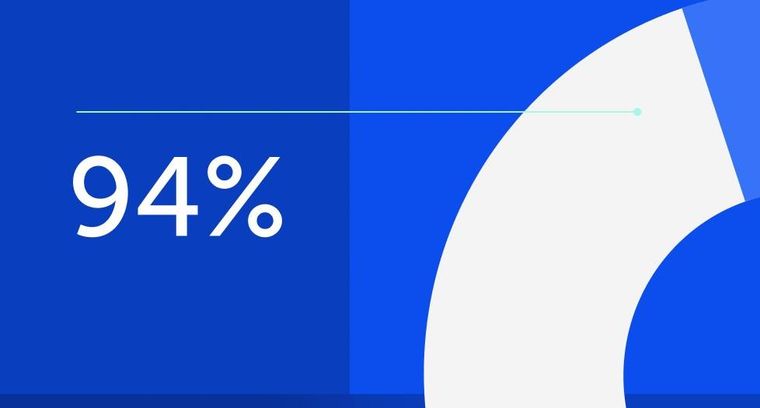
94% of researchers rate our articles as excellent or good
Learn more about the work of our research integrity team to safeguard the quality of each article we publish.
Find out more
REVIEW article
Front. Batter. Electrochem., 23 February 2024
Sec. Battery Materials Research
Volume 3 - 2024 | https://doi.org/10.3389/fbael.2024.1338069
This article is part of the Research TopicFrontiers in Batteries and Electrochemistry: Review CollectionView all 4 articles
This review focuses on recent advancements in single-crystal Ni-rich cathodes for Li-ion batteries. An in-depth analysis is provided of the key characteristics of single-crystal Ni-rich cathodes and a description of the synthesis methods, performance degradation mechanisms, and enhancement strategies tailored to these materials is given. Synthesis techniques such as solid-state and molten salt syntheses are discussed in detail. Additionally, we describe some of the nuanced challenges and solutions pertaining to single-crystal Ni-rich cathodes, including surface modification (coating and additives) to improve the initial efficiency and Li diffusion rate through doping, with the aim of prolonging cyclability. This review offers comprehensive insights into the development of single-crystal Ni-rich cathodes and suggests directions for advancing Li-ion battery technology using these specialized cathode materials.
Recently, the demand for Li-ion batteries (LIBs) has grown exponentially with their applications in large-scale devices such as electric vehicles and energy storage systems (ESS). The energy density of LIBs directly affects the performance of these large devices, including the driving range of electric vehicles and operating time of ESS, making them critically important. Furthermore, frequent fluctuations in fuel prices and increasing air pollution have increased the importance of eco-friendly transportation methods, especially electric vehicles. To meet the rapidly expanding market demand, it is necessary to enhance the energy density of LIBs (Wakihara, 2001; Natarajan and Aravindan, 2018; Kebede et al., 2022).
An LIB system composed of LiCoO2 and graphite was first developed by Sony in 1991 (Ozawa, 1994). Initially, cathode LiCoO2 exhibits a layered crystalline structure that allows the lithiation and delithiation of Li ions along a two-dimensional plane. Cathode materials with such layered structure have high Li-ion conductivity during the charge and discharge processes because of strong ionic bonding in the metal oxide (M–O) layers formed, which interact with adjacent M–O layers through strong Coulombic forces, facilitating the insertion and removal of Li ions. Unfortunately, LiCoO2 undergoes an irreversible phase transition to O1 when more than half of the Li ions are removed, limiting its practical capacity to 150 mAh g-1, despite its theoretical capacity of 274 mAh g-1 (Gabrisch et al., 2002; Hirooka et al., 2020). Nevertheless, LiCoO2 possesses many advantages such as excellent cycle life and ease of synthesis. However, with the expansion of secondary battery markets, there is a problem of increasing cobalt (Co) raw material prices associated with the growing consumption of LiCoO2. Furthermore, owing to its low reversible capacity, it is not suitable for battery systems that require high energy density, such as electric vehicles.
The limitations of LiCoO2 have prompted the exploration of the more cost-effective LiMO2 material based on nickel (Ni). Additionally, Ni-based materials can serve not only in batteries but also for various applications, such as catalysts (particularly in processes like the oxidative coupling of methane), making them easily accessible (Pickering et al., 1992). LiNiO2, which has a layered structure similar to that of LiCoO2, is an ideal substitute because of its low cost and high reversible capacity (Kalyani and Kalaiselvi, 2005). Ni is a crucial element for increasing the battery capacity because the oxidation potential of Ni2+ is lower than that of Co3+. Nevertheless, LiNiO2 also faces challenges in cycling performance attributed to structural instability during the processes of lithiation and delithiation. The problem can be partially resolved by substituting Ni with Co, Mn, or Al. Consequently, researchers have begun studying lithium nickel-cobalt-manganese oxide (Li[NixCoyMn1–x–y]O2, NCM) to address this issue (Tian et al., 2020; Chen S. et al., 2021).
NCM cathode have garnered significant attention and made progress owing to its layered structure, high capacity, and cost-effectiveness. The first NCM cathode developed was NCM333 (Li [Ni0.33Co0.33Mn0.33] O2), with an equal molar ratio of Ni, Co, and Mn. NCM333 has a discharge capacity of 150 mAh g-1 at a charging voltage of 4.3 V, which is similar to that of LiCoO2 (Wang et al., 2019). Increasing the Ni content effectively enhances the energy density and discharge capacity of NCM cathodes at the same charge voltage. To achieve a higher capacity, the nickel content was gradually increased, leading to the development of materials such as NCM622 (Li[Ni0.6Co0.2Mn0.2]O2) and NCM721 (Li[Ni0.7Co0.2Mn0.1]O2), with a nickel content of 60% or more. Furthermore, Ni-rich cathodes, such as NCM811 (Li[Ni0.8 Co0.1Mn0.1]O2) with a Ni content of over 80%, have been developed. Ni-rich cathodes have gained significant attention and are widely used because they offer higher capacity (>200 mAh g-1) than LiCoO2, making them one of the most prominent cathode materials in use today (Liu et al., 2015).
