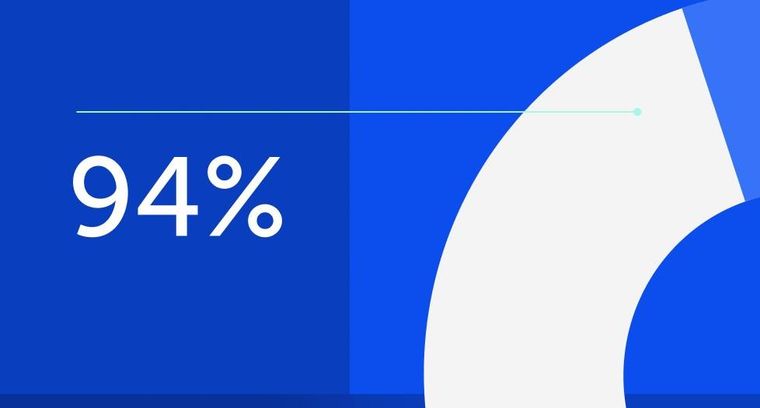
94% of researchers rate our articles as excellent or good
Learn more about the work of our research integrity team to safeguard the quality of each article we publish.
Find out more
ORIGINAL RESEARCH article
Front. Built Environ., 30 December 2022
Sec. Indoor Environment
Volume 8 - 2022 | https://doi.org/10.3389/fbuil.2022.1061760
This article is part of the Research TopicHealthy and Energy Efficient BuildingsView all 13 articles
This paper presents an advanced borehole heat exchanger that has been developed in order to apply a ground source heat pump to a volcanic island where the existing borehole heat exchangers are inapplicable by local ordinance. The advanced borehole heat exchanger was fabricated and installed at a verification-test site to evaluate its heat capacity in terms of refrigeration ton (RT). The proposed heat exchanger was also compared with the conventional heat exchanger that was made of high-density polyethylene (HDPE) heat exchanger. The thermal response test was carried out by flowing water at various temperatures into the heat exchangers at the fixed flow rate of 180 L/min. The results revealed that the maximum heat capacity for the developed heat exchanger was measured at 63.9 kW, which is 160% higher than that of the high-density polyethylene heat exchanger (39.9 kW). It was also found that the developed HX has the highest heat gain achieving 94 kW as compare to 21 kW for high-density polyethylene-Hx.
Fossil fuel-based power generation has achieved economies of scale through large-scale power generation complexes and, thus, has contributed to the policy goal of an inexpensive and stable power supply (Lanzi et al., 2011; Bogdanov et al., 2021). Fossil fuels, however, are also the cause of environmental pollution, in particular, carbon dioxide and particulate matter emissions, which exacerbate climate change (Shahzad et al., 2017; Alrowais et al., 2020; Gani, 2021; Martins et al., 2021). Accordingly, interest in the development of renewable energy industries and eco-friendly power generation has increased worldwide, focusing on the social, environmental, and technological aspects of renewables (Oh et al., 2012; 2019; Chen et al., 2020a; 2020b; 2021; Hoseinzadeh and Heyns, 2020; Jamil et al., 2021; Hoseinzadeh and Stephan Heyns, 2022).
Jeju self-governing province is promoting the expansion of renewable energy by conducting the “Carbon Free Island Jeju 2030” project, which is a low carbon green growth model to cope with climate change as well as to establish zero net energy island (Lee et al., 2021; Mun et al., 2021). Although the installed capacities of solar and wind energy are 130 MW and 270 MW, which is account for 60.7% of the total electricity demand of Jeju, their annual utilization rates are only 23% and 13%, respectively due to unstable weather conditions (Ko et al., 2019).
Geothermal heat pump systems tend to have higher energy efficiency than conventional air source heat pump systems, having no equipment exposed to the atmosphere, and are more stable than other heat sources in heating and cooling cycles throughout the year (Tye-Gingras and Gosselin, 2014). Most of the existing geothermal cooling and heating facilities in Korea were installed in the early 2000s, and ground heat exchanger technologies (e.g., vertical closed-loop type and open-loop type) suitable for domestic soil structures have been continuously developed (Yearbook of Regional Energy Statistics, 2022). It is difficult, however, to apply these technologies to high-density subsoils such as the porous basalt foundation (similar to granite) found on Jeju Island. The geology of the island, which was formed by volcanic activity, is characterized by repeated basalt and pyroclastic layers (clinker, scoria). In addition, small-scale rocks have accumulated—rather than extensive rock formation—in many areas due to volcanic eruptions and lava flows (Park et al., 2021). Consequently, structures that allow surface air or water to be easily introduced into the ground are prevalent, allowing for the relatively free flow of water and air.
