- 1State Key Laboratory of Disaster Reduction in Civil Engineering & Department of Structural Engineering, Tongji University, Shanghai, China
- 2Department of Building & Real Estate, The Hong Kong Polytechnic University, Kowloon, China
Structural and non-structural damage reported after recent strong earthquakes promotes a fundamental shift in structural design target from “collapse resistance” to “fast structural function recovery”. A unique class of metal called superelastic shape memory alloy (SMA) has been emerging as a promising solution to enhance the seismic resilience of structures. SMA core damping elements are the basic constituents of many newly-proposed seismic resistant members or devices, and they are directly responsible for the safety, integrity, and economical efficiency of the structures using them. This mini-review paper offers a comprehensive summary of the emerging SMA core damping elements recently developed, covering SMA monofilament wires, fibers, bars, flat plates, U-shaped plates, angles, cables, rings, helical springs, disc springs, and friction springs. These SMA core elements are suitable for various seismic application scenarios, and their efficiency have been verified through either full-scale or proof-of-concept experimental studies. The basic working principles, advantages, and potential shortcomings of these elements are discussed, and future research needs are outlined.
Introduction
Extensive structural damage has been observed during strong earthquakes in the past few decades, leading to slow, if not impossible, function recovery of both individual buildings and the entire community. From a structural engineering point of view, the loss of structural function is mainly attributed to 1) low-cycle fatigue damage of energy dissipation components, and 2) residual deformation. While the entire structure may not collapse after seeing a strong earthquake, extensive damage and residual deformation are very difficult to reinstate, leaving demolition a likely option. In addition, the residual deformation would put the structure in great danger given the risk of aftershocks, and some components, which are designed to be replaceable, are indeed impossible to be replaced in time given the health and safety considerations. These challenges provide a strong impetus for the development of low-damage alternatives to conventional structural systems (Fang et al., 2022a).
Superelastic shape memory alloy (SMA) is a unique class of metal offering a promising strategy to enhance the seismic resilience of engineering structures (Alam et al., 2007; Jani et al., 2014; Casciati 2019). Superelasticity allows the material to recover a strain of up to 10% spontaneously upon unloading at room temperature. NiTi-based SMA, also known as Nitinol, has the most reliable superelastic effect among the available SMA classes, and is now the most successful commercial SMA product (Jani et al., 2014). “Superelastic SMA core damping elements”, hereafter named “SMA elements” for ease of interpretation, are the most fundamental forms of SMA products that constitute more diverse damping devices and members used in structural systems. When utilized in structures, SMA elements provide lateral load resistance, energy dissipation, and concurrently, recentering capability, and they are often used at critical locations such as braces and beam-to-column connections. The reliability and efficiency of the SMA elements determine whether the structure behaves as intended during strong earthquakes.
While the applicability of SMA for seismic application has been widely examined via member- and system-level investigations, e.g., (Billah and Alam, 2016a, 2016b; Qiu and Zhu, 2017; Fang et al., 2020a), this mini-review focuses on the latest technological advances in SMA elements only, which serve as the “heart” of SMA-based members/structures. It is believed that a proper design of an SMA element itself and its associated connection is more important than studying a new member/structure that employs this element. In the following sections, all the major SMA element types that have been developed so far are introduced, where their advantages and potential limitations are discussed in detail. Critical challenges and further studies needing to respond to the identified issues are also presented. All the SMA elements collected in this mini-review have been justified with solid test evidence, whereas pure numerical studies without rigorous experimental validations are not within the scope of this paper. Figure 1 shows the SMA element types discussed in this study, where a qualitative index, namely, load resistance efficiency, is used to indicate the necessary gross material consumption in order to achieve a certain desired property such as load resistance or energy dissipation. As SMA is expensive, a high efficiency implies that the material may be used in a more economical manner.
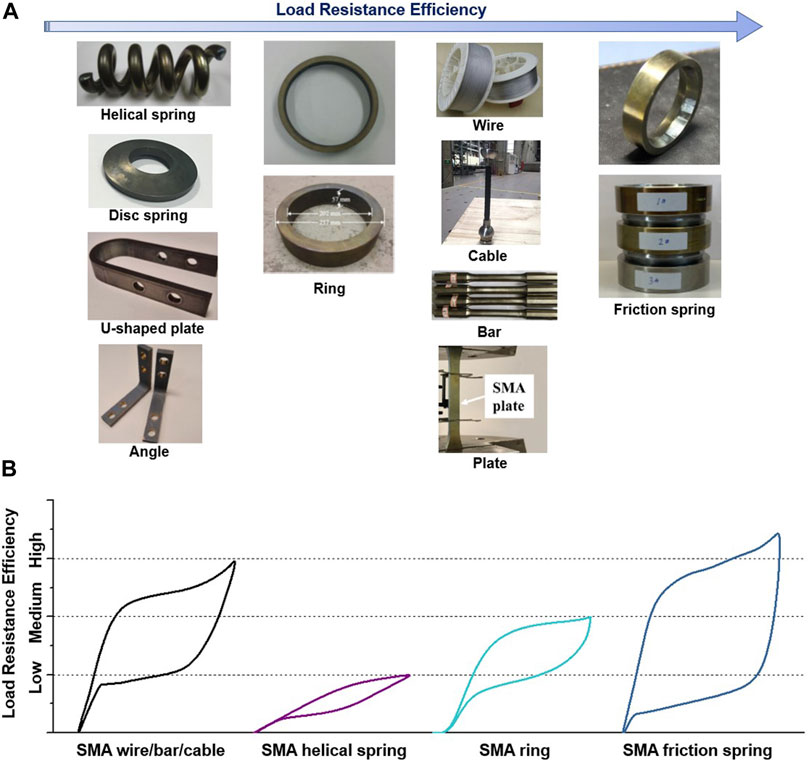
FIGURE 1. Available SMA element types: (A) general configuration, (B) illustration of typical load-deformation behavior of selected elements.
