- 1School of Materials and Mineral Resources Engineering, Universiti Sains Malaysia, Nibong Tebal, Malaysia
- 2Mechanical Engineering Department, Engineering Faculty, Universitas Sebelas Maret, Surakarta, Indonesia
- 3Cluster for Polymer Composites, Science and Engineering Research Center, Universiti Sains Malaysia, Nibong Tebal, Malaysia
Non-woven kenaf fiber (KF) mat reinforced acrylic-based polyester resin composites were prepared by an impregnation process followed by compression molding. They were exposed to durability test of accelerated weathering and water absorption. Accelerated weathering test through UV irradiation caused modification in chemical, mechanical, surface appearance, and color change of the composites. Two competing reactions occurred throughout the exposure period, i.e., post-crosslinking and photo-oxidation process. FTIR analysis revealed that the former occurred at the early stage of exposure while the latter toward the end of the exposure, exhibited by an accentuated increase in carbonyl and vinyl index. The post-crosslinking process contributes to the improvement in flexural properties and thermal stability of the composites, whereas the oxidation process does not. SEM observation showed that the degradation by photo-oxidation resulted in the formation of voids and blisters on composite's sample. Water uptake of all composites was found to follow Fickian behavior. Good recoveries (exceeding 79%) of flexural properties were obtained upon re-drying. However, a significant reduction in flexural strength and modulus was obtained in the wet state condition. SEM observation revealed that full recovery was not possible because of the impairment of the—matrix interfacial region. Relatively higher flexural properties were exhibited by alkali-treated KF composites even after the durability test due to the improved strength and—matrix adhesion following the treatment.
Introduction
The increase in environmental awareness is the vital factor that motivates many researchers to explore and develop new alternatives capable of replacing traditional polymer composite materials. The new alternatives (called “green composites”) should have a lower negative environmental impact than the traditional polymer composite materials. Green composites can be defined as materials composed of, in part or wholly, constituents which come ultimately from a renewable resource (Baillie and Jayasinghe, 2004). This definition applies to the matrix and reinforcement phase. Thus, by definition, natural fiber that reinforces polymer composites (NFPC) can be called green composites because the reinforcing fibers come from renewable sources. These fibers usually originated from some abundant plants, which make them inexpensive. Compared to inorganic-mineral like glass fiber, natural fibers are less abrasive toward processing machinery and tooling, less dangerous to the production employees in case of inhalation, and easy to be incinerated. They also lead to final composites with lower specific weight per strength, as well as, exhibiting thermal and acoustic insulation properties (Herrera-Franco and Valadez-González, 2004).
Current environmental concerns have stimulated interest in the recycling. Recyclability of NFPC is depending on the polymer matrices component either thermoplastic or thermosetting. Thermoplastics are easily recyclable as compared to thermosets because the polymer chain does not degrade when melted down, allowing this material to be reprocessed. On the other hand, thermoset matrix recycling is unfeasible because of the thoroughly cross-linked nature. Nevertheless, recent technologies are now being deployed in recycling thermoset composites. Recently, recycling thermoset composites could be carried out through mechanical recycling by grinding the thermoset composites into smaller particles/powder in order to be used as filler in other composites system or by thermal recycling for energy recovery (Pickering, 2006).
The industries are exploiting NFPC because of their lightweight characteristic and are cost-effective. These attributes make them as potential alternative materials to the expensive aramid, carbon, or glass fibers. Improved technology in manufacturing techniques in NFPC allows the automotive industry to use these composites for interior trimmings (Koronis et al., 2013). The first carmaker to use natural fibers as reinforcement in composites was Mercedes-Benz in the 90's, by manufacturing door panels from epoxy reinforced jute fibers composites (Rohit and Dixit, 2016). This trend was soon adopted by other major carmakers to fabricate various interior trimmings including roof upholstery, headrests, parcel shelves, and spare wheel cover using NFPC. Depending on the applications, it is sometimes necessary to improve the mechanical properties through the fiber pre-treatment, and the treated fibers are then used in several ways to obtain mats, non-woven structures, rowing etc. Among various types of natural fiber, kenaf fibers (KF; Hibiscus cannabinus) are largely grown in Malaysia because of climate suitability. The mechanical properties of KF are more or less identical to jute but are considered stronger, whiter and more lustrous (Umoru et al., 2014). The tensile strength and modulus are comparable to flax fiber, widely used in automotive parts of European cars (Karus and Kaup, 2002). Realizing the potential of KF for the manufacturing industry, the Malaysia government believe that this crop plant could be the third commodity plant of the nation after rubber and palm oil (Salim et al., 2019). The National Kenaf and Tobacco Board (NKTB) of Malaysia are playing a prominent role in promoting the usage of KF in various industries, including the automotive industry, in Malaysia.
Based on the polymer matrices point of view, the automotive industry demands a crucial characteristic and high selective polymer material in fulfilling the requirement of high thermal stability and short processing time. Several works on conventional thermoset resins, such as polyester and vinyl ester, reported that these resins could reinforce natural fibers (Ariawan et al., 2017; Navaneethakrishnan and Athijayamani, 2017). However, the major drawback of these resins is the emission of styrene that occurs not only during processing, but also from the finished products. This limits the usage of these resins in the automotive industry, especially in the manufacturing interior trimmings for passenger cars (Islam and Miao, 2013). The introduction of environmentally friendly acrylic-based polyester resin by the trade name of Acrodur® resin by BASF has emerged as a new verdict in polymer binder technology. Dissimilar with traditional reactive resins, organic substances, for example, phenol or formaldehyde, are not released during the cross-linking process. Only water is the by-product during the cross-linking process (Karbstein et al., 2013). Below the crosslinking temperature, the resin exhibits thermoplastic properties allowing the resin to be processed using thermoplastic processing means. After the curing process, the material has thermoset properties with good chemical resistance, heat resistance and high structural integrity. The combination of ease processing, good mechanical properties, and environmentally friendly gives Acrodur® resin the enormous potential to be used as an alternative material in the automotive industry besides polyolefin thermoplastic. A prototype of natural fiber Acrodur® composites for the door trim of BMW 7 series has been developed recently by Dräxlmaier Group, Germany (Malnati, 2010).
In any application, the durability of materials is a serious concern. Environmental exposure, including sunlight exposure and moisture uptake during actual service, tends to degrade the natural fiber, especially at the exposed region. Besides, it degrades the polymer matrices that might deteriorate the mechanical properties of NFPC or even worse contribute to the parts failure during service. Durability in terms of environmental exposure is measured through the changes in mechanical performance, thermal, chemical, and the material appearances after experiencing a certain period of weathering test. Some commonest damaging effects in the composites are color fading, surface erosion, mechanical properties and weight losses which might shorten the service life of the product (Lopez et al., 2006). Water absorption property is another major factor that should be considered when dealing with NFPC. The characteristics of water absorption in NFPC are influenced by several factors: fiber content, fiber orientation, temperature, exposed surface area, fiber permeability, void content, and the hydrophilicity of individual components (Dhakal et al., 2007). The degradation of the fiber-matrix interface region due to the water absorption contributes to the reduction of stress transfer proficiencies; therefore, the mechanical properties of NFPC (Yang et al., 2011).
The properties of NFPC composites are determined by the constituent properties i.e., fiber and matrix as well as the properties of the fiber-matrix interface (Pothan et al., 2003). Excellent fiber-matrix interaction leads to an effective distribution of stress and load between fiber and matrix thus improving the mechanical strength of composites (Akil et al., 2011). The surface of the natural fibers can be modified physically or chemically. However, the fundamental principle still remain the same i.e., removing the surface contamination and providing an intimate contact between the surfaces on a molecular scale (Mukhopadhyay and Fangueiro, 2009). The effective method is to roughen the surface of natural fiber to increase the contact area and facilitate mechanical interlocking (Edeerozey et al., 2007). Such surface modification would not only enhance the wettability of fibers toward polymer matrix that might improve the composite's strength, but would concurrently decrease the moisture absorption of the composites.
Alkali treatment or mercerization is one of the common chemical treatments that are proven to enhance the mechanical properties of the reinforced composites in several studies (Krishnan et al., 2018; Sepe et al., 2018). This treatment is by far the most efficient chemical treatment to improve the wettability of fibers toward resin and enhancing the fiber strength. It is interesting to discover that some studies reported a dramatically improve of natural fiber's tensile strength after elevated alkali treatment (Rong et al., 2001; Saha et al., 2010). Van de Weyenberg et al. (2006) pointed out that the enhancement of flexural and tensile properties of alkali treated flax fiber reinforced epoxy composites that they obtained were combination of better mechanical interlocking by the rougher topography, larger number of individual fibrils, and better chemical bonding owing to more hydroxyl groups on the fiber surface enable to form hydrogen bonds with the matrix resin. Besides improving the mechanical properties of NFPC, Sreekumar et al. (2009) also reported that alkali treated sisal fiber reinforced polyester composites absorbed less water at all water temperatures during hygrothermal test compared to the untreated one due to the removal of hydrophilic hemicellulose during alkalization. Heat treatment can be considered as an alternative ecological treatment as it does not required any usage of hazardous chemical. Several researchers found that this treatment has great influence in changing the mechanical properties, biological properties, color, hardness, and chemical properties of wood as lignocellulosic materials (Gündüz et al., 2008; Ates et al., 2009). In composite applications, previous research by Sreekumar et al. (2009) revealed that heat treatment of sisal fibers at 100°C for 4 h increased crystallinity and removed moisture in sisal fibers. This treatment resulted in the increase of tensile and flexural properties of sisal fiber composites, without significantly reducing the impact strength of composites like the alkali treatment, benzoylated, and permanganate treatment. In terms of durability toward natural weathering exposure, Ariawan et al. (2018) reported that alkali treated KF composite shows better durability compared to the heat treated KF composite particularly for the first 6 months exposure. However, they found that prolonged natural weathering exposure diminishes the effect of fiber treatment in enhancing mechanical properties.
