- Laboratory for Processing of Advanced Composites (LPAC), Institute of Materials, Ecole Polytechnique Fédérale de Lausanne (EPFL), Lausanne, Switzerland
Fiber reinforced polymers are massively used as an alternative to metals in structural applications. The brittle nature of their matrix, however, makes them more susceptible to crack formation and propagation resulting in costly repair operations and increased environmental impact. Intrinsic healable composites provide a good alternative to these conventional composite materials, whereas their mechanical properties in static solicitation or impact testing are well documented, only few studies address fatigue testing. This research focuses on 3-point bending fatigue tests of polymer-blend based healable E-glass composite materials. The S–N curve was first built to compare the fatigue behavior of the healable system to a conventional epoxy composite. A statistical approach based on Weibull statistics was developed to predict the failure probability as a function of the applied stress amplitude, to compare both systems at equivalent probability of failure. The healable system showed a higher fatigue resistance at high cycle fatigue. Furthermore, a full stiffness recovery was obtained and a life extension of at least five times compared to the reference system when healed after reaching a 90% chance of survival. The healable system thus opens new perspectives for more sustainable load-bearing composites.
Introduction
The use of fiber reinforced polymers as a stiff and lightweight alternative to metal in structural applications enables to reach higher performance especially in transport, energy, and aerospace industry. However, the brittle nature of these materials makes them more prone to damage during manufacturing, handling, maintenance activities or during operation. Repair is not straightforward and often requires to remove part of the damaged zone and adhesively bond composite patches (Bond et al., 2008; Katnam et al., 2015; Préau et al., 2016). The overall budget for composite materials repair is thus significant and expected to reach not less than 22 Bn$ worldwide by 2026 (MarketsAndMarkets, 2017); in parallel, tons of unrecycled composite waste are produced due to unrepaired damaged structures, reaching 40,000 tons in France for the year 2015 (JEC-GROUP, 2017). Self-healing and more especially healable composites are a promising alternative to conventional composites to reduce repair costs and waste because of their ease of repair, demanding no additional material, which sometimes goes along with increased recyclability using moderate manpower and energy.
Healable polymer systems have been under investigation in the recent years, in particular integrating healing functionalities into thermoset polymers for the autonomous repair of subcritical damage in composite materials (Cohades et al., 2018). Two approaches are usually identified: a) extrinsic healable systems, where an extrinsic healing agent is integrated in the matrix through loaded microcapsules or vascules, and is released after damage events so as to flow, fill, and heal the crack after polymerization (Blaiszik, et al., 2010; Kling and Czigàny 2014), b) intrinsic healable systems, based on a modification of the matrix chemistry itself providing autonomous healing capabilities to the system (Garcia, 2014). Extrinsic systems generally show a reduction in composite mechanical properties by the integration of a large amount of capsules or vascules necessary to reach good healing capabilities; alternatively, the volume fraction of structural fibers is reduced, and the textile structure modified to make sufficient space for the healing agent containers; finally, these are limited to one healing cycle, and/or require the use of external pumping systems to circulate the healing fluids (Kessler and White, 2001; Patel et al., 2010; Norris et al., 2013; Patrick et al., 2014; Manfredi et al., 2015; Zhu et al., 2016). The intrinsic healing approach solves most of these issues providing the initial matrix with healable capabilities through reversible covalent (Park et al., 2009; Heo and Sodano 2015) bonds (Post et al., 2017; Shabani et al., 2020), supramolecular chemistries (Sordo and Michaud, 2016) or polymer blends (Pingkarawat et al., 2013; Cohades and Michaud 2017). Even if these intrinsic systems demonstrate good healing capabilities, and allow composites with a high load of reinforcing fibers, their mechanical properties are usually below those of conventional epoxy in term of stiffness, strength and damage tolerance. This is particularly true for composites based on matrices that heal at room temperature, which tend to show high mobility of bonds, and thus low mechanical properties (Deng et al., 2015; Sordo and Michaud 2016).
