- Department of Civil Engineering, Aalto University, Espoo, Finland
Improved productivity and the elimination of waste are key goals for lean methods in construction production control. One such lean method is a kit-based logistics management in which task-based materials are delivered just-in-time and aligned with assembly operations on-site. Digital platforms could enable a situational awareness of work and material flows, potentially increasing the benefit and applicability of kitting. The aim of the current research is to utilize a real-time indoor tracking of material and labor flows to evaluate an assembly kit–based management of construction projects. We propose a linked data framework to connect labor, material, and scheduling information to integrate heterogenous data. The contribution of the study is threefold: first, a feasible method is developed to enable real-time detection of work and material flows inside the building for logistics management purposes. Second, several key performance indicators for effective evaluation of kit-based production flow in construction are provided, which allows management to tackle root causes of problems and to enhance timely and productive logistic solutions. Thirdly, by applying the linked data method, the study introduces a novel approach to integrate heterogenous data from both indoor tracking and schedules.
Introduction
Construction sites are frequently thought of as chaotic environments in which waste occurs as a consequence of complex on-site management. As a result, sites suffer from productivity loss and waste related to crews’ waiting times, rework, unnecessary movement, material handling, and unused inventories in workspaces and of materials (Sacks et al., 2010). This complexity has motivated the development of several production control approaches in construction (Zhao et al., 2019). Lean construction principles are often applied to enhance workflows and eliminate waste by focusing on workflow variability to improve overall project performance (Thomas et al., 2002). The variability of flow is a key root cause of waste (Seppänen et al., 2010), and therefore measuring and addressing variability is important to eliminate waste and enhance productivity. In this regard, field material management has become a crucial management process (Grau et al., 2009) to address the variability of material flows, to minimize waste, and to ultimately improve project performance.
In the context of material flows, the construction process includes numerous wasteful activities that result from material mishandling on-site. For example, Teizer et al. (2020) monitored shell and interior construction and indicated the notable wasteful activities, including 1) unnecessary handling of material (10%), 2) searching for the right resources (6%), and 3) waiting to use the resource (3%), all of which caused wasted effort related to material mishandling. Misplaced materials cause waste such as rework and delays in tasks (Ju et al., 2012), both of which hinder labor performance. The spaces used to store materials can also potentially block workflows (Arbulu and Ballard, 2004) and affect production progress. Site managers and engineers thus must improve material handling and production flows by utilizing materials at the right time and in the right location.
A kitting logistics solution synchronizes material deliveries with workers’ daily tasks into work location levels (Tetik et al., 2020) and could play a key part in stabilizing production flows. Assembly kits, which are carriers that contain material parts for different tasks (Hanson and Medbo, 2012), are transported directly to work locations so the materials can be quickly utilized or installed by workers in the right places without being stored on-site (Tommelein and Li, 1999). Still, kitting practices face the challenges of monitoring in time and efficiently for the direct involvement of workers who use the material batches in work locations. For example, previous methods for evaluating the impacts of kitting practices were based on manual observations and videos (Tetik et al., 2020), which makes evaluating the solution both labor intensive and time consuming. Kitting logistics practice requires smooth information flows among different operations: a situation that also leads to the potential for automation (Zheng et al., 2020).
The use of automated tracking solutions for material management could address these challenges and enhance construction productivity and workflow by providing site managers with easy-to-use metrics to evaluate the process of flows. In building projects, automated material monitoring could help workers know the locations of materials. In this way, searching times for materials are eliminated, productivity is improved, and material handling efficiency is enhanced (Gurmu, 2019).
Despite the expected benefits for site management from localization technologies (Grau et al., 2009), little research has been conducted on tracking systems that cover both materials and workers to support lean principles for enhancing material management and related workflows. Although the collection of tracking data based on labor and material could improve construction material and workflow management, such data is still isolated from the scheduling information of planned on-site operations. Such fragmentation leads to difficulties for various stakeholders when evaluating and comparing the actual labor and material flow situation with the planned conditions based on an integrated database. The worker and material positioning data thus should be combined with the scheduling information in order to investigate the schedule compliance of labor and material interactions.
The linked data approach is a set of design principles within Semantic Web technologies for publishing data in a structured format (Bizer and Schultz, 2009). Such an approach can structure heterogenous data with interlinks to provide formalized and structured data integration. The linked data approach also provides a machine-readable format for computers to understand the meaning of the data so they can produce meaningful query results. While construction industry researchers have investigated these capabilities of the linked data approach (Pauwels et al., 2015), they have yet to use the linked data approach to integrate the positional data of workers and materials with scheduling data.
Based on the above background, our aim is to improve the management of kit-based practice by implementing a passive indoor tracking solution to automatically detect the presence of multiple workers as well as material kits delivered directly to various work locations. We then evaluate the interactions of the material kit and labor flows. Previous research has indicated substantial periods of time when workers are absent from work locations (Zhao et al., 2019), so we consider an investigation of how the kitting solution influences the presence of workers to be an interesting line of research. New insights could also be gained relevant to the evaluation of material management practice (e.g., the kitting solution) and enhancement potentials by tracking both labor and material kits at the same time. Finally, a linked data framework is proposed to unite external data streams (e.g., scheduling information) to ensure data model interoperability and to evaluate the compliance of workers with material kits against the schedule. A broader image of construction resource interrelations thus can be established for future application development.
Technical Background
In this section, the technical background is reviewed from previous studies related to tracking technologies that have been applied in construction for labor and material monitoring, linked data, and Semantic Web technologies. Tracking technologies can be divided into vision- and radio-based tracking methods. Table 1 summarizes the previous tracking applications used in the construction industry and presents conclusions from research related to our empirical study on tracking solutions for material and labor flows in construction.
Vision-Based Tracking in Construction
Several vision-based methods have been proposed and implemented for monitoring site occurrences involving labor, material, and equipment. The methods are generally easy to deploy and are non-intrusive (Cai and Cai, 2020), although achieving smooth and continuous tracking that is satisfactory for labor and material flows could be a complex undertaking. For instance, recent research (Asadi et al., 2019) examined the possibility of using Building Information Modeling (BIM) coordinate system from camera poses of image frames, which enabled localization and mapping items between image frames and BIM views. The research demonstrated the effectiveness of real-time registration of images with BIMs, which could potentially enhance visibility of tracking process for resources such as labor or materials in the BIM platform. However, the method heavily depends on camera pose estimation and the interior structure of the buildings such as curved walls or arches may be prone to higher error of analysis. Those limitations may complicate the generalizability of applying this method as the use of a secondary positional sensor such as inertial measuring unit (IMU) and ultrawide band (UWB) may often be needed to address these issues (Asadi et al., 2019).
Despite the possibility of identifying site activities and detecting task status from workers (Luo et al., 2018), the current state-of-the-art vision-based methods may not achieve our aim of tracking both material and labor due to challenges in long-term and robust monitoring of multiple objectives (Cai and Cai, 2020). For our use case, each work location would have to have a camera to ensure the visibility of resources on-site for the entire tracking period; in addition, multiple tracked resources (e.g., workers and materials) might interfere in the view and occlude each other within confined work locations such as apartments. Given the requirement for extensive data sets while training the system (e.g., Luo et al., 2018) and the demands for proper shooting angles from cameras (Zhang et al., 2018), these complexities mean that vision-based tracking solutions may not be practical for analyzing the interactive movement of labor and materials.
Radio-Based Tracking in Construction
Another category of sensor-based monitoring consists of radio-based tracking technologies, which are already being applied in many construction projects. Such technologies are typically based on radio signals that are sent and received among tags (such as beacons) and gateways (Cai and Cai, 2020; Dror et al., 2019). Radio-based tracking technologies are less accurate compared with vision-based tracking technologies (over 1 m for radio-frequency identification [RFID] and Bluetooth Low Energy [BLE] technology), but they are reliable in tracked object detection and identification during the tracking period (Cai and Cai, 2020). Because of the capability of providing reliable information to exclude false detection (Cai and Cai, 2020), radio-based tracking technologies may be more suitable for analyzing the interactions of multi-resource movements when the constant accuracy of resource identity is required during the entire monitoring period.
Some common tracking methods include Zigbee (Zhang et al., 2021), accelerometer wristband (Ryu et al., 2019), Wi-Fi module (Yang et al., 2020), the aforementioned RFID (Guven and Ergen 2021) and BLE (Olivieri et al., 2017; Park et al., 2017; Zhao et al., 2017). These methods all appear to eliminate the effort involved in manual data collection in construction while being accurate and providing in-time data feedback through an automated process. For instance, the RFID solution enables tracking by attaching tags that are active, semi-active, or passive and having scanners or antennas read the tags (Ergen et al., 2007; Li et al., 2020).
