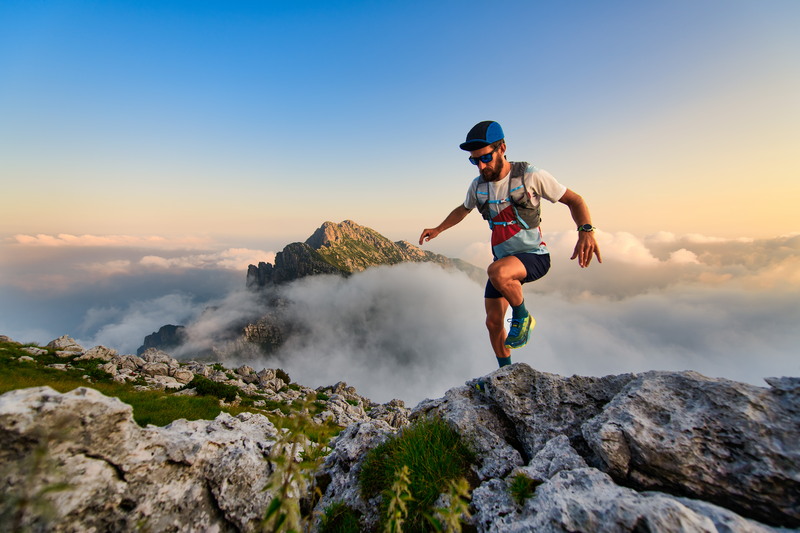
94% of researchers rate our articles as excellent or good
Learn more about the work of our research integrity team to safeguard the quality of each article we publish.
Find out more
ORIGINAL RESEARCH article
Front. Mater. , 07 February 2020
Sec. Polymeric and Composite Materials
Volume 7 - 2020 | https://doi.org/10.3389/fmats.2020.00003
This article is part of the Research Topic Biodegradable Matrices and Composites View all 25 articles
With over 1 billion tons of food waste generated annually, there is potential for the waste to be re-purposed. The generation of products from food-industry waste not only reduces the environmental burden of the materials but gives a new value to waste. A common waste material from the food industry is chicken feathers (ChF), a by-product of the chicken meat processing industry. In this work, ChF were subjected to slow pyrolysis at varying temperatures. A complete analysis was completed to determine the yield, ash, chemical composition and morphology of the samples. X-ray diffraction analysis indicated that lower temperature samples were more amorphous, whereas higher temperature samples exhibited more graphitic content. After characterization, the biocarbon was combined with poly(lactic acid) (PLA) to generate sustainable 100% biobased composites. Both composites had moduli that were more than 115% greater than that of the neat polymer. The success of the composites demonstrated that ChF biocarbon can be used as a sustainable and cost effective filler. The use of this material gives new purpose to a waste product and contributes to the goal of sustainable product development.
According to the UN Food and Agriculture Organization has reported that nearly one third of food globally is lost or wasted, equating to nearly 1.3 billion tons of waste (Food Agriculture Organization of the United Nations, 2019). Food industry waste may be generated from food or beverage processing which may consist of such things as fruit/vegetable pomace, meat processing by-products or even nut shells. The majority of meats that are mass processed globally are pork, beef and chicken. Chicken alone is estimated to have 98.4 million tons processed in 2019 (United States Department of Agriculture, 2019). This is a large amount of waste which may carry an environmental burden. It is estimated that feathers constitute 5–7 wt.% of the chicken (Onifade et al., 1998), suggesting more than 4.7 million tons will be produced in 2019 alone.
Chicken feathers (ChFs) are an abundantly available food industry waste in need of valorization. With billions of kilograms generated from commercial meat processing of ChFs (Acda, 2010), there has been particular interest in the removal of these materials in an economical and environmentally considerate manner (Tesfaye et al., 2017). Although this waste can be incinerated, some of it may end up in landfill where it can produce methane gas. The production of methane gas possesses a greater concern for global greenhouse gas production and atmospheric damage. As an alternative to landfill or incineration, some research has been conducted to look into the biodegradation of ChF through bacterial fermentation (Zaghloul et al., 2011). In some cases, the high protein content of feathers has suggested their use as animal feed stock, but some nutritional value is lost during processing and there could be concerns with digestibility (Papadopoulos, 1985).
An alternative to landfill, animal feed or incineration is to generate value added products from the waste. To do so, the complete composition is required to determine what can be extracted, whether the material is thermally stable and other key features. According to literature, ChFs contain about 82% crude protein, 2% crude fiber, 0.8% crude lipid, and 1.5% ash (Tesfaye et al., 2017). Of the protein content, 90% is made of keratin (Zaghloul et al., 2011) which has suggested it use in animal feed after proper treatment (Tesfaye et al., 2017). Based on the chemical composition and surplus of ChFs available, research has shifted its focus to the use of these materials in value-added applications.
The use of ChF to generate value-added composites has been studied by Cheng et al. In their work, ChF fibers were combine in a poly(lactic acid) (PLA) matrix to generate green composites. The ChF fibers were combined at weight concentrations of 2, 5, 8, and 10%. The authors determined that the addition of ChF fibers resulted in increasing the elastic modulus by 116%. Overall, the addition of ChF fibers to the PLA matrix resulted in successful development of composites that could be used in non-load bearing applications (Cheng et al., 2009). Other works also combined ChF with PLA and found similar results with increased stiffness (Özmen and Baba, 2017). To further improve the performance of ChF composites, Reddy et al. combined powdered ChFs and glycerol as a matrix with jute fiber reinforcement for compression molding applications (Reddy et al., 2014). From those works, ChF have proven to be a material capable of generating sustainable composites. However, there are other uses for waste ChF.
In addition to the use of ChF directly, there have been many efforts to carbonize the material through pyrolysis. Pyrolysis is a thermochemical conversion of biological waste. As a result of heating samples to high temperature in an inert atmosphere, the biomass is converted to syn-gas, bio-oil, and biocarbon (Mohanty et al., 2018). Currently, research has looked into the use of ChF biocarbon as a hydrogen storage material (Senoz and Wool, 2011), the development of microspheres (Gao et al., 2014), as well as supercapacitors (Zhao et al., 2015). There are many other potential uses for this ChF biocarbon in electronics and composites.