SMA elements
Monofilament SMA wires
Monofilament SMA wire is one of the most popular elements because of its mature manufacturing technology, good availability in market, high load resistance efficiency, and simple way of working. Monofilament SMA wires are tension-only elements, and are often considered in a damping device. Monofilament SMA wires have already been used in historic buildings such as the S. Giorgio Church, the St. Francis Basilica and the San Feliciano Cathedral (Indirli and Castellano, 2008). Preload can be applied to the SMA wires to enhance the initial stiffness, “yield” strength, and self-centering capability. The fundamental mechanical behavior of individual SMA wires has been widely studied since the 1990s (Piedboeuf et al., 1998; Tobushi et al., 1998; Wolons et al., 1998; Dolce and Cardone, 2001; Tamai and Kitagawa, 2002). One consensus from the existing studies is that an SMA wire, if produced through an appropriate manufacturing process, can exhibit outstanding ductility, hysteretic repeatability, recoverability, and fatigue performance. However, the behavior of an SMA wire is indeed sensitive to the temperature and loading rate.
However, great challenges still exist in practical implementation of SMA wires. One concerning issue is the difficulty of anchorage, especially for SMA wires with a diameter exceeding 1 mm. This problem results from the smooth surface of the wires and high hardness of the SMA material, making conventional grippers such as U-connectors ineffective. Another concern is the relatively small load resistance of individual SMA wires, rendering hundreds or even thousands of SMA wires needed in a “full-scale” device. This not only complicates the arrangement of the wires but also makes anchorage more challenging. Therefore, SMA wires are more suited to proof-of-concept studies, whereas the opportunity for application in modern construction is remote.
SMA fibers
Randomly distributed superelastic SMA fibers have recently been proposed to promote crack closure capability of concrete members. Failure to control crack of a concrete structure is often responsible for corrosion of the reinforcement and hence deterioration of the functionality and serviceability over its service life. SMA fibers are expected to be a viable alternative to conventional steel fibers, where the latter undergoes permanent residual deformation after yielding and the cracks of the member would not close if no external treatment (e.g., external tensioning) is applied. The SMA fibers are also very competitive when compared with fiber reinforced polymer (FRP) products which have limited ultimate tensile strain (and hence tends to fail in a brittle manner) and behave linearly with no energy dissipation capability.
The development of superelastic SMA fibers is still in its early stage, where strands and wires (Daghash and Ozbulut, 2016; Sherif et al., 2017, 2018) were mostly considered. Bonding is critical issue that cannot be easily resolved because form-setting of superelastic SMA fibers is difficult and expensive and often requires special treatment such as annealing. Some researchers have studied the use of thermally activated martensitic SMAs as fibers in cementitious matrix to provide prestressing, and these fibers are more easily produced into dog-bone shaped, paddled, chipped, and crimped shapes (Lee et al., 2018, 2021).
SMA bars/bolts
Larger scale SMA bars may be more preferred for civil engineering application because of their large load resistance and ease of construction. One of the most typical application scenarios for SMA bars is beam-to-column connections, where SMA bars are further machined into the bolt form (Speicher et al., 2011; Fang et al., 2014; Wang et al., 2017a; Fang et al., 2017, 2018a). These bolts, which are often preloaded, provide moment resistance, energy dissipation, and self-centering capabilities for the connections. Alternatively, SMA bolts can be buckling-restrained such that they are subjected to both tension and compression, providing stable two-directional flag-shaped hysteresis. Some new damping devices have been developed based on this concept (Wang and Zhu, 2018a; Qiu et al., 2020).
Caution should be exercised that SMA bolts are vulnerable to premature fracture at the threaded section. According to the existing experimental study (Fang et al., 2014; 2015a), the net threaded-to-shank diameter ratio of SMA bolts are recommended to range between 1.25 and 1.4. A smaller ratio would cause unexpected fracture at a large strain, whereas an overly large ratio would cause more significant material waste during the machining process. In addition, the performance of SMA bars/bolts is generally inferior to SMA wires, and special annealing is needed to trigger superelasticity (Wang et al., 2016).