The advantage of passive RFID technology is that those tags do not need a separate power supply and are small, inexpensive, and suitable for nearly all kinds of materials (Teizer et al., 2020). This solution would be helpful for detecting material flows in different work locations in parallel with workers’ movements. Passive RFID tags cannot be used in large-scale environments, however (Wu et al., 2019), and potential signal blocking under chaotic and dynamic indoor construction conditions still causes challenges in the signal quality of this tracking method (Teizer et al., 2020; Costin et al., 2012). In recent study, RFID tracking methods have also been experimented into integration of BIM. Chen et al. (2020) proposed a framework to integrate the use of detailed look-ahead plans when applying BIM and RFID technologies, aiming at enhancing supply chain visibility and material flow process in pursuit of Industry 4.0. However, despite of the potentials to integrate the tracking method into BIM, the framework has only been implemented on simulated projects, and the benefits from the real-world projects have not yet been investigated.
Furthermore, Yang et al. (2020) developed an automatic monitoring system connecting workers and their associated tools for pair checking by using Wi-Fi networks on construction sites. The study demonstrated high potential of using radio-based technology to enable near real-time detection of interaction of workers and tools. Their research was conducted only as a lab test and was focused on construction safety. They did not consider production flows or operations in their study.
Compared to other radio-based tracking solutions, the BLE tracking method has the following characteristics and advantages for indoor monitoring of multiple resources in parallel: 1) the BLE tracking method involves minimal false negative alerts and requires the least input of infrastructure and time for calibration (Park et al., 2016); 2) the solution is cost efficient and lightweight for passive monitoring in previously tested construction projects (Zhao et al., 2019); 3) the solution supports multiple resource tracking with reliable identity information, which is important in workers’ material handling. The BLE tracking method thus can be a suitable approach for tracking both labor and material flows for the purpose of improving material handling and evaluating a specific material management solution on-site. To the best of our knowledge, no reported studies to date have used the BLE tracking method within building projects’ indoor environments to investigate the interactions of construction workers and materials.
Linked Data and Semantic Web Technologies
Linked data is an approach in which the web is used to create links between data from different systems or sources. The use of linked data offers significant advantages to alleviate the problem of information heterogeneity. Using this approach, data is machine-readable, explicit, and linked to other external data sets and can in turn be linked to and from external data sets (Bizer et al., 2011). The four basic uses of linked data include 1) the use of Uniform Resource Identifiers (URIs) to name resources; 2) the use of Hypertext Transfer Protocol (HTTP) URIs to provide access to resources via the internet; 3) the provision of extra information about resources using various standards, including the Resource Description Framework (RDF) and RDF query languages such as SPARQL, when looking up URIs; and 4) the provision of links to related URIs to explore more related factors.
RDF is the critical technology involved in establishing the “web of data,” where data is encoded in the form of “subject, predicate, object” triples (Bizer et al., 2011). These triples are statements with resources modeled as subjects with their associated properties and the value or object of the properties. RDF provides a graph structure in which users can look up any URI in an RDF graph over the web to retrieve additional information. Thus, each RDF triple is part of the global web of data, and each RDF triple can be used as a starting point to explore the data space.
Increasing implementations of linked data have recently emerged in the construction domain. Construction information and data are often characterized as fragmented, since the construction information is usually acquired via various information sources and from different stakeholders who work in various construction disciplines and use a variety of tools, systems, and software. For example, Pauwels et al. (2015) reviewed various applications of linked data in the architecture, engineering, and construction (AEC) domain and concluded that linked data was used to improve information interoperability and to link across domains to fuse construction information for further information utilization. Curry et al. (2013) explored the use of the linked data approach to integrate cross-domain building data in order to serve a holistic database for the building lifecycle. Lee et al. (2016) proposed a linked data framework to share construction defect information to integrate the defect data from different silos to alleviate insufficient defect data sharing. To our knowledge, however, no recent works have used the linked data approach to integrate indoor positioning and scheduling information to support the investigation of on-site material and labor interactions.
Possibilities for the Tracking of Kits and Workers in Production Flow Improvement
Material handling in construction is still frequently reviewed as primitive, and advanced on-site material management practice is necessary for improvement (Caldas et al., 2006). Site material management could substantially benefit from automated tracking technology and automation in detection (Grau et al., 2009). For example, the use of material tracking practice could enhance worker productivity (Nasir et al., 2010) and minimize the time workers spend on searching for the right materials (Gurmu, 2019). In particular, material tracking may be used to evaluate and improve logistics practice: a material kitting solution which was proposed to enhance the time efficiency (Hanson and Medbo, 2012).
Specifically, the kitting solution in logistics allows for more efficient and prompt material deliveries directly to work locations. With origins in manufacturing industries, the concept of kitting involves packing and delivering the products necessary for an assembly task into one single package to a designated workplace (Bozer and McGinnis, 1992). Because kits can be delivered close to the exact work locations, the practice can enhance productivity by allowing for more efficient material usage in work locations and reducing the time spent looking for components required for various tasks (Tetik et al., 2020), thus contributing to overall work progress and production stability. But the relationship between material storage and project productivity has not been examined thoroughly in construction logistics (Seppänen and Peltokorpi, 2016). Kitting is usually used with other logistics practices such as logistics hubs and just-in-time (JIT) delivery. Logistics hubs can be configured to support assembly and kitting activities (Hamzeh et al., 2007). Tetik et al. (2020) showed, using four case studies, that a kitting intervention could stabilize assembly work and increase workers’ productivity and workplace utilization. They measured work performance via schedule compliance, the share of value-adding time in work locations, and labor productivity by applying the camera-based video monitoring (for 44 days in total) and manual observation (for 25 days in total) methods of data collection. While their research did demonstrate the value of kits, their research method was resource intensive and may not be implemented scalably by practitioners who wish to improve their logistics practices. The management of kitting still encounters potential challenges because no automated way currently exists to calculate key performance indicators (KPIs), which are used to evaluate the success of the kitting method. Therefore, the benefits often remain anecdotal, which may hinder the implementation of such systems.
In the current paper, we first explain the indoor positioning system infrastructure and a case in which a kitting logistics solution was used; we then develop a linked data framework to connect the typically heterogeneous information sources of labor, materials, and schedules. Next a novel method is proposed to calculate the time-matching level of workers and materials in work locations based on their detected uninterrupted presence. Finally, new KPIs are introduced to evaluate the kitting practice for the improvement of site material management and work progress in construction.
Methods
We follow the design science research methodology in this study (Peffers et al., 2007) and will demonstrate our research method in terms of system infrastructure, case description, time-matching level calculations, and the proposed linked data framework.
The real-time tracking system that was used in previous research (Zhao et al., 2019) was implemented in this case, but we expanded our focus into the integration of labor and material tracking in work locations using a kit-based logistic solution. The underlying kitting solution, as part of the material management practice, can be assessed based on the “uninterrupted presence levels” of workers, as captured by the tracking system. A worker’s uninterrupted presence level is an uninterrupted period that the worker spends in the same work location before moving to another location. A threshold is set to define how much time workers need to stay at one work location before their jobs are considered uninterrupted (Zhao et al., 2019). For system implementation, we followed the process of a BLE-based real-time tracking system from a previous study (Zhao et al., 2019), including 1) setting up the real-time tracking system based on site floor plans, 2) evaluating the system accuracy by comparing the system results to a researcher’s known movements (ground-truth data), 3) verifying the coverage of the system based on ground-truth data, and 4) capturing and analyzing the uninterrupted presence of workers and material kits.
Next, the real-time tracking system architecture and model are demonstrated. Then our case study is introduced in more detail.
Real-Time Tracking System Infrastructure
Our current research uses the same BLE-based real-time tracking system that Zhao et al. (2019); Zhao et al. (2021) used in their previous study. In the model, BLE beacons were used that could be associated with construction workers who had previously agreed to be monitored. The beacons send their media access control (MAC) address to the gateways (Raspberry Pi) periodically at an approximately one second frequency; the gateways then transmit the information to the cloud. The information contains a unique MAC address of each beacon assigned to a worker’s profile and a time interval for the worker’s presence in the database. The data analyzer identifies the beacons’ locations from the magnitude of the received signal strength indicator (RSSI). To solve the potential signal flickering problems (the gateways are close to each other, and the results that are detected flicker between locations (Zhao et al., 2019)), the system uses recent RSSI values; the oldest values are removed when new values are pushed in the data analyzer. The RSSI value is averaged and the outlier values minimized to mitigate potential flickering interference. When a worker moves from one location to another and is detected by a different gateway, a new time interval is automatically generated in the system. The cloud provides downloadable data for future analysis. The architecture of the indoor tracking application used in our case studies is illustrated in Figure 1 (Zhao et al., 2019).
