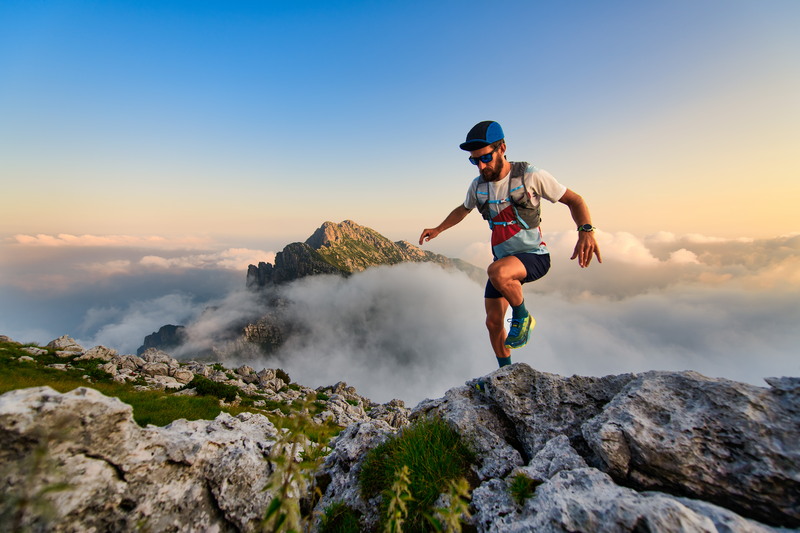
94% of researchers rate our articles as excellent or good
Learn more about the work of our research integrity team to safeguard the quality of each article we publish.
Find out more
HYPOTHESIS AND THEORY article
Front. Built Environ. , 09 May 2024
Sec. Structural Sensing, Control and Asset Management
Volume 10 - 2024 | https://doi.org/10.3389/fbuil.2024.1354657
In Accelerated Bridge Construction (ABC), Ultra-High Performance Concrete (UHPC) is often used for connecting precast concrete bridge components, including deck portions of the Deck Bulb-T girders. An alternative low-cost non-proprietary UHPC has been proposed for use in place of the proprietary UHPC for connecting the precast components. The pullout behavior of steel reinforcing bars in closure pour with typical range for embedment lengths is studied for both proprietary and non-proprietary UHPC materials.
Accelerated Bridge Construction (ABC) technologies are being adopted by many Departments of Transportation (DOTs) in the United States. ABC increases safety by lowering exposure to construction activities and increases mobility and economic opportunities by reducing traffic interruptions and delays. ABC requires that bridge precast concrete components to be effectively connected to one another in the field. In ABC, most of the bridge components are prefabricated off-site. The prefabricated components are transported to the construction site and are assembled. While assembling the components, gaps are provided between the bridge segments for connecting the components in the field; these gaps are referred to as closure pours. There are various materials available for use in the closure pour. Normal weight concrete, high early strength concrete with fibers, high strength grout, and Ultra-High Performance Concrete (UHPC) are some of the materials that are used.
UHPC is an advanced material that is commonly used for the casting of closure pour in highway bridges because of its excellent material properties. The compressive strength of UHPC reaches up to 140 MPa (20 ksi) or more. Despite having various advantages, UHPC also comes with some downsides. UHPC is typically a proprietary material that has high installation cost requires rigorous quality control requirements (Ebrahimpour et al., 2018). Wille and Boisvert-Cotulio (2013) were among the first researchers in the United States (U.S.) who spearheaded the development of the first set of non-proprietary UHPC materials. The research was supported by the U.S. Federal Huighway Administration with the long-term goals to facilitate the use of UHPC among U.S. suppliers and contractors, accelerate its application in construction, and promote a more resilient and sustainable future infrastructure. Among other researchers developing non-properiatray UPHC are Qiao, et al. (2016), Berry, et al. (2017), El-Tawil, et al. (2018), and Morcous, et al. (2020).