Ni-rich cathodes have had positive effects in terms of energy density owing to their high discharge capacity and relatively high operating voltage (3.6 V). However, as the Ni content increases, battery life deteriorates. Figure 1 illustrates the discharge capacity retention of three different materials with varying nickel content: NCM-622, NCM-811, and NCM-90, at 4.3 V, 4.4 V, and 4.5 V (Kim et al., 2019). As shown in Figure 1A, the initial cycle discharge capacities of these three materials at 4.3 V are 180.3, 200.5, and 212.0 mAh g-1, respectively. As expected, an increase in the nickel content leads to a higher capacity, with NCM-90 having the highest nickel content and capacity. However, as the charge and discharge cycles were repeated, sharp capacity degradation occurred, and after 100 cycles, the capacity retention was inversely proportional to the nickel content. NCM-90, with the highest Ni content, retained only 89.9% of its initial capacity, whereas NCM-811 and NCM-622 exhibited high capacity retentions of 93.8% and 96.3%, respectively. Notably, at 4.4 V and 4.5 V, increasing the nickel content also led to a shorter cycling life. The three main causes of this reduction in the lifespan of Ni-rich cathodes are electrolyte decomposition, cation mixing, and microcracking.
FIGURE 1. Cycling performance of NCM cathodes (NCM-622, 811, and 90) tested in 2032 coin-type half-cells using Li metal anodes cycled between 2.7 V and (A) 4.3 V, (B) 4.4 V, and (C) 4.5 V at a current density of 0.5 C (90 mA g−1) and 30°C; (D) relationship between the capacity retention and discharge capacity of the Ni-rich cathodes with charge potentials of 4.3, 4.4, and 4.5 V (Kim et al., 2019). Copyright 2019, Journal of Materials Chemistry A.
As shown in Figure 2 (Sun et al., 2018), Ni-rich polycrystalline cathodes are synthesized using the co-precipitation method by preparing a mixed solution of transition metal sulfates, such as NiSO4·6H2O, MnSO4·H2O, and CoSO4·7H2O, in a molar ratio of x:y:z. To achieve uniform precursor production, sodium hydroxide (NaOH) and NH3·H2O are appropriately used as precipitants, pH controllers, and complexing agents while pumping the mixed solution into a Continuous Stirred-Tank Reactor (CSTR). CSTR induces the precipitation of (NixMnyCoz)(OH)2.
FIGURE 2. Schematic diagram of a continuous stirred-tank reactor (CSTR) and the co-precipitation method (Sun et al., 2018). Copyright 2018, Dalton Transactions.
To synthesize a precursor with a uniform cation distribution, various factors such as pH, stirring speed, and temperature must be considered during the co-precipitation process. In a study conducted by Sun et al., the pH value was adjusted to ∼9, and the circulator bath was maintained at a temperature of 50°C with a stirring speed of approximately 500 rpm to synthesize Ni-rich precursors (Sun et al., 2018). In the work of Gomez-Martin et al., the precursor Ni0.90Mn0.05Co0.05(OH)2 was manufactured by setting the pH value in the range of 7–10, maintaining the circulator bath at a temperature of 60°C, and using a stirring speed of 1,300 rpm (Gomez-Martin et al., 2022).
Next, excess Li sources, such as LiOH or Li2CO3, were added to the co-precipitated (NixMnyCoz)(OH)2 precursor and thoroughly mixed. During heat treatment, Li ions were transported to the secondary particle precursor, resulting in Ni-rich secondary particles. Excess Li was used to compensate for Li loss during sintering. In addition, for Ni-rich synthesis, low-temperature sintering is required to prevent cation mixing. In the study by Hua et al., a mixed material was preheated at 550°C for 6 h and then sintered at 850°C for 12 h to synthesize NCM523 (Hua et al., 2014).
In contrast, Xu et al. used a Li:M molar ratio of 1.05:1 to mix LiOH and Ni0.8Co0.1Mn0.1 precursor, followed by low-temperature heat treatment in an oxygen atmosphere (heating the mixture at 500°C for 5 h and then sintering at 740°C for 10 h) to obtain the final Ni-rich NCM811 (Xu et al., 2019). The excess Li reactant and relatively low temperature (<800°C) synthesis inherent to Ni-rich cathodes often leave residual Li impurities on the surface. Residual Li compounds such as LiOH and Li2CO3 can undergo electrochemical decomposition during charging, leading to the generation of carbon dioxide and oxygen gases, which can be problematic (Rahman and Saito, 2007; Robert et al., 2015).
LiPF6-based commercial electrolytes, which are essential components of LIBs, are unstable and decompose at high voltages. This instability is particularly pronounced in the case of Ni-rich cathodes, where electrolyte side reactions are accelerated. This is because Ni ions are unstable; in the absence of Li, Ni4+ readily undergoes reduction to Ni3+ and Ni2+, which promotes the decomposition of LiPF6. As shown in Figure 3 (Liu et al., 2015), electrolyte side reactions occur, resulting in the formation of a thick NiO layer on the electrode surface. The NiO layer acts as a solid that hinders both ion and electron conduction, leading to an increase in battery impedance. Additionally, a dense and high-density cathode electrolyte interface (CEI) layer composed of LiF and Li2O forms over the NiO layer. As cycling progresses, these high-resistance byproducts accumulate, impairing Li diffusion and leading to degradation of the battery life (Lee et al., 2022).
FIGURE 3. Microstructure and composition of the cathode electrolyte interface (CEI) at the surface of Ni-rich cathode materials (Liu et al., 2015). Copyright 2015, Angewandte Chemie International Edition. Solid-electrolyte interface.
Effective CEI formation using electrolyte additives can improve the electrochemical performance of Ni-rich cathodes by blocking the series of side reaction loops that occur when the base electrolyte contacts the surface. In a study by Jiao et al., a dense and inorganic-rich CEI layer formed in an electrolyte containing a trimethylsilyl 2-(fluorosulfonyl) difluoroacetate (TMSFS) additive significantly improved the lifespan of NCM90 (Jiao et al., 2021). Zou et al. used a 1,2,4-1H-triazole (HTZ) additive to form an effective protective layer that blocked direct contact between the NCM90 surface and electrolyte. With this additive, the capacity retention after 150 cycles of 1 C high-rate charge and discharge was significantly enhanced, reaching 86.6%, which is much higher than the 74.8% retention obtained with the base electrolyte (Zou et al., 2021b).
As shown in Figure 4A (Ryu et al., 2018), NCM cathodes undergo H2–H3 phase transitions near 4.2 V, resulting in unequal volume changes along the c- and a-axes. This anisotropic contraction and expansion, especially in Ni-rich cathodes with more than 80% Ni, can lead to severe internal deformation, causing microcracks that separate primary particles from each other. Some microcracks are interconnected, forming tunnels from the core to the surface when their density is sufficiently high. This provides pathways for electrolyte infiltration to penetrate the secondary particle cores, significantly increasing the non-surface area in contact with the electrolyte. The increased surface exposure due to microcracks accelerates and exacerbates surface degradation issues such as the previously mentioned side reactions, resulting in the generation of high-resistance materials such as NiO. This not only leads to capacity degradation, but also generates a significant amount of gas, posing safety concerns. Although some level of surface degradation due to Li insertion and extraction on the secondary particle surface is inevitable during charging and discharging, microcracks that lead to structural collapse dominate the performance degradation in Ni-rich cathodes.
