determine the dynamic modulus of elasticity following the NBR 15630 standard (Associacao Brasileira De Normas Tecnicas, 2009a). The test involves measuring the time in microseconds (μs) for an ultrasonic wave to pass through the specimen over a distance “L.” The propagation speed of the ultrasonic wave (V) in mm/μs can be determined from the equipment’s result using Eq. 1:
Where:
L—Height of the specimen (mm);
t—Time (microseconds) that the ultrasonic wave takes to travel the distance “L” obtained using an ultrasonic pulse velocity tester.
The dynamic modulus of elasticity (Ed) can be determined using Eq. 2:
Where:
Ed—Dynamic modulus of elasticity (MPa);
V—Velocity of ultrasonic wave propagation (mm/μs); ρ—Apparent mass density of the specimen (kg/m³) and
μ—Poisson coefficient—Adopted equal to 0.2 according to NBR 15630 (ABNT, 2008).
The capillary absorption test was conducted following the guidelines of NBR 9779 (Associacao Brasileira De Normas Tecnicas, 2012), which closely resembles the procedures outlined in ASTM C1403 (ASTM C1403, 2015) except for the shape of the specimens used, which were cylinders rather than cubes. Six specimens were cast for the test and were thoroughly soaked in lime water for 28 days. They were then weighed to determine their wet mass and dried in an oven at approximately 105°C ± 5°C until they reached a constant mass. After cooling to room temperature (23 ± 2)°C, they were weighed again and placed on wooden supports in a closed container at a constant temperature of around (23 ± 2)°C as shown in Figure 5. Water was added to the container until it reached a height of 5 mm above the bottom face of the specimens. The weights of the specimens were measured at 24 h, 48 h, and 72 h after they were introduced to the water. After each weighing, the specimens were immediately returned to the container. The specimens were broken using diametral compression in accordance with the NBR 7222 standard (Associacao Brasileira De Normas Tecnicas, 2011) after the final weighing, which allowed for the observation of water rising inside the specimens. The amount of water absorbed was calculated in g/cm2 by dividing the weight difference between the wet and dry specimens by the cross-sectional area in contact with water at each moment.
In this study, the SSA had a specific gravity of 2.66 g/cm3, a unit weight of 1,453 kg/m3, a void index of 42%, and a water absorption rate of 1.24%. The particle size distribution curve of the conventional fine aggregate and SSA, which is almost entirely within the recommended limits of NBR 7211 (Associacao Brasileira De Normas Tecnicas, 2009b), is presented in Figure 6. The SSA particle size contains a minimal amount of grains larger than 1.18 mm, less than 0.1%. This is because the milling process aimed to obtain grains that resemble sand grains as closely as possible. This study avoided larger dimensions to avoid elongation of the SSA particles and their significant impact on the mixtures’ workability.
Figure 7 displays the differential thermogravimetry (DTG) analysis of the SSA. The results indicate that the SSA remains stable up to approximately 630°C, with only a slight reduction in mass due to the evaporation of bound water from 194.36°C onwards. Additionally, there is a mass loss of 2.64% due to the decomposition of monosulfate when subjected to temperatures between 200°C and 360°C. The primary valley observed around 800°C corresponds to the decomposition of calcium carbonate (CaCO3) and the production of calcium oxide (CaO) and carbon dioxide (CO2). The results demonstrate that 97.86% of the SSA’s composition is CaCO3, highlighting its potential as a fine aggregate.
The thermogravimetric analysis of Sururu shells, as well as other mollusks such as mussels, oysters, and cockles, found in literature, generally indicate that calcining shells at temperatures above 600°C produce shell powder residues with a high CaO content. Table 4 shows the chemical composition of the SSA aggregate obtained through X-ray fluorescence spectrometry. Based on the findings, it can be concluded that Sururu shells have a chemical composition akin to limestone and other mollusks, primarily comprising calcium carbonate.
Figure 8 presents the average consistency and density of the mortar specimen. The results showed that the workability of the mortar was negatively impacted by the addition of SSA, as depicted in Table 5. A decrease in workability was observed as the percentage of SSA replacement increased. The flow test results revealed a reduction of 6.4%, 16.4%, and 31.5% in the mortar spread after substituting 10%, 20%, and 40% of sand with SSA, respectively. This is because SSA has a higher absorption capacity than conventional aggregate. The adverse effect of SSA on workability was also reported by other authors such as Wang et al. (2013), Safi et al. (2015), and others cited by Mo et al. (2018), who attributed it to the irregular shape and higher surface area of the particles, causing increased friction between materials.