Healing efficiency is generally determined in composite materials through static fracture mechanics tests, in mode I or II, bending tests or compression after impact (Tsangouri et al., 2015); however, few studies are carried out on cyclic damage progression, as found in fatigue, although this case is one where small matrix cracks initially develop, that may be healed if caught at an early stage. Several studies were conducted on the fatigue resistance of extrinsic self-healing systems showing a retardation of failure due to the increased tortuosity of the crack path (Brown et al., 2005; Hamilton et al., 2012; Luterbacher et al., 2016; Ye, et al. 2017; Kim et al., 2019); however, little work is reported on the fatigue performance of intrinsically healable composites, although it is a key parameter for their long term integration as a structural material. To the best of our knowledge, only Pingkarawat and co-workers (Pingkarawat et al., 2012; Pingkarawat et al., 2013; Pingkarawat et al., 2014; Ladani et al., 2019) investigated the fatigue behavior of carbon-epoxy composites, using thermoplastic additives and only in double cantilever beam forced crack propagation mode, under cyclic loading. They found that thermoplastic additives in general helped retard the fatigue crack growth in mode I due to the presence of bridging thermoplastic ligaments formed in the healing operation at the crack location. Polyethylene-co-methacrylic acid (EMAA) was found to be the most effective, and was shown to also delay crack growth under cyclic loading when under the form of stitches, provided the quantity was high enough, or when they were combined with carbon fiber tows (Pingkarawat et al. 2014; Ladani et al., 2019). In this research, a commercial healable system based on epoxy/thermoplastic polymer blends was tested in 3-point bending fatigue to investigate its performance compared to a conventional epoxy-based composite. This loading method was chosen to concentrate the damage at the center of the specimen and to mimic potential applications where the part is loaded in flexural mode. Furthermore, a statistical approach based on Weibull statistics was developed to predict the probability of failure of the samples as a function of any applied stress amplitude. This approach was used as a damage criterion to reach a similar extent of damage in the two systems before healing, and re-testing to assess the healing efficiency.
Materials and Methods
Materials and Samples Preparation
Two types of resin were used to produce the samples. A first set of plates was produced with the healable system from CompPair Technologies Ltd. This novel resin system is based on epoxy/thermoplastic blends capable of autonomous healing by heat treatment at 150°C for 30 min. The second set was produced with the EPIKOTE™ MGS RIMR 135 from Hexion, a difunctional bisphenol A/epichlorohydrin derived liquid epoxy resin commonly used in rotor blades industry for wind turbines or boat building and cured with EPIKURE™ Curing Agent MGS™ RIMH 137 with a 100:30 weight mixing ratio and used as reference. The reinforcement was a woven twill 2 × 2 E-glass fabric with a nominal areal weight of 390 g/m2, 6 end/cm for wrap fibers and 6.7 picks/cm for weft fibers, with a diameter of 9 μm, a yarn thickness of 0.45 mm, warp tex of 68 × 5 and weft tex of 272, from Suter-Kunststoffe AG.
Both systems were produced by vacuum assisted resin infusion molding. Sixteen layers of reinforcements were cut in 350 mm × 250 mm rectangles and stacked following a quasi-isotropic stacking sequence of [(+45/−45);(0/90)]4s. The stack was infused at room temperature through the long edge with the resin systems and then cured at 60°C for 6 h. A post-cure treatment was then performed for 4 h at 80°C and 1 h at 100°C to reach the infinite glass transition temperature of the system (Tg,inf = 97°C). The resulting composite had a target fiber volume fraction (Vf) of 50 vol% with a thickness of ∼5 mm.
Fractured samples from each system were transversally cut, embedded in EPOFIX resin (Struers, Inc., Cleveland, United States) and polished to a 1 µm diamond paste finish. The crack profiles were then observed with an optical microscope (Olympus BH-2).
Three-Point Bending Fatigue Testing
Rectangular samples were cut from the infused plates with dimensions following 3-point bending ASTM D7264 (ASTM International, 2015) with a length, width and span-to-thickness ratio of respectively, 120, 13 mm and 16:1 (80 mm for 5 mm thick samples). The analysis method following this norm implies treating the material as homogeneous which is incorrect for a stack of laminates. In the special case of the symmetrical quasi-isotropic layup studied here, a preliminary static stress analysis with Altair ESAcompTM, using a woven 2–2 Twill glass and an equivalent epoxy resin, showed that it can be approximated as a homogeneous material in 3-point bending, allowing the use of this simple approach for comparison purposes. Nonetheless, the values provided in this work are thus an apparent maximal stress, apparent maximal strain, and apparent flexural secant modulus as defined in the norm, and are also based on a small strain approximation. The tests were performed at a frequency of 5 Hz on a 100 kN servo-hydraulic Schenk testing machine. Preliminary tests were performed at 0.1, 2, and 5 Hz to confirm that the heat generation due to micro-friction in the crack regions was negligible up to 5 Hz, in order to ensure that no healing could take place due to local heating during fatigue testing (Herman et al., 1990; Gagel et al., 2006; Adam and Horst 2017; Movahedi-Rad et al., 2018). These preliminary tests at 0.1 and 2 Hz were also integrated in the final S–N curve.