FIGURE 4. (A) Capacity fading scheme of Ni-rich cathode materials (Xu et al., 2018). Copyright 2018, Chemistry of materials. (B) Schematic illustration of the effect of boron doping on an NCM90 cathode’s mechanical stability during charge and discharge cycling (Park et al., 2018). Copyright 2018.
Morphological design has garnered significant attention from researchers in recent years for mitigating microcracks. Park et al. designed a radial morphology of primary particles via boron doping, as shown in Figure 4B (Park et al., 2018). This design effectively improved the cycling performance of NCM90. Anisotropic volumetric changes in randomly oriented primary particles lead to localized stress concentration, resulting in microcracks and accelerated capacity fading owing to infiltration of electrolyte into the particles. However, modifying the morphology through boron doping induces and effectively suppresses microcracks, leading to a significant improvement in cycling stability.
Ni-rich cathodes such as LiCoO2 adopt an O3 structure with an ideal R3m space group. In this structure, the transition metal sites (3a) and Li sites (3b) are clearly separated. A layered structure is formed with alternating metal oxide layers composed of transition metals, oxygen, and Li, creating a regular O–Li–O–M–O–Li–O–M–O pattern. The M-O layers formed by strong ionic bonding interact with adjacent M-O layers through strong Coulombic forces, making it easy for Li ions to move within them.
However, it has been reported that during the synthesis of Ni-rich cathodes and even during the electrochemical charge and discharge processes, Ni ions migrate to Li sites. This is because Ni3+ is unstable and prefers to become Ni2+, which has an ionic radius of 0.069 nm, similar to that of Li+ (0.076 nm), allowing for easy migration of Ni ions to Li vacancies and causing cation mixing (Liu et al., 2015; Kim et al., 2021). Cation mixing shortens the distance between the layers, hindering the diffusion of Li ions and reducing the diffusivity of Li. In particular, because of surface defects, Ni on the surface is more unstable and more likely to be transformed into Ni2+, leading to more severe cation mixing at the surface (Lee et al., 2014).
Owing to the occurrence of microcracks as mentioned earlier, Ni-rich cathodes expose new surfaces, resulting in a much higher degree of cation mixing than in other cathodes. This cation-mixing phenomenon increases the activation energy barrier for Li insertion and extraction during the charge and discharge processes, and worsens as cycling progresses, ultimately leading to capacity degradation.
Ni-rich cathodes with relatively low nickel content have been the focus of numerous studies aimed at improving their electrochemical performance. Several strategies have been explored to address the challenges and enhance the longevity and efficiency of these cathodes. One approach is surface coating, which involves coating the surface of the cathode particles with materials such as metal oxides (e.g., Al2O3 (Negi et al., 2020), ZrO2 (Yao et al., 2020), TiO2 (Qin et al., 2016)), or inorganic non-metallic oxides (e.g., SiO2 (Khollari et al., 2019)). This coating helps block direct contact with the electrolyte, inhibits side reactions, and improves surface stability. Coating is effective for mitigating issues related to surface degradation. Doping is another effective technique in which metal elements [e.g., Zr (Schipper et al., 2016), Co (Xu et al., 2020), Al (Dixit et al., 2017)] or non-metallic elements [e.g., B (Gao et al., 2021)] are introduced into the cathode particles. The addition of dopants to Ni-rich cathode materials contributes to stabilizing the crystal structure and suppressing the cation mixing effect, thereby enhancing lithium ion diffusion capability (Kim et al., 2021). Combining coating and doping approaches has proven to be effective in addressing issues such as side reactions and cation mixing, thereby ensuring a long lifespan for NCM cathodes. However, as the Ni content increases, especially in Ni-rich cathodes with Ni content exceeding 80%, the effectiveness of these strategies diminishes. This is particularly evident in the inability of coating and doping to effectively suppress microcrack formation, which becomes a dominant factor affecting performance. In such cases, achieving an appropriate balance between energy density and long-term lifespan is crucial for practical use.
Figure 5 presents schematic diagrams of crack-free single-crystal Ni-rich and polycrystalline materials. As shown, the primary contributing factor to the degradation of polycrystalline materials is microcracking induced by volumetric changes. These microcracks propagate with cycling and extend to the particle surface through grain boundary, resulting in particle fracture and exacerbation of electrolyte sub-reactions. In contrast, single crystals exhibit a monocrystalline structure that effectively prevents the initiation of microcracks, even in the presence of volumetric changes during charge and discharge cycles (Fan et al., 2020; Ni et al., 2022). Consequently, single crystals do not experience the structural issues associated with particle fracture due to sub-reactions. Moreover, their monocrystalline nature provides superior electronic conductivity compared with that of their polycrystalline counterparts, naturally leading to an extended operational lifespan.
FIGURE 5. Schematic diagrams depicting crack-free single-crystal Ni-rich materials compared to polycrystalline materials.
Single crystals, with their distinct characteristics, offer a far-reaching solution compared to secondary particles by fundamentally addressing the issue of particle fracture, resulting in a remarkable enhancement in performance. In a study by Qian et al., a comparison was drawn between single crystals and secondary particles in NCM622 with relatively low Ni content (Figure 6A) (Qian et al., 2020). In stark contrast to secondary particles formed by the aggregation of smaller primary particles, single crystals can be considerably larger. When assessing NCM622, the capacity loss for single crystals (approximately 1–2 μm in size) and polycrystalline structures (approximately 200–500 nm) was found to be 6% and 48%, respectively.
FIGURE 6. (A) Electrochemical characterizations and SEM images of single-crystal and polycrystalline NCM622 (Qian et al., 2020). Copyright 2020, Energy Storage Materials, (B) Schematic illustration of crack evolution and the internal morphological difference for N-NCM and SC-NCM cathodes during prolonged cycling, and cycling performance of N-NCM and SC-NCM electrodes in pouch-type full cells (Fan et al., 2020). Copyright 2020. Nano Energy.