The Hydrogeologic characteristic of the island hinders the employment of the existing borehole heat exchanger such as a vertical closed-loop geothermal heat exchanger and a horizontal closed-loop heat exchanger that extract geothermal energy by conduction heat transfer with the ground. Furthermore, the drilling cost is relatively high compared to inland areas since the thickness of the soil layer is thin as well as the ground is mainly composed of rocks. It is also banned to use an open-loop geothermal system on Jeju Island due to regulations that prohibits the use of groundwater as an energy source.
For such reasons, Jeju Island has been recognized as an area where the use of geothermal energy is inappropriate. To address this problem, underground air in basalt layers has been utilized as the heat source in systems installed in agricultural facilities on Jeju Island (Kang and Lim, 2016). The geothermal energy harvested by such method, however, has not been certified as a renewable energy source for the reason that it is different from the existing geothermal energy utilization method. Adoption of the technology has been hampered due to the high relative humidity of the underground air as well as the claim that radon exists (in trace amounts) and that the process releases underground CO2.
Recently, the land use ordinances of Jeju Island have been revised to allow the installation of heat exchangers in groundwater, given that geothermal energy based on groundwater has a very high heat capacity, the feasibility of such systems is expected to be high. Although cooling and heating systems that use groundwater heat sources were supplied after the ordinance revision, the heat exchangers used in these systems are made of high-density polyethylene (HDPE), which has also been used in underground air source systems.
Many studies have been conducted both theoretically and experimentally in order to improve the thermal energy system’s efficiency (Ng et al., 2021; Alizadeh et al., 2022; Hossein Zolfagharnasab et al., 2022). Hossein Zolfagharnasab et al. (2022) applied porous materials to a shell and tube heat exchanger and investigated the heat transfer rate. They concluded that the proposed porous-filled heat exchanger exhibits 60% higher efficiency compared to the conventional heat exchanger. Ng et al. (2021) developed a thermodynamic platform that can be used to assess the energy efficiency of combined power generation and desalination plants. The proposed platform was evaluating the energy efficiency of any thermal system by introducing the primary energy concept. Alizadeh et al. (2022) experimentally investigated heat pipes in order to improve the energy performance of a heat-recovery system. Their result revealed that the heat-pipe heat exchanger could reduce the consumption of natural gas by 510,132 SCM a year.
In this study, an advanced heat exchanger made of a stainless with high thermal conductivity was developed to increase the utilization of geothermal heat, including groundwater heat. In addition, the heat capacities of the developed heat exchangers were compared with HDPE heat exchanger in order to assess the feasibility of geothermal energy systems suitable for the particular geology of Jeju Island.
A borehole was excavated using the method stipulated in the ordinance of Jeju Island. Based on the excavation point, concrete is poured into the area of at least 3 m (horizontal) by 3 m (vertical) at a thickness of 30 cm or more and cured for at least 24 h. Excavation to a certain depth (35 m by the ordinance) is then performed with a diameter of 450 mm, and grouting is performed to prevent groundwater pollution caused by the collapse of the perforation area. Afterward, the second perforation is performed to the required depth with a 250 mm borehole. In addition, a corrosion-resistant casing must be installed at the top of the borehole to prevent water pollution and damage to the perforation area.
In Table 1, we present the dimensions of the borehole constructed for the experiment. The borehole was constructed in accordance with the regulations of the ordinance, and the total borehole depth was 65 m due to the underground water level.
The flow velocity of the groundwater varies depending on the altitude difference. Due to the presence of pyroclastic layers, upper groundwater also falls from the top to the bottom of the borehole. The largest problem with the commonly used HDPE heat exchangers is that they are lost from the inlet/outlet headers due to the flow of groundwater and the impact of falling upper groundwater. This inhibits the function of the exchanger and causes groundwater pollution. It is also difficult to insert the exchangers into the borehole during the installation because of the high buoyancy and low thermal conductivity of the plastic units. Owing to the low thermal conductivity, it is also questionable whether such units can acquire sufficient thermal energy from the groundwater.