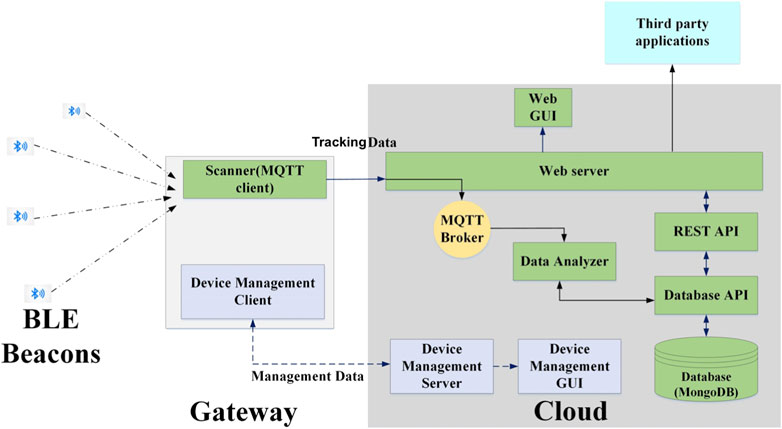
FIGURE 1. The architecture of the tracking system applied in our case studies (adapted from Zhao et al., 2019).
Case Description
The case a renovation project was selected in Helsinki, Finland. The renovation work was undertaken in a three-floor building during June 2018. The case project team applied a kitting logistics solution because of the potential to improve workplace utilization rates by minimizing the wasted efforts of material transportation from storage areas to the site (Tetik et al., 2020). We placed one gateway in each apartment, with nine total installed gateways (eight gateways in eight apartments and one at the entry on the ground floor). Eight workers (including carpenters, plumbers, plasterers, and bricklayers) agreed to be monitored and were given the beacons; each of the eight material kits was also attached with beacon tags for monitoring. Due to the different sizes of the apartments, the quantities of materials in the kits could be different, but the materials were the same for the tracked tasks in each apartment. Each material kit was assigned to each apartment for the tasks shown in Table 2. As shown in the table, each kit included the necessary material for the bathroom renovation in that specific apartment. The possibility of attaching both material and labor data enabled us to monitor the interactions of workers as they went about their on-site material-related tasks.
Figure 2 shows a simplified floor plan, with gateways marked in the jobsite. Table 2 shows a task schedule summary for tracked workers and tasks. Each tracked task follows the same sequence from apartment A3 to A4, A8, A7, A1, A2, A6, and A5. Each successor apartment in the sequence for the same task is always scheduled half a day later than the former apartment, skipping weekends. The scheduled worktime is from 7:00 to 11:00 in the morning for the first half day, and from 11:30 to 15:30 in the afternoon for the second half day. The tasks listed in the table only covered work that was done in bathrooms. Workers from other trades (such as electricians and painters) were on the site during the tracking period in the workflow, but we did not monitor their tasks.
System Coverage and Accuracy
To ensure the quality of the results, we needed to first test the accuracy and coverage of the tracking system. The definition of “accuracy” and “coverage” from previous research (Zhao et al., 2019) was followed: accuracy is defined as the proportion of how much time, detected by the system, is recorded in the correct location and at the correct time, while coverage is defined as the share of the total time detected by any gateway of the system. For any incorrectly detected times recorded in the system, we classified these times into three non-match categories (Zhao et al., 2019): 1) non-match category 1 (the beacons detected by an incorrect gateway for a period of over a minute); 2) non-match category 2 (data flickering issue, the beacons detected by gateways that were near each other); and 3) non-match category 3 (the beacons that were not detected at all due to coverage problems.
The system accuracy and coverage were evaluated by comparing the tracking results with ground-truth data (Zhao et al., 2019). We had a researcher simulate workers’ possible job routines on-site in both cases. The researcher self-recorded his movements to serve as the ground-truth data. Table 3 presents a summary of the system accuracy and coverage results in this case. Compared to previous renovation project tracking in which the system reached 71% coverage and 55% accuracy via the same tracking method, with gateways installed at stairwells on each floor (Zhao et al., 2019), our tracking data achieved sufficient system accuracy without sacrificing coverage, mainly because we placed gateways in each apartment near the bathroom area where the material-related work was scheduled in this renovation project. This placement decreased the interference compared to the previously reported case, where gateways on adjacent floors could interfere with each other and cause detection inaccuracies.
Linked Data Framework
The proposed framework is designed to provide automatic identification of labor and material KPIs with limited human disturbance in order to support stakeholders in understanding the situation of on-site operations (see Figure 3). The framework also connects the database of indoor positioning data with external data sources such as schedules. Three tracks have been designed in this framework, including Data collecting, Linked data implementing, and Data processing. The Data collecting is the initial track that obtains the indoor positioning tracking data of the labor and material kits, as described in Real-Time Tracking System Infrastructure section—the real-time tracking system infrastructure and project scheduling data. Following the data collecting track, the Linked data implementing track triggers. The major objective of this track is to prepare, convert, and link the data collected from the indoor positioning system and schedules, based on the linked data method, to create an integrated database that holds the comprehensive indoor positioning data and scheduling data. In this track, as a first step, the indoor positioning data of the tracking labor and material kits collected from the indoor positioning system and the project schedule is mapped in a certain ontology and schema for formalizing and creating the interlinks. The data is then converted into RDF graphs and stored in the RDF graph store. The final track is the Data processing, in which the integrated RDF graph is processed and queried to calculate the KPIs of workers’ overlapping time levels and material kits based on the principles introduced in the following part.
Calculation of Workers’ Time-Matching Levels and Material Kits in One Apartment
Since kitting material logistic solutions require each material kit to be delivered directly to each work location (in this case, each apartment bathroom), workers’ time-matching levels and material kits can be used to indicate how well the underlying kitting solution has worked and whether the workers were able to use materials from the kits to conduct their tasks in various work locations. The workers’ time-matching levels and kits refer to the time period when workers’ detected presences overlap with the kits’ detected presences.
Workers and material kits at one work location can have the following interactions: 1) both the material kit and workers are in the work location; 2) the material kit is in the work location, but the worker is not; 3) the worker is in the work location, but the material kit is not; and 4) neither the material kit nor the worker is in the work location. Scenario (1) is the best scenario when a worker is scheduled to perform the material-related tasks at that location, while scenarios (3) and (4) could indicate issues with the kitting solution because workers are working without the kit, or material kits have not been delivered as planned.
The raw data was analyzed to estimate the overlapping time level of workers and material kits for each apartment using the following steps.
1) The uninterrupted presence threshold represents the minimum time period that a worker needs to be present at one site location without interruption gaps to be able to count this presence as uninterrupted (Zhao et al., 2019). We set this threshold for 10 min as the highest-tested value in Zhao et al.‘s work (2019) because we wanted to focus on longer continuous working periods rather than brief visits in a location. Because we installed one gateway in each apartment in the building, we were able to classify all detected uninterrupted worker presences by each work location (in this case, each apartment). The threshold was not applied on material kits because, due to their weight and immobility, their location is more fixed, and filtering out short visits is not required.
2) For a single apartment, we aggregated all detected presences of the material kit assigned to that apartment. For example, in apartment 1, we searched for all detected presences of the material kit assigned for apartment 1.
3) T1 = the uninterrupted presence of a worker during the same time when the material kit for that assigned apartment was present.
4) T2 = the uninterrupted presence of a worker matched the time period of a material kit that was assigned to other apartments but was present in the current apartment.
5) T3 = the uninterrupted presence of a worker that did not fall into time periods of any material in that apartment (the uninterrupted presence of the worker thus =
6) T4 = the operational time of each worker, which was defined as the time from a worker’s first detected time of the day to the last detected time of the day (Zhao et al., 2019).
7) The presence index (Zhao et al., 2019) =
8) The time-matching level of workers and materials in one apartment was then estimated by comparing T1, T2, T3, and T4 and their ratios:
• TMD (time matching for designated) =
• TMA (time matching for any) =
• NM (no material) =
9) Next, we followed the linked data framework, with the aim of connecting the indoor positioning data with the external scheduling information to enable further actual and as-planned comparisons of KPI calculations:
Figure 4 shows how the STMD and STMM calculations were carried out based on detected presences and scheduling information.
In addition to calculating the time-matching level of workers and material kits, we were also interested in the following metrics related to the time and movements of material kits to evaluate the performance of the logistics system: 1) delivery times of the kits to the first detected apartment on-site; 2) removal times of the kits from the last detected apartment on-site; 3) number of times each kit moved between the delivery time and removal time. Those metrics contribute to understanding in more details of the material flows such as waiting time and the level of unnecessary inventory. Although these metrics are not new, the novelty of the method lies in using the proposed lightweight monitoring system to obtain the time and location information automatically and passively to analyze these metrics without time consuming data collection efforts.
In summary, together with comparing the time-matching level of workers and material kits based on their overlapping uninterrupted presence, kit delivery times, and movements based on the analyses of automatically detected temporal and spatial information by the real-time tracking system, we were able to assess the soundness of the kitting solution in this case, such as by examining how well the kitting material management practice worked in each work location.
Implementation of the Linked Data Framework
Our aim was to establish and develop an automated process of data analysis modeling where the tracking data of cross-type resources such as materials and labors, together with workers’ schedules, could be linked and integrated into one proposed framework. Based on the architecture discussed in the Method section, we then implemented the linked data framework for the case study (Figure 5).
