- Advanced Institute of Industrial Technology, Tokyo, Japan
Currently, technologies related to the construction industry have increased in their complexities and garnered important advancements. However, the pandemic upset the entire structure of industries, including the construction industry. Hence, a precise prescription is required for a right future direction of the construction industry. This study aims to provide a method for understanding the fundamental characteristics of the building industry via industrial analysis. In this article, the “Architecture concept” is adopted as an academic tool of consideration and is carried out a practical analysis on the building industry to provide a novel perspective. Previous studies analyzed several industries in this “architectural concept.” However, the analysis based on this concept has not progressed significantly for the building industry. Because this concept was created focusing on architecture, it has a high affinity with the building industry. Therefore, with the cooperation of multiple experts, we categorized the building components and modularization of the production process according to the selected indicators; then, we investigated the trends of the entire Japanese building industry. By analyzing the results of this survey, one can understand the basic correlation between the physical modularity of components and the independence of the design information creation process. This study contributes to providing the method to understanding the fundamental characteristics of the building industry and provides to presents the possibility of inter-industry and inter-regional comparisons from this perspective.
Introduction
In many aspects of the construction industry, including building demand, building planning ideas, supply chains, and building construction processes, the impact of the pandemic and the development of fundamental technology including information technology, computer technology and communication technology, have increased the prospects of novel systems requiring alterations (Bodenstein et al., 2020). In particular, the approach to physical distance is being replaced by remote work and video conferencing (Brussevich et al., 2020; Kikuchi et al., 2020). Consequently, this approach is consensually considered to be effective for collaborative design and component production across regions, which has never been implemented in the construction industry. Therefore, it is necessary to discuss characteristics of the construction industry to grasp the different trends in each region by understanding the characteristics of the construction industry in these regions. Hence, I would like to establish a method for grasping the characteristics of building production, as well as consider the direction in this industry that can be comprehended by this method.
The design of projects in the construction industry is performed in a multi-layered process (Bennett 1991). Many designers, such as architectural, architectural structural, and architectural equipment designers, as well as designers of components such as incidental products and systems, carry out designs according to conventional processes. In the case of a building with a high degree of complexity and large number of parts, architects, designers, and engineers of various parts, materials, and systems, collaborate to create designs.
Furthermore, customization is often performed in the building industry with all projects designed with unique designs, structures, and specifications. In addition, technical knowledge in this industry is wide and composed of several subject areas, such as architectural planning, design, structure, materials, air conditioning equipment, sanitary equipment, and electric equipment areas. Apart from architectural designers, several component and product designers participate in one architectural project. To understand the characteristics of a building industry, it is considered that the analysis of design sharing from the architectural perspective is crucial.
This research project was conducted from 2018 to 2020. The outline of the Japanese construction industry in the past decade is as follows. First, an overview of the situation 10 years ago and its change are provided, focusing on the relationship between general contractors and suppliers. The building investment value was 43.0 trillion yen in 2009, 47.5 trillion yen in 2014, and 65.4 trillion yen in 2019 (JFCC 2020). The number of bankruptcies during those periods were 4,087 in 2009, 1965 in 2014, and 1,444 in 2019 (JFCC 2020). The percentages of general contractor orders received were 61.7% in 2009, 64.3% in 2014, and 65.6% in 2019 (JFCC 2020). Overall, Japan’s construction investment grew steadily during this period, but the relationship between general contractors and supplier orders has not changed significantly. The Japan Federation of Construction Contractors (JFCC) shared the same view and commented no significant change in the division of work between general contractors and suppliers.
The purpose of this study is to develop the idea of industrial analysis and provide an understanding for the characteristics of the present industry, as well as create a prescription for the discussion on future possibilities. To develop such an idea, two theories can be considered: functional theory, which statically explains why the system exists, and occurrence theory, which explains how the system was created dynamically. In this research, I functionally consider the project organisation of a relatively stable building industry. In particular, I consider the relationship between the characteristics of the objects to be created and the organisation of the construction project. Specifically, I will consider the relationship between the characteristics of the component to be created and the design information creation process for that component.
Theoretical Background
Industrial Analysis Based on Design Information
The organisation of a construction project, which is an important aspect of the construction industry, is created transiently during the project period. This organisation consists of many companies and has a complicated structure. When discussing the industrial theory of the construction industry, understanding the characteristics and modus operandi of an organisation is part of the main perspective. Therefore, I focus on design information, which contains the purpose behind the design carried out by organisations. It is therefore important to understand how to share knowledge, such that the creation of information and analysis of its flow is enabled. Several studies have been conducted on the sharing of knowledge, as well as the organisational possibilities that result from sharing.
Knowledge sharing can be understood as receipt and provision of information of tasks, and the important point is knowledge sharing includes collaborations with others to develop new processes and ideas (Park and Kim, 2015). Knowledge sharing has an important influence on the development of products or services, through from actions such as solving problems, the will to assist others, and learn new skills from others. (Davenport and Prusak, 2000). Knowledge sharing can also be gained via communication with other experts, which can be developed with objectivisation and documentation of knowledge passed on to others (Cummings, 2004; Sousa et al., 2015).
There are several discussions on the importance of the connection between organisational capability and knowledge sharing behaviour (Sita Nirmala and Chitale, 2012; Swift and Hwang, 2013). In general, it is possible to understand that learning is the result of processing significant knowledge (Swart and Kinnie, 2010). It is also possible to recognise that knowledge sharing could be a foundation for organisational capability (Sita Nirmala and Chitale, 2012). Behaviour of knowledge sharing could improve organisational capability through knowledge creation, transfer, and mobility (Lee et al., 2012; Swift and Hwang, 2013). On the other hand, with knowledge sharing, designers and engineers sustain their learning flow throughout the whole organisation and develop their flow for practical decision (Yang, 2007).
Organisational capability can have a important role in acquiring knowledge to correspond to the transformation of external environment (Hoe and McShane, 2010). On the other hand, organisational capability is recognised as an significant point to gain and maintain a continuous advantage for organisations in a business development (Guinot et al., 2016).
Most of these studies do not target transient project-type organisations, such as those in the building industry. In addition, very few studies present design information as a target that can be obtained by organisational learning. However, differences in the conditions for each project and the complexity of sharing designs are inevitable considerations in the construction field. Therefore, in this paper, I focus on the characteristics of organisational ability obtained from organisational learning. Then, I develop a method to objectively understand the sharing of information and knowledge created via organisational ability. As the main target of this research, I consider the process of creating design information shared by many organisations in the construction field.
In these studies, production activities by multiple organizations have been considered, and based on these considerations, knowledge sharing and organizational capabilities have been discussed. However, these discussions restrict a unified perspective on conceptual and abstract knowledge sharing, as well as organizational capabilities. Therefore, in this research, I focus on the process of creating design information expressed by them. In addition, there may be limits to the subject of research in two respects.
First, these previous studies do not target temporary project-type organizations, which are conventional in the construction industry. Second, these previous studies have not fully discussed projects in areas that span several technical and knowledge areas, such as the building industry. Differences in the conditions of each project and the complexity of sharing design work, as well as important issues in the construction field based on such projects, are inevitable. Therefore, it is crucial to analyse the process of creating design information, which is the same process for many organizations in the construction field.
In this study, I consider the influence of the characteristics of design information on design work sharing from the perspective of modularity. In particular, an empirical analysis is conducted focusing on the factors affecting the modularity of function and structure. Several studies have investigated the relationships between companies, including their product modularity analyses, for the automobile, computer, and other industries in various regions, including Japan. However, there has been almost no analysis on the building industry, which deals in technology areas from cutting-edge to fairly mature, or how the interdependence of components is managed by the various designers involved in a project.
Product Modularity and Modularization
In this section, I consider how the characteristics of design information affect the sharing of design work from the viewpoint of modularity, which is a typical method for analyzing design information. Specifically, an empirical analysis will be conducted focusing on the factors that affect the modularity of functions and structures. Various studies have analyzed the relationships between companies in terms of product modularity in automobiles, computers, and other industries in various regions, including Japan (Fujimoto, 2012; Kobayashi et al., 2014; Manning and Reinecke 2016; Liu et al., 2018). However, little research has been done on Architecture-base on the technical characteristics of the building industry. The reason for this cannot be logically proved. Possible reasons are the characteristics of the building industry, such as the complexity of technical knowledge, the diversity of related industries, and the peculiarities of each project. For these reasons, it is possible that many mass-produced products were studied in academic fields such as business administration, sociology, and design engineering, but architecture was not studied.
Architectural concepts, which are design concepts based on the interdependence of elements, were studied by Simon and Alexander, researchers in the fields of economics and architecture, respectively (Alexander, 1964; Simon, 1969). Therefore, this theory was partly derived from the perspective of architecture. Considering the importance and effectiveness of studying architecture based on this theory, I consider that there is great potential in proceeding with it in this study. This idea leads to the development of a method that can elucidate the characteristics of conventional industrial structures.
Concept of Product Architecture
For a long time, one of the concepts highlighted by the field of business administration is modularisation, which focuses on the interdependence between components (Alexander, 1964; Simon, 1969). This concept suggests that when creating an artifact, a pattern is created in the interdependence of the constituent elements due to the design concept of the creator. Alexander created this idea for architectural composition. This design concept expressed in the function and composition of the created product is called “Product Architecture” (Baldwin and Clark, 2000). In other words, “Product Architecture” is a basic design concept. In particular, it is based on how the functions of a product are configured and how they are distributed among parts and materials (Ulrich, 1995).
There are two typical indexes in the concept of “Architecture”: “Modular–Integral” and “Open–Close.” An index of “Modular–Integral” is based on interfaces between elements (Ulrich, 1995). If a system is “Integral Architecture,” the rules of design of interfaces must be adjusted to each other, and optimum coordination must be sought for that particular system to fully elicit its potential performance. In contrast, “Modular Architecture” provides standardized interfaces linking different parts and modules. Therefore, it is possible to produce various products by putting together independent parts as long as they are compatible with these interfaces. With “Modular Architecture,” the independence of each module is maintained, and evolution of a system is accelerated. Standardization of interfaces between modules causes a restriction of the range of total system performance (Blees et al., 2010; Mortensen et al., 2016).
“Open Architecture” is one kind of modular “Architecture” with industry standardized interfaces, under which parts and modules can be gathered across corporate and product borders. Open is based upon the concept concerning the common use coverage of interfaces; it is possible to make the information of interfaces simple in modular “Architecture.” This is the point of the relationship of modular and open indexes. The Open-Closed axis is a very important viewpoint, but this paper focuses on the index of Modular–Integral axis to clarify the confusion between the functions of products.
