- Institute of Numerical Methods and Informatics in Civil Engineering (IIB), Department 13, Technical University of Darmstadt, Darmstadt, Germany
Construction site logistics deals with the transport and storage of materials as part of the execution of a construction project. An important part of construction logistics is informing those who are involved in the project about the current status of the ordered materials. On the one hand, the missing overview of the material inventory on the construction site and incoming deliveries makes efficient daily work planning on the construction site more difficult. On the other hand, unnecessary search and travel times reduce the productive working hours of employees on the construction site. In order to provide a better overview, the information from existing data sources must be linked and visualized in an easily understandable way for all project participants. Therefore, a digital construction logistics twin is proposed in this paper. Here, the challenge lies in the creation of the digital twin. The aim of this paper is to reduce the manual entry and planning effort needed. Therefore, an approach is proposed, which uses the Building Information Model (BIM), information from the technical specifications and bill of quantities as well as catalogue data from the building materials trade. The Building Information Model comprises the three-dimensional building model, information about the building components, the construction schedule (4D BIM) and the planned storage spaces on the constructions site. The catalogue data adds relevant logistic attributes and could also enables guidelines to be checked, e.g., as part of a sustainability certification (e.g., LEED). If the suppliers’ telemetry data were integrated, end-to-end material tracking would even be possible, similar to “track-and-trace” services from parcel service providers for end customers. The provision of all this data via a Building Information Model server as a “single source of truth” increases the transparency of the construction and logistics processes for everyone involved in the project. Also, this information would, for example, favor the use of autonomous means of transport, which reduces the need for manpower for transport on the construction site.
1 Introduction
Construction workers only spend one-third of their working time on productive activities. At the same time, 32% of the work time is wasted on searching for construction equipment and materials and on unnecessary movements on the construction site (Girmscheid, 2015). As cost pressure rises and skilled workers are missing, the efficiency of construction work needs to be improved. Mobile devices and augmented reality (AR) technologies enable the visualization of construction data relevant to a construction worker’s specific task. This can improve their efficiency. For example, a smartphone application that navigates the construction workers around the construction site could reduce search and movement times. For the visualization of said construction data, the data must first be collected and stored in a structured and accessible manner. This can be done through digital twins. A digital twin is the digital representation of an object in the real world. The concept of digital twins proposed by Grieves (2016) involves the physical object in the real world, the digital object in the virtual world and data or communication links between these two. In addition to managing the data, the digital twin also enables the simulation of the behavior of the represented object or supplements the physical object with digital services. Depending on the requirements of a building’s digital twin, this includes the three-dimensional building model, structural properties, component information regarding the manufacturer, maintenance intervals and more. The challenge in creating a digital twin lies in designing a suitable data structure, collecting and linking the required data and creating suitable interfaces for using the data (Tao et al., 2018). In this paper, the focus lies on the fusion of construction logistics data with existing building model data. The preceding research follows the methodology shown in Figure 1. It is explored what attributes are necessary for construction logistics and how they are connected to the building model. Consideration was given to minimizing the amount of work required for digital twin modeling. Therefore, it is examined which data is already available, which format the data is present and how it can be used in the modeling process. Finally, an illustrative case study is used to test the application of the data fusion approach for the digital construction logistics twin.

FIGURE 1. Methodical procedure inspired by design science research method (Peffers et al., 2007).
2 Basics of construction logistics
Construction logistics deals with the transport and storage of materials, the management of storage areas and materials on the construction site as well as control and communication of the material flow on the construction site (Weber, 2007). As shown in Figure 2, procurement logistics delivers the materials up to the boundaries of the construction site. There the material can be stored temporarily or delivered directly to a temporary storage area in the building. From there, the materials get transported to the place of installation. After installation, the remaining waste is transported back to an interim storage space at the boundaries of the construction site. From there, disposal logistics deals with the removal of the collected waste on the construction site.
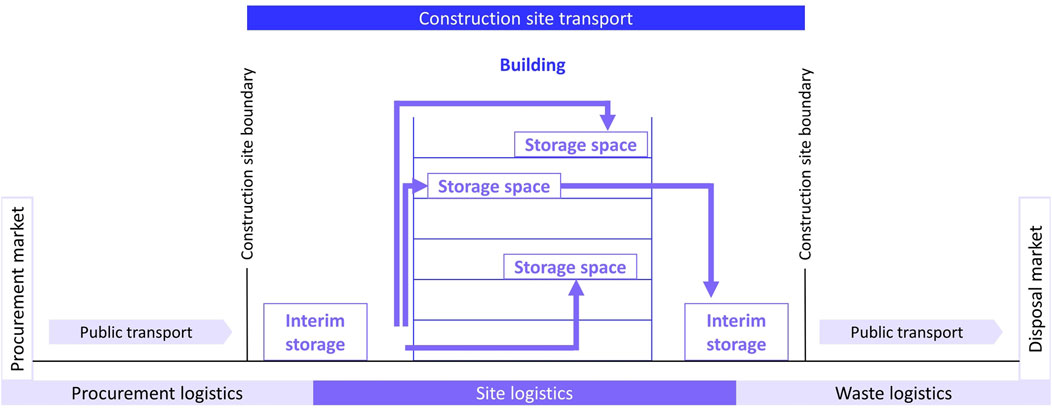
FIGURE 2. Logistics of a construction project/construction site transport (Blecken et al., 2001).
