- 1School of Engineering, University of Birmingham, Birmingham, United Kingdom
- 2Institution of Transportation Study, University of California, Berkeley, Berkeley, CA, United States
It is undeniably true that transportation systems positively impact human life but, the use of transportation systems also emits greenhouse gasses in the environment which leads to global warming. In this day and age, various technologies are being combined with transportation systems, aimed at reducing the global impact of greenhouse gas emissions. The high-speed rail (HSR), which is well-known for low CO2 emissions, has continually been improved, especially its model.
In this study, the material replacement method is taken to account for a feasibility study on the next model of the HSR. There are three types of composite materials that consist of glass filled with epoxy, glass filled with polyester and glass filled with nylon, replacing the six chief parts of HSR components.
As a result, the total weight of rolling stock has significantly reduced to 24.61% on average so, it can decrease the amount of fuel in the HSR operation. Also, the feasibility of the recyclability (%Rcyc) and recovery rate (%Rcov) is critical in judging the suitability of the replacement. The research found that the replacement of CFRP (Carbon fiber reinforced polymer) generates a positive result on %Rcyc value at 73.9% compared with 61.4% in the original model. Besides, the %Rcov at 78.9% is higher than the 73.1% of the original model.
Highlights
- This study clearly explains the calculation methods of %Rcyc and %Rcov of the end-of-life rolling stock of the HSR that is suitable for all industries to adopt in their recycling processes.
- The research is the world's first to provide composite material replacement methods of the HSR rolling stocks. And, the result shows that the total weight of HSR can be reduced up to 24% by a substitute CFRP in the six chief parts of the HSR's components.
- There are three types of composite materials, including glass filled with epoxy, polyester and nylon, which were all compared with the original model. The results indicated that the replacement by composite material can increase values of %Rcyc to 11.7% and %Rcov to 5% compared with the original model.
- The parametric study was also applied to predict the recycling rate of aluminium with steel and pure steel, with regards to the improvement of manufacturing technologies. The change is predicted to decrease the amount of waste in landfills by up to 85% by 2039.
Introduction
With regards to the dramatic growth in railway industries around the world, rails have become one of the most crucial public transportation modes, directly creating a positive impact on human life. However, growth and demand are causing large scale issues in terms of its global impact. Many researchers have revealed that the increase of the world's temperature to 36.5°F is an effect of transportation emissions, which includes high-speed rails around the world (Damm et al., 2016; Yeh et al., 2017).
The report from the UIC showed that transportation sector CO2 emissions, accounted for 24.7% of global emanation in 2015. In comparisons of CO2 emissions from transportation sectors, nearly three quarters came from the road (motor vehicles etc.); while 4.2% of the global transportation emissions was a result of rail sectors around the world (Yeh et al., 2017). Therefore, attempts to get passengers to change their mode of transport from cars to trains, has boosted the gradual growth of rail networks in many areas i.e., China, France, and the USA.
The issue of most concern is the methodology needed to reduce the amount of CO2 released into the atmosphere from the transportation sector which directly relates to air quality, and which is a significant cause of severe diseases.
Heavy duty vehicles confirmedly have a greater effect on air quality compared to rail and passenger vehicles (Kinnon et al., 2019). The high rates of CO2 emissions impact the ozone and PM2.5, which is a particle matter air pollution less than 2.5 in diameter, especially in big cities. Health effects from PM2.5 have manifested with numerous symptoms i.e., airway damage (Deng et al., 2013; Longhin et al., 2013; Wang et al., 2013), cardiovascular impairment (Kamal et al., 2011; Torres-Ramos et al., 2011; Davel et al., 2012) and diabetes mellitus (Mendez et al., 2013; Xu et al., 2013; Liu et al., 2014). Therefore, the train as a means of transport has become a critical driver in promoting a cleaner environment.
Moreover, improvements in the railway industry can be found in various aspects, aiming to provide a positive impact and improvements in global railway operation efficiency; for example, many researchers have focused on combustion systems changing from diesel to electric operated trains (Oanh et al., 2010; Mwambeleko and Kulworawanichpong, 2017; Khan and Gillies, 2019). Chan's and research 2019 mentioned that the substitution of electric systems on rail networks could reduce GHG emissions (including CO2) up to 27,000 tons per year or a decrease of 98% from the current operation on the rail network (Chan et al., 2013).
Some have pointed to the management of end-of-life rolling stock (Smink, 2007; Merkisz et al., 2014; Kaewunruen et al., 2019). Regarding Kaewunruen's and (2019) findings, the end-of-life rolling stock of HSR contains 37 components and, the study described that recyclability rates (%Rcyc) and recoverability rates (%Rcov) were 61.4 and 73.9%, respectively (Kaewunruen et al., 2019). The main reason for this was that the rolling stock model was composed of steel and mixed aluminium and steel. Consequently, waste management methods through end-of-life rolling stock, can reduce left over landfill waste which in turn leads to a decrease in CO2 emissions.
