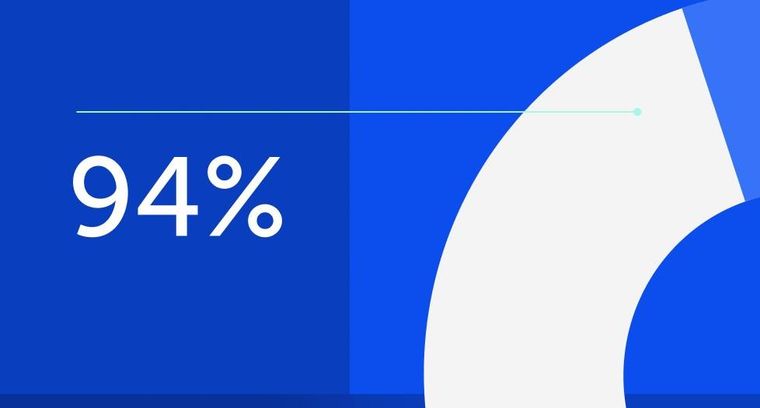
94% of researchers rate our articles as excellent or good
Learn more about the work of our research integrity team to safeguard the quality of each article we publish.
Find out more
ORIGINAL RESEARCH article
Front. Built Environ., 22 June 2022
Sec. Construction Management
Volume 8 - 2022 | https://doi.org/10.3389/fbuil.2022.909018
This article is part of the Research TopicInsights: Frontiers in Built EnvironmentView all 16 articles
Equipment sharing between contractors can relieve equipment shortages and enhance construction productivity. Previous studies focused on how to allocate cooperative gains of resource sharing among contractors, and yet how to ensure the owner and contractors form a coalition that contributes to maximizing resource-sharing gains still needs to be studied. This article examines the contract design problem of motivating the contractors and owner to willingly cooperate to increase the amount of shared equipment to an optimal level to maximize the project’s overall gain through equipment sharing. First, two trilateral equipment-sharing game models including a critical contractor, a non-critical contractor, and the owner are developed, which represent contractors’ different leadership positions in equipment sharing. Then, a set of revenue-sharing contracts are devised to compensate the contractors’ equipment-sharing cost and the owner’s extra duration reward cost by reassigning the consequently increased operation income. Eventually, a numerical study demonstrates that the proposed contracts can prompt members to make decisions according to an optimal solution to maximize the overall gains of equipment sharing, and each member’s gain and the construction duration compression are improved. This article contributes to onsite resource management by introducing a revenue-sharing contract to fairly compensate construction members’ equipment-sharing costs to achieve optimal cooperative gains.
Critical construction equipment can be found in large-scale infrastructure construction projects; examples of such equipment include tower belt conveyors (which pour massive, highly intensified concrete in hydropower station projects) and deepwater riprap leveling barges (which are used in the seabed-immersed tube construction of the Hong Kong-Zhuhai-Macao bridge). Gransberg et al. (2006) defined construction machines that undertake construction tasks on a critical path as critical equipment. Since it is imperative to identify which construction equipment assigned to the project can directly affect the project completion time, the concept of critical equipment includes two key points:
(1) The first is to check the float available in each activity in the schedule and classify the equipment associated with each critical activity as critical equipment.
(2) The second point is to declare the equipment that physically or technically cannot be increased within a specific period as critical equipment, letting the non-critical ones rise and fall based on the needs of the project.
To be clear, critical equipment in the research is defined as construction machines that are limited and fixed in quantity during a certain period and undertake construction tasks on a critical path. For example, the tunnel boring machine is critical equipment compared to excavators in a metro construction project. Due to the complex and uncertain characteristics of the construction environment, critical equipment shortages occasionally happen, thus resulting in project postponements and extra costs (Zhang et al., 2020). Though equipment sharing can mitigate critical equipment shortages and improve equipment productivity, contractors make decisions independently and lack mutual trust. Consequently, one contractor may incur equipment idleness, while another is experiencing equipment shortages, thereby decreasing the performance of the project (Bendoly et al., 2010). Thus, the key problem of contractors’ resource sharing is to design a contract to coordinate the conflicts of interests among contractors and the owner, which is grounded in the theory of construction supply chain management (CSCM) (Xue et al., 2007). CSCM focuses on cooperative relationships among members during construction engineering, and its objective is to optimize construction performance and improve the client’s utility with fewer costs (Feldman and Tamir, 2012). In previous studies of CSCM coordination, these selfish behaviors can be coordinated through mechanisms such as auction and negotiation, when the owner supplies most equipment resources (Fink, 2006). In auctions, contractors bid for resources within a certain time period, and the use of the resources is appointed to the highest bidder by the owner (Lee et al., 2003). In the negotiation mechanism, multiple contractors negotiate with a mediator (the owner or a general contractor), who allocates the shared resources according to protocols of minimizing project costs or delays (Lau et al., 2006). Auction and negotiation help bridge contractors’ onsite needs of resources and the owner’s resource allocation, which are implemented when most resources belong to the owner (Xia et al., 2008). However, in large-scale projects, critical equipment resources are often dispersedly owned by multiple contractors, thus limiting the coordinating effect of the owner, and requiring a coordination mechanism representing the contractors’ interests and decision-making.
To reflect the contractors’ interests during resource sharing, current studies applied cooperative game theories that focus on assigning overall cooperative gain to contractors (Gkatzelis et al., 2016; Moradi et al., 2019; Akhbari, 2020). These studies contribute to determining how to verify the fairness and validity of cooperative gain allocation rules. Nevertheless, in construction practice, how to devise a cooperative mechanism that ensures the owner and contractors act in ways consistent with the optimal resource-sharing solution still needs to be researched. Therefore, the authors consider the contract design problem of how to optimize every participant’s interest and to maximize the project gain of equipment sharing. The novelty of this research is proposing a cooperative contract based on revenue-sharing to motivate equipment-sharing members to comply with the equipment-sharing solution which optimizes the project’s overall gain through modeling a trilateral game among the critical contractor, noncritical contractor, and owner.
