- Centre for Energy Technology, School of Mechanical Engineering, The University of Adelaide, Adelaide, SA, Australia
The intermittent nature of solar energy limits its further deployment to applications where firm supply and constant output is required. While energy storage is a viable option to increase solar share, in itself is not sufficient without an additional dispatchable energy source. Combustion of both fossil-based and renewable fuels can provide the demand ready energy source required and lends itself to hybridization with tower based Concentrated Solar Thermal, CST, energy. The Hybrid Solar Receiver Combustor, HSRC, is a novel technology that integrates both sources of energy in one device and offers tangible benefits in increased solar share, thermal efficiency and reduced capital and operation costs. This paper reports a brief review of the different findings from experimental and computational research carried out at the Center for Energy Technology of the University of Adelaide into optimizing the HSRC design, developing the first-of-a-kind laboratory-scale HSRC unit and evaluating its performance under different fuels, operating conditions and modes of operation. It highlights the benefits and need for utilizing MILD combustion in the HSRC to match the heat transfer characteristics and stability required to achieve similar operational range and efficiency from both sources of energy. A 5-kWel xenon-arc solar simulator and the combustion of a wide variety of fuels are used as the energy sources. This paper reports on the effectiveness of MILD combustion under these conditions and in particular it discusses flame stability envelop and its relation to heat extraction, temperature and pollutant emissions. It also reports on thermal efficiency, heat losses and heat flux distribution within the cavity for all fuels and operating conditions. It is found that the HSRC thermal performance is similar under the three operation modes (solar, combustion, and combined) and that operating under MILD combustion mode allowed fuel flexibility, homogeneous heat distribution and very low emission of NOx and CO. Also found that H/C ratio plays a minor role in the radiated energy to the heat exchanger within the cavity. Future research and further technology development need is also discussed in this paper.
Introduction
Concerted effort has been spent on carbon abatement from the energy generation sector over the last two decades. The majority of the investment has targeted the power generation sector as it accounts for more than third of carbon emission (IEA, 2018). Renewable power from wind, solar PV, and hydro have made a tangible impact on carbon emission worldwide. Multiple agencies have predicted that almost all of electricity generation will be carbon neutral by the year 2050, consistent with meeting current commitments to COP21 (http://www.cop21paris.org). However, decarbonizing the power sector alone will not be enough to keep the CO2 level in the atmosphere below 350 ppm to prevent the atmosphere temperature from rising above 2 degrees (https://unfccc.int/process-and-meetings/the-paris-agreement/the-paris-agreement). Hence, beyond electrical energy, the two major energy sectors that should be targeted are the industry and transport sectors (Philibert, 2017). Philibert (2017) notes that electricity makes up to 26% of industry needs and the rest is in the form of thermal energy, almost half of it is at temperatures above 400°C. Similarly, transport is a major contributor to carbon emission, and while electric vehicles are likely to play a role in the light duty transport market, alternative fuels that can utilize existing internal combustion technologies will also be needed. The above highlights the need for generating renewable thermal energy at temperatures above 400°C and the production of alternative renewable fuels to replace fossil fuels.
Concentrating Solar Thermal (CST) technologies are promising avenues to generate high temperature thermal energy as well as alternative fuels, termed solar fuels (Kodama, 2003; Romero and Steinfeld, 2012; Agrafiotis et al., 2014). CST inherent intermittency is incompatible with industry needs of firm dispatchable supply and processes that require constant operating conditions (Jafarian et al., 2013, 2014). Thermal energy storage is one avenue to store heat using molten salts, phase change material or sensible energy storage. Thermal storage in locations of excellent solar resource can double the solar share from 20 to 40% (Nathan et al., 2017, 2018). Nonetheless, storage alone will never be sufficient to guarantee firm supply from a CST system, without solar multiples of more than 50 times, even at the best solar locations (Kueh et al., 2015). This finding highlights the need for the coupling of CST systems with other dispatchable source of energy to guarantee firm supply and constant output. Nathan et al. (2014) proposed the concept of combining CST and combustion as a means to solve this problem. The “hybrid” system capitalizes on CST low CO2 emissions feature and harnesses stored chemical energy in fuels via combustion. This allows to use CST when needed while also encompassing the utilization of a wide range of fuels (including alternative, renewables low-carbon, and/or carbon-free fuels) and technologies able to offer a trade-off between the net cost and the net level of CO2 mitigation.
The Hybrid Solar-Receiver-Combustor (HSRC) concept is a cost-effective and efficient method to utilize combustion to compensate for the variability and intermittency of the solar resource for applications in high-temperature processes (Nathan et al., 2014). Of the possible CST technologies available, the tower system with a large heliostat field and a cavity receiver are the most suitable to achieve the required high temperature and to contain the combustion products and achieve exhaust heat recovery. Cavity receivers trap the radiation via the aperture and reduces re-radiation inherent in tubular and bill-board style receivers (Goswami and Kreith, 2007). This single device concept allows three modes of operation namely; solar-only, combustion-only and a mixed-mode. A sketch of the HSRC concept is shown in Figure 1.
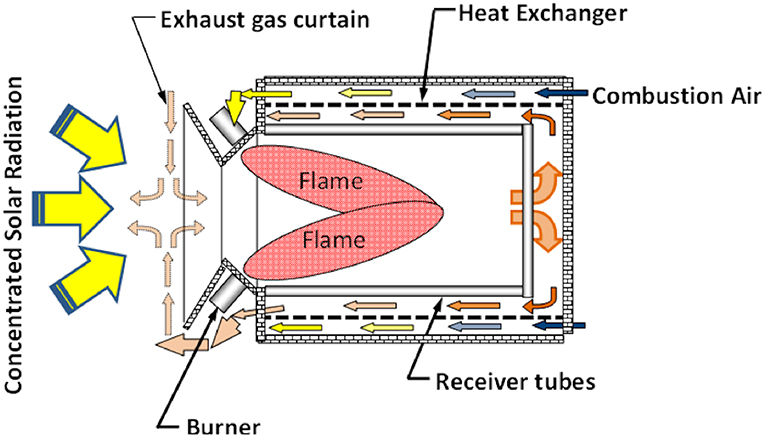
Figure 1. Schematic diagram of the conceptual design of the Hybrid Solar Receiver Combustor, HSRC. Adapted from Lim et al. (2016a).