Lightweight materials have also been applied across transportation industries. In the USA, nearly one-third of pollution was emitted from transportation. Many researchers revealed that the reduction on the total weight (i.e., car body) could decrease fuel consumption; in other words, the amount of CO2 emissions would be degraded (Office of Energy Efficiency Renewable Energy, 2016). Nowadays, car industries have entirely adopted lightweight material replacement techniques in their model.
In this study, the material replacement technique is applied to the HSR model. The “original model” of the end-of-life HSR from Kaewunruen's and research (2019) will be compared with the “new model,” which includes substitution with lightweight material on the HSR's body and other parts. The study aims to improve the performance of both Rcyc and Rcov rates which leads to a reduction in CO2 emissions which greatly impacts human health.
Methodology
Aiming to reduce rolling stock body mass, the feasibility of substitution of materials used in the original model, with lightweight materials, must be considered as follows. First, the selection of materials for replacement in the original model, which mostly consists of aluminium and steel; determining which rolling stock parts need to be replaced with light-weight material should be thoroughly considered. Second, the calculation of component mass, after replacing the old materials, is addressed by analyzing the change in total mass of the rolling stock. Lastly, the impact of end-of-life rolling stock must be considered; since the change in body weight leads to leftover landfill waste CO2 emissions.
Material Replacement Technique
Based on Kaewunruen's and (2019) research, there are some parts of HSR rolling stock that can be replaced by lightweight materials, i.e., composite material, Advanced High Strength Steel (AHSS) and Magnesium. An obvious benefit of the lightweight material in the vehicle's body was revealed by the US government showing that a “10% reduction in vehicle weight can lead to an 8% improvement in fuel economy” (Kaewunruen et al., 2019). This refers to the decrease in fuel demand for powering vehicle, which in turn degrades CO2 emissions. Nonetheless, the main body and other parts of the HSR's rolling stock are made from aluminium and steel so, the substitution of those parts must be of a lighter weight than aluminium.
Nowadays, composite materials are applied to some car body components in order to reduce total rolling stock weight and GHG emissions (Rezaei et al., 2009; UK Department of Transport, 2014; Kaewunruen et al., 2019). The material contains remarkable properties, i.e., high stiffness, high strength, low density, and is suitable for reforming in to multi-shaped components (Kaewunruen et al., 2019).
Composite materials are made from more than one component and, a well-known composite material is reinforced plastic (Wambua et al., 2003; The Engineering Toolbox, 2008; Dutta and Barman, 2019) which is currently being used in various industries. Reinforced plastic was applied to some parts of the HSR and passenger trains, mostly in the car body.
In this study, three types of composite materials were chosen to replace some parts of the HSR, including glass-filled epoxy (35%), glass-filled polyester (35%), and glass-filled nylon (35%). Moreover, reinforced plastic contains higher values of energy recovery rates compared to other materials, thus making it a suitable replacement material for the rolling stock model (Hofstatter et al., 2007; Hassan et al., 2012; International Environmental Product Declaration System, 2013; Delogu et al., 2017; Masterbond, 2019).
The main reason of selecting the three above-mentioned composite materials is the current market availability, especially for glass-filled epoxy (Ritts et al., 2011; Khan et al., 2017). Moreover, many industries have made attempts to lower the cost of composite materials. This study therefore provides case studies on replacement composite materials in HSR rolling stock.
Calculation of Components' Mass
The primary purpose of replacing the material is to reduce the total mass of the train which in turn leads to a decrease in CO2 emissions. The “original model” has a total weight of 265,000 kg, as this model contains steel and aluminium in more than 50% of all components. However, the replacement of composite material effects the body weight. Thus, the weight of the “improved model” of the HSR rolling stock, can be calculated using Equation (1).
where; m = mass (kg); V = Volume (m3); ρ = Density (kg/m3)
The perspective on replacing composite materials focuses on some rolling stock parts based on the feasibility study. There are six main parts including the roof, door, car body/tumblehome, brake control unit, break rheostat/dynamic brake and bogie transom. Composite material replacement is divided into three cases studies, as shown in Table 1. As a result, the total weight of the HSR rolling stock is changed, reducing CO2 emissions due to higher Rcyc and Rcov rates compared to aluminium or steel.
