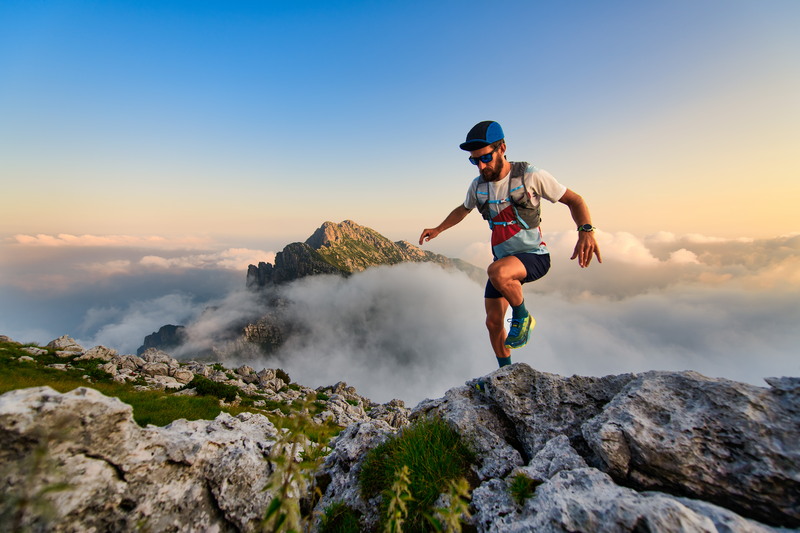
94% of researchers rate our articles as excellent or good
Learn more about the work of our research integrity team to safeguard the quality of each article we publish.
Find out more
ORIGINAL RESEARCH article
Front. Built Environ. , 26 March 2021
Sec. Sustainable Design and Construction
Volume 7 - 2021 | https://doi.org/10.3389/fbuil.2021.631307
This study describes the properties of geopolymer composites reinforced with bidirectional jute fibers. Their flexural strength is 12 MPa, four times higher than the strength of non-reinforced reference geopolymers. The bidirectional jute-reinforced geopolymer composite (JGC) is characterized by ductility and high elongation as well as strain hardening with a modulus of 66 MPa. It is found that the introduction of bidirectional jute fibers in the geopolymer matrix increases the adsorption capacity of Cr ions from 2.7 to 6.4 mg/g (pH = 5). The JGC can be recycled by grinding the material, and then using both the geopolymer material and the jute micro-fibers as filler and reinforcement for a new geopolymer matrix. The micro-fiber jute-reinforced composite obtained showed noteworthy mechanical properties, with strength three times higher than that of the reference material, when 2.5 wt% filler was added. Moreover, the ductility of the composite can be substantially enhanced by increasing (up to 10 wt%) the proportion of recycled jute-based geopolymer filler. These composites are therefore proposed as candidate materials for applications in the context of a circular economy.
Geopolymer cement is (Alshaaer et al., 2002; Komnitsas et al., 2007, 2009; Alshaaer, 2013) produced through the alkali activation of aluminum silicates to form hard, stable products of a tectosilicate nature (Alshaaer et al., 2012). Geopolymers have attractive properties such as low-temperature hardening, excellent mechanical behavior, and are suitable for several applications. They may be used in waste stabilization (Komnitsas et al., 2015), toxicity reduction, water purification, and passive cooling systems (Alshaaer et al., 2017). However, the production cost of geopolymers may be higher than that of ordinary cement, while with the use of alkaline solutions in field applications may entail certain difficulties. In the last 20 years, researchers have intensively investigated the development of strategies to commercialize geopolymers as multi-functional “green” materials for construction and water purification purposes (Alshaaer et al., 2015).
As with other brittle materials, natural and synthetic reinforcement fibers are needed to improve the elastic properties and increase the mechanical performance of end-geopolymer products. Fibers from polymers (Puertas et al., 2003; Sun and Wu, 2008), carbon, glass fibers (Natali et al., 2011), metals (Zhao et al., 2007), or minerals (Li and Xu, 2009) may be used to reinforce the geopolymeric matrix. Apart from increasing the toughness of geopolymer composites, fibers can enhance ductility and tensile strength, thereby optimizing their mechanical performance. From an environmentally friendly standpoint, natural fibers that can be recycled may be preferable as means of reinforcement. For instance, the potential of luffa cylindrical fibers in reinforced metakaolin-based geopolymer composites has been explored (Alshaaer et al., 2017), with excellent results: the compressive strength increased from 12.8 to 31.2 MPa, and the flexural strength from 3.4 to 14.2 MPa. In addition, the vascular features of the luffa fibers improved the self-healing characteristics of this product (Alshaaer, 2020). The effect of other natural fibers—bamboo, pineapple leaf fibers (Correia et al., 2013), cotton fibers, coir fibers and raffia fibers (Korniejenko et al., 2016; Silva et al., 2020a)—on the mechanical performance of geopolymer composites have also been investigated, mainly to determine the optimum weight percentage of the fiber addition. The results indicate that the optimum fiber weight percentage vary from 1% to 5 wt%, depending on the fiber type.