Recently, at Idaho State University (ISU) a non-proprietary UHPC was developed for bridge applications (Shokrgozar, 2023). At 28 days, the non-proprietary mix has a compressive strength of 124 MPa (18 ksi) with a cost of approximately $390 per cubic meter ($300 per cubic yard). Since very often UHPC is a proprietary product and because of its cost, bridge engineers are searching for alternative mixes. The cost of proprietary UHPC exceeds $1,600 per cubic meters (Berry et al., 2017). An on-site engineer who is responsible for inspecting and guiding the process is also needed while using the proprietary UHPC which increases the overall costs. The purpose of this research project was to understand the pullout behavior between steel bar and UHPC, both for proprietary and non-proprietary UHPC.
Figure 1A shows a bridge cross-section composed of five Deck Bulb-T girders and four closure pours between the deck portions. Figure 1B shows the detail drawing of a closure pour with both transverse and longitudinal reinforcing bars. The typical width of the closure connections ranges from 152 mm (6 in.) to 254 mm (10 in.), with embedment length of the transverse bar having a range of 127 (5 in.) to 229 mm (9 in.).
Two types of bonds should be considered for field-cast connections. First, the bond between the steel bar and the concrete and second, the bond between the field-cast concrete and the precast bridge elements (Xing et al., 2015). This research focuses on the bond between the steel bar and the field-cast concrete. Early work on the study of pullout bond strength and bond-slip behavior of reinforcing bars in conventional reinforced concrete is abounding (Mathey and Watstein, 1961; Lutz and peter 1967; Goto, 1971). These studies investigated bond response mechanism of deformed bars in normal concrete and the effect of lateral reinforcement on bond-slip and bond strength. Rao et al. (2007) studied the reinforcing bar bond strength in high-strength concrete (HSC). Various parameters such as bar diameter, strength of concrete, lateral confinement, and embedment length were studied. Two concrete mixes with compressive strength of 30 MPa (4,350 psi) and 60 MPa (8,700 psi) were used. Cubes of size 150 mm × 150 mm × 150 mm (5.9 in × 5.9 in × 5.9 in) were used for compressive strength of concrete as well as for pullout specimen. The bars were placed in the middle of the specimen and the embedment length was achieved by using PVC tubes. Three types of specimens were used: unconfined, confined with spirals, and confined with ties (Rao et al., 2007). Monotonic load was applied by means of the actuator and the rate of the stroke control was maintained at 0.025 mm/s. Bond stress was expressed as:
Where,
For the research project presented herein, based on prior experimental work on developing UHPC, the material constituents necessary for UHPC were defined, and locally available materials in the northwestern United States were identified (Shokrgozar, 2023). This included different types of cement, silica fumes, supplemental materials, high-range water reducers (HRWRs), aggregates and fibers. Next, these materials were preselected based on availability, cost, region, particle size distribution, and chemical and physical composition.
The mix design of the non-proprietary UHPC used in this paper is shown in Table 1. More information about the materials is provided in the dissertation by Shokrgozar (2023). The cost of the non-proprietary UHPC is less than $390 per cubic meter ($300 per cubic yard). The cost of shipping and placement is not included. The fine aggregate used for this mix is volcanic rock (Shokrgozar, 2023).
The gradation specifications of upper and lower limits of ASTM C144, Standard Specification for Aggregate for Masonry Mortar (ASTM, 2020), and the gradation of the modified Andreasen & Andersen (A&A) used for UHPC used in this research are shown below in Table 2. In preliminary trial mixes, different aggregate gradations were used. This gradation proved to provide the best workability and compression strength.
