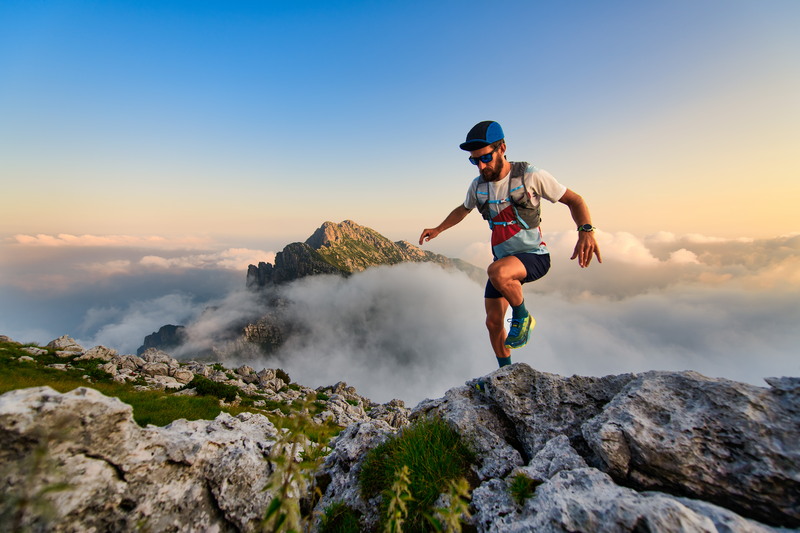
95% of researchers rate our articles as excellent or good
Learn more about the work of our research integrity team to safeguard the quality of each article we publish.
Find out more
HYPOTHESIS AND THEORY article
Front. Built Environ. , 23 June 2023
Sec. Construction Materials
Volume 9 - 2023 | https://doi.org/10.3389/fbuil.2023.1214788
This article is part of the Research Topic Additive Manufacturing in Construction View all 6 articles
Agricultural waste can be used in cement block production for a number of reasons, including its environmental, economic, and labor benefits. This study examines the mechanical, durability, and cost-effectiveness characteristics of cement blocks. A cement block made from agriculture waste promotes sustainable construction practices, since waste agriculture is often dumped in landfills and regarded as a waste material. Carbon dioxide (CO2) emissions produced by the construction sector, either from the firing of clay bricks or from the production of cement, contribute significantly to global warming. In many developing countries, air pollution from agricultural activities is primarily accounted for the emissions from agricultural machinery and openly burning agro-waste. Farming is one of the leading causes of water and soil pollution. Hence, adopting agricultural waste into cement production would significantly reduce the environmental impact of concrete structures. The goal of this research is to determine whether agricultural waste products, such as vermiculite, pistachio shells, sugarcane bagasse, and coconut husks, can be used to substitute sand in concrete blocks. The water absorption capacity of waste materials, density, flexural strength, fire resistance, and compressive strength of waste materials as admixtures in concrete were evaluated using experimental tests. In most cases, the concrete blocks made from agricultural waste were strong enough to satisfy ASTM standards. The specimens containing coconut husks and pistachio shells, among others, were found to be fairly strong and durable, even when isolating them from water.
The low cost and ease of construction of masonry-built houses have made it popular in developing countries. Furthermore, masonry structures have an appearance of long-term durability. Generally, masonry blocks are produced using a combination of cement and river sand. In the literature, it is evident that several additional cementitious materials have been used for sustainable construction materials production, including fly ash, waste glass powder, rice husk ash and metakaolin (Tayeh et al., 2021) (Sathvik et al., 2023). A rapid increase in the demand for river sand has occurred in many countries due to recent infrastructure developments. Due to its non-renewable nature, river sand supply cannot satisfy the increasing demand soon.
Managing crop residue is a major concern for farmers in India and all around the world, as they struggle to manage economic sustainability, adopt clean agriculture practices, and meet long-term production goals (Zhao et al., 2018). Ecological contamination is increasing alongside population growth because of waste creation and unrestricted use of raw resource (Rashad, 2016). Another source of pollution is the unrestricted use of agricultural resources. In particular, agricultural waste is dumped openly and is becoming a severe problem as open dumping harms both public health and degrades the whole environment. Instead of dumping them, agricultural waste products resulted to potentially be turned into valuable resources to limit their negative impacts on the environment (Loutou et al., 2019).
The need for fine aggregates is rapidly increasing in emerging countries, owing to the recent growth in the building sector. River sand is employed in various civil engineering projects. In India in 1992 the annual sand requirement of the construction industry was 9.4 × 106 m3. However, this amount has been underestimated because it covers only a portion of the country (Phonphuak et al., 2017). According to cement consumption and engineering calculations, the demand for sand was estimated to be 17.37 × 106 m3 in 2007. River sand is India’s most frequently adopted fine aggregate, and its over-exploitation to fulfill demand has had various negative repercussions (Zhao et al., 2018). The Mines and Minerals (Development and Regulation) Act of 1957 governs the development and regulation of mines and minerals (Taki et al., 2020), and the Sustainable Sand Mining Management Guidelines for 2016 of the Ministry of Environment, Food, and Climate Change regulate the exploration and mining of minerals. Keeping track of all sand mining and transportation licenses is the responsibility of the Indian Geological Survey and Mines Bureau. In light of the available statistics, it is estimated that the annual supply of sand is approximately 7.99 × 106 m3, which is significantly lower than the corresponding demand (Teimouri et al., 2019).
Several researchers have investigated the feasibility of using waste materials to produce masonry blocks owing to the exceeding abundance of waste materials and the lack of sand (Jittin et al., 2020). A viable solution to the environmental issue is to recycle waste materials and convert them into construction materials. Debris originating from construction, demolition, industry, and nature can be repurposed as building materials. By substituting fine aggregates with 89% building and demolition debris, concrete blocks with a compressive strength greater than 7 MPa can be produced (Phonphuak et al., 2016). In contrast, concrete blocks composed entirely of construction and demolition debris were reported to be more unstable than control blocks. Researchers have claimed that developing bricks containing lighter, more thermally efficient, and compressible waste will provide more cost-effective materials for constructing sustainable buildings. Numerous materials have been investigated for the manufacturing of masonry blocks and coal bottom ash, including granite sawing waste, waste marble powder, fly ash, glass powder, crumb rubber, cotton waste, paper mill waste, and cigarette butts (Munir et al., 2018). The report compared these different waste materials in terms of water absorption rate and compressive strength. The study also demonstrated the feasibility of using these materials as partial replacements for sand (Kazmi et al., 2018).
Previous research has employed different waste materials in masonry blocks (Kostrzewa-Demczuk et al., 2021), including tea waste in bricks, straw in clay, and sawdust in adobe. Concrete was prepared using rice husks instead of sand and gravel, whereas agricultural rice husks or rice husks treated with 5% lime solution were used. The results confirmed that concrete containing rice-husk is lightweight and has good insulating properties. Other industrial by-products were combined to create lightweight blocks, rice husks, and fly ash (Akinyemi et al., 2021). In addition to weighing approximately 1,100 kg/m3, the resulting blocks were thermal insulators, generating 0.20 W per meter (Zhang et al., 2020a). This research aims to provide a practical guide for the management of agriculture waste, utilize technology in their operations, and contribute to the development of a more sustainable and efficient construction industry. The following research objectives are addressed in this study:
O1 To determine whether agricultural waste can be partially substituted for sand in the production of cement blocks.