Lim et al. (2016a,b,c, 2017a,b) have identified an HSRC configuration that achieves similar thermal performance in the combustion-only mode to that of a stand-alone combustor through an efficient use of the sensible heat from the combustion products. They showed that such a system has the potential to lower the capital cost by up to 21%. They also estimated that the HSRC can achieve up to a 19% reduction (depending on the natural gas price) in the levelized cost of electricity relatively to an equivalent cavity receiver with a back-up, stand-alone combustor. This estimate could be low as it only considers, as stated by Nathan et al. (2017), “the first three of the following five potential benefits that were identified by Nathan et al. (2014), as being: (1) reduced heat losses by reducing the total area heat exchange surfaces; (2) avoided start-up and shut-down losses associated with the need to warm-up the combustion system prior to its use; (3) reduced total infrastructure by the need to construct only one device instead of two; (4) increased capacity to manage thermal shock associated with short-term fluctuations in solar resource by using combustion to compensate for any reduction in Concentrating Solar Radiation (CSR); and (5) potential to harvest the solar resource at a lower total flux, owing to the possibility of supplementing the solar resource with combustion”. While a movable shutter can be used to seal the aperture during combustion-only operations, the simultaneous use of both the solar resource and the fuel is needed to harness the potential benefits (4) and (5). This, in turn, results in a combustion process directly-irradiated by CSR. As highlighted by Nathan et al. (2017), “this is a unique combustion regime, given that CSR can readily achieve fluxes some three to five times higher than is found in conventional systems (2–4 MW/m2 compared with the 800 kW/m2 of a gas turbine). The radiation also extends right through the visible spectrum, while irradiation from combustion systems is typically dominated by the infra-red spectrum”. Therefore, new fundamental understandings of these interactions are needed to progress the technology development.
Dong et al. (2016) and Medwell et al. (2011) investigated the influence of CSR on the structure of laminar jet flames and in particular soot propensity. They found that most of the radiation is absorbed by the fuels, ethylene in this case, that peak soot volume fraction increased by up to 250% and that the overall soot volume fraction increased by 55%.
Based on the techno-economics work of Lim et al. (2016a,b,c, 2017a,b), Chinnici et al. conducted multiple studies (Chinnici et al., 2017a,b, 2018a,b,c, 2019a,b) to investigate design concepts of an experimental HSRC system that can work under a variety of fuels, is suitable to hybridization with CSR and achieves equivalent high thermal efficiency for all three modes of operation. Chinnici et al. (2018a) proposed the use of MILD combustion (de Joannon et al., 2012; Evans et al., 2017, 2019) in the cavity due to its stability, fuel flexibility, efficient use of low-carbon and carbon-free, renewable fuels (Derudi et al., 2007; Parente et al., 2008; Ayoub et al., 2012), low emission and enhanced and semi-homogenous heat transfer. This paper provides a review of the different findings from the experimental and computational research into optimizing the HSRC design and evaluating its performance under different fuels and operating conditions.
Methods
This section describes in brief the methods employed by Chinnici et al. (2017a,b, 2018a,b,c, 2019a,b) in the design, development and testing of the first-of-a-kind HSRC unit. A combination of numerical and experimental analyses was performed with the aim to achieve a proof-of-concept of the HSRC technology while also advancing current fundamental understanding of MILD and mixed processes.
Computational Fluid-Dynamic (CFD) was employed both in the initial design optimization of the device (geometry, selection of the most appropriate combustion technology) and to better understand the influence of the two main modes of operation (combustion-only and solar-only) and fuel type on heat transfer, thermal performance and combustion characteristics within the HSRC. To this aim, a 3-D CFD RANS model of a HSRC unit was developed using commercial codes to identify an optimized configuration and to complement the experimental investigation. A Monte-Carlo ray tracing method was used to describe the heat transfer from CSR. The MILD process was modeled using the Eddy Dissipation Concept (EDC) for turbulence-chemistry interactions, simplified and detailed mechanism for the chemistry, and the Discrete Ordinate (DO) approach for the radiation. Additional details of the model set-up and mesh can be found in Chinnici et al. (2017a,b, 2018b). In the design stage, the influence of several geometrical and operating parameters on the performance of the device was assessed to identify an optimized HSRC configuration for further experimental tests. In particular, the influence of the length-to-diameter (L/D) cavity ratio, the shape of the outlet section of the cavity, the annular jet arrangement, the heat exchanger (HX) design, and the type of combustion mode (conventional vs. MILD) were investigated. In a second stage, the CFD model of the optimized HSRC configuration was validated against experimental data and further numerical analysis was carried out to better understand the heat transfer mechanisms within the device.
Based on the initial design optimization, a 20 kW laboratory scale MILD HSRC (Figure 2) was developed, built and tested. All the details of the experimental set-up and rig can be found in Chinnici et al. (2018a), so that only the key features are summarized here. The device retains all the characteristics of conventional tubular solar receivers, i.e., an insulated cavity (with a length-to-diameter cavity ratio, L/D = 3) with an opening to allow CSR into it, and a heat exchanger (HX) carrying out the heat transfer fluid, HTF (air). In addition, the device features a combustor with a unique annular jet arrangement (Long et al., 2017, 2018a,b), which generates an intense recirculation of hot products needed for the establishment of the MILD regime, and a conical outlet section for the exhaust. For solar-only operations, the aperture was open while it was sealed by a conventional swirl burner (used to pre-heat the cavity prior to switch to MILD combustion) for combustion-only and combined modes (Chinnici et al., 2018a). A 5 kWel xenon-arc solar simulator and the combustion of a wide variety of fuels, namely natural gas (NG), liquefied petroleum gas (LPG), hydrogen (H2), and their blends (H2/NG, H2/LPG with different H2%) were used as the energy sources for the three modes. The total power input, Pin, the equivalence ratio, ϕ, and the total HTF flow rate (QHTF) were varied in the range 10–20 kWth, 0.8–1, and 150–1,000 slpm, respectively. Table 1 summarizes all the key operating conditions investigated by Chinnici et al. (2017a,b, 2018a,b,c, 2019a,b).
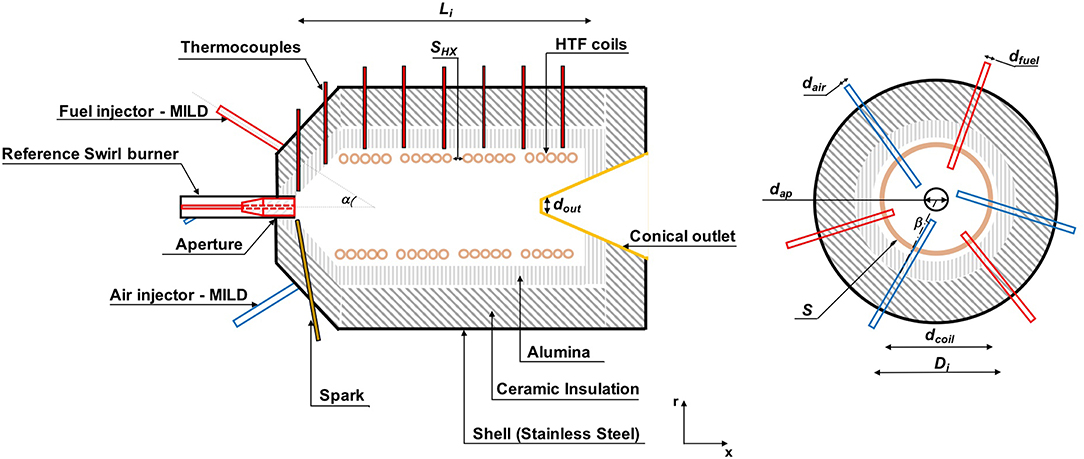
Figure 2. Schematic diagram of the 20-kW laboratory-scale MILD HSRC showing left) a side-view and right) an end-view. Adapted from Chinnici et al. (2018a).