Jute is a suitable natural fiber that can be used for the production of eco-friendly geopolymer composites. Indeed, the “Food and Agriculture Organization of the United Nations (FAO)” refers to jute as a “future fiber” and highlights the environmental benefits of its use (Food and Agriculture Organization of the United Nations, 2010). A 103 m2 of jute farm is estimated to consume about 1.5 metric tons of CO2 and to release 1.1 metric tons of O2. In another study, chopped jute fiber (length 10 mm) was used to reinforce geopolymer composites (Guido et al., 2020): in comparison with the control samples, 1.5 wt% jute fiber reinforcement resulted in an increase of 222, 64, and 45% for the flexural, compressive, and tensile strength, respectively. Yet the effect of jute addition on the properties of geopolymer composites has not been explored, despite its availability and low prices. Therefore, this study aims to synthesize geopolymer composite using continuous bidirectional jute fibers that can be used as materials for environmental applications, and then evaluate their micropollutant adsorption capacity.
The present paper aims to investigate the synthesis, characterization, and recycling of a functional jute-based geopolymer composite. The novelty of this study is that preparation and evaluation of the effect of continuous bidirectional jute fibers is described in addition to the properties of geopolymer composites. Also, the jute-based geopolymer composites were recycled and introduced as filler material in a new geopolymer matrix. These objectives are in line with circular economy principles for natural fiber-based geopolymer composites (Geissdoerfer et al., 2017).
Geopolymer cement was synthesized using kaolinitic soil, Na2SiO3 solution, and NaOH solution. After heating the kaolinitic soil to 750°C for 5 h in a furnace (Nabertherm, United States) to obtain the respective amorphous kaolin (metakaolin), alkali activator (NaOH and Na2SiO3) solutions were added to dissolve and geopolymerize the aluminosilicates. A sodium hydroxide (NaOH) solution, 6 mol/L (M), was prepared using pure sodium hydroxide pellets (Merck, Germany) and deionized water, while the Na2SiO3 solution was composed of 27 wt% SiO2, and 8 wt% Na2O (Pan et al., 1999; Mohanty et al., 2000; Aluko et al., 2020).
The natural jute mat was introduced as reinforcement as reported in Figure 1. The source of these bidirectional bundles of fibers is a plant called Corchorus olitorius (Chaitanya et al., 2020). Each fiber bundle has a diameter of roughly 1 mm.
The alkali activators, NaOH and Na2SiO3, were mixed using Si: Al: Na molar ratios of 2:1:1 (Alshaaer, 2020). The source of SiO2 is the Na2SiO3 solution, Na2O results from the alkali activator solutions, and Al2O3 from the calcined kaolinitic soil (metakaolin). The water to Na2O molar ratio in the activating solution was 7. The aqueous alkali solution (NaOH, H2O, and Na2SiO3) was prepared first by stirring its components for 5 min. After that, metakaolin was added and mixed mechanically with the alkali solution for 10 min. Finally, the produced geopolymer paste was molded using rectangular molds, which were then sealed and cured in an oven (Raypa, Spain) at 40°C for 1 day. Three samples of reference geopolymer (RG) were cut to dimensions 1 cm × 2 cm × 12 cm.
The hand lay-up technique, described in a previous study (Alshaaer et al., 2017), was used to prepare the composites. In this study, the synthesis procedure is reported in Table 1. In preparing the geopolymer composites, four bidirectional jute fiber mats, each 8 cm × 12 cm (Figure 1) were used for reinforcement. The total weight of the jute fibers was 15 wt% of the geopolymer mixture. After gently pressing the paste, the mold was cured in an oven at 40°C for 1 day. The produced geopolymer composites, approximately8 mm thick, were cut to dimensions 12 cm × 2 cm. Three specimens of jute fiber-reinforced geopolymer composites (JGC) were prepared.
