- 1Graduate School of Science and Engineering, Yamagata University, Yamagata, Japan
- 2otuA Inc., Tokyo, Japan
- 3Innovation Center for Organic Electronics (INOEL), Yamagata University, Yamagata, Japan
Soft-matter robotics, which is named for robots made from soft materials, will possibly conquer the limit of conventional rigid body dynamics of hard robots made from hard materials. For example, a snake-like robot, of which body is made from soft materials, will walk in various environments including narrow spaces like drain pipes with complicated structure. Here we developed a walking robot with the friction control of double-network hydrogel (DN gel) on its feet, as the first model based on the concept of the soft-matter robotics. It is found that with appropriate control of the friction of DN gel, the inchworm walking robot has realized its high velocity for pipe inspection. We discussed the physical principle of the walking motion of the inchworm search robot and its actual mechanism to provide thrust for its walking motion.
Introduction
The conventional robots are mainly composed of hard materials such as metals and plastics based on rigid body dynamics. However, such conventional robots have a possibility to hurt humans and other animals incidentally. For this reason, various types of soft robots are being developed to realize intrinsic safety against living creatures. For instance, the Whitesides research group developed the soft robots made with soft elastomeric polymers (Shepherd et al., 2011; Morin et al., 2012). In other case, amoeba-inspired robot was also developed (Umedachi et al., 2015). Also, there are a few studies utilizing material science of soft matters such as colloid, surfactant, and polymer hydrogels for the same purpose.
Polymer hydrogel is one of the representative soft matter and has been widely studied for many years. Hydrogel is commonly composed of three-dimensional polymer network and a lot of water (~90 wt%). So far, various types of tough hydrogels have been developed. For example, slide ring crosslinked (Okumura and Ito, 2001) and nanocomposite (Haraguchi and Takehisa, 2002) types. Such tough hydrogels are expected to be applied to various fields such as medical field and soft robotics.
Double-network hydrogel (DN gel) is one of the famous tough hydrogels (Gong et al., 2003) and is also expected to be applied to soft robotics. DN gel is a kind of inter-penetrating polymer gels and is composed of two different polymer networks: The first one is rigid and brittle and the second one is soft and highly ductile. To utilize the toughness of DN gel for various mechanical parts, many studies of gel friction have been carried out and reported (Gong et al., 1997, 1999; Gong and Osada, 1998; Gong, 2006; Kosukegawa et al., 2013; Ren et al., 2015; Mizukami et al., 2018). Furthermore, the technique of friction control method on hydrogels using electric field was developed (Wada et al., 2018). However, robots developed by utilizing such techniques have not been reported yet.
As the other practical background of this research, there are many old buildings without any remaining drawing data that was made more than 50 years ago in Japan. These old buildings need maintenance, but for that purpose, we must get the three-dimensional data of inner structure like drain pipes of the buildings. For this reason, the pipe inspection robots with various mechanisms have been developed nowadays.
At Yamagata University in Japan, many professors are working together to realize the novel research field of “Soft-matter robotics” that provides new soft materials to manufacture various soft robots that can conquer the limit of ordinary rigid body dynamics and solve difficult problems in present society. As one of those real soft-matter robots, the mobile search robot, that can provide thrust with extending and shrinking motions of its multiple segments by using embedded prismatic actuators like an inchworm, has been studied and developed. This robot is designed to realize the automated inspection in narrow spaces like drain pipes in commercial buildings to search the damaged parts of the pipes that should be fixed by human workers. For this purpose, at first, the inspection robots with ordinary wheels have been developed in other research groups (Hirose et al., 1999; Kakogawa et al., 2017), but their sizes were not small enough to inspect inside of the water supply pipes with the diameters of <18 mm in Japan. In another previous research, inspection robots with soft cilia have been developed (Isaki et al., 2006; Wang and Gu, 2008). These robots also have vibrator like a small motor with biased weight on its rotating output axis to utilize the elasticity of cilia for the thrust of the robot. However, these robots can't be considered as the real soft-matter robots because they have rigid parts like motors and metallic weight and gears, which make them difficult to miniaturize because of these rigid parts. So we have been trying to realize effective peristaltic motion of the inspection robot without conventional power transmission mechanisms like wheels, crawlers and legs for small enough inspection robots. The peristaltic motion with pneumatic actuators by using air pressure has been utilized also for pipe inspection robots in a previous research (Kishi et al., 2013; Robertson and Paik, 2017). However, the diameter of the pipe was still limited up to 1-inch or more in these former studies. Therefore, we have been trying to develop a pipe inspection robot whose segments are activated with flexible linear actuators like fishing lines or other organic actuators with biocompatibility. The mechanism of the prototype of the walking robot to confirm the physical principle of the thrust is introduced in this paper.