In this study, equipment sharing among multiple contractors and the owner is as follows: when the critical contractor (the contractor who undertakes construction activity on a critical path) needs to expedite construction time, he will pay rent to a noncritical contractor (the contractor who undertakes construction activity that is not on a critical path) for extra equipment. Then, by reducing the critical path duration, the critical contractor gains more time reward, and the owner benefits from the project’s running income due to early completion. The authors analyze and model the decision-making based on game theory: first, by modeling a trilateral game among the critical contractor, noncritical contractor, and owner, the individual equipment-sharing gains of these participants under a non-cooperative situation and construction system optimal equipment-sharing plan are determined. Second, concerning the effect of different equipment-sharing leaderships, several revenue-sharing contracts based on static transferable utility are devised to maximize all the participants’ gains when the participants make decisions according to the system optimal equipment-sharing scheme.
The remainder of the article is organized as follows: in Section 2, the authors review previous construction resource-sharing research and explain how the proposed coordination mechanism can coordinate the interest conflicts of the owner and contractors and realize the construction system optimum. In Section 3, the authors describe the basic problem in equipment sharing. In Section 4, Stackelberg game models under two leading scenarios are developed. Then, in Section 5, the system optimal equipment-sharing scheme is determined, and a revenue-sharing contract is devised. In Section 6, a numerical analysis is conducted to demonstrate the effect of the contract. Finally, the article concludes and discusses the authors’ research work.
In previous literature on the resource-sharing problem, the notation of resource sharing in the construction project is introduced by Perera (1983) regarding the resource allocation problem of linear construction. Perera applied resource-hour as the basic unit of sharing constrained resources (labor, equipment, etc.) between construction activities. By scheduling intermittent construction of noncritical activities, Karra and Nasr (1986) presented resource sharing between noncritical activity and critical activity to save the cost of renting equipment for critical activities. Xu et al. (2013) defined resource sharing as the optimal allocation of multiple types of equipment to multiple construction sites in several stages to raise construction productivity and reduce cost. Considering the above literature, the authors conclude in this study that resource sharing consists of cooperative behaviors in which contractors share the usage of equipment, thereby significantly affecting the construction schedule so that both their individual gains and construction schedule can be optimized.
Previous studies classify onsite construction resource-sharing problems as resource-constrained project scheduling problems (RCPSPs) and aim mainly to minimize construction costs and improve the construction schedule (Hartmann and Briskorn, 2010; Xu and Zeng, 2011; Kucuksayacigil and Ulusoy, 2020). Unlike traditional RCPSP studies, which regard equipment sharing as a solution to optimizing construction engineering objectives, this study sees the equipment-sharing problem as a process that coordinates the interest and decision-making of every participant. Previous research on the coordination mechanism of resource sharing can be analyzed from three perspectives: combinatorial auction, negotiation, and game theory. In a combinatorial auction, contractors bid for the price of using several resources at a certain amount for a certain duration. The owner who acts as the auctioneer will distribute the combinatorial resources to the highest bidder and then start the next round of the auction until all the contractors’ needs are satisfied (Confessore et al., 2007; Villahoz et al., 2010; Wang et al., 2014).
In a negotiation, the owner acts as a negotiator who receives conflicting resource demands from contractors and determines the resource allocation according to a series of negotiation rules that aim to achieve project objectives, such as minimizing the project cost or construction time (Homberger, 2007; Homberger, 2012). Compared to traditional resource allocation optimization methods, combinatorial auction and negotiation contribute to the timely reflection of resource demands from the contractors and can provide mutually beneficial contracts after multiple rounds of negotiations until contracts are accepted by both the owner and contractors. Additionally, the owner is assumed to own all the construction resources in the previous coordination mechanisms and is, therefore, responsible for determining the cooperative criterion in the coordination process and final determination of the resource allocation.
However, in large-scale construction projects, the owner’s coordinating role can be challenged by contractors who own most of the construction equipment; thus, both independent decision-making and coalition forming by contractors should be examined. Game theory, including non-cooperative game and cooperative game, presents a suitable analytical framework for decentralized decision-making during resource sharing (Cachon and Zipkin, 1999).
Non-cooperative game theory can facilitate predicting the expected gains and behaviors of decision-makers who aim at maximizing individual interests. Samaddar et al. (2006) applied the Stackelberg game model to simulate joint knowledge resource sharing between corporations and determined the requirements of resource sharing between new and established firms. Moufid et al. (2017) modeled cheating behaviors during equipment sharing (such as hiding sharing time and lowering maintenance cost in production equipment sharing) among small-sized manufacturing enterprises and revealed the relationship between the probability of detecting cheating and detection cost. Concerning construction equipment-sharing research, Liu et al. (2018) suggested the motivative effect of a time incentive applied by the owner can benefit equipment sharing among contractors by developing the leader–follower game model. When there is no binding cooperative contract or authority to coordinate, non-cooperative game theory can help studies on resource sharing establish theoretical frameworks to investigate the influence of self-interested behaviors of resource-sharing members on their cooperation results.
Different from the non-cooperative game for maximizing individual interests, if cooperation can bring more income than competition, the players in an equipment-sharing game will choose to form a cooperative coalition and decide the fair and efficient allocation of the benefits of resource-sharing cooperation. The allocation methods of cooperative benefits are applied in construction resource-sharing scenarios such as cost savings/profit allocation among partnering firms, delay penalties and expedition rewards allocation among activities, and apportionment of construction costs for a public project (Eissa et al., 2021a). Considering the minimal equipment reserve for each contractor to carry out construction work, Asgari et al. (2014) developed a cooperative game model of sharing temporary and constant equipment among activities and allocated cooperative gains according to a Shapley value solution. By integrating the sharing cost of equipment operation, transportation, and installation, Hafezalkotob et al. (2018) proposed a cooperative game model of resource sharing between different construction stages to optimize construction system gain. Moradi et al. (2019) established a robust optimization model of sharing resources that are uncertain in availability during uncertain activity duration and compared subcontractors’ satisfaction levels to different cooperative gain allocation rules. In the project-scheduling problem of sharing renewable resources between subprojects, Akhbari (2020) applied the Shapley–Shubik power index and DP (propensity to disrupt) value to evaluate the stability and fairness of allocation rules, including the Shapley value, nucleolus, and Nash–Harsanyi solution. Eissa et al. (2021b) developed a conceptual framework to allocate profit among construction joint ventures (CJVs) based on each firm’s marginal contribution in order to reduce profit-share-related disagreements among CJV members. Li et al. (2021) proposed a multi-agent-based cooperative approach to mitigate resource competition of decentralized project managers and reach a negotiation protocol of resource allocation with a central decision-maker of all projects.