Composites containing biocarbon have been under substantial investigation. Biocarbon from other waste materials such as lignin (Demir et al., 2015) and miscanthus (Behazin et al., 2016) have been studied. The use of ChF biocarbon may have potential for unique composites. There are some limitations with biocarbon composites. The mechanical performance of the biocomposites is largely dependent on the size (Nagarajan et al., 2016), pyrolysis temperature and structure of the biocarbon. Like biocomposites made with other natural fibers, compatibilizers can be used to improve performance (Codou et al., 2018). The combination of ideal biocarbon, matrix materials and compatibilizers can improve the biocomposites' performance and generate successful products for a number of applications.
The use of food processing industry waste to generate value-added products provides societal, economic and environmental benefits. The use of ChF diverts waste from landfill which may produce harmful gases such as methane and generates cost effective materials. This paper intends to provide a physical and chemical analysis of ChF biocarbon generated at two pyrolysis temperatures. The ChF biocarbon was combined with PLA matrix to generate sustainable composites. The thermal, mechanical properties and composition of the samples were analyzed. The valorization of ChF through the generation of sustainable natural filler for composites applications offers a safe and suitable alternative use for this material.
Maple Leaf Foods Inc. (Canada) sterilized the chicken feathers (ChFs) in an autoclave steam sterilization system and then supplied the ChFs to the University of Guelph. For the preparation of polymer composites, Ingeo PLA 3251D (NatureWorks LLC, USA) was used as the polymer matrix.
The only pre-treatment to these materials were the sterilization upon receiving samples. ChFs were dried in an oven at 85°C in order to remove moisture. There were two samples of ChF analyzed in this work which included: (1) pulverized (powder) and (2) as received feathers. The pulverized samples were ground for 5–7 s in a cryogenic grinder (Lab made, modified by CCR Technologies, Canada) at 3,600 rpm. The ChF powder was dried in a vacuum oven at 85°C for 24 h before pyrolysis.
To produce biocarbon in greater quantities, ChFs and ChF powder were directly pyrolyzed in a large-scale tube furnace. A stainless steel reactor was manufactured in situ in substitution of the ceramic reactor. The pyrolyzer was supplied with a thermocouple to accurately measure the internal temperature, and an externally suppled nitrogen source which was used during the process. The samples were then pyrolyzed at temperatures of 300 and 600°C with a residence time of 30 min. After pyrolysis, the furnace was cooled to room temperature. Samples collected after pyrolysis were ball milled for 1 h using a Retsch ball mill machine at 300 rpm. Ball milled samples were further characterized. The yield content was obtained by calculating the difference in mass of the original ChF in comparison resulting biocarbon left after pyrolysis.
Biocomposites were made by combining PLA and ChF produced at two different biocarbon pyrolysis temperatures (300 and 600°C). Processing was conducted in a 15 mL micro-compounder, DSM Xplore, with a twin screw extruder (Netherlands). The processing temperature was 190°C and the screw speed was 100 rpm. The retention time was 2 min before injection molding at 30°C in a DSM Xplore microinjection molding machine. ChF biocarbon content was set at 20 wt.% in this composite.
Maleic-anhydride grafted (MA-g) PLA composites were fabricated under the same conditions.
Two methods were used to measure the ash content of ChF powder and ChF biocarbon: gravimetric and thermogravimetric. The gravimetric method was based on ASTM D1762-84 (reapproved 2013). Samples were loaded into a crucible, heated to 750°C for 6h and then cooled. Final weights were obtained as per the ASTM standard. The thermogravimetric method, based on ASTM E1131-08, was completed by thermogravimetric analysis (TGA, Q500, TA Instruments, USA). ChF powder and ChF biocarbon were heated from room temperature to 110°C at a rate of 10°C/min and held for 5 min in a nitrogen atmosphere. Then, the samples were continued to be heated to 900°C at a rate of 10°C/min and kept for 15 min. After that, the atmosphere was switched to air and the samples kept at 900°C for another 10 min.
Spectra were obtained from a Thermo Scientific Nicolet 6700 FTIR spectrometer (Waltham, Massachusetts, USA). The attenuated total reflectance (ATR) mode was used and the spectra were obtained by 64 scans at a resolution of 4 cm−1. The background samples of the surrounding atmosphere were taken prior to samples collection. The spectra were obtained between wave numbers of 500 and 4,000 cm−1 in transmittance mode.
A TGA Q5500 (TA Instruments, USA) was used in combination with a FTIR machine of the same make as mentioned above. The experiment analyzed about 6 mg over a ramped heating (20°C/minute) of 25 to 650°C in an inert atmosphere. A total of 8 scans were taken per minute and combined. A Gram-Schmidt curve was made for further analysis to determine the relative absorbance of each volatile gas released during the pyrolysis study. A future study could be completed in further works as a comparison of this process to traditional petroleum-based fillers as well as the overall environmental impact.
The elemental and morphology analyzes of ChF powder and ChF biocarbon were examined by a ProX scanning electron microscope (SEM) (Phenom-World BV, Eindhoven, The Netherlands) with energy-dispersive spectroscopy (EDS) integrated into the setup. SEM images were recorded at 10 kV accelerating voltage. The elemental determinations by EDS spectra were obtained at 10 kV under a 90 s collection time. In this process the samples were analyzed uncoated.
For PLA/ChF composite, the fractured surfaces of impact samples were sputtered with a thin layer of gold for 10 s. Then, SEM images of PLA/ChF composites were taken at 10 kV accelerating voltage.
X-ray diffraction spectroscopy (XRD) of biocarbon was completed using a X-Ray Diffractometer (MultiFlex Rigaku, Rigaku, Japan) with a 2 kW CuKα source. A horizontal sample mount was also implemented in combination with a diffracted beam monochromator. Diffraction patterns were obtained between 5° and 50° with a scan speed of 1.2° per minute.
Raman spectroscopy was conducted on a DXR2 Raman Spectroscope (Thermo Scientific, USA). Raman analysis was used to determine the relative amounts of graphitic vs. disordered carbon in the samples. The machine was operated at 10 times zoom through a 50 μm slit.
Thermogravimetric analysis (TGA) (TA instrument, Q500, USA) was used to characterize the thermal stability of the polymer composites. All samples experienced heating from room temperature to 600°C at a rate of 10°C/min in a nitrogen atmosphere. Differential scanning calorimetry (DSC) (TA instrument, Q200, USA) was used to study the melting temperature, glass transition temperature and crystallization temperature. Samples were placed in a nitrogen atmosphere and heated from 0 to 200°C at a rate of 10°C/min, held for 3 min and cooled to 0°C at a rate of 10°C/min.