Ontology Selection and Mapping
A standard data structure was used as the basis for formalizing and integrating the indoor positioning data. In this research, we used the extension of digital construction ontologies (Törmä and Zheng, 2020), or DiCon, for the logistics structure (Zheng et al., 2020). DiCon is a set of ontologies that may be used to define the basic terminologies and relations of the digitalized construction process. DiCon is also used to model and represent the digitalized information obtained from the implementation of information and communication technologies (ICTs) in the construction domain. Using DiCon, we used classes including “person,” “batches,” “location,” “sensors,” and “events” and their interrelations to represent the indoor position data in this case. In the DiCon logistics extension, the “material kit” is defined to represent material kits, which are groups of material batches. The mapping of the data to DiCon and logistics is shown in Figure 6. For the scheduling data, the information of every task and its assigned location and labor can also be represented based on DiCon. Every record of the indoor positioning system is considered to be an “event,” which is observed by a beacon and a gateway during a time interval when the gateway captures the signal from the beacon. Both beacons and gateways are considered to be sensors where beacons are hosted by workers and material, which are known as the instance of “person” and “material kit” classes in the DiCon logistics extension. The gateways are hosted by apartment, which is a “location.”
Data Conversion and Storage
In order to establish the linked data for further data processing, the data and information obtained from the indoor positioning system and project schedule must be converted from tabular format in a spreadsheet into RDF format based on the previous result of ontology mapping. To achieve the conversion, in this case, a Python script was developed by utilizing an open source Python library called RDFlib (2009) to handle the conversion process.
After the conversion, the RDF graphs were generated and stored in the Graph DB store. Graph DB is among the most popular RDF stores for storing and managing semantic information serialized in RDF format. In the Graph DB environment, users can also conduct SPARQL queries to process, search, and retrieve information from the database.
After the implementation of the linked data framework, we then conducted data analysis on material flows and time-matching levels of workers and kits, with the aim of calculating the material-related metrics introduced in the Method section.
Results
Material Flows
Figure 7 shows an example of one material kit (assigned for apartment A7) that was moved inside the building during the tracking period. The material kit was first detected at apartment A7 at 07:03 on June 1. The material kit was then moved to apartment A2 at 17:04 on June 17 and subsequently moved to apartment A1 at 11:04 on June 22. Finally, the kit was moved to the entry area of the building at 08:20 on June 26. Table 4 provides a summary of the moving times of each material kit with its delivery and removal times on-site, in addition to the schedules of task start and end times in the respective apartments. Because the presence of the material kit for apartment A3 was not found in the system due to the loss of the beacon attached to the kit, we decided to exclude apartment A3 from the analysis.
Out of a total of seven material kits, six were delivered on-site earlier than required (the first task scheduled in the apartment), and six were removed from the site later than required (the last task scheduled in the apartment). On average, kits were moved 6.9 times between apartments. The average number of move times for the cases where kits were delivered earlier than required (apartments 1, 2, 5, 6, 7, and 8) was 6.6, lower than for the kit that was delivered later than required (apartment 4), which was moved 8 times. In our case, the delays of material kits delivered later than the first tasks scheduled led to more movement of kits between apartments on average. It should be noted that if the kitting solution had worked perfectly, no movements between apartments would have occurred.
For the task schedule in apartment A7, the material kit for apartment A7 was moved away from apartment A7 at 12:43 on June 17, but the scheduled end time of the last task in that apartment was at 11:30 on June 22. However, after the material kit for A7 was moved away, the material kit for A4 was moved to apartment A7 from June 18 to June 21, which covered the remaining time for tasks required in the apartment.
The material kit for A7 was observed in apartment A1 from June 22 to June 26, which covered the remaining time for tasks required in apartment A1 after the material kit for A1 had already been moved away, at 12:28 on June 18. These kit movements showed that the implementation of the kitting process encountered problems during this project because the originally assigned kit could not be used to complete the work.
Time-Matching Level of Labor and Materials in the Apartment
Next, we calculated how the material flow interacted with the location information of workers in the apartment. Due to space limitations, we have visualized the results of only one apartment (apartment A7), and we present the results of the whole data set in a later section. Figure 8 shows a visualization of the carpenter in apartment A7, while the material kits for A4 and A7 were detected as being present during the same tracking period of June 1 to 21. Figure 8 also shows that the worker was mostly present throughout the same time range as the material kit for A7 in that apartment, except for his or her presence from June 18 to 21, when the material kit for A7 was undetected while the material kit for A4 was present. Because the task of suspended ceiling plating was scheduled in apartment A7 starting on the afternoon of June 18, the worker could have taken the suspended ceiling plates from the material kit assigned for apartment A4 instead.
Table 5 summarizes the TMD, TMA, and NM results for carpenter one and how these values were calculated in apartment A7. Because we set the threshold of an uninterrupted presence for workers at 10 min, all time intervals from workers that are shorter than 10 min were omitted from the analysis. The 11.1% of NM time of the assigned worker (carpenter 1) with material presence represents time in which the worker was detected in the apartment without any material kits being around. A few possible reasons for this situation are as follows.
1) The worker was waiting for the material.
2) The worker had to retrieve the material from other places (or parts of other kits) and then returned to do the work.
3) Materials were delivered as supplemental orders and were not included in the original kits.
4) The worker could have been with the material kit for apartment A3, since the movement of that kit remained unknown due to the loss of the beacon for that kit.
5) The material kit was incorrectly detected (for example, because of flickering between apartments). This impact was minimal, however, because during manual investigation of the time period between June 1 and 27, from the kit being delivered to the site until its removal, we noted that only 4.33 min of flickering (detection in different apartments) occurred. Although the exact activities of the worker during this time were unknown, the first three points could be regarded as an indication of problems in the kitting process. In addition, we noted two time gaps in the material kit for apartment A7, between June 3 and 4 and between June 13 and 14. During these times, the material kit for apartment A7 was found in A3: from 11:06 on June 3 to 6:54 on June 4, and from 15:34 on June 13 to 7:10 on June 14.
Evaluation of the Time-Matching Level in all Tracked Locations and for Different Tracked Workers
To determine whether the tracking of material kits and labor together would add more insightful information to the evaluation of the kitting solution on-site, we then calculated and summarized the metrics, grouped by location and workers (see Tables 6 and 7).
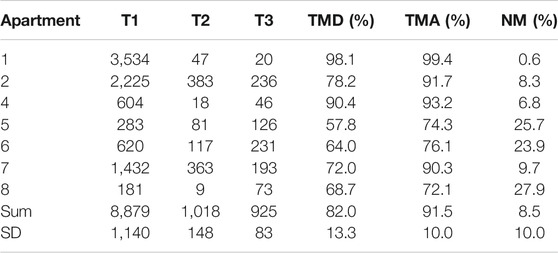
TABLE 6. Summary of the time-matching levels in all apartments (all numbers in minutes except percentages).
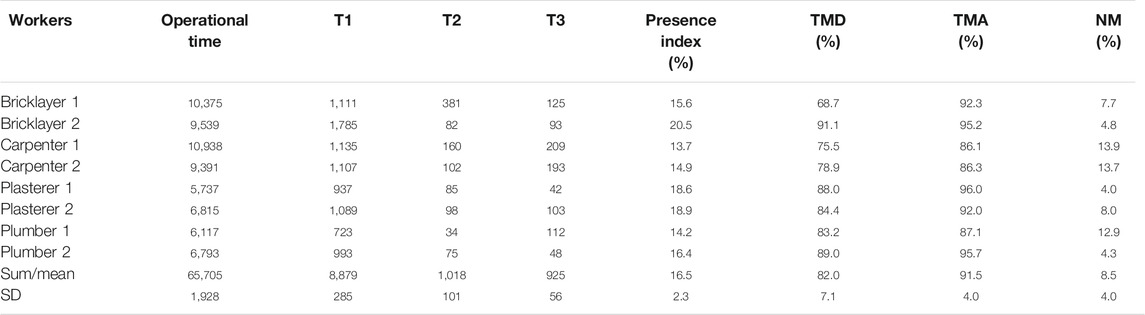
TABLE 7. Summary of the time-matching levels for each individual worker (all numbers in minutes except percentages).
Overall, 8.5% of the total uninterrupted presence of all workers (925 min) represented the time when the workers were present either with the A3 kit or with no material kits in the same apartment. In addition, 18% of the total uninterrupted presences (1,943 min) represented the time when the workers were present without material kits designated for the underlying apartments. The standard deviation (SD) of all apartments (except apartment 3) was 10%, so we noted some locations where the kitting process worked better (i.e., with a low NM value, for example 0.6% in apartment 1) and some locations where workers were not using the kits for a large portion of time (for example apartment 8, with 27.9%).
Next, the time-matching level based on individual workers throughout their operations in all work locations was evaluated (Table 7).