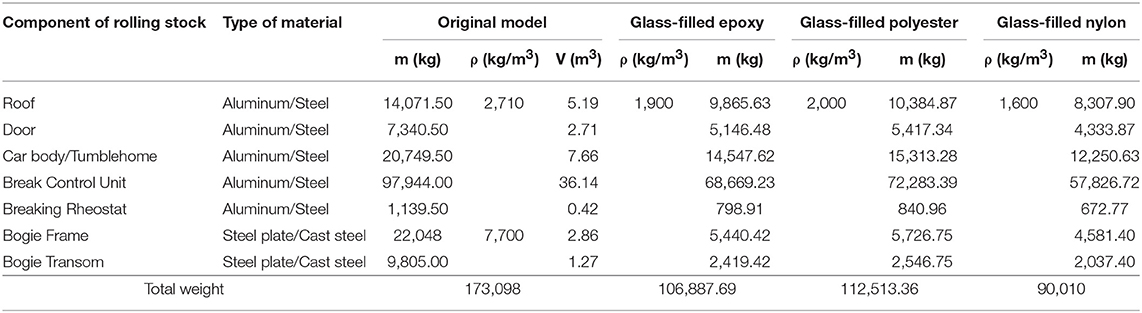
Table 1. The calculation of the HSR weight in three case studies after composite material replacement.
The key finding in Table 1 is the difference in the total mass of the six main parts after substitution with various type of composite materials. The original model is compared to three different types of composite materials. The different properties of glass filled with epoxy, polyester and nylon illustrate density values as 1,900 km/m3, 2,000 km/m3, and 1,600 km/m3 respectively.
As a result, the original model weighed 173,098 kg; whereas, composite materials such as glass filled with epoxy, polyester and nylon weigh 106,887.69, 112.513.36, and 90,010 kg respectively. The low-density property of composite materials significantly impacts the total weight of the HSR, and so, positively contributing to a light-weight car body. Therefore, the replacement with composite materials leads to a reduction in the amount of fuel consumed during the operation.
The Impact With the End-of-Life Rolling Stock
Regarding end-of-life rolling stock CO2 emissions, many researchers have measured its performance by greenhouse gas emission rates, through recycling rates (%Rcyc) and recovery rates (%Rcov) (Song and Lee, 2010; International Environmental Product Declaration System, 2013; Kaewunruen et al., 2019).
The recycling process of end-of-life rolling stock aims at turning waste parts into useable material and to decrease environmental impact. The full process includes three stages; pre-treatment, dismantling, and shredding. First, the pre-treatment stage removes all liquid, toxicities, fuel and gases. The process aims at preventing accidents during the transfer of rolling stock parts to the recycling process. The total mass of end-of-life rolling stock, which relates to the pre-treatment stage, is carried out in the form of m[P]Reuse, m[P]R, and m[P]E. Then, the rolling stock parts are sent to the dismantling stage that separate useful material parts in the rolling stock, i.e., cables, train seats, tables etc. The m[D]Reuse, m[D]R, m[D]E values are calculated as the total mass of the end-of-life rolling stock at the dismantling stage. The shredding process, lastly, aims at grinding large parts into small parts. The amount of m[S]R and m[S]E represent the total mass of the vehicle at the shredding stage.
There are differences in the material properties of the rolling stock. Some parts are suitable for recycling such as a metal, elastomer, glass, representing MRF values of more than 80%; on the other hand, a higher ERF value, as shown in reinforced polymers, are materials suitable for the energy recovery process. Therefore, the recycling process of end-of-life rolling stock should consider the material properties of all parts, which increases both Rcyc and Rcov values. The calculation of Rcyc and Rcov rates are shown as follows;
where;
Rcyc(%) = vehicle recyclability by percentage [%];
Rcov (%) = vehicle recoverability by percentage [%];
mv = total mass of rolling stock [kg];
MRF = Mass recovery factor [%];
ERF = Energy recovery factor [%];
i = material subscription;
j = {m[P]Reuse, m[P]R, m[P]E, m[D]Reuse, m[D]E, m[D]R, m[D]E, m[S]R, m[S]E}
m[P]Reuse = total mass of materials which can be considered reusable at the pre-treatment step [kg];
m[P]R = mass of materials which can be considered recyclable at the pre-treatment step [kg];
m[P]E = mass of materials which can be considered as energy recoverable at the pre-treatment step [kg];
m[D]Reuse = total mass of materials which can be considered reusable at the dismantling step [kg];
m[D]R = mass of materials which can be considered recyclable at the dismantling step [kg];
m[D]E = mass of materials which can be considered as energy recoverable at the dismantling step [kg];
m[S]R = mass of materials which can be considered recyclable at the shredding step [kg];
m[S]E = mass of materials which can be considered as energy recoverable at the shredding step [kg].
Results
The calculation of the Rcyc and Rcov values, divide the CFRP materials, which are useful composite materials, into six rolling stock parts. The substitution in material and property causes a change in total mass, Reuse, m[P]R, m[P]E, m[D]R, m[D]E, m[S]R, m[S]E, Rcyc, Rcov, and waste values. The reason for this is the Rcyc and Rcov of CFRP is 95% (Pillan et al., 2019); whereas, the value of aluminium represents a Rcyc of 14% and Rcov of 33% (International Environmental Product Declaration System, 2013; Delogu et al., 2017).