Table 1. Experimental operating conditions for all the modes of operation investigated by Chinnici et al.
The device features a series of N-thermocouples to continuously measure the inner wall cavity temperature, the total heat transfer rate through each section of the HX, the total heat extracted from the HX as well as the total and specific (radiative, convective, conductive) heat losses. A portable gas analyser was also employed to continuously monitor the composition of the exhaust stream. Details of these measurements together with their accuracies and definition of warm-up and steady-state conditions can be found in (Chinnici et al., 2018a).
To assess the performance of the device for each case investigated, Chinnici et al. defined an “absorption efficiency” (ηabs), i.e., the ratio of the heat absorbed by the HX to the total thermal input. To assess the effects of heat recovery on the performance of the device, they also defined a “potential thermal efficiency” (ηth), assuming that 80% of the sensible heat in the exhaust stream is recovered. The energy balance of the system for each mode, together with the details regarding the measurements and calculations of each efficiency and heat loss terms can be found in Chinnici et al. (2018a, 2019b).
Key Research Findings
As discussed in section Methods, the research into the HSRC and its operation involved initial design optimization and experimental testing. This section presents the key findings from the experimental and computational research into optimizing the design and evaluating the HSRC performance under different fuels and operating conditions at laboratory-scale. The experimental rig described in section Methods was used to investigate the effect of mode of operation, fuel type and heat extraction on the stability and thermal performance characteristics of the device.
Computational Analysis
Influence of Geometry and Modes of Operation on Performance
The geometrical parameters are essential for achieving the desired thermal efficiency and operation flexibility of the device. The reasons for this dependency relates to the importance of high rate of recirculation and reactants injection separation to achieve MILD combustion conditions. It also relates to the different heat transfer modes between the solar resource (radiation) and combustion (mostly convection). Ensuring the capture and distribution of solar radiation as well as the enhanced recirculation rate for MILD combustion requires careful selection of the aspect ratio of the diameter and the length of the device.
Figure 3 presents the combined effects of varying the length-to-diameter cavity ratio (L/D, for a fixed D), outlet shape (with and without cone), and mode of operation (MILD, conventional combustion, and solar-only mode) on the calculated thermal performance of the device, employing NG as fuel. Here, Pin was fixed to 12 kW for all cases (with ϕ = 0.9 for combustion operations) and a fixed temperature (Tcoil = 1,000 K) was applied as boundary conditions to the HX. It can be seen that the cavity length strongly influences the performance of the device. In particular, it was found that, for a conical outlet section, relatively long cavities (L/D ≥ 3) are required to achieve similar performance under the different modes while for all the other configurations the values of ηth were predicted to be lower for combustion operations than for the solar-only modes. This because, for combustion-only and mixed operations, the predicted values of the heat losses due to the unrecovered heat from the exhaust are greater than the convective heat losses under solar-only mode. Also, it can be seen that the shape of the outlet section is a key design parameter. In particular, for HSRC geometries with a circular outlet section, a cavity of sufficiently length (L/D > 5) is needed to achieve similar performance under the different modes. This because the use of a conical outlet enhances the recirculation of hot products into the device, which leads to an increase in the convective heat transfer rate. Figure 3 also shows that, for a fixed HSRC geometry, the MILD regime provides a better match with the solar-only mode in terms of performance in comparison with conventional combustion processes.
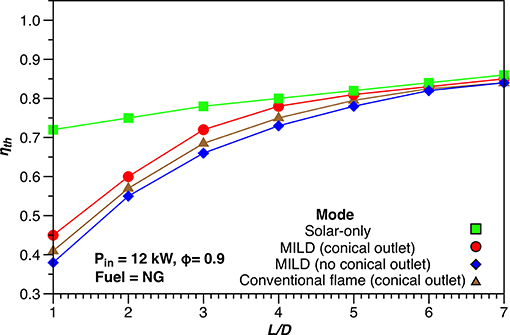
Figure 3. Calculated values of the thermal efficiency, ηth, as a function of the length-to-diameter cavity ratio, L/D, by varying the shape of the outlet section, mode of operation and combustion type (MILD vs. conventional).
Figure 4 presents the influence of the air jets arrangement on the calculated value of the recirculation rate factor, Kv (Chinnici et al., 2017b), for MILD operations and for a fixed value of L/D (L/D = 3) and shape of the outlet section (conical). Here, the azimuthal angle of the air jet, β, was varied while fixing its inclination angle (α = 30°). It can be seen that the design of the annular burner arrangement significantly influences Kv, and hence the recirculation of hot products within the device and the rate of convective heat transfer. In particular, it was found that the maximum peak value of Kv (6.3, which is a value higher than that of conventional MILD burners) was generated for a value of β = 5°. This configuration also features a value of Kv > 3 for more than 35% of the device length. Therefore, this burner configuration was selected for further experimental investigation.
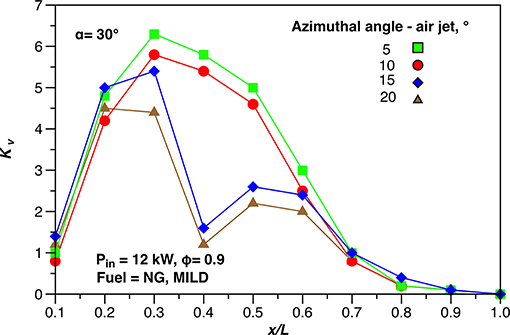
Figure 4. Calculated values of the recirculation rate factor, Kv, along the x-axis of the device, by varying the azimuthal angle (β) of the air jets, and for a fixed value of the air jet inclination angle (α). The case refers to MILD operations (fuel = NG) with L/D = 3 and a conical outlet.
Overall, the numerical analysis of the device indicates that the geometry design and the selection of the combustion regime are critical parameters that need to be taken into account to identify suitable, optimized HSRC configurations for which similar performance can be achieved in the different modes of operation.