For the individual workers, the SD values for NM were much smaller than for the locations. The problems with kitting seemed to occur mostly with carpenters, while other trades showed smaller NM values. The carpenters were scheduled to do the non-material-related task (layout) first, and then to start using the materials in the kit; therefore they may have been in work locations before the kits had arrived, thus leaving larger NM values compared to other crews. In addition, all workers were detected to have periods in the presence of material kits other than those that were designated, on average 9.4% of the time [T2/(T1 + T2 + T3)]. The results in Table 7 show an estimate of how well the kitting solution worked for each tracked worker.
Estimation of Compliance With the Schedule
Next, SPARQL queries were used to calculate how well the uninterrupted presences of workers and material kits matched with the schedule. The proposed linked data framework was used to create an integrated RDF graph of the linked indoor positioning data and the scheduling information. This section presents an example of using SPARQL queries based on semantic logics and structured data to explore the worker and material kit interaction performance in compliance with the schedule. In the example, the “time matching for designated” (TMD) indices were further specified to investigate the compliance with the schedules. TMD was further addressed as the time-matching level of a worker’s uninterrupted presence matching the material kit assigned to a specific apartment in compliance with the schedule (“scheduled time matching for designated” [STMD]). STMD was designed to identify the time of labor-material matching in the schedule-assigned work locations, while STMM was designed to investigate the spatial-temporal metric of the material kit in compliance with the schedule. Due to space limitations, the STMD of carpenter two in apartment seven and the STMM of the A7 material kit were selected as a case to illustrate the query process. The queries were conducted in the Graph DB environment. The results of the queries show the capability to flexibly process and retrieve meaningful information from organized indoor positioning data formed in RDF.
The first query is used to identify the uninterrupted presence of carpenter two in apartment 7 (T1 + T2 + T3) from the processed database, in which the uninterrupted presence threshold of 10 min had already been applied. The query could thus be directly conducted to find all the records of the uninterrupted presence of carpenter 2. In this query, the variables to be explored were “?duration.” In SPARQL, SELECT is a reserved function for listing all the variable results of interest that satisfy the conditions from the WHERE section. The query follows the logic where a worker hosts a beacon first and then the beacon and gateway observe the event, which contains the temporal information of the presence duration. In this case, we specified apartment seven and carpenter 2 as an example.
The second query is used to find the total overlapping time of a worker with an apartment-assigned material kit and to check if the worker’s presence is in the designated apartments of all scheduled activities of carpenter 2—in other words, to identify the T1 that fits the schedule. The query follows the logic of first searching material kits and worker temporal overlaps at designated apartments and then comparing the identified overlapping time to the scheduled operation time in that location. The logic of identifying the overlap and comparing the overlapping time with the schedule is based on Allen’s interval algebra (Allen, 1983).
We conducted the third query to find the duration of the corresponding material kit localized in the assigned apartment that fit the schedule. Allen’s interval algebra (Allen, 1983) was also used in this query to find the overlap time of the scheduled activity and material presence in the target apartment.
The results of the three queries were then further processed based on the principles defined in the Method section. The accumulated results from the first query represent the uninterrupted presence of carpenter two in apartment 7 (T1 + T2 + T3), which is 2,233.32 min. The accumulated results from the second query represent the total time of the labor and the designated material kit in compliance with the schedule, which is 228 min. By dividing the uninterrupted presence accumulated from the result of the first query, the STMD may be calculated as 10.21%. The accumulated results from the third query represent the total time of the material kit in the assigned apartment that matches the scheduled tasks in that location, which is 2,132.27 min. By dividing the total duration of the planned tasks (7,200 min) accumulated from the schedule, the STMM of the A7 material kit was calculated to be 29.61%.
As shown in the example, calculating the STMD and STMM is possible by integrating the indoor positioning data and the scheduling information. The results of the STMD and STMM values are an enrichment of the material-related KPIs, which can provide further information for site managers to evaluate how the underlying kitting solution has worked for a specific worker (e.g., carpenter 2) or the kit (e.g., the A7 material kit) against his or her schedule. The implementation of the linked data framework also provides an alternative for identifying the desired time-matching level of workers and material kits in construction operations with a more automated and flexible procedure.
To summarize the results, the following outcome based on the proposed methods and the real-time monitoring system was achieved: 1) calculated kit moving times inside the building and analysis of the material kit flows from the delivery to the site until the removal of the kits. 2) investigated in detail the time-matching level of labor and materials in apartments, providing insights and evaluation of the tested kitting solution. 3) estimated level of compliance with schedule by applying the proposed linked data framework to connect other external available data sources. Next, the discussion was presented regarding the generalizability, reliability of the system, comparison to previous studies, contribution to knowledge, implication and limitation as follows.
Discussion
Generalizability of the Method and the Reliability of the System
Little research to date has focused on the combination of real-time tracking for labor and material in construction sites for the purposes of addressing material mishandling and evaluating kitting solutions. In a few previous empirical works, researchers have analyzed material tracking data to support better material handling and site-work performance, but the generalizability of their methods has varied. For instance, Grau et al. (2009) developed localization algorithms based on a combination of RFID and Global Positioning System (GPS) technologies to capture the time spent on activities directly related to tracked steel material components and to analyze the impact of the tracking application on steel erection productivity. Because GPS is unsuitable for indoor environments, however, the generalizability of this method is limited to the outdoors. Tetik et al. (2020) evaluated the applicability of kitting by comparing four projects with and without kitting solutions, with a focus on the impact of work performance and management requirements. While they showed that kitting solutions could improve product flow and work performance, our focus is on the effectiveness of an applied kitting solution by showing the variability of kit presences associated with workers in multiple work locations. Their method can be used to capture logistics performance on a more detailed level but is not scalable due to the manual analysis required. Our approach presents a scalable solution based on the uninterrupted presence of workers and kits in work locations that still enables the calculation of KPIs, which can be used to evaluate logistics performance.
Our case was an apartment renovation project where small locations (in this case apartment bathrooms) enclosed with walls were used for analysis. Due to the project type, the accuracy and coverage values were high. In earlier research, Bluetooth-based systems showed lower accuracy and coverage values in projects with large, open areas. Kitting as a logistics solution has often been implemented first on project types with small work areas, because kitting is mainly used to solve issues related to a lack of space (Corakci, 2008). Large open areas typically have better possibilities to store materials, and thus the benefits of kitting may not be so large.
Generalizability to other project types should be explored in future research. The current method depends on apartment-specific material kits delivered to each work location. This type of logistics enables easy tracking because tracking beacons are required only for each kit. Although the system could, in theory, be applied for other types of materials as well, each tracked material has associated costs in time. A typical construction site contains an enormous amount of materials, and tagging all materials is not always practical. We analyzed this kitting solution in particular because of its ability to easily map materials to locations and tasks and the low number of tracked elements required. Previous researchers who have investigated materials on worksites, such as Grau et al. (2009), have taken a similar approach by focusing on individual types of materials, although the individual materials in the kits are also of interest. In future studies, the current method could be applied on selected individual materials to determine if their movements differ from the movements of kits.
The reliability of the system depends on the following factors: 1) the tracking accuracy and coverage. In our case, the accuracy reached 88.4% and the coverage reached 97.1%, which indicated high overall tracking reliability of system. 2) system implementation and maintenance. The system depends on assurance of gateway connectivity, power availability, and on workers and material kits carrying beacons at all times. In our case the beacon for the A3 kit was unfortunately lost onsite, which affected the monitoring of A3 apartment.
In any case, based only on the movement of tracked material kits, knowing whether a specific material part in a kit has been utilized is difficult. In the future, we aim to test the performance of a kitting solution by focusing on the material utilization level. For instance, the tracking method could be supplemented by vision-based technology, such as by integrating a camera monitoring and indoor positioning system in the work location. By implementing both vision-based technology and indoor positioning, we would not need to monitor the videos all the time but could instead shift our focus to the time period when the KPIs (e.g., NM) are alerted during the kitting process.
Comparison to Project-Level Presence Indices of Previous Studies
The concept of project-level presence indices was first introduced by Zhao et al. (2019). Such indices indicate the percentage of workers’ uninterrupted presences inside their daily accumulated operation times at the project level. This setup means that project-level indices only show workers’ uninterrupted presence values and take all workers into account. By differentiating work locations and non-work locations, project-level indices require small amounts of context information but provide important indications such as estimates of the overall efficiency of the worksite based on the share of workers’ actual presence levels throughout a project.
Compared with project-level presence indices, in the current paper the concept was expanded further by dividing indices into categories based on the time-matching of material kits. These material-related uninterrupted presence metrics include TMD, TMA, and NM, which also require tracking data from the material kits for each work location. A project-level presence index is a metric of operations flow at the project level. Therefore, the material-related uninterrupted presence uses the resource flows from both material and labor perspectives, which creates opportunities to evaluate the current material management practice (in this case, the kitting solution). For instance, in the current case, the overall project-level presence index was 16.5%, which was lower than in previous studies with the same threshold value (Zhao et al., 2019). The index also indicates that 83.5% of the time, the worker was either undetected inside the building or was detected at one location for less than 10 min. Additionally, in our case the tracked material kits were not always at the designated location, and the workers were not always present with the correct kit in the apartment.