An Instron 3382 Universal Testing Machine was used for the measurement of mechanical properties of PLA/ChF composites. ASTM D638 was used as a standard for the tensile test at room temperature with a rate of 5 mm/min. Flexural properties of PLA/ChF composites were characterized based on ASTM D790 with a testing rate of 1.4 mm/min and a span of 52 mm. Five test pieces of each sample were tested for tensile and flexural tests to take the average value, and all tensile and flexural properties were analyzed with Bluehill software.
It is important to evaluate the pyrolysis yield to determine if the material is feasible for large scale applications, such as automotive parts. For this work, the yield of biocarbon for chicken feathers (ChFs) and powder at 300°C was 55% (Table 1). Comparatively, this is a high yield. However, at higher pyrolysis temperatures, the yield decreased to 25 and 16% for powder and feathers, respectively. The decrease in yield as the temperature increased has been reported by others (Budai et al., 2014; Arnold et al., 2016). There is often a decrease in yield at higher temperature because more constituents are decomposed, such as higher molecular weight molecules. This means that the oxygen and hydrogen groups in the material are removed at higher temperatures. This was confirmed later through elemental analysis of the samples.
Ash content of biocarbon varies greatly depending on the feedstock material (Ronsse et al., 2013), and is mainly comprised of a combination of hydrogen, nitrogen, oxygen and sulfur (Tesfaye et al., 2017). The two methods to generate ash content are described above in the methods section. The ash content for the ChFs was found to be 1.5% regardless of the method (Table 2), which is consistent with literature (Wool, 2005). In fact, Wool (2005) suggested that the extremely low ash would make this waste material useful for fuel generation.
However, biocarbon samples experienced different values for the ash content dependent on the methods used. It is probable that the ChF samples did not experience the same trend as their maximal degradation temperature is substantially lower than that of the biocarbon and is not affected by the final operating temperature.
For the biocarbon samples, the maximal operating temperature for the gravimetric method, based on ASTM D1762-84 (reapproved 2013), was 750°C. By comparison, the TGA method, based on the ASTM E1131-08, reached a final operating temperature of 900°C. For example, the ash content of 600°C ChF biocarbon measured by the gravimetric method was 5.4%, but was 8.9% by the TGA method.
In addition to ash content, the TGA method also provided valuable information as to the content of highly volatile matter, volatile matter, and combustible material. An example of the analysis is displayed in Figure 1. A summary of all remaining materials can be found in Table 3. The volatile matter remaining in the 300°C sample was greater than that of the 600°C sample. This was a result of a lower pyrolysis temperature since less matter is removed during the process. Likewise, there is more combustible material for the higher temperature BC samples.
The combination of highly volatile and volatile material from chicken feathers was 77.4% which is very similar to other works with ChFs (Tesfaye et al., 2017; Table 3). The volatile materials are a combination of hydrocarbons, methane and carbon monoxide as well as some nitrogen gas and carbon dioxide (Tesfaye et al., 2017). When comparing the biocarbon sources, the lower pyrolysis temperature produced a larger percentage of volatile matter. This corresponds with literature where biomass sources with lower ignition temperatures often possess greater volatile matter content. This is a result of volatile content being directly correlated with heating rate and final temperature (Basu, 2010).
FTIR spectra of the ChF powder and ChF biocarbon samples are shown in Figure 2. The ChFs show a distinctive peak at 3,279 cm−1 which can be attributed to the O-H stretching (Mothé et al., 2018). Another absorption band at 2,922 cm−1 corresponds to the aliphatic C-H stretching vibrations (Mothé et al., 2018). The peak at 1,482 cm−1 that is noted in ChFs and lower temperature biocarbon samples is associated with C-H stretching of alkanes (Azargohar et al., 2014). The peak at 1,660 cm−1 is assigned to C=O stretching vibrations, and the peaks at 1,513 and 1,445 cm−1 correspond to the amine groups N-H2 and N-H, respectively (Mothé et al., 2018). In fact, Mothé et al. attributed these peaks to the keratin structures within the ChFs (Mothé et al., 2018). As determined in the elemental analysis below, there is approximately 3 wt.% of sulfur in the ChF samples, suggesting that the bands near 1,230 cm−1 may be related to the presence of thiol groups (Mothé et al., 2018). Lastly, the peak at 1,523 cm−1 is associated with the C=C bonds contained in the samples (Azargohar et al., 2014). The presence of this bond is later confirmed by Raman analysis.
The FTIR spectra for the biocarbon samples displayed a decrease in peak intensity from ChF where the 600°C samples show no peaks. The diminishing peaks are a result of removing the functional groups with higher pyrolysis temperatures having the greatest impact. This has also been found in works by Snowdon et al. with carbonized lignin (Snowdon et al., 2014). The largest peak in the 300°C biocarbon, around 1,640 cm−1, is probably produced from C=O conjugated bonds (Snowdon et al., 2014).
For most biomass sources, the commonly produced gases during pyrolysis include: carbon dioxide, methane, carbon monoxide and hydrogen gas (Domínguez et al., 2007). The volatile matter generated during the pyrolysis process is depicted in Figure 3A. This work obtained resulted similar to that of pyrolyzed turkey feathers. The gaseous products of turkey feather subject to pyrolysis in air were examined to determine the major gaseous materials. For the 600°C turkey feathers: hydrogen gas < methane < carbon dioxide < carbon monoxide (Domínguez et al., 2007). For this work, effluent containing carbonyl groups was in the greatest concentration followed by carbon dioxide. All volatile materials were identified from the Gram Schmidt curve in Figure 3B. Most of the volatiles were identified as similar to other FTIR-TGA analysis in literature (Singh et al., 2011; Ma et al., 2014). However, unique to ChFs, there is substantially more nitrogen content which is evolved as NH4 from the samples. The production of NH4 was much greater than the amount produced through pyrolysis of other types of biomasses (e.g., woody or grass-based). This was most likely attributed to the increased nitrogen content in the sample as confirmed in EDS and elemental analysis discussions below.
Figure 3. TGA-FTIR analysis of chicken feathers with (A) maximal evolved volatiles and (B) Gram-Schmidt spectra.