In this study jute-reinforced geopolymer composites (JGC) were processed into recycled fine aggregates, less than 425 μm, and micro-jute fibers of length less than 1000 μm (RJG), which were subsequently used as filler to prepare new geopolymers. Reference geopolymers containing 0% (RG), 2.5% (RJG1), 5% (RJG2), and 10% (RJG3) of recycled JGC were prepared and their mechanical performance was investigated. Three specimens of each series were prepared for mechanical testing. Their compositions are specified in Table 1. A schematic diagram of the experimental design is illustrated in Figure 2.
Scanning electron microscopy, SEM (F50, Netherlands), was used to study the morphology and the microstructure of the specimens, which were coated with platinum. Energy Dispersive X-ray spectroscopy (EDX) was used for the elemental analysis. The mass loss during heating of the powdered samples (∼100 mg) was measured using a thermogravimetric analyzer (TGA) (Netzsch, Germany, TG 209 F1 Libra). The temperature increased from 40 to 850°C at a rate of 5°C/min under a helium atmosphere. The elemental analysis of Cr ions was carried out using Inductively Coupled Plasma-Optical Emission Spectrometry (ICP-OES) (iCAP 7000, Thermo Fisher Scientific Inc., United States).
The mechanical properties of three specimens for each series were determined by means of three-point tensile bending (ASTM D790–10), using a universal testing machine (HD-B615-S, China). The span between the supports was 8 cm; the speed of the machine’s head during the test was 2 mm/min. The specimen’s dimensions were: height = (0.8–1) cm, width = 2 cm and length = 12 cm. The flexural stress (σ) was determined using the following equation:
where F is the maximum load (N) at crack extension, L is the span of the sample, b is the specimen width, and d is the specimen thickness (depth). Values of the flexural modulus were computed using the initial slope of the stress-strain curve. The strain hardening modulus is the slope of the stress versus strain curve after the point of yield of a material.
The constituents of jute fibers are hemicellulose, lignin and cellulose (Aluko et al., 2020), in proportions, 20–26 wt% hemicellulose, 12–15 wt% lignin, and 58–63 wt% cellulose (Pan et al., 1999). The density of jute fibers varies from 1.30 to 1.45 g/cm3 (Mohanty et al., 2000). The surface morphology of the jute was investigated by SEM, and the results are presented in Figure 3. Each jute fiber is composed of several fibrils held together by a natural resin material called lignin (Silva et al., 2020b). The jute fibers are arranged as wrapped bundles of 1 mm diameter (Figure 3).
As presented in Figure 4, SEM analysis of the jute-based geopolymer composite (JGC) shows that their microstructure contains a geopolymer matrix (point a) together with the jute fibers (point b). Figure 4A shows a SEM image of the flexural fracture of JGC. Owing to the aggressive alkali environment during geopolymerization reactions, the hemicellulose and lignin (binding resin) present in the jute fibers could be extracted. Subsequently, the fibers broke down into fibrils of several microns in diameter (Figure 4A, point c). This process leads to an increased surface area of the fiber fraction, hence to a stronger interface adhesion with the geopolymeric matrix (Alshaaer et al., 2017). The SEM analysis, Figure 4A shows no fiber pull-out from the geopolymer matrix or formation of gaps between fiber and matrix. This is a good indication of strong fiber-matrix adhesion, a very important property for all composites (Drzal and Madhukar, 1993).
Figure 4. SEM image of JGC, the jute fiber-geopolymer matrix (A), the geopolymer matrix (B), and the meso-pore network in the geopolymer matrix (C).
Previous studies (Alshaaer et al., 2017) reveal that kaolinitic soil contains a relatively high percentage, 14%wt, of TiO2. Heating the kaolinitic soil and the subsequent geopolymerization result in the formation of an amorphous phase that can be dissolved in a highly alkaline solution, and the transformation into a stable and strong binding material (geopolymer matrix), as discussed in other studies (Alshaaer et al., 2014; Alshaaer, 2020).
The morphology and the microstructure of the geopolymer matrix are shown by the SEM analysis of Figure 4B. Metakaolin, as an amorphous aluminosilicate, dissolves in the alkaline solution and is transformed into a stable and strong tectosilicate (geopolymer matrix) (Silva et al., 2020a). The resulting geopolymer matrix acts as a binder (Aluko et al., 2020; Marczak et al., 2020) in which an amorphous matrix (point B) coexists with a partially unreacted precursor (metakaolin) (point A). More detailed analysis of the reactions between the alkali activating solution and the precursors can be found in our previous research (Alshaaer et al., 2017).