According to the density measurements, a slight rise in mass density was observed for SSA10. On the other hand, despite having a higher specific mass than conventional aggregate, SSA20 and SSA40 exhibited a decrease in mass density. This decrease is thought to be due to the angular shape of SSA, resulting in air getting trapped between the particles. Cuadrado-Rica et al. (2016) and Martínez-García et al. (2017) have previously noted similar findings, indicating that this reduction in mass density could be a prevalent characteristic of SSA aggregates due to their distinct properties. Additionally, Hamada et al. (2023) assert that the lower density is attributed to poor particle packing in the composite incorporating seashells as aggregate.
According to Figure 9, the inclusion of SSA in mortar specimens resulted in a reduction in their compressive strength. The results show that replacing 10%, 20%, and 40% of fine aggregate with SSA resulted in an 11.7%, 15.8%, and 41.9% reduction in 7-day compressive strength, respectively. After 28 days of curing, all samples continued to gain strength. However, with respect to the control group with no SSA (SSA00), the 28-day compressive strength of the SSA samples was still lower. Nevertheless, the gap between the compressive strength of SSA samples and the control sample was reduced in most cases. After 28 days, the specimens with 10% SSA had the highest compressive strength compared to other replacement levels, showing only a 2.7% reduction compared to the control sample. Samples with 20% SSA also showed a 17.6% reduction in mean strength. In comparison, those incorporating 40% SSA showed a significant drop (43.7%) in compressive strength.
Other studies that used mollusk shells as a replacement for fine aggregate also reported a similar reduction in compressive strength (Elliott Richardson and Fuller, 2013; Eziefula et al., 2018; Martínez-García et al., 2019a). One explanation could be due to the porous nature of these shells, which can significantly compromise the mechanical properties of the interfacial transition zone between the paste and aggregate. In addition, according to Eziefula, Ezeh, and Eziefula (2018), flaky and elongated in shape aggregates have a poor bond with the cement paste, resulting in a greater volume of voids within the concrete matrix, which subsequently leads to a reduction in compressive strength.
The dynamic modulus of elasticity measures a material’s capacity to withstand deformation under dynamic loading, such as vibration or oscillation. Based on Figure 10, replacing 10% of fine aggregate with SSA has a negligible impact on mortar specimens’ calculated dynamic modulus of elasticity. The error bars in Figure 7 indicate no significant statistical difference relative to the control group. However, with the inclusion of the SSA substitution level, Ed was substantially reduced by 13% in SSA20 and 42.6% in SSA40 samples.
Aggregate properties can significantly impact the dynamic modulus of elasticity of concrete (Zheng et al., 2008; Beushausen and Dittmer, 2015; Rao et al., 2016; Vishalakshi et al., 2018). The size, shape, texture, and surface characteristics of aggregates can all influence the interlocking and bonding of aggregates with the cement paste, which can affect the elastic properties of concrete (Vishalakshi et al., 2018). Generally, smaller particle sizes and a smoother surface of aggregates tend to produce a higher modulus of elasticity due to the increased interlocking of particles and better bonding with the cement paste. On the other hand, rough and angular aggregates can produce a lower modulus of elasticity due to a reduced interlocking of particles and weaker bonding with the cement paste (Beshr et al., 2003).
SSA and mollusk shells generally have a more porous structure than traditional aggregates, leading to lower concrete density and, therefore, lower stiffness (Eziefula et al., 2018). Additionally, seashells are often irregular in shape and have a rough surface texture, which can reduce the interlocking of particles and weaken the bonding with the cement paste, resulting in a lower modulus of elasticity (Martínez-García et al., 2019b).
According to Figure 11, the incorporation of SSA has a positive effect on reducing capillary absorption in the mortar specimen. The best performance was observed in the SSA10 specimen, with an average reduction of more than 99% in capillary absorption at 24, 48, and 72 h compared to the control sample. This was followed by SSA20 and SSA40, which also showed a reduction in capillary absorption. The results indicate that capillary absorption increased with time during the first 72 h of exposure to water. There was no significant difference in performance between the control sample and SSA40 at 24 and 72 h. However, the results show a considerable reduction in capillary absorption after 48 h.
