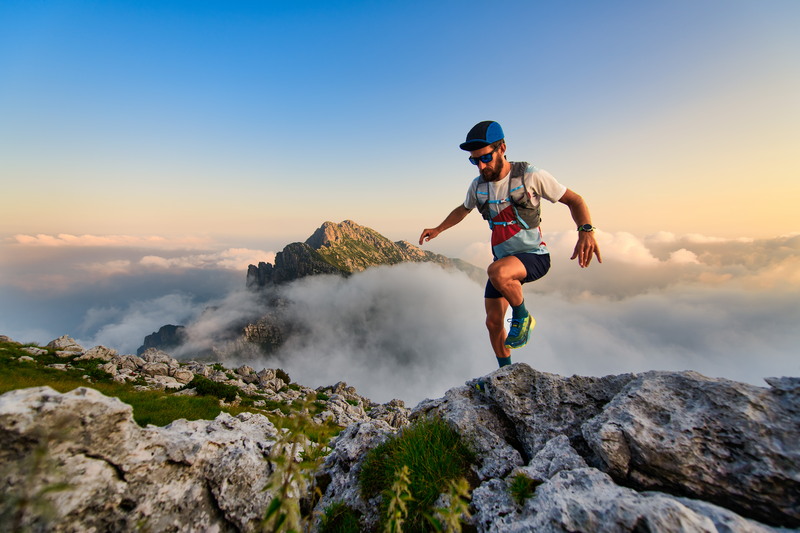
95% of researchers rate our articles as excellent or good
Learn more about the work of our research integrity team to safeguard the quality of each article we publish.
Find out more
OPINION article
Front. Built Environ. , 19 May 2021
Sec. Sustainable Design and Construction
Volume 7 - 2021 | https://doi.org/10.3389/fbuil.2021.685067
Waste rubber is a major environmental hazard, as its unscientific disposal significantly pollutes the environment. To avoid this, rubber is processed using pyrolysis that can help generate multiple by-products that find several applications. One of these by-products is carbon black, which can be incorporated into cementitious materials. This negates the need for the disposal of rubber, while reducing the demand for other construction material. Rubber is commonly produced from scrap tires using two technologies: cryogenic grinding and mechanical grinding at an ambient temperature below the glass transition temperature. The cementitious material with shredded rubber offers damping properties, ductility, and higher flexural strength than concrete without rubber. Rubberised concrete is advantageous because of its low density, chloride permeability resistance, freeze-thaw resistance, good sound absorption, acid resistance, bending impact strength and toughness, and increased damping capacity. These advantages make rubberised cement attractive for applications including earthquake-resistant elements, noise screens, rubberised cement beams with high impact resistance, pavements, and lightweight concrete.
However, many studies have concluded that using rubber in concrete usually leads to an effective decrease in the cement strength. The reduction in strength is mostly due to the following reasons. First, the rubber's hydrophilicity leads to a matrix which is less dense at the interfacial transition zone (ITZ) and causes the hydraulic phase to migrate. Moreover, the higher modulus of elasticity of soft rubber produces rubber called “soft core.” During the loading procedure, high stress concentrations form adjacent to the rubber and are more likely to make the rubberised concrete crack faster. As a result, the rubber surface needs to be altered by chemical or physical methods to offset the decrease in mechanical strength of the cement. The surface treatment of rubber particles can strengthen the interfacial adhesion between the rubber particles and the cement matrix and strengthen the bonding.
Cleaning the rubber with water eliminates additives, organics, impurities, and soil on its surface deposited during its production. Some researchers have concluded that rubberised concrete created with rubber that has been washed with water is slightly stronger than the control group rubberised concrete. The compressive strength of the cement increased by 15% (Raffoul et al., 2016). Rostami et al. (2000) concluded that small rubber particles exclusively washed in water could strengthen the resistance of rubberised cement, increasing its strength by 16%. Moreover, a reformatory water soaking method has been discovered to restrain the hydrophilicity of rubber. The rubber is dipped in water for 24 h before the mixing process. Commonly used pre-cementitious materials include silica fumes (SF), mortar, cement paste (LP), and limestone powder. The automatic characteristics of miscellaneous rubberised cement could be efficiently improved by coating the rubber with cementitious substances. In thesplitting tensile strength test, which indicated that rubber particles treated with silane coupling agents (SCAs), a concrete matrix, or cement coating are more firmly connected than untreated ones. Cement hydration products remained on the exterior of the coated rubber, whereas the uncoated rubber was uncovered. Usually, rubber processing includes layering cementitious substances on the rubber and air-seasoning the exterior (Kashani et al., 2018). The coating treatment upon ordinary rubberised concrete (ORC) improves bending resistance.