The tests were conducted at room temperature under load control with a loading ratio of R = 0.1 in compression. At least three (Ncycle > 106) and usually five (Ncycle < 106) replicates were carried out for each stress conditions to establish the S–N curve of the two systems. Note that because of the difference in volume fraction of fibers (Vf) between the healable and reference systems (Table 1), all the results are presented normalized to an equivalent volume fraction of Vf = 50% (which was the theoretical target volume fraction) for better comparison. This difference is due to the higher viscosity of the healable system that leads to a lower fiber compaction during infusion.
To investigate the healing efficiency of the system, a damage criterion was defined through Weibull statistical analysis of the fatigue experiments allowing direct access to a survival probability of the sample at a specific stress amplitude as a function of the number of cycles. This approach was necessary to take into account any difference in thickness and stiffness between the two systems and be able to compare and reach a similar amount of damage prior healing, since there is not direct access to damage levels in these bulk fatigue experiments, as compared to forced crack growth as performed in the literature.
The healing performance tests were performed at the stress amplitude of 220 MPa (Vf = 50% equivalent) at 5 Hz. Once the sample had reached a number of cycles corresponding to a survival probability of 90% (determined from the Weibull statistical study), the tests were stopped, the samples were healed at 150°C for 30 min in an oven, but under no applied pressure, then cooled down for an additional 30 min at room temperature (approximately 20 min from 150°C to ambient plus an additional 10 min for temperature equilibration) and again tested in fatigue at the exact same stress amplitude. This test-healing procedure was repeated several times, and at each step the change of the apparent flexural secant modulus calculated from the estimated maximal strain value at the maximal load of each cycle to determine the lifetime extension of the materials.
Results and Discussion
S–N Curve Determination
The results of the fatigue tests, in the form of conventional S–N curves (stress amplitude vs. number of cycles to failure), are given in Figure 1 for the two studied systems, along with a standard power law fit. The stress amplitude was corrected to an equivalent volume fraction of Vf = 50% to take into account the large difference in thickness due to the processing of the healable system. This correction was carried out simply multiplying the stress amplitude by the ratio 0.5/Vf explaining the scattering of the point regarding the applied stress. The ultimate strength in static mode of the reference system (437 ± 20 MPa) is slightly higher than that of the healable systems (361 ± 23 MPa) due to the presence of the thermoplastic phase accordingly reducing the flexural strength. Note that this diminution follows a rule of mixture considering the amount of thermoplastic present in the healable system, confirming the good quality of the composites. Damage, however, progresses faster in the pure epoxy system with a fatigue curve decreasing faster and even crossing the healable systems endurance curve at a stress amplitude of ∼200 MPa. The healable system is thus more durable than the reference one in particular for a stress amplitude lower than 200 MPa, i.e., for high cycle fatigue. This case of fatigue is typically the solicitation observed in structural parts during their lifetime. In both systems, damage mainly occurred by interlaminar crack propagation through the fiber tows and at the resin/fiber interface (see Figure 2). Whereas the crack path in the reference system clearly follows the tows outer boundary or directly progresses through the tows, the healable system shows a similar crack path location, but with a greater tortuosity which is expected since the system is tougher than pure epoxy. Note that the lower fiber volume fraction in the healable samples probably led to resin pockets known to affect the local stress concentration and reduce the fatigue performance of the material (Silva et al., 2005). However, as the damage mostly propagated through the fiber tows, we assumed that this effect can be neglected when comparing our two types of samples. Nevertheless, the overall fatigue resistance of the healable systems might therefore be underestimated here, keeping a conservative approach in the conclusions drawn.
