- 1Laboratory for Tribology and Interface Nanotechnology, Faculty of Mechanical Engineering, University of Ljubljana, Ljubljana, Slovenia
- 2Laboratory for Surface Science and Technology, ETH Zürich, Zurich, Switzerland
- 3Laboratory for Neutron Scattering and Imaging, Paul Scherrer Institute, Villigen, Switzerland
Neutron reflectometry (NR) has proven to be an important analytical tool for investigations of the adsorption in boundary lubrication for both simple and complex additives by using either deuterated additives or the base carrier lubricant. NR enables in-situ measurements of the adsorption during surface exposure to additivated lubricants, and at the same time provides quantitative parameters for the adsorbed layer with sub-nanometer precision. In this work, NR was successfully used to determine the thickness and the density of the adsorbed layers of various lubricating additives (oiliness additives and ZDDP) on different DLC coatings. First, the influence of the coating structure and the presence of the doping element on the adsorption of two simple oiliness additives, i.e., hexadecanol and hexadecanoic acid, are presented. Second, the interaction ability of the ZDDP additive on a hydrogenated DLC (a-C:H) coating was measured as a function of the temperature and exposure time. Finally, an in-house-developed tribological rig was implemented in the neutron beam reflectometer to investigate the ZDDP film's growth and removal. The results show the unique ability of NR to provide direct evidence of the adsorption of additives on DLC coatings as a function of several relevant engineering parameters, such as time, temperature, and rubbing.
Introduction
Diamond-like carbon (DLC) coatings are, due to their inherent low-friction and anti-wear properties (Grill, 1999; Donnet, 2008; Haque et al., 2009), very promising materials for many machine-component applications, in particular those operating under the most demanding boundary-lubrication conditions (Spikes, 2004). On the other hand, the low reactivity of DLC coatings results in weak interactions with the lubricating additives (Ali and Christophe, 2006), and therefore in the formation of weakly adhered tribofilms (Equey et al., 2008; Topolovec-Miklozic et al., 2008; Vengudusamy et al., 2011).
Ex-situ analyses of such tribofilms with conventional analytical tools (i.e., XPS, ATR FT-IR, optical ellipsometry, optical interferometry, SIMS, SEM, and EDS) require surface cleaning to remove the excess lubricant and/or to work in a vacuum, which can affect the presence as well as the composition of the remaining tribofilms on poorly reactive DLC coatings. Additionally, the main component of DLC coatings and most of the lubricating additives is carbon, which absorbs a significant portion of the EM radiation. Changes due to thin-film adsorption often represent a weak component in the signal and are therefore difficult to determine with conventional spectroscopic techniques. All of this leads to contradictory results regarding the interactions between DLC coatings and lubricating additives (de Barros'Bouchet et al., 2005; Kalin and Vižintin, 2006; Haque et al., 2007a,b, 2010; Equey et al., 2008; Topolovec-Miklozic et al., 2008; Vengudusamy et al., 2011; Oblak and Kalin, 2015; Kalin et al., 2016) and to a poor understanding of the lubrication mechanisms of these materials.
To overcome the above-mentioned issues, we have introduced neutron reflectometry (NR) to investigate the lubrication of DLC coatings. This technique has proven to be indispensable for providing direct evidence including quantitative information about the adsorption of additives (Kalin et al., 2014; Simič et al., 2014). It enables in-situ measurements of the depth profiles of thin films and interfaces during surface exposure to additive molecules with a sub-nanometer precision (Giovanna, 2001). This is particularly crucial when it comes to preventing the loss of evidence relating to additive adsorption, which very often takes place as a result of cleaning (rinsing, ultra-sonication) and/or other treatments of sensitive samples such as DLC/tribofilm interfaces.
The working principle of NR is to measure the reflected over the incident intensity of a well collimated neutron beam upon its reflection by a surface and/or interface of interest as shown in Figure 1. The advantage of NR is that neutrons, unlike other probes (electrons, photons, x-rays), interact with the atomic nuclei of the sample rather than the electron cloud, which allows them to penetrate deep into the sample without affecting its chemical and physical properties. This provides an insight into the morphological parameters across an interface of the sample, such as the thickness and surface roughness, as well as the interface roughness and the density of individual layers (Penfold and Thomas, 1990; Russell, 1996; Giovanna, 2001).
Other unique advantages of NR over traditional techniques and x-ray reflectometry include the high sensitivity of neutrons to light elements (hydrogen and carbon) and the different scattering power (scattering cross-section) for isotopes of the same element. For example, hydrogen and deuterium have different amplitudes and phases of the scattering cross-section, and therefore hydrogen substitution with deuterium can be used to differentiate between the additive and the base liquid molecules. This makes NR particularly suitable for the investigation of hidden interfaces, such as adsorbed layers at the interface between the DLC coating and the additivated lubricant.
In this paper we present the results of NR measurements for various DLC/additivated-lubricant interfaces, demonstrating the unique ability of NR to provide direct evidence of additive adsorption on DLC coatings (as a function of various parameters). First, the influence of the coating's structure and the presence of the doping element on the adsorption of two oiliness additives, i.e., hexadecanol and hexadecanoic acid, are presented. Second, the adsorption ability of the ZDDP additive with respect to a hydrogenated DLC (a-C:H) coating was measured as a function of the temperature and the exposure time. Finally, an in-situ tribological study of the ZDDP film growth and removal is presented. For the latter study, our own-design tribological rig for implementation in the neutron beam reflectometer was used.