The mixing process of the non-proprietary UHPC was similar to typical steps used by other researchers (Graybeal, 2013; Wille and boisvert-Cotulio, 2013). The steps are as follows: (1) mix sand/aggregate and silica fume for 5 min, (2) add cement and supplemental material and mix for an additional 5 min, (3) add 1/3 of the HRWR to the water, (4) add the water-HRWR mixture within 1 min after pouring is started, (5) add the remaining HRWR within 1 min after pouring is started, (6) increase mixing speed, (7) add fibers if applicable, (8) mix until fluidity is optimized (between 5–10 min). As it can be seen, the mixing process took a long time and one can reasonably assume that fibers were well-mixed in the process. In addition, we used a vertical mixer which is the standard mixer for UHPC.
For this project, a proprietary UHPC from a major manufacturer in the United States is used. This type of proprietary UHPC is typically used in bridge closure pours in ABC applications. As noted above, the non-proprietary UHPC was developed at Idaho State University (Shokrgozar, 2023).
To determine material properties, UHPC concrete samples were cast in accordance with ASTM C1856/C1856M, Standard Practice for Fabricating and Testing Specimens of Ultra-High Performance Concrete (ASTM, 2017). UHPC was mixed in the laboratory with a vertical mixer. 51 mm × 51 mm × 51 mm (2 in. × 2 in. × 2 in.) cubes were cast for determining the compressive strength of the UHPC. 78 mm (3 in.) diameter by 152 mm (6 in.) cylinders were cast for determining the split tensile strength. The samples were removed from their respective molds after 24 h of casting and were moist cured in lime-saturated water for 28 days and removed afterwards for testing. Compressive strength tests were performed in accordance with ASTM C109, Standard Test Method for Compressive Strength of Hydraulic Cement Mortars Using 2-in Cube Specimens (ASTM Standard, 2020). The split tensile test was done in accordance with ASTM C496, Standard Test Method for Splitting Tensile Strength of Cylindrical Concrete Specimens (ASTM Standard, 2017). The flow table test of UHPC mixes were done in accordance with ASTM C1856/C1856M, Standard Practice for Fabricating and Testing Specimens of Ultra-High Performance Concrete (ASTM Standard, 2017).
Pullout test specimens were prepared to determine the ultimate force and bond-slip relationship between bar and UHPC with the bars having typical embedment length used in closure pour connection. Figure 2A shows the cross-section of two side-by-side Deck Bulb-T girders. Figure 2B shows the close-up view of the closure pour connection between the two girders. Figure 2C shows the the pullout specimen that represents the bottom half of the closure pour connection. The goal was to determine the pullout behavior of a 19 mm diameter (No. 6 or 0.75 in. diameter) transverse bar (the middle bar) in presence of two opposing transverse bars. To make the bond-slip behavior more realistic when it comes to concrete confinement, 13 mm diameter (No. 4 or 0.5 in. diameter) longitudinal bars were also included as shown in Figure 2C. The bars were ASTM A615 Grade 60 with yield and ultimate strength values of 60 ksi (414 MPa) and 90 ksi (621 MPa), respectively. The size of pullout specimen was 381 mm × 254 mm × 102 mm (15 in. × 10 in. × 4 in.). Specimens with the top bar (the bar under consideration) embedment lengths,
Figure 2. (A) Cross-section of two girders, (B) closure pour connection, and (C) pullout specimen schematic (1 mm = 0.0394 in.).
The top bar embedment length was achieved by using the PVC pipe extending from the bottom of the bar to the bottom of the specimen. Experimentally, the bond-slip of the top bar was measured at two locations: (1) at the top where the bar immediately exits the specimen, and (2) at the bottom of the bar (by inserting a displacement sensor inside the PVC pipe). The displacements (slips) at these locations are denoted by St and Sb in Figure 2C. The 13 mm bars used as longitudinal reinforcement was placed at 25 mm (1 in.) from both top and bottom of the mold. The specimens were cured for 28 days prior to testing.