In this paper, a closer look is taken at the site logistics. There are several different ways to organize the construction logistics, which affect the way materials are transported and stored on the construction site (Voigtmann and Bargstädt, 2010a). The site logistics can either be organized individually by each company or managed centrally by a project participant or the project owner. Central storage and data sharing are economically advantageous if the site logistics is centrally organized because it increases the number of users in the shared data environment and thereby multiplies the positive effects of such a data storage system. Furthermore, deliveries can be bundled to increase the degree of capacity utilization. The shipments can contain the daily, weekly or monthly required quantity of materials. This affects the needed storage space. Also, the shipment can be delivered during working hours or at night, so it does not stall construction. The materials on the construction site can be stored centrally in a big interim storage area, decentrally in storage areas in each story or even closer to the point of installation. Depending on the overall site logistics organization the storage areas can be directly assigned to the project participants. To increase the proximity of the storage area to the installation point it is reasonable to use shared storage areas. The existence of storage areas can be temporary depending on their location and the construction progress. Finally, materials can be pre-commissioned to the project participant who will use them or to the floor and construction section where they will be installed. Due to the higher costs and the rather short-term supply chain of construction projects, this is a rarely used organizational structure (Sullivan et al., 2011).
Poor logistics planning and organization lead to a loss of efficiency and disruption of construction work (Hasenclever et al., 2011). In logistic systems, the flow of information is a fundamental part. The preceding flow of information announces a corresponding flow of material in advance and enables the preparation of the receipt of goods (Weber, 2007). The goal of site logistics is to reduce the negative impact of schedule deviations. They can be generated by delivery delays, production delays (among other things due to missing materials) and additional planning deviations due to change requests of the client. The challenge is to keep track of the stored materials on the construction site, the materials already produced and on the way to the site and the materials that are scheduled in the supply chain. As seen in Figure 3, orders can be postponed until dispatch to manage the storage usage on the construction site. To achieve this, effective management tools for the information and material flow on the construction site are needed (Almohsen and Ruwanpura, 2013).
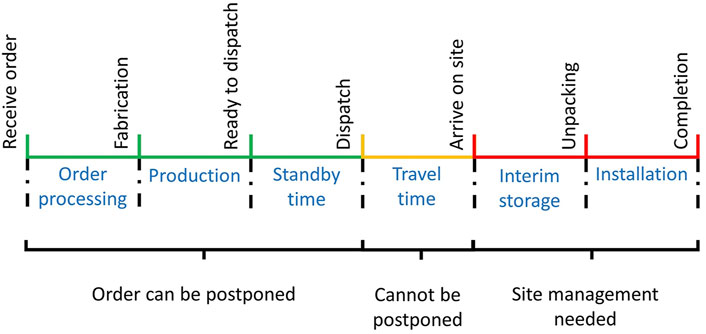
FIGURE 3. Stages of a building material in the construction supply chain (Cheng and Kumar, 2015).
Such a management tool for construction site logistics could simplify collaboration by sharing important information between the project participants, like storage location of material, planned delivery date or similar. Almohsen and Ruwanpura (2013) identified that the materials stored on the construction site are documented poorly and due to the distributed storage areas, it impossible to get a quick overview. An interactive map could help to locate the materials and indicate scarce material stocks. For this, appropriate logistics data must be available. According to Omar and Ballal (2009), information and communication technologies (ICT) and wireless technologies could enhance supply chain performance in the construction industry by providing useful information along the supply chain. Collaboration along the supply chain gets stimulated this way. Likewise Irizarry et al. (2013) call for a better understanding of the construction supply chain and claim that existing management approaches are not sufficient. With a similar intent, Hasenclever et al. (2011) define the requirements for a cross-company construction site management system as shown in Figure 4.