To date, there have been several works done on the usage of Acrodur® resin in NFPC (Islam and Miao, 2013; Khalfallah et al., 2014; Salim et al., 2017). However, to the best of our knowledge, studies concerning weathering exposure to Acrodur® reinforced natural fiber composites have not been done. Previous study by the author has focused on the effect of fiber treatments toward the wettability and mechanical properties of Acrodur® reinforced KF composites (Salim et al., 2019). Pursuant to that work, the current study aims to investigate the effect of fiber surface treatments i.e., alkali treatment, alkali treatment at elevated temperature and heat treatment toward the durability properties of the composites under an accelerated weathering exposure. This could be crucial in order to seek the viability of the composites to be used in automotive industry. Furthermore, excellent fiber to matrix adhesion following these treatments also might decrease the rate amount of water absorbed by the composites. Thus, the effect of surface treatment on water absorption properties of KF reinforced Acrodur® composites will also be reported in the current study.
Materials and Methods
Materials
Untreated kenaf fiber (UTKF) was supplied by the National Kenaf and Tobacco Board (NKTB), Malaysia. These fibers then underwent a needle punching process to form a non-woven KF mat with an areal density of 1,350 g/m2. The preparation of the mats was given elsewhere (Salim et al., 2011). Acrodur® resin 950 L used in this study was obtained from BASF. This resin is an aqueous acrylic resin based on modified polycarboxylic acid and a polyalcohol (crosslinking agent) that create a polyester thermoset material upon curing by crosslinking reaction at a temperature above 130°C (Figure 1).
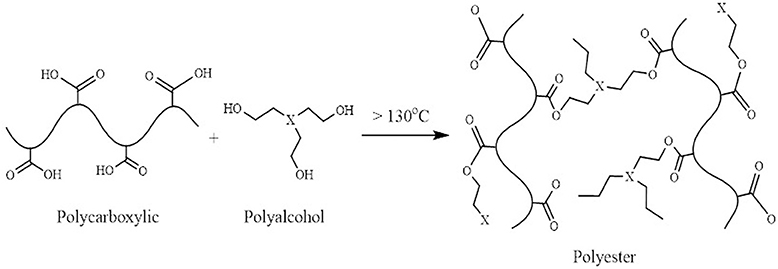
Figure 1. Crosslinking reaction of Acrodur® resin (Islam and Miao, 2013).
Fiber Pre-treatment
Alkali treatment of KF in the form of non-woven mats was done by soaking the mats for 3 h in 6% NaOH solution. Post-treatment, the KF mats were rinsed with 1% acetic acid solution to neutralize the excess of NaOH followed by washing with distilled water before drying process in an oven for 24 h at 60°C. For elevated alkali treatment, similar procedure was applied except the treatment was executed in hot alkali solution at 60°C. The treatment was done in a water bath to ensure uniform heat application during the treatment. Heat treatment of NWKF was conducted by heating the non-woven KF mat at 140°C for 10 h inside air circulation oven based on optimum heat treatment of KF suggested by Ariawan et al. (2014).
Composite Preparation
Non-woven KF reinforced Acrodur® composites were prepared by resin impregnation process as reported elsewhere (Ahmad Rasyid et al., 2019). Post-impregnation, the semi-finished material (prepreg) was dried inside a vacuum oven at 60°C until the residual moisture was 15%. The prepregs were then compression molded using GOTECH model GT7014-H hydraulic hot press machine at 210°C with a pressure of 10 bar to produce the composite laminate. These parameters was selected based on the previous work by Salim et al. (2017). The composite samples were prepared with a fixed volume fraction of 45% Vf. Untreated KF composites, alkali- treated KF composites, alkali-treated KF composites at elevated temperature (60°C) and heat- treated KF composites are referred to as the UTKC, ATKC, AHTKC, and HTKC, respectively.
Accelerated Weathering Test
The composite samples were subjected to accelerated weathering test using Q-SUN Xe-3 xenon arc chamber from Q-Lab (USA) according to SAE J2412 standard, i.e., accelerated exposure of automotive interior trim components using a controlled irradiance xenon-arc apparatus. The samples were fixed on the chamber tray and were subjected to accelerated weathering through dark and light cycle alternately with parameters as tabulated in Table 1 until 1,500 h of total exposure time. Such exposure time was selected based on SEM analysis where significant changes appeared on the composites surfaces. The average UV irradiance was set to 0.55 W/m2 at 340 nm wavelength and window filter was used to simulate the actual condition inside a passenger car. The samples were collected after 500 h interval of exposure time to determine the degree of degradation. Before the mechanical test, the samples were cleaned using a dry cloth and re-conditioned for 24 h at room temperature inside a desiccator.
Water Absorption
The water absorption study was conducted following ASTM D 570. Flexural samples were used to measure weight changes during the water absorption test. Initially, the samples were dried at 60°C for 24 h followed by their cooling to room temperature inside a desiccator. Then the samples were submerged into distilled water at room temperature. The weight changes overtime were taken periodically until equilibrium was achieved, meaning, no further increment to the sample's weight was observed. The water uptake percentage of the specimens was calculated at different time intervals by using Equation (1):
where, M (%) is the water uptake, Mt is the weight of the wet sample at a given time, and Mo is the initial weight of the sample. Diffusion coefficient (D) was evaluated from the slope of moisture content vs. the square root of the time by Equation (2):
where, M1 and M2 are the water content (percentage weight) at times t1 and t2, respectively, Mm is the maximum weight gain (%), and h is the thickness of composites (mm). Flexural test was then conducted on the wet and re-dried samples to evaluate the residual and recovery properties of the composites, respectively.
Physical Test
The color change of all samples was determined before and after UV irradiation at every 500 h intervals using a portable spectrophotometer Konica Minolta Chroma Meter model CR-400 (Japan) equipped with a CIELAB system. The CIELAB system measurement consists of three parameters, namely L*, a*, and b*, where L* represents lightness, which varies from 100 (white) to 0 (black), and a* and b* are the chromaticity indices, with +a* representing the red direction, –a* as green, +b* as yellow, and –b* as blue. The changes in a*, and b*, L* were calculated based on Equations (3)–(5), respectively.
where ΔL*, Δa*, and Δb* are the differences in the initial and final values of a*, b*, and L*, respectively, a1, b1, and L1 are the initial color parameters; and a2, b2, and L2 are the color parameters after UV irradiation exposure. The total change in color (ΔE*) was calculated based on ASTM D2244 using the Euclidean formula as shown in Equation (6). Lower ΔE* value corresponds to a smaller color difference and indicates strong resistance to UV radiation. The measurement was done at five locations on each sample, and the average values were calculated.
The chemical changes of the composites due to the accelerated weathering exposure were determined using a Fourier Transform Infrared Spectroscopy (FT-IR, Perkin-Elmer Spectrum One, USA), using potassium bromide (KBr) pellet method. Prior to the characterization, the discolored area of the exposed region (composite surface) was scraped off using scraping knife and thoroughly mixed with KBr. This mixture was compressed into pellets before FT-IR analysis. The transmittance spectra were recorded within the range of 400–4,000 cm−1 wavelength with a spectral resolution and number of scans of 1 cm−1 and 32 scans, respectively. The carbonyl and vinyl indexes were then calculated using the following Equations (7) and (8), respectively (Satoto et al., 1997).
where I1,720 and I914 are the intensity peak of carbonyl and vinyl, respectively. These peaks were normalized to I2,920 peak, attributed to the alkane stretching vibration of the methylene group (-C-H-) that was chosen as the reference peak.
Meanwhile surface appearance of composites after accelerated weathering and water absorption test were observed using FESEM model FEI Verios 460L. Fracture surface observation by FESEM also was conducted to investigate fiber-matrix adhesion and KF structure within the composites after water absorption test. All samples characterized by SEM were mounted on aluminum stubs and sputter-coated with gold before observation at a pressure of 2 mbar for 1 min.
Mechanical Testing
Flexural strength and modulus of the composites before and after the durability tests were determined using the three-point bending test method with sample geometry of 130 × 13 × 3 mm following the ASTM D790 standard and maintaining a span to depth ratio of 16:1. The test was conducted using Instron 5969 universal testing machine (USA) with a crosshead speed of 2 mm/min at room temperature and 50% relative humidity. The strength and modulus values given are the means from five individual samples.