The specimen and the locations of the displacement sensors (linear potentiometers) are shown in Figures 3A, B. It should be noted that placement of bars in specimen is symmetrical. That is, the transvers bars were placed in the middle the specimen with centers located 5 cm (2 in.) from each side. There is one displacement sensor at the bottom measuring the bar bottom slip (i.e., Sb, in Figure 2C) relative to the bottom surface of specimen. On the top there are two displacement sensors measuring the top slip (i.e., St, in Figure 2C) with respect to the top of the specimen. The two top displacements were averaged to remove any rotations. Figure 4 shows the pullout test setup (Aryal, 2022).
As shown in Figure 4, a displacement-controlled servo-hydraulic actuator was used to apply the load to the specimens. A 1000 kN (225 kips) capacity load cell was connected to the head of the actuator. The loading rate of 0.5 mm/min was used by the actuator to pull the specimen. Displacements were measured at the top and bottom of the top bar. These displacements were measured with the help of 102 mm (4 in.) stroke potentiometers. Force and displacement data were collected from the pullout tests.
Table 3 shows the results of the standard tests on both the proprietary and the non-proprietary specimens. As it can be seen, both UHPC materials have similar material properties, with proprietary UHPC having slightly higher strength values.
The specimens cast from proprietary UHPC were designated as P5-A, P5-B, P5-C, P7-A, P7-B, P9-A, P9-B, and P9-C. The specimens cast from non-proprietary UHPC were designated as NP5-A, NP5-B, NP7-A, NP7-B, NP9-A, and NP9-B. The specimens were named based on their UHPC mix and bar embedment length. For example, P5-A stands for pullout specimen made from proprietary UHPC with 5 in. (127 mm) embedment length, sample A. Data was collected up to the point of failure which was defined by either concrete failure or fracture of the upper bar. Table 4 summarizes the results of the pullout tests.
The results show that for proprietary specimens, concrete failed for specimens with smaller embedment, whereas bar broke for specimens with larger embedment. For non-proprietary specimens, concrete failed for all embedment lengths. Concrete cracking first initiated at the top surface and propagated vertically and horizontally across the specimen. The upper bar displacement (slip) at top (
Table 5 shows the comparison of average ultimate force, average slip at ultimate force, and average ultimate shear stress for proprietary and non-proprietary UHPC.
From Table 5, it is clear that although bars with larger embedment lengths result in larger ultimate forces, the bond shear stresses as obtained by Eq. 1 (i.e., normalized values) are closer to one another. Figure 7 shows the graph of the average shear stress versus slip for all proprietary and non-proprietary specimens having embedment lengths of 127 mm (5 in.), 178 mm (7 in.), and 229 mm (9 in.); i.e., for use with typical closure pour widths of between 152 mm (6 in.) to 254 mm (10 in.). Figure 7 shows that the non-proprietary UHPC has a smaller initial slope and behaves somewhat more ductile. On Figure 7, the limit of the working shear stresses measured in a bridge in Idaho is also shown (Ebrahimpour et al., 2020). As a part of the research by Ebrahimpour et al. (2020) the transverse bars in four closure pour connections of the bridge were instrumented with strain gages. This working shear stress limit is approximately 5.5 MPa (0.8 ksi). Since both curves in Figure 7 behave somewhat linearly in this range, fitted lines are also shown in Figure 7 in the linear regions which may be used in computer modeling of the closure pour UHPC. In both fitted line equations shown in Figure 7, the shear stress,
Figure 7. Average stress versus slip for all proprietary and non-proprietary specimens having embedment lengths of 127 mm (5 in), 178 mm (7 in), and 229 mm (9 in).
As seen in Figure 7, the bar slip in non-proprietary UHPC is slightly more at the working stress level of 5.5 MPa. This difference is less than 0.005 cm or 0.05 mm which is smaller than bond slip of about 0.1 mm at the same bond stress measured by Rao et al. (2007). Having noted this, the extra slip in non-proprietary UHPC and its effect on deck transverse deflection needs to be further investigated.