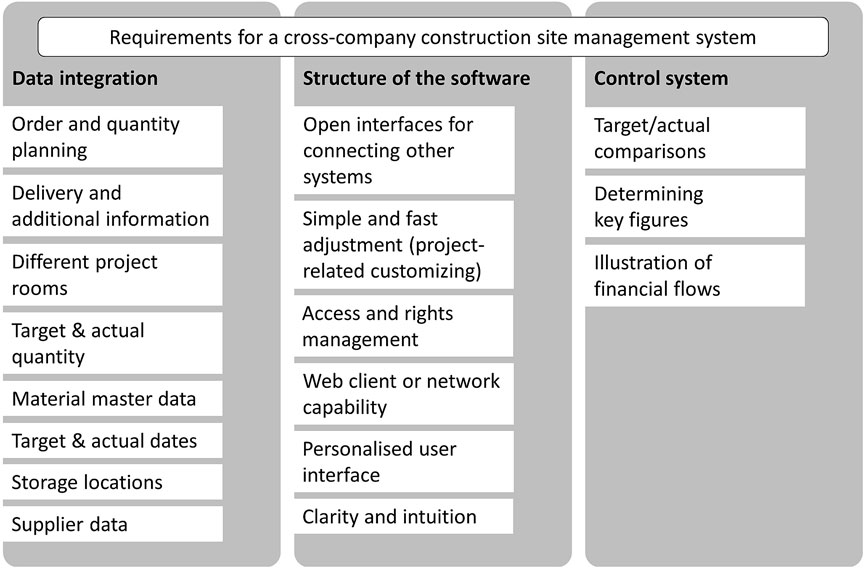
FIGURE 4. Requirement for a construction site management system (Hasenclever et al., 2011).
Existing software tools are addressing the mentioned challenges of site logistics. On the one hand, the material flow on the construction site is analyzed and divided into groups regarding quantities, the value of goods or the time needed from production to delivery (Irizarry et al., 2013). Based on that logistic planning approaches for the different material groups are chosen. On the other hand, online platforms are used, which allow logistic data to be recorded manually and then enable the management of material flows on the construction site based on this data (e.g., (INFORM GmbH, 2022)). To this end, suppliers can book time windows for notification of deliveries. Via a mobile application, the suppliers’ drivers receive instructions on the destination of the delivery and can confirm changes in the status of the delivery. In the event of a delay in delivery, the time slot can be adjusted and the site manager gets informed. In addition, the means of transport required for transport on the construction site, such as construction hoists and cranes, can be reserved via the platform’s resource management. In this way, access and delivery data can be recorded and storage areas and means of transport such as construction elevators can be booked. The recorded data can then be used to control the transport processes and to synchronize the floor logistics. In addition, all data is made available at any time via a mobile application. The integration of BIM data or the automated import of data from suppliers is not possible with the existing tools. The integration of BIM data is planned at least partially. However, entering the deliveries still requires a lot of manual entry effort.
3 Definition of objectives for a digital construction logistics twin
The basic vision of the digital construction logistic twin is to enrich the construction logistics planning data with more detail but without increasing the planning effort. It could improve the storage and transport on the construction site by delivering more and better-visualized information to the workers. At the same time, to keep planning efforts low, the digital construction twin should use existing data sources and reasonably link the received data.
For the support of the site logistics, the digital construction logistics twin needs to allow complex database queries to provide information on the following exemplary inquiries:
• Give an overview of all deliveries that are delivered on the key date.
• List all current inventory of the construction site, possibly filtered by trade, floor, area or item type.
• Display the current status of a key element in the construction supply chain.
Thus, a structured storage of the data is needed. SQL and NoSQL database schemes offer the described capabilities, but first the objects and attributes that need to be saved should be identified.
Voigtmann and Bargstädt (2010b) define relevant attributes for the simulation of construction logistics. For the planning and execution of transports on the construction site, these attributes are equally relevant. Additionally, information related to the building or the construction site is necessary, such as the address of the construction site, the installation schedule, etc. Furthermore, current production and logistic process data is needed, which shows whether a building element is already ordered, in production or on the way to the construction site. This status data enables the management of the construction site logistics and the work planning of the other project participants on the construction site. Based on this, the following relevant attributes for the construction site logistics can be identified:
Logistic-related data:
• General characteristics of building elements (dimensions, weight, stackability)
• Delivery properties of building materials and components (dimensions, pack sizes, transport aids, weight of a package, pallet details, hazardous material information)
• Transport properties (required mode of transport)
• Necessary work area for the installation of a building element
• Accessibility and availability of workspace for warehouse processes during/after process execution
• Status of building material or a building element in the construction supply chain
Building-related data:
• Geolocation of the building or the construction site
• Quantities of the needed building materials
• Installation point of a building element
• Planned date of installation of a building element
4 Development of a data fusion approach for a digital construction logistics twin
The challenge in creating a digital twin lies in designing a suitable data structure, collecting and linking the required data and creating suitable interfaces for using the data (Tao et al., 2018). This paper is specifically about the process of data fusion, which is the automatic or semi-automatic linking of information from different data sources into a representation that provides meaningful support for solving a problem (Boström et al., 2007). Inspired by Naumann et al. (2006), the data fusion process can be divided into the following steps:
1) Identification of different data sources
2) Schema mapping
3) Data Fusion
4.1 Data sources for the digital construction logistics twin
To create the digital construction logistics twin, suitable data sources need to be identified. Therefore, existing data sources are evaluated for their usability in the digital construction logistics twin to reduce the manual entry and planning effort while at the same time increasing the overall information content. For the building-related data, the building information model (BIM) could be enhanced with information from the technical specifications of the building. Then, the data entities can be reasonably linked or fused with logistics data from catalog data of the building materials trade (see Figure 5).