To address these problems, a heat exchanger with pipes made of STS316 (stainless steel) was developed. The new unit enables the use of welding or flanges, is applicable to a site where a longer heat exchanger is needed due to the high altitude, causes little concern over the separation caused by the pressure of upper groundwater, and has high thermal conductivity and corrosion resistance. The largest benefit of this type of heat exchanger is that it is possible to remove it for repair or replacement without damage to the borehole. The geometry of the two different heat exchangers is shown in Figure 1. In the case of the HDPE heat exchanger (Figure 1A), eight U-tubes from the heat exchanger supply header inside the casing at the top of the borehole are connected to the return header. A U-tube has an outer diameter of 34 mm, a thickness of 3.5 mm, and a length of 70 m. The newly developed STS316 heat exchanger is shown in Figure 1B.
FIGURE 1. Borehole heat exchangers used in Jeju island.(A) HDPE heat exchanger, (B) Stainless steel heat exchanger.
The two main pipes (inlet and return pipes) with a diameter of 48.6 mm and a thickness of 2.8 mm are surrounded by the coil-type pipe, with a diameter of 16 mm and a thickness of 2.1 mm, to increase the heat transfer area. The heat exchanger comprises 15 coil heat exchangers as it is distributed to three coil heat exchangers per 6 m of the main pipe. The circulating water descends to the location of groundwater through the inlet pipe and passes through the coil-type pipe and the return pipe, resulting in heat exchange. The total length of the main pipe is 70 m, and that of the coil-type pipe is 810 m. The dimensions of each heat exchanger are given in Table 2.
A facility cultivation farm located in Doryeon-dong, Jeju-si, was selected as the experimental site at which we compared the performance of the heat exchangers. After drilling two holes according to the dimensions in Table 1, the HDPE and STS316 heat exchangers were inserted, and their thermal characteristics were compared and analyzed.
The borehole heat exchangers are generally evaluated by thermal response testing, which is a method for determining the thermal properties of ground materials, mainly the thermal conductivity and ground temperature. The heat transfer fluid (HTF) circulates inside the heat exchanger while it either absorbs or releases heat from/to the grout and the surrounding soil depending on the operation mode (heating or cooling). Thus, the rate of heat transfer (W/m) that can be extracted by the heat transfer is approximated by measuring the thermal conductivity. In this study, however, thermal response testing is unable to use since the heat transfer between HFT in the heat exchanger and the groundwater mainly takes place by convection mechanism. Hence, it is difficult to find out the rate of heat transfer for the proposed borehole heat exchangers without measuring the conductivity.
In this study, therefore, we calculated the rate of heat transfer in the unit of Watt by measuring the temperature of the outlet water that passed through the heat exchanger while inputting constant energy into the heat exchanger.
The rate of heat transfer can be expressed using Eq. 1 and the mean temperature with Eq. 2.
where
In the experimental apparatus of this study, the inlet temperature (
Figure 2 shows a schematic of the experimental apparatus. The main devices include a 100 kW hot water boiler to increase the temperature of the influent, a circulating water pump, sensors to measure the temperature and flow rate, and the data-recording device. First, each ground heat exchanger was filled with water (the circulating water). The circulation pump was operated with no energy input until the temperature of the groundwater and circulating water was maintained at a steady state. The initial temperature of the circulating water was then determined.
The flow rate was maintained at a constant level, approximately 180 LPM. The inlet temperature of the circulating water was increased by operating the boiler. A steady state was assumed to have been reached when the mean temperature of the inlet and outlet temperatures (Tm) showed no change for more than 10 min, at which point the next experiment was performed by inputting additional energy. Through this stepwise input of energy, three experiments were performed for the HDPE heat exchanger and four experiments for the stainless steel heat exchanger.
Because the heat release capacity of the portable experimental apparatus could not exceed 100 kW, all experiments were carried out within this range. The experimental conditions for the HDPE heat exchanger and the newly developed STS316 heat exchanger are shown in Table 3. In the case of the HDPE heat exchanger, three experiments were performed while changing the inlet temperature of the circulating water from 21.6°C to 36.2°C. As for the STS316 heat exchanger, experiments were performed in four cases while changing the inlet temperature from 19.7°C to 27.1°C. A constant flow rate of approximately 180 LPM was maintained. The surface area was 59.8°m2 for the HDPE heat exchanger and 51.4°m2 for the STS316 heat exchanger.