Chemical modification of the rubber surface is limited to latex treatment. In this treatment, rubber is soaked in a solution that includes CS2, KMnO4, acid, SCA, acetone, Ca(OH)2, and NaOH, and exposed to UV radiation and partial oxidation. Chemical treatment removes the dust and dirt on the rubber surface, cleans the oil, and increases the hydrophilicity and unevenness of rubber. The most commonly used method to improve the properties of rubberised cement is to apply NaOH liquor to alter the rubber. This is because NaOH liquor-treated rubber exhibits better wear resistance, fracture energy, and flexural strength. Moreover, Pelisser et al. (2011) discovered that the addition of SF and treatment with NaOH can lead to a more stable ITZ. Youssf et al. (2014) stated that using NaOH liquor to treat rubber decreases the plunge of the mixture by 25%. NaOH treatment can also help improve the durability of rubberised cement. In addition, the modification of the NaOH solution resulted in a decrease in the resistivity of the mixture and boosted the adhesion between the rubber and cement (Guo et al., 2017). The specimens with low electrical resistance exhibit strengthened durability over a long period. The SCA acts as an aggregate to enhance the adhesion between the concrete matrix and rubber by facilitating adhesion at the interface. It acts on the inorganic/organic interfacing section to physically and chemically make the cement matrix and rubber combine into a strongly connected structure. Colom et al. (2006) processed rubber with SCA and found that the rubber's tensile stiffness and strength increased. Stewart et al. (2013) testified that the concrete paste can react with the hydrolysate of SCA, which can enhance the link between the cement paste and observably improve the microstructure. The mechanical performance of the rubberised cement can be effectively improved by SCA treatment, which gives rise to the flexural strength and compressive strength of rubberised mortar. Guo et al. (2017) processed rubber using SCAs (Z-6040 and Z-6020) that resulted in strengthened bonding between the rubber aggregates and the cement paste.
Acid liquor treatment can haemolyze carboxylic compounds, lactones, or esters on the rubber exterior. Furthermore, acid treatment can improve the shape and roughness of the rubber. By acid treatment, several points are formed on the exterior of the molecules, and the adhesion between the rubber and the cement matrix is affected significantly. Compared to HNO3, treatment with H2SO4 is more efficient for enhancing the strength and damping of cementitious rubber composites. However, the H2SO4-treated rubber demonstrates a large increase in damping, and its surface energy is higher than that of the as-received rubber. The Ca(OH)2 solution exhibited more environmentally-friendly features, weaker alkalinity, and lower hazard levels than the NaOH solution (Muñoz-Sánchez et al., 2016). They discovered that the flexural and capsule strengths of rubberized mortar increased by up to 33 and 26%, respectively.
The low modulus of elasticity and hydrophilicity of rubber lead to stress concentration and weak adhesion between the cement matrix and rubber. Modifying the rubber surface chemically and physically enhances the connection between the cement interface and rubber, thus improving the durability and mechanical characteristics of rubberised concrete.
Water washing alone is not sufficient for increasing the strength of rubberised cement. However, as the most economical and environmentally friendly method, water washing could efficiently remove the impurities in rubber that are soluble in water before adding the mixture. It displays promising improvement in the hydrophilicity of the rubber exterior.
The process in which rubber was coated with cementitious materials improved the ITZ adhesion and increased its elastic modulus. Thus, it was highly effective for enhancing the durability and mechanical characteristics of rubberised concrete. Moreover, the raw materials used in this process can be used in various applications. Hence, they are promising for rubberised cement mass and industrial production for structural applications.
The majority of researchers claim that NaOH-treated rubber strengthens the mechanical characteristics of rubberised concrete. Different processing times, sizes of rubber particles, liquor concentration, and rubber sources may have contributed to the incompatible results.
A chemical bond between the cement matrix and the rubber surface is formed by SCA treatment, which makes the surface of rubber hydrophilic, thus enhancing the durability and mechanical characteristics of rubberised concrete.
Rubber drenched in chemical liquor is reusable in multiple operations widening the industrial applications of this method and helping save costs. Rubber surface modifiers, which are poisonous to the environment and humans, are being severely restricted to guard against potential secondary pollution.