SSA’s beneficial effect on mortars’ capillary absorption can be attributed to the rough surface texture of the aggregate. This texture can create a more complex pathway for water to travel through the mortar matrix, thereby reducing the amount of water absorbed by the specimen. However, it is essential to note that there is a trade-off between surface texture and aggregate shape. If the SSA content exceeds a certain threshold, it could negatively impact capillary absorption. This is mainly because an increase in the angularity of aggregate shape can increase the capillary network, resulting in higher capillary absorption. Therefore, as the replacement level of SSA increases, so does the capillary absorption.
This phenomenon was also noted in the experiments conducted by Martínez-García et al. (2019a), who investigated the influence of mussel shell aggregate on the pore structure of lime mortar. The authors also emphasized that the presence of a natural protein (chitin) in mussel shell particles, which may exhibit hydrophilic properties, may decrease the water contact angle and, consequently, the capillary water absorption.
Figure 12 presents Pearson’s correlation matrix for the variables investigated in this study, which include SSA replacement level, density, 7- and 28-day compressive strength, 24- and 72-h capillary absorption, and dynamic modulus of elasticity. The correlation values between SSA replacement level and other variables align with the discussions in previous sections, revealing that SSA replacement level has a significantly negative correlation with density (ρ = −0.92), 7- and 28-day compressive strength (ρ ≤ −0.90), and dynamic modulus of elasticity (ρ = −0.97). The correlation observed between the levels of SSA substitution and the resultant compressive strength is similar to the findings of Bamigboye et al. (2022) in their research, with a value of −0.92 for 28 days of curing. Conversely, a low positive correlation was observed between SSA replacement levels and 24- and 72-h capillary absorption (ρ = 0.25), indicating that SSA marginally enhances water absorption through capillary action.
Figure 12. Relationship between SSA replacement level and physical and mechanical properties of mortar (CS, compressive strength; CA, capillary absorption; DME, dynamic modulus of elasticity).
The significant negative correlation between SSA replacement level and critical properties such as density, compressive strength, and dynamic modulus of elasticity can be attributed to the inherent characteristics of seashells. Unlike sand, seashells are less dense and more porous, resulting in a less compact mortar and a higher volume of voids. This reduced density and altered internal structure weaken the interfacial transition zone between the aggregate and cement paste, thereby decreasing the mortar’s compressive strength and stiffness under dynamic loads, as reflected by the lower dynamic modulus of elasticity. Concurrently, the slight positive correlation between SSA levels and capillary absorption suggests that the porous nature of seashells marginally increases the mortar’s ability to absorb water through capillary action.
Figure 12 illustrates a strong positive correlation among density, compressive strength, and dynamic modulus of elasticity, indicating that as the density of a material increases, so do its compressive strength and stiffness under dynamic loading. This relationship is attributed to the more compact microstructure of denser materials, which have fewer voids and defects, leading to an enhanced ability to withstand and distribute applied loads effectively (Silva et al., 2016). Conversely, a strong negative correlation is observed between capillary absorption and these variables, suggesting that materials with higher porosity and capillary action tend to exhibit lower density, reduced compressive strength, and decreased dynamic modulus of elasticity (Lian et al., 2011). The increased voids and pore spaces in such materials reduce their overall mass per unit volume and compromise their structural integrity and stiffness, allowing for more deformation under applied stresses. These correlations align with established principles in materials science, confirming that a denser, less porous material is generally stronger and stiffer, while higher capillary absorption is indicative of a weaker and more deformable structure (Abdul and Wong, 2004; Choucha et al., 2018; Iffat, 2015; R. Othman et al., 2021; Saberian et al., 2017).
This research investigated the potential of Sururu shells as a substitute for fine aggregates in mortar mixtures. The study focused on the effects of substituting natural fine aggregate with 10, 20, and 40% with Sururu Shell Aggregate (SSA) on consistency, density, compressive strength, dynamic modulus of elasticity, and capillary absorption of mortar mixtures.
The findings showed a decrease in workability with the increase of SSA substitution. A slight increase in mass density of specimens with 10% SSA was observed, while those containing 20% and 40% SSA showed decreased mass density. The compressive strength of mortar specimens was also reduced with higher SSA replacement levels. However, all samples continued to gain strength after 28 days of curing, reducing the difference with the control sample. The dynamic modulus of elasticity was minimally affected at 10% SSA replacement, but significantly reduced at 20% and 40%. Additionally, SSA reduced capillary absorption in the mortar specimens, with the best performance observed in 10% SSA replacement specimens.