Morphological characteristics of ChF powder and ChF biocarbon samples at differing pyrolysis temperatures are shown in Figure 4. The ChF powder was cryogenically ground for only 5~7 s, resulting in variation of particle size and structure. The two most distinguishable structures in the ChF samples are fibrous tubes and large platelets (Figure 4A). The fibrous tubes may be from the barbs on the feathers whereas the platelets may be from the quill (calamus) and rachis (Belarmino et al., 2012). The ChF biocarbon samples pyrolyzed at 600°C displayed larger sizes than lower temperature samples. This was also found by Quosai et al. where the higher temperature samples had a greater surface area (Quosai et al., 2018). The larger surface area of the 600°C biocarbon may have fostered an increased opportunity for interactions with the polymer matrix and resulted in improved mechanical performance over 300°C samples, as noted below.
Figure 4. SEM images of (A) ChF powder, (B) ChF biocarbon 300°C (powder), (C) ChF biocarbon 300°C (feathers), (D) ChF biocarbon 600°C (powder), and (E) ChF biocarbon 600°C (feathers).
The elemental composition including carbon, nitrogen, oxygen, and sulfur was obtained via EDS for ChF and is displayed in Table 4. The ChF samples were found to have relatively similar amounts of C, N, and O around ~30 wt.% and S content about 3.3 wt.%. Based on literature, there is a large variation of elemental composition of samples. The variation in experimental vs. literature is a result of different analysis methods as well as a difference in the quills vs. barbs content of the samples (Gao et al., 2014).
The elemental composition of ChF biocarbon was also obtained via EDS and is recorded in Table 4. It was found that the carbon content was similar for all samples, regardless of the pyrolysis temperature or original ChF structure (i.e. powder or feathers). Similar results were reported for nitrogen. The sulfur content of the BC samples decreased substantially as a result of disulfide bond cleavage at higher pyrolysis temperatures (Zhao et al., 2015). Essentially, the amounts of carbon, nitrogen and oxygen were similar as show via EDS. This was a unique finding for this work since other works have shown that increasing the pyrolysis temperature substantially increases carbon content. For example, green waste and wood biocarbon from 300 to 600°C pyrolysis temperature experienced more than 60% increase in carbon content (Ronsse et al., 2013). This is most likely due to the higher nitrogen content in the samples as compared to other woody biomasses.
The XRD results of ChF powder and biocarbon samples pyrolyzed at different temperatures are shown in Figure 5. There were two distinguishable peaks at 2θ = 9° and 19° for ChF. The peak at 9° is associated with the α-helix configuration of keratin, whereas the 19° is actually a combination of two indistinguishable peaks for the β-sheet structure of keratin for ChF samples (Ma et al., 2016). The structures for the 300°C biocarbon, regardless of whether the starting material was feathers or powder, resulted in a broad peak with its maximum at 2θ = 20°. In literature, this peak was associated with the amorphous carbon (Yu et al., 2018). However, the peak for the 600°C biocarbon reaches it maximal value at 2θ = 26°. This peak is more likely associated with graphitic carbon (Major et al., 2018), or more specifically the (002) plane (Yu et al., 2018). In literature, higher pyrolysis temperatures are associated with a reduction in interplanar d-spacing of the graphitic sheets such that the spacing between the planes decreases. This may explain the shift in peaks between the 300 and 600°C samples (Arnold et al., 2016).
The Raman spectra for ChF biocarbon are displayed in Figure 6. The spectra were analyzed from 800 to 2,000 cm−1 to determine the graphitic content in the samples. A total of five peaks were used to fit the data, as used in literature (Anstey et al., 2016). The spectra for the feather and powder samples were similar, so only the powders are discussed in this section. The peak intensity is much greater for lower temperature ChF biocarbon. This was also found in samples which were derived from Miscanthus (Major et al., 2018). The peak maximums at 1,350 and 1,550 cm−1 for the D and G bands, correspondingly and were found in both samples. This aligns with literature for other biocarbon samples (Anstey et al., 2016). In literature, the D band corresponds with the sp2 orbital and represents the disordered content in the samples; whereas the G band is associated with the sp2 orbitals of the graphitic content in the sample. The ID/IG ratios for the 300 and 600°C were 1.06 and 1.07, respectively, which describe the graphitization of the samples (Major et al., 2018). Biocarbon samples from other waste biomass that were pyrolyzed at 475°C (between the pyrolysis temperatures of this work) found similar ratios for ID/IG at 1.10 and 1.11 for wheat straw and poultry litter, respectfully (Azargohar et al., 2014). The Raman spectra are aligned with other results. The ID band is associated with C-C bonds contained in aromatic rings (Li et al., 2006). The relative strength of this peak can be correlated with the large carbon content in the samples, as proven by elemental analysis. Furthermore, the IG peak has been documented in literature to correspond to C=C, also found in aromatic structures (Li et al., 2006). The C=C bonds were confirmed in FTIR analysis.
Biocomposites were made with combining 20 wt.% ChF (pulverized powder) biocarbon and 80 wt.% PLA. Tensile and flexural properties of neat PLA and ChF biocarbon composites are shown in Figure 7. The tensile strength, elongation at break and flexural strength decreased with increasing biocarbon content. The decrease in both tensile and flexural strength is common for samples with higher filler content. In fact, Chang et al. noted that biocarbon content >15 wt.% leads to agglomeration of the particles and reduced stress transfer (Chang et al., 2019). This was further confirmed by the reduction in impact strength compared to the neat polymer. However, the tensile and flexural moduli increased with the addition of filler. In fact, the highest composite values obtained were 16 and 26% greater than neat polymer for tensile and flexural modulus, respectfully. This finding is common for biocarbon composites since the biocarbon restricts the mobility of the matrix polymer chains, thereby increasing the stiffness of the samples (Ogunsona et al., 2018).
Figure 7. ChF biocarbon composites (A) tensile strength and modulus, (B) flexural strength and modulus. Sample labels in the x axis are as follows: (I) Neat PLA, (II) 80/20 PLA/ biocarbon (300°C), (III) 80/20 PLA/biocarbon (600°C), (IV) 77/20/3 PLA/biocarbon/MA-g-PLA (600°C).
