- 1State Key Laboratory of Green Building Materials, China Building Materials Academy, Beijing, China
- 2Institute of Cement Science and New Building Materials, China Building Materials Academy, Beijing, China
- 3Department of Civil, Environmental and Geomatic Engineering, University College London, London, United Kingdom
- 4Guangxi Yufeng Group Co., Ltd., Liuzhou, China
- 5China Three Gorges Corporation, Beijing, China
An accurate quantification of periclase in high magnesia Portland cement (HMPC) is vital to evaluate the expansive property of this cement at a later age in practice. However, the existing methods to achieve this quantification either are limited in number or produce inaccurate results. In this study, a new technique to quantitatively determine the content of periclase in HMPC was demonstrated by combining an autoclave test, a thermogravimetric analysis (TGA) and a chemical analysis; this was achieved by using the periclase standard substance (PSS) as the internal standard. The accuracy of this technique was evaluated with regard to the recovery rate. In this study, an analytical-grade reagent such as magnesium carbonate basic [Mg(OH)2⋅3MgCO3⋅3H2O] or magnesium hydroxide [Mg(OH)2] calcined at 1400°C is recommended to be the PSS. The autoclave pressure should be 2.2 MPa and the autoclave time should be 4 h. This novel technique can avoid the interference of fused MgO in cement and can eliminate the influence of Mg(OH)2 and Ca(OH)2 (induced by the partial overlapping of their decomposition temperatures during TGA) on the periclase content. The results show that the recovery of PSS is between 99.92 and 100.14%, indicating that the technique presents a good recovery effect and a relatively high accuracy. Therefore, this new technique can be used to evaluate the expansive properties of HMPC and can serve as a guide for using HMPC in different practical applications according to the demand of a project.
Introduction
Periclase calcined at high temperatures tends to get hydrated extremely slowly, and the volume expansion caused by the formation of magnesium hydroxide [Mg(OH)2] is observed quite late (Ruan and Unluer, 2017a,b,c). A large number of MgO concrete technologies (Mo et al., 2014) were proposed after 40 years of research on the characteristics of mass concrete. According to these technologies, MgO concrete suffers a volume expansion when subjected to a temperature drop. This volume expansion could effectively compensate the shrinkage due to the decrease in temperature (Zhu, 2000; Ye et al., 2004; Ruan et al., 2020) and could improve the crack resistance of the concrete. These technologies could ensure that all or most of the traditional temperature control measures applied in mass concrete are discarded, such as precooling of aggregates, ice mixing, embedding cooling water pipes and blocking. A high-quality mass concrete can be cast in a fast and economical manner using these technologies, resulting in the research, promotion and application of HMPC (Wang et al., 2013).
MgO has been observed to exist in two forms in cement clinkers, namely, fused and free states, wherein the fused MgO does not exhibit an expansive effect. However, MgO in the form of free crystals (also known as periclase) expands by approximately 117% on its own volume during the slow hydration process, exhibiting slight expansibility at a later age (Wang et al., 2013). Therefore, the MgO content cannot be simply used to evaluate the expansion of HMPC at a later age, but rather the periclase content in the cement should be used to do so (Xu et al., 2017). In order to accurately evaluate the expansion of HMPC at a later age, it is necessary to quantitatively determine the periclase content in this cement. Due to the interference of fused MgO in the process of determining the periclase content, no international standard has been established for the quantitative determination of periclase in cement clinkers. Thus far, numerous methods, such as the Bogue–Taylor method, the ammonium nitrate method and the Toropow–Kacenielen–bogen method, have been widely used globally (Arjunan and Kumar, 1994; Katyal et al., 1998). However, Katyal et al. (1998), Xu et al. (2016) and Cao et al. (2017) argued that these methods cannot completely separate fused MgO during the extraction process, i.e. they cannot effectively distinguish the contents of fused MgO and periclase.