Materials and Methods
Samples
Due to restrictions relating to accelerating and guiding, the intensity of the incident neutron beam is usually rather low, and so in order to avoid long measurement times, samples with a large surface area (typically around 50 × 50 mm2) need to be used. In addition, a low surface roughness (ideally Ra < 2 nm) and a low coating thickness (preferably around 50 nm and up to maximum of 500 nm) are required to resolve thin adsorbed layers with sub-nanometer precision, whereas, the adhesive interlayers during coating deposition are avoided to facilitate the analysis of the reflectivity profiles.
The coatings used in our studies were hydrogenated (a-C:H) and silicon-doped (a-C:H:Si) DLC coatings. The coatings were deposited on ultra-flat silicon blocks with a surface roughness of Rq = 0.3 nm (Yamanaka Semiconductor Co., Japan), using a 13.56-MHz radio-frequency plasma-assisted CVD (RF PACVD) process. The thickness of the DLC coatings was in the range 50–60 nm for the adsorption studies of oiliness additives and in the range of 300–350 nm for the adsorption studies of the ZDDP additive.
A contrast between the specimen of interest and the surrounding media is a prerequisite for the successful detection of thin, adsorbed layers. Good contrast in the scattering length density (SLD, the definition is given later in subsection The Neutron Reflectometer and the Measuring Procedure) was achieved by employing deuterated hexadecanoic acid or hexadecanol (98 at. % D, Sigma–Aldrich Co., LLC.) with non-deuterated PAO6 oil (Neste Oil, Espo, Finland). In contrast, more complex and application-based molecules of ZDDP are not easy to deuterate, so a non-deuterated ZDDP additive (The Lubrizol Corporation, Ohio, USA) was used in deuterated decane/octadecane (98.4 at. % D, CDN Isotopes, Quebec, Canada), in order to obtain the relevant contrast. A solution of 0.7 wt. % oiliness additives and a solution of 1.0 wt. % ZDDP were used in our experiments.
The Neutron Reflectometer and the Measuring Procedure
The NR experiments were performed at the continuous spallation source (SINQ) at the Paul Scherrer Institute (PSI, Switzerland), using the Apparatus for Multi-Option Reflectometry (AMOR) operated in a neutron wavelength range of 3.5 Å < λ < 12 Å in the time-of-flight (TOF) detection mode (Gupta et al., 2004). A schematic of the AMOR reflectometer is shown in Figure 1. The measurements were performed using a horizontal sample-plane geometry. At the instrument position, the continuous neutron beam is pulsed using two choppers. A set of three slits was used to obtain the desired beam footprint on the sample's surface. The slits after the beam reflection were used to ensure that only specular reflection at an angle 2θ with respect to the incident beam reaches the detector. The sample's reflectivity was calculated as the ratio of the reflected beam to the incident beam intensities. In the case of specular reflection, the reflectivity is measured as a function of the momentum transfer vector perpendicular to the surface qz (reflectivity profile), which is defined as . In order to obtain the reflectivity profile in the qz range , measurements were performed at two angles of incidence, i.e., and 1.3°. The variation of the neutron reflectivity with the momentum-transfer vector depends on the contrast in the scattering length density ρ, across the interface. The scattering length density is defined as
where bi is the scattering length of the nuclear species i and ni is its number density.
In our experiments the reflectivity was measured under static conditions and after the in-situ tribological testing (in dynamic conditions) using the tribotester rig shown in Figure 2. The test rig has two openings, which allows the neutron beam to enter the silicon block on one side and reflect from the backside of the coating. A PTFE counter body with dimensions of ∅ = 10 mm × 40 mm was connected via a holder to a loading stage to reach a normal load of 160 N, which corresponds to 10 MPa of the maximum initial Hertzian contact pressure. The holder with the loading stage is mounted on a slider driven by an actuator that simultaneously ensures a reciprocating sliding movement, thus creating the tribological contact. The tribotester rig also has a heating unit to enable high-temperature testing.
In order to obtain the thickness and the density of the adsorbed layer with the highest accuracy, the reflectivity measurements for all the samples were performed according to the following procedure (Hirayama et al., 2012; Kalin et al., 2014; Simič et al., 2014). In the first step, the reflectivity for the air/DLC interface was measured to determine the thickness and the vertical distribution of the scattering length density (SLD) of the coating itself (Figure 3A). In the second step, the sample surface was covered with base liquid/oil. This helped us to check whether any interactions between the pure liquid and the coating or liquid diffusion into the coating take place (Figure 3B). In the final step, the pure base liquid was replaced by the additive solution in the base liquid (Figure 3C). In the case of adsorption, a change in the reflectivity profile with respect to those measured in the first two steps is expected. In static measurements, the last step was repeated to monitor changes in the additive adsorption with the exposure time, whereas, in dynamic experiments, the reflectivity was measured in sequence after each application of rubbing for 30 min (383 cycles). The thickness and the density of the adsorbed layers were analyzed by fitting the model reflectivity profile to the measured profile according to Parratt's theory (Parratt, 1954).