SMA cables
SMA cable is a viable solution that exhibits the benefits of both SMA wires and bars. An SMA cable is produced by helically wrapping a series of SMA strands, and each strand consists of a series of helically wrapped monofilament SMA wires. Existing experimental studies on SMA cables (Reedlunn et al., 2013; Mas et al., 2017; Sherif and Ozbulut, 2017; Fang et al., 2019a) showed that their hysteretic behavior is comparable to monofilament SMA wires; compared with SMA bars, SMA cables are more cost effective and requires no annealing. However, the performance tends to deteriorate when an increased number of SMA wires are involved in a cable. This phenomenon could be due to the more pronounced nonlinear stress distribution for larger scale SMA cables. Moreover, as SMA cables are harder than steel ones, anchorage is a major challenge. Failure of SMA cables is often found at the anchorage due to slippage. Shi et al. (2021) recently proposed two mechanical anchorage solutions, namely, spike-type and end stop-type anchorages, and their reliability was examined through a series of tests. End stop type was found to be most suited to SMA cables. SMA cables have now been considered in many structural members such as braces (Chen et al., 2020) and isolation bearings (Liang et al., 2020). In 2021, SMA cable-based bearings was used for the first time in the Datianba #2 highway bridge in China (Fang et al., 2022b).
SMA flat plates
The available tests on superelastic SMA flat plates are limited. Murasawa et al. (2006) first carried out tensile tests on SMA plates, and confirmed the strong link between inhomogeneous deformation behavior and macroscopic deformation behavior when they are subjected to cyclic loading. Zhou et al. (2021) examined the tension-release behavior of SMA flat plates, with particular focus of their potential applications in beam-to-column connections. A similar study was conducted by Wu et al. (2022) who focused on timber connections. The SMA plates were found to display similar hysteretic behavior to SMA bars. For practical application, SMA plates may be bolt-connected to the adjacent members, rendering potential weak sections and hence premature fracture near the bolt holes. This should receive sufficient attention, but no study is currently available.
SMA U-shaped plates
SMA U-shaped plate is a special type of damping element that can provide large deformability and relatively high flexibility, making it particularly suitable for isolation bearings. A unique bending behavior is displayed by a U-shaped plate which consists of a flexible circular region. The geometry allows either in-plane or out-of-plane paralleled movements between two straight legs. So far, the only experimental results on SMA U-shaped plates were reported by Wang and Zhu (2018b), who confirmed that the element could exhibit stable flag-shaped hysteretic behavior when subjected to multiple loading cycles, with residual deformation being less than 2% of the maximum deformation. The main concern is the low-cycle fatigue facture which tends to occur at the junction between the circular region and the straight legs, where a high stress demand exists. The occurrence of fracture may also be related to the manufacturing process where stress concentration and cold hardening occur during the bending process. Fe-SMA U-shaped plates were also tested (Zhang J. et al., 2022), where superior low-cycle fatigue resistance was observed.
SMA angles
Angles are a common type of connecting elements used in connections. They are expected to transfer axial force, shear force, and bending moments, and provide energy dissipation for the connections when earthquake happens. When angles are endowed with superelasticity, extra self-centering capability is enabled. Wang et al. (2020) conducted an experimental study on SMA angles. The results are similar to those from the SMA U-shaped plate tests. Again, low-cycle fatigue fracture at stress concentration location occurred which should receive sufficient attention.
SMA rings
SMA rings enable flexible deformation at any direction of loading because of their bisymmetric configuration. This is an essential advantage compared with other SMA elements which are expected to act only in one or two directions. The load carrying mechanisms of an SMA ring subjected to pushing and pulling actions are not the same, leading to slightly different hysteretic behaviors. Under idealized situations, e.g., no fracture happens, the SMA rings would first experience bending and finally be stretched when under pulling; and would under significant bending until fully compressed when under pushing. Dong et al. (2006) first conducted a proof-of-concept study on 1 mm-thick SMA rings. Gao et al. (2016) tested a full scale SMA ring, and employed it in a cross-braced system with the ring serving as central damping elements linking four tension cables. The manufacturing steps of an SMA ring include disk cutting, heating, hammer forging, ring rolling, and annealing. Alternatively, Choi et al. (2018) applied wire cutting to flat SMA plates to produce SMA rings.
SMA helical springs
SMA helical springs can have a very large stroke and could recover large deformations accompanied by moderate energy dissipation. The high flexibility and large deformability make them ideal candidates for structural isolation and other scenarios where large deformation demand is expected (Liu et al., 2019). The typical manufacturing of a SMA helical spring involves: 1) heating SMA wires or bars to low-red heat temperatures, 2) bending the softened SMA around a mandrel to produce a helix, and 3) applying annealing to the finished coils to enable form-setting and to achieve uniform properties and good superelasticity. Small-scale tests have been done by Aguiar et al. (2010) and Liu et al. (2019), who reported excellent self-centering capability of the SMA springs with an equivalent damping ratio of more than 2%. Larger scale tests were conducted by Speicher et al. (2009), based on which a detailed analytical model proposed by Mirzaeifar et al. (2011) was verified. The influence of varying material properties and temperatures on the hysteretic behavior of SMA helical springs was revealed by Savi et al. (2015).