Ulrich defines modular “Architecture” as “a one-to-one mapping from functional elements in the function structure to the physical components of the product, and specifies de-coupled interfaces among components” (Ulrich, 1995). On the other hand, integral “Architecture” is defined as “a complex (non-one-to-one) mapping from functional elements to physical components and/or coupled interfaces between components”. It is important to note that most products do not fully satisfy the definition of either modular or integral “Architecture.” (Clark and Fujimoto, 1991; Fujimoto, 2019).
Returning to the reference of firms’ competitiveness in the manufacture of products with an integral “Architecture,” examples of this type of product includes cars, motorbikes, games software, and compact consumer electronics etc (Bresman, 2013; Cabigiosu et al., 2015). By competitiveness, Fujimoto is referring to both productive and market performance. Productive and market performance in turn influence profit, and competitiveness results from having leading performance in any of these areas.
Integral Architecture has the potential to renew the entire product fundamentally (Clark and Fujimoto, 1991). Fundamental value engineering of materials or parts, such as using reused parts, using recycled materials, and low-cost components, will ultimately impact the design of other parts. Moreover, there is some possibility of integration of Architecture of new products. Thoroughly changing the Architecture from scratch to fundamentally reduce all development costs can be a radicallyintegral product in the whole of industry.
Research on integral Architecture has been conducted in various industrial areas in Japan, and the trends have been pointed out (Tomita 2009; Ikuine, 2012, Fujimoto, 2012; Na and Park, 2016). This is consistent with the point that Japanese companies tend to be strongly integral, as a result of Architecture-based analysis of many products (Fujimoto, 2006). Some researchers have discussed objects that integrate products and services as a system (Dewit et al., 2021), but it is essential to discuss physical structures and soft artificial objects that do not appear as forms.
In the next stage of our study, I tried to analyze the merit and demerit of the systems of “Architecture” type (Ulrich, 1995; Otto et al., 2016). Generally, with modular “Architecture,” the independence of each module is accelerated to be developed and maintained by a total system. On the other hand, standardization of interfaces between modules causes a restriction of the range of total system performance. With integral “Architecture,” it is possible to get total high-performance to meet any requirement. However, it is difficult to get the fundamental grade performance with a small amount of resources, and it is not so easy to stop the development of the performance of a system in many cases (Figure 1). These two types have their own merits and demerits. It is almost impossible to say which is better in general—they are different types of system. But it is necessary to understand the characteristics of these types and make strategies to fit these “Architecture” types.
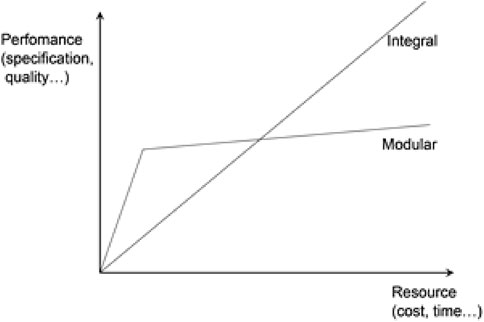
FIGURE 1. Performance of integral “architecture” and modular “architecture” (reference; Ulrich, 1995).
This fundamental idea is applied in different research areas and used in investigations on production systems. Based on this viewpoint, the design concept characteristics were evaluated in this study, and the advantages and disadvantages of the modular and integral types were examined. Previous studies utilizing this concept include content focusing on production systems (Allman and Zhang 2020) and content related to the fusion of creators’ organizations (Tee et al., 2019).
The situation in the construction industry applies to these conditions. Companies of various parts and materials in the building industry make modular products for their own companies, and there are many ideas that are not industry standards.
Researches pointed out the relationship between organizational modularity and product modularity, and that is the hypothesis of the Mirroring (Cabigiosu and Camuffo, 2012; MacCormack, et al., 2012).
The most important point of this study is that organizational modularity makes influence with creating product modularization (Brusoni and Prencipe, 2011). By recombining organizational units, it is possible to establish a physical interface and achieve interoperability between modules by realizing organizational modularity of research and development (Mortensen, et al., 2011).
Despite scant discussions about the construction industry, it is not unlikely that it will be an essential indication due to the characteristics of the industry in which many technical fields participate. Therefore, it has been considered that the modularization of products can be a useful factor in realizing the sustainability approach of an organizational unit.
If one can understand the design concept expressed by the designer, then one can understand the modularization and integration of components. In this case, it is effective to consider that it may appear as a result of the activities conducted based on the design concept. In other words, it is necessary to pay attention to the structural composition of the designed object, the functional composition of the designed object, and the relationship between the function and structure of the designed object. In particular, buildings are constructed by combining different components. Therefore, depending on whether each component is modular, it is possible to understand the characteristics of each building, which is a large-scale human-made object as a whole.
The following is a summary of the contents of the above review. The concept of architecture, which is an academic tool for industrial analysis, has been used as an academic perspective when creating product configurations and product creation processes, as in many previous studies. In particular, these studies have logically discussed modularization based on rationality to reduce complexity and integration based on the idea of improving overall performance. However, despite the fact that this idea was proposed for the building domain, there were few cases where the Architecture concept was used for the building industry. Therefore, since there are many previous studies targeting Japanese industry, it is considered to be important for examining the Japanese construction industry.
Methodology
Technical Knowledge Used in Construction Design
Architecture is built using several types of elements. Therefore, technical knowledge in many industrial and product fields is required. However, technical knowledge used for design is extensive and it is difficult for architects to design all of the elements. For example, knowledge of many fields such as electricity, electronics, information, and machinery, and knowledge in specialised fields such as frames, fittings, equipment, security systems, and management systems is required. The architectural process must successfully integrate all of these. In Japanese architectural projects, architects who are design contractors play an important role during the design stage. In each project, the role of the architect is to create architectural designs, including integrating knowledge from outside of the architectural field.
Usually, in the Japanese construction industry, the architectural designer is the design manager on the contract. The design manager divides many design processes with architectural structural designers, building equipment designers, and product and component designers. In this process, it is important to consider how the scope of design work and scope of responsibility for quality are considered. The division and sharing of work and responsibilities is among multiple designers based on their different fields of technical knowledge. It is necessary to be understood carefully the process, such as who created the policies and who approved the content, to confirm the root of any problems.
The design manager is contractually responsible for all architectural parts, materials, and product designs. Therefore, the design manager is responsible for explaining the reasons for choosing the products and materials. They also have an obligation to finalize architecture, while making adjustments during the process. However, architectural designers may not have knowledge of all of the details involved with the various parts, equipment, and other components. For example, they may rely on the knowledge of a parts designer without having knowledge of the part. For that purpose, architects need to clearly show the reasons for introducing products and systems, and provide technical guarantees on safety and functionality, in cooperation with many engineers.
In this section, I consider who creates the basic design information, who creates detailed information on production, who stores design information, and who has responsibility for quality in the architectural design process.
As architecture is based on many different kinds of technical knowledge, some elements require highly specialised knowledge. If design management is done incorrectly, the designers and builders responsible for the whole building may not be able to successfully evaluate the various elements. For example, there is a possibility that information provided by the parts and materials designers is used by the main designer and the constructor without proper understanding. In some cases, obvious defects may be included because of these communications issues.
In this chapter, I examine the relationship between the main designer and the part designer by following the location of technical knowledge while referring to the concept of previous researches on the Japanese automobile industry. (Nishiguchi and Alexandre, 1997; Fujimoto, 2014; Fujimoto, 2019).
Table 1 shows the contents of previous research considering the automotive industry. In this study, the authors focused on Design works and Responsibility and authority as indicators, and classified the relationships between multiple designers into five types. In the case of internal manufacturing, only the car manufacturer has technical knowledge. In the case of commercial parts, only the part supplier has technical knowledge.
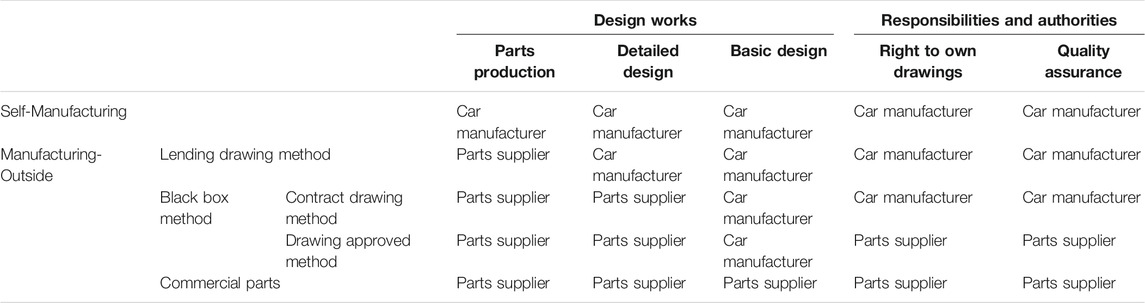
TABLE 1. Classification of design activities in the automobile industry (reference; Fujimoto and Kastu, 2001).
One characteristic of the Japanese automobile industry highlighted by previous research is that multiple designers can design the same parts. For example, the designer of the car manufacturer and of the part supplier may have technical knowledge to design the same part. In other words, in this case, a plurality of designers has the same level of technical knowledge. In particular, it has been emphasised that the car manufacturer designer and the part supplier designer have almost the same level of technical knowledge in the contract drawing method and drawing approval method. This indicates that designers in both positions can stimulate each other and maintain a high level of technical knowledge. It is also considered that the product shows that high performance can be maintained.
Patterns of Design Sharing in the Construction Industry
In the design process for each component of the building, the designer begins the basic design of the component based on the overall design concept of the building. Table 2 shows this design process through a summary of the design assignments and represents a pattern based on the assignment among multiple designers. The ‘Main architect’ includes not only typical architects but also the structural and equipment engineers who are contractually required to take responsibility for the client. The “General contractor” is a building contractor who contracts directly with the owner, and the ‘Sub-contractor’ is responsible for one type of component.