A compatibilizer, maleic-anhydride-grafted-PLA (MA-g-PLA), was combined at 3 wt.% with the 600°C biocarbon samples. The MA content of 3 wt.% was chosen based upon success in literature with natural fillers and PLA (Yu et al., 2014) as well as PBS (Gowman et al., 2018; Picard et al., 2019). To increase the adhesion between filler and matrix, compatibilizing agents have been studied with biocarbon (Codou et al., 2018). The 600°C biocarbon composite was chosen to be compatibilized based on its superior performance to the 300°C samples where the tensile strength and flexural strength increased by 31 and 53% from 300 to 600°C biocomposites, respectfully. The improvement in mechanical performance of samples containing MA-g-PLA was further confirmed via SEM (Figure 8C). The reduction of gaps between the biocarbon and matrix suggested improved interfacial adhesion between these constituents (Behazin et al., 2017a), resulting in improved stress transfer between the filler and compatibilized matrix (Picard et al., 2019).
The impact strength for the neat polymer was 22.9 J/m. However, the uncompatibilized sample experienced a reduction in impact strength as compared to the neat to 14.32 J/m for 300°C ChF BC samples and 17.23 J/m for 600°C ChF BC samples. This was attributed to poor surface adhesion between the filler and matrix. Similar results have been reported in literature with other natural fillers as well (Picard et al., 2019). The addition of MA-g-PLA improved the impact strength to 19.53 J/m for the 77//20/3 (PLA/ChF biocarbon/Ma-g-PLA) samples. Similarly, increased impact strength from the addition of a compatibilizer has been found in literature with compatibilized biopolymer and miscanthus grass as the natural filler (Muthuraj et al., 2017). Further properties analysis showed that the addition of 20 wt.% ChF BC had no significant change on density with both samples exhibiting a density of 1.25 g/cm−3.
The losses in mechanical performance of the ChF biocarbon at 20 wt.% in this work were comparable to that of ChF in PLA composites at weight percentages of 0–10. In fact, in this work the tensile modulus was 4 GPa or greater were as 5 wt.% ChF PLA composites experienced a max tensile modulus near 4 GPa but the other concentrations of ChFs resulted in inferior tensile moduli (Cheng et al., 2009). Although there were some challenges with mechanical performance it is important to note that ChF biocarbon could also be combined with other higher strength materials such as engineering thermoplastics. In this case, the ChF biocarbon would offer superior thermal stability as well as little to no odor during the extrusion process as compared to ChFs. The volatile matter was already expelled from ChF biocarbon, as seen in the TGA-FTIR analysis and would not interfere with the extrusion process. Based on the TGA analyses, ChFs would degrade during the higher processing temperatures.
The glass transition temperature (Tg), melting temperature (Tm), and crystallization temperature (Tc) are displayed in Table 5. The Tg decreases with the addition of biocarbon. This is also noted in works with PLA and biocarbon (Salak et al., 2014). In this work, there was no notable change in the melt temperature that was taken from the second heating cycle. The melting temperature form the second heating had the thermal history removed and is, therefore, a more accurate measure. The Tc value slightly increased with the addition of biocarbon suggesting that the biocarbon may act as a nucleating agent for the PLA (Behazin et al., 2017b). Similar results were found with biocarbon and PP composites (Behazin et al., 2017b).
Table 5. Thermal results obtained from digital scanning calorimetry for neat polymer and composites.
The maximum degradation temperature and 5% weight loss are displayed in Table 6. The weight loss was around 5% at the end of the first heating plateau. The addition of biocarbon to the polymer increased the degradation rate, as noted from the lower temperature. This has often been found in literature with biocarbon in a polyamide matrix (Ogunsona et al., 2018). Overall, the polymer was found to be stable over the entire processing window. However, the addition of biocarbon slightly reduced the thermal stability of the samples. Other biocomposites also experience this decrease in thermal stability with addition of natural filler; for example natural filler composites made with apple pomace in BioPBS (Picard et al., 2019), biocarbon in polyamide (Ogunsona et al., 2018), and wood flour in PLA (Liu et al., 2010).
SEM images of the impact surfaces of neat polymer and composites are displayed in Figure 8. Figure 8A shows the typical fracture surface of PLA which is smooth as a result of the brittle, semi-crystalline nature of the polymer (Ferrarezi et al., 2013). The brittle nature of the polymer is confirmed by the relatively high tensile strength, as noted in Figure 7A. Figure 8B shows gaps between the ChF biocarbon and matrix material. As discussed earlier, this is noted as a decrease in interfacial adhesion and is the reason for reduced mechanical performance (Picard et al., 2019). From Figure 8, it was noted that the matrix remained relatively smooth with improved adhesion to the biocarbon. The SEM confirms that there was less de-cohesion between the filler and the biocarbon, resulting in less pull-out. Similar results were found in literature with compatibilized biocarbon composites (Codou et al., 2018) and confirmed by improved impact strength.
The use biocarbon as a filler offers greater thermal stability over natural fillers from food/ beverage industry waste. For example apple pomace and grape pomace are wastes from the wine and cider or juice industries begin degradation at substantially lower temperatures. For example, 5% weight loss of the sample occurs at approximately 120°C (Picard et al., 2019) and 175°C (Gowman et al., 2018), respectfully. Neat chicken feather (ChF) fibers have been found to begin to lose 5 wt.% at just over 100°C (Özmen and Baba, 2017). Conversely, ChF biocarbon 300 and 600°C did not experience 5% weight loss until about 220 and 400°C, respectfully. This suggests that ChF biocarbon offers the added benefit of thermal stability and could function with high temperature engineering thermoplastics. Works comparing ChF to pyrolyzed ChF biocomposites have confirmed improved thermal stability (Senoz et al., 2013).
Moreover, ChF feather biocarbon is a food industry waste product and can be obtained at no cost. This is one advantage over petroleum produced carbon black. The production of biocarbon compared to petroleum products requires less energy during the heating process since carbon black requires conversion temperatures of 1,320–1,540°C (United States Environmental Protection Agency, 1983). In this work the maximal pyrolysis temperature was 600°C which is nearly half of carbon black. Also, ChF biocarbon is black in color and could replace carbon black where it is used as a coloring agent. Other works have investigate the viability of biocarbon and determined that it can be used as a feasible alternative as well as functional in non-electrical applications (Snowdon et al., 2014).