ZJ and XZha: conceptualization and methodology. YufZ: writing. LY: supervision. XH: revising. XZho and YuhZ: reviewing and editing. All authors contributed to the article and approved the submitted version.
This research was supported by the National Undergraduate Innovation and Entrepreneurship Training Program (Grant Nos. 202011276014Z and 202011276001) and the Nanjing Institute of Technology 2020 Challenge Cup Support Project (ID: TZ20200015).
XZha and YuhZ were employed by company Jiangsu Victoria Incubator Pty Ltd.
The remaining authors declare that the research was conducted in the absence of any commercial or financial relationships that could be construed as a potential conflict of interest.
Colom, X., Cañavate, J., Carrillo, F., Velasco, J. I., Pagès, P., Mujal, R., et al. (2006). Structural and mechanical studies on modified reused tyres composites. Eur. Polym. J. 42, 2369–2378. doi: 10.1016/j.eurpolymj.2006.06.005
Guo, S. C., Dai, Q. L., Si, R. Z., Sun, X., and Lu, C. (2017). Evaluation of properties and performance of rubber-modified concrete for recycling of waste scrap tire. J. Clean. Prod. 148, 681–689. doi: 10.1016/j.jclepro.2017.02.046
Kashani, A., Ngo, T. D., Hemachandra, P., and Hajimohammadi, A. (2018). Effects of surface treatments of recycled tyre crumb on cement-rubber bonding in concrete composite foam. Constr. Build. Mater. 171, 467–473. doi: 10.1016/j.conbuildmat.2018.03.163
Muñoz-Sánchez, B., Arévalo-Caballero, M. J., and Pacheco-Menor, M. C. (2016). Influence of acetic acid and calcium hydroxide treatments of rubber waste on the properties of rubberized mortars. Mater. Struct. 50, 1–16. doi: 10.1617/s11527-016-0912-7
Pelisser, F., Zavarise, N., Longo, T. A., and Bernardin, A. M. (2011). Concrete made with recycled tire rubber: effect of alkaline activation and silica fume addition. J.Clean. Prod. 19, 757–763. doi: 10.1016/j.jclepro.2010.11.014
Raffoul, S., Garcia, R., Pilakoutas, K., Guadagnini, M., and Medina, N. F. (2016). Optimization of rubberised concrete with high rubber content: An experimental investigation. Constr. Build. Mater. 124, 391–404. doi: 10.1016/j.conbuildmat.2016.07.054
Rostami, H., Lepore, J., Silverstraim, T., and Zundi, I. (2000). “Use of recycled rubber tires in concrete,” in Proceedings of the International Conference on Concrete (London: Thomas Telford Services Ltd).
Stewart, A., Schlosser, B., and Douglas, E. P. (2013). Surface modification of cured cement pastes by silane coupling agents. ACS Appl. Mater. Interfaces 5, 1218–1225. doi: 10.1021/am301967v
Keywords: rubberized concrete, solid waste, surface treatment, cementitious material, enhancement method
Citation: Jiang Z, Zhang X, Zhang Y, Yu L, Hu X, Zhou X and Zhang Y (2021) Surface Treatment of Rubberized Waste Reinforced Concrete. Front. Built Environ. 7:685067. doi: 10.3389/fbuil.2021.685067
Received: 24 March 2021; Accepted: 06 April 2021;
Published: 19 May 2021.
Edited by:
Junbo Sun, University of Western Australia, AustraliaCopyright © 2021 Jiang, Zhang, Zhang, Yu, Hu, Zhou and Zhang. This is an open-access article distributed under the terms of the Creative Commons Attribution License (CC BY). The use, distribution or reproduction in other forums is permitted, provided the original author(s) and the copyright owner(s) are credited and that the original publication in this journal is cited, in accordance with accepted academic practice. No use, distribution or reproduction is permitted which does not comply with these terms.
*Correspondence: Xiwen Zhang, enh3MTAwOGt4QDEyNi5jb20=
†These authors have contributed equally to this work and share first authorship
Disclaimer: All claims expressed in this article are solely those of the authors and do not necessarily represent those of their affiliated organizations, or those of the publisher, the editors and the reviewers. Any product that may be evaluated in this article or claim that may be made by its manufacturer is not guaranteed or endorsed by the publisher.
Research integrity at Frontiers
Learn more about the work of our research integrity team to safeguard the quality of each article we publish.