In addition to chemical methods, there are electrical conduction methods (Yu, 1998) and XRD (Deng et al., 2015; Xu et al., 2017; Wang et al., 2019) technologies for achieving the quantification of the periclase content. Chen and Xu (2010) elucidated that the electrical conduction method is easily affected by factors such as the temperature, concentration, voltage, current, distance between two electrodes and electrode insertion depth, resulting in a large measurement error in conductivity; consequently, this reduces the accuracy of the measured content of periclase. The XRD method can be affected by the errors induced during X-ray powder diffractometry via equipment faults, the plotting of the standard curve and the selection of the pure phase, thereby reducing the accuracy of the measured content of periclase. Numerous standard substances have been used in the existing methods of periclase quantification such as ZnO (Xu et al., 2014, 2017; Wang et al., 2019) and α-Al2O3 (Rehsi and Majumdar, 1968). Owing to the fact that different elements have varying physical and chemical properties, these standard substances can easily interfere with the quantification of periclase. Furthermore, the methods used for periclase quantification are limited. In order to overcome the inaccuracies associated with the determination of the periclase content in cement, this paper presents a new technique that combines several methods for the quantitative determination of the periclase content in HMPC. Furthermore, an attempt has been made to evaluate the accuracy of this technique with regard to the recovery rate. Here, a combination of the autoclave test, TGA and chemical analysis is used to prepare the PSS and optimise the test conditions. The results obtained indicate that this novel technique can be used to assess the expansive property of HMPC while facilitating the utilisation of HMPC for different application demands.
Materials and Experimental Methods
Raw Materials
Magnesian Raw Materials
Five kinds of analytical-grade reagents including magnesium carbonate basic [Mg(OH)2⋅3MgCO3⋅3H2O], magnesium hydroxide [Mg(OH)2], magnesium phosphate [Mg3(PO4)2], magnesium sulphate (MgSO4) and magnesium silicate (MgSiO3) produced by Sinopharm Chemical Reagent Co., Ltd. (China) were used.
Cement
Seven kinds of cements were fabricated in the laboratory using raw materials including limestone, silica, iron powder, bauxite, dolomite and natural dihydrate gypsum. These raw materials, whose chemical compositions are shown in Table 1, have been obtained from Sichuan Jiahua Jinping Special Cement Co., Ltd. (China). The raw materials were dried and ground into powder, with sieve residue content of less than 10.0%. After homogenisation, the powder was used as a raw meal and calcined into a cement clinker in a high temperature furnace, according to the program designed in Table 2. The calcined clinker and dihydrate gypsum were ground together into powder with the specific surface area of 320 ± 10 m2/kg to prepare the cement. Furthermore, the SO3 content in cement was controlled to be between 2.0 and 2.2%. Seven kinds of cements with MgO contents of 1.61, 2.72, 3.26, 4.75, 5.58, 7.48 and 8.59%, respectively, have been used in this study. According to the increasing order of their MgO contents, these cements are numbered from 1# to 7#. The chemical compositions of the cements are shown in Table 3.
Four kinds of cement clinker samples with MgO contents of 4.75, 5.58, 7.48 and 8.59%, respectively (corresponding to 4#, 5#, 6# and 7#), were fixed with sulphur. The upper surface of each kind of cement clinker was ground to be smooth. Subsequently, they were scanned using a Quanta 250 FEG FE-SEM that was produced by the FEI Corporation (United States). FE-SEM had an acceleration voltage ranging from 200 V to 30 kV and was equipped with the INCAX-MAX 50 X-ray energy spectrometer produced by the Oxford Corporation (United Kingdom). The resolution ratio of the energy spectrometer was 127 eV and the element test scope was from B5 to U92. FE-SEM was used to conduct point scanning and Mg element map scanning to correspondingly observe the size, distribution and relative content of periclase in the clinker. Schematics comparing the point and map scannings of the cement clinker with different MgO contents are shown in Figure 1. Figure 1A of each number represents the point scanning diagram; Figure 1B of each number is the map scanning diagram, which shows the distribution of elemental Mg in red colour. Figures 1A,B of each number correspond to each other; the minerals with spherical or polygonal shapes, the red parts, distributed around the alite or the belite are periclase. It can be observed from these figures that increasing the MgO content leads to a surge in the content of periclase and also tends to concentrate the distribution.