Based on the evaluated mechanical properties, the authors conclude that Sururu shells have a potential to be incorporated as fine aggregate into mortar in small quantities, preferably less than 10 percent by weight of sand. However, it is essential to note that this study only focused on the mechanical and physical properties of mortar mixtures with SSA. Factors such as durability and environmental impact were not considered, and the laboratory conditions used may not reflect the performance of SSA-based mortar in real-world construction settings. The long-term effects of using SSA in mortar mixtures require further investigation to establish the durability and lifespan of structures constructed with SSA-based mortar. To further our understanding of SSA as an eco-friendly alternative in construction, future research should explore its environmental impact as a substitute for fine aggregates in mortar mixtures, including the carbon footprint and energy consumption associated with the production and transportation of SSA.
The original contributions presented in the study are included in the article/supplementary material; further inquiries can be directed to the corresponding author.
AdSC: Data curation, Investigation, Writing–original draft. EK: Funding acquisition, Supervision, Writing–review and editing. AS: Writing–review and editing. MS: Writing–review and editing, Investigation. EM: Supervision, Writing–review and editing. MS: Formal Analysis, Supervision, Visualization, Writing–original draft, Writing–review and editing.
The authors declare that financial support was received for the research, authorship, and/or publication of this article. This study was financed in part by the Coordenação de Aperfeiçoamento de Pessoal de Nível Superior—Brasil (CAPES)—Finance Code 001.
The authors gratefully acknowledge the support of Colorado State University Library for covering the cost of open-access publication. This generous contribution has enabled our research to be accessible to a broad audience, fostering greater collaboration and advancing the dissemination of knowledge within our field.
The authors declare that the research was conducted in the absence of any commercial or financial relationships that could be construed as a potential conflict of interest.
All claims expressed in this article are solely those of the authors and do not necessarily represent those of their affiliated organizations, or those of the publisher, the editors and the reviewers. Any product that may be evaluated in this article, or claim that may be made by its manufacturer, is not guaranteed or endorsed by the publisher.
Abdul, R. H., and Wong, H. (2004) Re-evaluation of strength and stiffness relationships for high-strength concrete.
Associacao Brasileira De Normas Tecnicas (1997) NBR 7215: Cimento Portland: Determinação da resistência à compressão. Brazil: Rio de Janeiro.
Associacao Brasileira De Normas Tecnicas (2005) NBR 13278: Argamassa para assentamento e revestimento de paredes e tetos - Determinação da densidade de massa e do teor de ar incorporado. Rio de Janeiro, Brazil.
Associacao Brasileira De Normas Tecnicas (2009a) NBR 15630: Argamassa para assentamento e revestimento de paredes e tetos - Determinação do módulo de elasticidade dinâmico através da propagação de onda ultrassônica. Brazil: Rio de Janeiro.
Associacao Brasileira De Normas Tecnicas (2009b) NBR 7211: Agregados para concreto. Brazil: Rio de Janeiro.
Associacao Brasileira De Normas Tecnicas (2011) NBR 7222: Concreto e argamassa — Determinação da resistência à tração por compressão diametral de corpos de prova cilíndricos. Rio de Janeiro, Brazil.
Associacao Brasileira De Normas Tecnicas (2012) NBR 9779: Argamassa e concreto endurecidos: Determinação da absorção de água por capilaridade. Brazil: Rio de Janeiro.
ASTM C1403 (2015) Standard test method for rate of water absorption of masonry mortars. Philadelphia, PA: ASTM International.
ASTM C1437-20 (2020) Standard test method for flow of hydraulic cement mortar. West Conshohocken, PA: ASTM International.