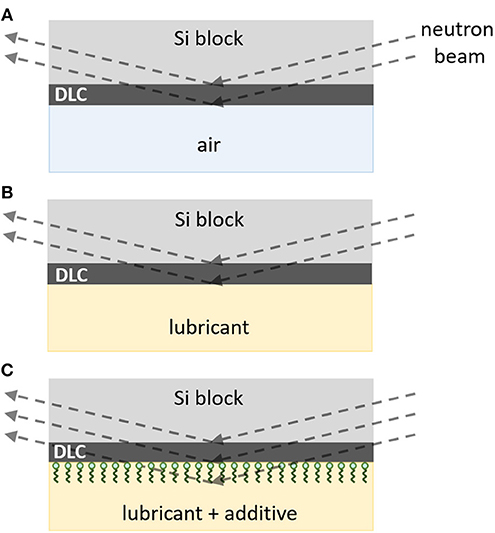
Figure 3. Experimental procedure used to measure the adsorption of additive molecules to the DLC coating with the highest accuracy: (A) first, reflectivity profile for air/DLC interface is measured, (B) then the reflectivity profile of the coating is checked in the presence of the base liquid, and (C) the base liquid is replaced by an additive solution. The last step can be repeated to monitor either the influence of the exposure time on the adsorption in static experiments or the influence of rubbing on the film growth/removal in dynamic experiments.
The results in the form of graphs are presented as reflectivity profiles, i.e., the reflected beam intensity, normalized to 1, as a function of the momentum transfer vector qz. The reflectivity profiles, obtained in all the subsequent steps are offset along the y axis to provide better clarity. The optimum fitting curves and the SLD profiles extracted from these fitting results are also presented. The χ2 values for the fits were found to be in the range from 2.0 × 10−2 to 7.8 × 10−3, meaning that this technique can provide a reliable thickness determination on a small scale. The uncertainty in the thickness calculation is, in principle, given by the chosen Δq/q of the experiment and is usually found to be in the range of ± 2–3 Å. The fitting parameters are the thickness, the density, and the roughness of the investigated structure, i.e., a monolayer, a bilayer, or a more complex multi-layer. To avoid any ambiguities in the construction of the theoretical model, additional measurements of the layer's thickness, roughness, surface coverage, and layer structure can be made with other complementary surface-sensitive techniques, such as AFM, X-ray reflectivity, XPS, AES, TOF-SIMS, etc.
It should also be noted that the measured NR provides an averaged value over a large surface area (the scanning footprint in our case was ~40 × 40 mm), and therefore, the spatial resolution in the lateral dimension is per se non-existent. For this reason NR is insensitive to the local thickness of the film and/or the distribution of defects.
Results
Adsorption of the Oiliness Additives
Figure 4A shows the measured reflectivity profiles for the a-C:H coating exposed first to the base oil and then to the solution of hexadecanoic acid at 25°C. A shift of the reflectivity profile toward lower qz values was observed upon exchanging the base oil with the additive solution, which is an indication of the interactions between the hexadecanoic acid and the a-C:H coating. The fitting of the reflectivity profiles revealed that an ~0.9-nm-thick layer was formed on the a-C:H coating during the 3-h exposure to the solution of hexadecanoic acid. This can be better seen from the SLD profile and schematic of the layer structure in Figure 4B that was extracted from the fitted reflectivity curve. The SLD value of the adsorbed layer was calculated to be ~3.2 × 10−6 Å−2, which corresponds to a layer density of about 50% of the bulk value (the SLD of hexadecanoic acid = 6.4 × 10−6 Å−2). In addition, the fitting revealed that the DLC coating is relatively homogeneous over the whole coating thickness, which was found to be 54.2 nm.
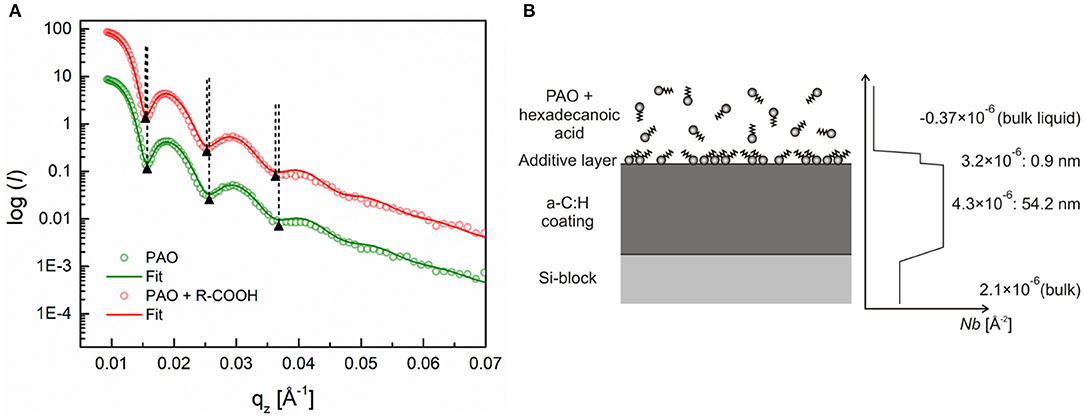
Figure 4. (A) Neutron reflectivity profiles (dots) and best fits (continuous lines) for an a-C:H DLC coating measured in air, pure PAO oil and a 0.7 wt.% solution of hexadecanoic acid, (B) schematic of additive adsorption on an a-C:H DLC coating and the SLD profile extracted from the fitted curve. Adapted from Simič et al. (2014).
The reflectivity profiles for the a-C:H DLC coating, exposed to air, base oil, and to the solution of hexadecanol in the final step, are presented in Figure 5A. In comparison to the hexadecanoic acid, hexadecanol exhibits very poor adsorption to the a-C:H DLC coating. This is evident from the absence of the phase shift between the reflectivity profiles for the a-C:H coating exposed to the base oil and to the additive solution. The SLD profile in Figure 5B also shows that here the coating was homogeneous over the whole coating thickness, which was calculated to be around 53.4 nm.