The walking robot's ability to move with adequate control of the friction of the DN gel on the bottom of its feet and the linear motions of the ball screws that are activated by DC motors are examined with running experiments by using this first prototype.
In this paper, we introduce the specifications of the first prototype of the walking robot utilizing the friction control technique of hydrogel, which is composed of polymer network and water and results of its fundamental running experiments. The materialistic features of the DN gel and its manufacturing process are also explained. To the best of our knowledge, this is the first report of inchworm walking robot possessing DN gel feet utilizing electric control technique of the frictional resistance of DN gel.
Properties of DN Gel
Preparation Procedure
The polymer hydrogel is composed of three-dimensional and crosslinked polymer network and water. The mesh size of polymer network is several nanometers and the water content ratio is usually ~90 wt%. Here, we show the preparation method of DN gels, one of the famous tough gels.
We prepared DN gel samples utilizing a method shown in the previous studies (Wada et al., 2018; Yoshida et al., 2018). First, we dissolved a 2-acrylamideo-2-methylpropanesulfonic acid sodium salt aqueous solution (NaAMPS, Sigma-Aldrich Co. LLC. St. Louis, Missouri, USA, 50 wt%) monomer, a N, N'-methylenebisacrylamide (MBAA, Wako Pure Chemical Industries, Ltd. Osaka, Japan) crosslinker and a 2-Oxoglutaric Acid (α-keto, Wako Pure Chemical Industries, Ltd. Osaka, Japan) photo-initiator in deionized pure water by stirring for 30 min. The concentration of the NaAMPS monomer, MBAA crosslinker and α-keto initiator was 22.9, 0.2, 0.1 wt%, respectively. The molar ratio between monomer, crosslinker and initiator was NaAMPS:MBAA:a-keto = 1:0.02:0.01. Furthermore, the pre-gel solution was sandwiched by two glass plates with 2.6 mm spacing and was then exposed to ultraviolet (UV) light using a LED light source at room temperature for 20 min to synthesize the first polymer network (first gel). Supplementary Figure 1 shows the spectrum of UV light source, obtained using a spectrometer ezSpectra 815V (Oaktree-lab., Yamanashi, Japan) and the power of UV light at stage is 10 mW/cm2, measured using a light power meter LabMax (Coherent, Inc., Santa Clara, California, USA). The size of first gel was 75 × 75 × 2.6 mm.
The first gel was swollen in a second pre-gel solution for 1 day. The second pre-gel solution contained N, N-Dimethylacrylamide (DMAAm, Tokyo Chemical Industry Co., Ltd. Tokyo, Japan, 20.5 wt%) monomer, MBAA (<0.1 wt%), and α-keto (<0.1 wt%). The molar ratio between monomer, crosslinker, and initiator was DMAAm:MBAA:a-keto = 1:2 × 10−4:1 × 10−3. The second gel was polymerized by UV exposure for 2 h. The first gel was cut to remove part of the polymerization residue. Finally, prepared DN gel was swollen by pure water and the lengths of one side of first gel were changed into 2.5-times longer than the first gel. For robot feet, we cut the DN gel into 28 × 18 × 10 mm.
Here, we introduce approximate cost of gel feet parts. In terms of mixing ratio of materials, the cost of monomers is dominant in polymer network. Ten grams of NaAMPS aqueous solution and 25 g of DMAAm are required for DN gel preparation before cutting into small size. The prices of NaAMPS solution and DMAAm are 100 USD/L and 55 USD/500 g, respectively. Ten grams of NaAMPS solution corresponds to 1 USD while 25 g of DMAAm corresponds to 3 USD. Furthermore, approximately 0.16 USD is required for two DN gel foot since we cut into 28 × 18 × 10 mm. In addition, 90 wt% water is required for DN gel (Gong et al., 2003).