O2 Evaluation of the physical, mechanical, and thermal properties of cement blocks incorporating agricultural waste as a partial sand replacement.
O3 Analyze the environmental and structural impacts of substituting agricultural waste for sand in cement blocks.
O4 Analyze the environmental impact of using agricultural waste in cement blocks by conducting life cycle assessments and comparing them to traditional sand-based blocks.
O5 Examine the economic viability of using agricultural waste in cement blocks, considering the cost of materials, production, and potential market acceptance.
Several mechanical properties have been investigated for concrete containing coconut husk as a coarse aggregate, including flexural strength (Singh et al., 2018) (Javed et al., 2020), compressive strength, impact resistance, and splitting tensile strength. Coconut husk can be used as aggregates in lightweight concrete. In addition, such concrete’s final, binding strength is significantly greater than the theoretical bond strength. Furthermore, recent studies have indicated that coconut shell-reinforced concrete beams exhibit good flexural strength (Rashad, 2016). Moreover, lightweight coconut husk concrete beams exhibit the same flexural behavior as other types of lightweight concrete (Li et al., 2020b).
As a result, research and development efforts have increasingly focused on developing a sustainable replacement for river sand. Several municipal and industrial wastes are being used as river sand replacements, according to the existing literature (Bisht et al., 2020). These include construction and demolition wastes, fly ash, quarry dust, ash generated by red ceramic kilns, marble waste, recycled PET sand, and bottom ash. Several studies have demonstrated that construction materials containing industrial waste could meet the standards as a partial or full alternative to river sand (Debrah and Dinis, 2023). It is costly and requires a lot of energy to turn industrial waste into fine aggregate. Consequently, reusing present materials or substituting renewable materials for river sand are the focus of the new developments (Sandanayake et al., 2022).
Even though these waste materials could be used as fertilizers, insulation, or fuel, considerable percentages are disposed to avoid excessive accumulation (Li et al., 2020a). Previous investigations have shown that abundant plant waste in rural regions can be utilized to build less expensive structures (Journal and Scientific, 2014). More research is required on developing and using masonry blocks containing agricultural waste materials, particularly in their strength and longevity (Sutcu et al., 2019) (Kim et al., 2019). Furthermore, no studies have been conducted comparing different waste materials. Consequently, a suitable choice of the preferred waste material for concrete block preparation cannot be made.
The present research aims to partially identify the best agricultural waste sources for concrete block manufacturing and determine whether agricultural waste can partially substitute sand in concrete block manufacturing (Wu et al., 2021). Sand is replaced by sugarcane bagasse, vermiculite, pistachio shells, and coconut husks. The effects of these agricultural waste materials are evaluated in terms of density, water absorption rate, compressive strength, flexural strength, and durability of cinder blocks to get better results.
This paper is organized as follows. Materials and methods are explained in Section 2. Results of various tests carried out on different concrete block mixtures are explained in Section 3. Discussion of the results and comparison with previous studies is presented in Section 4. Finally, the concluding remarks are summarized in Section 5.
Materials used in this study were Portland cement grade 53, fine aggregate, vermiculite, pistachio shells, coconut husk, and sugarcane bagasse. These specimens were cast and tested for mechanical, alkaline, and acidic resistance properties. A thermal analysis was also conducted.
Concrete was constructed from ordinary Portland cement grade 53 as its cementitious component. Approximately 1,362 kg per cubic meter of cement and agriculture waste was shown in Figure 1, and its specific gravity was anticipated to be 3.15.
FIGURE 1. Agricultural wastes used in the study: (A) vermiculite, (B) coconut husk, (C) pistachio shells, and (D) sugarcane bagasse.
The cement’s chemical compositions and physical properties are listed in Table 1 (Pitarch et al., 2021) (Wong et al., 2018). Four types of agricultural waste present in India were selected: vermiculite, pistachio shells, sugarcane bagasse, and coconut husks, as shown in Figure 1. The vermiculite, coconut husks, and pistachio shells were not processed, whereas the sugarcane bagasse was crushed into 20 mm × 20 mm pieces using a mortar and pestle (Onochie and Balkis, 2021).
TABLE 1. Physical and chemical properties (Mohajerani et al., 2019).
Table 2 lists the physical characteristics of the solid waste utilized for concrete block manufacturing. The samples were collected using a screening process (Gładysz et al., 2018).
The blocks are comprised of agricultural river sand. Quartz sand is known as silica sand in bulk. The density and specific gravity of the sand were 1,476 kg/m3 and 2.67, respectively. Sieve analysis was performed to ensure that the local river sand complied with the American Society of Testing and Materials (ASTM) C136/C136M specifications. The analysis shows that the local river sand exhibited a fineness modulus of 3.43. The sand passed through a 4.75 mm sieve to a 75 µ sieve. When particle size ranges become narrower, the particle size distribution curve slopes steeper. According to the experimental results, the river sand used in this study was of poor quality (Yang et al., 2020). Figure 2 depicts the sieve analysis of the materials employed. Following ASTM C128, ASTM C29/C29M, and ASTM C136/C136M, the specific gravity, bulk density and fineness modulus may be calculated (Danso et al., 2015).
Synthesis of pistachio shell particles was carried out using the top-down method. At different intervals of time, coarse particles were ground into finer particles. The raw pistachio shells would need to be cleaned and dried. Then, the shells would be broken down into coarse particles using a mechanical process such as crushing or milling.
Nutshell particles were grounded into ultrafine powder by ball milling raw pistachio shell particles. This experiment involved the ball milling of an RFA sample without grinding aids, followed by grinding aids. Amine and chloride-based grinding aid were used to obtain the ultrafine particles. The pulverizer had three chambers to produce ultrafine particles, as shown in Figure 3. The technical details of the ultrafine pulverizer equipment are summarized in Table 3.
FIGURE 3. Ultrafine pulverizer equipment 1, 2, 3—Chambers, 4—Laser, 5–2 HP motor, 6—Digital indicator.
The samples were pulverized in a horizontal attrition laboratory pulverizer with a 440°C stainless steel dual cylinder model, as shown in Figure 4. The grinding media was composed of 20 kg stainless steel balls with Φ 12 mm and Φ 25 mm, as shown in Figure 5. A sample is collected at various grinding intervals and then stored in an airtight container for analysis. In this process, stainless steel cylinders and balls were used as an effective grinding media with low wear loss. The grinding efficiency is higher and has a long performance compared to the alumina and glass-based grinding media (Shah et al., 2022).
A particle size analyzer and Blaine’s fineness test were used to determine the size of the pistachio shell particles reduced during ball mill grinding. The ground pistachio shell particle having excellent particle was estimated at different micron sizes.
A Blaine’s fineness test was performed to determine the specific surfaces of the RFA sample and the ball mill grinding with varying grinding intervals of samples, as shown in Table 4. The materials were ground at 15, 30, 45, 60, 120, and 180-min intervals. The test results indicate that increasing the grinding time results in smaller particles. The grinding interval of 30, 60, 120, and 180 min of the sample gave 243%, 359%, 385%, and 394% higher fineness, respectively, compared with the samples. Similar results were found in a sample. The comparison of the samples after 120 min of grinding shows that samples produced more favorable results due to their natural grinding aid properties (Neves et al., 2022). Similar results in particle size reduction through Blaine’s fineness values were also obtained by Mo et al. (2018).