Based on Figure 4B, it is deduced that there are three phases in the produced geopolymeric matrix: the unreacted metakaolin (point e), gaps or voids left after the dissolution of metakaolin (point d), and the amorphous geopolymer gel (point f), which acts as a binding material and is considered the most important component. This gel is the result of reactions between metakaolin (a source of Al ions) and the alkaline solution (a source of Si and Na ions). The EDX results (Figure 5), reveal that the amorphous or microcrystalline geopolymer phase contains, by atomic percentage, Si (16.65%), Al (7.56%), and Na (7.25%). The molar ratio of Si:Na:Al is 2.3:1:1, which is close to that of the precursors, as discussed in section “ıPreparation of Reference Geopolymer (RG).” SEM analysis, Figure 4C shows that as a result of the reactions between the alkali activating solution and the precursors, the overall matrix of the geopolymer and the regions between the residual metakaolin layers were filled with nano-porous Na-Al-Si amorphous matrix having a mesopore structure of size ∼25 nm.
Detailed analysis of the characteristics of the geopolymer matrix, the geopolymer composite (JGC) and the structural and bound H2O molecules in the jute fibers was approached by means of thermo-gravimetric analysis (TGA) (Figure 6). Heating the jute fibers up to 800°C results in a total mass loss of 93% (Figure 6A). The thermal decomposition and degradation of jute fibers was found to occur in three major stages. The first stage entailed the loss of surface humidity between 40 and 105°C. The second stage, between 200 and 400°C, entailed the pyrolysis of cellulose and hemicellulose constituents of the jute fibers, while the third stage of thermal degradation, between 400 and 500°C, involves the decomposition of natural resin (lignin) and other associated compounds (Chaitanya et al., 2020).
The thermal events in a geopolymer matrix occur in three temperatures ranges: 25–150°C, 150–400°C, and 400–700°C, as shown by the TGA curves (Figure 6B). The loss of mass below 150°C is the result of releasing surface humidity. The second mass loss range (150–400°C) is due to the release of zeolitic water. The third range of mass loss (450–600°C) results from the release of strongly bounded zeolitic water (Alshaaer, 2013). The JGC mass loss as a function of temperature shows a behavior similar to that of the geopolymer, but higher mass loss is seen at temperatures between 235 and 380°C (Figure 6C). This increment in mass loss of the composites is attributed to the thermal decomposition of the jute fiber fraction constituents (cellulose and hemicellulose) (Figure 6A).
The jute-based geopolymer composite (JGC) is introduced in this research as a functional composite for various engineering and environmental applications, including construction and water purification systems. Geopolymers were introduced in our previous work (Alshaaer et al., 2014) as construction materials to be used for water treatment, storage, and transportation. In line with the findings of previous studies (Yousef et al., 2009; Alshaaer et al., 2012), adsorption of the reference geopolymer (RG) toward Cr amounts to 2.7 mg/g (pH = 5) (Figure 7). The formation of a mineral matrix with a mesopore structure, as identified in the present study and illustrated in Figure 4C, has higher pore surface area, and thus increased adsorption capacity. By introducing the jute fibers in the geopolymer matrix, the adsorption capacity of the JGC increases to 6.4 mg/g (at pH = 5) as shown in Figure 7. This high increase in the adsorption capacity of the bulk samples of the composites is a result of the high absorption characteristics of the jute, ∼100% by weight (Marczak et al., 2020).
Figure 7. Adsorption of Cr(III) (period: 24 h, pH = 5, Each bar represents the measurement of the individual sample).
Typical stress-strain curves of the RG and the JGC are illustrated in Figure 8. The ultimate flexural stress of the reference geopolymer matrix is 3 MPa (Figure 8B). But when the bidirectional jute fibers are introduced into the geopolymer as reinforcement with a weight of 15 wt% (Table 1), the ultimate flexural stress of the JGC increases to 12 MPa. Introducing jute fibers into the geopolymer matrix causes a sharp increment in flexural strength. Thus, the yield and ultimate stresses are characteristics of the fiber matrix interface in JGC. Meanwhile, the flexural strength increases fourfold with the incorporation of jute into the composites. These results agree with a previous study involving the use of chopped jute fibers during the preparation of geopolymer bricks (Silva et al., 2020a).