The use of ChF biocarbon as mentioned previous is also beneficial to that of plain ChF due to lesser concerns for odor. The evolved gases, displayed in TGA-FTIR analysis, would not be present during the extrusion process as compared to that of ChF alone. In addition to the previously discussed benefits of ChF biocarbon, the use of biocarbon materials has also been suggested to replace traditional in organic fillers such as mineral fillers (Myllytie et al., 2016). There is also a reduction in the density of biocarbon as compared to traditional inorganic fillers such as glass fiber and talc; to 1.3 g/cm3 for biocarbon from 2.7 g/cm3 for talc and glass fiber (Chang et al., 2019). This leads to light-weight composites and the corresponding benefits of reduced fuel consumption when implemented in the automotive industry. There are many benefits that have been discussed in relation to the implementation of ChF biocarbon in composite applications. The use of biologically based materials helps to improve the sustainability, cost, and adds value to newly made products.
Chicken feathers (ChF), a byproduct of the meat processing industry, are abundantly available and in need of new uses to avoid end of life in landfill or incineration. This work features the thermochemical conversion of ChFs to biocarbon for value-added applications. ChFs were pyrolyzed at 300 and 600°C to generate sustainable natural filler for biocomposites. The biocarbon produced at 300°C resulted in a surprising yield of 55% and both biocarbon samples possessed exceptional thermal stability at much greater temperatures than that of many traditional natural fillers. With this in mind, ChF biocarbon was combined with PLA, a biodegradable and biobased plastic. The biocomposites were analyzed for their mechanical performance. Despite a decrease in tensile strength, the tensile modulus for each composite blend was greater than that of the neat polymer. SEM images determined the biocarbon was well-distributed throughout the matrix such that it could act as a reinforcing agent. The composites contained 20 wt.% of the 600°C ChF biocarbon, and a biobased biodegradable polymer also displayed improved flexural and tensile modulus over that of the neat polymer. ChF biocarbon has the added benefits of reduced odor during processing as compared to ChFs, as well the ChF biocarbon could function well as a replacement to traditional petroleum-based colorants like carbon black as well as mineral fillers like talc. The successful combination of natural filler and biobased, biodegradable polymer suggests the use of these biocomposites for sustainable packaging applications.
The raw data supporting the conclusions of this article will be made available by the authors, without undue reservation, to any qualified researcher.
All authors listed have made a substantial, direct and intellectual contribution to the work, and approved it for publication.
All of the mentioned funding sources mentioned above provided financial support for this work. Maple Leaf Foods also provided in-kind support and donated samples.
The authors declare that this study received in-kind support and donation of samples from Maple Leaf Foods (Mississauga, Ontario, Canada). Maple Leaf Foods was not involved in the study design, collection, analysis, interpretation of data, the writing of this article or the decision to submit it for publication.
The authors are thankful to the Ontario Ministry of Agriculture, Food and Rural Affairs (OMAFRA) (Canada)/University of Guelph—Bioeconomy for Industrial Uses Research Program Project # 030331; the Natural Sciences and Engineering Research Council (NSERC) (Canada), Canada Discovery Grants Project # 400320 and 401111; and the Ontario Research Fund, Research Excellence Program; Round-7 (ORF-RE07) from the Ontario Ministry of Research, Innovation and Science (MRIS) Project # 052644 and 052665, for their financial support. A special thanks to Maple Leaf Foods (6897 Financial Drive, Mississauga, Ontario, L5N 0A8) for their donation of the samples.
Acda, M. N. (2010). “Sustainable use of waste chicken feather for durable and low cost building materials for tropical climates,” in Sustainable Agriculture: Technology, Planning and Management, eds A. Salazar and I. Rios (Laguna Beach, CA: Nova Science Publishers, Inc.), 353–366.
Anstey, A., Vivekanandhan, S., Rodriguez-Uribe, A., Misra, M., and Mohanty, A. K. (2016). Oxidative acid treatment and characterization of new biocarbon from sustainable Miscanthus biomass. Sci. Total Environ. 550, 241–247. doi: 10.1016/j.scitotenv.2016.01.015
Arnold, S., Rodriguez-Uribe, A., Misra, M., and Mohanty, A. K. (2016). Slow pyrolysis of bio-oil and studies on chemical and physical properties of the resulting new bio-carbon. J. Clean. Prod. 172, 2748–2758. doi: 10.1016/j.jclepro.2017.11.137
Azargohar, R., Nanda, S., Kozinski, J. A., Dalai, A. K., and Sutarto, R. (2014). Effects of temperature on the physicochemical characteristics of fast pyrolysis bio-chars derived from Canadian waste biomass. Fuel 125, 90–100. doi: 10.1016/j.fuel.2014.01.083
Basu, P. (2010). “Biomass Characteristics,” in Biomass Gasification, Pyrolysis and Torrefaction, eds R. Zanol and M. L. Kuhl (London: Elsevier Inc.), 27–63. doi: 10.1016/B978-0-12-374988-8.00002-7
Behazin, E., Misra, M., and Mohanty, A. K. (2017a). Compatibilization of toughened polypropylene/biocarbon biocomposites: a full factorial design optimization of mechanical properties. Polym. Test. 61, 364–372. doi: 10.1016/j.polymertesting.2017.05.031
Behazin, E., Misra, M., and Mohanty, A. K. (2017b). Sustainable biocarbon from pyrolyzed perennial grasses and their effects on impact modified polypropylene biocomposites. Compos. Part B Eng. 118, 116–124. doi: 10.1016/j.compositesb.2017.03.003