Figures 3, 4 show the inlet/outlet temperatures, mean temperature, and heat gain obtained from Eq. 1 for the HDPE and STS316 heat exchangers, respectively. The inlet/outlet temperatures of the HDPE heat exchanger continuously and gradually increased, and it took considerable time to reach a steady state. In the case of STS316, however, a steady state was reached rapidly—within approximately 25 min after the temperature rise.
In Figure 3, CASE 1 represents the experimental data when the mean inlet temperature of the circulating water in the HDPE exchanger was set to 21.6°C. The mean outlet temperature was 20.7°C, and the heat gain was approximately 11.2 kW. In CASE 2, the mean inlet temperature of the circulating water was set to 28.7°C. The mean outlet temperature was 26.7°C, and the heat gain was approximately 25.2 kW. In CASE 3, the mean inlet temperature of the circulating water was set to 36.2°C. The mean outlet temperature was 33.1°C, and the heat gain was approximately 39.9 kW.
In Figure 4, CASE 4 represents the experimental data when the mean inlet temperature of the circulating water in the STS316 exchanger was set to 19.7°C. The mean outlet temperature was 18.1°C, and the heat gain was approximately 20.4 kW. In CASE 5, the mean inlet temperature of the circulating water was set to 21.6°C. The mean outlet temperature was 19.2°C, and the heat gain was approximately 30.7 kW. In CASE 6, the mean inlet temperature of the circulating water was set to 23.4°C. The mean outlet temperature was 20.2°C, and the heat gain was approximately 40.9 kW. In CASE 7, the mean inlet temperature of the circulating water was set to 27.1°C. The mean outlet temperature was 22.1°C, and the heat gain was approximately 63.9 kW.
In the heat capacity test, the maximum heat capacity was found to be approximately 39.9 kW for the HDPE pipe and 63.9 kW for the STS316 pipe, indicating that the heat gain of the STS316 heat exchanger can be approximately 160% higher than that of the HDPE heat exchanger.
Figure 5 shows the variations of the heat gain for two different heat exchangers with the outlet temperatures of circulating water. It is noteworthy that in the cooling mode, the circulating water enters in to the condenser of a water-to-water heat pump and its temperature rises by the refrigerant that circulate the loop of heat pump and then it flows back to the borehole heat exchanger to release the heat to the groundwater. From this graph, we can predict the heat gain for the heat exchangers at any given outlet temperature. For instance, when the inlet temperature to the condenser of a heat pump is at 25°C which is a test condition under KS B 8292 standards for a water-to-water geothermal heat pump unit, the heat gain for STS heat exchanger is equal to 94 kW. It can be easily inferred that the performance of STS heat exchanger is four times higher than that of the HDPE heat exchanger.
In this study, an advanced borehole exchanger was developed and investigated by comparing it performance with a conventional high-density polyethylene (HDPE) exchanger. The key findings from this study include:
1) The heat gain of the STS heat exchanger was found to be approximately four times higher than that of the HDPE heat exchanger under the same borehole conditions and ground loop system test conditions (KS B 8292; water-to-water geothermal heat pump unit), notwithstanding that the heat transfer area of the STS exchanger is approximately 15% smaller.
2) When the outlet temperature was measured while changing the inlet temperature of the circulating water in each heat exchanger, it was found that considerable time was required for the HDPE heat exchanger to reach a steady state. In contrast, the STS316 heat exchanger reached a steady state approximately 25 min after the temperature rise.
3) The difference in performance is probably due to the difference in thermal properties of the HDPE and STS heat exchangers; the STS unit has a relatively higher thermal conductivity, which is favorable for acquiring heat from the ground. Thus, the STS heat exchanger has a higher heat gain.
It is expected that the results of this study will be useful in designing new heat exchangers in the Jeju area. Further research should be carried out on ground heat exchangers made of different materials other than STS and HDPE heat exchangers. Furthermore, it is expected that the COP can be improved up to five when a water-to-water heat pump uses the proposed bore hole heat exchanger in Jeju island.
The original contributions presented in the study are included in the article/supplementary material, further inquiries can be directed to the corresponding author.
JK: data collection and draft manuscript. Y-MK: data analysis. YK: figures. QC: study conception. CX: result interpretation. SO: manuscript preparation and funding.
This work was supported by the Renewable Surplus Sector Coupling Technology Program of the Korea Institute of Energy Technology Evaluation and Planning (KETEP) granted financial resource from the Ministry of Trade, Industry and Energy, Republic of Korea (No. 20226210100050) and supported by Korea Institute of Planning and Evaluation for Technology in food and Planning (IPET) funded by Ministry of Agriculture, Food and Rural Affairs (MAFRA) (No. 320048-3).