The geopolymer matrix, being a brittle material, does not exhibit strain-hardening and has no yield point. Thus, its maximum strength would be as indicated in Figure 8. Like other composite materials, JGC has an overall flexural behavior defined by a linear elastic range up to the yield point, 5 MPa. The JGC exhibits ultimate flexural strength of 12 MPa, along with strain of approximately 0.115, after which strain softening of the composite occurs. Meanwhile, the strain-hardening modulus of the JGC was determined, 66 MPa (Alshaaer et al., 2015).
The introduction of bidirectional jute fibers as reinforcement generally enhances the mechanical performance of composites (Drzal and Madhukar, 1993), since their strength relies on the transfer of stress between the jute fibers and the geopolymer brittle matrix. The alkaline geopolymerization reactions result in a degradation of the natural resin (lignin) within the jute, splitting the fiber bundles and increasing the contact zone between the fibers and the brittle matrix (Correia et al., 2013), causing the ductile failure illustrated in Figure 8A. The alkaline geopolymerization treatment of jute fibers moreover causes the fibrillation of fiber to small fibrils (Figure 4). As the fiber diameter decreases, the surface area increases, thereby favoring the wettability of fibers within the geopolymer matrix.
The previously used composite materials were milled into aggregates measuring less than 425 μm (Figure 9A, point b) and jute fibrils with length under 1000 μm, as shown in Figure 9A (point a). As a result of milling, the jute fiber fraction was transformed into microfibrils with a diameter not exceeding 100 μm and a length less than 1,000 μm (Figure 9A, point a). Applying more magnification (Figure 9B), it is evident that the jute fibers are completely coated with a geopolymer layer having a rough surface, as seen in Figure 9B. These wastes of jute-reinforced geopolymer composites were used again as filler and reinforcements of new geopolymer products, as this study aimed to completely recycle the JGC and enable a zero-waste approach.
Figure 9. (A) Lower magnification SEM image, and (B) higher magnification SEM image of the powdered JGC; jute fibrils (1), and the geopolymer aggregates (2).
Figure 10 shows the derivatives of TG curves, rate of mass loss, of RJG composites with different powdered JGC contents. All the specimens, RJG1, RJG2, and RJG3, exhibited similar mass loss trends characteristic of geopolymer matrix (Figure 6B), and geopolymer composite (JGC) (Figure 6C), during the heating process from room temperature up to 600°C. The significant weight loss before 200 °C of RJG1, RJG2 and RJG3 was due to water loss by evaporation of weakly bonded water as, respectively, reported in Figures 10A–C. An increasing trend in the rate of mass loss was observed when heating in the temperature ranges 200–400°C and 400–600°C and increasing the powdered JGC contents. This increment in mass loss peaks is due to the addition of the recycled jute fiber fraction constituents.
As can be seen in Figure 11, the resulting RJG1 specimens showed an increase in strength from 3 to 8.8 MPa after using just 2.5%wt of JGC as filler. Increasing the percentage of JGC filler to 5 wt% of the total weight led to a decrease in strength to 7.7%, but an increase in material elongation and improvement in terms of ductility were also observed. When the JGC filler addition was increased to 10 wt%, the strength of the resulting materials decreased by 4.4%, yet their mechanical behavior was close to that of the composite materials, JGC; also, the ductility was increased, while elongation, 0.007, was seven times greater than that of the reference geopolymers.
Figure 11. Stress–strain curves of reference geopolymer (RG), jute-reinforced geopolymer composite (JGC) and recycled jute-reinforced geopolymer composites (RJG1, RJG2, and RJG3).
Figure 12 shows typical fractographs of the recycled jute-based composites with different ratios of powdered JGC filler, RJG2 and RJG3, after flexural tests. The microstructure of the RJG3 is characterized by the presence of three phases (Figure 12A): geopolymer matrix (point 1), residual metakaolin (point 2), and RJG filler (point 3). The major phase is the geopolymer matrix, which is characterized by a well-organized nano-pore network (Figures 12A,B, point 1). Compared with JGC (Figure 4), a minor layer of residual metakaolin is observed in RJG3 (Figures 12A,B). This is an indication of enhancement in the setting reactions due to the addition of the RJG porous fillers, and thus more geopolymer matrix was formed. The porous features of the RJG filler (Figure 12A point 3) assist the slow release of the alkaline solution during curing, so that more products of the binder material (geopolymer matrix) were formed.