The sieve residue and Blaine’s fineness-specific surface area of ball-milled pistachio shell with and without different grinding aid results. The results demonstrated that the sieve residue gradually decreases more with an increase in the grinding times of GPS, AGPS, and CGPS samples compared with that of the RPS samples. The specific surface area increases gradually up to 120 min after reaching the saturation point. After 120 min percentage of the ground effect is minimum. A similar trend was observed by Vayghan et al. (2012). The percentage of sieve residue progressively decreases with an increase in the grinding period up to 120 min, which was identified as the inflection point. After the inflection point, the sieve residue increases due to particles’ agglomeration. A grinding aid improves the specific surface area and residue levels compared with RPS particles; the optimum grinding time was established at 120 min for ultrafine pistachio shells. This is discussed in the upcoming section (Asim et al., 2021).
Based on the volume of mold, the percentage of materials made in an appropriate quantity of the cement mix was selected. In light of the primary purpose of this study, i.e., evaluating the effectiveness of agricultural waste as partially substitutes for sand in concrete block manufacturing, the same mix proportions used in the above research were determined to be suitable and adequate for this study (Zong et al., 2014). Accordingly, a cement-to-sand volume ratio of 1:6 was employed in the control block, and blocks with four agricultural wastes were compared to this block (Wangqiang et al., 2019). The proportions of cement to sand to agricultural waste were 1:5:1-Mix 1 (M1), 1:4:2-Mix 2 (M2), and 1:3:3-Mix 3 (M3), respectively. As the proportion of agricultural waste increases in a given slump when cement blocks are made from agricultural waste, the ratio of water to cement increases accordingly. A high amount of water is required for the mortar mixture to flow because agricultural wastes have a high absorption capacity (Goel et al., 2018).
Moreover, the water consumption was comparable for the mortar mixes in which vermiculite and pistachio shells were added to the control mortar mix. This may be because these materials are less dense and absorb less water than the others. Similar findings were obtained by adding tobacco trash to concrete (Gupta et al., 2021) demonstrating a high-water requirement for a given slump value. This was because the increase in sugarcane bagasse made the mortar mix unusable. Adding sugarcane bagasse ash to concrete led to a similar discovery.
To ensure consistency in workability, the cement-to-water ratio was maintained at a slump value of 50 mm. Depending on the aggregate particle size and gradation and the amount of sugarcane bagasse in mortar, the amount of water varied depending on the requirement. Vermiculite mortars, coconut husk mortars, and pistachio shell mortars contained a cement-to-water ratio of 0.75–1.10 (Costa et al., 2020). On the contrary, cement mortar containing sawdust and sugarcane bagasse required significantly more water to achieve a 50 mm slump. Coconut husk and pistachio shell were found to adversely affect the workability of the mortar mix in this study (Zhang et al., 2020b).
Table 5 summarizes the mixtures of materials and water needed to produce a slump. A higher proportion of agricultural wastes in the mortar mixture changed the required amount of water for mortar production. When agricultural waste is added to cement mortar, the workability generally decreases (Lopes et al., 2011). Consequently, the mortar is compacted to an even greater degree. Water consumption increases when waste material is included in the set work process. Brick blocks were mixed and compressed by hand in the experimental software. The first step was measuring and combining the cement, sand, and waste items to produce a homogeneous mixture. After this, water was continuously added to the mixture until it became homogeneous. It took approximately 20–30 min to mix the mixture thoroughly. Based on the proportions indicated in The masonry blocks dimensions are 215, 105, and 65 mm were produced (Benli et al., 2020). The casting was showing in Figure 6.
The collection of samples included 400 blocks: 25 for the control blocks and 375 for the waste blocks. Each of the three mortar mixes like waste-type blocks (1:5:1, 1:4:2, and 1:3:3, respectively). Five cement blocks were used to determine the compressive and flexural strength for each mixing ratio, along with three cement blocks to determine the density, water absorption, acid attack resistance, and alkaline attack resistance for each mixing ratio, as shown in Figure 7 (Bergmann Becker et al., 2022).
By the Indian Standard IS 516 (1959), the compressive strength of the cement blocks was determined at 28 days of age. The testing was conducted using a universal machine operating at a 2 mm/min displacement rate. A load under the ultimate load was applied, and the strengths of all the agricultural waste materials in each of the three mixes were calculated (da Silva Araujo Filho et al., 2018).
As required by the Indian Standard IS 516 (1959), a three-point bending test was conducted to measure the tensile strength of the cement blocks. Placing cement blocks over the steel rods achieved a clear span of 175 mm, with the concentrated load applied at the midpoint of the span. Tests were conducted on a universal testing machine with displacement control at 2 mm per minute (Koksal et al., 2020b).
By ASTM C140, control mortar blocks and those containing agricultural wastes were weighted and measured to determine their density and water absorption. An oven at 100°C for 24 h was used to dry the cement blocks over 28 days. The specimens were held in the indoor laboratory setting until they reached room temperature. We removed the blocks from their submerged state, removed the surface water, and verified their weights (Mo et al., 2018).
The water absorption rate is given by
For the alkaline resistance test, the specimens were immersed in 3% NaOH solution for 30 days, whereas, for the acid resistance test, the specimens were immersed in 3% H2SO4 solution for 60 days. These are the standard procedures described in ASTM C289-07 and ASTM C1152M-04. Using Eq. 2, the weight loss after immersion was calculated by weighing the specimens before and after immersion (Bari et al., 2021):
Waste from the coconut industry, including husks, shells, and fibers, is one of the most readily available byproducts. This material has several inherent properties that make it an attractive candidate for potential use in construction materials, including a high level of lignocellulosic content, a low density, and fibrous structure. The fiber content in coconut waste can explain the superior strength of cement blocks containing coconut waste. Among their many advantages, fibers are highly effective at adhering to cement matrices, creating a network that enhances tensile strength and prevents cracking. Essentially, these fibers serve as reinforcements that distribute stresses and prevent crack propagation, enhancing the overall stability of the blocks. Particle packing and porous filling in the cement matrix are facilitated by the irregular shapes and sizes of coconut waste particles. Because coconut waste particles are irregular, they efficiently fill the spaces between cement grains, increasing density and reducing porosity. By increasing the density of the blocks, it is possible to make them more robust and less susceptible to external forces due to the increased compressive strength. The pozzolanic reaction can occur when calcium hydroxide, which is present in cement, is combined with organic compounds present in coconut waste, including lignin and cellulose. A calcium silicate hydrate gel, which is generated during this reaction, fills the pores, and improves the interlocking of cement particles because of this reaction. A C-S-H gel is formed during the cementing process, which strengthens the cement matrix, enhances its binding properties, and results in a higher strength.
Numerous factors affect concrete density, including the specific gravity, cement-to-water ratio and quantity of sand used, amount of waste material replaced, and amount of water absorbed. Based on this study’s findings, density decreases in all cases where agricultural wastes are included because agricultural wastes have a high unit weight and low specific gravity. Based on the dry density of cement blocks containing varying proportions of waste material, as illustrated in Figure 8, the blocks were classified by the ASTM specifications. Table 6 summarizes the weights of the cement blocks and whether they are light- or medium-weight. The dry densities of the control blocks are virtually identical to those of the standard weight categories. Cement blocks with ratios of 1:3:3 and 1:4:2 for each waste material are classified as lightweight blocks (Muñoz et al., 2020).
Most structural components in modern society (i.e., masonry units) do not carry loads. ASTM specified a minimum requirement of 4.14 MPa of compressive strength for assessing cement blocks based on an average of three samples. In contrast, the Indian standard specifies a minimum compressive strength value of 1.3 MPa based on the average of three specimens (Reis et al., 2020).