Previous studies on cooperative game theory shed light on how to allocate cooperative gains and how to verify the fairness and validity of allocation rules (Kemahlioglu-Ziya and Bartholdi, 2011; Guajardo and Rönnqvist, 2015). However, in practice, the pursuit by contractors of their own self-interests may impede the implementation of gain allocation methods. Thus, the authors expand the cooperative gain allocation research on traditional cooperative resource leveling to coordination mechanism design, which focuses on how to prompt decision-makers to willingly achieve the system optimum.
As in a BOT project, the concession period defines the time span in which the private investor has the right to commercially operate the infrastructure facility before it is transferred back to the government. Since the concession period is fixed, early completion of construction will result in a longer operation period which brings additional income (such as highway tolls and business advertisements). Considering construction contractors’ equipment sharing can reduce the delay of the construction project, the financing model BOT (Build-Operate-Transfer) is used to describe the functional relationship between equipment sharing and the owner’s interest. In a BOT (Build-Operate-Transfer) construction project, a critical contractor, a noncritical contractor, and the owner together constitute the basic equipment-sharing problem. Specifically, to prevent construction delay, the owner rewards contractors for early completion and penalizes them for delays. When additional equipment is needed to compress the construction duration to gain more time reward or lessen a penalty, a critical contractor will share equipment from other noncritical contractors. Additionally, the compression of the construction period can produce more operation income for the owner since the operation period will be extended in the fixed concession period of the BOT project (Zhang et al., 2016). Decision-making in equipment sharing involves two steps: first, the critical contractor (who needs equipment) proposes an equipment rent price to the noncritical contractor (who offers extra equipment). Then, taking the possible time penalty and construction cost into account, the noncritical contractor will determine the amount of shared equipment to maximize his or her own interest in responding to the critical contractor’s request. The gains of both contractors will then reach equilibrium after the contractors’ negotiation. The equipment-sharing process is modeled as a Stackelberg game in which the critical contractor acts as the leader and the noncritical contractor acts as the follower. The game model is presented in Figure 1.
During equipment sharing between contractors, bargaining power, which represents the right to decide equipment rent price, usually determines the leadership of the decision-making process. In practice, the construction time of critical contractors who undertake critical activities is directly associated with the project schedule. Thus, the critical contractor often possesses the bargaining power and acts as the leader of equipment sharing. However, if more than one critical contractor proposes identical equipment demands, if more critical machines break down, or if equipment demand surges due to design modification, the bargaining power will be handed over to the noncritical contractors, who have excessive equipment resources. In this scenario, equipment sharing can be modeled as a Stackelberg game in which the noncritical contractor acts as the leader and the critical contractor acts as the follower. In this article, the effects of two different leadership scenarios on the game equilibrium of the owner and contractors are analyzed.
In this article, the owner and contractors are assumed to be rational individuals who seek to maximize their own interests. Moreover, each player’s information is assumed to be symmetric, i.e., the owner and contractors have full information on their income and payment.
Three important parameters are introduced in this section: reward/penalty type, construction cost, and amount of shared equipment. To be specific, the reward/penalty type reflects the owner’s influence on the contractors’ construction duration. Construction cost represents the relationship between the contractor’s gain and construction duration. The amount of shared equipment shows the quantitative effect of equipment sharing on each contractor’s construction duration. Based on these parameters, gains of the owner and contractors are associated, and how both participate in equipment sharing is revealed.
In the construction industry, the reward/penalty type for construction duration is usually implemented in linear form; therefore, the reward for early completion or punishment for the delay is based on a fixed reward/penalty coefficient (Jaraiedi et al., 1995; Shr and Chen, 2003). The function of reward/penalty is
The reward/penalty amount of the noncritical contractor is expressed as follows:
Construction cost can be approximatively described as a convex function of construction duration (Callahan et al., 1992; Shr and Chen, 2003). In this study, the relationship between construction cost and duration is expressed as the quadratic function
The construction cost–duration function of the noncritical contractor is expressed as follows:
Considering critical activities will generally be allocated with more resources (manpower, equipment, and materials) than noncritical activities, the authors assume that duration changes for critical contractors consume more cost than those for noncritical contractors (
To describe the relationship between the amount of shared equipment and construction cost, the amount of shared equipment is represented by a machine team marked as Mt, which means one team of operators working on one piece of equipment in a unit period. The construction production of the machine team is marked as Dw. While performing construction tasks, the productivity of the same equipment is assumed to be identical for every contractor and match their estimated level. The amount of the critical contractor’s own equipment is marked as ma, and the contract duration before and after equipment sharing is marked as da1 and da2, respectively. Since the total construction task equals the product of production per unit time and construction duration, the critical contractor’s construction amount is expressed as
Similarly, the duration variation of the noncritical contractor is given as follows:
A list of mentioned symbols and descriptions is presented in Table 1.
The critical contractor’s gain consists of three parts: contract income, which includes a fixed fee (Ca) and a reward/penalty (Wa); the equipment rent payment, which is the product of the rent price (P) and shared equipment amount (Mt); and the construction cost (C(da)). The gain function before equipment sharing is as follows:
The critical contractor’s gain function after equipment sharing is as follows:
As the leader in the Stackelberg equipment-sharing game, the critical contractor will decide the optimal rent price P before the noncritical contractor makes a decision. The decision-making problem is as follows:
The gain of the noncritical contractor consists of three parts: contract income, which includes a fixed fee (Cb) and a reward/penalty (Wb); equipment rent income, which is the product of the rent price (P) and shared equipment amount (Mt); and the construction cost (C(db)). The gain function before equipment sharing is as follows:
The noncritical contractor’s gain function after equipment sharing is as follows:
As the follower in the equipment-sharing game, the non-critical contractor’s decision-making problem is to decide the optimal shared equipment amount Mt according to the critical contractor’s optimal rent price to maximize the gain of the noncritical contractor. The decision-making problem is as follows:
Based on backward induction, the solution of the Stackelberg equipment-sharing game is obtained in three steps (Rasmusen, 2006). First, in response to any certain rent price P from the critical contractor, the noncritical contractor’s optimal shared amount Mt is determined by solving the derivative of the gain function (
Second, as the second derivative of the gain function
The final step is to substitute the equilibrium rent price P (Eq. 14) in Eq. 13; thus, the noncritical contractor’s equilibrium shared equipment amount is as follows:
Equation 15 shows that only when the noncritical contractor’s original equipment amount is higher than that of the critical contractor (mb > ma), equipment sharing will occur (Mt*>0). This observation can be explained by comparing the duration variations of both contractors (Eqs 5, 6). Once the shared amount Mt is determined, the more original equipment there is, the less the duration variation and duration reward/penalty. In other words, only when the noncritical contractor’s penalty for the delay is less than the critical contractor’s reward can equipment sharing be profitable and applicable to both contractors.