Bamigboye, G., Enabulele, D., Odetoyan, A. O., Kareem, M. A., Nworgu, A., and Bassey, D. (2021). Mechanical and durability assessment of concrete containing seashells: a review. Cogent Eng. 8 (1), 1883830. doi:10.1080/23311916.2021.1883830
Bamigboye, G. O., Okechukwu, U. E., Olukanni, D. O., Bassey, D. E., Okorie, U. E., Adebesin, J., et al. (2022). Effective economic combination of waste seashell and river sand as fine aggregate in green concrete. Sustainability 14, 12822. doi:10.3390/su141912822
Beshr, H., Almusallam, A., and Maslehuddin, M. (2003). Effect of coarse aggregate quality on the mechanical properties of high strength concrete. Constr. Build. Mater. 17 (2), 97–103. doi:10.1016/s0950-0618(02)00097-1
Beushausen, H., and Dittmer, T. (2015). The influence of aggregate type on the strength and elastic modulus of high strength concrete. Constr. Build. Mater. 74, 132–139. doi:10.1016/j.conbuildmat.2014.08.055
Boudjellal, K., Bouabaz, M., and Bensebti, S. E. (2020). Formulation of a concrete based on grinded seashells as partial substitution for sand. Civ. Environ. Eng. Rep. 30 (4), 56–71. doi:10.2478/ceer-2020-0050
Cardoso, A. d. S., Rabbani, E. R. K., Delmiro, T. D., Mocock, J. F. B., Silva, S. P. R. d., Filippelli, G., et al. (2023). Mollusk shell waste: alternatives for reuse in construction. Int. J. Environ. Waste Manag. 31 (1), 61–80. doi:10.1504/ijewm.2023.129727
Choucha, S., Benyahia, A., Ghrici, M., and Said Mansour, M. (2018). Correlation between compressive strength and other properties of engineered cementitious composites with high-volume natural pozzolana. Asian J. Civ. Eng. 19 (5), 639–646. doi:10.1007/s42107-018-0050-3
Cuadrado-Rica, H., Sebaibi, N., Boutouil, M., and Boudart, B. (2016). Properties of ordinary concretes incorporating crushed queen scallop shells. Mater. Struct. 49, 1805–1816. doi:10.1617/s11527-015-0613-7
Djobo, Y., Elimbi, A., Manga, J. D., and Ndjock, I. D. L. (2016). Partial replacement of volcanic ash by bauxite and calcined oyster shell in the synthesis of volcanic ash-based geopolymers. Constr. Build. Mater. 113, 673–681. doi:10.1016/j.conbuildmat.2016.03.104
Edalat-Behbahani, A., Soltanzadeh, F., Emam-Jomeh, M., and Soltan-Zadeh, Z. (2021). Sustainable approaches for developing concrete and mortar using waste seashell. Eur. J. Environ. Civ. Eng. 25 (10), 1874–1893. doi:10.1080/19648189.2019.1607780
El Biriane, M., and Barbachi, M. (2021). State-of-the-art review on recycled mussel shell waste in concrete and mortar. Innov. Infrastruct. Solutions 6, 29–10. doi:10.1007/s41062-020-00394-9
Elliott Richardson, A., and Fuller, T. (2013). Sea shells used as partial aggregate replacement in concrete. Struct. Surv. 31 (5), 347–354. doi:10.1108/ss-12-2012-0041
El Mendili, Y., and Benzaama, M. H. (2022). Investigation of mechanical and thermal performance of concrete with scallop shells as partial cement replacement: alternative binder and life cycle assessment. CivilEng 3 (3), 760–778. doi:10.3390/civileng3030044
Eo, S.-H., and Yi, S.-T. (2015). Effect of oyster shell as an aggregate replacement on the characteristics of concrete. Mag. Concr. Res. 67 (15), 833–842. doi:10.1680/macr.14.00383
Eziefula, U. G., Ezeh, J. C., and Eziefula, B. I. (2018). Properties of seashell aggregate concrete: a review. Constr. Build. Mater. 192, 287–300. doi:10.1016/j.conbuildmat.2018.10.096
Ez-Zaki, H., Diouri, A., Kamali-Bernard, S., and Sassi, O. (2016). Composite cement mortars based on marine sediments and oyster shell powder. Mater. Construccíon 66 (321), e080. doi:10.3989/mc.2016.01915
Felipe-Sesé, M., Eliche-Quesada, D., and Corpas-Iglesias, F. (2011). The use of solid residues derived from different industrial activities to obtain calcium silicates for use as insulating construction materials. Ceram. Int. 37 (8), 3019–3028. doi:10.1016/j.ceramint.2011.05.003
Hadjadj, M., Guendouz, M., and Boukhelkhal, D. (2024). The effect of using seashells as cementitious bio-material and granite industrial waste as fine aggregate on mechanical and durability properties of green flowable sand concrete. J. Build. Eng. 87, 108968. doi:10.1016/j.jobe.2024.108968
Hamada, H. M., Abed, F., Tayeh, B., Al Jawahery, M. S., Majdi, A., and Yousif, S. T. (2023). Effect of recycled seashells on concrete properties: a comprehensive review of the recent studies. Constr. Build. Mater. 376, 131036. doi:10.1016/j.conbuildmat.2023.131036
Hart, A. (2020). Mini-review of waste shell-derived materials’ applications. Waste Manag. Res. 38 (5), 514–527. doi:10.1177/0734242x19897812
Hasnaoui, A., Bourguiba, A., El Mendili, Y., Sebaibi, N., and Boutouil, M. (2021). A preliminary investigation of a novel mortar based on alkali-activated seashell waste powder. Powder Technol. 389, 471–481. doi:10.1016/j.powtec.2021.05.069
Her, S., Park, T., Zalnezhad, E., and Bae, S. (2021). Synthesis and characterization of cement clinker using recycled pulverized oyster and scallop shell as limestone substitutes. J. Clean. Prod. 278, 123987. doi:10.1016/j.jclepro.2020.123987
Iffat, S. (2015). Relation between density and compressive strength of hardened concrete. Concr. Res. Lett. 6 (4), 182–189.