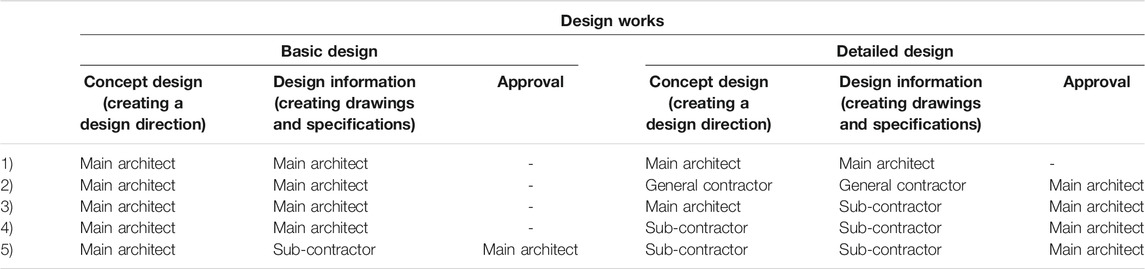
TABLE 2. Classification of design process in architectural industry (basic design and detail design).
The contents of the design sharing on the horizontal axis in Table 2 represent the roles and duties that can be shared in the design process. The design process can be broadly divided into basic design and detailed design. In each process, it is possible to divide the design policy, create the actual design information, and approve the design information.
The core design information is created mainly by translating the user’s request into the form and function of the component. Therefore, it is considered natural that the main designer creates the design information. The main designer should have a direct meeting with the client and understand what the client wants. The main architect is responsible for explaining the design contents to the client.
Given the functionality of this main architect, I consider the patterns in Table 1 individually. Table 2 describes the roles of designers and engineers in the basic design and detailed design processes for components, materials, and equipment installed in buildings. It can be difficult for those not responsible for creating the design information to continuously obtain updated knowledge that can be gained from the process of creating the design information. In addition, when a designer/engineer who does not create design information is only in charge of approval, it may be difficult to maintain the ability to judge approval. If a designer/engineer has not created a design policy and has not created design information for many years, it is challenging to maintain technical knowledge.
For the pattern of 1) in Table 2, the main architect sets the design policy and creates design information (information on the design summarised in drawings, specifications, etc.). In pattern 2), the main architect is in charge of creating a basic design policy, creating design information for the basic design, and approving the detailed design. Then, a general contractor engineer is responsible for creating detailed design policies and design information. In both of these patterns, the main architect and general contractor who contracted with the client participated in the design process.
In 3), the main architect is in charge of creating a basic design policy, creating basic design information, creating a detailed design policy, and approving detailed design information. Then, the engineer of the subcontractor creates design information of the detailed design. In this pattern, the client does not contract with a subcontractor. Therefore, in some cases, the client may not be aware that the subcontractor is participating in the project. However, the main architect creates a detailed design policy, confirms that the design information is in accordance with the policy, and approves it. Thereby, the main architect can fully make decisions based on his technical knowledge.
In 4), the main architect is in charge of creating the basic design policy and design information, and approving the detailed design. A subcontractor engineer is responsible for creating a detailed design policy and creating design information. The main architect will not be responsible for creating policies and creating design information for the detailed design. This is repeated for many projects, making it difficult for the main architect to maintain detailed design technical knowledge.
In 5), the main architect is in charge of creating the basic design policy, approving the basic design information, and approving the detailed design information. In other words, the main architect does not take charge of creating the design information at all. As in 4), if this is repeated in many projects continuously, there is a concern that the main architect may have a problem with keeping detailed design technical knowledge. In particular, not creating design information means not having to make many decisions and learning experiences in the actual design process. This means that the main architect may not be able to accumulate technical information and knowledge throughout each building project.
Table 3 summarises the detailed design of parts, materials, and equipment, and contracts, production, and responsibilities, corresponding to 1)−5) in Table 2. The contracted designer is a designer recognized by the client. In many Japanese architectural projects, the client only contracts with the main architect and the main builder. In other words, the client does not make direct contract with most subcontractors. In many cases, even if many subcontractors participate in the project, the client hardly recognizes which company is participating. However, the quality of parts, materials, and equipment may not be guaranteed by the main architect or main contractor who has contracted directly with the client. This is considered problematic both legally and practically. In addition, an organization that guarantees quality must respond to complaints after completion. For this purpose, any organization that performs quality assurance needs to store drawings and specifications that contain design information.
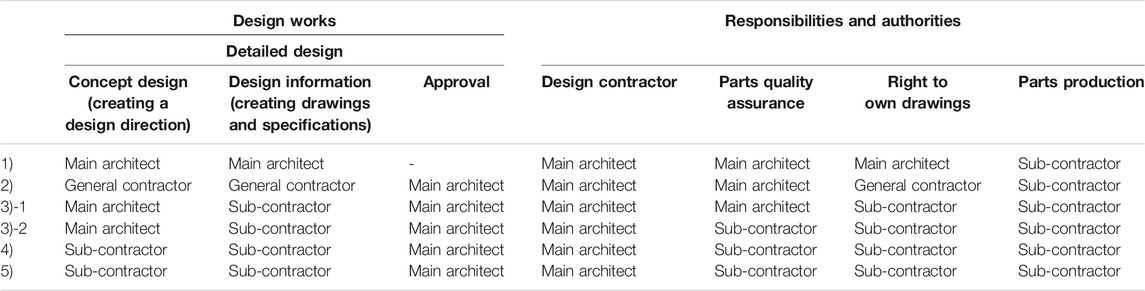
TABLE 3. Classification of design process in architectural industry (detail design and responsibilities).
In pattern 1), the main architect is a contractor with the client. The architect is responsible for quality assurance and stores design information. Then, the subcontractor manufactures the target parts, materials, and devices. In 2), many aspects are the same as in 1), but the general information is stored by the general contractor. In the case of 2), the quality is nominally guaranteed by the main architect, but it is possible that the general contractor may actually guarantee quality. Category 3), in Table 2 has two sub-categories in Table 3. In 3) −1, the client contracts with the main architect, and the main architect is in charge of quality assurance. The subcontractor is responsible for creating and storing design information, such as drawings. The difference between 3) −2 and 3) −1 is that 3) −2 guarantees the quality of the sub-contractor’s work. For both 3) −1 and 3) −2, the subcontractor saves the design information. Therefore, the subcontractor may be responsible for substantial quality assurance. In 4) and 5), the main architect contracts with the client, while the subcontractor is responsible for the quality assurance of the target parts, materials and equipment, storage of design information, and manufacturing. In this case, the main architect is the contractor, but the subcontractor is in charge of all substantive actions. For the client, a subcontractor who does not have a direct contract will be responsible for manufacturing and quality assurance. Clients often do not understand why the subcontractor is involved in their project, which has serious implications.
It is possible to describe these frameworks using some examples.
In steelwork, the building structure designer plans the construction structure during the primary design process. In the detailed design process, the direction is determined by the building structure designer, but the engineer of the steel frame fabricator draws the structural details based on the direction. Next, the building structure designer confirms the drawing contents, approves it if no problem in the contents is found, and takes responsibility for the contents. However, the drawing is drawn by the fabricator and contains detailed information about the detailed drawing level, and the fabricator owns the drawing. Subsequently, the fabricator manufactures the actual steel frame member according to the specifications. Therefore, steelwork is the type of 3)−1.
In the case of an elevator component, the architect selects the outline and basic specifications of the elevator. However, except for the outer shape and basic specifications, the engineers at the elevator company design and take responsibility. Elevator company engineers are responsible for several processes, from basic design to detailed design, manufacturing, and installation. Therefore, in the architectural blueprint, only the outer shape and specifications of the elevator are specified. Therefore, elevator component is the type of 5).
There have been many ideas about the causes of the selection of different sharing patterns. For example, Asanuma attempted to explain it from the perspective of “relevant skills” based on the peculiarities of corporate technology (Asanuma and Kikutani, 1992). In addition, attempts have been made to explain the concept of organizational ability (Clark and Fujimoto, 1991; Fujimoto, 2006) in regard to the uniqueness of “organizational ability”. The idea of ‘transaction cost theory’ was also proposed (Williamson, 2009) based on uncertainty, transaction frequency, and transaction specificity.
However, it is considered that the design sharing pattern in the construction industry cannot be explained by these ideas. This is because within a single industry, it is customary to have a significantly different sharing pattern for each component. Further, even in the case of components having small technical differences, the sharing patterns may be significantly different. Even in the case of components that have a large technical difference, they may have the same sharing pattern. There are various mixed cases in terms of cost and transaction frequency. Therefore, there is a high possibility that I need to use a different idea from the ones mentioned above.
The idea in Table 1 has the potential to allow international comparisons for the automotive industry with uniform parameters. In this case, there are two major differences from the construction industry. The first is the designer’s position. The automobile industry usually designs the main parts in-house, but the construction industry may employ an independent architect or an internal designer of the general contractor. This point was analyzed in the previous section. The second difference is the diversity of technical knowledge fields. The automobile industry uses technical knowledge in the areas of mechanical engineering and electronics for automobile manufacturing. To that end, both manufacturers and suppliers work based on technical knowledge in the same area. However, the building industry requires several types of technical knowledge.
Architects have knowledge specifically in the field of architectural planning. The contents include knowledge of site conditions, zoning plans, flow line plans, functional plans for major uses, space composition, space design, and building-related regulations. Structural designers for a building systematically grasp technical knowledge about building structures and knowledge of related laws and regulations. Mechanical and engineering designers of general contractors have basic knowledge of the mechanical and electrical equipment required for construction and knowledge of related laws and regulations. Suppliers’ designers and engineers have knowledge of the components that their company supplies. This knowledge is made up of unique information of each component. For example, knowledge of design of piling is related to the structure of piles, the relationship with geology, the characteristics of pile drivers, information on neighboring properties, related regulations, and various precautions when driving piles on sites. Knowledge of design of an elevator includes drive systems, safety systems, disaster response technology, maintenance knowledge, rope material knowledge, related regulations, and so on. It can be understood, therefore, that the knowledge of the building designer and that of the supplier’s engineer are different. Table 4 summarizes the technical knowledge of typical components.
Due to such a condition, it is possible that the technical engineer who was originally responsible for the technical confirmation was not sufficiently capable. On the contrary, there is a possibility of technological development through effective collaboration between engineers in different technical fields. This paper focuses on such aspects of the construction industry, which are different from the automobile industry, and conducts basic discussions to understand its importance, potential, and danger.