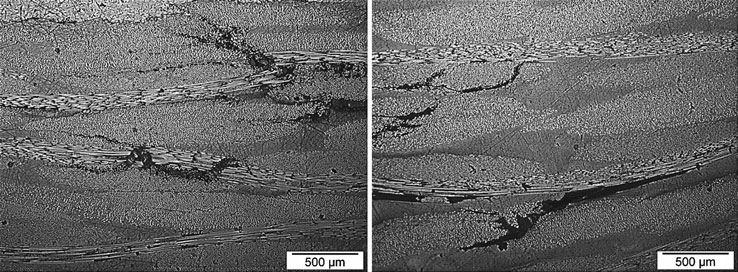
FIGURE 2. (Left) Micrograph of a reference sample after failure (σa = 191.8 MPa). (Right) Micrograph of a healable sample after failure (σa = 204.9 MPa).
Damage Criterion Determination—Weibull Statistics
To evaluate the healing efficiency of the healable systems in fatigue, a damage criterion had to be established, so as to determine when to stop the test for each sample at the same amount of damage. Indeed, simply fixing a stress amplitude and stopping the test at an arbitrary number of cycles would not affect the two systems identically because of their different intrinsic fatigue response. The same conclusion is reached when considering the reduction in flexural secant modulus because of the statistical nature of the tests. Damage was thus considered as a probability of failure based on a two parameters Weibull distribution characterized by a probability density function f(x) (Khashaba, 2003; Sakin and Ay, 2008):
where α and β are the shape and the scale parameter, respectively. Following the methods described in Sakin and Ay (2008), the cumulative density function is obtained by integrating the probability density function, obtaining a probability of failure Ff and a probability of survival Fs for a number of cycles x:
By taking the natural logarithm and rearranging, the following linear regression model is obtained:
With
To determine the Weibull parameters, the unreliability of each fatigue tests must be determined. The median ranks, the true probability of failure that the ith sample of a group should have in a group of n samples at a 50% confidence level, can be used to estimate this value. In this study, Bernard’s median rank approximation was used:
By grouping the fatigue tests of similar stress amplitude in groups of n samples, the median rank of each sample with a rank i = 1, 2, 3, ..., n could be determined. From the Weibull lines obtained by plotting
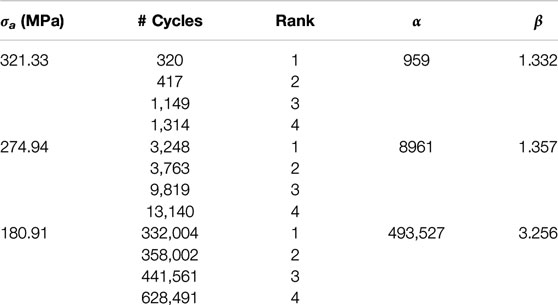
TABLE 3. Weibull’s parameter and the parameters used to draw the Weibull lines for the reference system.
The curves obtained from the median rank analysis only provide a survival probability for a determined stress amplitude; there is no direct generalization. To extend this analysis to the full range of possible stress values, the dependence of the Weibull parameters with respect to the stress amplitude must be quantified. From the definition of the survival probability and assuming that the number of cycles x generally follows a power law behavior with respect to the applied stress σ:
The stress can now be directly linked to the first Weibull parameter α as:
As β is usually much smaller than α and assuming a constant value for FS the expression would reduce to:
From this simple analysis, α seems to be linked by a power law to σ. However, fitting the experimental data shows that the relation is closer to:
From this, it is then possible to find an expression for α as a function of the stress amplitude fitting the experimental results as:
The same approach was performed with the second Weibull parameter β. Starting from the last expression of the previous analysis:
Assuming again a constant value for Fs and taking the exponential on the expression gives:
The stress amplitude is then exponentially linked to β. It is finally possible to find an expression for β as a function of the stress amplitude fitting the experimental results as:
These fitting approaches were successfully applied to both Weibull parameters on the two studied systems. An example of the obtained fits is shown for the healable system in Figure 7 as well as the detailed fitting parameters in Table 4.
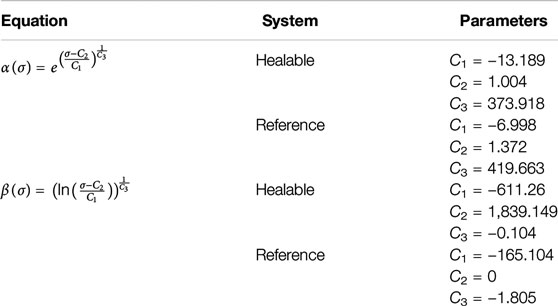
TABLE 4. Detailed fitting parameters to determine the Weibull parameters as a function of the stress amplitude.