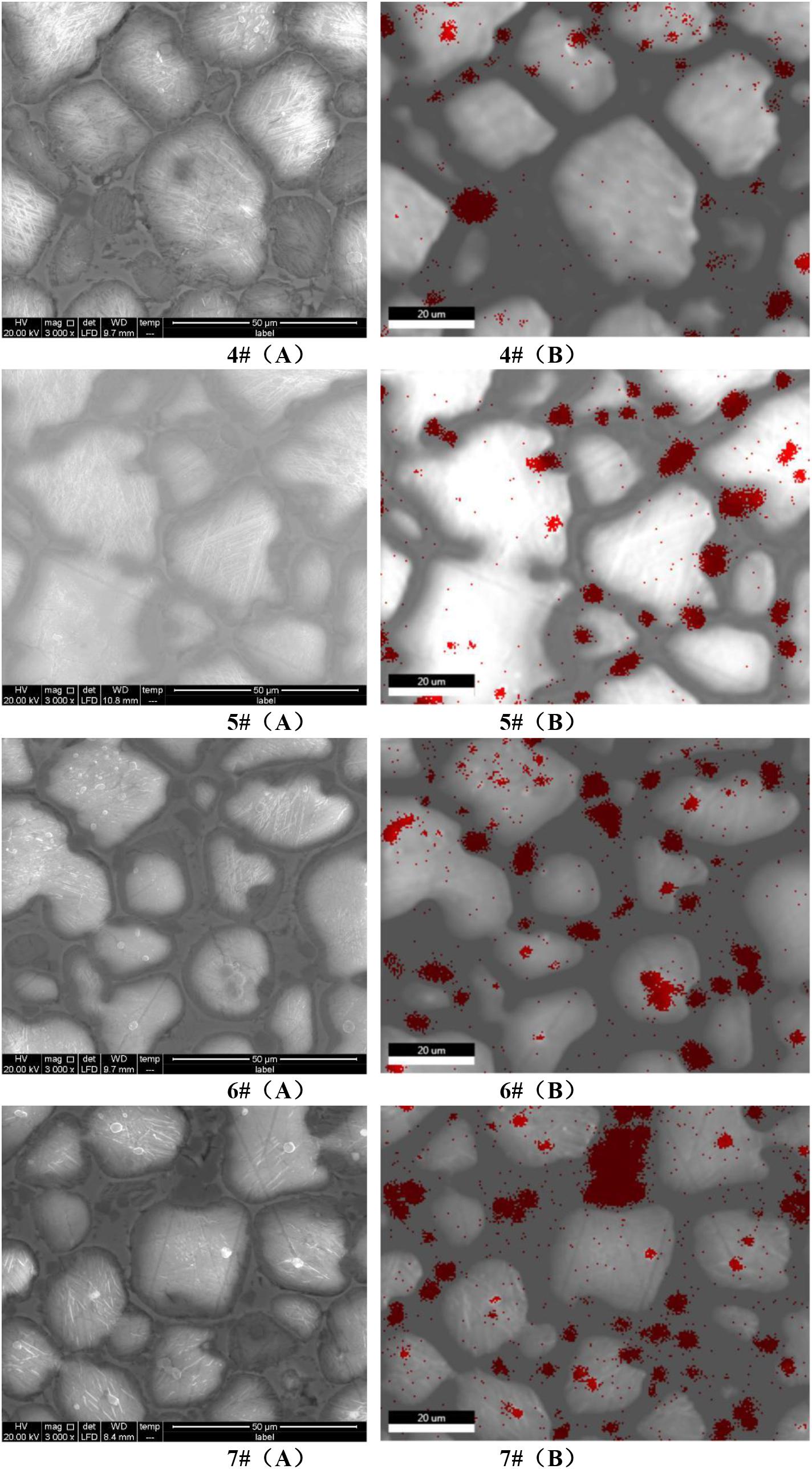
Figure 1. Comparison diagrams of point scanning and map scanning of cement clinker with different MgO contents (A) and (B) of each number represent the point scanning diagram and the Mg element distribution diagram, respectively; the red part in the diagrams represent the distribution of Mg element.
Experimental and Analytical Methods
Preparation of PSS
To reduce the influence of different chemical and physical properties in different elements, magnesian analytical-grade reagents including Mg(OH)2⋅3MgCO3⋅3H2O, Mg(OH)2, Mg3(PO4)2, MgSO4 and MgSiO3 were used as the raw materials for the PSS preparation. The materials were tableted, calcined at a certain temperature (300, 400, 500, 600, 700, 800, 900, 1000 and 1400°C) in a high-temperature furnace for 1 h and then taken out for rapid cooling to room temperature (approximately 20–25°C). The calcined product was ground into powder with the size within 45 μm and then stored and sealed in the desiccator.
XRD Analysis
The prepared PSS powder was pressed into tablets for the XRD analysis. The D8 ADVANCE X-ray powder diffractometry produced by Bruker AXS (Germany) was used for the XRD analysis. The instrument parameters are as follows: the tube voltage was 38 kV, the tube current was 40 mA, the target material was CuKα, the scanning range was approximately 5°–70°, the scanning speed was 5°/min and the step length was 0.02°.
Autoclave Test
According to the GB/T 750-1992 autoclave method for soundness of Portland cement, the sample to be tested was mixed and stirred evenly; subsequently, it was placed in the curing chamber at 20 ± 2°C for 24 h. After curing, the sample was taken out and placed into a box to be boiled for 3 h. The FZ-31 Leishi boiling box was produced by Hebei Kexi Instrument and Equipment Co., Ltd. (China). YZF-20 autoclave produced by Wafangdian Jianke Test Instrument Manufacturing Co., Ltd. (China) was used to autoclave the sample after being boiled.