As illustrated in Table 2, the replacement of six components on the new HSR rolling stock model changes the overall weight of the original model from 265,000 to 201,124.69 kg; in other words, it decreases the total weight by 24.61%. The decrease in the total weight decreases the energy required to operate the HSR. Additionally, the leftover landfill waste is approximately 14,420 kg compared to the 88,201 kg in the original model.
Moreover, the overall recyclability rates of the new model is 73.10% compared with the 61.4% in the original model, which increases % Rcyc by 11%. Also, an increase of 5% in Rcov is revealed with the upgrade, increasing the Rcov from 73.9% in the original model to 78.9% in the improved model, as illustrated in Figure 1. The significant increase in both rates, greatly reduces both landfill waste and CO2 emissions in the long term.
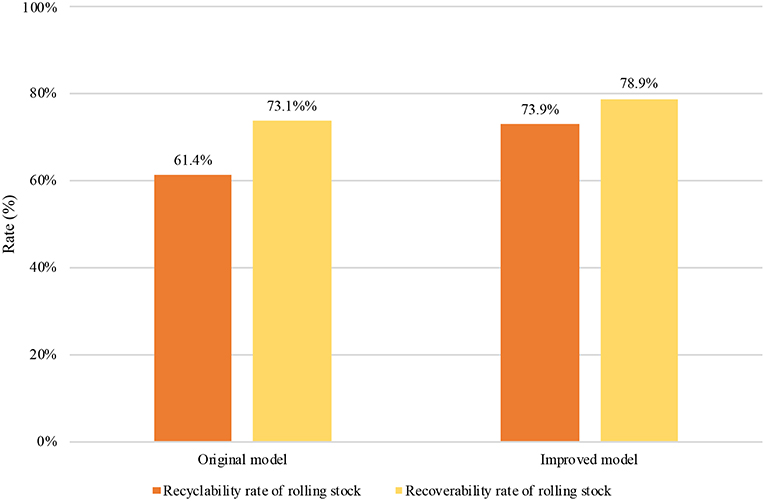
Figure 1. The comparison of recyclability rate (Rcyc) and recovery rate (Rcov) between the original model and the improved model.
In conclusion, substituting CFRP material in the HSR's body, provides long-term benefits in the recycling process of the end-of-life HSR vehicle. The recyclable materials, which were applied to the new model of the HSR, reduces the waste left over after the end-of-life stage. Also, the energy requirements in operating the new HSR model are lower than in the original model, as the materials used in the new model are light-weight and therefore requires less energy to operate. In other words, CO2 combustion and emissions will certainly be decreased directly because of a variation in the whole train body mass.
The Parametric Study of Time Effect on MRF and ERF Values
The technology revolution in manufacturing has increased recyclability production. Since the industrial era, various materials have been applied to abandoned products to support human needs. However, un-recyclable products have significantly impacted the environment which has pushed the idea of recyclability and the recycling of end-of-life products across industries forward.
Aluminum and steel materials are mostly used in sectors such as transportation and construction, as well as in other products. Products that are made from those materials and which are leftover or unused have increased landfill waste, significantly damaging the environment. Nevertheless, the improvement of recycling technologies and regulations to limit CO2 emissions have provoked an increasing number of recycling products. As shown in the example of aluminium production in Figure 2, the percentage of recycling components in aluminium production has risen after 1980 (Greem, 2007).
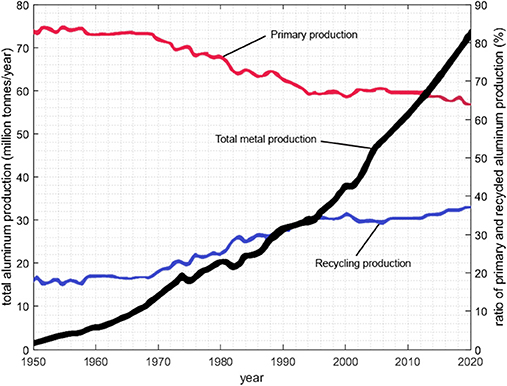
Figure 2. The percentage of recycling component in aluminium production (adapted from Greem, 2007).
In the transportation sector, mixed aluminium with steel and pure steel make up the majority of components in HSR rolling stock which consists of 51.55 and 36.52%, respectively. The recycling rate of aluminium production relates to its respective industry. In 2007, for instance, the rate was approximately 90% in the transportation sector and 85% in the construction sector, but 60% in the beverage can production industry (Damgaard et al., 2009; European Aluminium Association, 2009; Martin, 2013; Bowyer et al., 2015; Rybica et al., 2016; Ip et al., 2018).