Thermal Testing
The changes in thermal properties before and after the durability test were analyzed using Thermogravimetric analysis (TGA). The analysis was conducted using a Perkin Elmer Pyris Diamond TGA analyzer at a heating rate of 10°C/min at the room temperature range to 600°C. An average sample weight of 15 mg of each composite specimen was analyzed under an inert atmosphere of nitrogen gas.
Results and Discussions
Accelerated Weathering Exposure
In this study, a Q-SUN Xe-3 weathering chamber using a xenon arc lamp was used to simulate sunlight irradiation. The xenon arc lamps produced the most realistic reproduction of full-spectrum sunlight, including ultraviolet (UV), visible light (VL), and infrared (IR) radiation. Regarding UV radiation, the spectrum can be subdivided into several ranges defined most broadly as a 10–400 nm wavelength. On the other hand, the bond dissociation energy of most polymeric matrices is within the range of 290–400 nm (Feldman, 2002; Gu, 2008). This wavelength lies in the same region of the UV-A and UV-B wavelengths, which is between 320 and 400 nm and between 280 and 320 nm, respectively. Therefore, several chemical reactions might occur, mainly on the exposed surface of composites as a result of these UV irradiations that might influence the mechanical properties of the composites.
FT-IR Analysis
Figures 2A–D exhibits the FT-IR spectra of composites before and after accelerated weathering exposure for 500, 1,000, and 1,500 h. Similar major absorbance peaks for the spectrums before and after exposure could be observed but with different intensities, indicating the same characteristic of chemical constituents within the composites. However, the presence of some additional peaks particularly after accelerating weathering test suggests some modifications did occur due to the exposure. Table 2 summarizes the characteristics of the absorption peak of the spectrums.
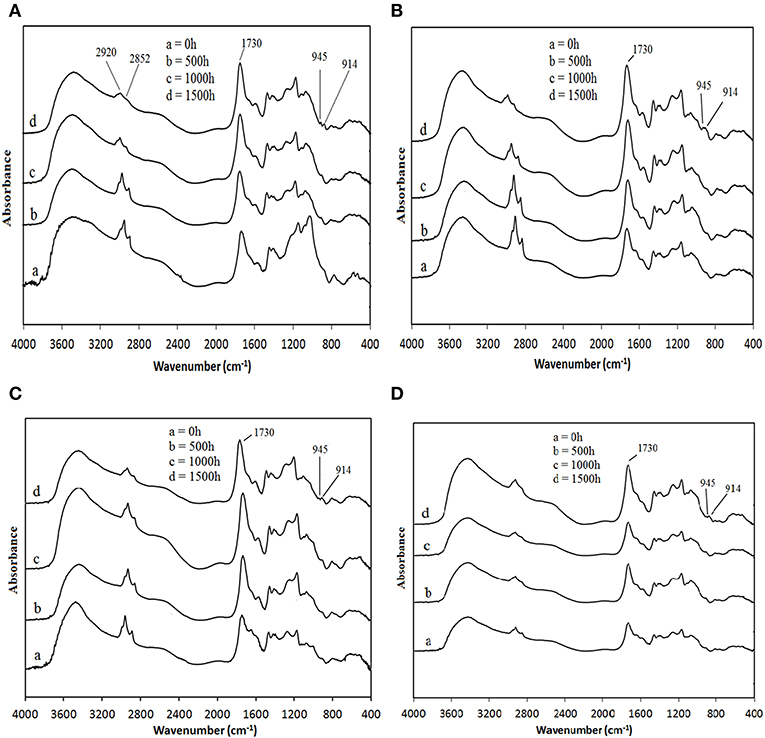
Figure 2. FT-IR spectra of composites during weathering exposure (A) UTKC, (B) ATKC, (C) AHTKC, and (D) HTKC.
The FT-IR spectra of the weathered samples of all composites revealed some changes, especially at the peak 1,720 cm−1 corresponding to the C=O stretching vibration of carbonyl groups. The carbonyl index (CI) was calculated based on Equation (7) to gain a better insight into these changes. According to Table 3, all composites did not exhibit an accentuated increase in the carbonyl index at the first 1,000 h exposure. This result could be related to the competition between the oxidation and crosslinking processes (Gulmine et al., 2003). It seems to indicate that composite samples exposed to an accelerating weathering test below 1,000 h were favorable to undergo crosslinking process. The presence of chromophoric carbonyl groups within the polymer chain absorbs solar UV radiation and producing free radicals. These polymer radicals are then terminated via bimolecular recombination or crosslinking based on Norrish type I mechanism.
However, the CI of all composites was found to increase after 1,500 h exposure. This is due to the presence of oxidation products such as a mixture of carboxylic acid and ketone species as a result of photo-oxidative degradation of polyester (Ariawan et al., 2018). The FT-IR spectra of all composites exposed at a period of 1,500 h also showed the presence of the peaks at 945 and 914 cm−1, which represent the vinyl groups. The formation of these groups can be verified by the increased vinyl index (VI) of the composites especially after 1,500 h exposure (see Table 3). This can be attributed to carbonyl degradation as consequences of polymer chain scission in both matrix and natural fiber via the Norrish type II mechanism (Azwa et al., 2013). The generation of carbonyl and vinyl groups through polymer chain scission resulted in the reduction in molecular weight and thereby might decrease the strength, toughness and fracture strain of polymers (Noriman and Ismail, 2011). The changes in mechanical properties of the composites after accelerated weathering exposure are reported in the following section Flexural Properties.
Changes in Surface Color
The UV radiation during the weathering test promotes photo-oxidative, thermo-oxidative, and photolytic reactions that impair the polymer properties (Pillay et al., 2009). The extent of degradation ranges from minor surface discoloration affecting the aesthetic appeal in indoor applications to extensive loss of mechanical properties (Müller et al., 2003). Even though there is no precise correlation between accelerated weathering and natural weathering test, Chang and Chang (2001) reported that discoloration in the accelerated light fastness test is 250 times more severe than that in the actual indoor exposure test. The characterization of the color changes concerning the exposure time of the indoor accelerated weathering test in this study was conducted based on CIELAB color.
Figure 3 exhibits the changes in the surface color index as exposure time increases. It can be seen that the accelerated weathering exposure to the composites induced color alteration as shown by the changes in the color index components ΔL, Δa, Δb, and therefore resulting in the total color changes ΔE. As the exposure time increases, the composites only suffered minimal changes in Δa. On the contrary, all composites sustained a significant increment in ΔL and Δb which meant that the surface color became lighter and shifted toward yellow as the exposure time increases. This result is consistent with the work reported by Muasher and Sain (2006). They found that significant color fading (increased ΔL) and yellowing (increased Δb) of HDPE filled composites started to occur after exposure to a natural weathering test.
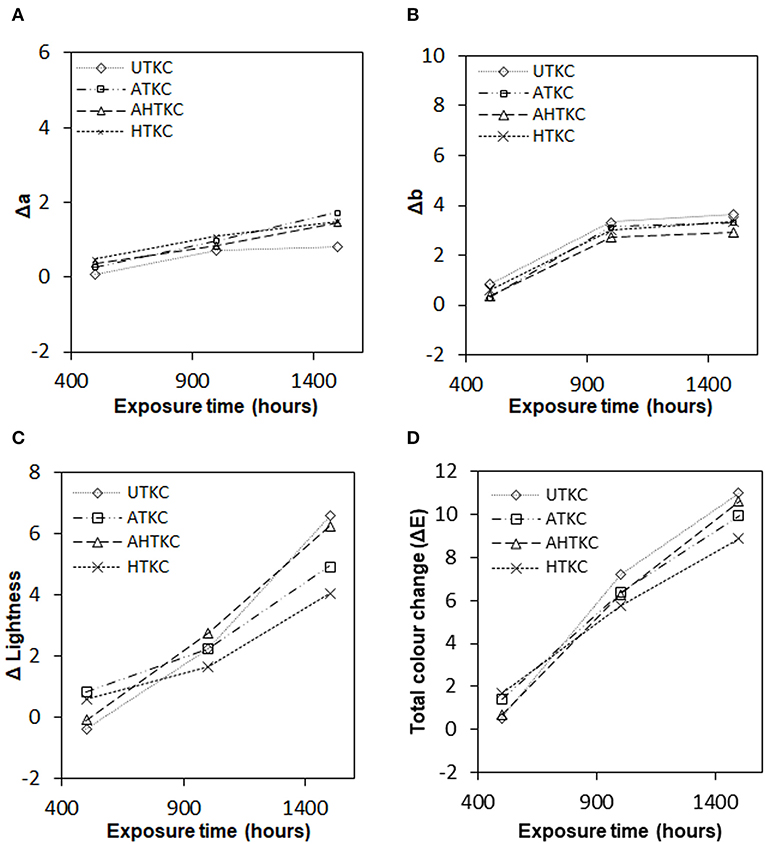
Figure 3. Effect of accelerated weathering exposure on (A) the relationship between green and red color, (B) the relationship between blue and yellow color, (C) the brightness relationship between light and dark, and (D) total color change.