TGA
The lateral section of the sample after the autoclave test was cut out, and the internal fresh part was selected to be ground into powder with a maximum size of 45 μm. The STA 449 F3 Jupiter synchronous TG-DSC thermal analyser produced by the NETZSCH Group (Germany) was used to conduct TGA on the ground material, with a temperature range from 50 to 1000°C and a heating rate of 10 K/min.
Chemical Analysis
Samples for the chemical analysis were prepared as that for TGA. According to the GB/T 176-2017 methods for the chemical analysis of cement, the f-CaO content in the powder was determined.
Optimisation of Experimental Conditions
In order to determine the autoclave pressure ‘P’ and the time ‘t’ required to complete the hydration of periclase in cement, the cement with MgO content of 7.48% was selected to quantitatively determine its periclase content by using the method described in this paper under different autoclave pressures (2.0, 2.2 and 2.4 MPa) and different times (3.0, 3.5, 4.0, 4.5 and 5.0 h).
Determination Method of Recovery Rate
In order to verify the reliability of the determination method described in this paper, PSS was added into seven kinds of cements with MgO contents of 1.61, 2.72, 3.26, 4.75, 5.58, 7.48 and 8.59%, respectively, according to the mass ratio of the cement to PPS, i.e. 95 to 5 g. Subsequently, they were evenly stirred to obtain a mixed cement that was used to determine the periclase content. The recovery rate of PSS was employed to verify the accuracy of this determination method.
Testing of Expansion Rate
The expansion rate of the cement after 90 days of curing (with different MgO contents) can indirectly demonstrate the changes occurring in the periclase content of the cement. According to the JC/T 313-2009 test method for determining the expansion ratio of expansive cement, the prepared cement paste was demoulded after 24 h and cured in water at 20 ± 1°C to a specified age (1, 3, 7, 14, 21, 28, 60, 90 and 360 days); this was achieved after the initial length was measured using the BC156-300 comparator manufactured by Wuxi Jianyi Instrument and Machinery Co., Ltd. (China). The measurement range of the comparator was approximately 275–300 mm, and the accuracy was 0.01 mm. The length of the cement paste was measured and its expansion rates at different curing ages were calculated. E360d is the expansion rate of the cement paste on the 360th day, E28d is the expansion rate of the cement paste on the 28th day and α is the later expansion increasing rate after 90 days of curing, which is calculated using Formula (1) expressed in percentage.
Results and Discussion
Preparation of PSS
Determination of Magnesian Raw Materials
The XRD patterns of different magnesium raw materials calcined in a furnace at 1000°C for 1 h are shown in Figure 2. Based on this figure, it can be seen that the XRD diffraction peaks of calcined Mg(OH)2⋅3MgCO3⋅3H2O and calcined Mg(OH)2 are in very close proximity to those of periclase (Yang and Yue, 2000), indicating that the calcined products are pure MgO. The XRD diffraction peak of calcined MgSO4 reached the periclase diffraction peak, indicating that the calcined product is a mixture of MgO and is not pure. Periclase diffraction peak is not observed in the XRD diffraction peaks of calcined Mg3(PO4)2 and calcined MgSiO3, indicating that these calcined products do not contain MgO. Therefore, the PSS should be prepared by calcining analytical-grade reagents Mg(OH)2⋅3MgCO3⋅3H2O or Mg(OH)2.
Determination of Calcination Temperature
The XRD patterns of the calcined products of Mg(OH)2⋅3MgCO3⋅3H2O and Mg(OH)2 at different calcination temperatures are separately shown in Figures 3, 4, respectively. It can be seen from Figures 3, 4 that the XRD diffraction peaks of the calcined products are in close proximity to those of periclase when Mg(OH)2⋅3MgCO3⋅3H2O or Mg(OH)2 was calcined at temperatures above 500°C (Yang and Yue, 2000), indicating that the calcined products at this temperature comprise pure MgO. Given that the density of MgO obtained by calcination at different temperatures is different (Liu et al., 2006), in order to obtain MgO with similar properties as those of periclase in cement, it is appropriate to select 1400°C as the calcination temperature for preparing PSS. In order to facilitate a better comparison, the method described in this paper uniformly selects the calcined product of analytical-grade reagent Mg(OH)2 at 1400°C as the PSS.