4.1.1 Building information model
The digital twin of a building is a virtual model which contains information about the represented building and provides this data for simulation and evaluation of the building’s behavior. Building Information Modelling (BIM) delivers such a model. It comprises a three-dimensional representation of a building with attributes concerning the schedule, structural properties, the name of the manufacturing companies, etc. The scope and elaboration of the model depend on the level of detail (LOD) and the number of attributes on the level of information (LOI). The LOD and LOI are determined by the project owner. The BIM method aims to create a single source of information, with which all project participants work. In the so-called “big open BIM” approach, the model is provided via a common data environment (CDE) and the project participants work at the same time together with the same status of the model. Using suitable interfaces, each discipline can work with its special software on the model. This is the ideal process for how the planning of buildings should be carried out in the future. This planning method offers advantages not only to the planners, like automated collision checking or the automatic creation of component lists, but the extensive planning data can also be beneficial on the construction site. For example, this data includes installation scheduling, lean cycle planning, data about the construction progress and delivery times. The data can be stored as attributes linked to the building components in the model. In research, this is referred to as 4D or 5D planning (Spengler and Peter, 2020).
In this way, the building information model (BIM) can provide logistics with information about the material, quantity and location. Though, the main challenge is the LOD of the model. Not all materials delivered to the construction site are modeled and have an existing digital counterpart. Therefore, the material flow on the construction site needs to be digitized in different ways. The following classification helps to identify how the materials appear in the construction logistics twin. The categories are sorted in ascending order of processing workload to be implemented in the digital construction logistics twin. Already modeled building elements are easier to implement than building elements that are not existing in the model. Furthermore, the number of items increases the implementation effort. Consumable elements require a complex strategy to assign building materials to building elements.
• Category 1: Special building component, only one instance in the building and the model.
• Category 2: Building components, several instances in the building and the model
• Category 3: Consumable building supplies, used in the building to create a building component, merged product in the model
• Category 4: Unmodeled special building component, one instance in the building
• Category 5: Unmodeled building components, several instances in the building
• Category 6: Unmodeled consumable building supplies, used in the building to create a building component
4.1.2 Technical specifications and bill of quantities
Building elements often consist of different components, which get separably or even inseparably connected during installation. Sometimes these components are not contained in construction drawings. Therefore, the existence of the individual components, the desired product quality or the demand for functionality is defined in the bill of quantities and the associated technical specifications. Particularly in Germany, it is common for construction work to be awarded through a public tender. The needed manufacturer-independent technical specifications of standard building components are provided by the German Joint Committee for Electronics in Construction (“Gemeinsamer Ausschuß für Elektronik im Bauwesen”: abbreviation GAEB) with their standard service book (latest version StLB-Bau (GAEB, 2022)). Template texts for technical descriptions can also be found on manufacturers’ websites. Furthermore, GAEB provides a standard data format, which allows the exchange of digital tender data. The latest structure is based on the extensible markup language (XML), which is a file format for structured storage of data, and enables the linking of BIM elements with tender quantities (Faschingbauer, 2019). With this data, it is possible to link building elements in the digital model with products from the tender documents. Also, models with a low level of detail can be enriched by products and materials defined in the technical specifications.
4.1.3 Catalogue data in the building materials trade
In the building materials trade, the global trade item number (GTIN) is used to identify trading units (GS1, 2022). The GTIN comes from the GS1 system (in Europe formerly the EAN system) and provides a worldwide unique identification system for goods, services, locations, transport units, etc. The GTIN aims to secure consistent worldwide merchandise management. With the GTIN article master data can easily be exchanged along the supply chain between the partners involved. In the construction sector the consistent exchange of data between builder’s merchants and construction companies using the GTIN has only been marginally pursued so far (Nour and Beucke, 2004; Almohsen and Ruwanpura, 2013).
A trading unit can be a product category, but also a box containing several products or even a pallet containing several boxes. As shown in Figure 6, this creates a complex article hierarchy, which is documented in article catalogs of dealers and manufacturers. Individual trading units can be identified with the GTIN and the serial number. To exchange the catalog data which contains the GTIN and further specifications, several data formats are used. In the following section, common data formats are listed and evaluated in terms of their usability for the digital construction logistics twin:
4.1.3.1 Excel/PDF
The Portable Document Format (PDF) is a platform-independent file format. It is a widely used format for text documents and is easy to read and write. Excel is a proprietary file format from the commonly used spreadsheet program Microsoft Excel. As well as the PDF format, it is easy to read and write and allows simple structuring of data. One disadvantage of these file formats is that the contained data is not readily machine-readable.