With regards to the end-of-life HSR rolling stock, recycling rates have continuously increased due the advancement of technologies (Greem, 2007; Damgaard et al., 2009; Martin, 2013). The recycling rate of mixed aluminium and steel was only at 90% of the recycling rate in 2006 and it increased by 1% the following year. At present, the recycling rate sits at 94%, which is almost higher than any other materials. In terms of steel recycling, the trend in recycling rates has also increased from 88% in 2012 to 90% in 2019. The obvious increase of recycling rates on mixed aluminium with steel and pure steel are impacted by recycling technologies. It directly generates a positive impact across end-of-life rolling stock, reducing the amount of waste leftover and the global environmental impact.
The prediction on MRF values of the second top material used in HSR is provided to predict future values. The research considers data from at least 3 consecutive years. The data was processed using a regression analysis with logarithmic interpolation. The achieved coefficients included 95% confidence bounds. The goodness of fit was examined under the sum of squares due to an error. As a result, the recycling rate of mixed aluminium and steel is predicted to be 95 and 96% in 2029 and 2039 respectively. Additionally, the recycling rate for steel is predicted to be 93% in 2029 and 95% in 2039 as shown in Figures 3, 4.
An increase in recycling rates in the majority of components will have a positive impact on the end-of-life rolling stock in the future as landfill waste will be reduced. With regards to the calculation of left-over residue, using Equation (3) shows that there will be 267,601.51 kg of recyclable components and 16,610.49 kg of waste in 2029. In 2039, left-over waste will have decreased to 13,094.98 and 270,799.02 kg of recyclable components. This shows that upgrading to recycling technologies will decrease the global impact to the environment.
To compare left-over landfill waste, there are four end-of-life rolling stock models; the original model, the improved model with the CFRP material replacement, the predictive model in 2029 and the predictive model in 2039 as shown in Figure 5. The original model shows a large amount of waste at 88,201 kg compared to 13,094.98 kg in the predictive model in 2039. Therefore, the decrease in waste is ~85% from the original model.
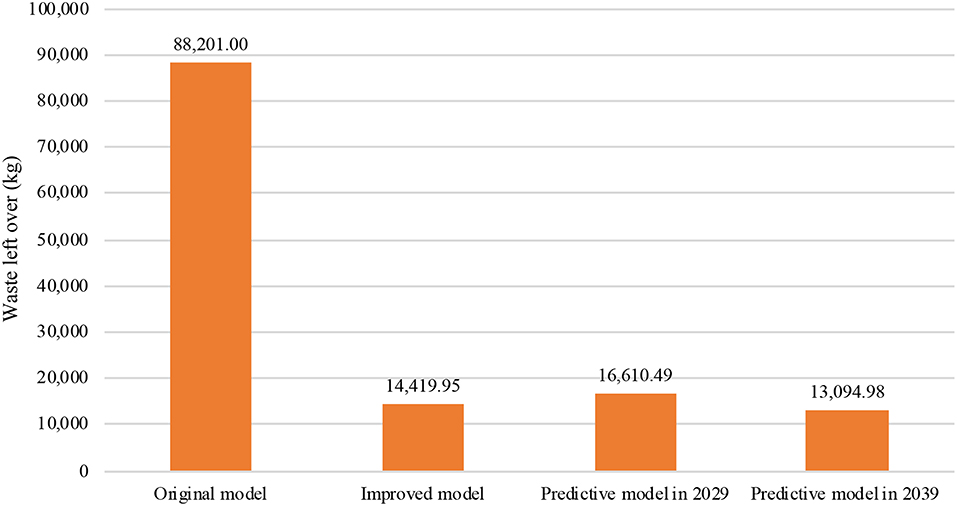
Figure 5. The comparison of left-over waste between the original model, improved model, predictive model in 2029 and 2039.
Discussion
The HSR system consistently provides a service that positively impacts human life; however, the dramatic growth of the HSR has created higher atmospheric CO2 emissions. Thus, the notion of reducing CO2 emissions has been addressed in various aspects, from changing operation systems to electric trains and even material replacement.
Within this study, the CFPR replacement material was developed based on the “original model” in Kaewunruen et al. (2019) research. While the original model comprises more than 35 parts, there are only six parts of the component that can feasibly be replaced with the composite materials.
First, the three types consisting of glass filled with epoxy, polyester and nylon, have been replaced in the six components. As a result, the total weight of the improved model is reduced by 24.61%, on average. This shows that all composite materials are suitable for substitution in the HSR's parts and, the decreased weight of the improved model therefore reduces the amount of fuel required for operation which leads to a decrease in CO2 emissions.
Additionally, the end-of-life HSR leftover landfill waste is reduced by nearly 84% as shown in the calculation in Table 2. The end-of-life rolling stock of the new model remains at only 14,420 kg; whereas the original model produced more than 80,000 kg in landfill. The initiative to reduce CO2 leads to the use of recyclable and recoverable materials, like CFRP materials. in the rolling stock component. As a result, the overall %Rcyc and %Rcov is dramatically improved by 73.1% and 78.9%, respectively. The increase in both values refers to the reduction of CO2 emissions from landfill.