Jović, M., Mandić, M., Šljivić-Ivanović, M., and Smičiklas, I. (2019). Recent trends in application of shell waste from mariculture. Stud. Mar. 32 (1), 47–62. doi:10.5281/zenodo.3274471
Kim, S., Kim, Y. T., Oh, L. S., Kim, H. J., and Lee, J. (2022). Marine waste upcycling—recovery of nylon monomers from fishing net waste using seashell waste-derived catalysts in a CO 2-mediated thermocatalytic process. J. Mater. Chem. A 10 (37), 20024–20034. doi:10.1039/d2ta02060b
Kuo, W.-T., Wang, H.-Y., Shu, C.-Y., and Su, D.-S. (2013). Engineering properties of controlled low-strength materials containing waste oyster shells. Constr. Build. Mater. 46, 128–133. doi:10.1016/j.conbuildmat.2013.04.020
Leone, R., Calà, A., Capela, M. N., Colajanni, S., Campisi, T., and Saeli, M. (2023). Recycling mussel shells as secondary sources in green construction materials: a preliminary assessment. Sustainability 15 (4), 3547. doi:10.3390/su15043547
Lertwattanaruk, P., Makul, N., and Siripattarapravat, C. (2012). Utilization of ground waste seashells in cement mortars for masonry and plastering. J. Environ. Manag. 111, 133–141. doi:10.1016/j.jenvman.2012.06.032
Li, G., Xu, X., Chen, E., Fan, J., and Xiong, G. (2015). Properties of cement-based bricks with oyster-shells ash. J. Clean. Prod. 91, 279–287. doi:10.1016/j.jclepro.2014.12.023
Lian, C., Zhuge, Y., and Beecham, S. (2011). The relationship between porosity and strength for porous concrete. Constr. Build. Mater. 25 (11), 4294–4298. doi:10.1016/j.conbuildmat.2011.05.005
Loffi, S. B. (2014) Estudo sobre o comportamento de uma argamassa incorporada com cascas de ostras. Engenharia Ambiental e Sanitária-Pedra Branca.