Technique for the Quantitative Determination of Periclase Content
Determination Principle and Steps
A new technique for the quantitative determination of periclase in HMPC is established by combining the autoclave test, TGA and chemical analysis, with PSS as the internal standard. Its basic principle involves the utilisation of the autoclave test to prepare the periclase in cement; subsequently, it is completely hydrated to form an Mg(OH)2 product (Kasselouris et al., 1985; Ali and Mullick, 1998) under high temperature and pressure. A TG-DSC thermal analyser is used to determine the total content of Mg(OH)2 and Ca(OH)2 in the autoclaved cement product (Yang and Yue, 2000). The chemical analysis method is adopted to detect the content of f-CaO in the autoclaved cement product, which is then converted into Ca(OH)2 in the autoclaved cement product. The Mg(OH)2 content in the autoclaved cement product can be obtained by calculating the difference in the values of these two contents [the content of Ca(OH)2 and the total content of Ca(OH)2 and Mg(OH)2]; subsequently, the periclase content in cement can be obtained.
The determination of periclase in HMPC includes the steps I to V.
I. The to-be-tested cement, PSS and water were mixed according to the mass ratio of 95 g:5 g:25 g and then stirred evenly to prepare the MCPS.
II. After being cured for 24 h in the 20 ± 2°C curing chamber, the MCPS was boiled in the boiling box for 3 h and autoclaved under pressure P for a certain time t.
III. The lateral section of the MCPS was cut out after the autoclave test and the internal fresh region was selected to be ground into powder with a maximum size of 45 μm. The f-CaO content of the powder was detected by using the chemical analysis method. Subsequently, the Ca(OH)2 content in the autoclaved product of MCPS was calculated according to Formula (2). The weight loss value within the range of 300–600°C in the autoclaved product of MCPS was analysed by using the TG-DSC thermal analyser.
where MrCa(OH)2 represents the relative molecular mass of Ca(OH)2 and MrCaO represents the relative molecular mass of CaO. ω1 is the content of f-CaO obtained by chemical analysis of the autoclaved product of MCPS and ω2 is the content of Ca(OH)2 in the autoclaved product of MCPS. ω1 and ω2 are both expressed as percentages.
IV. The to-be-tested cement and water were mixed according to the mass ratio of 95 g:25 g and then stirred evenly to prepare the TCPS. Steps II and III were repeated to obtain the content of Ca(OH)2 in the autoclaved product of TCPS according to Formula (3) and the weight loss value within the range of 300–600°C.
where ω3 is the content of f-CaO obtained by chemical analysis of the autoclaved product of TCPS and ω4 is the content of Ca(OH)2 in the autoclaved product of TCPS. ω3 and ω4 are both expressed as percentages.
V. According to the Ca(OH)2 content and the weight loss values within the range of 300–600°C in autoclaved products of MCPS and TCPS, respectively, the content of periclase in the to-be-tested cement was calculated.
It is assumed that the content of periclase in the to-be-tested cement is ω, which is expressed as a percentage; the total mass of hydration products from the autoclaved to-be-tested cement is x1, in which the mass of Mg(OH)2 is x2, the mass of the hydration product formed by autoclaving PSS is x3 and the hydration product is just Mg(OH)2. The weight loss value of the autoclaved product of MCPS and TCPS within the temperature of 300–600°C is ω5 and ω6, respectively. The content of Mg(OH)2 in TCPS is the ω7 value expressed as a percentage and the content of Mg(OH)2 in MCPS is the ω8 value expressed as a percentage. Based on the above results, Formulae (4)–(8) were obtained.
According to Formulae (4)–(8), the content of periclase in the to-be-tested cement can be obtained by calculation, which is shown in Formula (9).
Optimisation of Experimental Conditions
Under different experimental conditions, including autoclave pressure P and autoclave time t, the content of periclase in cement 6# was determined. The experimental plan and results are shown in Table 4. It can be seen from Table 4 that the detected content of periclase in cement 6# increased when the autoclave pressure or autoclave time was appropriately increased, indicating that further hydration of periclase in the cement could be promoted under both situations. When the autoclave pressure reached 2.2 MPa and the autoclave time reached 4 h, the detected content of periclase in the cement basically remained unchanged if the pressure or time was further increased. This result indicated that the periclase in the cement had been completely hydrated. Therefore, for the quantitative determination of periclase in HMPC described in this paper, the autoclave pressure should be 2.2 MPa and the autoclave time should be 4 h.