Lastly, the parametric study showed that the improvement in technology directly impacts the end-of-life rolling stock's left over waste. In the original model, there is 88,201 kg left over residues but, in the predictive model in 2039, there will be only 13,094.98 kg left over waste. This means that almost all components can be recycled during the manufacturing processes. However, the research highly recommended following the material replacement method using CFRP material (improved model) for following two reasons. First, the “improved model” produces a slightly different amount of left-over waste. Furthermore, while the improved model is currently ready to implement, the predictive model in 2039 is requires future and developing technologies to support the recycling process.
Conclusion
The improved model of the HSR rolling stock, using replacement CFRP materials and techniques shows a decrease in CO2 emissions. This study confirms that the decrease in CO2 emissions in the atmosphere is a results of the reduction in fuel used for operating lightweight rolling stock. Additionally, CFRP material is ideal for recycling and recovering processes, which in turn decreases end-of-life rolling stock waste. Therefore, using CFRP materials to replace components in the new HSR model is feasible and desirable.
Data Availability
The raw data supporting the conclusions of this manuscript will be made available by the authors, without undue reservation, to any qualified researcher.
Author Contributions
PR conceived and designed the analysis and taken the case study from SK's research, contributes the methodology to compare with other composites materials and carried out the results. SK provided deeply information on data analysis section. Z-JS provided critical feedback and helped shape the research, analysis and manuscript.
Conflict of Interest Statement
The authors declare that the research was conducted in the absence of any commercial or financial relationships that could be construed as a potential conflict of interest.
Acknowledgments
PR gratefully acknowledges the Royal Thai Government for the Ph.D. scholarship at the University of Birmingham, United Kingdom. SK acknowledges the Australian Academy of Science (AAS) and the Japan Society for the Promotion of Sciences (JSPS), for the JSPS Invitation Fellowship for Research (Long-term), Grant No. JSPS-L15701, at the Railway Technical Research Institute (RTRI) and the University of Tokyo, Japan. Z-JS acknowledges the recommendations of the research project at the University of California, Berkeley.
References
Bowyer, J., Bratkovich, S., Fernholz, K., Frank, M., Groot, H., Howe, J., et al. (2015). Understanding Steel Recovery and Recycling Rates and Limitation to Recycling. Available online at: http://www.dovetailinc.org/report_pdfs/2015/dovetailsteelrecycling0315.pdf (Accessed March 15, 2019).
Chan, K. S., Miranda-Moreno, L., and Patterson, Z. (2013). Analysis of GHG emissions for city passenger trains: is electricity an obvious option for montreal commuter trains? J. Transport. Technol. 3, 17–29. doi: 10.4236/jtts.2013.32A003
Damgaard, A., Larsen, A. W., and Christensen, T. H. (2009). Recycling of metals: accounting of greenhouse gases and global warming contributions. Waste Manag. Res. 27, 773–780. doi: 10.1177/0734242X09346838
Damm, A., Koberl, J., Prettenthaler, F., Rogler, N., and Toglhofer, C. (2016). Impacts of +2C global warming on electricity demand in Europe. Clim. Serv. 7, 12–30. doi: 10.1016/j.cliser.2016.07.001
Davel, A. P., Lemos, M., Pastro, L. M., Pedro, S. C., de André, P. A., Hebeda, C., et al. (2012). Endothelial dysfunction in the pulmonary artery induced by concentrated fine particulate matter exposure is associated with local but not systemic inflammation. Toxicology 295, 39–46. doi: 10.1016/j.tox.2012.02.004
Delogu, M., Del Pero, F., Berzi, L., Pierini, M., and Bonaffini, D. (2017). End-of-Life in the railway sector: analysis of recyclability and recoverability for different vehicle case studies. Waste Manag. 60, 439–450. doi: 10.1016/j.wasman.2016.09.034
Deng, X., Zhang, F., Rui, W., Long, F., Wang, L., and Feng, Z. (2013). PM2.5-induced oxidative stress triggers autophagy in human lung epithelial A549 cells. Toxicol. In Vitro 27, 1762–1770. doi: 10.1016/j.tiv.2013.05.004
Dutta, T., and Barman, A. (2019). Green and sustainable manufacturing of metallic, ceramic and composite materials. Mater. Sci. Mater. Eng. doi: 10.1016/B978-0-12-803581-8.11023-9
European Aluminium Association (2009). Global Aluminium Recycling: A Cornerstone of Sustainable Development. Available online at: http://www.world-aluminium.org/media/filer_public/2013/01/15/fl0000181.pdf (accessed March 15, 2019).
Greem, J. A. S. (2007). Aluminium Recycling and Procession for Energy Conservation and Sustainability. ASM International.