By substituting Eq. 15 in the critical contractor’s duration variation (Eq. 5), the duration variation of the construction project is as follows:
By substituting the equilibrium value of P (Eq. 14) and Mt (Eq. 15) in the critical contractor’s gain function (Eq. 8), we can obtain the critical contractor’s optimal gain:
By a similar calculation, the noncritical contractor’s optimal gain is as follows:
From the perspective of whole-life management, early completion of construction will result in additional income (such as highway tolls and business advertisements) in the project operation period (Chen and Ma, 2007; Lv et al., 2015). As in a BOT project, the concession period of the owner is certain and marked as dc, and the expected unit operation income is marked as r. The operation period dr will be prolonged when the construction period da is shortened, thus resulting in extra operation income r. Thus, operation income Ur becomes a function of the construction duration:
In this study, we assume the owner pays a fixed total price and duration reward/penalty to the contractors. The contract payment to both contractors is marked as Pa+b.
Since the owner’s gain consists of contract payment Pa+b and operation income Ur, the objective of the owner is to determine the optimal reward/penalty coefficient Io to maximize his or her gain.
Proposition 1:. Uo(Io) is convex with respect to Io.Proof: By substituting Eqs 5, 6, and 15 in Eq. 21, we obtain
By calculating and simplifying the second derivative of Uo, we obtain
The optimal reward/penalty coefficient Io is determined by solving the first derivative of the owner’s gain function (
The owner’s optimal gain is as follows:
The results of Eqs 14–18 show that when the contractors’ original equipment amounts and duration-cost coefficients are fixed, the equilibrium values of the equipment-sharing game are determined by the owner’s decision, which is the reward/penalty coefficient. In other words, the contractors’ optimal equipment rent price, shared amount, and gains all depend on the optimal reward/penalty coefficient. Therefore, by substituting Eq. 22 in Eqs 14, 15, 17, and 18, the equilibrium values of the owner and two contractors are calculated, as shown in Table.2.
When demand for equipment resources surpasses supply, the noncritical contractor will gain bargaining power and take leadership of the equipment sharing. In this situation, the game sequence is in reverse: first, the noncritical contractor will offer equipment rent price P. Then, considering the rent payment and duration reward, the critical contractor will respond to the offered rent price by deciding its optimal shared equipment amount Mt.
As the leader in the equipment-sharing game, the noncritical contractor will decide the optimal rent price P to maximize his or her gain.
In reaction to the noncritical contractor’s rent price, the critical contractor will determine the optimal shared equipment amount Mt to maximize his or her gain. The critical contractor’s decision-making is described as follows:
The solution of the equilibrium values in Scenario II is similar to the solution in Scenario I, and the values are presented in Table 3.
By comparing the rent price and shared amount in both scenarios, we obtain
As Eqs 26 and 27 show, the equipment rent price is lower in Scenario I than that in Scenario II. Furthermore, as a1 > b1 and mb > ma, the shared equipment amount is higher in Scenario I than that in Scenario II (Mt*>Mtl).
Proposition 2. When the critical contractor leads the equipment sharing (Scenario I), the shared equipment amount is higher and the equipment rent price is lower than in Scenario II.By comparing the contractors’ gains in both scenarios, we obtain
Proposition 3:. When the non-critical contractor leads the equipment sharing, the critical contractor’s gain will decrease, and the non-critical contractor’s gain will increase.The difference in the owner’s gains in both scenarios is as below:
Proposition 4. The owner’s gain is higher in Scenario I than that in Scenario II.From Proposition 2–4, it can be concluded that when the noncritical contractor leads the equipment sharing, the critical contractor has to pay more rent but will acquire fewer equipment. Since the noncritical contractor takes the privilege of setting the equipment rent price, he or she will select the price that benefits merely himself or herself. The critical contractor has no choice but to follow the noncritical contractor’s decision. As a result, through offering equipment and receiving rent, the noncritical contractor actually obtains most of the construction duration reward belonging to the critical contractor. When the reward/penalty coefficient remains the same, fewer equipment will be shared in Scenario II. Consequently, the reduction of the construction duration becomes limited, and the owner’s operation income falls.A comparison of the values obtained in the two scenarios is presented in Table 4.
In construction engineering, as owners and contractors are subjects who aim to optimize their self-interest, their resource allocation scheme is not always consistent with the utility of the construction engineering system (Meng and Gallagher, 2012; Kerkhove and Vanhoucke, 2016). In the construction engineering system, if there exists an optimal solution that maximizes the total gain of all equipment-sharing members, obtaining this solution will be the objective of the coordination mechanism (Kuipers et al., 2013). The gain of the system Usys consists of the gains of the owner Uo, critical contractor Ua, and noncritical contractor Ub:
Equation 31 indicates that the system gain Usys includes only the owner’s operation income and the construction costs of both contractors. By substituting Eqs 3–6 in Eq. 31, the simplified gain function of the system shows the system gain Usys is a quadratic function of the shared equipment amount Mt.
Proposition 5:. Usys is convex with respect to Mt.Proof: By calculating the second derivative of system gain, we obtain
The systematic optimal amount of shared equipment is marked as Mts. By solving the equation of the first derivative of the system gain function (
By comparing the optimal shared equipment amounts of Scenarios I (
The owner’s decisions (
A comparison of the owner’s decision variable Io and gain Uo in Scenarios I–III is presented in Table 5.Based on the results in Table 5, in Scenarios I and II where individual interests are maximized, the reward/penalty coefficients are less than those in Scenario III where the system gain is optimized (Ios*>Io* and Iosl > Iol). Additionally, the owner’s gains are higher in Scenarios I and II than those in Scenario III. Specifically, to achieve system optimum, the owner should raise the reward/penalty coefficient to a certain value (Ios* and Iosl); therefore, the owner would pay more reward to reduce the same construction duration. In contrast, contractors will benefit from the owner’s system optimal decision. As a consequence, the owner will retain his or her individual interest-maximizing decisions (Io* and Iol) instead of the system optimal decisions (Ios* and Iosl).According to the above analysis, for the sake of the construction engineering system optimum, the owner and contractors should sign revenue-sharing contracts, which fairly distribute operational income brought by equipment sharing so that the owner can willingly raise the reward/penalty coefficient according to the system optimum.