The pulled-out micro jute fibrils of the RJG filler can be clearly seen (marked by the yellow arrow) distributed on the fractographs of RJG3 (Figure 12C, point 4) and RJG2 (Figure 12D, point 4). It may be induced that the jute fibrils were pulled out during the fracture process. These fibrils would help consume fracture energy and enhance the flexural strength (Figure 10), of the composites via the mechanical interlock between the jute micro fibrils and the geopolymer matrix. The distribution of the holes and grooves left after the jute microfibrils were pulled out is shown in Figures 12A,B (point 5). The roots of the microfibrils are seen to be well bonded with the matrix, indicating a good bonding state in the composites. However, when the content of microfibrils reaches 10 wt%, RJG3, the microfibrils showed apparent agglomeration (Figure 12C, point 7) owing to their high surface energy and chemical adsorption. Agglomeration could result in defects such as residual pores in the prepared composites. During the fracture process, such defects might easily evolve into cracks due to local stress-concentration, which would be the main reason behind the decrease in flexural strength of composites with higher jute microfibril content. The fact that the cracks stop across the microfibril in the composites (Figure 12C, point 6) is an indication that the microfibrils helped to hinder cracking on the path of propagation and further enhance the flexural strength of the composites.
The findings of this study demonstrate that the wastes of jute-reinforced geopolymer composite (JGC) affect the properties of new geopolymer materials (RJ1, RJ2, and RJ3) in two senses: mesopore structure (Figure 4C), and amorphous aluminosilicate constituents (Figure 4B). The primary geopolymer aggregates with mesopore structure absorb the alkali solution during mixing and release it adequately through secondary geopolymerization reactions (Alshaaer, 2020). The unreacted metakaolin and the amorphous sodium aluminosilicate matrix react with the alkali solution to form a strong binder matrix between the aggregates and the geopolymers (Alshaaer, 2013). At the same time, jute microfibers play an important role and result in the production of materials of higher strength and highly elastic properties, as seen for RJG3 and other composite materials (Mohanty et al., 2000).
This study confirms that JGC can be completely recycled as reactive fillers and jute microfibrils, the new material exhibiting high mechanical performance. The jute-based geopolymer composites can therefore be recycled and used according to circular economy principles. A diagram of the life-cycle of jute-reinforced geopolymer composite is offered in Figure 13.
The novelty of this study lies in the preparation and evaluation of the effect of continuous bidirectional jute fibers in addition to determination of the properties of geopolymer composites. Furthermore, the prepared jute-based geopolymer composites were completely recycled and introduced as filler material in a new geopolymer matrix. These objectives are in line with circular economy principles for natural fiber-based geopolymer composites.
This study focuses on novel, functional, green composites of a geopolymer matrix that is reinforced with bidirectional jute fibers. The jute fibers are arranged as continuous wrapped bundles of 1 mm diameter, while each jute fiber is made up of several fiber cells held together by lignin. The ultimate flexural strength is increased fourfold by introducing bidirectional jute fibers in the geopolymer matrix with a weight percentage of 15 wt%. The ultimate flexural strength of the JGC, 12 MPa, was obtained at elongation of approximately 0.115, followed by softening of the composite. The JGC exhibits a strain hardening modulus of 66 MPa.
New jute-based composites with mesoporous aggregates and microfibers, prepared by recycling the JGC, showed an increase in strength from 3 to 8.8 MPa when only 2.5 wt% of JGC was used as filler. Increasing the percentage of JGC filler to 5 wt% of the total weight resulted in 7.7% decreased strength, increased material elongation and an improvement in ductility. Increasing the JGC filler to 10 wt% led to a decrease in strength of the resulting materials, to 4.4 MPa, yet their ductility was enhanced with high failure strain, 0.007. This strain is seven times greater than that of the reference geopolymers. Recycling the jute-reinforced geopolymer composite was found to have three effects on new geopolymer materials in terms of jute microfibrils, mesopore structure, and amorphous aluminosilicate constituents. It is also confirmed that JGC can be completely recycled as reactive filler and jute microfibrils, providing for a new material giving high mechanical performance. Thus, the jute-based geopolymer composites can be completely recycled following the principles of circular economy.
The raw data supporting the conclusions of this article will be made available by the authors, without undue reservation.
MA carried out the experiment and wrote the manuscript.
The author declares that the research was conducted in the absence of any commercial or financial relationships that could be construed as a potential conflict of interest.