Single crystals devoid of microcracks exhibit limited performance degradation even in the presence of surface degradation factors such as surface reactions. Fan et al. extended the comparison to Ni-rich cathodes with 83% Ni content. In the case of single crystals, the effective suppression of crack formation resulted in an impressive capacity retention of 84.8% after 600 charge–discharge cycles at a 1 C current rate, as shown in Figure 6B. This figure is significantly higher than the 57.4% observed for secondary particles. Consequently, single crystals demonstrate exceptional structural stability, effectively mitigating microcrack formation even in Ni-rich cathodes with high Ni content, making them ideal solutions for high-capacity and long-life applications (Fan et al., 2020). Furthermore, according to Kong et al., the presence of crystal gaps in polycrystalline materials increases inhomogeneity during cycling, resulting in elevated heat generation. This leads to superior performance in single crystals compared to polycrystalline structures. Therefore, single crystals exhibit significantly better thermal stability at high temperatures (Kong et al., 2022).
The absence of cracks in Ni-rich single-crystal cathodes has led to increased research on synthesis methods in recent years. Furthermore, owing to the instability of Ni3+ ions, synthesizing single-crystal Ni-rich cathodes with a high nickel content, such as LiNiO2, is challenging. Consequently, methods with commercial potential, such as solid-state synthesis using precursors and molten salt synthesis, are limited. While there are several other synthesis methods, such as sol–gel (Huang et al., 2011) and spray pyrolysis (Leng et al., 2021), they encounter challenges like complex and immature preparation processes and high synthesis costs, rendering them unsuitable for commercial production. Additionally, methods such as hydrothermal synthesis (Li et al., 2014) have limitations due to the small particle size (<1 µm), and mass production is also challenging. Therefore, in our study, specifically focus on two promising methods: solid-state and melt salt synthesis.
The solid-state synthesis of single-crystal Ni-rich cathodes has become a well-optimized and commercially viable process. As the methodology for producing (NixMnyCoz)(OH)2 precursors (as shown in Figure 2) has matured, these precursor materials have become readily available. The precursor materials, when mixed with lithium sources (LiOH or Li2CO3) and subjected to heat treatment, facilitate the movement of Li ions within the secondary particle precursor at temperatures around 700°C, making it easy to form Ni-rich cathode materials (Deng et al., 2019). However, to form single crystals instead of polycrystals, it is necessary to heat treat the primary particles at a high temperature of around 900°C, allowing them to grow sufficiently into single crystals (Qian et al., 2020).
Simulation calculations of sintering temperature and time for single-crystal growth have shown that sintering time has a minimal effect on particle size, whereas temperature is very important. Sintering below 750°C has negligible impact on crystal growth due to Li diffusion rates. Above 800°C, slight volatilization of Li2O occurs, which promotes mass transport of Li ions. Additionally, grain boundary diffusion starts at temperatures above 800°C, requiring higher temperatures for increasing single crystal size (Langdon and Manthiram, 2021). However, maintaining the temperature above 900°C can lead to excessive Li volatilization, necessitating precise temperature control.
Wang et al. illustrated the mechanism of solid-state synthesis using precursors (Figure 7A) (Wang et al., 2020). Similar to the synthesis of polycrystalline Ni-rich cathodes, the direct synthesis of (NixMnyCoz)(OH)2 precursors with Li sources results in single crystals with sizes of a few hundred nanometers. To achieve electrochemical performance like that of polycrystalline Ni-rich cathodes, the crystals need to be grown to sizes of at least 2–4 µm. Increasing the size of single-crystal particles is not only important with higher heat treatment temperatures but also requires milling. Lattice formation relies primarily on the mobility of oxygen and Li ions. Milling helps achieve a more uniform distribution and reduces the particle size, enhancing the pathways for oxygen and Li-ion transport and significantly accelerating crystal growth.
FIGURE 7. (A) Growth mechanism of solid-state reactions (Wang et al., 2020). Copyright 2020, Frontiers in Chemistry. (B) SEM images of synthesized single crystal NCM 811 (Yang et al., 2020). Copyright 2020, Int. J. Electrochem. Sci. (C) SEM images of synthesized single crystal LiNi0.83Co0.11Mn0.06O2(Fan et al., 2020). Copyright 2020, Nano Energy.
To obtain single crystals through solid-state synthesis, grinding to reduce the particle size and maintaining temperatures in the range of 800°C–900°C is essential. Yang et al. successfully synthesized single crystals in the size range of 1–4 µm through a two-step heat treatment process at 870°C and 830°C after ball milling, as shown in Figure 7B (Yang et al., 2020). Fan et al. also achieved single crystals with particle sizes of 3–5 μm by conducting a 10-h heat treatment at 830 °C (as shown in Figure 7C) (Fan et al., 2020).
These findings highlight the key parameters and steps involved in the solid-state synthesis of single-crystal Ni-rich cathodes, paving the way for enhanced performance in advanced energy storage applications.
The most commonly used sources of Li for an LIB are LiOH and Li2CO3. The choice of source plays a critical role in the synthesis of NCM materials, because Li-ion mobility increases at temperatures above the melting point of the salt. For example, Li et al. demonstrated that by using an excess of Li2CO3 with a Li/TM M ratio of 1.15, the Li-ion concentration could be increased, enabling the synthesis of large NMC622 single crystals, up to 6 μm, at a high temperature (>900°C) (Li et al., 2018). However, for Ni-rich alloys with higher nickel content, cation mixing becomes significant at high temperature, resulting in potential degradation of the electrochemical performance even if the synthesis is successful.
To synthesize high-performance Ni-rich cathodes while minimizing the synthesis temperature, efforts have been made to mix molten salts in appropriate proportions by leveraging eutectic points. For instance, the melting point of LiOH is relatively high at 471°C, and Li2CO3 has a melting point of 723 °C. However, Jiang et al. reported that a 0.24Li2CO3–0.76LiOH system can reduce the melting temperature to 423 °C (Figure 8A) (Jiang et al., 2020). Furthermore, Chen et al. demonstrated that by mixing LiOH and LiCl in a molar ratio of 0.63:0.37, melting could occur at 275°C (Chen Z. et al., 2021). Additionally, Chang et al. found that a 0.38LiOH–0.62LiNO3 system could be melted at 175°C (Figure 8B) (Chang et al., 2009).
FIGURE 8. (A) Phase diagram of LiOH–Li2CO3 (Jiang et al., 2020). Copyright 2020, ACS Sustainable Chemistry and Engineering. (B) Phase diagram of LiOH and LiCl (Chen Z. et al., 2021). Copyright 2020, Frontiers in Energy R.esearch.