To limit the members’ selfish behaviors during equipment sharing, a coordination mechanism based on revenue-sharing contracting is designed to allocate cooperative system gain (Wang et al., 2004). The contracts must comply with two requirements:
(1) The members’ gain must not be lower than the gain before the revenue-sharing contract is signed.
(2) The contracts must ensure only the system optimal solution can bring the members the highest gain so that the members will not deviate from the system optimal solution. The revenue-sharing contracts are presented below:
When the critical contractor leads the equipment sharing (Scenario I), the critical contractor’s gain function under the contract is
When the non-critical contractor leads the equipment sharing (Scenario II), the critical contractor’s gain function under the contract is
In both Scenarios I and II, the efficiency principle should be satisfied:
The authors adopt a revenue-sharing contract based on a transferable subsidy (Cachon and Lariviere, 2005). The form of the contract is Ti = kiIo + wi, i = a, b, o. The first part of the contract represents every member’s extra subsidy (which is linear in the owner’s decision variable Io), and ki represents the subsidy that each member has to pay when the owner raises/decreases a unit of the reward/penalty coefficient. Furthermore, ki ensures the derivative of every member’s gain function under contract will be 0 when the member makes a system optimal decision. For example,
In this study, to reflect the effect of different bargaining powers of the contractors and the owner on the equipment-sharing game, each member’s gain under the contract is assigned a share proportional to the gain that the individual optimal gain represents over the system gain before contracting (Audy et al., 2012; Guajardo and Rönnqvist, 2015), as follows:
Proposition 6:. When the critical contractor leads the equipment sharing (Scenario I), under the contracts Ta = -koIo + wa, Tb = wb, and To = koIo-wa-wb, the owner will select the system optimal reward/penalty coefficient
The non-critical contractor’s gain function under the contract is as follows:
By conducting a backward induction, after the contracts are signed, the critical contractor’s optimal rent price will be
The noncritical contractor’s optimal shared equipment amount will be
The owner’s gain function under the contract is as follows:
Since the second derivative of the gain function is negative (
According to the contract, as
Proposition 7:. When the noncritical contractor leads the equipment sharing (Scenario II), under the contracts Ta = -joIo + wa, Tb = wb, and To = joIo-wa-wb, the owner will select the system optimal reward/penalty coefficient
Constants wa and wb are applied to ensure the owner and contractors will receive the same gain proportion in system gain before contracting. In addition, the importance of subsidy coefficients ko and jo is that members obtain the maximized system gain share only when each member makes a decision that complies with the system optimum instead of the individual optimum.
For a better illustration of the effect of the developed revenue-sharing contracts, this article used a numerical example with two different scenarios. Consider a large construction project in which two contractors undertake construction tasks in critical and noncritical paths, respectively, and the owner applies a duration reward/penalty to both contractors to control the project schedule. During the construction period, the fixed contract price of a critical contractor is $50 million, and the contract construction duration of the project is 300 days. Additionally, the fixed contract price of a noncritical contractor is $10 million, and the contract construction duration of the project is 200 days. Before the contractors start equipment sharing, the critical contractor owns 10 pieces of a certain kind of heavy machine, and the noncritical contractor owns 22 pieces of an identical machine. In the construction phase of the projects, contractors are encouraged to spontaneously share heavy machines among themselves to save construction costs and to be rewarded for early completion (or to avoid a penalty). The values of other parameters in this section are based on the authors’ investigations of two Chinese large-scale infrastructure projects (the Xiangjiaba hydropower station and the Hong Kong-Zhuhai-Macao bridge). The logical relationship of the parameters is based on the analysis of the functional relationship between construction cost and time (Callahan et al., 1992; Shr and Chen, 2006). The parameters are listed in Table 6.
The contracts can be obtained according to Section 5:
Figure 2 shows the owner’s gain functions before and after revenue-sharing contracts are signed. The owner will raise his reward/penalty coefficient from Io∗ = 137.5 (Eq. 22) before contracting to Ios∗ = 322.1 (Eq. 33) after contracting. Moreover, the owner’s gain rises from Uo = 497.53 (Eq. 23) before contracting to
Table 7 shows the comparisons of the construction system members’ gains and the construction durations in Scenario I when the coordination mechanism is implemented. When revenue-sharing contracts are put into effect, the construction system gain increases from Usys = 782.67 (Eq. 31) to Usys = 1,165.45 (Eq. 31). In addition, the construction duration is reduced by 8.9 days. The proportions of members’ gains to system gain remain the same before and after contracting. In other words, the system gain allocation rules of the contracts are based on the members’ individual optimal gains as determined by the bargaining power of the members during equipment sharing.
The contracts are obtained according to the coordination mechanism design section:
Figure 5 shows the owner’s gain functions before and after revenue-sharing contracts are signed. The owner will raise his reward/penalty coefficient from Iol = 137.5 (Table 3) before contracting to Iosl = 502.9 (Eq. 34) after contracting. The owner’s gain rises from
Table 8 shows the comparisons of the construction system members’ gains and the construction durations in Scenario Ⅱ. When revenue-sharing contracts are implemented, the construction system gain increases from Usys = 550.16 (Eq. 31) to Usys = 1,165.45 (Eq. 31). In addition, the construction duration is reduced by 11.29 days.
By analyzing the results of Section 6, the authors can make three conclusions as follows:
Conclusion 1: In both Scenarios I and II, the revenue-sharing contracts can motivate the owner and contractors to willingly make decisions according to the system optimal solution.
The objective of the revenue-sharing contracts is to compensate the owner by reallocating system gain so that the owner can select the system optimal reward/penalty coefficient Io, which is the key decision-making variable to achieve system optimum according to the coordination mechanism design section. Under the contracts, to make the owner raise the reward/penalty coefficient, both the critical and noncritical contractors should share certain parts of their gains as subsidies with the owner.
Conclusion 2: In both Scenarios I and II, the gain of the equipment-sharing leader is higher than the gain of the follower.
According to the leader–follower game models of equipment sharing, the leader’s gain is always higher than the follower’s gain. The stronger bargaining power (the critical contractor’s influence on duration and the noncritical contractor’s equipment ownership), which is possessed by the leader, gives the leader a first-move advantage. The leader can always make a decision to benefit himself more than the follower, while the follower can react only after the leader has decided the rent price.
Conclusion 3: Before contracting, both the construction system gain and duration compression are higher in Scenario I than in Scenario II.