Heat Transfer Analysis of MILD and Solar-Only Modes
To further assess how the mode of operation and composition of the fuel influence the dominant heat transfer mechanisms within the device, Table 2 reports the calculated values of the radiative (), convective (), and the total rate of energy absorbed by the HTF pipes, for solar-only operations (Pin = 12 kW, inlet peak flux = 1 MW/m2), and for five fuels (NG, LPG, H2, NG/H2 = 1/1 v/v, and LPG/H2 = 1/1 v/v) under MILD operations (Pin = 12 kW, ϕ = 0.9), for the optimized laboratory-scale HSRC configuration. The calculated values of ηth, mean absorption coefficient, αg, and normalized emissive source term, , are also reported. Here, Tg is the mean gas temperature within the cavity and the subscript r represents reference values (Tr = 298 K and ag, r = 1 m−1). It can be seen that the majority of the energy input is transferred by radiation under solar mode and by a combination of radiation and convection under MILD combustion. For combustion operations, the ratio was found to be >1 for all the cases investigated. For the H2 case, the calculated values of and Re were greater than those of LPG, NG, and fuel blends cases. This because of a higher flame temperature, despite a lower value of αg (Chinnici et al., 2018b). In addition, the NG case features the smallest value of Re (despite αgbeing the lowest) due to the lower adiabatic flame temperature (the emissive power is a function of Tg4). For the NG case, a higher value of was calculated in comparison with the other cases, “owing to a greater inlet air jet momentum, which, in turn, leads to an increase in the recirculation rate” (Chinnici et al., 2018b). Overall, the analysis highlights that, for the geometry and operating conditions investigated, the H/C ratio of the fuel stream plays a minor role in the radiated energy to the heat exchanger within the cavity under MILD operations. This is mainly because the calculated mean equivalent optical length is relatively small (~0.2 m).
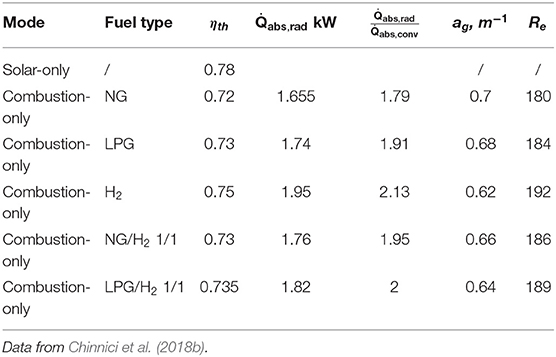
Table 2. Calculated values of the average absorption coefficient, ag, normalized emissive source term, Re, convective and radiative heat transfer rates, and thermal efficiency for all the cases analyzed here (Pin = 12 kW, ϕ = 0.9, boundary conditions HTF coils: Tcoil = 1,000 K).
Experimental Analysis
Influence of Mode of Operation and Fuel Type on Wall Temperature, Heat Flux Distribution, and Pollutants Emissions
Figure 5 presents the axial distribution of the normalized wall temperature (inner layer), Tc/Tc, max, and normalized heat flux through the HTF coils, Q/Qmax, for combustion-only (MILD and conventional combustion), solar-only and mixed mode (MILD and solar simultaneously), for a fixed value of Pin (12 kW for combustion operations), ϕ (0.9) and QHTF (150 slpm), and for the NG case. Here, Qmax and Tc, max are the maximum peak of the heat flux and wall temperature, respectively. It can be seen that the combustion-only and solar-only modes feature two different heat flux distributions, indicating that there is a need to manage the challenges associated with it (e.g., thermal stresses on HTF pipes). Nevertheless, it can also be seen that the MILD regime features a relatively uniform flux, and that this characteristic is also preserved under mixed conditions. That is, the use of a MILD process reduces the risk associated with hot spots within the HSRC for both combustion and combined operations in comparison with conventional combustion processes.
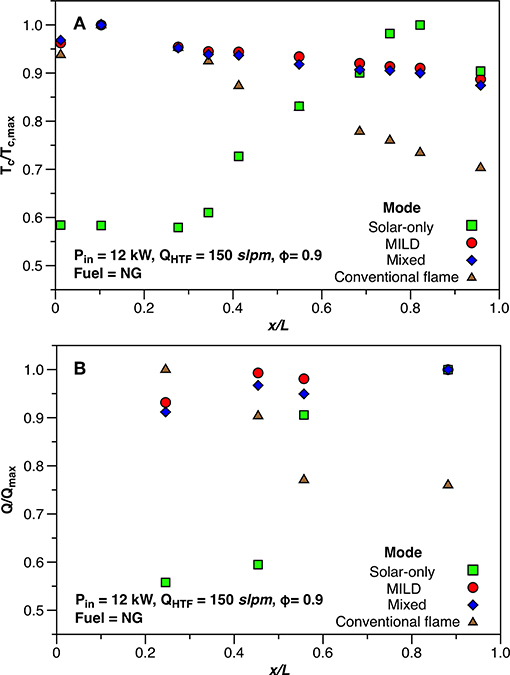
Figure 5. Axial distribution for all modes of operation of (A) the wall cavity temperature normalized by its maximum value, Tc/Tc,max , and (B) heat flux through HTF coils normalized by its maximum value, Q/Qmax. Conditions for combustion operations: Pin = 12 kW, ϕ = 0.9, QHTF = 150 slpm, fuel = NG. Data from Chinnici et al. (2018a,b, 2019b).
Figure 6 presents the measured values of Tc, Q under stable MILD and mixed operations, for a fixed HTF flow rate (QHTF = 150 slpm) and by varying the fuel type (Pin = 12 kW and ϕ = 0.9). It can be seen that, regardless of the composition of the fuel and mode of operation, the cavity features uniform heat flux and temperature distribution. The substitution of NG with LPG or H2 leads to a relatively small increase in the measured values of Tc and Q (of up to 1.5 and 3.5%, respectively). In addition, the simultaneous addition of CSR and MILD combustion into the cavity does not alter the shape of the heat flux and wall cavity temperature. This indicates that the MILD regime of NG, LPG, H2, and their blends can be successfully established and sustained in a cavity collecting heat from multiple energy sources and in fluid/heat communication with the ambient through the aperture. It is worth noting that only a small fraction of ambient air (<10% of the inlet combustion air) was entrained into the device under mixed operations, for all the cases investigated.
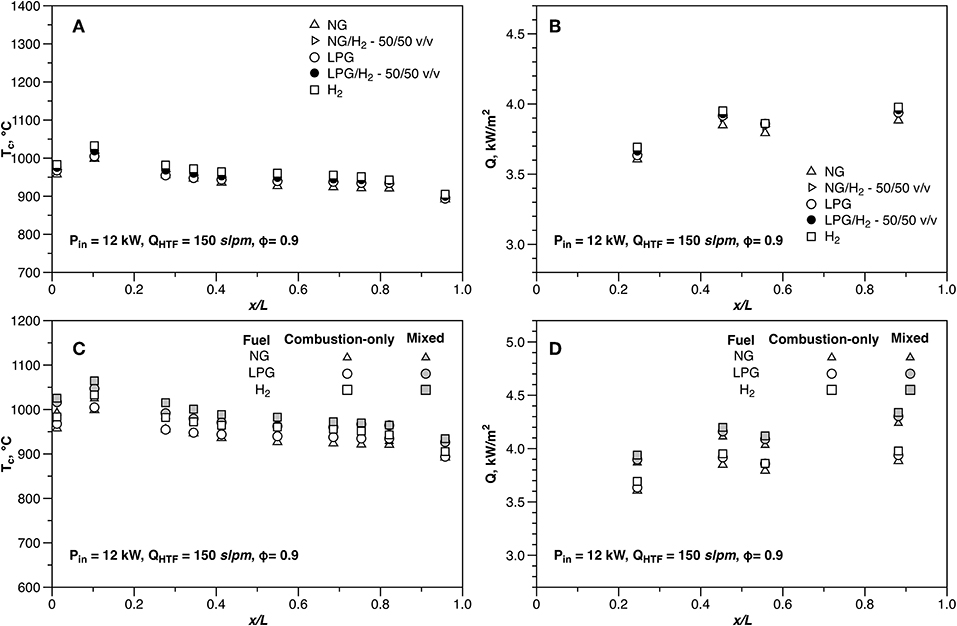
Figure 6. (A,C) Measured axial distribution of the wall cavity temperature, Tc, and (B,D) heat flux through the HTF coils, Q, for the MILD (A,B) and mixed (C,D) modes of operation, as a function of the fuel type, and for a fixed HTF flow rate (150 slpm), thermal input (Pin = 12 kW) and equivalence ratio (ϕ = 0.9). Data from Chinnici et al. (2018a,b); Chinnici et al. (2019a).