Although melt salt synthesis offers the advantage of lowering the synthesis temperature, it introduces impurities because of the use of various salts, necessitating thorough purification processes. Additionally, the excessive use of additional salts to take advantage of the eutectic point can potentially interfere with Li-ion mobility, resulting in smaller crystal size. Molten-salt synthesis has promising advantages; however, it remains a complex process that requires optimization and further research to overcome the challenges and limitations of commercialization.
Ni-rich single-crystal cathodes also undergo surface degradation, resulting in relatively low first-cycle charge/discharge efficiency. The irreversible capacity generated during the initial cycle cannot return to its original value, presenting a significant challenge when transitioning from half-cell evaluations, where there is an unlimited supply of Li, to full-cell applications, where the supply of cathode material is constrained. Therefore, it is imperative to improve the initial Coulombic efficiency.
One reason for a low initial Coulombic efficiency is surface degradation issues such as side reactions and cation mixing during the initial charging process. Ni on the surface becomes unstable and undergoes cation mixing, leading to the formation of byproducts, such as NiO, when reacting with the electrolyte. Hence, surface modifications such as those resulting from the use of additives and coatings are essential for Ni-rich single-crystal cathodes, as in the case of their polycrystalline counterparts. These modifications aim to either block direct contact with the electrolyte or stabilize surface Ni ions, thereby increasing the activation energy for severe cation mixing and improving efficiency.
For instance, the addition of 0.3% 1,2,4-1H-triazole as an effective CEI forming additive improved the first-cycle efficiency of Ni-rich single-crystal cathodes with 90% Ni content from 89.1% to 89.8 (Zou et al., 2021b). Coating the surface of Ni-rich single-crystal cathodes with PMMA and PVDF with 80% Ni content increased the first-cycle efficiency from 83.9% to 84.4% (Han et al., 2020). This effect was attributed to the capture of surface Ni ions, which alleviated surface degradation. Moreover, Zou et al. demonstrated surface modification through the substitution of Ta5+ ions and transition metals via strontium, which alleviated surface degradation. LiNi0.8Co0.1Mn0.1O2, subjected to similar surface modifications, exhibited comparable charge capacity but enhanced discharge capacity (211.2 mAh g−1 at 0.1 C), resulting in a high first-cycle efficiency of 93.8% (Zou et al., 2021a).
Unfortunately, surface modifications, such as Li diffusion imbalance and bulk structure degradation, have limitations in addressing the fundamental issues in Ni-rich single-crystal cathodes. Therefore, the extent of improvement through surface modification remains limited, typically within a few percentage points. Further research and deeper understanding of these mechanisms are required to explore the full potential of this intriguing area.
Generally, single crystals with micron-sized primary particles have slower Li+ diffusion rates than polycrystals due to long Li+ diffusion paths, and single crystals exhibit a persistent Li diffusion imbalance within the particles. These low-rate performance characteristics of single crystals lead to continuous degradation over repeated cycles (Zhong et al., 2020; Ryu et al., 2021). Doping with single crystals addresses this problem by forming strong bonds between the doping elements and oxygen, suppressing the cation mixing effect. This effectively stabilizes the crystal structure and mitigates the internal structural deformation caused by slow Li-ion diffusion.
For instance, in a study by Sim et al., a 0.05 mol% Va-doped single crystal with 84% Ni content exhibited an excellent initial discharge capacity (204.4 mAh g-1) and a capacity retention rate of 88.1% over 80 cycles (Sim et al., 2019). This improvement was attributed to the enhancement of Li-ion kinetics through Va-ion doping. Liu et al. achieved a significant enhancement in the rate capability and lifespan by doping 0.6 mol% B into LiNi0.83Co0.05Mn0.12O2 single crystals (Liu et al., 2021). They formed pouch-type full cells and demonstrated a remarkable capacity retention rate of 91.35% after 500 charge-discharge cycles, a significant improvement compared to the undoped sample (66.95%).
Ou et al., by contrast, co-doped Al and Zr into LiNi0.88Co0.09Mn0.03O2 single crystals (Ou et al., 2022). This co-doping strategy improved rate performance and lifespan, even at low voltages, as well as at high voltages up to 4.6 V. The cells maintained a high capacity of 121.2 mAh g−1 even after 350 cycles at a high discharge rate of 5.0 C. This success can be attributed to the synergy of Al and Zr co-doping, in which Al ions are effectively incorporated into the single-crystal NCM lattice, whereas the less soluble Zr ions tend to aggregate on the external particle surface. This synergy improves Li-ion mobility, alleviating internal deformation, and effectively suppressing Li/Ni cation mixing, even under high-voltage conditions and complete Li depletion.
Attempts to address the Li diffusion imbalance in Ni-rich single crystals through doping are ongoing. They fundamentally enhance Li-ion mobility and ensure crystal structure stability, ultimately leading to an extended lifespan.
This review aims to comprehensively cover various aspects of single-crystal Ni-rich materials, including their significance, synthesis methods, electrochemical characteristics, and strategies for addressing existing issues. Ni-rich materials with a nickel content of 80% or higher have competitive advantages for high-capacity applications, such as electric vehicles. Polycrystalline Ni-rich materials synthesized using co-precipitation methods have several drawbacks including surface instability, intergranular cracks, and cation mixing. Intergranular cracks, which expose new surfaces and exacerbate surface degradation, are particularly detrimental to the lifespan of these materials. In contrast, single crystals are considered to be an effective and fundamental solution because they do not suffer from microcracks.
There are two primary methods for synthesizing single-crystal Ni-rich materials: solid-state synthesis using precursors, and molten salt synthesis. Solid-state synthesis methods have been widely studied because they allow easy access to precursor materials through commercial co-precipitation, making solid-state synthesis approachable. To achieve highly reactive single crystals with sizes in the range of 2–5 μm, thorough grinding of the precursors is necessary, followed by annealing at an appropriate temperature in the range of 800°C–900°C. However, the high synthesis temperature of solid-state methods can exacerbate cation mixing issues. To address this issue, researchers are exploring molten-salt synthesis methods that leverage eutectic points to lower the synthesis temperature. Nevertheless, an additional step for the thorough removal of residual salts is required for molten salt synthesis.
Even in microcrack-free single crystals, surface modification effectively enhances the first charge-discharge efficiency by suppressing surface degradation, similar to the effect observed in polycrystals. However, current improvements in this regard are not dramatic and remain limited to a few percentage points. Single crystals have particle sizes ranging from 1 to 4 μm, and are significantly larger than the several-hundred-nanometer-sized particles in polycrystals. This difference in particle size results in lower Li diffusion rates within the particles, leading to intraparticle Li diffusion imbalances that significantly reduce the lifespan of these materials. To address this issue, many studies have focused on doping to effectively enhance Li diffusion rates, thus improving the overall lifespan of the material.