Mechanism of the Friction Change of DN Gel by Applying Electric Field
We previously discussed the friction change mechanism of DN gel and its mechanism was reported in the previous paper in detail (Wada et al., 2018). There are protons (H+) in the solution inside the gel, and such protons are moved to the cathode side by adding the voltage. The movement of protons induces the osmotic unbalance between anode and cathode sides, hence, water molecules are also moved to cathode side. The water molecules form lubricant layer between polymer network and cathode electrode and then reduce the frictional coefficient of the DN gel from 0.04 to 0.07 to about 0.02. It means that the friction will decrease about 2–3 times smaller by electric field with several voltages. Figure 1 shows the schematic illustration of the friction change mechanism of DN gel, induced by electric field.
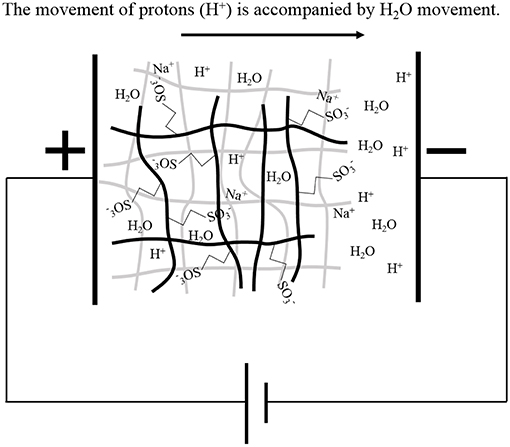
Figure 1. Schematic illustration of friction change mechanism of DN gel. Protons are moved to the cathode side by adding the voltage.
The Walking Robot With DN Gel
Figure 2 shows the concept image of the pipe inspection robot. In this study, we have developed the first prototype of this inspection robot. The information of the inspection robot with DN gel is shown below in detail.
The Mechanism of the Walking Robot
The first prototype of the inchworm search robot to test its fundamental physical principles is composed of two ball screws and two DC motors that extend and shrink its body. The rectangle feet of the robot has DN gel on their bottoms and the friction of the DN gel is controlled with current. The front view, the top view, the side view, and the oblique view of the inchworm search robot are shown in Figure 3. The mechanical structure of the inchworm search robot is shown in Figure 4. The specifications of the robot are shown in Table 1. Even though most of the mechanical elements of the present prototype are still rigid, we will replace them with soft actuators and soft structures in the next phase of this research.
Here, we show approximate cost of this prototype robot. Two leg parts were made of Form 2 (3D printer) resin, and 2 USD was required for this material. The prices of structures to hold DN gel on the leg, guiderails, and motorholders were 1, 5, and 3 USD, respectively. The total cost of main body was 11 USD. In addition, the prices of motors, coupling parts, screws, bolts, and nuts were 50, 26, 616, 9, and 8 USD, respectively. The total cost of these small parts was 700 USD. Also 90 USD were required for obtaining control circuit (Arduino mega) and 1 USD was required for conductive tape. The total cost of this prototype was approximately 800 USD.
Motion of the Walking Robot
The sequential pictures of the walking motion of the inchworm search robot captured from video are shown in Figure 5 (also the Supplementary Movie 1 shows the actual motion of the inchworm search robot.) In these serial pictures, the robot moves toward left direction. In the first picture, the front DN gel under the front foot of the robot is activated with electric current from the anode above it. Because of this electric current, the friction of the DN gel reduces because of the water emerges from its inside, and the front foot moves forward smoothly as shown in the second picture of Figure 5. In this phase, the two legs open with the motions of the two ball screws with the clockwise rotations of the front and rear motors.
After that, the anode on the rear DN gel makes the current flow inside of the rear DN gel and its friction reduces because of the water emerges inside of the rear DN gel. With this small friction, the rear foot can move forward smoothly as shown in the third picture of Figure 5. In this phase, the two legs close with the motions of the two ball screws with the counterclockwise rotations of the front and rear motors.
The gait diagram of the walking motion of the inchworm search robot for one step of its walking motion is shown in Figure 6. The one step of the walking robot takes 40 s. In the first 18 s, the front DN gel is activated and its friction reduces. So, by opening the legs with clockwise rotations of the front and the rear motors, front foot moves forward as shown in the second picture of Figure 5. After that, the rear DN gel is activated for 18 s and reduced the friction of the rear foot. So, by closing the legs with counterclockwise rotations of the front and the rear motors, rear foot moves forward as shown in the third picture of Figure 5. By repeating this peristaltic motion with changing friction of DN gel, the inchworm search robot can continue moving forward.