Marques, F. B., Watterson, A., da Rocha, A. F., and Cavalli, L. S. (2020). Overview of Brazilian aquaculture production. Aquac. Res. 51 (12), 4838–4845. doi:10.1111/are.14828
Martínez-García, C., González-Fonteboa, B., Carro-López, D., and Martínez-Abella, F. (2019a). Impact of mussel shell aggregates on air lime mortars. Pore structure and carbonation. J. Clean. Prod. 215, 650–668. doi:10.1016/j.jclepro.2019.01.121
Martínez-García, C., González-Fonteboa, B., Carro-López, D., and Martínez-Abella, F. (2019b). Recycled mollusc shells. New Trends Eco-efficient Recycl. Concr., 191–205. Elsevier. doi:10.1016/b978-0-08-102480-5.00008-7
Martínez-García, C., González-Fonteboa, B., Martínez-Abella, F., and Carro-López, D. (2017). Performance of mussel shell as aggregate in plain concrete. Constr. Build. Mater. 139, 570–583. doi:10.1016/j.conbuildmat.2016.09.091
Mo, K. H., Alengaram, U. J., Jumaat, M. Z., Lee, S. C., Goh, W. I., and Yuen, C. W. (2018). Recycling of seashell waste in concrete: a review. Constr. Build. Mater. 162, 751–764. doi:10.1016/j.conbuildmat.2017.12.009
Nduka, D. O., Akanbi, E. T., Ojo, D. O., Babayemi, T. E., and Jolayemi, K. J. (2023). Investigation of the mechanical and microstructural properties of masonry mortar made with seashell particles. Materials 16, 2471. doi:10.3390/ma16062471
Olivia, M., Mifshella, A. A., and Darmayanti, L. (2015). Mechanical properties of seashell concrete. Procedia Eng. 125, 760–764. doi:10.1016/j.proeng.2015.11.127
Othman, N. H., Bakar, B. H. A., Don, M. M., and Johari, M. A. M. (2013). Cockle shell ash replacement for cement and filler in concrete. Malays. J. Civ. Eng. 25 (2), 201–211. doi:10.11113/mjce.v25.15853
Othman, R., Jaya, R. P., Muthusamy, K., Sulaiman, M., Duraisamy, Y., Abdullah, M. M. A. B., et al. (2021). Relation between density and compressive strength of foamed concrete. Materials 14 (11), 2967. doi:10.3390/ma14112967
Oyejobi, D., Raji, S., Aina, S., and Siva, A. (2019). Physio-chemical and microstructural characteristics of selected pozzolanic materials for cement and concrete production. Niger. J. Technol. Dev. 16 (3), 111–119. doi:10.4314/njtd.v16i3.4
Peceño, B., Alonso-Fariñas, B., Vilches, L., and Leiva, C. (2021). Study of seashell waste recycling in fireproofing material: technical, environmental, and economic assessment. Sci. Total Environ. 790, 148102. doi:10.1016/j.scitotenv.2021.148102
Petrielli, F. A. d. S. (2008) Viabilidade técnica e econômica da utilização comercial das conchas de ostras descartadas na localidade do Ribeirão da Ilha. Florianopolis, Santa Catarina.
Rao, S. K., Sravana, P., and Rao, T. C. (2016). Experimental studies in Ultrasonic Pulse Velocity of roller compacted concrete pavement containing fly ash and M-sand. Int. J. Pavement Res. Technol. 9 (4), 289–301. doi:10.1016/j.ijprt.2016.08.003
Rodríguez-Galán, M., Alonso-Fariñas, B., Baena-Moreno, F. M., Leiva, C., Navarrete, B., and Vilches, L. F. (2019). Synthetic slag production method based on a solid waste mix vitrification for the manufacturing of slag-cement. Materials 12 (2), 208. doi:10.3390/ma12020208
Ruslan, H. N., Muthusamy, K., Mohsin, S. M. S., Jose, R., and Omar, R. (2022). Oyster shell waste as a concrete ingredient: a review. Mater. Today Proc. 48, 713–719. doi:10.1016/j.matpr.2021.02.208
Saberian, M., Jahandari, S., Li, J., and Zivari, F. (2017). Effect of curing, capillary action, and groundwater level increment on geotechnical properties of lime concrete: experimental and prediction studies. J. Rock Mech. Geotechnical Eng. 9 (4), 638–647. doi:10.1016/j.jrmge.2017.01.004
Safi, B., Saidi, M., Daoui, A., Bellal, A., Mechekak, A., and Toumi, K. (2015). The use of seashells as a fine aggregate (by sand substitution) in self-compacting mortar (SCM). Constr. Build. Mater. 78, 430–438. doi:10.1016/j.conbuildmat.2015.01.009
Sangeetha, P., Shanmugapriya, M., Saravanan, K. S., Prabhakaran, P., and Shashankar, V. (2022). Mechanical properties of concrete with seashell waste as partial replacement of cement and aggregate. Mater. Today Proc. 61, 320–326. doi:10.1016/j.matpr.2021.09.501
Silva, R. V., De Brito, J., and Dhir, R. K. (2016). Establishing a relationship between modulus of elasticity and compressive strength of recycled aggregate concrete. J. Clean. Prod. 112, 2171–2186. doi:10.1016/j.jclepro.2015.10.064