Several factors determine the compressive strength of a concrete mix, including the matrix strength, the strength of the agriculture sample, the cement concentration, and the proportion of water in cement. Several researchers have reported that replacing aggregates with agricultural waste materials decreased the compressive strength in each trial (Santiago-De la Rosa et al., 2017). The compressive strength of concrete decreased by 24% when 15% of coarse aggregates were replaced with pistachio shells. Similar results were reported when periwinkle shells were used as the waste material (Iwaro et al., 2017). Even though farm waste was used instead of coarse aggregates in those studies, concrete containing agricultural waste exhibited less strength than the control concrete (Tomassetti et al., 2020).
In one experiment, pistachio shells were used to replace fine aggregates with a mix ratio of 1:2:3, resulting in a decrease of concrete strength by 49% and 64% when 25% and 50% of the sand was replaced with pistachio shell, respectively. The strength of mortar with cork as a fine aggregate decreased by 34% and 69%, respectively. These results are consistent with those obtained in previous work (Wang et al., 2022).
Figure 9 displays a concrete block compression test program to demonstrate the compressive strength of cement blocks. The results of this study indicate that the type of waste used and the percentage of replacement significantly affect the cement blocks’ compressive strength. As the waste content of the block increased, its compressive strength decreased. This may be because the proportion of water to cement in the mortar with agricultural materials added is more significant than that in the reference mortar, in addition to the fact that agricultural residue has a considerably lower mechanical resistance than sand (Mashaly et al., 2016) (Liberalesso et al., 2021) (Karatas et al., 2019). Moreover, agricultural waste has a lower density than the river sand, which may decrease the compressive strength, as shown in Figure 10. The coconut cement blocks have incredible compressive strengths over those containing sugarcane bagasse, as coconut husk is denser than other agricultural waste materials (Onesippe Potiron et al., 2022).
Meanwhile, straw yields the lowest compressive strength among agricultural waste materials. The ASTM C129 specifies minimum requirements for most cement blocks, except those with a 1:3:3 mix ratio. When the mix ratio is 1:3:3, the cement block is by ASTM C129 specifications. However, four cement blocks, apart from those containing coconut husk in a 1:3:3 ratio, satisfy the standard when the arithmetic mean of their density is used. To calculate normalized power, a control block was utilized as a reference. It is estimated that each mixture of coconut husk, rice husks, vermiculite and pistachio shells has at least 50% of the compressive strength of a cement block (Gencel et al., 2021).
The ability of a block to withstand flexural loads can be estimated by measuring flexural stress. As a rule, fractures occur on the tensile side of the block, which lies closest to the center of the cross-section. Figure 10 illustrates the flexural strength of the cement blocks. It can be observed that the flexural strength decreases as waste material content increases. Several factors, including the type, particle size, and density of the waste material to be recycled, in conjunction with the moisture content of the cement mortar, determine the flexural strength. Similarly, agricultural material’s compressive and flexural strength decreased (Brooks et al., 2020).
Pistachio shells were also utilized, and it was recognized that decreasing their effective binding would decrease the flexural strength. When oil palm shells were used as coarse aggregates, the concrete lost 39% of its compressive strength compared to the control concrete at 30%. The findings are consistent with those obtained by adding coconut husk to the cement mortar. Using cork as fine aggregate in mortar as a test material, flexural strength decreased by 23% and 46% at 20% and 50%, respectively, compared with the control hardened mortar. The type of waste was considered in this experiment. Cement blocks containing coconut husk have higher flexural strength than those containing sugarcane bagasse (Zhan et al., 2021).
The experimental results were evaluated using linear regression to generate a proportionality equation relating the cement blocks’ flexural strength (ft) to their compressive strength (fcu) in the conventional form ft = a fcub. Eq. 3, associated with a coefficient of termination (R2) of 0.89, relates the flexural strength of cement blocks to their compressive strength, and the flexural strength of the cement blocks was calculated using this equation (Koksal et al., 2020a):
The standard error for Eq. 3 is calculated to be 0.03 MPa, indicating that the proposed equation can describe the experimental data.
Concrete blocks can absorb water based on the configuration of their pores. Porous cement blocks are vulnerable to water and chemicals. The main disadvantage of using waste material as a sand substitute in cement blocks is that it absorbs a large amount of water. The water absorption rate of a cement block containing waste material is generally significantly higher than that of a control cement block. A previous study revealed that agricultural waste could be substituted for fine or coarse pebbles to increase water absorption. When oil palm shells were combined with coconut shells as coarse aggregates, water absorption increased substantially. In addition, cement mortar’s water absorption capacity depended on the agricultural waste’s water absorption capacity. The same observation revealed that substituting discarded oyster shell sand increased the absorption rate by 1.1%–1.6% compared to control concrete (Fiala et al., 2020).
Except for the coconut husk in all mix proportions, the water absorption rate tended to increase when waste materials were added. The coconut husk blocks absorbed water at approximately the same rate in all mix proportions and a rate less than the control blocks. The lack of bulk density of agricultural waste could also explain the absence of solid materials in the mortar mix (Naveen Kumar et al., 2020).
As shown in Figure 11, each sample mix absorbs water at a different rate. According to ASTM C55-11, tile can absorb water at 208, 240 kg/m3 for medium-weight masonry blocks, and 320 kg/m3 for lightweight masonry blocks. It is found that blocks consisting of rice husk, sawdust, and straw in the proportions of 1:3:3, as well as straw in all mix proportions, have water absorption rates greater than the specified value. This finding suggests that blocks containing rice husk, sawdust, and straw are more susceptible to external agent penetration than blocks containing pistachio shells and coconut husk (Mohajerani et al., 2019).
Figure 12 illustrates how an acid attack decreases the densities of the control and agricultural waste blocks. Based on the data, the density decreases as agricultural waste increases after 30 and 60 days. As a result of the inclusion of sugarcane bagasse in cement blocks, the density of the blocks decreases dramatically by 200 kg per cubic meter after 60 days, as opposed to the control blocks dropping by only 40 kg per cubic meter. It has also been observed that cement blocks reinforced with rice husks, sawdust, and pistachio shells display a decrease in density of up to 120 kg/m3 after 60 days. Conversely, the cement blocks containing coconut husk exhibit a density loss of 40–80 kg/m3, which is modest and close to the control block (Goel and Kalamdhad, 2018).
According to Figure 13, an alkaline attack results in a decrease in the density of control blocks and agricultural waste blocks. The density of the agricultural waste decreases with increased exposure for 30 and 60 days. The cement blocks containing coconut husks, vermiculite, and sugarcane bagasse exhibit a density loss of 150 kg/m3 after 60 days, in contrast to 75 kg/m3 for the control block. Meanwhile, the cement blocks with coconut husk display a density loss of 40–70 kg/m3, which may be considered modest and close to the control block (Rabello and Carlos da Conceição Ribeiro, 2021).
It is possible to use the Pearson correlation coefficient to test the relationship between physical parameters, such as density, strength, and flexibility, and durability characteristics, such as wettability, acid-propelling properties, and alkaline resistance. Table 7 presents the Pearson coefficients for the parametric correlations, and significant values (two-tailed) are indicated in square brackets. In addition to the positive correlation of agricultural waste with dry density (i.e., the fact that the dry density decreases when agricultural waste is taken into consideration), it is also significant that agricultural waste has positive correlations with bending strength, resistance to acid attacks, resistance to alkali attacks, and compressive strength. Agricultural waste addition benefits density but not strength or durability, as shown in Figure 14 (Sevinç and Durgun, 2021).