Lignin is the most sensitive constituent to light in lignocellulosic material, including natural fiber that is responsible for photochemical reactions. The oxidation of lignin initiated by the absorbed UV radiation leads to the formation of a paraquinone chromophoric structure, having α-carbonyl, biphenyl, and ring-conjugated double bond structures (Butylina et al., 2012). These substances are the leading cause of discoloration, mainly giving the yellow characteristic of the exposed samples (Azwa et al., 2013). It is interesting to note that a more significant increase in ΔL for all composites occurred within the range of 1,000–1,500 h exposure time. This is attributed to the further degradation of chromophores that leads to color fading by a photobleaching process and generation of free radicals that may cause substantial degradation of lignin and photo-oxidation of cellulose and hemicellulose.
Regarding the polymeric matrix, the photochemical conversion is dependent on the spectral irradiance of the applied polychromatic light source, especially in the case of yellowing when it is the result of photodegradation and subsequent photobleaching of the chromophores causing yellowing. In general, the maximum sensitivity of polyesters (various formulations) to light spectrum is approximately at a 325 nm wavelength which lies in the region of UV-A (Rabek, 2012). Therefore, it can be presumed that the increase in the ΔL and Δb values was also contributed by the chromophores photodegradation within the polyester matrix.
Besides, high humidity applied during weathering exposure (90% RH during the light cycle) induces moisture absorption of hydrophilic cellulose and consequently promotes an oxidation reaction which facilitates the penetration of light, thereby, accelerating the photo-degradation effect in composites (Stark, 2006). The increase in total color change, ΔE of all the composites, as exposure time increases, was significantly contributed by the increase in the ΔL and Δb values.
Flexural Properties
Since the aging of polymers results from the competition between continuous crosslinking and chain scission, such competition could lead to the alteration of mechanical properties as the exposure time increases. Figures 4A,B depicts the changes in flexural strength and modulus of the composites concerning the accelerated weathering exposure. Prior to accelerated weathering test (0 h), flexural strength and modulus of AHTKC were the highest followed by ATKC, HTKC, and UTKC. This shows that fiber surface treatment could impart better flexural properties to Acrodur® composites by improving fiber to matrix adhesion. Detailed explanations of the effect of surface treatment on wettability and mechanical properties of KF reinforced Acrodur® composites could be found in the author's previous work (Salim et al., 2019). In regard to accelerated weathering exposure, a general pattern was acquired where the flexural strength and modulus of all composites were found to increase slightly as the exposure time increases. Temperature and UV radiation can either impose scission of the chemical bonds of the matrix (i.e., main C–C chain scission), leading to photo/thermo-oxidation and crazing of the material (Segovia et al., 2000) or leading to polymer post-curing (Boinard et al., 2000).
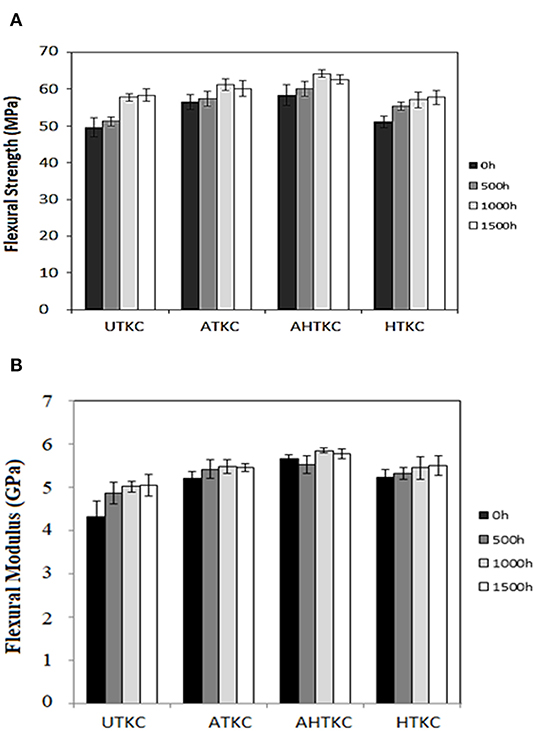
Figure 4. Flexural properties of the composites with respect to the accelerated weathering exposure time (A) flexural strength and (B) flexural modulus.
As mentioned earlier, there were competing reactions between photo-oxidation and crosslinking process of the polymer matrices in which crosslinking was more dominant to occur during the initial stage of exposure. This occurrence might very well-describe the improvement in flexural properties and thermal stability of the composites exposed to weathering test up to 1,000 h. A similar observation was described by Woo et al. (2008). They found that the tensile strength of epoxy-organoclay nanocomposites increased after UV exposure for 1,000 h. According to them, the composites tensile strength increased because of the association to the favorable chain crosslinking process that is to occur.
Additionally, previous work by the authors found that the developed Acrodur® composites did not achieve a fully cured state, and the degree of crosslinking was reported to be around 84% (Salim et al., 2018). Combination of high temperature applied, and heat emitted by the UV light might also initiate further post-curing process of the pre-polymer to form rigid polyester. This condition might also contribute to the increment of the flexural properties.
On the contrary, the notable increase in the yellowing effect, and the significant increment in CI of the composite samples exposed for 1,500 h signify the onset of degradation by photo-oxidation occurring within the polymer matrices as well as KF. This was explained by the deterioration of thermal stability and a slight reduction of flexural properties of most composites after 1,500 h exposure. The decrease in these properties was due to the scissoring of polymer macromolecules (Bagherpour et al., 2009). The UV radiation that was absorbed by the polymer matrix resulted in the formation of free radicals. Once free radicals have been produced, reaction with oxygen generates hydroperoxides that can dissociate further to produce a series of decompositions. Therefore, further degradation of the composites was expected to occur if the exposure period exceeded 1,500 h.
Figure 5 exhibits the SEM images of the composites before and after the accelerated weathering exposure for 1,500 h. The observation that was made, based on the color changes and SEM images, suggests that the composites endured yellowing but not cracking. However, the formation of blister and sink marks were observed on the composite's surface. According to Kaczmarek (1996), during UV irradiation of polymers, volatile degradation products are removed from the specimen surface, leaving behind pit or pore-type structures. In this current study, the formation of this structure could also be because of water evaporation during the post-curing process. Furthermore, during the light cycle, application of high temperature (70°C) and heat radiation from UV evaporated uncured substances leaving voids on the surface of the composite. The presence of blisters and sink marks could accelerate further degradation by providing pathways for oxygen diffusion into the specimen bulk for the photo-oxidation process to occur (Signor et al., 2003).
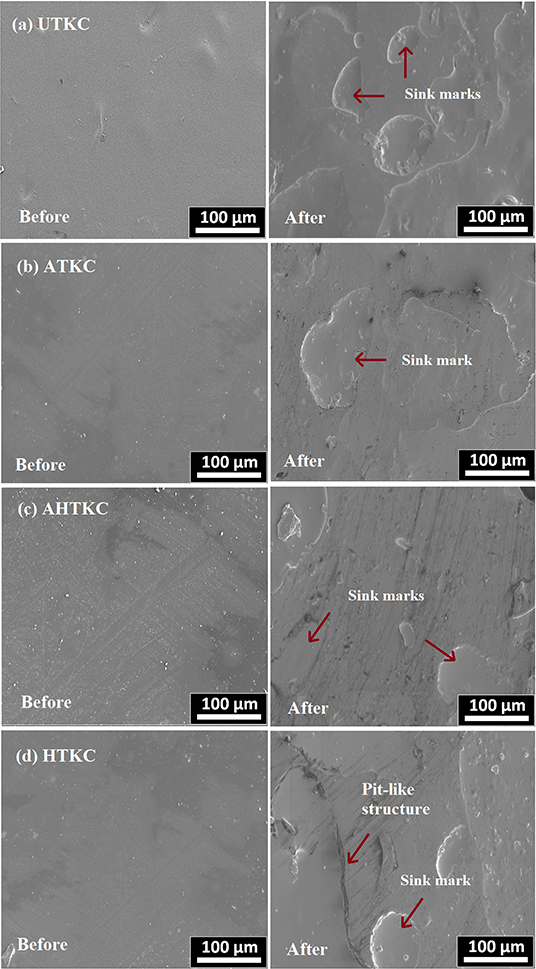
Figure 5. SEM images of surface appearance before and after weathering test for (a) UTKC, (b) ATKC, (c) AHTKC, and (d) HTKC.
The flexural properties of the composites, however, were barely affected from 1,000 to 1,500 h of exposure time (see Figures 4A,B) even in the presence of blisters and voids. It should be noted that the defects mainly occur on the composite's surface. For that reason, the reinforcing ability of treated KF could still impart better flexural properties to the composites. As can be seen in Figure 4, AHTKC still exhibits the highest flexural strength and modulus followed by ATKC, HTKC, and UTKC throughout exposure time. The effectiveness of the surface treatment in improving the flexural properties of the composites was found to sustain after the weathering test.
