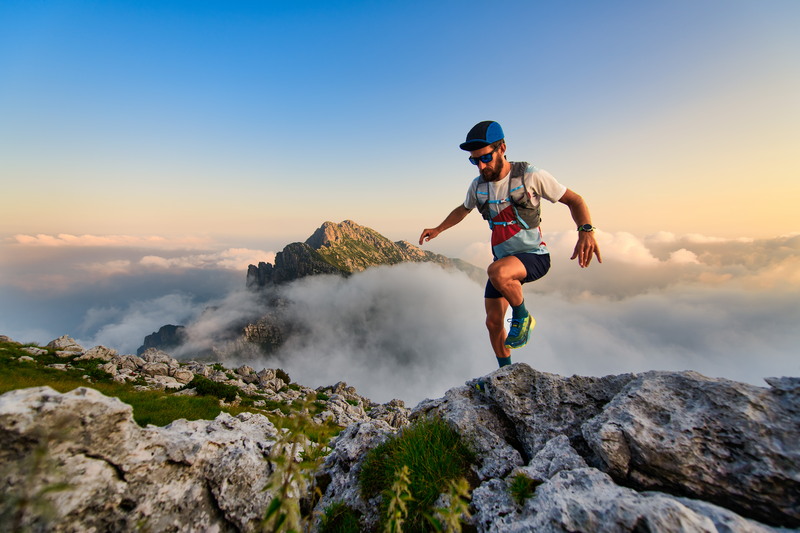
94% of researchers rate our articles as excellent or good
Learn more about the work of our research integrity team to safeguard the quality of each article we publish.
Find out more
ORIGINAL RESEARCH article
Front. Bioeng. Biotechnol. , 24 May 2021
Sec. Bioprocess Engineering
Volume 9 - 2021 | https://doi.org/10.3389/fbioe.2021.631089
This study aimed to utilize the enzymatic hydrolysis of leftover cooked rice (LCR) for fermentative ethanol production. Effect of glucoamylase volumes (V1: 5 U/g, V2: 25 U/g, and V3: 50 U/g) on the performance of LCR hydrolysis was also evaluated. It was found that the highest chemical oxygen demand (COD) of 77.5 g/L and reducing sugar (RS) of 34.6 g/L were achieved at V3. The LCR hydrolyzate obtained from enzymatic hydrolysis was then used as feedstock for ethanol fermentation. Higher ethanol production was obtained when RS increased from 18.7 g/L (V1) to 23.2 g/L (V2). However, lower ethanol production was found when RS further increased to 34.6 g/L (V3) probably because too high RS concentration led to the inhibition on the yeast. The maximum ethanol production and yield were 21.1 g/L and 0.3 g ethanol/g LCR, respectively. The LCR could be a promising substrate for fermentative ethanol production for industrial application.
Graphical Abstract. A combination bioprocess for ethanol production via hydrolysis and fermentation.
Due to the depletion of the fossil fuel and emission of the greenhouse gases, it is urgent to look for the renewable and clean alternative fuels to satisfy the global energy demands (Florentino-Madiedo et al., 2018; Li et al., 2019). Ethanol is considered to be one of the promising substitutes because it could meet the above requirements (Balat and Balat, 2009; Wychen and Laurens, 2013). Biological ethanol production from various types of substrates (corn, wheat, etc.) has been realized (Kim and Dale, 2004). However, these substrates are not the prospective choices for ethanol production since the global demand for food has not been satisfied (Condon et al., 2015). So, utilization of organic wastes for fermentative ethanol production has gained a great of attentions (Himmel et al., 2007).
The cooked rice is one of the most important staple foods, especially in China and East Asia countries (Liu et al., 2013; Han et al., 2017). It was reported that around 34 million tons of cooked rice were wasted per year in China (Zhao et al., 2019). The leftover cooked rice (LCR), which is rich in carbohydrate (starch), should be a good feedstock for bio-ethanol generation (Chen et al., 2016). However, it is difficult for microorganisms to directly utilize starch for fermentative ethanol production (Xu and Wang, 2017). Pre-treatment is required to make the LCR to be the fermentable nutrients (Rodriguez et al., 2015; Uçkun Kiran and Liu, 2015). There are three main methods used for biomass or organic solid waste pretreatments (Karimi and Taherzadeh, 2016; Lyu et al., 2019), including physical (shredding and heating), chemical (acid and alkaline), and biological (enzyme) methods. Enzymatic hydrolysis is regarded as a better choice compared to the others because it is performed at the mild condition and has no corrosion problem (Aditiya et al., 2016). However, information about enzymatic hydrolysis of LCR and ethanol fermentation from the LCR hydrolyzate is limited.