MH: Writing–original draft. V-CH: Writing–review and editing. JM: Writing–review and editing.
The author(s) declare financial support was received for the research, authorship, and/or publication of this article. This work was supported by the Technology Innovation Program (20010900) funded by the Ministry of Trade, Industry, and Energy (MOTIE, Korea).
The authors declare that the research was conducted in the absence of any commercial or financial relationships that could be construed as a potential conflict of interest.
All claims expressed in this article are solely those of the authors and do not necessarily represent those of their affiliated organizations, or those of the publisher, the editors and the reviewers. Any product that may be evaluated in this article, or claim that may be made by its manufacturer, is not guaranteed or endorsed by the publisher.
Chang, Z., Chen, Z., Wu, F., Yuan, X.-Z., and Wang, H. (2009). The synthesis of Li (Ni1/3Co1/3Mn1/3) O2 using eutectic mixed lithium salt LiNO3–LiOH. Electrochimica acta 54, 6529–6535. doi:10.1016/j.electacta.2009.06.013
Chen, S., Zhang, X., Xia, M., Wei, K., Zhang, L., and Zhang, X., (2021a). Issues and challenges of layered lithium nickel cobalt manganese oxides for lithium-ion batteries. J. Electroanal. Chem. 895, 115412. doi:10.1016/j.jelechem.2021.115412
Chen, Z., Wang, T., Yu, H., Guo, J., Zhong, H., and Hu, C., (2021b). Closed-loop utilization of molten salts in layered material preparation for lithium-ion batteries. Front. Energy Res. 8, 587449. doi:10.3389/fenrg.2020.587449
Deng, S., Xue, L., Li, Y., Lin, Z., Li, W., and Chen, Y., (2019). Structural evolution and formation mechanism of LiNiO2 during high-temperature solid-state synthesis. J. Electrochem. Energy Convers. Storage 16, 31004. doi:10.1115/1.4042552
Dixit, M., Markovsky, B., Aurbach, D., and Major, D. T. (2017). Unraveling the effects of Al doping on the electrochemical properties of LiNi0. 5Co0. 2Mn0. 3O2 using first principles. J. Electrochem. Soc. 164, A6359–A6365. doi:10.1149/2.0561701jes
Fan, X., Hu, G., Zhang, B., Ou, X., Zhang, J., and Zhao, W., (2020). Crack-free single-crystalline Ni-rich layered NCM cathode enable superior cycling performance of lithium-ion batteries. Nano Energy 70, 104450. doi:10.1016/j.nanoen.2020.104450
Gabrisch, H., Yazami, R., and Fultz, B. (2002). The character of dislocations in LiCoO[sub 2]. Electrochem. solid-state Lett. 5, A111. doi:10.1149/1.1472257
Gao, S., Shi, B., Liu, J., Wang, L., Zhou, C., Guo, C., et al. (2021). Boron doping and LiBO2 coating synergistically enhance the high-rate performance of LiNi0. 6Co0. 1Mn0. 3O2 cathode materials. ACS Sustain. Chem. Eng. 9, 5322–5333. doi:10.1021/acssuschemeng.0c09265
Gomez-Martin, A., Reissig, F., Frankenstein, L., Heidbüchel, M., Winter, M., and Placke, T., (2022). Magnesium substitution in Ni-rich NMC layered cathodes for high-energy lithium ion batteries. Adv. Energy Mater. 12, 2103045. doi:10.1002/aenm.202103045
Han, Y., Heng, S., Wang, Y., Qu, Q., and Zheng, H. (2020). Anchoring interfacial nickel cations on single-crystal LiNi0. 8Co0. 1Mn0. 1O2 cathode surface via controllable electron transfer. ACS Energy Lett. 5, 2421–2433. doi:10.1021/acsenergylett.0c01032
Hirooka, M., Sekiya, T., Omomo, Y., Yamada, M., Katayama, H., and Okumura, T., (2020). Improvement of float charge durability for LiCoO2 electrodes under high voltage and storage temperature by suppressing O1-Phase transition. J. Power Sources 463, 228127. doi:10.1016/j.jpowsour.2020.228127
Hua, W., Zhang, J., Zheng, Z., Liu, W., Peng, X., and Guo, X.-D., (2014). Na-doped Ni-rich LiNi 0.5 Co 0.2 Mn 0.3 O 2 cathode material with both high rate capability and high tap density for lithium ion batteries. Dalton Trans. 43, 14824–14832. doi:10.1039/c4dt01611d
Huang, Z.-D., Liu, X.-M., Oh, S.-W., Zhang, B., Ma, P.-C., and Kim, J.-K. (2011). Microscopically porous, interconnected single crystal LiNi 1/3 Co 1/3 Mn 1/3 O 2 cathode material for Lithium ion batteries. J. Mater. Chem. 21, 10777–10784. doi:10.1039/c1jm00059d
Jiang, G., Zhang, Y., Meng, Q., Zhang, Y., Dong, P., Zhang, M., et al. (2020). Direct regeneration of LiNi0. 5Co0. 2Mn0. 3O2 cathode from spent lithium-ion batteries by the molten salts method. Acs Sustain. Chem. Eng. 8, 18138–18147. doi:10.1021/acssuschemeng.0c06514
Jiao, T., Liu, G., Zou, Y., Yang, X., Zhang, X., and Fu, A., (2021). A novel trimethylsilyl 2-(fluorosulfonyl) difluoroacetate additive for stabilizing the Ni-rich LiNi0. 9Co0. 05Mn0. 05O2/electrolyte interface. J. Power Sources 515, 230618. doi:10.1016/j.jpowsour.2021.230618
Kalyani, P., and Kalaiselvi, N. (2005). Various aspects of LiNiO2 chemistry: a review. Sci. Technol. Adv. Mater. 6, 689–703. doi:10.1016/j.stam.2005.06.001
Kebede, A. A., Kalogiannis, T., Van Mierlo, J., and Berecibar, M. (2022). A comprehensive review of stationary energy storage devices for large scale renewable energy sources grid integration. Renew. Sustain. Energy Rev. 159, 112213. doi:10.1016/j.rser.2022.112213
Kim, J.-H., Park, K.-J., Kim, S. J., Yoon, C. S., and Sun, Y.-K. (2019). A method of increasing the energy density of layered Ni-rich Li [Ni 1− 2x Co x Mn x] O 2 cathodes (x= 0.05, 0.1, 0.2). J. Mater. Chem. A 7, 2694–2701. doi:10.1039/c8ta10438g