JK was employed by Intertech Co., Ltd.
The remaining authors declare that the research was conducted in the absence of any commercial or financial relationships that could be construed as a potential conflict of interest.
All claims expressed in this article are solely those of the authors and do not necessarily represent those of their affiliated organizations, or those of the publisher, the editors and the reviewers. Any product that may be evaluated in this article, or claim that may be made by its manufacturer, is not guaranteed or endorsed by the publisher.
Alizadeh, A., Ghadamian, H., Aminy, M., Hoseinzadeh, S., Khodayar Sahebi, H., and Sohani, A. (2022). An experimental investigation on using heat pipe heat exchanger to improve energy performance in gas city gate station. Energy 252, 123959. doi:10.1016/j.energy.2022.123959
Alrowais, R., Qian, C., Burhan, M., Ybyraiymkul, D., Shahzad, M. W., and Ng, K. C. (2020). A greener seawater desalination method by direct-contact spray evaporation and condensation (DCSEC): Experiments. Appl. Therm. Eng. 179, 115629. doi:10.1016/j.applthermaleng.2020.115629
Bogdanov, D., Ram, M., Aghahosseini, A., Gulagi, A., Oyewo, A. S., Child, M., et al. (2021). Low-cost renewable electricity as the key driver of the global energy transition towards sustainability. Energy 227, 120467. doi:10.1016/j.energy.2021.120467
Chen, Q., Alrowais, R., Burhan, M., Ybyraiymkul, D., Shahzad, M. W., Li, Y., et al. (2020a). A self-sustainable solar desalination system using direct spray technology. Energy 205, 118037. doi:10.1016/j.energy.2020.118037
Chen, Q., Muhammad, B., Akhtar, F. H., Ybyraiymkul, D., Muhammad, W. S., Li, Y., et al. (2020b). Thermo-economic analysis and optimization of a vacuum multi-effect membrane distillation system. Desalination 483, 114413. doi:10.1016/j.desal.2020.114413
Chen, Q., Burhan, M., Shahzad, M. W., Ybyraiymkul, D., Akhtar, F. H., Li, Y., et al. (2021). A zero liquid discharge system integrating multi-effect distillation and evaporative crystallization for desalination brine treatment. Desalination 502, 114928. doi:10.1016/j.desal.2020.114928
Gani, A. (2021). Fossil fuel energy and environmental performance in an extended STIRPAT model. J. Clean. Prod. 297, 126526. doi:10.1016/j.jclepro.2021.126526
Hoseinzadeh, S., and Heyns, P. S. (2020). Thermo-structural fatigue and lifetime analysis of a heat exchanger as a feedwater heater in power plant. Eng. Fail Anal. 113, 104548. doi:10.1016/j.engfailanal.2020.104548
Hoseinzadeh, S., and Stephan Heyns, P. (2022). Development of a model efficiency improvement for the designing of feedwater heaters network in thermal power plants. J. Energy Resour. Technol. 144, 072102. doi:10.1115/1.4054196
Hossein Zolfagharnasab, M., Zamani Pedram, M., Hoseinzadeh, S., and Vafai, K. (2022). Application of Porous-Embedded shell and tube heat exchangers for the Waste heat Recovery Systems. Appl. Therm. Eng. 211, 118452. doi:10.1016/j.applthermaleng.2022.118452
Jamil, M. A., Goraya, T. S., Ng, K. C., Zubair, S. M., Xu, B. B., and Shahzad, M. W. (2021). Optimizing the energy recovery section in thermal desalination systems for improved thermodynamic, economic, and environmental performance. Int. Commun. Heat Mass Transf. 124, 105244. doi:10.1016/j.icheatmasstransfer.2021.105244
Kang, Y.-K., and Lim, T.-S. (2016). The Analysis of heating performance of heat pump system for agricultural facility using underground air in Jeju area - focused on the Jeju Area -. KIEAE J. 16, 109–114. doi:10.12813/kieae.2016.16.6.109
Ko, W., Lee, J., and Kim, J. (2019). The effect of a renewable energy certificate incentive on mitigating wind power fluctuations: A case study of Jeju island. Appl. Sci. 9, 1647. doi:10.3390/app9081647
Lanzi, E., Verdolini, E., and Haščič, I. (2011). Efficiency-improving fossil fuel technologies for electricity generation: Data selection and trends. Energy Policy 39, 7000–7014. doi:10.1016/j.enpol.2011.07.052