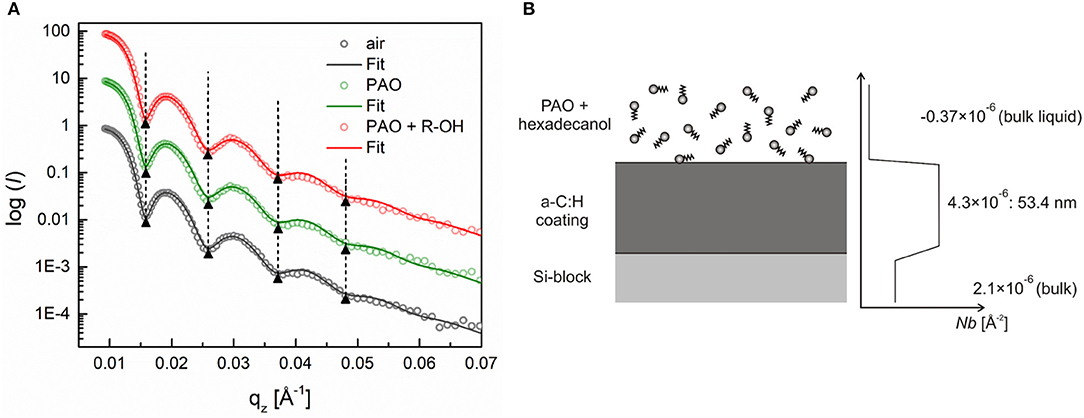
Figure 5. (A) Neutron reflectivity profiles (dots) and best fits (continuous lines) for an a-C:H DLC coating measured in air, pure PAO oil and a 0.7 wt.% solution of hexadecanol, (B) schematic of the additive adsorption on an a-C:H DLC coating and the SLD profile extracted from the fitted curve. Adapted from Kalin et al. (2014).
The same measurement procedure was also conducted for the a-C:H:Si DLC coating for both oiliness additives at 25°C. The obtained results contrast to what was observed in the case of the a-C:H DLC coating. Figure 6 shows first the measured reflectivity and the calculated SLD profiles for the adsorption of the hexadecanoic acid. The absence of a phase shift indicates that no continuous layer was formed during the coating's exposure to this additive.
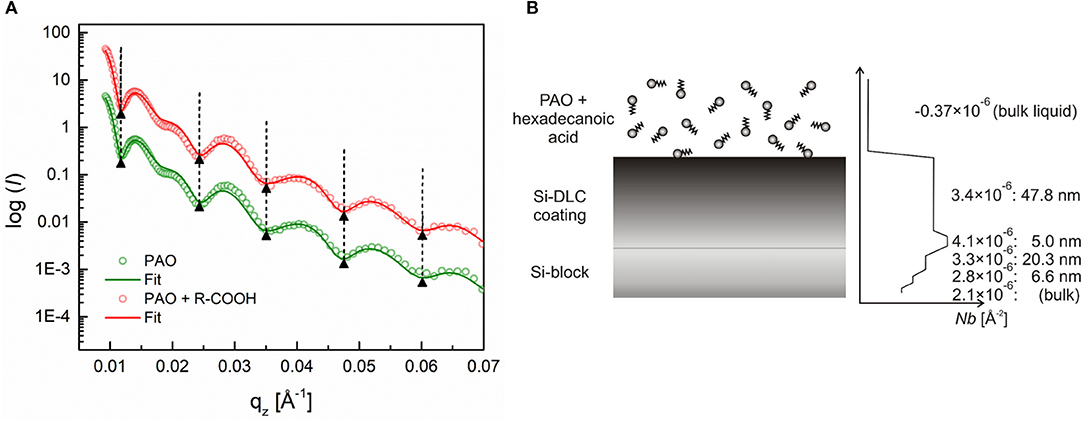
Figure 6. (A) Neutron reflectivity profiles (dots) and best fits (continuous lines) for an a-C:H:Si coating measured in pure PAO oil and a 0.7 wt.% solution of hexadecanoic acid, (B) Schematic of the additive adsorption on an a-C:H:Si DLC coating and the SLD profile extracted from the fitted curve. Adapted from Simič et al. (2014).
On the other hand, the base oil's substitution with the hexadecanol solution causes a shift of the reflectivity profile toward lower qz values, as can be seen in Figure 7A. This shift corresponds to the formation of an ~1.3-nm-thick layer (Figure 7B). The SLD value of the adsorbed layer, extracted from the fitted reflectivity curve, was around 2.2 × 10−6 Å−2, which corresponds to a layer density of around 37% of the density of the bulk hexadecanol (SLD = 5.9 × 10−6 Å−2).
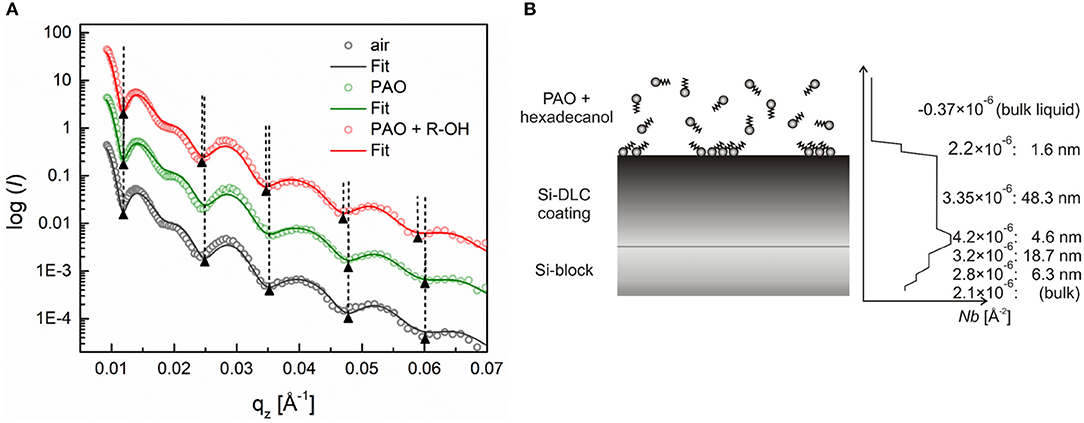
Figure 7. (A) Neutron reflectivity profiles (dots) and best fits (continuous lines) for an a-C:H:Si coating measured in pure PAO oil and a 0.7 wt.% solution of hexadecanol, (B) Schematic of the additive adsorption on an a-C:H:Si DLC coating and the SLD profile extracted from the fitted curve. Adapted from Kalin et al. (2014).