The running experiments to confirm the effect of the control of friction of DN gel in peristaltic motion of the inchworm search robot were conducted according to this gait diagram with the first prototype. The result of these running experiments were shown in Figure 7. In this figure, the bar shows the moving distance of the walking robot with its three steps and the average value of the moving distance in five times of experiments is plotted as the height of the bar. Three steps of the walking robot means three cycles of the gait diagram shown in Figure 6 and it takes 120 s. The error bar also shows the standard deviation of five experimental values.
In this bar graph, “With current for forward motion” means the condition to activate the two legs and DN gel blocks according to the gait diagram of Figure 6 to move the robot anterior direction that is the same direction as “target direction (left)” of Figure 5.
“Without current” of Figure 7 means the condition to activate only two legs without any current for DN gel. So in this condition, the friction of DN gel blocks was not controlled and there was not any difference between the supporting leg and the moving leg of the robot. So the robot moved only 3.6 mm in average to anterior direction.
“With current for backward motion” of Figure 7 means the condition to activate the two legs and DN gel blocks in the opposite way of the gait diagram of Figure 6. Namely, the current flows inside of DN gel blocks in the opposite timing of Figure 6, so the robot moves backward. This posterior direction is right side of Figure 5 that is opposite to “target direction.”
As shown in the bar graph of Figure 7, with the control of the friction of DN gel blocks on the bottoms of the two legs, the velocity of the robot increased with the steady peristaltic motion. Without current to control the friction of DN gel, the velocity of the robot is quite small and in t-test, there were significant differences between the moving distance of three steps under the condition of “With current for forward motion” and the one under the condition of “Without current.” The moving distances under the condition of “With current for backward motion” and the one under the condition of “Without current” also have significant difference in t-test. So the physical benefit of the control of friction of DN gel to increase the velocity of the walking robot was confirmed quantitatively.
In the t-test of between the moving distance of three steps under the condition of “With current forward motion” and the one under the condition of “With current for backward motion,” there was not any significant difference. This is because of the symmetric structure of the first prototype of the inchworm search robot utilizing electric control technique of DN gel. This result also proved that the repeatability of the moving principle of peristaltic motion of the walking robot in any directions.
The uncertainty analysis of the results of running experiments of the robot with or without current for DN gel was conducted as shown in Table 2.
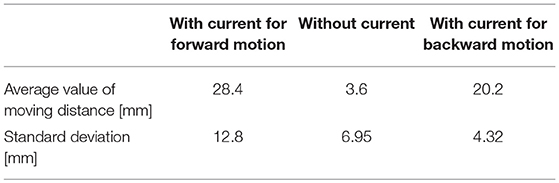
Table 2. The uncertainty analysis of the results of running experiments of the robot with or without current for DN gel.
Schematic Diagram of the Control Circuit
The schematic diagram of the control circuit of the inchworm search robot is shown in Figure 8. The Arduino Mega 2560 microcontroller and DC12V power supply are deployed outside of the body of the gel slider walking robot as shown in Figure 8. The mechanism of the gel slider walking robot is composed of DC geared motor and 2 feet activated by two ball screws. On the foot of the robot, an electric anode is deployed to make electric current flow in the DN gel sheet attached to the bottom of its foot. A cathode rail composed of long conductive metallic plate is put on the ground and makes electric current flow inside of DN gel sheet.
When the electric current flows inside of the DN gel, water emerges from the DN gel and friction between the DN gel and a cathode rail on the floor becomes smaller.
Discussion
In this research, we have successfully developed the first prototype of the inchworm search robot utilizing the unique properties of DN gel feet and demonstrate fundamental running experiment. The results of running experiment confirmed that this robot can realize effective peristaltic motion by using DC motors and friction change effect of DN gel feet as the soft-matter robot based on biomimetics with significant differences. Detailed discussion is shown below.