Alshaaer, M. (2013). Two-phase geopolymerization of kaolinite-based geopolymers. Appl. Clay Sci. 86, 162–168. doi: 10.1016/j.clay.2013.10.004
Alshaaer, M. (2020). Synthesis and characterization of self-healing geopolymer composite. Constr. Build. Mater. 245, 118432. doi: 10.1016/j.conbuildmat.2020.118432
Alshaaer, M., Abu Mallouh, S., Al-Kafawein, J., Al-Faiyz, Y., Fahmy, T., Kallel, A., et al. (2017). Fabrication, microstructural and mechanical characterization of luffa cylindrical fibre - reinforced geopolymer composite. Appl. Clay Sci. 143, 125–133. doi: 10.1016/j.clay.2017.03.030
Alshaaer, M., Alkafawein, J., Al-Fayez, Y., Fahmy, T., and Hamaideh, A. (2015). “Synthesis of geopolymer cement using natural resources for green construction materials,” in Recent Advances in Earth Sciences, Environment and Development. Proceedings of the 8th International Conference on Engineering Mechanics, Structures, Engineering Geology (EMESEG’15), Konya.
Alshaaer, M., Cuypers, H., and Wastiels, J. (2002). “Stabilisation of kaolinitic soil for construction purposes by using mineral polymerisation technique,” in Proceedings of the 6th International Conference Technology for Developing Countries, Amman.
Alshaaer, M., El-Eswed, B., Yousef, R. I., Khalili, F., and Rahier, H. (2012). Development of functional geopolymers for water purification, and construction purposes. J. Saudi Chem. Soc. 20, S85–S92.
Alshaaer, M., Zaharaki, D., and Komnitsas, K. (2014). Microstructural characteristics and adsorption potential of a zeolitic tuff–metakaolin geopolymer. Desalination Water Treat. 56, 338–345. doi: 10.1080/19443994.2014.938306
Aluko, O. G., Yatim, J. M., Ab Kadir, M. A., and Yahya, K. (2020). A review of properties of bio-fibrous concrete exposed to elevated temperatures. Constr. Build. Mater. 260:119671. doi: 10.1016/j.conbuildmat.2020.119671
Chaitanya, S., Cheedarala, R. K., and Song, J. I. (2020). Microwave-synthesized Mg+2 doped jute fibers and their application as a reinforcement in biocomposites. Compos. B Eng. 197:108154. doi: 10.1016/j.compositesb.2020.108154
Correia, E., Torres, S., Alexandre, M., Gomes, K., Barbosa, N., and Barros, S. (2013). Mechanical performance of natural fibers reinforced geopolymer composites. Mater. Sci. Forum 758, 139–145. doi: 10.4028/www.scientific.net/msf.758.139
Drzal, L. T., and Madhukar, M. S. (1993). Fibre-matrix adhesion and its relationship to composite mechanical properties. J. Mater. Sci. 28, 569–610. doi: 10.1007/bf01151234
Food and Agriculture Organization of the United Nations (2010). Future Fibres. Available online at: http://www.fao.org/economic/futurefibres/home/en/ (accessed March 15, 2021).
Geissdoerfer, M., Savaget, P., Bocken, N., and Hultink, E. J. (2017). The Circular Economy – A new sustainability paradigm? J. Clean. Prod. 143, 757–768. doi: 10.1016/j.jclepro.2016.12.048
Guido, S., Suyeon, K., Bruno, B., Javier, N., and Rafael, A. (2020). Optimization of a reinforced geopolymer composite using natural fibers and construction wastes. Constr. Build. Mater. 258:119697. doi: 10.1016/j.conbuildmat.2020.119697
Komnitsas, K., Zaharaki, D., and Perdikatsis, V. (2007). Geopolymerisation of low calcium ferronickel slags. J. Mater. Sci. 42, 3073–3082. doi: 10.1007/s10853-006-0529-2
Komnitsas, K., Zaharaki, D., and Perdikatsis, V. (2009). Effect of synthesis parameters on the compressive strength of low-calcium ferronickel slag inorganic polymers. J. Hazard. Mater. 161, 760–768. doi: 10.1016/j.jhazmat.2008.04.055
Komnitsas, K., Zaharaki, D., Vlachou, A., Bartzas, G., and Galetakis, M. (2015). Effect of synthesis parameters on the quality of construction and demolition wastes(CDW) geopolymers. Adv. Powder Technol. 26, 368–376. doi: 10.1016/j.apt.2014.11.012
Korniejenko, K., Fraczek, E., Pytlak, E., and Adamski, M. (2016). Mechanical properties of geopolymer composites reinforced with natural fibers. Procedia Eng. 151, 388–393. doi: 10.1016/j.proeng.2016.07.395
Li, W., and Xu, J. (2009). Impact characterization of basalt fiber reinforced geopolymeric concrete using a 100-mm-diameter split Hopkinson pressure bar. Mater. Sci. Eng. A 513, 145–153. doi: 10.1016/j.msea.2009.02.033
Marczak, D., Lejcus, K., and Misiewicz, J. (2020). Characteristics of biodegradable textiles used in environmental engineering: a comprehensive review. J. Clean. Prod. 268, 122–129.