Now that an expression for the Weibull parameters as a function of the applied stress was found, it is possible to determine the survival curve at any stress amplitude. A comparison of the experimental values and the fitted survival curves as well as additional new ones obtained from the fitting approach at intermediate values are shown for the healable and reference system in Figures 8 and 9.
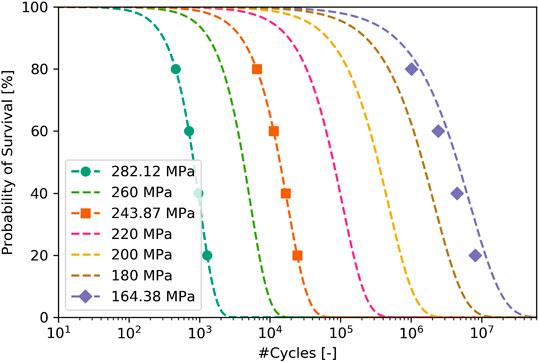
FIGURE 8. Survival curves of the healable system obtained from the fitted Weibull parameters (dashed lines) as well as the initial experimental data (solid dots).
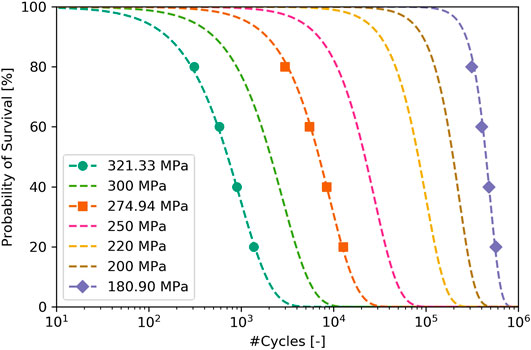
FIGURE 9. Survival curves of the reference obtained from the fitted Weibull parameters (dashed lines) as well as the initial experimental data (solid dots).
The obtained fits closely follow the experimental data giving a good approximation of the survival probability of the samples as a function of the stress amplitude. It is interesting to note on Figure 8 that the curve at 164 MPa slightly diverges from the prediction. This can be linked to the reduced number of tested samples at this low stress amplitude because of the time scale of the experiments (sometimes extending up to 17 days of tests).
Healing Efficiency
The healing efficiencies of each system were tested at 220 MPa (Vf = 50% equivalent) until a probability of survival of 90% was reached. This probability corresponds to 18,401 cycles for the healable system and 32,205 cycles for the reference system (see Table 5). This difference is justified by the chosen stress amplitude that corresponds to a region before the crossing of the two S–N curves (see Figure 1). The change of the relative flexural secant modulus of each system as a function of the number of cycles is shown in Figure 10. The efficiency of the healing procedure is clearly observed for the healable system: when stopping the test at a 90% probability of survival, the sample could sustain 10 test/heal repetitions. Note however, that the healable system could not be tested in a row because of the extended testing time. The tests were stopped for 12 h after the 5th healing cycle, explaining the sudden peak of the relative modulus because of the longer time allowed for stress relaxation. The reference system on the other hand shows no improvement in durability from the healing cycle. Only a small regain of properties was observed after the first (and only) healing which was attributed to the relaxation of internal stresses barely affecting its durability. The secant modulus decrease of the reference sample is more marked after healing, indicating that the healing step did not increase the fatigue resistance of the reference system. Interesting to notice as well is the increase in relative modulus for the healable system just after healing, which is especially visible after the 6th healing cycle. This different behavior compared to the reference system can be attributed to the increased toughness of the healable system, artificially increasing the relative modulus by friction. These observations confirm the excellent efficiency of the healable system to recover its mechanical properties in fatigue.
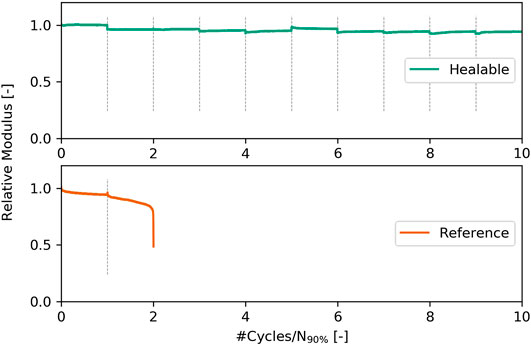
FIGURE 10. Relative secant modulus as a function of the number of cycles normalized by the number of cycles corresponding to a probability of 90% of survival for the healable and reference system. The vertical dashed lines correspond to each healing cycle.