Moving distance was 28.4 mm in the case of “With current for forward motion” while that in the case of “Without current” was 3.6 mm. The difference between such two cases was approximately 25 mm and the difference is regarded as significant due to statistical analysis. The results indicate that electric control method of DN gel feet strongly contributes to its steady motion and is quite beneficial for inchworm search robot.
In the case of “Without current,” moving distance was not 0.0 mm but 3.6 mm. The friction coefficient of DN gel is generally lower than 0.1 (Wada et al., 2018; Yoshida et al., 2018) without electric field, and we predicted that the robot would not move with low friction feet in this experimental setup. Even without current flow on the DN gel feet, there may be small difference between the friction coefficients of front and rear DN gels, so the robot moved slightly with the displacement of 3.6 mm. With electric current on DN gels, much larger difference of friction coefficients emerges between front and rear DN gels in the walking motion of the inchworm robot, so it moved with larger displacement of 28.4 mm.
The control of friction of DN gel worked well to switch the functions of feet of the robot, from supporting foot to hold the robot at one place to moving foot to push the body of the robot forward to reproduce the essence of the physical principle of real inchworms' motions in nature. This control function of the friction of its feet makes the robot actually faster. Because most of body parts of this first prototype is still composed of hard matters, we will utilize the soft actuators to reproduce the actual inchworm motion that can adapt narrow space like complicated small pipes in the next phase of this research. Present DN gel block used in this research still has simple shapes, therefore we will also manufacture DN gels with complicated shapes to develop the real soft robots made with soft materials to reproduce motions of natural creature like inchworms, snails and caterpillars more precisely. To realize these steady progresses, we plan to utilize our own 3D gel printer (Muroi et al., 2013; Ota et al., 2018). Our 3D gel printer has a special ability to form the complex soft system using hydrogel material to develop the novel soft robots. By using peristaltic motion with friction control of DN gel for thrust, the size of the mobile robot can be miniaturized compared with the traditional method such as the pipe inspection robot with conventional active wheels (Roh and Choi, 2005; Li et al., 2008), cilia with vibration motors (Wang and Gu, 2008), pneumatic artificial muscles (Kishi et al., 2013), and legs that need more components. We can also increase the number of segments with linear actuators from present two to more in the next prototype of the small inchworm search robot.
In this paper, we only considered the linear actuator that can be used inside of the segment of the walking robot, but in the next step, we can also consider adapting other types of flexible and soft actuators like jamming mechanisms in previous studies for more robust and flexible soft-matter robots (Kim et al., 2013; Fujita et al., 2018). We will continue our effort to realize soft-matter robots that can work in external environment with high safety against human bodies and biocompatibility to coexist with natural environment.
Conclusion
In this paper, we introduced the specifications and capacity of progress of the first prototype walking robot utilizing friction control technique of DN gels and explained the results of its fundamental running experiments. The materialistic features of the DN gel and its manufacturing process were also explained in detail. We demonstrated that the control of friction of DN gel using electric field can be utilized for the steady peristaltic motion of the small mobile robot to produce strong thrust in narrow and closed environment like pipes. In the next step of this research, we will also utilize some new core technologies like flexible sensors and stretchable cables that can be deployed inside and outside of the bodies of the soft-matter robots to enhance their functions. The original core technologies shown in this paper will lead us to overcome the limitations of conventional rigid body dynamics and open the new era of soft-matter robotics to realize the future human civilization that can coexist with nature more peacefully and productively.
Author Contributions
All the authors had discussed together for more than 2 years to plan this study based on a new concept of soft-matter robotics before starting an actual experiment. HH and YS designed the robot. KY and HF prepared the DN gel samples. MT assembled the robot and performed the experiments. KY, RT, and HF wrote the manuscript.
Funding
This study was partly supported by the national project named the Program of Open Innovation Platform with Enterprises, Research Institute and Academia (OPERA) from the Japan Science and Technology Agency (JST) (grant no. JPMJOP1614), and the Ministry of Education, Culture, Sports, Science and Technology (MEXT) in Japan.
Conflict of Interest Statement
HH is working in the company otuA Inc.
The remaining authors declare that the research was conducted in the absence of any commercial or financial relationships that could be construed as a potential conflict of interest.
Acknowledgments
We thank Mr. Kyuichiro Takamatsu (Yamagata Univ.) for his technical assistance.