Figure 7 shows the influence of the mode of operation (MILD and mixed) and fuel composition on the NOx emissions, for a fixed value of Pin, ϕ, and QHTF (Pin = 12 kW, ϕ = 0.9, QHTF = 150 slpm). It can be seen that for stable MILD operations, ultra-low NOx emissions (<20 ppmv @ 3%O2) were measured for all the cases investigated. It can be seen that a variation in the fuel type only leads to a relatively minor change in the NOx emissions (the maximum NOx variation was ~6 ppmv, obtained by replacing NG with H2). Also, it was found that the NOx emissions exhibit almost a linear dependence on the percentage of H2 in the fuel stream. This trend is consistent with previous works in different MILD burner configurations. In addition, it can be seen that the presence of CSR does not alter the NOx emissions of the MILD process significantly. This further indicates that the fundamental characteristics of the MILD regime are preserved in the mixed mode. It is also worth noting that the CO emissions were <10 ppmv for all cases investigated, indicating that the residence time within the cavity is sufficient to enable complete conversion, and that the maximum recorded NOx value under MILD conditions was ~85% lower than that of conventional combustion (not shown).
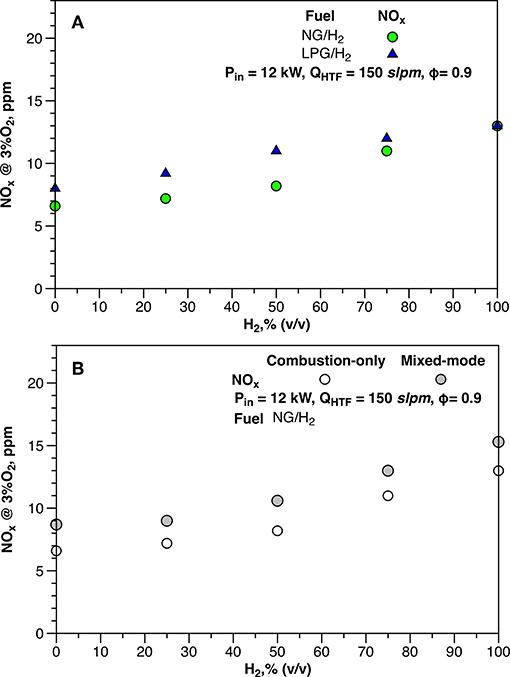
Figure 7. Measured NOx emissions for the MILD (A,B) and mixed (B) modes of operation, as a function of the fuel type, and for a fixed HTF flow rate (150 slpm), thermal input (Pin = 12 kW) and equivalence ratio (ϕ = 0.9). Data from Chinnici et al. (2018a,b); Chinnici et al. (2019a).
Influence of Mode of Operation, Fuel Type, and Heat Extraction on Thermal Performance and Heat Losses
Figure 8 presents the measured values of ηabs and ηth for the different fuels considered here, under MILD and mixed operations (Pin = 12 and 15 kW, ϕ = 0.9), and by varying QHTF. The measured performance for conventional combustion and solar-only operations are also reported for comparison. A comparison of ηth under the different modes highlights that the device can achieve similar performance (up to ~90%) in all modes, with a maximum outlet HTF temperature (Tmax, HTF) >750°C. This despite the energy sources (CSR, chemical energy stored in fuels) collected into the device being different in nature and featuring different heat transfer mechanisms. Also, the values of ηabs are higher for the MILD regime than those of conventional combustion (up to ~5%), and similar to those of the solar-only mode. For mixed operations, a net thermal gain was found in comparison with combustion operations. In particular, despite a slight decrease in ηth (~2%), the specific fuel consumption, i.e., the fuel consumption per unit of useful thermal output to the HTF (Chinnici et al., 2018a), was reduced by up to 20%. It can also be seen that, for MILD operations, the replacement of NG or LPG with H2 leads to an increase in ηabs, of up to ~9%. This difference is attributed to a higher radiative heat transfer rate (due to a higher cavity temperature) rather than the convection term. In fact, for the H2 case, the inlet jet air momentum is ~45% lower than that of LPG and NG, which, in turn, leads to a lower recirculation rate within the cavity (and hence, a lower rate of convective heat transfer).
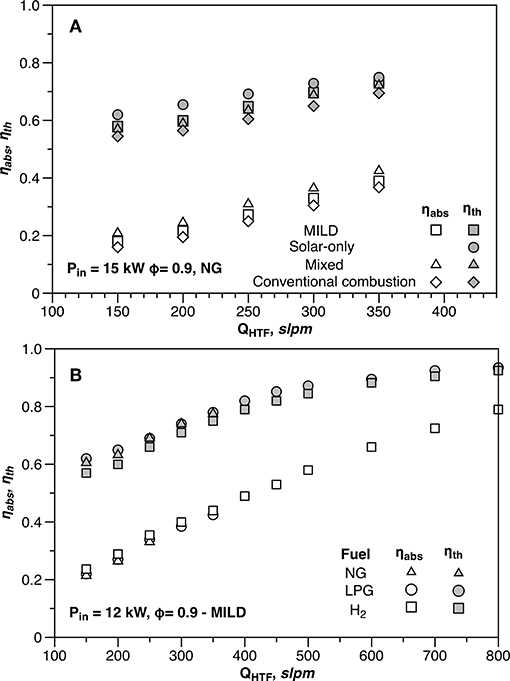
Figure 8. Measured values of absorption (ηabs) and thermal (ηth) efficiencies for (A) the different modes of operation, and (B) the different fuel analyzed under MILD conditions. Data from Chinnici et al. (2018b).