Behazin, E., Ogunsona, E., Rodriguez-Uribe, A., Mohanty, A. K., Misra, M., and Anyia, A. O. (2016). Mechanical, chemical, and physical properties of wood and perennial grass biochars for possible composite application. BioResources 11, 1334–1348. doi: 10.15376/biores.11.1.1334-1348
Belarmino, D. D., Ladchumananandasivam, R., Belarmino, L. D., Pimentel, J. R. D. M., da Rocha, B. G., Galvão, A. O., et al. (2012). Physical and morphological structure of chicken feathers (Keratin Biofiber) in natural, chemically and thermally modified forms. Mater. Sci. Appl. 03, 887–893. doi: 10.4236/msa.2012.312129
Budai, A., Wang, L., Gronli, M., Strand, L. T., Antal, M. J., Abiven, S., et al. (2014). Surface properties and chemical composition of corncob and miscanthus biochars: effects of production temperature and method. J. Agric. Food Chem. 62, 3791–3799. doi: 10.1021/jf501139f
Chang, B. P., Mohanty, A. K., and Misra, M. (2019). Sustainable biocarbon as an alternative of traditional fillers for poly(butylene terephthalate)-based composites: thermo-oxidative aging and durability. J. Appl. Polym. Sci. 136, 1–14. doi: 10.1002/app.47722
Cheng, S., Lau, K., Liu, T., Zhao, Y., Lam, P. M., and Yin, Y. (2009). Mechanical and thermal properties of chicken feather fiber/PLA green composites. Compos. Part B Eng. 40, 650–654. doi: 10.1016/j.compositesb.2009.04.011
Codou, A., Misra, M., and Mohanty, A. K. (2018). Sustainable biocarbon reinforced nylon 6/polypropylene compatibilized blends: effect of particle size and morphology on performance of the biocomposites. Compos. Part A Appl. Sci. Manuf. 112, 1–10. doi: 10.1016/j.compositesa.2018.05.018
Demir, M., Kahveci, Z., Aksoy, B., Palapati, N. K. R., Subramanian, A., Cullinan, H. T., et al. (2015). Graphitic biocarbon from metal-catalyzed hydrothermal carbonization of lignin. Ind. Eng. Chem. Res. 54, 10731–10739. doi: 10.1021/acs.iecr.5b02614
Domínguez, A., Menéndez, J. A., Fernández, Y., Pis, J. J., Nabais, J. M. V., Carrott, P. J. M., et al. (2007). Conventional and microwave induced pyrolysis of coffee hulls for the production of a hydrogen rich fuel gas. J. Anal. Appl. Pyrolysis 79, 128–135. doi: 10.1016/j.jaap.2006.08.003
Ferrarezi, M. M. F., de Oliveira Taipina, M., da Silva, L. C. E., Gonçalves, M., and Carmo Gonçalves, M. (2013). Poly(ethylene glycol) as a compatibilizer for poly(lactic acid)/thermoplastic starch blends. J. Polym. Environ. 21, 151–159. doi: 10.1007/s10924-012-0480-z
Food Agriculture Organization of the United Nations (2019). Global Initiative on Food Loss and Waste Reduction. FAO. Available online at: http://www.fao.org/save-food/resources/keyfindings/en/ (accessed August 14, 2019).
Gao, L., Hu, H., Sui, X., Chen, C., and Chen, Q. (2014). One for two: conversion of waste chicken feathers to carbon microspheres and (NH4)HCO3. Environ. Sci. Technol. 48, 6500–6507. doi: 10.1021/es5006708
Gowman, A., Wang, T., Rodriguez-Uribe, A., Mohanty, A. K., and Misra, M. (2018). Bio-poly(butylene succinate) and its composites with grape pomace: mechanical performance and thermal properties. ACS Omega 3, 15205–15216. doi: 10.1021/acsomega.8b01675
Li, X., Hayashi, J., and Li, C.-Z. (2006). FT-Raman spectroscopic study of the evolution of char structure during the pyrolysis of a Victorian brown coal. Fuel 85, 1700–1707. doi: 10.1016/j.fuel.2006.03.008
Liu, X., Khor, S., Petinakis, E., Yu, L., Simon, G., Dean, K., et al. (2010). Effects of hydrophilic fillers on the thermal degradation of poly(lactic acid). Thermochim. Acta 509, 147–151. doi: 10.1016/j.tca.2010.06.015
Ma, B., Qiao, X., Hou, X., and Yang, Y. (2016). Pure keratin membrane and fibers from chicken feather. Int. J. Biol. Macromol. 89, 614–621. doi: 10.1016/j.ijbiomac.2016.04.039
Ma, Z., Chen, D., Gu, J., Bao, B., and Zhang, Q. (2014). Determination of pyrolysis characteristics and kinetics of palm kernel shell using TGA-FTIR and model-free integral methods. Energy Convers. Manag. 89, 251–259. doi: 10.1016/j.enconman.2014.09.074
Major, I., Pin, J.-M., Behazin, E., Rodriguez-Uribe, A., Misra, M., and Mohanty, A. (2018). Graphitization of Miscanthus grass biocarbon enhanced by in situ generated FeCo nanoparticles. Green Chem. 20, 2269–2278. doi: 10.1039/C7GC03457A
Mohanty, A. K., Vivekanandhan, S., Pin, J.-M., and Misra, M. (2018). Composites from renewable and sustainable resources: challenges and innovations. Science 362, 536–542. doi: 10.1126/science.aat9072
Mothé, M. G., Viana, L. M., and Mothé, C. G. (2018). Thermal property study of keratin from industrial residue by extraction, processing and application. J. Therm. Anal. Calorim. 131, 417–426. doi: 10.1007/s10973-017-6845-8
Muthuraj, R., Misra, M., and Mohanty, A. K. (2017). Biodegradable biocomposites from poly(butylene adipate-co-terephthalate) and miscanthus: preparation, compatibilization, and performance evaluation. J. Appl. Polym. Sci. 134, 1–9. doi: 10.1002/app.45448
Myllytie, P., Misra, M., and Mohanty, A. K. (2016). Carbonized lignin as sustainable filler in biobased poly(trimethylene terephthalate) polymer for injection molding applications. ACS Sustain. Chem. Eng. 4, 102–110. doi: 10.1021/acssuschemeng.5b00796
Nagarajan, V., Mohanty, A. K., and Misra, M. (2016). Biocomposites with size-fractionated biocarbon: influence of the microstructure on macroscopic properties. ACS Omega 1, 636–647. doi: 10.1021/acsomega.6b00175
Ogunsona, E. O., Codou, A., Misra, M., and Mohanty, A. K. (2018). Thermally stable pyrolytic biocarbon as an effective and sustainable reinforcing filler for polyamide bio-composites fabrication. J. Polym. Environ. 26, 3574–3589. doi: 10.1007/s10924-018-1232-5