SMA disc springs
SMA disc springs, also known as SMA Belleville washer springs, are a relatively new family member of SMA elements. The key benefits include small size for narrow-space installation, small risk of premature fracture (because of the upper limit of deformation when flattened), and flexible load resistance and deformability realized via different stacking patterns (i.e., in series, in parallel, or in combination). An SMA disc spring could be produced by either form-setting or waterjet cutting (Speicher et al., 2009; Maletta et al., 2013). SMA disc springs deform via the development of hoop stress, where the maximum stress is induced at the two edge corners of the cross-section, and the remaining cross-sectional area remains at low-stress levels (Fang et al., 2016). Because of this stress distribution pattern as well as the special conical geometry, the load resistance of SMA disc springs is generally not large. Fang et al. (2020b) and Zheng et al. (2021) have considered using SMA disc springs for rocking bridge piers, where these springs serves as energy dissipative holding-down devices to enable a controlled rocking behavior.
SMA friction springs
SMA friction springs exhibit the largest load carrying capacity among all the available SMA element types, so they are especially suited to structures with heavy load resistance and energy dissipation demands (Fang et al., 2015b). The concept of SMA friction springs stemmed from conventional high-strength steel friction springs which consist of outer and inner steel rings placed alternately via wedged contact surfaces (Wang et al., 2019a; Zhang R. et al., 2022). The compressive deformation of conventional friction springs is provided by expansion of the outer rings and contraction of the inner rings. Similarly, an SMA ring spring set consists of a series of SMA outer rings and strong steel inner rings placed alternately. The main difference is that the nonlinear deformation demand is only provided by the expansion of the SMA outer rings, whereas the steel inner rings stay elastic.
Due to the large recoverable strain provided by the SMA, SMA friction springs can have much larger deformability than the conventional steel friction springs; the energy dissipation is also much increased because of the combined effect of superelasticity and friction. As the SMA outer rings have a uniform hoop stress distribution over the ring thickness, the load resistance efficiency is high, and therefore the SMA ring springs normally achieve larger load resistance than SMA tensile elements, e.g., cables and bars, given the same consumption of the SMA material. SMA friction springs have been applied to high-performance braces and beam-to-column connections which have been verified via a series of experimental programs (Wang et al., 2017b, 2019b; Fang et al., 2018b, 2019b).
Discussion
While a great progress has been made in the development of SMA core damping elements, challenges still exist. It is unlikely that a single SMA element could possess all necessary positive properties with no shortcomings. For example, achieving large load resistance and large deformability are often conflicting objectives when designing an SMA element. Table 1 summarizes the advantages and potential limitations of the different types of SMA elements. Some extra concerns are discussed as follows:
1) Degradation effect. Accumulation of residual deformation and decrease of phase transformation plateau are common phenomena for most commercial SMA products. Small-scale SMA wires normally have the smallest degradation effect, whereas larger scale SMA bars and plates would exhibit more evident degradation under repeated loading. Mechanical training is a viable way to mitigate degradation. An alternative strategy is to force the SMA elements to undergo tension-compression cycles rather than tension-release cycles. Great research opportunity exists in understanding and mitigating the degradation effect of large scale SMA elements.
2) Annealing. The degradation effect of a large scale SMA element can also be mitigated via an appropriate annealing procedure. Annealing promotes the precipitation of Ti3Ni4 which can facilitate the martensitic transformation and hinder plastic flow in the surrounding austenite matrix, and therefore greatly enhance the superelasticity of the SMA (McCormick et al., 2007; Tyber et al., 2007). At present, the “best” annealing scheme for a specific SMA element is often obtained via trial-and-error procedures on a case-by-case basis, and the data could end up being commercial secrets. This knowledge gap needs to be bridged in future studies.
3) Scale effect. Scaled specimens are expected to provide different responses in comparison to their full-scale counterparts, and this needs special attention. The reasons for the scale effect of SMA elements include inconsistent manufacturing and annealing strategy for different SMA elements, which are different from conventional dampers, e.g., Quaglini et al. (2022).
4) Temperature effect. SMAs are temperature-sensitive materials. The typical “effective” range for ensuring superelasticity is less than 40 °C (Fang and Wang, 2020). In other words, the annual temperature difference should be less than 40 °C to prevent loss of superelasticity at low temperatures and early development of plastic strain at high temperatures. This condition can be satisfied for most indoor environments, but may be violated if the SMA elements are for the outdoor use. The issue needs to be addressed from a probabilistic perspective.