To further assess the influence of the mode of operation on thermal performance, Table 3 reports the values of the total and specific heat losses for the MILD and mixed operations, for the different fuels investigated here (Pin = 12 kW, ϕ = 0.9, QHTF = 150 slpm). The values for the solar-only mode are also reported for comparison. For solar-operations, the convective heat losses represent the main loss, ~45% of the total losses due to the relatively low cavity temperature. For MILD operations, the sensible heat in the exhaust represents the main loss, ~70% of the total losses. For mixed operations, the additional convective and radiative losses are relatively low (~5% of the total losses), which further explains the thermal net gain in comparison with combustion-only operations. Also, the convective term is similar for both MILD and mixed operations, which indicates that only a small amount of ambient air is entrained into the cavity through the aperture under mixed mode (~2.5% of the combustion air), for the geometry analyzed here.
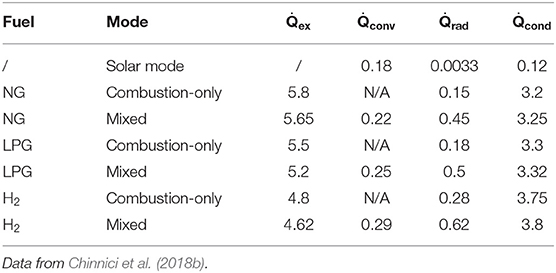
Table 3. Measured values of the heat losses for the different modes of operation and fuel analyzed, conditions for combustion operations: Pin = 12 kW, ϕ = 0.9, QHTF = 150 slpm.
Influence of Mode of Operation, Fuel Type, and Heat Extraction on Stability Characteristics
Figure 9 presents the stability maps (ηabs-H2% domain) for both MILD and MILD-solar processes for all the fuels investigated here, and for different values of the heat extraction (for a fixed value of Pin and ϕ). It can be seen that, regardless of the fuel composition and mode of operation, the stability maps feature three distinctive regions. For low to moderate values of the heat extraction, the MILD process can be successfully stabilized within the HSRC, which features no visible flame, ultra-low NOx (<20 ppmv) and a uniform temperature field. An increase in the heat extracted leads to the occurrence of a dynamic behavior, which features temporal oscillations of species and temperature, appearance of a reddish-colored flame and high CO emissions (up to ~1,000 ppmv). This well-known behavior is attributed to an insufficient amount of enthalpy needed to stabilize the MILD process. A further increase in the heat extracted leads to the conditions Tout < Tself−ign (being Tout and Tself−ign the exhaust temperature and the self-ignition temperature of the mixture, respectively) or τign> τres (being τign and τres the ignition delay time of the mixture and the mean gas residence time within the cavity, respectively), so that the combustion process can no longer be sustained.
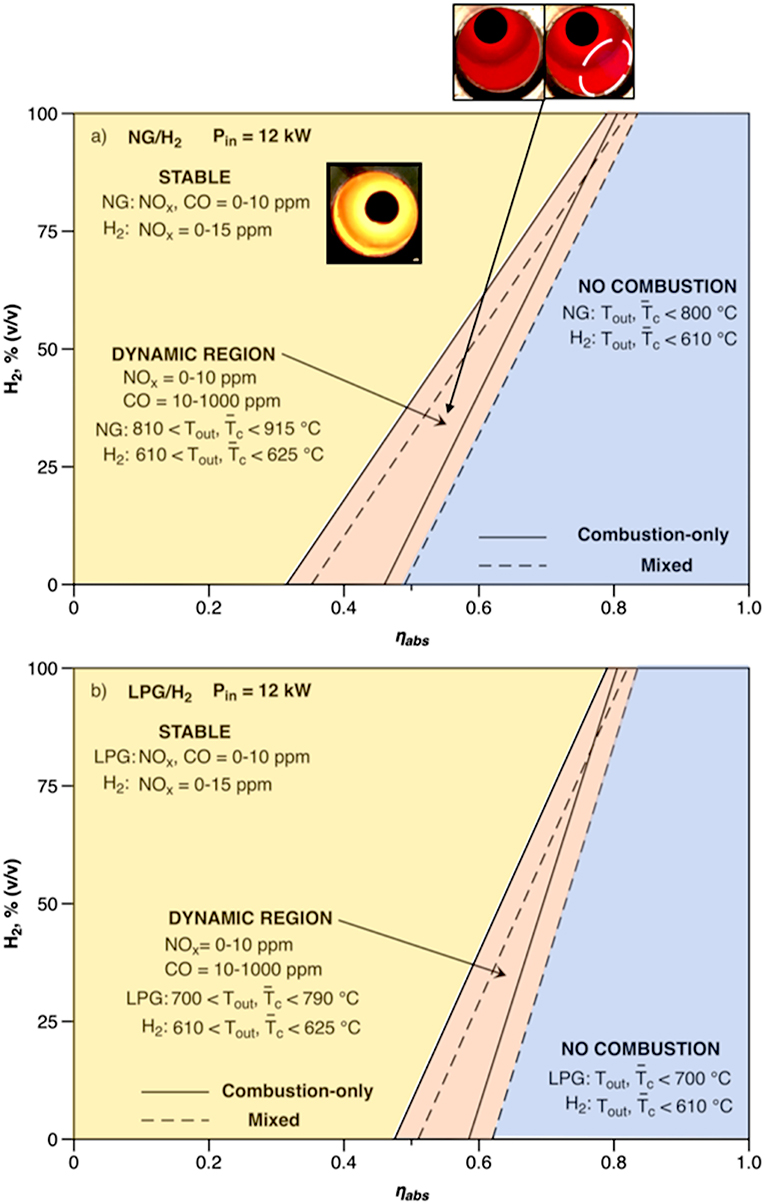
Figure 9. Experimental stability maps for combustion-only and mixed operations, and for (a) NG/H2 and (b) LPG/H2 mixtures (Pin = 12 kW, ϕ = 0.9). The deduced boundaries for each system behavior are based on ~100 data points for each fuel. Typical in-furnace images for stable MILD and dynamic behavior are also reported (photos taken during combustion-only modes with the aperture open prior to switch to mixed operations). Data from Chinnici et al. (2018b).
For both MILD and combined operations, it can be seen that the combustion process can be stabilized in a wider range of conditions by substituting NG with H2 or LPG (the extension of the dynamic region reduces of ~60 and ~20%, respectively, in comparison with the NG case). This is attributed to thermo-kinetic effects rather than thermal only (Chinnici et al., 2018b) since the cavity temperature varied of only ~2% by varying the fuel composition. In addition, it can be seen that either the addition of H2 or CSR to the MILD regime enhances the stability of the combustion process, shifting the instability limits toward lower operating temperatures and reducing the extension of the dynamic region.