4.1.3.2 IDM
The Integrated Data Model (IDM) is an XML-based format that contains master data for the product components, materials and versions of these materials. Furthermore, relationships and conditions can be defined for materials and product components, which enable the calculation of prices for certain product configurations. It is widely used for fitted furniture that requires high planning efforts, such as kitchen furniture, upholstery and living room furniture. Each of the branches has developed its adaptions and specifications of the IDM format (e.g., IDM kitchen, IDM upholstery, IDM living room furniture).
4.1.3.3 Datanorm
Datanorm is a file format based on text files in tabular form. It is widely used to exchange article master data in the auxiliary building trade such as the plumbing, heating and electrical industries. Due to its simple structure, the data format can only transport a limited amount of information. The data content for other processes, like warehouse logistics, can only be mapped to a limited extent.
4.1.3.4 EDIFACT/PRICAT
Electronic Data Interchange for Administration, Commerce and Transport (EDIFACT, 2022) is a cross-industry international standard for the exchange of electronic data in business transactions. “It comprises a set of standards, directories and guidelines for the electronic data interchange of structured data, between independent computerized systems.” (EDIFACT, 2022) EDIFACT is available in various industry-specific versions, such as EANCOM for the consumer goods industry, EDIFURN for the furniture industry or EDITRANS for the logistics industry. The price catalog message (PRICAT) is a message type from the worldwide EANCOM transaction standard, which enables the electronic data exchange of catalogs and business documents; in particular, the article-related data content that is required as a basis for the electronic exchange of orders, order confirmations, delivery and payment notifications, invoices or ECR applications.
4.1.3.5 OFML
The Office Furniture Modelling Language (OFML) is a data standard created by the German Furniture Manufacturers Association (“Industrieverband Büro und Arbeitswelt e.V.“, abbreviation: IAB). It established a general standard for the description, configuration of furniture and spatial planning of furniture in the furniture industry. It also allows the combination of furniture from different manufacturers. It comprises different levels, which describe the different capabilities of a model. The basic level is a table-based interface for the description of hierarchical geometries in 2D and 3D. The other levels extend the model with further functionalities and integrate arbitrary complex data, such as logistic attributes.
4.1.3.6 openTRANS
Fraunhofer IAO and the university Duisburg-Essen (Germany) developed openTRANS as an XML-based standard for the support of electronic data interchange (EDI) in business transactions between trading companies. It supports electronic procurement and enables the exchange of business documents such as orders and invoices.
4.1.3.7 BMEcat
On the initiative of the German Association for Materials Management, Purchasing and Logistics (“Bundesverband Materialwirtschaft, Einkauf und Logistik e. V.“, abbreviation: BME) the XML-based standardized exchange format for catalog data in the B2B area has been developed. In addition to order information, logistics data can also be transmitted. Therefore, an additional element exists, which can hold information like product dimensions (length, height, width, volume, weight), delivery times, transport conditions and means, origin and customs tariff information and dangerous goods information. Due to the XML format, the multitude of logistical parameters and the broad usage in the building materials trade industry, BMEcat is the most promising data source for the digital construction logistics twin.
4.2 Schema mapping
To structure and visualize the links in the data, the Entity-Relationship-Model (ERM) is used. This also simplifies the conversion from the structured data model to a database model. In the process of development, the attributes mentioned in chapter 3 can be grouped and assigned to the following five key objects:
• Building project: Stores information about the geolocation of the construction site.
• Building element: Stores information about the general characteristics of building elements as well as the installation point, the necessary work area for installation and quantities.
• Project Phase: Helps determine the planned date of installation and the availability of storage spaces.
• Storage space: Stores information about the accessibility of storage spaces.
• Delivery: Stores among other things the status in the production supply chain.
• Trade item: Stores information about building materials like delivery and transport properties.
Based on that, the objects and their attributes can be put in relation to each other (see Figure 7).
4.3 Data fusion
The data sources mentioned are now to be linked to one another. The data of the BIM is a sufficient basis for the digital construction logistics twin. It contains the most important building-related data, such as spatial and basic component information and planned storage areas. To connect the building-related data with logistic attributes, the GTIN should be used. The GTIN identifies building materials as supplied by the building materials trade. By linking the quantities from the BIM and the logistic properties of the trade units, a logistical plan can be created for the construction site, which includes transport units, transport dates and storage areas. Each item that is planned for delivery on the construction site is identified via a unique identifier. This identifier should be visible on the package for further identification in the transport processes on the construction site.
This linking approach enables the planning and tracking of building elements of categories 1, 2 and 3. Unmodeled construction elements can be brought into the BIM by adding appropriate attributes to increase the LOI of the model. Therefore, depending on the LOD and LOI of the BIM, it makes sense to expand the building data using the tender and offer data. This can be achieved as (Faschingbauer, 2019) proposed. There, an XML-based multimodel scheme, which allows the linking of GAEB XML and IFC is developed. The challenges are product-unspecific tenders or technical specifications that are kept very general and only contain the desired functionality, but not specific products. In this case, the contractor should be obliged to supply corresponding product data, more precisely the GTIN of the used products.