Onifade, A. A., Al-Sane, N. A., Al-Musallam, A. A., and Al-Zarban, S. (1998). A review: potentials for biotechnological applications of keratin-degrading microorganisms and their enzymes for nutritional improvement of feathers and other keratins as livestock feed resources. Bioresour. Technol. 66, 1–11. doi: 10.1016/S0960-8524(98)00033-9
Özmen, U., and Baba, B. O. (2017). Thermal characterization of chicken feather/PLA biocomposites. J. Therm. Anal. Calorim. 129, 347–355. doi: 10.1007/s10973-017-6188-5
Papadopoulos, M. C. (1985). Processed chicken feathers as feedstuff for poultry and swine. a review. Agric. Wastes 14, 275–290. doi: 10.1016/S0141-4607(85)80009-3
Picard, M. C., Rodriguez-Uribe, A., Thimmanagari, M., Misra, M., and Mohanty, A. K. (2019). Sustainable biocomposites from poly(butylene succinate) and apple pomace: a study on compatibilization performance. Waste Biomass Valorization 2019, 1–13. doi: 10.1007/s12649-019-00591-3
Quosai, P., Anstey, A., Mohanty, A. K., and Misra, M. (2018). Characterization of biocarbon generated by high- and low-temperature pyrolysis of soy hulls and coffee chaff: for polymer composite applications. R. Soc. Open Sci. 5, 1–16. doi: 10.1098/rsos.171970
Reddy, N., Jiang, J., and Yang, Y. (2014). Biodegradable composites containing chicken feathers as matrix and jute fibers as reinforcement. J. Polym. Environ. 22, 310–317. doi: 10.1007/s10924-014-0648-9
Ronsse, F., van Hecke, S., Dickinson, D., and Prins, W. (2013). Production and characterization of slow pyrolysis biochar: influence of feedstock type and pyrolysis conditions. GCB Bioenergy 5, 104–115. doi: 10.1111/gcbb.12018
Salak, F., Uemura, S., and Sugimoto, K. (2014). Thermal pretreatment of kudzu biomass (Pueraria lobata)as filler in cost-effective PLA biocomposite fabrication process. Polym. Eng. Sci. 55, 340–348. doi: 10.1002/pen.23909
Senoz, E., Stanzione, J. F., Reno, K. H., Wool, R. P., and Miller, M. E. N. (2013). Pyrolyzed chicken feather fibers for biobased composite reinforcement. J. Appl. Polym. Sci. 128, 983–989. doi: 10.1002/app.38163
Senoz, E., and Wool, R. P. (2011). Hydrogen storage on pyrolyzed chicken feather fibers. Int. J. Hydrogen Energy 36, 7122–7127. doi: 10.1016/j.ijhydene.2011.03.061
Singh, S., Wu, C., and Williams, P. T. (2011). Pyrolysis of waste materials using TGA-MS and TGA-FTIR as complementary characterisation techniques. J. Anal. Appl. Pyrolysis 94, 99–107. doi: 10.1016/j.jaap.2011.11.011
Snowdon, M. R., Mohanty, A. K., and Misra, M. (2014). A study of carbonized lignin as an alternative to carbon black. ACS Sustain. Chem. Eng. 2, 1257–1263. doi: 10.1021/sc500086v
Tesfaye, T., Sithole, B., Ramjugernath, D., and Chunilall, V. (2017). Valorisation of chicken feathers: characterisation of chemical properties. Waste Manag. 68, 626–635. doi: 10.1016/j.wasman.2017.06.050
United States Department of Agriculture (2019). Livestock and Poultry: World Markets and Trade. Available online at: https://apps.fas.usda.gov/psdonline/circulars/livestock_poultry.pdf (accessed August 13, 2019).
United States Environmental Protection Agency (1983). “6.1 Carbon Black,” in Compilation of Air Pollutant Emission Factors (Washington, DC), 1–10. Available online at: https://www3.epa.gov/ttn/chief/ap42/ch06/final/c06s01.pdf (accessed November 12, 2019).
Wool, R. P. (2005). “Carbon Fibers from Chicken Feathers,” in Bio-Based Polymers and Composites, eds R. P. Wool and X. S. Sun (New York, NY: Elsevier Inc.), 435–447. doi: 10.1016/B978-012763952-9/50005-8
Yu, M., Saunders, T., Su, T., Gucci, F., and Reece, M. (2018). Effect of heat treatment on the properties of wood-derived biocarbon structures. Materials 11:1588. doi: 10.3390/ma11091588
Yu, T., Jiang, N., and Li, Y. (2014). Study on short ramie fiber/poly(lactic acid) composites compatibilized by maleic anhydride. Compos. Part A Appl. Sci. Manuf. 64, 139–146. doi: 10.1016/j.compositesa.2014.05.008
Zaghloul, T. I., Embaby, A. M., and Elmahdy, A. R. (2011). Biodegradation of chicken feathers waste directed by Bacillus subtilis recombinant cells: scaling up in a laboratory scale fermentor. Bioresour. Technol. 102, 2387–2393. doi: 10.1016/j.biortech.2010.10.106
Keywords: biocarbon, biocomposite, sustainability, biodegradable, interface, chicken feathers
Citation: Li Z, Reimer C, Picard M, Mohanty AK and Misra M (2020) Characterization of Chicken Feather Biocarbon for Use in Sustainable Biocomposites. Front. Mater. 7:3. doi: 10.3389/fmats.2020.00003
Received: 30 September 2019; Accepted: 07 January 2020;
Published: 07 February 2020.
Edited by:
Alessandro Pegoretti, University of Trento, ItalyReviewed by:
Veronique Michaud, École Polytechnique Fédérale de Lausanne, SwitzerlandCopyright © 2020 Li, Reimer, Picard, Mohanty and Misra. This is an open-access article distributed under the terms of the Creative Commons Attribution License (CC BY). The use, distribution or reproduction in other forums is permitted, provided the original author(s) and the copyright owner(s) are credited and that the original publication in this journal is cited, in accordance with accepted academic practice. No use, distribution or reproduction is permitted which does not comply with these terms.
*Correspondence: Amar K. Mohanty, bW9oYW50eUB1b2d1ZWxwaC5jYQ==; Manjusri Misra, bW1pc3JhQHVvZ3VlbHBoLmNh
†These authors have contributed equally to this work
Disclaimer: All claims expressed in this article are solely those of the authors and do not necessarily represent those of their affiliated organizations, or those of the publisher, the editors and the reviewers. Any product that may be evaluated in this article or claim that may be made by its manufacturer is not guaranteed or endorsed by the publisher.
Research integrity at Frontiers
Learn more about the work of our research integrity team to safeguard the quality of each article we publish.