The current research extends the research conducted by Zhao et al. (2019) by investigating also material flows which have not been addressed in their previous studies. Zhao et al. (2019) assessed an overall percentage of workers’ uninterrupted presence level for all workers in the project during the tracking period. This kind of project-level indices cannot be used to understand root causes of problems to inform improvement interventions. The project-level presence indices reflect on the productivity level of the entire project but do not include connections to task schedule or other site data sources. The measurement of labor and material kit integrated uninterrupted presence creates some new and deeper analysis opportunities. The efficiency of the logistic system can be analyzed by looking at materials and labor together in connection with the schedule. For that purpose, our study introduces new material-related metrics which can be used to provide supplemental information on top of the project-level uninterrupted presence indices. Therefore, the key motivation of this research was to broaden the knowledge of previous studies toward material management practices.
Overall, presence indices, which also consider material flows, provide a deeper understanding of production performance than those indices that rely only on the tracking systems of workers’ location. In addition to project-level presence indices, the several metrics can be used to evaluate the kitting logistics solution from the following perspectives.
1) Waiting or other non-value-adding time spent in work locations can be analyzed from time-matching levels between workers and material kits (TMA and NM). The smaller the NM (or larger the TMA) value, the lower time disparity of workers who lack any kits.
2) Success of having a correct kit in a work location can be analyzed from time-matching levels between workers and the material kits assigned to the specific apartment (TMD). A larger TMD value implies that the assigned material kit with planned material contents was more successfully adopted in practice. The difference between TMA and TMD (TMA-TMD) also suggests a time level where the kits assigned to other apartments were occupied in the apartment when the assigned kit was absent, thus indicating potential work that workers needed to use from other apartments’ materials for the underlying apartment. The TMA value may indicate problems with the bill of materials used to assemble the kit and will likely rise as a result of incorrect quantities or kinds of materials in the kits.
3) Success of following the original work plan can be analyzed from time-matching levels between workers with material kits under their original schedules (STMD and STMM). Larger STMD or STMM values imply that workers are spending time with material kits in work locations following the original plans. This information could be particularly valuable in projects that use, for example, the takt production concept, where the schedule is committed and followed (Frandson and Tommelein, 2014).
4) Unnecessary inventory can be calculated from the detected delivery time of material kits compared with the time when the first task requires the material in that kit. The lower the time gap between these two times, the less waiting or delays of the material to be used will occur. Unnecessary inventory is one waste type related to materials, and kitting practice is typically planned to be JIT (Tetik et al., 2020; Tommelein and Li, 1999).
5) Wasted time for moving of materials can be analyzed from the moving times of material kits between work locations. With more detected moving times of material kits, workers unavoidably waste more time transporting kits to the required apartments. In an optimally working kitting process, only one movement of the kit to its location, and then one movement out, should occur once all materials have been consumed.
In summary, we argue that a well-performing kitting solution should have 1) high TMA and TMD values, 2) ideally little difference between TMA and TMD values, and 3) no kit movements between work locations. If scheduling information is taken into consideration, then a good performance should also require high STMD and STMM values with the least possible time gap between detected delivery times and task schedules required for the underlying material kits.
Contributions to Current Knowledge
In the current paper, we contribute to tracking methods in construction by developing and demonstrating a method to manage kit-based logistics management using an indoor real-time tracking system to monitor both material and worker flows. More specifically, the tracking method is developed to integrate material kit and labor tracking for a kitting logistics solution in a scalable way by measuring the uninterrupted presences of both labor and material kits.
One of the specific contributions to the methods based on the presence of materials and workers in work locations is that the developed method does not require manual observation or watching through camera videos to understand the process. For example, using camera monitoring and manual observations, Tetik et al. (2020) pointed out that the effects of random factors may be large due to a relatively small data set. Our method does not rely on manual analysis and thus is scalable to large data sets, which will help to avoid random factors.
In addition to the methodological development, the contribution to construction management lies in the introduction and demonstration of several KPIs to evaluate the effectiveness of the kitting solution. When the kitting process works in an optimal way, it fulfills the following requirements: 1) kits only go to the right apartment, 2) kits only move in once and out once, and 3) workers are present in the planned work location with the correct kit. The results have shown that none of the requirements were met in the project we tested, so the implemented kitting practice was far from optimal. Calculating these KPIs in real time could allow management to find the root causes of problems and to continuously improve on material logistic solutions. Such a system could be seen as a digital twin of the logistics process and could drive improvement in the way that Sacks et al. (2020) proposed in their recent paper on digital twin construction.
In the current paper, the existing knowledge was also contributed on data linkages in construction projects by we investigating the labor-material interaction in compliance with operation schedules. By applying the linked data method, we introduced a novel approach to integrating heterogenous data from both positioning tracking and schedules. With our introduction of the linked data approach, the cross-type resource data in construction becomes linked and machine-readable, which provides easy utilization of semantics for KPI calculations and the ability to conduct analyses without fragmentary raw data processing. The integrated data enables the evaluation of the effectiveness of kitting solutions compared to the plans, which cannot be achieved by individual data streams alone.
Managerial Implications
This work has several managerial implications for operations management in construction based on the proposed tracking application framework. First, the proposed system and KPIs can help site managers to understand how well the applied kitting solution performs. For instance, the disparity from the optimal situation quantified by NM can be used to indicate the amount of time when workers are present without any materials. Managers can use the method and KPIs when reallocating working resources to those places where the kitting practice appears to have the most challenges. For example, our case apartment A8 was found to be the most complex work location with the highest NM and kit-moving times, which should urge the site managers in this case to pay special attention to the task progress in apartment A8. Faulty amounts or kinds of materials for that apartment likely explained these issues.
Second, for logistics providers, the automated detected timestamps of kit delivery and removal in/out from the work locations, and the value difference between TMA and TMD, can provide useful information about the correctness and punctuality of kit deliveries. If TMA is equal to TMD, then all assigned material kits have been correctly placed in the apartments, and no other material kits are needed for replacement. Logistics providers can use the information of kit delivery and removal to estimate approximate kit usage using cycle times in each work location. They can also estimate the right quantity and correct size of kits to be delivered to the assigned apartment. Based on real-time data logistics, providers can dynamically update kit delivery plans and executions to the site (Kalsaas et al., 2014).
Third, for task schedulers, the study will provide practical KPIs for evaluating and continuously improving their processes. STMD can be used to evaluate the compliance levels of workers with the assigned material kits in apartments, while STMM can be used to evaluate the share of time when the material kit is placed elsewhere under the task schedule.
In summary, our research has introduced these KPI metrics to enable real-time monitoring for detecting problems in kitting practices in work locations. These metrics can potentially benefit logistics providers, site managers, and schedule planners. Lean interventions should be undertaken accordingly if the problems appear to be continuous, as indicated by the KPIs.
The linked data method also provides the opportunity to align heterogenous data sets from various domains or systems with the indoor position tracking system. With linked data sets, more applications can be used based on indoor positioning than just KPI identification. For example, by combining real-time indoor positioning tracking with building information modeling (BIM), users can gain a prompt and direct visual-based awareness of the on-site work situation and thus can flexibly adjust and control the on-site work to improve productivity.
Overall, we have shown that waste is a problem with flows during value-adding activities on-site rather than being caused only by a single worker or by individual materials being misplaced. The use of presence information from both workers and materials can offer simple KPIs that can act as proxies for waste indication—for instance, to evaluate how much the presence of workers and material kits would be affected by JIT logistics (e.g., kitting practice) in different projects.
Limitations
The current research does have a few limitations. One of the main limitations of this method may be described as identification issues of materials and kits. Based on the real-time tracking system used in this case, which showed satisfactory coverage (97.1%) and accuracy (88.4%), we saw relatively good results from worker and material timestamps to reduce resource flows on-site. We were unable to identify the presence of specific materials in the kits, however, because we only placed beacons to monitor the kits in our study. In future studies, we propose to add features such as sending notices to workers for simple confirmation of their current activities (such as waiting for materials, idle status, etc.) when the TMA degree appears to decrease during the day. In this way, sorting through all uninterrupted worker presences to search for time durations could be avoided, which hinders the effectiveness of the kitting solution. We would also be able to learn the actual reasons for better effectiveness from workers’ direct confirmations.
Another limitation is that one beacon for the A3 kit was lost onsite, so the NM periods may have included times in which workers were actually with the A3 kit, thus making the actual NM smaller. In this case, some indication of the effectiveness of the underlying kitting practice could still be obtained by examining the value of TMD and checking on a worker’s status with the correct material kits in an apartment (i.e., the designated kits). For future study, beacons will be tagged with the material kits all the time during the tracking periods.