One of the advantages of using non-proprietary is its cost. The material cost of the non-proprietary UHPC is less than the proprietary UHPC. Another consideration of using non-proprietary UHPC is being able to use local materials (e.g., aggregates and cement) and domestic fibers. Such materials make the use of non-proprietary UHPC more appealing since its use will not be affected by supply-chain and it is also more environmentally friendly. In addition, with the use of the non-preoperatory UHPC, the added cost of an on-site engineer can be eliminated. With proper guidance, this responsibility can be given to the department of transportation bridge project manager and the on-site inspector.
Through laboratory experimentation, it was seen that the material properties of non-proprietary UHPC are comparable to proprietary UHPC. These included compressive strength, tensile strength, and flow table tests. The bond-slip response of the proprietary and non-proprietary UHPC were also similar. However, on average, the non-proprietary UHPC exhibits more bond-slip than the proprietary UHPC. Simplified linear equations are suggested in the linear range of bond shear stress versus slip.
More work needs to be done in determining whether the developed UHPC satisfies all the design requirements. Some future work may include: (1) environmental durability, including freeze-thaw, chloride ion penetration, and carbonation with comparisons made with proprietary UHPC, (2) the effect of the additional bond-slip in non-proprietary UHPC in relation to allowable deflection of the deck, and (3) the effect of fiber size on bond-slip behavior of reinforcing bar in UHPC.
The raw data supporting the conclusion of this article will be made available by the authors, without undue reservation.
AS: Data curation, Investigation, Methodology, Supervision, Writing–original draft. BA: Data curation, Methodology, Writing–review and editing. AE: Funding acquisition, Supervision, Writing–review and editing. MM: Supervision, Writing–review and editing.
The author(s) declare that no financial support was received for the research, authorship, and/or publication of this article.
The authors are thankful to Jared Cantrell, the laboratory manager at Idaho State University, for his help in the lab. The authors are also grateful to Pocatello Ready Mix and Cannon Builders for their generous material donations to complete this project.
Author AS was employed by Tindal Engineering Corporation. Author BA was employed by David Evans and Associates.
The remaining authors declare that the research was conducted in the absence of any commercial or financial relationships that could be construed as a potential conflict of interest.
All claims expressed in this article are solely those of the authors and do not necessarily represent those of their affiliated organizations, or those of the publisher, the editors and the reviewers. Any product that may be evaluated in this article, or claim that may be made by its manufacturer, is not guaranteed or endorsed by the publisher.
Aryal, B. (2022). Pullout behavior of steel reinforcing bars in ultra-high performance concrete for field cast connection of bridge precast decks (USA: Idaho State University, Pocatello, ID). MS Thesis.
ASTM (2017) Standard practice for fabricating and testing specimens of ultra-high performance concrete. West Conshohocken, PA: ASTM International.
ASTM (2020) “Standard test method for compressive strength of hydraulic cement Mortars using 2-in,” in Or [50-mm] cube specimens. West Conshohocken, PA: ASTM International.
ASTM Standard (2017). Standard test method for splitting tensile strength of cylindrical concrete specimens. Annu. Book ASTM Stand. 9.
ASTM Standard (2020) Standard specification for aggregate for Masonry mortar. West Conshohocken, PA: ASTM International.
Berry, M., Snidarich, R., and Wood, C. (2017). Development of non-proprietary ultra-high performance concrete: project summary report. Mont. Dept. Transp. Res. Programs.
Ebrahimpour, A., Mashal, M., Casanova, M., Rashique, U., Clauson, C., and Ali, S. (2018) Effectiveness of high-early strength concrete class 50AF with polypropylene fibers as a cost-effective alternative for field-cast connections of precast elements in accelerated bridge construction. Report No. FHWA-ID-16-246. Washington, DC: FHWA.
Ebrahimpour, A., Mashal, M., Clauson, C., and Ali, S. (2020) Field performance of HES class 50AF concrete with fibers as field-cast connection between Deck Bulb-T Girders in ABC applications. Washington, DC: FHWA. Report No. FHWA-ID-22-288.