In this paper, I examine the fundamental way of thinking about how designers of architecture and components create design information and share the design process. In particular, I focus on designers’ thinking. This way of thinking can be discussed from the same perspective, even if the object to be created changes. Regarding this design thinking, discussions focusing on the interdependence between components have been conducted mainly in the field of business administration. The target has been in several industrial fields such as the automobile and computer industries. However, for the construction industry, discussions on the interdependence of components have not progressed. Initially, Alexander’s theory was aimed at architecture, but since then, it has made little progress. In other words, this theory has some aspects derived from the idea of architecture. Therefore, there is great potential for the importance and effectiveness of considering architecture based on this theory.
Component Interdependence and Method of Design Sharing
Characteristics of Design Thinking of Component Structure
A modular component and an integral component are often mixed in one product or service. Therefore, there are few purely modular products or services. However, it is possible to recognize the relative degree of modularity when considering specific parts. In this paper, I will examine characteristics related to the design concept of the major components delivered by parts manufacturers and material manufacturers in the construction industry.
Figure 2 is a diagram for consideration based on the structural hierarchy. It shows the relationship between the total structure (St) and the component structures (S1, S2) that are secondarily obtained.
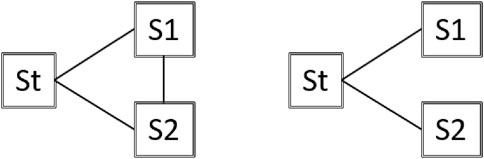
FIGURE 2. Interdependence betweenstructural elements (construction modularity elements in the construction industry).
In the integral type of structure on the left of Figure 2, the overall structure (St) and the structures of all parts (S1, S2) are interdependent. Therefore, when changing the design of the structure (S1) of one component, adjustment with the total structure (St) and adjustment with the structure (S2) of the other component becomes necessary.
• (1–1) Structural interdependence with other parts (S2 → S1)
This is the case where the interdependence of elements occurs in the structure of parts (S1) and the total structure (St). The component designer will design the structure of S1 while adjusting the relationship between the structure of their component (S1) and the total structure (St).
• (1–2) Structural interdependence with total (St → S1)
This is the case where the interdependence of elements occurs between the component structures (S1, S2). The component designer, when designing, needs to adjust the relationship between the component structures (S1) and (S2). Considering the modular type on the right of Figure 1 in the same process, the structures (S1, S2) of all parts are not dependent on each other. In other words, mutual relationships have been resolved or eased. In addition, the structure of parts (S1) does not need to be integrated with the structure of total (St) due to the realization of the interface. Modularisation allows component designers to reduce the need to consider other components in terms of structure and to focus on the idealization and development of their component structure.
Characteristics of Design Thinking in Terms of the Relationship Between Function and Structure
Figure 3 considers the functions to be realized and the structure of the parts to realize them. The functional aspect is expressed by a main function (Ft) and sub-functions (F1, F2). In addition, the structural aspect of the parts is expressed by the total structure (St) and sub-structures (S1, S2). Generally, the architectural concept can be expressed by such a function hierarchy and structure hierarchy.
In the integral type of structure on the left of Figure 3, all relationships are interdependent. Therefore, when considering the design of the structure of one component (S1), the interdependence of the components of various aspects will influence it.
• (2–1) Functional interdependence with other components (S2 → F1 → S1, S2 → F2 → S1)
In this case, the component (S1) may have a functional interdependence with another component (S2). This means that for one function (F1 or F2), not only the structure of the component (S1), but also the structure of another component (S2), will be designed while mutually adjusting.
• (2–2) Mutual dependency between sub-functions (F2 → F1 → S1, F1 → F2 → S1)
This pattern requires that the design of the configuration of one component (S1) establishes a plurality of mutually dependent functions (F1, F2). To create a complex bundle of functions, the structure of the S1 components needs to be considered while making adjustments.
• (2–3) Functional interdependence with Architecture (Ft → F1 → S1, Ft → F2 → S1)
This pattern is a case in which the function of the entire building is realized by a plurality of subsidiary functions. A plurality of secondary functions (F1, F2) is adjusted to each other and the function of the total building (Ft) is established. Based on the mutual adjustments of Ft, F1 and F2, the component designer will design the structure (S1) of his component.
To describe the modular type of structure on the right side of Figure 3 in the same way, the three types of interdependence mentioned above do not apply. In other words, the designer of the component (S1) for a certain function (F1) can proceed with the design without being greatly affected by other influences. That is, there is functional interdependence with other components (S2), interdependence with other functions (F2), and interdependence with total function (Ft).
Further, as modularisation progresses, the degree of freedom in designing inside of the component system increases. Interdependence with other components becomes part of the design condition of the target component. This means that such conditions can be reduced in a component design that has become more modular. Therefore, the component designer can concentrate on the design and development of his or her component without paying too much attention to the conditions of the entire building and the conditions of other components.
Classification of Component Characteristics by Architecture Concept
I explain modularisation by typifying it in the context of this section. First, the four interdependencies are the basic framework. They are functional interdependence with other components, structural interdependence with other components, functional interdependence with the entire building, and structural interdependence with the entire building. Then, the parameters that specifically indicate them are extracted. In addition, parameters are extracted for the characteristics of the component so that it can be examined according to the context here.
A) Functional interdependence with other components.
A) -1 Functional Completeness
Functional completeness is the degree to which a desired function can be achieved with only one component. In other words, it is the degree to which it is functionally independent of other components and is an index of low functional interdependence of a component with another component.
A) -2 Possibility of Identification of Quality Defect
This is the degree to which it is possible to identify whether one component is the cause of overall quality defects. In other words, the quality defect special degree is an index indicating the high degree of functional interdependence between a specific component and another component in the process of examining the overall functional defects.
B) Structural interdependence with other components.
B) -1 Suppressing the complexity of the mounting parts
Suppression of the complexity of the attachment parts is an index relating to the number of elements and the degree of complexity of the interface (attachment part) between the component and the surrounding components. A high degree of this means that the component is structurally in contact with another component in a small number of parts. In other words, this index can be said to be one of the parameters of structural interdependence with other components.
B) -2 Commonality of the Mounting Parts
The degree of commonality of attachment parts is the degree to which attachment parts are structurally made common to all components. In other words, this is an index showing the versatility of the interface. The high degree of this index means that the periphery of the mounting portion can be designed without being affected by other components. In that sense, it shows structurally low interdependence, that is, modularisation.
C) Interdependence With Overall Building
C) -1 Structural Independence From the Main Unit
Low independence means that the design content related to the overall structure and the design content related to the component structure are strongly interdependent. This means that the design contents, such as the mechanism, structure, and design, are related to each other in the building as a whole. Therefore, the designer of the entire building may also design various components.
C) -2 Functional Independence From the Main Unit
If the degree of independence is low, the component does not complete its function. The function of the component system is designed to support a part of the whole function. In the case of a particularly strong relationship, the function of the component may be necessary to create the overall function.
D) Component Characteristics
Each component has its own characteristics. If modularisation progresses, there is a tendency to create a component that you design without considering the overall structure or structure of other components. Therefore, it is more effective to concentrate on the characteristics of the target component. It is possible to use uncertainty and complexity as general parameters (references).
D) -1 Technical Maturity
Uncertainty tends to increase when the maturity of the technology used to design the component is low. It is conceivable that this index may be estimated from changes in patent acquisition. It is the degree to which the speed and size of the technical change of the component is shown.
D) -2 Controlling Component Complexity
The index is the number of elements in the target component and the interdependence between elements within the target component. When a component has a high complexity, many factors are included inside the component, so it is necessary to solve various problems in the component design and development.
As described above, the formulation was mainly based on the concept of Architecture, considering the characteristics of the entire building and components. Then, I proposed an operable index for use in the empirical analysis. Using these indicators, in the next section, the relationship between the characteristics of the components and the selection of the design sharing pattern will be examined based on typical technical departments of general contractors in Japan.
Hypotheses Related to Design Sharing Patterns
The modular design sharing pattern discussed here focuses on the ‘entrust a series of tasks’ pattern. Studies have singled out this pattern as one of the sources of international competitiveness in the Japanese automobile industry (Fijimoto, 2007a). Simply put, this idea involves sharing related work groups along the value chain by the prime contractor who outsources them to parts suppliers. It has been demonstrated that this sharing pattern targets component suppliers with the aim of reducing costs and improving quality by accumulating capabilities that correspond to work groups over the long term (Clark and Fujimoto, 1991). Patterns that simply entrust manufacturing (Patterns 1) and Pattern 2)) and detailed design and manufacturing of parts collectively (Patterns 3)-1 and 3)-2), as well as those that completely depend on the supplier for component development (Pattern 4), Pattern 5)) are all considered design-sharing patterns. These patterns represent the decisions of the main contractor on outsourcing designs. The central focus here is on the component characteristics that influence the decision-making process when selecting these patterns.
While referring to the considerations in Research Settings, I aimed to create a hypothesis that is logically consist in the design sharing pattern. In particular, based on the idea that “sharing between companies regarding design activities and responsibilities is divided at points where design interdependence is low” (Alexander, 1964; Fujimoto, 2006), I propose the following four hypotheses relative to the sharing pattern.
• Hypothesis 1: High component interdependence
First, I consider three indicators: functional interdependence with other components (Si → S1, St → S1), rules for interface with other components (Si → Fj → S1, Fi → Fj → S1), and interdependence with the whole building (Ft → Fj → S1). If these modularisations do not improve, it may be challenging to divide and request the detailed design of the component designer alone. Consequently, the two patterns are likely to match. In the first pattern, pattern 1), the architect performs basic and detailed designs while in the second pattern, pattern 2), the architect performs the basic design and the contractor is in charge of the detailed design.
• Hypothesis 2: Medium-component interdependence
Here, I focus on three indicators: functional interdependence with other parts (Si → S1, St → S1), the rule for interface with other parts (Si → Fj → S1, Fi → Fj → S1), and interdependence with the whole building (Ft → Fj → S1). As these indicators become more modular, substantive detailed designs can be outsourced to component suppliers. However, intermediate cases (pattern 3)-1) exist, where it is difficult to provide the supplier with assurance on the quality of the component design, including cases (pattern 3)-2) where the design quality assurance is easily provided to the supplier.
• Hypothesis 3: Low-component interdependence
Again, I focus on three indicators: functional interdependence with other parts (Si → S1, St → S1), the rule for interface with other parts (Si → Fj → S1, Fi → Fj → S1), and interdependence with the whole building (Ft → Fj → S1). When these indicators exhibit high modularity, they tend to be patterns 4) or 5). Especially in extreme cases, it is very possible that the architect will only suggest the direction of basic design, which is pattern 5).