Conclusion
The potential of healable composites as an alternative to conventional composites was confirmed through 3-point bending fatigue tests. The tested healable system showed enhanced fatigue resistance compared to the reference system at high cycle fatigue, opening a door to the use of these materials in highly solicited structural parts. A damage criterion based on Weibull statistics was successfully derived and used to work out a probability of failure. Following this method, the life of the healable system could be extended by at least five times compared to that of the reference system by consecutive testing/healing cycles. Note that this approach could also be used to predict the failure of composite parts during their operation, or to organize the maintenance schedule for parts submitted to cyclic loading during their service. Even if the mechanical properties of this healable system show promising results, its processing under the present form led to a reduced fiber volume fraction compared to conventional systems. This study nonetheless demonstrates the high potential of this material system at equivalent volume fraction.
Data Availability Statement
The raw data supporting the conclusions of this article will be made available by the authors, without undue reservation.
Author Contributions
NH, AC, and VM conceived the experiments, discussed the methods and results, and prepared the manuscript. NH and AC manufactured the test coupons and performed the experimental test and analysis.
Funding
The initial research for this work was supported by the Swiss National Fund (project no. 20020-15007-1) and later by the EPFL Enable grants program.
Conflict of Interest
The authors declare that the research was conducted in the absence of any commercial or financial relationships that could be construed as a potential conflict of interest.
Acknowledgments
We would like to thank Hexion for providing the reference epoxy resin.
References
Adam, T. J., and Horst, P. (2017). Fatigue damage and fatigue limits of a GFRP angle-ply laminate tested under very high cycle fatigue loading. Int. J. Fatigue 99, 202–214. doi:10.1016/j.ijfatigue.2017.01.045
ASTM International (2015). ASTM D7264. Standard test method for flexural properties of polymer matrix composite materials.
Blaiszik, B. J., Kramer, S. L. B., Olugebefola, S. C., Moore, J. S., Sottos, N. R., and White, S. R. (2010). Self-healing polymers and composites. Annu. Rev. Mater. Res. 40, 179–211. doi:10.1146/annurev-matsci-070909-104532
Bond, I. P., Trask, R. S., and Williams, H. R. (2008). Self-healing fiber-reinforced polymer composites. MRS Bull. 33, 770–774. doi:10.1557/mrs2008.164
Brown, E., White, S., and Sottos, N. (2005). Retardation and repair of fatigue cracks in a microcapsule toughened epoxy composite-part II: in situ self-healing. Compos. Sci. Technol. 65, 2474–2480. doi:10.1016/j.compscitech.2005.04.053
Cohades, A., Branfoot, C., Rae, S., Bond, I., and Michaud, V. (2018). Progress in self‐healing fiber‐reinforced polymer composites. Adv. Mater. Interfaces 5, 17. doi:10.1002/admi.201870084
Cohades, A., and Michaud, V. (2017). Thermal mending in E-glass reinforced poly(ε-caprolactone)/epoxy blends. Compos. Part A Appl. Sci. Manuf. 99, 129–138. doi:10.1016/j.compositesa.2017.04.013
Deng, W., You, Y., and Zhang, A. (2015). “7-Supramolecular network-based self-healing polymer materials,” in Recent advances in smart self-healing polymers and composites. Woodhead Publishing Series in Composites Science and Engineering. Sawston, United Kingdom: Wodhead Publishing, 181–210. doi:10.1016/B978-1-78242-280-8.00007-8
Gagel, A., Lange, D., and Schulte, K. (2006). On the relation between crack densities, stiffness degradation, and surface temperature distribution of tensile fatigue loaded glass-fibre non-crimp-fabric reinforced epoxy. Compos. Part A Appl. Sci. Manuf. 37, 222–228. doi:10.1016/j.compositesa.2005.03.028
Garcia, S. J. (2014). Effect of polymer architecture on the intrinsic self-healing character of polymers. Eur. Polym. J. 53, 118–125. doi:10.1016/j.eurpolymj.2014.01.026
Hamilton, A. R., Sottos, N. R., and White, S. R. (2012). Mitigation of fatigue damage in self-healing vascular materials. Polymer 53, 5575–5581. doi:10.1016/j.polymer.2012.09.050
Heo, Y., and Sodano, H. A. (2015). Thermally responsive self-healing composites with continuous carbon fiber reinforcement. Compos. Sci. Technol. 118, 244–250. doi:10.1016/j.compscitech.2015.08.015
Herman, W. A., Hertzberg, R. W., and Manson, J. A. (1990). The influence of loading history on fatigue in engineering plastics. J. Mater. Sci. 25, 434–440. doi:10.1007/bf00714052
JEC-GROUP (2017). Overview of the global composites market: at the crossroads. France: Frédérique Mutel, JEC Group.