When the noncritical contractor (instead of the critical contractor) leads the equipment sharing, the critical contractor needs to pay more rent to acquire the same equipment amount. As a result, the cost of equipment sharing rises, and the amount of shared equipment drops. Furthermore, the construction duration decreases; this decrease will reduce the system income in the project operation period.
Based on the above analysis and conclusions, several managerial implications are provided for construction engineering practitioners and academics:
(1) Equipment is shared only when the critical contractor’s equipment rent is sufficient, which fairly compensates the noncritical contractor’s delay penalty and construction cost.
(2) To acquire sufficient equipment and income, the critical contractor needs to avoid sharing equipment with a noncritical contractor who has more bargaining power. Additionally, the critical contractor can cooperate with more than one noncritical contractor to strengthen his leadership.
(3) To ensure the sustainability of equipment sharing cooperation, the owner can raise the reward/penalty coefficient of the critical contractor (thereby creating more reward to rent equipment) or reduce the reward/penalty coefficient of the non-critical contractor (thereby lowering the rent price), since the owner can profit from the project’s operation income with more shared-equipment.
(4) While designing the construction contracts, the keynote is to find the decision-making variable that directly determines the system gain by analyzing interactions among the contractors and the owner. Then, through subsidies to the key decision-making variables, such as time incentives and shared-equipment amount, the construction engineering members will comply with the system optimal solution.
In this research, the problem of construction equipment sharing between contractors in leadership and non-leadership roles during the construction period is studied. Based on analyzing the effect of the duration reward/penalty on equipment-sharing productivity and operation income for the owner brought by duration compression, two trilateral equipment-sharing game models of the owner, critical contractor, and noncritical contractor are developed. To maximize system gain and reduce duration, revenue-sharing contracts based on static transferable utility are devised to motivate equipment-sharing members to make decisions according to the system optimal solution. The numerical study demonstrates that the revenue-sharing contracts can make the owner and contractors willingly select the system optimal solution rather than the individual optimal solution, no matter which contractor leads the equipment sharing. Under the contracts, the gains of all members will increase, and the construction duration is compressed.
This study contributes to the academic research on construction engineering for building a trilateral game model of the decision-making among the owner and contractors. By comparing the effects of different leadership roles and duration reward/penalty on equipment-sharing results, researchers can further study bilateral and trilateral games of construction engineering corporations. However, this article applies revenue-sharing contracting to the coordination problem of construction resource sharing. Concerning resource cooperation between contractors, unlike traditional studies that focus on cooperative gain allocation rules design, the authors focus on contracting, which can diminish members’ selfish deviation from the system optimal solution. The contract design pattern in this article can help project management better utilize incentive contracting and select resource-sharing partners.
During contract designing, since equipment-sharing members are independent from each other and make decisions on their own, the composition of each member’s gain function needs in-depth study; the elements needing in-depth study include construction cost, duration reward/penalty, operation income, and equipment rent. Furthermore, when the system optimal solution is determined, how to assign system gain fairly and efficiently to members is also important to the availability of the signed contracts. In this article, to better reflect the equipment-sharing leadership and bargaining power of each member, the authors adopt a proportional allocation method in which every member’s proportionate share of system gain under the contracts stays the same as the share before contracting. However, in construction engineering practice, both the gain compositions and leaderships of contractors are more complex. Thus, system gain allocation rules based on the construction onsite situation that can promptly express the needs of construction firms should be studied in further research.
The authors consider the equipment-sharing problem while assuming the critical path of construction activities will not change during equipment sharing. However, in practice, equipment sharing may cause several changes to the critical path, such as a critical path turns to a noncritical path and one critical path grows to two or more critical paths. When the critical path changes, contractors who need extra equipment should not only carefully select equipment suppliers but also consider the following additional construction cost and potential equipment shortage.
As the objective of equipment sharing is to reduce project delay, when the noncritical path becomes a new critical one, more shared equipment will not reduce the construction time of the new critical path but prolong it and induce an unnecessary delay penalty. At this moment, equipment sharing will come to an end. It means that the contractors’ game of equipment sharing will end before it reaches equilibrium. In other words, the amount of shared equipment and contractors’ gains are determined by the construction schedule (the time difference between the critical path and noncritical path), instead of the leader–follower game equilibrium. As the total equipment sharing gain is fixed before equipment sharing, the bargaining game theory provides a systematic and analytical framework of how to allocate the gains between the contractors, which mainly focus on price negotiation, revenue and risk allocation, and concession period negotiation in the construction field (Nash, 1950; Rubinstein, 1982). In the next research, the authors will apply the bargaining game theory to the problem of equipment sharing gain allocation.
In addition, equipment-sharing models can be extended to more general forms, such as one critical contractor sharing with two or more non-critical contractors or multiple contractors sharing with each other to meet their specific construction requirements, thereby leading to more complicated game models. Finally, this study assumes that game information is symmetric to all members. While in an unsymmetrical information situation, contractors and the owner may reach other kinds of equilibria, such as a Bayesian Nash equilibrium. Then, the contracts in this article need to be redesigned.
The original contributions presented in the study are included in the article/supplementary material; further inquiries can be directed to the corresponding author.
ZL conducted scientific research, performed numerical study, and wrote the paper. HW and YX reviewed and edited the manuscript drafts. All authors were involved in conceiving the study, data analysis, and structure of the paper.
This work has been supported by the National Natural Science Foundation of China (Nos. 71821001 and 71390524).
Author ZL was employed by the company China Construction Eighth Engineering Division Corp., Ltd.
The remaining authors declare that the research was conducted in the absence of any commercial or financial relationships that could be construed as a potential conflict of interest.
All claims expressed in this article are solely those of the authors and do not necessarily represent those of their affiliated organizations, or those of the publisher, the editors, and the reviewers. Any product that may be evaluated in this article, or claim that may be made by its manufacturer, is not guaranteed or endorsed by the publisher.
The authors thank the editors and reviewers for their beneficial comments and suggestions, which have helped them improve this article.
Akhbari, M. (2020). Contractors’ Partnership in Project Resource Management Application of Cooperative Game Theory Approach. Sci. Iran. 27 (1), 469–480.