• Hypothesis 4: Low technical maturity of components
When the component development and design capabilities of the component supplier are high, maturity of component technical development level is low, and component complexity is high, the component design is likely to be outsourced. In other words, the design will be entrusted to a component supplier who has accumulated specialised knowledge. This is a common-sense judgement when deciding between in-house and external productions.
Based on these hypotheses, I verified the representative components. Regarding the design sharing of these components, the concept of verification was based on the basic model of several hundred projects. Therefore, these conditions have been generalised here, hence, I discuss design sharing based on the differences in the characteristics of the components.
Results
Research Settings
The purpose of this research is to describe the most typical and most commonly recognized typologies of components and their design work processes in the Japanese building industry. Therefore, the knowledge of engineers and researchers is summarized. Engineers are experts in a central position in the Japanese construction industry. The researchers are members of the Architectural Institute of Japan’s Committee on Building Management, and university professors who are centripetal in Japanese scholarship in this area. The method was based on the idea of the Delphi method using feedback. The flow of the survey is as follows. First, we interviewed multiple subjects, then made multiple drafts, then asked experts to discuss based on those drafts, and finally summarized them into one draft by the subjects. Get it. And this flow was done almost twice. The details are as follows.
I conducted questionnaire and hearing surveys with the cooperation of three of Japan’s leading general contractors. Sales of each company in 2018 was around one trillion yen. I requested the managers of the technical departments that consist of over 30 staff of each company to supervise the opinions of the departments, then I investigated the characteristics of each component using a questionnaire. Regarding the results, I asked the managers of the three companies to cooperate with us in applying the Delphi method to derive a unified evaluation for each part. Using this method, a comparative evaluation from a uniform perspective will be made on the presumption that the design work carried out in an extremely large number of construction projects was assumed.
Specifically, I asked about the eight indicators in Methodology on a five-point subjective rating (Likert scale). The subjects were asked to award a score of “5” when the degree of modularisation was high and a score of “1” when the degree of modularisation was low. Among the technical departments of leading companies, the answers were collected by one manager, and the results were unified by the managers of three different companies by collating them from three companies. Using this process, it is possible to avoid the unnatural bias of the scores between the components owing to subjective evaluations while sufficiently including specialised knowledge.
The contents of the survey are discussed here. The target components (building parts, building equipment products, building materials, etc.) were examined by the technical department managers of the three different companies mentioned earlier, and they selected the major components of the building project. Then, for office, condominium, and factory construction projects ordered by major general contractors through the end of last year, I requested the extraction of each of the 20 project types, which were considered major, from each building type, after which I confirmed the pattern of design sharing. In this case, the Delphi method was adjustable. Regarding the components provided by each manager, I summarised all the proposals for the three companies, requested that everyone review them again, and finally summarised them into one result. Concerning the division of responsibilities for the design of these components, I arranged them by applying them to the above-mentioned six patterns. The contents are presented in Table 3.
1. Managers supervised the ideas of each company’s technical departments that cooperated in the investigation. First, they argued and drew a unified conclusion on the types of typical component construction that should be the subject of this study. The obtained results are presented in the vertical axis of Table 3.
2. I asked them to evaluate each component on a five-point subjective evaluation (Likert scale) for the eight indicators in Methodology (reprinted on the horizontal axis of Table 3). Specifically, I asked them to gather the opinions of each company’s technical departments, and to provide evaluation values by each technical department.
3. Regarding the evaluation contents of the three companies, in addition to the numerical values presented, I prepared the average and standard deviation of each numerical value and asked the managers representing each company to review them. Then, they exchanged ideas and summarized their views on problems and directions.
4. Based on a unified view, I asked them to recreate the evaluation values by summarizing the opinions of the technical departments of each company.
5. Regarding the evaluation values recreated by each company, in addition to the values presented, I prepared the average and standard deviation of each value and asked the three managers representing each company to see them. By exchanging ideas while summarizing the views of each company, the three managers were able to summarize the figures (Table 3). There was no dissenting opinion from any company regarding this final figure.
In parallel, after 1, after 4, and after 5, four university professors of AIJ’s building management committee members revised the content, and there is no problem as a unified view of the construction industry. I recognized that. In particular, after 5, the researchers had no objection. As a result, a unified answer was derived while suppressing arbitrariness by integrating the highest level knowledge of Japanese architectural fields, both business leaders and research leaders.
Research Result
In this section, to discuss the impact of the design sharing pattern from the perspective of the architectural concept, as described in Component Interdependence and Method of Design Sharing, I analysed the eight evaluation axes based on the target’s degree of modularisation. The content of this result expresses one aspect of the construction field’s characteristics.
Table 4 presents the basic descriptive statistics and correlation coefficients between the variables. Here, the correlation between variables that are actually considered to represent the same concept are verified.
Because modular and integral components are often combined in one product or service, very few purely modular products exist. However, it is possible to recognise the relative degree of modularity when considering specific parts. In this study, I will examine characteristics related to the design concept of the major components delivered by parts and material manufacturers in the construction industry.
The following can be understood from the analysis results. First, there is a positive correlation between “functional perfection of parts” and “particular quality defects of parts”. These form two questions about “functional interdependence with other components”. Similarly, there is a positive correlation between the two questions on ‘structural interdependence with other parts’ and “interdependence with the entire building”. In addition, there is a positive correlation between the six indicators related to function and structure. This means that each index has a positive correlation from the modularisation perspective. However, regarding the component characteristics, the results obtained are different from those of other indexes.
The “technical maturity of parts” exhibits insignificant correlation with all other indexes. This means that the findings of previous research on other industries, which tend to become more modular as technology matures, do not fit perfectly into the building industry (Chesbrough and Kusunoki, 2001). Regarding the “suppression of complexity of parts,” a positive correlation is observed with “structural interdependence with other parts”. This indicates that when the complexity of the components is suppressed, a minimum correlation in the functional relationship between components is observed, and it also suggests a weak relationship with the overall structure. Simultaneously, the correlation between the “technical proficiency of parts,” which is considered to be an index of the characteristics relative to the modularisation of the same component, is small.
Next, these contents were categorised according to the design sharing pattern, then the average and standard deviation of the variables that exhibit the characteristics of the component were calculated (Table 5), after which a basic analysis of variance was performed (Table 6). This was done to examine whether the difference between the modularisation characteristics of components depends on the design sharing patterns 1)–5). From these contents, I will sort out the variables that exhibit the characteristics of the component, especially those that are considered to influence the pattern of design sharing.
First, “functional perfection,” “independence of mounting parts,” “independence from the main body in terms of configuration” and “poor quality” are correlated to the pattern of design sharing (significance level 5%). In particular, “functional perfection,” “independence of attachment parts,” and “independence from the main body in terms of configuration” are demonstrated to be related at a comparatively high level in this analysis of variance. However, for “possibility of identification of quality defect,” the F value is approximate to the value in the F distribution table (significance level 5%).
Moreover, “commonality of mounting parts,” “functional independence from the main unit,” “controlling component complexity,” and “technical maturity” exhibited no relationship with the design sharing pattern (significance level 5%). In one hand, regarding “commonality of mounting parts,” “functional independence from the main unit,” and “controlling component complexity,” it is inferred that the F value is relatively approximate to the value in the F distribution table. On the other hand, regarding technical maturity, the analysis of variance shows that there is no relationship at a relatively high level.
Next, I examine the influence of the degree of modularisation for all patterns of design sharing. In other words, I consider whether the direction of leaving several tasks to the supplier, which is suitable for the modularisation of components, influences the pattern of component design sharing (Table 7 and 8).
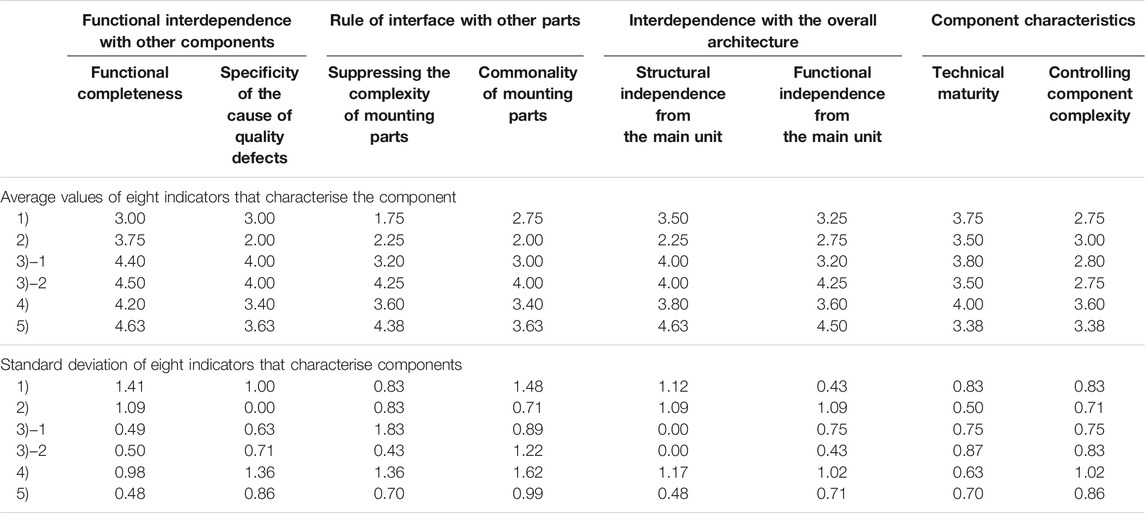
TABLE 7. The average and standard deviation of the variables showing the characteristics of thecomponent.
First, by referring to the average value in the pattern of the design sharing in pattern 1), it can be inferred that the overall modularisation does not improve. In particular, regarding “functional perfection” and “independence of attached parts,” I demonstrate that their modularisations are lower than those of other patterns of sharing. These two indicators have a statistically significant relationship with the design sharing pattern. Therefore, pattern 1) is a design sharing pattern performed for those whose functions and structures are not modularised. This is consistent with the hypothesis. However, the results show that ‘technical maturity’ is not consistent with the hypothesis presented in Consideration of Hypothesis.
Regarding pattern 2), “independence from the main body in terms of composition,” modularization has not improved more than that of other design sharing patterns. Moreover, in pattern 2), the average value of the eight indicators is also the smallest value, and from this point, it is considered to be a typical sharing pattern in which modularisation has not improved. These contents are consistent with the hypothesis in Consideration of Hypothesis. However, even in this case, “technical maturity” is in the direction of modularisation, which is not consistent with the hypothesis.