5) Long-term effect. Little attention has been paid to the life-cycle behavior of SMA elements. Two potential issues are worth future investigations. The first one is corrosion. Although SMAs are anti-corrosion materials, the contact between SMA and steel (e.g., SMA ring springs) may cause galvanic corrosion to the steel elements. The other issue is the loss of prestress of the SMA elements. Mechanical slippage at the anchorage and creep of the material are two possible causes which need future confirmation.
The above problems partly result from the lack of an effective knowledge exchange between the communities of material scientists and civil engineers. New research opportunities do arise with new SMA elements springing up. There is no reason not to embrace the new technology as long as it is used in the right place at the right time.
Author contributions
CF wrote the first draft of the manuscript. MY contributed to conception and design of the study. Both authors contributed to manuscript revision, read, and approved the submitted version.
Funding
The financial supports from the National Natural Science Foundation of China (NSFC) with Grant Nos. 52078359 and 51778456 are gratefully acknowledged. Support for this study was also provided by the Shanghai Rising-Star Program (20QA1409400).
Conflict of interest
The authors declare that the research was conducted in the absence of any commercial or financial relationships that could be construed as a potential conflict of interest.
Publisher’s note
All claims expressed in this article are solely those of the authors and do not necessarily represent those of their affiliated organizations, or those of the publisher, the editors and the reviewers. Any product that may be evaluated in this article, or claim that may be made by its manufacturer, is not guaranteed or endorsed by the publisher.
References
Aguiar, R. A., Savi, M. A., and Pacheco, P. M. (2010). Experimental and numerical investigations of shape memory alloy helical springs. Smart Mat. Struct. 19 (2), 025008. doi:10.1088/0964-1726/19/2/025008
Alam, M. S., Youssef, M. A., and Nehdi, M. (2007). Utilizing shape memory alloys to enhance the performance and safety of civil infrastructure: a review. Can. J. Civ. Eng. 34 (9), 1075–1086. doi:10.1139/l07-038
Billah, A. M., and Alam, M. S. (2016a). Performance-based seismic design of shape memory alloy–reinforced concrete bridge piers. I: development of performance-based damage states. J. Struct. Eng. (N. Y. N. Y). 142 (12), 04016140. doi:10.1061/(asce)st.1943-541x.0001458
Billah, A. M., and Shahria Alam, M. (2016b). Performance-based seismic design of shape memory alloy–reinforced concrete bridge piers. II: methodology and design example. J. Struct. Eng. (N. Y. N. Y). 142 (12), 04016141. doi:10.1061/(asce)st.1943-541x.0001623
Casciati, S. (2019). SMA-Based devices: Insight across recent proposals toward civil engineering applications. Smart Struct. Syst. Int. J. 24 (1), 111–125.
Chen, J., Fang, C., Wang, W., and Liu, Y. (2020). Variable-friction self-centering energy-dissipation braces (VF-SCEDBs) with NiTi SMA cables for seismic resilience. J. Constr. Steel Res. 175, 106318. doi:10.1016/j.jcsr.2020.106318
Choi, E., Nam, T. H., and Kim, W. J. (2018). Cyclic tests in pushing and pulling actions of SMA rings in superelastic or martensitic states. Sci. Adv. Mat. 10 (9), 1250–1257. doi:10.1166/sam.2018.3290
Daghash, S. M., and Ozbulut, O. E. (2016). Characterization of superelastic shape memory alloy fiber-reinforced polymer composites under tensile cyclic loading. Mater. Des. 111, 504–512. doi:10.1016/j.matdes.2016.09.034
Dolce, M., and Cardone, D. (2001). Mechanical behaviour of shape memory alloys for seismic applications 2. Austenite NiTi wires subjected to tension. Int. J. Mech. Sci. 43 (11), 2657–2677. doi:10.1016/s0020-7403(01)00050-9
Dong, Y. S., Xiong, J. L., Li, A. Q., and Lin, P. H. (2006). A passive damping device with TiNi shape memory alloy rings and its properties. Mater. Sci. Eng. A 416 (1-2), 92–97. doi:10.1016/j.msea.2005.09.079
Fang, C., Liang, D., Zheng, Y., and Lu, S. (2022b). Seismic performance of bridges with novel SMA cable-restrained high damping rubber bearings against near-fault ground motions. Earthq. Eng. Struct. Dyn. 51 (1), 44–65. doi:10.1002/eqe.3555