Asgari, S., Afshar, A., and Madani, K. (2014). Cooperative Game Theoretic Framework for Joint Resource Management in Construction. J. Constr. Eng. Manage. 140 (3), 04013066. doi:10.1061/(asce)co.1943-7862.0000818
Audy, J.-F., D’Amours, S., and Rönnqvist, M. (2012). An Empirical Study on Coalition Formation and Cost/Savings Allocation. Int. J. Prod. Econ. 136 (1), 13–27. doi:10.1016/j.ijpe.2011.08.027
Bendoly, E., Perry-Smith, J. E., and Bachrach, D. G. (2010). The Perception of Difficulty in Project-Work Planning and its Impact on Resource Sharing. J. Operations Manag. 28 (5), 385–397. doi:10.1016/j.jom.2009.11.011
Cachon, G. P., and Lariviere, M. A. (2005). Supply Chain Coordination with Revenue-Sharing Contracts: Strengths and Limitations. Manag. Sci. 51 (1), 30–44. doi:10.1287/mnsc.1040.0215
Cachon, G. P., and Zipkin, P. H. (1999). Competitive and Cooperative Inventory Policies in a Two-Stage Supply Chain. Manag. Sci. 45 (7), 936–953. doi:10.1287/mnsc.45.7.936
Callahan, M. T., Quackenbush, D. G., and Rowings, J. E. (1992). Construction Project Scheduling. New York: McGraw-Hill.
Chen, J. H., and Ma, S. H. (2007). A Revenue Incentive Model of Project Duration Coordination between Project Corporation and Contractor. Chin. J. Manag. Sci. 15 (3), 114–122.
Confessore, G., Giordani, S., and Rismondo, S. (2007). A Market-Based Multi-Agent System Model for Decentralized Multi-Project Scheduling. Ann. Oper. Res. 150 (1), 115–135. doi:10.1007/s10479-006-0158-9
Eissa, R., Eid, M. S., and Elbeltagi, E. (2021b). Conceptual Profit Allocation Framework for Construction Joint Ventures: Shapley Value Approach. J. Manage. Eng. 37 (3), 04021016. doi:10.1061/(asce)me.1943-5479.0000911
Eissa, R., Eid, M. S., and Elbeltagi, E. (2021a). Current Applications of Game Theory in Construction Engineering and Management Research: A Social Network Analysis Approach. J. Constr. Eng. Manage. 147 (7), 04021066. doi:10.1061/(asce)co.1943-7862.0002085
Feldman, M., and Tamir, T. (2012). Conflicting Congestion Effects in Resource Allocation Games. Operations Res. 60 (3), 529–540. doi:10.1287/opre.1120.1051
Fink, A. (2006). Supply Chain Coordination by Means of Automated Negotiations between Autonomous agentsMultiagent Based Supply Chain Management. Berlin: Springer, 351–372. doi:10.1007/978-3-540-33876-5_13
Gkatzelis, V., Kollias, K., and Roughgarden, T. (2016). Optimal Cost-Sharing in General Resource Selection Games. Operations Res. 64 (6), 1230–1238. doi:10.1287/opre.2016.1512
Gransberg, D. D., Popescu, C. M., and Ryan, R. C. (2006). Construction Equipment Management for Engineers, Estimators, and Owners. London: Taylor & Francis.
Guajardo, M., and Rönnqvist, M. (2015). Cost Allocation in Inventory Pools of Spare Parts with Service-Differentiated Demand Classes. Int. J. Prod. Res. 53 (1), 220–237. doi:10.1080/00207543.2014.948577
Hafezalkotob, A., Hosseinpour, E., Moradi, M., and Khalili-Damghani, K. (2018). Multi-resource Trade-Off Problem of the Project Contractors in a Cooperative Environment: Highway Construction Case Study. Int. J. Manag. Sci. Eng. Manag. 13 (2), 129–138. doi:10.1080/17509653.2017.1323240
Hartmann, S., and Briskorn, D. (2010). A Survey of Variants and Extensions of the Resource-Constrained Project Scheduling Problem. Eur. J. Operational Res. 207 (1), 1–14. doi:10.1016/j.ejor.2009.11.005
Homberger, J. (2007). A Multi-Agent System for the Decentralized Resource-Constrained Multi-Project Scheduling Problem. Int. Trans. Oper. Res. 14 (6), 565–589. doi:10.1111/j.1475-3995.2007.00614.x
Homberger, J. (2012). A (μ, λ)-coordination Mechanism for Agent-Based Multi-Project Scheduling. OR Spectr. 34 (1), 107–132. doi:10.1007/s00291-009-0178-3
Jaraiedi, M., Plummer, R. W., and Aber, M. S. (1995). Incentive/Disincentive Guidelines for Highway Construction Contracts. J. Constr. Eng. Manag. 121 (1), 112–120. doi:10.1061/(asce)0733-9364(1995)121:1(112)
Karaa, F. A., and Nasr, A. Y. (1986). Resource Management in Construction. J. Constr. Eng. Manag. 112 (3), 346–357. doi:10.1061/(asce)0733-9364(1986)112:3(346)
Kemahlioglu -Ziya, E., and Bartholdi, J. J. (2011). Centralizing Inventory in Supply Chains by Using Shapley Value to Allocate the Profits. Manuf. Serv. Operations Manag. 13 (2), 146–162.