Hassan, B., Oghenevweta, J. E., and Aigbodion, V. S. (2012). Potentials of maize stalk ash as reinforcement in polyster composites. J. Miner. Mater. Character. Eng.11, 445–459. doi: 10.4236/jmmce.2012.114032
Hofstatter, T., Pedersen, D. B., Tosello, G., and Hansen, H. N. (2007). “Challenges and opportunities of fibre-reinforced polymers in additive manufacturing with focus on industrial applications,” in Proceedings of the Joint Special Interest Group Meeting Between Euspen and ASPE: Dimensional Accuracy and Surface Finish in Additive Manufacturing (Lyngby: The European Society for Precision Engineering and Nanotechnology).
International Environmental Product Declaration System, (2013). Product Category Rules (PCR) for Preparing an EPD for Rail Vehicles Version 2.0 ISO/TC267. Facility Management. London: International Organisation for Standardization.
Ip, K., Testa, M., Raymond, A., Graves, S. C., and Gustowski, T. (2018). Performance evaluation of material separation in a material recovery facility using a network flow model. Resourc. Conserv. Recyclin. 131, 192–205. doi: 10.1016/j.resconrec.2017.11.021
Kaewunruen, S., Rungskunroch, P., and Jennings, D. (2019). A through-life evaluation of end-of-life rolling stocks considering asset recycling energy recovering, and financial benefit. J. Clean. Produc. 212, 1008–1024. doi: 10.1016/j.jclepro.2018.11.271
Kamal, A. S., Rohr, A. C., Mukherjee, B., Morishita, M., Keeler, G. J., Harkema, J. R., et al. (2011). PM2.5-induced changes in cardiac function of hypertensive rats depend on wind direction and specific sources in Steubenville, Ohio. Inhal. Toxicol. 23, 417–430. doi: 10.3109/08958378.2011.580387
Khan, A., Savi, P., Quaranta, S., Rovere, M., Giorcelli, M., Tagliaferro, A., et al. (2017). Low-cost carbon fillers to improve mechanicak properties and conductivity of epoxy composites. Polymers 9:642. doi: 10.3390/polym9120642
Khan, M. U., and Gillies, A. U. (2019). Diesel particulate matter: Monitoring and control improves safety and air quality. Adv. Produc. Safe Respons. Coal Minin. 2019, 199–213. doi: 10.1016/B978-0-08-101288-8.00009-2
Kinnon, M. M., Zhu, S., Carreras-Sospedra, M., Soukup, J. V., Dabdub, D., Samuelsen, G. S., et al. (2019). Considering future regional air quality impacts of the transportation Sector. Energy Policy 124, 63–80. doi: 10.1016/j.enpol.2018.09.011
Liu, C., Xu, X., Bai, Y., Wang, T. Y., Rao, X., Wang, A., et al. (2014). Air pollution-mediated susceptibility to inflammation and in- sulin resistance: influence of CCR2 pathways in mice. Environ. Health Perspect. 122, 17–26. doi: 10.1289/ehp.1306841
Longhin, E., Holme, J. A., Gutzkow, K. B., Arlt, V. M., Kucab, J. E., Camatini, M., et al. (2013). Cell cycle alterations induced by urban PM2.5 in bronchial epithelial cells: characterization of the process and possible mechanisms involved. Part Fibre Toxicol. 10:63. doi: 10.1186/1743-8977-10-63
Martin, E. (2013). How to Run a Profitable MRF in Today's Market. Available online at: https://resource-recycling.com/recycling/2018/10/23/how-to-run-a-profitable-mrf-in-todays-market/ (accessed March 15, 2019).
Masterbond (2019). Effect of Fillers on Epoxy Properties. Available online at: https://www.masterbond.com/articles/effect-fillers-epoxy-properties (accessed March 12, 2019).
Mendez, R., Zheng, Z., Fan, Z., Rajagopalan, S., Sun, Q., and Zhang, K. (2013). Exposure to fine airborne particulate matter induces macrophage infiltration, unfolded protein response and lipid deposition in white adipose tissue. Am. J. Transl. Res. 5, 224–234.
Merkisz, J., Jacyna, M., Merkisz-Guranowska, A., and Pielecha, J. (2014). Exhaust emissions from modes of transport under actual traffic conditions. WIT Trans. Ecol. Environ. 190, 1139–1150. doi: 10.2495/EQ141062
Mwambeleko, J. J., and Kulworawanichpong, T. (2017). Battery electric multiple units to replace diesel commuter trains serving short and idle routes. J. Energy Storage 11, 7–15. doi: 10.1016/j.est.2017.01.004
Oanh, K., Thiansathit, W., Bond, T. C., Subramanian, R., Winijkul, E., and Paw-armart, I. (2010). Compositional characterization of PM2.5 emitted from in-use diesel vehicles. Atmosphere. Environ. 44, 15–22. doi: 10.1016/j.atmosenv.2009.10.005
Office of Energy Efficiency Renewable Energy (2016). A Path to Lightweight Material in Car and Truck. Available online at: https://www.energy.gov/eere/articles/timeline-path-lightweight-materials-cars-and-trucks (accessed March 12, 2019).