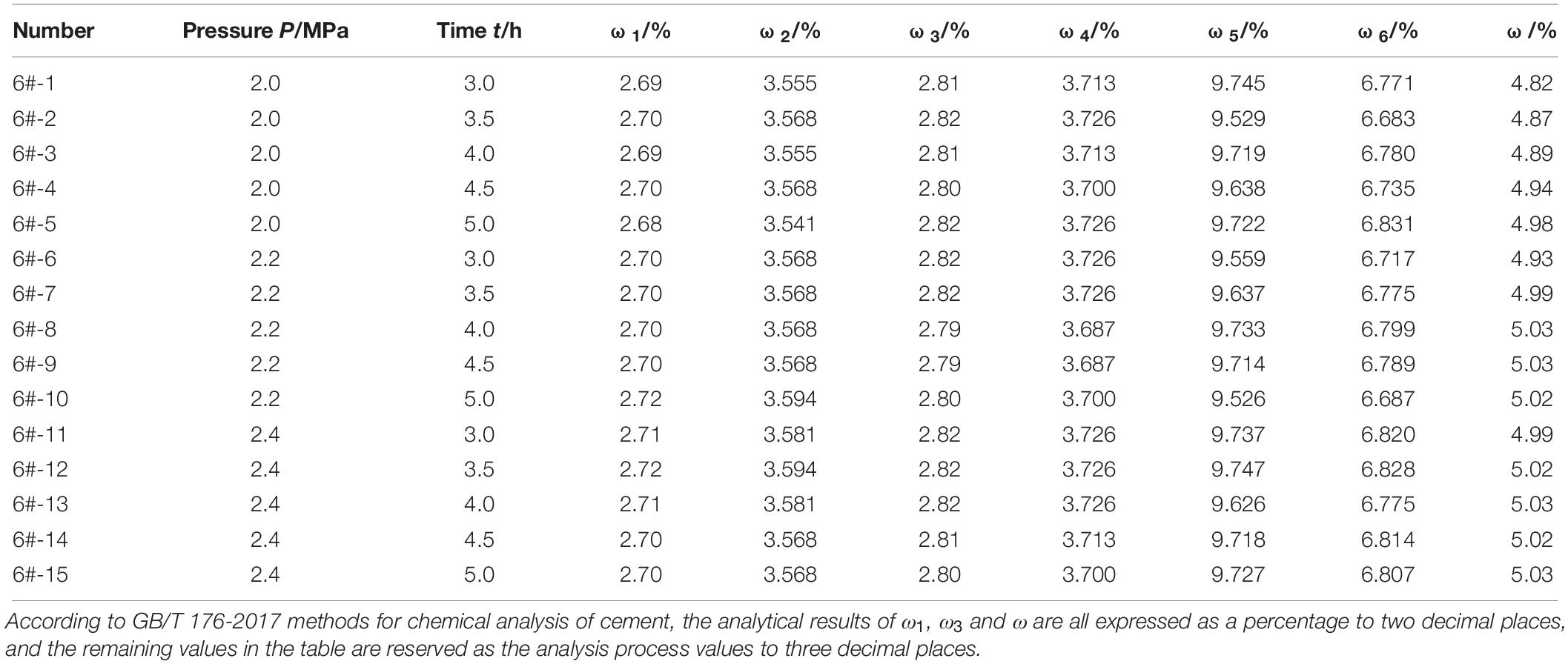
Table 4. Determined contents of periclase in cement 6# under different autoclave pressures and autoclave time.
Determination of Recovery Rate
Through the above tests, the quantitative determination method of periclase in HMPC and its related conditions (autoclave pressure P and autoclave time t) were determined. It is assumed that ω9 represents the content of periclase in the mixed cement, which was prepared by evenly mixing the to-be-tested cement and PSS in accordance with the mass ratio of 95 g:5 g; m represents the practical recovery content of PSS, and its unit is g; ω10 represents the recovery rate of PSS, where ω9 and ω10 are expressed as percentage. In light of the above, Formulae (10)–(12) can be obtained.
According to Formulae (4), (5), (7), (8) and (10), ω9 can be obtained as the content of periclase in mixed cement, which is shown in Formula (13).
The determination results and recovery rates are shown in Table 5. It can be seen from Table 5 that with the increase in the MgO content in cement, the content of periclase also increased, which is consistent with the SEM results shown in Figure 1. The recovery rate of PSS in cement with different MgO contents ranged from 99.92 to 100.14%, showing a good recovery effect and a relatively high accuracy.
Expansion Rate of the Cement
In order to verify the change rule of periclase content in cement, the expansion of the cement with different MgO contents at different ages were studied, as shown in Figures 5, 6. It can be seen from Figures 5, 6 that with the increase in the MgO content, the expansion of each cement at each age improved, while the later expansion increasing rate improved first and then decreased. As shown in Figure 1, the increase in the MgO content in cement increased the periclase content, so the expansion rate and the later expansion increasing rate were also on the rise, which is consistent with the change rule of the periclase content measured by the quantitative determination technique described in this paper in Table 5. With further increase in the periclase content, the crystal size of periclase increased, as shown in Figure 1, and the hydration rate slowed, which resulted in a decrease in the later expansion increasing rate.