Conclusions
The current paper provided a review of the design, development, and testing of the first-of-a-kind Hybrid Solar Receiver Combustor technology, carried out at the Center for Energy Technology of the University of Adelaide. The key findings from the research into the HSRC and its operation are as follows:
- Technology Development: Despite the different nature of the energy sources and their different heat transfer contributions (radiation-dominated for CSR, combination of radiation, and convection for the combustion process), similar thermal performance can be achieved under the different modes of operation, for a wide range of operating conditions and fuel type. The experimental investigation showed that a net thermal gain can be achieved for very low solar fluxes (~6%) under combined mode, with a maximization of solar harness relatively to conventional tubular receiver and ~20% reduction in the specific fuel consumption in comparison with combustion-only operations. This confirms that the economic benefits estimated by previous techno-economic analyses are realistic in terms of LCOE and fuel consumption reduction. The use of MILD combustion for combustion-only and combined operations allows fuel flexibility/switchability, homogeneous heat distribution, very low emission of NOx and CO, and a better heat transfer match with CSR in comparison with conventional combustion processes. Nevertheless, the heat flux distributions for the solar and combustion-only modes of operation are significantly different for the present configuration, indicating that an appropriate design of the combustor and solar concentrating optics is required to minimize these differences and develop suitable control strategies for large-scale applications.
- Fundamental understanding: The main features of the MILD regime (ultra-low NOx, uniform temperature) are preserved in the combined mode (regardless of the fuel composition), despite the addition of CSR to the process and the heat/mass transport into and from the cavity through the aperture. The stability analysis revealed that both MILD and MILD-solar processes can be successfully stabilized in a wide range of heat extraction values. Also, the combustion process can be stabilized in a broader range of operating conditions by either adding CSR or H2 to the MILD regime. Furthermore, it was found that H/C ratio of the fuel stream only play a minor role in the radiated energy to the heat exchanger within the cavity and pollutant emissions.
Future directions
A review of the key findings and current understanding of the influence of CSR on a combustion process also highlighted the need for further research to support the technology development. Particularly, the available experimental data are limited to a very low value of the solar-to-fuel, S/F, ratio (<10%) so that new data are required to assess the performance of the mixed mode at medium to high S/F values (10–50%). Also, all the data were collected under no wind conditions, so that the effects of wind speed and direction on the performance and stability characteristics of the device are presently not available. This is critical as the wind significantly influences the convective heat losses within a solar receiver. Data under well-controlled conditions (wind tunnel) are required to fill in this gap and for model validation. The use of active controls (e.g., sealing gas systems) to mitigate the effects arising from wind should be also investigated prior to scale-up. Measurements under transients loading are also needed to assess the system response in terms of performance and mechanical/thermal stresses. The use of different alternative fuels (e.g., syngas, ammonia) under MILD and mixed operations needs to be investigated to further the understanding of the influence of the fuel composition on performance.
The analysis also showed that a cavity of sufficient length (L/D ≥ 3) is needed to achieve similar performance under the different modes of operation. The calculated difference in the heat transfer rate between MILD and concentrated solar radiation implies that a different combustion technology, featuring higher radiative heat transfer rates, and heat fluxes similar to those of CSR (e.g., infrared radiant burners), may be required for direct hybridization of very short cavities or for solar receiver design different from tubular receivers (e.g., billboard receivers).
Author Contributions
All the authors contributed to the conception and design of the work. In addition, AC performed the experimental and numerical analyses, collected and interpreted the data, and drafted the majority of the paper. BD drafted the introduction of the manuscript and revised the paper. GN provided a critical review of the paper.
Funding
The support of the Australian Research Council and of FCT Combustion and Vast Solar through the ARC Linkage scheme LP110200060 was gratefully acknowledged.
Conflict of Interest
The authors declare that the research was conducted in the absence of any commercial or financial relationships that could be construed as a potential conflict of interest.
Acknowledgments
This work was supported with supercomputing resources provided by the Phoenix HPC service at the University of Adelaide. The authors also acknowledge the use of the Thebarton facilities of the University of Adelaide.
References
Agrafiotis, C., von Storch, H., Roeb, M., and Sattler, C. (2014). Solar thermal reforming of methane feedstocks for hydrogen and syngas production - a review. Renew. Sustain. Energy Rev. 29, 656–682. doi: 10.1016/j.rser.2013.08.050
Ayoub, M., Rottier, C., Carpentier, S., Villermaux, C., Boukhalfa, A. M., and Honore, D. (2012). An experimental study of mild flameless combustion of methane/hydrogen mixtures. Int. J. Hydrogen Energy 37, 6912–6921. doi: 10.1016/j.ijhydene.2012.01.018
Chinnici, A., Nathan, G. J., and Dally, B. B. (2018a). Experimental demonstration of the hybrid solar receiver combustor. Appl. Energy 224, 426–437. doi: 10.1016/j.apenergy.2018.05.021
Chinnici, A., Nathan, G. J., and Dally, B. B. (2018b). Combined solar energy and combustion of hydrogen-based fuels under MILD conditions. Int. J. Hydrogen Energy 43, 20086–20100. doi: 10.1016/j.ijhydene.2018.09.027
Chinnici, A., Nathan, G. J., and Dally, B. B. (2018c). Performance of a hybrid solar receiver combustor. AIP Conf. Proc. 2033:180004. doi: 10.1063/1.5067176
Chinnici, A., Nathan, G. J., and Dally, B. B. (2019a). An experimental study of the stability and performance characteristics of a Hybrid Solar Receiver Combustor operated in the MILD combustion regime. Proc. Combust. Inst. 37, 5687–5695. doi: 10.1016/j.proci.2018.05.099
Chinnici, A., Tian, Z. F., Lim, J. H., Nathan, G. J., and Dally, B. B. (2017a). Comparison of system performance in a hybrid solar receiver combustor operating with MILD and conventional combustion. Part I: Solar-only and combustion-only employing conventional combustion. Solar Energy 147, 489–503. doi: 10.1016/j.solener.2017.02.055
Chinnici, A., Tian, Z. F., Lim, J. H., Nathan, G. J., and Dally, B. B. (2017b). Comparison of system performance in a hybrid solar receiver combustor operating with MILD and conventional combustion. Part II: Effect of the combustion mode. Solar Energy 147, 479–488. doi: 10.1016/j.solener.2017.02.054
Chinnici, A., Tian, Z. F., Lim, J. H., Nathan, G. J., and Dally, B. B. (2019b). Thermal performance analysis of a syngas-fuelled hybrid solar receiver combustor operated in the MILD combustion regime. Combust. Sci. Technol. 191, 2–17. doi: 10.1080/00102202.2018.1452381
de Joannon, M., Chinnici, A., Sabia, P., and Ragucci, R. (2012). Optimal post-combustion conditions for the purification of CO2-rich exhaust streams from non-condensable reactive species. Chem. Eng. J. 211–212, 318–326. doi: 10.1016/j.cej.2012.09.053
Derudi, M., Villani, A., and Rota, R. (2007). Sustainability of mild combustion of hydrogen-containing hybrid fuels. Proc. Combust. Inst. 31, 3393–3400. doi: 10.1016/j.proci.2006.08.107
Dong, X., Sun, Z., Gu, D., Ashman, P. J., Alwahabi, Z. T., Dally, B. B., et al. (2016). The influence of high flux broadband irradiation on soot concentration and temperature of a sooty flame. Combust. Flame 171, 103–111. doi: 10.1016/j.combustflame.2016.05.026
Evans, M. J., Chinnici, A., Medwell, P. R., and Ye, J. (2017). Ignition features of methane and ethylene fuel-blends in hot and diluted coflows. Fuel 203, 279–289. doi: 10.1016/j.fuel.2017.04.113
Evans, M. J., Medwell, P. R., Sun, Z., Chinnici, A., Ye, J., Chan, Q. N., et al. (2019). Downstream evolution of n-heptane/toluene flames in hot and vitiated coflows. Combust. Flame 202, 78–89. doi: 10.1016/j.combustflame.2019.01.008
Goswami, D. Y., and Kreith, F. (2007). Handbook of Energy Efficiency and Renewable Energy. Boca Raton, FL: CRC Press.