5 Case study of utilizing a digital logistics twin from the developed data fusion approach
The demonstration application consists of a database that stores the construction logistics data, a management tool that imports and connects the data from the different data sources and an exemplary mobile application that enables the query of the database and visualizes the requested information.
In order to always use the latest planning status and at the same time be able to work independently of proprietary file formats, the IT system is to be implemented according to the “big open BIM” approach, e.g., as a container solution for a BIM server. The demonstrator uses a SQL database, which holds the logistic attributes and is linked to a geometry file that contains the 3D building model and other building-related data. The system is hosted on a server and can be queried via a Web API. A Web API is a programming interface that allows two software systems to exchange information with HTTP requests over the internet. This way, the construction logistics twin can be accessed by all project participants at the same time.
With the management tool, building projects can be created and the baseline data can be imported and processed. Initially, the BIM is linked which contains the planning data of the detailed design, the scheduling and possible storage areas from the logistics planning. The BIM also needs to comprise the GTIN of the specific building materials which are installed. The executing companies should add this information to the BIM either by including their digital offer documents, more specifically the technical specifications and the bill of quantities containing building materials and prices, or by hand. Additionally, catalog data of the suppliers can be added, which includes the logistic attributes of the required building materials like pack size, weight, required mode of transport, etc. With this input, the management tool then supports the creation of a detailed logistics plan with delivery times and storage areas for each building element. For this purpose, packages, storage locations and installation times are linked with each other. A corresponding algorithm could work according to the following scheme:
1) Neighboring building elements more specifically the assigned building materials of the same type and adjacent project phases are combined into packages.
2) The nearest storage area is searched for the package.
3) The availability of the corresponding storage space and other parameters (see below) are checked.
4) In case of a positive check result, the package will be linked to the corresponding storage space otherwise a further storage space will be searched for (go to step 2).
From the point of view of the availability of storage space, it should be checked whether the planned packages fit geometrically into the storage space. In addition, it could be checked to what extent the load on the storage area is compatible with the static boundary conditions and whether the building materials in the corresponding package can reach their destination within the structure without additional repacking.
The created planning data is then stored in the construction logistics twin.
To demonstrate the advantages of the construction logistics twin, the mobile application visualizes storage areas and stored materials on the construction site. It is also used to record the current status of deliveries by having staff in the supply chain scan QR codes on the materials and track the smartphone location of delivery drivers. Via the web API, the mobile application can connect to the server and exchange the required logistics data. Depending on the user group, selected data is made available. For example, the project owner or a logistics manager can check the inventory on the construction site using a controlling dashboard (see Figure 8).
On the construction site, the logisticians are shown the planned storage location of a delivered package and the construction site personnel are shown the storage location of the material that they are looking for using the three-dimensional building model (see Figure 9).
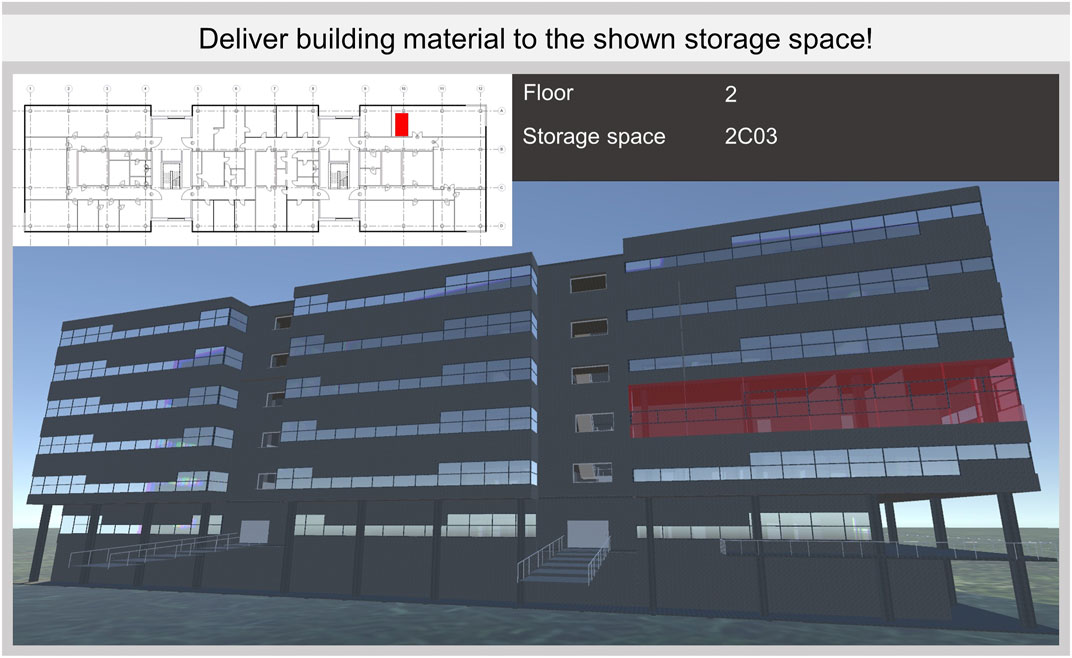
FIGURE 9. Visualization of a searched storage space based on the digital construction logistics twin.