Mohanty, A. K., Misra, M., and Hinrichsen, G. (2000). Biofibres, biodegradable polymers and biocomposites: an overview. Macromol. Mater. Eng. 276, 1–24. doi: 10.1002/(sici)1439-2054(20000301)276:1<1::aid-mame1>3.0.co;2-w
Natali, A., Manzi, S., and Bignozzi, M. (2011). Novel fiber-reinforced composite materials based on sustainable geopolymer matrix. Procedia Eng. 21, 1124–1131. doi: 10.1016/j.proeng.2011.11.2120
Pan, N., Day, A., and Mahalanabis, K. K. (1999). Chemical composition of jute and its estimation. Man-Made Textiles India, 42, 467–473.
Puertas, F., Amat, T., Fernández-Jiménez, A., and Vázquez, T. (2003). Mechanical and durable behaviour of alkaline cement mortars reinforced with polypropylene fibres. Cem. Concr. Res. 33, 2031–2036. doi: 10.1016/s0008-8846(03)00222-9
Silva, G., Kim, S., Aguilar, R., and Nakamatsu, J. (2020a). Natural fibers as reinforcement additives for geopolymers - a review of potential eco-friendly applications to the construction industry. Sustain. Mater. Technol. 23:e00132. doi: 10.1016/j.susmat.2019.e00132
Silva, G., Kim, S., Bertolotti, B., Nakamatsu, J., and Aguilar, R. (2020b). Optimization of a reinforced geopolymer composite using natural fibers and construction wastes. Constr. Build. Mater. 258:119697.
Sun, P., and Wu, H. (2008). Transition from brittle to ductile behavior of fly ash using PVA fibers. Cem. Concr. Compos. 30, 29–36. doi: 10.1016/j.cemconcomp.2007.05.008
Yousef, R. I., El-Eswed, B., Alshaaer, M., Khalili, F., and Khoury, H. (2009). The influence of using Jordanian natural zeolite on the adsorption, physical, and mechanical properties of geopolymers products. J. Hazard. Mater. 165, 379–387. doi: 10.1016/j.jhazmat.2008.10.004
Keywords: geopolymers, jute fiber, composite, stress-strain, ductility, circular economy, recyclability
Citation: Alshaaer M (2021) Synthesis, Characterization, and Recyclability of a Functional Jute-Based Geopolymer Composite. Front. Built Environ. 7:631307. doi: 10.3389/fbuil.2021.631307
Received: 19 November 2020; Accepted: 08 March 2021;
Published: 26 March 2021.
Edited by:
Castorina Silva Vieira, University of Porto, PortugalReviewed by:
Dang Mao Nguyen, EA4038 Laboratoire Génie des Procédés et Matériaux (LGPM), FranceCopyright © 2021 Alshaaer. This is an open-access article distributed under the terms of the Creative Commons Attribution License (CC BY). The use, distribution or reproduction in other forums is permitted, provided the original author(s) and the copyright owner(s) are credited and that the original publication in this journal is cited, in accordance with accepted academic practice. No use, distribution or reproduction is permitted which does not comply with these terms.
*Correspondence: Mazen Alshaaer, bWF6ZW4uYWxzaGFhZXJAeWFob28uY29t
Disclaimer: All claims expressed in this article are solely those of the authors and do not necessarily represent those of their affiliated organizations, or those of the publisher, the editors and the reviewers. Any product that may be evaluated in this article or claim that may be made by its manufacturer is not guaranteed or endorsed by the publisher.
Research integrity at Frontiers
Learn more about the work of our research integrity team to safeguard the quality of each article we publish.