In contrast to the a-C:H DLC, the silicon-doped coatings were found to be less homogenous over the coating thickness, as can be seen from the SLD profiles (Figures 5B, 6B). These coatings consist of roughly two layers, a bottom thinner layer with a thickness of around 5 nm and the SLD of around 4.1 × 10−6 Å−2, and a topmost thicker layer with a thickness of around 48 nm and an SLD of around 3.4 × 10−6 Å−2.
Adsorption of ZDDP on an A-C:H DLC Coating at Various Temperatures
Figure 8A shows the reflectivity profiles for a-C:H DLC coating exposed first to air, then pure deuterated decane and finally to the ZDDP solution in deuterated decane at 25°C for different exposure times. The corresponding SLD profiles, extracted from fitted curves, are presented in Figure 8B. We can see that the reflectivity profiles remained unchanged upon decane substitution with the ZDDP solution, regardless of the exposure time. This indicates poor adsorption of the ZDDP molecules on the a-C:H DLC coating at 25°C.
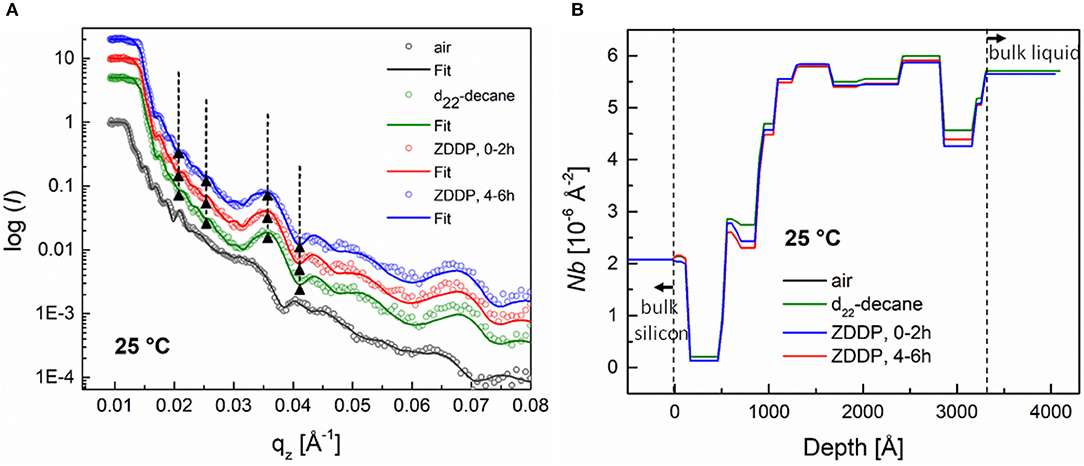
Figure 8. (A) Neutron reflectivity profiles (dots) and best fits (continuous lines) for an a-C:H coating measured in air, in deuterated decane, and finally in the presence of a 1 wt.% ZDDP solution for various exposure times at 25°C, (B) SLD profiles extracted from the fitted curve. The SLD profile for an a-C:H coating in air is omitted for the sake of clarity.
The reflectivity and the corresponding SLD profiles obtained at elevated temperature, i.e., 120°C, are presented in Figure 9. Under these conditions, differences in the reflectivity profile upon exchanging pure decane with the ZDDP solution occurred during the first 2 h of the exposure to ZDDP. The phase shift toward lower qz values that appeared only at qz values above 0.03 indicates that interactions between the ZDDP and the a-C:H DLC coating take place. The fitting revealed that this phase shift corresponds to the formation of an ~0.8-nm-thick layer. With longer exposure times, i.e., 4–6 h, the phase shift toward lower qz values became more pronounced than that observed during first 2 h. It also appeared at qz values below 0.03. The fitting of the reflectivity curves indicates that during this time a 1.2-nm-thick layer was formed. The presence of the interaction layer upon coating exposure to the ZDDP and its growth with further exposure (4–6 h) can be seen in the SLD profiles in Figure 9B.