Pillan, B., Loubet, P., Schrijvers, D., and Sonnemann, G. (2019). Life Cycle Assessment of Carbon Fibers Recycling – Comparison of Emerging Processes. Available online at: https://www.wrforum.org/profile/carbon-fibers-recycling/ (accessed March 12, 2019).
Rezaei, F., Yunus, R., and Ibrahim, N. A. (2009). Effect of fiber length on thermomechanical properties of short carbon fiber reinforced polypropylene composites. Mater. Des. 30:260e263. doi: 10.1016/j.matdes.2008.05.005
Ritts, A. C., Yu, Q., Li, H., Lombardo, S. J., Han, X., Xia, Z., et al. (2011). Plasma treated multi-walled carbon nanotubes (MWCNTs) for epoxy nanocomposites. Polymers 3, 2142–2155. doi: 10.3390/polym3042142
Rybica, J., Tiwari, A., and Leeke, G. A. (2016). Technology readiness level assessment of composites recycling technologies. Clean. Produc. 112, 1001–1012. doi: 10.1016/j.jclepro.2015.08.104
Smink, C. K. (2007). Vehicle recycling regulations: lessons from Denmark. J. Clean. Prod. 15, 1135–1146. doi: 10.1016/j.jclepro.2006.05.028
Song, J. S., and Lee, K. M. (2010). Development of a low-carbon product design system based on embedded GHG emissions. Resour. Conserv. Recycl. 54, 547–556. doi: 10.1016/j.resconrec.2009.10.012
The Engineering Toolbox (2008). Typical Properties of Engineering Materials Like Steel, Plastics, Ceramics and Composites. Available online at: https://www.engineeringtoolbox.com/engineering-materials-properties-d_1225.html (accessed March 12, 2019).
Torres-Ramos, Y. D., Montoya-Estrada, A., Guzman-Grenfell, A. M., Mancilla-Ramirez, J., Cardenas-Gonzalez, B., Blanco-Jimenez, S., et al. (2011). Urban PM2.5 induces ROS generation and RBC damage in COPD patients. Front. Biosci. 3, 808–817. doi: 10.2741/e288
UK Department of Transport (2014). Guidance on Measuring and Reporting Greenhouse Gas (GHG) Emissions From Freight Transport Operations. Available online at: https://www.gov.uk/government/uploads/system/uploads/attachment_data/file/218574/ghg-freight-guide.pdf (accessed March 12, 2019).
Wambua, P., Ivens, J., and Verpoest, I. (2003). Natural fibres: can they replace glass in fibre reinforced plastics? J Comp. Sci. Technol. 63, 1259–1264. doi: 10.1016/S0266-3538(03)00096-4
Wang, G., Zhao, J., Jiang, R., and Song, W. (2013). Rat lung response to ozone and fine particulate matter (PM) exposures. Environ. Toxicol. 30, 343–356. doi: 10.1002/tox.21912
Xu, X., Jiang, S. Y., Wang, T. Y., Bai, Y., Zhong, M., Wang, A., et al. (2013). Inflammatory response to fine particulate air pollution exposure:neutrophil versus monocyte. PLoS ONE 8:e71414. doi: 10.1371/journal.pone.0071414
Keywords: composite material, rolling stock, recyclability, recoverability, emission, CFRP, end-of-life rolling stock, material replacement
Citation: Rungskunroch P, Kaewunruen S and Shen Z-J (2019) An Improvement on the End-of-Life of High-Speed Rail Rolling Stocks Considering CFRP Composite Material Replacement. Front. Built Environ. 5:89. doi: 10.3389/fbuil.2019.00089
Received: 16 March 2019; Accepted: 19 June 2019;
Published: 03 July 2019.
Edited by:
Sanjay Shrawan Nimbalkar, University of Technology Sydney, AustraliaReviewed by:
Yan Quan Sun, Central Queensland University, AustraliaPing Liu, Jiangsu University of Science and Technology, China
Copyright © 2019 Rungskunroch, Kaewunruen and Shen. This is an open-access article distributed under the terms of the Creative Commons Attribution License (CC BY). The use, distribution or reproduction in other forums is permitted, provided the original author(s) and the copyright owner(s) are credited and that the original publication in this journal is cited, in accordance with accepted academic practice. No use, distribution or reproduction is permitted which does not comply with these terms.
*Correspondence: Sakdirat Kaewunruen, cy5rYWV3dW5ydWVuQGJoYW0uYWMudWs=