IEA (2018). Global Energy & CO2 Status Report. The Latest Trends in Energy and Emissions 2018. IEA Report.
Jafarian, M., Arjomandi, M., and Nathan, G. J. (2013). A hybrid solar and chemical looping combustion system for solar thermal energy storage. Appl. Energy 103, 671–678. doi: 10.1016/j.apenergy.2012.10.033
Jafarian, M., Arjomandi, M., and Nathan, G. J. (2014). The energetic performance of a novel hybrid solar thermal & chemical looping combustion plant. Appl. Energy 132, 74–85. doi: 10.1016/j.apenergy.2014.06.052
Kodama, T. (2003). High-temperature solar chemistry for converting solar heat to chemical fuels. Prog. Energy Combus. Sci. 29, 567–597. doi: 10.1016/S0360-1285(03)00059-5
Kueh, K., Nathan, G. J., and Saw, W. (2015). Storage capacities required for a solar thermal plant to avoid unscheduled reductions in output. Solar Energy 118, 209–221. doi: 10.1016/j.solener.2015.04.040
Lim, J. H., Chinnici, A., Dally, B., and Nathan, G. (2017a). Assessing the techno-economics of modular hybrid solar thermal systems. AIP Conf. Proc. 1850:110007. doi: 10.1063/1.4984481
Lim, J. H., Chinnici, A., Dally, B. B., and Nathan, G. J. (2016a). Assessment of the potential benefits and constraints of a hybrid solar receiver and combustor operated in the MILD combustion regime. Energy 116, 735–745. doi: 10.1016/j.energy.2016.10.017
Lim, J. H., Dally, B. B., Chinnici, A., and Nathan, G. J. (2017b). Techno-economic evaluation of modular hybrid concentrating solar power systems. Energy 129, 158–170. doi: 10.1016/j.energy.2017.04.067
Lim, J. H., Nathan, G., Dally, B., and Chinnici, A. (2016c). Techno-economic assessment of a hybrid solar receiver and combustor. AIP Conf. Proc. 1734:070020. doi: 10.1063/1.4949167
Lim, J. H., Nathan, G. J., Hu, E., and Dally, B. B. (2016b). Analytical assessment of a novel hybrid solar tubular receiver and combustor. Appl. Energy 162, 298–307. doi: 10.1016/j.apenergy.2015.10.048
Long, S., Lau, T. C. W., Chinnici, A., Tian, Z. F., Dally, B. B., and Nathan, G. J. (2017). Experimental and numerical investigation of the iso-thermal flow characteristics within a cylindrical chamber with multiple planar-symmetric impinging jets. Phys Fluids 29:105111. doi: 10.1063/1.4986132
Long, S., Lau, T. C. W., Chinnici, A., Tian, Z. F., Dally, B. B., and Nathan, G. J. (2018a). Iso-thermal flow characteristics of rotationally symmetric jets generating a swirl within a cylindrical chamber. Phys Fluids 30:055110. doi: 10.1063/1.5026719
Long, S., Lau, T. C. W., Chinnici, A., Tian, Z. F., Dally, B. B., and Nathan, G. J. (2018b). The influence of aspect ratio on the iso-thermal flow characteristics of multiple confined jets. Phys Fluids 30:125108. doi: 10.1063/1.5063500
Medwell, P. R., Nathan, G. J., Chan, Q. N., Alwahabi, Z. T., and Dally, B. B. (2011). The influence on the soot distribution within a laminar flame of radiation at fluxes of relevance to concentrated solar radiation. Combust. Flame 158, 1814–1821. doi: 10.1016/j.combustflame.2011.01.006
Nathan, G. J., Battye, D. L., and Ashman, P. J. (2014). Economic evaluation of a novel fuel-saver hybrid combining a solar receiver with a combustor for a solar power tower. Appl. Energy 113, 1235–1243. doi: 10.1016/j.apenergy.2013.08.079
Nathan, G. J., Dally, B. B., Alwahabi, Z. T., Van Eyk, P. J., Jafarian, M., and Ashman, P. J. (2017). Research challenges in combustion and gasification arising from emerging technologies employing directly irradiated concentrating solar thermal radiation. Proc. Combus. Inst. 36, 2055–2074. doi: 10.1016/j.proci.2016.07.044
Nathan, G. J., Jafarian, M., Dally, B. B., Saw, W. L., Ashman, P. J., Hu, E., et al. (2018). Solar thermal hybrids for combustion power plant: a growing opportunity. Prog. Energy Combust. Sci. 64, 4–28. doi: 10.1016/j.pecs.2017.08.002
Parente, A., Galletti, C., and Tognotti, L. (2008). Effect of the combustion model and kinetic mechanism on the MILD combustion in an industrial burner fed with hydrogen enriched fuels. Int. J. Hydrogen Energy 33, 7553–7564. doi: 10.1016/j.ijhydene.2008.09.058
Philibert, C. (2017). Renewable Energy for Industry: From Green Energy to Green Materials and Fuels. IEA Report.
Keywords: hybrid systems, MILD combustion, concentrated solar energy, hydrogen, heat transfer
Citation: Chinnici A, Nathan GJ and Dally BB (2019) Hybrid Solar-MILD Combustion for Renewable Energy Generation. Front. Mech. Eng. 5:61. doi: 10.3389/fmech.2019.00061
Received: 29 April 2019; Accepted: 03 October 2019;
Published: 22 October 2019.
Edited by:
Alessandro Parente, Université Libre de Bruxelles, BelgiumReviewed by:
Mário Costa, Instituto Superior Técnico, Universidade de Lisboa, PortugalSudarshan Kumar, Indian Institute of Technology Bombay, India
Copyright © 2019 Chinnici, Nathan and Dally. This is an open-access article distributed under the terms of the Creative Commons Attribution License (CC BY). The use, distribution or reproduction in other forums is permitted, provided the original author(s) and the copyright owner(s) are credited and that the original publication in this journal is cited, in accordance with accepted academic practice. No use, distribution or reproduction is permitted which does not comply with these terms.
*Correspondence: Alfonso Chinnici, YWxmb25zby5jaGlubmljaUBhZGVsYWlkZS5lZHUuYXU=