Since the indoor condition of the accelerated weathering test was applied in the current study, no water spray cycle was conducted to simulate rain. This might result in a slower degradation rate. Zhao et al. (2010) reported a more severe degradation of polyester under accelerated weathering for an outdoor application using a similar xenon arc lamp that involved water spray for 12 min followed by 108 min dry condition with the RH value of 65%. The formation of crack was recorded as early as 400 h exposure. The presence of water might also accelerate the degradation mechanism (Bagherpour et al., 2009).
Thermal Properties
Thermogravimetric analysis (TGA) and the rate of derivative thermogravimetric analysis (DTG) curves for unexposed samples and weathered samples are shown in Figures 6A–D, while Table 4 summarizes the thermal properties of the corresponding samples. Surprisingly, the accelerated weathering exposure was found to impart slight improvement in the thermal stability of the composite at least for the initial stage of exposure. This can be seen by the gradual increment of onset degradation temperature (Tonset) as well as the temperature at which 10% degradation occurs (T10) of the composites for the first 1,000 h. This occurrence could be related to the polymer matrices post-curing as well as crosslinking process initiated by UV radiation that are more favored to occur over oxidation, especially during the first 1,000 h. The obtained result is in parallel with the previous FT-IR analysis that suggests the degradation by photo-oxidation was presumed to occur dominantly only after 1,000 h. This can be shown by the significantly increased CI of the composites samples that were exposed for 1,500 h as presented earlier in Table 3. In the literature, Ding and Liu (2006) also reported an increase in thermal stability of polyurethane sealant after exposure to UV-A radiation. They also found that the post-curing that occurred increased the tensile and hardness properties of the sealant.
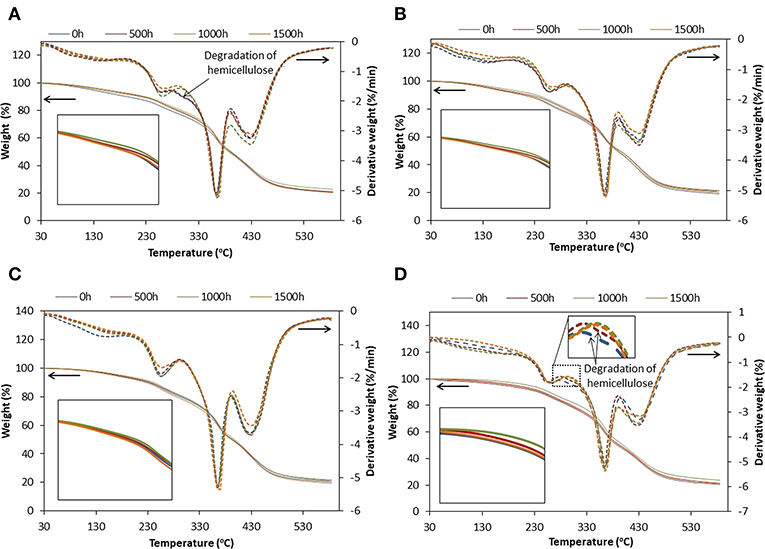
Figure 6. TGA and DTG curves of composites after accelerated weathering exposure (A) UTKC, (B) ATKC, (C) AHTKC, and (D) HTKC.
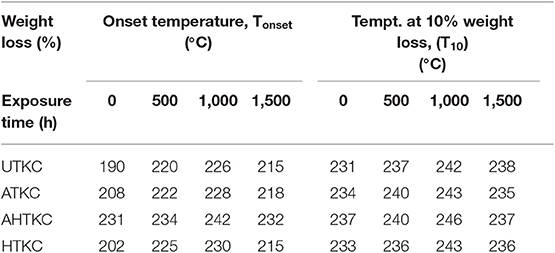
Table 4. Thermal properties of composites with respect to exposure time of accelerated weathering test.
The DTG curves of the unexposed and exposed composite samples generally exhibited similar decomposition stages with some noticeable changes after exposure. The first stage of weight losses for the composites occurs at 80°C and above due to the moisture evaporation from the composites constituent of KF and Acrodur® resin. Within the temperature 180–280°C, the weight losses of the composites were due to the decomposition of lower boiling point components of polyester as well as some portion of hemicellulose, pectin and wax (Shebani et al., 2008). Since the degradation range of hemicellulose is between 220 and 320°C (Azwa et al., 2013), further decomposition of hemicellulose residual could also be detected by a small weight loss between 280 and 320°C for the unexposed sample of UTKC (see Figure 6A) and HTKC (see Figure 6D). This stage was not visible in alkali-treated KF composites of ATKC and AHTKC because of the absence of hemicellulose content in the KF and the elimination of this constituent during alkalization. It is interesting to note that this decomposition stage was also found to disappear for UTKC and HTKC samples that were exposed for 1,000 and 1,500 h. This indicates that the degradation of hemicellulose could occur during accelerated weathering by UV radiation via photo-oxidation.
The last stage of the decomposition of the composites is related to the degradation of the cross-linked acrylic polymer of the matrix resin that occurs at temperature between 280 and 525°C. The degradation stage at a temperature between 380 and 520°C was attributed to the decomposition of the cross-linked acrylic polymer (Akpan et al., 2017). The degradation rate at this stage could give a probable insight into the crosslinking formation that might occur by the post-curing and crosslinking process during weathering exposure. As it can be seen, the degradation peak of the composites exposed at 500 h and 1,000 exhibit higher intensity in the DTG curve compared to the unexposed samples and exposed samples at 1,500 h. This occurrence is generally applied to composites, which signifies that the post-curing and crosslinking process are most likely to occur at the initial stage of exposure while photo-oxidation that occurs at the final stage of exposure causes degradation of polyester.
Water Absorption Properties
Kinetic of Water Absorption
Figure 7 shows the water absorption curves for the composites. All samples exhibited a typical Fickian behavior, i.e., rapid water uptake at the initial stage, and later a saturation level was attained without any further increase in water absorption. Generally, the maximum water uptake for KF reinforced composite (UTKC) in this current study was found to be significantly lower by almost 50% compared to KF/hemp reinforced Acrodur® composite reported by Medina and Schledjewski (2009).
However, the water uptake is higher, compared to other types of thermosetting resin and thermoplastic resin composites. Several studies have reported that the maximum water uptake of unsaturated polyester/KF composite of comparable fiber loading is in the range of 10–25% (Nosbi et al., 2010; Mazuki et al., 2011). Meanwhile, the water uptake for PP/kenaf fiber composites is within the range of 10–18% (Law and Ishak, 2011). This difference is because of the water-based property of Acrodur® resin. Before curing, the resin is hydrophilic and water-soluble. After thermally cured, besides providing rigidity and strength to the resin, the formation of crosslinking upon curing imparts hydrophobicity properties. During the composites' fabrication process, it is not applicable to obtain a complete curing reaction as it requires exposing the fiber at a high temperature (210°C) over a more extended period which might degrade the natural fiber. Indeed, Khalfallah et al. (2014) reported that the optimum degree of curing of Acrodur®/flax tape composite that is suitable in the automotive industry is 72%. Based on this, higher water uptake to Acrodur® KF composites can be expected as the uncured resin tends to be dissolved during water immersion, creating more voids to be filled up with water molecules.
Table 5 summarizes the maximum water uptake (Mm) and diffusion coefficient (D) of Acrodur® composites. It is interesting to note that fiber surface treatment could provide some improvement in reducing the water absorption properties of the composites. ATKC and AHTKC exhibit a significant reduction in Mm by 25 and 30% and a slight decrease in D by 5 and 12% compared to UTKC, respectively. This may be attributed to the removal of hemicellulose and lignin during alkalization in which the removal was more effective by the application of heat as in the case of AHTKC composites. Hemicellulose is considered to be mainly responsible for water uptake, even though non-crystalline cellulose and lignin might also play an essential role in the water absorption process.
Furthermore, during alkalization, the amorphous waxy cuticle layer of the fibers, which holds the water molecules is removed, thereby limiting water containment in the composites (Sreekala et al., 2002). As a result, the maximum water uptake, Mm of the alkali treated KF composites was relatively lower compared to UTKC composite. Sreekala et al. (2002) explained that the water absorption is not only dependent on the fiber and matrix structures, but also the fiber–matrix interface. Alkali treatment to KF promotes the activation of hydroxyl groups of the cellulose unit by breaking the hydrogen bond, leading to good fiber/matrix interaction. Excellent interaction between the fibers and matrix might reduce the void along the interface, which consequently inhibits water penetration and reducing the D and Mm values of the alkali-treated KF composites. It is worth noting that HTKC exhibited a considerably lower D value with 1.34 × 10–11 m/s2. This could be due to the swelling, and cell shrinking that contributed to less water absorption by cell walls (Ates et al., 2009). Despite that, the Mm value of HTKC was relatively higher than ATKC and AHTKC. Therefore, this signifies high total water uptake at the saturation level is contributed by water containment at the interfacial region because of poor fiber-matrix wettability.