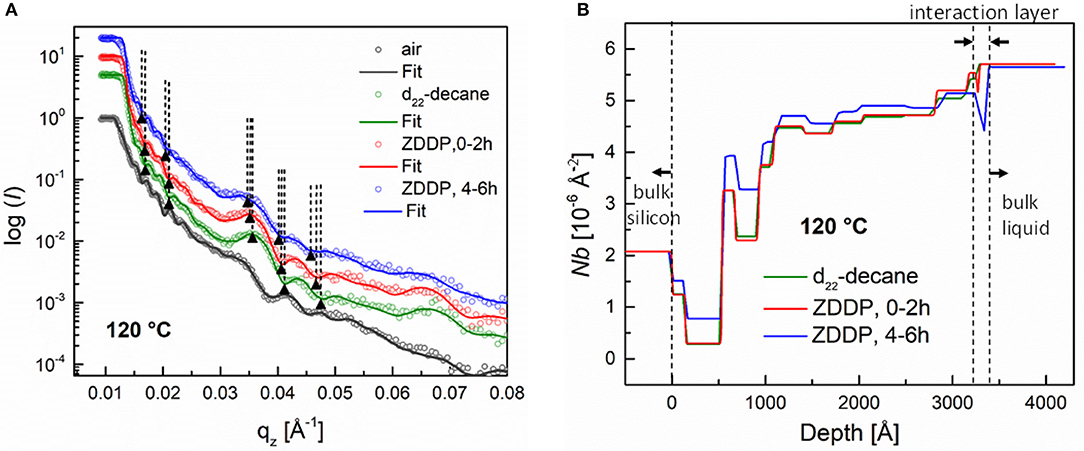
Figure 9. (A) Neutron reflectivity profiles (dots) and best fits (continuous lines) for an a-C:H coating measured in air, in deuterated decane and finally in the presence of a 1 wt.% ZDDP solution for various exposure times at 120°C, (B) SLD profiles extracted from fitted curve. The SLD profile for an a-C:H coating in air is omitted for the sake of clarity.
The SLD profiles in Figures 8B, 9B also show that the a-C:H DLC coatings used in this study were not perfectly homogenous over the coating thickness. This can be seen from the presence of layers of various densities in the film. In addition, it was observed that the SLD values of the individual layers changed when decane was substituted with the ZDDP solution. These changes could be attributed to the diffusion of the ZDDP solution into the coating through the coating imperfections (e.g., defects, pinholes).
In-situ Tribological Measurements of ZDDP Film Growth and Removal
Figure 10A shows the NR profiles for the a-C:H coating measured at 100°C during exposure to air, then pure octadecane, after that to ZDDP solution for 4 h and finally after each application of rubbing in the presence of ZDDP. The corresponding SLD profiles are presented in Figure 10B.
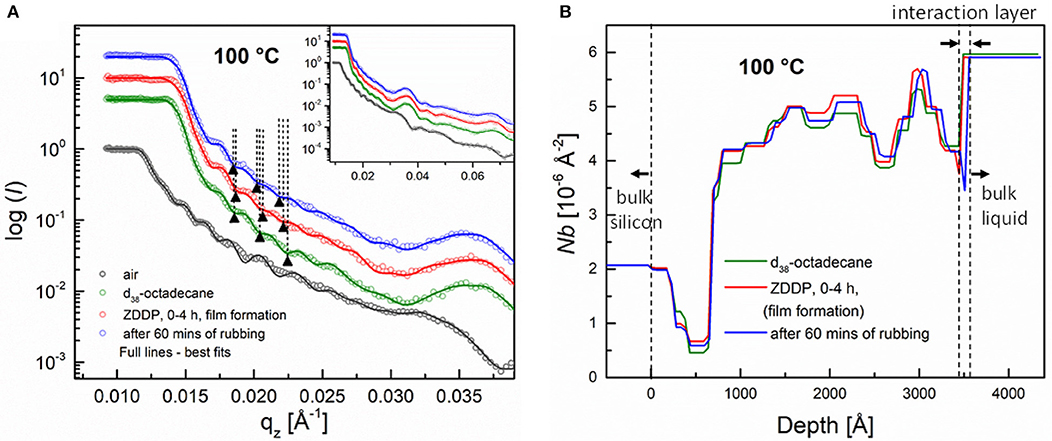
Figure 10. (A) Neutron reflectivity profiles (dots) and best fits (continuous lines) for an a-C:H coating measured at 100°C in air, in deuterated octadecane, in presence of a 1 wt.% ZDDP solution and finally after rubbing in the presence of ZDDP. Inset shows profiles over the whole qz range. (B) The SLD profiles extracted from fitted curves. The SLD profile for an a-C:H coating in air is omitted for the sake of clarity.
The coating's exposure to ZDDP for the first 4 h resulted in the shift of the neutron reflectivity toward lower qz values with respect to that obtained in pure octadecane. As obtained from fitting the data, this difference in the NR corresponds to the thickness change due to the adsorption of the ~1.2-nm-thick layer. Similar to that observed at 120°C in section Adsorption of ZDDP on an a-C:H DLC Coating at Various Temperatures, the SLD values of the individual layers changed upon exchanging the pure base liquid (i.e., octadecane) for the ZDDP solution.
The reflectivity profile obtained after the application of rubbing for 30 min (after 383 cycles) shifted further toward lower qz values, when compared to the reflectivity measured in octadecane and ZDDP during the first 4 h of exposure. The fitting showed that the thickness increased from ~1.2 to 1.7 nm. Upon further exposure to rubbing for another 30 min (in total 60 min of rubbing and 766 cycles) no major changes in the reflectivity were observed (data not shown).
Discussion
We have shown that in-situ measurements of DLC-coating/lubricant interfaces using NR provide a unique, quantitative determination of the physical properties, i.e., thickness and density, of the interaction layers. In addition, the sub-nanometer precision enabled the detection of very small differences in the thickness and density due to the film's formation (adsorption)/removal. Information about these differences is often lost when delicate interfaces, such as a DLC/adsorbed layer, are investigated with traditional techniques.