Conclusion
In order to overcome the determination inaccuracy of the periclase content in cement, a new technique combining several methods for the quantitative determination of periclase content in HMPC was demonstrated, and the accuracy of this technique was evaluated with the recovery rate. The main conclusions drawn are as follows:
1. A quantitative technique for determining the content of periclase in HMPC was established by combining the autoclave test, TGA and chemical analysis, with PSS as the internal standard. The method of “autoclave test” can ensure the complete hydration of periclase in the to-be-tested cement. The method of “TGA” can effectively avoid the interference of the fused MgO in cement. The method of “chemical analysis” can eliminate the influence of Mg(OH)2 and Ca(OH)2 (induced by the partial overlapping of their decomposition temperatures during TGA) on the determination result of periclase content.
2. In this technique, the analytical-grade reagents magnesium carbonate basic [Mg(OH)2⋅3MgCO3⋅3H2O] or magnesium hydroxide [Mg(OH)2] calcined at 1400°C should be selected as PSS. The autoclave pressure should be 2.2 MPa and the autoclave time should be 4 h.
3. This technique presents a recovery rate ranging from 99.92 to 100.14%, showing a good recovery effect and a relatively high accuracy. Therefore, this technique can be used to evaluate the expansion of HMPC and can serve as a guide for different projects in choosing HMPC according to the project’s practical application demand.
Data Availability Statement
The raw data supporting the conclusions of this article will be made available by the authors, without undue reservation.
Author Contributions
ZM conducted the majority of the test and wrote the initial draft manuscript. YY was the project coordinator and designed the experiment. ZL, LW, and BW conducted partial experiment. ZW and CL collected the data and revised the manuscript. All authors contributed to the article and approved the submitted version.
Funding
The authors gratefully acknowledge the funding from the National Key Research and Development Program of China (No. 2016YFB0303601) and China Scholarship Council. This research was supported by the State Key Laboratory of Green Building Materials of China Building Materials Academy.
Conflict of Interest
BW was employed by the company Guangxi Yufeng Group Co., Ltd., CL was employed by the company China Three Gorges Corporation.
The remaining authors declare that the research was conducted in the absence of any commercial or financial relationships that could be construed as a potential conflict of interest.
Abbreviations
f-CaO, free calcium oxide; FE-SEM, field emission scanning electron microscope; HMPC, high magnesia Portland cement; MCPS, mixed cement paste sample; PSS, periclase standard substance; TCPS, to-be-tested cement paste sample; TGA, thermogravimetric analysis; TG-DSC, thermogravimetric analysis–differential scanning calorimetry; XRD, X-ray powder diffraction.
References
Ali, M. M., and Mullick, A. K. (1998). Volume stabilization of high MgO cement: effect of curing conditions and fly ash addition. Cem. Concr. Res. 28, 1585–1594. doi: 10.1016/s0008-8846(98)00140-9
Arjunan, P., and Kumar, A. (1994). Rapid techniques for determination of free lime and free magnesia in cement clinker and portlandite in hydrates. Cem. Concr. Res. 24, 343–352. doi: 10.1016/0008-8846(94)90061-2
Cao, Y., Wu, H., Xu, M., and Jiang, M. (2017). Determination of periclase content in cement with chemical Method. Res. Appl. Build. Mater. 4, 1–5.
Chen, F., and Xu, L. (2010). Quantitative method view of periclase in cement. Mater. Rep. 24, 193–195. doi: 10.3901/CJME.2010.02.195
Deng, L., Cai, P., and Du, J. (2015). Calculation of the periclase content in cement clinker by Rietveld full-spectrum fitting method. Cement 11, 56–58.
Kasselouris, V., Ftikos, C., and Parissakis, G. (1985). On the hydration of MgO in cement pastes hydrated up to eight years. Cem. Concr. Res. 15, 758–764. doi: 10.1016/0008-8846(85)90140-1
Katyal, N. K., Ahluwalia, S. C., Parkash, R., and Sharma, R. N. (1998). Rapid estimation of free magnesia in OPC clinker and 3CaO:SiO2 system by complexometry. Cem. Concr. Res. 4, 481–485. doi: 10.1016/s0008-8846(98)00027-1
Liu, G., Ma, L., and Liu, J. (2006). Data Manual for Chemical and Physical Properties (Inorganic). Beijing: Chemical Industry Press, 256.