Flexural Properties
Table 6 shows the flexural properties of the composites in wet and re-dried states. Water absorption causes a dramatic reduction in the flexural strength and flexural modulus of all composites. The significant reduction in flexural strength of composites could be associated with fiber swelling that compromises fiber-matrix interfacial bonding (Dhakal et al., 2007). Also, the water molecules act as plasticisers that reduce the rigidity of the cellulose structure and thus, the flexural modulus of the reinforced composites (Akil et al., 2009). Notwithstanding, slightly better retention strength in ATKC and AHTKC as compared to UTKC and HTKC were observed. This could be attributed to the improved fiber–matrix bonding which minimizes the adverse effect of the interfacial region by the water molecules penetration.
The flexural properties of all the composites exhibit good recovery (exceeding 79%) upon re-drying, suggesting that the role of water as plasticiser has been removed or has a reversible physical process. As stated by Bera et al. (2007) the re-drying process reduces the plasticization effect in composite constituents. However, full recovery of the flexural properties could not be achieved. This might be due to the defects or flaws imposed by water penetration and during the re-drying process.
Figures 8A–D exhibits the SEM images of composites surfaces while Figures 9A–D shows the fracture surfaces of the composites after being subjected to the water absorption test, followed by the re-drying step. The formation of micro-cracks and micro-voids observed on the surfaces of the composites might explain the reduction in flexural properties following the test. Notably, UTKC and HTKC exhibit a slightly better recovery percentage of flexural strength and flexural modulus upon re-drying compared to ATKC and AHTKC. The result suggests that water penetration, followed by re-dying, might reduce or diminish the treatment effect in enhancing fiber to matrix adhesion in ATKC and AHTKC. As stated by Dhakal et al. (2007) water absorption by hydrophilic KF could lead to interfacial de-bonding in the composites. This could be proven by the occurrence of a crack at an interfacial region that occurs in all composites regardless of the treatment applied, shown in Figure 9. However, AHTKC still exhibits the highest flexural strength and modulus compared to all composites. As observed in the SEM image of AHTKC fracture surfaces (see Figure 9C), there was still matrix resin that remained intact or adhered to KF. This could provide some reinforcing effect of the KF to the composites.
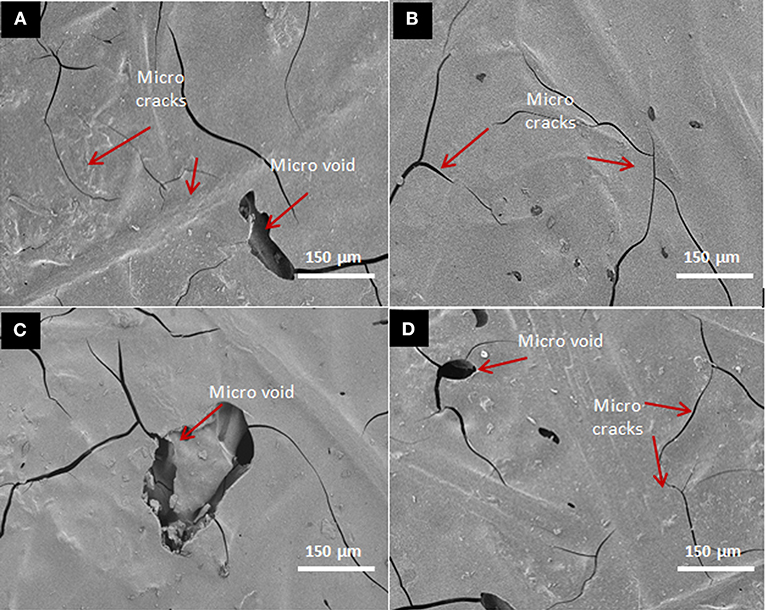
Figure 8. SEM images of composites surfaces after water absorption test (A) UTKC, (B) ATKC, (C) AHTKC, and (D) HTKC.
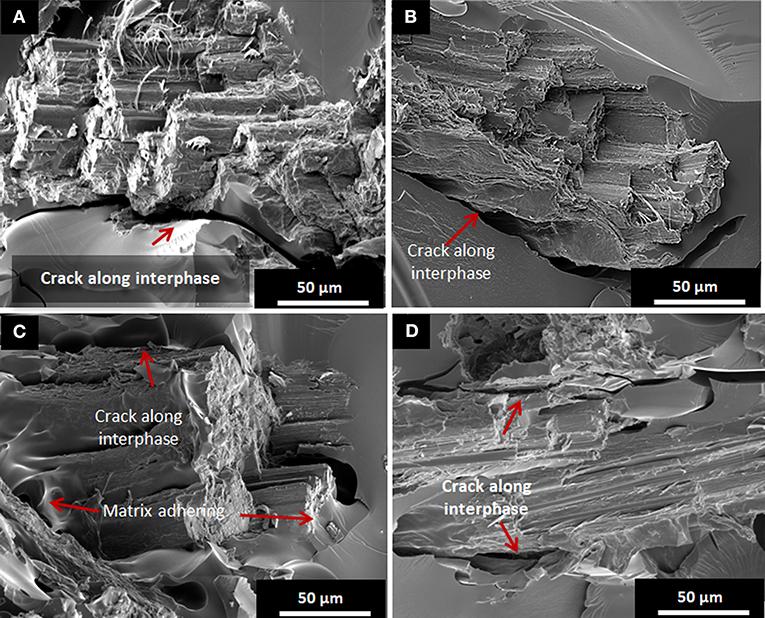
Figure 9. SEM images of flexural fracture surfaces after water absorption test (A) UTKC, (B) ATKC, (C) AHTKC, and (D) HTKC.
Conclusions
The current study analyses the effects of accelerated weathering and water absorption test of KF reinforced Acrylic-based polyester resin with the trade name of Acrodur®. The post-crosslinking process that occurs during the accelerated weathering test is found to improve the flexural and thermal properties of the composites at the early stage of exposure. Toward the final stage (total exposure of 1,500 h), slight decrease in flexural properties are recorded due to the photochemical degradation. This is confirmed by the FT-IR analysis, color change measurement, and reduction in thermal stability of the composites. All composites exhibit Fickian behavior in water absorption test conducted at room temperature. The flexural properties of various composites dramatically reduce after the test. However, upon re-drying, good recovery in flexural properties could be observed in all composites exceeding 80%. Full recovery is not possible because of the formation of crack at the fiber-matrix interfacial region. The efficiency of fiber surface treatment in improving flexural properties of composite could be seen at every condition even after the accelerated weathering and water absorption tests. KF reinforced Acrodur® composites exhibit excellent durability toward solar ray radiation, but the usage of these composites in the automotive industry is limited to the interior components, because of the permanent damage to the composite induced by water absorption.
Data Availability Statement
All datasets generated for this study are included in the article/supplementary material.
Author Contributions
MS, RM, MFA, and ZM designed the experiments. MS, DA, MFA, and MZA performed the experiments. ZM supervised the work. MS, RM, and ZM wrote the paper (original draft, reviewing, and editing). All of the authors analyzed the data.
Conflict of Interest
The authors declare that the research was conducted in the absence of any commercial or financial relationships that could be construed as a potential conflict of interest.
Acknowledgments
Authors would like to acknowledge the financial support given by Universiti Sains Malaysia and the Ministry of Education by providing RUC Grant (Grant No: 1001/PBAHAN/814134) and LRGS Grant (Grant No: 1001/ PKT/8640012), respectively.
References
Ahmad Rasyid, M. F., Salim, M. S., Akil, H. M., Karger-Kocsis, J., and Mohd Ishak, Z. A. (2019). Non-woven flax fibre reinforced acrylic based polyester composites: the effect of sodium silicate on mechanical, flammability and acoustic properties. Exp. Poly. Lett. 13, 553–564. doi: 10.3144/expresspolymlett.2019.47
Akil, H. M., Cheng, L. W., Mohd Ishak, Z. A., Abu Bakar, A., and Abd Rahman, M. A. (2009). Water absorption study on pultruded jute fibre reinforced unsaturated polyester composites. Comp. Sci. Technol. 69, 1942–1948. doi: 10.1016/j.compscitech.2009.04.014
Akil, H. M., Omar, M. F., Mazuki, A. A. M., Safiee, S., Ishak, Z. A. M., and Abu Bakar, A. (2011). Kenaf fiber reinforced composites: a review. Mater. Design 32, 4107–4121. doi: 10.1016/j.matdes.2011.04.008
Akpan, E. I., Wetzel, B., and Friedrich, K. (2017). Processing and properties of short wood fiber/acrylate resin composites. Poly. Comp. 40, 91–98. doi: 10.1002/pc.24604
Ariawan, D., Mohd Ishak, Z. A., Mat Taib, R., Ahmad Thirmizir, M. Z., and Phua, Y. J. (2014). Effect of heat treatment on properties of kenaf fiber mat/unsaturated polyester composite produced by resin transfer molding. Appl. Mech. Mater. 699, 118–123. doi: 10.4028/www.scientific.net/AMM.699.118
Ariawan, D., Salim, M. S., Mat Taib, R., Ahmad Thirmizir, M. Z., and Mohammad Ishak, Z. A. (2018). Durability of alkali and heat-treated kenaf fiber/unsaturated polyester composite fabricated by resin transfer molding under natural weathering exposure. Adv. Poly. Technol. 37, 1420–1434. doi: 10.1002/adv.21801
Ariawan, D., Salim, M. S., Mat Taib, R., Ahmad Thirmizir, M. Z., and Mohd Ishak, Z. A. (2017). Interfacial characterisation and mechanical properties of heat treated non-woven kenaf fibre and its reinforced composites. Comp. Interfaces 6440, 1–17. doi: 10.1080/09276440.2017.1354562
Ates, S., Hakan Akyildiz, M., and Hasan Ozdemir, B. (2009). Effects of heat treatment on calabrian pine. BioResources 4, 1032–1043.