Kerkhove, L. P., and Vanhoucke, M. (2016). Incentive Contract Design for Projects: The Owner׳s Perspective. Omega 62, 93–114. doi:10.1016/j.omega.2015.09.002
Kucuksayacigil, F., and Ulusoy, G. (2020). Hybrid Genetic Algorithm for Bi-objective Resource-Constrained Project Scheduling. Front. Eng. Manag. 7 (3), 426–446. doi:10.1007/s42524-020-0100-x
Kuipers, J., Mosquera, M. A., and Zarzuelo, J. M. (2013). Sharing Costs in Highways: A Game Theoretic Approach. Eur. J. Operational Res. 228 (1), 158–168. doi:10.1016/j.ejor.2013.01.018
Lau, J. S. K., Huang, G. Q., Mak, K. L., and Liang, L. (2006). Agent-based Modeling of Supply Chains for Distributed Scheduling. IEEE Trans. Syst. Man. Cybern. A 36 (5), 847–861. doi:10.1109/tsmca.2005.854231
Lee, Y.-H., Kumara, S. R. T., and Chatterjee, K. (2003). Multiagent Based Dynamic Resource Scheduling for Distributed Multiple Projects Using a Market Mechanism. J. Intelligent Manuf. 14 (5), 471–484. doi:10.1023/a:1025753309346
Li, F., Xu, Z., and Li, H. (2021). A Multi-Agent Based Cooperative Approach to Decentralized Multi-Project Scheduling and Resource Allocation. Comput. Industrial Eng. 151, 106961. doi:10.1016/j.cie.2020.106961
Liu, Z., Wang, H., and Li, H. (2018). Model of Equipment Sharing between Contractors on Construction Projects. J. Constr. Eng. Manag. 144 (6), 04018039. doi:10.1061/(asce)co.1943-7862.0001485
Lv, J. N., Ye, G., Liu, W., Shen, L. Y., and Wang, H. X. (2015). Alternative Model for Determining the Optimal Concession Period in Managing BOT Transportation Projects. J. Manag. Eng. 31 (4). doi:10.1061/(asce)me.1943-5479.0000291
Meng, X., and Gallagher, B. (2012). The Impact of Incentive Mechanisms on Project Performance. Int. J. Proj. Manag. 30 (3), 352–362. doi:10.1016/j.ijproman.2011.08.006
Moradi, M., Hafezalkotob, A., and Ghezavati, V. (2019). Robust Resource-Constrained Project Scheduling Problem of the Project's Subcontractors in a Cooperative Environment under Uncertainty: Social Complex Construction Case Study. Comput. Industrial Eng. 133, 19–28. doi:10.1016/j.cie.2019.04.046
Moufid, M. E., Roy, D., Hennequin, S., and Cortade, T. (2017). Game Theory Model of a Production Resource Sharing Problem: Study of Possible Cheatings. IFAC-PapersOnline 50 (1), 10532–10537. doi:10.1016/j.ifacol.2017.08.1301
Perera, S. (1983). Resource Sharing in Linear Construction. J. Constr. Eng. Manag. 109 (1), 102–111. doi:10.1061/(asce)0733-9364(1983)109:1(102)
Rasmusen, E. (2006). Games and Information: An Introduction to Game Theory. third edition. New York: Wiley-Blackwell.
Rubinstein, A. (1982). Perfect Equilibrium in a Bargaining Model. Econometrica 50 (1), 97–110. doi:10.2307/1912531
Samaddar, S., Nargundkar, S., and Daley, M. (2006). Inter-organizational Information Sharing: The Role of Supply Network Configuration and Partner Goal Congruence. Eur. J. Operational Res. 174 (2), 744–765. doi:10.1016/j.ejor.2005.01.059
Shr, J. F., and Chen, W. T. (2003). A Method to Determine Minimum Contract Bids for Incentive Highway Projects. Int. J. Proj. Manag. 21 (8), 601–615. doi:10.1016/s0263-7863(02)00056-x
Shr, J. F., and Chen, W. T. (2006). Functional Model of Cost and Time for Highway Construction Projects. J. Mar. Sci. Technol. 14 (3), 127–138. doi:10.51400/2709-6998.2066
Villahoz, J. J. L., del Olmo Martínez, R., and Arauzo, A. A. (2010). Combinatorial Auctions for Coordination and Control of Manufacturing MAS: Updating Prices Methods. Proc. 5th Int. Workshop Soft Comput. Models Industrial Appl. Guimaraes, Portugal 73, 27–30. doi:10.1007/978-3-642-13161-5_4
Wang, H., Guo, M., and Efstathiou, J. (2004). A Game-Theoretical Cooperative Mechanism Design for a Two-Echelon Decentralized Supply Chain. Eur. J. Operational Res. 157 (2), 372–388. doi:10.1016/s0377-2217(03)00233-9
Wang, L., Zhan, D. C., and Nie, L. S. (2014). Multi-project Decentralized Scheduling Problem Solving by Market Mechanism. Jisuanji Jicheng Zhizao Xit. Integr. Manuf. Syst. 20 (8), 1969–1979.
Xia, Y., Chen, B., and Kouvelis, P. (2008). Market-based Supply Chain Coordination by Matching Suppliers' Cost Structures with Buyers' Order Profiles. Manag. Sci. 54 (11), 1861–1875. doi:10.1287/mnsc.1080.0900
Xu, J., Meng, J., Zeng, Z., Wu, S., and Shen, M. (2013). Resource Sharing-Based Multiobjective Multistage Construction Equipment Allocation under Fuzzy Environment. J. Constr. Eng. Manage. 139 (2), 161–173. doi:10.1061/(asce)co.1943-7862.0000593
Xu, J., and Zeng, Z. (2011). Applying Optimal Control Model to Dynamic Equipment Allocation Problem: Case Study of Concrete-Faced Rockfill Dam Construction Project. J. Constr. Eng. Manage. 137 (7), 536–550. doi:10.1061/(asce)co.1943-7862.0000325
Xue, X., Wang, Y., Shen, Q., and Yu, X. (2007). Coordination Mechanisms for Construction Supply Chain Management in the Internet Environment. Int. J. Proj. Manag. 25 (2), 150–157. doi:10.1016/j.ijproman.2006.09.006
Zhang, J., Zheng, H., He, W., and Huang, W. (2020). West-East Gas Pipeline Project. Front. Eng. Manag. 7 (1), 163–167. doi:10.1007/s42524-019-0056-x
Keywords: equipment sharing, revenue-sharing contract, construction time-cost function, duration reward/penalty, construction time and cost
Citation: Liu Z, Wang H and Xie Y (2022) Revenue-Sharing Contract Design for Construction Onsite Equipment Sharing. Front. Built Environ. 8:909018. doi: 10.3389/fbuil.2022.909018
Received: 31 March 2022; Accepted: 11 May 2022;
Published: 22 June 2022.
Edited by:
Yongkui Li, Tongji University, ChinaReviewed by:
Jiayu Chen, City University of Hong Kong, Hong Kong SAR, ChinaCopyright © 2022 Liu, Wang and Xie. This is an open-access article distributed under the terms of the Creative Commons Attribution License (CC BY). The use, distribution or reproduction in other forums is permitted, provided the original author(s) and the copyright owner(s) are credited and that the original publication in this journal is cited, in accordance with accepted academic practice. No use, distribution or reproduction is permitted which does not comply with these terms.
*Correspondence: Yong Xie, eHlodXN0QDE2My5jb20=
Disclaimer: All claims expressed in this article are solely those of the authors and do not necessarily represent those of their affiliated organizations, or those of the publisher, the editors and the reviewers. Any product that may be evaluated in this article or claim that may be made by its manufacturer is not guaranteed or endorsed by the publisher.
Research integrity at Frontiers
Learn more about the work of our research integrity team to safeguard the quality of each article we publish.