Katnam, K. B., Comer, A. J., Roy, D., Da Silva, L. F. M., and Young, T. M. (2015). Composite repair in wind turbine blades: an overview. J. Adhes. 91, 113–139. doi:10.1080/00218464.2014.900449
Kessler, M. R., and White, S. R. (2001). Self-activated healing of delamination damage in woven composites. Compos. Part A Appl. Sci. Manuf. 32, 638–699. doi:10.1016/s1359-835x(00)00149-4
Khashaba, U. A. (2003). Fatigue and reliability analysis of unidirectional GFRP composites under rotating bending loads. J. Compos. Mater. 37 (4), 317–331. doi:10.1177/0021998303037004680
Kim, S. Y., Sottos, N. R., and White, S. R. (2019). Self-healing of fatigue damage in cross-ply glass/epoxy laminates. Compos. Sci. Technol. 175, 122–127. doi:10.1016/j.compscitech.2019.03.016
Kling, S., and Czigány, T. (2014). Damage detection and self-repair in hollow glass fiber fabric-reinforced epoxy composites via fiber filling. Compos. Sci. Technol. 99, 82–88. doi:10.1016/j.compscitech.2014.05.020
Ladani, R. B., Wang, C. H., and Mouritz, A. P. (2019). Delamination fatigue resistant three-dimensional textile self-healing composites. Compos. Part A Appl. Sci. Manuf. 127, 105626. doi:10.1016/j.compositesa.2019.105626
Luterbacher, R., Trask, R. S., and Bond, I. P. (2016). Static and fatigue tensil properties of crossply laminates containing vascules for self-healing applications. Smart Mater. Struct. 25, 015003. doi:10.1088/0964-1726/25/1/015003
Manfredi, E., Cohades, A., Richard, I., and Michaud, V. (2015). Assessment of solvent capsule-based self-healing for woven E-glass fibre-reinforced polymers. Smart Mater. Struct. 24, 1–11. doi:10.1088/0964-1726/24/1/015019
MarketsAndMarkets (2017). Report code CH 4906. Composite repairs market by type (structural, semi-structural, cosmetic), process (hand lay-up, vacuum infusion, autoclave), end-use industry (aerospace and defense, wind energy, automotive and transportation), and region—global forecast to 2026.