In this section, we discuss the effects of direct flame on specimens of different blends. Concrete structures can be affected by fire or another source of heat. Figure 15 shows the means of igniting the test fire.
For example, performed a similar test to (Abdel-Gawwad et al., 2020). Its flame tool, however, differed slightly from that of to approximate the actual behavior. The test used 12 samples with dimensions of 100 mm × 100 mm × 100 mm. Two cubes represented each replacement ratio. As shown in Figure 16, the specimen showed two distinct forms before and after burning for 300 s. A high level of combustibility is found in the mixes containing agricultural wastes, as shown in Figure 16 (Figures 16A–F). Comparing the fire resistance of the reference sample to other samples provided a high rating. The results of testing of samples indicate that water vapor and filtration of water are observed in the presence of M1, M2, and M3 mixtures. None of the other mixtures has been filtered or evaporated indicates that these mixes have a high permeability.
FIGURE 16. (A) M1 specimen forms before and after. (B) M2 specimen forms before and after. (C) M3 specimen forms before and after. (D) C1 specimen forms before and after. (E) CM1 specimen forms before and after. (F) S1 Specimen forms before and after the test.
As a result of being exposed to direct flame, cracks appeared on that surface and the adjacent surface. Cracks appeared irregularly, while the adjacent samples showed random cracks. Due to the burning of the specimen on the surface, it was impossible to detect cracks in the other samples. Figure 17 illustrates cracked surfaces after testing.
Near the direct flame surface, tiny bubbles of the specimen were formed. Replacement ratios of 30%, 40%, and 50% were all affected by this condition. Reference samples passed heat more rapidly than others. The opposite of the direct flame caused these samples to change condition when transferred and touched. The temperature difference between the reference samples and the other mixes was more significant, which were not treated and had been exposed to less heat during and after testing. As a result of agricultural combustion, toxic white smoke was emitted at 30%, 40%, and 50% replacement ratios. Figure 17 illustrates the same behavior noted by other authors—smoke rises from the samples.
This study aimed to quantify sample usage for block construction. The impact of agricultural waste on mortar consumption could be determined by estimating the amount of mortar required for each cement block case. The material consumption was determined using the quantities of sand and cement required and the total cost per 1,000 cement blocks, as shown in Figure 18. In addition, values of INR 920 (USD 5.98) for 50 kg bags of cement, INR 13920 (USD 90.53) for 1 m3 sand, and INR 157 (USD 1.02) for aggregate transport per cubic meter per kilometer were utilized in the cost calculations (Zhan et al., 2021).
The total cost was determined by factoring in 10% material waste and labor costs at the unskilled labor pay rate for building activity. The costs associated with waste material processing were not included in the computations. When one-sixth of the sand was replaced with agricultural waste, the mortar cost was reduced by 10%, while when a third of the sand was substituted, the cost decreased by 20%–30%. Because cement makes up approximately 50% of the cost of construction materials, an increase in agricultural production does not necessarily lead to an increase in overall construction costs (Schiavoni et al., 2016).
Researchers have discovered that when concrete blocks are realized with additional agricultural waste materials, the strength of the blocks is usually reduced. By ASTM standards, blocks should have a minimum compressive strength of 4.12 MPa. Considering this limit, cement blocks containing agricultural waste at a ratio of 1:3:3 are unlikely to be advantageous for building construction. According to Indian standards, wall blocks with no load-bearing capability can have a compressive strength of 1.3 MPa. Therefore, all the tested bricks are suitable for non-load bearing structures or low-story buildings (Mo et al., 2018).
Cement blocks containing agricultural waste satisfy the flexural strength standards, but durability is a primary concern (Onesippe Potiron et al., 2022). Additionally, cement blocks containing significant agricultural waste exhibit deterioration in form and appearance. For instance, the cement block appears uneven because of the large amount of agricultural waste on its surface. Buildings constructed from cement blocks containing coconut husk, vermiculite, and sugarcane bagasse would have an ugly appearance and applying joint mortar and surface plaster would be challenging (Seddik Hassan et al., 2022).
An analysis of the energy requirements and CO2 emissions of the production of a unit volume of mortar was conducted to assess the environmental benefits associated with the use of agriculture waste in cement-sand blocks. In the production of hardened mortar, the embodied energy was calculated as 4.5, 0.081, and 0.01 MJ for 1 kg of cement, sand, and water, respectively, with carbon dioxide emissions calculated as 0.73, 0.0048, and 0.001 kg. In calculating the energy embodied and carbon emissions for coco shell, we considered the agriculture waste as waste from the coconut fiber extraction process.
Concrete blocks containing agricultural waste have many benefits over conventional cement blocks, including a lower cost, lower density, and higher porosity. Due to the lower weight of the cement blocks, the construction process can be faster, and labor costs can be reduced by incorporating agricultural waste. Furthermore, cement blocks with higher porosity have lower heat conductivity, thus increasing the building’s insulation properties (Iwaro and Mwasha, 2019).
The purpose of this study was to assess the properties of different agricultural wastes used in concrete blocks as sand substitutes in rural areas of India. Several experimental tests on various aspects (durability, flexural and compression tests, fire resistance, and acidity resistance) were conducted to determine which waste materials would be most appropriate for the construction of sustainable buildings. Vermiculite, coconut husks, pistachio shells, and sugarcane bagasse were utilized as sand substitutes. The following conclusions can be drawn from the experimental findings:
The compressive and flexural strength of agricultural waste blocks is lower than that of cement blocks containing 6% sand and 1% cement. Many cement blocks containing agricultural waste, except those containing powder, meet the ASTM minimum strength requirements.
White smoke samples displayed malodorous and toxic characteristics, with a replacement ratio of 30% or greater. Although sugarcane specimens may be used for external work, they are not recommended for internal work due to their poor fire-resistant behavior, except if the specimens are coated with insulating materials. The fire behavior test also revealed that the agricultural waste brick had a greater degree of permeability than the standard concrete.
Alkaline and acid resistance of cement blocks containing coconut husks and pistachio shells was comparable to that of the control blocks. A 60-day exposure to acidic or alkaline solutions led to a substantial decrease in the density of cement blocks containing coconut husk and husk-composite cement blocks as compared to the control blocks. A sustainable approach is taken in this study by using agricultural wastes in the manufacture of blocks in order to conserve resources and convert by-products into valuable products.
Despite meeting the ASTM C55-11 strength criterion, agricultural waste cement blocks do not meet ASTM C55-11 durability requirements. The cement blocks containing coconut husks and pistachio shells demonstrated acceptable strength and durability. Low-strength cement blocks are therefore suitable for use in building construction. These cement blocks will be suitable for use in housing projects in the building sector after additional studies have been conducted on their long-term durability.
The durability of the material has been evaluated only in terms of compression and flexural strength, as well as acid and alkaline resistance. Further research will be conducted to evaluate additional mechanical characteristics and durability of cement blocks containing agricultural waste.
The original contributions presented in the study are included in the article/Supplementary Material, further inquiries can be directed to the corresponding author.
SM: Conceptualization, Data curation, Formal analysis, Writing—original draft. PS: Writing revision, editing, supervision, data analysis and conceptualization. AK: Writing-review and editing, Formatting, Finalize draft. SS: Supervision, AR: Writing-review and editing. LK: Writing-review and editing. VL: Writing—review and editing. VL: Writing-review and editing. All authors contributed to the article and approved the submitted version.