Therefore, this study aimed to utilize the enzymatic hydrolysis of LCR as substrate for fermentative ethanol production. Effect of glucoamylase volumes (V1: 5 U/g, V2: 25 U/g, and V3: 50 U/g) on the performance of LCR hydrolysis was investigated. RS produced in the LCR hydrolyzate was then fermented by the yeast for ethanol production. The efficiency of ethanol fermentation was also examined. It was expected that this work could provide a practical solution for LCR treatment and ethanol production in China and East Asia countries.
The schematic diagram of fermentative ethanol production from enzymatic hydrolysis of LCR was shown in Figure 1. The separated hydrolysis and fermentation process was selected in this study because of different temperatures required for enzymatic hydrolysis (95°C) and ethanol fermentation (30°C). It should be emphasized that sterilization and additional pH buffer and supplement were not applied. This is crucial for industrial application because the ethanol production cost could be inevitably reduced.
Figure 1. Schematic diagram and materials balance of fermentative ethanol production from enzymatic hydrolysis of leftover cooked rice with the enzyme volume of 25 U/g (V2). No sterilization and additional pH buffer and supplement were applied in this study.
The LCR was collected from the canteen of Hangzhou Dianzi University in Hangzhou, China. Its nutrients were analyzed and showed in Table 1. The LCR was first ground into the smaller size by the blender and then used for enzymatic hydrolysis (Farah Amani et al., 2017). Different from complex substrates (such as food waste), a combination enzymes (protease and cellulase) are not necessary in this study to break the LCR into fermentable sugars. The glucoamylase used for enzymatic hydrolysis was provided by the Ningxia Chemicals Ltd. (Ningxia, China). The optimal temperature range of the enzyme was 90–100°C with activity of 7 × 104 U/mL. The dry yeast Saccharomyces cerevisiae for ethanol fermentation was supplied by Zhejiang Jinhuanbao Biotechnology Company Limited (Huzhou, China). It was pre-cultivation with glucose and tap water (100:1:1,000, w/w/w) at the temperature of 30°C for 30 min. Then, the produced soluble yeast was utilized as inoculum for ethanol fermentation.
Leftover cooked rice hydrolysis was carried out in the bioreactor with effective volume of 500 mL. The LCR with 70 g was taken into the bioreactor with addition of tap water to the level of 500 mL. Effect of glucoamylase volumes (V1: 5 U/g, V2: 25 U/g, and V3: 50 U/g) on the performance of LCR hydrolysis was evaluated. The hydrolysis conditions were 95°C and 400 rpm, respectively. When the reducing sugar (RS) reached a maximum and became stable, the mixture was filtrated by the filtration paper to get the LCR hydrolyzate.
Utilization of LCR hydrolyzate as substrate for ethanol fermentation was conducted in another bioreactor. Inoculum (10 mL pre-cultivated yeast solution) was injected into the bioreactor with the produced LCR hydrolyzate. The ethanol fermentation was operated at the conditions of 30°C and 400 rpm agitation speed. Around 10 mL samples were taken at the intervals for ethanol, chemical oxygen demand (COD) and RS analysis.
The RS was determined by the DNS method, while the COD concentration was measured based on the Standard Methods (Franson, 1995). The produced ethanol was analyzed by the gas chromatography which was equipped with the flame ionization detector (FID). Nitrogen was used as the carrier gas. The detailed information for the ethanol analysis was provided in our published study (Han et al., 2019).
In this part, LCR was hydrolyzed by glucoamylase to produce the LCR hydrolyzate which was then used as substrate for ethanol fermentation. Effect of enzyme volumes on the hydrolysis efficiency was also evaluated. Figure 2 described the production of COD in the enzymatic hydrolysis of LCR. It can be observed that COD enhanced from V1 to V3 and the highest COD concentration of 77.5 g/L was obtained with V3. This is because higher enzyme volume could be benefit for enzymatic hydrolysis. It is similar to Ali Mandegari study (Ali Mandegari et al., 2017) that the hydrolysis rate was determined by the added amount of the enzyme. However, the enzyme volume of V3 (50 U/g) was twice higher than V2 (25 U/g) and 10 times than V1 (5 U/g), while the COD production increased 10.6% for V2 and 28% for V3 compared to V1. Ye et al. (2018) found that the enzyme activity might be inhibited by the glucose produced during hydrolysis. So, the enzyme volume of 5 U/g (V1) could to be the economic choice for LCR hydrolysis.
Figure 2. Production of the chemical oxygen demand in the enzymatic hydrolysis of leftover cooked rice.