Azwa, Z. N., Yousif, B. F., Manalo, A. C., and Karunasena, W. (2013). A review on the degradability of polymeric composites based on natural fibres. Mater. Design 47, 424–442. doi: 10.1016/j.matdes.2012.11.025
Bagherpour, S., Bagheri, R., and Saatchi, A. (2009). Effects of concentrated HCl on the mechanical properties of storage aged fiber glass polyester composite. Mater. Design 30, 271–274. doi: 10.1016/j.matdes.2008.04.078
Baillie, C., and Jayasinghe, R. (2004). Green Composites: Polymer Composites and the Environment. Woodhead Publishing Series in Composites Science and Engineering. Cambridge, UK: Elsevier Science.
Bera, T., Mula, S., Ray, P. K., and Ray, B. C. (2007). Effects of thermal shocks and thermal spikes on hygrothermal behavior of glasspolyester composites. J. Reinforced Plast. Comp. 26, 725–738. doi: 10.1177/0731684409076732
Boinard, E., Pethrick, R. A., Dalzel-Job, J., and Macfarlane, C. J. (2000). Influence of resin chemistry on water uptake and environmental ageing in glass fibre reinforced composites-polyester and vinyl ester laminates. J. Mater. Sci. 35, 1931–1937. doi: 10.1023/A:1004766418966
Butylina, S., Hyvärinen, M., and Kärki, T. (2012). A study of surface changes of wood-polypropylene composites as the result of exterior weathering. Poly. Degrad. Stabil. 97, 337–45. doi: 10.1016/j.polymdegradstab.2011.12.014
Chang, H.-T., and Chang, S.-T. (2001). Correlation between softwood discoloration induced by accelerated lightfastness testing and by indoor exposure. Poly. Degrad. Stabil. 72, 361–365. doi: 10.1016/S0141-3910(01)00039-8
Dhakal, H. N., Zhang, Z. Y., and Richardson, M. O. W. (2007). Effect of water absorption on the mechanical properties of hemp fibre reinforced unsaturated polyester composites. Comp. Sci. Technol. 67, 1674–1683. doi: 10.1016/j.compscitech.2006.06.019
Ding, S. H., and Liu, D. Z. (2006). Durability evaluation of building sealants by accelerated weathering and thermal analysis. Construct. Build. Mater. 20, 878–881. doi: 10.1016/j.conbuildmat.2005.06.026
Edeerozey, A. M. M., Akil, H. M., Azhar, A. B., and ZainalAriffin, M. I. (2007). Chemical modification of kenaf fibers. Mater. Lett. 61, 2023–2025. doi: 10.1016/j.matlet.2006.08.006
Feldman, D. (2002). Polymer weathering: photo-oxidation. J. Polym. Environ. 10, 163–173. doi: 10.1023/A:1021148205366
Gu, H. (2008). Degradation of glass fibre/polyester composites after ultraviolet radiation. Mater. Des. 29, 1476–1479. doi: 10.1016/j.matdes.2007.07.010
Gulmine, J. V., Janissek, P. R., Heise, H. M., and Akcelrud, L. (2003). Degradation profile of polyethylene after artificial accelerated weathering. Poly. Degrad. Stabil. 79, 385–397. doi: 10.1016/S0141-3910(02)00338-5
Gündüz, G., Korkut, S., and Korkut, D. S. (2008). The effects of heat treatment on physical and technological properties and surface roughness of camiyani black pine (pinus nigra arn. subsp. pallasiana var. pallasiana) wood. Biores. Technol. 99, 2275–2280. doi: 10.1016/j.biortech.2007.05.015
Herrera-Franco, P. J., and Valadez-González, A. (2004). Mechanical properties of continuous natural fibre-reinforced polymer composites. Comp. Appl. Sci. Manufact. 35, 339–345. doi: 10.1016/j.compositesa.2003.09.012
Islam, M., and Miao, M. (2013). Optimising processing conditions of flax fabric reinforced acrodur biocomposites. J. Comp. Mater. 48, 3281–3292. doi: 10.1177/0021998313508995
Jia, Z., Li, X., and Zhao, Q. (2010). Effect of artificial weathering on surface properties of unsaturated polyester (UP) resin. Mater. Chem. Phys. 121, 193–197. doi: 10.1016/j.matchemphys.2010.01.021
Kaczmarek, H. (1996). Changes to polymer morphology caused by u.v. irradiation: 1. Surface damage. Polym. 37, 189–194. doi: 10.1016/0032-3861(96)81086-X
Karbstein, H., Funk, J., and Norton, J. (2013). “Lightweight bio-composites with Acrodur® resin technology,” in 13th Annual Automotive Composites Conference and Exhibition (Novi, MI: ACCE), 415–431.
Karus, M., and Kaup, M. (2002). Natural fibres in the European automotive industry. J. Indust. Hemp 7, 119–31. doi: 10.1300/J237v07n01_10
Khalfallah, M., Abbès, B., Abbès, F., Guo, Y. Q., Marcel, A., Duval, F., et al. (2014). Innovative flax tapes reinforced acrodur biocomposites: a new alternative for automotive applications. Mater. Design 64, 116–126. doi: 10.1016/j.matdes.2014.07.029
Koronis, G., Silva, A., and Fontul, M. (2013). Green composites: a review of adequate materials for automotive applications. Comp. Eng. 44, 120–127. doi: 10.1016/j.compositesb.2012.07.004
Krishnan, T., Jayabal, S., and Naveen Krishna, V. (2018). Tensile, flexural, impact, and hardness properties of alkaline-treated sunnhemp fiber reinforced polyester composites. J. Nat. Fibers 17, 326–336. doi: 10.1080/15440478.2018.1492488
Law, T. T., and Ishak, Z. A. M. (2011). Water absorption and dimensional stability of short kenaf fiber-filled polypropylene composites treated with maleated polypropylene. J. Appl. Poly. Sci. 120, 563–572. doi: 10.1002/app.33184
Lopez, J. L., Sain, M., and Cooper, P. (2006). Performance of natural-fiber-plastic composites under stress for outdoor applications: effect of moisture, temperature, and ultraviolet light exposure. J. Appl. Poly. Sci. 99, 2570–2577. doi: 10.1002/app.22884
Malnati, P. (2010). Interior Innovation: The Value Proposition. Computer Technology. Available online at: https://www.compositesworld.com/articles/interior-innovation-the-value-proposition (accessed October 10, 2019).
Mazuki, A. A. M., Akil, H. M., Safiee, S., Arifin, Z., Ishak, M., and AbuBakar, A. (2011). Degradation of dynamic mechanical properties of pultruded kenaf fiber reinforced composites after immersion in various solutions. Comp. Eng. 42, 71–76. doi: 10.1016/j.compositesb.2010.08.004
Medina, L. A., and Schledjewski, R. (2009). Water glass as hydrophobic additive for natural fiber reinforced composites. J. Nanostruct. Poly. Nanocomp. 5, 107–14. Available online at: http://www.escm.eu.org/docs/eccm13/0213.pdf
Muasher, M., and Sain, M. (2006). The efficacy of photostabilizers on the color change of wood filled plastic composites. Polym. Degrad. Stab. 91, 1156–1165. doi: 10.1016/j.polymdegradstab.2005.06.024
Mukhopadhyay, S., and Fangueiro, R. (2009). Physical modification of natural fibers and thermoplastic films for composites — a review. J. Thermoplast. Comp. Mater. 135, 134–162. doi: 10.1177/0892705708091860
Müller, U., Rätzsch, M., Schwanninger, M., Steiner, M., and Zöbl, H. (2003). Yellowing and IR-changes of spruce wood as result of UV-irradiation. J. Photochem. Photobiol. Biol. 69, 97–105. doi: 10.1016/S1011-1344(02)00412-8
Navaneethakrishnan, S., and Athijayamani, A. (2017). Taguchi method for optimization of fabrication parameters with mechanical properties in sisal fibre-vinyl ester composites. Aust. J. Mech. Eng. 15, 74–83. doi: 10.1080/14484846.2015.1093258
Noriman, N. Z., and Ismail, H. (2011). The effects of electron beam irradiation on the thermal properties, fatigue life and natural weathering of styrene butadiene rubber/recycled acrylonitrile-butadiene rubber blends. Mater. Design 32, 3336–3346. doi: 10.1016/j.matdes.2011.02.020
Nosbi, N., Akil, H. M., Mohd Ishak, Z. A., and Abu Bakar, A. (2010). Degradation of compressive properties of pultruded kenaf fiber reinforced composites after immersion in various solutions. Mater. Design 31, 4960–4964. doi: 10.1016/j.matdes.2010.04.037
Pickering, S. J. (2006). Recycling Technologies for thermoset composite materials-current status. Comp. Appl. Sci. Manufact. 37, 1206–1215. doi: 10.1016/j.compositesa.2005.05.030
Pillay, S., Vaidya, U. K., and Janowski, G. M. (2009). Effects of moisture and UV exposure on liquid molded carbon fabric reinforced nylon 6 composite laminates. Comp. Sci. Technol. 69, 839–846. doi: 10.1016/j.compscitech.2008.03.021
Pothan, L. A., Oommen, Z., and Thomas, Z. (2003). Dynamic mechanical analysis of banana fiber reinforced polyester composites. Comp. Sci. Technol. 63, 283–293. doi: 10.1016/S0266-3538(02)00254-3
Rabek, J. F. (2012). Photostabilization of Polymers: Priciples and Application. Dordrecht: Springer.