6 Conclusion and further development
This research shows, how existing data sources can be used to create a digital construction logistics twin. Furthermore, it demonstrates how this data can be valuable for the project participants by visualizing the logistic processes to the workers on the construction site. In the sense of a case study, it focuses on given data sources and their individual data schemes. However, the standardization of the data shared between the project participants would simplify the process of data fusion and allows the efficient utilization of the data in additional use cases. Thus, the standardization of exchange formats should continue to be pursued.
The presented approach does not take into account building materials without a GTIN, such as individual pieces or custom-made products. To add this data, the material passport of a building could be used, which contains all the products and materials installed in a building (Luscuere, 2017). It is created during the design or construction phase and is used to identify and track which materials and products can be reused in a building in case of a refurbishment. But again, keeping the data up to date is a major challenge. So the digital twin could also complement the material passport. The combination of material passports and digital construction logistics twins should therefore be considered in further study.
Likewise, things that are only required for the creation of the building and do not appear in the finished building are not taken into account. These are among others, tools, formwork and scaffolding. With the chosen approach, the logistics planning of these things can be supplemented manually. In further investigations, it would be useful to find methods that reduce the manual entry effort here as well.
In practice, it will be important to check to what extent the executing companies are willing to share their logistics data and whether they can add this data to the BIM. Many small and medium-sized companies lack the expertise, software and personnel to work with BIM. Yet providing catalog data from their suppliers and entering GTINs is critical to successfully building the digital construction logistics twin. A possible solution would be to delegate the data entry and management of the digital construction logistics twin to a project participant. Furthermore, the regular updating of the digital construction logistics twin in the event of planning changes and supplements would have to be agreed upon between the parties involved so that the digital construction logistics twin remains up to date. The current concept does not support automatic updates of the digital construction logistics twin via some kind of sensor network or data analysis.
In the future, further applications could be developed that are based on the data of the digital construction logistics twin. For example, transport processes on the construction site could be automated by autonomous conveyor vehicles that work based on the digital construction logistics twin.
Data availability statement
The original contributions presented in the study are included in the article/supplementary material, further inquiries can be directed to the corresponding author.
Author contributions
MG contributed to conception, design and development of the demonstrator. Also, MG wrote the first draft of the manuscript. All authors contributed to manuscript revision, read, and approved the submitted version.
Funding
We acknowledge support by the Deutsche Forschungsgemeinschaft (DFG—German Research Foundation) and the Open Access Publishing Fund of Technical University of Darmstadt.
Conflict of interest
The authors declare that the research was conducted in the absence of any commercial or financial relationships that could be construed as a potential conflict of interest.
Publisher’s note
All claims expressed in this article are solely those of the authors and do not necessarily represent those of their affiliated organizations, or those of the publisher, the editors and the reviewers. Any product that may be evaluated in this article, or claim that may be made by its manufacturer, is not guaranteed or endorsed by the publisher.
References
Almohsen, A., and Ruwanpura, J. (2013). “Logistics management in the construction industry,” in Proceedings, Annual Conference - Canadian Society for Civil Engineering, 5 January 2013 (Berlin, Germany: Springer), 4.
Blecken, U., Boenert, L., and Blömeke, M. (2001) Studie zur Akzeptanz einer Dienstleistung Logistik in der Bauindustrie Universität Dortmund, Lehrstuhl Baubetrieb.
Boström, H., Andler, S. F., Brohede, M., Johansson, R., Karlsson, A., van Laere, J., et al. (2007). On the definition of information fusion as a field of research. Situat. Awareness-Information Fusion 2007, 1–10.
Cheng, J. C. P., and Kumar, S. (2015). “A BIM-based framework for material logistics planning,” in IGLC proceedings. Presented at the IGLC 23. Editors M. Mandujano, L. Alarcon, J. Kunz, and C. Mourgues (Perth, Australia: Global Problems- Global Solutions), 33–42.
EDIFACT (2022). Introducing UN/EDIFACT | UNECE. Available at: https://unece.org/trade/uncefact/introducing-unedifact (Accessed 11 1, 23).
GAEB (2022). STLB-bau online - Ausschreibungstexte, Leistungsbeschreibungen, Leistungsverzeichnisse, Standardleistungsbuch, GAEB. Available at: https://www.stlb-bau-online.de/(Accessed 11 1, 23)
Girmscheid, G. (2015). “AVOR - Planung der Ausführung,” in Angebots-und Ausführungsmanagement-prozessorientiert: Erfolgsorientierte Unternehmensführung, VDI-Buch. Editor G. Girmscheid (Berlin, Heidelberg: Springer), 121–302. doi:10.1007/978-3-642-55291-5_12
Grieves, M. (2016). Origins of the digital twin concept. Digit. Twin 2016, 61609. doi:10.13140/RG.2.2.26367.61609
GS1 (2022). GS1. Available at: https://www.gs1.org/home (Accessed 11 1, 23).