For pattern 3)-1, the average value of the eight indicators is approximate to the overall average value. Therefore, from the modularisation perspective, it is positioned in the middle of the six design sharing patterns. I consider that a tendency toward modularisation exists in terms of “functional perfection” and “independence from the main body in terms of composition” in which the influence on the design sharing pattern is recognised. In addition, “possibility of identification of quality defect” exhibits high modularity. No clear tendency is observed in the component characteristics. However, a high degree of interdependence between components has been verified in terms of function and structure, and it is considered that it does not contradict the hypothesis of Consideration of Hypothesis.
In pattern 3)-2, the eight indicators exhibit a high average value, and it can be inferred that modularisation keeps improving. In particular, “functional perfection,” “independence of attachment parts,” “possibility of identification of quality defect,” and “standardisation of attachment parts” exhibit high values, thus indicating modularisation. This content is quite inconsistent with the hypothesis in Consideration of Hypothesis. Considering the relatively low influence level of “technical maturity” an inference can be drawn. In the technically novel component field, even if the modularisation of the function and structure of the component does not proceed owing to the importance of technical expertise, suppliers with specialised knowledge are responsible for several tasks.
As for pattern 4), it can be inferred that modularisation keeps improving based on the consideration of the component characteristics, “reduction of complexity of parts” and “technical maturity”. Provided the technology is mature, as the complexity of the component decreases, the designer of the entire building is likely to decide policy alone while the designer employed by the supplier will be in charge of most of the design work. In this case, there is concern that technical knowledge may be biased toward the supplier. However, the average value of the eight indicators of this pattern is lower than the that of pattern 3)-2. It can be observed that modularisation has not improved owing to the interdependence of functional and structural aspects. Although this is consistent with the hypothesis in Consideration of Hypothesis in terms of component characteristics, it is considered that the functional and structural aspects are less consistent.
In pattern 5), the average value of the eight indicators is the highest. In addition, “functional perfection,” “independence of mounting parts,” and “independence from the main body in terms of configuration,” which influence the pattern of design sharing, exhibit the highest values. This design sharing pattern is consistent with the hypothesis in Consideration of Hypothesis. The most modular components are the ones where designers employed by the suppliers do most of the design work.
Consideration of Hypothesis
This section summarizes whether the hypothesis in Chapter 3 was correct.
For Hypothesis 1–Hypothesis 3, the results were almost consistent. In other words, as the functional and physical modularization of components progresses, it will affect the division of the design process. This was investigated using four indicators, and all the indicators showed almost consistent results.
Hypothesis 4 could not be considered correct. The correlation between the modularisation of components and design process sharing was determined to be insignificant. This hypothesis is based on the theory of dynamics in Architecture, as described above. As the technology matures, the understanding of where to break it up and how to organise the interface, both physically and functionally, is enhanced, thus resulting in more modularization. The hypothesis here was that such a modularisation is likely to provide an understanding for the rational separation of design sharing. However, the relationship determined between the two indicators was insignificant. This may be owing to other factors. For example, even if the technology matures, highly specialised knowledge is still required, and it is possible that the division of the design process is unlikely to change. In addition, there may be cases in which multiple related industrial areas are considered, commercial and information flows are complicated, and the design process does not change. Other cases that can be considered are the characteristics of the supply chain and the peculiarities of industry practices. In any case, the results of the survey showed that there was almost no simple relationship between the maturity of the technology and the sharing pattern of the design process.
Discussion
Figure 4 depicts a summary of the survey. In the Japanese construction industry, if a component is modular, it is generally modular in the design process. It has been pointed out in previous studies targeting other industries (Fujimoto) that this is not always the case. This is because even if a component is modular, it is significantly influenced by the internal and external environments, including technical characteristics and industry practices. However, this study on the Japanese construction industry offers the potential to review existing industry practices and international supply chains strategically.
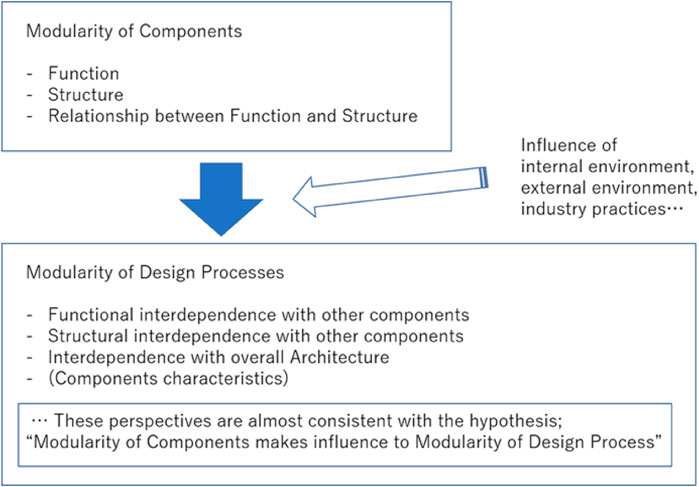
FIGURE 4. Modularity of components influences modularity of design process. The following is a summary of hypotheses that are at least partially consistent with the architectural concepts for each design sharing pattern.
The first is functional interdependence with other components. Functional completeness’ is considered to affect all design sharing patterns. The content of this analysis is highly consistent with the hypothesis presented in Consideration of Hypothesis, and the direction of requesting tasks in many process ranges is compatible with the fact that modularisation is in progress. In particular, components that have a low degree of functional completeness and fine adjustments with surrounding functions, such as patterns 1) and 2), are considered to have a high degree of functional interdependence. Apparently, there is hardly any tendency to abandon tasks in many process ranges. This point is consistent with analysis results.
When the cause of quality defects exhibits a high degree of specificity, the analysis results may possibly affect the selection of patterns 3)-1 and 3)-2. In these design sharing patterns, although the architect leads the basic design, the supplier is in charge of creating the design information that corresponds with the actual design. Therefore, at the time of the detailed design, a collaborative process, such as the information exchange between the architect and supplier, is required. This is consistent with the fact that both designers clarify the responsibility for quality in the actual work process during the discussions on the contents of the detailed design. In this regard, to make use of the contents and intentions of the basic design in the detailed design, it is highly plausible that the design information is examined more thoroughly than other patterns. This is believed to be correlated with pointing out the strong aspects of Japanese companies in the automobile industry, as well as other industries (Fujimoto, 2019).
However, the degree of modularity of “possibility of identification of quality defect” of patterns 4) and 5), which is considered to be relatively inadequate, is functionally fine-tuned between the components around it. This point does not agree with the hypothesis. Because the designer of the entire building is not substantially involved in the detailed design, the intention of the basic design may not be reflected in the detailed design. In other words, challenges, such as dealing with phenomena that are difficult to anticipate owing to relationships with the surrounding components, may occur.
Next, I focus on structural interdependence. Although the improvement in the “standardisation of mounting parts” indicates structural modularisation, this analysis shows that pattern 3)-2 is affected. In this pattern, the direction and detailed design are shared between designers for detailed design, and the supplier is responsible for providing design quality assurance. Having the supplier take responsibility for design quality means that the supplier is responsible for more tasks. Therefore, provided each component is standardised and can be designed without considering the relationship with other components, it is possible to focus more on the internal design of the component. However, the possible unexpected occurrence of a situation, when other components are affected, poses a risk. This is compatible with the modularisation in many industries. As components become modular, price competition tends to become more important than quality competition (Clark and Fujimoto, 1991). This is consistent with cases in Japan, such as shutters and aluminium fittings.
Regarding “suppressing the complexity of mounting parts” and “structural independence from the main unit,” there is a correlation between the design sharing pattern and modularisation of components. Almost all design sharing pattern results agree with the hypothesis. As components become more modular, there is a tendency to leave more tasks to suppliers.
Finally, I consider the characteristics of the components. “Technical maturity” exhibits minimum correlation with the design sharing pattern and is not consistent with the hypothesis. This may indicate that the main technologies of the construction industry are being utilised at a stable level of technology without major improvements within a certain period of time. Previous research on other industries, such as the computer parts industry, has exhibited empirically called architectural dynamics, a modular and integral round trip as technology matures (Chesbrough and Kusunoki, 2001). However, even if “technical maturity” is high in the construction industry, modularisation tends to be limited, which is an interesting aspect. In particular, it is considered that the basis of this tendency is on the fixed characteristics of the practices owing to the complicated correlation of many elements of the construction industry, and the characteristics of the integralisation found in other industries, such as the Japanese automobile industry (Fujimoto, 2007b).
Some components that have become more modular tend to have challenges, such as an uneven distribution of technical knowledge. This means that the building industry in Japan does not respond appropriately to enhancements in modularisation. In addition, regarding components that have not been modularised, challenges and limitations tend not to be recognised regarding the uneven distribution of technical knowledge and the suppliers’ scope of responsibility. In this case, although there is a tendency for costs to increase, overall performance can be improved by integrating many elements (Bennett, 1991). It can be concluded that this fact is compatible with the characteristics and tendencies of other industries in Japan (Takeishi, 2002; Shintaku, 2008; Fukuzawa and Inamizu, 2017), and could be demonstrated to be one of the factors that contribute to the discussion on the comparison of industrial characteristics.
From this analysis, a correlation was determined between the component characteristics and division of design processes in the Japanese construction industry. This is consistent with the indications to other industries, such as the Japanese automobile industry. Additionally, this correlation may indicate the strength of the Japanese construction industry.
Based on this discussion, three directions can be considered in the future. One of such possible directions is confirming the indications made to other industries in Japan. The remaining points are “long-term continuous relationships with parts companies” and “fierce capacity building competition among minority parts companies”. By confirming these facts, I will increase the range in which some of the characteristics of the Japanese construction industry can be objectively understood. The second direction is the possibility of comparing between regions. In this discussion, I have considered a point in the Japanese construction industry when components are modularized, in which there is a tendency to request for design and production from parts manufacturers. By investigating and comparing whether the division of design is more advanced in other regions, it will be possible to understand some of the characteristics of the region. The third direction involves the prospects for alterations in the business system over time. At this stage, I understand the content of this study. However, by investigating changes over time, I expect that the characteristics of changes in the design and production systems can be understood.