Figure 3 showed the production of the RS in the enzymatic hydrolysis of LCR with different enzyme volumes (V1–V3). Similar to the COD production, the RS increased with increasing of enzyme volumes. The highest RS obtained for V1–V3 were 18.7, 23.2, and 34.6 g/L, respectively. This result was similar to Farah Amani (Farah Amani et al., 2017) who reported that the rate of hydrolysis enhanced with increasing of enzyme volumes used. The kinetic models for enzyme volumes and COD/RS were shown in Table 2. It was found that enzyme volumes (x) and COD/RS (y1/y2) have a good linear relationship which could be expressed as y1 = 188.69x + 58.3 (R2 = 0.994) and y2 = 178.77x + 15.9 (R2 = 0.967), respectively.
Figure 4 showed the performance of ethanol fermentation from LCR hydrolyzate. No additional pH buffer and supplement was applied in this study. Also, the sterilization was not needed because the further practical application could be taken into account (Leung et al., 2012). As shown in Figure 4A, the COD decreased at the beginning of the ethanol fermentation since the RS contained in the LCR hydrolyzate was consumed by the yeast. Then, the COD stabilized at around 50 h as the ethanol was produced (Ali Mandegari et al., 2017). The final COD concentrations for V1-V3 were 51, 45.2, and 60.7 mg/L, respectively.
Figure 4B described the RS consumed in the fermentative ethanol production. No lag period was observed for all the batches since the yeast used in this study had good adaptation (Jelena et al., 2012). The RS was consumed and the ethanol produced (Figure 4C) at the beginning of the fermentation. This result is different from Kim’s study (Ye et al., 2018) that the ethanol production from enzymatic hydrolysis of food waste was not found until 20 h after inoculation of yeast. This is probably because the filtration after enzymatic hydrolysis was not applied in Kim’s study (Ye et al., 2018) and the inhibitors (such as oil) inhibited the activity of the yeast for ethanol production. In this study, the ethanol production increased with increasing of RS concentration (V1 and V2) and the highest ethanol production of 21.1 g/L was achieved with V2. However, it was found that the ethanol production became lower when the RS concentration further increased. This is probably because the RS concentration is too high to inhibit the activity of yeast for ethanol production (Manfredi et al., 2018). In the batch V3, the RS further decreased from 30 h, while the COD and ethanol were no longer increased. It was indicated that the RS was consumed by the yeast for anabolic reaction (microorganism growth), not for catabolic metabolism (ethanol production) (Erdei et al., 2013). The kinetic performance of ethanol fermentation from LCR hydrolyzate was described in Table 3. It was observed that the maximum productivity of ethanol and ethanol yield of 0.84 g/L/h and 0.3 g ethanol/g LCR could be calculated, respectively.
Table 3. Kinetic values by yeast for fermentative ethanol production from LCR hydrolyzate with the enzyme volume of 25 U/g (V2).
Some studies reported the comparison of bioethanol production between separate hydrolysis and fermentation (SHF) and simultaneous saccharification and fermentation (SSF). In this study, SHF should be the better choice for bioethanol production from LCR due to the following two reasons. First, the temperatures for hydrolysis (95°C) and fermentation (30°C) are different. Higher hydrolysis efficiency could be obtained with SHF. Second, the inhibitors (such as oil) for ethanol fermentation could be removed by filtration after hydrolysis with SHF. Similar results have been found by other researchers. Ye et al. (2018) got the highest ethanol yields of 0.31 and 0.43 g ethanol/g TS from food waste for SSF and SHF, respectively. F Alfani et al. (2000) compared the bioethanol production from wheat straw with SSF and SHF. It was found that the ethanol yield was 68% of the theoretical yield for SSF, while the theoretical yield for SHF was 81%.
The ethanol yield obtained from this study was 0.3 g ethanol/g LCR which was equivalent to 0.75 g ethanol/g dry LCR (Figure 1). To our knowledge, this is the first study to report the fermentative ethanol production from LCR. This study also demonstrated that the LCR is a promising substrate for ethanol fermentation.
Utilization of LCR hydrolyzed by different glucoamylase volumes for fermentative ethanol production was investigated in this study. The highest COD of 77.5 g/L and RS of 34.6 g/L in the LCR hydrolyzate were obtained with the enzyme volume of 50 U/g. In the ethanol fermentation, no lag period was observed and the doubling time was 30 h. The ethanol productivity and ethanol yield were 0.84 g/L/h and 0.3 g ethanol/g LCR, respectively. To our knowledge, this is the first study to report the fermentative ethanol production from LCR and provide the basic information for further industrial application.
The original contributions presented in the study are included in the article/supplementary material, further inquiries can be directed to the corresponding author/s.