Lee, J., Lee, J., and Wi, Y.-M. (2021). Impact of revised time of use tariff on variable renewable energy curtailment on Jeju island. Electron. (Basel) 10, 135. doi:10.3390/electronics10020135
Martins, T., Barreto, A. C., Souza, F. M., and Souza, A. M. (2021). Fossil fuels consumption and carbon dioxide emissions in G7 countries: Empirical evidence from ARDL bounds testing approach. Environ. Pollut. 291, 118093. doi:10.1016/j.envpol.2021.118093
Mun, H., Moon, B., Park, S., and Yoon, Y. (2021). A study on the economic feasibility of stand-alone microgrid for carbon-free island in Korea. Energies (Basel) 14, 1913. doi:10.3390/en14071913
Ng, K. C., Burhan, M., Chen, Q., Ybyraiymkul, D., Akhtar, F. H., Kumja, M., et al. (2021). A thermodynamic platform for evaluating the energy efficiency of combined power generation and desalination plants. NPJ Clean. Water 4, 25. doi:10.1038/s41545-021-00114-5
Oh, S. J., Lee, Y. J., Chen, K., Kim, Y. M., Lim, S. H., and Chun, W. (2012). Development of an embedded solar tracker for the enhancement of solar energy utilization. Int. J. Energy Res. 36, 249–258. doi:10.1002/er.1813
Oh, S. J., Shahzad, M. W., Burhan, M., Chun, W., Kian Jon, C., KumJa, M., et al. (2019). Approaches to energy efficiency in air conditioning: A comparative study on purge configurations for indirect evaporative cooling. Energy 168, 505–515. doi:10.1016/j.energy.2018.11.077
Park, J. B., Koh, G. W., Jeon, Y., Park, W. B., Moon, S. H., and Moon, D. C. (2021). Geology and volcanism of hyeongjeseom (islet) volcano, Jeju island. Econ. Environ. Geol. 54, 187–197. doi:10.9719/EEG.2021.54.2.187
Shahzad, M. W., Burhan, M., Ang, L., and Ng, K. C. (2017). Energy-water-environment nexus underpinning future desalination sustainability. Desalination 413, 52–64. doi:10.1016/j.desal.2017.03.009
Tye-Gingras, M., and Gosselin, L. (2014). Generic ground response functions for ground exchangers in the presence of groundwater flow. Renew. Energy 72, 354–366. doi:10.1016/j.renene.2014.07.026
Yearbook of Regional Energy Statistics (2022). Yearbook of regional energy statistics. Available at: http://www.kesis.net.
HDPE high-density polyethylene
RT refrigeration ton
STS stainless steel
Q heat transfer rate (kW)
T temperature (oC)
Keywords: borehole heat exchanger, ground-source heat pump, volcanic island, renewable energy, thermal response test
Citation: Kim JW, Kim Y-M, Ko YJ, Chen Q, Xin C and Oh SJ (2022) Study on an advanced borehole heat exchanger for ground source heat pump operating in volcanic island: Case study of Jeju island, South Korea. Front. Built Environ. 8:1061760. doi: 10.3389/fbuil.2022.1061760
Received: 05 October 2022; Accepted: 19 December 2022;
Published: 30 December 2022.
Edited by:
Xiaolin Wang, University of Tasmania, AustraliaReviewed by:
Muhammad Wakil Shahzad, Northumbria University, United KingdomCopyright © 2022 Kim, Kim, Ko, Chen, Xin and Oh. This is an open-access article distributed under the terms of the Creative Commons Attribution License (CC BY). The use, distribution or reproduction in other forums is permitted, provided the original author(s) and the copyright owner(s) are credited and that the original publication in this journal is cited, in accordance with accepted academic practice. No use, distribution or reproduction is permitted which does not comply with these terms.
*Correspondence: Seung Jin Oh, b2hzODY4MEBraXRlY2gucmUua3I=
Disclaimer: All claims expressed in this article are solely those of the authors and do not necessarily represent those of their affiliated organizations, or those of the publisher, the editors and the reviewers. Any product that may be evaluated in this article or claim that may be made by its manufacturer is not guaranteed or endorsed by the publisher.
Research integrity at Frontiers
Learn more about the work of our research integrity team to safeguard the quality of each article we publish.