Kim, S.-B., Kim, H., Park, D.-H., Kim, J.-H., Shin, J.-H., and Jang, J.-S., (2021). Li-ion diffusivity and electrochemical performance of Ni-rich cathode material doped with fluoride ions. J. Power Sources 506, 230219. doi:10.1016/j.jpowsour.2021.230219
Kong, X., Zhang, Y., Li, J., Yang, H., Dai, P., and Zeng, J., (2022). Single-crystal structure helps enhance the thermal performance of Ni-rich layered cathode materials for lithium-ion batteries. Chem. Eng. J. 434, 134638. doi:10.1016/j.cej.2022.134638
Langdon, J., and Manthiram, A. (2021). A perspective on single-crystal layered oxide cathodes for lithium-ion batteries. Energy Storage Mater. 37, 143–160. doi:10.1016/j.ensm.2021.02.003
Lee, J., Urban, A., Li, X., Su, D., Hautier, G., and Ceder, G. (2014). Unlocking the potential of cation-disordered oxides for rechargeable lithium batteries. science 343, 519–522. doi:10.1126/science.1246432
Lee, W., Lee, S., Lee, E., Choi, M., Thangavel, R., and Lee, Y., (2022). Destabilization of the surface structure of Ni-rich layered materials by water-washing process. Energy Storage Mater. 44, 441–451. doi:10.1016/j.ensm.2021.11.006
Leng, J., Wang, J., Peng, W., Tang, Z., Xu, S., and Liu, Y., (2021). Highly-dispersed submicrometer single-crystal nickel-rich layered cathode: spray synthesis and accelerated lithium-ion transport. Small 17, 2006869. doi:10.1002/smll.202006869
Li, H., Li, J., Ma, X., and Dahn, J. R. (2018). Synthesis of single crystal LiNi0. 6Mn0. 2Co0. 2O2with enhanced electrochemical performance for lithium ion batteries. J. Electrochem. Soc. 165, A1038–A1045. doi:10.1149/2.0951805jes
Liu, W., Oh, P., Liu, X., Lee, M., Cho, W., and Chae, S., (2015). Nickel-rich layered lithium transition-metal oxide for high-energy lithium-ion batteries. Angew. Chem. Int. Ed. 54, 4440–4457. doi:10.1002/anie.201409262
Liu, Y., Fan, X., Luo, B., Zhao, Z., Shen, J., and Liu, Z., (2021). Understanding the enhancement effect of boron doping on the electrochemical performance of single-crystalline Ni-rich cathode materials. J. Colloid Interface Sci. 604, 776–784. doi:10.1016/j.jcis.2021.07.027
Natarajan, S., and Aravindan, V. (2018). Burgeoning prospects of spent lithium-ion batteries in multifarious applications. Adv. Energy Mater. 8, 1802303. doi:10.1002/aenm.201802303
Negi, R. S., Culver, S. P., Mazilkin, A., Brezesinski, T., and Elm, M. T. (2020). Enhancing the electrochemical performance of LiNi0. 70Co0. 15Mn0. 15O2 cathodes using a practical solution-based Al2O3 coating. ACS Appl. Mater. Interfaces 12, 31392–31400. doi:10.1021/acsami.0c06484
Ni, L., Zhang, S., Di, A., Deng, W., Zou, G., and Hou, H., (2022). Challenges and strategies towards single-crystalline Ni-rich layered cathodes. Adv. Energy Mater. 12, 2201510. doi:10.1002/aenm.202201510
Ou, X., Liu, T., Zhong, W., Fan, X., Guo, X., and Huang, X., (2022). Enabling high energy lithium metal batteries via single-crystal Ni-rich cathode material co-doping strategy. Nat. Commun. 13, 2319. doi:10.1038/s41467-022-30020-4
Ozawa, K. (1994). Lithium-ion rechargeable batteries with LiCoO2 and carbon electrodes: the LiCoO2/C system. Solid State Ionics 69, 212–221. doi:10.1016/0167-2738(94)90411-1
Park, K., Jung, H., Kuo, L., Kaghazchi, P., Yoon, C. S., and Sun, Y. (2018). Improved cycling stability of Li [Ni0. 90Co0. 05Mn0. 05] O2 through microstructure modification by boron doping for Li-ion batteries. Adv. energy Mater. 8, 1801202. doi:10.1002/aenm.201801202
Pickering, I. J., Maddox, P. J., and Thomas, J. M. (1992). Time-resolved in situ X-ray diffraction studies of a lithium nickel oxide catalyst during the oxidative coupling of methane. Chem. Mater. 4, 994–999. doi:10.1021/cm00023a013
Qian, G., Zhang, Y., Li, L., Zhang, R., Xu, J., and Cheng, Z.,(2020). Single-crystal nickel-rich layered-oxide battery cathode materials: synthesis, electrochemistry, and intra-granular fracture. Energy Storage Mater. 27, 140–149. doi:10.1016/j.ensm.2020.01.027
Qin, C., Cao, J., Chen, J., Dai, G., Wu, T., and Chen, Y., (2016). Improvement of electrochemical performance of nickel rich LiNi 0.6 Co 0.2 Mn 0.2 O 2 cathode active material by ultrathin TiO 2 coating. Dalton Trans. 45, 9669–9675. doi:10.1039/c6dt01764a
Rahman, M. K., and Saito, Y. (2007). Investigation of positive electrodes after cycle testing of high-power Li-ion battery cells: III: an approach to the power fade mechanism using FT-IR-ATR. J. power sources 174, 889–894. doi:10.1016/j.jpowsour.2007.06.222
Razmjoo Khollari, M. A., Paknahad, P., and Ghorbanzadeh, M. (2019). Improvement of the electrochemical performance of a nickel rich LiNi 0.5 Co 0.2 Mn 0.3 O 2 cathode material by reduced graphene oxide/SiO 2 nanoparticle double-layer coating. New J. Chem. 43, 2766–2775. doi:10.1039/c8nj05835k
Robert, R., Bunzli, C., Berg, E. J., and Novák, P. (2015). Activation mechanism of LiNi0. 80Co0. 15Al0. 05O2: surface and bulk operando electrochemical, differential electrochemical mass spectrometry, and X-ray diffraction analyses. Chem. Mater. 27, 526–536. doi:10.1021/cm503833b
Ryu, H.-H., Namkoong, B., Kim, J.-H., Belharouak, I., Yoon, C. S., and Sun, Y.-K. (2021). Capacity fading mechanisms in Ni-rich single-crystal NCM cathodes. ACS Energy Lett. 6, 2726–2734. doi:10.1021/acsenergylett.1c01089