The authors declare that the research was conducted in the absence of any commercial or financial relationships that could be construed as a potential conflict of interest.
All claims expressed in this article are solely those of the authors and do not necessarily represent those of their affiliated organizations, or those of the publisher, the editors and the reviewers. Any product that may be evaluated in this article, or claim that may be made by its manufacturer, is not guaranteed or endorsed by the publisher.
Asim, N., Badiei, M., Torkashvand, M., Mohammad, M., Alghoul, M. A., Gasaymeh, S. S., et al. (2021). Wastes from the petroleum industries as sustainable resource materials in construction sectors: Opportunities, limitations, and directions. J. Clean. Prod. 284, 125459. doi:10.1016/j.jclepro.2020.125459
Abdel-Gawwad, H. A., Sanad, S. A., and Mohammed, M. S. (2020). A clean approach through sustainable utilization of cement kiln dust, hazardous lead-bearing, and sewage sludges in the production of lightweight bricks. J. Clean. Prod. 273, 123129. doi:10.1016/j.jclepro.2020.123129
Akinyemi, B. A., Orogbade, B. O., and Okoro, C. W. (2021). The potential of calcium carbide waste and termite mound soil as materials in the production of unfired clay bricks. J. Clean. Prod. 279, 123693. doi:10.1016/j.jclepro.2020.123693
Bari, H., Salam, M. A., and Safiuddin, M. (2021). Fresh and hardened properties of brick aggregate concrete including coconut shell as a partial replacement of coarse aggregate. Constr. Build. Mater 297, 123745. doi:10.1016/j.conbuildmat.2021.123745
Benli, A., Karatas, M., and Anil Toprak, H. (2020). Mechanical characteristics of self-compacting mortars with raw and expanded vermiculite as partial cement replacement at elevated temperatures. Constr. Build. Mater 239, 117895. doi:10.1016/j.conbuildmat.2019.117895
Bergmann Becker, P. F., Effting, C., and Schackow, A. (2022). Lightweight thermal insulating coating mortars with aerogel, EPS, and vermiculite for energy conservation in buildings. Cem. Concr. Compos 125, 104283. doi:10.1016/j.cemconcomp.2021.104283
Bisht, K., Kabeer, K. I. S. A., and Ramana, P. V. (2020). Gainful utilization of waste glass for production of sulphuric acid resistance concrete. Constr. Build. Mater 235, 117486. doi:10.1016/j.conbuildmat.2019.117486
Brooks, A. L., Shen, Z., and Zhou, H. (2020). Development of a high-temperature inorganic synthetic foam with recycled fly-ash cenospheres for thermal insulation brick manufacturing. J. Clean. Prod. 246, 118748. doi:10.1016/j.jclepro.2019.118748
Costa, J. A. C., Martinelli, A. E., do Nascimento, R. M., and Mendes, A. M. (2020). Microstructural design and thermal characterization of composite diatomite-vermiculite paraffin-based form-stable PCM for cementitious mortars. Constr. Build. Mater 232, 117167. doi:10.1016/j.conbuildmat.2019.117167
da Silva Araujo Filho, R. G., de Oliveira Freitas, J. C., de Freitas Melo, M. A., and Braga, R. M. (2018). Lightweight oil well cement slurry modified with vermiculite and colloidal silicon. Constr. Build. Mater 166, 908–915. doi:10.1016/j.conbuildmat.2017.12.243
Danso, H., Martinson, D. B., Ali, M., and Williams, J. B. (2015). Physical, mechanical and durability properties of soil building blocks reinforced with natural fibres. Constr. Build. Mater 101, 797–809. doi:10.1016/j.conbuildmat.2015.10.069
Debrah, J. K., and Dinis, M. A. P. (2023). Chemical characteristics of bottom ash from biomedical waste incinerators in Ghana. Environ. Monit. Assess. 195, 568. doi:10.1007/s10661-023-11132-w
Fiala, L., Konrád, P., Fořt, J., Keppert, M., and Černý, R. (2020). Application of ceramic waste in brick blocks with enhanced acoustic properties. J. Clean. Prod. 261, 121185. doi:10.1016/j.jclepro.2020.121185
Gencel, O., Sarı, A., Ustaoglu, A., Hekimoglu, G., Erdogmus, E., Yaras, A., et al. (2021). Eco-friendly building materials containing micronized expanded vermiculite and phase change material for solar based thermo-regulation applications. Constr. Build. Mater 308, 125062. doi:10.1016/j.conbuildmat.2021.125062
Gładysz, P., Stanek, W., Czarnowska, L., Sładek, S., and Szlęk, A. (2018). Thermo-ecological evaluation of an integrated MILD oxy-fuel combustion power plant with CO2 capture, utilisation, and storage – a case study in Poland. Energy 144, 379–392. doi:10.1016/j.energy.2017.11.133
Goel, G., and Kalamdhad, A. S. (2018). A practical proposal for utilisation of water hyacinth: Recycling in fired bricks. J. Clean. Prod. 190, 261–271. doi:10.1016/j.jclepro.2018.04.179
Goel, G., Kalamdhad, A. S., and Agrawal, A. (2018). Parameter optimisation for producing fired bricks using organic solid wastes. J. Clean. Prod. 205, 836–844. doi:10.1016/j.jclepro.2018.09.116
Gupta, V., Siddique, S., and Chaudhary, S. (2021). Optimum mixing sequence and moisture content for hydrated lime fly ash bricks. J. Clean. Prod. 285, 124859. doi:10.1016/j.jclepro.2020.124859
Iwaro, J., and Mwasha, A. (2019). Effects of using coconut fiber–insulated masonry walls to achieve energy efficiency and thermal comfort in residential dwellings. J. Archit. Eng. 25, 04019001. doi:10.1061/(asce)ae.1943-5568.0000341
Iwaro, J., Mwasha, A., Vayghan, A. G., et al. (2017). Energy efficiency and thermal comfort in historic buildings: A review. Renew. Sustain Energy Rev. 144, 9491–9532. doi:10.1016/j.scs.2016.02.013
Javed, U., Khushnood, R. A., Memon, S. A., Jalal, F. E., and Zafar, M. S. (2020). Sustainable incorporation of lime-bentonite clay composite for production of ecofriendly bricks. J. Clean. Prod. 263, 121469. doi:10.1016/j.jclepro.2020.121469
Jittin, V., Bahurudeen, A., and Ajinkya, S. D. (2020). Utilisation of rice husk ash for cleaner production of different construction products. J. Clean. Prod. 263, 121578. doi:10.1016/j.jclepro.2020.121578
Journal, I., and Scientific, O. F. (2014). Reuse of natural waste material for making light weight bricks. Int. J. Sci. Technol. Res. 3, 49–53.