Movahedi-Rad, A. V., Keller, T., and Vassilopoulos, A. P. (2018). Fatigue damage in angle-ply GFRP laminates under tension-tension fatigue. Int. J. Fatigue 109, 60–69. doi:10.1016/j.ijfatigue.2017.12.015
Norris, C. J., Bond, I. P., and Trask, R. S. (2013). Healing of low-velocity impact damage in vascularised composites. Compos. Part A Appl. Sci. Manuf. 44, 78–85. doi:10.1016/j.compositesa.2012.08.022
Park, J. S., Kim, H. S., and Thomas Hahn, H. (2009). Healing behavior of a matrix crack on a carbon fiber/mendomer composite. Compos. Sci. Technol. 69, 1082–1087. doi:10.1016/j.compscitech.2009.01.031
Patel, A. J., Sottos, N. R., Wetzel, E. D., and White, S. R. (2010). Autonomic healing of low-velocity impact damage in fiber-reinforced composites. Compos. Part A Appl. Sci. Manuf. 41, 360–368. doi:10.1016/j.compositesa.2009.11.002
Patrick, J. F., Hart, K. R., Krull, B. P., Diesendruck, C. E., Moore, J. S., and White, S. R. (2014). Continuous self-healing life cycle in vascularized structural composites. Adv. Mater. 26, 4302–4308. doi:10.1002/adma.201400248
Pingkarawat, K., Bhat, T., Craze, D. A., Wang, C. H., Varley, R. J., and Mouritz, A. P. (2013). Healing of carbon fibre-epoxy composites using thermoplastic additives. Polym. Chem. 4, 5007. doi:10.1039/c3py00459g
Pingkarawat, K., Wang, C. H., Varley, R. J., and Mouritz, A. P. (2012). Self-healing of delamination fatigue cracks in carbon fibre–epoxy laminate using mendable thermoplastic. J. Mater. Sci. 47, 4449–4456. doi:10.1007/s10853-012-6303-8
Pingkarawat, K., Wang, C. H., Varley, R. J., and Mouritz, A. P. (2014). Healing of fatigue delamination cracks in carbon–epoxy composite using mendable polymer stitching. J. Intell. Mater. Syst. Struct. 25, 75–86. doi:10.1177/1045389X13505005
Post, W., Cohades, A., Michaud, V., van der Zwaag, S., and Garcia, S. J. (2017). Healing of a glass fibre reinforced composite with a disulphide containing organic-inorganic epoxy matrix. Compos. Sci. Technol. 152, 85–93. doi:10.1016/j.compscitech.2017.09.017
Préau, M., and Hubert, P. (2016). Processing of co-bonded scarf repairs: void reduction strategies and influence on strength recovery. Compos. Part A Appl. Sci. Manuf. 84, 236–245. doi:10.1016/j.compositesa.2016.01.016
Sakin, R., and Ay, İ. (2008). Statistical analysis of bending fatigue life data using Weibull distribution in glass-fiber reinforced polyester composites. Mater. Design 29, 1170–1181. doi:10.1016/j.matdes.2007.05.005
Shabani, P., Shokrieh, M. M., and Saeedi, A. (2020). A novel model to simulate the formation and healing of cracks in self-healing cross-ply composites under flexural loading. Compos. Struct. 235, 111750. doi:10.1016/j.compstruct.2019.111750
Silva, J. M. A., Devezas, T. C., Silva, A. P., and Ferreira, J. A. M. (2005). Mechanical characterization of composites with embedded optical fibers. J. Compos. Mater. 39 (14), 1261–1281. doi:10.1177/0021998305050423
Sordo, F., and Michaud, V. (2016). Processing and damage recovery of intrinsic self-healing glass fiber reinforced composites. Smart Mater. Struct. 25, 084012. doi:10.1088/0964-1726/25/8/084012
Tsangouri, E., Aggelis, D., and Van Hemelrijck, D. (2015). Quantifying thermoset polymers healing efficiency: a systematic review of mechanical testing. Prog. Polym. Sci. 49–50, 154–174. doi:10.1016/j.progpolymsci.2015.06.002
Ye, X. J., Zhu, Y., Yuan, Y. C., Song, Y. X., Yang, G. C., and Rong, M. Z. (2017). Improvement of fatigue resistance of epoxy composite with microencapsulated epoxy-SbF5 self-healing system. Express Polym. Lett. 11, 853–862. doi:10.3144/expresspolymlett.2017.82
Keywords: self-healing, composites, fatigue, failure prediction, Weibull statistics
Citation: Hostettler N, Cohades A and Michaud V (2020) Statistical Fatigue Investigation and Failure Prediction of a Healable Composite System. Front. Mater. 7:561852. doi: 10.3389/fmats.2020.561852
Received: 13 May 2020; Accepted: 24 August 2020;
Published: 14 September 2020.
Edited by:
Patricia Krawczak, IMT Lille Douai, FranceReviewed by:
Ming Qiu Zhang, Sun Yat-sen University, ChinaNancy Sottos, University of Illinois at Urbana-Champaign, United States
Ruben Dirk Sevenois, Ghent University, Belgium
Copyright © 2020 Hostettler, Cohades and Michaud. This is an open-access article distributed under the terms of the Creative Commons Attribution License (CC BY). The use, distribution or reproduction in other forums is permitted, provided the original author(s) and the copyright owner(s) are credited and that the original publication in this journal is cited, in accordance with accepted academic practice. No use, distribution or reproduction is permitted which does not comply with these terms.
*Correspondence: Véronique Michaud, veronique.michaud@epfl.ch