Fang, C., Liang, D., Zheng, Y., Yam, M. C., and Sun, R. (2020b). Rocking bridge piers equipped with shape memory alloy (SMA) washer springs. Eng. Struct. 214, 110651. doi:10.1016/j.engstruct.2020.110651
Fang, C., Ping, Y., Chen, Y., Yam, M. C. H., Chen, J., Wang, W., et al. (2020a). Seismic performance of self-centering steel frames with SMA-viscoelastic hybrid braces. J. Earthq. Eng., 1–28. doi:10.1080/13632469.2020.1856233
Fang, C., Wang, W., He, C., and Chen, Y. (2017). Self-centring behaviour of steel and steel-concrete composite connections equipped with NiTi SMA bolts. Eng. Struct. 150, 390–408. doi:10.1016/j.engstruct.2017.07.067
Fang, C., Wang, W., Qiu, C., Hu, S., MacRae, G. A., Eatherton, M. R., et al. (2022a). Seismic resilient steel structures: a review of research, practice, challenges and opportunities. J. Constr. Steel Res. 191, 107172. doi:10.1016/j.jcsr.2022.107172
Fang, C., Wang, W., Ricles, J., Yang, X., Zhong, Q., Sause, R., et al. (2018b). Application of an innovative SMA ring spring system for self-centering steel frames subject to seismic conditions. J. Struct. Eng. (N. Y. N. Y). 144 (8), 04018114. doi:10.1061/(asce)st.1943-541x.0002127
Fang, C., Wang, W., Zhang, A., Sause, R., Ricles, J., Chen, Y., et al. (2019b). Behavior and design of self-centering energy dissipative devices equipped with superelastic SMA ring springs. J. Struct. Eng. (N. Y. N. Y). 145 (10), 04019109. doi:10.1061/(asce)st.1943-541x.0002414
Fang, C., Yam, M. C., Chan, T. M., Wang, W., Yang, X., Lin, X., et al. (2018a). A study of hybrid self-centring connections equipped with shape memory alloy washers and bolts. Eng. Struct. 164, 155–168. doi:10.1016/j.engstruct.2018.03.006
Fang, C., Yam, M. C., Lam, A. C., and Xie, L. (2014). Cyclic performance of extended end-plate connections equipped with shape memory alloy bolts. J. Constr. Steel Res. 94, 122–136. doi:10.1016/j.jcsr.2013.11.008
Fang, C., Yam, M. C., Lam, A. C., and Zhang, Y. (2015b). Feasibility study of shape memory alloy ring spring systems for self-centring seismic resisting devices. Smart Mat. Struct. 24 (7), 075024. doi:10.1088/0964-1726/24/7/075024
Fang, C., Yam, M. C., Ma, H., and Chung, K. F. (2015a). Tests on superelastic Ni–Ti SMA bars under cyclic tension and direct-shear: towards practical recentring connections. Mat. Struct. 48 (4), 1013–1030. doi:10.1617/s11527-013-0212-4
Fang, C., Zheng, Y., Chen, J., Yam, M. C., and Wang, W. (2019a). Superelastic NiTi SMA cables: thermal-mechanical behavior, hysteretic modelling and seismic application. Eng. Struct. 183, 533–549. doi:10.1016/j.engstruct.2019.01.049
Fang, C., Zhou, X., Osofero, A. I., Shu, Z., and Corradi, M. (2016). Superelastic SMA Belleville washers for seismic resisting applications: Experimental study and modelling strategy. Smart Mat. Struct. 25 (10), 105013. doi:10.1088/0964-1726/25/10/105013
Gao, N., Jeon, J. S., Hodgson, D. E., and DesRoches, R. (2016). An innovative seismic bracing system based on a superelastic shape memory alloy ring. Smart Mat. Struct. 25 (5), 055030. doi:10.1088/0964-1726/25/5/055030
Indirli, M., and Castellano, M. G. (2008). Shape memory alloy devices for the structural improvement of masonry heritage structures. Int. J. Archit. Herit. 2 (2), 93–119. doi:10.1080/15583050701636258
Jani, J. M., Leary, M., Subic, A., and Gibson, M. A. (2014). A review of shape memory alloy research, applications and opportunities. Mater. Des. 56, 1078–1113. doi:10.1016/j.matdes.2013.11.084
Lee, J. H., Choi, E., and Jeon, J. S. (2021). Experimental investigation on the performance of flexural displacement recovery using crimped shape memory alloy fibers. Constr. Build. Mater. 306, 124908. doi:10.1016/j.conbuildmat.2021.124908
Lee, J. H., Lee, K. J., and Choi, E. (2018). Flexural capacity and crack-closing performance of NiTi and NiTiNb shape-memory alloy fibers randomly distributed in mortar beams. Compos. Part B Eng. 153, 264–276. doi:10.1016/j.compositesb.2018.06.030
Liang, D., Zheng, Y., Fang, C., Yam, M. C., and Zhang, C. (2020). Shape memory alloy (SMA)-cable-controlled sliding bearings: Development, testing, and system behavior. Smart Mat. Struct. 29 (8), 085006. doi:10.1088/1361-665x/ab8f68