The results on the adsorption ability of the hexadecanol and hexadecanoic acid to the a-C:H and the a-C:H:Si DLC coatings showed that the adsorption of these two additives is specific to the coating structure. The adsorbed layer of the hexadecanoic acid molecules was detected only on the hydrogenated coating, whereas in the case of the hexadecanol, the layer formation occurred only for the silicon-doped coating (Figures 4–7). These results are surprising since we would expect a stronger adsorption on the a-C:H:Si than on the a-C:H DLC coating in the case of both additives. The reason for this is the polar component of the surface energy of the a-C:H:Si coating surface, which is almost two times larger than that of the a-C:H coating surface (Kalin and Polajnar, 2013).
However, it should be mentioned that the measured reflectivity represents an averaged value over a large surface area (the scanning footprint was ~40 × 40 mm), which means that if adsorption occurs on a smaller fraction of the sample's surface, it might not be detected. This also implies that adsorption on the interfaces between the a-C:H:Si coating and the hexadecanoic acid solution, as well as between the a-C:H coating and the hexadecanol solution cannot be excluded completely.
In contrast to the oiliness additives, the adsorption of the ZDDP additive to the a-C:H coating did not occur at 25°C, but only upon increasing the temperature to 100°C (Figures 8, 9). This is in agreement with studies performed by others, as well as with our previous results on the temperature dependence of the ZDDP thermal film's formation extracted from ATR FT-IR and XPS measurements. However, the NR results showed that the first 2 h of exposure to the ZDDP solution at 120°C already resulted in the formation of an ~0.8-nm-thick layer. With longer exposure times (i.e., 4–6 h) the film thickness increased to around 1.2 nm. Longer exposures than 4–6 h were not tested, and therefore, a further increase in the film thickness cannot be excluded.
The influence of in-situ rubbing on the growth/removal of an a priori formed ZDDP film on the a-C:H coating revealed that after the first application of rubbing (for 30 min), the film thickness increased by around 42% (see Figure 10). An additional 30 min of rubbing caused no further change in the film thickness. However, these are the first results using in-situ tribological experiments and NR. In order to further elucidate the influence of rubbing on the ZDDP film growth/removal on DLC coatings, additional measurements are required and are already in progress. They will be reported in a separate, more detailed, study. In addition, we should mention that in the case of the reflectivity measurements performed after rubbing, the time required to obtain sufficient counting statistics was rather long (around 4 h). This, of course, made the interpretation of the rubbing's influence on the film growth/removal more challenging. Faster reflectivity measurements will improve our understanding and are the next step in our investigations.
Conclusions
1. Neutron reflectometry is an essential tool for a quantitative determination of the physical properties of adsorbed layers at the interfaces between DLC coatings and an additivated lubricant with sub-nanometer precision.
2. The adsorption of oiliness additives at 25°C depends on the coating structure. In the case of hexadecanoic acid, the interaction layer was detected only on the a-C:H coating with a thickness of around 0.9 nm and a layer density of around 50% of the bulk density. On the other hand, the adsorption of hexadecanol molecules was observed in the case of the a-C:H:Si coating only, whereby an interaction layer with a thickness of 1.3 nm and a density of around 35% of the bulk density was formed.
3. ZDDP only interacts with the a-C:H DLC coating at an elevated temperature of 100°C. After the first 2 h of exposure to the ZDDP solution, an 0.8-nm-thick layer was formed. With an increase of the exposure time to 4–6 h, the layer thickness increased to 1.2 nm.
4. A unique, own-design of tribotester was used for the in-situ tribological experiments at the interface between the a-C:H DLC and the ZDDP solution. The application of rubbing on an a priori formed interaction layer at 100°C was found to promote the film growth, as the thickness increased from 1.2 to 1.7 nm.
Data Availability
All datasets generated for this study are included in the manuscript and/or the supplementary files.
Author Contributions
MK and LČ designed the research and the experimental matrix. LČ, RS, and TG carried out the experiments at PSI on the neutron reflectometer AMOR. LČ, RS, TG, and MK analyzed results. LČ and MK wrote the paper.
Funding
This research was performed in the framework of the research project (ARRS-PROJ-JR-Prijava/2014-I/168, Nanoscale engineering of the contact interfaces for green lubrication technology) funded by the Slovenian Research Agency.
Conflict of Interest Statement
The authors declare that the research was conducted in the absence of any commercial or financial relationships that could be construed as a potential conflict of interest.
Acknowledgments
This work is based on experiments performed at the Swiss Spallation source SINQ, Paul Scherrer Institute, Villigen, Switzerland. We acknowledge F. Meunier from Oerlikon for providing the DLC coatings used in this work.
References
Ali, E., and Christophe, D. (2006). Tribology of diamond-like carbon films: recent progress and future prospects. J. Phys. D 39:R311. doi: 10.1088/0022-3727/39/18/R01
de Barros'Bouchet, M. I., Martin, J. M., Le-Mogne, T., and Vacher, B. (2005). Boundary lubrication mechanisms of carbon coatings by MoDTC and ZDDP additives. Tribol. Int. 38, 257–264. doi: 10.1016/j.triboint.2004.08.009
Donnet, C. E. A. (2008). Tribology of Diamond-Like Carbon Films: Fundamentals and Applications. New York, NY: Springer Verlag.