Karatas, M., Benli, A., and Toprak, H. A. (2019). Effect of incorporation of raw vermiculite as partial sand replacement on the properties of self-compacting mortars at elevated temperature. Constr. Build. Mater 221, 163–176. doi:10.1016/j.conbuildmat.2019.06.077
Kazmi, S. M. S., Munir, M. J., Wu, Y. F., Hanif, A., and Patnaikuni, I. (2018). Thermal performance evaluation of eco-friendly bricks incorporating waste glass sludge. J. Clean. Prod. 172, 1867–1880. doi:10.1016/j.jclepro.2017.11.255
Kim, Y., Lee, Y., Kim, M., and Park, H. (2019). Preparation of high porosity bricks by utilizing red mud and mine tailing. J. Clean. Prod. 207, 490–497. doi:10.1016/j.jclepro.2018.10.044
Koksal, F., Mutluay, E., and Gencel, O. (2020a). Characteristics of isolation mortars produced with expanded vermiculite and waste expanded polystyrene. Constr. Build. Mater 236, 117789. doi:10.1016/j.conbuildmat.2019.117789
Koksal, F., Sahin, Y., and Gencel, O. (2020b). Influence of expanded vermiculite powder and silica fume on properties of foam concretes. Constr. Build. Mater 257, 119547. doi:10.1016/j.conbuildmat.2020.119547
Kostrzewa-Demczuk, P., Stepien, A., Dachowski, R., and Krugiełka, A. (2021). The use of basalt powder in autoclaved brick as a method of production waste management. J. Clean. Prod. 320, 128900. doi:10.1016/j.jclepro.2021.128900
Li, L. G., Lin, Z. H., Chen, G. M., and Kwan, A. K. H. (2020a). Reutilizing clay brick dust as paste substitution to produce environment-friendly durable mortar. J. Clean. Prod. 274, 122787–122811. doi:10.1016/j.jclepro.2020.122787
Li, Z., Wu, J., Yue, X., Qiu, F., Yang, D., and Zhang, T. (2020b). Study on the application of waste bricks in emulsified oil-water separation. J. Clean. Prod. 251, 119609. doi:10.1016/j.jclepro.2019.119609
Liberalesso, T., Tassi, R., Ceconi, D. E., Allasia, D. G., and Arboit, N. K. S. (2021). Effect of rice husk addition on the physicochemical and hydrological properties on green roof substrates under subtropical climate conditions. J. Clean. Prod. 315, 128133. doi:10.1016/j.jclepro.2021.128133
Lopes, C., Herva, M., Franco-Uría, A., and Roca, E. (2011). Inventory of heavy metal content in organic waste applied as fertilizer in agriculture: Evaluating the risk of transfer into the food chain. Environ. Sci. Pollut. Res. 18, 918–939. doi:10.1007/s11356-011-0444-1
Loutou, M., Taha, Y., Benzaazoua, M., Daafi, Y., and Hakkou, R. (2019). Valorization of clay by-product from moroccan phosphate mines for the production of fired bricks. J. Clean. Prod. 229, 169–179. doi:10.1016/j.jclepro.2019.05.003
Mashaly, A. O., El-Kaliouby, B. A., Shalaby, B. N., El – Gohary, A. M., and Rashwan, M. A. (2016). Effects of marble sludge incorporation on the properties of cement composites and concrete paving blocks. J. Clean. Prod. 112, 731–741. doi:10.1016/j.jclepro.2015.07.023
Mo, K. H., Lee, H. J., Liu, M. Y. J., and Ling, T. C. (2018). Incorporation of expanded vermiculite lightweight aggregate in cement mortar. Constr. Build. Mater 179, 302–306. doi:10.1016/j.conbuildmat.2018.05.219
Mohajerani, A., Hui, S. Q., Mirzababaei, M., Arulrajah, A., Horpibulsuk, S., Abdul Kadir, A., et al. (2019). Amazing types, properties, and applications of fibres in construction materials. Mater. (Basel) 12, 2513–2545. doi:10.3390/ma12162513
Munir, M. J., Kazmi, S. M. S., Wu, Y. F., Hanif, A., and Khan, M. U. A. (2018). Thermally efficient fired clay bricks incorporating waste marble sludge: An industrial-scale study. J. Clean. Prod. 174, 1122–1135. doi:10.1016/j.jclepro.2017.11.060
Muñoz, P., Letelier, V., Zamora, D., and Morales, M. P. (2020). Feasibility of using paper pulp residues into fired clay bricks. J. Clean. Prod. 262, 121464. doi:10.1016/j.jclepro.2020.121464
Naveen Kumar, K., Vijayan, D. S., Divahar, R., Abirami, R., and Nivetha, C. (2020). An experimental investigation on light-weight concrete blocks using vermiculite. Mater Today Proc. 22, 987–991. doi:10.1016/j.matpr.2019.11.237
Neves, H. S. de C., da Silva, T. L., da Silva, M. G. C., Guirardello, R., and Vieira, M. G. A. (2022). Ion exchange and adsorption of cadmium from aqueous media in sodium-modified expanded vermiculite. Environ. Sci. Pollut. Res. 29, 79903–79919. doi:10.1007/s11356-021-16841-8
Onesippe Potiron, C., Bilba, K., Ratiarisoa, R. V., Savastano Junior, H., and Arsene, M. A. (2022). Enhancement of the reactivity of sugarcane bagasse ash for Pozzolan-Lime Paste: Effect of particle size. Constr. Build. Mater 350, 128561. doi:10.1016/j.conbuildmat.2022.128561
Onochie, K. K., and Balkis, A. P. (2021). Polypropylene fiber reinforced Alker as a structurally stable and sustainable building material. J. Clean. Prod. 279, 123600. doi:10.1016/j.jclepro.2020.123600
Phonphuak, N., Kanyakam, S., and Chindaprasirt, P. (2016). Utilization of waste glass to enhance physical-mechanical properties of fired clay brick. J. Clean. Prod. 112, 3057–3062. doi:10.1016/j.jclepro.2015.10.084
Pitarch, A. M., Reig, L., Tomás, A. E., Forcada, G., Soriano, L., Borrachero, M., et al. (2021). Pozzolanic activity of tiles, bricks and ceramic sanitary-ware in eco-friendly Portland blended cements. J. Clean. Prod. 279, 123713. doi:10.1016/j.jclepro.2020.123713
Rabello, L. G., and Carlos da Conceição Ribeiro, R. (2021). A novel vermiculite/vegetable polyurethane resin-composite for thermal insulation eco-brick production. Compos Part B Eng. 221, 109035. doi:10.1016/j.compositesb.2021.109035
Rashad, A. M. (2016). Vermiculite as a construction material – a short guide for Civil Engineer. Constr. Build. Mater 125, 53–62. doi:10.1016/j.conbuildmat.2016.08.019
Reis, G. S., Cazacliu, B. G., Cothenet, A., Poullain, P., Wilhelm, M., Sampaio, C. H., et al. (2020). Fabrication, microstructure, and properties of fired clay bricks using construction and demolition waste sludge as the main additive. J. Clean. Prod. 258, 120733. doi:10.1016/j.jclepro.2020.120733
Sandanayake, M., Bouras, Y., and Vrcelj, Z. (2022). A feasibility study of using coffee cup waste as a building material - life cycle assessment and multi-objective optimisation. J. Clean. Prod. 339, 130498. doi:10.1016/j.jclepro.2022.130498
Santiago-De la Rosa, N., Mugica-Álvarez, V., Cereceda-Balic, F., Guerrero, F., Yáñez, K., and Lapuerta, M. (2017). Emission factors from different burning stages of agriculture wastes in Mexico. Environ. Sci. Pollut. Res. 24, 24297–24310. doi:10.1007/s11356-017-0049-4
Sathvik, S., Shakor, P., Hasan, S., Awuzie, B. O., Singh, A. K., Rauniyar, A., et al. (2023). Evaluating the potential of geopolymer concrete as a sustainable alternative for thin white-topping pavement. Front. Mater. 10, 1181474. doi:10.3389/fmats.2023.1181474