As discussed so far, many industrial and technical fields are participating in the construction project. It was suggested that it is wrong to make all construction processes modular by over-concentrating on the increasing modularization of specific products. It was understood that it may be necessary to consider the characteristics of the components, as well as the decision to proceed with modularization. In contrast, I understand why it is problematic to be biased toward the integral type of thinking. However, it has been pointed out that the creators are fundamentally biased in their design ideas (Fujimoto). It has also been pointed out that many Japanese companies are biased toward the integral type. Starting from the content of this paper, I established the possibility of comparing the building industries in different regions. In other words, it is important to carefully understand the bias of design ideas in each region, and the scope of modularization that is being promoted in the building industry. I believe that these understandings have provided us with the potential to propose a prescription for the future direction of the building industry in each region.
The paper discusses the specific design and production information elements. However, in the construction industry, it is also important to discuss the factors at the stage which influences how space is utilized in society. As shown in Figure 5, when an architectural product is created, three types of information are generated (Fujimoto). Information1 is mainly created by the designer, Information2 is created by the manufacturer, and Information3 is created by the user. In this paper, from the viewpoint of inter-industry comparison, information 1-2 is targeted first, and the possibility of inter-industry comparison with previous research on other industries is also examined.
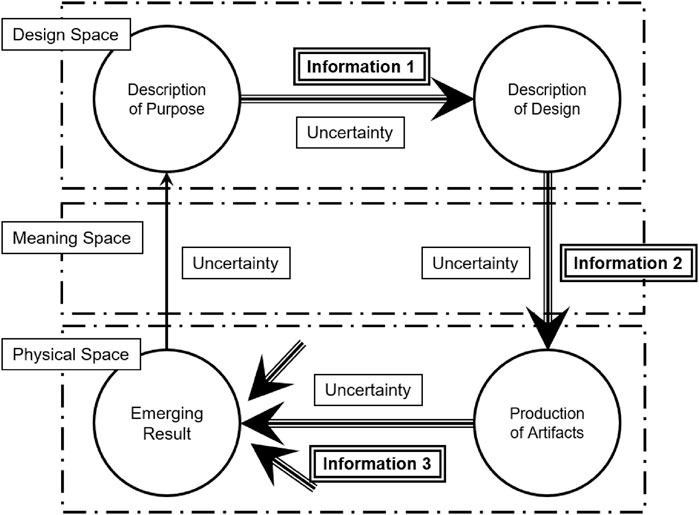
FIGURE 5. Fundamental process to create artifacts (redraw with reference to Clark and Fujimoto, 1991).
In recent years, digitized technology has developed rapidly, and BIM/CIM, ICT, i-Construction, etc., have started being used in the construction industry. Since they are based on digitization technology, the most basic feature is that there are breaks between the elements. Therefore, they are characteristically easily adapted to modularization. However, these technologies are currently being used in the construction industry, primarily through the replacement of existing technologies. In short, the focus is on doing the same thing, and making it easier to reduce human error and keep records. In Figure 6, these are mainly the fundamental value technologies of Information1-2. In other words, the fundamental value of Information1-2 can be controlled by the maturity of technology, considering the dynamic theory of architecture, and it is natural that modularization is progressing (Kusunoki chess blow). However, with regard to the other four items, there is almost no direct influence from these new production technologies such as BIM/CIM, so it is necessary to discuss the advantages of the transition to modularization again. This paper focuses on those who have technical knowledge to create information like these ones. The reason for this is that it is important to focus on the point who can create information and who cannot create that. The paper provides a comprehensive view of the construction industry. At the same time, it is possible to compare industries and regions in the construction industry.
Conclusion
The purpose of this study is to develop a new industrial theory of the construction industry, and to create a prescription to demonstrate some of the future directions of the industry.
As a crucial tool, I adopted the Architecture concept, which has provided a precise analysis of multiple Japanese industries, as I focused on the Japanese construction industry. In other Japanese industries, it has been mentioned that product manufacturers are effective because they allow component manufacturers handle the component development process. I investigated and analysed whether the Japanese construction industry exhibits this strength with this tool. Specifically, I investigated and analysed whether the modularised components created design information via the modularised design process. Although the results could not be confirmed with some indicators, it was generally confirmed that the design information was created by the modularized design process for the modularized components.
Regarding the modular systems, which are becoming more modular, they did not significantly contradict the basic statement of the hypothesis, which suggests the design work should be entrusted to the task of design sharing. However, problems were identified owing to responses to defective quality and uneven distribution of technical knowledge. Concerning components that have not been modularised, because the architect is responsible for most of the design work, there are no challenges in the building production where customisation is the basis. In addition, for parts and products that have a relatively moderate degree of modularity, architects and part designers can maintain stable performance by sharing design information and promoting the coordination of industry areas. This is consistent with the analyses of other industries and is considered to represent the characteristics of the Japanese production technology.
I believe that the development of this analysis method for architecture has made it possible to demonstrate the characteristics of industrial structure, consider the uneven distribution of technical knowledge, and recognise compatibility between product characteristics and production organisation from one perspective. In addition, I believe that this expands the possibilities of regional comparisons of the building industry, as well as inter-industry comparisons of the building industry and other industries, including temporal comparisons of changes over time.
With the method demonstrated here, it is possible to recognise how the industrial structure changes owing to changes in the external environment, which is a major factor while fixing product characteristics. This is important for a better understanding of the sharing of design work in the industrial sector of Japanese construction projects.
Owing to the multi-layered global network, faster computer and wider communication technologies, the possibility of altering industrial characteristics is increasing. Hence the necessity of a future vision based on an understanding of industrial characteristics. Even in the building industry, and in addition to these fundamental changes, rapid changes are feasible owing to the development of technologies such as IT, BIM, and AI. In particular, I must understand how the industry has been impacted by a pandemic by objectively comparing the effects before and after it. Many people have already recognaized the physical distance is being replaced by remote work and video conferencing. Therefore, this phenomenon is consensually considered to be effective for collaborative design process across regions, which has never been implemented in the construction industry.
However, this study has two limitations. The first is the limitation of the analysis perspective. Here, I adopted the concept of Architecture as an analytical perspective. This concept attempts to interpret the design concept when the creator designs an object via component interdependence, and it provides the possibility of clarifying the fundamental part of the creator’s way of thinking. However, when discussing the industrial theory of one industry, there is the limitation of discussing one perspective alone. Here, there are many factors such as social structure, culture, law, system, technical field, knowledge field, trading customs, commercial distribution, logistics, and information flow, and it is necessary to discuss them. Furthermore, I conducted research and analysis in specific areas, and this is the second limitation of this research. In this study, Japan, which is the target area of a number of sophisticated previous studies in other industries was considered as a region where discussions on regional characteristics are considered to have matured. However, I do not understand how the characteristics of the Japanese region affect the characteristics of the construction industry. Therefore, it will be necessary to conduct the same survey in several regions in the future.
The significance of this research can be summarised as follows: owing to the rapid development of fundamental technology and changes in the external environment, such as pandemics, it is necessary to have a clear idea of the future direction of the construction industry based on industrial analysis. This study was able to elucidate some of the characteristics of the Japanese construction industry. This study also provides a method for understanding industrial characteristics. Therefore, I believe that I were able to present the possibility of inter-industry and inter-regional comparisons from this perspective. This is considered to have demonstrated the content that could present a prescription for discussion in the industry, especially in the face of various challenges in the future.
Data Availability Statement
The raw data supporting the conclusions of this article will be made available by the authors, without undue reservation.
Ethics Statement
Ethical review and approval was not required for the study on human participants in accordance with the local legislation and institutional requirements.
Author Contributions
The author confirms being the sole contributor of this work and has approved it for publication.
Conflict of Interest
The author declares that the research was conducted in the absence of any commercial or financial relationships that could be construed as a potential conflict of interest.
Publisher’s Note
All claims expressed in this article are solely those of the authors and do not necessarily represent those of their affiliated organizations, or those of the publisher, the editors and the reviewers. Any product that may be evaluated in this article, or claim that may be made by its manufacturer, is not guaranteed or endorsed by the publisher.
Acknowledgments
I express my sincere thanks to Prof. Takahiro Fujimoto, Prof. Tomonari Yashiro (at the University of Tokyo), Dr. Yongjiang Shi and Rob Phaal (at the University of Cambridge) for helpful discussions and comments on the manuscript. I thank the Editor and Reviewers for their thoughtful suggestions during the review process.
References
Asanuma, B., and Kikutani, T. (1992). Risk Absorption in Japanese Subcontracting: A Microeconometric Study of the Automobile Industry. J. Japanese Int. Econ. 6 (1), 1–29.
Allman, A., and Zhang, Q. (2020). Dynamic Location of Modular Manufacturing Facilities with Relocation of Individual Modules. Eur. J. Oper. Res. 286 (2), 494–507. doi:10.1016/j.ejor.2020.03.045
Baldwin, C., and Clark, K. (2000). Design Rules, Vol. 1: The Power of Modularity. Boston: The MIT Press.
Bennett, J. (1991). International Construction Project Management, General Theory and Practice. London, U.K: Butterworth and Co. Ltd.
Blees, C., Kipp, T., Beckmann, G., and Krause, D. (2010). Development of Modular Product Families: Integration of Design for Variety and Modularization, 25. Göteborg, Sweden: International NordDesign Conference–27. 08.2010.
Bodenstein, M., Corsetti, G., and Guerrieri, L. (2020). Social Distancing and Supply Disruptions in a Pandemic. Washington: Board of Governors of the Federal Reserve System. doi:10.17016/FEDS.2020.031
Bresman, H. (2013). Changing Routines: A Process Model of Vicarious Group Learning in Pharmaceutical R&D. Amj. 56, 35–61. doi:10.5465/amj.2010.0725
Brusoni, S., and Prencipe, A. (2011). Patterns of Modularization: the Dynamics of Product Architecture in Complex Systems. Eur. Manage. Rev. 8, 67–80. doi:10.1111/j.1740-4762.2011.01010.x
Brussevich, M., Dabla-Norris, E., and Khalid, S. (2020). Who Will Bear the Brunt of Lockdown Policies? Evidence from Tele-Workability Measures Across Countries. No: IMF Working Paper, 20–88. doi:10.5089/9781513546285.001
Cabigiosu, A., Campagnolo, D., Furlan, A., and Costa, G. (2015). Modularity in KIBS: The Case of Third-Party Logistics Service Providers. Industry and Innovation. 22, 126–146. doi:10.1080/13662716.2015.1023012
Cabigiosu, A., and Camuffo, A. (2012). Beyond the "Mirroring" Hypothesis: Product Modularity and Interorganizational Relations in the Air Conditioning Industry. Organ. Sci. 23, 686–703. doi:10.1287/orsc.1110.0655
Chesbrough, H., and Kusunoki, K. (2001). “The Modularity Trap: Innovation, Technology Phase Shiftsand the Resulting Limits of Virtual Organizations,” in Managing Industrial Knowledge. Editors I. Nonaka, and D. Teece (London: Sage).