Supplementary Material
The Supplementary Material for this article can be found online at: https://www.frontiersin.org/articles/10.3389/fmech.2019.00044/full#supplementary-material
References
Fujita, M., Tadakuma, K., Komatsu, H., Takane, E., Nomura, A., Ichimura, T., et al. (2018). Jamming layered membrane gripper mechanism for grasping differently shaped-objects without excessive pushing force for search and rescue mission. s. Adv. Robot. 32, 590–604. doi: 10.1080/01691864.2018.1451368
Gong, J. P. (2006). Friction and lubrication of hydrogels—Its richness and complexity. Soft Matter 2, 544–552. doi: 10.1039/B603209P
Gong, J. P., Higa, M., Iwasaki, Y., Katsuyama, Y., and Osada, Y. (1997). Friction of gels. J. Phys. Chem. B 101, 5487–5489. doi: 10.1021/jp9713118
Gong, J. P., Iwasaki, Y., Osada, Y., Kurihara, K., and Hamai, Y. (1999). Friction of gels. 3. Friction on solid surfaces. J. Phys. Chem. B 103, 6001–6006. doi: 10.1021/jp9902553
Gong, J. P., Katsuyama, Y, Kurokawa, T., and Osada, Y. (2003). Double network hydrogels with extremely high mechanical strength. Adv. Mater. 15, 1155–1158. doi: 10.1002/adma.200304907
Gong, J. P., and Osada, Y. (1998). Gel friction: a model based on surface repulsion and adsorption. J. Chem. Phys. 109:8062. doi: 10.1063/1.477453
Haraguchi, K., and Takehisa, T. (2002). Nanocomposite hydrogels: a unique organic-inorganic network structure with extraordinary mechanical, optical, and swelling/de-swelling properties. Adv. Mater. 14, 1120–1124. doi: 10.1002/1521-4095(20020816)14:16<1120::AID-ADMA1120>3.0.CO;2-9
Hirose, S., Ohno, H., Mitsui, T., and Suyama, K. (1999). “Design of in-pipe inspection vehicles for /spl phi/25, /spl phi/50, /spl phi/150 pipes,” in Proceedings of 1999 IEEE International Conference on Robotics and Automation (Detroit, MI: IEEE), 1050–4729.
Isaki, K., Niitsuma, A., Konyo, M., Takemura, F., and Tadokoro, S. (2006). “Development of an active flexible cable by ciliary vibration drive for scope camera,” in Proceeding of 2006 IEEE/RSJ International Conference on Intelligent Robots and Systems (Beijing: IEEE), 3946–3951.
Kakogawa, A., Komurasaki, Y., and Ma, S. (2017). “Anisotropic shadow-based operation assistant for a pipeline-inspection robot using a single illuminator and camera,” in Proceeding of 2017 IEEE/RSJ International Conference on Intelligent Robots and Systems (IROS2017) (Vancouver, BC: IEEE), 1305–1310.
Kim, Y. J., Cheng, S., Kim, S., and Iagnemma, K. (2013). A novel layer jamming mechanism with tunable stiffness capability for minimally invasive surgery. IEEE Trans. Robot. 29, 1031–1042. doi: 10.1109/TRO.2013.2256313
Kishi, T., Ikeuchi, M., and Nakamura, T. (2013). “Development of a peristaltic crawling inspection robot for 1-inch gas pipes with continuous elbows,” in Proceedings of 2013 IEEE/RSJ International Conference on Intelligent Robots and Systems (Tokyo: IEEE).
Kosukegawa, H., Fridrici, V., Kapsa, P., Sutou, Y., Adachi, K., and Ohta, M. (2013). Friction properties of medical metallic alloys on soft tissue-mimicking poly(vinyl alcohol) hydrogel biomodel. Tribol. Lett. 51, 311–321. doi: 10.1007/s11249-013-0165-3
Li, P., Ma, S., Li, B., and Wang, Y. (2008). “Design of a mobile mechanism possessing driving ability and detecting function for in-pipe inspection,” in Proceedings of 2008 IEEE International Conference on Robotics and Automation (Pasadena, CA: IEEE), 3992–3997.