Schiavoni, S., D’Alessandro, F., Bianchi, F., and Asdrubali, F. (2016). Insulation materials for the building sector: A review and comparative analysis. Renew. Sustain Energy Rev. 62, 988–1011. doi:10.1016/j.rser.2016.05.045
Seddik Hassan, A. M., Aly, R. M. H., Alzahrani, A. M. Y., Abd El-razik, M. M., and Shoukry, H. (2022). Improving fire resistance and energy performance of fast buildings made of hollow polypropylene blocks. J. Build. Eng. 46, 103830. doi:10.1016/j.jobe.2021.103830
Sevinç, A. H., and Durgun, M. Y. (2021). A novel epoxy-based composite with eggshell, PVC sawdust, wood sawdust and vermiculite: An investigation on radiation absorption and various engineering properties. Constr. Build. Mater 300, 123985. doi:10.1016/j.conbuildmat.2021.123985
Shah, M. I., Zakari, A., Kumar, S., Abbas, S., and Sheraz, M. (2022). Quantifying the effect of waste on soil health in European union: What are the roles of technology, natural capital, and institutional quality? Environ. Sci. Pollut. Res. 29, 73227–73240. doi:10.1007/s11356-022-20909-4
Singh, S. K., Kulkarni, S., Kumar, V., and Vashistha, P. (2018). Sustainable utilization of deinking paper mill sludge for the manufacture of building bricks. J. Clean. Prod. 204, 321–333. doi:10.1016/j.jclepro.2018.09.028
Sutcu, M., Erdogmus, E., Gencel, O., Gholampour, A., Atan, E., and Ozbakkaloglu, T. (2019). Recycling of bottom ash and fly ash wastes in eco-friendly clay brick production. J. Clean. Prod. 233, 753–764. doi:10.1016/j.jclepro.2019.06.017
Taki, K., Gahlot, R., and Kumar, M. (2020). Utilization of fly ash amended sewage sludge as brick for sustainable building material with special emphasis on dimensional effect. J. Clean. Prod. 275, 123942. doi:10.1016/j.jclepro.2020.123942
Tayeh, B. A., Almeshal, I., Magbool, H. M., Alabduljabbar, H., and Alyousef, R. (2021). Performance of sustainable concrete containing different types of recycled plastic. J. Clean. Prod. 328, 129517. doi:10.1016/j.jclepro.2021.129517
Teimouri, Z., Salem, A., and Salem, S. (2019). Regeneration of wastewater contaminated by cationic dye by nanoporous activated carbon produced from agriculture waste shells. Environ. Sci. Pollut. Res. 26, 7718–7729. doi:10.1007/s11356-018-04094-x
Tomassetti, L., Di Giuseppe, D., Zoboli, A., Paolini, V., Torre, M., Paris, E., et al. (2020). Emission of fibres and atmospheric pollutants from the thermal treatment of asbestos containing waste (ACW). J. Clean. Prod. 268, 122179. doi:10.1016/j.jclepro.2020.122179
Vayghan, A. G., Khaloo, A. R., Nasiri, S., and Rajabipour, F. (2012). Studies on the effect of retention time of rice husk combustion on the ash’s chemo-physical properties and performance in cement mixtures. J. Mater Civ. Eng. 24, 691–697. doi:10.1061/(asce)mt.1943-5533.0000426
Wang, S., Gainey, L., Marinelli, J., Deer, B., Wang, X., Mackinnon, I. D., et al. (2022). Effects of vermiculite on in-situ thermal behaviour, microstructure, physical and mechanical properties of fired clay bricks. Constr. Build. Mater 316, 125828. doi:10.1016/j.conbuildmat.2021.125828
Wangqiang, C., yan, Lin X., Meidong, X., and Luo, X. G. (2019). Performance of non-fired bricks containing oil-based drilling cuttings pyrolysis residues of shale gas. J. Clean. Prod. 206, 282–296. doi:10.1016/j.jclepro.2018.09.128
Wong, C. L., Mo, K. H., Yap, S. P., Alengaram, U. J., and Ling, T. C. (2018). Potential use of brick waste as alternate concrete-making materials: A review. J. Clean. Prod. 195, 226–239. doi:10.1016/j.jclepro.2018.05.193
Wu, J. D., Guo, L. P., and Qin, Y. Y. (2021). Preparation and characterization of ultra-high-strength and ultra-high-ductility cementitious composites incorporating waste clay brick powder. J. Clean. Prod. 312, 127813. doi:10.1016/j.jclepro.2021.127813
Yang, Z., Qiang, Z., Guo, M., Yi, G., Shi, Y., Cheng, F., et al. (2020). Pilot and industrial scale tests of high-performance permeable bricks producing from ceramic waste. J. Clean. Prod. 254, 120167. doi:10.1016/j.jclepro.2020.120167
Zhan, Q., Zhou, J., Wang, S., Su, Y., Liu, B., Yu, X., et al. (2021). Crack self-healing of cement-based materials by microorganisms immobilized in expanded vermiculite. Constr. Build. Mater 272, 121610. doi:10.1016/j.conbuildmat.2020.121610
Zhang, S., Dong, R., Wang, M., Jia, W., and Lu, Z. (2020a). Synthesis mechanisms on waste poplar fiber lightweight biomass bricks. J. Clean. Prod. 246, 118981. doi:10.1016/j.jclepro.2019.118981
Zhang, S., He, P., and Niu, L. (2020b). Mechanical properties and permeability of fiber-reinforced concrete with recycled aggregate made from waste clay brick. J. Clean. Prod. 268, 121690. doi:10.1016/j.jclepro.2020.121690
Zhao, Y., Gao, J., Chen, F., Liu, C., and Chen, X. (2018). Utilization of waste clay bricks as coarse and fine aggregates for the preparation of lightweight aggregate concrete. J. Clean. Prod. 201, 706–715. doi:10.1016/j.jclepro.2018.08.103
Keywords: flexural strength, compressive strength, workability, agricultural waste, durabilility
Citation: Mohammed SA, Shakor P, S. S, Rauniyar A, Krishnaraj L, Kumar Singh A and Laghi V (2023) An environmental sustainability roadmap for partially substituting agricultural waste for sand in cement blocks. Front. Built Environ. 9:1214788. doi: 10.3389/fbuil.2023.1214788
Received: 30 April 2023; Accepted: 12 June 2023;
Published: 23 June 2023.
Edited by:
Paul Awoyera, Covenant University, NigeriaReviewed by:
Afonso Azevedo, State University of Northern Rio de Janeiro, BrazilCopyright © 2023 Mohammed, Shakor, S., Rauniyar, Krishnaraj, Kumar Singh and Laghi. This is an open-access article distributed under the terms of the Creative Commons Attribution License (CC BY). The use, distribution or reproduction in other forums is permitted, provided the original author(s) and the copyright owner(s) are credited and that the original publication in this journal is cited, in accordance with accepted academic practice. No use, distribution or reproduction is permitted which does not comply with these terms.
*Correspondence: Pshtiwan Shakor, cHNodGl3YW5uQHlhaG9vLmNvbQ==, cHNodGl3YW4uc2hha29yQHNwdS5lZHUuaXE=
Disclaimer: All claims expressed in this article are solely those of the authors and do not necessarily represent those of their affiliated organizations, or those of the publisher, the editors and the reviewers. Any product that may be evaluated in this article or claim that may be made by its manufacturer is not guaranteed or endorsed by the publisher.
Research integrity at Frontiers
Learn more about the work of our research integrity team to safeguard the quality of each article we publish.