Hasenclever, T., Horenburg, T., Höppner, G., Klaubert, C., Krupp, M., Popp, K. H., et al. (2011). “Logistikmanagement in der Bauwirtschaft,” in Digitale Baustelle - innovativer Planen, effizienter Ausführen: Werkzeuge und Methoden für das Bauen im 21. Jahrhundert. Editors W. Günthner, and A. Borrmann (Berlin Heidelberg: Springer), 205–290. doi:10.1007/978-3-642-16486-6_5
INFORM GmbH, 2022. Construction site logistics needs a flexible software solution. Available at: https://www.inform-software.com/logistics/truck-supply-control/construction-site-logistics (Accessed 1.10.23).
Irizarry, J., Karan, E. P., and Jalaei, F. (2013). Integrating BIM and GIS to improve the visual monitoring of construction supply chain management. Automation Constr. 31, 241–254. doi:10.1016/j.autcon.2012.12.005
Luscuere, L. M. (2017). Materials Passports: Optimising value recovery from materials. Proc. Institution Civ. Eng. - Waste Resour. Manag. 170, 25–28. doi:10.1680/jwarm.16.00016
Naumann, F., Bilke, A., Bleiholder, J., and Weis, M. (2006). Data fusion in three steps: Resolving inconsistencies at schema-, tuple-, and value-level. Bull. IEEE Comput. Soc. Tech. Comm. Data Eng. 2006, 21–31.
Nour, M., and Beucke, K. (2004). “IFC supported distributed, dynamic & extensible constuction products information models,” in EWork and EBusiness in architecture, engineering and construction: Proceedings of the 5th European conference on product and process modelling in the building and construction industry - ECPPM 2004. Editor Attila Dikbas (Instanbul, Turkey: CRC Press), 249–260.
Omar, B., and Ballal, T. (2009). Intelligent wireless web services: Context-aware computing in construction-logistics supply chain. ITcon 14, 289–308.
Peffers, K., Tuunanen, T., Rothenberger, M. A., and Chatterjee, S. (2007). A design science research methodology for information systems research. J. Manag. Inf. Syst. 24, 45–77. doi:10.2753/mis0742-1222240302
Spengler, A. J., and Peter, J. (2020). “Begrifflichkeiten,” in Die Die Methode Building Information Modeling: Schnelleinstieg für Architekten und Bauingenieure (Fachmedien, Wiesbaden: Springer), 5–16. doi:10.1007/978-3-658-30235-1_2
Sullivan, G., Barthorpe, S., and Robbins, S. (2011). Managing construction logistics. Netherlands: John Wiley & Sons.
Tao, F., Zhang, H., Liu, A., and Nee, A. Y. C. (2018). Digital twin in industry: State-of-the-Art. IEEE Trans. Industrial Inf. 15, 2405–2415. doi:10.1109/tii.2018.2873186
Voigtmann, J., and Bargstädt, H.-J. (2010a). “Construction logistics planning by simulation,” in Proceedings of the 2010 Winter Simulation Conference, Baltimore, MD, USA, 05-08 December 2010 (IEEE), 3201–3211. doi:10.1109/WSC.2010.5679012
Voigtmann, J., and Bargstädt, H.-J. (2010b). “Simulationsgestütztes Supply Network Management auf Baustellen,” in Supply chain network management: Gestaltungskonzepte und Stand der praktischen Anwendung. Editors C. Engelhardt-Nowitzki, O. Nowitzki, and H. Zsifkovits (Wiesbaden: Gabler), 167–186. doi:10.1007/978-3-8349-6000-9_11
Keywords: construction logistics, digital twin, DATA FUSION, building information model (BIM), product data, visualization
Citation: Gehring M and Rüppel U (2023) Data fusion approach for a digital construction logistics twin. Front. Built Environ. 9:1145250. doi: 10.3389/fbuil.2023.1145250
Received: 15 January 2023; Accepted: 21 February 2023;
Published: 06 March 2023.
Edited by:
Jesus Balado, University of Vigo, SpainReviewed by:
Silvia María González Collazo, University of Vigo, SpainOluseye Olugboyega, Obafemi Awolowo University, Nigeria
Eftychia Kalogianni, Delft University of Technology, Netherlands
Copyright © 2023 Gehring and Rüppel. This is an open-access article distributed under the terms of the Creative Commons Attribution License (CC BY). The use, distribution or reproduction in other forums is permitted, provided the original author(s) and the copyright owner(s) are credited and that the original publication in this journal is cited, in accordance with accepted academic practice. No use, distribution or reproduction is permitted which does not comply with these terms.
*Correspondence: Maximilian Gehring, Z2VocmluZ0BpaWIudHUtZGFybXN0YWR0LmRl