Liu, Y., Wang, H., Qiu, C., and Zhao, X. (2019). Seismic behavior of superelastic shape memory alloy spring in base isolation system of multi-story steel frame. Materials 12 (6), 997. doi:10.3390/ma12060997
Maletta, C., Filice, L., and Furgiuele, F. (2013). NiTi Belleville washers: Design, manufacturing and testing. J. intelligent material Syst. Struct. 24 (6), 695–703. doi:10.1177/1045389x12444490
Mas, B., Biggs, D., Vieito, I., Cladera, A., Shaw, J., Martínez-Abella, F., et al. (2017). Superelastic shape memory alloy cables for reinforced concrete applications. Constr. Build. Mater. 148, 307–320. doi:10.1016/j.conbuildmat.2017.05.041
McCormick, J., Tyber, J., DesRoches, R., Gall, K., and Maier, H. J. (2007). Structural engineering with NiTi. II: mechanical behavior and scaling. J. Eng. Mech. 133 (9), 1019–1029. doi:10.1061/(asce)0733-9399(2007)133:9(1019)
Mirzaeifar, R., DesRoches, R., and Yavari, A. (2011). A combined analytical, numerical, and experimental study of shape-memory-alloy helical springs. Int. J. Solids Struct. 48 (3-4), 611–624. doi:10.1016/j.ijsolstr.2010.10.026
Murasawa, G., Yoneyama, S., Sakuma, T., and Takashi, M. (2006). Influence of cyclic loading on inhomogeneous deformation behavior arising in NiTi shape memory alloy plate. Mat. Trans. 47 (3), 780–786. doi:10.2320/matertrans.47.780
Piedboeuf, M. C., Gauvin, R., and Thomas, M. (1998). Damping behaviour of shape memory alloys: Strain amplitude, frequency and temperature effects. J. Sound Vib. 214 (5), 885–901. doi:10.1006/jsvi.1998.1578
Qiu, C., Fang, C., Liang, D., Du, X., and Yam, M. C. (2020). Behavior and application of self-centering dampers equipped with buckling-restrained SMA bars. Smart Mat. Struct. 29 (3), 035009. doi:10.1088/1361-665x/ab6883
Qiu, C., and Zhu, S. (2017). Shake table test and numerical study of self‐centering steel frame with SMA braces. Earthq. Eng. Struct. Dyn. 46 (1), 117–137. doi:10.1002/eqe.2777
Quaglini, V., Dubini, P., Furinghetti, M., and Pavese, A. (2022). Assessment of scale effects in the experimental evaluation of the coefficient of friction of sliding isolators. J. Earthq. Eng. 26 (1), 525–545. doi:10.1080/13632469.2019.1687054
Reedlunn, B., Daly, S., and Shaw, J. (2013). Superelastic shape memory alloy cables: Part I–isothermal tension experiments. Int. J. Solids Struct. 50 (20-21), 3009–3026. doi:10.1016/j.ijsolstr.2013.03.013
Savi, M. A., Pacheco, P. M. C., Garcia, M. S., Aguiar, R. A., De Souza, L. F. G., Da Hora, R. B., et al. (2015). Nonlinear geometric influence on the mechanical behavior of shape memory alloy helical springs. Smart Mat. Struct. 24 (3), 035012. doi:10.1088/0964-1726/24/3/035012
Sherif, M. M., Khakimova, E. M., Ozbulut, O. E., Harris, D. K., and Ozyildirim, H. C. (2018). Behavior of mortar beams with randomly distributed superelastic shape memory alloy fibers. J. Intelligent Material Syst. Struct. 29 (4), 684–695. doi:10.1177/1045389x17721029
Sherif, M. M., and Ozbulut, O. E. (2017). Tensile and superelastic fatigue characterization of NiTi shape memory cables. Smart Mat. Struct. 27 (1), 015007. doi:10.1088/1361-665x/aa9819
Sherif, M. M., Tanks, J., and Ozbulut, O. E. (2017). Acoustic emission analysis of cyclically loaded superelastic shape memory alloy fiber reinforced mortar beams. Cem. Concr. Res. 95, 178–187. doi:10.1016/j.cemconres.2017.02.021
Shi, F., Zhou, Y., Ozbulut, O. E., and Cao, S. (2021). Development and experimental validation of anchorage systems for shape memory alloy cables. Eng. Struct. 228, 111611. doi:10.1016/j.engstruct.2020.111611
Speicher, M., Hodgson, D. E., DesRoches, R., and Leon, R. T. (2009). Shape memory alloy tension/compression device for seismic retrofit of buildings. J. Mat. Eng. Perform. 18 (5), 746–753. doi:10.1007/s11665-009-9433-7
Speicher, M. S., DesRoches, R., and Leon, R. T. (2011). Experimental results of a NiTi shape memory alloy (SMA)-based recentering beam-column connection. Eng. Struct. 33 (9), 2448–2457. doi:10.1016/j.engstruct.2011.04.018
Tamai, H., and Kitagawa, Y. (2002). Pseudoelastic behavior of shape memory alloy wire and its application to seismic resistance member for building. Comput. Mater. Sci. 25 (1-2), 218–227. doi:10.1016/s0927-0256(02)00266-5