Equey, S., Roos, S., Mueller, U., Hauert, R., Spencer, N. D., and Crockett, R. (2008). Tribofilm formation from ZnDTP on diamond-like carbon. Wear 264, 316–321. doi: 10.1016/j.wear.2007.03.012
Giovanna, F.-C. (2001). Neutron reflectivity at the solid/liquid interface: examples of applications in biophysics. J. Phys. Condensed Matter 13:4973. doi: 10.1088/0953-8984/13/21/322
Grill, A. (1999). Diamond-like carbon: state of the art. Diamond Relat. Mater. 8, 428–434. doi: 10.1016/S0925-9635(98)00262-3
Gupta, M., Gutberlet, T., Stahn, J., Keller, P., and Clemens, D. (2004). AMOR — the time-of-flight neutron reflectometer at SINQ/PSI. Pramana 63, 57–63. doi: 10.1007/bf02704051
Haque, T., Morina, A., and Neville, A. (2010). Influence of friction modifier and antiwear additives on the tribological performance of a non-hydrogenated DLC coating. Surf. Coat. Technol. 204, 4001–4011. doi: 10.1016/j.surfcoat.2010.05.017
Haque, T., Morina, A., Neville, A., Kapadia, R., and Arrowsmith, S. (2007a). Non-ferrous coating/lubricant interactions in tribological contacts: assessment of tribofilms. Tribol. Int. 40, 1603–1612. doi: 10.1016/j.triboint.2007.01.023
Haque, T., Morina, A., Neville, A., Kapadia, R., and Arrowsmith, S. (2007b). Study of the ZDDP antiwear tribofilm formed on the DLC coating using AFM and XPS techniques. J. ASTM Int. 4:7. doi: 10.1520/JAI100937
Haque, T., Morina, A., Neville, A., Kapadia, R., and Arrowsmith, S. (2009). Effect of oil additives on the durability of hydrogenated DLC coating under boundary lubrication conditions. Wear 266, 147–157. doi: 10.1016/j.wear.2008.06.011
Hirayama, T., Torii, T., Konishi, Y., Maeda, M., Matsuoka, T., Inoue, K., et al. (2012). Thickness and density of adsorbed additive layer on metal surface in lubricant by neutron reflectometry. Tribol. Int. 54, 100–105. doi: 10.1016/j.triboint.2012.04.012
Kalin, M., Oblak, E., and Akbari, S. (2016). Evolution of the nano-scale mechanical properties of tribofilms formed from low- and high-SAPS oils and ZDDP on DLC coatings and steel. Tribol. Int. 96, 43–56. doi: 10.1016/j.triboint.2015.12.013
Kalin, M., and Polajnar, M. (2013). The correlation between the surface energy, the contact angle and the spreading parameter, and their relevance for the wetting behaviour of DLC with lubricating oils. Tribol. Int. 66, 225–233. doi: 10.1016/j.triboint.2013.05.007
Kalin, M., Simič, R., Hirayama, T., Geue, T., and Korelis, P. (2014). Neutron-reflectometry study of alcohol adsorption on various DLC coatings. Appl. Surf. Sci. 288, 405–410. doi: 10.1016/j.apsusc.2013.10.047
Kalin, M., and Vižintin, J. (2006). Differences in the tribological mechanisms when using non-doped, metal-doped (Ti, WC), and non-metal-doped (Si) diamond-like carbon against steel under boundary lubrication, with and without oil additives. Thin Solid Films 515, 2734–2747. doi: 10.1016/j.tsf.2006.03.034
Oblak, E., and Kalin, M. (2015). Relationship between the nanoscale topographical and mechanical properties of tribochemical films on DLC coatings and their macroscopic friction behavior. Tribol. Lett. 59:49. doi: 10.1007/s11249-015-0575-5
Parratt, L. G. (1954). Surface studies of solids by total reflection of x-rays. Phys. Rev. 95:2. doi: 10.1103/PhysRev.95.359
Penfold, J., and Thomas, R. K. (1990). The application of the specular reflection of neutrons to the study of surfaces and interfaces. J. Phys. Condensed Matter 2:1369.
Russell, T. P. (1996). On the reflectivity of polymers: neutrons and X-rays. Phys. B 221, 267–283. doi: 10.1016/0921-4526(95)00937-X
Simič, R., Kalin, M., Hirayama, T., Korelis, P., and Geue, T. (2014). Fatty acid adsorption on several DLC coatings studied by neutron reflectometry. Tribol. Lett. 53, 199–206. doi: 10.1007/s11249-013-0257-0
Spikes, H. (2004). The history and mechanisms of ZDDP. Tribol. Lett. 17, 469–489. doi: 10.1023/B:TRIL.0000044495.26882.b5
Topolovec-Miklozic, K., Lockwood, F., and Spikes, H. (2008). Behaviour of boundary lubricating additives on DLC coatings. Wear 265, 1893–1901. doi: 10.1016/j.wear.2008.04.051
Keywords: DLC coatings, adsorption, additives, neutron reflectometry, in-situ measurement
Citation: Čoga L, Simič R, Geue T and Kalin M (2019) Additive Adsorption on DLC Coatings in Static and Tribological Conditions Using Neutron Reflectometry. Front. Mech. Eng. 5:10. doi: 10.3389/fmech.2019.00010
Received: 30 November 2018; Accepted: 04 March 2019;
Published: 29 March 2019.
Edited by:
Ashlie Martini, University of California, Merced, United StatesReviewed by:
Yong Luo, China University of Mining and Technology, ChinaLiran Ma, Tsinghua University, China
Hamed Ghaednia, Ford Motor Company, United States
Copyright © 2019 Čoga, Simič, Geue and Kalin. This is an open-access article distributed under the terms of the Creative Commons Attribution License (CC BY). The use, distribution or reproduction in other forums is permitted, provided the original author(s) and the copyright owner(s) are credited and that the original publication in this journal is cited, in accordance with accepted academic practice. No use, distribution or reproduction is permitted which does not comply with these terms.
*Correspondence: Mitjan Kalin, mitjan.kalin@tint.fs.uni-lj.si