Mizukami, M., Ren, H.-Y., Furukawa, H., and Kurihara, K. (2018). Deformation of contacting interface between polymer hydrogel and silica sphere studied by resonance shear measurement. J. Chem. Phys. 149:163327. doi: 10.1063/1.5037326
Morin, S. A., Shepherd, R. F., Kwok, S. W., Stokes, A. A., Nemiroski, A., and Whitesides, G. M. (2012). Camouflage and display for soft machines. Science 337, 828–832. doi: 10.1126/science.1222149
Muroi, H., Hidema, R., Gong, J., and Furukawa, H. (2013). Development of optical 3D gel printer for fabricating free-form soft & wet industrial materials and evaluation of printed double-network gels. J. Solid Mech. Mater. Eng. 7, 163–168. doi: 10.1299/jmmp.7.163
Okumura, Y., and Ito, K. (2001). The polyrotaxane gel: a topological gel by figure-of-eight cross-links. Adv. Mater. 13, 485–487. doi: 10.1002/1521-4095(200104)13:7<485::AID-ADMA485>3.0.CO;2-T
Ota, T., Yoshida, K., Tase, T., Sato, K., Tanaka, M., Saito, A., et al. (2018). Influence of 3D-printing conditions on physical properties of hydrogel objects. Mech. Eng. J. 5:17–00538. doi: 10.1299/mej.17-00538
Ren, H.-Y., Mizukami, M., Tanabe, T., Furukawa, H., and Kurihara, K. (2015). Friction of polymer hydrogels studied by resonance shear measurements. Soft Matter 11, 6192–6200. doi: 10.1039/C5SM01087J
Robertson, M. A., and Paik, J. (2017). New soft robots really suck: vacuum-powered systems empower diverse capabilities. Sci. Robot. 2:eaan6357. doi: 10.1126/scirobotics.aan6357
Roh, S.-G., and Choi, H. R. (2005). Differential-drive in-pipe robot for moving inside urban gas pipelines. IEEE Trans. Robot. 21, 1–17. doi: 10.1109/TRO.2004.838000
Shepherd, R. F., Ilievski, F., Choi, W., Morin, S. A., Stokes, A. A., Mazzeo, A. D., et al. (2011). Multigait soft robot. Proc. Natl. Acad. Sci. U.S.A. 108, 20400–20403. doi: 10.1073/pnas.1116564108
Umedachi, T., Ito, K., and Ishiguro, A. (2015). Soft-bodied amoeba-inspired robot that switches between qualitatively different behaviors with decentralized stiffness contro. l. Adapt. Behav. 23, 1–11. doi: 10.1177/1059712314564784
Wada, M., Yamada, K., Kameyama, T., Yamada, N., Yoshida, K., Saito, A., et al. (2018). Electric control of friction on surface of high-strength hydrogels. Microsyst. Technol. 24, 639–646. doi: 10.1007/s00542-017-3417-6
Wang, Z., and Gu, H. (2008). A bristle-based pipeline robot for III-constraint pipes. IEEE ASME Trans. Mechatron. 13, 383–392. doi: 10.1109/TMECH.2008.924133
Keywords: soft-matter robotics, double-network hydrogel, friction control, biomimetics, bioinspired robotics, inchworm walking robot, pipe inspection
Citation: Takagi M, Yoshida K, Hoshino H, Tadakuma R, Suzuri Y and Furukawa H (2019) Sliding Walk With Friction Control of Double-Network Gel on Feet of Inchworm Robot. Front. Mech. Eng. 5:44. doi: 10.3389/fmech.2019.00044
Received: 30 November 2018; Accepted: 02 July 2019;
Published: 19 July 2019.
Edited by:
Darwin Lau, The Chinese University of Hong Kong, ChinaReviewed by:
Peter M. Lee, Southwest Research Institute, United StatesAlpaslan Atmanli, National Defense University, Turkey
Copyright © 2019 Takagi, Yoshida, Hoshino, Tadakuma, Suzuri and Furukawa. This is an open-access article distributed under the terms of the Creative Commons Attribution License (CC BY). The use, distribution or reproduction in other forums is permitted, provided the original author(s) and the copyright owner(s) are credited and that the original publication in this journal is cited, in accordance with accepted academic practice. No use, distribution or reproduction is permitted which does not comply with these terms.
*Correspondence: Hidemitsu Furukawa, ZnVydWthd2EmI3gwMDA0MDt5ei55YW1hZ2F0YS11LmFjLmpw