WH, XC, and YZ designed the experiments. YL and BC performed the biological experiments. XX, JT, and PH analyzed the data. WS and ZZ assisted with the ethanol content measurement. WH and JT supervised the manuscript. XC, YZ, and WH wrote the manuscript with contributions from all authors. All authors contributed to the article and approved the submitted version.
This work was supported by NSFC-Zhejiang Joint Fund for the Integration of Industrialization and Information (U1709215) and National Science Foundation of China (Nos. 61771178 and 41373121).
XC, YZ, WS, ZZ, and WH were employed by the company Zhejiang Jinhuanbao Biotechnology Company Limited.
The remaining authors declare that the research was conducted in the absence of any commercial or financial relationships that could be construed as a potential conflict of interest.
Aditiya, H. B., Mahlia, T. M. I., Chong, W. T., Nur, H., and Sebayang, A. H. (2016). Second generation bioethanol production: a critical review. Renew. Sustain. Energy Rev. 66, 631–653. doi: 10.1016/j.rser.2016.07.015
Alfani, F., Gallifuoco, A., Saporosi, A., and Cantarella, A. S. M. (2000). Comparison of SHF and SSF processes for the bioconversion of steam-exploded wheat straw. J. Ind. Microbiol. Biotechnol. 25, 184–192. doi: 10.1038/sj.jim.7000054
Ali Mandegari, M., Farzad, S., and Gorgens, J. F. (2017). Economic and environmental assessment of cellulosic ethanol production scenarios annexed to a typical sugar mill. Bioresour. Technol. 224, 314–326. doi: 10.1016/j.biortech.2016.10.074
Balat, M., and Balat, H. (2009). Recent trends in global production and utilization of bio-ethanol fuel. Appl. Energy 86, 2273–2282. doi: 10.1016/j.apenergy.2009.03.015
Chen, P., Xie, Q., Addy, M., Zhou, W., Liu, Y., Wang, Y., et al. (2016). Utilization of municipal solid and liquid wastes for bioenergy and bioproducts production. Bioresour. Technol. 215, 163–172. doi: 10.1016/j.biortech.2016.02.094
Condon, N., Klemick, H., and Wolverton, A. (2015). Impacts of ethanol policy on corn prices: a review and meta-analysis of recent evidence. Food Policy 51, 63–73. doi: 10.1016/j.foodpol.2014.12.007
Erdei, B., Galbe, M., and Zacchi, G. J. B. (2013). Simultaneous saccharification and co-fermentation of whole wheat in integrated ethanol production. Bioenergy 56, 506–514.
Farah Amani, A. H., Toh, S. M., Tan, J. S., and Lee, C. K. (2017). The efficiency of using oil palm frond hydrolysate from enzymatic hydrolysis in bioethanol production. Waste Biomass Valorization 9, 539–548. doi: 10.1007/s12649-017-0005-z
Florentino-Madiedo, L., Díaz-Faes, E., García, R., and Barriocanal, C. (2018). Influence of binder type on greenhouse gases and PAHs from the pyrolysis of biomass briquettes. Fuel Process. Technol. 171, 330–338. doi: 10.1016/j.fuproc.2017.11.029
Franson, M. A. H. (1995). American public health association American water works association water environment federation. Methods 6:86.