Ryu, H.-H., Park, K.-J., Yoon, C. S., and Sun, Y.-K. (2018). Capacity fading of Ni-rich Li [Ni x Co y Mn1–x–y] O2 (0.6≤ x≤ 0.95) cathodes for high-energy-density lithium-ion batteries: bulk or surface degradation? Chem. Mater. 30, 1155–1163. doi:10.1021/acs.chemmater.7b05269
Schipper, F., Dixit, M., Kovacheva, D., Talianker, M., Haik, O., Grinblat, J., et al. (2016). Stabilizing nickel-rich layered cathode materials by a high-charge cation doping strategy: zirconium-doped LiNi 0.6 Co 0.2 Mn 0.2 O 2. J. Mater. Chem. A 4, 16073–16084. doi:10.1039/c6ta06740a
Sim, S.-J., Lee, S.-H., Jin, B.-S., and Kim, H.-S. (2019). Improving the electrochemical performances using a V-doped Ni-rich NCM cathode. Sci. Rep. 9, 8952. doi:10.1038/s41598-019-45556-7
Sun, Y., Zhang, Z., Li, H., Yang, T., Zhang, H., and Shi, X., (2018). Influence of Ni/Mn distributions on the structure and electrochemical properties of Ni-rich cathode materials. Dalton Trans. 47, 16651–16659. doi:10.1039/c8dt03552k
Tian, F., Fan, X., Wang, Q., Ouyang, X., Wei, H., and Shen, Q. (2020). Influence of dodecyl sulfate anions doped hydroxide precursor on enhanced electrochemical properties of LiNixCoyMn1-x-yO2 as lithium-ion battery cathodes. Int. J. Electrochem. Sci. 15, 10157–10172. doi:10.20964/2020.10.24
Wakihara, M. (2001). Recent developments in lithium ion batteries. Mater. Sci. Eng. R Rep. 33, 109–134. doi:10.1016/s0927-796x(01)00030-4
Wang, J.-Q., Fu, X.-Y., Zhang, L.-L., Ding, X.-K., Liu, J., Li, T., et al. (2019). Enhanced electrochemical performance of graphene supported LiNi1/3Co1/3Mn1/3O2/C hybrid cathode for lithium-ion batteries. J. Electrochem. Soc. 166, A1806. doi:10.1149/2.0411910jes
Wang, T., Ren, K., He, M., Dong, W., Xiao, W., and Pan, H., (2020). Synthesis and manipulation of single-crystalline lithium nickel manganese cobalt oxide cathodes: a review of growth mechanism. Front. Chem. 8, 747. doi:10.3389/fchem.2020.00747
Xu, D., Yang, F., Liu, Z., Zeng, X., Deng, Y., and Zheng, Y., (2020). Effects of Co doping sites on the electrochemical performance of LiNi 0.5 Mn 1.5 O 4 as a cathode material. Ionics 26, 3777–3783. doi:10.1007/s11581-019-03284-y
Xu, X., Huo, H., Jian, J., Wang, L., Zhu, H., and Xu, S., (2019). Radially oriented single-crystal primary nanosheets enable ultrahigh rate and cycling properties of LiNi0. 8Co0. 1Mn0. 1O2 cathode material for lithium-ion batteries. Adv. Energy Mater. 9, 1803963. doi:10.1002/aenm.201803963
Xu, Z., Rahman, M. M., Mu, L., Liu, Y., and Lin, F. (2018). Chemomechanical behaviors of layered cathode materials in alkali metal ion batteries. J. Mater. Chem. A 6, 21859–21884. doi:10.1039/c8ta06875e
Yang, C., Zhu, Z., Wei, W., and Zhou, L. (2020). Superior cycle stability of single crystal nickel-rich layered oxides with micron-scale grain size as cathode material for lithium ion batteries. Int. J. Electrochem. Sci. 15, 5031–5041. doi:10.20964/2020.06.03
Yao, L., Liang, F., Jin, J., Chowdari, B. V. R., Yang, J., and Wen, Z. (2020). Improved electrochemical property of Ni-rich LiNi0. 6Co0. 2Mn0. 2O2 cathode via in-situ ZrO2 coating for high energy density lithium ion batteries. Chem. Eng. J. 389, 124403. doi:10.1016/j.cej.2020.124403
Zhong, Z., Chen, L., Huang, S., Shang, W., Kong, L., and Sun, M., (2020). Single-crystal LiNi0. 5Co0. 2Mn0. 3O2: a high thermal and cycling stable cathodes for lithium-ion batteries. J. Mater. Sci. 55, 2913–2922. doi:10.1007/s10853-019-04133-z
Zou, Y., Mao, H., Meng, X., Du, Y., Sheng, H., and Yu, X., (2021a). Mitigating the kinetic hindrance of single-crystalline Ni-rich cathode via surface gradient penetration of tantalum. Angew. Chem. Int. Ed. 60, 26535–26539. doi:10.1002/anie.202111954
Keywords: single-crystal Ni-rich cathodes, lithium-ion batteries, synthesis methods, enhancement strategies, crack-free
Citation: Hong M, Ho V-C and Mun J (2024) Comprehensive review of single-crystal Ni-rich cathodes: single-crystal synthesis and performance enhancement strategies. Front. Batteries Electrochem. 3:1338069. doi: 10.3389/fbael.2024.1338069
Received: 14 November 2023; Accepted: 31 January 2024;
Published: 23 February 2024.
Edited by:
Xingcheng Xiao, General Motors, United StatesReviewed by:
Xianyang Wu, Argonne National Laboratory (DOE), United StatesCopyright © 2024 Hong, Ho and Mun. This is an open-access article distributed under the terms of the Creative Commons Attribution License (CC BY). The use, distribution or reproduction in other forums is permitted, provided the original author(s) and the copyright owner(s) are credited and that the original publication in this journal is cited, in accordance with accepted academic practice. No use, distribution or reproduction is permitted which does not comply with these terms.
*Correspondence: Junyoung Mun, bXVuanlAc2trdS5lZHU=
Disclaimer: All claims expressed in this article are solely those of the authors and do not necessarily represent those of their affiliated organizations, or those of the publisher, the editors and the reviewers. Any product that may be evaluated in this article or claim that may be made by its manufacturer is not guaranteed or endorsed by the publisher.
Research integrity at Frontiers
Learn more about the work of our research integrity team to safeguard the quality of each article we publish.