Soltanzadeh, F., Behbahani, A. E., Pereira, E. N., and Teixeira, C. A. (2021). A life-cycle approach to integrate environmental and mechanical properties of blended cements containing seashell powder. Sustainability 13 (23), 13120. doi:10.3390/su132313120
Tayeh, B. A., Hasaniyah, M. W., Zeyad, A., and Yusuf, M. O. (2019). Properties of concrete containing recycled seashells as cement partial replacement: a review. J. Clean. Prod. 237, 117723. doi:10.1016/j.jclepro.2019.117723
Tayeh, B. A., Hasaniyah, M. W., Zeyad, A. M., Awad, M. M., Alaskar, A., Mohamed, A. M., et al. (2020). Durability and mechanical properties of seashell partially-replaced cement. J. Build. Eng. 31, 101328. doi:10.1016/j.jobe.2020.101328
Varhen, C., Carrillo, S., and Ruiz, G. (2017). Experimental investigation of Peruvian scallop used as fine aggregate in concrete. Constr. Build. Mater. 136, 533–540. doi:10.1016/j.conbuildmat.2017.01.067
Vishalakshi, K., Revathi, V., and Reddy, S. S. (2018). Effect of type of coarse aggregate on the strength properties and fracture energy of normal and high strength concrete. Eng. Fract. Mech. 194, 52–60. doi:10.1016/j.engfracmech.2018.02.029
Wang, H.-Y., Kuo, W.-T., Lin, C.-C., and Po-Yo, C. (2013). Study of the material properties of fly ash added to oyster cement mortar. Constr. Build. Mater. 41, 532–537. doi:10.1016/j.conbuildmat.2012.11.021
Xuan, M. Y., Cho, H. K., and Wang, X. Y. (2023). Performance improvement of waste oyster-shell powder–cement binary system via carbonation curing. J. Build. Eng. 70, 106336. doi:10.1016/j.jobe.2023.106336
Yang, E.-I., Kim, M.-Y., Park, H.-G., and Yi, S.-T. (2010). Effect of partial replacement of sand with dry oyster shell on the long-term performance of concrete. Constr. Build. Mater. 24 (5), 758–765. doi:10.1016/j.conbuildmat.2009.10.032
Yang, E.-I., Yi, S.-T., and Leem, Y.-M. (2005). Effect of oyster shell substituted for fine aggregate on concrete characteristics: Part I. Fundamental properties. Cem. Concr. Res. 35 (11), 2175–2182. doi:10.1016/j.cemconres.2005.03.016
Yao, Z., Xia, M., Li, H., Chen, T., Ye, Y., and Zheng, H. (2014). Bivalve shell: not an abundant useless waste but a functional and versatile biomaterial. Crit. Rev. Environ. Sci. Technol. 44 (22), 2502–2530. doi:10.1080/10643389.2013.829763
Yoon, G.-L., Kim, B.-T., Kim, B.-O., and Han, S.-H. (2003). Chemical–mechanical characteristics of crushed oyster-shell. Waste Manag. 23 (9), 825–834. doi:10.1016/s0956-053x(02)00159-9
Keywords: recycled aggregates, Sururu shell, waste management, mortar, concrete
Citation: Cardoso AdS, Kohlman Rabbani ER, Silva ALd, Sá MKCRGd, Monteiro EB and Shakouri M (2024) Evaluating Sururu shell waste (Mytella falcata) as an eco-friendly recycled aggregate in mortar production. Front. Built Environ. 10:1381169. doi: 10.3389/fbuil.2024.1381169
Received: 02 February 2024; Accepted: 24 April 2024;
Published: 27 May 2024.
Edited by:
K. I. Syed Ahmed Kabeer, Anna University, IndiaReviewed by:
Naraindas Bheel, University of Technology Petronas, MalaysiaCopyright © 2024 Cardoso, Kohlman Rabbani, Silva, Sá, Monteiro and Shakouri. This is an open-access article distributed under the terms of the Creative Commons Attribution License (CC BY). The use, distribution or reproduction in other forums is permitted, provided the original author(s) and the copyright owner(s) are credited and that the original publication in this journal is cited, in accordance with accepted academic practice. No use, distribution or reproduction is permitted which does not comply with these terms.
*Correspondence: Mahmoud Shakouri, bWFobW91ZC5zaGFrb3VyaUBjb2xvc3RhdGUuZWR1
Disclaimer: All claims expressed in this article are solely those of the authors and do not necessarily represent those of their affiliated organizations, or those of the publisher, the editors and the reviewers. Any product that may be evaluated in this article or claim that may be made by its manufacturer is not guaranteed or endorsed by the publisher.
Research integrity at Frontiers
Learn more about the work of our research integrity team to safeguard the quality of each article we publish.