Han, W., Hu, Y., Li, S., Huang, J., Nie, Q., Zhao, H., et al. (2017). Simultaneous dark fermentative hydrogen and ethanol production from waste bread in a mixed packed tank reactor. J. Clean. Product. 141, 608–611. doi: 10.1016/j.jclepro.2016.09.143
Han, W., Xu, X., Gao, Y., He, H., Chen, L., Tian, X., et al. (2019). Utilization of waste cake for fermentative ethanol production. Sci. Total Environ. 673, 378–383. doi: 10.1016/j.scitotenv.2019.04.079
Himmel, M. E., Ding, S. Y., Johnson, D. K., Adney, W. S., Nimlos, M. R., Brady, J. W., et al. (2007). Biomass recalcitrance: engineering plants and enzymes for biofuels production. Science 315, 804–807. doi: 10.1126/science.1137016
Jelena, M. D., Vucurovic, D., Sinisa, N. D., and Grahovac, J. (2012). Kinetic modelling of batch ethanol production from sugar beet raw juice. Appl. Energy Appl. Energy 99, 2192–2197. doi: 10.1016/j.apenergy.2012.05.016
Karimi, K., and Taherzadeh, M. J. (2016). A critical review of analytical methods in pretreatment of lignocelluloses: composition, imaging, and crystallinity. Bioresour. Technol. 200, 1008–1018. doi: 10.1016/j.biortech.2015.11.022
Kim, S., and Dale, B. E. (2004). Global potential bioethanol production from wasted crops and crop residues. Biomass Bioenergy 26, 361–375. doi: 10.1016/j.biombioe.2003.08.002
Leung, C. C. J., Cheung, A. S. Y., Zhang, A. Y.-Z., Lam, K. F., and Lin, C. S. K. (2012). Utilisation of waste bread for fermentative succinic acid production. Biochem. Eng. J. 65, 10–15. doi: 10.1016/j.bej.2012.03.010
Li, P., Sakuragi, K., and Makino, H. (2019). Extraction techniques in sustainable biofuel production: a concise review. Fuel Process. Technol. 193, 295–303. doi: 10.1016/j.fuproc.2019.05.009
Liu, Y., Yuan, X.-Z., Huang, H.-J., Wang, X.-L., Wang, H., and Zeng, G.-M. (2013). Thermochemical liquefaction of rice husk for bio-oil production in mixed solvent (ethanol–water). Fuel Process. Technol. 112, 93–99. doi: 10.1016/j.fuproc.2013.03.005
Lyu, H., Zhang, J., Zhou, J., Shi, X., Lv, C., and Geng, Z. (2019). A subcritical pretreatment improved by self-produced organic acids to increase xylose yield. Fuel Process. Technol. 195:106148. doi: 10.1016/j.fuproc.2019.106148
Manfredi, A. P., Ballesteros, I., Saez, F., Perotti, N. I., Martinez, M. A., and Negro, M. J. (2018). Integral process assessment of sugarcane agricultural crop residues conversion to ethanol. Bioresour. Technol. 260, 241–247. doi: 10.1016/j.biortech.2018.03.114
Rodriguez, C., Alaswad, A., Mooney, J., Prescott, T., and Olabi, A. G. (2015). Pre-treatment techniques used for anaerobic digestion of algae. Fuel Process. Technol. 138, 765–779. doi: 10.1016/j.fuproc.2015.06.027
Uçkun Kiran, E., and Liu, Y. (2015). Bioethanol production from mixed food waste by an effective enzymatic pretreatment. Fuel 159, 463–469. doi: 10.1016/j.fuel.2015.06.101
Wychen, S., and Laurens, L. (2013). Determination of Total Solids and Ash in Algal Biomass: Laboratory Analytical Procedure (LAP). Golden, CO: NREL, 5100–60956.
Xu, Y., and Wang, D. (2017). Integrating starchy substrate into cellulosic ethanol production to boost ethanol titers and yields. Appl. Energy 195, 196–203. doi: 10.1016/j.apenergy.2017.03.035
Ye, G., Zeng, D., Zhang, S., Fan, M., Zhang, H., and Xie, J. (2018). Ethanol production from mixtures of sugarcane bagasse and Dioscorea composita extracted residue with high solid loading. Bioresour. Technol. 257, 23–29. doi: 10.1016/j.biortech.2018.02.008
Keywords: ethanol fermentation, glucoamylase, leftover cooked rice, reducing sugar, hydrolysis
Citation: Chen X, Zhao Y, Chen B, Su W, Zhang Z, Liu Y, Xu X, Tang J, Hou P and Han W (2021) Effects of Enzyme Volumes on Hydrolysis and Fermentation for Ethanol Production From Leftover Cooked Rice. Front. Bioeng. Biotechnol. 9:631089. doi: 10.3389/fbioe.2021.631089
Received: 19 November 2020; Accepted: 28 April 2021;
Published: 24 May 2021.
Edited by:
Carol Sze Ki Lin, City University of Hong Kong, ChinaReviewed by:
Reinaldo Gaspar Bastos, Federal University of São Carlos, BrazilCopyright © 2021 Chen, Zhao, Chen, Su, Zhang, Liu, Xu, Tang, Hou and Han. This is an open-access article distributed under the terms of the Creative Commons Attribution License (CC BY). The use, distribution or reproduction in other forums is permitted, provided the original author(s) and the copyright owner(s) are credited and that the original publication in this journal is cited, in accordance with accepted academic practice. No use, distribution or reproduction is permitted which does not comply with these terms.
*Correspondence: Wei Han, aGFud2VpMTk4MkBoZHUuZWR1LmNu
Disclaimer: All claims expressed in this article are solely those of the authors and do not necessarily represent those of their affiliated organizations, or those of the publisher, the editors and the reviewers. Any product that may be evaluated in this article or claim that may be made by its manufacturer is not guaranteed or endorsed by the publisher.
Research integrity at Frontiers
Learn more about the work of our research integrity team to safeguard the quality of each article we publish.