Rohit, K., and Dixit, S. (2016). A review - future aspect of natural fiber reinforced composite. Poly. Renew. Res. 7, 43–60. doi: 10.1177/204124791600700202
Rong, M. Z., Zhang, M. Q., Liu, Y., Yang, G. C., and Zeng, M. H. (2001). The effect of fiber treatment on the mechanical properties of unidirectional sisal-reinforced epoxy composites. Comp. Sci. Technol. 61, 1437–1447. doi: 10.1016/S0266-3538(01)00046-X
Saha, P., Manna, S., Chowdhury, S. R., Sen, R., Roy, D., and Adhikari, B. (2010). Enhancement of tensile strength of lignocellulosic jute fibers by alkali-steam treatment. Biores. Technol. 101, 3182–3187. doi: 10.1016/j.biortech.2009.12.010
Salim, M. S., Ahmad Rasyid, M. F., Abdullah, M. A., Mat Taib, R., and Mohd Ishak, Z. A. (2018). Mechanical, thermal and flammability properties of nonwoven kenaf reinforced acrylic based polyester composites: effect of water glass treatment. IOP Confer Series Mater. Sci. Eng. 368:012040. doi: 10.1088/1757-899X/368/1/012040
Salim, M. S., Ahmad Rasyid, M. F., Mat Taib, R., and Mohd Ishak, Z. A. (2017). Processing parameters optimisation of nonwoven kenaf reinforced acrylic based polyester composites. AIP Confer. Proc. 1901:110007. doi: 10.1063/1.5010548
Salim, M. S., Ariawan, D., Ahmad Rasyid, M. F., Ahmad Thirmizir, M. Z., Mat Taib, R., Mohd, and Ishak, Z. A. (2019). Effect of fibre surface treatment on interfacial and mechanical properties of non-woven kenaf fibre reinforced acrylic based polyester composites. Poly. Comp. 40, E214–E226. doi: 10.1002/pc.24605
Salim, M. S., Ishak, Z. A. M., and Abdul Hamid, S. (2011). Effect of stitching density of nonwoven fiber mat towards mechanical properties of kenaf reinforced epoxy composites produced by resin transfer moulding (RTM). Key Eng. Mater. 471–472, 987–992. doi: 10.4028/www.scientific.net/KEM.471-472.987
Satoto, R., Subowo, W. S., Yusiasih, R., Takane, Y., Watanabe, Y., and Hatakeyama, T. (1997). Weathering of high-density polyethylene in different latitudes. Poly. Degrad. Stabil. 56, 275–279. doi: 10.1016/S0141-3910(96)00213-3
Segovia, F., Ferrer, C., Salvador, M. D., and Amigó, V. (2000). Influence of processing variables on mechanical characteristics of sunlight aged polyester-glass fibre composites. Poly. Degrad. Stabil. 71, 179–184. doi: 10.1016/S0141-3910(00)00168-3
Sepe, R., Bollino, F., Boccarusso, L., and Caputo, F. (2018). Influence of chemical treatments on mechanical properties of hemp fiber reinforced composites. Comp. Eng. 133, 210–217. doi: 10.1016/j.compositesb.2017.09.030
Shebani, A. N., van Reenen, A. J., and Meincken, M. (2008). The effect of wood extractives on the thermal stability of different wood species. Thermochim. Acta 471, 43–50. doi: 10.1016/j.tca.2008.02.020
Signor, A. W., VanLandingham, M. R., and Chin, J. W. (2003). Effects of ultraviolet radiation exposure on vinyl ester resins: characterization of chemical, physical and mechanical damage. Poly. Degrad. Stabil. 79, 359–368. doi: 10.1016/S0141-3910(02)00300-2
Sreekala, M. S., Kumaran, M. G., and Thomas, S. (2002). Water sorption in oil palm ® ber reinforced phenol formaldehyde composites. Comp. Appl. Sci. Manufact. 33, 763–777. doi: 10.1016/S1359-835X(02)00032-5
Sreekumar, P. A., Thomas, S. P., Saiter, J. M., Joseph, K., Unnikrishnan, G., and Thomas, S. (2009). Effect of fiber surface modification on the mechanical and water absorption characteristics of sisal/polyester composites fabricated by resin transfer molding. Comp. Appl. Sci. Manufact. 40, 1777–1784. doi: 10.1016/j.compositesa.2009.08.013
Stark, N. M. (2006). Effect of weathering cycle and manufacturing method on performance of wood flour and high-density polyethylene composites. J. Appl. Poly. Sci. 100, 3131–3140. doi: 10.1002/app.23035
Thirmizir, A. M. Z., Mohd Ishak, Z. A., Rahim, M. T. R. S., and Mohamad Jani, S. (2011). Natural weathering of kenaf bast fibre-filled poly(butylene succinate) composites: effect of fibre loading and compatibiliser addition. J. Poly. Environ. 19, 263–273. doi: 10.1007/s10924-010-0272-2
Umoru, P. E., Boryo, Doris, E. A., Aliyu, A. O., and Adeyemi, O. O. (2014). Processing and evaluation of chemically treated kenaf bast (Hibiscus cannabinus). Int. J. Scienti. Tech. Res. 3, 1–6. Available online at: http://www.ijstr.org/final-print/july2014/Processing-And-Evaluation-Of-Chemically-Treated-Kenaf-Bast-hibiscus-Cannabinus.pdf
Van de Weyenberg, I., Chi Truong, V. T., Vangrimde, B., and Verpoest, I. (2006). Improving the properties of UD flax fibre reinforced composites by applying an alkaline fibre treatment. Comp. Appl. Sci. Manufact. 37, 1368–1376. doi: 10.1016/j.compositesa.2005.08.016
Woo, R. S. C., Zhu, H., Leung, C. K. Y., and Kim, J.-K. (2008). Environmental degradation of epoxy-organoclay nanocomposites due to uv exposure : part II residual mechanical properties. Comp. Sci. Technol. 68, 2149–2155. doi: 10.1016/j.compscitech.2008.03.020
Yang, Y., Ota, T., Morii, T., and Hamada, H. (2011). Mechanical property and hydrothermal aging of injection molded jute/polypropylene composites. J. Mater. Sci. 46, 2678–2684. doi: 10.1007/s10853-010-5134-8
Keywords: natural fiber reinforced composites, accelerated weathering degradation, water absorption, kenaf fiber mat, Acrodur resins
Citation: Salim MS, Ariawan D, Ahmad Rasyid MF, Mat Taib R, Ahmad Thirmizir MZ and Mohd Ishak ZA (2020) Accelerated Weathering and Water Absorption Behavior of Kenaf Fiber Reinforced Acrylic Based Polyester Composites. Front. Mater. 7:26. doi: 10.3389/fmats.2020.00026
Received: 22 October 2019; Accepted: 21 January 2020;
Published: 11 February 2020.
Edited by:
Alessandro Pegoretti, University of Trento, ItalyReviewed by:
Mustapha Kaci, University of Béjaïa, AlgeriaPietro Russo, Italian National Research Council, Italy
Fabrizio Sarasini, Sapienza University of Rome, Italy
Copyright © 2020 Salim, Ariawan, Ahmad Rasyid, Mat Taib, Ahmad Thirmizir and Mohd Ishak. This is an open-access article distributed under the terms of the Creative Commons Attribution License (CC BY). The use, distribution or reproduction in other forums is permitted, provided the original author(s) and the copyright owner(s) are credited and that the original publication in this journal is cited, in accordance with accepted academic practice. No use, distribution or reproduction is permitted which does not comply with these terms.
*Correspondence: Zainal Arifin Mohd Ishak, emFyaWZpbkB1c20ubXk=