In this research, Linked data method was implemented to integrate the heterogeneous indoor positioning and the operation schedule information. Such integration combines data sources from different systems, and further enables the calculation of the KPIs with schedule compliance (STMD and STMA) that cannot be achieved with solo data streams based on previous methods. However, in this research only these two data sources were obtained, which means that only STMD and STMA can be calculated. If more types of data sources could be acquired, more potential KPIs could be also calculated. For example, if the BIM model of the project could also be obtained, it is possible to use the BIM quantity takeoff to calculate the workload of each task in the schedule, and further to calculate the work efficiency of each task. In the future research, the goal is to collect comprehensive digitalized data from one construction project and integrate all digital data sources and develop more accurate KPIs to represent the construction productivity.
Conclusion
In this paper, we have illustrated how our proposed real-time tracking system and linked data framework were applied in an indoor bathroom renovation construction project for the automated detection and analysis of time-matching levels of material kits and workers based on their uninterrupted presence. New KPIs were developed that can be measured in real time and offer opportunities to improve material and labor flows for kitting logistics solutions based on the proposed metrics. We have learned that notable durations occurred in work locations in which workers were without kits on-site. The variability of these durations in different places should be noted for managing kitting solution practices.
Compared to tracking for workers only, the information in this work consists of the integration of labor and material tracking and the evaluation of current kitting logistic solutions based on overlapping times of workers and kits. The current method works by revealing the observed problems of kitting practices in real time, thus providing lean intervention opportunities for material-labor-related tasks on-site. Users can also evaluate the effectiveness of the kitting practice in work locations based on the metrics introduced in this paper. We aim to establish a linked data model that could be used to connect heterogeneous information of cross-type resources (such as labor and materials) and their schedules from external sources in construction so that an automated data analysis for proposed KPIs (such as STMD and STMM) could be executed smoothly for site managers’ decision-making in the future.
Data Availability Statement
The raw data supporting the conclusions of this article can be made available by the authors upon request.
Author Contributions
Conceptualization, JZ, YZ, OS, and AP; Methodology, JZ and YZ; Data Collection, JZ; Data Analysis, JZ and YZ; Writing—original draft, JZ; Writing—review and editing, JZ, YZ, OS, MT, and AP; Funding acquisition, OS.
Funding
This work was supported by the Intelligent Construction Site (iCONS) research project (Grant No. 2819/31/2016) and the Digitalizing Construction Workflows (DiCtion) research project (Grant No. 2758/31/2017) funded by the Business Finland, Aalto University, and a consortium of companies. In addition, the research was partially supported by the Building 2030 consortium of Aalto University and 21 companies.
Conflict of Interest
The authors declare that the research was conducted in the absence of any commercial or financial relationships that could be construed as a potential conflict of interest.
Publisher’s Note
All claims expressed in this article are solely those of the authors and do not necessarily represent those of their affiliated organizations, or those of the publisher, the editors and the reviewers. Any product that may be evaluated in this article, or claim that may be made by its manufacturer, is not guaranteed or endorsed by the publisher.
References
Allen, J. F. (1983). Maintaining Knowledge about Temporal Intervals. Commun. ACM 26, 832–843. doi:10.1145/182.358434
Angah, O., and Chen, A. Y. (2020). Tracking Multiple Construction Workers through Deep Learning and the Gradient Based Method with Re-matching Based on Multi-Object Tracking Accuracy. Automation in Construction 119, 103308. doi:10.1016/j.autcon.2020.103308
Arbulu, R., and Ballard, G. (2004). “Lean Supply Systems in Construction,” in Proc. 12th Ann. Conf. Int. Group Lean Const. (Copenhagen, Denmark: IGLC-12).
Asadi, K., Ramshankar, H., Noghabaei, M., and Han, K. (2019). Real-time Image Localization and Registration with BIM Using Perspective Alignment for Indoor Monitoring of Construction. J. Comput. Civ. Eng. 33 (5), 04019031. doi:10.1061/(ASCE)CP.1943-5487.0000847
Bizer, C., Heath, T., and Berners-Lee, T. (2009). Linked Data - the Story So Far. Int. J. Sem. Web Inform. Sys. 5 (3), 1–22. doi:10.4018/jswis.2009081901
Bizer, C., and Schultz, A. (2009). The Berlin SPARQL Benchmark. Int. J. Sem. Web Inf. Syst. 5 (2), 1–24. doi:10.4018/jswis.2009040101
Bozer, Y. A., and McGinnis, L. F. (1992). Kitting versus Line Stocking: a Conceptual Framework and a Descriptive Model. Int. J. Prod. Econ. 28 (1), 1–19. doi:10.1016/0925-5273(92)90109-k
Cai, J., and Cai, H. (2020). Robust Hybrid Approach of Vision-Based Tracking and Radio-Based Identification and Localization for 3D Tracking of Multiple Construction Workers. J. Comput. Civ. Eng. 34 (4), 04020021. doi:10.1061/(asce)cp.1943-5487.0000901
Cai, J., Zhang, Y., and Cai, H. (2019). Two-step Long Short-Term Memory Method for Identifying Construction Activities through Positional and Attentional Cues. Automation in Construction 106, 102886. doi:10.1016/j.autcon.2019.102886
Caldas, C. H., Torrent, D. G., and Haas, C. T. (2006). Using Global Positioning System to Improve Materials-Locating Processes on Industrial Projects. J. Constr. Eng. Manage. 132 (7), 741–749. doi:10.1061/(asce)0733-9364(2006)132:7(741)
Chen, Q., Adey, B. T., Haas, C., and Hall, D. M. (2020). Using Look-Ahead Plans to Improve Material Flow Processes on Construction Projects when Using BIM and RFID Technologies. Ci 20, 471–508. doi:10.1108/CI-11-2019-0133
Corakci, M. A. (2008). An Evaluation of Kitting Systems in Lean Production. Borås, Sweden: Master’s thesis, University College of Borås School of Engineering.
Costin, A., Pradhananga, N., and Teizer, J. (2012). Leveraging Passive RFID Technology for Construction Resource Field Mobility and Status Monitoring in a High-Rise Renovation Project. Automation in Construction 24, 1–15. doi:10.1016/j.autcon.2012.02.015
Curry, E., O’Donnell, J., Corry, E., Hasan, S., Keane, M., and O’Riain, S. (2013). Linking Building Data in the Cloud: Integrating Cross-Domain Building Data Using Linked Data. Adv. Eng. Inform. 27 (2), 206–219. doi:10.1016/j.aei.2012.10.003
Dror, E., Zhao, J., Sacks, R., and Seppänen, O. (2019). “Indoor Tracking of Construction Workers Using BLE: mobile Beacons and Fixed Gateways vs. Fixed Beacons and mobile Gateways,” in Proc. 27th Ann. Conf. Int. Group Lean Const. (Dublin, Ireland: IGLC-27). doi:10.24928/2019/0154
Ergen, E., Akinci, B., East, B., and Kirby, J. (2007). Tracking Components and Maintenance History within a Facility Utilizing Radio Frequency Identification Technology. J. Comput. Civ. Eng. 21 (1), 11–20. doi:10.1061/(asce)0887-3801(2007)21:1(11)
Frandson, A., and Tommelein, I. D. (2014). Development of a Takt-Time Plan: a Case Study. Const. Res. Cong. 2014, 1646–1655. doi:10.1061/9780784413517.168
Grau, D., Caldas, C. H., Haas, C. T., Goodrum, P. M., and Gong, J. (2009). Assessing the Impact of Materials Tracking Technologies on Construction Craft Productivity. Automation in Construction 18 (7), 903–911. doi:10.1016/j.autcon.2009.04.001
Gurmu, A. T. (2019). Tools for Measuring Construction Materials Management Practices and Predicting Labor Productivity in Multistory Building Projects. J. Constr. Eng. Manage. 145 (2), 04018139. doi:10.1061/(asce)co.1943-7862.0001611
Guven, G., and Ergen, E. (2021). Tracking Major Resources for Automated Progress Monitoring of Construction Activities: Masonry Work Case. Construction Innovation ahead-of-print, 1471–4175. doi:10.1108/CI-05-2020-0081
Hamzeh, F. R., Tommelein, I. D., Ballard, G., and Kaminsky, P. (2007). “Logistics Centers to Support Project-Based Production in the Construction Industry,” in Proc. 15th Ann. Conf. Int. Group Lean Const. (East Lansing, MI, USA: IGLC-15), 181–191.
Hanson, R., and Medbo, L. (2012). Kitting and Time Efficiency in Manual Assembly. Int. J. Prod. Res. 50 (4), 1115–1125. doi:10.1080/00207543.2011.555786
Ju, Y., Kim, C., and Kim, H. (2012). RFID and CCTV-Based Material Delivery Monitoring for cable-stayed Bridge Construction. J. Comput. Civ. Eng. 26 (2), 183–190. doi:10.1061/(asce)cp.1943-5487.0000134
Kalsaas, B. T., Gundersen, M., Berge, T. O., Koskela, L., and Saurin, T. A. (2014). “To Measure Workflow and Waste: a Concept for Continuous Improvement,” in 22nd Ann. Conf. Int. Group Lean Const. (Oslo, Norway: IGLC-22), 835–846.