Clark, K. B., and Fujimoto, T. (1991). Product Development Performance. Boston, MA: Harvard Business School Press.
Cummings, J. N. (2004). Work Groups, Structural Diversity, and Knowledge Sharing in a Global Organization. Management Sci. 50 (3), 352–364. doi:10.1287/mnsc.1030.0134
Davenport, T. H., and Prusak, L. (2000). Working Knowledge: How Organizations Manage What They Know. Boston, MA: Harvard Business School Press.
Dewit, I., Jacoby, A., and Matthyssens, P. (2021). Design Preconditions for Product-Service Integration. Designs. 5 (2), 29. doi:10.3390/designs5020029
Fujimoto, T. (2006). Architecture-based Comparative Advantage in Japan and Asia. Tokyo: Tokyo Univ., MMRC Discussion Study, No.94. Available at: http://merc.e.u-tokyo.ac.jp/mmrc/dp/index.html (Accessed December 11, 2020).
Fujimoto, T. (2007a). Architecture-Based Comparative Advantage - A Design Information View of Manufacturing. Evolut Inst. Econ. Rev. 4 (1), 55–112. doi:10.14441/eier.4.55
Fujimoto, T. (2007b). Competing to Be Really, Really, Good: The Behind-The-Scenes Drama of Capability-Building Competition in the Automobile Industry. Tokyo: I-House Press.
Fujimoto, T. (2012). An Economic Analysis of Architecture and Coordination: Applying Ricardian Comparative Advantage to Design Costs and Locations. Evolut Inst. Econ. Rev. 9 (1), 51–124. doi:10.14441/eier.a2012004
Fujimoto, T. (2014). The Long Tail of the Auto Industry Life Cycle. J. Prod. Innov. Manag. 31 (1), 8–16. doi:10.1111/jpim.12076
Fujimoto, T. (2019). Conclusion and Practical Implications. Tokyo: Tokyo Univ.. MMRC Discussion Study, No.515. Available at: http://merc.e.u-tokyo.ac.jp/mmrc/dp/index.html (Accessed December 11, 2020).
Fukuzawa, M., and Inamizu, N. (2017). Multi-functional Factories. Abas. 16, 229–241. doi:10.7880/abas.0170421a
Guinot, J., Chiva, R., and Mallén, F. (2016). Linking Altruism and Organizational Learning Capability: A Study from Excellent Human Resources Management Organizations in Spain. J. Bus Ethics. 138 (2), 349–364. doi:10.1007/s10551-015-2603-7
Hansen, C. L., and Mortensen, N. H. (2014). Proactive Identification of Scalable Program Architecture: How to Achieve a Quantum-Leap in Time-To-Market. Int. J. Ind. Eng. 21 (2), 74–85.
Ikuine, F. (2012). The Evolution of the Home Video Game Software Industry in Japan: An Empirical Study on Factors in the Industry's Evolution. Evolut Inst. Econ. Rev. 91, 37–50. doi:10.14441/eier.a2012003
JFCC (Japan Federation of Construction Contractors) (2020). Kensetsugyou Handbook 2020. Japanese. Available at: https://www.nikkenren.com/publication/handbook.html (accessed April 20, 2021).
Kikuchi, S., Kitao, S., and Mikoshiba, M. (2020). “Heterogeneous Vulnerability to the COVID-19 Crisis and Implications for Inequality in Japan.” RIETI Discussion Paper, 20. E-039.
Kobayashi, M., Tomino, Y., Shintaku, J., and Park, Y. (2014). Demand Fluctuation and Supply Chain Integration: Case Studies of Japanese Firms. Tokyo: Tokyo Univ.. MMRC Discussion Study, No.456. Available at: http://merc.e.u-tokyo.ac.jp/mmrc/dp/index.html (Accessed December 11, 2020).
Lee, S., Gon Kim, B., and Kim, H. (2012). An Integrated View of Knowledge Management for Performance. J. Knowledge Management. 16 (2), 183–203. doi:10.1108/13673271211218807
Liu, Y., Liang, X., and Shi, Y. (2018). Brokerage and Balance: Creating an Effective Organizational Interface for Product Modularization in Multinational R&D. Res. Pol. 47, 6 pp1133–1146. doi:10.1016/j.respol.2018.03.019
Loon Hoe, S., and McShane, S. (2010). Structural and Informal Knowledge Acquisition and Dissemination in Organizational Learning. Learn. Organ. 17 (4), 364–386. doi:10.1108/09696471011043117
MacCormack, A., Baldwin, C., and Rusnak, J. (2012). Exploring the Duality between Product and Organizational Architectures: A Test of the "mirroring" Hypothesis. Res. Pol. 41, 1309–1324. doi:10.1016/j.respol.2012.04.011
Manning, S., and Reinecke, J. (2016). A Modular Governance Architecture In-The-Making: How Transnational Standard-Setters Govern Sustainability Transitions. Res. Pol. 45 (Issue 3), pp618–633. doi:10.1016/j.respol.2015.11.007
Mortensen, N. H., Hansen, C. L., Hvam, L., and Andreasen, M. M. (2011). “Proactive Modeling of Market, Product and Production Architectures”, International Conference on Engineering Design. Copenhagen, Denmark: The Design Society.
Mortensen, N. H., Hansen, C. L., Løkkegaard, M., and Hvam, L. (2016). Assessing the Cost Saving Potential of Shared Product Architectures. Concurrent Eng. 24 (2), 153–163. doi:10.1177/1063293x15624133
Na, H. K., and Park, Y. W. (2016). Architecture of Interfirm Collaboration and Global: Competitive Advantage Findings from the Mobile Handset Industry. Tokyo: Tokyo Univ. MMRC Discussion Study, No.492. Available at: http://merc.e.u-tokyo.ac.jp/mmrc/dp/index.html (Accessed December 11, 2020).
Nishiguchi, T., and Alexandre, B. (1997). Self-Systemization in Chaos: The Toyota Group and the Aisin Precision Machinery Working paper/Hitotsubashi University. Tokyo: Institute of Innovation Research.
Otto, K., Hölttä-Otto, K., Simpson, T. W., Krause, D., Ripperda, S., and Moon, S. K. (2016). Global Views on Modular Design Research: Linking Alternative Methods to Support Modular Product Family Concept Development. J. Mech. Des. 138 (7), 071101. doi:10.1115/1.4033654
Park, S., and Kim, E.-J. (2015). Revisiting Knowledge Sharing from the Organizational Change Perspective. Eur. J. Train. Development. 39 (9), 769–797. doi:10.1108/ejtd-06-2015-0042
Shintaku, J. (2008). Strategic Technology Management by Korean LCD Manufacturers. Akamon Management Rev. 7 (1), 55–73. doi:10.14955/amr.070103
Sita Nirmala, K., and Chitale, C. M. (2012). Collaborative Knowledge Sharing Strategy to Enhance Organizational Learning. J. Mgmt Development. 31 (3), 308–322. doi:10.1108/02621711211208934
Sousa, M. J., Cascais, T., and Rodrigues, J. P. (2015). “Action Research Study on Individual Knowledge Use in Organizational Innovation Processes,” in New Contributions in Information Systems and Technologies. Editors A. Rocha, A. M. Correia, S. Costanzo, and L. P. Reis (Berlin: Spring Nature), 75–82. doi:10.1007/978-3-319-16528-8_8
Swart, J., and Kinnie, N. (2010). Organisational Learning, Knowledge Assets and HR Practices in Professional Service Firms. Hum. Resource Management J. 20 (1), 64–79. doi:10.1111/j.1748-8583.2009.00115.x
Swift, P. E., and Hwang, A. (2013). The Impact of Affective and Cognitive Trust on Knowledge Sharing and Organizational Learning. Learn. Organ. 20 (1), 20–37. doi:10.1108/09696471311288500
Takeishi, A. (2002). Knowledge Partitioning in the Inter-Firm Division of Labor: The Case of Automotive Product Development. Organ. Sci. 13 (3), 321–338. doi:10.1287/orsc.13.3.321.2779
Tee, R., Davies, A., and Whyte, J. (2019). Modular Designs and Integrating Practices: Managing Collaboration through Coordination and Cooperation. Res. Pol. 48, 51–61. doi:10.1016/j.respol.2018.07.017
Tomita, J. (2009). A Comparative Analysis Between LCD Panel and Flat Glass in the TFT-LCD Industry From Process Architecture-Based View. Tokyo: Tokyo Univ.. MMRC Discussion Study, No.252. Available at: http://merc.e.u-tokyo.ac.jp/mmrc/dp/index.html (Accessed December 11, 2020).
Ulrich, K. (1995). The Role of Product Architecture in the Manufacturing Firm. Res. Pol. 24, 419–440. doi:10.1016/0048-7333(94)00775-3
Williamson, O. E. (2009). Pragmatic Methodology: A Sketch, With Applications to Transaction Cost Economics. J. Econ. Method. 16 (2). doi:10.1080/13501780902940729
Keywords: technological knowledge, design process, knowledge mobility, design information, architecture concept
Citation: Yoshida S (2022) Characteristics of Project Organisations of the Japanese Construction Industry Focusing on the Modularity of Components. Front. Built Environ. 7:591035. doi: 10.3389/fbuil.2021.591035
Received: 03 August 2020; Accepted: 31 December 2021;
Published: 08 March 2022.
Edited by:
Zhen Chen, University of Strathclyde, United KingdomReviewed by:
Serdar Durdyev, Ara Institute of Canterbury, New ZealandKoki Arai, Kyoritsu Women’s University, Japan
Copyright © 2022 Yoshida. This is an open-access article distributed under the terms of the Creative Commons Attribution License (CC BY). The use, distribution or reproduction in other forums is permitted, provided the original author(s) and the copyright owner(s) are credited and that the original publication in this journal is cited, in accordance with accepted academic practice. No use, distribution or reproduction is permitted which does not comply with these terms.
*Correspondence: Satoshi Yoshida, eW9zaGlkYS1zYXRvc2hpQGFpaXQuYWMuanA=