Tobushi, H., Shimeno, Y., Hachisuka, T., and Tanaka, K. (1998). Influence of strain rate on superelastic properties of TiNi shape memory alloy. Mech. Mater. 30 (2), 141–150. doi:10.1016/s0167-6636(98)00041-6
Tyber, J., McCormick, J., Gall, K., DesRoches, R., Maier, H. J., Abdel Maksoud, A. E., et al. (2007). Structural engineering with NiTi. I: basic materials characterization. J. Eng. Mech. 133 (9), 1009–1018. doi:10.1061/(asce)0733-9399(2007)133:9(1009)
Wang, B., Zhu, S., Chen, K., and Huang, J. (2020). Development of superelastic SMA angles as seismic-resistant self-centering devices. Eng. Struct. 218, 110836. doi:10.1016/j.engstruct.2020.110836
Wang, B., and Zhu, S. (2018a). Cyclic tension–compression behavior of superelastic shape memory alloy bars with buckling-restrained devices. Constr. Build. Mater. 186, 103–113. doi:10.1016/j.conbuildmat.2018.07.047
Wang, B., and Zhu, S. (2018b). Superelastic SMA U-shaped dampers with self-centering functions. Smart Mat. Struct. 27 (5), 055003. doi:10.1088/1361-665x/aab52d
Wang, W., Fang, C., and Liu, J. (2016). Large size superelastic SMA bars: heat treatment strategy, mechanical property and seismic application. Smart Mat. Struct. 25 (7), 075001. doi:10.1088/0964-1726/25/7/075001
Wang, W., Fang, C., and Liu, J. (2017a). Self-centering beam-to-column connections with combined superelastic SMA bolts and steel angles. J. Struct. Eng. (N. Y. N. Y). 143 (2), 04016175. doi:10.1061/(asce)st.1943-541x.0001675
Wang, W., Fang, C., Yang, X., Chen, Y., Ricles, J., Sause, R., et al. (2017b). Innovative use of a shape memory alloy ring spring system for self-centering connections. Eng. Struct. 153, 503–515. doi:10.1016/j.engstruct.2017.10.039
Wang, W., Fang, C., Zhang, A., and Liu, X. (2019b). Manufacturing and performance of a novel self-centring damper with shape memory alloy ring springs for seismic resilience. Struct. Control Health Monit. 26 (5), e2337. doi:10.1002/stc.2337
Wang, W., Fang, C., Zhao, Y., Sause, R., Hu, S., Ricles, J., et al. (2019a). Self-centering friction spring dampers for seismic resilience. Earthq. Eng. Struct. Dyn. 48 (9), 1045–1065. doi:10.1002/eqe.3174
Wolons, D., Gandhi, F., and Malovrh, B. (1998). Experimental investigation of the pseudoelastic hysteresis damping characteristics of shape memory alloy wires. J. Intelligent Material Syst. Struct. 9 (2), 116–126. doi:10.1177/1045389x9800900205
Wu, Y. J., Xie, Q. F., Zhang, Y., Zhang, L. P., and Yang, H. F. (2022). Rotational performance of frictional glulam beam-to-column connections with shape memory alloy strips. J. Build. Eng. 45, 103520. doi:10.1016/j.jobe.2021.103520
Zhang, J., Fang, C., Yam, M. C., and Lin, C. (2022a). Fe-Mn-Si alloy U-shaped dampers with extraordinary low-cycle fatigue resistance. Engineering Structures. In press.
Zhang, R., Wang, W., Fang, C., Zhang, W., and Zhuang, L. (2022b). Self-centering devices with paralleled friction spring groups: development, experiment and system behavior. J. Earthq. Eng., 1–26. doi:10.1080/13632469.2021.2009059
Zheng, Y., Fang, C., Liang, D., and Sun, R. (2021). An innovative seismic-resilient bridge with shape memory alloy-washer-based footing rocking RC piers. J. Intelligent Material Syst. Struct. 32 (5), 549–567. doi:10.1177/1045389x20963167
Keywords: damping, shape memory alloy, seismic resilience, self-centering, critical review
Citation: Fang C and Yam MC (2023) Emerging superelastic SMA core damping elements for seismic application. Front. Built Environ. 8:953273. doi: 10.3389/fbuil.2022.953273
Received: 26 May 2022; Accepted: 11 July 2022;
Published: 04 January 2023.
Edited by:
Izuru Takewaki, Kyoto University, JapanReviewed by:
Christian Málaga-Chuquitaype, Imperial College London, United KingdomMarco Furinghetti, University of Pavia, Italy
Copyright © 2023 Fang and Yam. This is an open-access article distributed under the terms of the Creative Commons Attribution License (CC BY). The use, distribution or reproduction in other forums is permitted, provided the original author(s) and the copyright owner(s) are credited and that the original publication in this journal is cited, in accordance with accepted academic practice. No use, distribution or reproduction is permitted which does not comply with these terms.
*Correspondence: Cheng Fang, Y2hlbmdmYW5nQHRvbmdqaS5lZHUuY24=