Kim, D., Liu, M., Lee, S., and Kamat, V. R. (2019). Remote Proximity Monitoring between mobile Construction Resources Using Camera-Mounted UAVs. Automation in Construction 99, 168–182. doi:10.1016/j.autcon.2018.12.014
Lee, D.-Y., Chi, H.-l., Wang, J., Wang, X., and Park, C.-S. (2016). A Linked Data System Framework for Sharing Construction Defect Information Using Ontologies and BIM Environments. Automation in Construction 68, 102–113. doi:10.1016/j.autcon.2016.05.003
Li, C. T., Cheng, J. C. P., and Chen, K. (2020). Top 10 Technologies for Indoor Positioning on Construction Sites. Automation in Construction 118, 103309. doi:10.1016/j.autcon.2020.103309
Luo, X., Li, H., Cao, D., Yu, Y., Yang, X., and Huang, T. (2018). Towards Efficient and Objective Work Sampling: Recognizing Workers' Activities in Site Surveillance Videos with Two-Stream Convolutional Networks. Automation in Construction 94, 360–370. doi:10.1016/j.autcon.2018.07.011
Nasir, H., Haas, C. T., Young, D. A., Razavi, S. N., Caldas, C., and Goodrum, P. (2010). An Implementation Model for Automated Construction Materials Tracking and Locating. Can. J. Civ. Eng. 37 (4), 588–599. doi:10.1139/l09-178
Olivieri, H., Seppänen, O., and Peltokorpi, A. (2017). “Real-time Tracking of Production Control: Requirements and Solutions,” in Proc. 25th Ann. Conf. Int. Group Lean Const. (Heraklion, Greece: IGLC-25), 671–678. doi:10.24928/2017/0177
Park, J., Kim, K., and Cho, Y. K. (2017). Framework of Automated Construction-Safety Monitoring Using Cloud-Enabled BIM and BLE mobile Tracking Sensors. J. Const. Eng. Man. 143 (2), 5016019. doi:10.1061/(ASCE)CO.1943-7862.0001223
Park, J., Marks, E., Cho, Y. K., and Suryanto, W. (2016). Performance Test of Wireless Technologies for Personnel and Equipment Proximity Sensing in Work Zones. J. Const. Eng. Man. 142 (1), 4015049. doi:10.1061/(ASCE)CO.1943-7862.0001031
Pauwels, P., Törmä, S., Beetz, J., Weise, M., and Liebich, T. (2015). Linked Data in Architecture and Construction. Automation in Construction 57, 175–177. doi:10.1016/j.autcon.2015.06.007
Peffers, K., Tuunanen, T., Rothenberger, M. A., and Chatterjee, S. (2007). A Design Science Research Methodology for Information Systems Research. J. Manag. Inf. Syst. 24 (3), 45–77. doi:10.2753/MIS0742-1222240302
RDFlib (2009). Documentation. Retrieved from: https://rdflib.readthedocs.io/en/stable/.
Ryu, J., Seo, J., Jebelli, H., and Lee, S. (2019). Automated Action Recognition Using an Accelerometer-Embedded Wristband-type Activity Tracker. J. Constr. Eng. Manage. 145 (1), 04018114. doi:10.1061/(ASCE)CO.1943-7862.0001579
Sacks, R., Brilakis, I., Pikas, E., Xie, H. S., and Girolami, M. (2020). Construction with Digital Twin Information Systems. Data-cent. Eng. 1, 1. doi:10.1017/dce.2020.16
Sacks, R., Radosavljevic, M., and Barak, R. (2010). Requirements for Building Information Modeling Based Lean Production Management Systems for Construction. Automation in Construction 19 (5), 641–655. doi:10.1016/j.autcon.2010.02.010
Seppänen, O., Ballard, G., and Pesonen, S. (2010). The Combination of Last Planner System and Location-Based Management System. Lean Const. J. 2010, 43–54.
Seppänen, O., and Peltokorpi, A. (2016). “A New Model for Construction Material Logistics: from Local Optimization of Logistics towards Global Optimization of On-Site Production System,” in 24th Ann. Conf. Int. Group Lean Const. (Boston, MA, USA: IGLC-24), 73–82.
Teizer, J., Neve, H., Li, H., Wandahl, S., König, J., Ochner, B., et al. (2020). Construction Resource Efficiency Improvement by Long Range Wide Area Network Tracking and Monitoring. Automation in Construction 116, 103245. doi:10.1016/j.autcon.2020.103245
Tetik, M., Peltokorpi, A., Seppänen, O., Leväniemi, M., and Holmström, J. (2020). Kitting Logistics Solution for Improving On-Site Work Performance in Construction Projects. J. Const. Eng. Man. 147 (1), 05020020. doi:10.1061/(ASCE)CO.1943-7862.0001921
Thomas, H. R., Horman, M. J., de Souza, U. E. L., and Zavřski, I. (2002). Reducing Variability to Improve Performance as a Lean Construction Principle. J. Constr. Eng. Manage. 128 (2), 144–154. doi:10.1061/(ASCE)0733-9364(2002)128:2(144)
Tommelein, I. D., and Li, A. (1999). “Just-in-time concrete Delivery: Mapping Alternatives for Vertical Supply Chain Integration,” in Proc. 7th Ann. Conf. Int. Group Lean Const. (Berkeley, CA, USA: IGLC-7), 97–108.
Törmä, S., and Zheng, Y. (2020). Digital Construction Ontologies. Retrieved from: https://w3id.org/digitalconstruction (Accessed November 15, 2020).
Wu, C., Wang, X., Chen, M., and Kim, M. J. (2019). Differential Received Signal Strength Based RFID Positioning for Construction Equipment Tracking. Adv. Eng. Inform. 42, 100960. doi:10.1016/j.aei.2019.100960
Yang, X., Yu, Y., Shirowzhan, S., sepasgozar, S., and Li, H. (2020). Automated PPE-Tool Pair Check System for Construction Safety Using Smart IoT. J. Building Eng. 32, 101721. doi:10.1016/j.jobe.2020.101721
Zhang, B., Zhu, Z., Hammad, A., and Aly, W. (2018). Automatic Matching of Construction Onsite Resources under Camera Views. Automation in Construction 91, 206–215. doi:10.1016/j.autcon.2018.03.011
Zhang, S., Shang, C., Fang, X., He, S., Yu, L., Wang, C., et al. (2021). Wireless Monitoring-Based Real-Time Analysis and Early-Warning Safety System for Deep and Large Underground Caverns. J. Perform. Constr. Facil. 35 (2), 04020147. doi:10.1061/(ASCE)CF.1943-5509.0001534
Zhao, J., Olivieri, H., Seppänen, O., Peltokorpi, A., Badihi, B., and Lundstrom, P. (2017). “Data Analysis on Applying Real Time Tracking in Production Control of Construction,” in 2017 IEEE Int. Conf. Ind. Eng. And Eng. Man. (Banff, AB, Canada: IEEM), 573–577. doi:10.1109/IEEM.2017.8289956
Zhao, J., Seppänen, O., Peltokorpi, A., Badihi, B., and Olivieri, H. (2019). Real-time Resource Tracking for Analyzing Value-Adding Time in Construction. Automation in Construction 104, 52–65. doi:10.1016/j.autcon.2019.04.003
Zhao, J., Pikas, E., Seppänen, O., and Peltokorpi, A. (2021). Using Real-Time Indoor Resource Positioning to Track the Progress of Tasks in Construction Sites. Front. Built Environ 7, 661166. doi:10.3389/fbuil.2021.661166
Keywords: real-time tracking, construction management, linked data framework, material and labor tracking, data integration, kitting logistics solutions
Citation: Zhao J, Zheng Y, Seppänen O, Tetik M and Peltokorpi A (2021) Using Real-Time Tracking of Materials and Labor for Kit-Based Logistics Management in Construction. Front. Built Environ. 7:713976. doi: 10.3389/fbuil.2021.713976
Received: 24 May 2021; Accepted: 20 August 2021;
Published: 03 September 2021.
Edited by:
Samad Sepasgozar, University of New South Wales, AustraliaReviewed by:
Laura Florez-Perez, University College London, United KingdomLonghui Liao, Shenzhen University, China
Copyright © 2021 Zhao, Zheng, Seppänen, Tetik and Peltokorpi. This is an open-access article distributed under the terms of the Creative Commons Attribution License (CC BY). The use, distribution or reproduction in other forums is permitted, provided the original author(s) and the copyright owner(s) are credited and that the original publication in this journal is cited, in accordance with accepted academic practice. No use, distribution or reproduction is permitted which does not comply with these terms.
*Correspondence: Jianyu Zhao, amlhbnl1LnpoYW9AYWFsdG8uZmk=