El-Tawil, S., Tai, Y.-S., Meng, Bo, Hansen, W., and Liu, Z. (2018). Commercial production of non-proprietary ultra high performance concrete. Project summary report. Mich. Dep. Transp. Report No. RC-1670.
Graybeal, B. A. (2013) Development of non-proprietary ultra-high performance concrete for use in the highway bridge sector. Washington: FHWA.
Lutz, L. A., and Peter, G. (1967). Mechanics of bond and slip of deformed bars in concrete. ACI J., 711–721.
Mathey, R. G., and Watstein, D. (1961). Investigation of bond in beam and pull-out specimens with high-yield-strength deformed bars. Pap. read A. T. J. Proc.
Morcous, G., Hu, J., El-Khier, M. A., and Mendonca, F. (2020). Feasibility study of development of ultra-high performance concrete (UHPC) for highway bridge applications in Nebraska. Proj. Summ. Rep. Neb. Dep. Transp. Rep. No. SPR-P1 (18), M072.
Qiao, P., Zhou, Z., and Allena, S. (2016). Developing connections for longitudinal joints between deck Bulb tees – development of UHPC mixes with local materials. Wash. State Dep. Transp.
Rao, G. A., Pandurangan, K., Sultana, F., and Eligehausen, R. (2007). Studies on the pull-out strength of ribbed bars in high-strength concrete. Proc. FraMCoS- 6, 295–301.
Rashique, U., Ali, S., Ebrahimpour, A., and Mashal, M. (2022). Finite element modeling of longitudinal field-cast connections between precast deck bulb-T bridge girders. Struct. Eng. Int. 32 (3), 337–344. doi:10.1080/10168664.2020.1799730
Shao, Yi, and Billington, S. L. (2021). Bond performance of ultra-high-performance concrete (UHPC) under flexural states. Pap. read A. T. Proc. fib Symposium.
Shokrgozar, A. (2023) Bond strength behavior between non-proprietary UHPC and high strength precast concrete bridge components. Pocatello, ID: Idaho State University. Ph.D. Dissertation.
Wille, K., and Boisvert-Cotulio, C. (2013). Development of non-proprietary ultra-high performance concrete for use in the highway bridge sector: project summary report. Fed. Highw. Adm. Report No. FHWA-HRT-13-100.
Keywords: accelerated bridge construction (ABC), ultra high-performance concrete (UHPC), pullout test, closure pour, experimental tests
Citation: Shokrgozar A, Aryal B, Ebrahimpour A and Mashal M (2024) Bond-slip behavior of steel reinforcing bars in ultra-high performance concrete for field-cast connection of precast bridge decks. Front. Built Environ. 10:1354657. doi: 10.3389/fbuil.2024.1354657
Received: 12 December 2023; Accepted: 23 April 2024;
Published: 09 May 2024.
Edited by:
Jian Li, University of Kansas, United StatesReviewed by:
Ram Krishna Adhikari, University of Kansas, United StatesCopyright © 2024 Shokrgozar, Aryal, Ebrahimpour and Mashal. This is an open-access article distributed under the terms of the Creative Commons Attribution License (CC BY). The use, distribution or reproduction in other forums is permitted, provided the original author(s) and the copyright owner(s) are credited and that the original publication in this journal is cited, in accordance with accepted academic practice. No use, distribution or reproduction is permitted which does not comply with these terms.
*Correspondence: Ali Shokrgozar, YWxpc2hva3Jnb3phckBpc3UuZWR1
Disclaimer: All claims expressed in this article are solely those of the authors and do not necessarily represent those of their affiliated organizations, or those of the publisher, the editors and the reviewers. Any product that may be evaluated in this article or claim that may be made by its manufacturer is not guaranteed or endorsed by the publisher.
Research integrity at Frontiers
Learn more about the work of our research integrity team to safeguard the quality of each article we publish.