Mo, L., Deng, M., Tang, M., and Tabbaa, A. A. (2014). MgO expansive cement and concrete in China: past, present and future. Cem. Concr. Res. 57, 1–12. doi: 10.1016/j.cemconres.2013.12.007
Rehsi, S. S., and Majumdar, A. J. (1968). Quantitative determination of uncombined MgO in Portland cement clinker by X-Ray diffractometry. J. Appl. Chem. 18, 297–300. doi: 10.1002/jctb.5010181003
Ruan, S., Kastiukas, G., Liang, S., and Zhou, X. (2020). “Influence of early oven curing on the alkali activated binders with reactive magnesia replacement,” in Proceedings of the RICON19 – REMINE International Conference on Valorization of Mining Andindustrial Wastes into Construction Materials by Alkali-Activation, Covilhã, (Dubai: KnE Engineering), 207–214.
Ruan, S., and Unluer, C. (2017a). Effect of air entrainment on the performance of reactive MgO and PC mixes. Construct. Build. Mater. 142, 221–232. doi: 10.1016/j.conbuildmat.2017.03.068
Ruan, S., and Unluer, C. (2017b). Influence of supplementary cementitious materials on the performance and environmental impacts of reactive magnesia cement concrete. J. Clean. Prod. 159, 62–73. doi: 10.1016/j.jclepro.2017.05.044
Ruan, S., and Unluer, C. (2017c). Influence of mix design on the carbonation, mechanical properties and microstructure of reactive MgO cement-based concrete. Cem. Concr. Compos. 80, 104–114. doi: 10.1016/j.cemconcomp.2017.03.004
Wang, C., Yan, M., and Deng, M. (2019). Effects of cooling condition on the periclase in the low heat Portland cement clinker. J. Nanjing Tech. Univ. (Nat. Sci. Ed.) 41, 440–444.
Wang, X., Ma, Z., and Liu, Y. (2013). Research progress of the high-magnesia cement. Mater. Rep. 27, 302–304.
Xu, M., Wu, H., Chen, H., Chen, Y., Cao, Y., and Yang, K. (2017). Determination the periclase content in cement by the PONKCS method. New Build. Mater. 10, 28–34.
Xu, Y., Meng, H., Zuo, L., Zhu, X., and Lu, X. (2016). Determination of the content of periclase in cement clinker by ammonium nitrate method. Coal Ash. 6, 37–41.
Xu, Y., Xu, L., and Li, W. (2014). Quantitative determination of periclase and periclase hydration in high magnesium cement clinker with XRD internal standard method. J. Nanjing Tech. Univ. (Nat. Sci. Ed.) 36, 30–35.
Yang, N., and Yue, W. (2000). Mapping Manual of Inorganic Nonmetallic Materials. Wuhan: Wuhan University of Industry Press, 207.
Ye, Q., Chen, H., Wang, Y., Wang, S., and Lou, Z. (2004). Effect of MgO and gypsum content on long-term expansion of low heat Portland slag cement with slight expansion. Cem. Concr. Compos. 26, 331–337. doi: 10.1016/s0958-9465(02)00145-2
Yu, J. (1998). Quick determination of free magnesium oxide in cement clinker by electrical conduction. Cem. Eng. 4, 42–43.
Keywords: periclase content, quantitative determination, periclase standard substance, autoclave, thermogravimetric analysis, chemical analysis
Citation: Ma Z, Yao Y, Liu Z, Wei L, Wu B, Wen Z and Lu C (2020) A New Technique to Quantitatively Determine the Periclase Content in High Magnesia Portland Cement. Front. Mater. 7:225. doi: 10.3389/fmats.2020.00225
Received: 23 May 2020; Accepted: 22 June 2020;
Published: 24 July 2020.
Edited by:
Shaoqin Ruan, Zhejiang University, ChinaReviewed by:
Tingting Zhang, Dalian University of Technology, ChinaYongshan Tan, Nanjing University of Aeronautics and Astronautics, China
Copyright © 2020 Ma, Yao, Liu, Wei, Wu, Wen and Lu. This is an open-access article distributed under the terms of the Creative Commons Attribution License (CC BY). The use, distribution or reproduction in other forums is permitted, provided the original author(s) and the copyright owner(s) are credited and that the original publication in this journal is cited, in accordance with accepted academic practice. No use, distribution or reproduction is permitted which does not comply with these terms.
*Correspondence: Zhongcheng Ma, bWF6aG9uZ2NoZW5nLmNvbUAxNjMuY29t; Zhicheng Liu, emhpY2hlbmcubGl1LjE1QHVjbC5hYy51aw==